
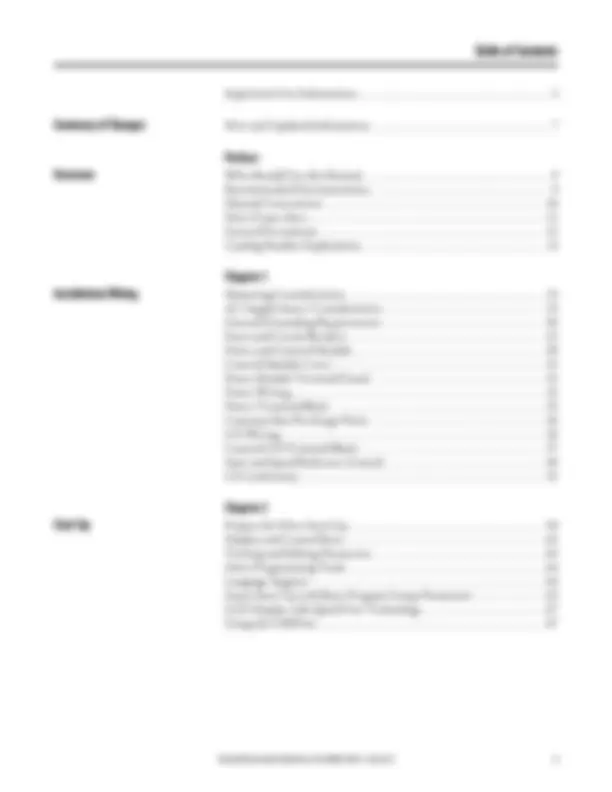
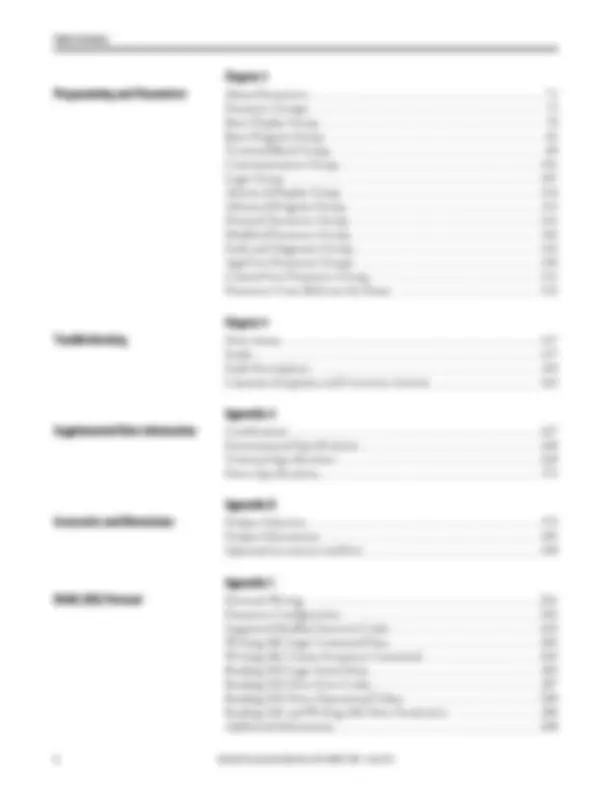
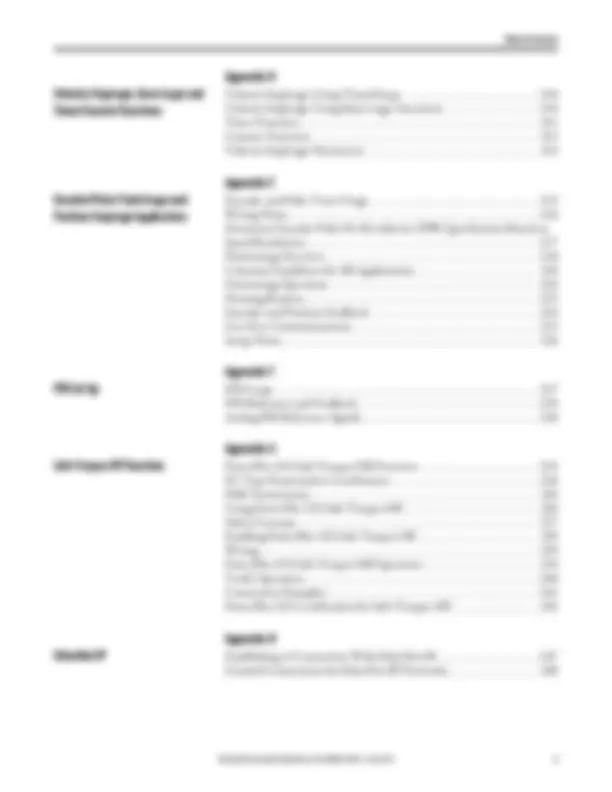
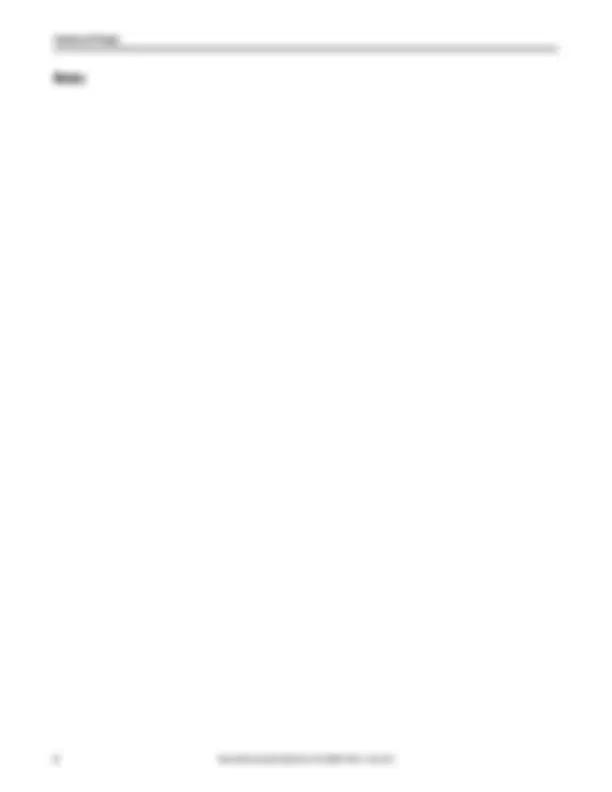
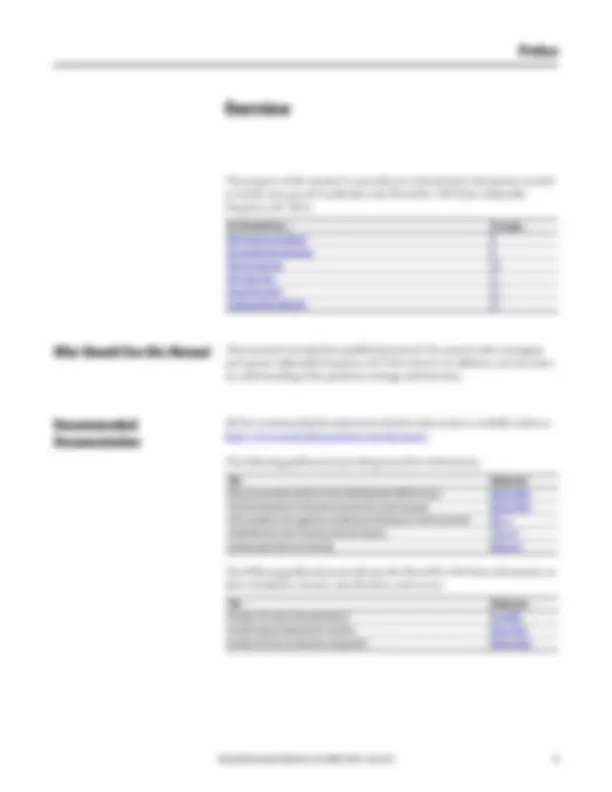
