
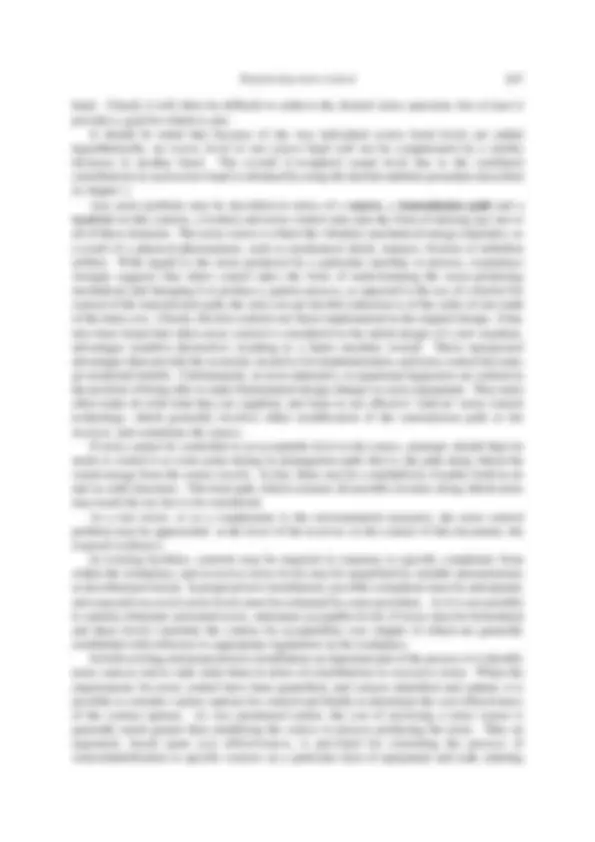
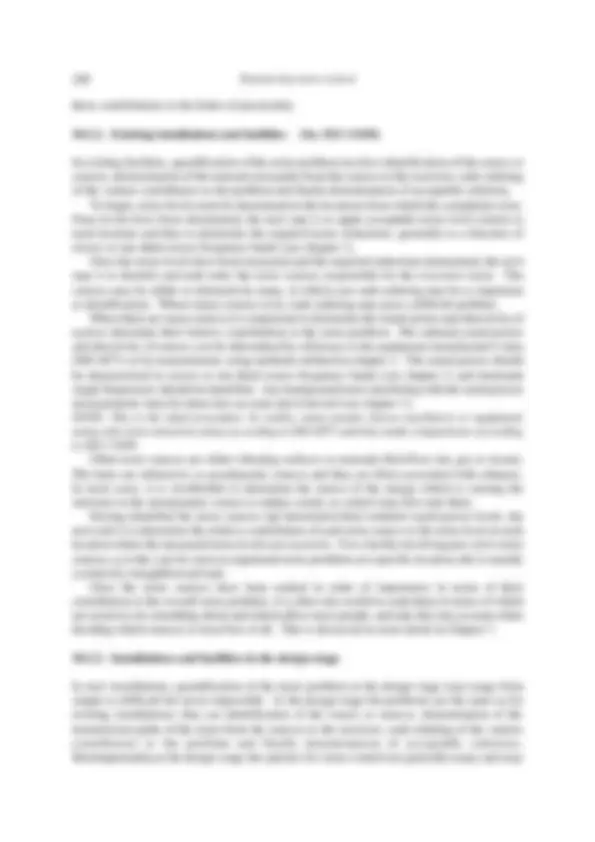
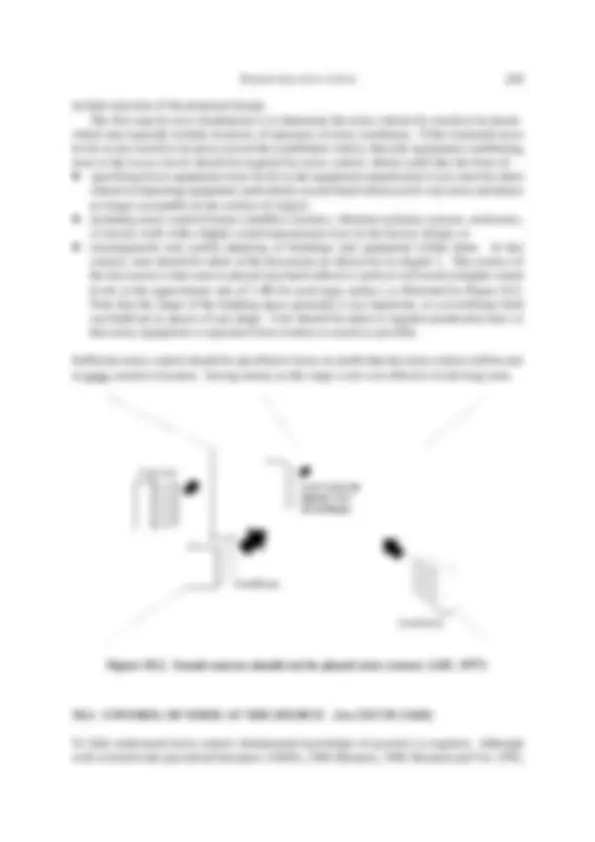
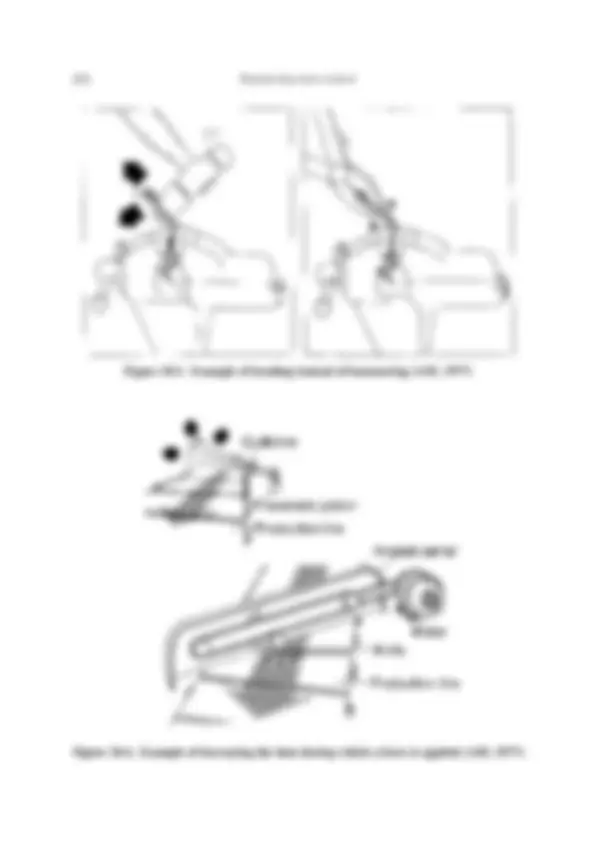
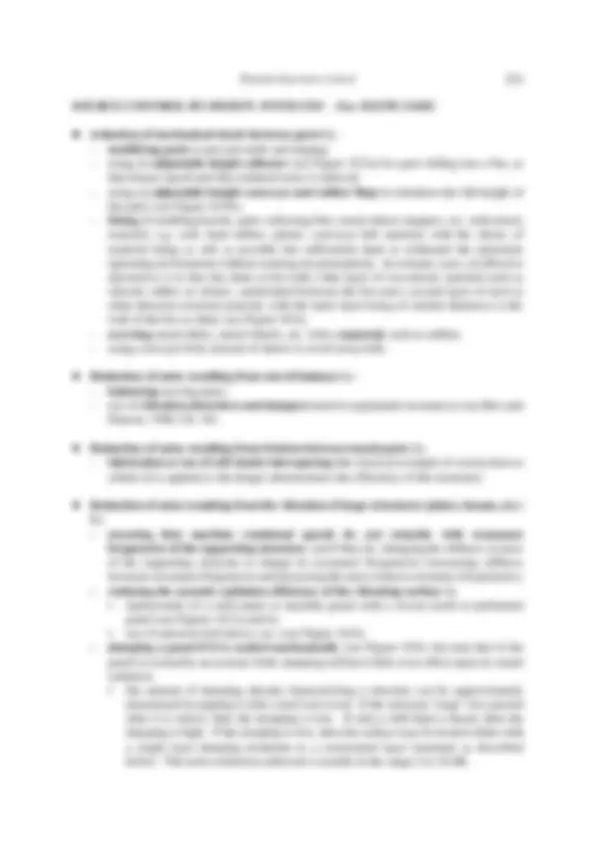
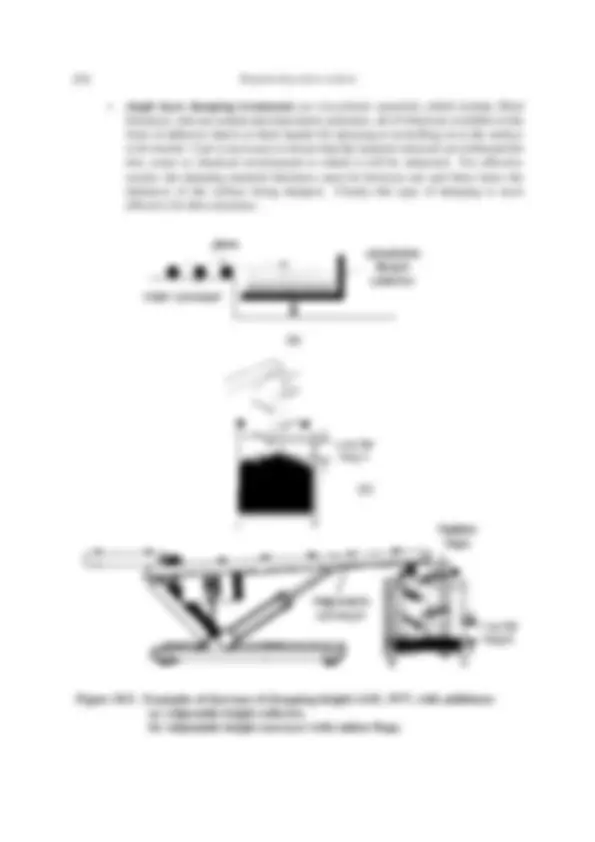
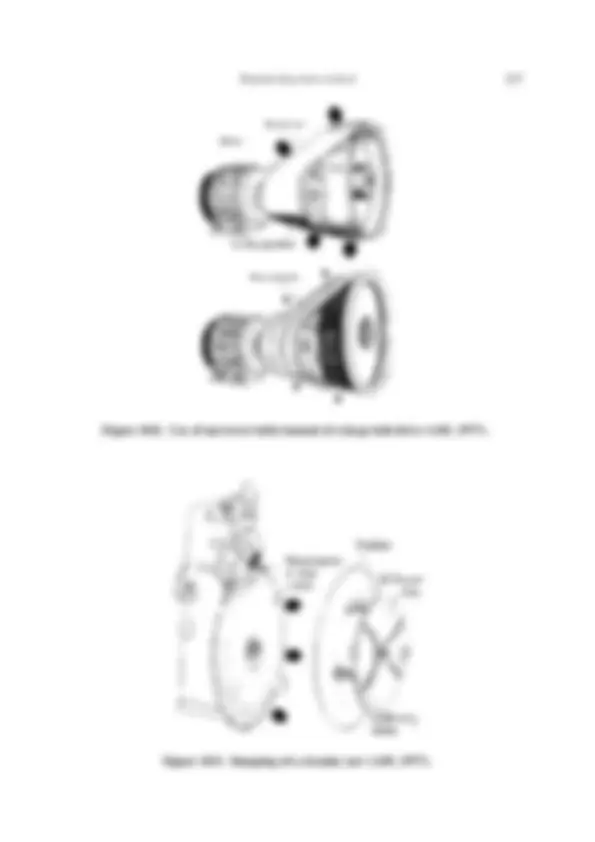
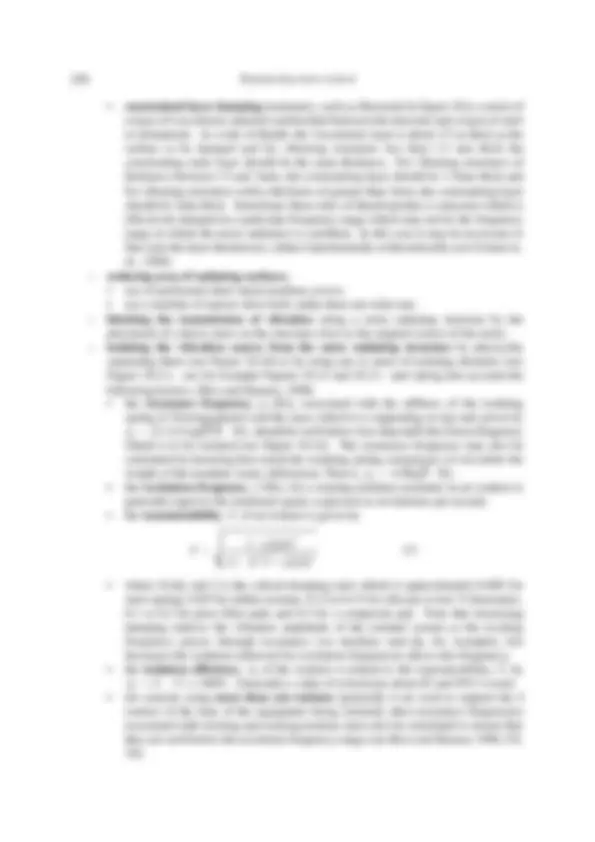
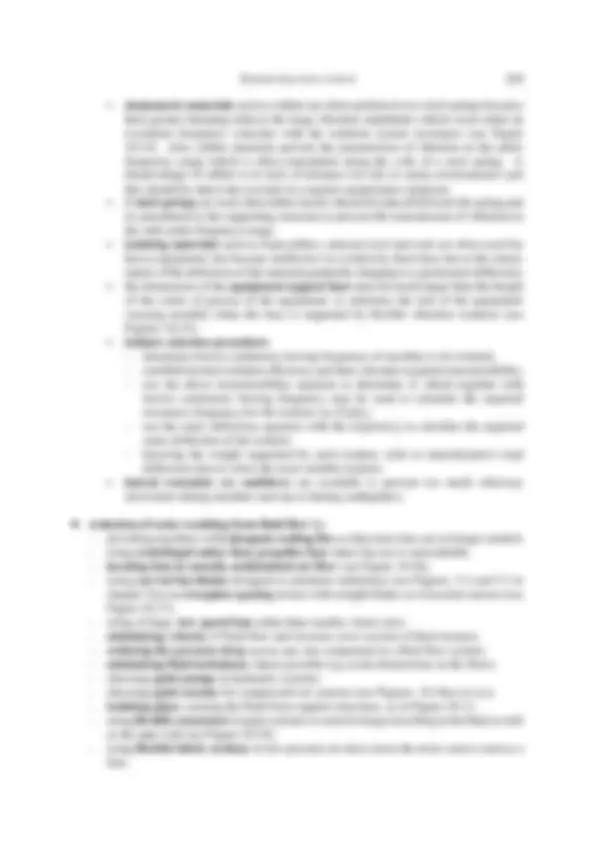
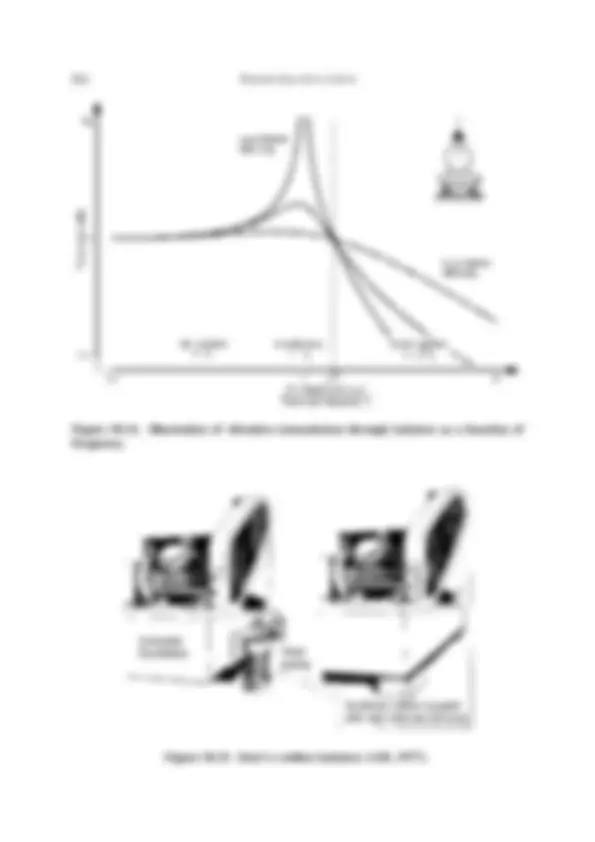
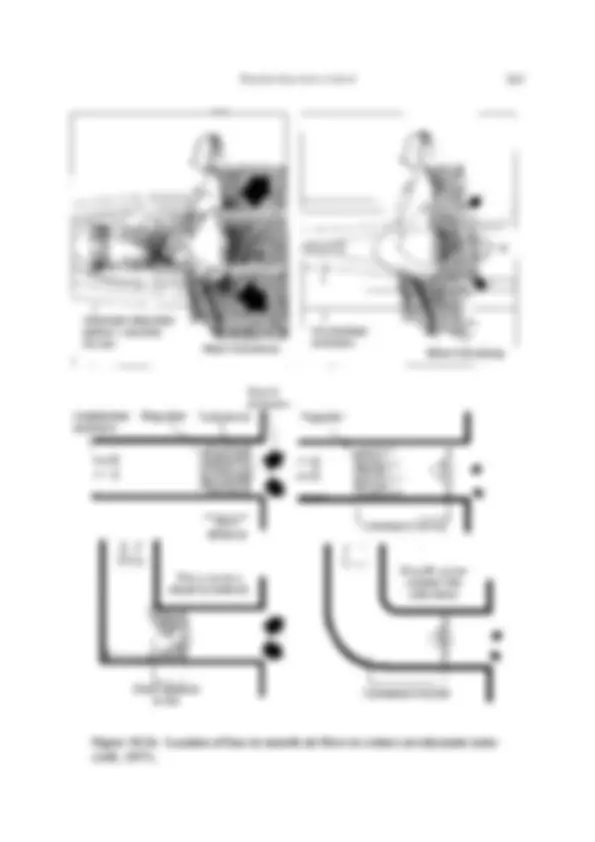
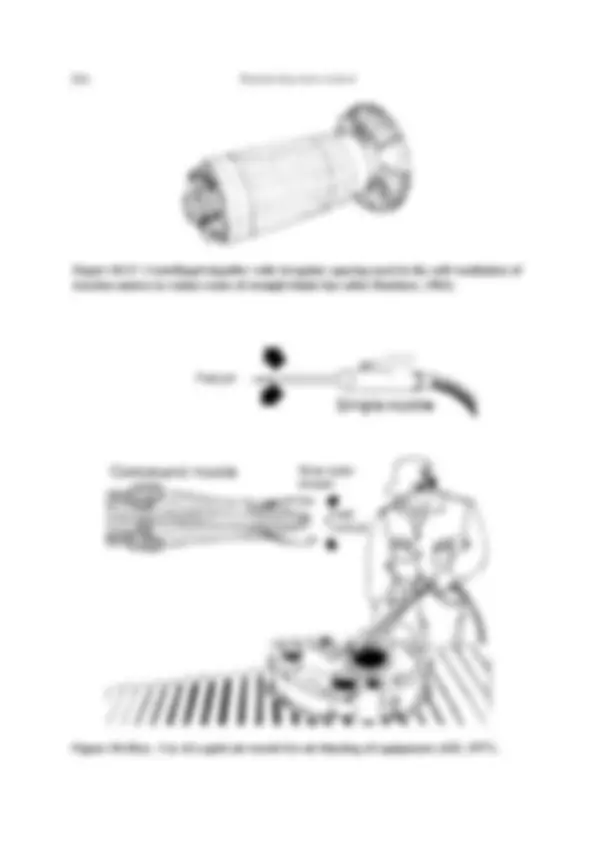
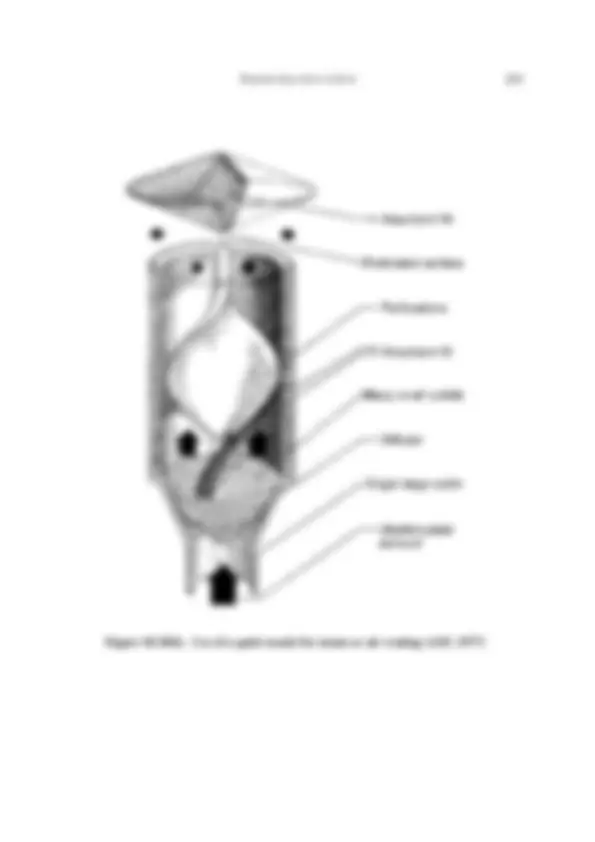
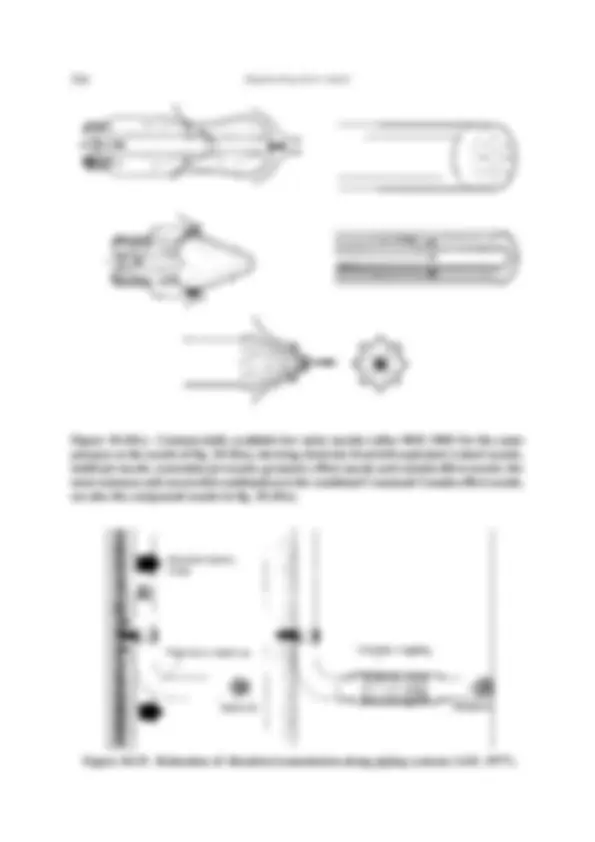
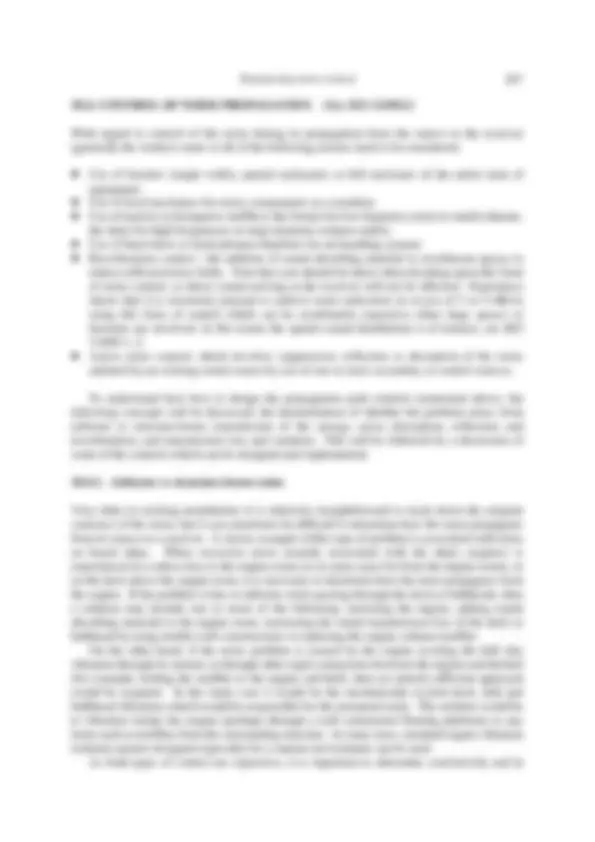
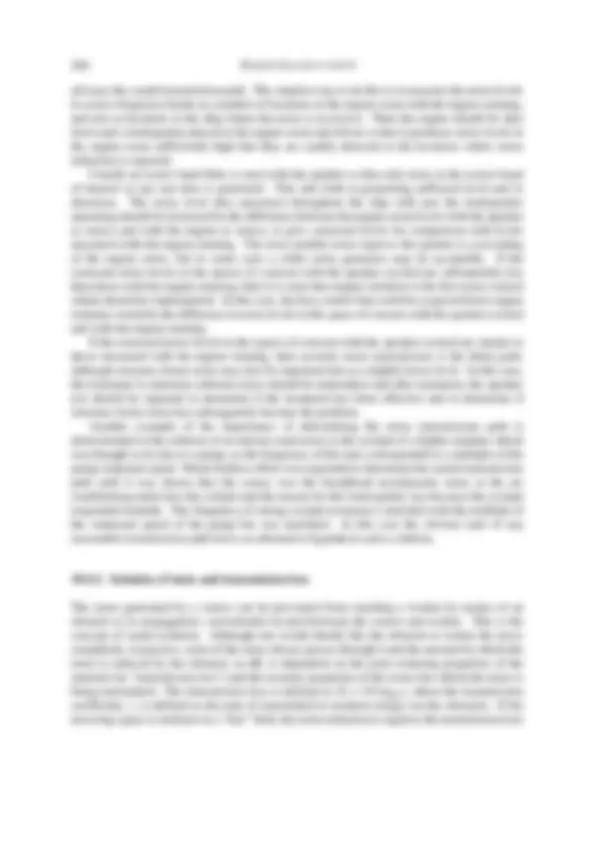
