
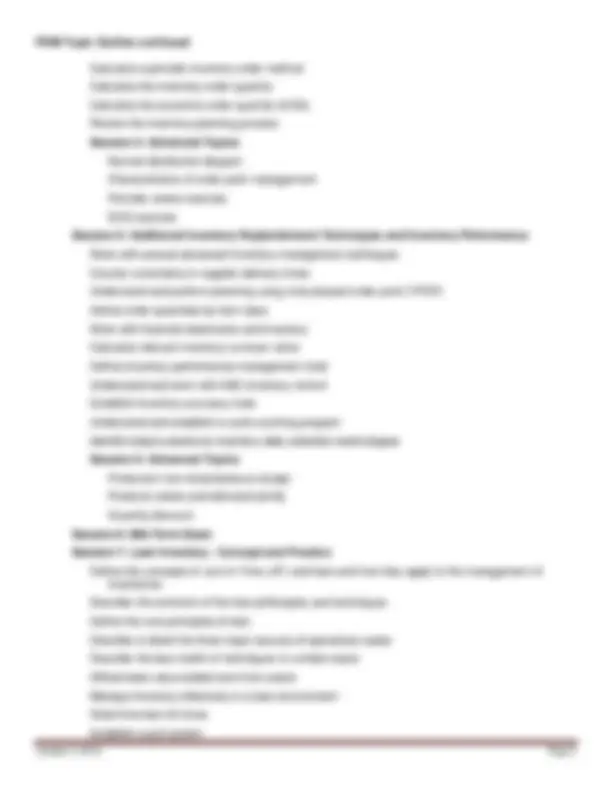
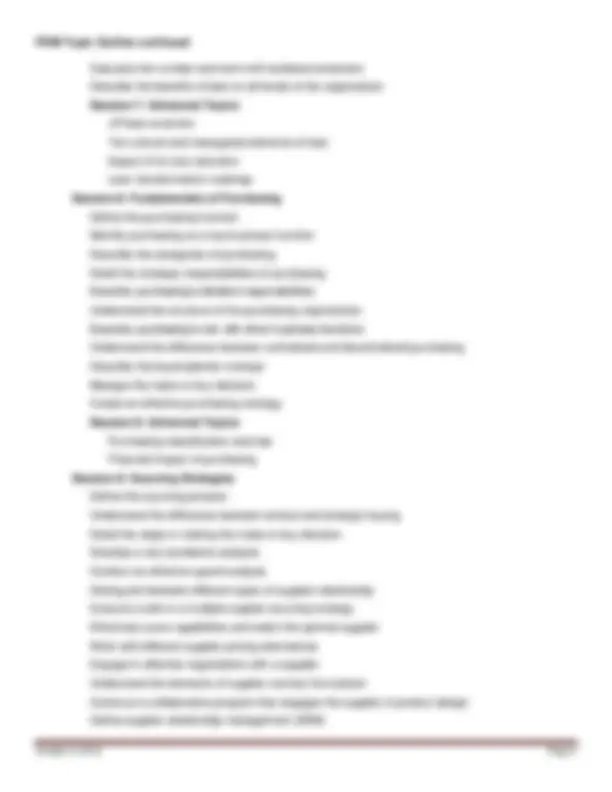
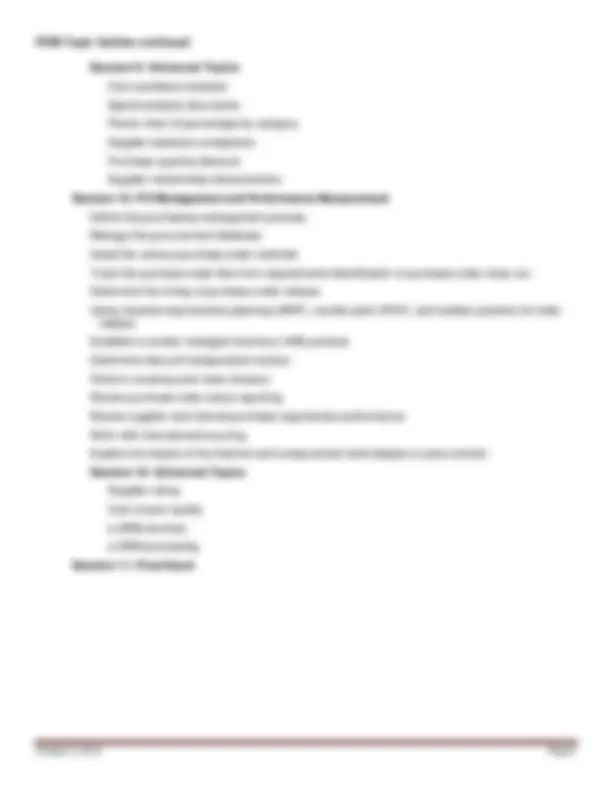
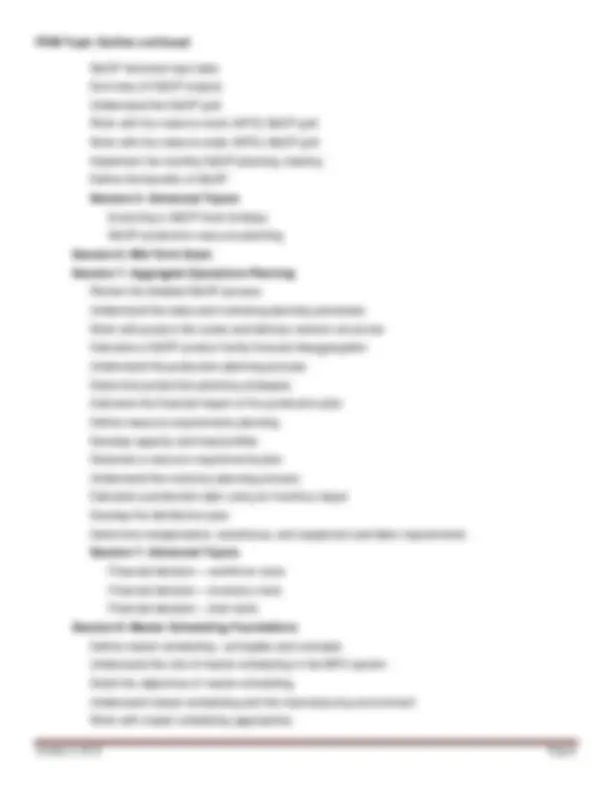
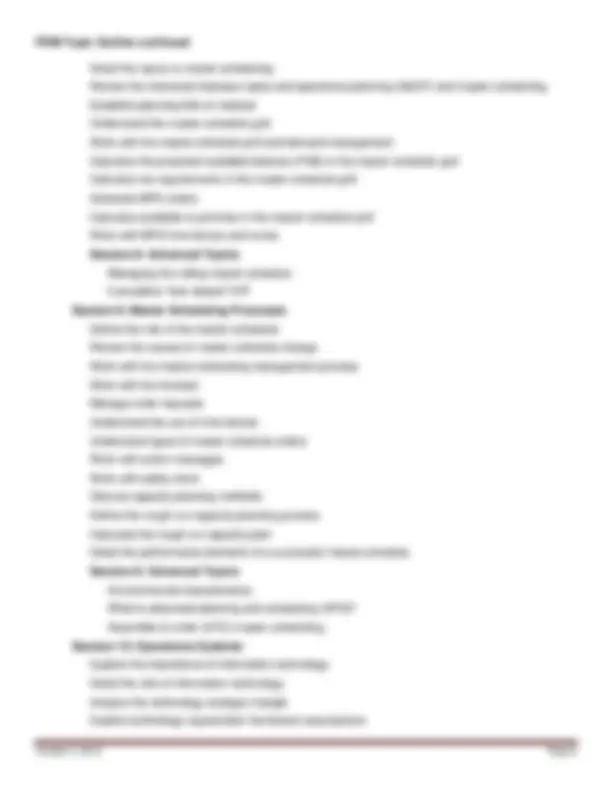
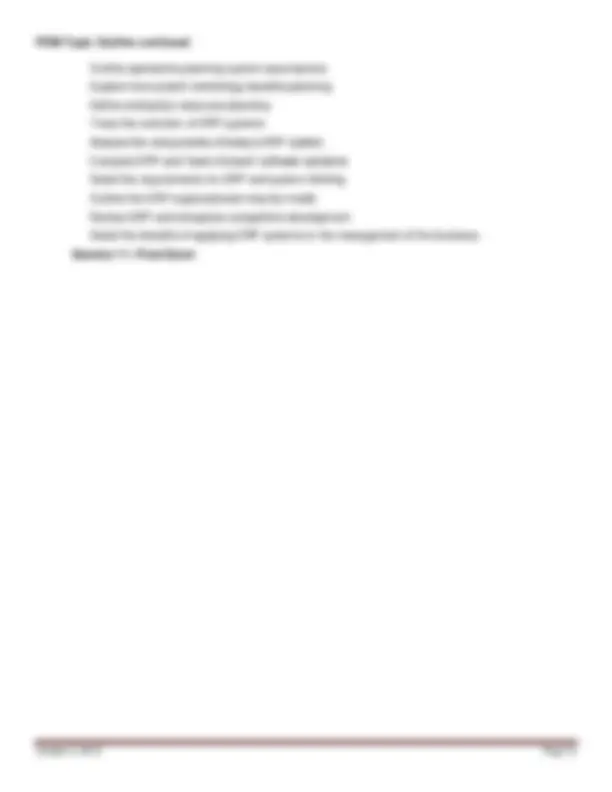
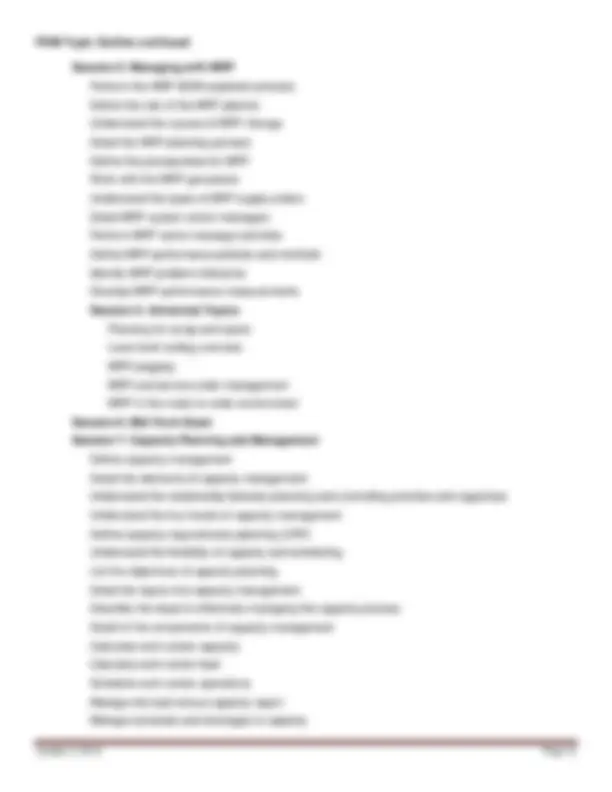
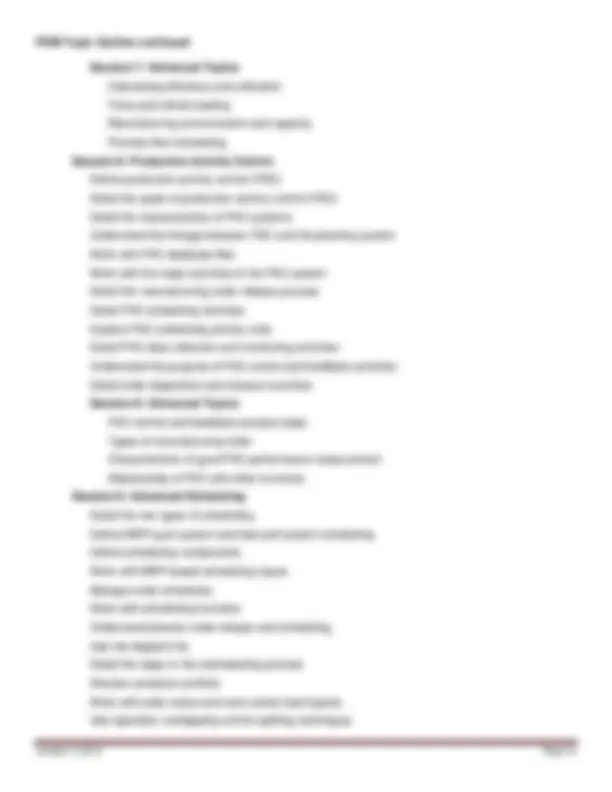
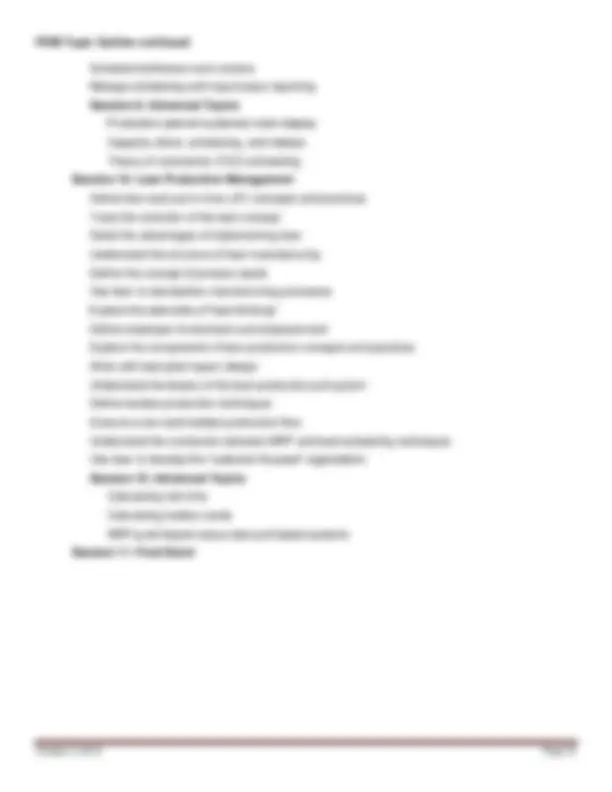
