
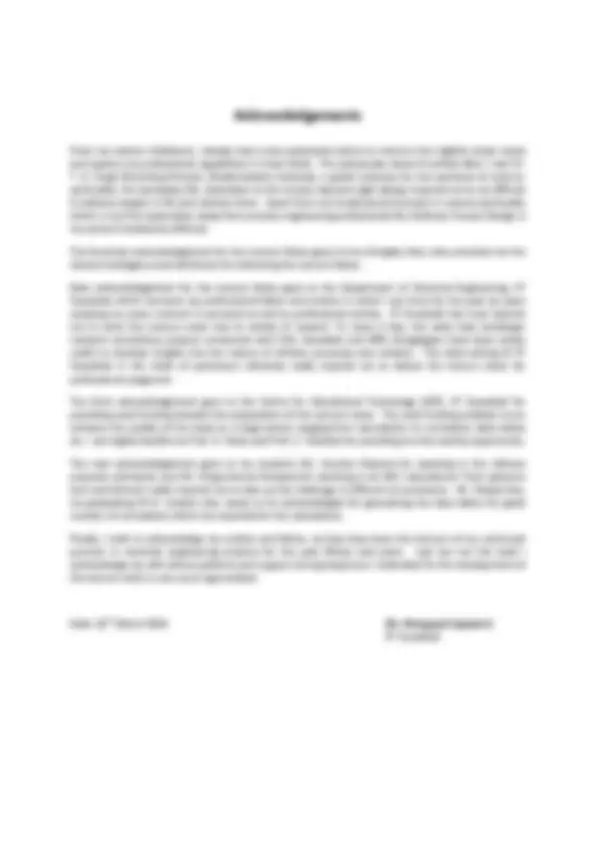
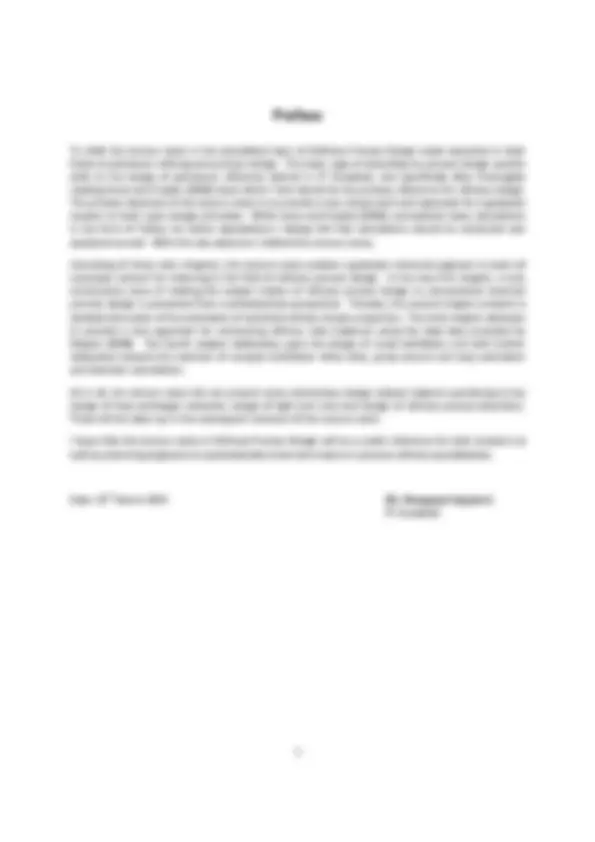
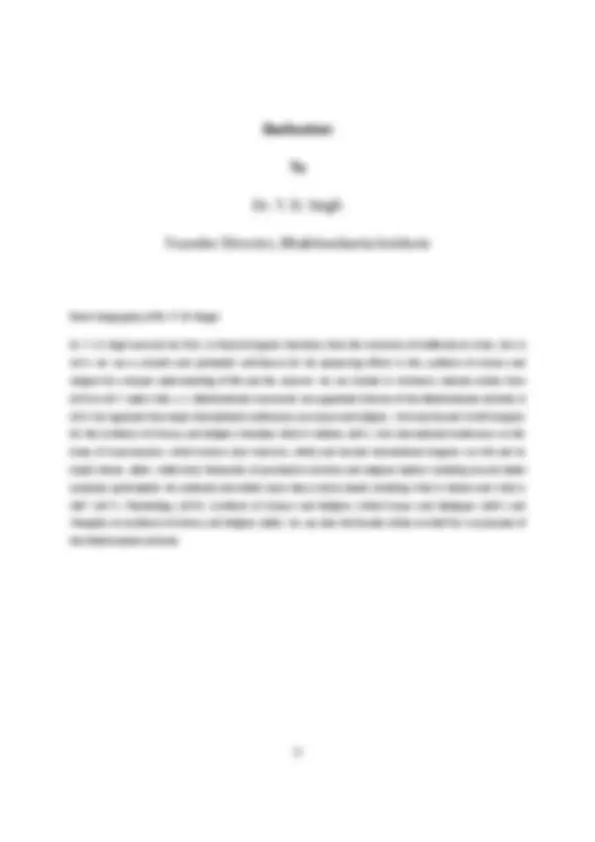
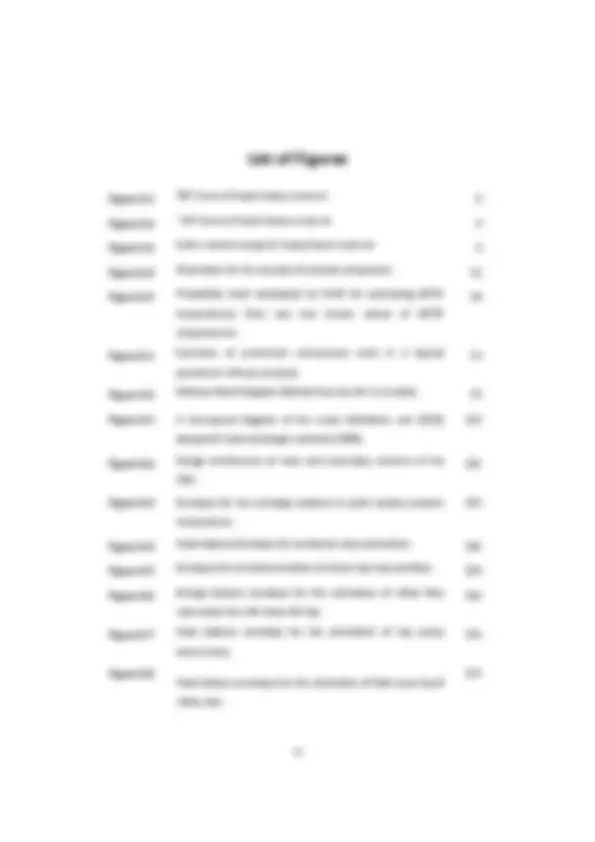
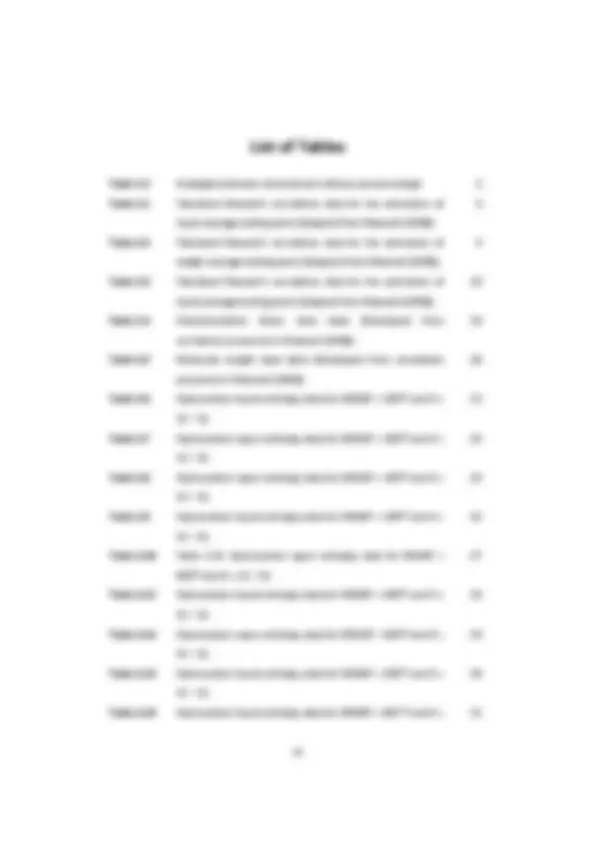
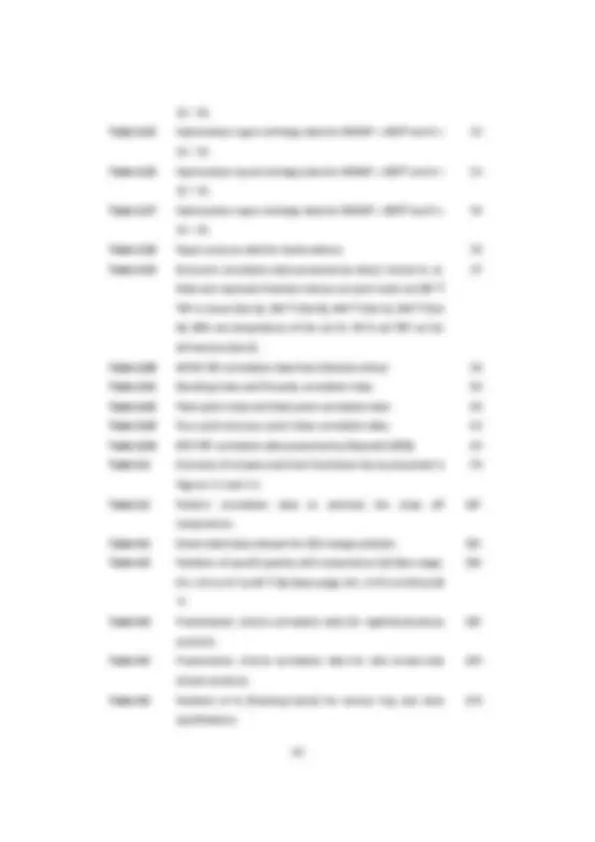
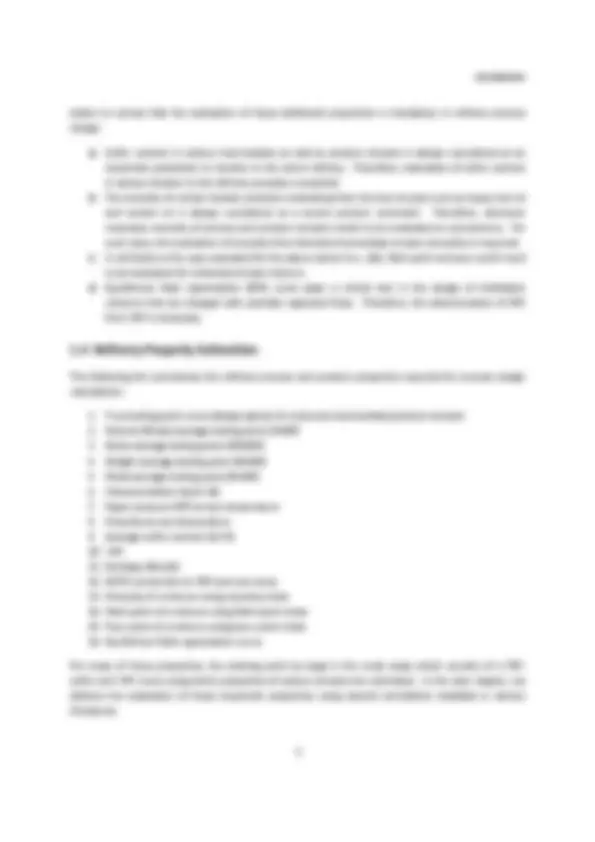
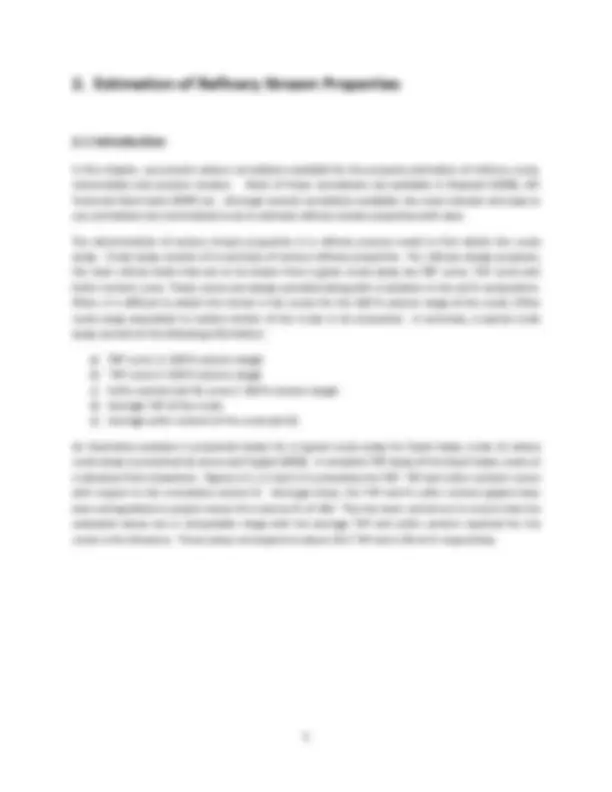
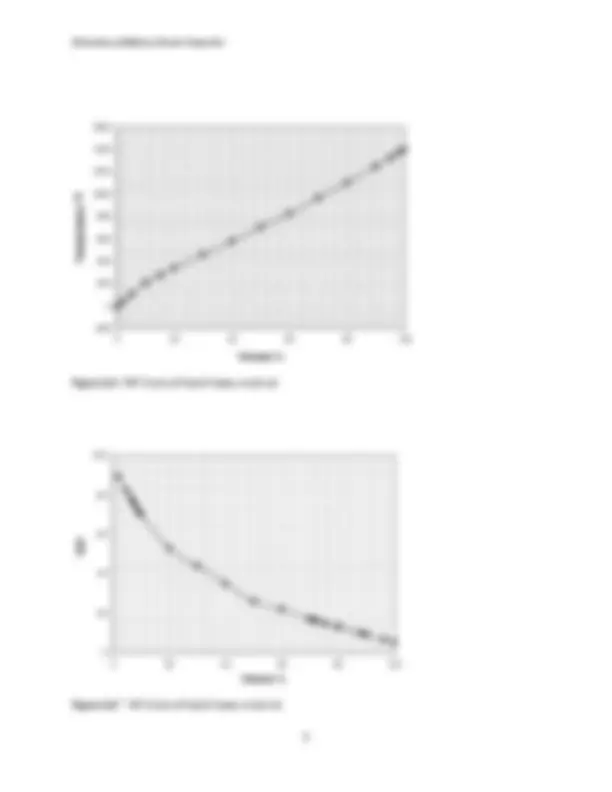
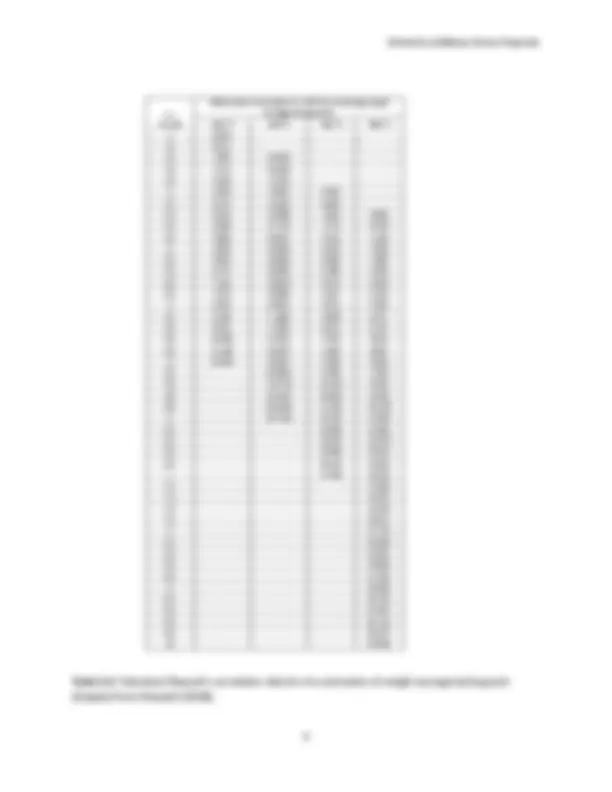
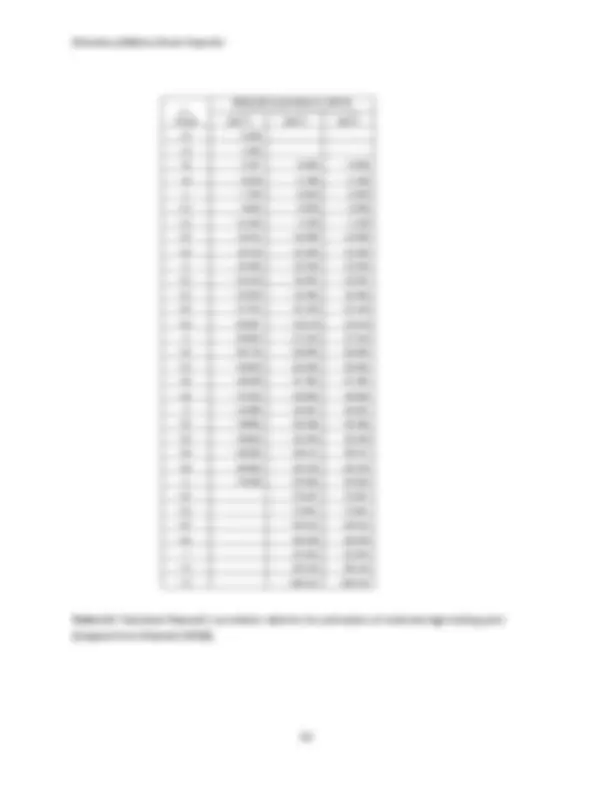
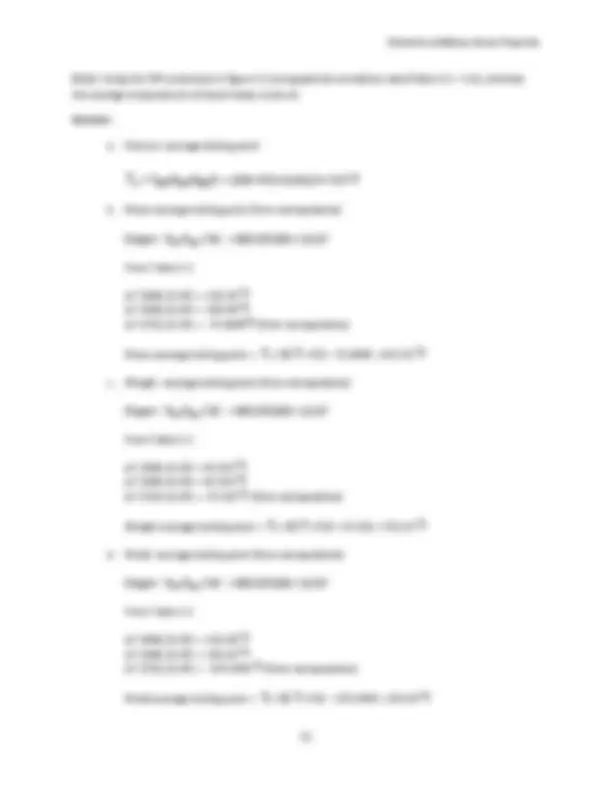
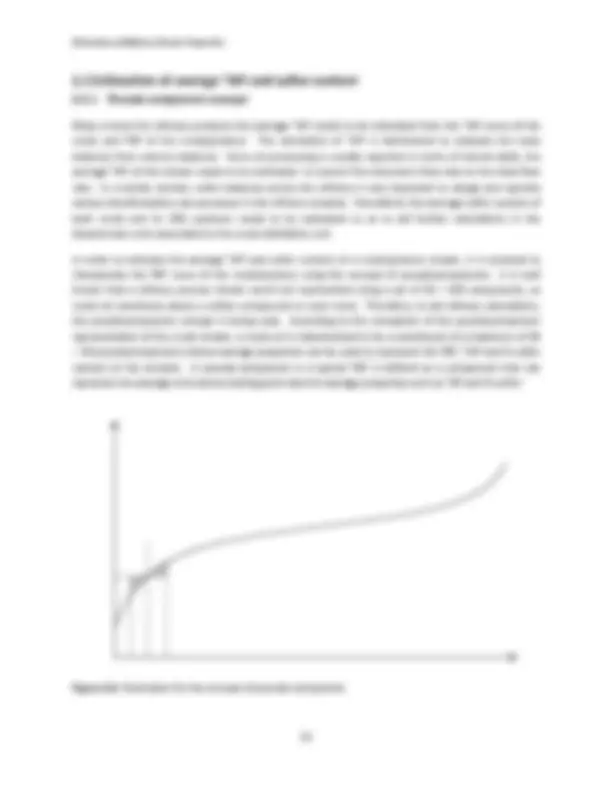
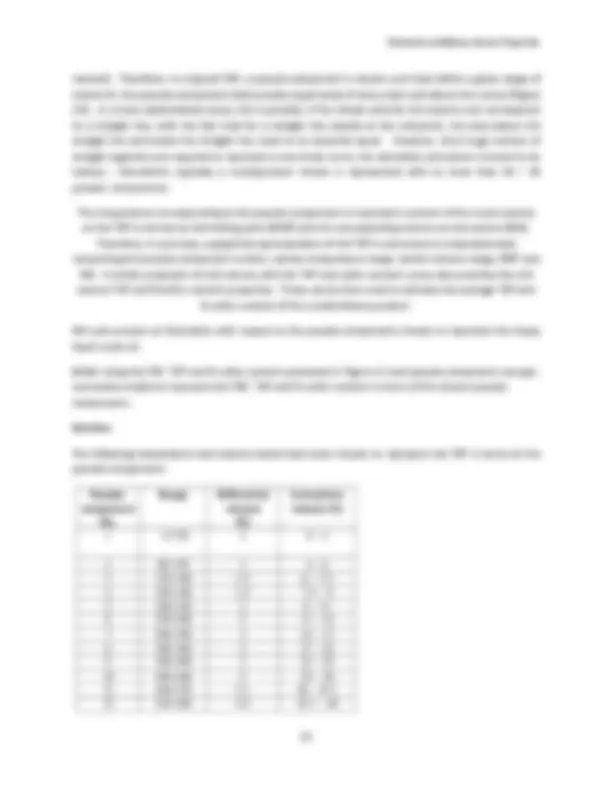
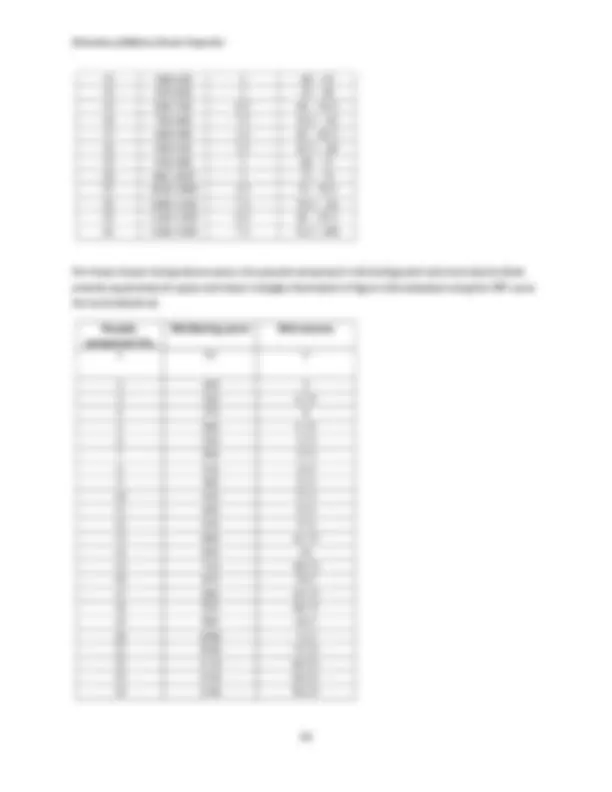

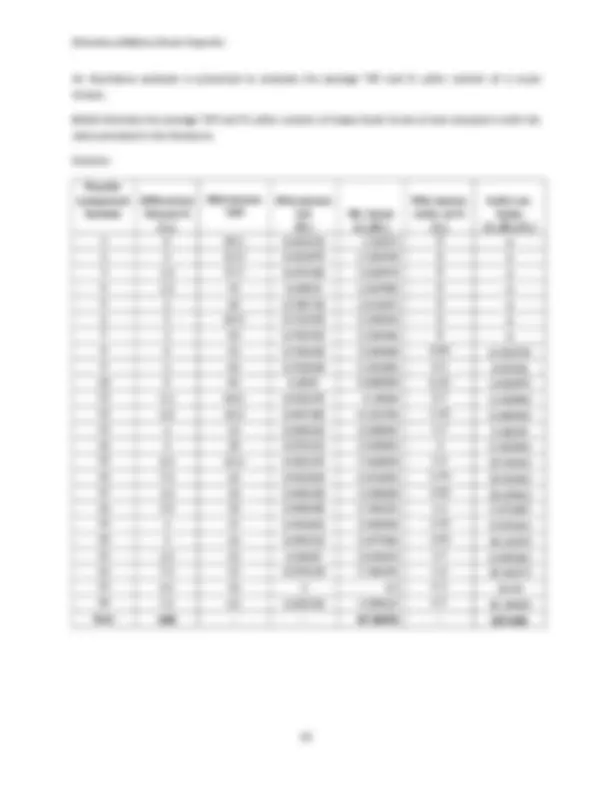
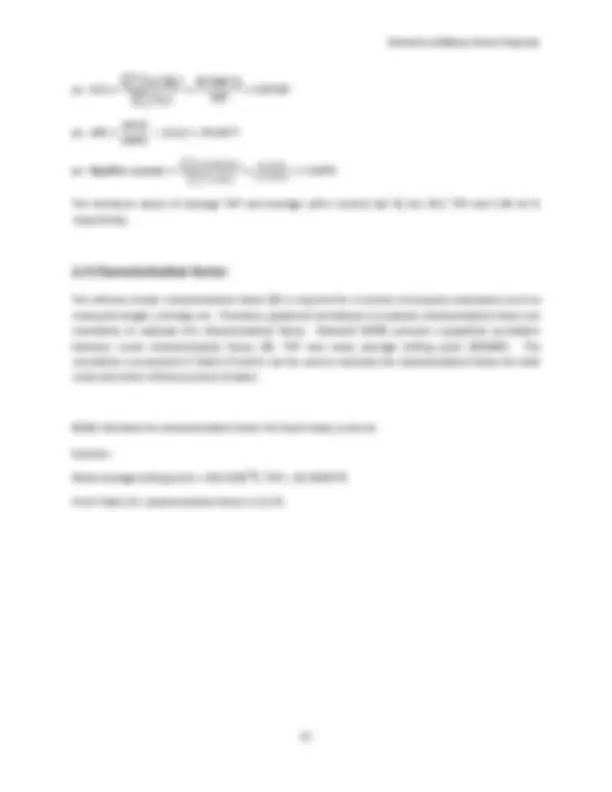
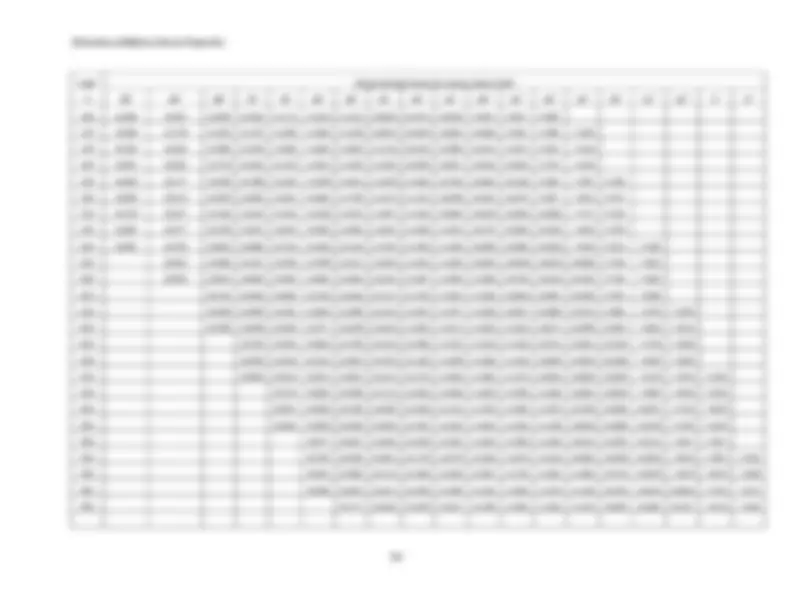
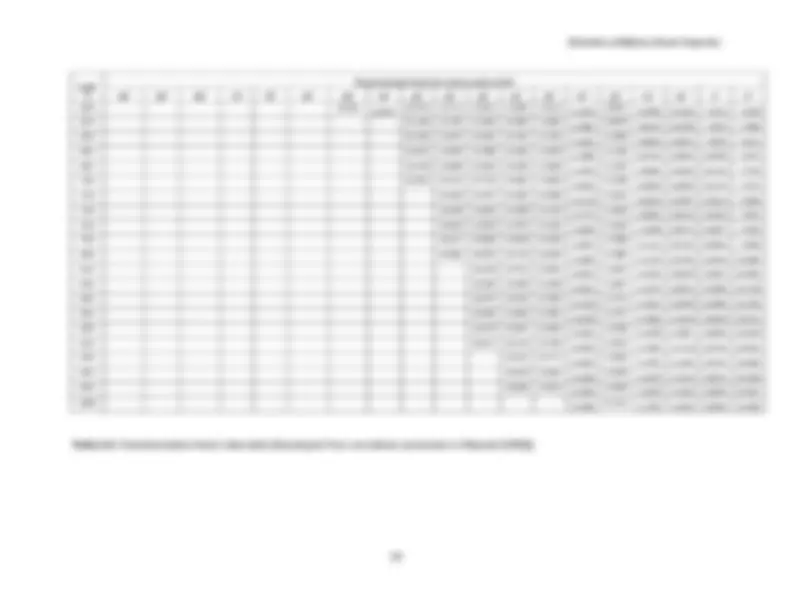
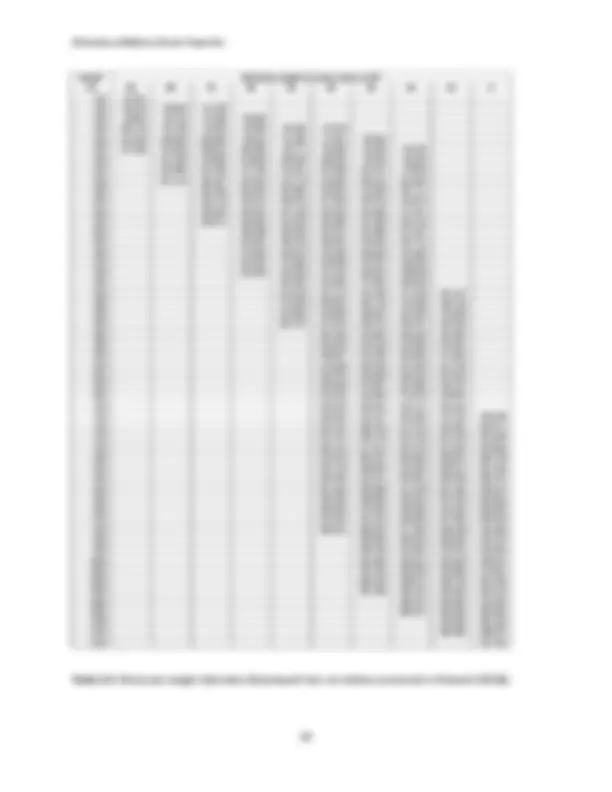
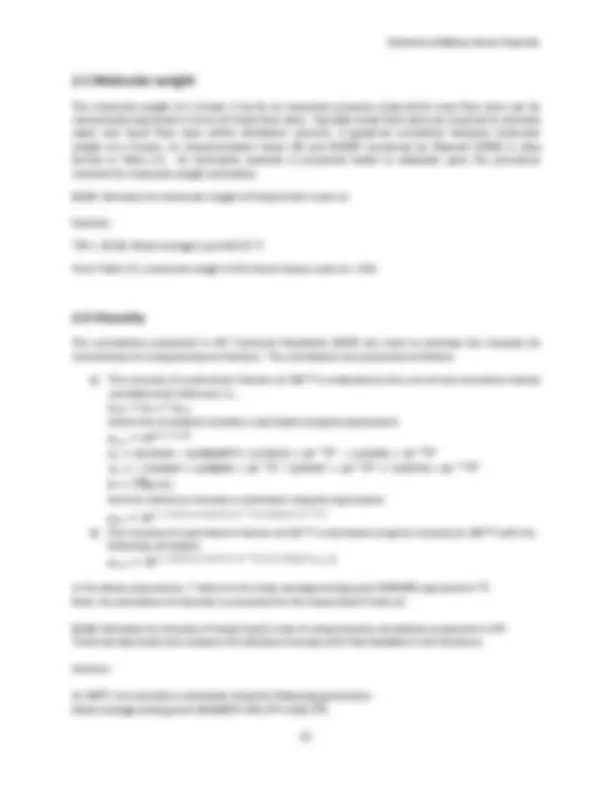
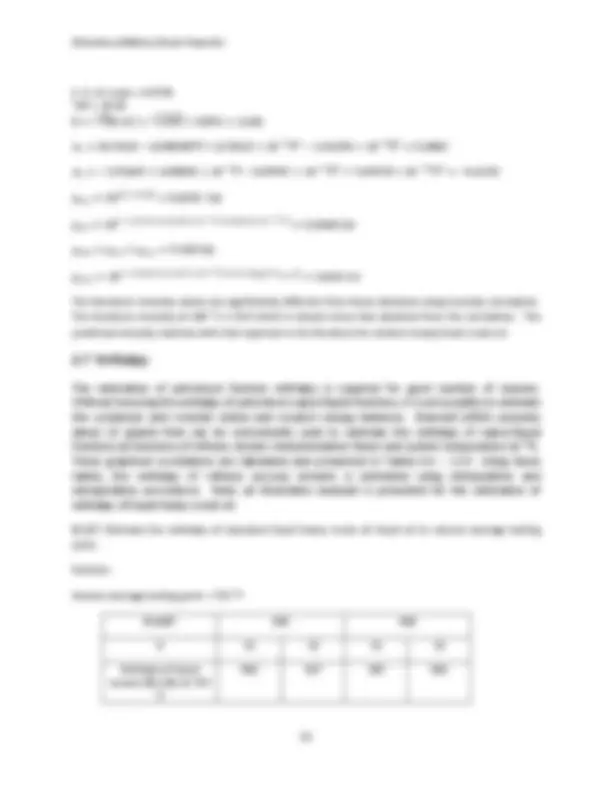
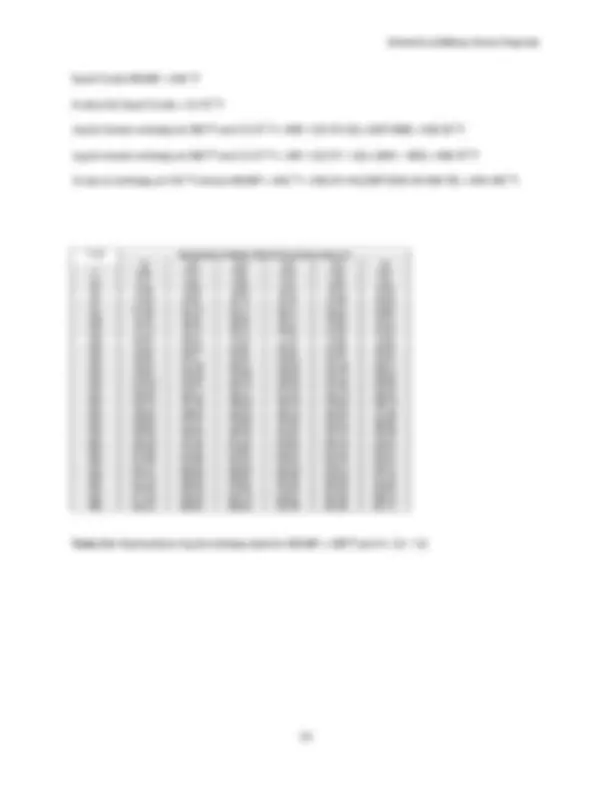
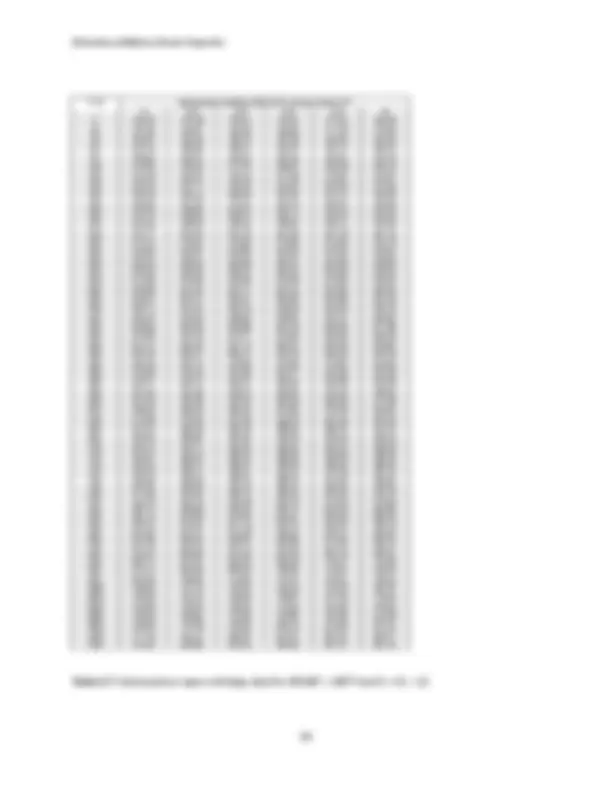
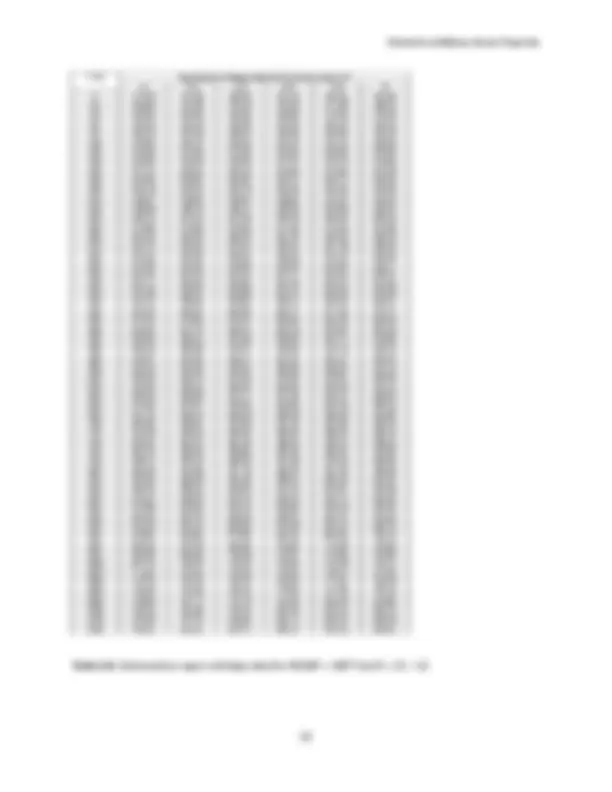
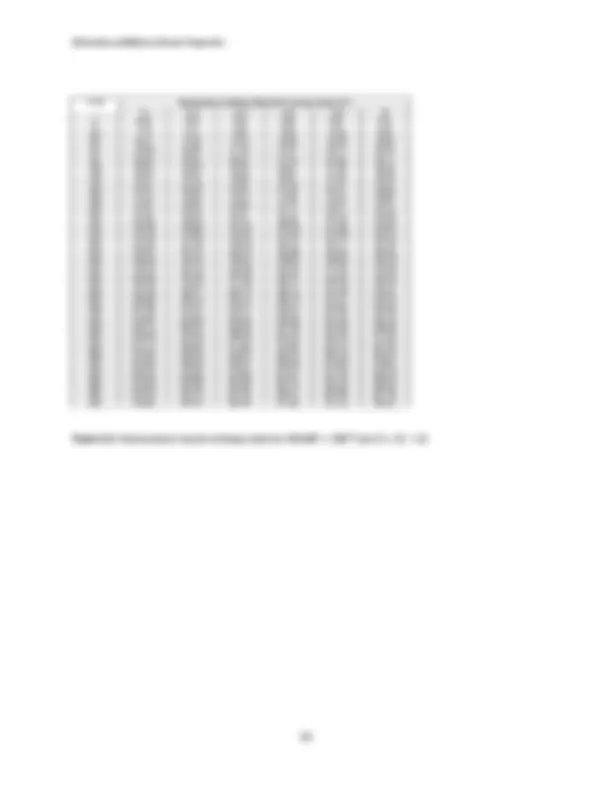
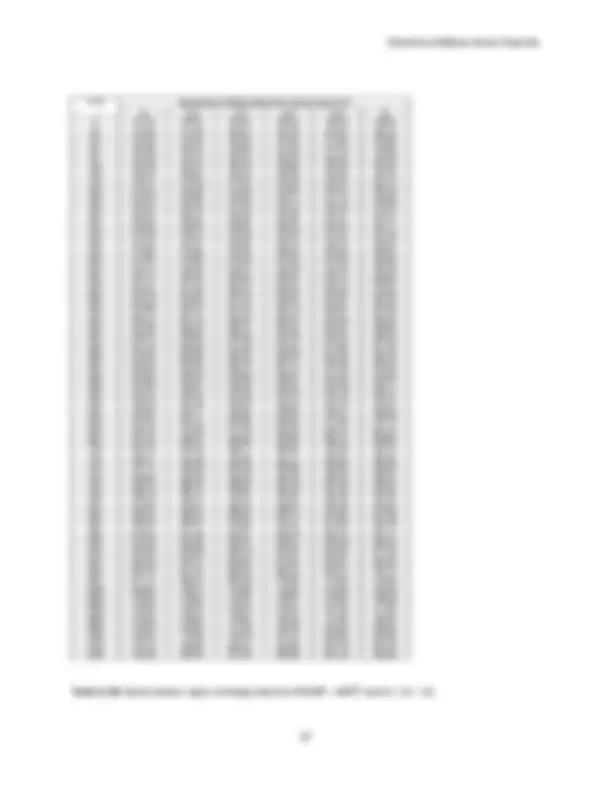
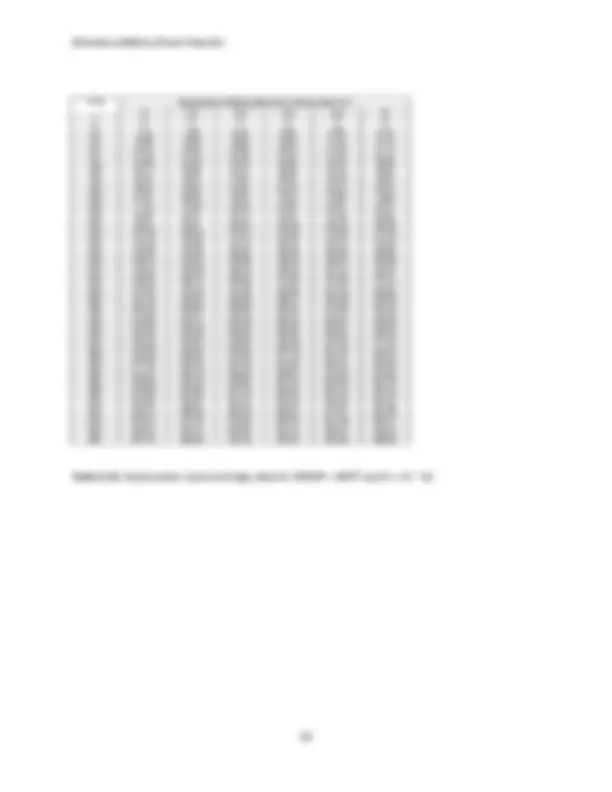
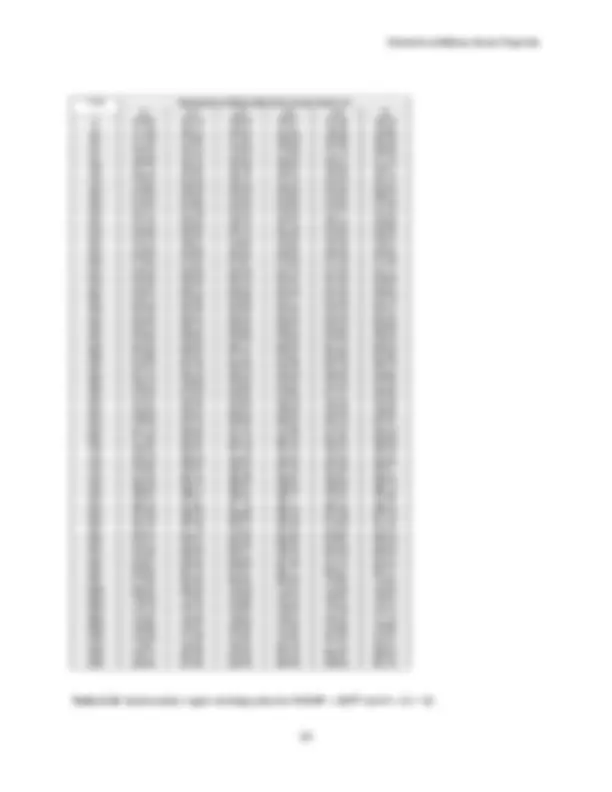
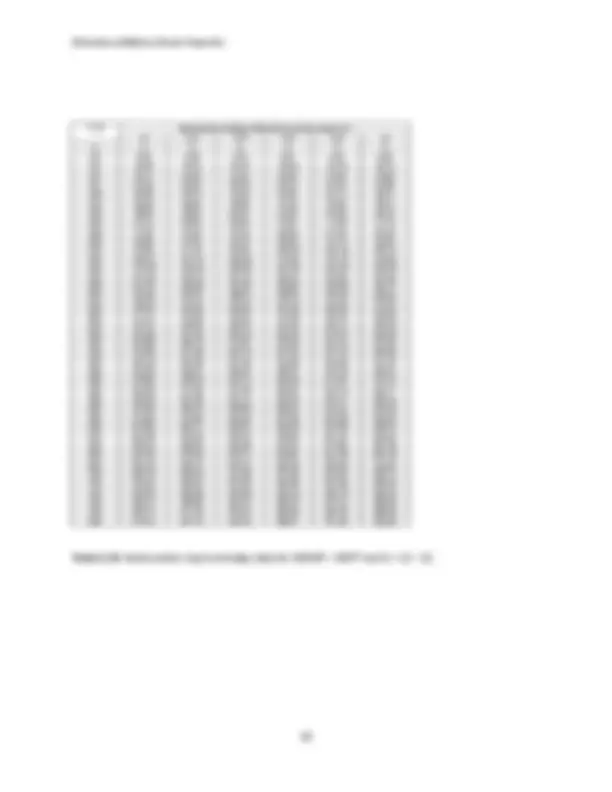
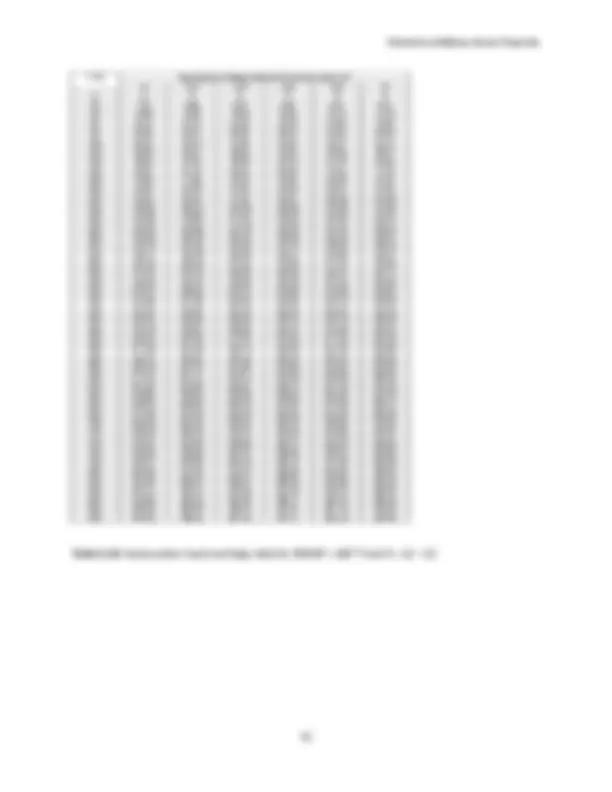
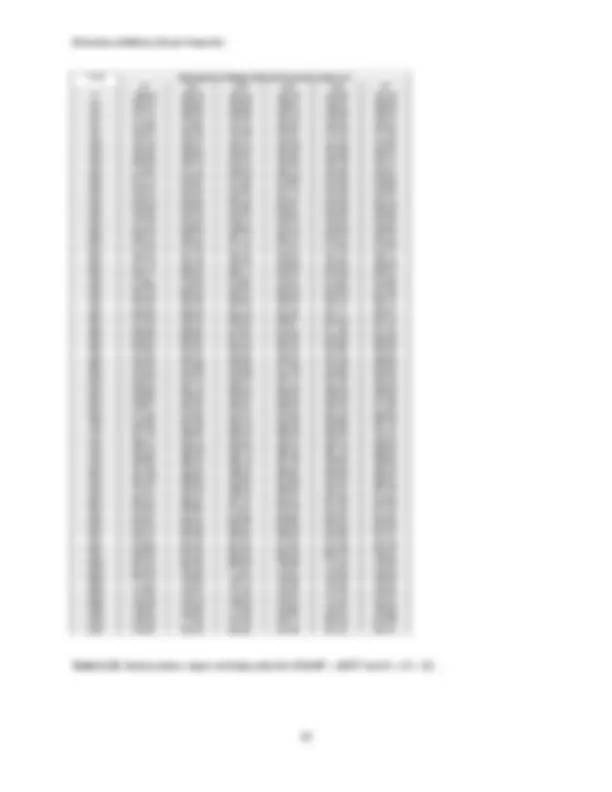
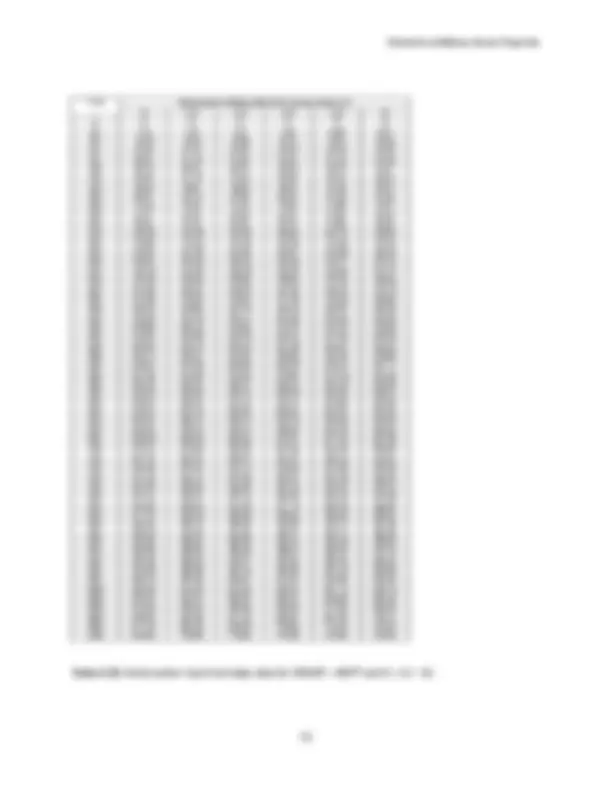
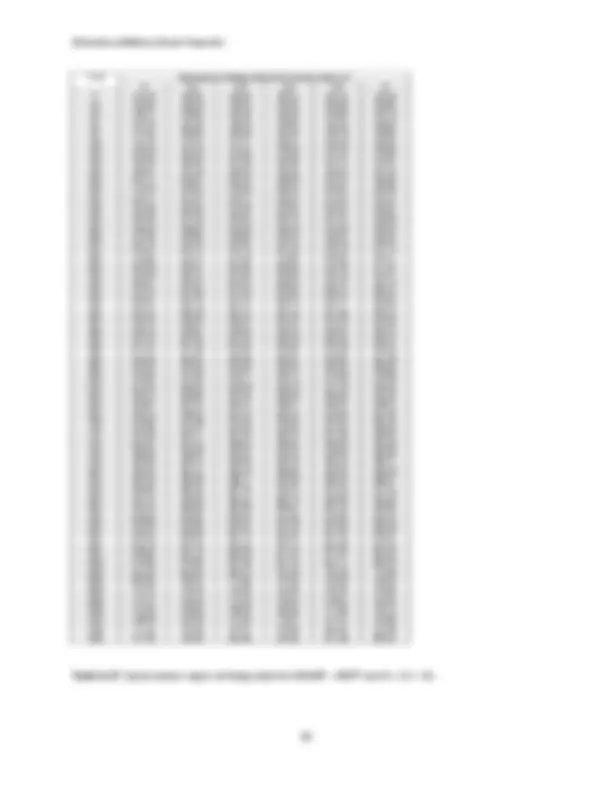
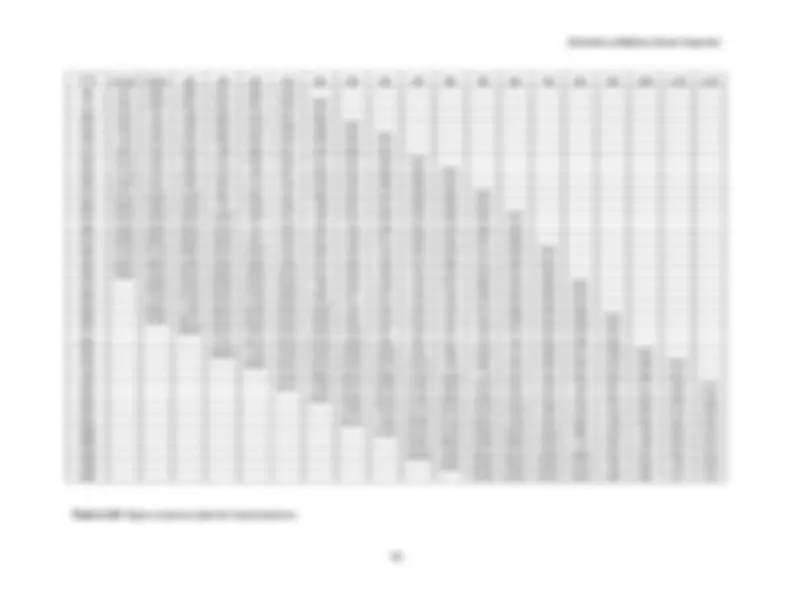
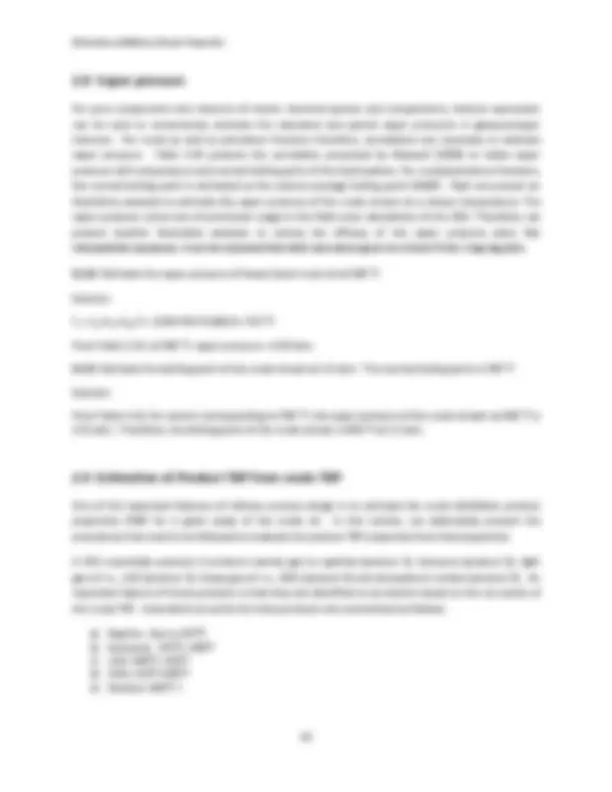
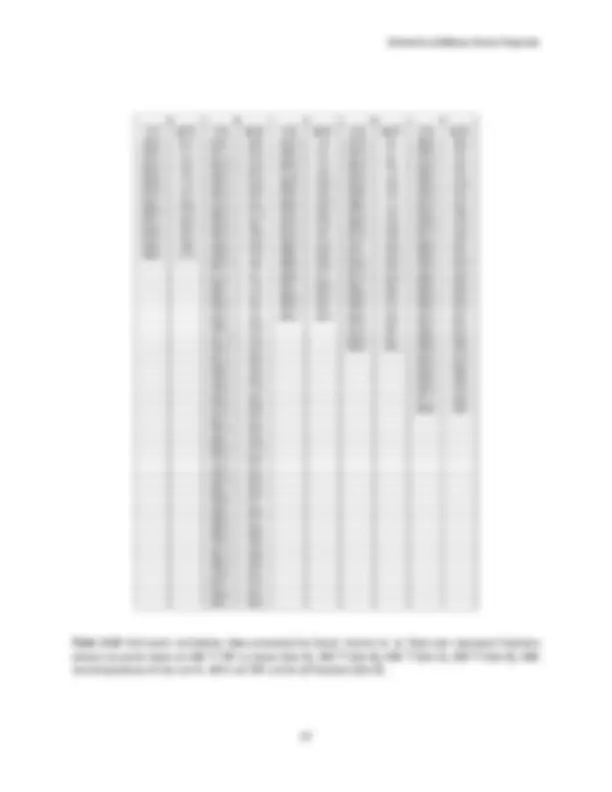
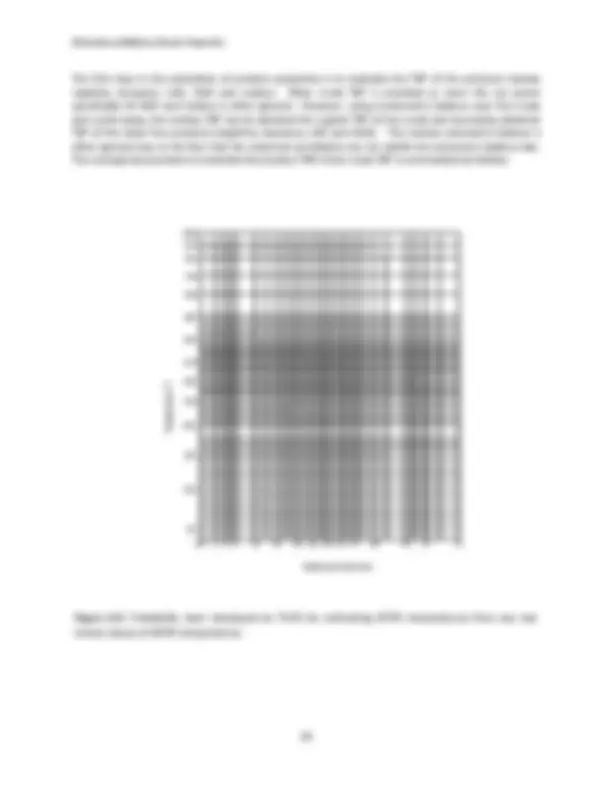
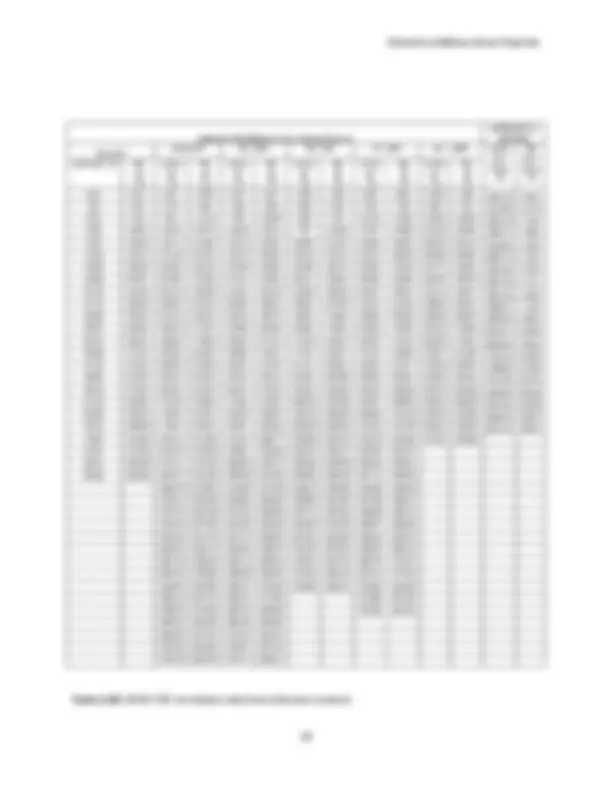
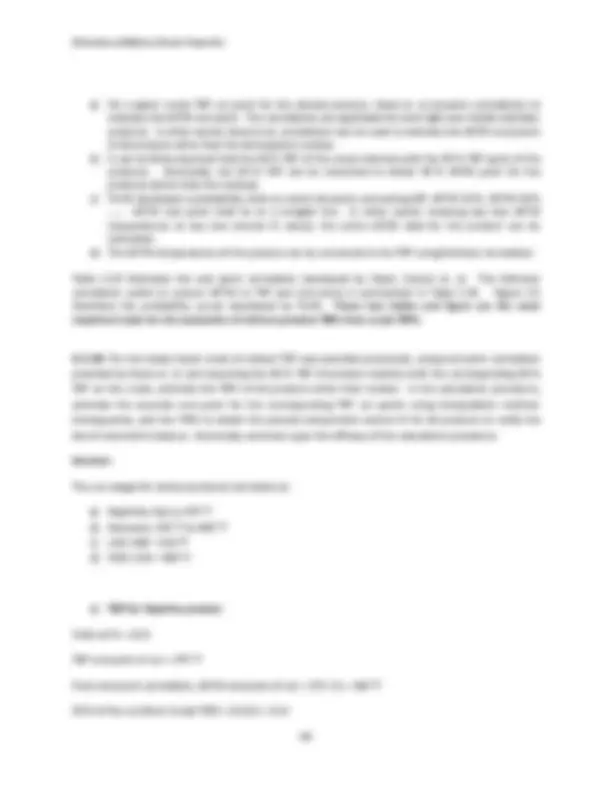
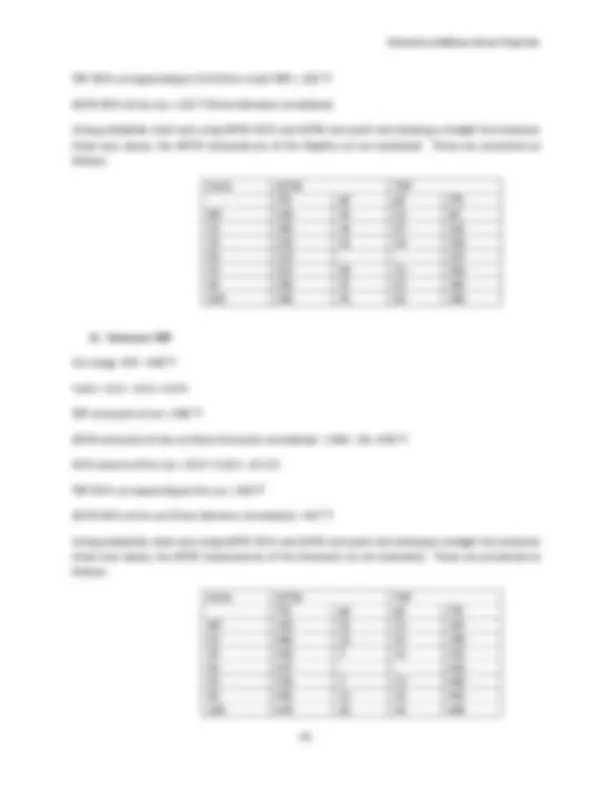
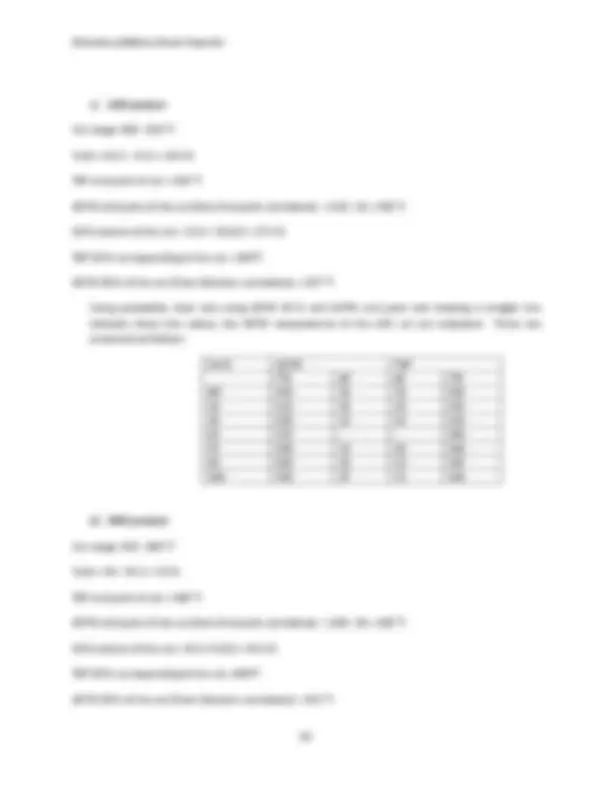
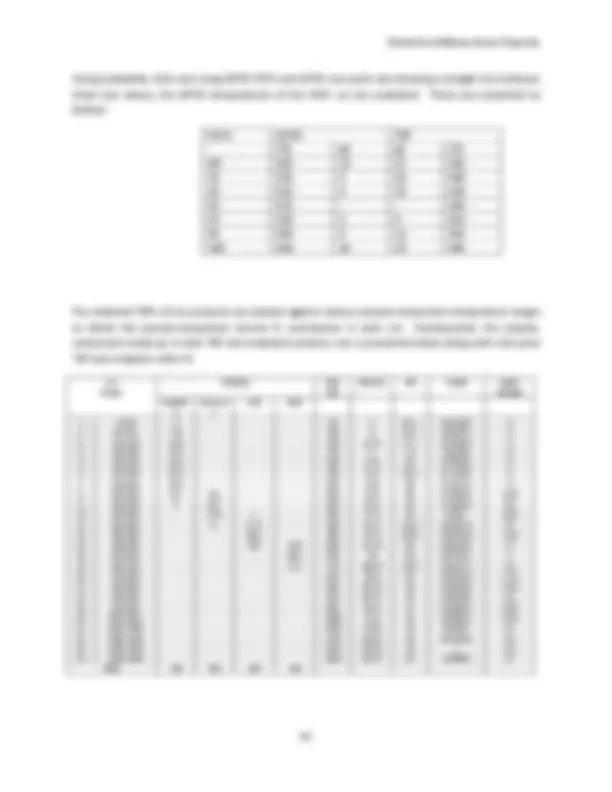
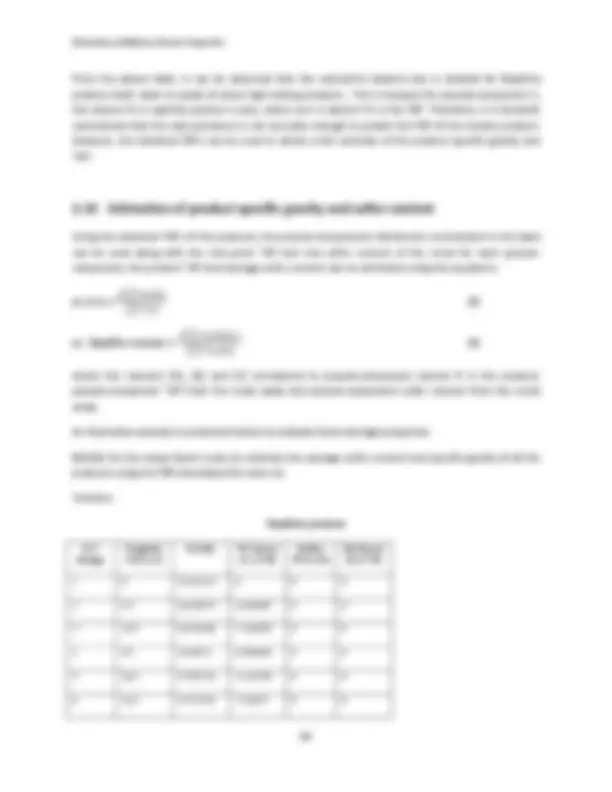
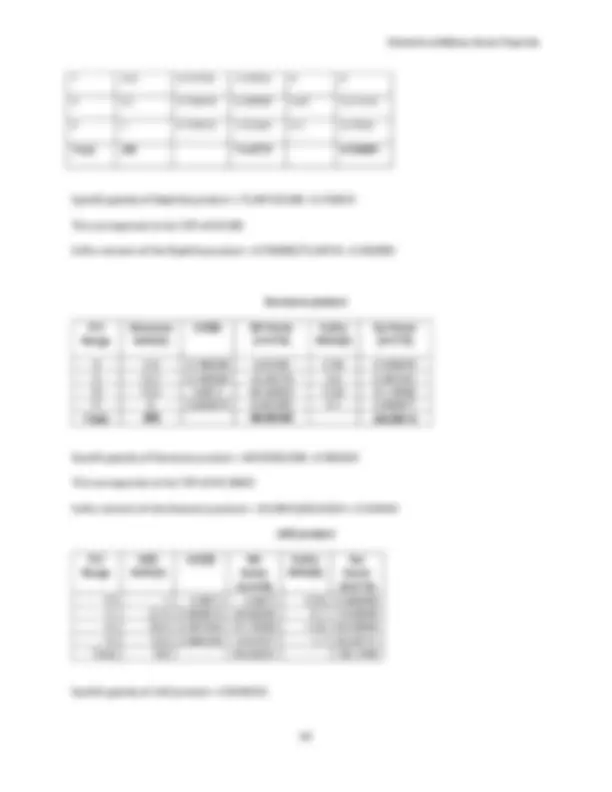
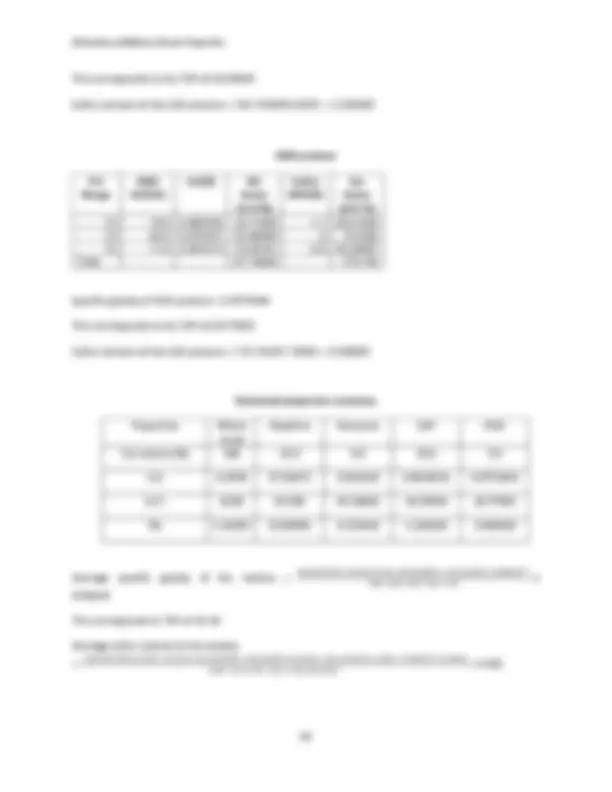
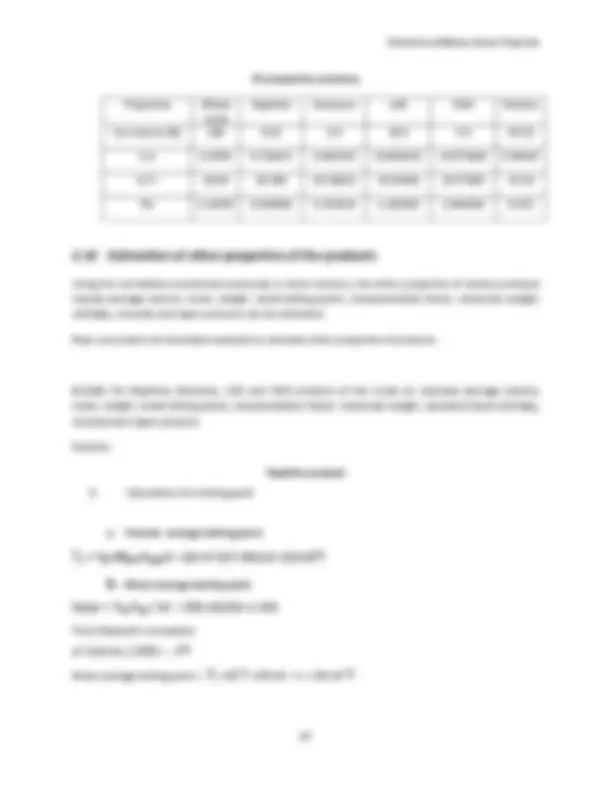
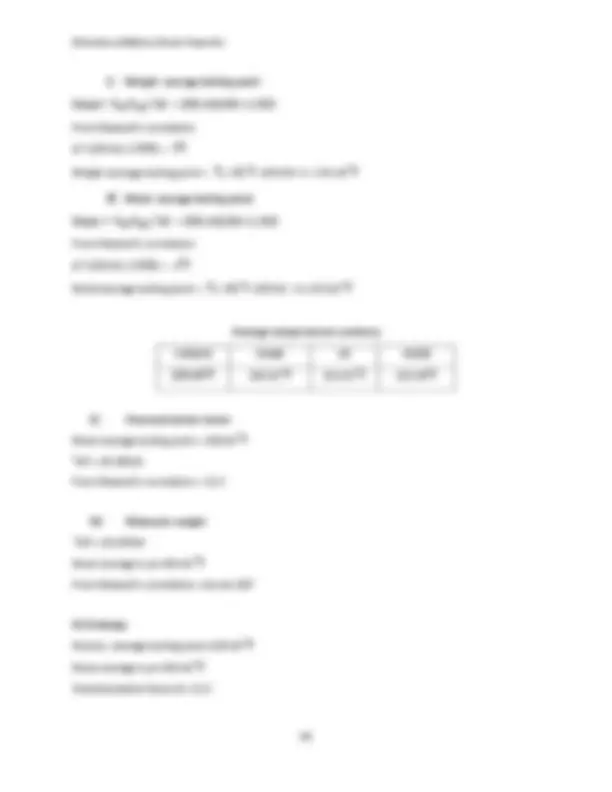
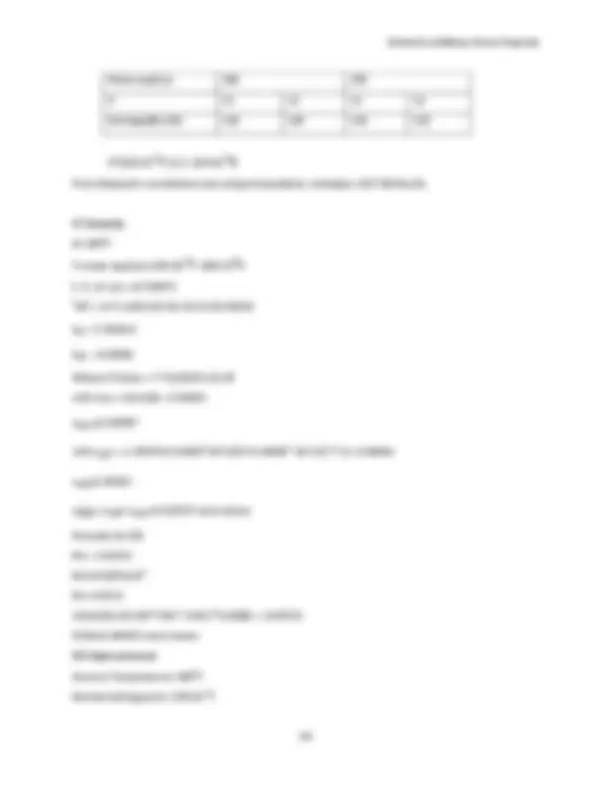
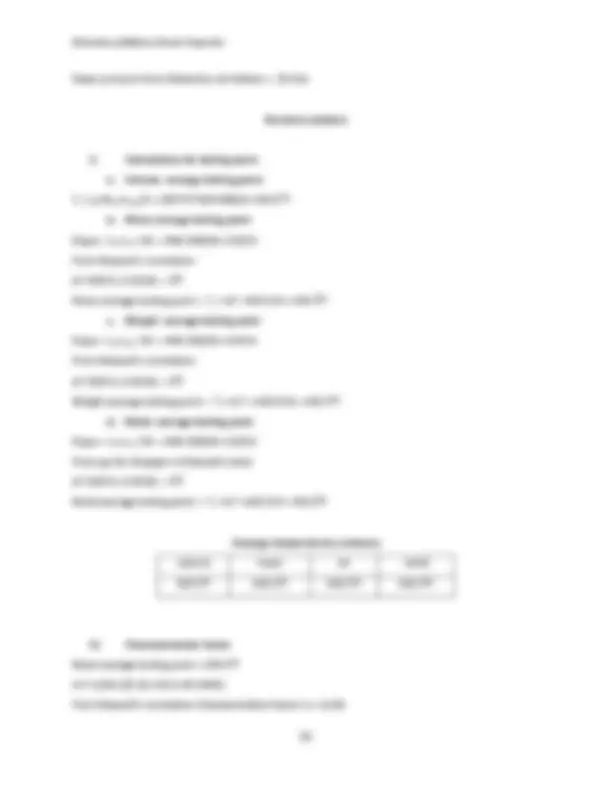
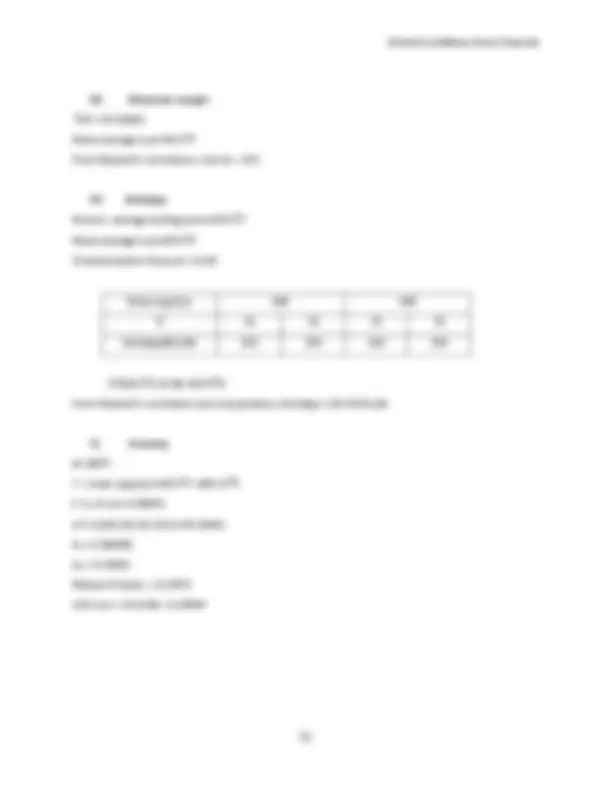
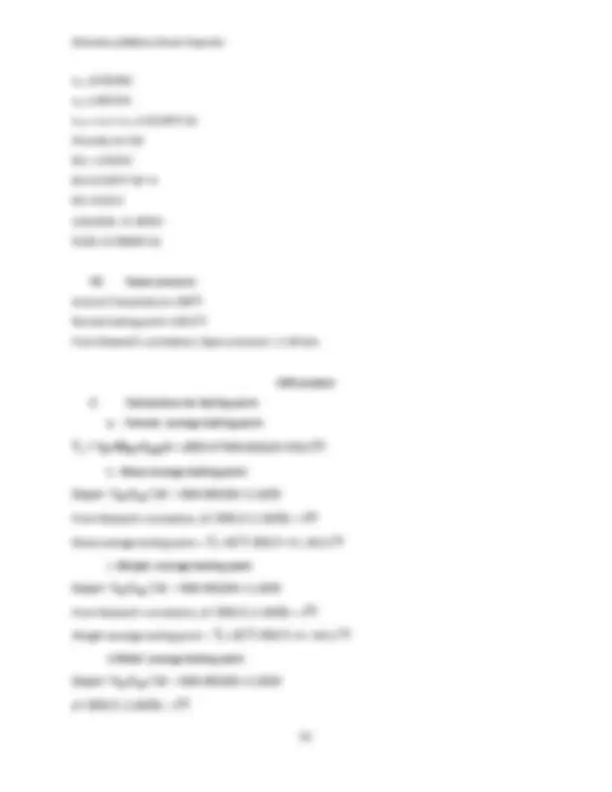
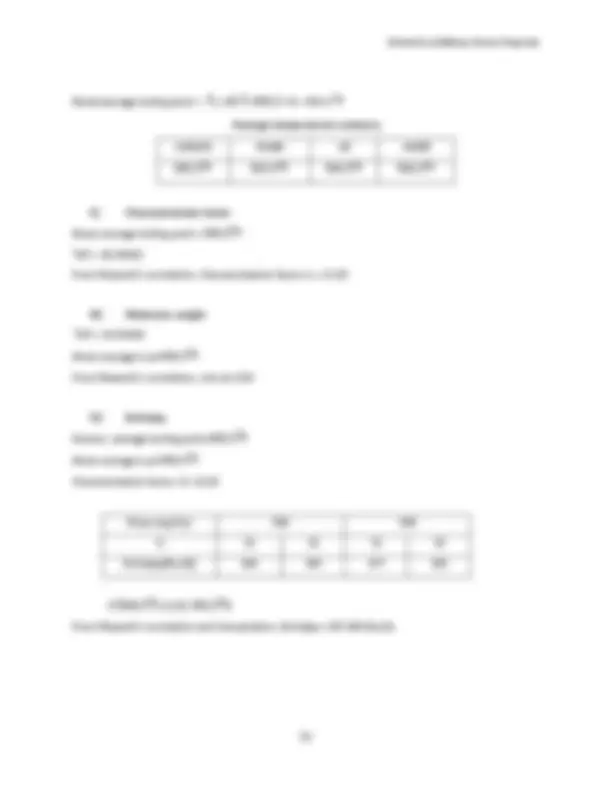
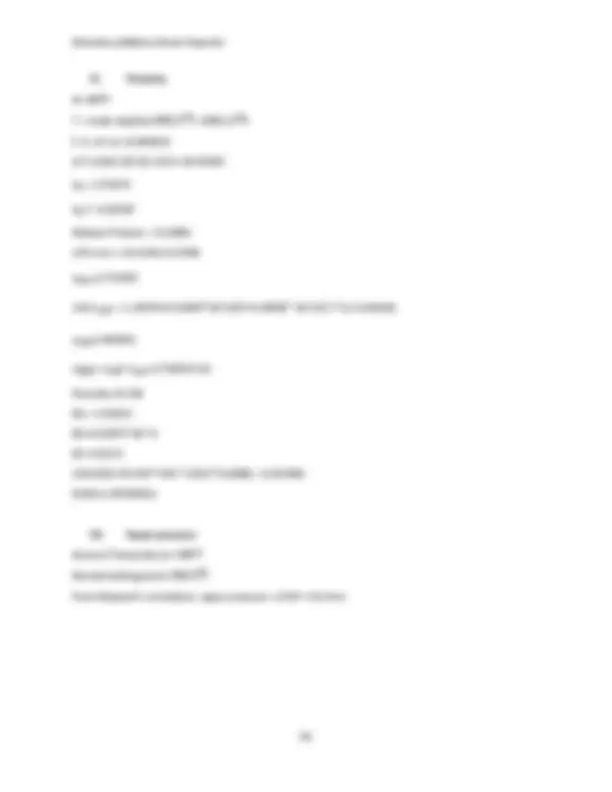
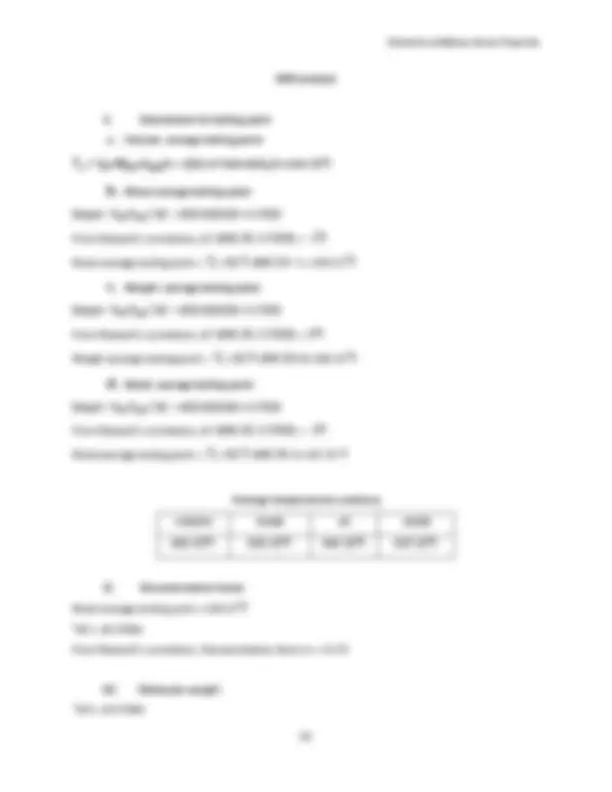