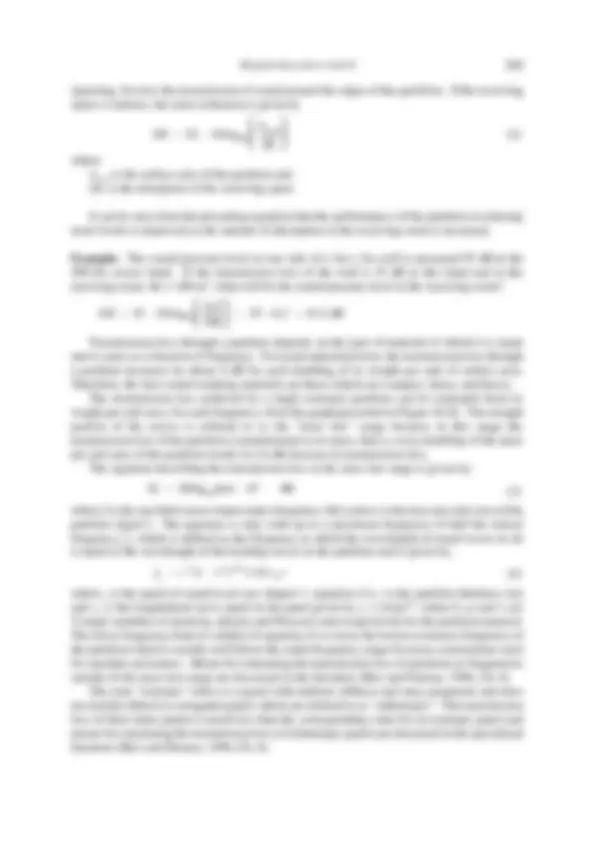
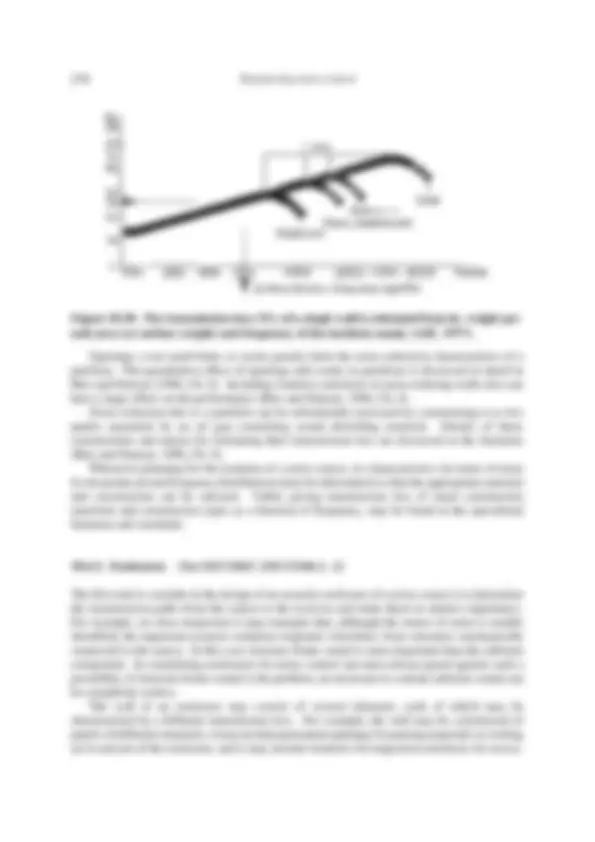
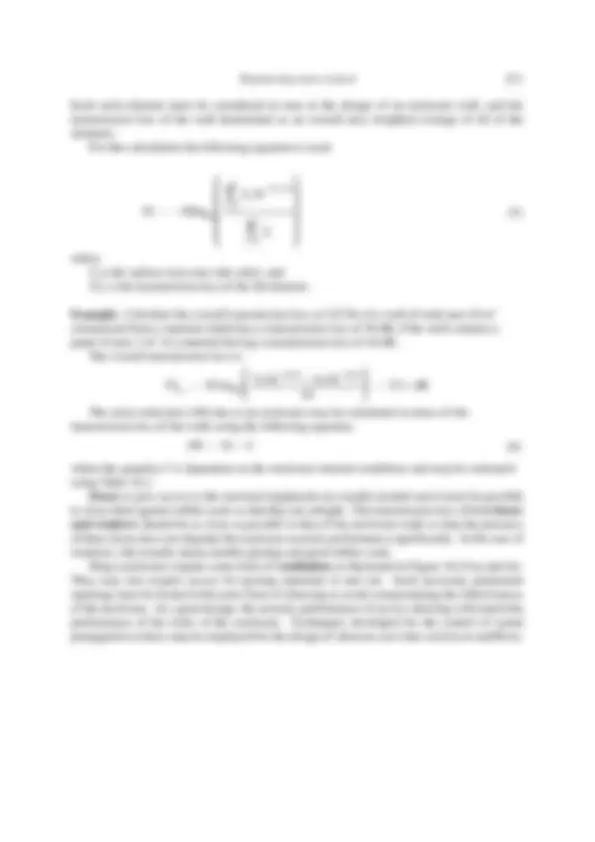
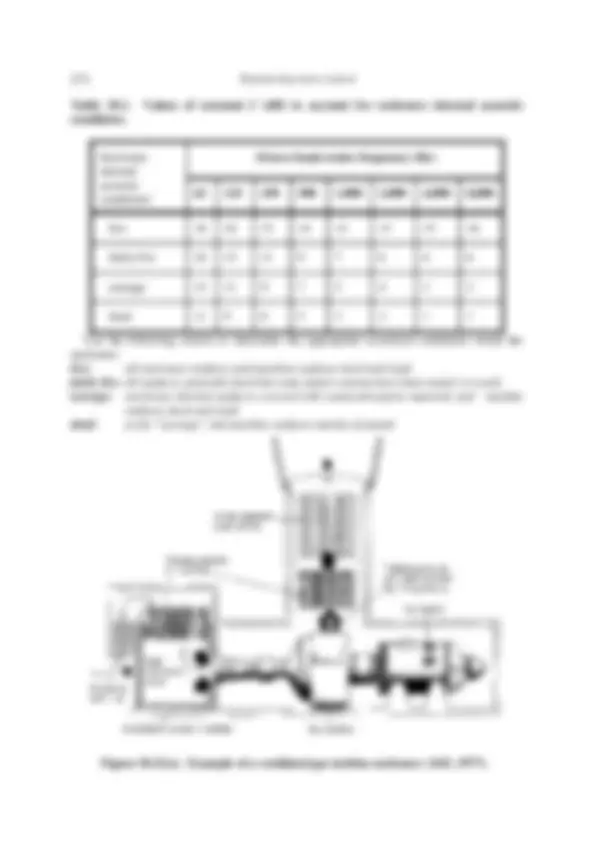

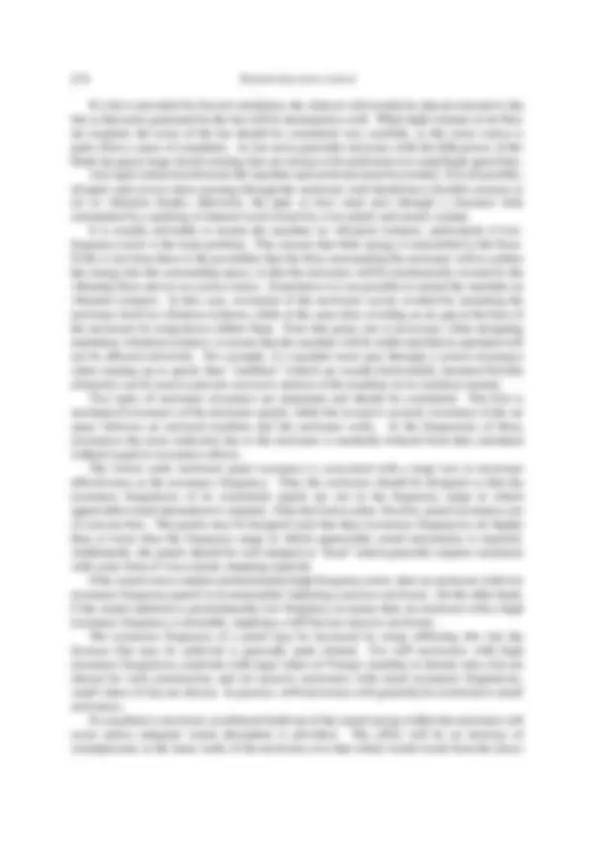
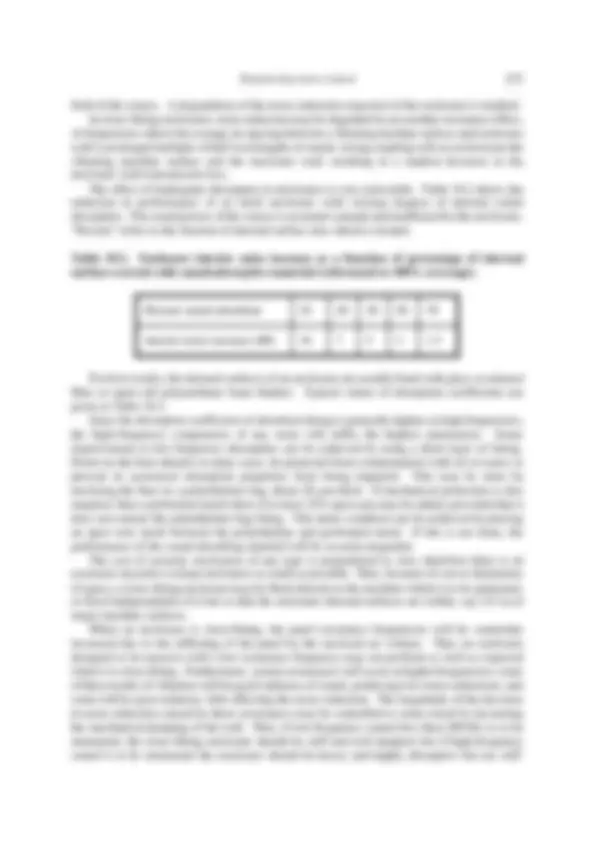
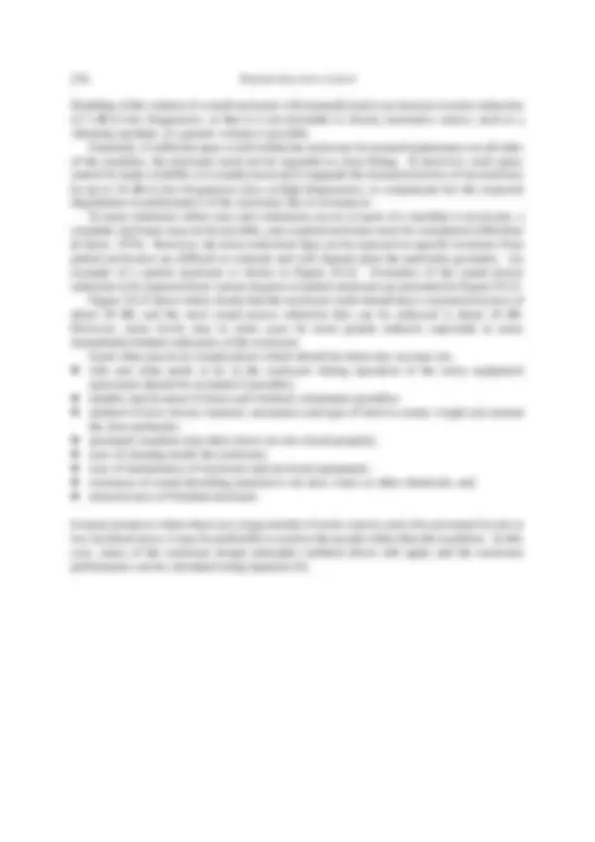
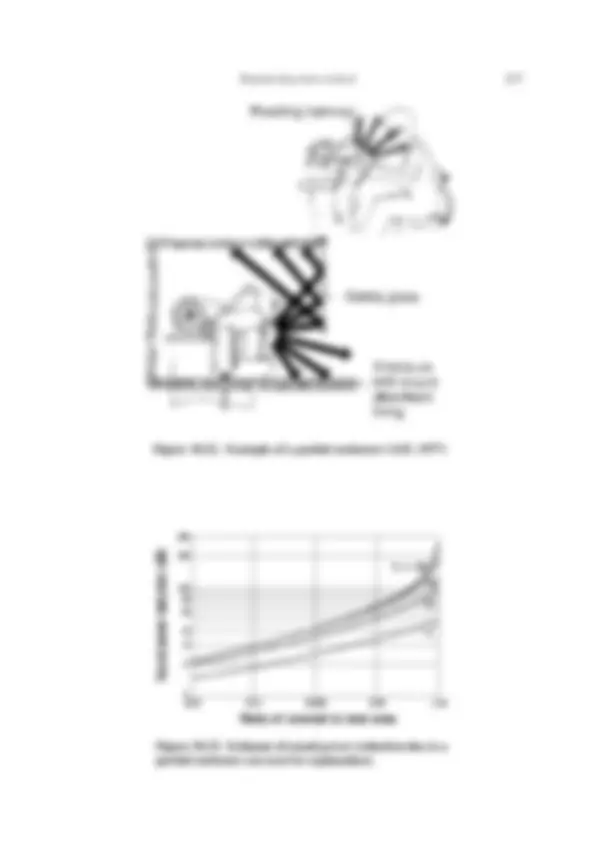
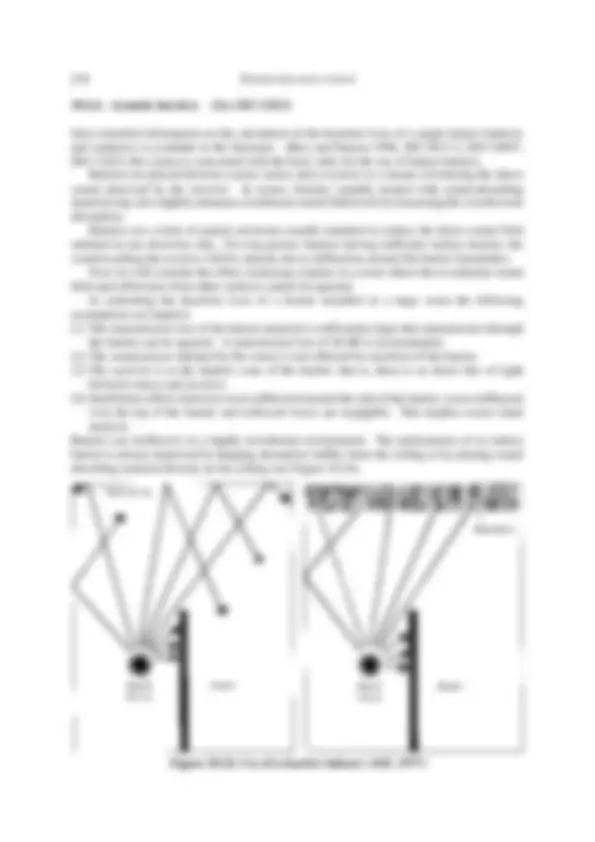
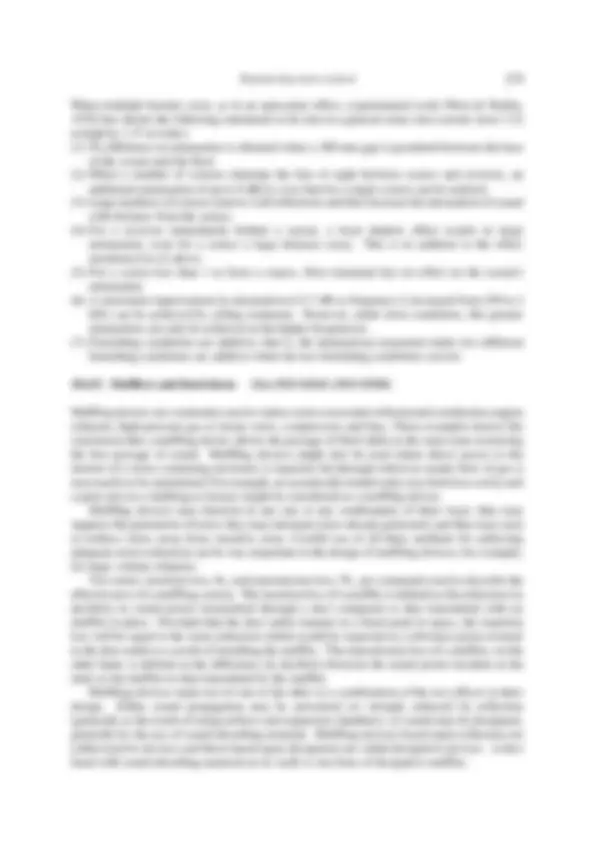
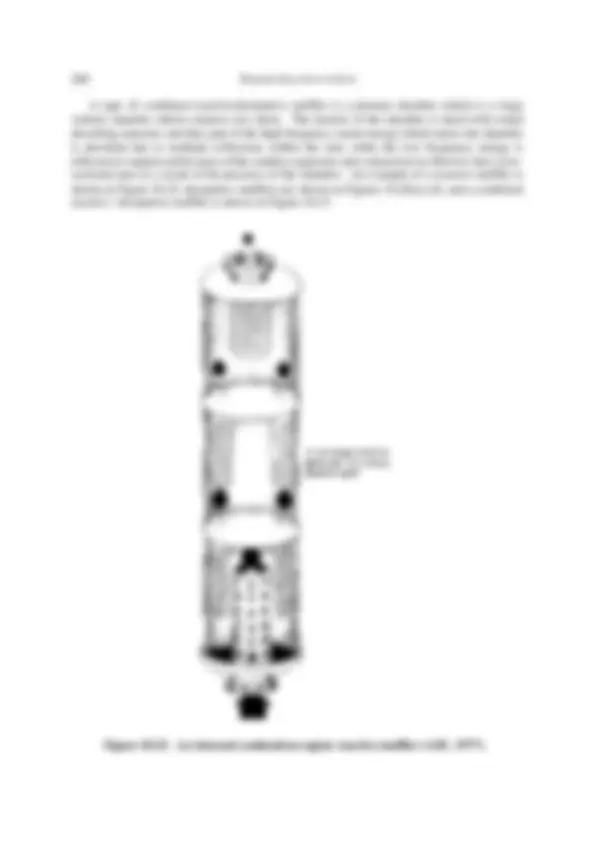
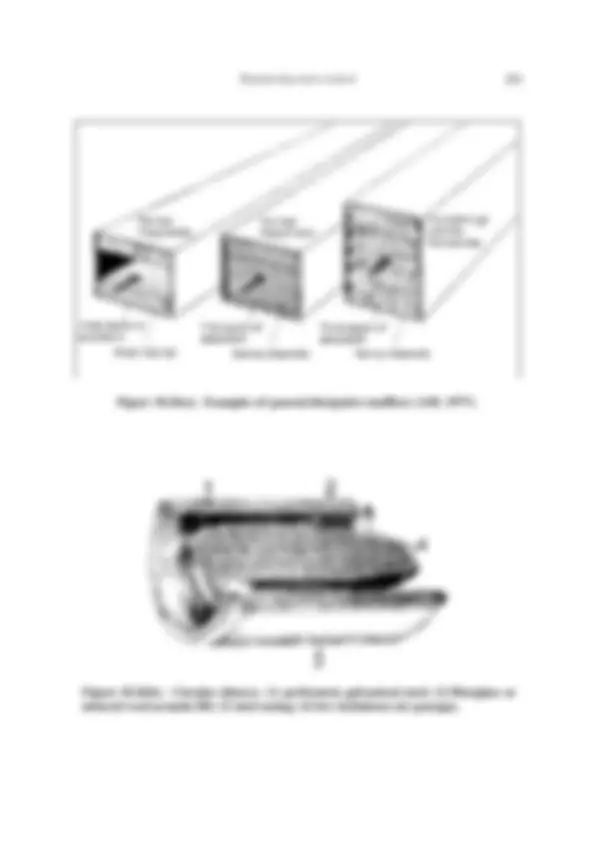
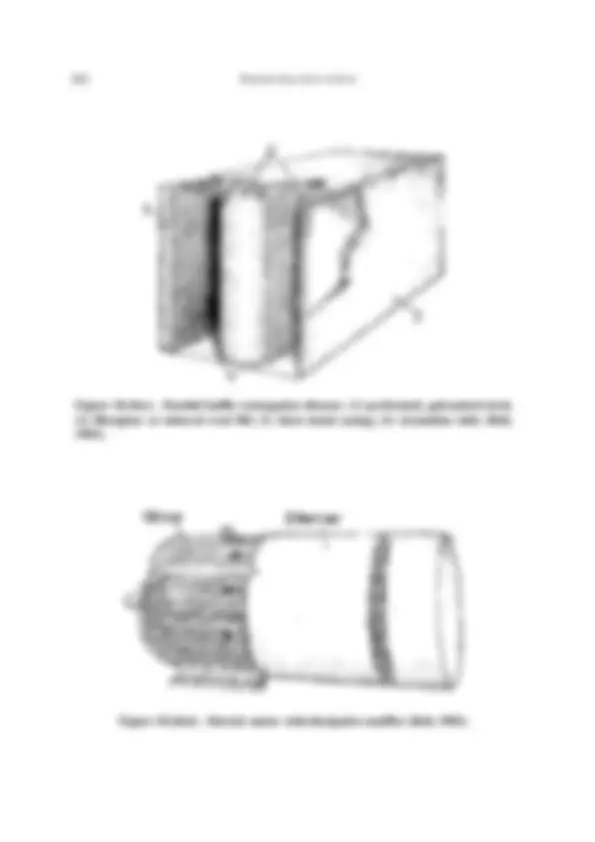
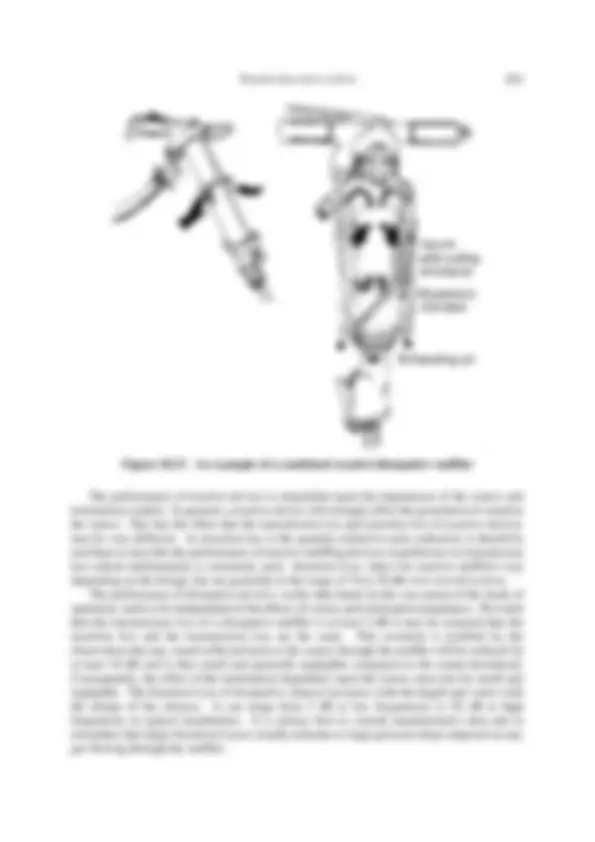
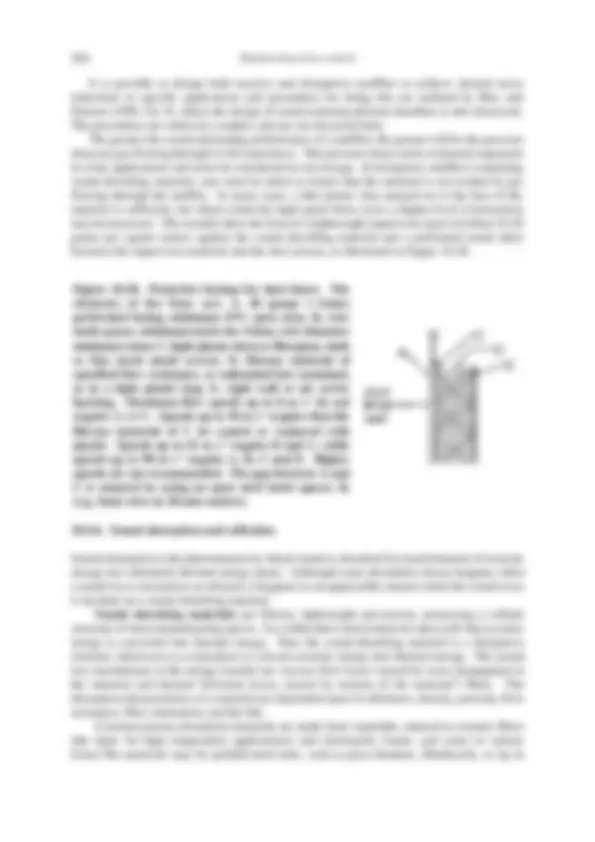

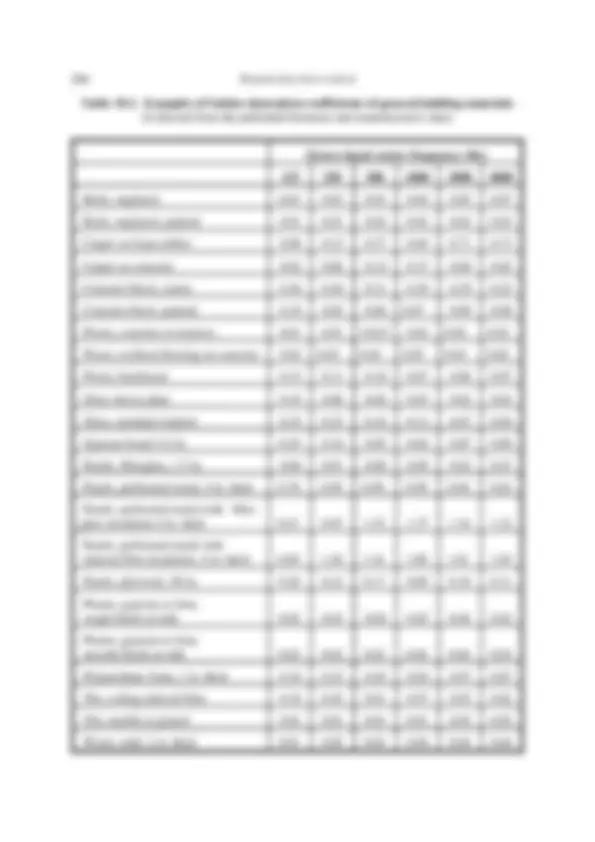
