
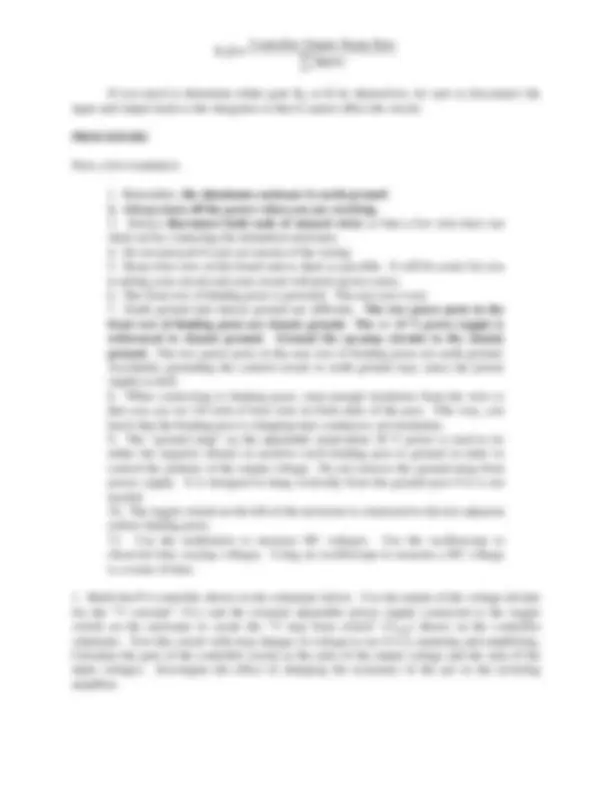
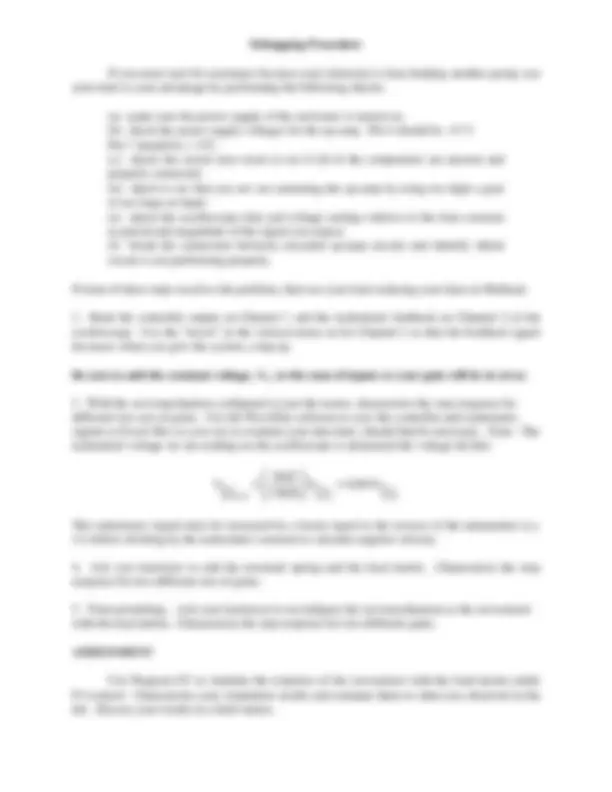
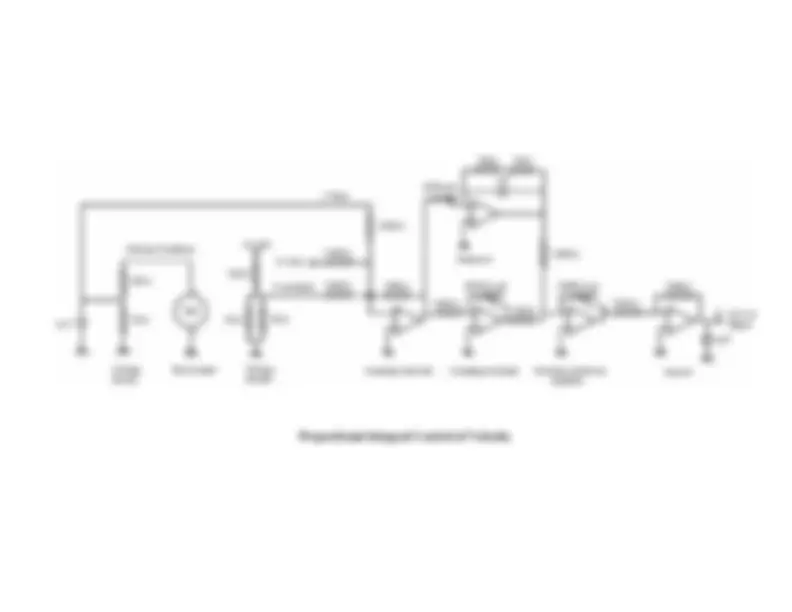
Study with the several resources on Docsity
Earn points by helping other students or get them with a premium plan
Prepare for your exams
Study with the several resources on Docsity
Earn points to download
Earn points by helping other students or get them with a premium plan
Community
Ask the community for help and clear up your study doubts
Discover the best universities in your country according to Docsity users
Free resources
Download our free guides on studying techniques, anxiety management strategies, and thesis advice from Docsity tutors
Instructions for lab 10 in me 479: dynamic systems, controls and mechatronics at lafayette college, focusing on proportional-integral (p-i) control of angular velocity in a servomechanism. The theoretical background of p-i control, pre-lab preparations, maximum control signal limitations, and procedures for determining controller gains. Students are expected to build and test the p-i controller circuit, read and analyze signals on an oscilloscope, and characterize the step response of the servomechanism.