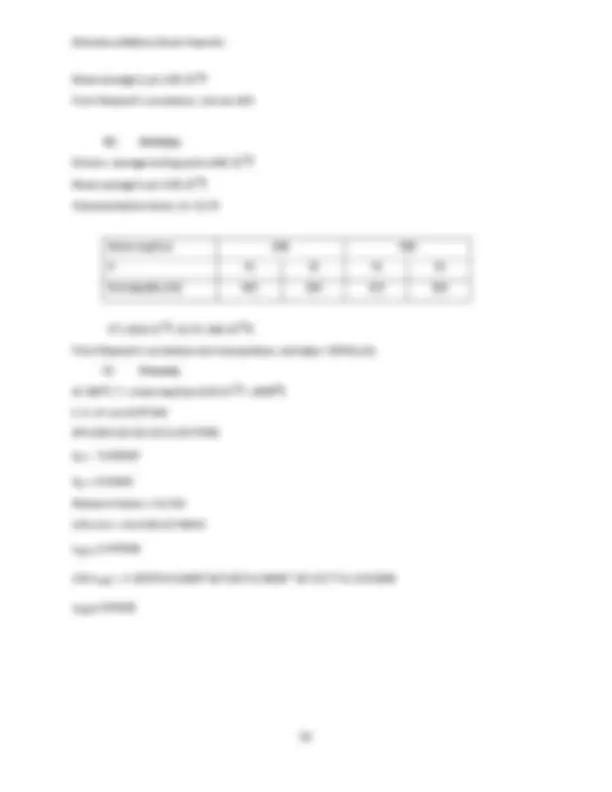
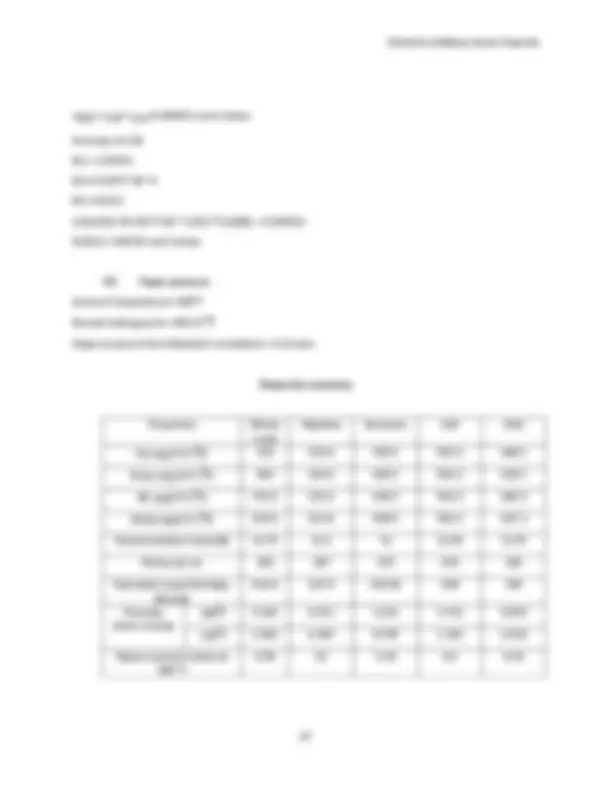
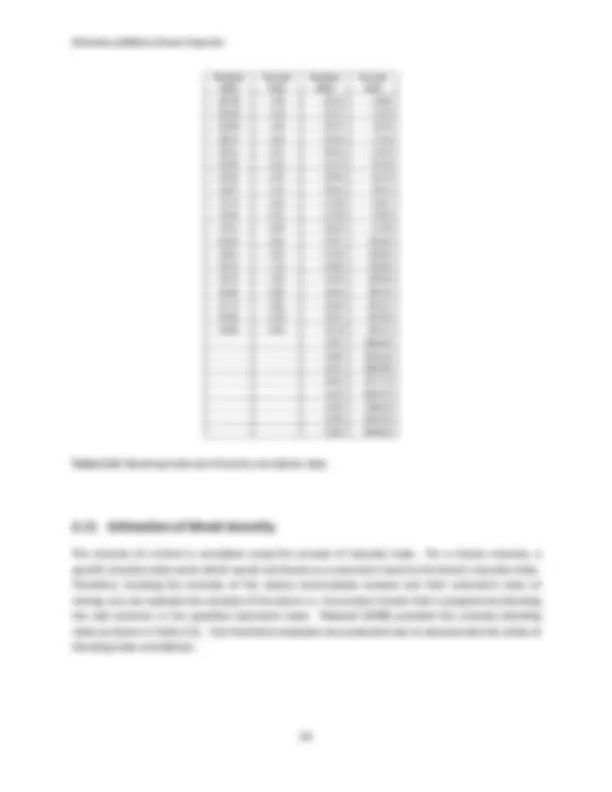
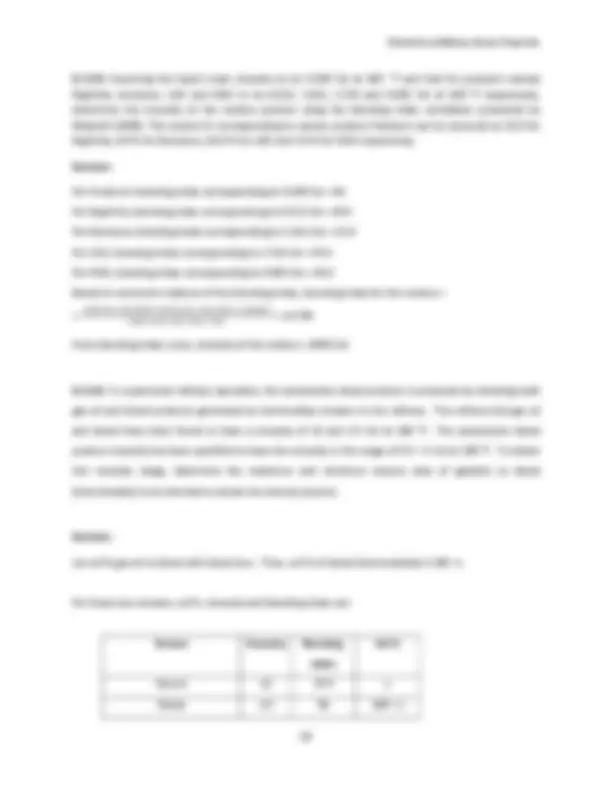
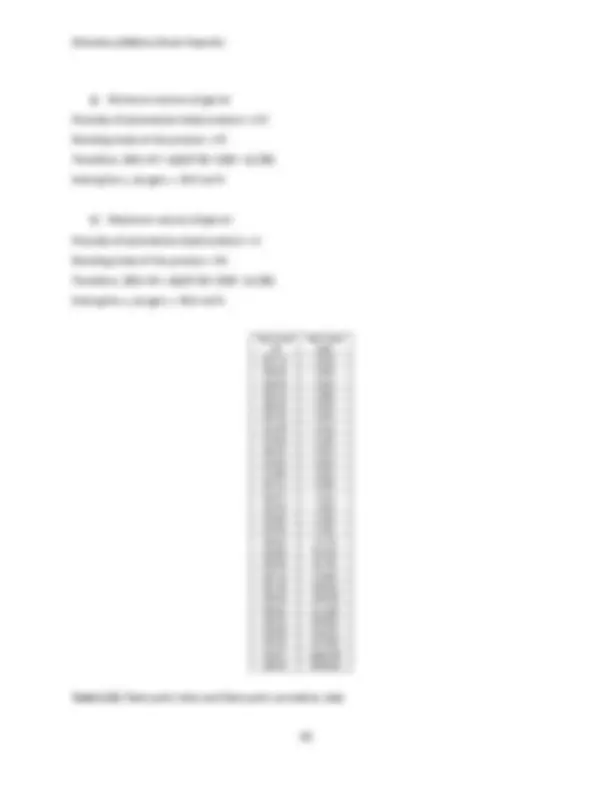
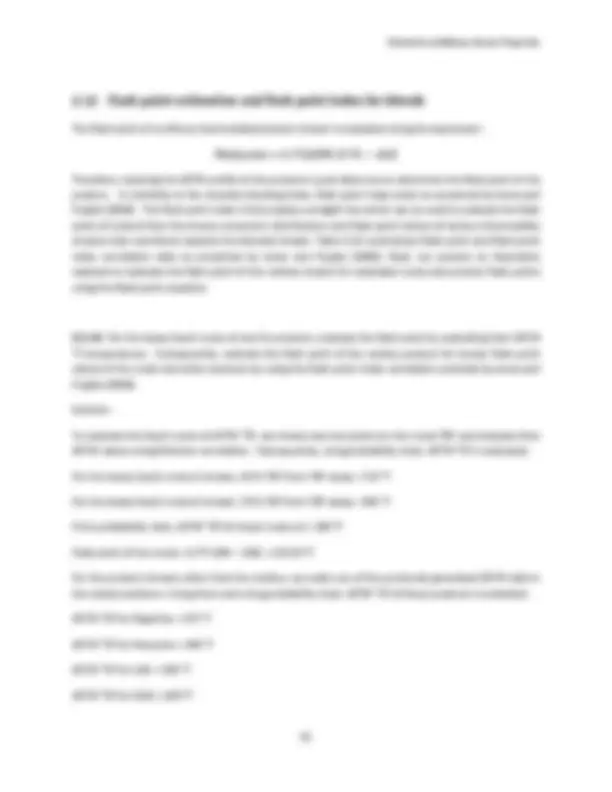
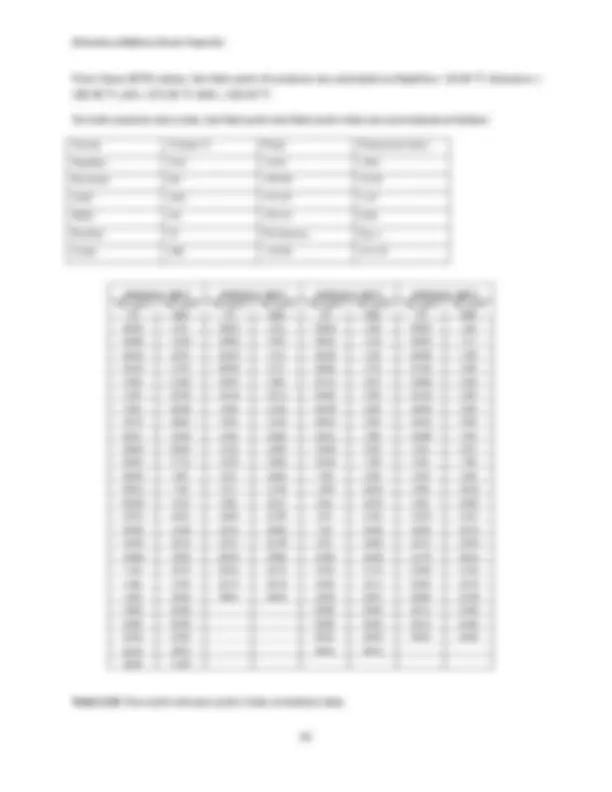
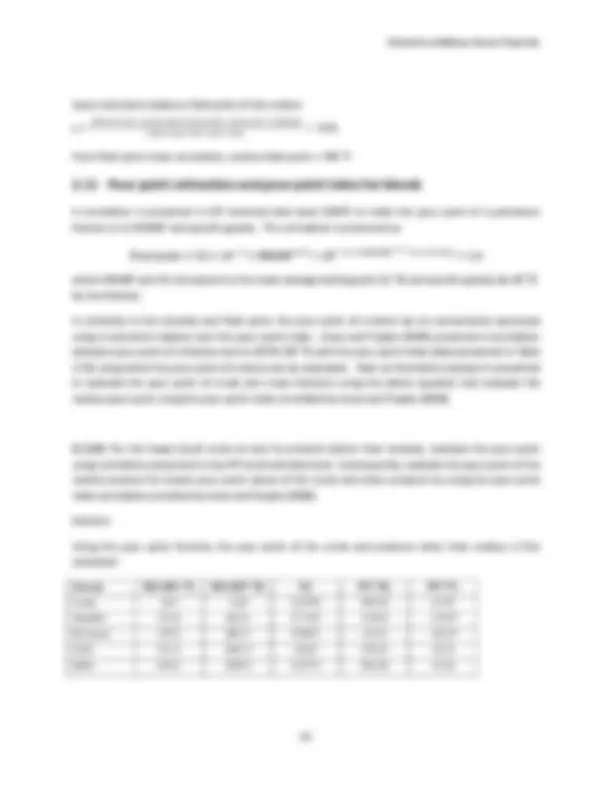
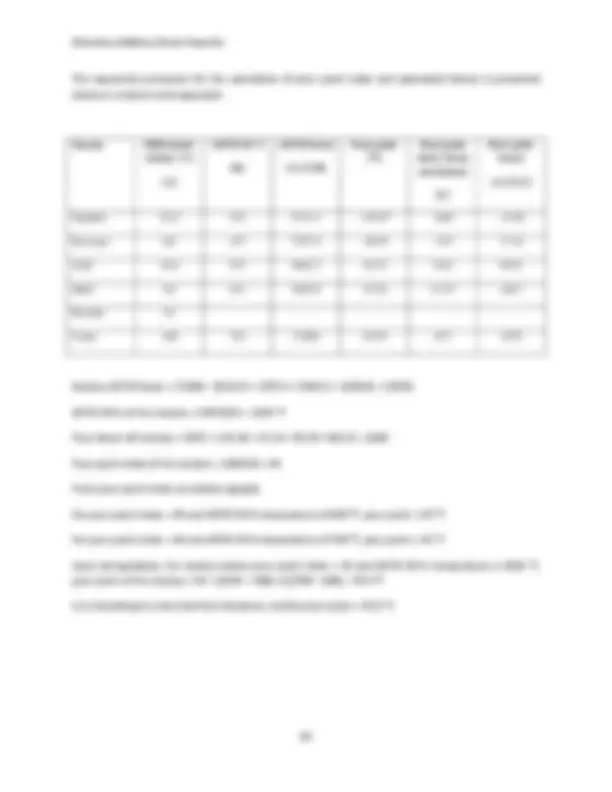
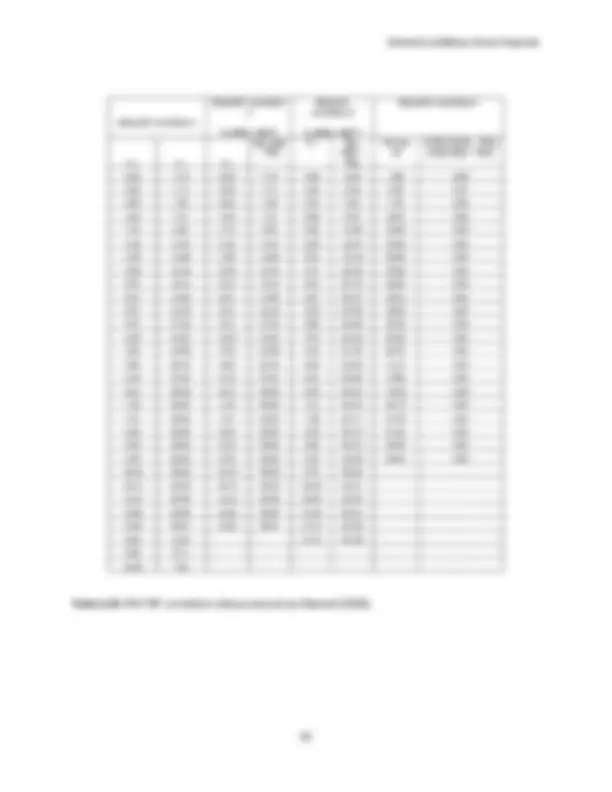
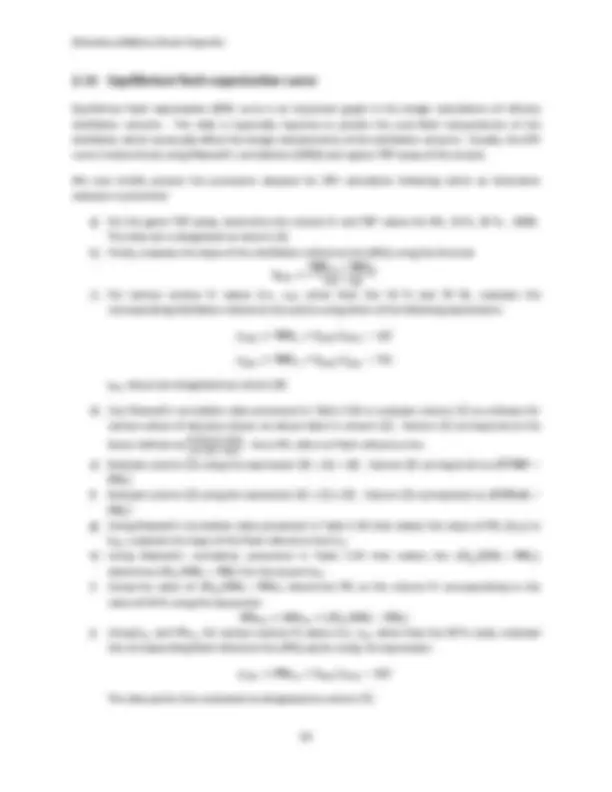
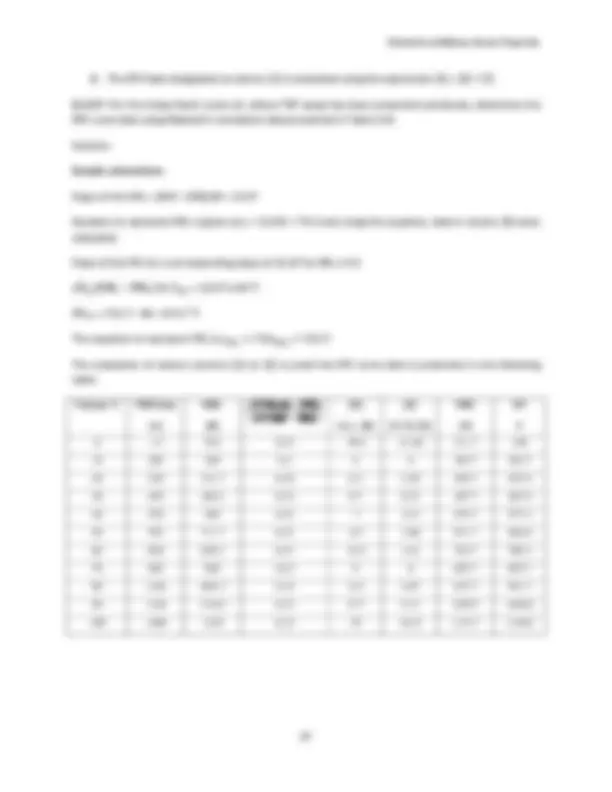
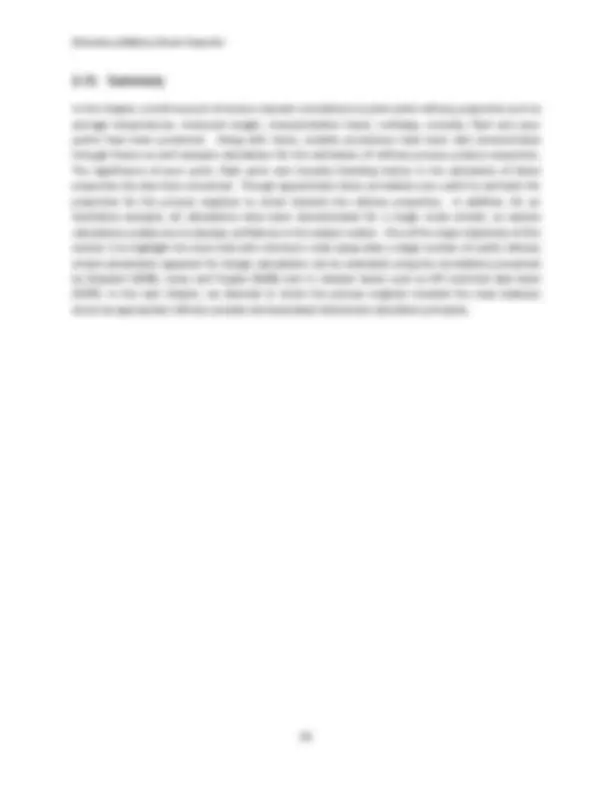
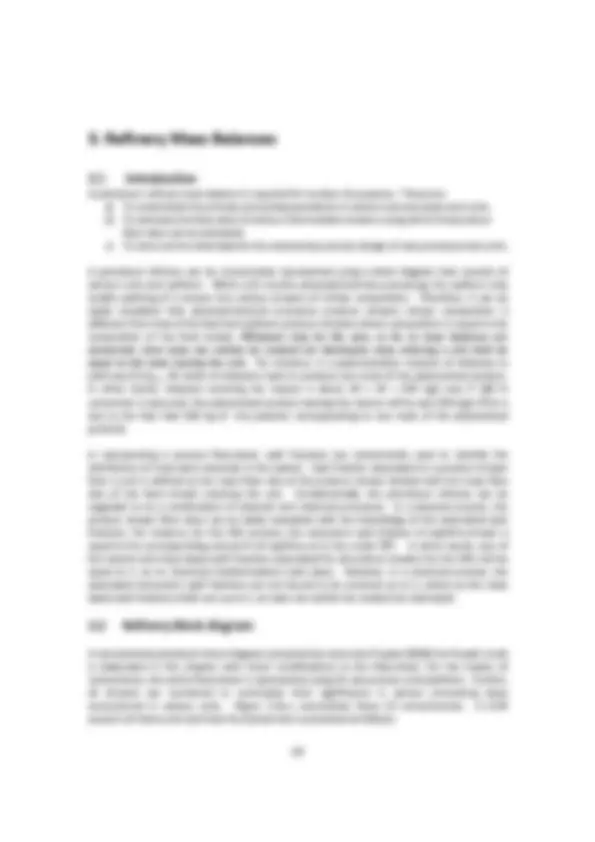
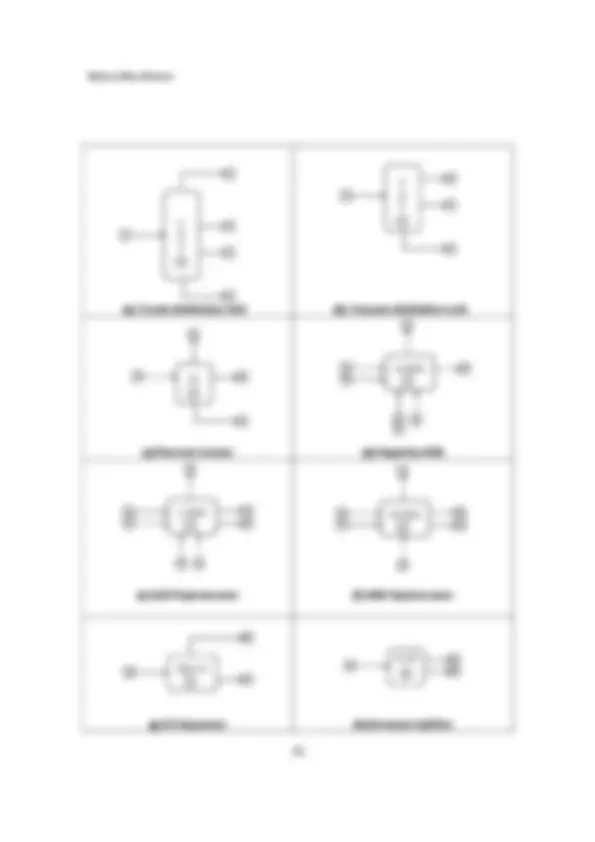
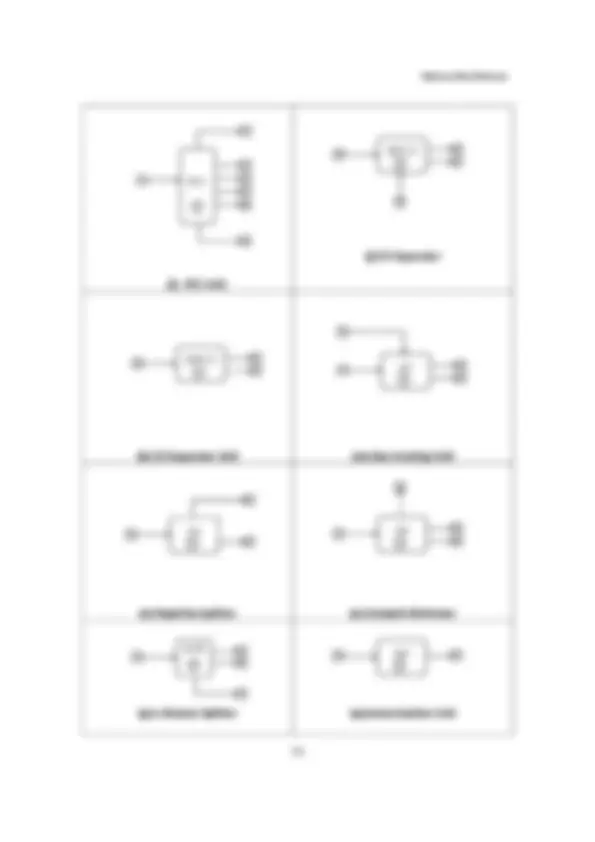
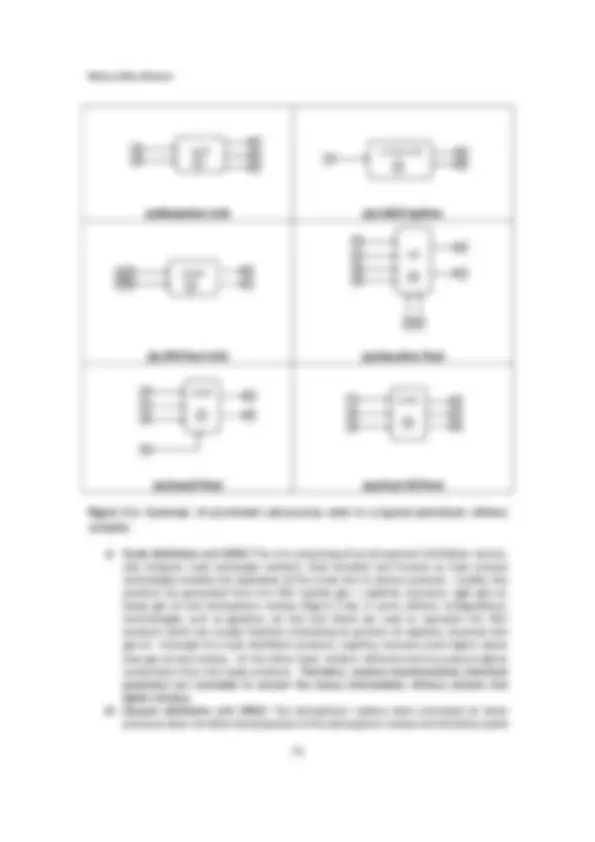
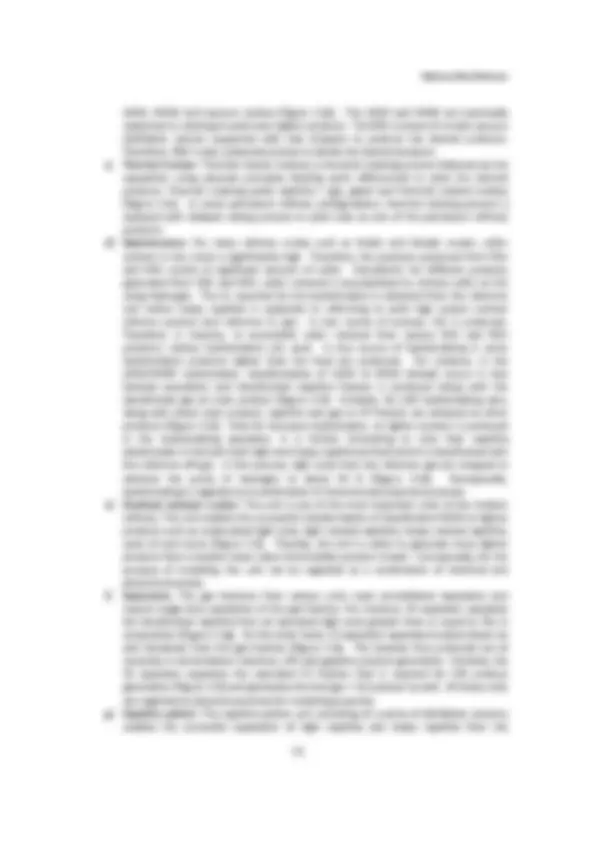
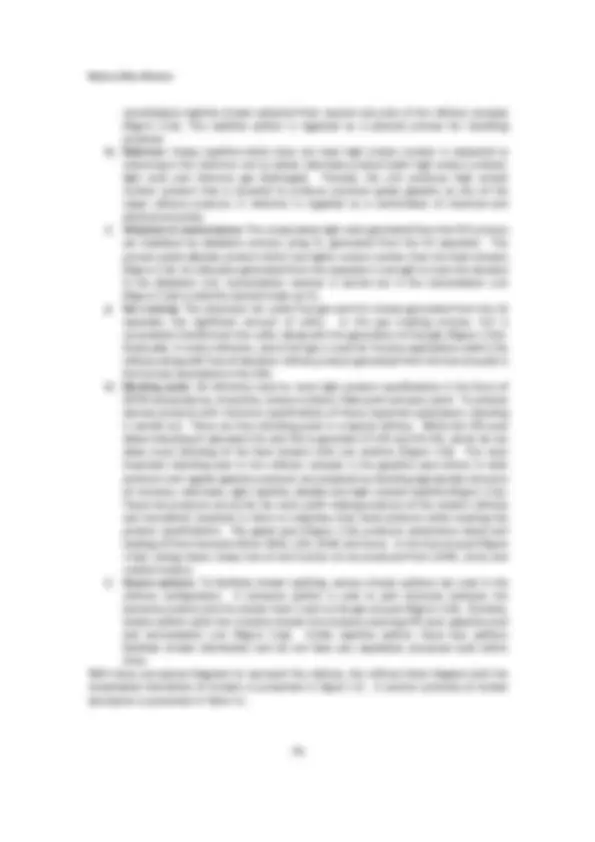
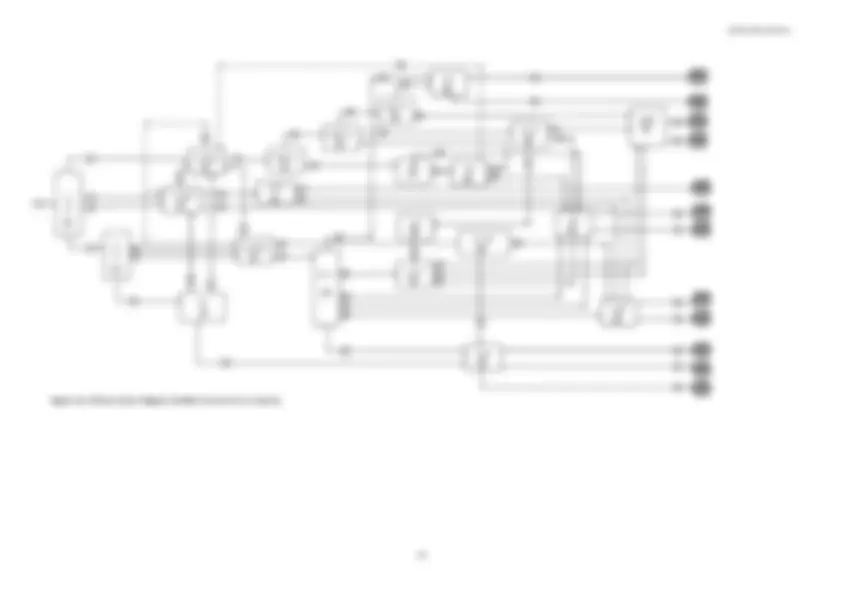
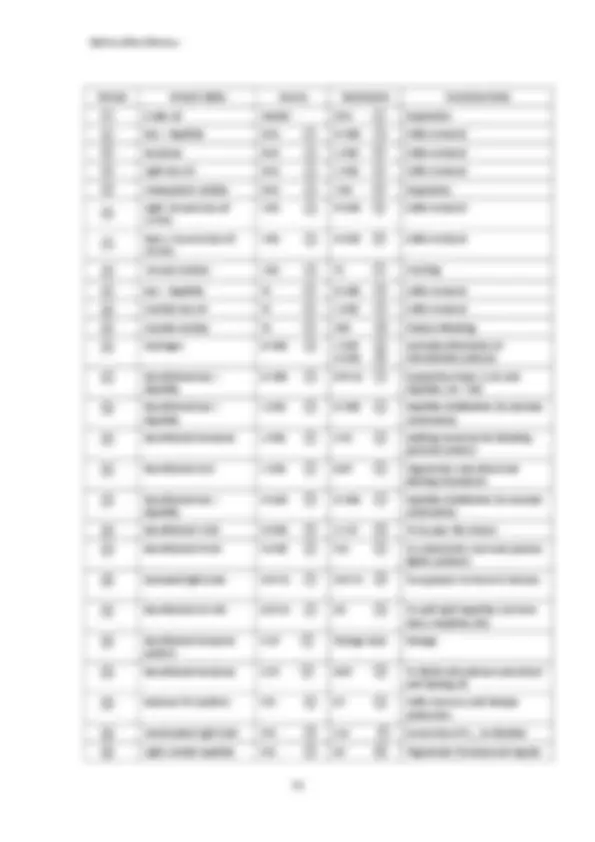
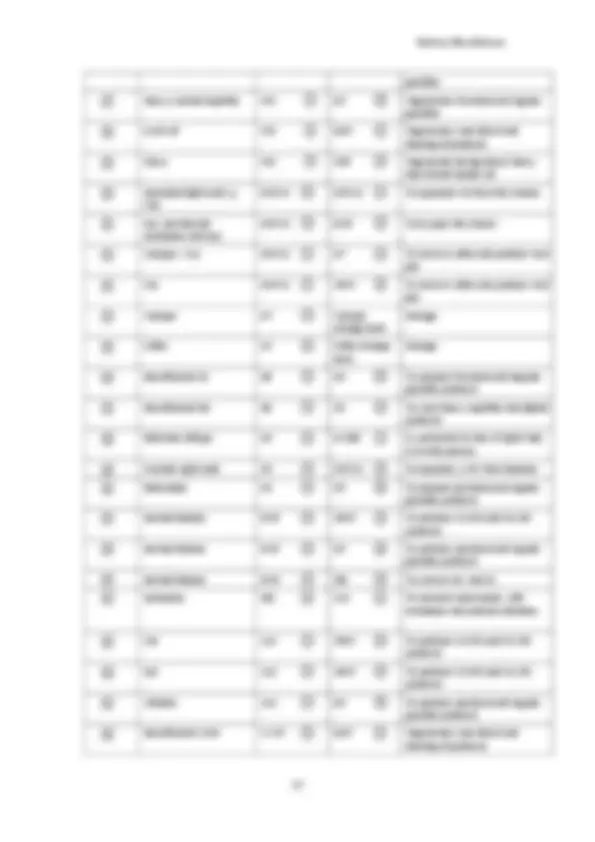
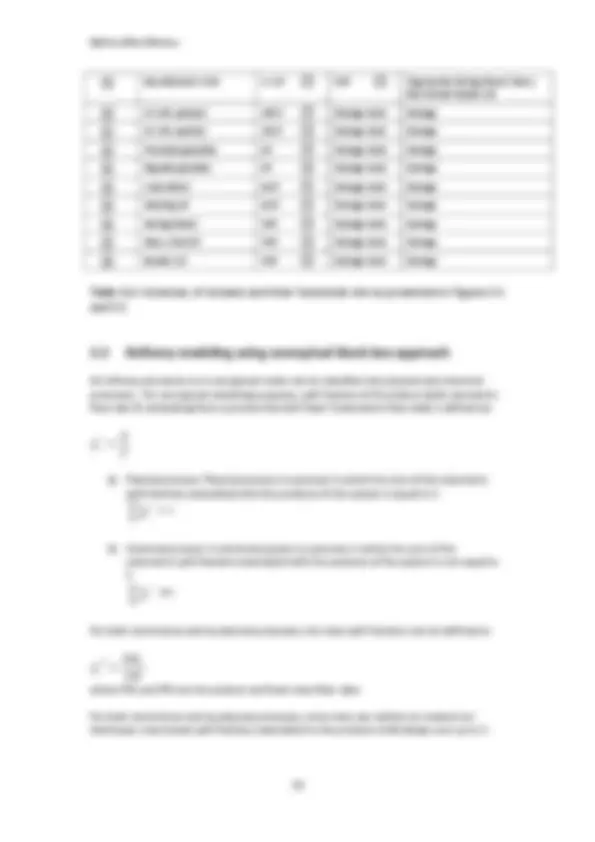
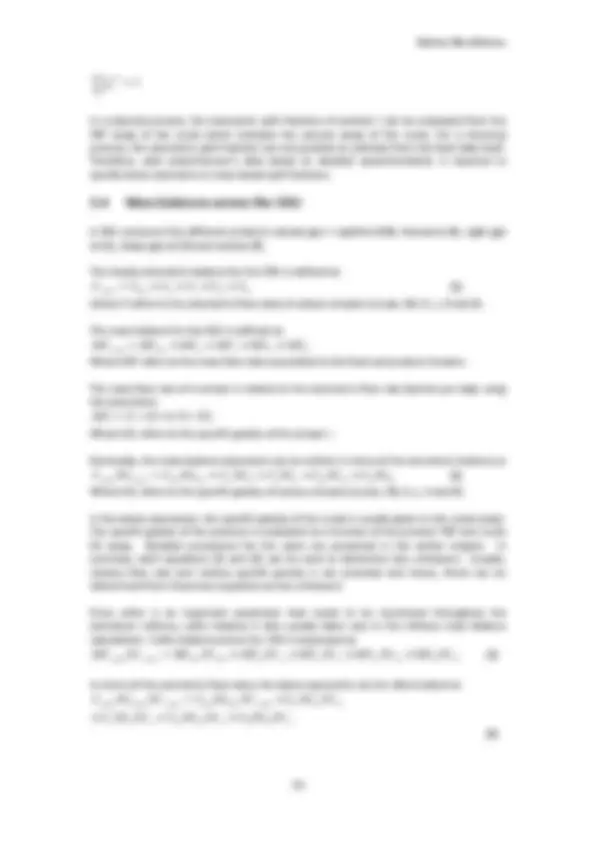
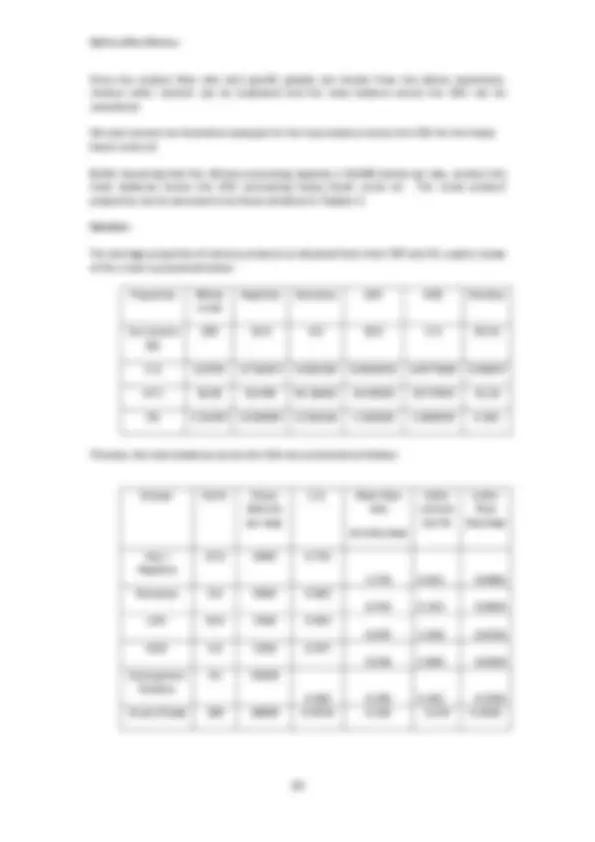
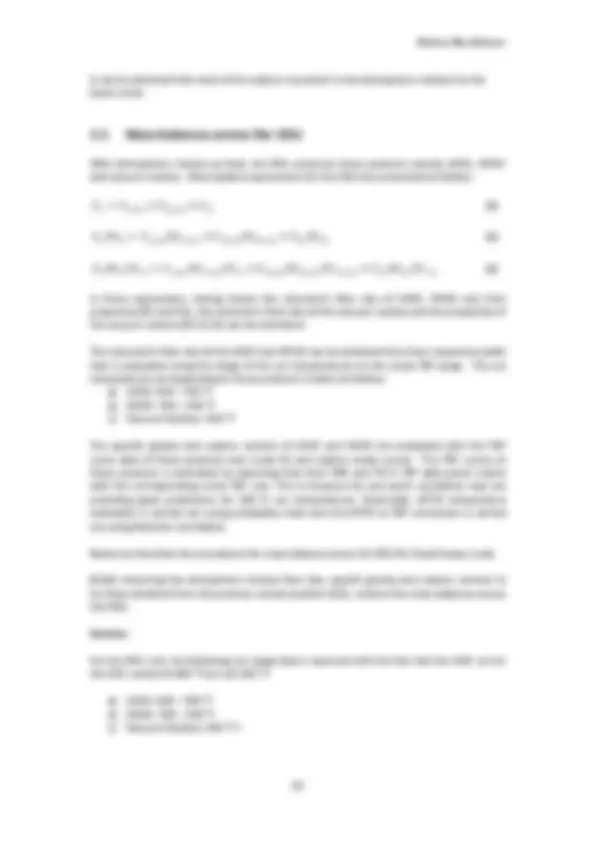
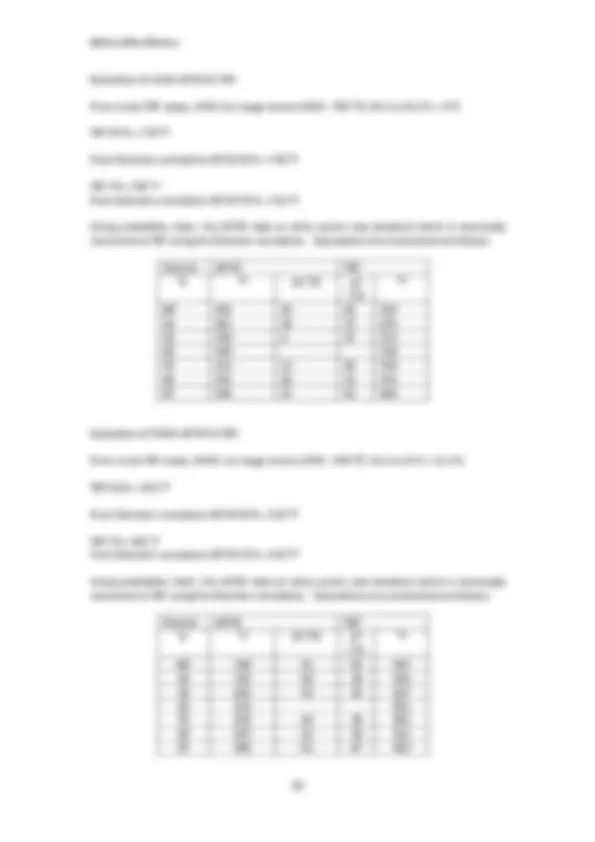
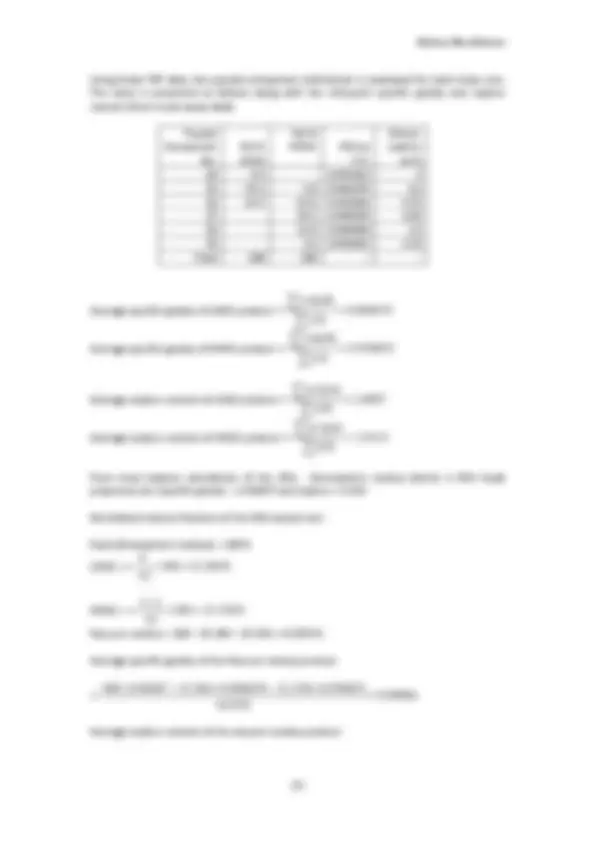
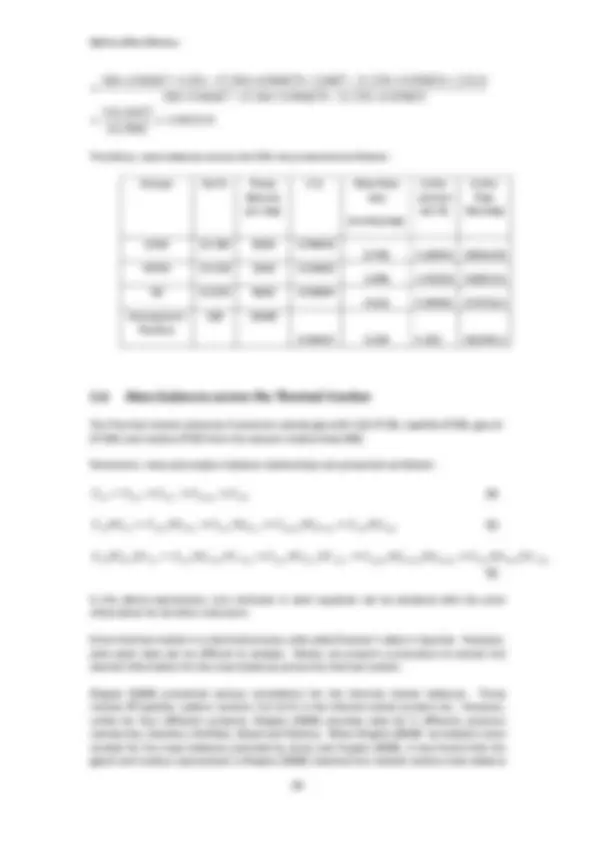
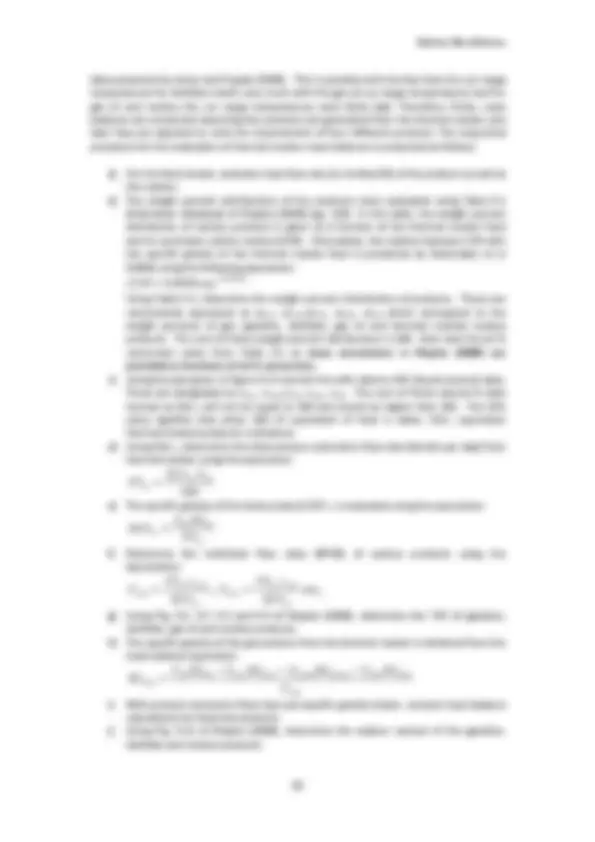
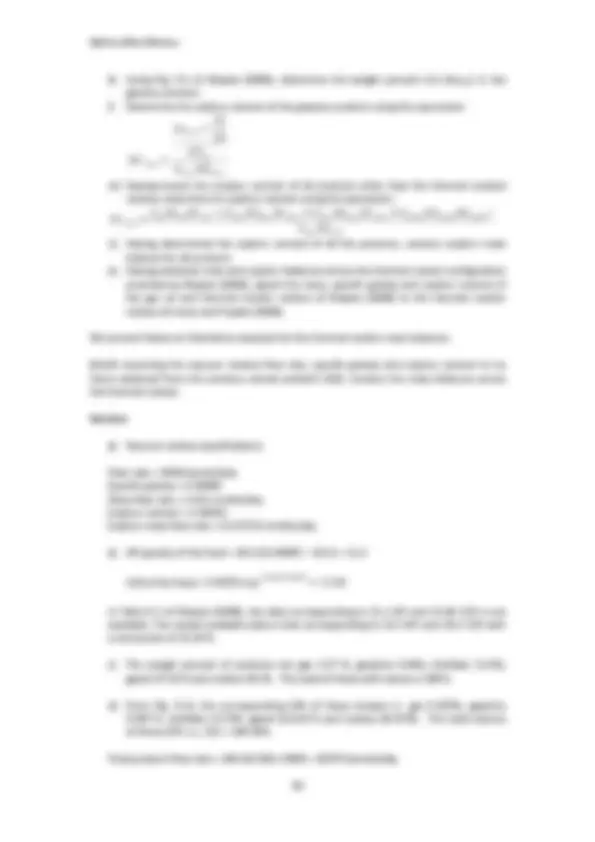
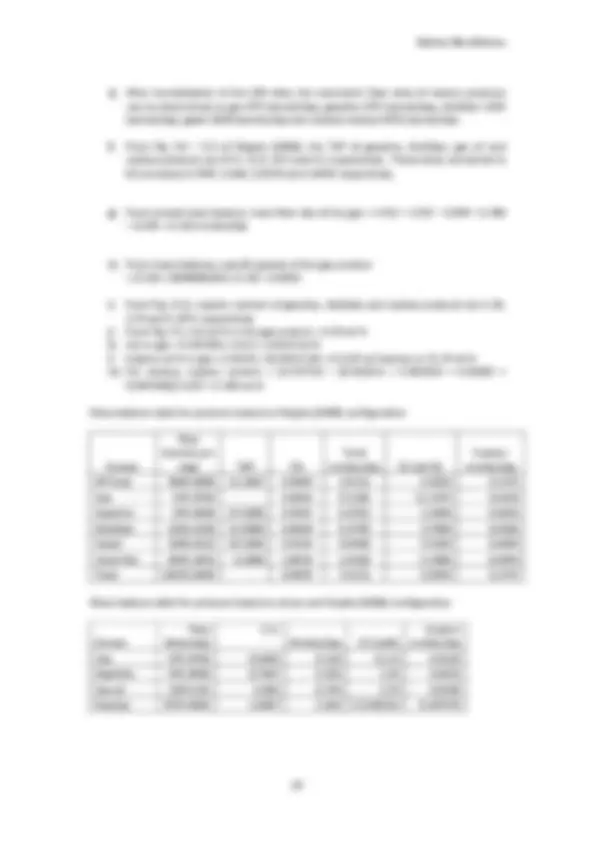
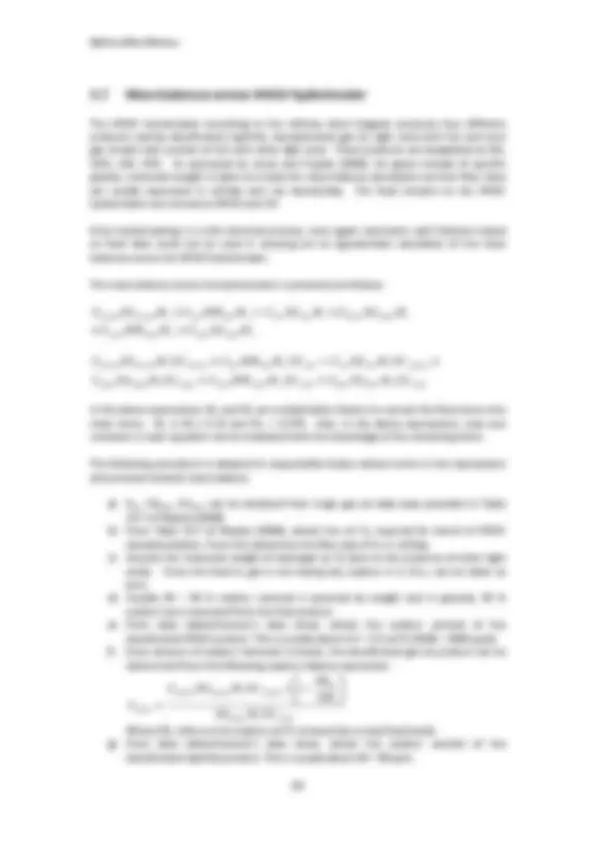
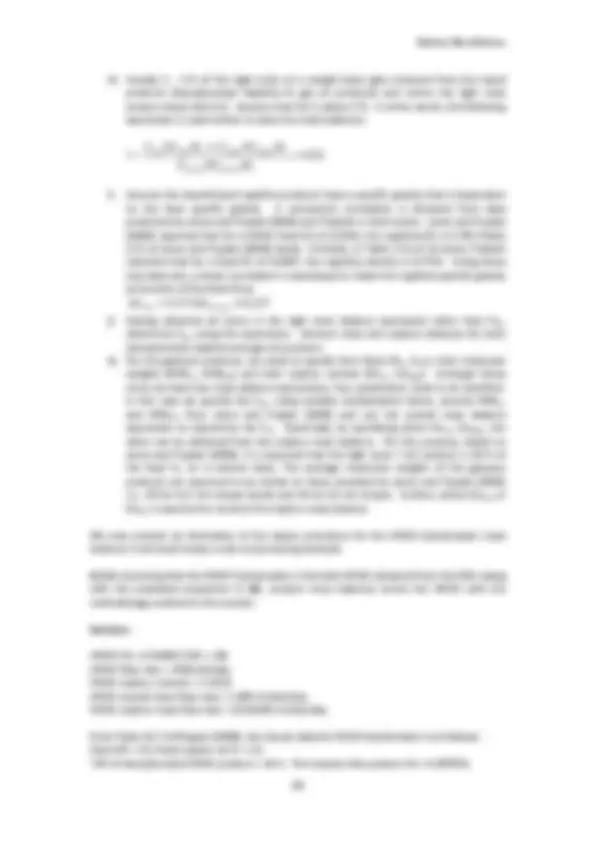
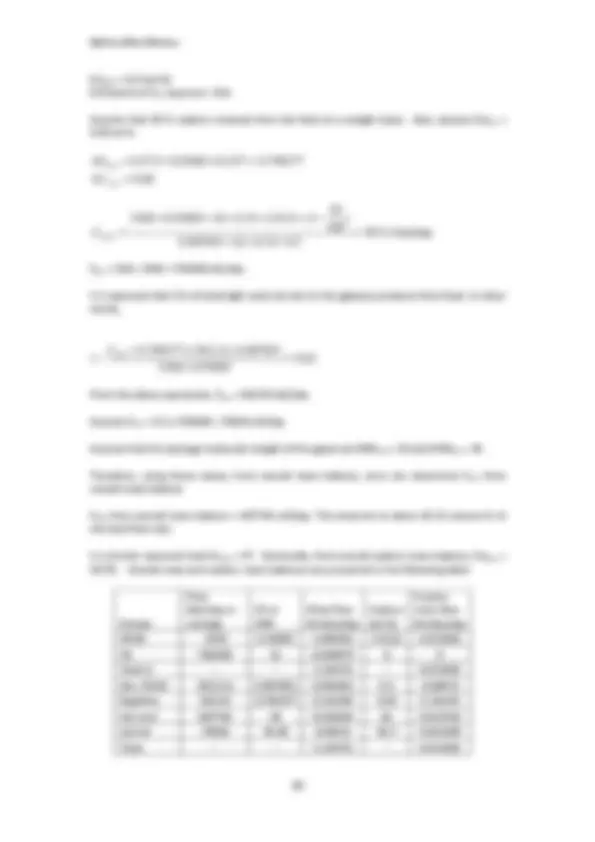
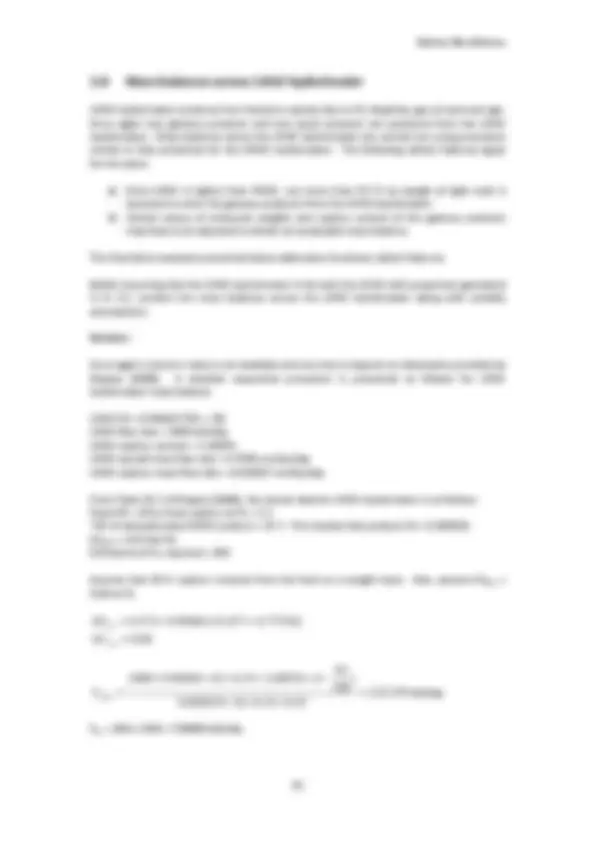
Study with the several resources on Docsity
Earn points by helping other students or get them with a premium plan
Prepare for your exams
Study with the several resources on Docsity
Earn points to download
Earn points by helping other students or get them with a premium plan
Community
Ask the community for help and clear up your study doubts
Discover the best universities in your country according to Docsity users
Free resources
Download our free guides on studying techniques, anxiety management strategies, and thesis advice from Docsity tutors
Notes on Refinery Process Design
Typology: Lecture notes
Uploaded on 02/11/2017
4
(3)1 document
1 / 193
This page cannot be seen from the preview
Don't miss anything!
ii
Preface
