
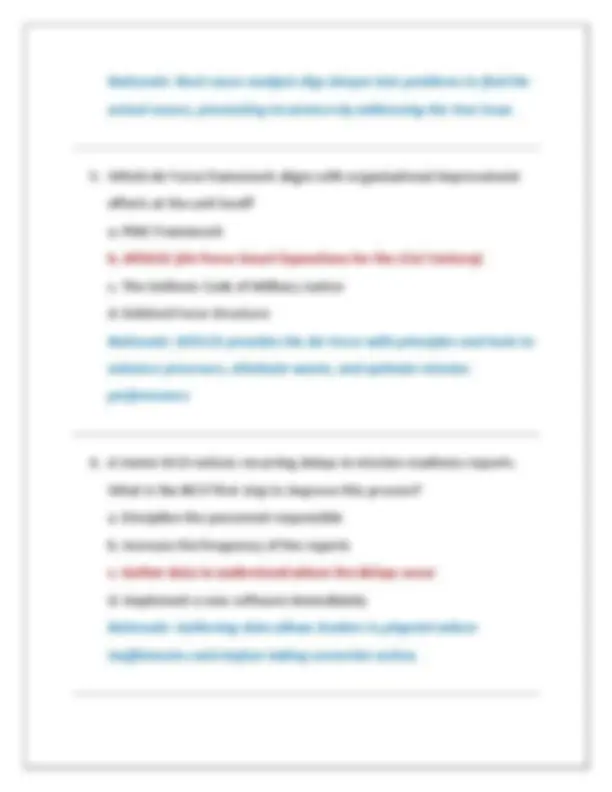
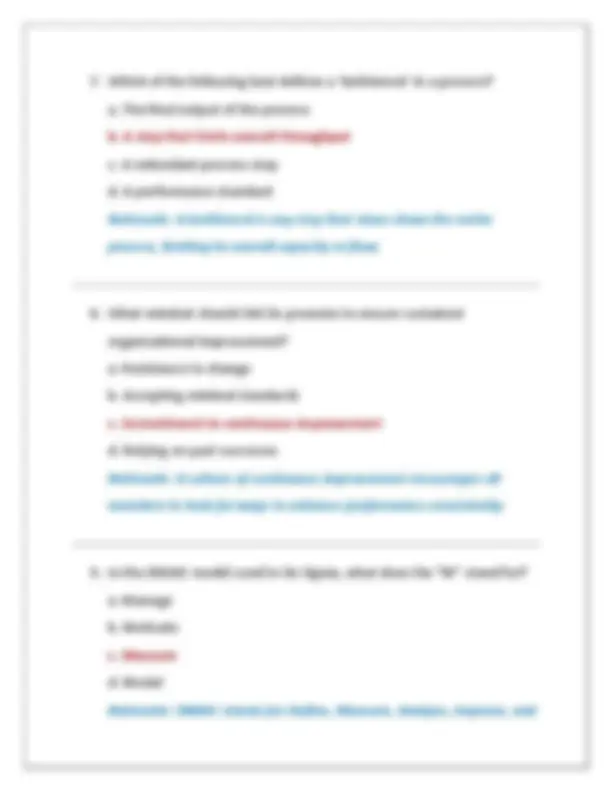
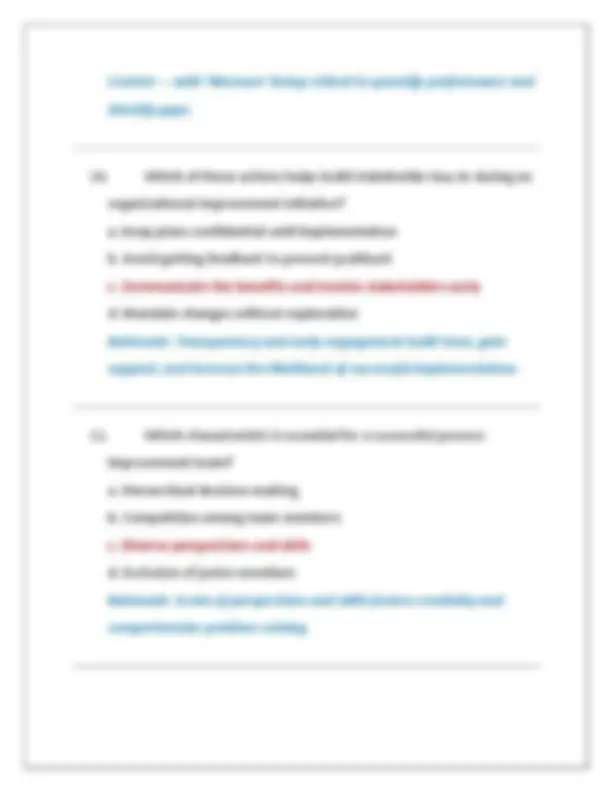
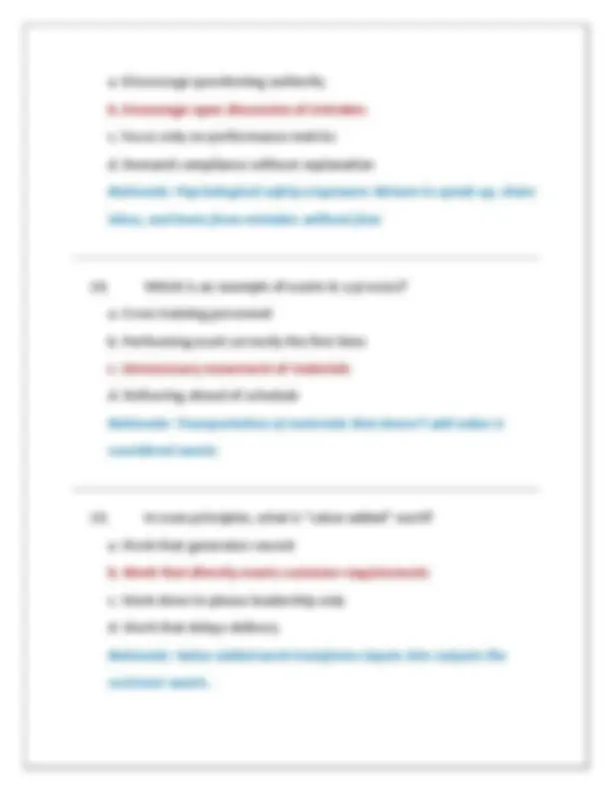
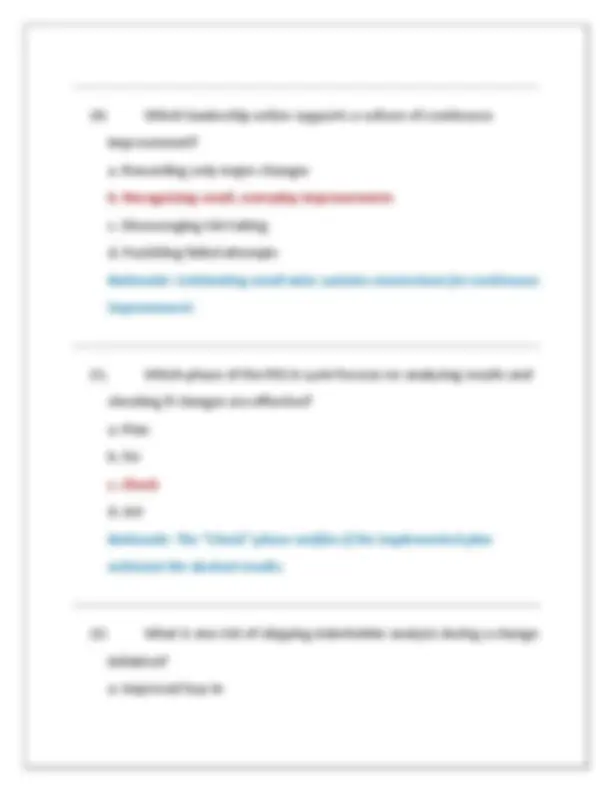
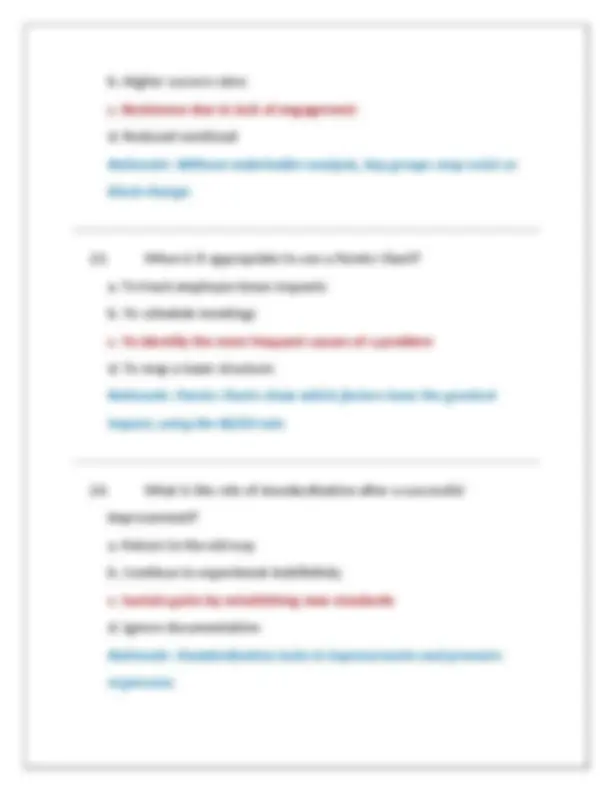
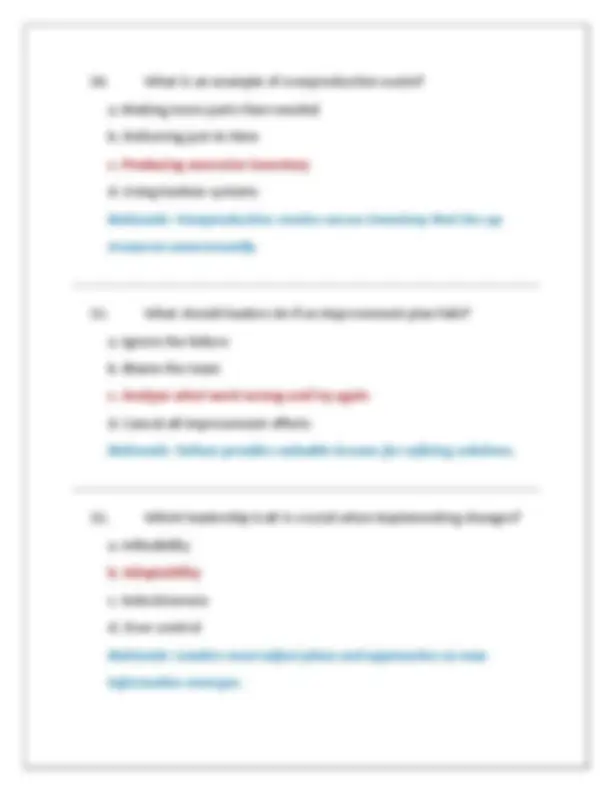

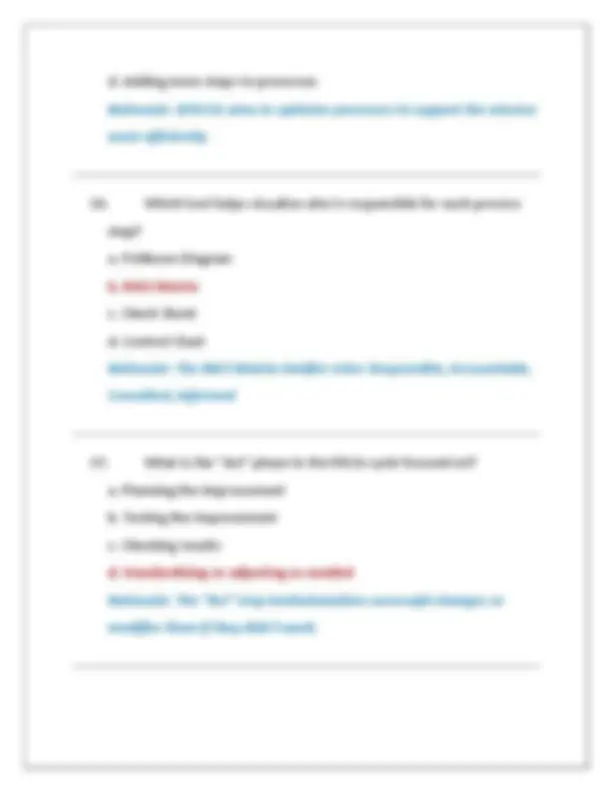
