
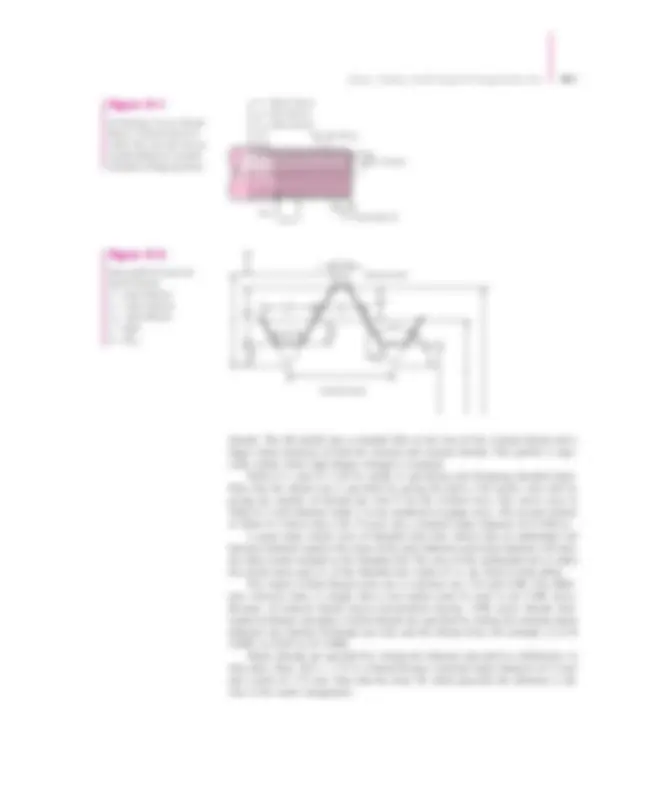
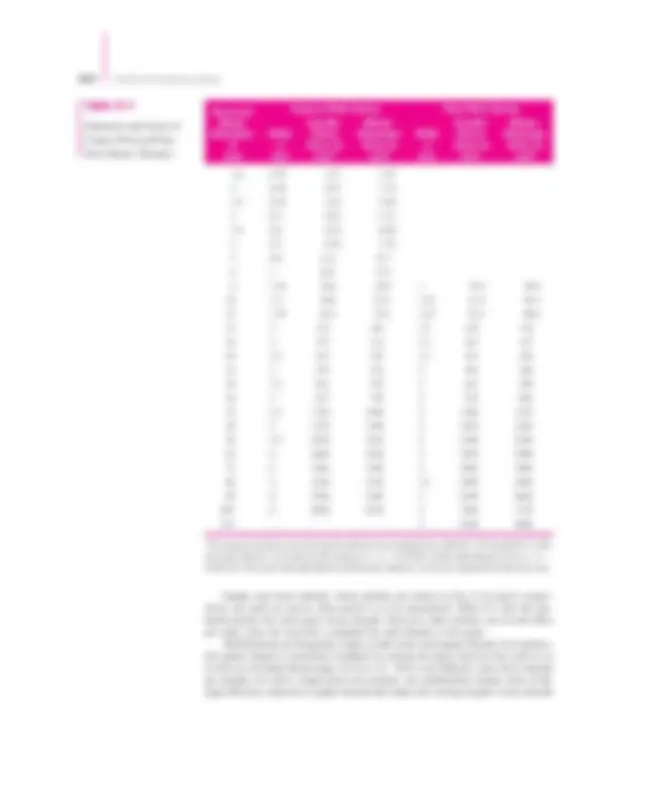
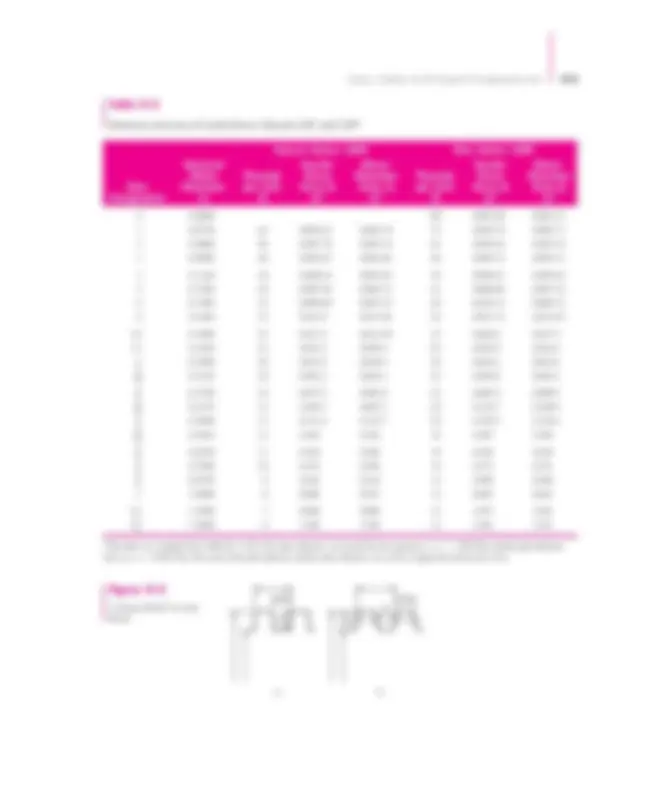
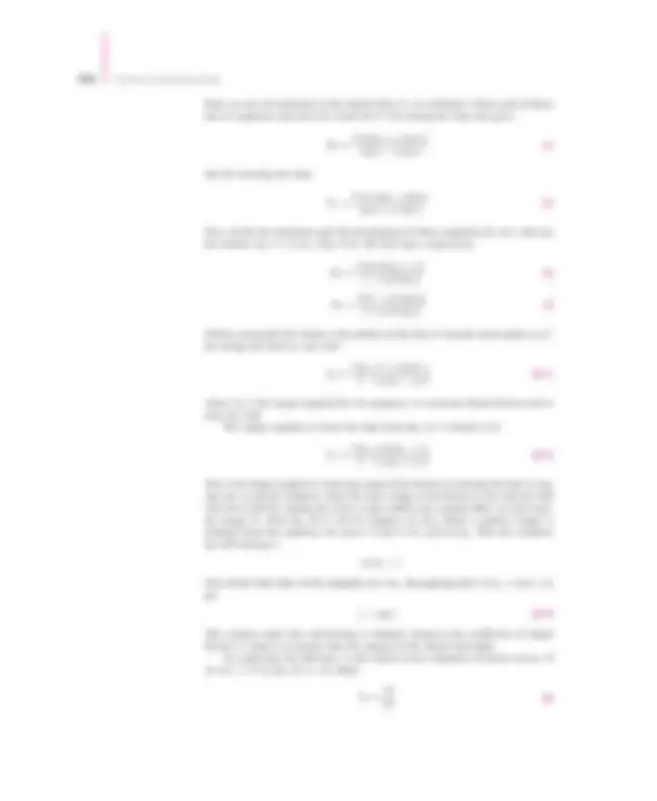
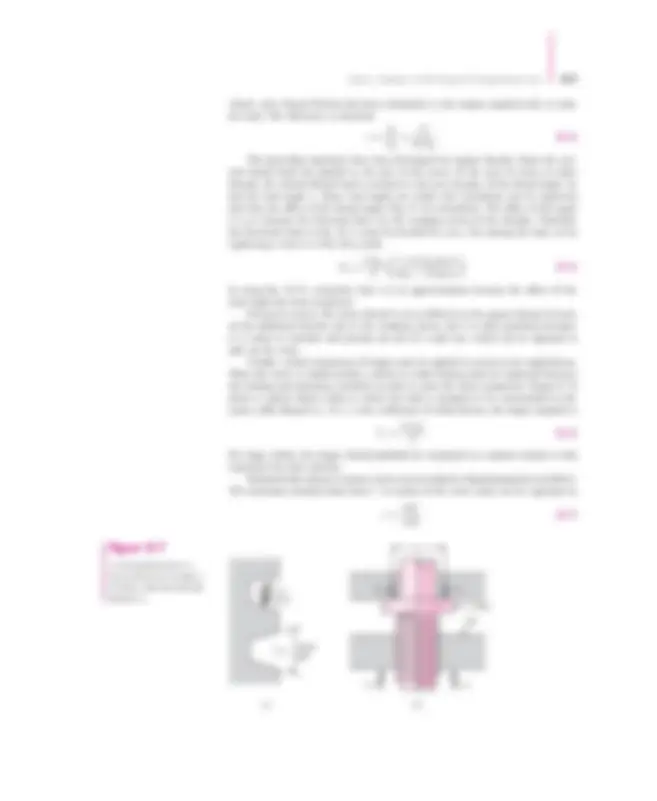
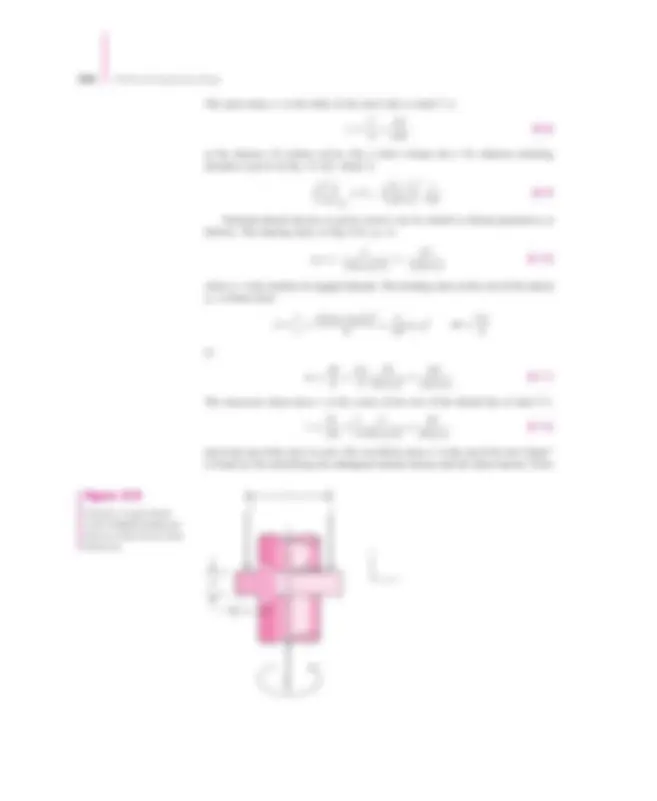
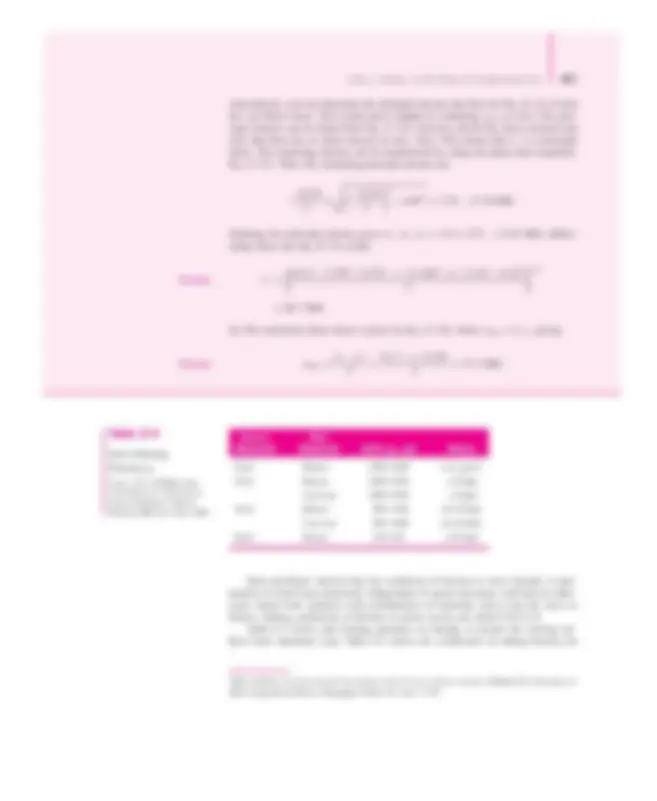
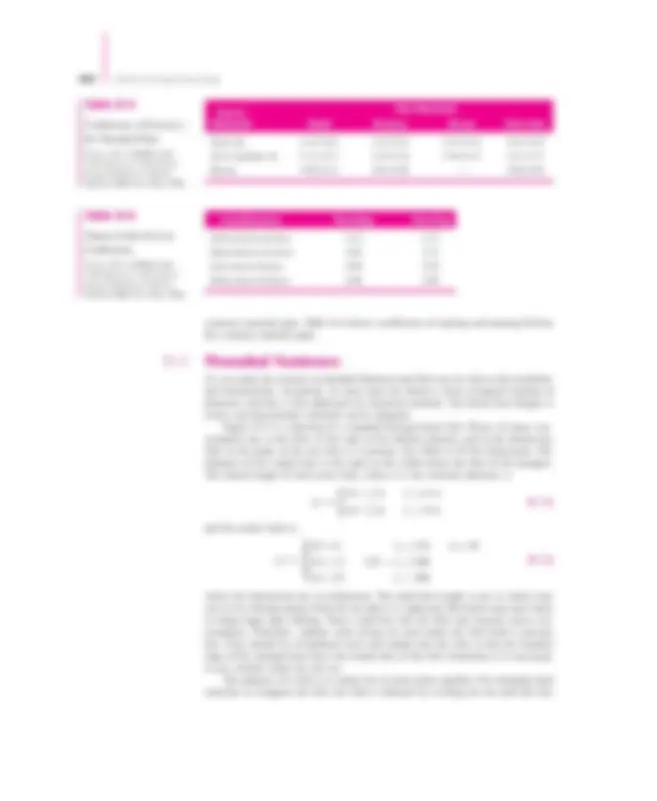
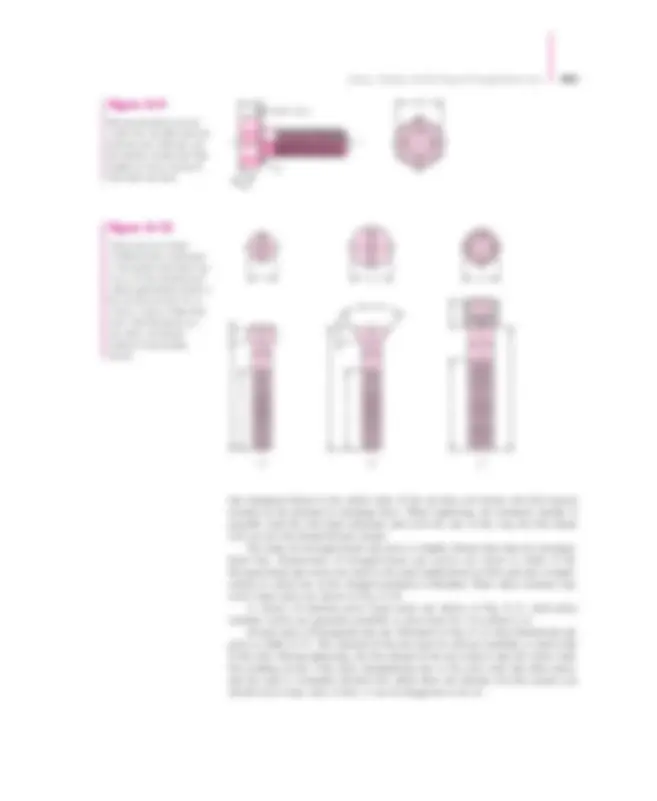
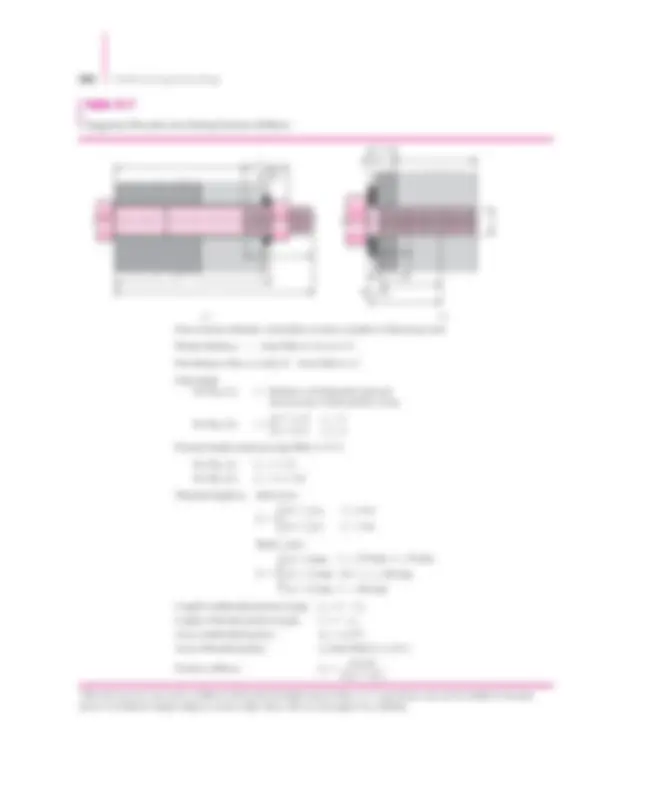
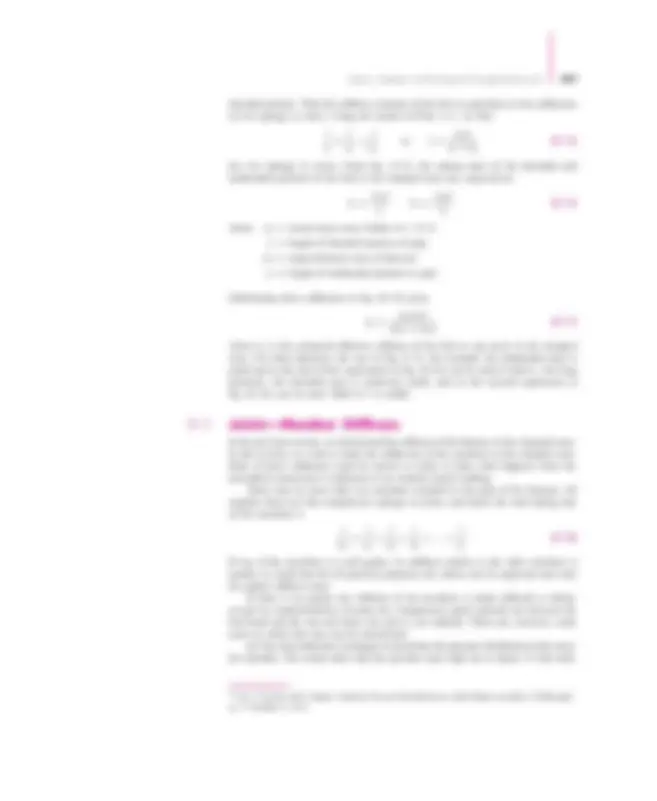
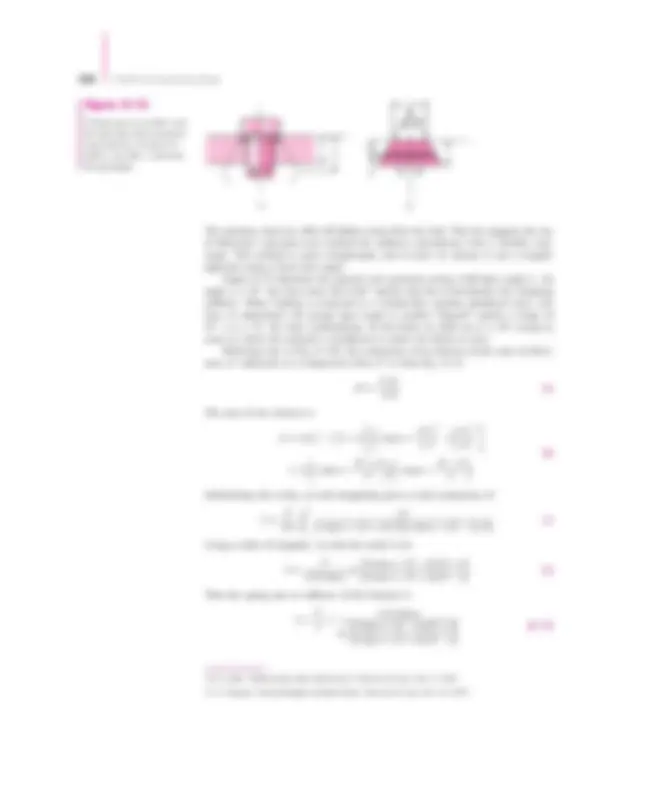
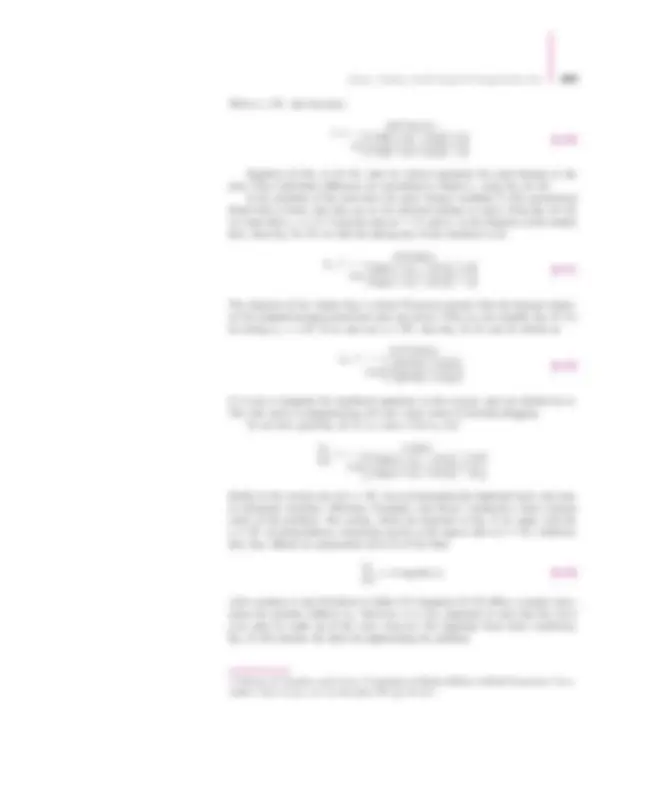