To fields draft of petroleumthe lecture refining notes in and the process specialized design. topic The of basic Refinery urge Process of extending Design my needs process expertise design inspecific both skills reading to Jonesthe design and Pujado of petroleum (2006) book refineries which startedI feel should in IIT beGuwahati, the primary and referencespecifically for after refinery thoroughly design. The student primary to learn objective upon ofdesign the lecture principles. notes While is to provideJones and a very Pujado simple (2006) and summarized lucid approach many for calculations a graduate in the form of Tables, for better explanations I always felt that calculations should be conducted and explained as well. With this sole objective I drafted the Lecture notes. Consisting necessary contentof three for main maturing chapters, in thethis fieldlecture of refinerynotes enables process a design.graduate In chemical the very engineer first chapter, to learn a very all introductory process design issue is presented of relating from the asubject philosophical matter perspective.of refinery processThereby, design the second to conventional chapter presents chemical a detailed to provide discussion a new approachof the estimation for conducting of essential refinery refinery mass stream balances properties. using theThe data third basechapter provided attempts by Maples elaborates (2000). towards The the fourth selection chapter of complexdeliberates distillation upon the reflux design ratio, of crudepump distillationaround unit unit duty with estimation further and diameter calculations. All design in all, of theheat lecture exchanger notes networks, did not present design someof light elementary end units anddesign design related of refinery chapters process pertaining absorbers. to the These will be taken up in the subsequent revisions of the Lecture notes. I hope that this lecture notes in Refinery Process Design will be a useful reference for both students as well as practicing engineers to systematically orient and mature in process refinery specialization.
Date: 16 th^ March 2010 ( IIT Dr. Guwahati Ramgopal Uppaluri )
iii
Dedication To Dr. T. D. Singh Founder Director, Bhaktivedanta Institute