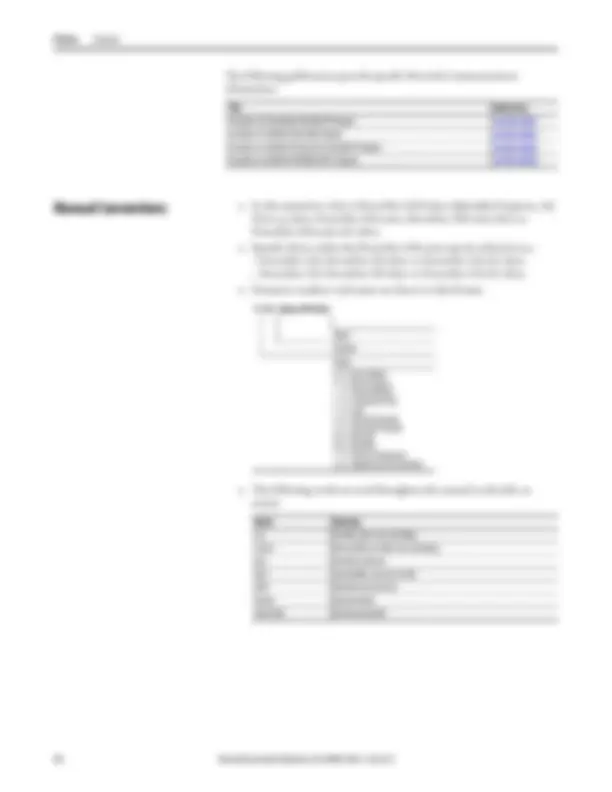
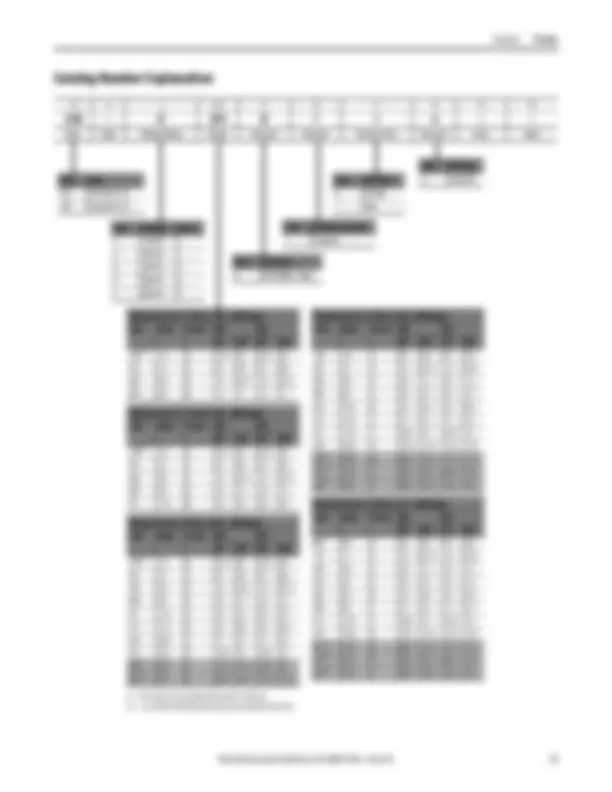
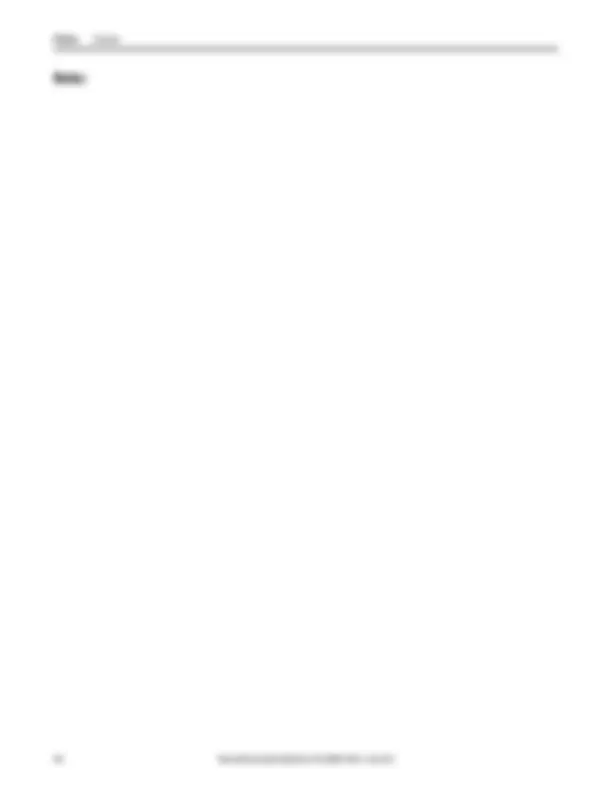
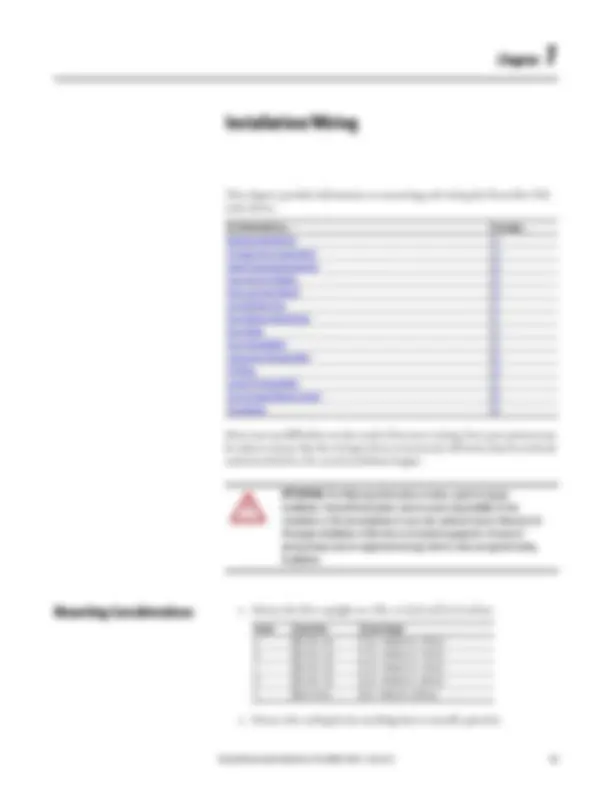