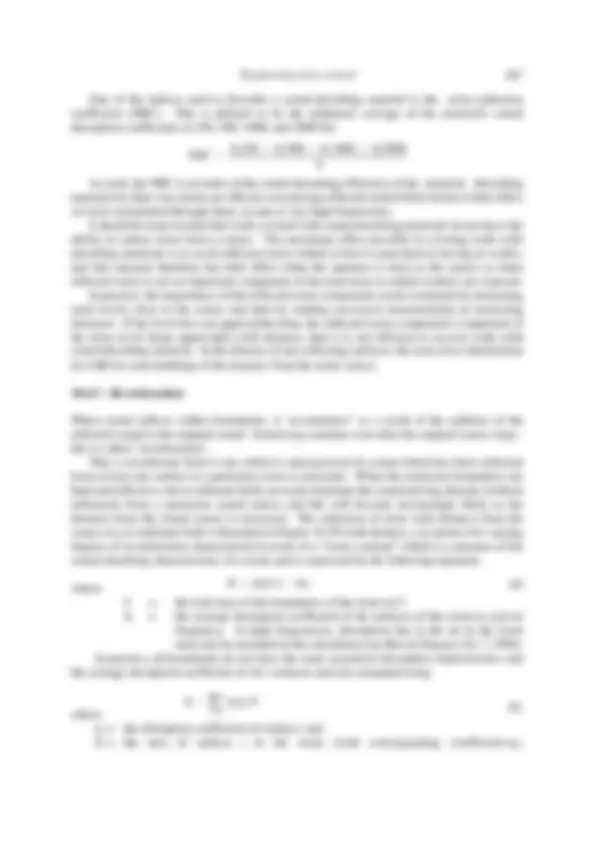
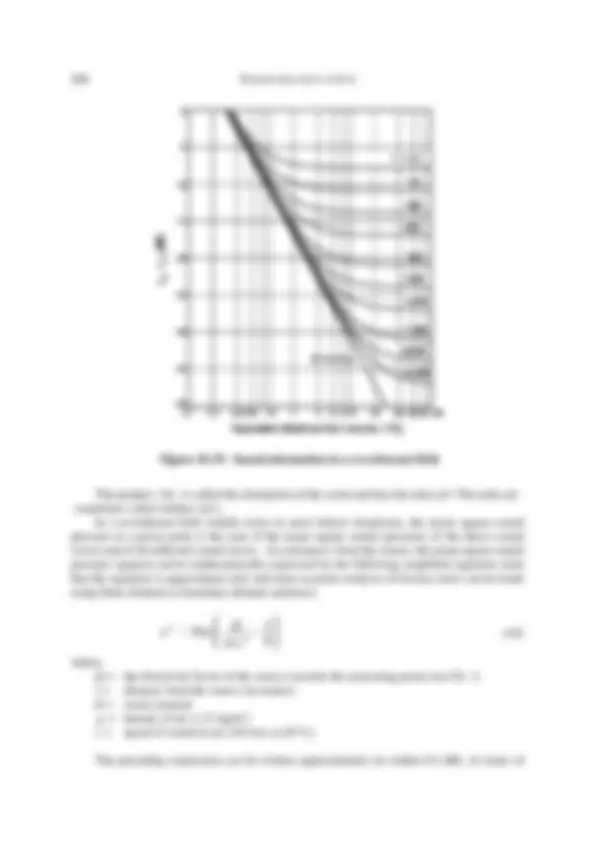
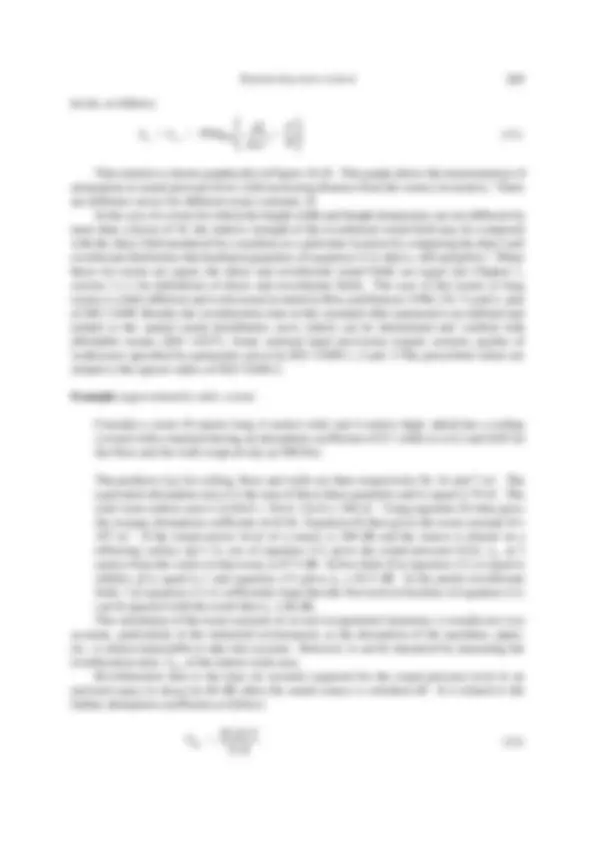
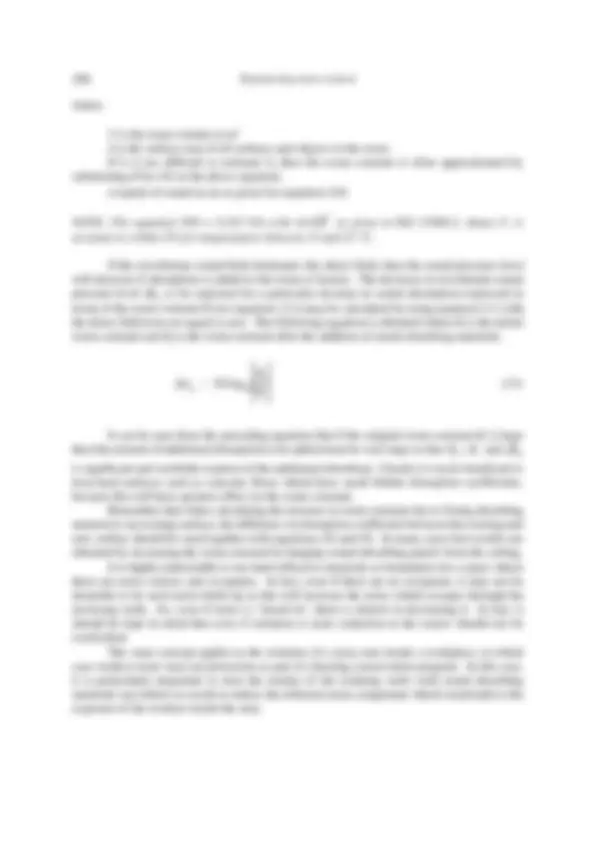
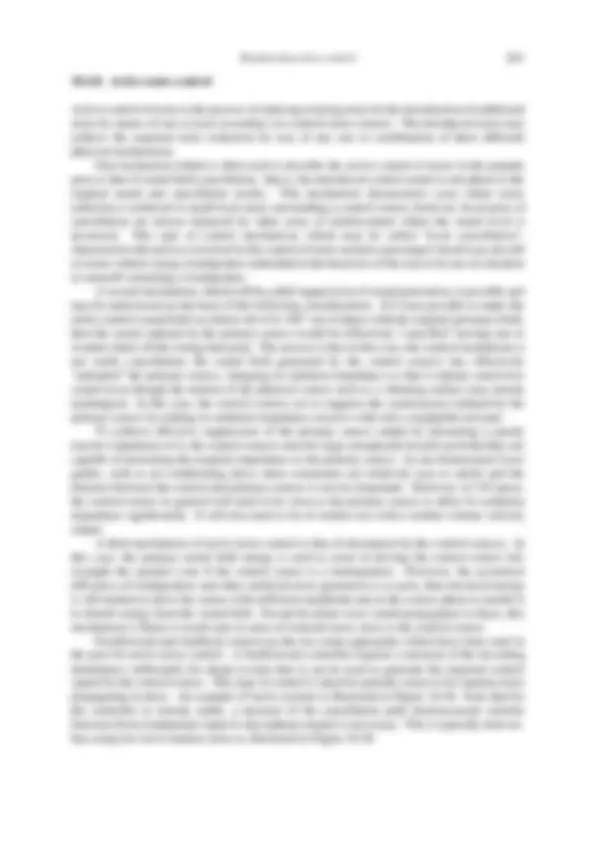
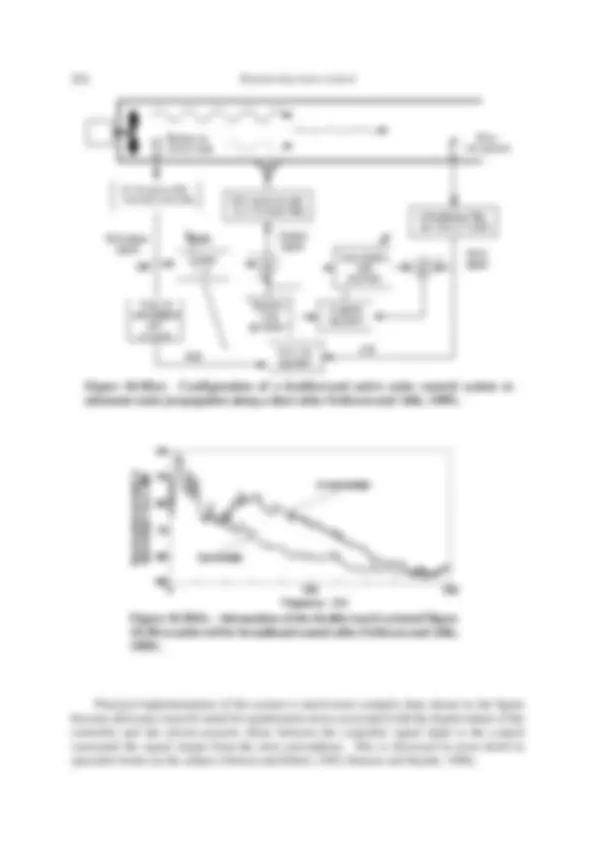
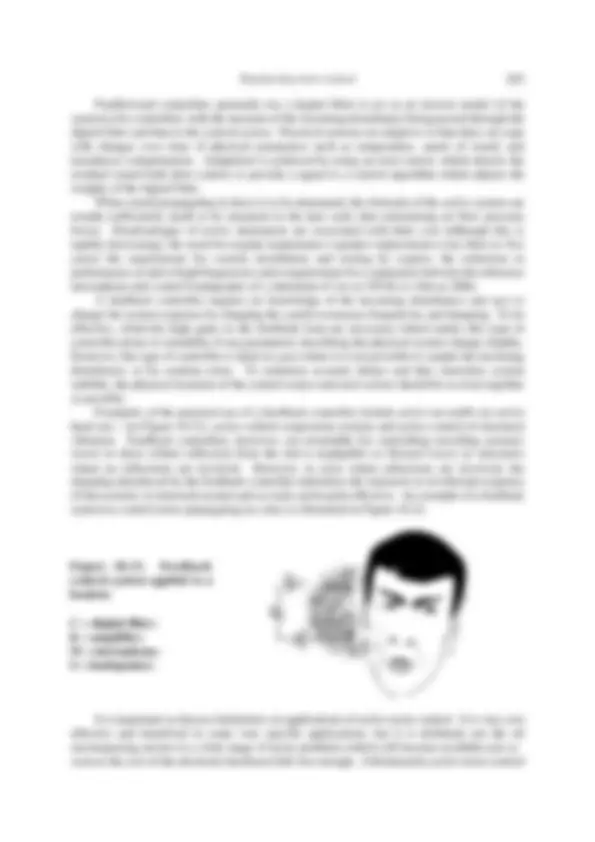
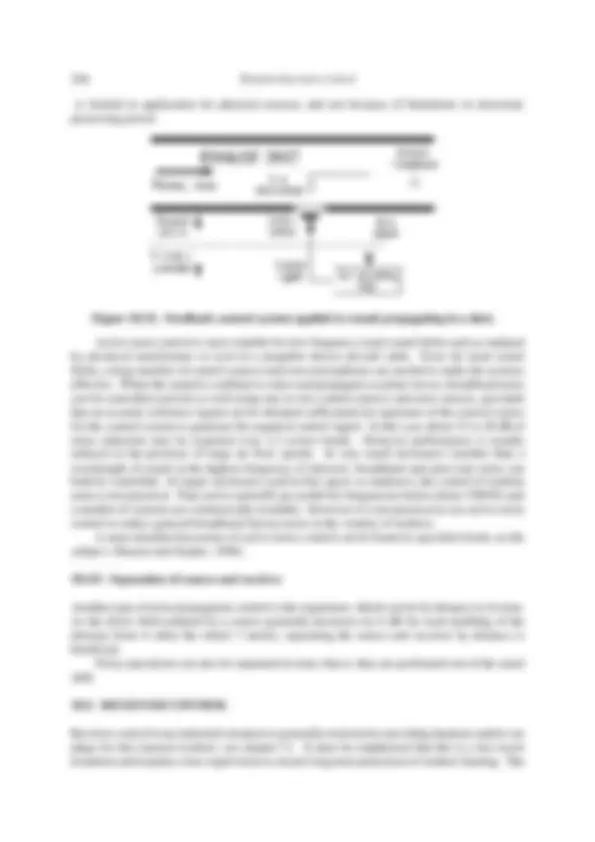
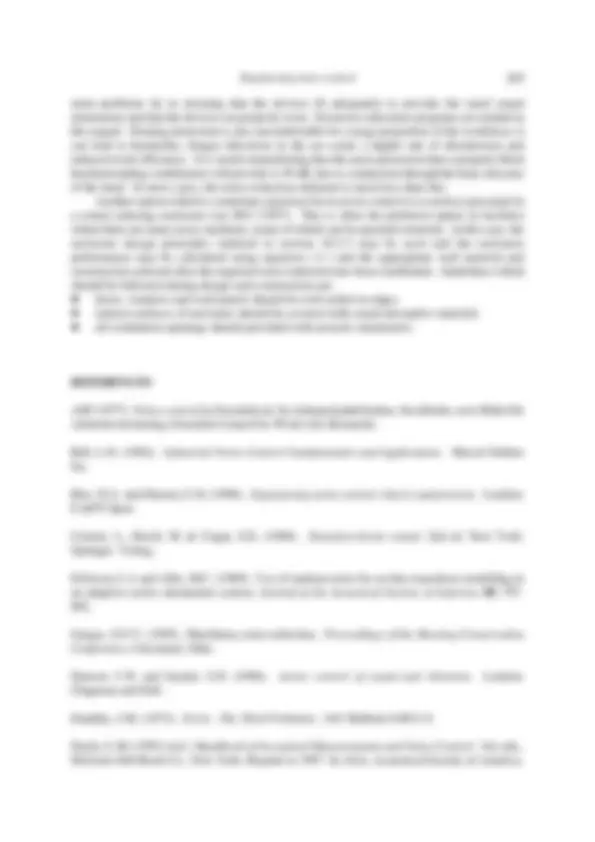
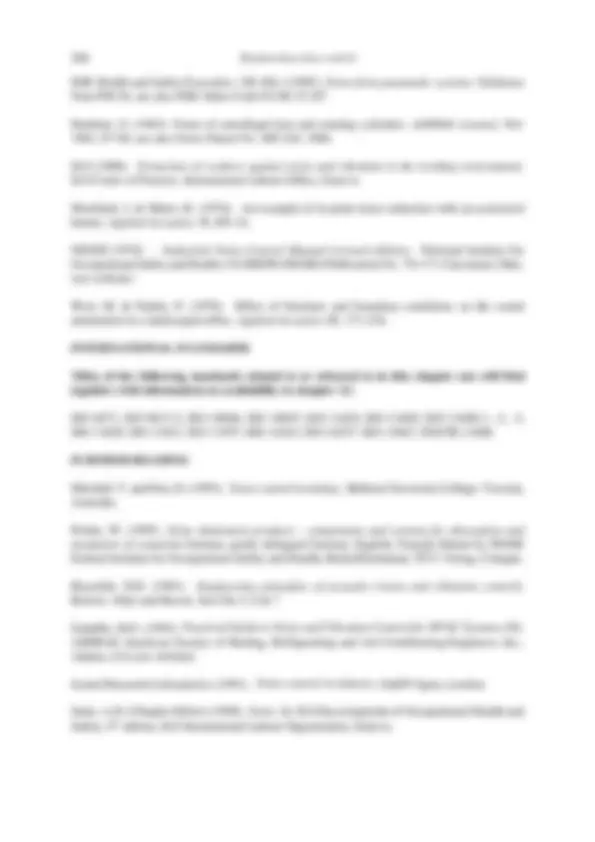
Study with the several resources on Docsity
Earn points by helping other students or get them with a premium plan
Prepare for your exams
Study with the several resources on Docsity
Earn points to download
Earn points by helping other students or get them with a premium plan
