
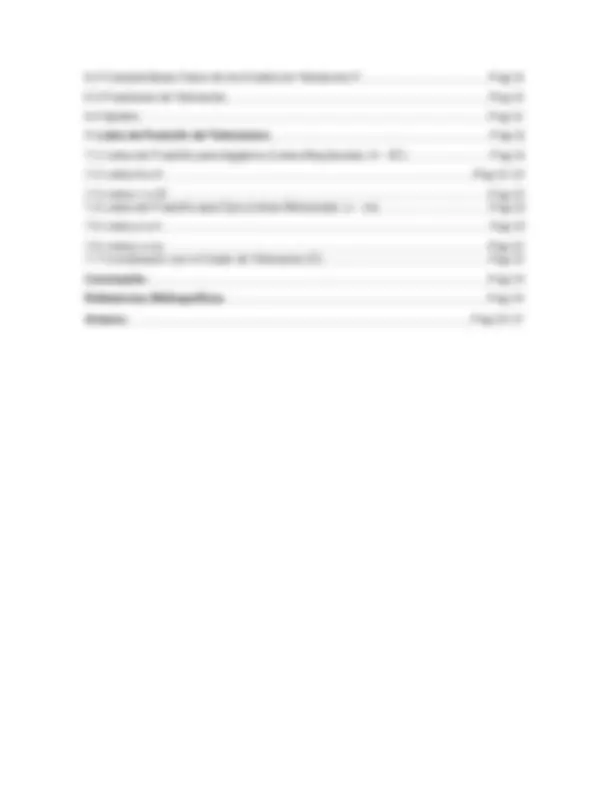
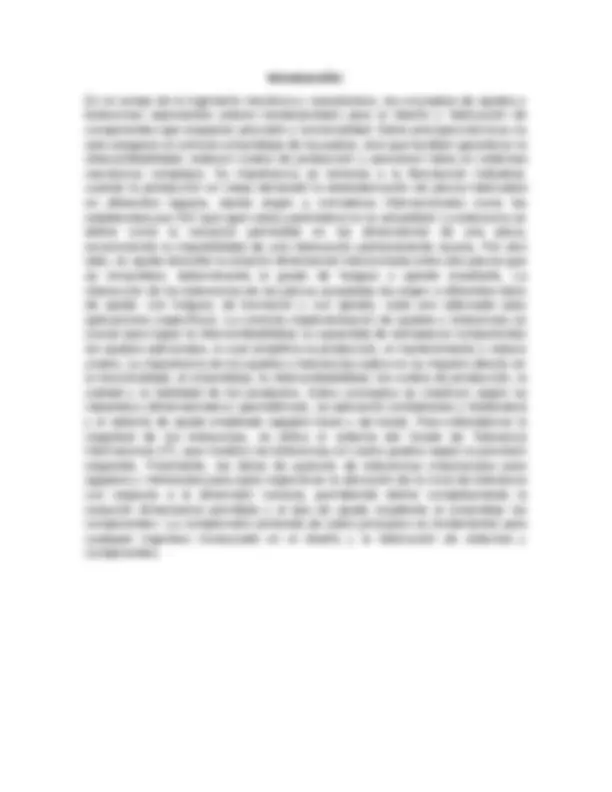
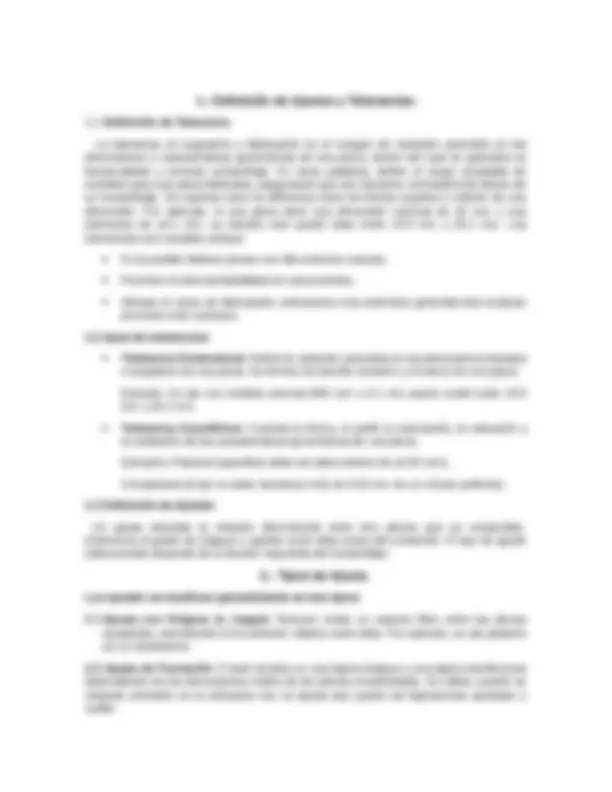
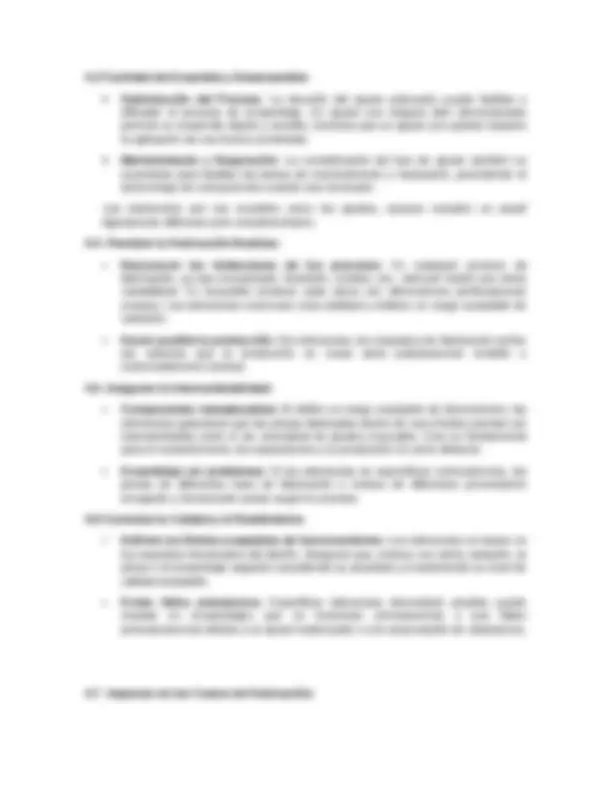
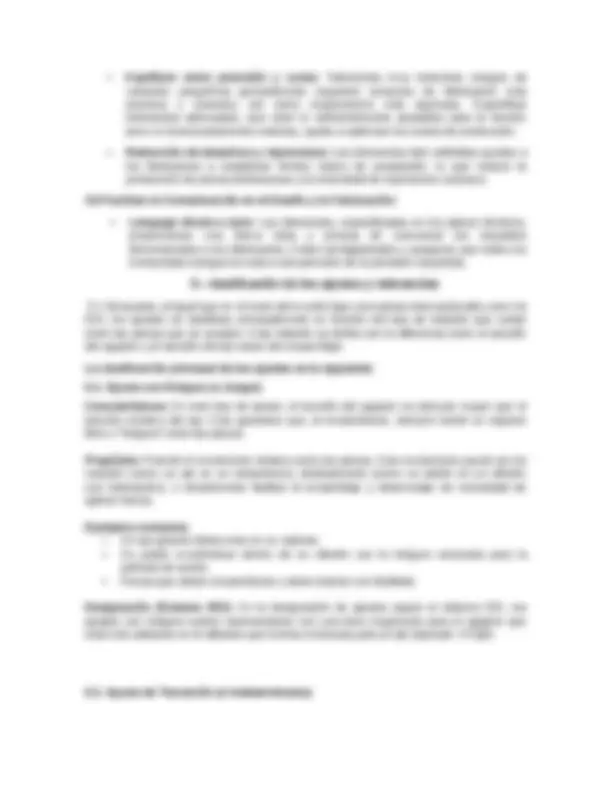
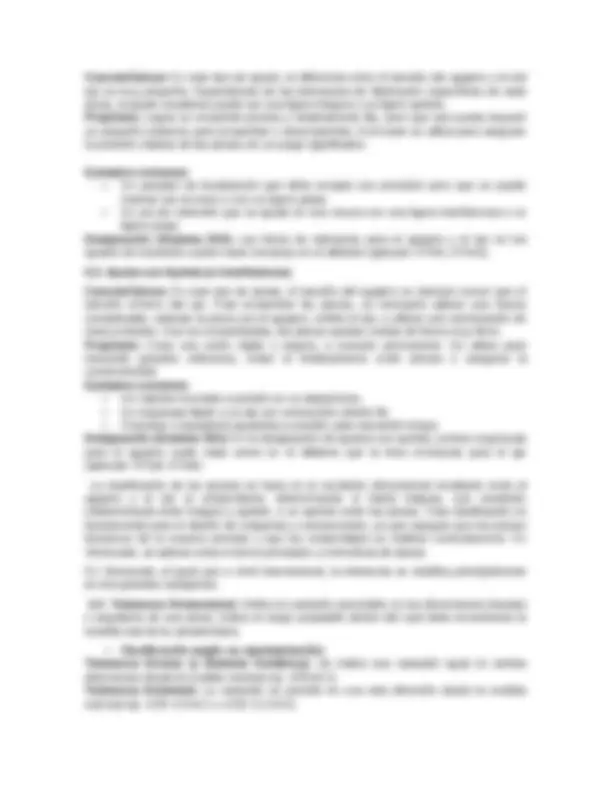
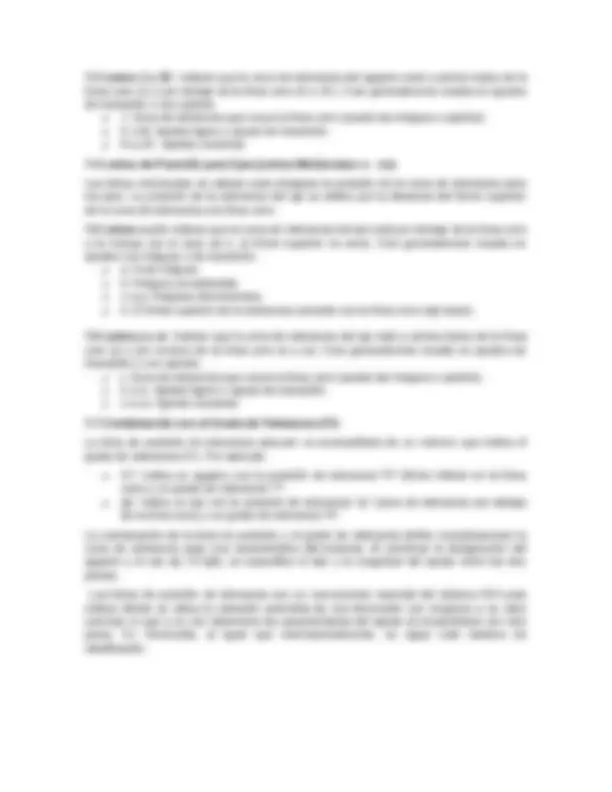