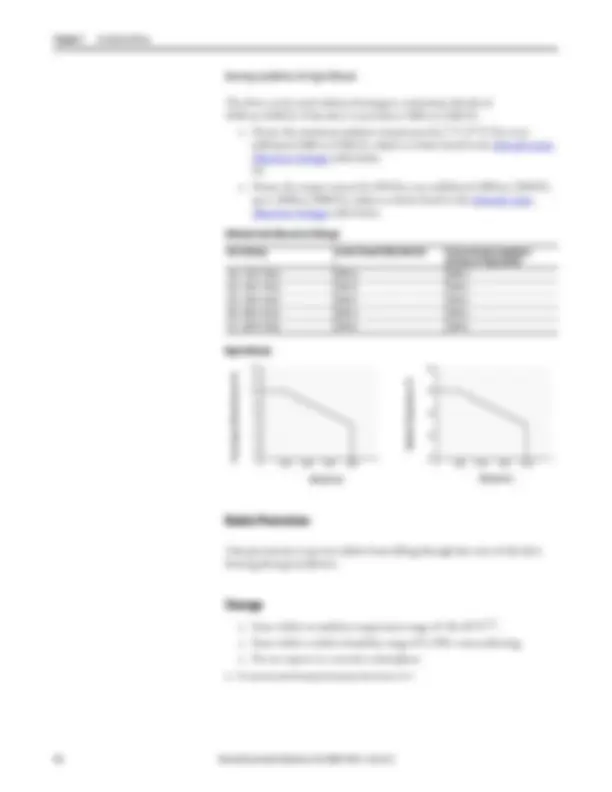
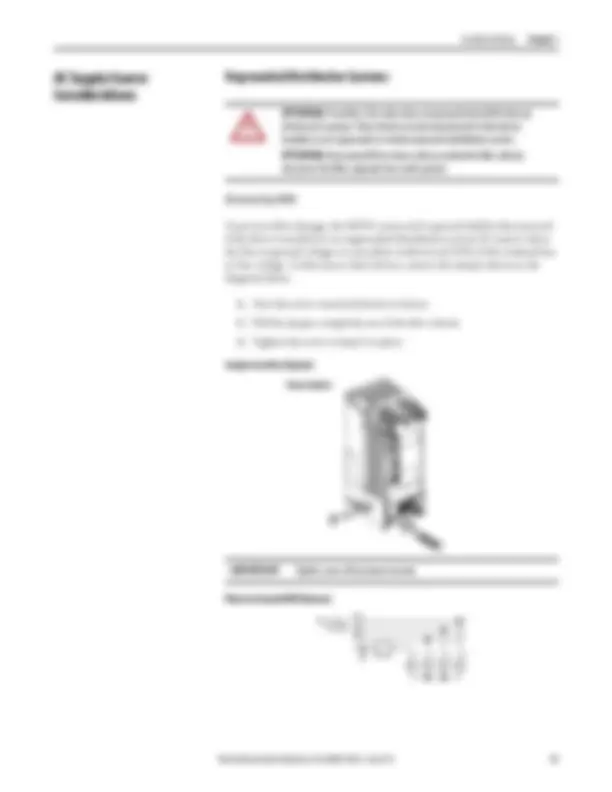
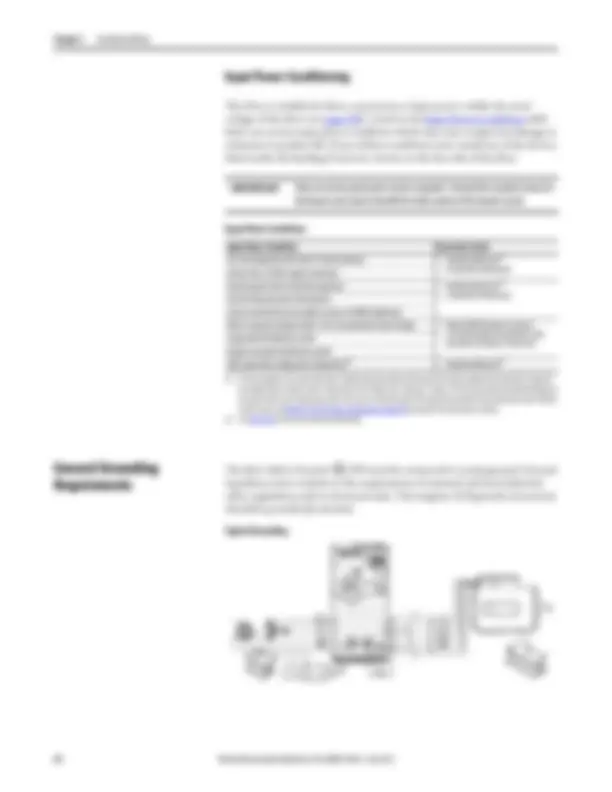
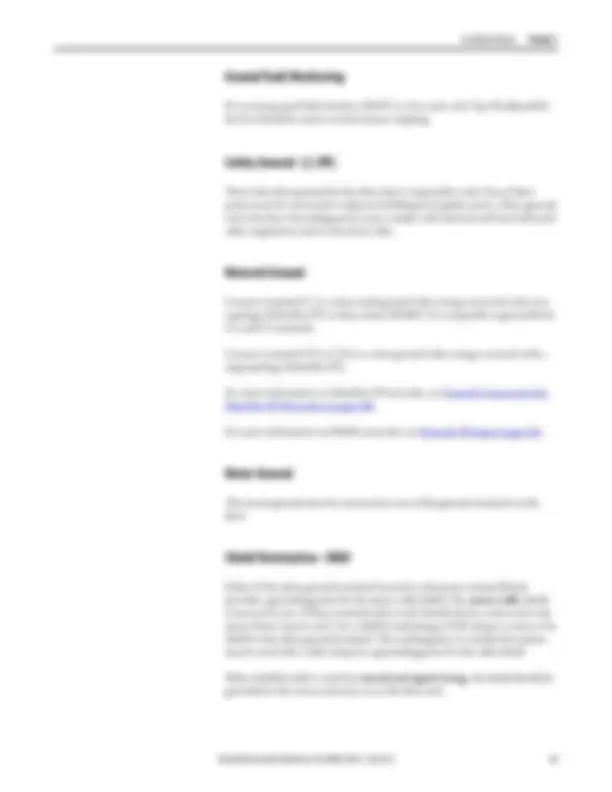
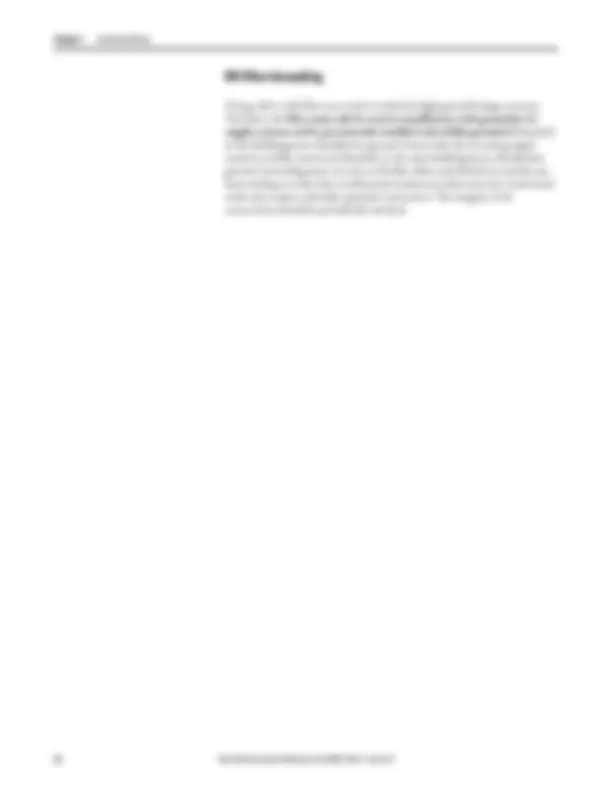
