
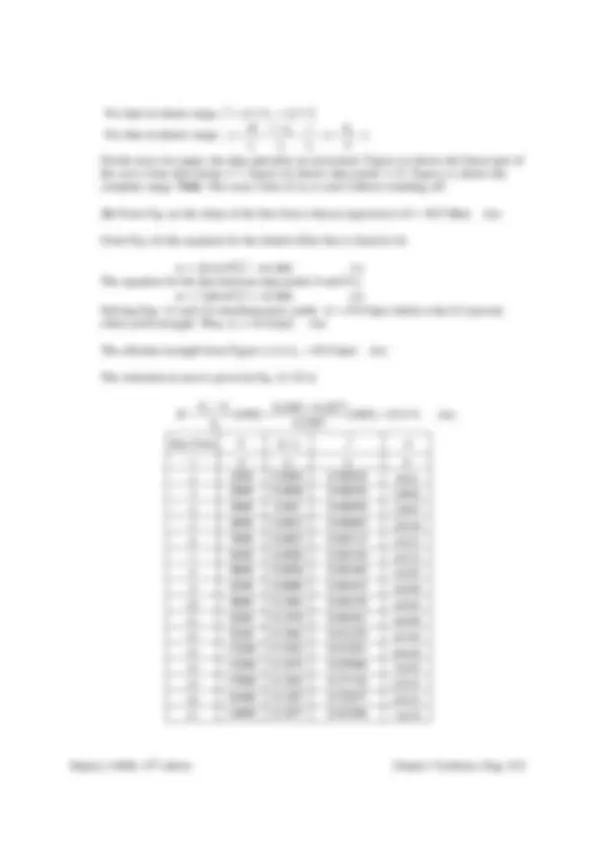
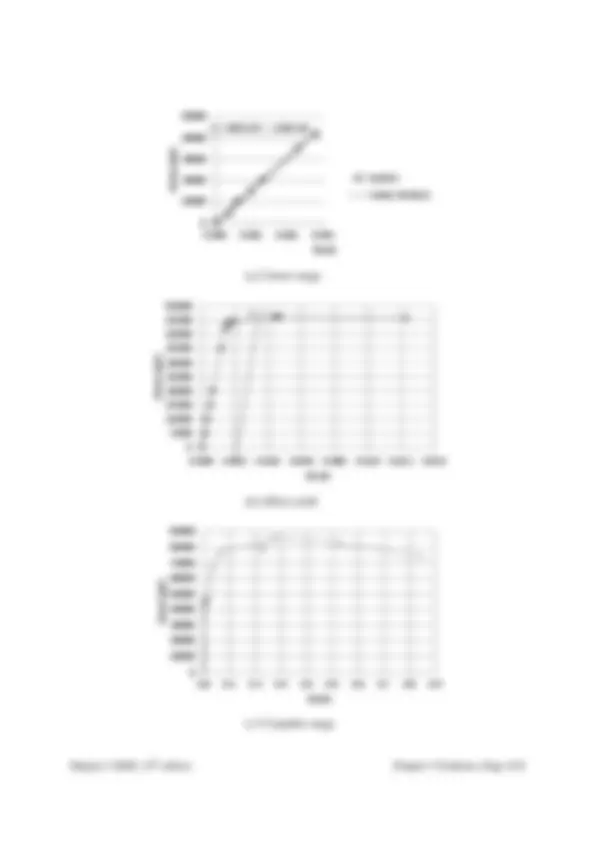
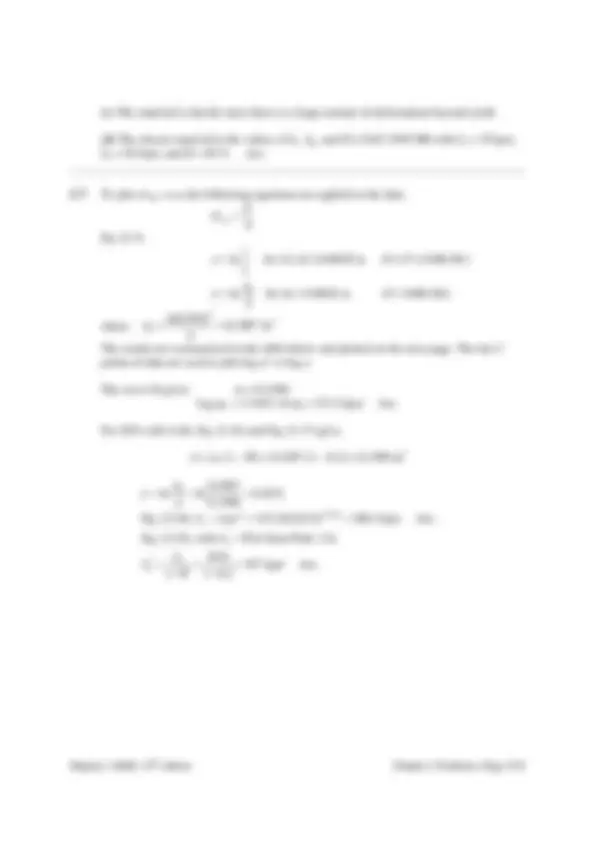
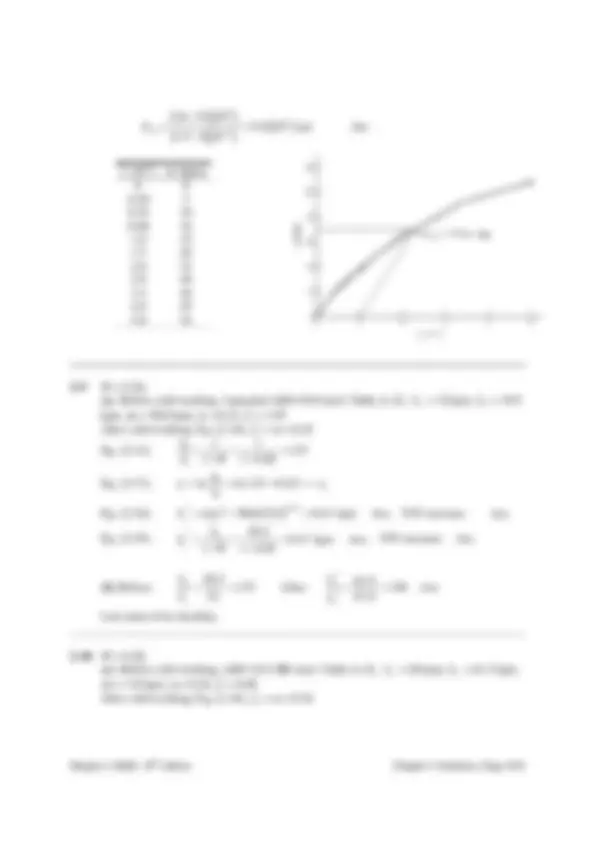
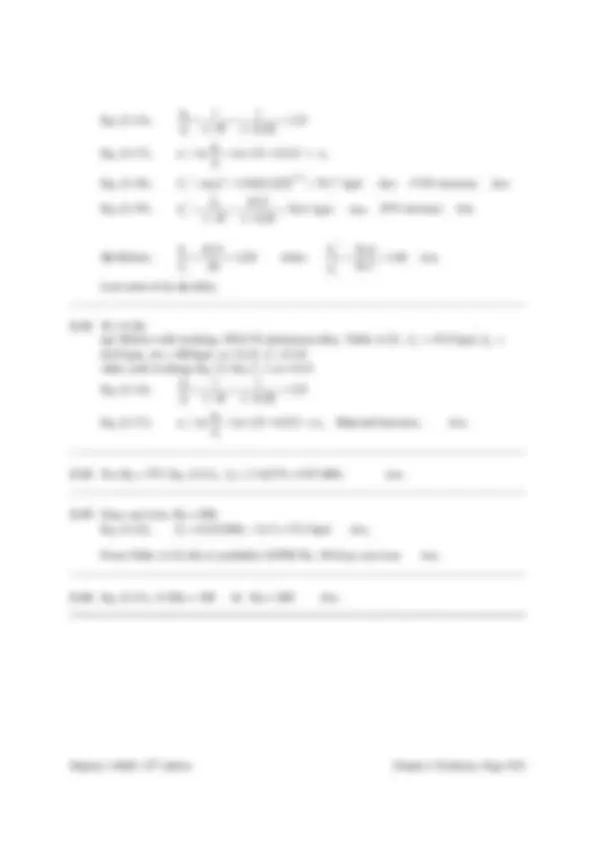
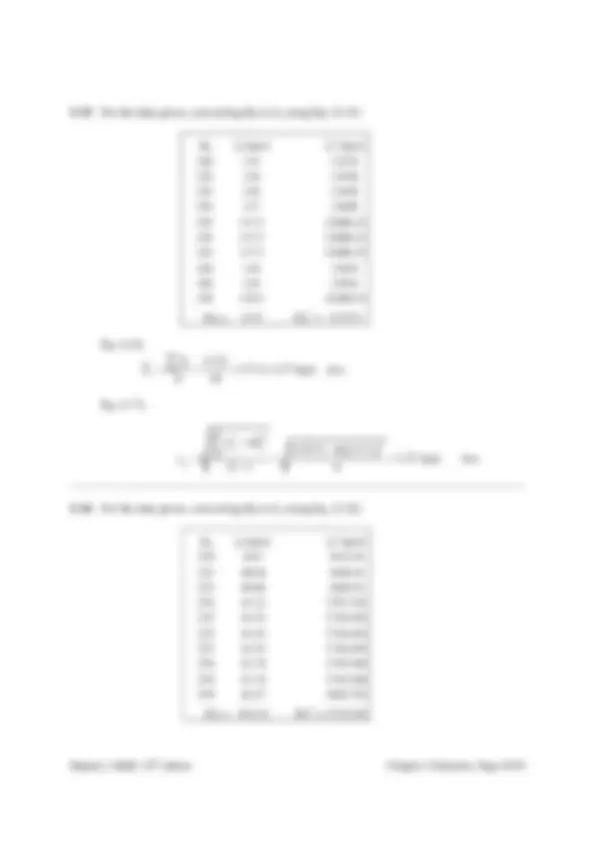
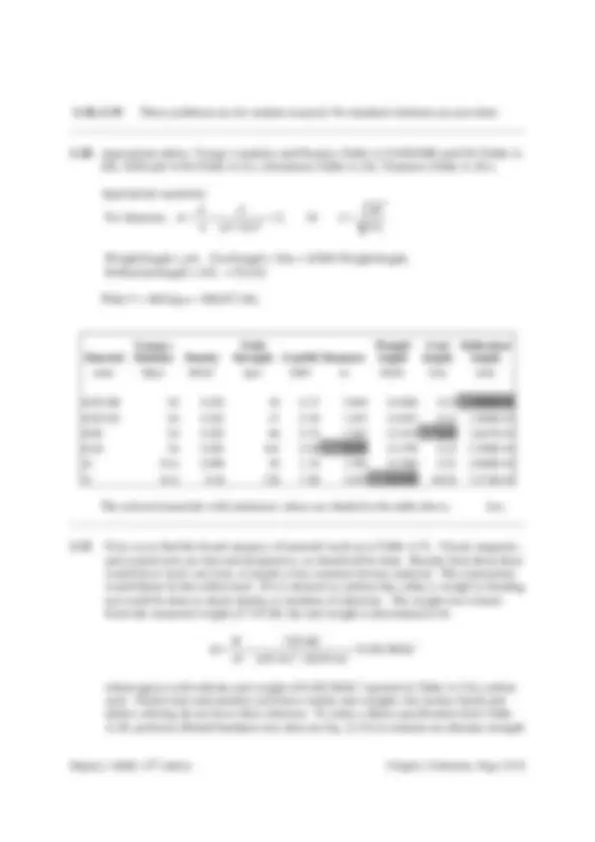
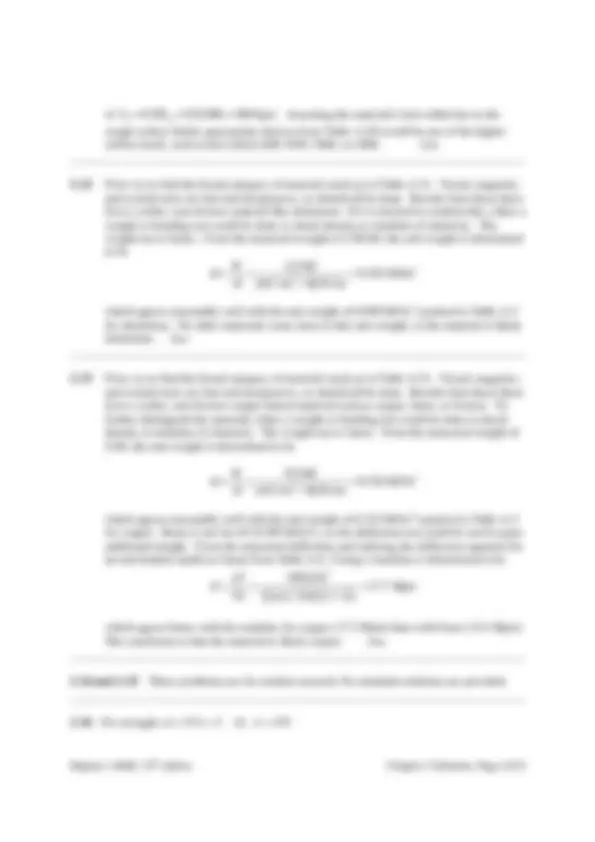
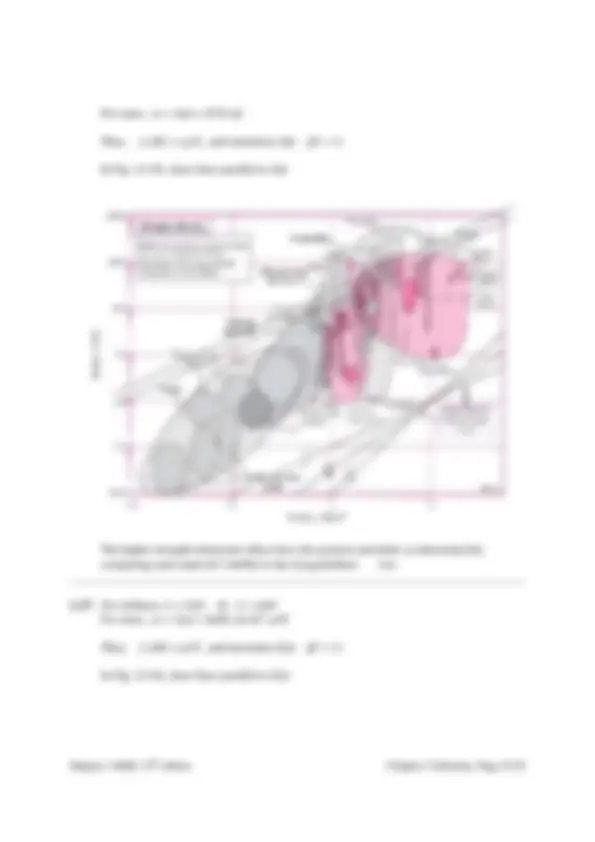
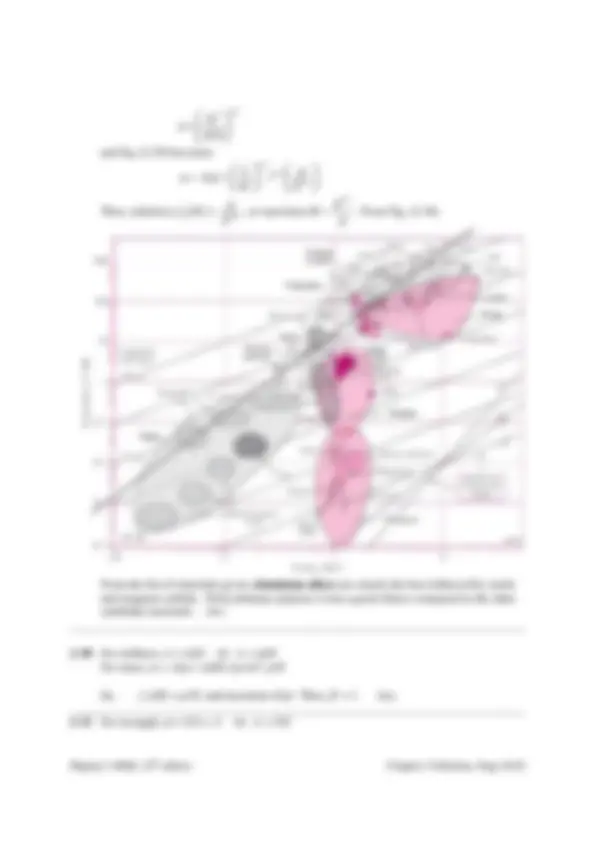
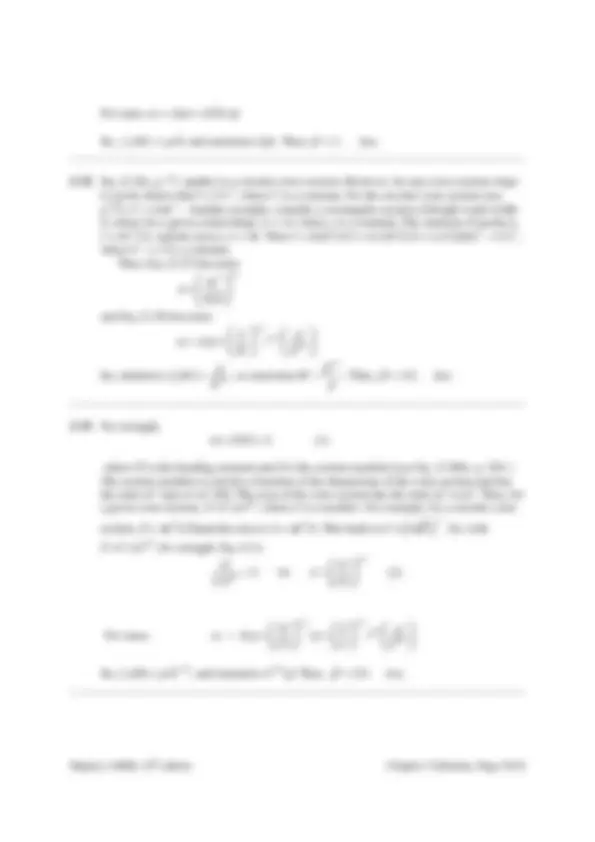
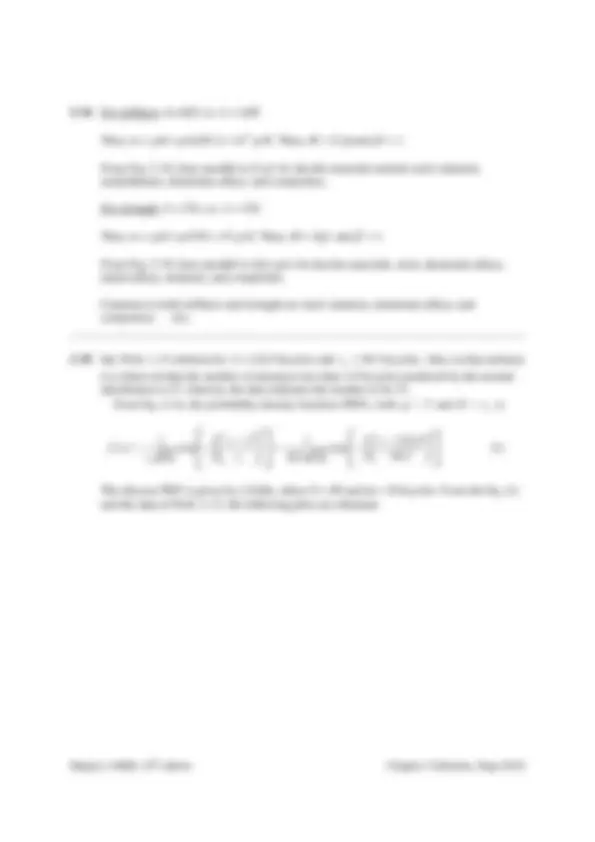
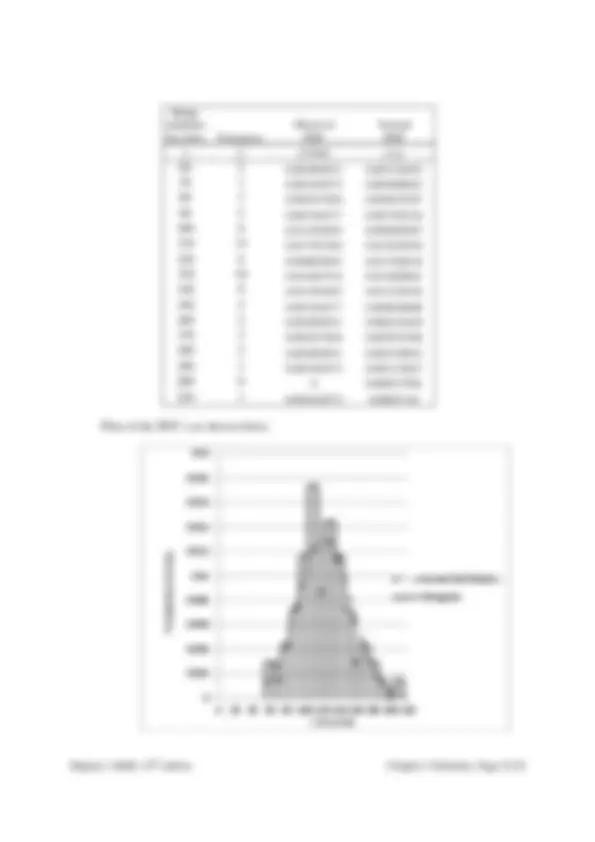
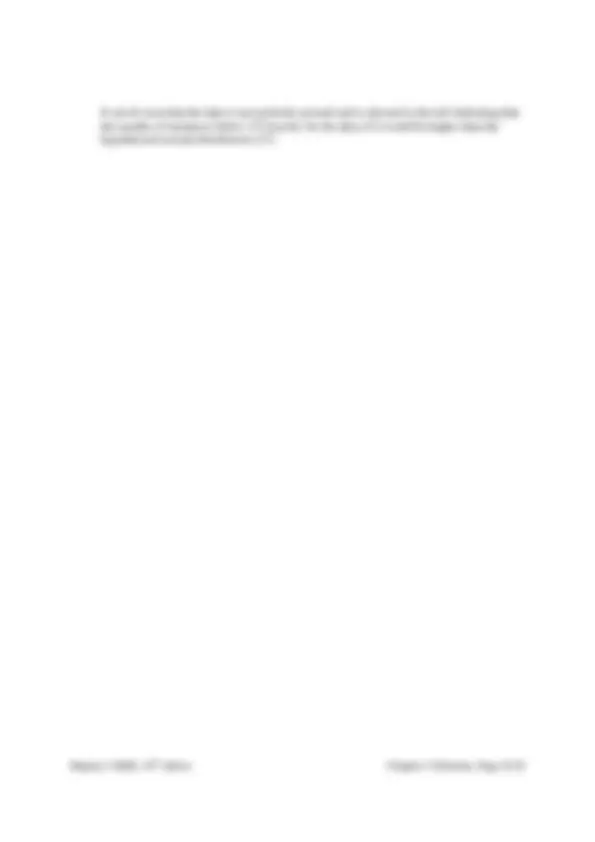
