
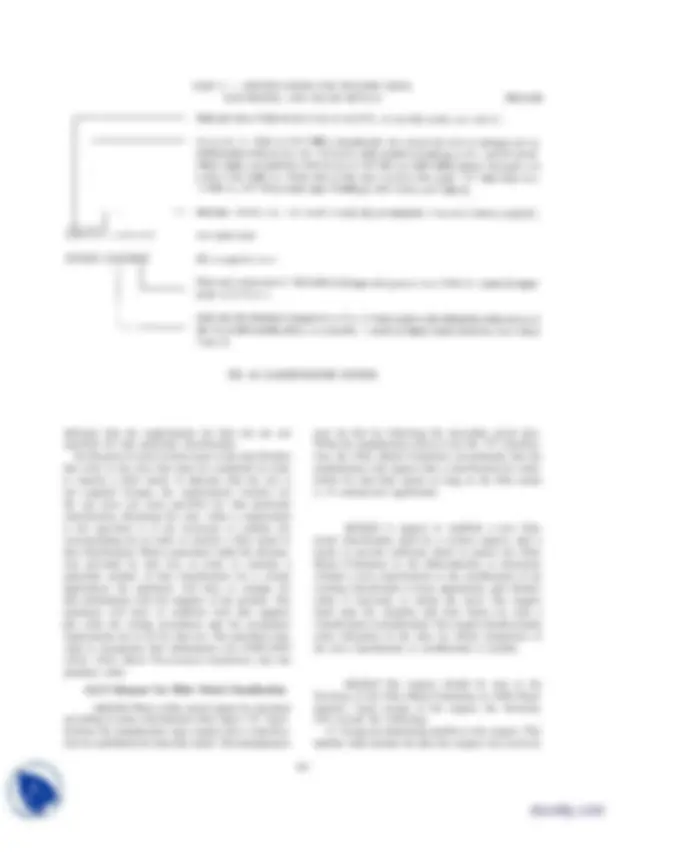
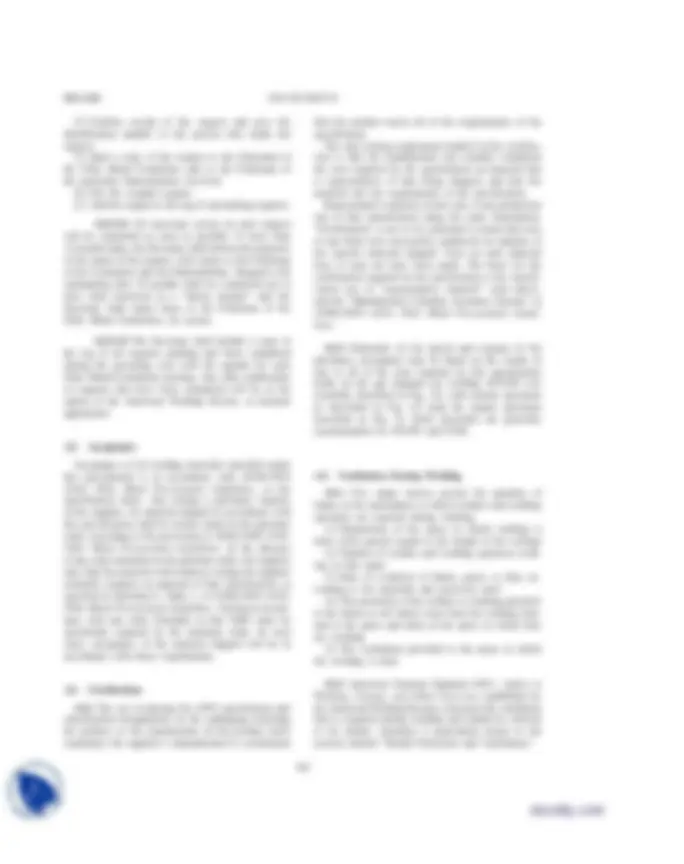
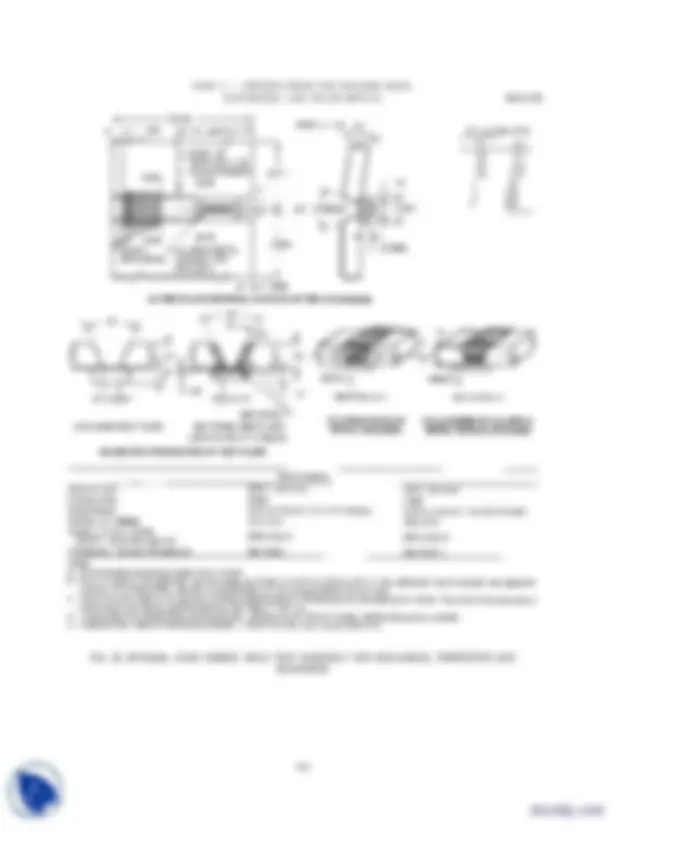
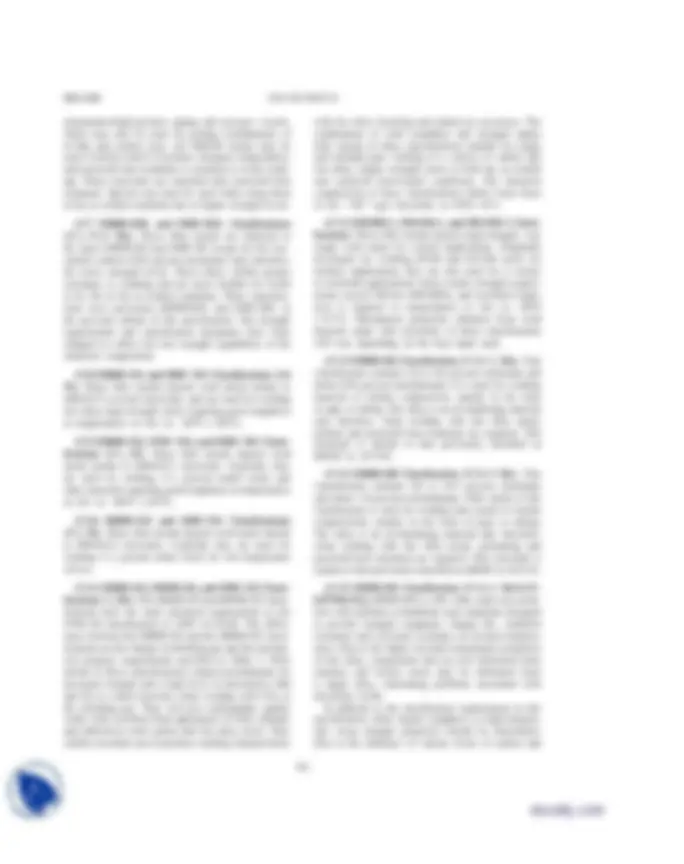
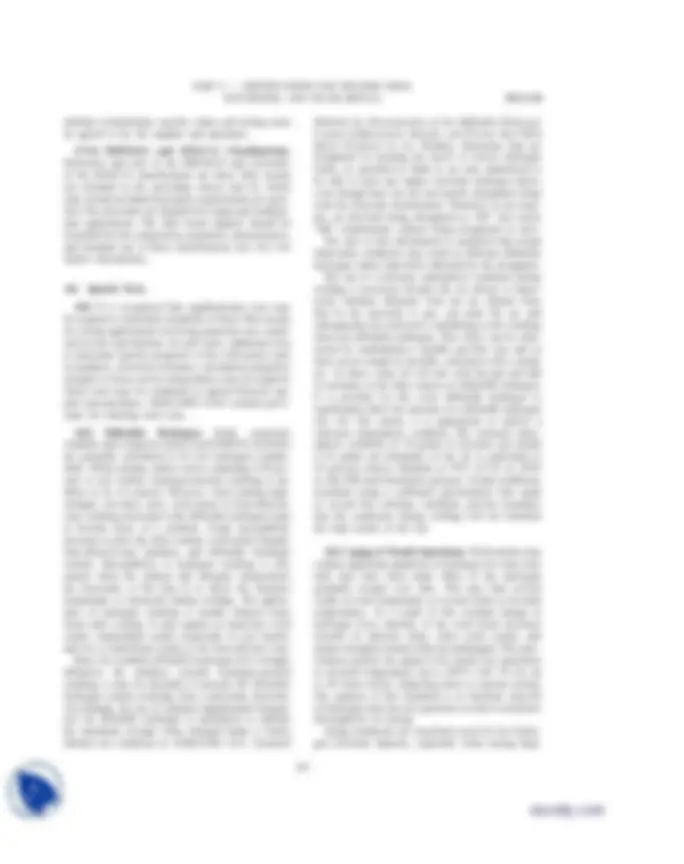
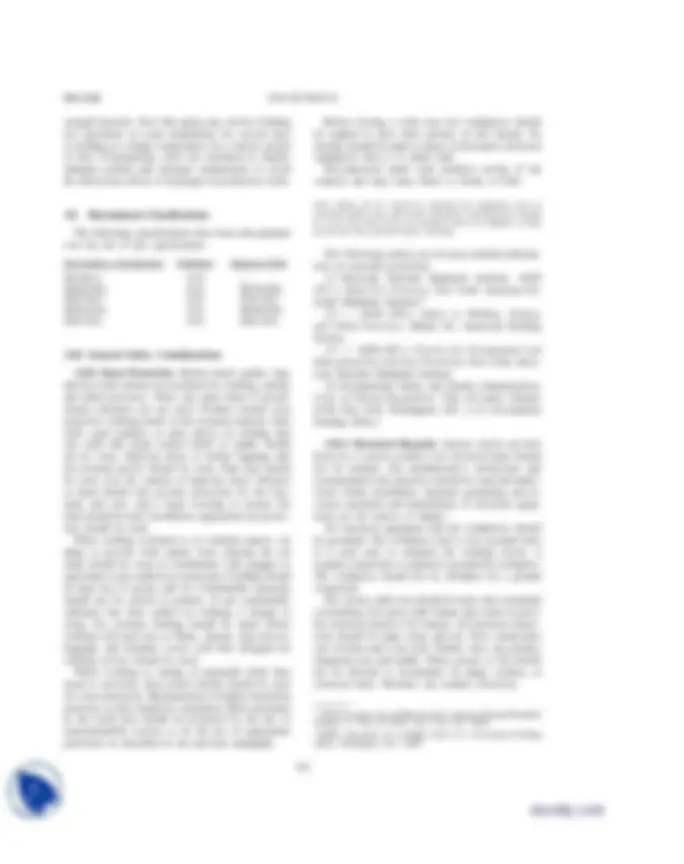
Study with the several resources on Docsity
Earn points by helping other students or get them with a premium plan
Prepare for your exams
Study with the several resources on Docsity
Earn points to download
Earn points by helping other students or get them with a premium plan
Community
Ask the community for help and clear up your study doubts
Discover the best universities in your country according to Docsity users
Free resources
Download our free guides on studying techniques, anxiety management strategies, and thesis advice from Docsity tutors
Information on the classification system for welding filler metals according to their chemical composition, with a focus on erxxs-g and exxc-g classifications. It also discusses the five major factors affecting the quantity of fumes in welding