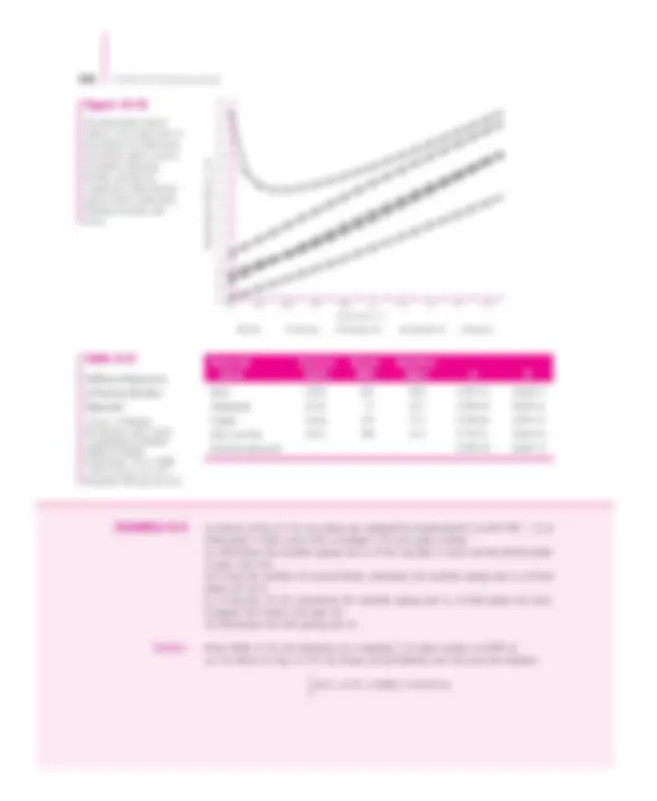
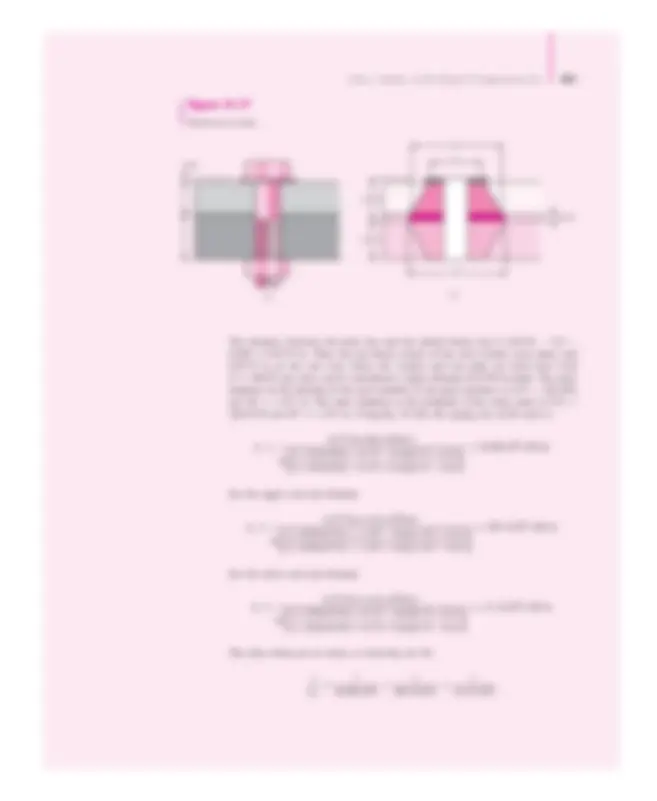
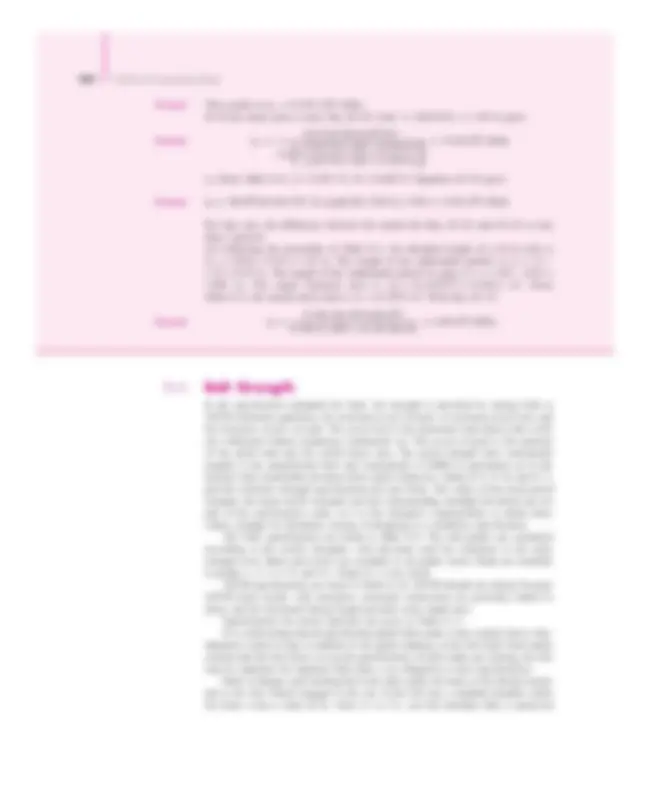
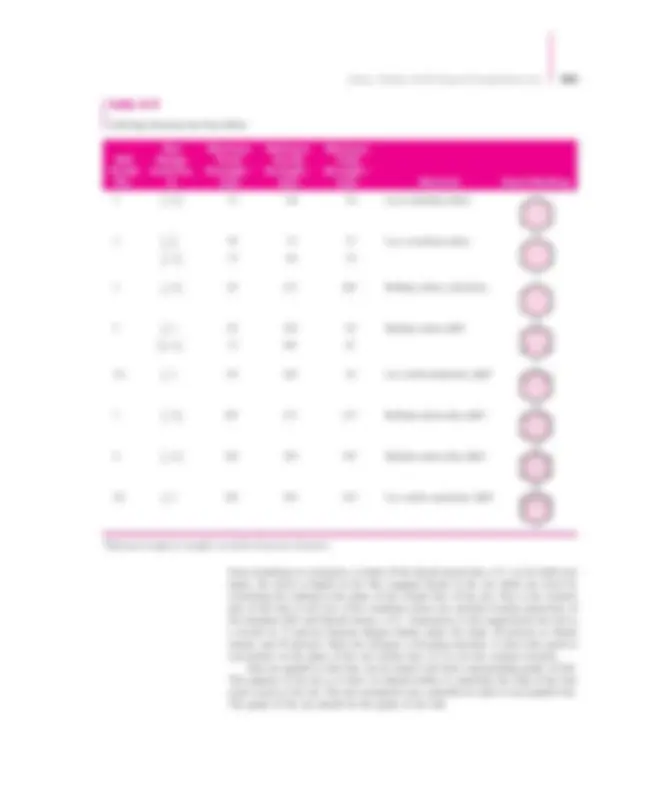
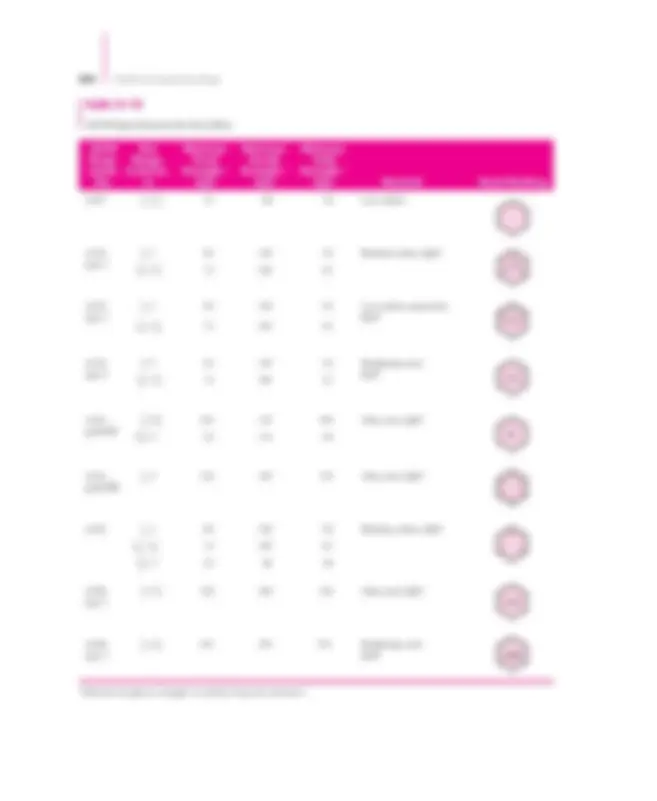
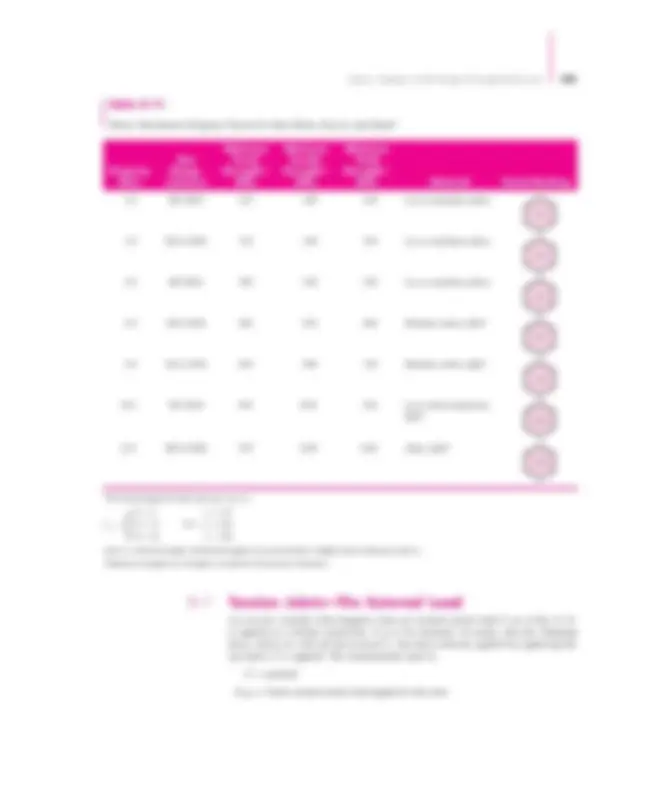
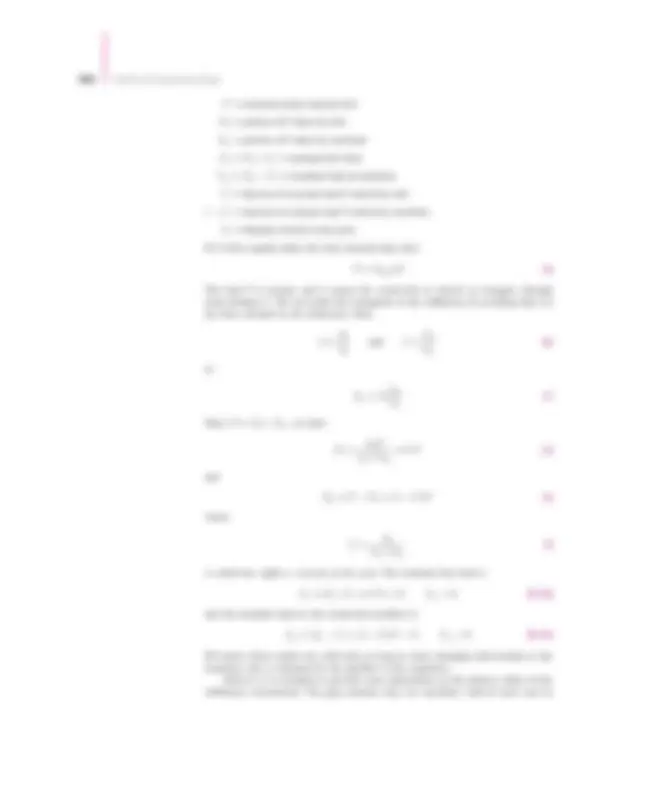
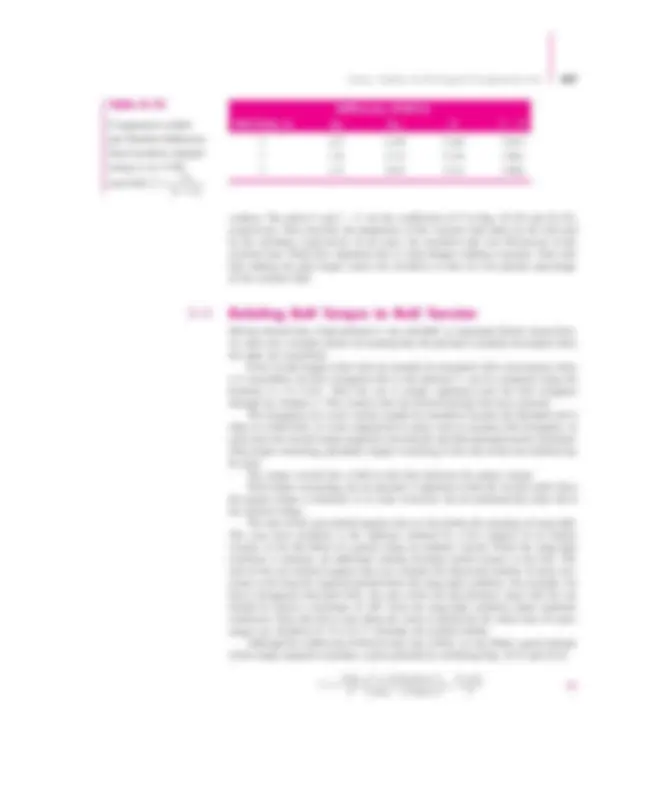
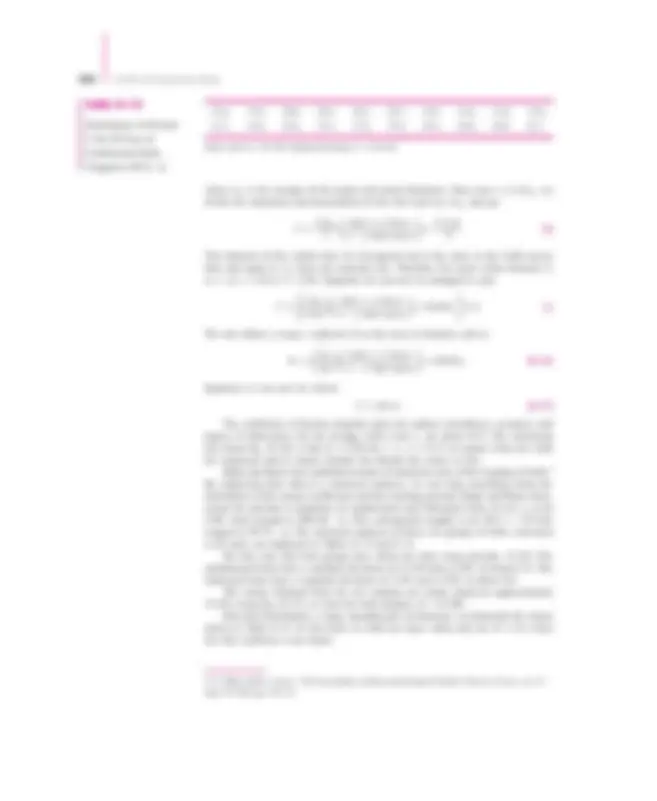
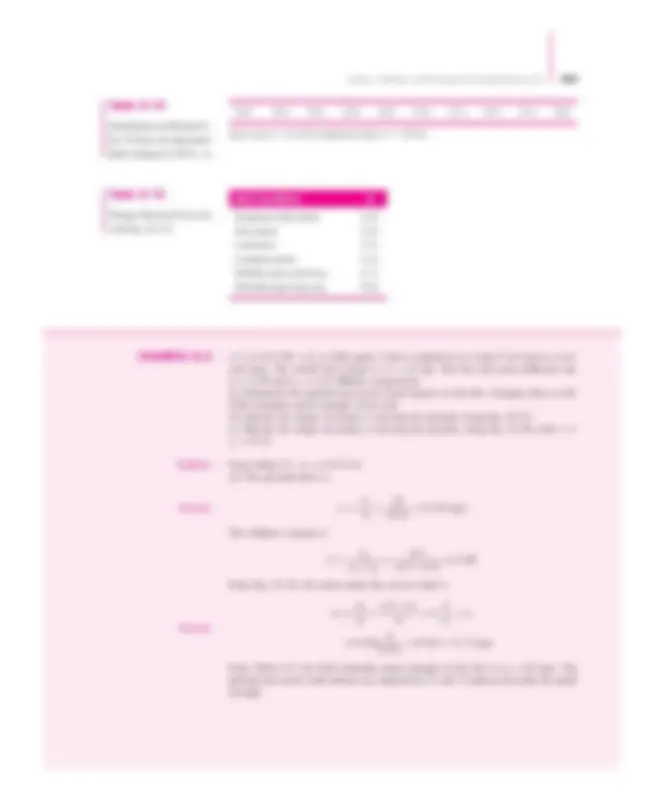
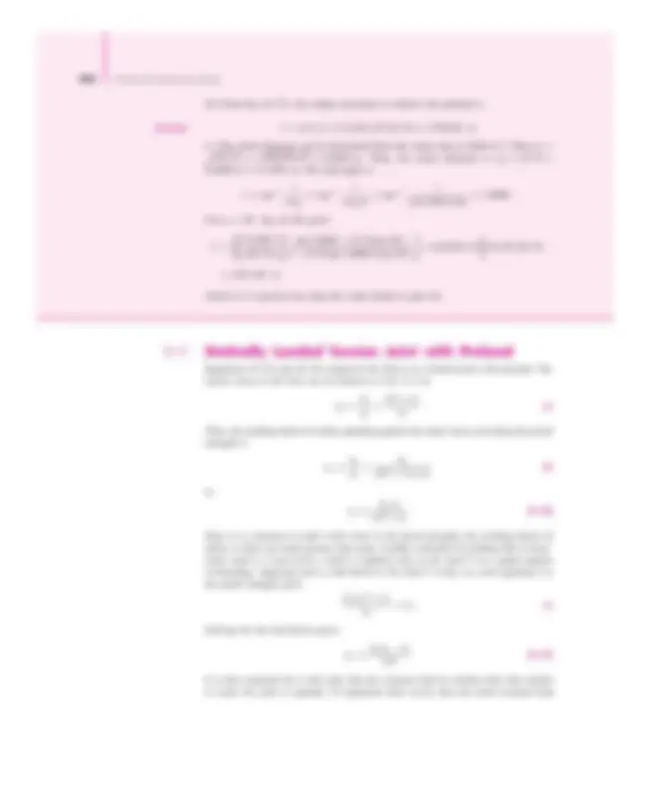
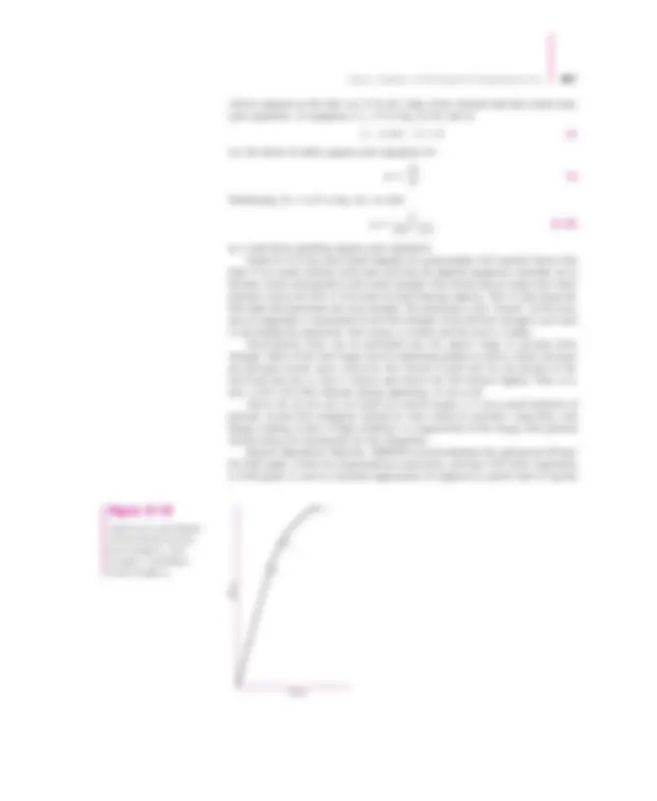
