
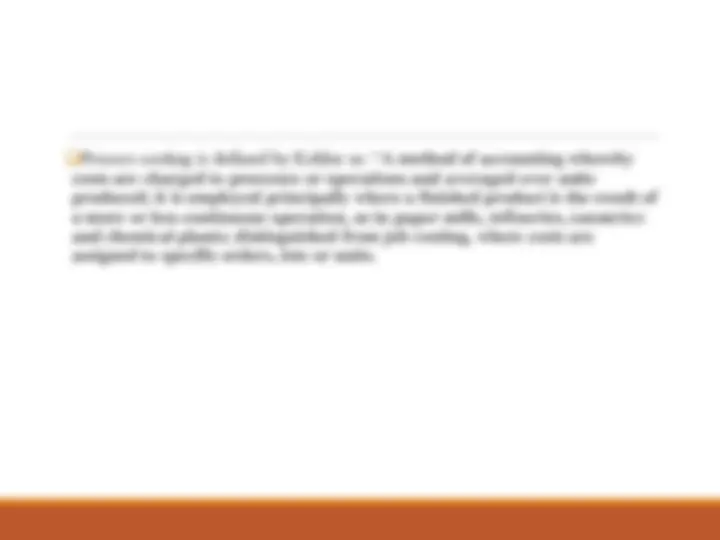
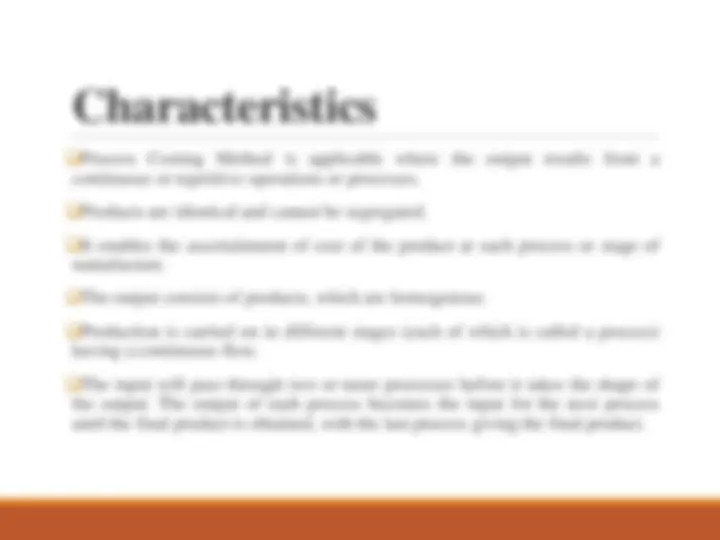
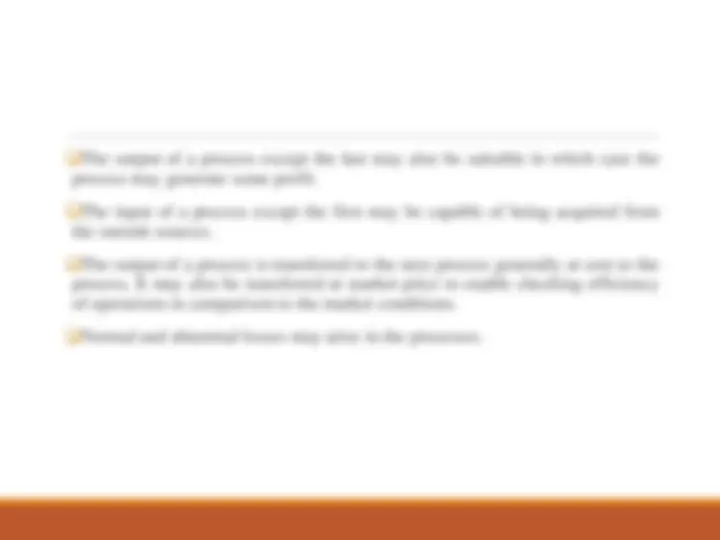
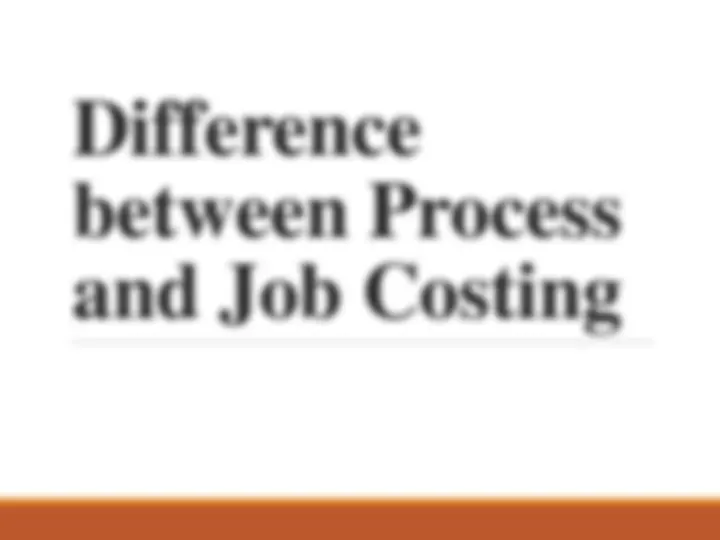
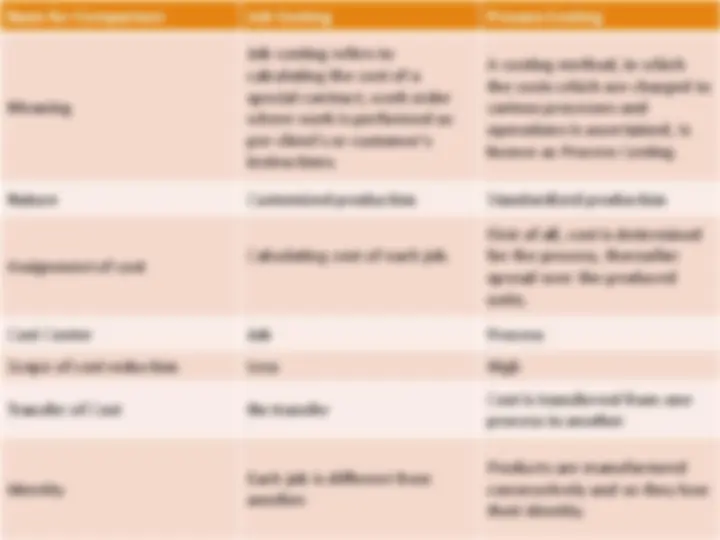
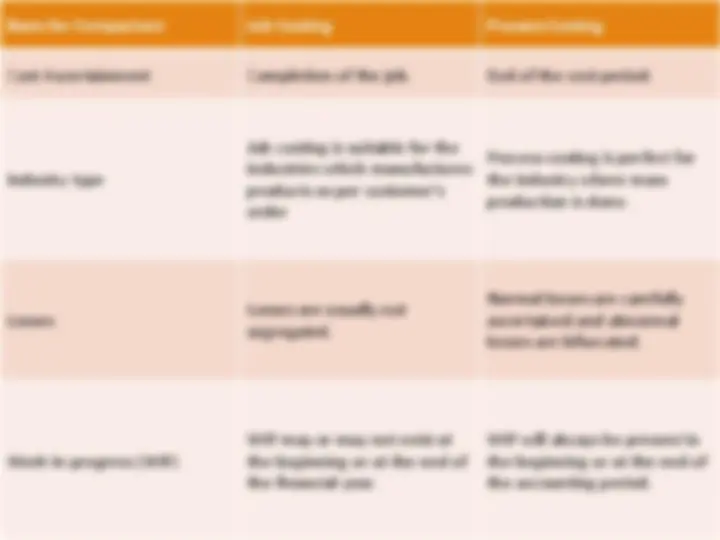
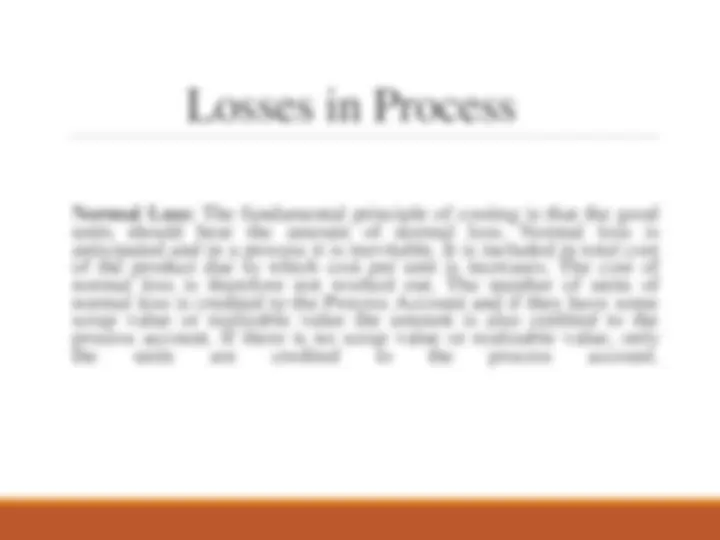
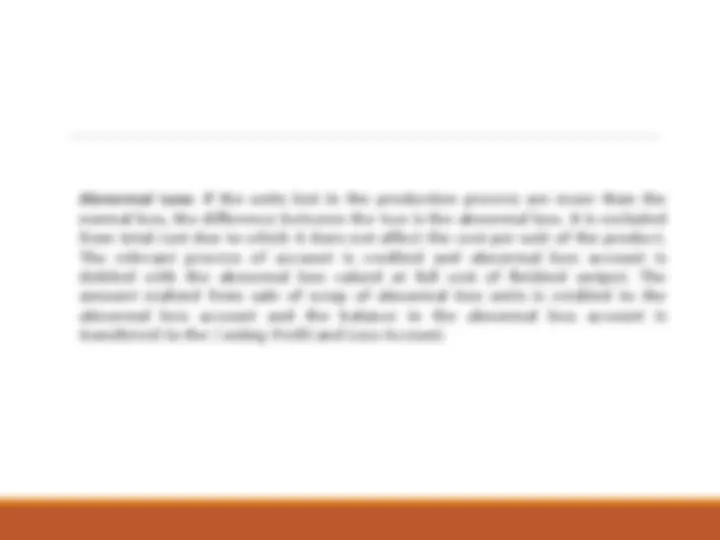