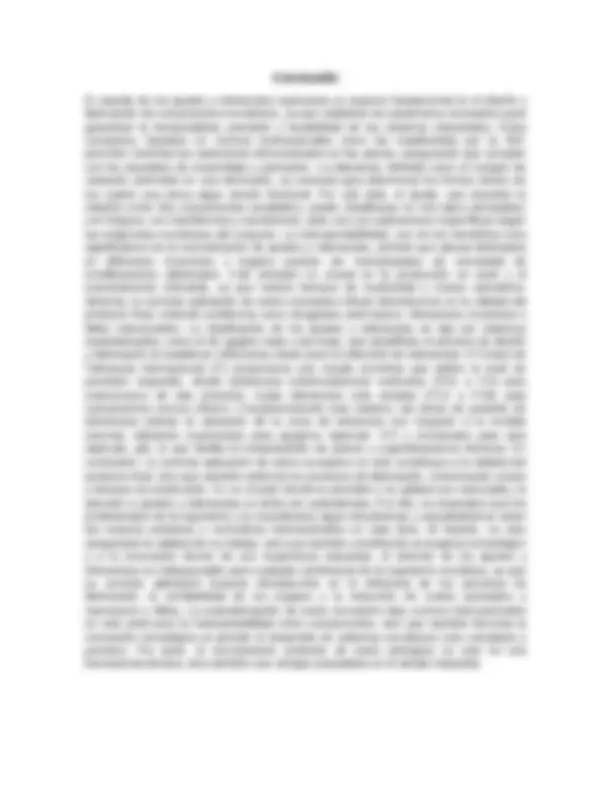
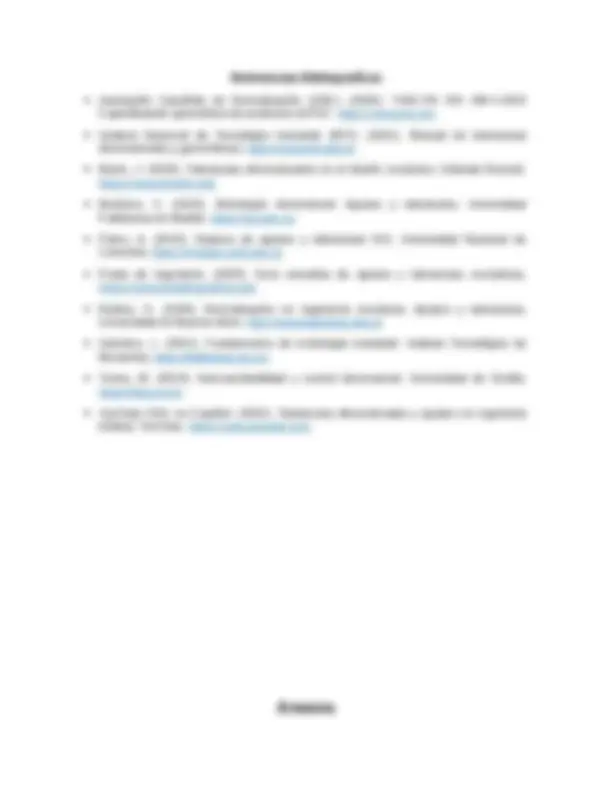
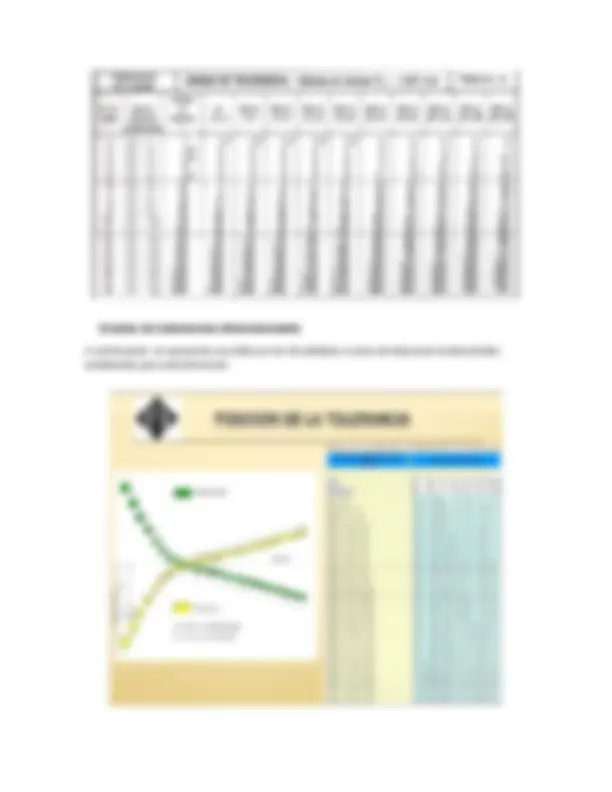
Study with the several resources on Docsity
Earn points by helping other students or get them with a premium plan
Prepare for your exams
Study with the several resources on Docsity
Earn points to download
Earn points by helping other students or get them with a premium plan
Community
Ask the community for help and clear up your study doubts
Discover the best universities in your country according to Docsity users
Free resources
Download our free guides on studying techniques, anxiety management strategies, and thesis advice from Docsity tutors
Tolerancia y ajuste en máquinas
Typology: Summaries
1 / 18
This page cannot be seen from the preview
Don't miss anything!