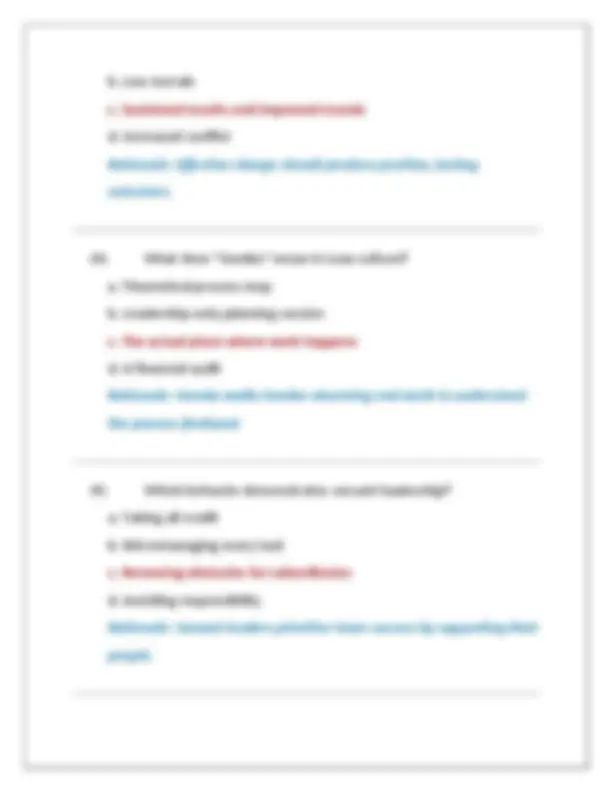
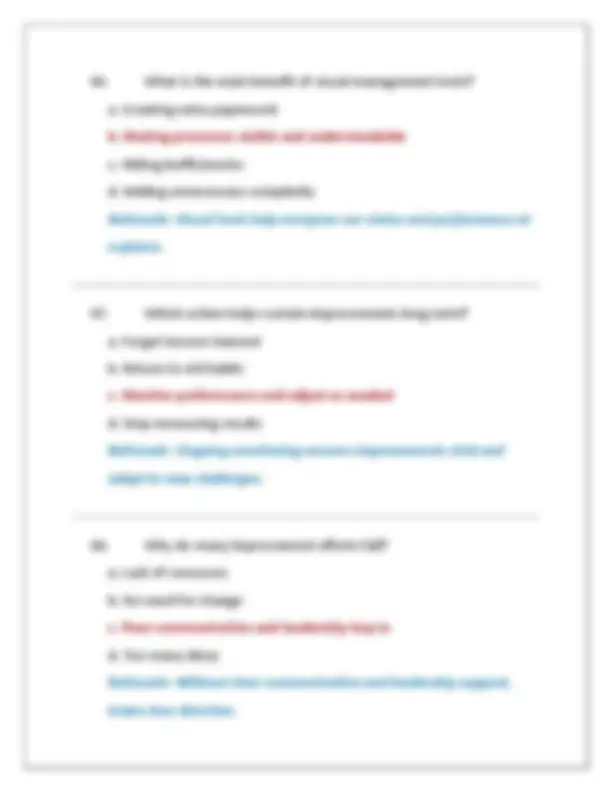
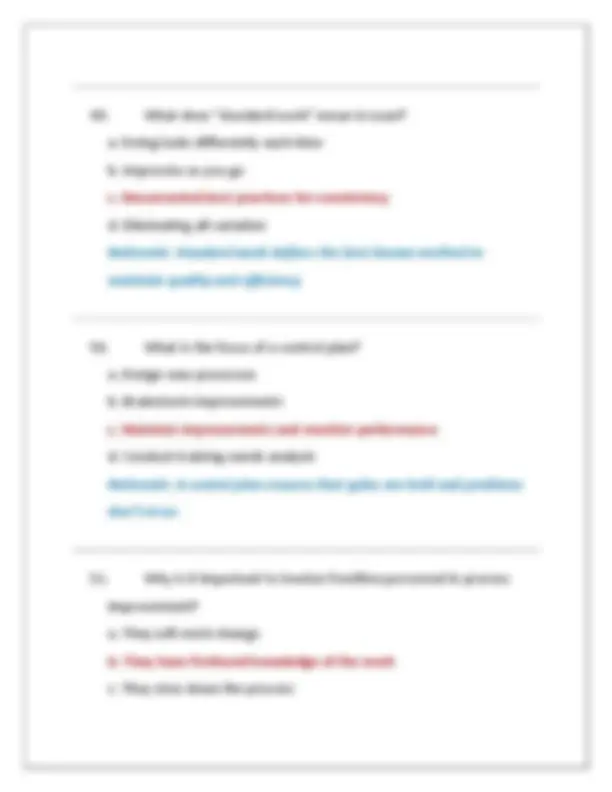
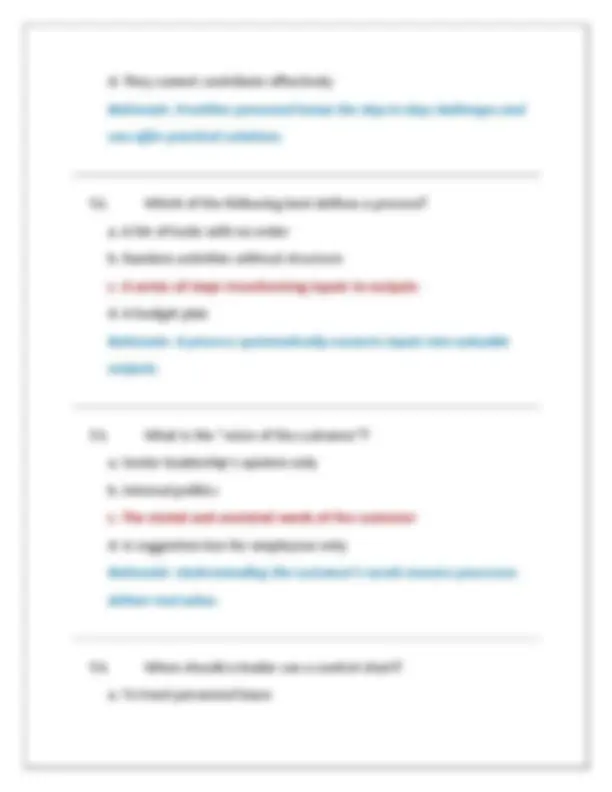
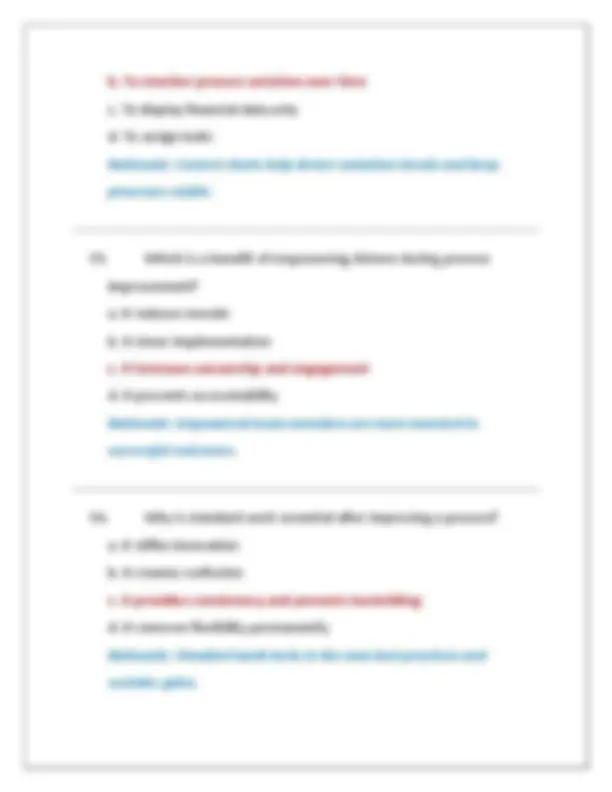
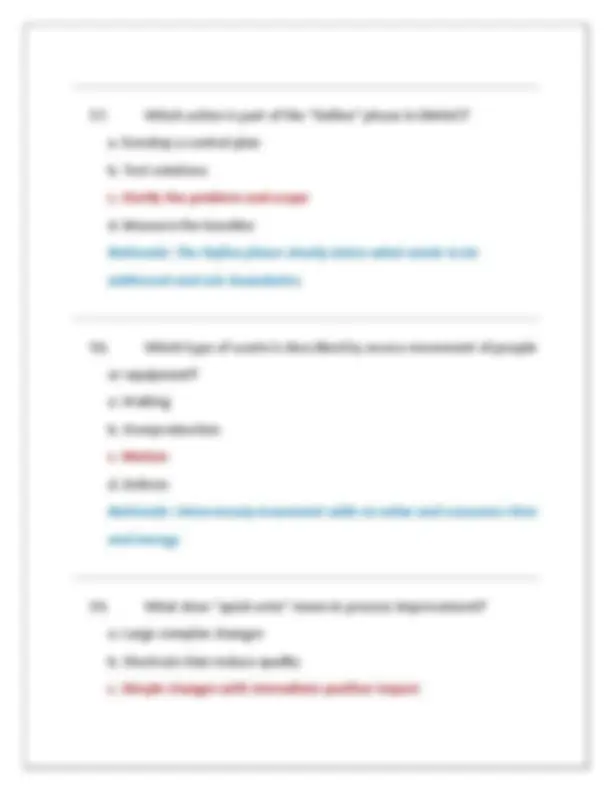
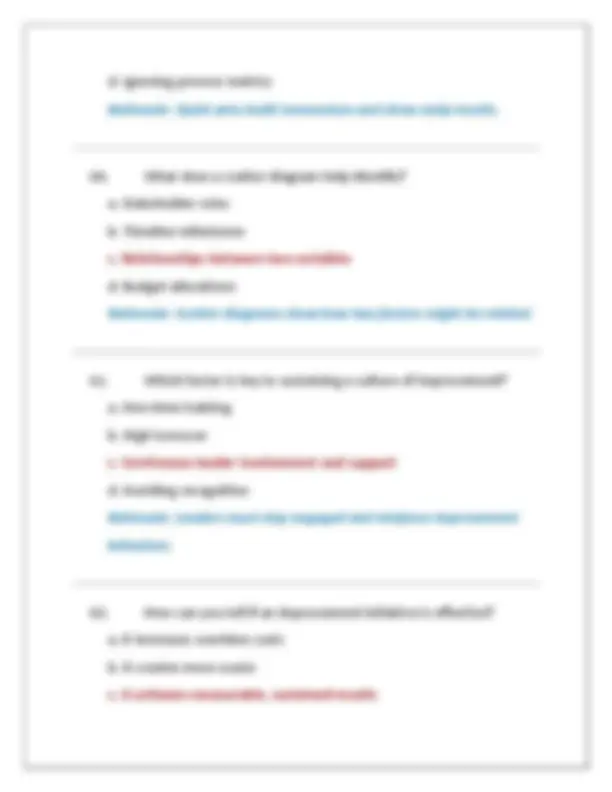
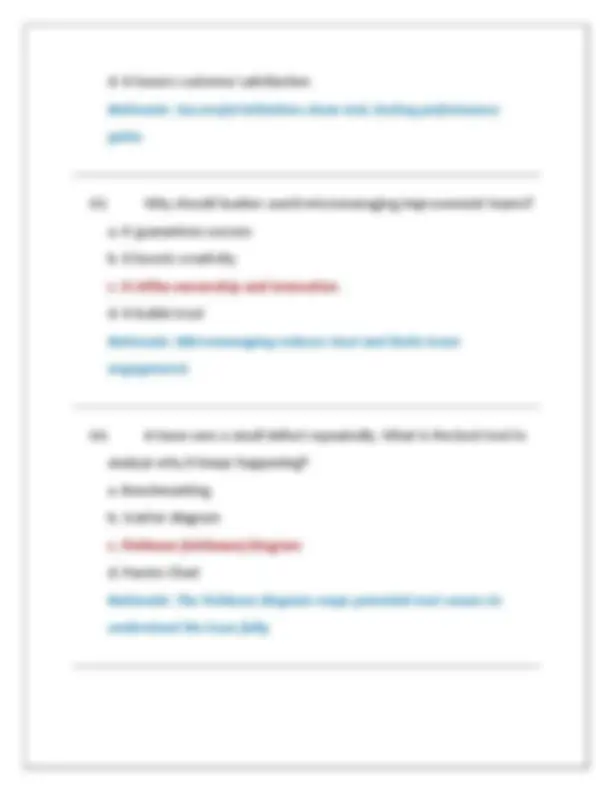