Community
Ask the community for help and clear up your study doubts
Discover the best universities in your country according to Docsity users
Free resources
Download our free guides on studying techniques, anxiety management strategies, and thesis advice from Docsity tutors
Types of sounds Way of reducing sound
Typology: Lecture notes
1 / 52
This page cannot be seen from the preview
Don't miss anything!
Professor Colin H. Hansen Dr Berenice I.F. Goelzer Department of Mechanical Engineering World Health Organization University of Adelaide South Australia 5005 AUSTRALIA chansen@mecheng.adelaide.edu.au*
As with any occupational hazard, control technology should aim at reducing noise to acceptable levels by action on the work environment. Such action involves the implementation of any measure that will reduce noise being generated, and/or will reduce the noise transmission through the air or through the structure of the workplace. Such measures include modifications of the machinery, the workplace operations, and the layout of the workroom. In fact, the best approach for noise hazard control in the work environment, is to eliminate or reduce the hazard at its source of generation, either by direct action on the source or by its confinement. Practical considerations must not be overlooked; it is often unfeasible to implement a global control program all at once. The most urgent problems have to be solved first; priorities have to be set up. In certain cases, the solution may be found in a combination of measures which by themselves would not be enough; for example, to achieve part of the required reduction through environmental measures and to complement them with personal measures (e.g. wearing hearing protection for only 2-3 hours), bearing in mind that it is extremely difficult to make sure that hearing protection is properly fitted and properly worn. This chapter presents the principles of engineering control of noise, specific control measures and some examples. Reading of chapter 1 is indispensable for the understanding of this chapter. Note that many of the specific noise control measures described are intended as a rough guide only. Further information on the subject can be found in ISO 11690 and in the specialised literature. Also suppliers of equipment and noise control hardware can often provide helpful noise control advice.
10.2. NOISE CONTROL STRATEGIES (See ISO 11690)
Prior to the selection and design of control measures, noise sources must be identified and the noise produced must be carefully evaluated. Procedures for taking noise measurements in the course of a noise survey are discussed in chapter 7.