1.1 Definición de Tolerancia La tolerancia en ingeniería y fabricación es el margen de variación permitido en las dimensiones o características geométricas de una pieza, dentro del cual se garantiza su funcionalidad y correcto ensamblaje. En otras palabras, define el rango aceptable de medidas para una pieza fabricada, asegurando que aún funcione correctamente dentro de un ensamblaje. Se expresa como la diferencia entre los límites superior e inferior de una dimensión. Por ejemplo, si una pieza tiene una dimensión nominal de 25 mm y una tolerancia de ±0.1 mm, su tamaño real puede estar entre 24.9 mm y 25.1 mm. Las tolerancias son cruciales porque: Es imposible fabricar piezas con dimensiones exactas. Permiten la intercambiabilidad de componentes. Afectan el costo de fabricación; tolerancias más estrechas generalmente implican procesos más costosos. 1.2 tipos de tolerancias: Tolerancia Dimensional : Define la variación permitida en las dimensiones lineales o angulares de una pieza. los límites de tamaño (máximo y mínimo) de una pieza. Ejemplo: Un eje con medida nominal Ø20 mm ± 0.1 mm puede medir entre 19. mm y 20.1 mm. Tolerancia Geométrica: Controla la forma, el perfil, la orientación, la ubicación y la oscilación de las características geométricas de una pieza. Ejemplos: Planitud (superficie debe ser plana dentro de ±0.05 mm). Circularidad (el eje no debe desviarse más de 0.02 mm de un círculo perfecto). 1.3 Definición de Ajustes Un ajuste describe la relación dimensional entre dos piezas que se ensamblan. Determina el grado de holgura o apriete entre ellas antes del ensamble. El tipo de ajuste seleccionado depende de la función requerida del ensamblaje.
Los ajustes se clasifican generalmente en tres tipos: 2.1 Ajuste con Holgura (o Juego): Siempre existe un espacio libre entre las piezas acopladas, permitiendo el movimiento relativo entre ellas. Por ejemplo, un eje giratorio en un rodamiento. 2.2 Ajuste de Transición : Puede resultar en una ligera holgura o una ligera interferencia dependiendo de las dimensiones reales de las piezas ensambladas. Se utiliza cuando se requiere precisión en la ubicación con un ajuste que puede ser ligeramente apretado o suelto.
Intercambiabilidad Limitada (Ajuste Selectivo): Las piezas se clasifican en grupos dentro de rangos más estrechos para lograr un ajuste preciso (ej: pistones y cilindros en motores de alta precisión). Requiere medición y selección previa al ensamblaje. Intercambiabilidad Funcional: Las piezas no son idénticas en dimensiones, pero cumplen la misma función (ej: repuestos compatibles de diferentes marcas).
Los ajustes son cruciales porque determinan la naturaleza de la unión entre dos piezas que se ensamblan y, por lo tanto, influyen directamente en cómo funcionará ese ensamblaje. Aquí te detallo su importancia: 4.1 Control del Movimiento Relativo: Ajustes con Holgura: Son esenciales cuando se requiere movimiento entre las piezas. Permiten la rotación de ejes en rodamientos, el deslizamiento de pistones en cilindros o el libre movimiento de eslabones en mecanismos. Un ajuste inadecuado (demasiado apretado) podría causar fricción excesiva, desgaste prematuro o incluso el agarrotamiento del sistema. Un ajuste demasiado holgado podría generar vibraciones, ruido o pérdida de precisión. Ajustes de Transición : Permiten un ensamble que puede ser ligeramente libre o ligeramente forzado. Son importantes cuando se busca una ubicación precisa con la posibilidad de desmontaje, como en la fijación de algunas tapas o cubiertas. Ajustes con Apriete: Son fundamentales para crear uniones fijas y seguras. Permiten la transmisión de fuerzas y pares de torsión sin deslizamiento entre las piezas, como en la unión de engranajes a ejes, la fijación de rodamientos en sus alojamientos o el montaje de elementos estructurales. Un apriete insuficiente podría resultar en un aflojamiento de la unión bajo carga, mientras que un apriete excesivo podría dañar las piezas durante el ensamblaje o generar tensiones internas no deseadas. 4.2 Aseguramiento de la Función del Ensamblaje: Alineación y Posicionamiento: El tipo de ajuste seleccionado contribuye a la correcta alineación y posicionamiento de los componentes dentro de un ensamblaje, lo cual es vital para el funcionamiento preciso de máquinas y mecanismos. Estanqueidad : En algunos casos, como en el ensamblaje de tuberías o recipientes a presión, un ajuste con apriete adecuado, a menudo combinado con elementos de sellado, es crucial para garantizar la estanqueidad y evitar fugas. Transmisión de Potencia: En sistemas de transmisión de potencia, como cajas de cambios o reductores, los ajustes precisos entre engranajes, ejes y rodamientos son esenciales para asegurar una transmisión eficiente y sin pérdidas excesivas de energía.