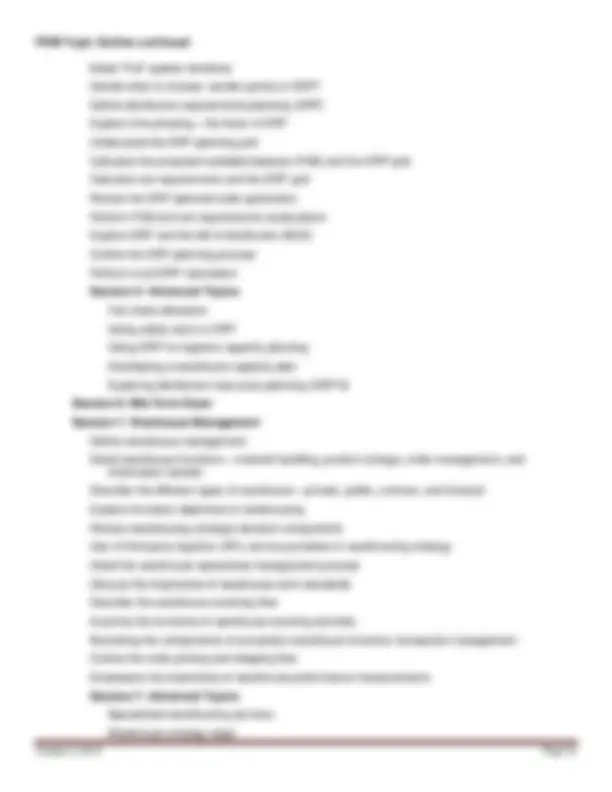
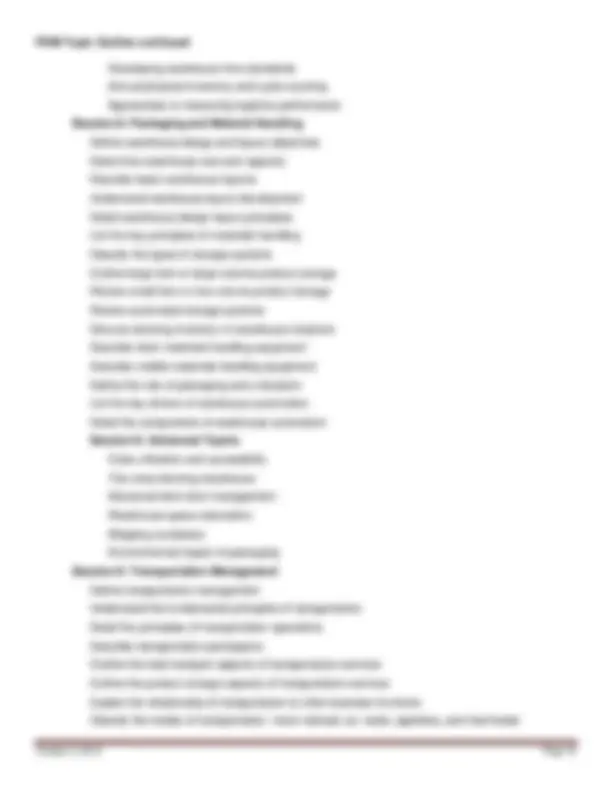
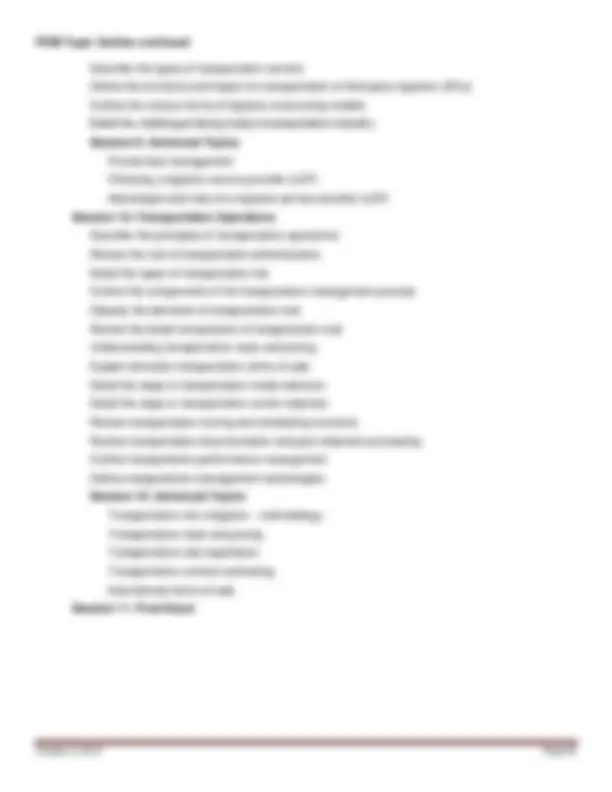
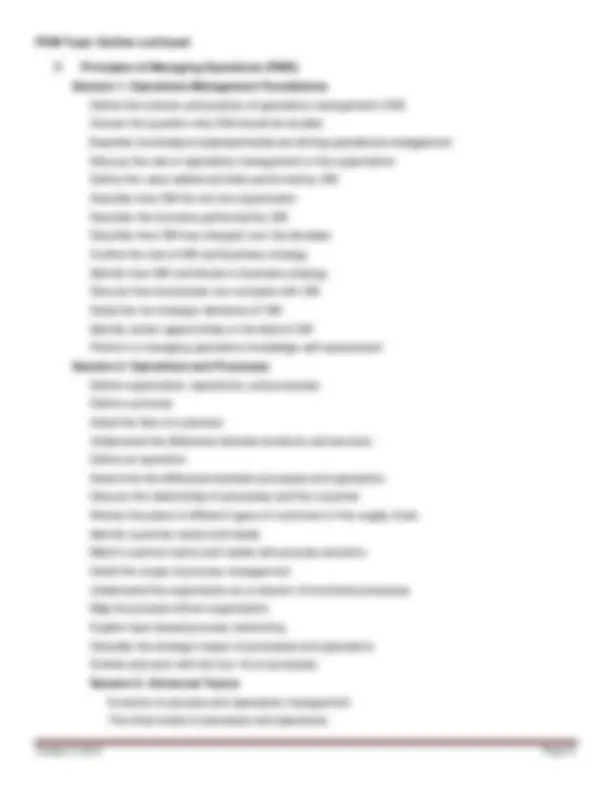
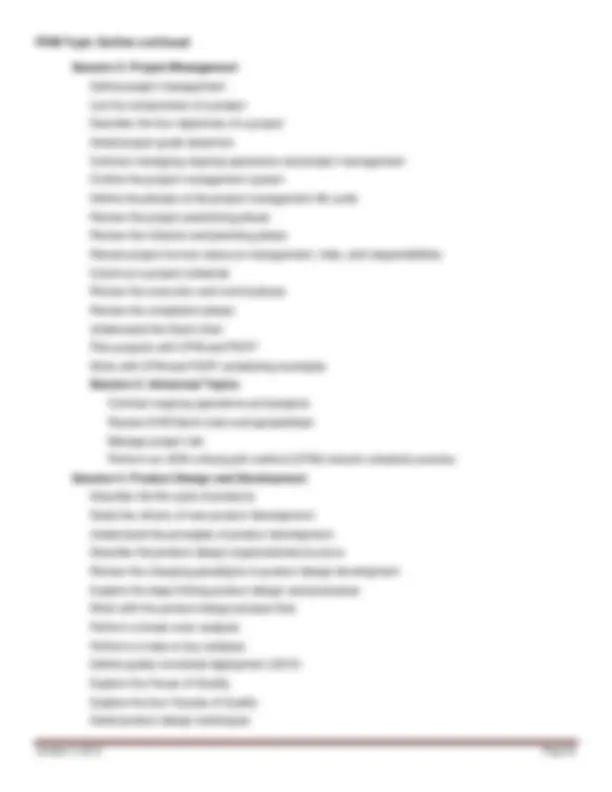
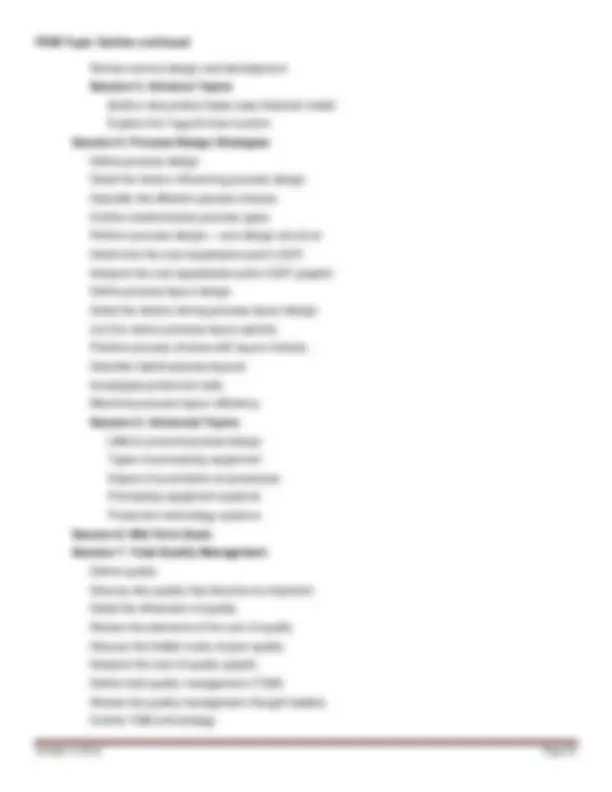

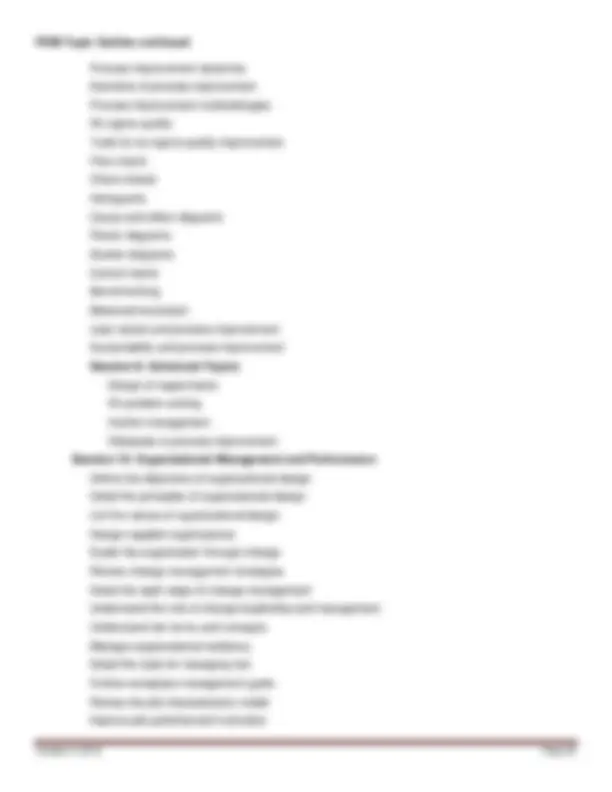
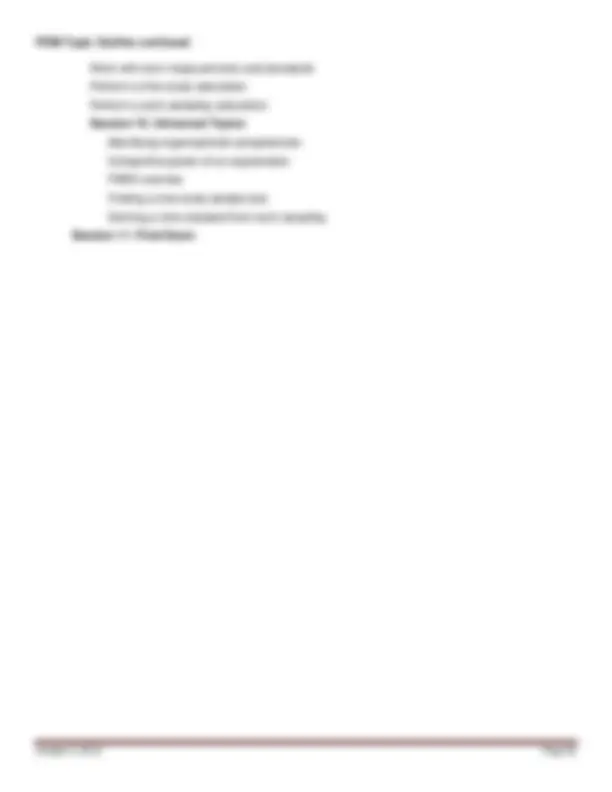
Study with the several resources on Docsity
Earn points by helping other students or get them with a premium plan
Prepare for your exams
Study with the several resources on Docsity
Earn points to download
Earn points by helping other students or get them with a premium plan
Community
Ask the community for help and clear up your study doubts
Discover the best universities in your country according to Docsity users
Free resources
Download our free guides on studying techniques, anxiety management strategies, and thesis advice from Docsity tutors
An outline for a university-level course on Operations Management (OM) with a focus on Inventory Management. The course covers topics such as the science and practice of OM, inventory management objectives, inventory management functions, inventory management strategies, inventory replenishment methods, and advanced inventory management techniques. Students will learn about the role of OM in business strategy, the importance of inventory management, and how to make trade-off decisions related to inventory. The document also includes sessions on distribution and logistics, process management, and total quality management.