environments and the necessary ventilation requirements. Additionally, the document covers the non-ionizing radiation safety measures during welding, including the use of welding filter plates and protective clothing.
Typology: Exercises
1 / 12
This page cannot be seen from the preview
Don't miss anything!
PART C — SPECIFICATIONS FOR WELDING RODS, ELECTRODES, AND FILLER METALS SFA-5.
O Protect yourself and others. Read and understand this information. FUMES AND GASES can be hazardous to your health. ARC RAYS can injure eyes and burn skin. ELECTRIC SHOCK can kill. O Before use, read and understand the manufacturer’s instructions, Material Safety Data Sheets (MSDSs), and your employer’s safety practices. O Keep your head out of the fumes. O Use enough ventilation, exhaust at the arc, or both, to keep fumes and gases away from your breathing zone and the general area. O Wear correct eye, ear, and body protection. O Do not touch live electrical parts. O See American National Standard Z49.1, Safety in Welding, Cutting, and Allied Processes, published by the American Welding Society, 550 N.W. LeJeune Road, Miami, Florida 33126; OSHA Safety and Health Standards, 29 CFR 1910, available from the U.S. Government Printing Office, Washington, DC 20402.
585
SFA-5.28 1998 SECTION II
(This Annex is not a part of ANSI⁄AWS A5.28-96, Specification for Low-Alloy Electrodes and Rods for Gas Shielded Arc Weld- ing, but is included for information only.)
A1. Introduction
The purpose of this guide is to correlate the electrode and rod classifications with their intended applications so the specification can be used effectively. Reference to appropriate base metal specifications is made when- ever that can be done and when it would be helpful. Such references are intended only as examples rather than complete listings of the materials for which each filler metal is suitable.
A2. Classification System
A2.1 The system for identifying the electrode classi- fications in this specification follows the standard pattern used in other AWS filler metal specifications as shown in Fig. A1.