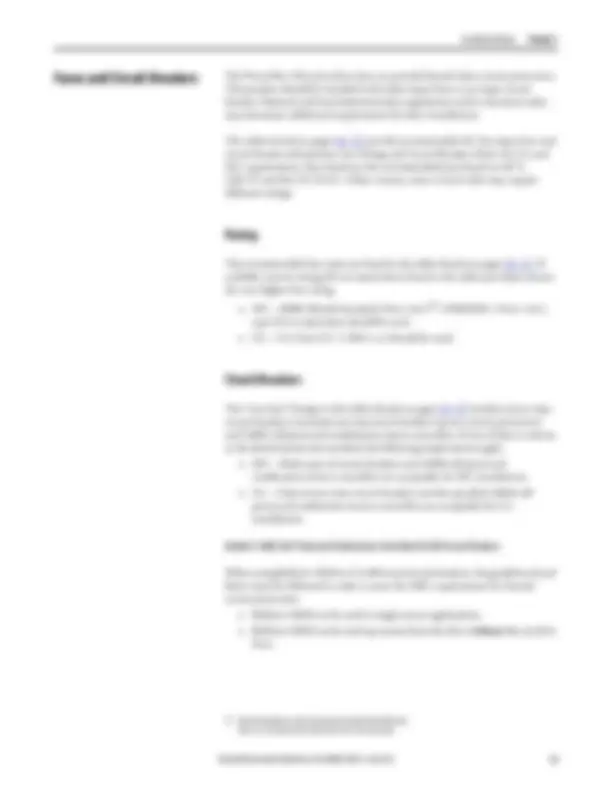
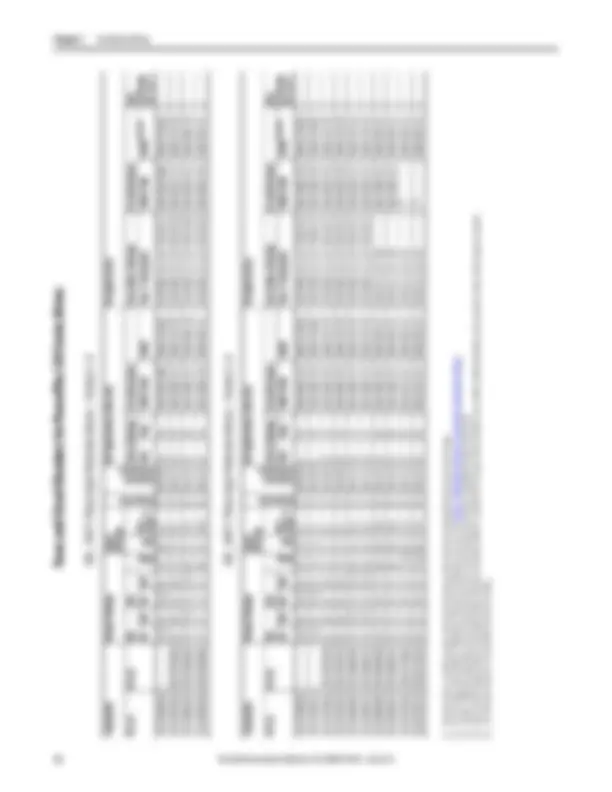
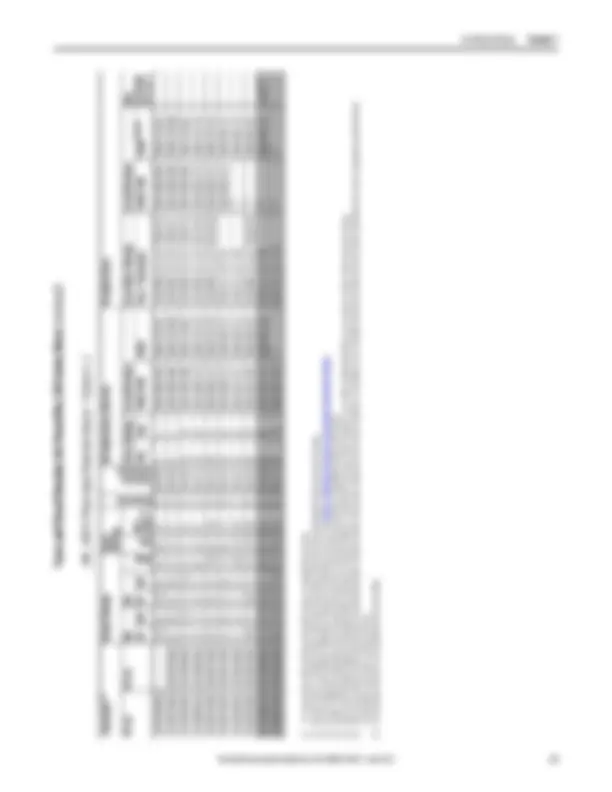
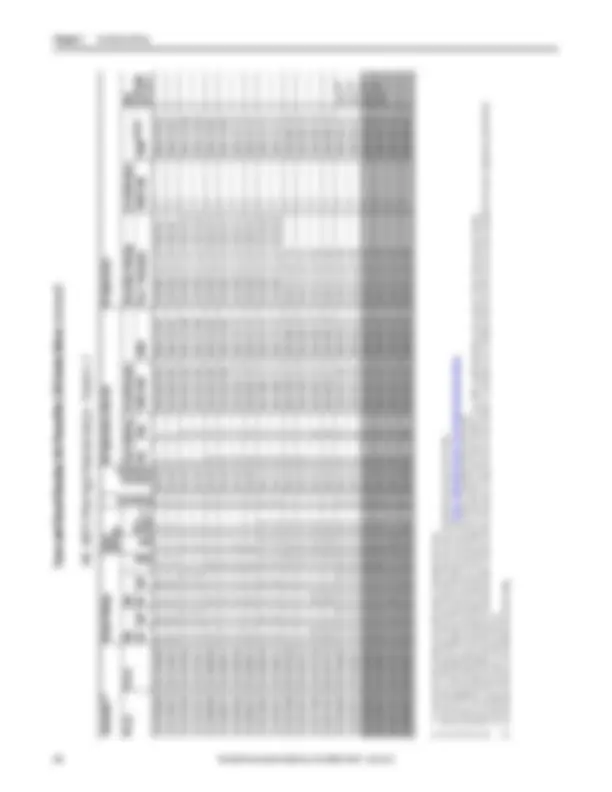
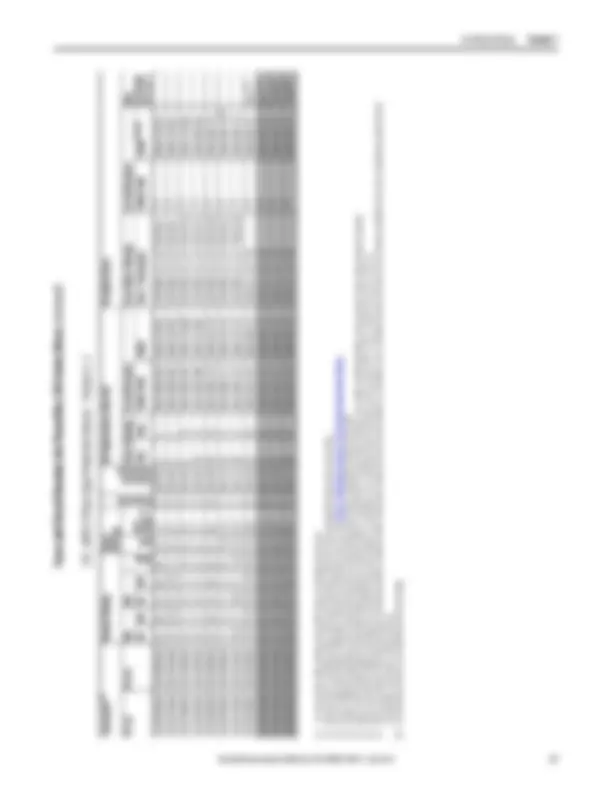