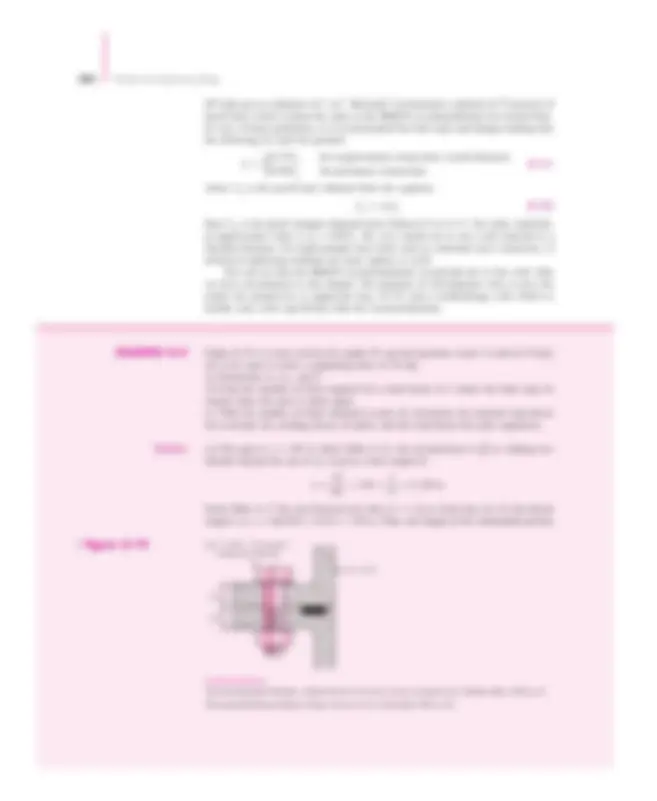
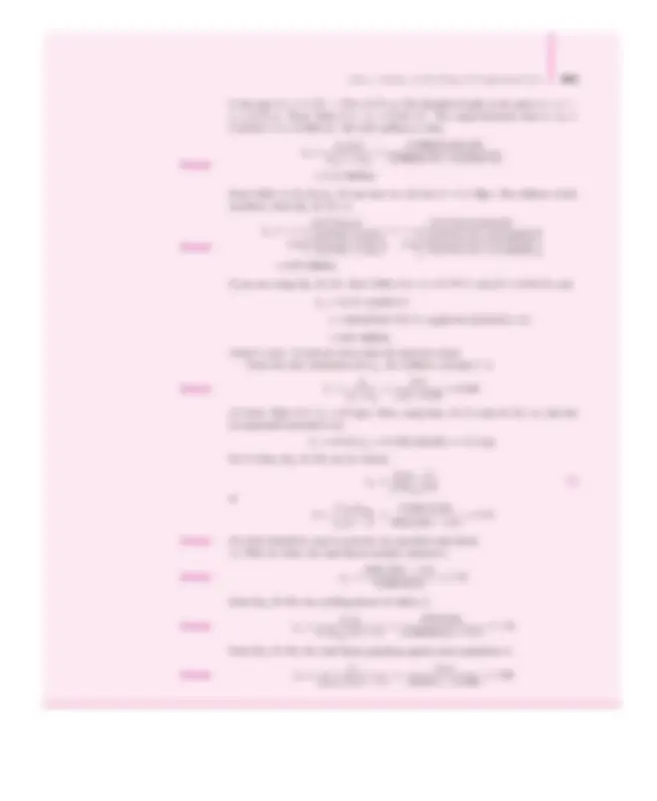
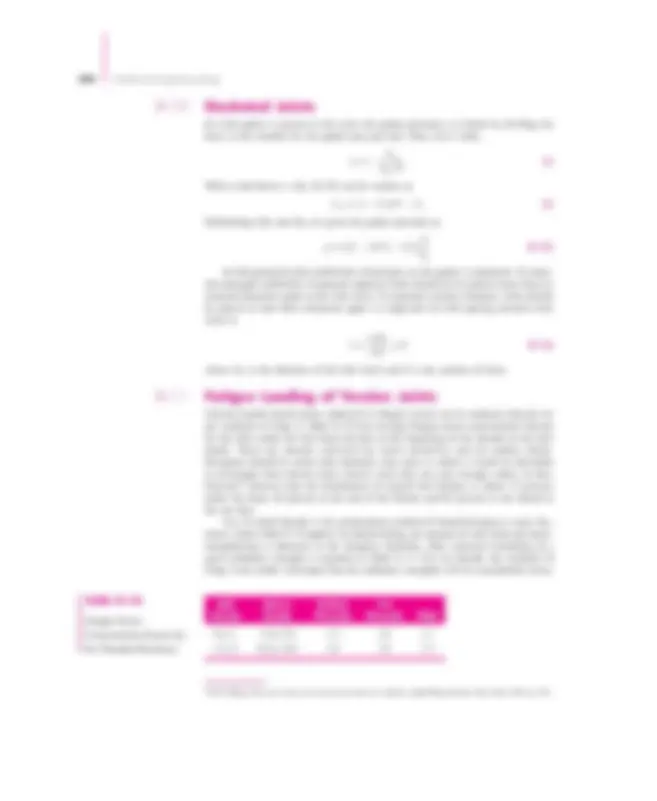
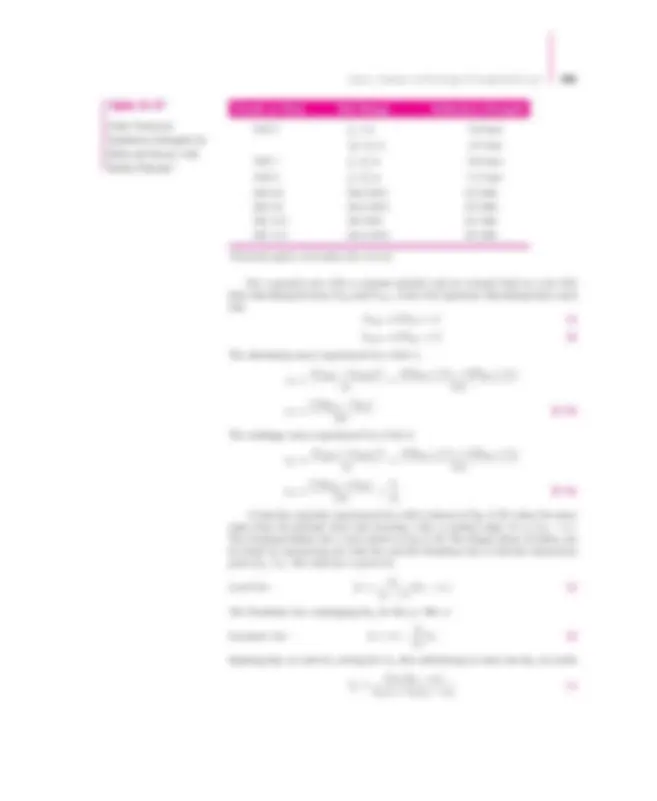
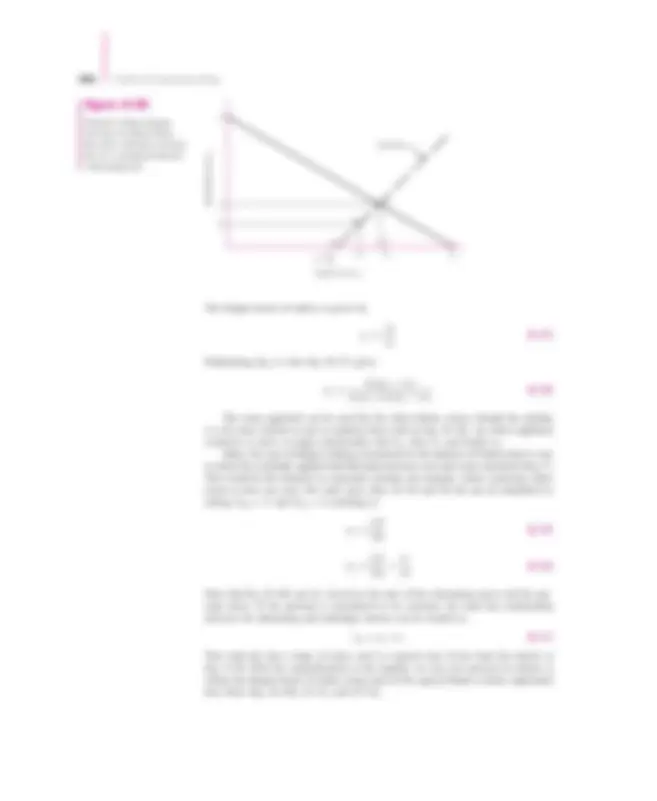
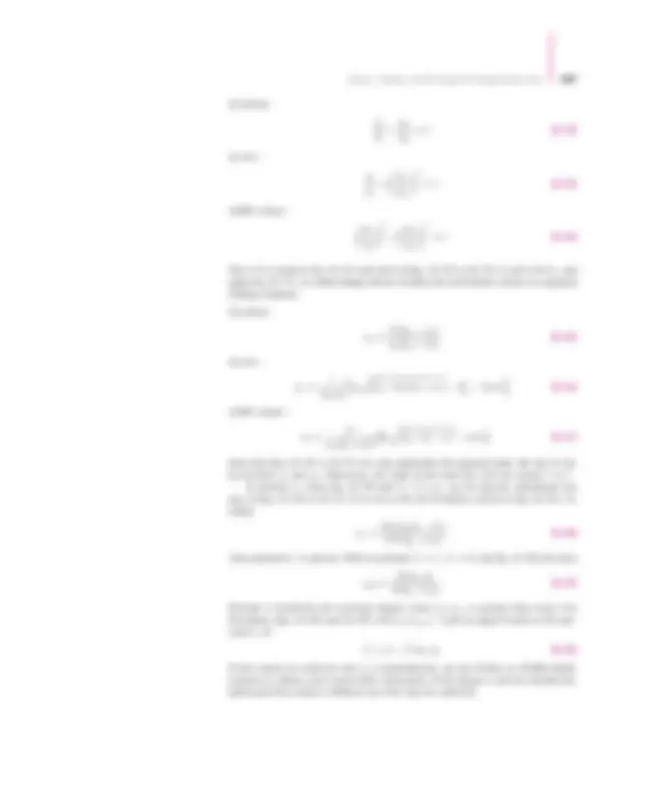
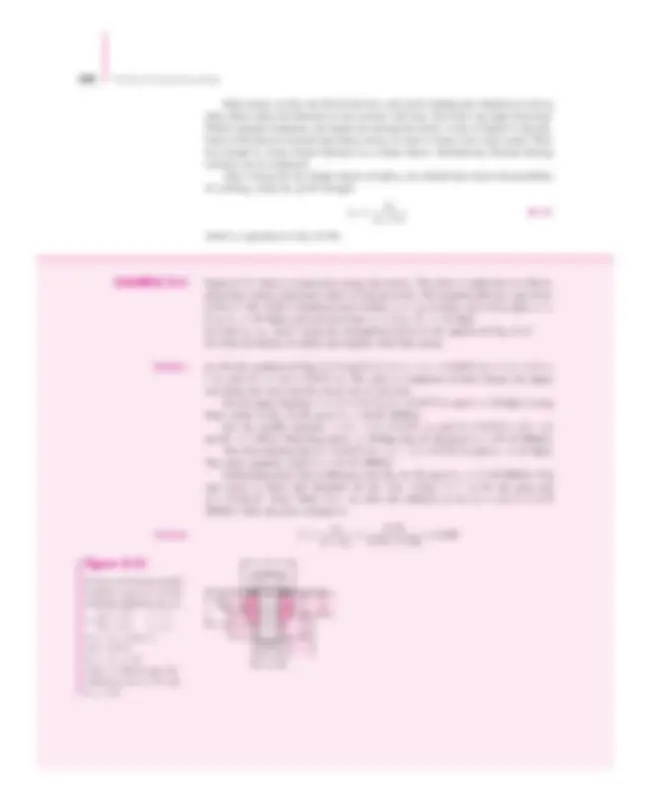
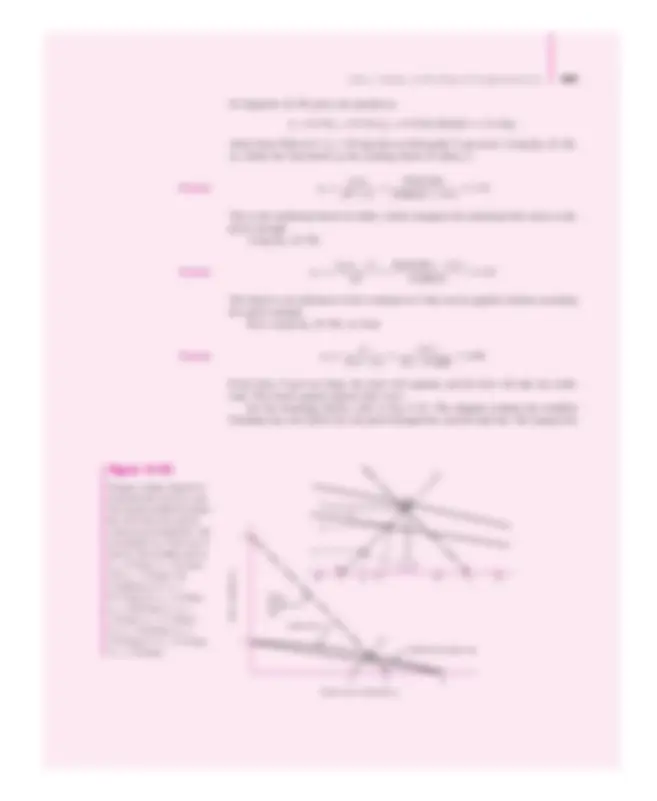
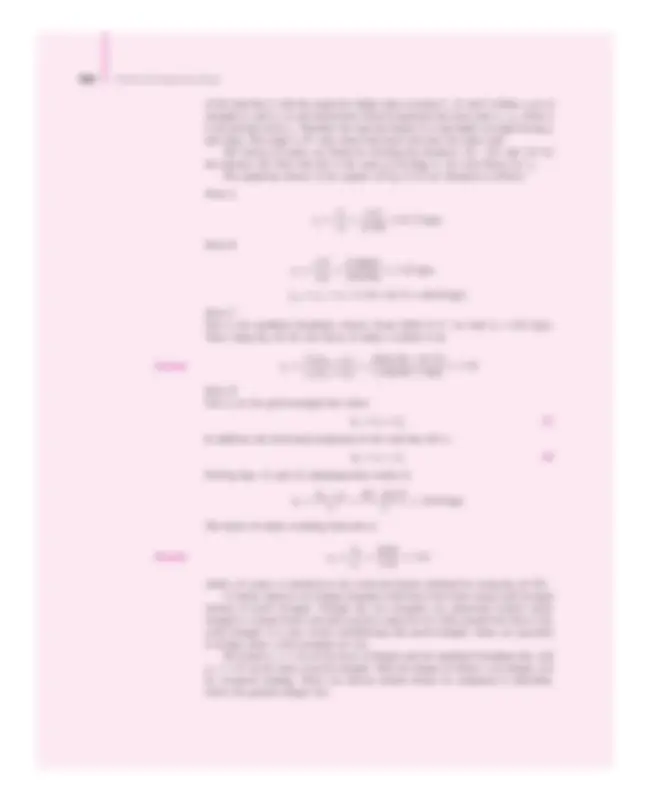
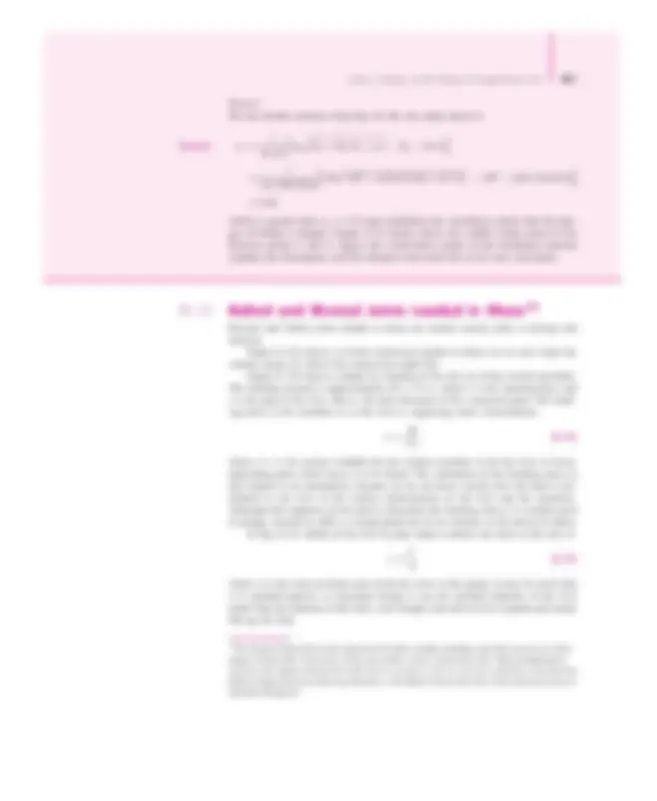
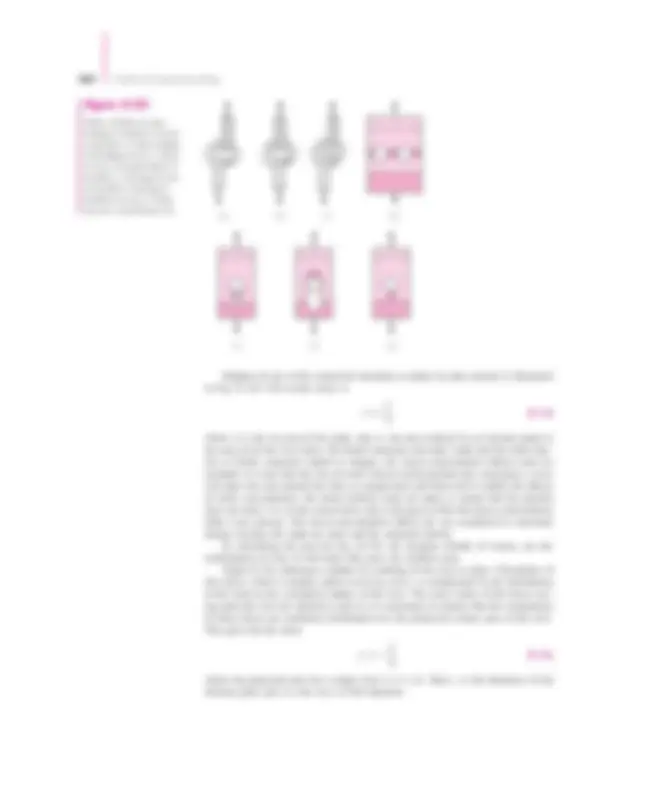
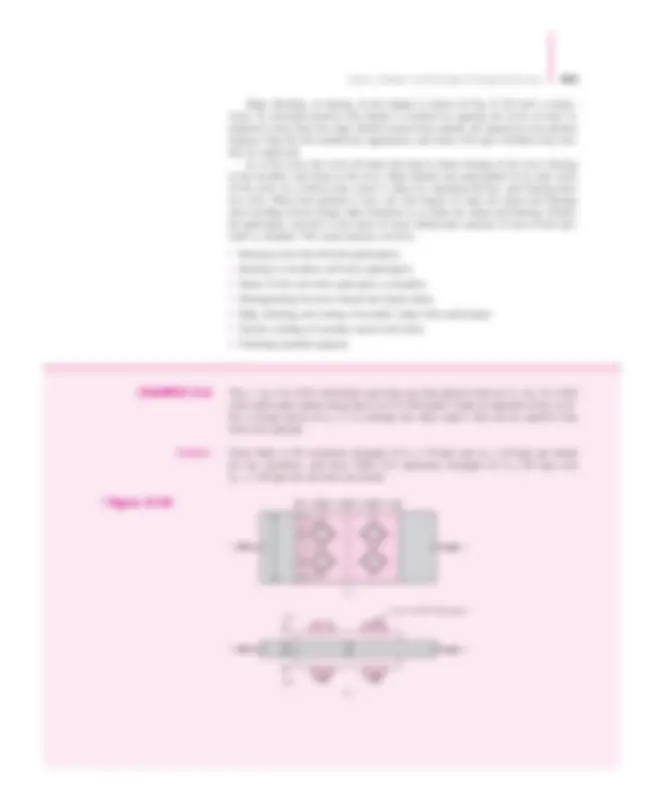
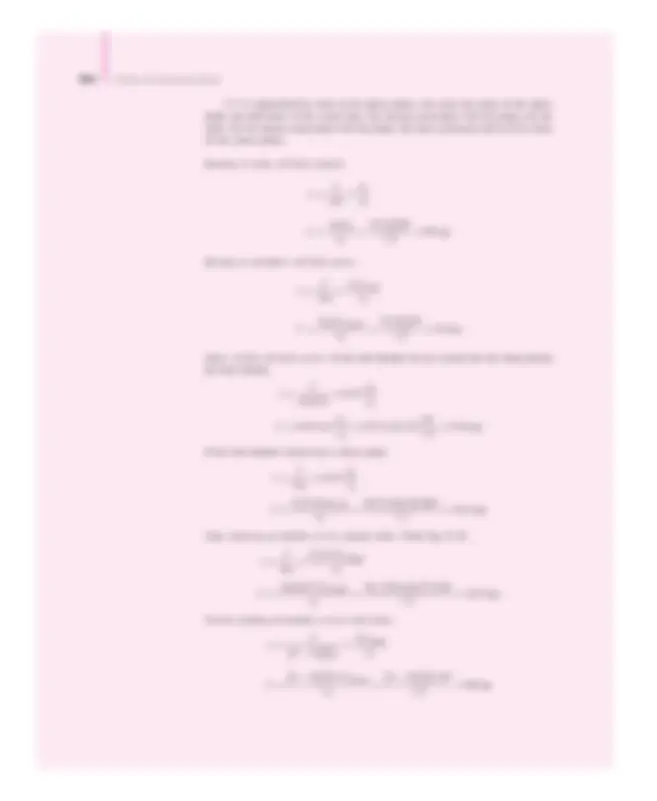