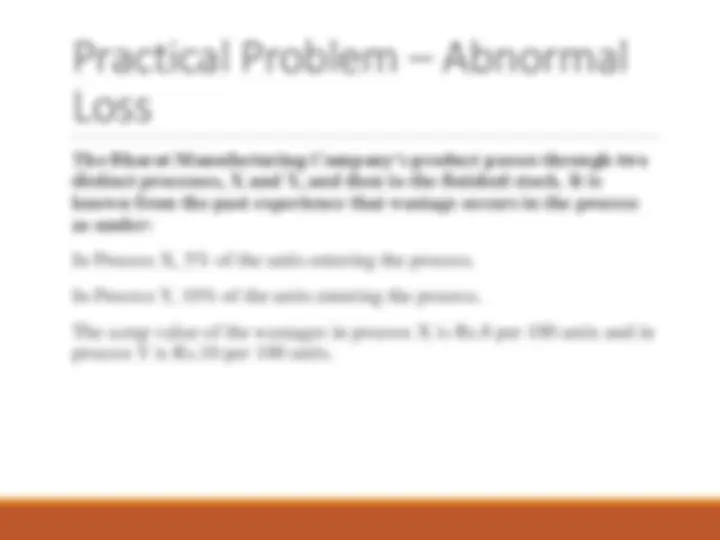
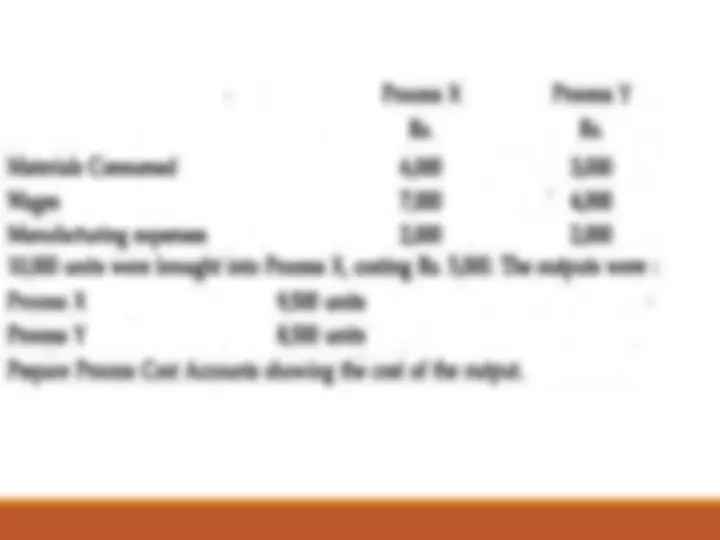
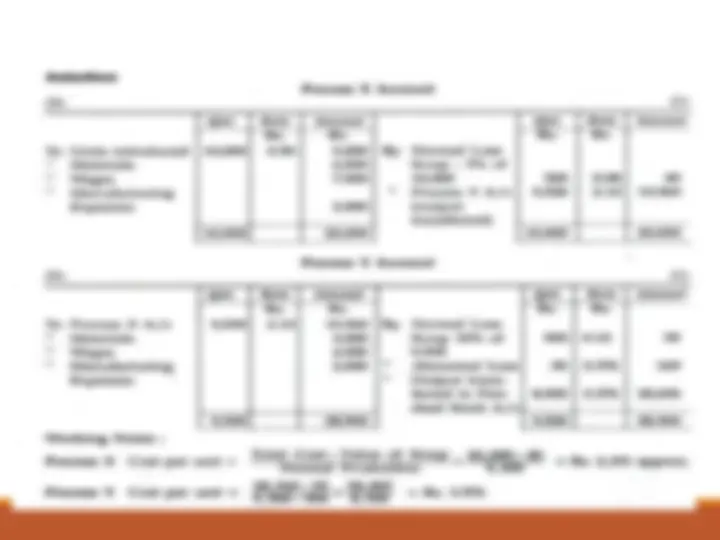

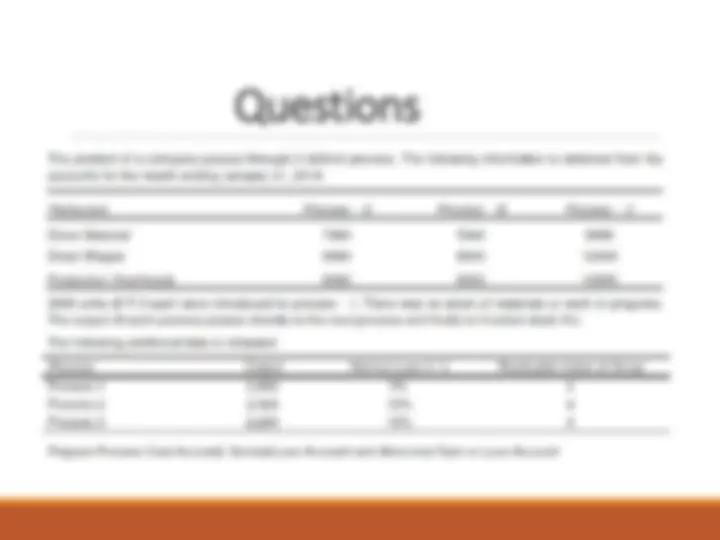
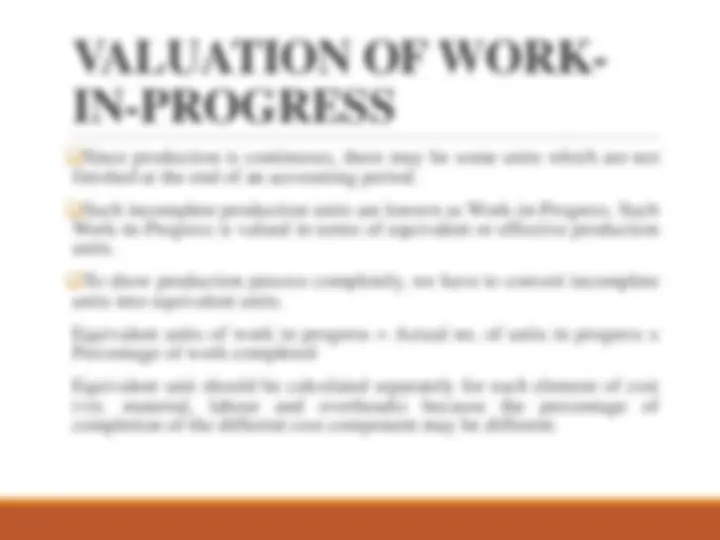
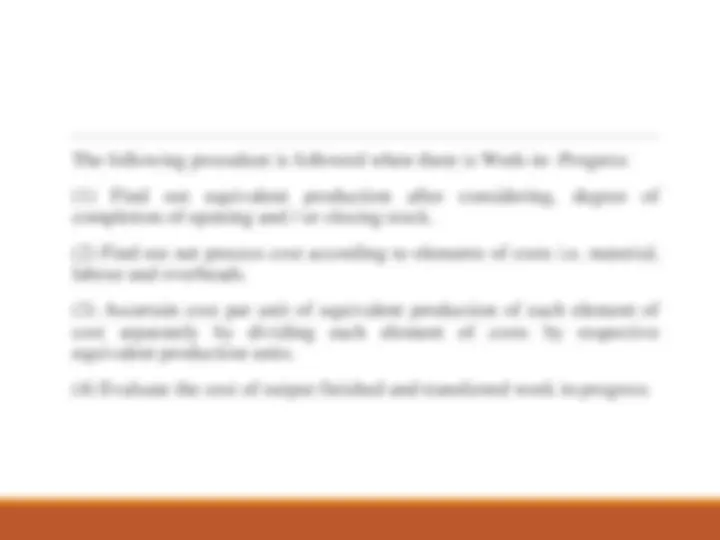
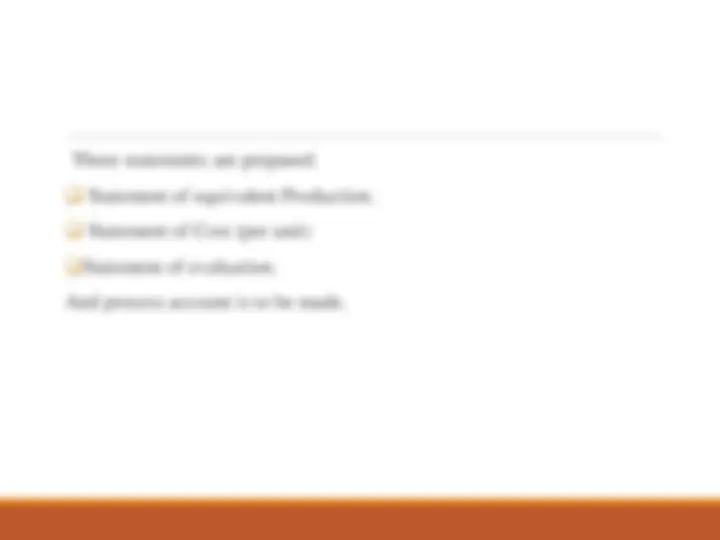
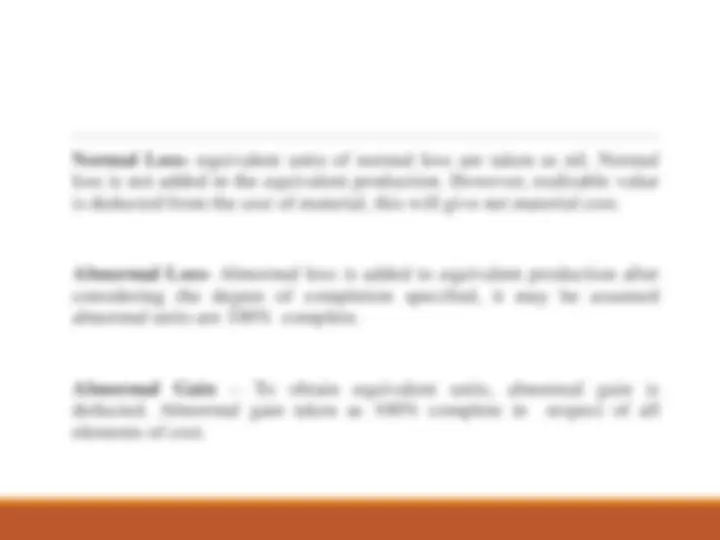