Typology: Study notes
1 / 26
This page cannot be seen from the preview
Don't miss anything!
I. Principles of Inventory Management (PIM) Session 1: Operation Management – Foundations Define the science and practice of operations management (OM) Answer the question why OM should be studied Describe how today’s business trends are driving operations management Discuss the role of operations management in the organization Define the value-added activities performed by OM Describe how OM fits into the organization Describe the functions performed by OM Describe how OM has changed over the decades Outline the role of OM and business strategy Identify how OM contributes to business strategy Discuss how businesses can compete with OM Detail the ten strategic decisions of OM Identify career opportunities in the field of OM Perform an inventory management knowledge self-assessment Session 2: Fundamentals of Inventory Management Define inventory management Define inventory management objectives Describe the different classes of inventory Identify the different levels of inventory management Review the characteristics of inventory in the supply chain Detail the strategic inventory management process Describe the elements of an effective inventory management strategy Balance demand and supply objectives Contrast the conflicting objectives of inventory management among marketing/sales, finance, and operations Understand inventory trade-off decisions Describe inventory and demand flows Define supply chain inventory and demand flows Describe inventory dynamics
Understand how inventory provides value Determine whether inventory is an asset or a liability Assess the impact of cash flow and inventory management Session 2: Advanced Topics Trade-off decisions by item class Subclasses of inventory Item numbering
Session 3: Purpose and Function of Inventory
Explain why companies carry inventory Define the five functions of inventory and describe their use Describe the purpose of decoupling inventories Detail the components of inventory decision making Use a simple formula to estimate inventory throughput and cycle and pipeline inventories Define the elements of inventory cost Understand and calculate inventory carrying costs Define the elements of manufacturing and purchasing costing Calculate the impact of stockout costs on the operation Discuss how excess and obsolete inventories affect inventory management Work with the five basic methods of inventory valuation. Session 3: Advanced Topics Measuring inventory throughput Cost of preventing a stockout Capacity associated costs Estimating inventory values Calculating order costs Inventory valuation methods
Session 4: Inventory Replenishment Management
Explain the basic functions of statistical inventory management Understand the difference between independent and dependent demand Define the theory of inventory replenishment management Describe the difference between continuous and periodic inventory review Describe the inventory replenishment planning process Define the seven inventory replenishment methods Work with the order point inventory ordering method Calculate safety stock Calculate the order point
Calculate the number and work with kanbans/containers Describe the benefits of lean on all levels of the organization Session 7: Advanced Topics JIT/lean evolution Ten cultural and managerial elements of lean Impact of lot size reduction Lean transformation roadmap
Session 8: Fundamentals of Purchasing
Define the purchasing function Identify purchasing as a key business function Describe the categories of purchasing Detail the strategic responsibilities of purchasing Describe purchasing’s detailed responsibilities Understand the structure of the purchasing organization Describe purchasing’s role with other business functions Understand the difference between centralized and decentralized purchasing Describe the buyer/planner concept Manage the make or buy decision Create an effective purchasing strategy Session 8: Advanced Topics Purchasing classification exercise Financial impact of purchasing
Session 9: Sourcing Strategies
Define the sourcing process Understand the difference between tactical and strategic buying Detail the steps in making the make or buy decision Develop a cost avoidance analysis Conduct an effective spend analysis Distinguish between different types of supplier relationship Execute a sole or a multiple supplier sourcing strategy Effectively score capabilities and select the optimal supplier Work with different supplier pricing alternatives Engage in effective negotiations with a supplier Understand the elements of supplier contract formulation Construct a collaborative program that engages the supplier in product design Define supplier relationship management (SRM)
Session 9: Advanced Topics Cost avoidance analysis Spend analysis documents Pareto chart of percentage by category Supplier selection comparison Purchase quantity discount Supplier relationship characteristics
Session 10: PO Management and Performance Measurement
Define the purchasing management process Manage the procurement database Detail the various purchase order methods Trace the purchase order flow from requirements identification to purchase order close-out Determine the timing of purchase order release Using material requirements planning (MRP), reorder point (ROP), and kanban systems for order release Establish a vendor managed inventory (VMI) process Determine inbound transportation factors Perform receiving and order closeout Review purchase order status reporting Review supplier and internal purchase organization performance Work with international sourcing Explore the impact of the Internet and computerized technologies on procurement Session 10: Advanced Topics Supplier rating Cost of poor quality e-SRM services e-SRM processing
Session 11: Final Exam
Detail the forecasting process Detail the benefits of forecast accuracy Describe the general forecasting techniques and data sources Review qualitative, quantitative, and causal forecasting techniques Discuss why forecasts fail Session 3: Advanced Topics Selection of forecasting models Pyramid forecasting Deseasonalized forecast Forecast trend with exponential smoothing (Holt’s model) Forecast trend extrapolation
Session 4: Demand Management