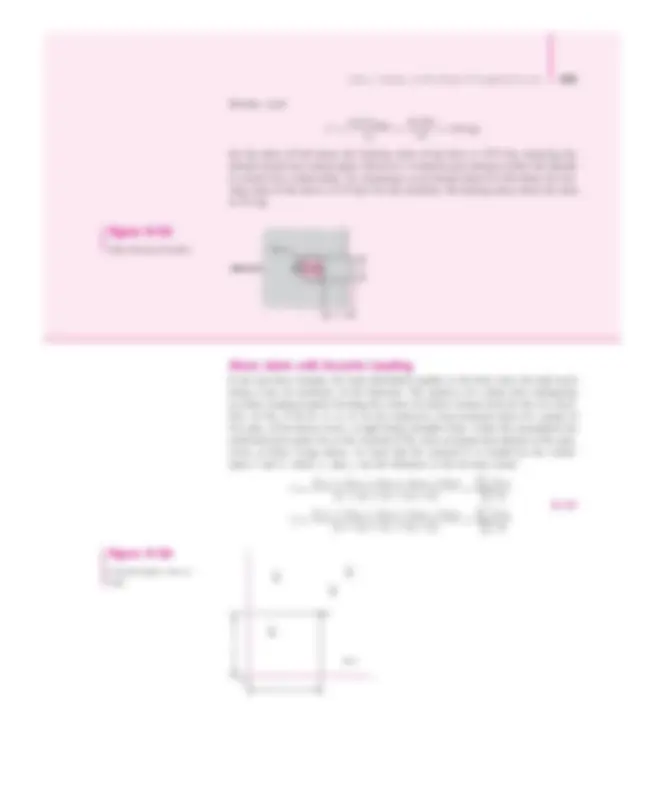
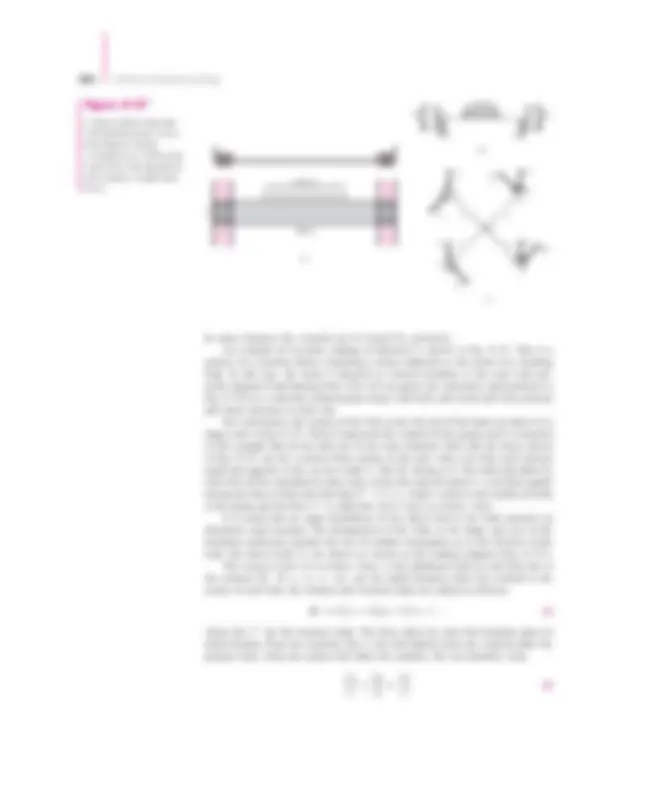
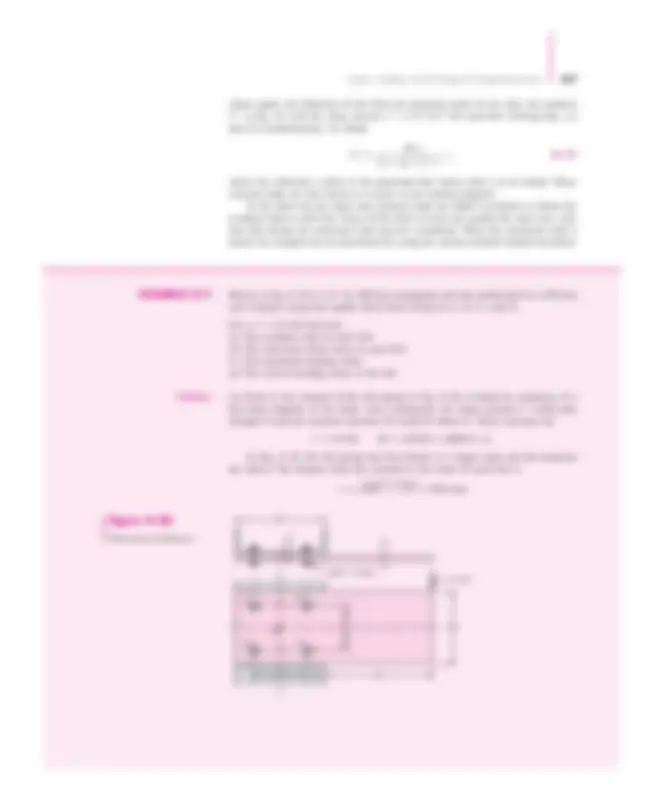
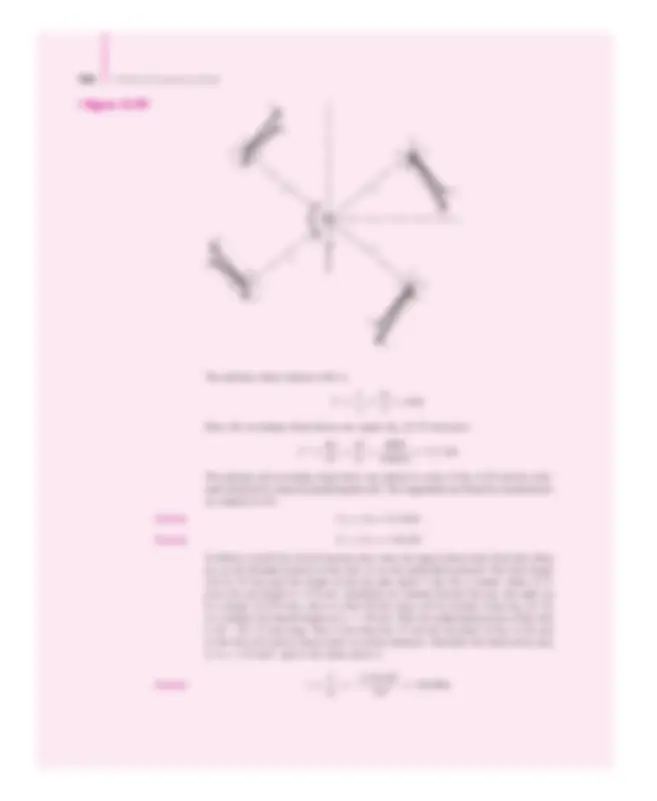
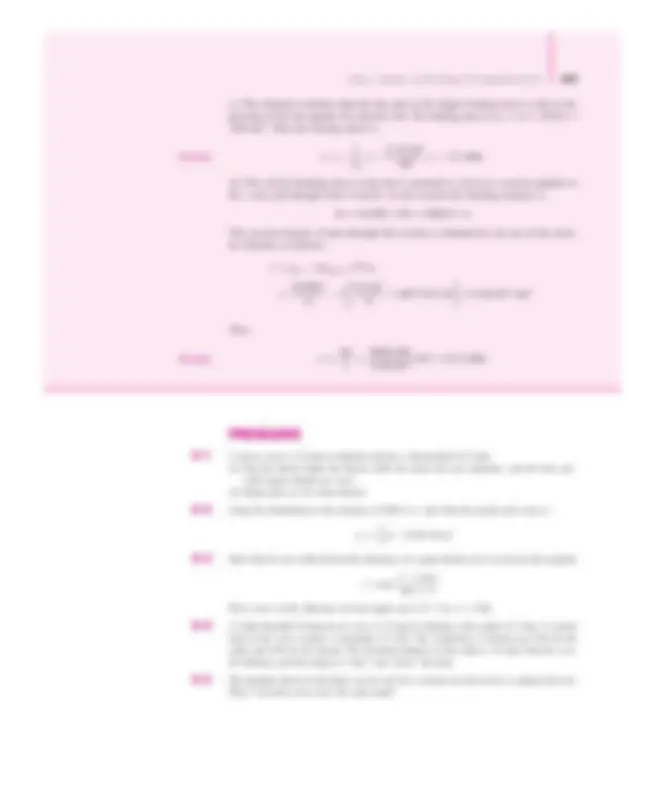
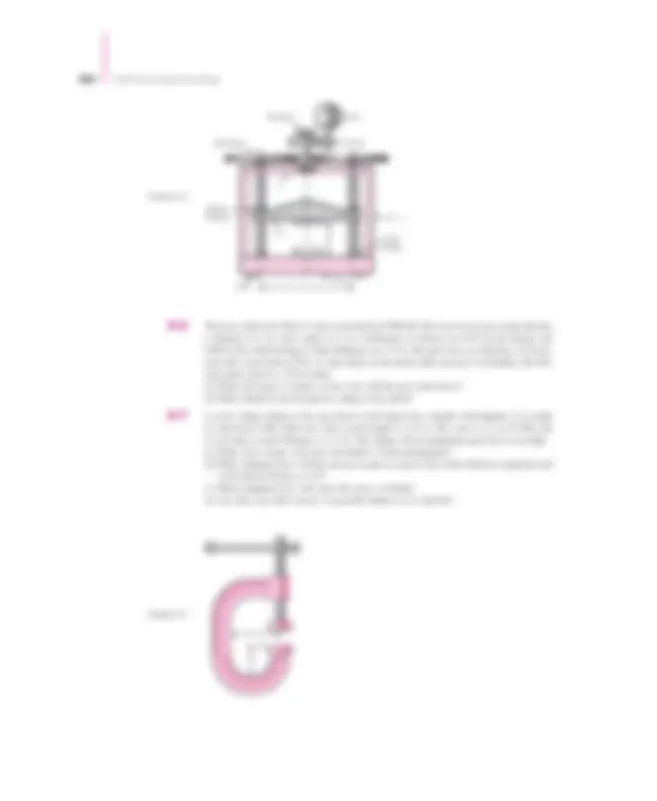
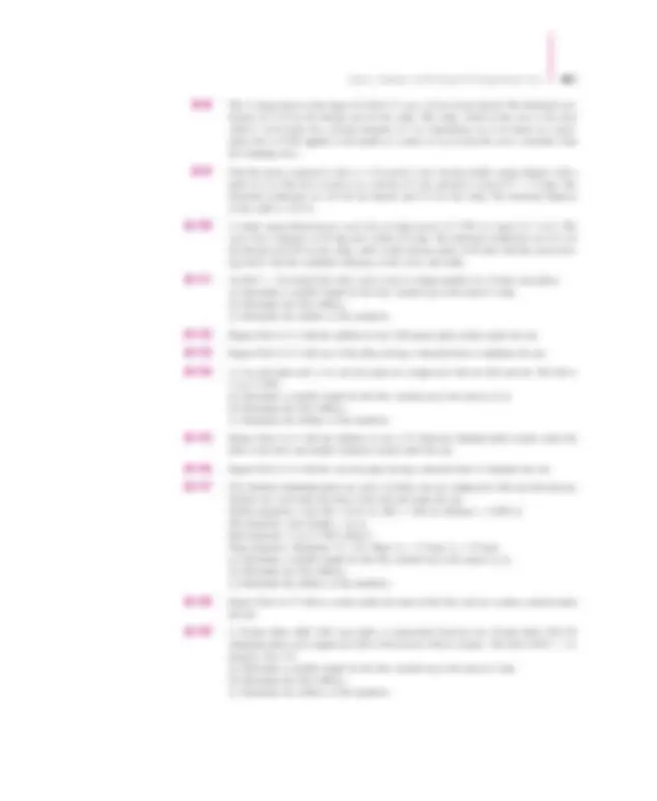
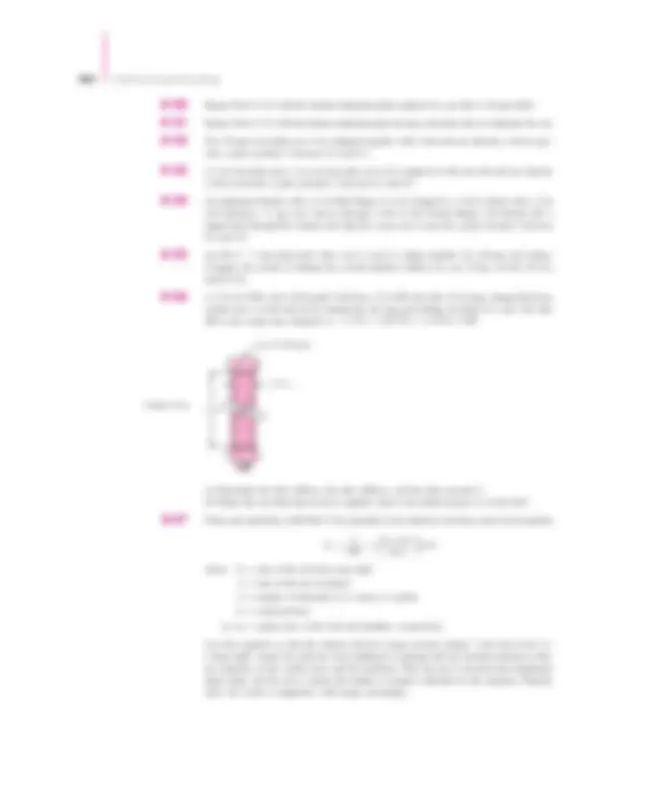
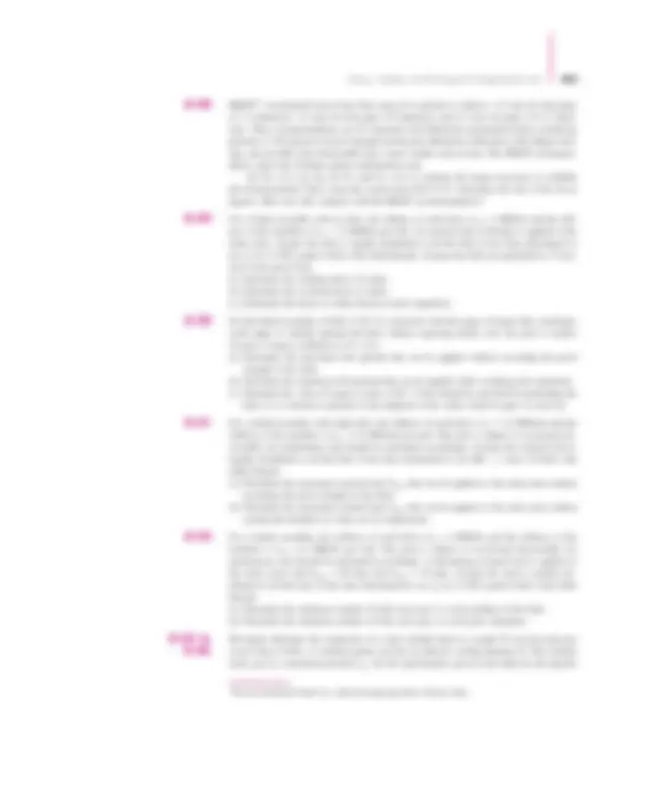
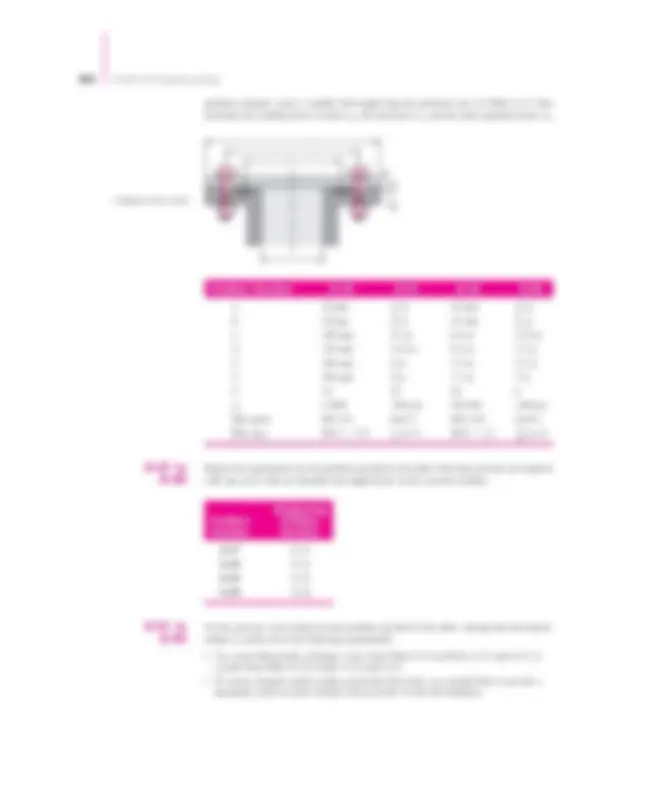
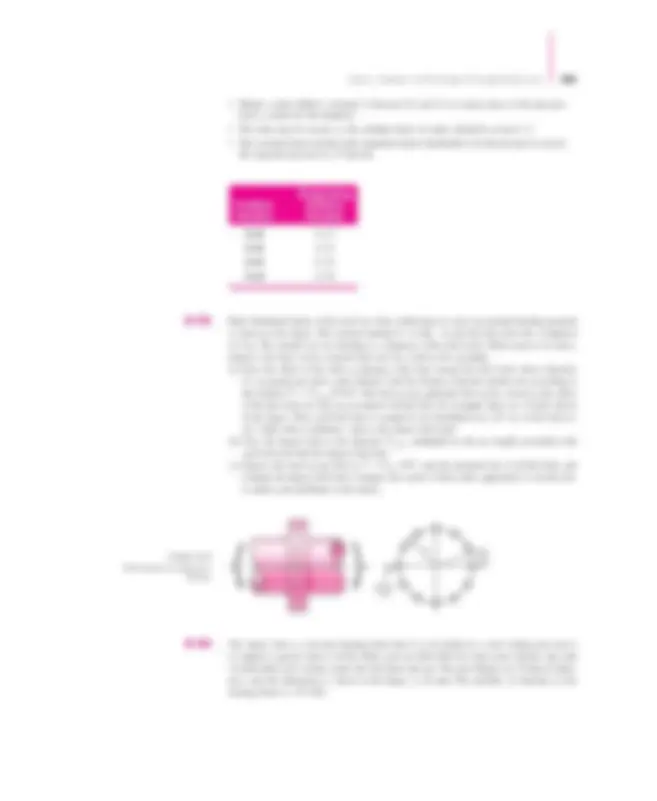
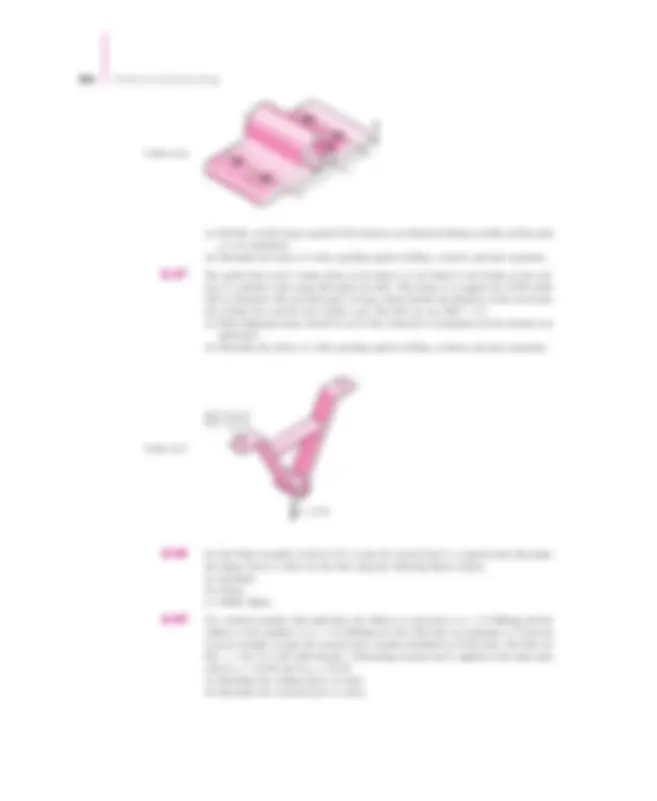