A2.2 The prefix “E” designates an electrode as in other specifications. The letters “ER” indicate that the filler metal may be used either as an electrode or a rod. The digits following (70, 80, 90, 100, 110, or
586
whether the electrode will meet a maximum diffusible hydrogen level of 16, 8, 4, or 2 ml ⁄100 g of weld metal when tested as outlined in this specification.
A2.3 “G” Classification and the Use of “Not Speci- fied” and “Not Required”
A2.3.1 This specification includes filler metals classified as ERXXS-G, and EXXC-G. The “G” indi- cates that the filler metal is of a general classification. It is “general” because not all of the particular require- ments specified for each of the other classifications are specified for this classification. The intent in establishing these classifications is to provide a means by which filler metals that differ in one respect or another (chemical composition, for example) from all other classifications (meaning that the composition of the filler metal, in the case of the example, does not meet the composition specified for any of the classifications in the specifica- tion) can still be classified according to the specification. The purpose is to allow a useful filler metal, one that otherwise would have to await a revision of the specification, to be classified immediately under the existing specification. This means, then, that two filler metals, each bearing the same “G” classification, may be quite different in some particular respect (chemical composition, again, for example).
A2.3.2 The point of difference (although not neces- sarily the amount of the difference) referred to above will be readily apparent from the use of the words “not required” and “not specified” in the specification. The use of these words is as follows: Not Specified is used in those areas of the specification that refer to the results of some particular test. It
SFA-5.28 1998 SECTION II
(2) Confirm receipt of the request and give the identification number to the person who made the request. (3) Send a copy of the request to the Chairman of the Filler Metal Committee and to the Chairman of the particular Subcommittee involved. (4) File the original request. (5) Add the request to the log of outstanding requests.
A2.3.3.4 All necessary action on each request will be completed as soon as possible. If more than 12 months lapse, the Secretary shall inform the requestor of the status of the request, with copies to the Chairman of the Committee and the Subcommittee. Requests still outstanding after 18 months shall be considered not to have been answered in a “timely manner” and the Secretary shall report these to the Chairman of the Filler Metal Committee, for action.
A2.3.3.5 The Secretary shall include a copy of the log of all requests pending and those completed during the preceding year with the agenda for each Filler Metal Committee meeting. Any other publication of requests that have been completed will be at the option of the American Welding Society, as deemed appropriate.
A3. Acceptance
Acceptance of all welding materials classified under this specification is in accordance with ANSI ⁄AWS A5.01 Filler Metal Procurement Guidelines, as the specification states. Any testing a purchaser requires of the supplier, for material shipped in accordance with this specification, shall be clearly stated in the purchase order, according to the provisions of ANSI ⁄AWS A5. Filler Metal Procurement Guidelines. In the absence of any such statement in the purchase order, the supplier may ship the material with whatever testing the supplier normally conducts on material of that classification, as specified in Schedule F, Table 1, of ANSI ⁄AWS A5. Filler Metal Procurement Guidelines. Testing in accord- ance with any other Schedule in that Table must be specifically required by the purchase order. In such cases, acceptance of the material shipped will be in accordance with those requirements.
A4. Certification
A4.1 The act of placing the AWS specification and classification designations on the packaging enclosing the product, or the classification on the product itself, constitutes the supplier’s (manufacturer’s) certification
588
that the product meets all of the requirements of the specification. The only testing requirement implicit in the certifica- tion is that the manufacturer has actually conducted the tests required by the specification on material that is representative of that being shipped, and that the material met the requirements of the specification. Representative material, in this case, is any production run of that classification using the same formulation. “Certification” is not to be construed to mean that tests of any kind were necessarily conducted on samples of the specific material shipped. Tests on such material may or may not have been made. The basis for the certification required by the specification is the classifi- cation test of “representative material” cited above, and the “Manufacturer’s Quality Assurance System” in ANSI /AWS A5.01 Filler Metal Procurement Guide- lines.
A4.2 (Optional) At the option and expense of the purchaser, acceptance may be based on the results of any or all of the tests required by this specification made on the gas tungsten arc welding (GTAW) test assembly described in Fig. A2, with tension specimen as described in Fig. A3 (and the impact specimen described in Fig. 5). Solid electrodes are generally recommended for GTAW and PAW.
A5. Ventilation During Welding A5.1 Five major factors govern the quantity of fumes in the atmosphere to which welders and welding operators are exposed during welding: (1) Dimensions of the space in which welding is done (with special regard to the height of the ceiling) (2) Number of welders and welding operators work- ing in that space (3) Rate of evolution of fumes, gases, or dust, ac- cording to the materials and processes used (4) The proximity of the welders or welding operators to the fumes as the fumes issue from the welding zone, and to the gases and dusts in the space in which they are working (5) The ventilation provided to the space in which the welding is done
A5.2 American National Standard Z49.1, Safety in Welding, Cutting, and Allied Processes (published by the American Welding Society), discusses the ventilation that is required during welding and should be referred to for details. Attention is particularly drawn to the section entitled “Health Protection and Ventilation.”