Define demand management Review the components of demand management Place demand management in the MPC system Evaluate forecast performance Use the measures of forecast error Calculate forecast error Determine the MAD and standard deviation of forecast error Calculate forecast bias and tracking errors Define customer relationship management Work with customer order management Define customer service management Explore demand management technology tools Define demand management performance Session 4: Advanced Topics Tracking signal Forecast error exercise Safety stock calculation Customer service gap analysis
Session 5: Sales and Operations Planning (S&OP)
Define sales and operations planning (S&OP) S&OP in the MPC system S&OP detailed planning process Determine product families S&OP planning inputs
S&OP historical input data Summary of S&OP outputs Understand the S&OP grid Work with the make-to-stock (MTS) S&OP grid Work with the make-to-order (MTO) S&OP grid Implement the monthly S&OP planning meeting Define the benefits of S&OP Session 5: Advanced Topics Executing a S&OP level strategy S&OP production resource planning
Session 6: Mid-Term Exam
Session 7: Aggregate Operations Planning
Review the detailed S&OP process Understand the sales and marketing planning processes Work with product life cycles and delivery network structures Calculate a S&OP product family forecast disaggregation Understand the production planning process Determine production planning strategies Calculate the financial impact of the production plan Define resource requirements planning Develop capacity and load profiles Generate a resource requirements plan Understand the inventory planning process Calculate a production plan using an inventory target Develop the distribution plan Determine transportation, warehouse, and equipment and labor requirements Session 7: Advanced Topics Financial decision – workforce costs Financial decision – inventory costs Financial decision – total costs
Session 8: Master Scheduling Foundations
Define master scheduling – principles and concepts Understand the role of master scheduling in the MPC system Detail the objectives of master scheduling Understand master scheduling and the manufacturing environment Work with master scheduling approaches
Outline operations planning system assumptions Explore how system technology benefits planning Define enterprise resources planning Trace the evolution of ERP systems Analyze the components of today’s ERP system Compare ERP and “best of breed” software solutions Detail the requirements for ERP and system thinking Outline the ERP organizational maturity model Review ERP and enterprise competitive development Detail the benefits of applying ERP systems to the management of the business.
Session 11: Final Exam
III. Principles of Manufacturing Management (PMM)
Session 1: Operations Management Foundations Describe how today’s business trends are driving operations management Define the science of operations management Identify the decisions made by operations managers Explain how operations management is important to both manufacturing and service functions Discuss the role of operations management in the organization Describe operations management’s role in supply chain management Provide examples of how operations management is a competitive weapon Identify career opportunities in the field of operations management Perform a manufacturing management self-assessment review Session 2: Introduction to Manufacturing Management Define manufacturing Review the components of manufacturing management Review product manufacturing choices Understand the impact of volume, variety, and lead time Explore product manufacturing choice positioning Detail manufacturing process choices Explore product and process choice positioning Review process layout options Explore process layout positioning Detail steps for developing a manufacturing strategy Outline manufacturing structural and infrastructural choices Understand product profiling Explore batch versus flow and push versus pull manufacturing techniques Detail job content and operator tasks Session 2: Advanced Topics: Product profiling Production plan issues Layout characteristics – exercise Performance objectives – exercise Process selection – unit costs Process selection – least cost Session 3: Manufacturing Product Structures Define the product structure Define the bill of material
Session 5: Managing with MRP
Perform the MRP BOM explosion process Define the role of the MRP planner Understand the causes of MRP change Detail the MRP planning process Define the prerequisites for MRP Work with the MRP generation Understand the types of MRP supply orders Detail MRP system action messages Perform MRP action message activities Define MRP performance policies and methods Identify MRP problem indicators Develop MRP performance measurements Session 5: Advanced Topics Planning for scrap and waste Lowe level coding overview MRP pegging MRP and service order management MRP in the make-to-order environment
Session 6: Mid-Term Exam
Session 7: Capacity Planning and Management
Define capacity management Detail the elements of capacity management Understand the relationship between planning and controlling priorities and capacities Understand the four levels of capacity management Define capacity requirements planning (CRP) Understand the flexibility of capacity and scheduling List the objectives of capacity planning Detail the inputs into capacity management Describe the steps to effectively managing the capacity process Detail of the components of capacity management Calculate work center capacity Calculate work center load Schedule work center operations Manage the load versus capacity report Manage excesses and shortages in capacity
Session 7: Advanced Topics Calculating efficiency and utilization Finite and infinite loading Manufacturing environments and capacity Process flow scheduling
Session 8: Production Activity Control
Define production activity control (PAC) Detail the goals of production activity control (PAC) Detail the characteristics of PAC systems Understand the linkage between PAC and the planning system Work with PAC database files Work with the major activities of the PAC system Detail the manufacturing order release process Detail PAC scheduling activities Explore PAC scheduling priority rules Detail PAC data collection and monitoring activities Understand the purpose of PAC control and feedback activities Detail order disposition and closeout activities Session 8: Advanced Topics PAC control and feedback process steps Types of manufacturing order Characteristics of good PAC performance measurement Relationship of PAC with other functions
Session 9: Advanced Scheduling