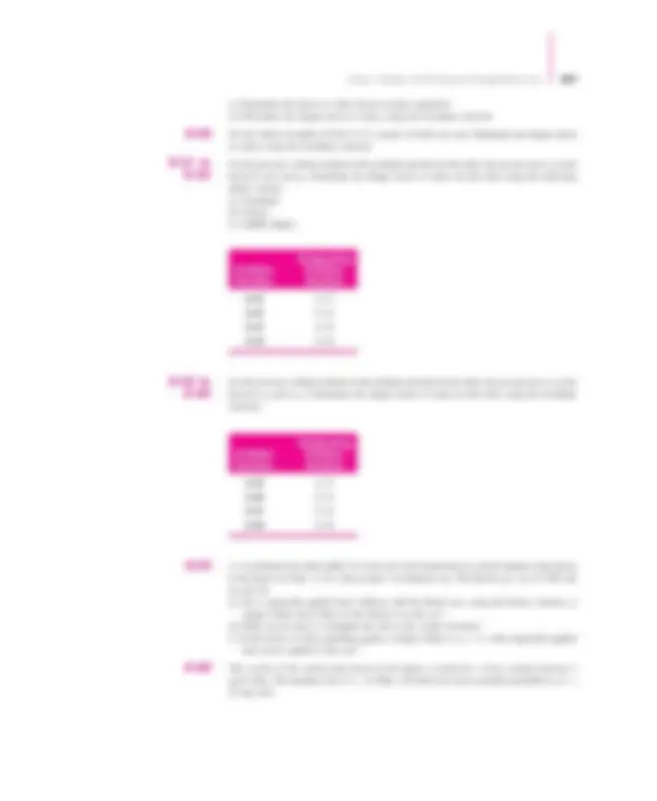
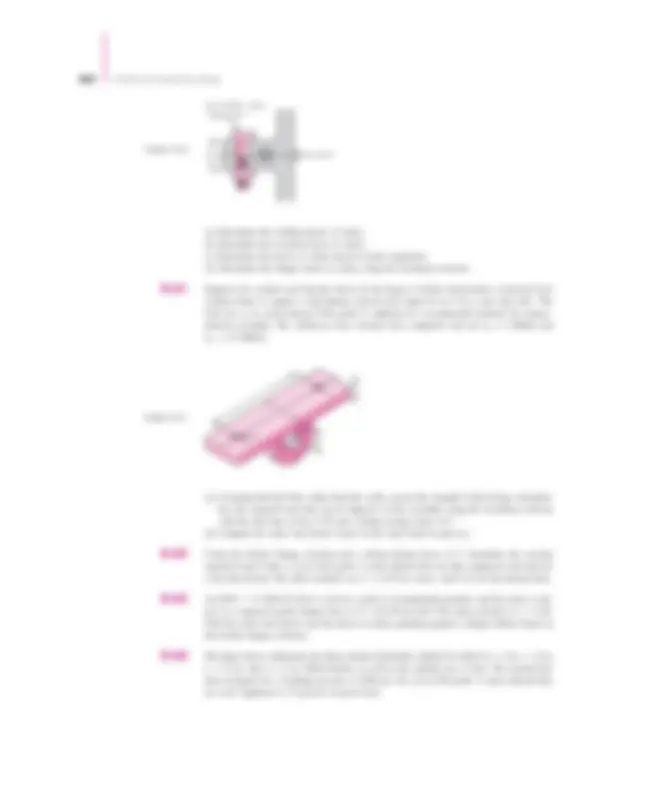
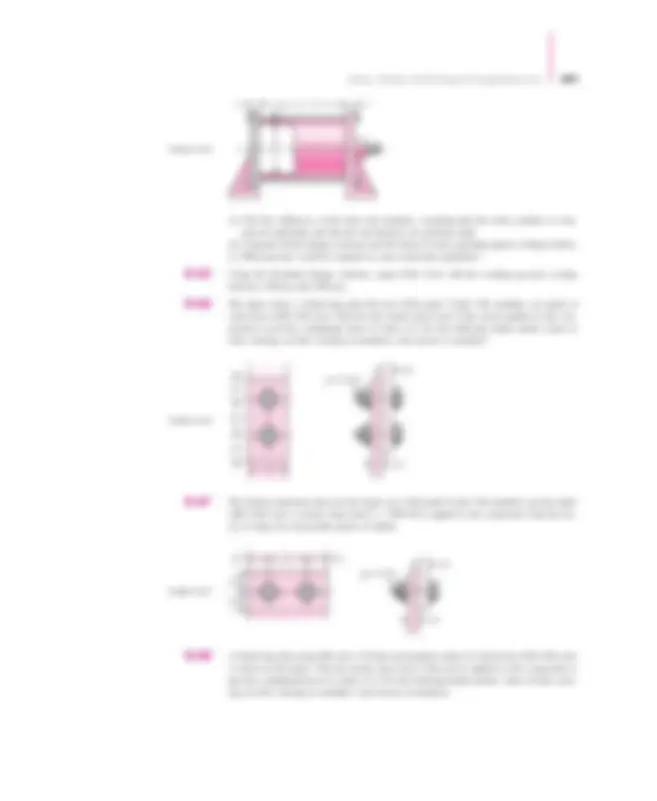
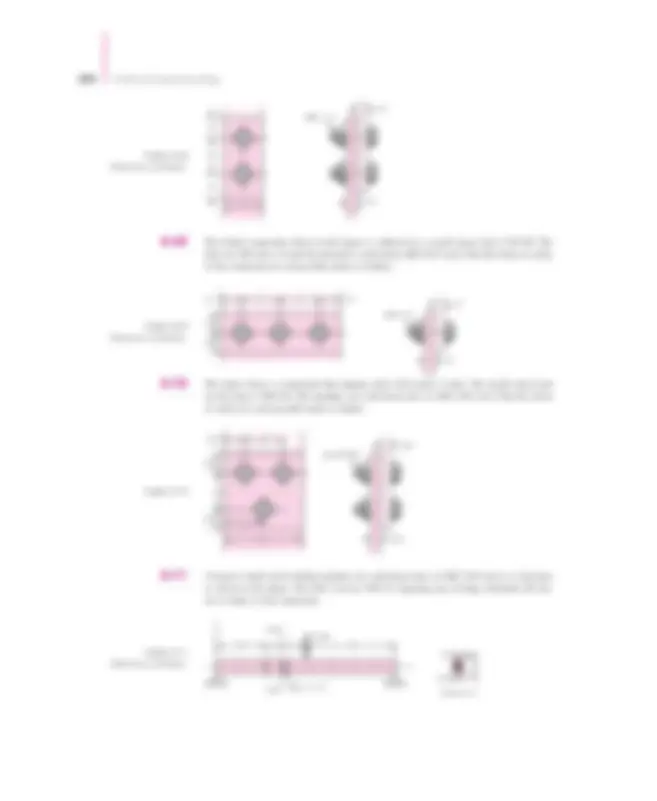
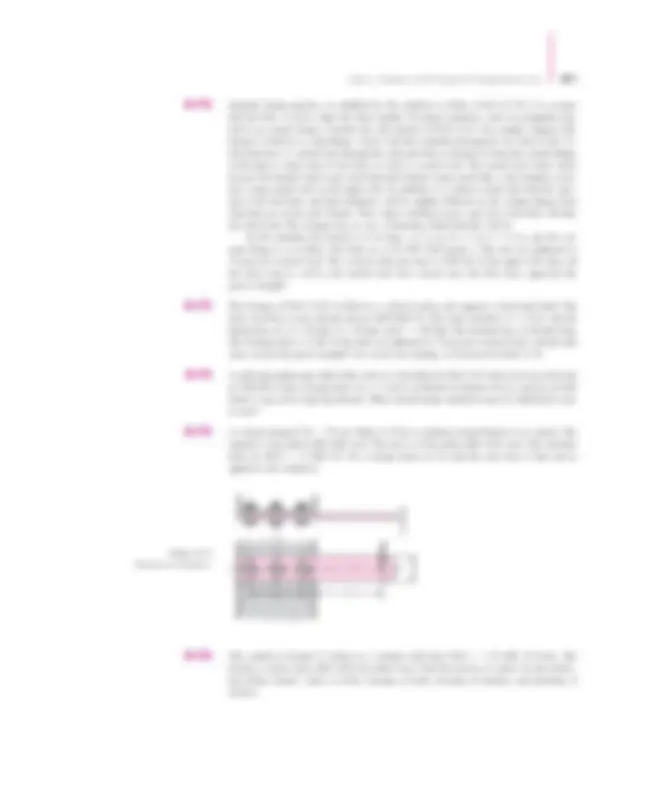
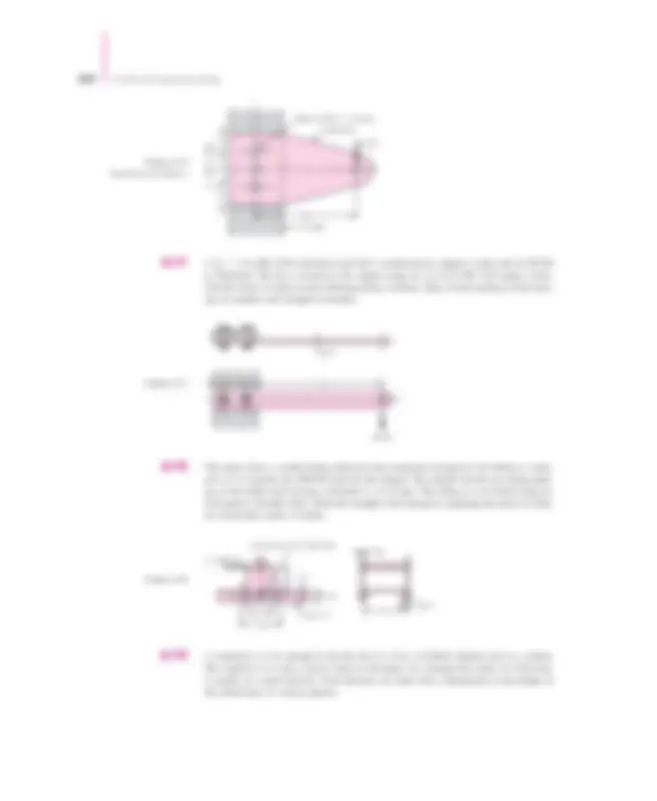

Study with the several resources on Docsity
Earn points by helping other students or get them with a premium plan
Prepare for your exams
Study with the several resources on Docsity
Earn points to download
Earn points by helping other students or get them with a premium plan
Community
Ask the community for help and clear up your study doubts
Discover the best universities in your country according to Docsity users
Free resources
Download our free guides on studying techniques, anxiety management strategies, and thesis advice from Docsity tutors
Lecture notes in Mechanical Engineering focused on the Screws, Fasteners, and the Design of Nonpermanent Joints | Shigley’s Mechanical Engineering Design Ch.8
Typology: Lecture notes
1 / 65
This page cannot be seen from the preview
Don't miss anything!