PART C — SPECIFICATIONS FOR WELDING RODS, ELECTRODES, AND FILLER METALS SFA-5.
FIG. A2 OPTIONAL GTAW GROOVE WELD TEST ASSEMBLY FOR MECHANICAL PROPERTIES AND SOUNDNESS
589
PART C — SPECIFICATIONS FOR WELDING RODS, ELECTRODES, AND FILLER METALS SFA-5.
spray mode, and a low level, where no transfer will take place. At a typical rate of 60 to 120 pulses per second, a melted drop is formed by the low-current arc, which is then “squeezed off” by the high-current pulse. This permits all-position welding.
A6.3 Globular Transfer. The mode of transfer that characterizes 100 percent CO 2 as a shielding gas is globular. Common practice with globular transfer is to use low arc voltage to minimize spatter. This buries the arc and produces deep penetration. Electrodes of 0.045 and 1 ⁄ 16 in. (1.1 and 1.6 mm) diameter normally are used at welding currents in the range of 275– amperes (DCEP), for this type of transfer. The rate at which droplets (globules) are transferred ranges from 20 to 70 per second, depending on the size of the electrode, the amperage, polarity, and arc voltage.
A6.4 Short Circuiting Transfer. This mode of transfer is obtained with small diameter electrodes (0.030 to 0.045 in. [0.8 to 1.1 mm]) using low arc voltages and amperages, and a power source designed for short circuiting transfer. The electrode short-circuits to the weld metal, usually at a rate of from 50 to 200 times per second. Metal is transferred with each short circuit, but not across the arc. Short circuiting gas metal arc welding of low-alloy steel is done most commonly with mixtures of argon and CO 2 as the shielding gas, with CO 2 alone, and occasionally with mixtures of helium-argon-CO 2. Penetration of welds made with CO 2 shielding gas is greater than with argon-CO 2 mixtures, but mixtures containing substantial amounts of argon or helium generally result in superior weld metal impact properties. Shielding gas mixtures of 50 to 90 percent argon-remainder CO 2 or 50 to 90 percent helium-remainder CO 2 result in higher short circuiting rates and lower minimum currents and volt- ages than does CO 2 shielding alone. This can be an advantage when welding thin plate or in the achievement of superior impact properties.
A7. Description and Intended Use of Electrodes and Rods A7.1 The following is a description of the characteris- tics and intended use of the filler metals classified by this specification. The designations and the chemical composition requirements for all classifications are given in Tables 1 and 2 of this specification. The mechanical properties of weld metals from filler metals of the various classifications will conform to the minimum requirements stated in Tables 3 and 4 of the specifi- cation.
591
A7.2 It should be noted that weld properties may vary appreciably depending on filler metal size and current used, plate thickness, joint geometry, preheat and interpass temperatures, surface conditions, base- metal composition and extent of alloying with the filler metal, and shielding gas. For example, when filler metals having an analysis within the range of Table 1 are deposited, the weld metal chemical composition will not vary greatly from the as-manufactured composi- tion of the filler metal when used with argon-oxygen shielding gas. However, they will show a considerable reduction in the content of manganese, silicon, and other deoxidizers when used with CO 2 as the shielding gas. A7.3 ER70S-A1 Classification (^1 ⁄ 2 Mo). Filler metal of this classification is similar to many of the carbon steel filler metals classified in ANSI /AWS A5.18, except that 1 ⁄ 2 percent molybdenum has been added. This addition increases the strength of the weld metal, espe- cially at elevated temperatures, and provides some increase in corrosion resistance; however, it will likely reduce the notch toughness of the weld metal. Typical applications include the welding of C-Mo base metals such as ASTM 204 plate and A335-P1 pipe. A7.4 ER80S-B2 and E80C-B2 Classifications (1- (^1) ⁄ 4 Cr-
2 Mo).^ Filler metals of these classifications are used to weld 1 ⁄ 2 Cr-^1 ⁄ 2 Mo, 1Cr-^1 ⁄ 2 Mo, and 1-^1 ⁄ 4 Cr-^1 ⁄ 2 Mo steels for elevated temperatures and corrosive service. They are also used for joining dissimilar combinations of Cr-Mo and carbon steels. All transfer modes of the GMAW process may be used. Careful control of preheat, interpass temperatures, and postheat is essential to avoid cracking. These electrodes are classified after postweld heat treatment. Special care must be used when using them in the as-welded condition due to higher strength levels. A7.5 ER70S-B2L and E70C-B2L Classifications (1-^1 ⁄ 4 Cr-^1 ⁄ 2 Mo). These filler metals are identical to the types ER80S-B2 and E80C-B2 except for the low- carbon content (0.05 percent maximum) and thus the lower strength levels. This alloy exhibits greater resist- ance to cracking and is more suitable for welds to be left in the as-welded condition or when the accuracy of the postweld heat treatment operation is questionable. These classifications were previously ER80S-B2L and E80C-B2L in the previous edition of this specification. The strength requirements and classification designator have been changed to reflect the true strength capabilities of the chemical composition. A7.6 ER90S-B3 and E90C-B3 Classifications (2-^1 ⁄ 4 Cr-1 Mo). Filler metals of these classifications are used to weld the 2-^1 ⁄ 4 Cr-1Mo steels used for high-
SFA-5.28 1998 SECTION II
temperature/high-pressure piping and pressure vessels. These may also be used for joining combinations of Cr-Mo and carbon steel. All GMAW modes may be used. Careful control of preheat, interpass temperatures, and postweld heat treatment is essential to avoid crack- ing. These electrodes are classified after postweld heat treatment. Special care must be used when using them in the as-welded condition due to higher strength levels.
