
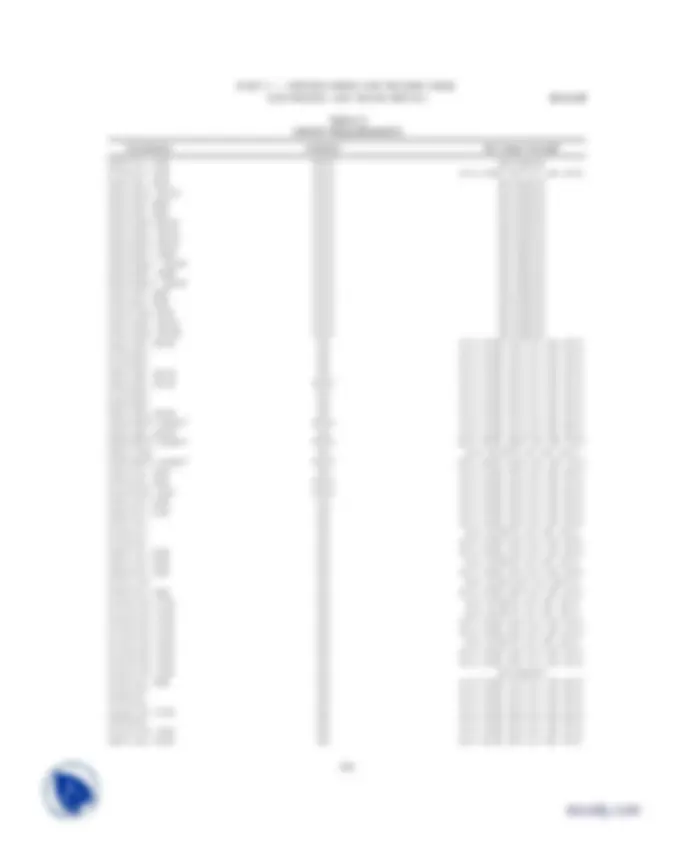
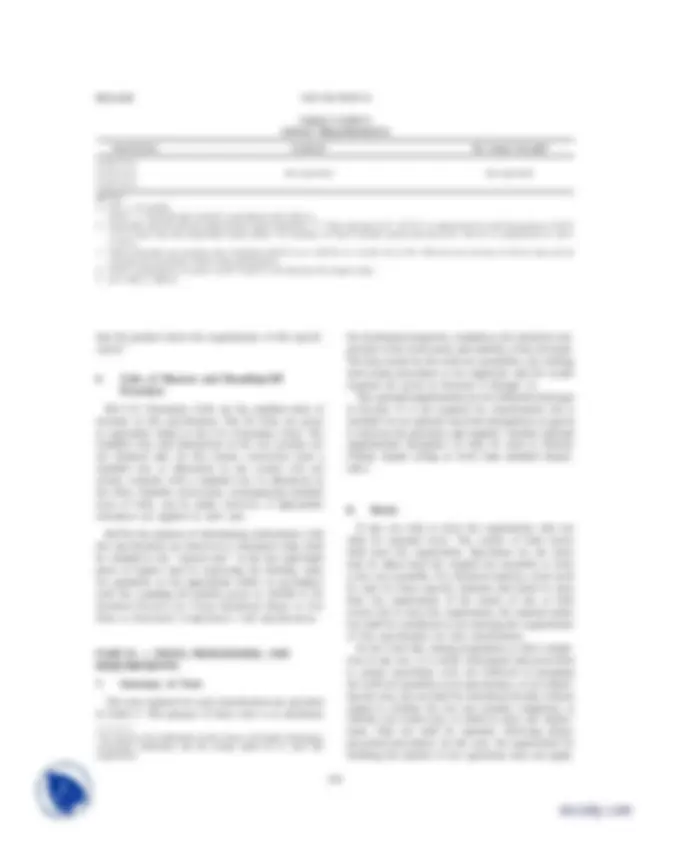
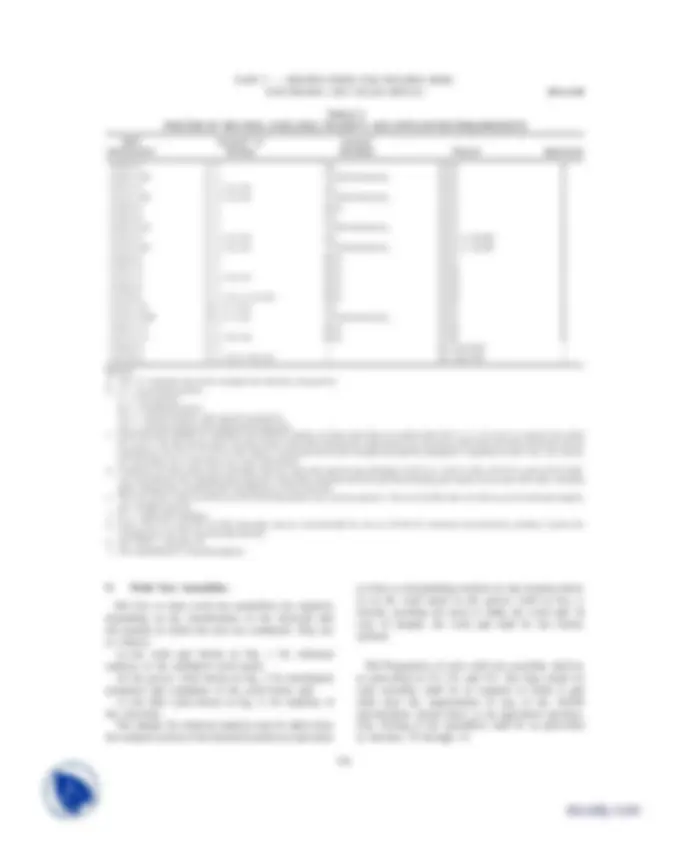
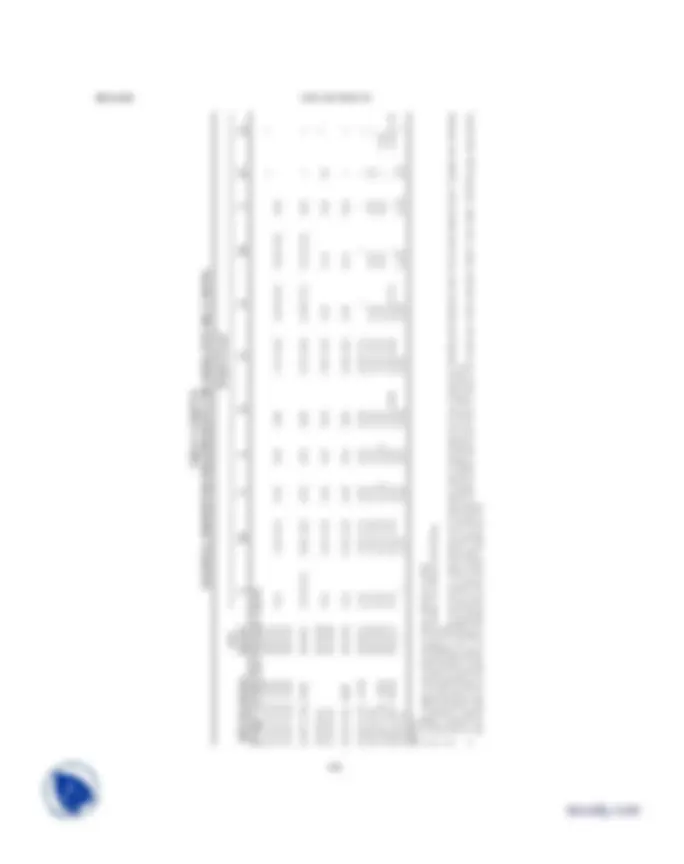
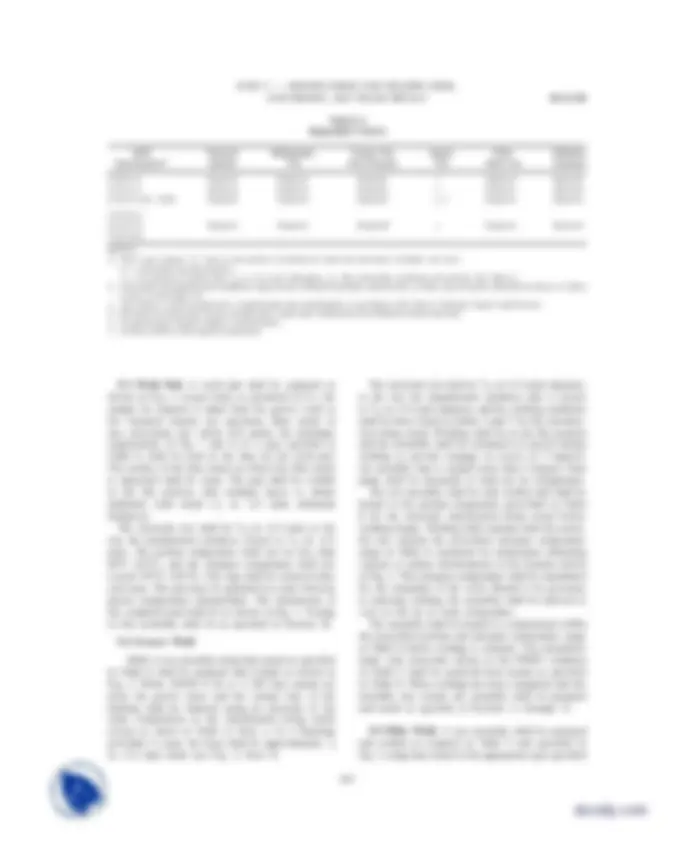
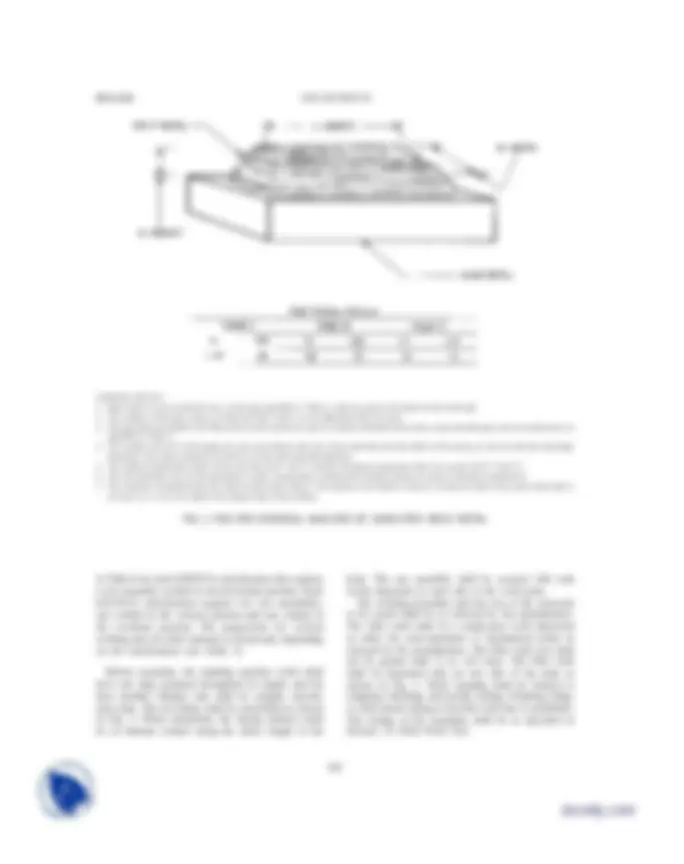
Study with the several resources on Docsity
Earn points by helping other students or get them with a premium plan
Prepare for your exams
Study with the several resources on Docsity
Earn points to download
Earn points by helping other students or get them with a premium plan
Community
Ask the community for help and clear up your study doubts
Discover the best universities in your country according to Docsity users
Free resources
Download our free guides on studying techniques, anxiety management strategies, and thesis advice from Docsity tutors
Information on astm standards for various types of welding electrodes and filler metals, including their classification, chemical composition requirements, and required tests. References to standards for carbon structural steel, pressure vessel plates, and high-yield strength quenched and tempered alloy steel plates. It also specifies impact requirements and position, shielding, polarity, and application requirements for different types of electrodes.