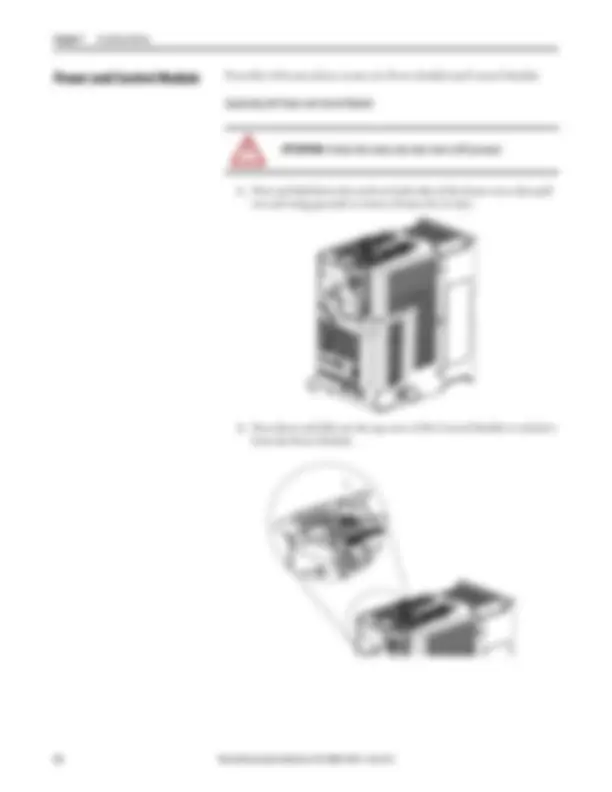
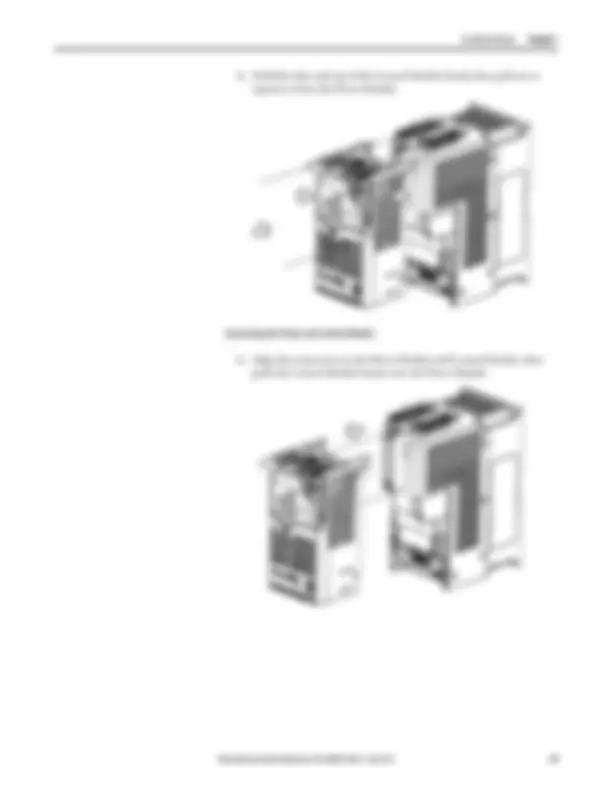
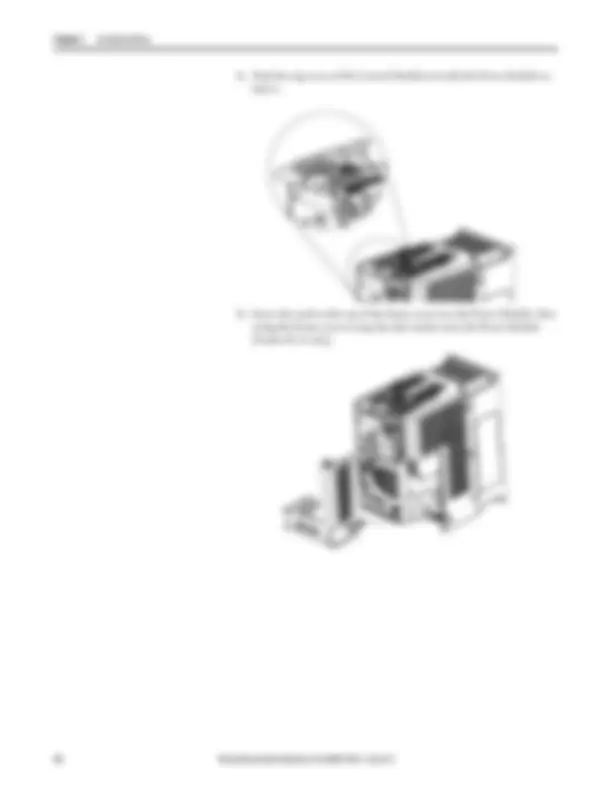
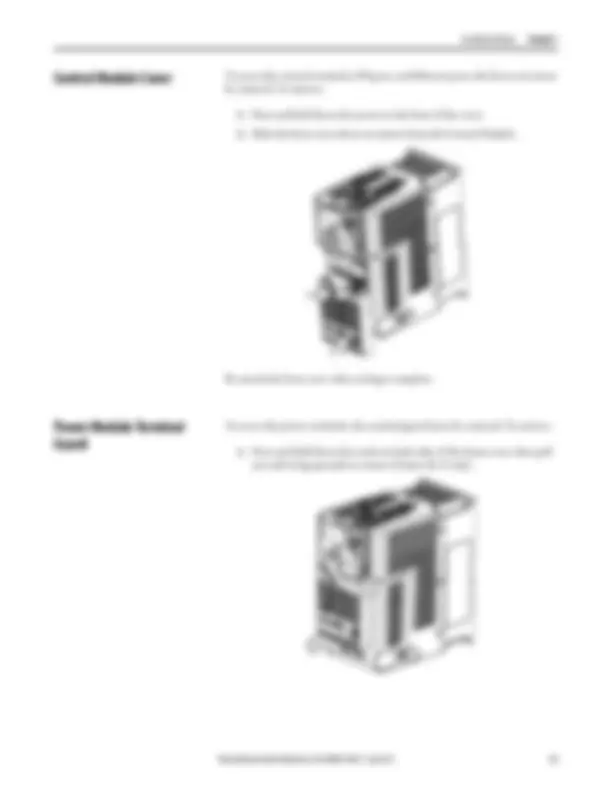
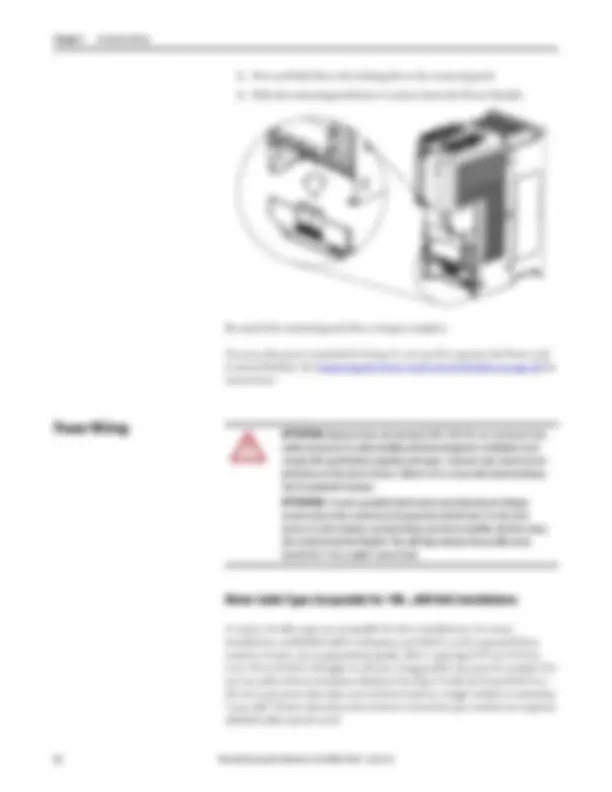