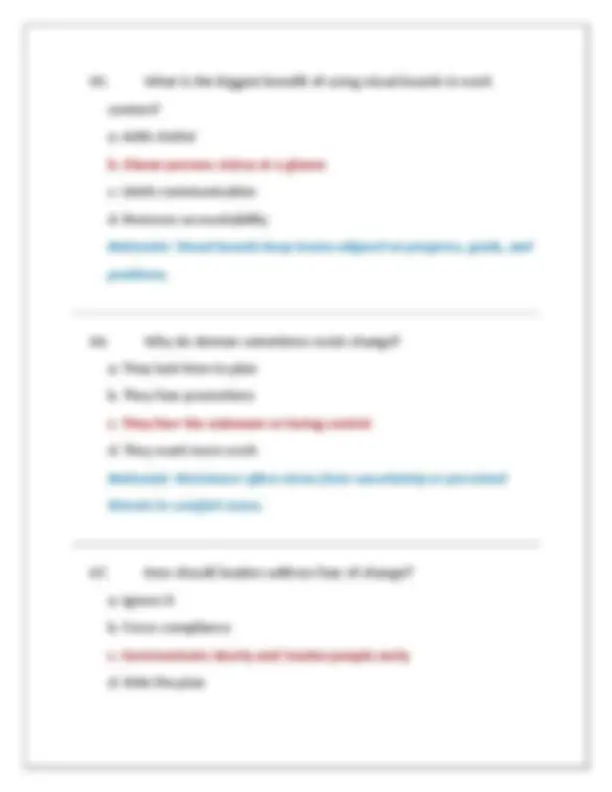
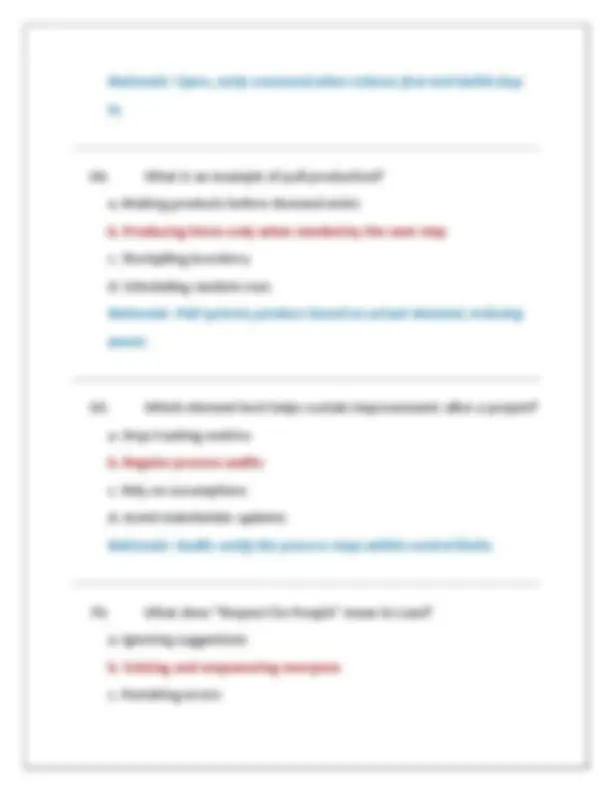
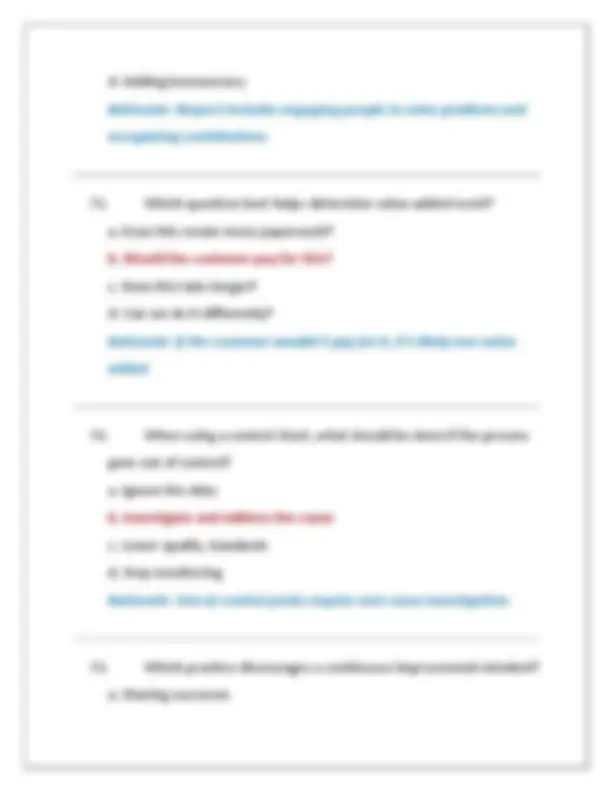
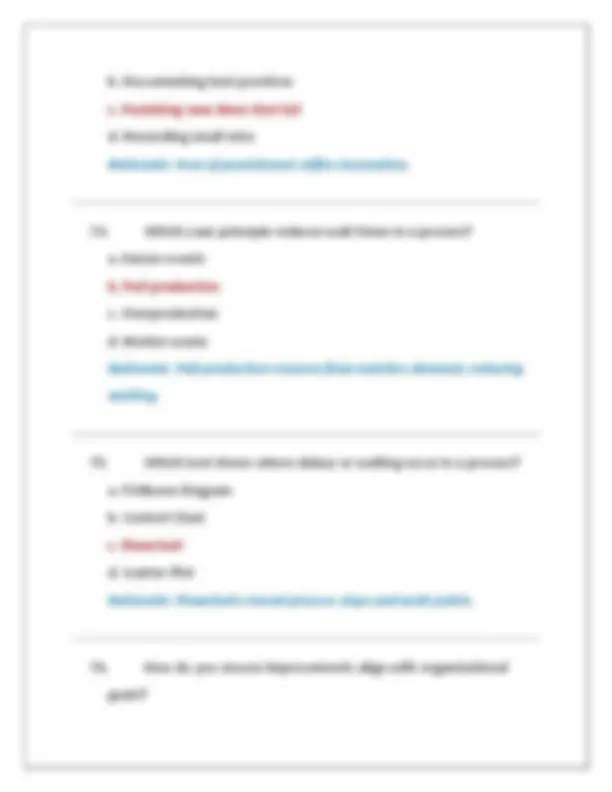
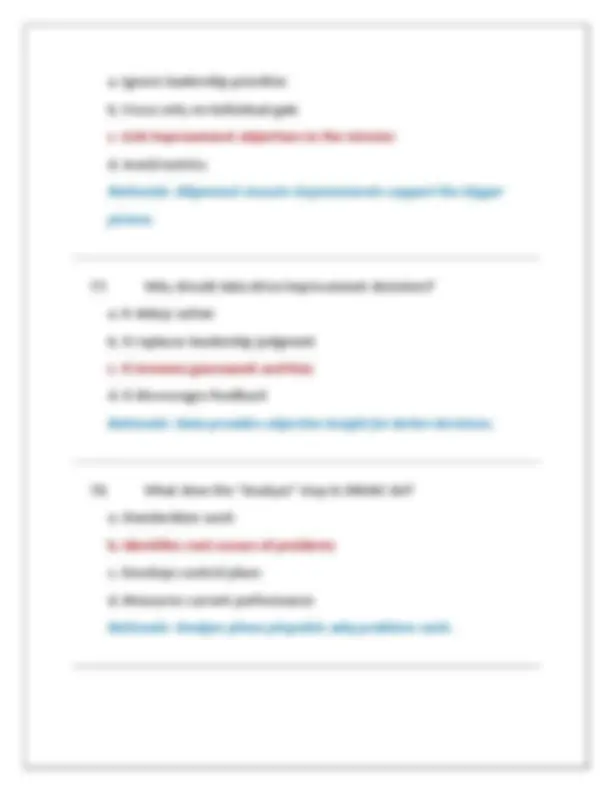
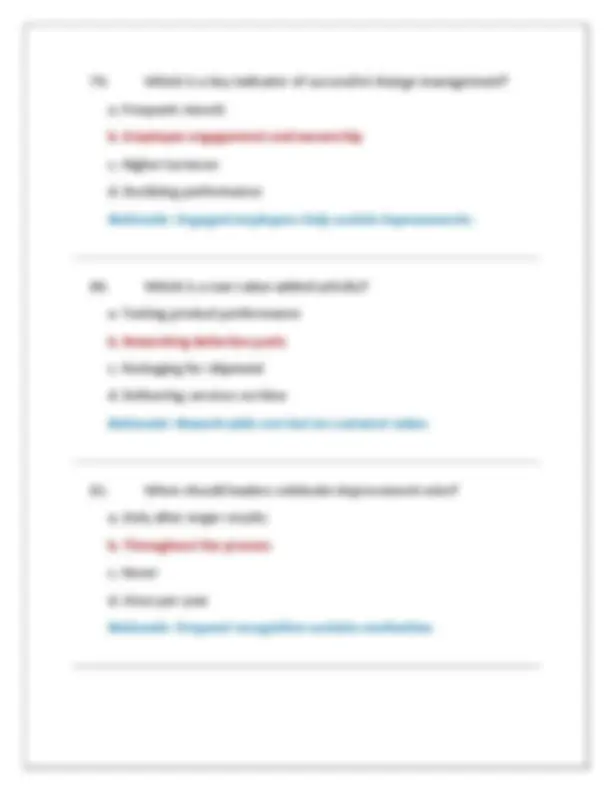
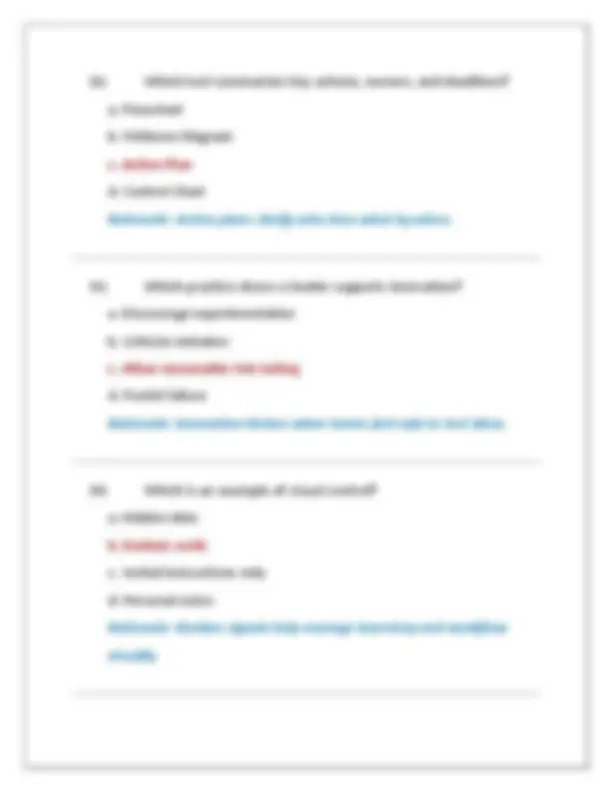
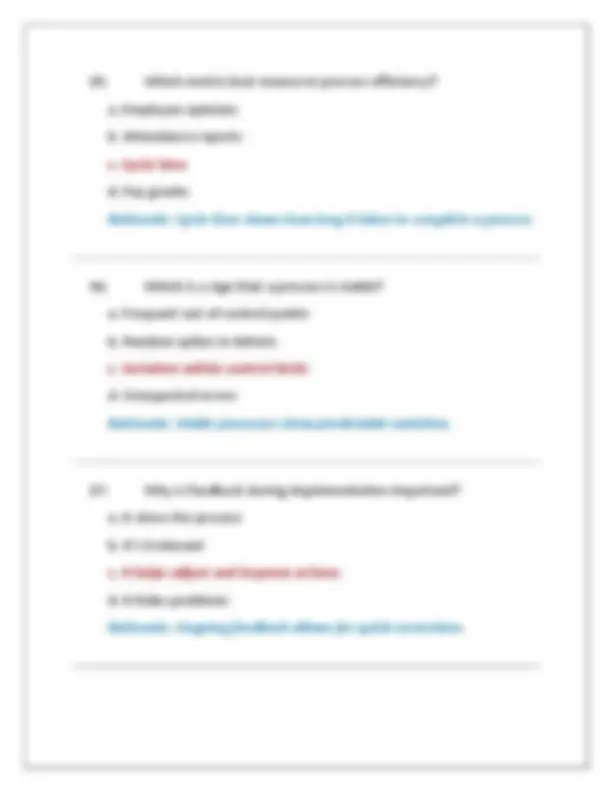