Study with the several resources on Docsity
Earn points by helping other students or get them with a premium plan
Prepare for your exams
Study with the several resources on Docsity
Earn points to download
Earn points by helping other students or get them with a premium plan
Community
Ask the community for help and clear up your study doubts
Discover the best universities in your country according to Docsity users
Free resources
Download our free guides on studying techniques, anxiety management strategies, and thesis advice from Docsity tutors
Shigley's Mechanical Engineering Design 10th Edition, Chapter 2 problems solution, Michael A. Latcha, PhD. ME 486
Typology: Lecture notes
1 / 22
This page cannot be seen from the preview
Don't miss anything!
2-1 From Tables A-20, A-21, A-22, and A-24c, ( a ) UNS G10200 HR: Sut = 380 (55) MPa (kpsi), Syt = 210 (30) MPa (kpsi) Ans. ( b ) SAE 1050 CD: Sut = 690 (100) MPa (kpsi), Syt = 580 (84) MPa (kpsi) Ans. ( c ) AISI 1141 Q&T at 540°C (1000°F): Sut = 896 (130) MPa (kpsi), Syt = 765 (111) MPa (kpsi) Ans. ( d ) 2024-T4: Sut = 446 (64.8) MPa (kpsi), Syt = 296 (43.0) MPa (kpsi) Ans. ( e ) Ti-6Al-4V annealed: Sut = 900 (130) MPa (kpsi), Syt = 830 (120) MPa (kpsi) Ans.