Typology: Exercises
1 / 10
This page cannot be seen from the preview
Don't miss anything!
1. Scope
This specification prescribes requirements for the
classification of low-alloy steel electrodes for flux cored
arc welding (FCAW). Metal cored low-alloy steel elec-
trodes are classified according to ANSI/AWS A5.28-
96, Specification for Low-Alloy Steel Filler Metals for
Gas Shielded Arc Welding. 1 Iron is the only element
whose content exceeds 10.5 percent in weld metal
produced using electrodes classified by this document.
PART A — GENERAL REQUIREMENTS
2. Normative References
2.1 ASTM Standards.^2 The following ASTM stan-
dards are referenced in the mandatory sections of this
document:
(a) A 36/A 36M, Specification for Carbon Struc-
tural Steel
(b) A 203/A 203M, Specification for Pressure Vessel
Plates, Alloy Steel, Nickel
(c) A 204/A 204M, Specification for Pressure Vessel
Plates, Alloy Steel, Molybdenum
(d) A 285/A 285M, Specification for Pressure Vessel
Plates, Carbon Steel, Low- and Intermediate-Tensile
Strength
(e) A 302/A 302M, Specification for Pressure Vessel
Plates, Alloy Steel, Manganese-Molybdenum and Man-
ganese-Molybdenum-Nickel
(^1) AWS standards can be obtained from the American Welding Society,
550 N.W. LeJeune Road, Miami, FL 33126. (^2) ASTM standards can be obtained from the American Society for Testing and Materials, 100 Barr Harbor Drive, West Conshohocken, PA 19428.
(f) A 387/A 387M, Specification for Pressure Vessel Plates, Alloy Steel, Chromium Molybdenum (g) A 514/A 514M, Specification for High-Yield Strength, Quenched and Tempered Alloy Steel Plate, Suitable for Welding (h) A 537/A 537M, Specification for Pressure Vessel Plates, Heat Treated, Carbon-Manganese-Silicon Steel (i) A 588/A 588M, Specification for High-Strength Low-Alloy Structural Steel with 50 ksi [345 MPa] Minimum Yield Point to 4 in. [100 mm] Thick (j) E 29, Practice for Using Significant Digits in Test Data to Determine Conformance with Specifications (k) E 142, Standard Test Methods for Controlling Quality of Radiographic Testing (l) E 350, Standard Test Methods for Chemical Analysis of Carbon Steel, Low-Alloy Steel, Silicon Elec- trical Steel, Ingot Iron, and Wrought Iron
2.2 AWS Standards. The following ANSI/AWS standards are referenced in the mandatory sections of this document: (a) ANSI/AWS A5.01, Filler Metal Procurement Guidelines (b) ANSI/AWS A4.3, Standard Methods for Determi- nation of the Diffusible Hydrogen Content of Marten- sitic, Bainitic, and Ferritic Steel Weld Metal Produced by Arc Welding (c) ANSI/AWS B4.0, Standard Methods for Mechan- ical Testing of Welds (d) ANSI/ASC Z49.1, Safety in Welding, Cutting, and Allied Processes
2.3 MIL Standards.^3 The following MIL standard is referenced in the mandatory sections of this document:
(^3) MIL standards are available from contracting activity or as directed by contracting activity.
Yield Strength @ 0.2% % Elongation in Tensile Strength Range Offset, Min. 2 in. (51 mm) AWS Classification a^ ksi MPa ksi MPa Min.