4.3 Facilidad de Ensamble y Desensamble: Optimización del Proceso : La elección del ajuste adecuado puede facilitar o dificultar el proceso de ensamblaje. Un ajuste con holgura bien dimensionado permite un ensamble rápido y sencillo, mientras que un ajuste con apriete requiere la aplicación de una fuerza controlada. Mantenimiento y Reparación: La consideración del tipo de ajuste también es importante para facilitar las tareas de mantenimiento y reparación, permitiendo el desmontaje de componentes cuando sea necesario. Las tolerancias son tan cruciales como los ajustes, aunque cumplen un papel ligeramente diferente pero complementario: 4.4. Permiten la Fabricación Realista:
Características: En este tipo de ajuste, la diferencia entre el tamaño del agujero y el del eje es muy pequeña. Dependiendo de las tolerancias de fabricación específicas de cada pieza, el ajuste resultante puede ser una ligera holgura o un ligero apriete. Propósito: Lograr un ensamble preciso y relativamente fijo, pero que aún pueda requerir un pequeño esfuerzo para ensamblar o desensamblar. A menudo se utiliza para asegurar la posición relativa de las piezas sin un juego significativo. Ejemplos comunes:
Tolerancia Bilateral Asimétrica: La variación permitida no es igual en ambas direcciones desde la medida nominal (ej: ∅25−0.1+0.2 ). Límites: Se especifican directamente los límites superior e inferior entre los cuales debe estar la dimensión (ej: ∅25.1/24.9).
El Grado de Tolerancia Internacional (IT) es un sistema estandarizado por la norma ISO 286 que define la magnitud de la tolerancia en función del tamaño nominal de una pieza y su nivel de precisión requerido. Estos grados se utilizan para garantizar la intercambiabilidad de componentes en la fabricación mecánica. 6.1 Clasificación de los Grados de Tolerancia Internacional (IT): El sistema ISO 286 define 18 grados de tolerancia , que van desde IT01 (la tolerancia más precisa y pequeña) hasta IT18 (la tolerancia menos precisa y más grande). Estos grados se utilizan para cuantificar la magnitud de la tolerancia dimensional. IT01 a IT4: Se utilizan para la fabricación de galgas de control, instrumentos de medición y componentes de alta precisión. IT5 a IT7: Adecuados para ajustes en ingeniería de precisión. IT8 a IT11: Para ingeniería general. IT12 a IT14: Para trabajos de chapa metálica o estampación.
7.3 Letras J a ZC : Indican que la zona de tolerancia del agujero está a ambos lados de la línea cero (J) o por debajo de la línea cero (K a ZC). Esto generalmente resulta en ajustes de transición o con apriete. ✔ J: Zona de tolerancia que cruza la línea cero (puede dar holgura o apriete). ✔ K a M: Apriete ligero o ajuste de transición. ✔ N a ZC: Apriete creciente. 7.4 Letras de Posición para Ejes (Letras Minúsculas: a - zc): Las letras minúsculas se utilizan para designar la posición de la zona de tolerancia para los ejes. La posición de la tolerancia del eje se define por la distancia del límite superior de la zona de tolerancia a la línea cero. 7.5 Letras a a h: Indican que la zona de tolerancia del eje está por debajo de la línea cero o la incluye (en el caso de h, el límite superior es cero). Esto generalmente resulta en ajustes con holgura o de transición. ✔ a: Gran holgura. ✔ b: Holgura considerable. ✔ c a g: Holguras decrecientes. ✔ h: El límite superior de la tolerancia coincide con la línea cero (eje base). 7.6 Letras j a zc : Indican que la zona de tolerancia del eje está a ambos lados de la línea cero (j) o por encima de la línea cero (k a zc). Esto generalmente resulta en ajustes de transición o con apriete. ✔ j: Zona de tolerancia que cruza la línea cero (puede dar holgura o apriete). ✔ k a m: Apriete ligero o ajuste de transición. ✔ n a zc: Apriete creciente. 7.7 Combinación con el Grado de Tolerancia (IT): La letra de posición de tolerancia siempre va acompañada de un número que indica el grado de tolerancia (IT). Por ejemplo: ✔ H7: Indica un agujero con la posición de tolerancia "H" (límite inferior en la línea cero) y un grado de tolerancia "7". ✔ g6: Indica un eje con la posición de tolerancia "g" (zona de tolerancia por debajo de la línea cero) y un grado de tolerancia "6". La combinación de la letra de posición y el grado de tolerancia define completamente la zona de tolerancia para una característica dimensional. Al combinar la designación del agujero y el eje (ej: H7/g6), se especifica el tipo y la magnitud del ajuste entre las dos piezas. Las letras de posición de tolerancia son un componente esencial del sistema ISO para indicar dónde se ubica la variación permitida de una dimensión con respecto a su valor nominal, lo que a su vez determina las características del ajuste al ensamblarse con otra pieza. En Venezuela, al igual que internacionalmente, se sigue este sistema de clasificación.