2-2 ( a ) Maximize yield strength: Q&T at 425°C (800°F) Ans.
( b ) Maximize elongation: Q&T at 650°C (1200°F) Ans.
2-3 Conversion of kN/m^3 to kg/ m^3 multiply by 1(10^3 ) / 9.81 = 102 AISI 1018 CD steel: Tables A-20 and A- ( )
370 10 3 47.4 kN m/kg. 76.5 102
S (^) y Ans ρ
= = ⋅
2011-T6 aluminum: Tables A-22 and A- ( )
169 10^3 62.3 kN m/kg. 26.6 102
S (^) y Ans ρ
= = ⋅
Ti-6Al-4V titanium: Tables A-24c and A- ( )
830 10^3 187 kN m/kg. 43.4 102
S (^) y Ans ρ
= = ⋅
ASTM No. 40 cast iron: Tables A-24a and A-5.Does not have a yield strength. Using the ultimate strength in tension ( )( )
42.5 6.89 103 40.7 kN m/kg 70.6 102
S ut (^) Ans ρ
= = ⋅
AISI 1018 CD steel: Table A- ( ) ( )
6 30.0 10 (^) 106 10 (^6) in.
Ans γ
2011-T6 aluminum: Table A- ( ) ( )
6 10.4 10 (^) 106 10 (^6) in.
Ans γ
Ti-6Al-6V titanium: Table A- ( ) ( )
6 16.5 10 (^) 103 10 (^6) in.
Ans γ
No. 40 cast iron: Table A- ( ) ( )
6 14.5 10 (^) 55.8 10 (^6) in.
Ans γ
G v E v G
Using values for E and G from Table A-5,
Steel:
v Ans
The percent difference from the value in Table A-5 is
0.0411 4.11 percent.
Ans
Aluminum:
v Ans
The percent difference from the value in Table A-5 is 0 percent Ans.