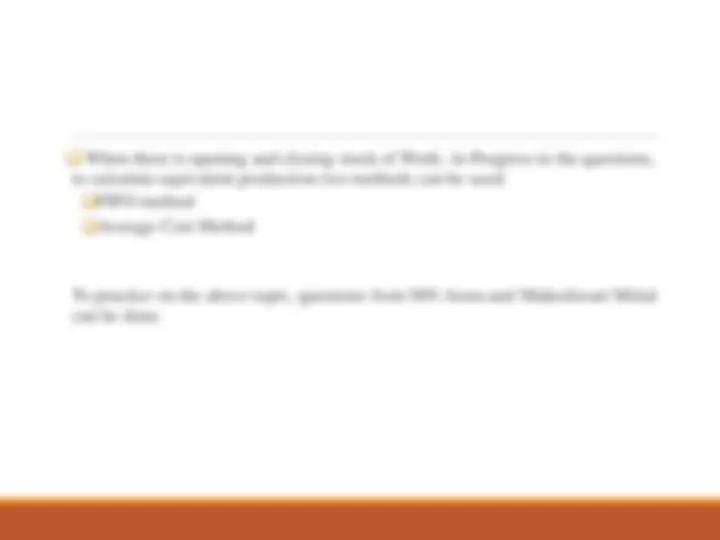
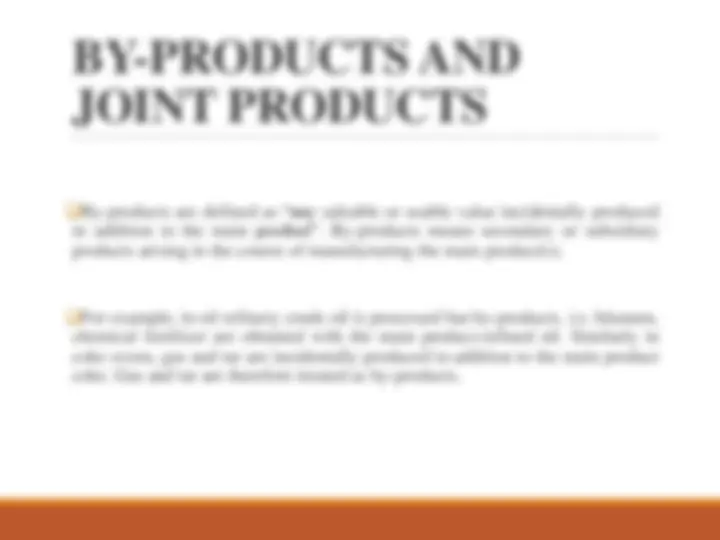
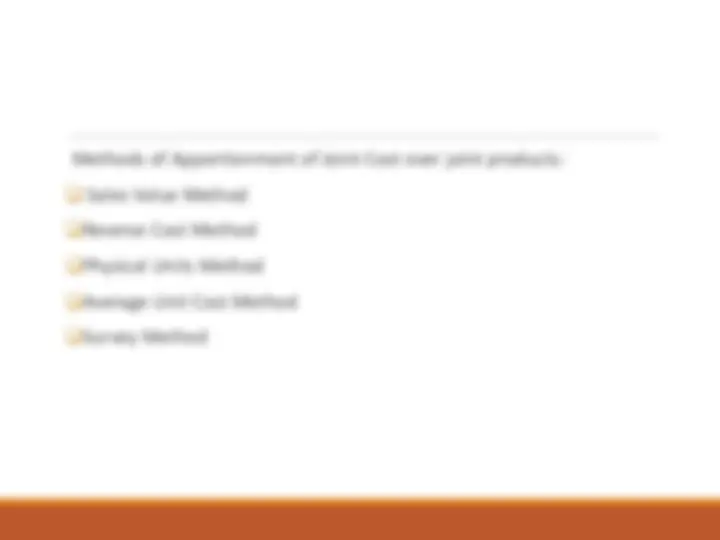
Study with the several resources on Docsity
Earn points by helping other students or get them with a premium plan
Prepare for your exams
Study with the several resources on Docsity
Earn points to download
Earn points by helping other students or get them with a premium plan
Community
Ask the community for help and clear up your study doubts
Discover the best universities in your country according to Docsity users
Free resources
Download our free guides on studying techniques, anxiety management strategies, and thesis advice from Docsity tutors
Process costing is an accounting method used to ascertain the cost of production at each process or stage of manufacture in industries where output results from continuous or repetitive operations. This method enables the determination of process costs periodically and the easy allocation of expenses to processes, making it suitable for standardized production. However, it has some disadvantages, such as the historical value of costs and the estimation of work-in-progress. the characteristics, advantages, and disadvantages of process costing, as well as its differences from job costing.