El estudio de los ajustes y tolerancias representa un aspecto fundamental en el diseño y fabricación de componentes mecánicos, ya que establece los parámetros necesarios para garantizar la funcionalidad, precisión y durabilidad de los sistemas industriales. Estos conceptos, basados en normas internacionales como las establecidas por la ISO, permiten controlar las variaciones dimensionales en las piezas, asegurando que cumplan con los requisitos de ensamblaje y operación. La tolerancia, definida como el margen de variación permitido en una dimensión, es esencial para determinar los límites dentro de los cuales una pieza sigue siendo funcional. Por otro lado, el ajuste, que describe la relación entre dos componentes acoplados, puede clasificarse en tres tipos principales: con holgura, con interferencia y transicional, cada uno con aplicaciones específicas según las exigencias mecánicas del conjunto. La intercambiabilidad, uno de los beneficios más significativos de la normalización de ajustes y tolerancias, permite que piezas fabricadas en diferentes momentos o lugares puedan ser reemplazadas sin necesidad de modificaciones adicionales. Este principio es crucial en la producción en serie y el mantenimiento industrial, ya que reduce tiempos de inactividad y costos operativos. Además, la correcta aplicación de estos conceptos influye directamente en la calidad del producto final, evitando problemas como desgastes prematuros, vibraciones excesivas o fallos estructurales. La clasificación de los ajustes y tolerancias se rige por sistemas estandarizados, como el de agujero base y eje base, que simplifican el proceso de diseño y fabricación al establecer referencias claras para la selección de tolerancias. El Grado de Tolerancia Internacional (IT) proporciona una escala numérica que define el nivel de precisión requerido, desde tolerancias extremadamente estrechas (IT01 a IT4) para instrumentos de alta precisión, hasta tolerancias más amplias (IT12 a IT18) para componentes menos críticos. Complementando este sistema, las letras de posición de tolerancias indican la ubicación de la zona de tolerancia con respecto a la medida nominal, utilizando mayúsculas para agujeros (ejemplo. H7) y minúsculas para ejes (ejemplo. g6), lo que facilita la interpretación de planos y especificaciones técnicas. En conclusión, La correcta aplicación de estos conceptos no solo contribuye a la calidad del producto final, sino que también optimiza los procesos de fabricación, minimizando costos y tiempos de producción. En un mundo donde la precisión y la calidad son esenciales, la atención a ajustes y tolerancias no debe ser subestimada. Por ello, es imperativo que los profesionales de la ingeniería y la manufactura sigan educándose y actualizándose sobre las mejores prácticas y normativas internacionales en esta área. Al hacerlo, no solo asegurarán la calidad de su trabajo, sino que también contribuirán al progreso tecnológico y a la innovación dentro de sus respectivas industrias. el dominio de los ajustes y tolerancias es indispensable para cualquier profesional de la ingeniería mecánica, ya que su correcta aplicación impacta directamente en la eficiencia de los procesos de fabricación, la confiabilidad de los equipos y la reducción de costos asociados a reprocesos y fallas. La estandarización de estos conceptos bajo normas internacionales no solo promueve la interoperabilidad entre componentes, sino que también fomenta la innovación tecnológica al permitir el desarrollo de sistemas mecánicos más complejos y precisos. Por tanto, el conocimiento profundo de estos principios no solo es una herramienta técnica, sino también una ventaja competitiva en el ámbito industrial.
El diagrama muestra las relaciones dimensionales entre dos piezas que se ensamblan, con ejemplos de ajustes de interferencia, transición y holgura.
Intercambiabilidad: La imagen muestra cómo diversas piezas de maquinaria, fabricadas por diferentes empresas, encajan perfectamente entre sí. Esto demuestra la importancia de la intercambiabilidad, que permite usar componentes estándar en
diferentes máquinas y sistemas, simplificando el diseño, la fabricación, el mantenimiento y las reparaciones.