Beryllium copper:
v Ans
The percent difference from the value in Table A-5 is
0.00351 0.351 percent.
Ans
Gray cast iron:
v Ans
The percent difference from the value in Table A-5 is
0.0142 1.42 percent.
Ans
2-6 ( a ) A 0 = π (0.503)^2 /4 = 0.1987 in^2 , σ = Pi / A 0
( a ) Linear range
( b ) Offset yield
( c ) Complete range
y = 3.05E+07x - 1.06E+
0
10000
20000
30000
40000
50000
0.000 0.001 0.001 0.
Stress (psi)
Strain
Series Linear (Series1)
0
5000
10000
15000
20000
25000
30000
35000
40000
45000
50000
0.000 0.002 0.004 0.006 0.008 0.010 0.012 0.
Stress (psi)
Strain
Y
0
10000
20000
30000
40000
50000
60000
70000
80000
90000
0.0 0.1 0.2 0.3 0.4 0.5 0.6 0.7 0.8 0.
Stress (psi)
Strain
U
( c ) The material is ductile since there is a large amount of deformation beyond yield.
( d ) The closest material to the values of Sy, Sut, and R is SAE 1045 HR with Sy = 45 kpsi, Sut = 82 kpsi, and R = 40 %. Ans.
2-7 To plot σ (^) true vs. ε, the following equations are applied to the data.
true
σ =
Eq. (2-4)
0 0
ln for 0 0.0028 in (0 8 400 lbf )
ln for 0.0028 in ( 8 400 lbf )
l l P l A l P A
ε
ε
where
2 2 0
0.1987 in 4
The results are summarized in the table below and plotted on the next page. The last 5 points of data are used to plot log σ vs log ε
The curve fit gives m = 0. log σ 0 = 5.1852 ⇒ σ 0 = 153.2 kpsi Ans.
For 20% cold work, Eq. (2-14) and Eq. (2-17) give,
A = A 0 (1 – W ) = 0.1987 (1 – 0.2) = 0.1590 in^2
0
0
ln ln 0.
Eq. (2-18): 153.2(0.2231) 108.4 kpsi.
Eq. (2-19), with 85.6 from Prob. 2-6,
107 kpsi. 1 1 0.
m y
u u u
S Ans
S S S Ans W
ε
′ σ ε
2-8 Tangent modulus at σ = 0 is
( )
( )
6 3
25 10 psi 0.2 10 0
σ −
∆ ò (^) −
Ans.
At σ = 20 kpsi
Shigley’s MED, 10th^ edition
( )(
20
∫ (10-^3 ) σ (kpsi) 0 0 0.20 5 0.44 10 0.80 16 1.0 19 1.5 26 2.0 32 2.8 40 3.4 46 4.0 49 5.0 54
( a ) Before cold working: kpsi, σ 0 = 90.0 kpsi, m After cold working: Eq. (
Eq. (2-14), 0 i^1 1 0.
Eq. (2-17), ε i = ln = ln1.25 = 0.223< ε u
Eq. (2-18), S (^) y ′^ = σ ε i = = Ans
Eq. (2-19), u 1 1 0. S ′^ = = = Ans − −
( b ) Before:
u y
Lost most of its ductility
( a ) Before cold working: AISI 1212 HR steel. Table A σ 0 = 110 kpsi, m = 0.24, After cold working: Eq. (
Chapter 2
)( )
( )
( )
3 6 3
14.0 10 psi 1.5 1 10 −
≈ = Ans.
) Before cold working: Annealed AISI 1018 steel. Table A-22, Sy = 0.25, ∫ f = 1. After cold working: Eq. (2-16), ∫ u = m = 0. 1 1
A 1 W 1 0.
ln 0 ln1.25 0. i u i
ε = = = < ε
0 90 0.223^ 61.8 kpsi^.
m S (^) y = σ ε i = = Ans 93% increase
61.9 kpsi. 1 1 0.
S S^ u Ans W
25% increase
= = After:
u y
ductility.
) Before cold working: AISI 1212 HR steel. Table A-22, Sy = 28 kpsi, 0.24, ∫ f = 0. q. (2-16), ∫ u = m = 0.
Chapter 2 Solutions, Page 8/
y = 32 kpsi,^ Su = 49.
93% increase Ans.
25% increase Ans.
Ans.
= 28 kpsi, Su = 61.5 kpsi,
2-15 For the data given, converting HB to Su using Eq. (2-21)
HB Su (kpsi) Su^2 (kpsi) 230 115 13225 232 116 13456 232 116 13456 234 117 13689 235 117.5 13806. 235 117.5 13806. 235 117.5 13806. 236 118 13924 236 118 13924 239 119.5 14280. Σ Su = 1172 Σ Su^2 = 137373
Eq. (1-6) 1172 117.2 117 kpsi. 10
u u
S Ans N
= ∑ = = ≈
Eq. (1-7),
(^10 2 ) 2 1 137373 10 117.2^ 1.27 kpsi. u 1 9
u u i S
s Ans N
=
∑
2-16 For the data given, converting HB to Su using Eq. (2-22)
HB Su (kpsi) Su^2 (kpsi) 230 40.4 1632. 232 40.86 1669. 232 40.86 1669. 234 41.32 1707. 235 41.55 1726. 235 41.55 1726. 235 41.55 1726. 236 41.78 1745. 236 41.78 1745. 239 42.47 1803. Σ Su = 414.12 Σ Su^2 = 17152.