*Present address: 26, ch. Colladon CH-1209 Geneva, Switzerland berenice@goelzer.net
Figure 10.1. Desired noise spectrum for an overall level of 90 dB(A).
To adequately define the noise problem and set a good basis for the control strategy, the following factors should be considered: type of noise noise levels and temporal pattern frequency distribution noise sources (location, power, directivity) noise propagation pathways, through air or through structure room acoustics (reverberation). In addition, other factors have to be considered; for example, number of exposed workers, type of work, etc. If one or two workers are exposed, expensive engineering measures may not be the most adequate solution and other control options should be considered; for example, a combination of personal protection and limitation of exposure. The need for control or otherwise in a particular situation is determined by evaluating noise levels at noisy locations in a facility where personnel spend time. If the amount of time spent in noisy locations by individual workers is only a fraction of their working day, then local regulations may allow slightly higher noise levels to exist. Where possible, noise levels should be evaluated at locations occupied by workers' ears. Normally the noise control program will be started using as a basis A-weighted immission or noise exposure levels for which the standard ISO 11690-1 recommends target values and the principles of noise control planning. A more precise way is to use immission and emission values in frequency bands as follows. The desired (least annoying) octave band frequency spectrum for which to aim at the location of the exposed worker is shown in Figure 10.1 for an overall level of 90 dB(A). If the desired level after control is 85 dB(A), then the entire curve should be displaced downwards by 5 dB. The curve is used by determining the spectrum levels (see chapter 1) in octave bands and plotting the results on the graph to determine the required decibel reductions for each octave
these contributions to the limits of practicality.
10.2.1. Existing installations and facilities (See ISO 11690)
In existing facilities, quantification of the noise problem involves identification of the source or sources, determination of the transmission paths from the sources to the receivers, rank ordering of the various contributors to the problem and finally determination of acceptable solutions. To begin, noise levels must be determined at the locations from which the complaints arise. Once levels have been determined, the next step is to apply acceptable noise level criteria to each location and thus to determine the required noise reductions, generally as a function of octave or one-third octave frequency bands (see chapter 1). Once the noise levels have been measured and the required reductions determined, the next step is to identify and rank order the noise sources responsible for the excessive noise. The sources may be subtle or alternatively many, in which case rank ordering may be as important as identification. Where many sources exist, rank ordering may pose a difficult problem. When there are many sources it is important to determine the sound power and directivity of each to determine their relative contributions to the noise problem. The radiated sound power and directivity of sources can be determined by reference to the equipment manufacturer's data (ISO 4871) or by measurement, using methods outlined in chapter 1. The sound power should be characterised in octave or one third octave frequency bands (see chapter 1) and dominant single frequencies should be identified. Any background noise interfering with the sound power measurements must be taken into account and removed (see chapter 1). NOTE: This is the ideal procedure. In reality, many people choose machinery or equipment using only noise emission values according to ISO 4871 and they make comparisons according to ISO 11689. Often noise sources are either vibrating surfaces or unsteady fluid flow (air, gas or steam). The latter are referred to as aerodynamic sources and they are often associated with exhausts. In most cases, it is worthwhile to determine the source of the energy which is causing the structure or the aerodynamic source to radiate sound, as control may best start there. Having identified the noise sources and determined their radiated sound power levels, the next task is to determine the relative contribution of each noise source to the noise level at each location where the measured noise levels are excessive. For a facility involving just a few noise sources, as is the case for most occupational noise problems at a specific location, this is usually a relatively straightforward task. Once the noise sources have been ranked in order of importance in terms of their contribution to the overall noise problem, it is often also useful to rank them in terms of which are easiest to do something about and which affect most people, and take this into account when deciding which sources to treat first of all. This is discussed in more detail in Chapter 7.
10.2.2. Installations and facilities in the design stage
In new installations, quantification of the noise problem at the design stage may range from simple to difficult but never impossible. At the design stage the problems are the same as for existing installations; they are identification of the source or sources, determination of the transmission paths of the noise from the sources to the receivers, rank ordering of the various contributors to the problem and finally determination of acceptable solutions. Mostimportantly,at the design stage the options for noise control are generally many and may
Figure 10.2. Sound sources should not be placed near corners (ASF, 1977)
include rejection of the proposed design. The first step for new installations is to determine the noise criteria for sensitive locations which may typically include locations of operators of noisy machinery. If the estimated noise levels at any sensitive location exceed the established criteria, then the equipment contributing most to the excess levels should be targeted for noise control, which could take the form of: specifying lower equipment noise levels to the equipment manufacturer (care must be taken whenever importing equipment, particularly second hand which can be very noisy and hence no longer acceptable in the country of origin); including noise control fixtures (mufflers, barriers, vibration isolation systems, enclosures, or factory walls with a higher sound transmission loss) in the factory design; or rearrangement and careful planning of buildings and equipment within them. In this context, note should be taken of the discussion on directivity in chapter 1. The essence of the discussion is that sources placed near hard reflective surfaces will result in higher sound levels at the approximate rate of 3 dB for each large surface, as illustrated in Figure 10.2. Note that the shape of the building space generally is not important, as a reverberant field can build-up in spaces of any shape. Care should be taken to organise production lines so that noisy equipment is separated from workers as much as possible.
Sufficient noise control should be specified to leave no doubt that the noise criteria will be met at every sensitive location. Saving money at this stage is not cost effective in the long term.
10.3. CONTROL OF NOISE AT THE SOURCE (See ISO TR 11688)
To fully understand noise control, fundamental knowledge of acoustics is required. Although well covered in the specialised literature ( OSHA, 1980; Beranek, 1988; Beranek and Ver, 1992;
Specification of quiet equipment.
Substitution of parts of equipment:
Change of work methods
Substitution of processes.
substitution of mechanical power generation and transmission equipment
replacement of worn moving parts (e.g., replace new rolling element bearings for worn ones);
minimising the number of noisy machines running at any one time.
Figure 10.3. Example of bending instead of hammering (ASF, 1977)
Figure 10.4. Example of increasing the time during which a force is applied (ASF, 1977).
Figure 10.5. Examples of decrease of dropping height (ASF, 1977, with additions) (a) Adjustable height collector. (b) Adjustable height conveyor with rubber flaps.
& single layer damping treatments are viscoelastic materials which include filled bitumens, silicone sealant and elastomeric polymers, all of which are available in the form of adhesive sheets or thick liquids for spraying or trowelling on to the surface to be treated. Care is necessary to ensure that the material selected can withstand the dirt, water or chemical environment to which it will be subjected. For effective results, the damping material thickness must be between one and three times the thickness of the surface being damped. Clearly this type of damping is most effective for thin structures.
Figure 10.6. Lining a hopper with an impact absorbing and damping construction. Note that to achieve a constraint layer treatment, the “heavy duty abrasion resistant inner skin“ in the lower figure could be replaced with a steel plate.
Figure 10.8. Use of narrower belts instead of a large belt drive (ASF, 1977).
Figure 10.9. Damping of a circular saw (ASF, 1977).
2
(1 X^2 )^2 (2 X )^2
& constrained layer damping treatments, such as illustrated in figure 10.6, consist of a layer of viscoelastic material sandwiched between the structure and a layer of steel or aluminium. As a rule of thumb, the viscoelastic layer is about 1/3 as thick as the surface to be damped and for vibrating structures less than 1.5 mm thick the constraining outer layer should be the same thickness. For vibrating structures of thickness between 1.5 and 3mm, the constraining layer should be 1.5mm thick and for vibrating structures with a thickness of greater than 3mm, the constraining layer should be 3mm thick. Sometimes these rules of thumb produce a structure which is effectively damped in a particular frequency range which may not be the frequency range in which the noise radiation is a problem. In this case it may be necessary to fine tune the layer thicknesses, either experimentally or theoretically (see Cremer et. al., 1988).
- reducing area of radiating surfaces ; & use of perforated sheet metal machine covers; & use a number of narrow drive belts rather than one wide one; - blocking the transmission of vibration along a noise radiating structure by the placement of a heavy mass on the structure close to the original source of the noise; - isolating the vibration source from the noise radiating structure by physically separating them (see Figure 10.10) or by using one or more of isolating elements (see Figure 10.11) - see for example Figures 10.12 and 10.13 - and taking into account the following factors ( Bies and Hansen, 1996 ) & the resonance frequency , f 0 (Hz), associated with the stiffness of the isolating spring ( k Newtons/metre) and the mass which it is supporting ( m kg) and given by f 0 [1 / (2 %)] k / m Hz, should be well below (less than half) the lowest frequency which is to be isolated (see Figure 10.14). The resonance frequency may also be calculated by knowing how much the isolating spring compresses ( d cm) under the weight of the machine (static deflection); That is, f 0 4.98/ d Hz. & the excitation frequency , f (Hz), for a rotating machine mounted on an isolator is generally equal to the rotational speed, expressed as revolutions per second. & the transmissibility , T , of an isolator is given by
& where X=f/f 0 and is the critical damping ratio which is approximately 0.005 for steel springs, 0.05 for rubber mounts, 0.12 to 0.15 for silicone or low-T elastomers, 0.1 to 0.2 for glass fibre pads and 0.3 for a composite pad. Note that increasing damping reduces the vibration amplitude of the isolated system as the exciting frequency passes through resonance (on machine start-up, for example), but decreases the isolation achieved for excitation frequencies above this frequency; & the isolation efficiency , , of the isolator is related to the transmissibility, T , by (1 T ) × 100%. Generally a value of between about 85 and 95% is used. & for systems using more than one isolator (generally 4 are used to support the 4 corners of the base of the equipment being isolated), then resonance frequencies associated with twisting and rocking motions must also be calculated to ensure that they are well below the excitation frequency range (see Bies and Hansen, 1996, Ch. 10);
Figure 10.10. Vibration isolation by separation (ASF, 1977).
Figure 10.11. Reduction of vibration transmission from piping systems (ASF, 1977).
Figure 10.12. Vibration isolation of a lift to minimise lift noise transmitted throughout a building structure and then into occupied spaces (ASF, 1977).
Figure 10.13. Vibration isolation to prevent noise transmitted through the machine supports to occupied spaces (ASF, 1977).
Figure 10.16. Location of fans in smooth air flows to reduce aerodynamic noise (ASF, 1977).
Figure 10.17. Centrifugal impeller with irregular spacing used in the self-ventilation of traction motors to reduce noise of straight blade fan (after Huebner, 1963 ).
Figure 10.18(a). Use of a quiet air nozzle for air blasting of equipment (ASF, 1977).