Chapter Outline 8–1 Thread Standards and Definitions 410 8–2 The Mechanics of Power Screws 414 8–3 Threaded Fasteners 422 8–4 Joints—Fastener Stiffness 424 8–5 Joints—Member Stiffness 427 8–6 Bolt Strength 432 8–7 Tension Joints—The External Load 435 8–8 Relating Bolt Torque to Bolt Tension 437 8–9 Statically Loaded Tension Joint with Preload 440
8–10 Gasketed Joints 444
8–11 Fatigue Loading of Tension Joints 444
8–12 Bolted and Riveted Joints Loaded in Shear 451
409
410 Mechanical Engineering Design
The helical-thread screw was undoubtably an extremely important mechanical inven- tion. It is the basis of power screws, which change angular motion to linear motion to transmit power or to develop large forces (presses, jacks, etc.), and threaded fas- teners, an important element in nonpermanent joints. This book presupposes a knowledge of the elementary methods of fastening. Typ- ical methods of fastening or joining parts use such devices as bolts, nuts, cap screws, setscrews, rivets, spring retainers, locking devices, pins, keys, welds, and adhesives. Studies in engineering graphics and in metal processes often include instruction on var- ious joining methods, and the curiosity of any person interested in mechanical engi- neering naturally results in the acquisition of a good background knowledge of fasten- ing methods. Contrary to first impressions, the subject is one of the most interesting in the entire field of mechanical design. One of the key targets of current design for manufacture is to reduce the number of fasteners. However, there will always be a need for fasteners to facilitate disas- sembly for whatever purposes. For example, jumbo jets such as Boeing’s 747 require as many as 2.5 million fasteners, some of which cost several dollars apiece. To keep costs down, aircraft manufacturers, and their subcontractors, constantly review new fastener designs, installation techniques, and tooling. The number of innovations in the fastener field over any period you might care to mention has been tremendous. An overwhelming variety of fasteners are available for the designer’s selection. Serious designers generally keep specific notebooks on fasteners alone. Methods of joining parts are extremely important in the engineering of a quality design, and it is necessary to have a thorough understanding of the per- formance of fasteners and joints under all conditions of use and design.
The terminology of screw threads, illustrated in Fig. 8–1, is explained as follows: The pitch is the distance between adjacent thread forms measured parallel to the thread axis. The pitch in U.S. units is the reciprocal of the number of thread forms per inch N. The major diameter d is the largest diameter of a screw thread. The minor ( or root) diameter dr is the smallest diameter of a screw thread. The pitch diameter d (^) p is a theoretical diameter between the major and minor diameters. The lead l , not shown, is the distance the nut moves parallel to the screw axis when the nut is given one turn. For a single thread, as in Fig. 8–1, the lead is the same as the pitch. A multiple-threaded product is one having two or more threads cut beside each other (imagine two or more strings wound side by side around a pencil). Standard- ized products such as screws, bolts, and nuts all have single threads; a double-threaded screw has a lead equal to twice the pitch, a triple-threaded screw has a lead equal to 3 times the pitch, and so on. All threads are made according to the right-hand rule unless otherwise noted. That is, if the bolt is turned clockwise, the bolt advances toward the nut. The American National (Unified) thread standard has been approved in this coun- try and in Great Britain for use on all standard threaded products. The thread angle is 60◦^ and the crests of the thread may be either flat or rounded. Figure 8–2 shows the thread geometry of the metric M and MJ profiles. The M profile replaces the inch class and is the basic ISO 68 profile with 60◦^ symmetric
412 Mechanical Engineering Design
Nominal Coarse-Pitch Series^ Fine-Pitch Series Major Tensile- Minor- Tensile- Minor- Diameter Pitch Stress Diameter Pitch Stress Diameter d p Area A (^) t Area A (^) r p Area A (^) t Area A (^) r mm mm mm^2 mm^2 mm mm^2 mm^2 1.6 0.35 1.27 1. 2 0.40 2.07 1. 2.5 0.45 3.39 2. 3 0.5 5.03 4. 3.5 0.6 6.78 6. 4 0.7 8.78 7. 5 0.8 14.2 12. 6 1 20.1 17. 8 1.25 36.6 32.8 1 39.2 36. 10 1.5 58.0 52.3 1.25 61.2 56. 12 1.75 84.3 76.3 1.25 92.1 86. 14 2 115 104 1.5 125 116 16 2 157 144 1.5 167 157 20 2.5 245 225 1.5 272 259 24 3 353 324 2 384 365 30 3.5 561 519 2 621 596 36 4 817 759 2 915 884 42 4.5 1120 1050 2 1260 1230 48 5 1470 1380 2 1670 1630 56 5.5 2030 1910 2 2300 2250 64 6 2680 2520 2 3030 2980 72 6 3460 3280 2 3860 3800 80 6 4340 4140 1.5 4850 4800 90 6 5590 5360 2 6100 6020 100 6 6990 6740 2 7560 7470 110 2 9180 9080
*The equations and data used to develop this table have been obtained from ANSI B1.1-1974 and B18.3.1-1978. The minor diameter was found from the equation dr = d −1.226 869 p , and the pitch diameter from dp = d − 0.649 519 p. The mean of the pitch diameter and the minor diameter was used to compute the tensile-stress area.
Table 8–
Diameters and Areas of Coarse-Pitch and Fine- Pitch Metric Threads.*
Square and Acme threads, whose profiles are shown in Fig. 8–3 a and b , respec- tively, are used on screws when power is to be transmitted. Table 8–3 lists the pre- ferred pitches for inch-series Acme threads. However, other pitches can be and often are used, since the need for a standard for such threads is not great. Modifications are frequently made to both Acme and square threads. For instance, the square thread is sometimes modified by cutting the space between the teeth so as to have an included thread angle of 10 to 15◦. This is not difficult, since these threads are usually cut with a single-point tool anyhow; the modification retains most of the high efficiency inherent in square threads and makes the cutting simpler. Acme threads
Screws, Fasteners, and the Design of Nonpermanent Joints 413
p p 2
p
p 2
p 2
d dr
d dr
p 2 29 °
( a ) ( b )
Figure 8– ( a ) Square thread; ( b ) Acme thread.
Coarse Series—UNC Fine Series—UNF Nominal Tensile- Minor- Tensile- Minor- Major Threads Stress Diameter Threads Stress Diameter Size Diameter per Inch Area At Area Ar per Inch Area At Area Ar Designation in N in^2 in^2 N in^2 in^2 0 0.0600 80 0.001 80 0.001 51 1 0.0730 64 0.002 63 0.002 18 72 0.002 78 0.002 37 2 0.0860 56 0.003 70 0.003 10 64 0.003 94 0.003 39 3 0.0990 48 0.004 87 0.004 06 56 0.005 23 0.004 51 4 0.1120 40 0.006 04 0.004 96 48 0.006 61 0.005 66 5 0.1250 40 0.007 96 0.006 72 44 0.008 80 0.007 16 6 0.1380 32 0.009 09 0.007 45 40 0.010 15 0.008 74 8 0.1640 32 0.014 0 0.011 96 36 0.014 74 0.012 85 10 0.1900 24 0.017 5 0.014 50 32 0.020 0 0.017 5 12 0.2160 24 0.024 2 0.020 6 28 0.025 8 0.022 6 1 4 0.2500^20 0.031 8^ 0.026 9^28 0.036 4^ 0.032 6 5 16 0.3125^18 0.052 4^ 0.045 4^24 0.058 0^ 0.052 4 3 8 0.3750^16 0.077 5^ 0.067 8^24 0.087 8^ 0.080 9 7 16 0.4375^14 0.106 3^ 0.093 3^20 0.118 7^ 0.109 0 1 2 0.5000^13 0.141 9^ 0.125 7^20 0.159 9^ 0.148 6 9 16 0.5625^12 0.182^ 0.162^18 0.203^ 0. 5 8 0.6250^11 0.226^ 0.202^18 0.256^ 0. 3 4 0.7500^10 0.334^ 0.302^16 0.373^ 0. 7 8 0.8750^9 0.462^ 0.419^14 0.509^ 0. 1 1.0000 8 0.606 0.551 12 0.663 0. 1 14 1.2500 7 0.969 0.890 12 1.073 1. 1 12 1.5000 6 1.405 1.294 12 1.581 1.
*This table was compiled from ANSI B1.1-1974. The minor diameter was found from the equation d (^) r = d − 1.299 038 p , and the pitch diameter from dp = d − 0.649 519 p. The mean of the pitch diameter and the minor diameter was used to compute the tensile-stress area.
Table 8–
Diameters and Area of Unified Screw Threads UNC and UNF*
Screws, Fasteners, and the Design of Nonpermanent Joints 415
F ⁄ 2
p
F
F ⁄ 2
Nut
dm
Figure 8–
Portion of a power screw.
dm
l
F
P (^) R f N
N
dm ( a ) ( b )
l
F
f N (^) P L N
y
x
y
x
Figure 8–
Force diagrams: ( a ) lifting the load; ( b ) lowering the load.
In Fig. 8–5 a square-threaded power screw with single thread having a mean diameter dm , a pitch p , a lead angle λ, and a helix angle ψ is loaded by the axial compressive force F. We wish to find an expression for the torque required to raise this load, and another expression for the torque required to lower the load. First, imagine that a single thread of the screw is unrolled or developed (Fig. 8–6) for exactly a single turn. Then one edge of the thread will form the hypotenuse of a right triangle whose base is the circumference of the mean-thread-diameter circle and whose height is the lead. The angle λ, in Figs. 8–5 and 8–6, is the lead angle of the thread. We represent the summation of all the axial forces acting upon the normal thread area by F. To raise the load, a force PR acts to the right (Fig. 8–6 a ), and to lower the load, PL acts to the left (Fig. 8–6 b ). The friction force is the product of the coefficient of friction f with the normal force N , and acts to oppose the motion. The system is in equilibrium under the action of these forces, and hence, for raising the load, we have ∑ Fx = PR − N sin λ − f N cos λ = 0 ∑ ( a ) Fy = − F − f N sin λ + N cos λ = 0
In a similar manner, for lowering the load, we have ∑ Fx = − PL − N sin λ + f N cos λ = 0 ∑ ( b ) Fy = − F + f N sin λ + N cos λ = 0
416 Mechanical Engineering Design
Since we are not interested in the normal force N , we eliminate it from each of these sets of equations and solve the result for P. For raising the load, this gives
F (sin λ + f cos λ) cos λ − f sin λ
( c )
and for lowering the load,
F ( f cos λ − sin λ) cos λ + f sin λ
( d )
Next, divide the numerator and the denominator of these equations by cos λ and use the relation tan λ = l /π dm (Fig. 8–6). We then have, respectively,
F [( l /π dm ) + f ] 1 − ( f l /π dm )
( e )
F [ f − ( l /π dm )] 1 + ( f l /π dm )
( f )
Finally, noting that the torque is the product of the force P and the mean radius dm /2, for raising the load we can write
Fdm 2
l + π f dm π dm − f l
(8–1)
where T (^) R is the torque required for two purposes: to overcome thread friction and to raise the load. The torque required to lower the load, from Eq. ( f ), is found to be
Fdm 2
π f dm − l π dm + f l
(8–2)
This is the torque required to overcome a part of the friction in lowering the load. It may turn out, in specific instances where the lead is large or the friction is low, that the load will lower itself by causing the screw to spin without any external effort. In such cases, the torque TL from Eq. (8–2) will be negative or zero. When a positive torque is obtained from this equation, the screw is said to be self-locking. Thus the condition for self-locking is
π f dm > l
Now divide both sides of this inequality by π dm. Recognizing that l /π dm = tan λ, we get
f > tan λ (8–3)
This relation states that self-locking is obtained whenever the coefficient of thread friction is equal to or greater than the tangent of the thread lead angle. An expression for efficiency is also useful in the evaluation of power screws. If we let f = 0 in Eq. (8–1), we obtain
Fl 2 π
( g )
418 Mechanical Engineering Design
dm
Ff
F
y
x
F
T
p /
p /
Figure 8– Geometry of square thread useful in finding bending and transverse shear stresses at the thread root.