E6XTX-X, -XM 60–80 410–550 50 340 22 E7XTX-X, -XM 70–90 480–620 58 400 20 E8XTX-X, -XM 80–100 550–690 68 470 19 E9XTX-X, -XM 90–110 620–760 78 540 17 E10XTX-X, -XM 100–120 690–830 88 610 16 E10XTX-K9, -K9M (c) (c) 82–97 560–670 18 E11XTX-X, -XM 110–130 760–900 98 680 15 E12XTX-X, -XM 120–140 830–970 108 745 14
EXXTX-G (b) EXXTG-X (b)^ Properties as agreed upon between supplier and purchaser EXXTG-G (b)
NOTES: (a) The “X’s” in actual classification designations will be replaced with appropriate designators for usability characteristics specified in Table 3 and for chemical composition as specified in Table 4. (b) Placement of a “G” in this designation indicates those properties that have been agreed upon between the supplier and purchaser. Other properties are dictated by the digit(s) or suffix replacing the X. Variations used in this specification include the following: (1) EXXTX-G — Alloy requirements are as agreed upon. The mechanical properties and slag system are as indicated by the digits used. (2) EXXTG-X — The slag system and shielding gas are as agreed upon. Mechanical properties and alloy requirements conform to those indicated by the digits. (3) EXXTG-G — The slag system, shielding gas, and alloy requirements are as agreed upon. Mechanical properties conform to those indicated by the digits. (c) For this classification, E10XTX-K9, K9M, the “10” is an approximation of the tensile strength, not a requirement.
(a) MIL-S-16216, Specification for Steel Plate, Alloy,
Structural, High Yield Strength (HY-80 and HY-100)
3. Classification
3.1 The electrodes covered by this specification are
classified according to the following:
(a) the mechanical properties of the weld metal, as
specified in Tables 1 and 2;
(b) certain usability characteristics of the electrode,
as specified in Table 3;
(c) the positions of welding for which the electrodes
are suitable, as specified in Table 3; and
(d) chemical composition of the weld metal, as speci-
fied in Table 4.
3.2 Electrodes classified under one classification shall
not be classified under any other classification in this
specification. However, gas shielded electrodes may be
classified with 100 percent CO 2 shielding gas, 75 to
80 percent argon/balance CO 2 shielding gas or both. The ‘‘M’’ designator means that the electrode has been
classified with a 75 to 80 percent argon/balance CO (^2)
shielding gas mixture.
3.3 The electrodes classified under this specification are intended for FCAW either with or without an external shielding gas. Electrodes intended for use without external shielding gas, or with the shielding gases specified in Table 3, are not prohibited from use with any other process or shielding gas for which they are found suitable.
4. Acceptance
Acceptance of the welding electrodes shall be in accordance with the provisions of ANSI/AWS A5.01, Filler Metal Procurement Guidelines.
5. Certification
By affixing the AWS Specification and Classification designations to the packaging, or the classification designations to the product, the manufacturer certifies
Classification Condition a^ Min. Impact Strength b
EXXXTX-G EXXXTG-G Not Specified e^ Not Specified e EXXXTG-X
NOTES: a. AW p As welded. PWHT p Postweld heat treated in accordance with Table 8. b. Electrodes with the optional supplemental impact designator “J” shall meet the 20 ft · lbf (27 J) requirement at a test temperature of 20°F (11°C) lower than the temperature shown above. For example, an E81T1-Ni1MJ would meet the 20 ft · lbf (27 J) requirement at −40°F (−40°C). c. These electrodes are presently also Classified E502TX-X or E505TX-X in AWS A5.22-95. With the next revision of A5.22, they will be removed and exclusively listed in this specification. d. PWHT temperatures in excess 1150°F (620°C) will decrease the impact value. e. See Table 1, Note b.
that the product meets the requirements of this specifi-
cation. 4
6. Units of Measure and Rounding-Off
Procedure
6.1 U.S. Customary Units are the standard units of
measure in this specification. The SI Units are given
as equivalent values to the U.S. Customary Units. The standard sizes and dimensions in the two systems are
not identical and, for this reason, conversion from a
standard size or dimension in one system will not
always coincide with a standard size or dimension in
the other. Suitable conversions, encompassing standard
sizes of both, can be made, however, if appropriate
tolerances are applied in each case.
6.2 For the purpose of determining conformance with
this specification, an observed or calculated value shall
be rounded to the ‘‘nearest unit’’ in the last right-hand
place of figures used in expressing the limiting value
for quantities in the appropriate tables in accordance
with the rounding-off method given in ASTM E 29,
Standard Practice for Using Significant Digits in Test
Data to Determine Conformance with Specifications.