Detail the two types of scheduling Define MRP-push system and lean-pull system scheduling Define scheduling components Work with MRP-based scheduling inputs Manage order schedules Work with scheduling functions Understand planner order release and scheduling Use the dispatch list Detail the steps in the rescheduling process Resolve schedule conflicts Work with order status and work center load reports Use operation overlapping and lot-splitting techniques
IV. Principles of Distribution and Logistics (PDL)
Session 1: Operations Management Foundations Describe how today’s business trends are driving operations management Define the science of operations management Identify the decisions made by operations managers Explain how operations management is important to both manufacturing and service functions Discuss the role of operations management in the organization Describe operations management’s role in supply chain management Provide examples of how operations management is a competitive weapon Identify career opportunities in the field of operations management Perform a distribution and logistics self-assessment review Session 2: Introduction to Distribution and Logistics Define distribution management Demonstrate the components of the supply and distribution channel Detail a channel design tree structure Describe the various types of channel intermediaries Identify the need for distribution channels Detail the roles performed by the distribution function Define logistics management Describe the functions of logistics management Explain the components of logistics operations Understand the concept and practice of reverse logistics Detail the components of an effective logistics strategy Explore the guidelines for creating a logistics strategy Understand the role of the logistics function in supply chain management Session 2: Advanced Topics The organization of logistics The distribution sorting process Value-added role of logistics Reverse logistics financial worksheet Session 3: Channel Network Design Define the activities involved in channel network design Explain the reasons for supply and distribution channels Detail critical channel network design considerations Understand channel network design factors Outline levels of channel network dependency
Work with the channel configuration attribute matrix Describe several different channel network design options Compare distribution network design option performance Deploy a framework for channel network design Discuss the micro decisions influencing distribution channel design Use the factor-rating method for channel network design Use the center-of-gravity method for channel network design Detail channel demand and capacity. Session 3: Advanced Topics Global channel facilities Delivery network facilitators Location break-even analysis
Session 4: Inventory Management
Define the inventory management function Identify the functions of inventory Outline he strategic inventory management process Understand the characteristics of inventory in the distribution channel Trace channel inventory and demand flows Identify the components of inventory replenishment Describe replenishment ordering techniques Understand the order point model Calculate order point safety stock Determine the replenishment order quantity Identify the components of inventory carrying cost Calculate the EOQ Work with minimum/maximum inventory controls Detail the replenishment planning process Session 4: Advance Topics The periodic review system Normal distribution diagram Measuring inventory performance Calculation order points with supplier lead time uncertainty Cycle counting processing
Session 5: Distribution Requirements Planning (DRP)
Describe distribution channel dependencies Detail “Push” system functions
Developing warehouse time standards Annual physical inventory and cycle counting Approaches to measuring logistics performance
Session 8: Packaging and Material Handling
Define warehouse design and layout objectives Determine warehouse size and capacity Describe basic warehouse layouts Understand warehouse layout development Detail warehouse design layout principles List the key principles of materials handling Classify the types of storage systems Outline large-item or large-volume product storage Review small-item or low-volume product storage Review automated storage systems Discuss stocking inventory in warehouse locations Describe dock materials handling equipment Describe mobile materials handling equipment Define the role of packaging and unitization List the key drivers of warehouse automation Detail the components of warehouse automation Session 8: Advanced Topics Cube utilization and accessibility The cross-docking warehouse Advanced dock door management Warehouse space calculation Shipping containers Environmental impact of packaging
Session 9: Transportation Management
Define transportation management Understand the fundamental principles of transportation Detail the principles of transportation operations Describe transportation participants Outline the load transport aspects of transportation services Outline the product storage aspects of transportation services Explain the relationship of transportation to other business functions Classify the modes of transportation: motor railroad, air, water, pipelines, and intermodal
Describe the types of transportation carriers Define the functions and impact on transportation of third-party logistics (3PLs) Outline the various forms of logistics outsourcing models Detail the challenges facing today’s transportation industry Session 9: Advanced Topics Private fleet management Choosing a logistics service provider (LSP) Advantages and risks of a logistics service provider (LSP)
Session 10: Transportation Operations
Describe the principles of transportation operations Review the role of transportation administration Detail the types of transportation risk Outline the components of the transportation management process Classify the elements of transportation cost Review the detail components of transportation cost Understanding transportation rates and pricing Explain domestic transportation terms of sale Detail the steps in transportation mode selection Detail the steps in transportation carrier selection Review transportation routing and scheduling functions Review transportation documentation and post-shipment processing Outline transportation performance management Define transportation management technologies Session 10: Advanced Topics Transportation risk mitigation - methodology Transportation rates and pricing Transportation rate negotiation Transportation contract estimating International terms of sale
Session 11: Final Exam