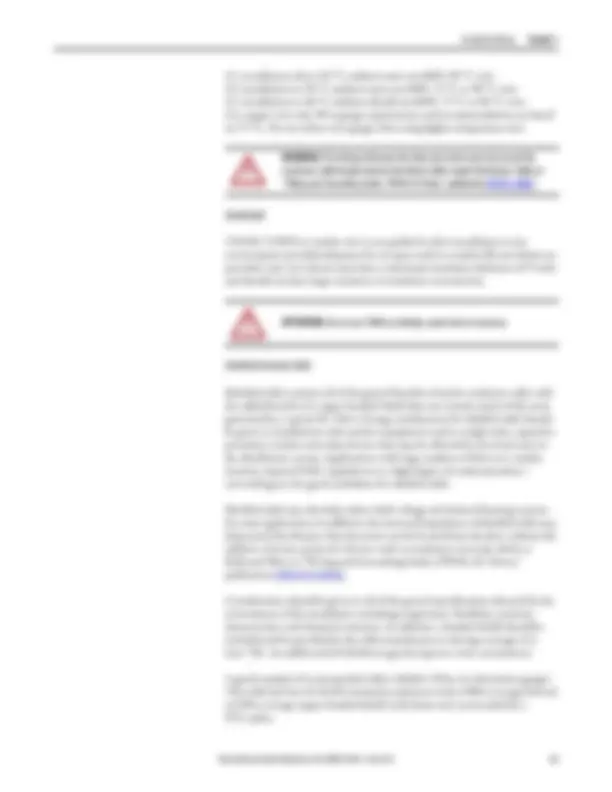
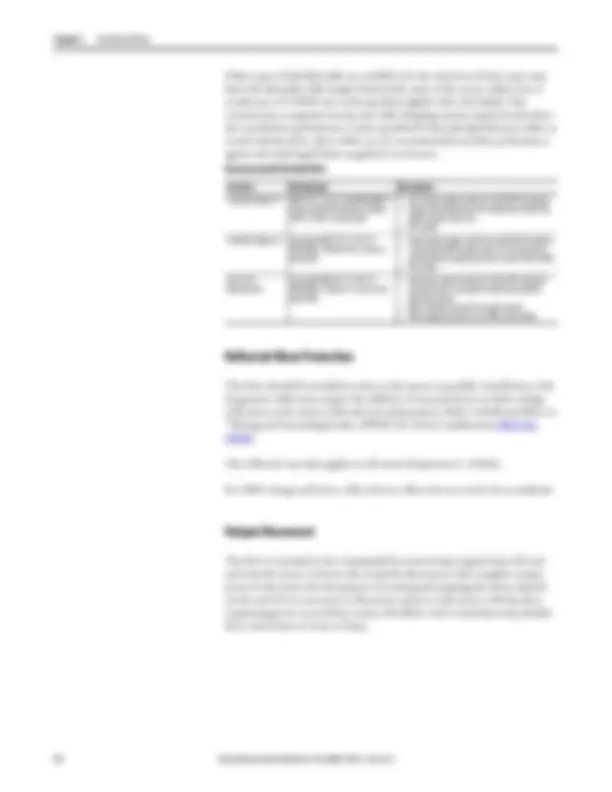
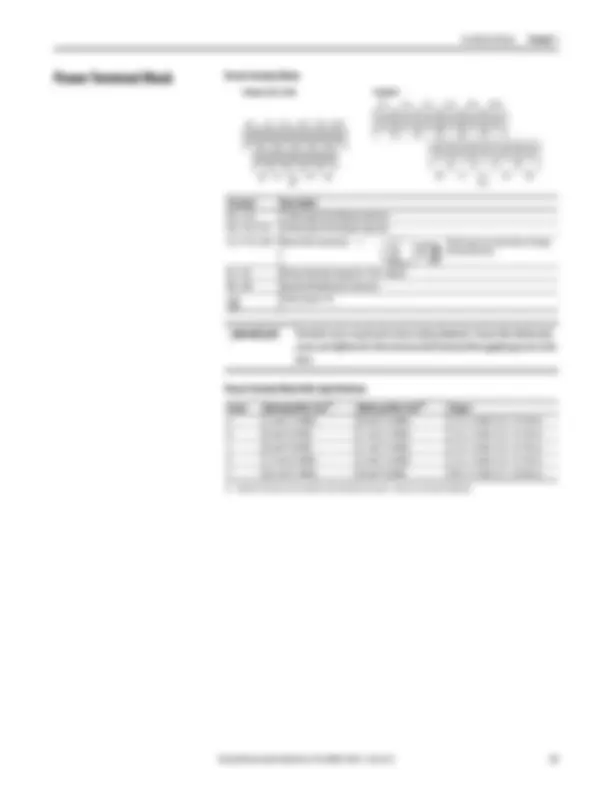
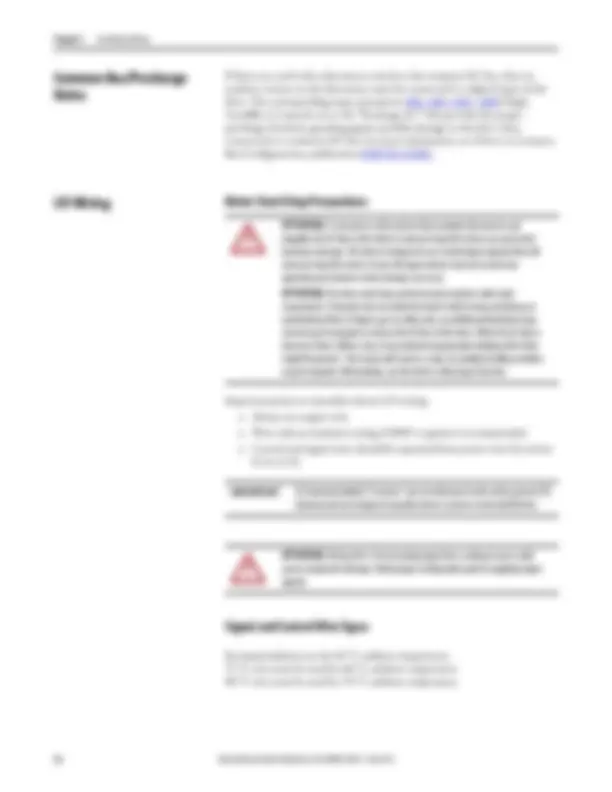