Short biography of Dr. T. D. Singh: Dr. T. D. Singh received his Ph.D. in Physical Organic Chemistry from the University of California at Irvine, USA in
vi
List of Figures
Figure 2.1 TBP^ Curve^ of^ Saudi^ heavy^ crude^ oil.^5 Figure 2.2 o^ API^ Curve^ of^ Saudi^ heavy^ crude^ oil.^5 Figure 2.3 Sulfur^ content^ assay^ for^ heavy^ Saudi^ crude^ oil.^6 Figure 2.4 Illustration^ for^ the^ concept^ of^ pseudo‐component.^12 Figure 2.5 Probability^ chart^ developed^ by^ Thrift^ for^ estimating^ ASTM temperatures from any two known values of ASTM temperatures.
Figure 3.1 Summary^ of^ prominent^ sub‐process^ units^ in^ a^ typical petroleum refinery complex.
Figure 3.2 Refinery^ Block^ Diagram^ (Dotted^ lines^ are^ for^ H^2 stream).^75 Figure 4.1 A Conceptual diagram of the crude distillation unit (CDU) along with heat exchanger networks (HEN).
Figure 4.2 Design^ architecture^ of^ main^ and^ secondary^ columns^ of^ the CDU.
Figure 4.3 Envelope for the enthalpy balance to yield residue product temperature.
Figure 4.4 Heat^ balance^ Envelope^ for^ condenser^ duty^ estimation.^158 Figure 4.5 Envelope^ for^ the^ determination^ of^ tower^ top^ tray^ overflow.^159 Figure 4.6 Energy^ balance^ envelope^ for^ the^ estimation^ of^ reflux^ flow rate below the LGO draw off tray.
Figure 4.7 Heat^ balance^ envelope^ for^ the^ estimation^ of^ top^ pump around duty
Figure 4.8 (^) Heat balance envelope for the estimation of flash zone liquid reflux rate.
viii
Table 2.15 Hydrocarbon vapor enthalpy data for MEABP = 600 o^ F and K = 11 – 12.
Table 2.16 Hydrocarbon liquid enthalpy data for MEABP = 800 o^ F and K = 11 – 12.
Table 2.17 Hydrocarbon vapor enthalpy data for MEABP = 800 o^ F and K = 11 – 12.
Table 2.18 Vapor pressure data for hydrocarbons. 35 Table 2.19 End point correlation data presented by Good, Connel et. al. Data sets represent fractions whose cut point starts at 200 o^ F TBP or lower (Set A); 300 o^ F (Set B); 400 o^ F (Set C); 500 o^ F (Set D); 90% vol temperature of the cut Vs. 90 % vol TBP cut for all fractions (Set E).
Table 2.20 ASTM‐TBP correlation data from Edmister ethod. 39 Table 2.21 Blending Index and Viscosity correlation data. 58 Table 2.22 Flash point index and flash point correlation data 60 Table 2.23 Pour point and pour point index correlation data. 62 Table 2.24 EFV‐TBP correlation data presented by Maxwell (1950). 65 Table 3.1 Summary of streams and their functional role as presented in Figures 3.1 and 3.2.