A7.7 ER80S-B3L and E80C-B3L Classifications (2-^1 ⁄ 4 Cr-1 Mo). These filler metals are identical to the types ER90S-B3 and E90C-B3 except for the low- carbon content (0.05 percent maximum) and, therefore, the lower strength levels. These alloys exhibit greater resistance to cracking and are more suitable for welds to be left in the as-welded condition. These classifica- tions were previously ER90S-B3L and E90C-B3L in the previous edition of this specification. The strength requirements and classification designator have been changed to reflect the true strength capabilities of the chemical composition.
A7.8 ER80S-Ni1 and E80C-Ni1 Classifications (1. Ni). These filler metals deposit weld metal similar to E8018-C3 covered electrodes, and are used for welding low-alloy high-strength steels requiring good toughness at temperatures as low as −50°F (−46°C).
A7.9 ER80S-Ni2, E70C-Ni2, and E80C-Ni2 Classi- fications (2-^1 ⁄ 4 Ni). These filler metals deposit weld metal similar to E8018-C1 electrodes. Typically, they are used for welding 2-^1 ⁄ 2 percent nickel steels and other materials requiring good toughness at temperatures as low as −80°F (−62°C).
A7.10 ER80S-Ni3 and E80C-Ni3 Classifications (3-^1 ⁄ 4 Ni). These filler metals deposit weld metal similar to E8018-C2 electrodes. Typically they are used for welding 3-^1 ⁄ 2 percent nickel steels for low-temperature service.
A7.11 ER80S-D2, ER90S-D2, and E90C-D2 Classi- fications (^1 ⁄ 2 Mo). The ER80S-D2 and ER90S-D2 classi- fications have the same chemical requirements as the E70S-1B classification of AWS A5.18-69. The differ- ences between the ER80S-D2 and the ER90S-D2 classi- fications are the change in shielding gas and the mechan- ical property requirements specified in Table 3. Filler metals of these classifications contain molybdenum for increased strength and a high level of deoxidizers (Mn and Si) to control porosity when welding with CO 2 as the shielding gas. They will give radiographic quality welds with excellent bead appearance in both ordinary and difficult-to-weld carbon and low-alloy steels. They exhibit excellent out-of-position welding characteristics
592
with the short circuiting and pulsed arc processes. The combination of weld soundness and strength makes filler metals of these classifications suitable for single and multiple-pass welding of a variety of carbon and low-alloy, higher strength steels in both the as-welded and postweld heat-treated conditions. The chemical composition of these classifications differs from those of the “-D2” type electrodes in AWS A5.5. A7.12 ER100S-1, ER110S-1, and ER120S-1 Classi- fications. These filler metals deposit high-strength, very tough weld metal for critical applications. Originally developed for welding HY80 and HY100 steels for military applications, they are also used for a variety of structural applications where tensile strength require- ments exceed 100 ksi (690 MPa), and excellent tough- ness is required to temperatures as low as −60°F (−51°C). Mechanical properties obtained from weld deposits made with electrodes of these classifications will vary depending on the heat input used. A7.13 ER80S-B6 Classification (5 Cr-^1 ⁄ 2 Mo). This classification contains 4.0 to 6.0 percent chromium and about 0.50 percent molybdenum. It is used for welding material of similar composition, usually in the form of pipe or tubing. The alloy is an air-hardening material and, therefore, when welding with this filler metal, preheat and postweld heat treatment are required. This electrode is similar to that previously classified as ER502 in A5.9-81. A7.14 ER80S-B8 Classification (9 Cr-1 Mo). This classification contains 8.0 to 10.5 percent chromium and about 1.0 percent molybdenum. Filler metal of this classification is used for welding base metal of similar compositions, usually in the form of pipe or tubing. The alloy is an air-hardening material and, therefore, when welding with this filler metal, preheating and postweld heat treatment are required. This electrode is similar to that previously classified as ER505 in A5.9-81. A7.15 ER90S-B9 Classification [9 Cr-1 Mo-0.2V- 0.07Nb(Cb)]. ER90S-B9 is a 9Cr-1Mo solid wire modi- fied with niobium (columbium) and vanadium designed to provide strength, toughness, fatigue life, oxidation resistance and corrosion resistance at elevated tempera- tures. Due to the higher elevated temperature properties of this alloy, components that are now fabricated from stainless and ferritic steels may be fabricated from a single alloy, eliminating problems associated with dissimilar welds. In addition to the classification requirements in this specification, either impact toughness or high-tempera- ture creep strength properties should be determined. Due to the influence of various levels of carbon and
SFA-5.28 1998 SECTION II
strength deposits. Note that aging may involve holding test specimens at room temperature for several days or holding at a higher temperature for a shorter period of time. Consequently, users are cautioned to employ adequate preheat and interpass temperatures to avoid the deleterious effects of hydrogen in production welds.