PART B — TESTS, PROCEDURES, AND
REQUIREMENTS
7. Summary of Tests
The tests required for each classification are specified
in Table 5. The purpose of these tests is to determine
(^4) See Section A4, Certification (in the Annex), for further information concerning certification and the testing called for to meet this requirement.
the mechanical properties, soundness, the chemical com- position of the weld metal, and usability of the electrode. The base metal for the weld test assemblies, the welding and testing procedures to be employed, and the results required are given in Sections 9 through 14. The optional supplemental test for diffusible hydrogen in Section 15 is not required for classification, but is included for an optional electrode designation as agreed to between the purchaser and supplier. Another optional supplemental designator (J) may be used to indicate Charpy impact testing at lower than standard temper- ature.
8. Retest
If any test fails to meet the requirement, that test shall be repeated twice. The results of both retests shall meet the requirement. Specimens for the retest may be taken from the original test assembly or from a new test assembly. For chemical analysis, retest need be only for those specific elements that failed to meet their test requirement. If the results of one or both retests fail to meet the requirement, the material under test shall be considered as not meeting the requirements of this specification for that classification. In the event that, during preparation or after comple- tion of any test, it is clearly determined that prescribed or proper procedures were not followed in preparing the weld test assembly or test specimen(s), or in conduct- ing the tests, the test shall be considered invalid, without regard to whether the test was actually completed, or whether test results met, or failed to meet, the require- ment. That test shall be repeated, following proper prescribed procedures. In this case, the requirement for doubling the number of test specimens does not apply.
AWS Position b, c^ of External Classificationa^ Welding Shielding d^ Polarity e^ Application f
EX0T1-X H, F CO 2 DCEP M EX0T1-XM H, F 75–80%Ar/bal CO 2 DCEP M EX1T1-X H, F, VU, OH CO 2 DCEP M EX1T1-XM H, F, VU, OH 75–80%Ar/bal CO 2 DCEP M EX0T4-X H, F None DCEP M EX0T5-X H, F CO 2 DCEP M EX0T5-XM H, F 75–80%Ar/bal CO 2 DCEP M EX1T5-X H, F, VU, OH CO 2 DCEP or DCEN g^ M EX1T5-XM H, F, VU, OH 75–80%Ar/bal CO 2 DCEP or DCEN g^ M EX0T6-X H, F None DCEP M EX0T7-X H, F None DCEN M EX1T7-X H, F, VU, OH None DCEN M EX0T8-X H, F None DCEN M EX1T8-X H, F, VU, or VD, OHi^ None DCEN M EXXT1-K9 VU, H, F, OH CO 2 DCEP M EXXT1-K9M VU, H, F, OH 75–80%Ar/bal CO 2 DCEP M EX0T11-X H, F None DCEN M EX1T11-X H, F, VD, OH None DCEN M EX0TG-X H, F — Not Specifiedh^ — EX1TG-X H, F, VU or VD, OH — Not Specifiedh^ —
NOTES: a. The “X” indicates the tensile strength and chemical composition. b. H p Horizontal position F p Flat position OH p Overhead position VU p Vertical position with upward progression VD p Vertical position with downward progression c. Electrode sizes suitable for welding in all positions usually are those sizes that are smaller than the 3 ⁄ 32 in. (2.4 mm) or nearest size called for in 9.4.1 for the groove weld. For that reason, electrodes meeting the requirements for the groove weld tests and fillet weld tests may be classified as EX1TX-X or EX1TX-XM (where X represents the tensile strength and usability designator) regardless of their size. See Section A7 and Figure A1 in the Annex for more information. d. Properties of weld metal from electrodes that are used with external gas shielding (EXXT1-X, EXXT1-XM, EXXT5-X, and EXXT5-XM) vary according to the shielding gas employed. Electrodes classified with the specified shielding gas should not be used with other shielding gases without first consulting the manufacturer of the electrode. e. The term DCEP refers to direct current electrode positive (dc, reverse polarity). The term DCEN refers to direct current electrode negative (dc, straight polarity). f. M p single and multipass. g. Some EX1T5-X and EX1T5-XM electrodes may be recommended for use on DCEN for improved out-of-position welding. Consult the manufacturer for the recommended polarity. h. See Table 1, footnote (b). i. Per manufacturer’s recommendations.