Table 4.1 Packie’s correlation data to estimate the draw off temperature.
Table 4.2 Steam table data relevant for CDU design problem. 152 Table 4.3 Variation of specific gravity with temperature (a) Data range: SG = 0.5 to 0.7 at 60 o^ F (b) Data range: SG = 0.72 to 0.98 at 60 o (^) F.
Table 4.4 Fractionation criteria correlation data for naphtha‐kerosene products.
Table 4.5 Fractionation criteria correlation data for side stream‐side stream products.
Table 4.6 Variation of Kf (Flooding^ factor)^ for^ various^ tray^ and^ sieve specifications.
1. Introduction
1.1 Introduction Many a times, petroleum refinery engineering is taught in the undergraduate as well as graduate education in a technological but not process design perspective. While technological perspective is essential for a basic understanding of the complex refinery processes, a design based perspective is essential to develop a greater insight with respect to the physics of various processes, as design based evaluation procedures enable a successful correlation between fixed and operating costs and associated profits. In other words, a refinery engineer is bestowed with greater levels of confidence in his duties with mastery in the subject of refinery process design. 1.2 Process Design Vs Process Simulation A process design engineer is bound to learn about the basic knowledge with respect to a simulation problem and its contextual variation with a process design problem. A typical process design problem involves the evaluation of design parameters for a given process conditions. However, on the other hand, a typical process simulation problem involves the evaluation of output variables as a function of input variables and design parameters. For example, in a conventional binary distillation operation, a process design problem involves the specification of Pressure (P), Temperature (T), product distributions (D, B, x (^) B , xD ) and feed (F, x (^) F) to evaluate the number of stages (N), rectifying, stripping and feed stages (N (^) R , N (^) S, N (^) F), rectifying and stripping section column diameters (DR and D (^) S), condenser and re‐boiler duties (QC and Q (^) R ) etc. On the other hand, a process simulation problem for a binary distillation column involves the specification of process design parameters (N (^) R , N (^) S, N (^) F) and feed (F, xF ) to evaluate the product distributions (D, xD , B, xB ). For a binary distillation system, adopting a process design procedure or process simulation procedure is very easy. Typically, Mc‐Cabe Thiele diagram is adopted for process design calculations and a system of equations whose total number does not exceed 20 are solved for process simulation. For either case, generating a solution for binary distillation is not difficult. For multi‐component systems involving more than 3 to 4 components, adopting a graphical procedure is ruled out for the purpose of process design calculations. A short cut method for the design of multi‐ component distillation columns is to adopt Fenske, Underwood and Gilliland (FUG) method. Alternatively, for the rigorous design of multi‐component distillation systems, a process design problem is solved as a process simulation problem with an assumed set of process design parameters. Eventually commercial process simulators such as HYSYS or ASPEN PLUS or CHEMCAD or PRO‐II are used to match the obtained product distributions with desired product distributions. Based on a trail and error
Introduction
below to convey that the evaluation of these additional properties is mandatory in refinery process design: a) Sulfur content in various intermediate as well as product streams is always considered as an important parameter to monitor in the entire refinery. Therefore, evaluation of sulfur content in various streams in the refinery complex is essential. b) The viscosity of certain heavier products emanating from the fuel oil pool such as heavy fuel oil and bunker oil is always considered as a severe product constraint. Therefore, wherever necessary viscosity of process and product streams needs to be evaluated at convenience. For such cases, the evaluation of viscosity from blended intermediate stream viscosities is required. c) In similarity to the case evaluated for the above option (i.e., (b)), flash point and pour point need to be evaluated for a blended stream mixture. d) Equilibrium flash vaporization (EFV) curve plays a critical role in the design of distillation columns that are charged with partially vaporized feed. Therefore, the determination of EFV from TBP is necessary.