The axial stress σ in the body of the screw due to load F is
σ =
π d r^2
(8–8)
in the absence of column action. For a short column the J. B. Johnson buckling formula is given by Eq. (4–43), which is ( F A
crit
= S (^) y −
S (^) y 2 π
l k
(8–9)
Nominal thread stresses in power screws can be related to thread parameters as follows. The bearing stress in Fig. 8–8, σ B , is
σ B = −
π dm n (^) t p / 2
π dm n (^) t p
(8–10)
where n (^) t is the number of engaged threads. The bending stress at the root of the thread σ b is found from
c
(π dr n (^) t ) ( p / 2 )^2 6
π 24
dr n (^) t p^2 M =
F p 4
so
σ b =
F p 4
π dr n (^) t p^2
π dr n (^) t p
(8–11)
The transverse shear stress τ at the center of the root of the thread due to load F is
τ =
π dr n (^) t p / 2
π dr n (^) t p
(8–12)
and at the top of the root it is zero. The von Mises stress σ ′^ at the top of the root “plane” is found by first identifying the orthogonal normal stresses and the shear stresses. From
Screws, Fasteners, and the Design of Nonpermanent Joints 419
the coordinate system of Fig. 8–8, we note
σ x =
π dr n (^) t p
τ x y = 0
σ y = −
π d^2 r
τ yz =
π d r^3 σ z = 0 τ zx = 0
then use Eq. (5–14) of Sec. 5–5. The screw-thread form is complicated from an analysis viewpoint. Remember the origin of the tensile-stress area A (^) t , which comes from experiment. A power screw lift- ing a load is in compression and its thread pitch is shortened by elastic deformation. Its engaging nut is in tension and its thread pitch is lengthened. The engaged threads cannot share the load equally. Some experiments show that the first engaged thread carries 0.38 of the load, the second 0.25, the third 0.18, and the seventh is free of load. In estimating thread stresses by the equations above, substituting 0. 38 F for F and set- ting n (^) t to 1 will give the largest level of stresses in the thread-nut combination.
EXAMPLE 8–1 A square-thread power screw has a major diameter of 32 mm and a pitch of 4 mm with double threads, and it is to be used in an application similar to that in Fig. 8–4. The given data include f = f (^) c = 0 .08, dc = 40 mm, and F = 6 .4 kN per screw. ( a ) Find the thread depth, thread width, pitch diameter, minor diameter, and lead. ( b ) Find the torque required to raise and lower the load. ( c ) Find the efficiency during lifting the load. ( d ) Find the body stresses, torsional and compressive. ( e ) Find the bearing stress. ( f ) Find the thread bending stress at the root of the thread. ( g ) Determine the von Mises stress at the root of the thread. ( h ) Determine the maximum shear stress at the root of the thread.
Solution ( a ) From Fig. 8–3 a the thread depth and width are the same and equal to half the pitch, or 2 mm. Also dm = d − p / 2 = 32 − 4 / 2 = 30 mm
Answer dr = d − p = 32 − 4 = 28 mm l = np = 2 ( 4 ) = 8 mm
( b ) Using Eqs. (8–1) and (8–6), the torque required to turn the screw against the load is
Fdm 2
l + π f dm π dm − f l
F f (^) c dc 2
8 + π( 0. 08 )( 30 ) π( 30 ) − 0. 08 ( 8 )
Answer = 15. 94 + 10. 24 = 26 .18 N · m
Screws, Fasteners, and the Design of Nonpermanent Joints 421
Screw Nut Material Material Safe pb , psi Notes Steel Bronze 2500–3500 Low speed Steel Bronze 1600–2500 ≤10 fpm Cast iron 1800–2500 ≤8 fpm Steel Bronze 800–1400 20–40 fpm Cast iron 600–1000 20–40 fpm Steel Bronze 150–240 ≥50 fpm
Table 8–
Screw Bearing
Pressure pb
Source: H. A. Rothbart and T. H. Brown, Jr., Mechanical Design Handbook, 2nd ed., McGraw-Hill, New York, 2006.
Alternatively, you can determine the principal stresses and then use Eq. (5–12) to find the von Mises stress. This would prove helpful in evaluating τmax as well. The prin- cipal stresses can be found from Eq. (3–15); however, sketch the stress element and note that there are no shear stresses on the x face. This means that σ x is a principal stress. The remaining stresses can be transformed by using the plane stress equation, Eq. (3–13). Thus, the remaining principal stresses are
Ordering the principal stresses gives σ 1 , σ 2 , σ 3 = 41.5, 2.79, − 13 .18 MPa. Substi- tuting these into Eq. (5–12) yields
Answer σ ′^ =
= 48 .7 MPa
( h ) The maximum shear stress is given by Eq. (3–16), where τmax = τ 1 / 3 , giving
Answer τmax =
σ 1 − σ 3 2
= 27 .3 MPa
(^1) Ham and Ryan, An Experimental Investigation of the Friction of Screw-threads, Bulletin 247, University of Illinois Experiment Station, Champaign-Urbana, Ill., June 7, 1932.
Ham and Ryan 1 showed that the coefficient of friction in screw threads is inde- pendent of axial load, practically independent of speed, decreases with heavier lubri- cants, shows little variation with combinations of materials, and is best for steel on bronze. Sliding coefficients of friction in power screws are about 0.10–0.15. Table 8–4 shows safe bearing pressures on threads, to protect the moving sur- faces from abnormal wear. Table 8–5 shows the coefficients of sliding friction for
422 Mechanical Engineering Design
common material pairs. Table 8–6 shows coefficients of starting and running friction for common material pairs.
As you study the sections on threaded fasteners and their use, be alert to the stochastic and deterministic viewpoints. In most cases the threat is from overproof loading of fasteners, and this is best addressed by statistical methods. The threat from fatigue is lower, and deterministic methods can be adequate. Figure 8–9 is a drawing of a standard hexagon-head bolt. Points of stress con- centration are at the fillet, at the start of the threads (runout), and at the thread-root fillet in the plane of the nut when it is present. See Table A–29 for dimensions. The diameter of the washer face is the same as the width across the flats of the hexagon. The thread length of inch-series bolts, where d is the nominal diameter, is
2 d + 14 in L ≤ 6 in 2 d + 12 in L > 6 in
(8–13)
and for metric bolts is
2 d + 6 2 d + 12 125 < 2 d + 25
L ≤ 125 d ≤ 48 L ≤ 200 L > 200
(8–14)
where the dimensions are in millimeters. The ideal bolt length is one in which only one or two threads project from the nut after it is tightened. Bolt holes may have burrs or sharp edges after drilling. These could bite into the fillet and increase stress con- centration. Therefore, washers must always be used under the bolt head to prevent this. They should be of hardened steel and loaded onto the bolt so that the rounded edge of the stamped hole faces the washer face of the bolt. Sometimes it is necessary to use washers under the nut too. The purpose of a bolt is to clamp two or more parts together. The clamping load stretches or elongates the bolt; the load is obtained by twisting the nut until the bolt
Screw Nut Material Material Steel Bronze Brass Cast Iron Steel, dry 0.15–0.25 0.15–0.23 0.15–0.19 0.15–0. Steel, machine oil 0.11–0.17 0.10–0.16 0.10–0.15 0.11–0. Bronze 0.08–0.12 0.04–0.06 — 0.06–0.
Table 8–
Coefficients of Friction f for Threaded Pairs Source: H. A. Rothbart and T. H. Brown, Jr., Mechanical Design Handbook, 2nd ed., McGraw-Hill, New York, 2006.
Combination Running Starting Soft steel on cast iron 0.12 0. Hard steel on cast iron 0.09 0. Soft steel on bronze 0.08 0. Hard steel on bronze 0.06 0.
Table 8–
Thrust-Collar Friction Coefficients Source: H. A. Rothbart and T. H. Brown, Jr., Mechanical Design Handbook, 2nd ed., McGraw-Hill, New York, 2006.
424 Mechanical Engineering Design
A
H
D
L ( a ) Round head
A D
L H
A
( b ) Flat head
A
H
D
L ( c ) Fillister head
D
L
H
( d ) Oval head
A
H
D
L ( e ) Truss head
W H
D
L ( g ) Hex head (trimmed)
80 to 82
°
80 to 82
°
R
A (^) D
L ( f ) Binding head
5 ° ±^3 °
W H
D
L ( h ) Hex head (upset)
Figure 8– Types of heads used on machine screws.
30 30
Approx. in
W H
( a ) ( b ) ( c ) ( d ) ( e )
30
H H
30
Approx. 1 in^ H 64 1 64
Figure 8– Hexagonal nuts: ( a ) end view, general; ( b ) washer-faced regular nut; ( c ) regular nut chamfered on both sides; ( d ) jam nut with washer face; ( e ) jam nut chamfered on both sides.
When a connection is desired that can be disassembled without destructive methods and that is strong enough to resist external tensile loads, moment loads, and shear loads, or a combination of these, then the simple bolted joint using hardened-steel washers is a good solution. Such a joint can also be dangerous unless it is properly designed and assembled by a trained mechanic.
Screws, Fasteners, and the Design of Nonpermanent Joints 425
P P
P P
l
Figure 8–
A bolted connection loaded in tension by the forces P. Note the use of two washers. Note how the threads extend into the body of the connection. This is usual and is desired. l is the grip of the connection.
l
Figure 8–
Section of cylindrical pressure vessel. Hexagon-head cap screws are used to fasten the cylinder head to the body. Note the use of an O-ring seal. l is the effective grip of the connection (see Table 8–7).
A section through a tension-loaded bolted joint is illustrated in Fig. 8–13. Notice the clearance space provided by the bolt holes. Notice, too, how the bolt threads extend into the body of the connection. As noted previously, the purpose of the bolt is to clamp the two, or more, parts together. Twisting the nut stretches the bolt to produce the clamping force. This clamping force is called the pretension or bolt preload. It exists in the connection after the nut has been properly tightened no matter whether the external tensile load P is exerted or not. Of course, since the members are being clamped together, the clamping force that produces tension in the bolt induces compression in the members. Figure 8–14 shows another tension-loaded connection. This joint uses cap screws threaded into one of the members. An alternative approach to this problem (of not using a nut) would be to use studs. A stud is a rod threaded on both ends. The stud is screwed into the lower member first; then the top member is positioned and fastened down with hardened washers and nuts. The studs are regarded as permanent, and so the joint can be disassembled merely by removing the nut and washer. Thus the threaded part of the lower member is not damaged by reusing the threads. The spring rate is a limit as expressed in Eq. (4–1). For an elastic member such as a bolt, as we learned in Eq. (4–2), it is the ratio between the force applied to the member and the deflection produced by that force. We can use Eq. (4–4) and the results of Prob. 4–1 to find the stiffness constant of a fastener in any bolted connection. The grip l of a connection is the total thickness of the clamped material. In Fig. 8–13 the grip is the sum of the thicknesses of both members and both washers. In Fig. 8–14 the effective grip is given in Table 8–7. The stiffness of the portion of a bolt or screw within the clamped zone will gen- erally consist of two parts, that of the unthreaded shank portion and that of the
Screws, Fasteners, and the Design of Nonpermanent Joints 427
threaded portion. Thus the stiffness constant of the bolt is equivalent to the stiffnesses of two springs in series. Using the results of Prob. 4–1, we find 1 k
k 1
k 2
or k =
k 1 k 2 k 1 + k 2
(8–15)
for two springs in series. From Eq. (4–4), the spring rates of the threaded and unthreaded portions of the bolt in the clamped zone are, respectively,
k (^) t =
A (^) t E l (^) t
k (^) d =
A (^) d E l (^) d
(8–16)
where A (^) t = tensile-stress area (Tables 8–1, 8–2) l (^) t = length of threaded portion of grip A (^) d = major-diameter area of fastener l (^) d = length of unthreaded portion in grip
Substituting these stiffnesses in Eq. (8–15) gives
k (^) b =
A (^) d A (^) t E A (^) d l (^) t + A (^) t l (^) d
(8–17)
where k (^) b is the estimated effective stiffness of the bolt or cap screw in the clamped zone. For short fasteners, the one in Fig. 8–14, for example, the unthreaded area is small and so the first of the expressions in Eq. (8–16) can be used to find k (^) b. For long fasteners, the threaded area is relatively small, and so the second expression in Eq. (8–16) can be used. Table 8–7 is useful.
In the previous section, we determined the stiffness of the fastener in the clamped zone. In this section, we wish to study the stiffnesses of the members in the clamped zone. Both of these stiffnesses must be known in order to learn what happens when the assembled connection is subjected to an external tensile loading. There may be more than two members included in the grip of the fastener. All together these act like compressive springs in series, and hence the total spring rate of the members is 1 k (^) m
k 1
k 2
k 3
k (^) i
(8–18)
If one of the members is a soft gasket, its stiffness relative to the other members is usually so small that for all practical purposes the others can be neglected and only the gasket stiffness used. If there is no gasket, the stiffness of the members is rather difficult to obtain, except by experimentation, because the compression region spreads out between the bolt head and the nut and hence the area is not uniform. There are, however, some cases in which this area can be determined. Ito^2 has used ultrasonic techniques to determine the pressure distribution at the mem- ber interface. The results show that the pressure stays high out to about 1.5 bolt radii.
(^2) Y. Ito, J. Toyoda, and S. Nagata, “Interface Pressure Distribution in a Bolt-Flange Assembly,” ASME paper no. 77-WA/DE-11, 1977.
428 Mechanical Engineering Design
The pressure, however, falls off farther away from the bolt. Thus Ito suggests the use of Rotscher’s pressure-cone method for stiffness calculations with a variable cone angle. This method is quite complicated, and so here we choose to use a simpler approach using a fixed cone angle. Figure 8–15 illustrates the general cone geometry using a half-apex angle α. An angle α = 45 ◦^ has been used, but Little 3 reports that this overestimates the clamping stiffness. When loading is restricted to a washer-face annulus (hardened steel, cast iron, or aluminum), the proper apex angle is smaller. Osgood 4 reports a range of 25 ◦^ ≤ α ≤ 33 ◦^ for most combinations. In this book we shall use α = 30 ◦^ except in cases in which the material is insufficient to allow the frusta to exist. Referring now to Fig. 8–15 b , the contraction of an element of the cone of thick- ness dx subjected to a compressive force P is, from Eq. (4–3),
d δ =
P dx E A
( a )
The area of the element is
A = π
r o^2 − r^2 i
= π
x tan α +
d 2
= π
x tan α +
D + d 2
x tan α +
D − d 2
) ( b )
Substituting this in Eq. ( a ) and integrating gives a total contraction of
δ =
π E
∫ (^) t
0
dx [ x tan α + ( D + d )/2][ x tan α + ( D − d )/2]
( c )
Using a table of integrals, we find the result to be
δ =
π Ed tan α
ln
( 2 t tan α + D − d )( D + d ) ( 2 t tan α + D + d )( D − d )
( d )
Thus the spring rate or stiffness of this frustum is
k =
δ
π Ed tan α
ln
( 2 t tan α + D − d )( D + d ) ( 2 t tan α + D + d )( D − d )
(8–19)
( a ) (^) ( b )
t
y t
D
x
y l 2 d
d w
d
x
dx
Figure 8–15 x Compression of a member with the equivalent elastic properties represented by a frustum of a hollow cone. Here, l represents the grip length.
(^3) R. E. Little, “Bolted Joints: How Much Give?” Machine Design, Nov. 9, 1967. (^4) C. C. Osgood, “Saving Weight on Bolted Joints,” Machine Design, Oct. 25, 1979.