
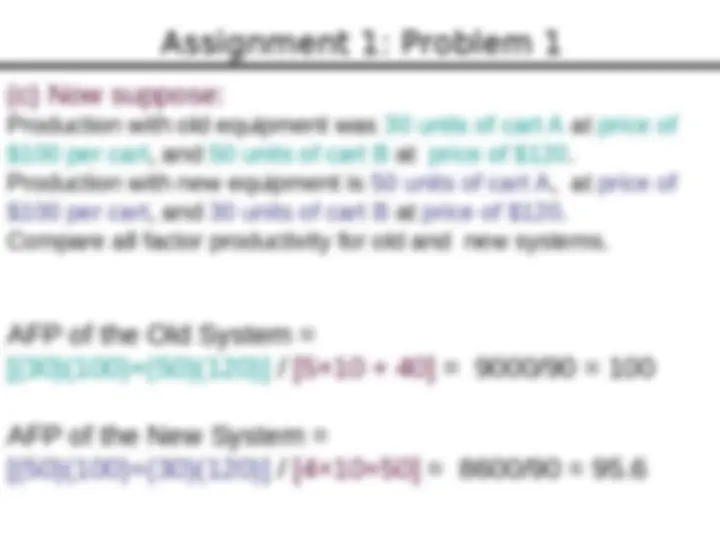
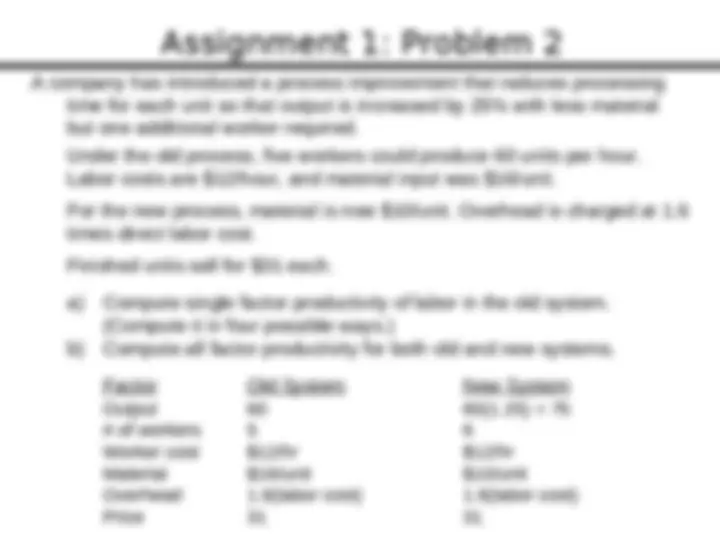
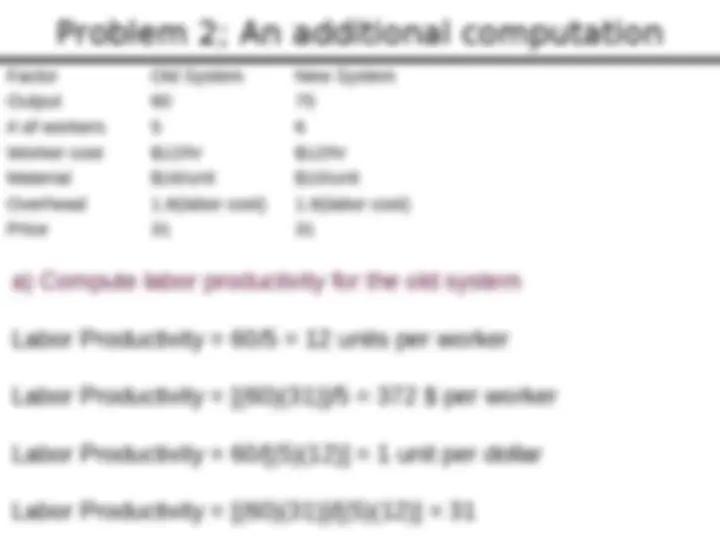
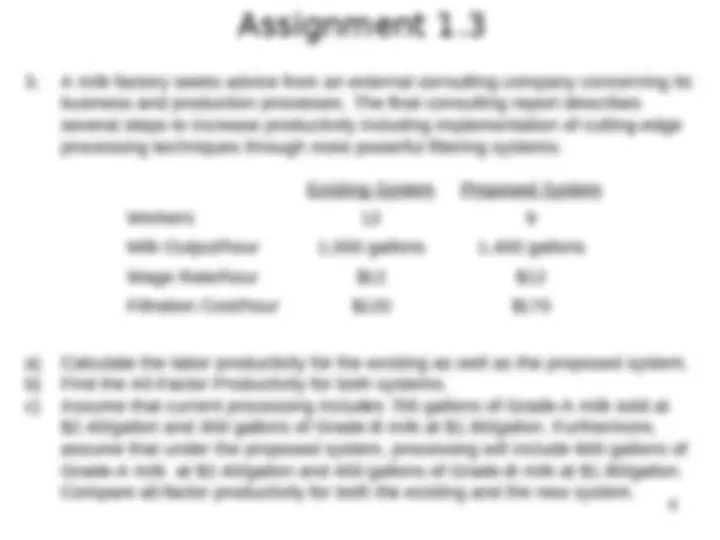
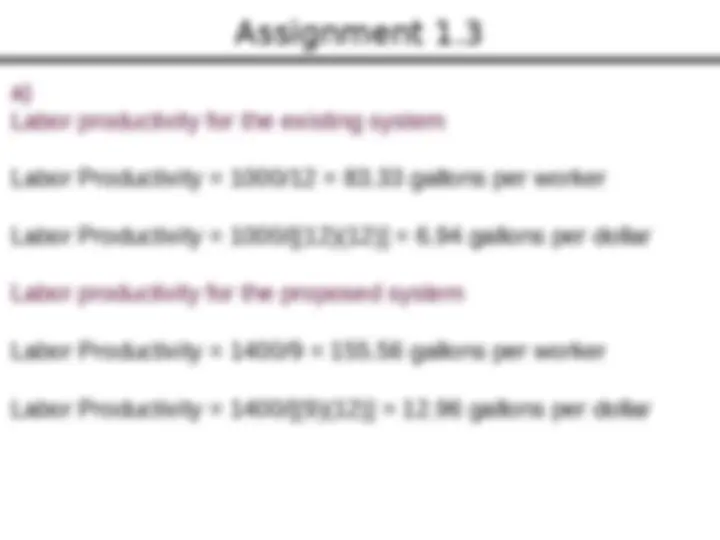
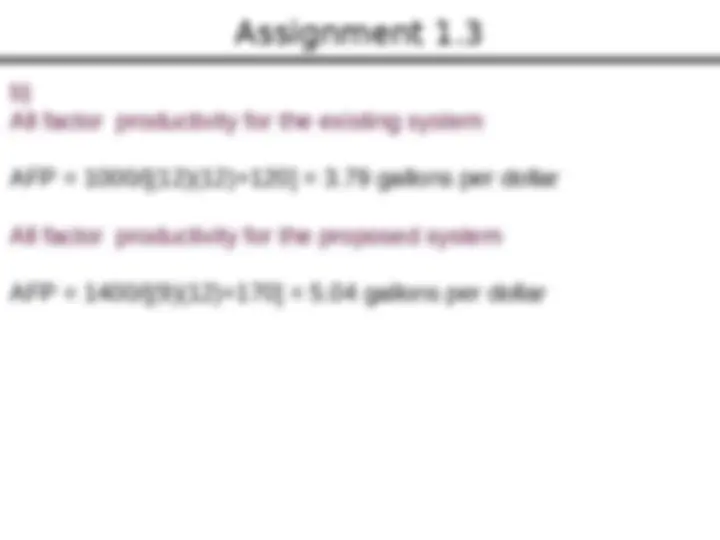
Study with the several resources on Docsity
Earn points by helping other students or get them with a premium plan
Prepare for your exams
Study with the several resources on Docsity
Earn points to download
Earn points by helping other students or get them with a premium plan
Community
Ask the community for help and clear up your study doubts
Discover the best universities in your country according to Docsity users
Free resources
Download our free guides on studying techniques, anxiety management strategies, and thesis advice from Docsity tutors
prProductivity and management prpoble,s solutuono
Typology: Assignments
1 / 11
This page cannot be seen from the preview
Don't miss anything!
A company that makes shopping carts for supermarkets recently purchased some new equipment that reduced the labor content of the jobs needed to produce shopping carts. The information regarding the old system (before adding the new equipment) and after adding the new equipment are given below. Current System New Equipment Added Output/hr 80 84 Workers 5 4 Wage/hr $10 $ Machine/hr $40 $ a) Compute labor productivity for both the Old System and the New System b) Compute AFP productivity for both the Old System and the New System c) Suppose production with old equipment was 30 units of cart A at price of $100 per cart, and 50 units of cart B at price of $120. Also suppose that production with new equipment is 50 units of cart A, at price of $100 per cart, and 30 units of cart B at price of $120. Compare all factor productivity for old and new systems.
Output 60 60(1.25) = 75
Worker cost $12/hr $12/hr Material $16/unit $10/unit Overhead 1.6(labor cost) 1.6(labor cost) Price 31 31
Factor Old System New System Output 60 75
Worker cost $12/hr $12/hr Material $16/unit $10/unit Overhead 1.6(labor cost) 1.6(labor cost) Price 31 31
Factor Old System New System Output 60 75
Worker cost $12/hr $12/hr Material $16/unit $10/unit Overhead 1.6(labor cost) 1.6(labor cost) Price 31 31
8