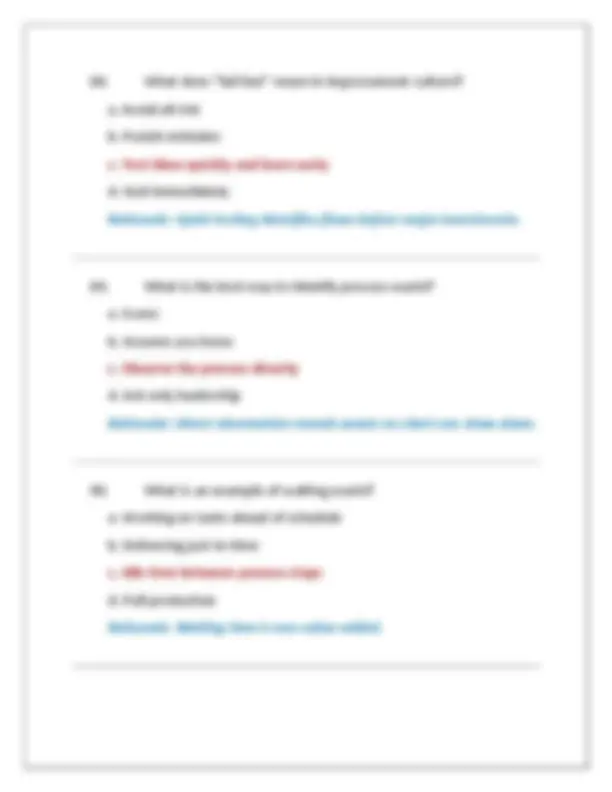
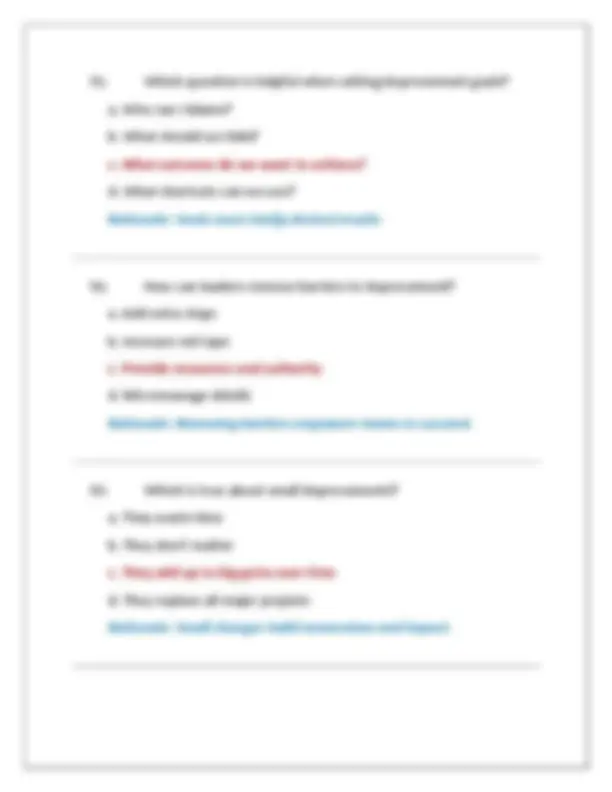
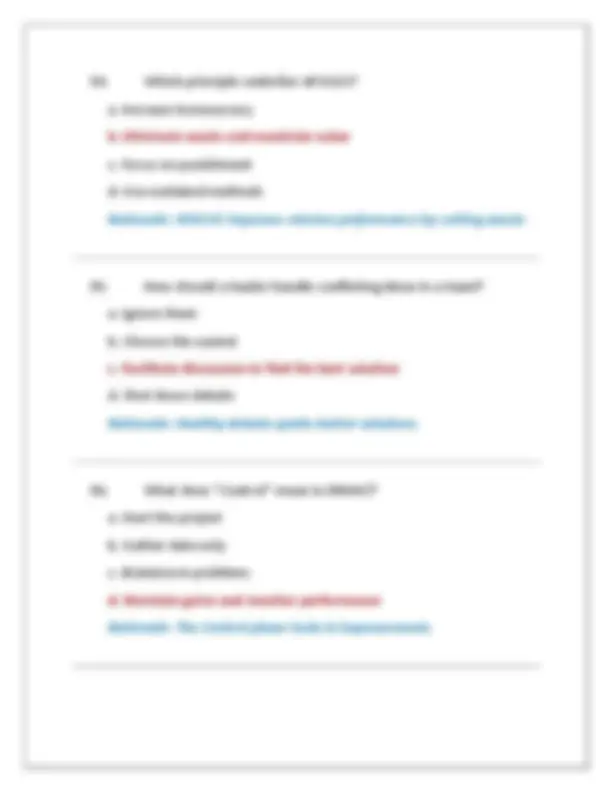
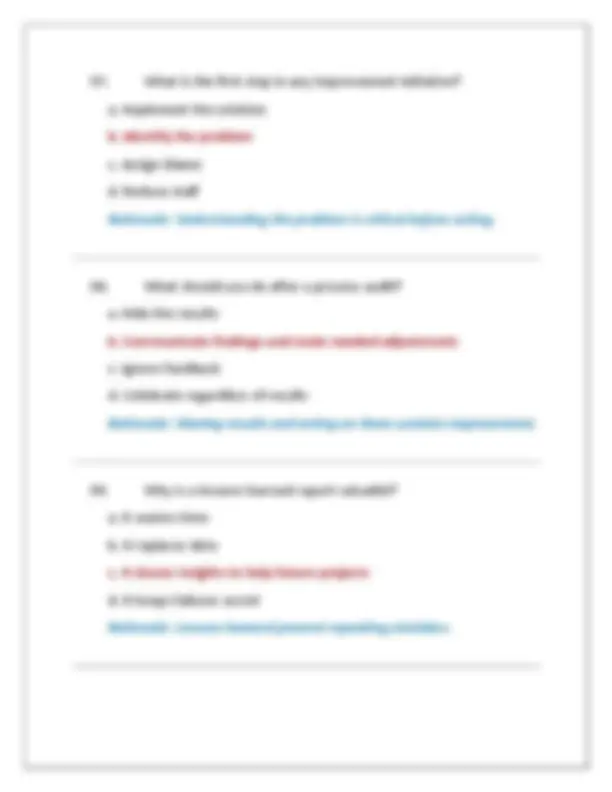

Study with the several resources on Docsity
Earn points by helping other students or get them with a premium plan
Prepare for your exams
Study with the several resources on Docsity
Earn points to download
Earn points by helping other students or get them with a premium plan
Community
Ask the community for help and clear up your study doubts
Discover the best universities in your country according to Docsity users
Free resources
Download our free guides on studying techniques, anxiety management strategies, and thesis advice from Docsity tutors
SNCOA LDR-303S IMPROVING ORGANIZATIONS PRACTICE EXAM QUESTIONS AND CORRECT ANSWERS (VERIFIED ANSWERS) PLUS RATIONALES 2025
Typology: Exams
1 / 38
This page cannot be seen from the preview
Don't miss anything!
Control — with ‘Measure’ being critical to quantify performance and identify gaps.
Rationale: The 5 Whys is a simple root cause analysis tool that asks “Why?” multiple times to reach the underlying issue.
a. Discourage questioning authority b. Encourage open discussion of mistakes c. Focus only on performance metrics d. Demand compliance without explanation Rationale: Psychological safety empowers Airmen to speak up, share ideas, and learn from mistakes without fear.
b. Higher success rates c. Resistance due to lack of engagement d. Reduced workload Rationale: Without stakeholder analysis, key groups may resist or block change.
Rationale: Lean focuses on providing maximum value with minimal waste.