A9. Discontinued Classifications
The following classifications have been discontinued over the life of this specification:
Discontinues Classification Published Replaced With
ER100S-2 1979 — ER80S-B2L 1979 ER70S-B2L E80C-BL2 1979 E70C-B2L ER90S-B3L 1979 ER80S-B3L E90C-B3L 1979 E80C-B3L
A10. General Safety Considerations
A10.1 Burn Protection. Molten metal, sparks, slag, and hot-work surfaces are produced by welding, cutting, and allied processes. These can cause burns if precau- tionary measures are not used. Workers should wear protective clothing made of fire-resistant material. Pant cuffs, open pockets, or other places on clothing that can catch and retain molten metal or sparks should not be worn. High-top shoes or leather leggings and fire-resistant gloves should be worn. Pant legs should be worn over the outside of high-top shoes. Helmets or hand shields that provide protection for the face, neck, and ears, and a head covering to protect the head should be used. In addition, appropriate eye protec- tion should be used. When welding overhead or in confined spaces, ear plugs to prevent weld spatter from entering the ear canal should be worn in combination with goggles or equivalent to give added eye protection. Clothing should be kept free of grease and oil. Combustible materials should not be carried in pockets. If any combustible substance has been spilled on clothing, a change to clean, fire resistant clothing should be made before working with open arcs or flame. Aprons, cape-sleeves, leggings, and shoulder covers with bibs designed for welding service should be used. Where welding or cutting of unusually thick base metal is involved, sheet metal shields should be used for extra protection. Mechanization of highly hazardous processes or jobs should be considered. Other personnel in the work area should be protected by the use of noncombustible screens or by the use of appropriate protection as described in the previous paragraph.
594
Before leaving a work area, hot workpieces should be marked to alert other persons of this hazard. No attempt should be made to repair or disconnect electrical equipment when it is under load. Disconnection under load produces arcing of the contacts and may cause burns or shock, or both.
Note: Burns can be caused by touching hot equipment such as electrode holders, tips, and nozzles. Therefore, insulated gloves should be worn when these items are handled, unless an adequate cooling period has been allowed before touching.
The following sources are for more detailed informa- tion on personal protection: (1) American National Standards Institute. ANSI Z41.1, Safety-Toe Footwear. New York: American Na- tional Standards Institute.^6 (2) —. ANSI Z49.1, Safety in Welding, Cutting, and Allied Processes. Miami, FL: American Welding Society. (3) —. ANSI Z87.1, Practice for Occupational and Educational Eye and Face Protection. New York: Amer- ican National Standards Institute. (4) Occupational Safety and Health Administration. Code of Federal Regulations, Title 29 Labor, Chapter XVII, Part 1910. Washington, D.C.: U.S. Government Printing Office.^7
A10.2 Electrical Hazards. Electric shock can kill; however, it can be avoided. Live electrical parts should not be touched. The manufacturer’s instructions and recommended safe practices should be read and under- stood. Faulty installation, improper grounding, and in- correct operation and maintenance of electrical equip- ment are all sources of danger. All electrical equipment and the workpieces should be grounded. The workpiece lead is not a ground lead. It is used only to complete the welding circuit. A separate connection is required to ground the workpiece. The workpiece should not be mistaken for a ground connection. The correct cable size should be used, since sustained overloading will cause cable failure and result in possi- ble electrical shock or fire hazard. All electrical connec- tions should be tight, clean, and dry. Poor connections can overheat and even melt. Further, they can produce dangerous arcs and sparks. Water, grease, or dirt should not be allowed to accumulate on plugs, sockets, or electrical units. Moisture can conduct electricity.