9. Weld Test Assemblies
9.1 Two or three weld test assemblies are required,
depending on the classification of the electrode and
the manner in which the tests are conducted. They are
as follows:
(a) the weld pad shown in Fig. 1 for chemical
analysis of the undiluted weld metal,
(b) the groove weld shown in Fig. 2 for mechanical
properties and soundness of the weld metal, and
(c) the fillet weld shown in Fig. 3, for usability of
the electrode. The sample for chemical analysis may be taken from
the reduced section of the fractured tension test specimen
or from a corresponding location (or any location above it) in the weld metal in the groove weld in Fig. 2, thereby avoiding the need to make the weld pad. In case of dispute, the weld pad shall be the referee method.
9.2 Preparation of each weld test assembly shall be as prescribed in 9.3, 9.4, and 9.5. The base metal for each assembly shall be as required in Table 6 and shall meet the requirements of any of the ASTM specifications shown there, or an equivalent specifica- tion. Testing of the assemblies shall be as prescribed in Sections 10 through 14.
Weight-Percent
a
AWS Classification
Number
b^
Mn
Si
Ni
Cr
Mo
Al
c^
Cu
Nickel-Steel Electrodes (Cont’d) EX8T1-Ni2, -Ni2M
E8XT5-Ni2, -Ni2M
E9XT1-Ni2, Ni2M
E7XT8-Ni
E8XT8-Ni
E8XT5-Ni3, -Ni3M
E9XT5-Ni3, -Ni3M
E8XT11-Ni
Manganese-Molybdenum Steel Electrodes E9XT1-D1, -D1M
All Other Low-Alloy Steel Electrodes E8XT5-K1, -K1M
Weight-Percent
a
AWS Classification
Number
b^
Mn
Si
Ni
Cr
Mo
Al
c^
Cu
All Other Low-Alloy Steel Electrodes (Cont’d) E11XT1-K4, -K4M
e^
e^
e^
e^
e^
e^
e^
NOTES:a.
Single values are maximum unless otherwise noted. b.
SAE/ASTM Unified Numbering System for Metals and Alloys. c.
For self-shielded electrodes only. d.
Classification also appears in AWS A5.22-95,
Specification for Stainless Steel Electrodes for Flux Cored Arc Welding and Stainless Steel Flux Cored Rods for Gas Tungsten Arc Welding.
These classifications will be deleted from the first revision of A5.22 following publication of this specification. e.
In order to meet the alloy requirements of the G group, the undiluted weld metal shall have the minimum of at least one of the elements listed in this table. Shielding gas, slag system,and mechanical properties are dictated by the digit(s) replacing X(s).
in Table 6 for each EX0TX-X classification that requires
a test assembly welded in the horizontal position. Each
EX1TX-X classification requires two test assemblies,
one welded in the vertical position and one welded in
the overhead position. The progression for vertical
welding may be either upward or downward, depending
on the classification (see Table 3).
Before assembly, the standing member (web) shall
have one edge prepared throughout its length, and the
base member (flange) side shall be straight, smooth,
and clean. The test plates shall be assembled as shown in Fig. 3. When assembled, the faying surfaces shall
be in intimate contact along the entire length of the
joint. The test assembly shall be secured with tack welds deposited at each end of the weld joint. The welding procedure and the size of the electrode to be tested shall be as selected by the manufacturer. The fillet weld shall be a single-pass weld deposited in either the semi-automatic or mechanized mode as selected by the manufacturer. The fillet weld size shall not be greater than 3 ⁄ 8 in. (9.5 mm). The fillet weld shall be deposited only on one side of the joint as shown in Fig. 3. Weld cleaning shall be limited to chipping, brushing, and needle scaling. Grinding, filing, or other metal cutting of the fillet weld face is prohibited. The testing of the assembly shall be as specified in Section 14, Fillet Weld Test.