Eq. (1-6)
41.4 kpsi. 10
u u
S Ans N
= ∑ = =
Eq. (1-7),
10 (^2 2 ) 1 17152.63^ 10 41.4^ 1.. u 1 9
u u i S
s Ans N
=
∑
2-17 ( a ) Eq. (2-9)
2 45.6 (^) 34.7 in lbf / in 3. R 2(30) u ≈ = ⋅ Ans
( b ) A 0 = π(0.503^2 )/4 = 0.19871 in^2
P (^) ∆ L A ( A 0 / A ) – 1 ∫ σ = P / A 0 0 0 0 0 1 000 0.000 4 0.000 2 5 032. 2 000 0.000 6 0.000 3 10 070 3 000 0.001 0 0.000 5 15 100 4 000 0.001 3 0.000 65 20 130 7 000 0.002 3 0.001 15 35 230 8 400 0.002 8 0.001 4 42 270 8 800 0.003 6 0.001 8 44 290 9 200 0.008 9 0.004 45 46 300 9 100 0.196 3 0.012 28 0.012 28 45 800 13 200 0.192 4 0.032 80 0.032 80 66 430 15 200 0.187 5 0.059 79 0.059 79 76 500 17 000 0.156 3 0.271 34 0.271 34 85 550 16 400 0.130 7 0.520 35 0.520 35 82 530 14 800 0.107 7 0.845 03 0.845 03 74 480
From the figures on the next page,
( )
5
1
3 3
66.7 10 in lbf/in.
T i i
u A
Ans
=
∑
2-18, 2-19 These problems are for student research. No standard solutions are provided.
2-20 Appropriate tables: Young’s modulus and Density (Table A-5)1020 HR and CD (Table A- 20), 1040 and 4140 (Table A-21), Aluminum (Table A-24), Titanium (Table A-24c)
Appropriate equations:
For diameter,
4 / 4 y y
F F F S d A d S
σ π π
= = = ⇒ =
Weight/length = ρ A , Cost/length = $/in = ($/lbf) Weight/length, Deflection/length = δ /L = F/ ( AE )
With F = 100 kips = 100(10^3 ) lbf,
Material
Young's Modulus Density
Yield Strength Cost/lbf Diameter
Weight/ length
Cost/ length
Deflection/ length units Mpsi lbf/in^3 kpsi $/lbf in lbf/in $/in in/in
1020 HR 30 0.282 30 0.27 2.060 0.9400 0.25 1.000E- 1020 CD 30 0.282 57 0.30 1.495 0.4947 0.15 1.900E- 1040 30 0.282 80 0.35 1.262 0.3525 0.12 2.667E- 4140 30 0.282 165 0.80 0.878 0.1709 0.14 5.500E- Al 10.4 0.098 50 1.10 1.596 0.1960 0.22 4.808E- Ti 16.5 0.16 120 7.00 1.030 0.1333 $0.93 7.273E-
The selected materials with minimum values are shaded in the table above. Ans.
2-21 First, try to find the broad category of material (such as in Table A-5). Visual, magnetic, and scratch tests are fast and inexpensive, so should all be done. Results from these three would favor steel, cast iron, or maybe a less common ferrous material. The expectation would likely be hot-rolled steel. If it is desired to confirm this, either a weight or bending test could be done to check density or modulus of elasticity. The weight test is faster. From the measured weight of 7.95 lbf, the unit weight is determined to be
3 2
7.95 lbf 0.281 lbf/in [ (1 in) / 4](36 in)
w = = =
which agrees well with the unit weight of 0.282 lbf/in^3 reported in Table A-5 for carbon steel. Nickel steel and stainless steel have similar unit weights, but surface finish and darker coloring do not favor their selection. To select a likely specification from Table A-20, perform a Brinell hardness test, then use Eq. (2-21) to estimate an ultimate strength
of Su = 0.5 HB = 0.5(200) = 100 kpsi. Assuming the material is hot-rolled due to the rough surface finish, appropriate choices from Table A-20 would be one of the higher carbon steels, such as hot-rolled AISI 1050, 1060, or 1080. Ans.
2-22 First, try to find the broad category of material (such as in Table A-5). Visual, magnetic, and scratch tests are fast and inexpensive, so should all be done. Results from these three favor a softer, non-ferrous material like aluminum. If it is desired to confirm this, either a weight or bending test could be done to check density or modulus of elasticity. The weight test is faster. From the measured weight of 2.90 lbf, the unit weight is determined to be 3 2
2.9 lbf 0.103 lbf/in [ (1 in) / 4](36 in)
w = = =
which agrees reasonably well with the unit weight of 0.098 lbf/in^3 reported in Table A- for aluminum. No other materials come close to this unit weight, so the material is likely aluminum. Ans.
2-23 First, try to find the broad category of material (such as in Table A-5). Visual, magnetic, and scratch tests are fast and inexpensive, so should all be done. Results from these three favor a softer, non-ferrous copper-based material such as copper, brass, or bronze. To further distinguish the material, either a weight or bending test could be done to check density or modulus of elasticity. The weight test is faster. From the measured weight of 9 lbf, the unit weight is determined to be
3 2
9.0 lbf 0.318 lbf/in [ (1 in) / 4](36 in)
w = = =
which agrees reasonably well with the unit weight of 0.322 lbf/in^3 reported in Table A- for copper. Brass is not far off (0.309 lbf/in^3 ), so the deflection test could be used to gain additional insight. From the measured deflection and utilizing the deflection equation for an end-loaded cantilever beam from Table A-9, Young’s modulus is determined to be
( )
3 3 4
17.7 Mpsi (^3 3) (1) 64 (17 / 32)
Fl E
which agrees better with the modulus for copper (17.2 Mpsi) than with brass (15.4 Mpsi). The conclusion is that the material is likely copper. Ans.