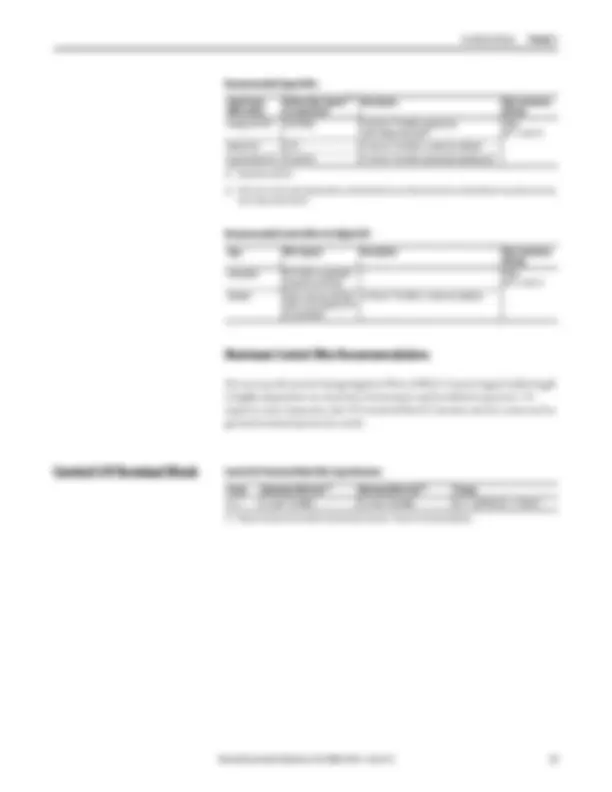
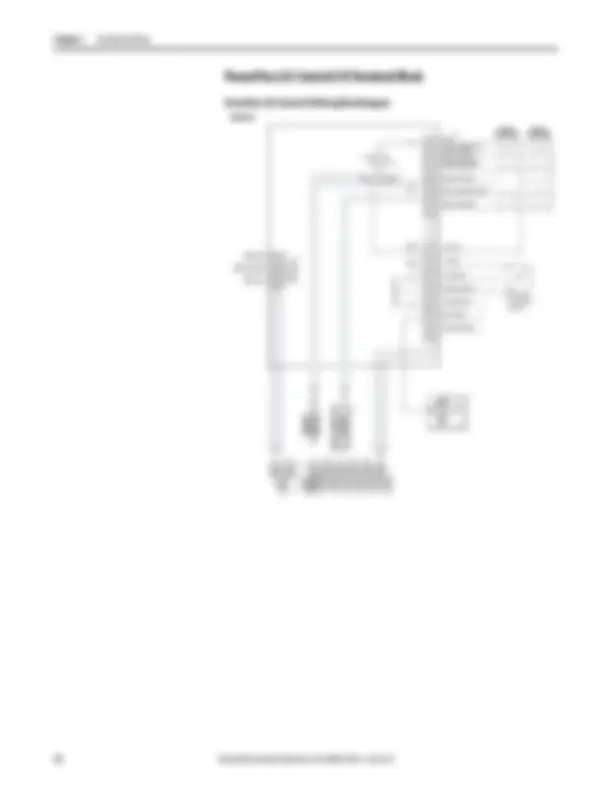
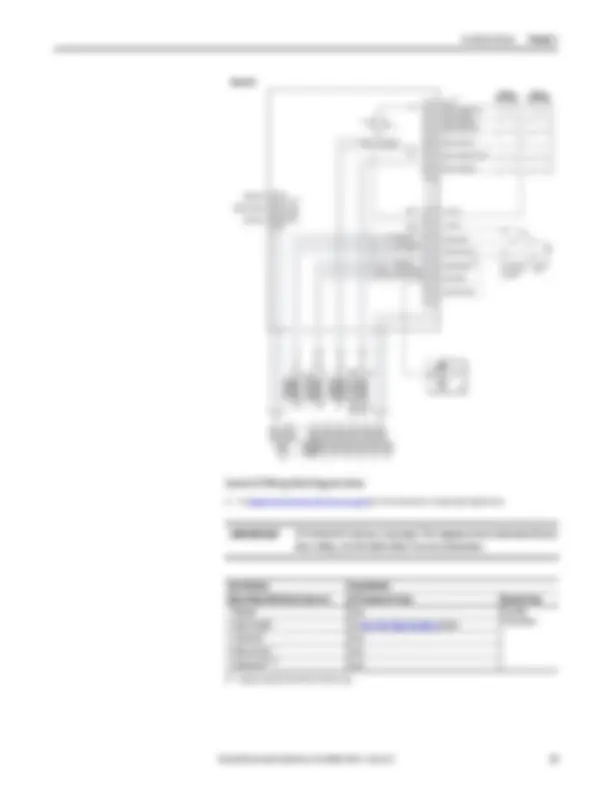
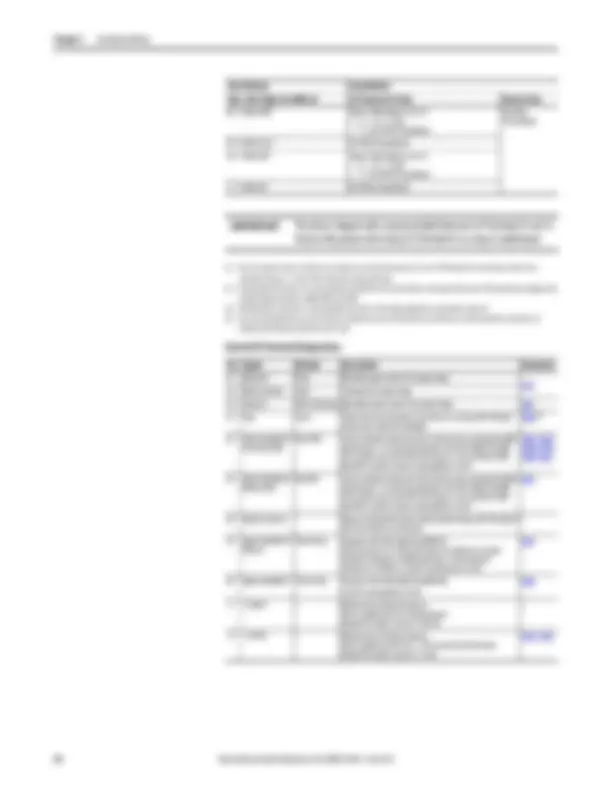
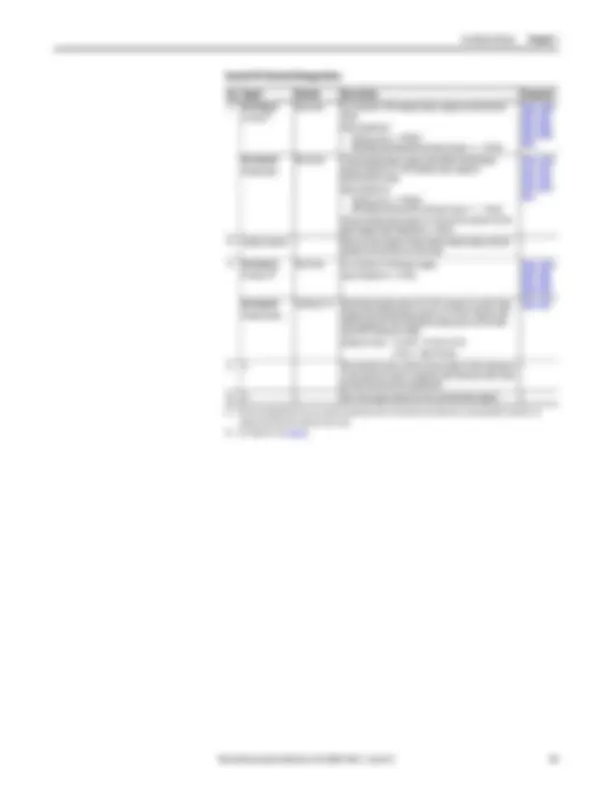