Typology: Lab Reports
1 / 5
This page cannot be seen from the preview
Don't miss anything!
© Dr. Seeler Department of Mechanical Engineering Fall 2004 Lafayette College ME 479: Dynamic Systems, Controls and Mechatronics Laboratory
Lab 10: Proportional-Integral (P-I) Control of Angular Velocity
The objective of Lab 10 is to place the angular velocity of servomechanism under proportional and integral (P-I) control.
THEORETICAL BACKGROUND
The proportional aspect of the control yields an instantaneous control action in response to an error. The integral action will increase the control action in response to persistent error. P- I controls adds an open-loop zero and a pole at the origin.
PRE-LAB
Review and understand the control circuit shown below. The circuit is significantly more complicated than those we have used previously because of the need to calculate the error and then act on it with both an inverting amplifier and an integrator. The output of the inverting amplifier and integrator are then summed to produce the control signal. We will use two “dual” op-amps and one single op-amp to implement this schematic. Dual op-amps are eight pin DIPs which contain two independent op-amps. The “pin-out” of a dual op-amp DIP is different than a single op-amp DIP. The +15 VDC and -15 VDC power supply pins are the top right (pin 8) and lower left (pin 4), respectively. The input and output pins of the two op-amps are on opposite sides of the DIP. The output pin is the top pin, the inverting input is the middle pin, and the non-inverting input is the bottom pin, as shown on the figure below. Dual op-amps have the generic designation 1458.
Notice that there are no pin numbers on the controller circuit schematic. Plan your circuit and add the pin numbers to the schematic BEFORE YOU COME TO LAB.
In normally, we drive a motor to achieve the fastest response possible, which usually results in a motor drive operating in its non-linear range. However, this laboratory exercise is intended to allow us to test the accuracy of linear control theory prediction of the response of the plant under closed-loop control. Consequently, we must prevent the pulse width modulated servoamplifier from saturating. The maximum output of the servoamplifier is approximately it power supply voltage of 56.5 VDC. The gains of the different servoamplifiers vary, but they are all less than 8. Therefore, if we use a maximum allowable servoamplier output voltage of slightly less than the power supply voltage, say 52 VDC, then we can calculate an upper limit for the controller output u which will prevent the servoamplifier from saturating by dividing the maximum allowable servoamp output by the assumed servoamplifier gain of 8.
The servoamplifier will not saturate if the maximum control signal u(t)max is:
max
52 volts u(t) 6.5 volts 8
We must keep the maximum control signal from exceeding that which would demand a greater voltage from the servoamplifier than it can supply. Both the size of the input step, ∆Vstep, and the gains, K, Kp and KI, affect the magnitude of the control signal. Read the control signal u(t) on channel one of the oscilloscope. If it exceeds 6.5 volts for a given gain, then reduce the step size.
The control signal u(t) is:
t t p I p c step Tach I c step Tach 0 0
u(t) K K e(t) K e(t)dt K K v v v K v v v dt
DETERMINING CONTROLLER GAINS KP, KI, and K
Make sure that the servoamplifier power supply is unplugged until you have tested your control circuit and determined the controller gains.
Test the controller circuit by giving it a step input Vstep < - Vconstant so that the error signal will change sign when the step is toggled on and off. (If the error signal does not change sign, then the integrator will saturate.) You should see the superposition of proportional and integral control action. Determine the proportional and integral gains from the initial step of the control signal and the slope of the control signal.
p
Initial Controller Output Step K K Inputs
The procedure for determining the integrator gain KI requires that the error signal change sign. This will be done by using a NEGATIVE step input of approximately -0.5 VDC from the adjustable power supply. A negative voltage will be created by moving the ground strap of the power supply from the negative (black) terminal to the positive (red) terminal.
Debugging Procedure
If you must wait for assistance because your instructor is busy helping another group, use your time to your advantage by performing the following checks:
(a) make sure the power supply of the enclosure is turned on. (b) check the power supply voltages for the op-amp. Pin 4 should be -15 V. Pin 7 should be + 15V. (c) check the circuit once more to see if all of the components are present and properly connected. (d) check to see that you are not saturating the op-amp by using too high a gain or too large an input. (e) check the oscilloscope time and voltage settings relative to the time constant or period and magnitude of the signal you expect. (f) break the connection between cascaded op-amp circuits and identify which circuit is not performing properly.
If none of these steps resolves the problem, then use your time reducing your data on Mathcad.
Be sure to add the constant voltage, VC, to the sum of inputs or your gain will be in error.
Tach Tach Tach Measured Actual Actual
The tachometer signal must be increased by a factor equal to the inverse of the attenuation (i.e.
Use Program CC to simulate the response of the servomotor with the load inertia under P-I control. Characterize your simulation results and compare them to what you observed in the lab. Discuss your results in a brief memo.
Proportional-Integral Control of Velocity