(^6) ANSI documents are available from the American National Standards Institute, 11 West 42 Street, New York, NY 10036 (^7) OSHA documents are available from U.S. Government Printing Office, Washington, D.C. 20402
PART C — SPECIFICATIONS FOR WELDING RODS, ELECTRODES, AND FILLER METALS SFA-5.
To prevent shock, the work area, equipment, and clothing should be kept dry at all times. Welders should wear dry gloves and rubber-soled shoes, or stand on a dry board or insulated platform. Cables and connections should be kept in good condition. Improper or worn electrical connections may create conditions that could cause electrical shock or short circuits. Worn, damaged, or bare cables should not be used. Open-circuit voltage should be avoided. When several welders are working with arcs of different polarities, or when a number of alternating current machines are being used, the open- circuit voltages can be additive. The added voltages increase the severity of the shock hazard. In case of electric shock, the power should be turned off. If the rescuer must resort to pulling the victim from the live contact, nonconducting materials should be used. If the victim is not breathing, cardiopulmonary resuscitation (CPR) should be administered as soon as contact with the electrical source is broken. A physician should be called and CPR continued until breathing has been restored, or until a physician has arrived. Electrical burns are treated as thermal burns; that is, clean, cold (iced) compresses should be applied. Con- tamination should be avoided; the area should be cov- ered with a clean, dry dressing; and the patient should be transported to medical assistance. Recognized safety standards such as ANSI ⁄ASC Z49.1, Safety in Welding, Cutting, and Allied Processes, and NFPA No. 70, National Electrical Code, should be followed.^8
A10.3 Fumes and Gases. Many welding, cutting, and allied processes produce fumes and gases which may be harmful to health. Fumes are solid particles which originate from welding filler metals and fluxes, the base metal, and any coatings present on the base metal. Gases are produced during the welding process or may be produced by the effects of process radiation on the surrounding environment. Management personnel and welders alike should be aware of the effects of these fumes and gases. The amount and composition of these fumes and gases depend upon the composition of the filler metal and base metal, welding process, current level, arc length, and other factors. The possible effects of over-exposure range from irritation of eyes, skin, and respiratory system to more severe complications. Effects may occur immediately or at some later time. Fumes can cause symptoms such as nausea, headaches, dizziness, and metal fume fever. The possibility of more serious health effects exists
(^8) NFPA documents are available form the National Fire Protection Association, 1 Batterymarch Park, Quincy, MA 02269.
595
when especially toxic materials are involved. In confined spaces, the shielding gases and fumes might displace breathing air and cause asphyxiation. One’s head should always be kept out of the fumes. Sufficient ventilation, exhaust at the arc, or both, should be used to keep fumes and gases from your breathing zone and the general area. In some cases, natural air movement will provide enough ventilation. Where ventilation may be question- able, air sampling should be used to determine if corrective measures should be applied. More detailed information on fumes and gases pro- duced by the various welding processes may be found in the following: (1) The permissible exposure limits required by OSHA can be found in Code of Federal Regulations, Title 29, Chapter XVII, Part 1910. (2) The recommended threshold limit values for fumes and gases may be found in Threshold Limit Values for Chemical Substances and Physical Agents in the Workroom Environment, published by the American Conference of Governmental Industrial Hygienists (ACGIH).^9 (3) The results of an AWS-funded study are available in a report entitled, Fumes and Gases in the Welding Environment, available from the American Welding Society. (4) Manufacturer’s Material Safety Data Sheet for the product. A10.4 Radiation. Welding, cutting, and allied opera- tions may produce radiant energy (radiation) harmful to health. One should become acquainted with the effects of this radiant energy. Radiant energy may be ionizing (such as x-rays), or nonionizing (such as ultraviolet, visible light, or infra- red). Radiation can produce a variety of effects such as skin burns and eye damage, depending on the radiant energy’s wavelength and intensity, if excessive exposure occurs. A10.4.1 Ionizing Radiation. Ionizing radiation is produced by the electron beam welding process. It is ordinarily controlled within acceptance limits by use of suitable shielding enclosing the welding area. A10.4.2 Nonionizing Radiation. The intensity and wavelengths of nonionizing radiant energy produced depend on many factors, such as the process, welding parameters, electrode and base-metal composition, fluxes, and any coating or plating on the base metal.
(^9) ACGIH documents are available form the American Conference of Governmental Industrial Hygienists, Kemper Woods Center, 1330 Kemper Meadow Drive, Cincinnati, OH 45240.