1.4 Refinery Property Estimation The following list summarizes the refinery process and product properties required for process design calculations:
2. Estimation of Refinery Stream Properties
2.1 Introduction In this chapter, we present various correlations available for the property estimation of refinery crude, intermediate and product streams. Most of these correlations are available in Maxwell (1950), API Technical Hand book (1997) etc. Amongst several correlations available, the most relevant and easy to use correlations are summarized so as to estimate refinery stream properties with ease. The determination of various stream properties in a refinery process needs to first obtain the crude assay. Crude assay consists of a summary of various refinery properties. For refinery design purposes, the most critical charts that are to be known from a given crude assay are TBP curve, o^ API curve and Sulfur content curve. These curves are always provided along with a variation in the vol % composition. Often, it is difficult to obtain the trends in the curves for the 100 % volume range of the crude. Often crude assay associated to residue section of the crude is not presented. In summary, a typical crude assay consists of the following information: a) TBP curve (< 100 % volume range) b) o^ API curve (< 100 % volume range) c) Sulfur content (wt %) curve (< 100 % volume range) d) Average o^ API of the crude e) Average sulfur content of the crude (wt %) An illustrative example is presented below for a typical crude assay for Saudi heavy crude oil whose crude assay is presented by Jones and Pujado (2006). A complete TBP assay of the Saudi heavy crude oil is obtained from elsewhere. Figures 2.1, 2.2 and 2.3 summarize the TBP, o^ API and sulfur content curves with respect to the cumulative volume %. Amongst these, the oAPI and % sulfur content graphs have been extrapolated to project values till a volume % of 100. This has been carried out to ensure that the evaluated values are in comparable range with the average o^ API and sulfur content reported for the crude in the literature. These values correspond to about 28.2 o^ API and 2.84 wt % respectively.