Typology: Study notes
1 / 29
This page cannot be seen from the preview
Don't miss anything!
❑Process costing is a method of operation costing which is used to ascertain the cost of production at each process, operation or stage of manufacture, where processes are carried in having one or more of the following features: ❑Where the product of one process becomes the material of another process or operation ❑Where there is simultaneous production at one or more process of different products, with or without by product, ❑Where, during one or more processes or operations of a series, the products or materials are not distinguishable from one another, as for instance when finished products differ finally only in shape or form.
❑Process Costing Method is applicable where the output results from a continuous or repetitive operations or processes. ❑Products are identical and cannot be segregated. ❑It enables the ascertainment of cost of the product at each process or stage of manufacture. ❑The output consists of products, which are homogenous. ❑Production is carried on in different stages (each of which is called a process) having a continuous flow. ❑The input will pass through two or more processes before it takes the shape of the output. The output of each process becomes the input for the next process until the final product is obtained, with the last process giving the final product.
❑The output of a process except the last may also be saleable in which case the process may generate some profit. ❑The input of a process except the first may be capable of being acquired from the outside sources. ❑The output of a process is transferred to the next process generally at cost to the process. It may also be transferred at market price to enable checking efficiency of operations in comparison to the market conditions. ❑Normal and abnormal losses may arise in the processes.
❑Cost obtained at the end of the accounting period are only of historical value and are not very useful for effective control. ❑Valuation of work-in-progress is generally done of estimated basis which introduces further inaccuracies in total cost. ❑Where different products arise in the same process, it is not possible to exactly ascertain the total cost of the products. ❑If any error occurs while calculating average costs, it will be carried through all the processes to the valuation of work in process and finished goods. ❑The computation of average cost is more difficult in those cases where more than one type of product is manufactured and a division of the cost element is necessary.
Basis for Comparison Job Costing Process Costing Cost Ascertainment Completion of the job. End of the cost period. Industry type Job costing is suitable for the industries which manufactures products as per customer's order Process costing is perfect for the industry where mass production is done. Losses Losses are usually not segregated. Normal losses are carefully ascertained and abnormal losses are bifurcated. Work-in-progress (WIP) WIP may or may not exist at the beginning or at the end of the financial year. WIP will always be present in the beginning or at the end of the accounting period.
The manufacture of product “Fanta” requires three distinct processes. On completion of the product is passed from Process 3 to finished stock. During the month of December 1992 , the following information was obtained: Production Overhead is absorbed by processes at a percentage of direct wages. Production during the period was 1 , 000 kgs. There was no stock of raw materials or work-in-progress at the beginning or at the end of the month.
Abnormal Loss: If the units lost in the production process are more than the normal loss, the difference between the two is the abnormal loss. It is excluded from total cost due to which it does not affect the cost per unit of the product. The relevant process of account is credited and abnormal loss account is debited with the abnormal loss valued at full cost of finished output. The amount realized from sale of scrap of abnormal loss units is credited to the abnormal loss account and the balance in the abnormal loss account is transferred to the Costing Profit and Loss Account.
❑The cost of normal loss is considered as part of the cost of production in which it occurs. If normal loss units have any realizable scrap value, the process account is credited by that amount. If there is no abnormal gain, then there is no necessity to maintain a separate account for normal loss. ❑Generally the cost of normal loss is absorbed by the cost units. Normal Output = Units introduced – Units of normal loss Normal Cost of Normal Output = Total Cost – Scrap value of Normal Loss. ❑In process A/c units of normal wastage is shown in unit column of credit side and if there is any scrap value then that will be shown in amount column of the credit side corresponding to lost units.