2-24 and 2-25 These problems are for student research. No standard solutions are provided.
2-26 For strength, σ = F/A = S ⇒ A = F/S
From the list of materials given, tungsten carbide (WC) is best, closely followed by aluminum alloys. They are close enough that other factors, like cost or availability, would likely dictate the best choice. Polycarbonate polymer is clearly not a good choice compared to the other candidate materials. Ans.
2-28 For strength, σ = Fl/Z = S (1)
where Fl is the bending moment and Z is the section modulus [see Eq. (3-26 b ), p. 104 ]. The section modulus is strictly a function of the dimensions of the cross section and has the units in^3 (ips) or m^3 (SI). Thus, for a given cross section, Z =C ( A )3/2, where C is a
1 4 π
−
. Then, for strength, Eq. (1) is 2/ 3/
Fl Fl S A CA CS
For mass,
2/3 2/ 5/ 2/
Fl F m Al l l CS C S
ρ = ρ= ^ ^ ρ=^ ^ ^
Thus, f (^) 3 ( M ) = ρ /S 2/3, and maximize S 2/3 / ρ ( β = 2/3)
In Fig. (2-19), draw lines parallel to S 2/3 / ρ
From the list of materials given, a higher strength aluminum alloy has the greatest potential, followed closely by high carbon heat-treated steel. Tungsten carbide is clearly not a good choice compared to the other candidate materials.. Ans.
2-29 Eq. (2-26), p. 77, applies to a circular cross section. However, for any cross section shape it can be shown that I = CA^2 , where C is a constant. For example, consider a rectangular section of height h and width b, where for a given scaled shape, h = cb , where c is a constant. The moment of inertia is I = bh^3 /12, and the area is A = bh. Then I = h ( bh^2 )/ = cb ( bh^2 )/12 = ( c /12)( bh )^2 = CA^2 , where C = c /12 (a constant). Thus, Eq. (2-27) becomes
For mass, m = Al ρ = ( F/S ) l ρ
So, f (^) 3 ( M ) = ρ /S , and maximize S/ ρ. Thus, β = 1. Ans.
2-32 Eq. (2-26), p. 77, applies to a circular cross section. However, for any cross section shape it can be shown that I = CA^2 , where C is a constant. For the circular cross section (see p.77), C = (4 π)−^1. Another example, consider a rectangular section of height h and width b, where for a given scaled shape, h = cb , where c is a constant. The moment of inertia is I = bh^3 /12, and the area is A = bh. Then I = h ( bh^2 )/12 = cb ( bh^2 )/12 = ( c /12)( bh )^2 = CA^2 , where C = c /12, a constant. Thus, Eq. (2-27) becomes 3 1/
3
kl A CE
and Eq. (2-29) becomes 1/ 5/ 3 1/
k m Al l C E
ρ ρ
ρ = , or maximize
ρ
=. Thus, β = 1/2. Ans.
2-33 For strength, σ = Fl/Z = S (1)
where Fl is the bending moment and Z is the section modulus [see Eq. (3-26 b ), p. 104 ]. The section modulus is strictly a function of the dimensions of the cross section and has the units in^3 (ips) or m^3 (SI). The area of the cross section has the units in^2 or m^2. Thus, for a given cross section, Z =C ( A )3/2, where C is a number. For example, for a circular cross
1 4 π
−
. So, with Z =C ( A )3/2, for strength, Eq. (1) is 2/ 3/
Fl Fl S A CA CS
For mass,
2/3 2/ 5/ 2/
Fl F m Al l l CS C S
ρ = ρ= ^ ^ ρ=^ ^ ^
So, f (^) 3 ( M ) = ρ /S 2/3, and maximize S 2/3 / ρ. Thus, β = 2/3. Ans.
2-34 For stiffness, k=AE/l , or, A = kl/E.
Thus, m = ρ Al = ρ ( kl/E ) l = kl^2 ρ /E. Then, M = E / ρ and β = 1.
From Fig. 2-16, lines parallel to E / ρ for ductile materials include steel, titanium, molybdenum, aluminum alloys, and composites.
For strength, S = F/A , or, A = F/S.
Thus, m = ρ Al = ρ F/Sl = Fl ρ /S. Then, M = S/ ρ and β = 1.
From Fig. 2-19, lines parallel to S/ ρ give for ductile materials, steel, aluminum alloys, nickel alloys, titanium, and composites.
Common to both stiffness and strength are steel, titanium, aluminum alloys, and composites. Ans.
2-35 See Prob. 1-13 solution for (^) x = 122.9 kcycles and sx = 30.3 kcycles. Also, in that solution
it is observed that the number of instances less than 115 kcycles predicted by the normal distribution is 27; whereas, the data indicates the number to be 31. From Eq. (1-4), the probability density function (PDF), with μ = x and σˆ^ = sx , is
(^2 ) 1 1 1 1 122. ( ) exp exp x^2 2 x 30.3^22 30.
x x x f x s π s π
The discrete PDF is given by f /( Nw ), where N = 69 and w = 10 kcycles. From the Eq. (1) and the data of Prob. 1-13, the following plots are obtained.