Estimation of Refinery Stream Properties
Volume %
0 20 40 60 80 100
Sulfur content (wt %)
0
1
2
3
4
5
6
Figure 2.3: Sulfur content assay for heavy Saudi crude oil.
2.2 Estimation of average temperatures The volume average boiling point (VABP) of crude and crude fractions is estimated using the expressions: ܸ ൌ் ܲܤܣ మబ^ ା்^ ఱబଷ ା்^ ఴబ (1)
ܸ ൌ் ܲܤܣ బ^ ାସ்^ ఱబ ା்^ భబబ (2) The mean average boiling point (MEABP), molal average boiling point (MABP) and weight average boiling point (WABP) is evaluated using the graphical correlations presented in Maxwell (1950). These are summarized in Tables 2.1 – 2.3 for both crudes and crude fractions. Where applicable, extrapolation of provided data trends is adopted to obtain the temperatures if graphical correlations are not presented beyond a particular range in the calculations. We next present an example to illustrate the estimation of the average temperatures for Saudi heavy crude oil.
o (^) F/vol%^ S^ TBP
Differentials to be added to values VABP of for VABP evaluating MEABP for various
Table 2.1: Tabulated Maxwell’s correlation data for the estimation of mean average boiling point
Estimation of Refinery Stream Properties
Table 2.3: Tabulated Maxwell’s correlation data for the estimation of molal average boiling point
Estimation of Refinery Stream Properties
Q 2.1: Using the TBP presented in Figure 2.1 and graphical correlation data (Table 2.1 – 2.3), estimate the average temperatures of Saudi heavy crude oil. Solution: a. Volume average boiling point Tv = t 20 +t 50 +t 80 /3 = (338+703+1104)/3= 715 0 F b. Mean average boiling point (from extrapolation) Slope = t 70 ‐t 10 / 60 = 965 ‐205/60= 12. From Table 2.
Mean average boiling point = T (^) v + ∆ T =715 – 73.0895 = 641.91 0 F c. Weight average boiling point (from extrapolation) Slope = t 70 ‐t 10 / 60 = 965 ‐205/60= 12. From Table 2.
Weight average boiling point = T (^) v + ∆ T =715 + 37.215 = 752.21 0 F d. Molal average boiling point (from extrapolation) Slope = t 70 ‐t 10 / 60 = 965 ‐205/60= 12. From Table 2.
Molal average boiling point = T (^) v + ∆ T =715 – 179.3495 = 535.65 0 F