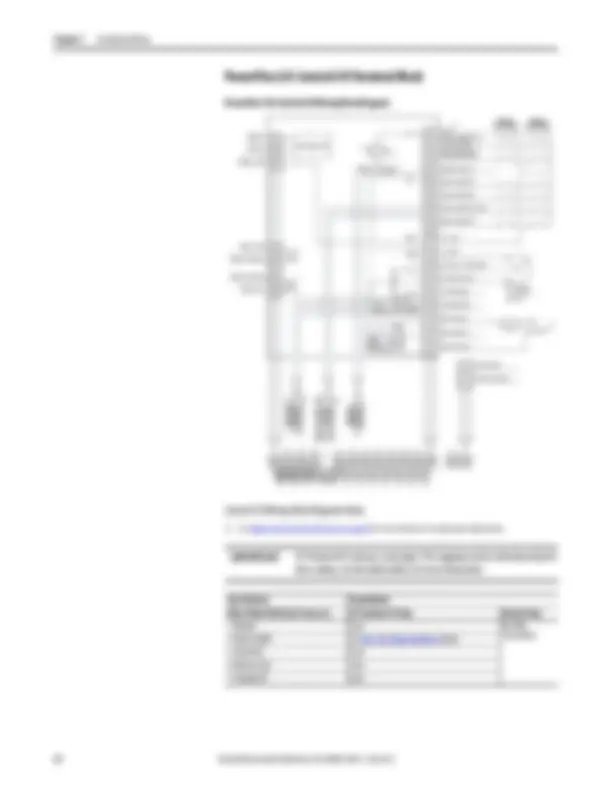
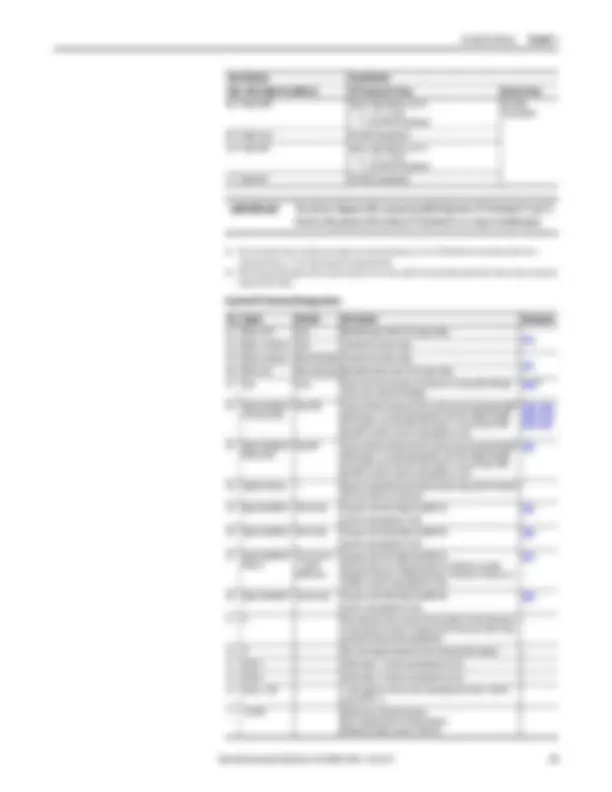
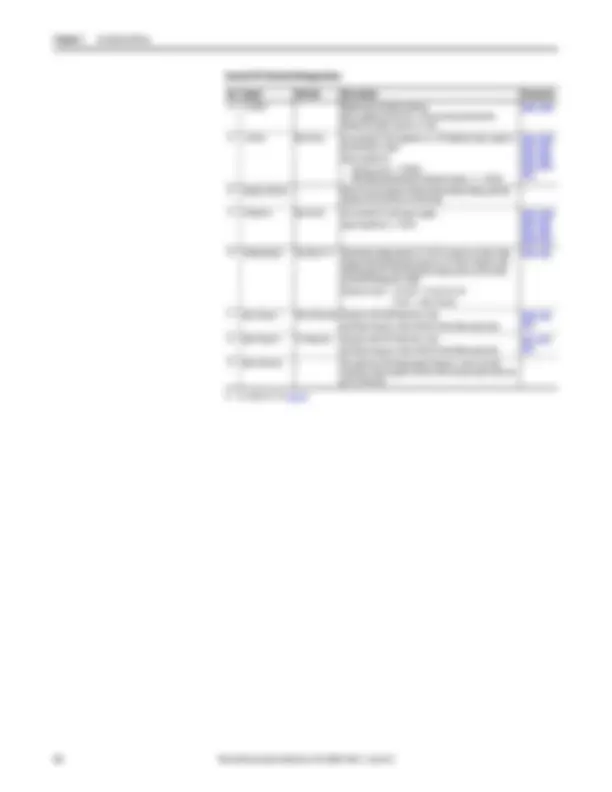
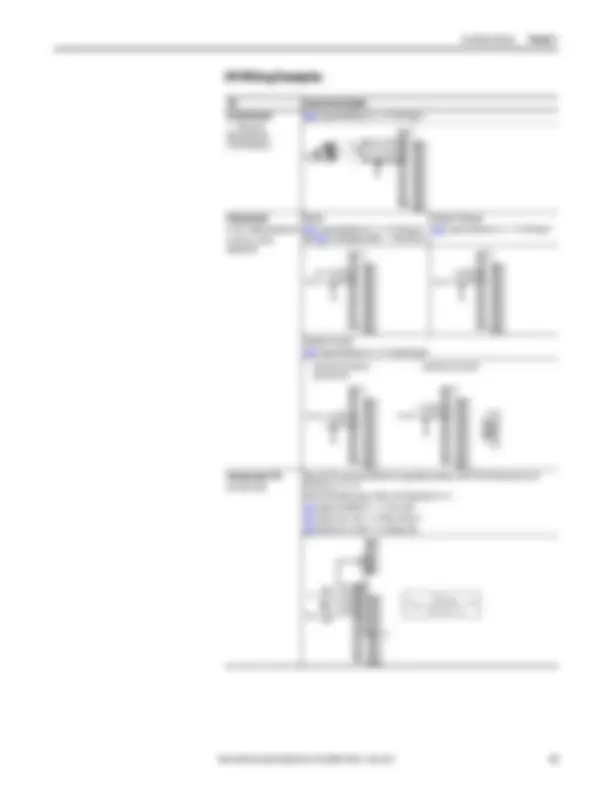
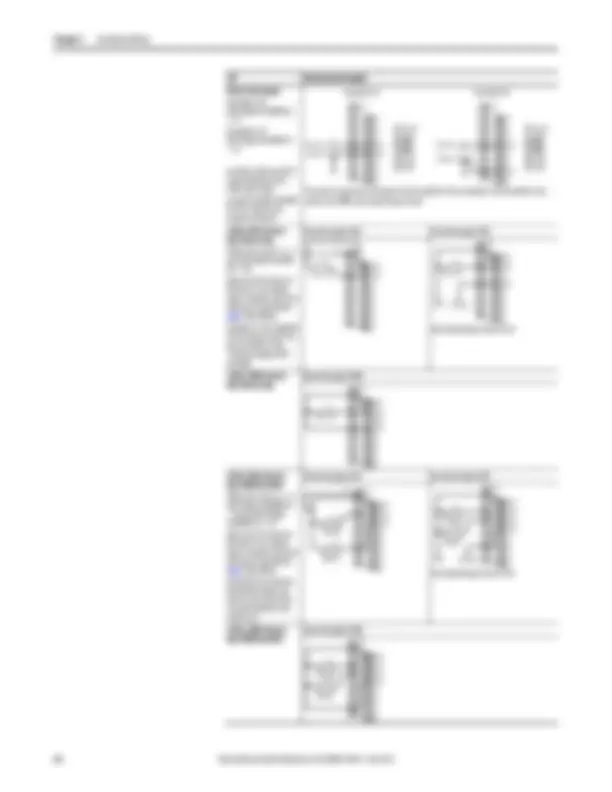
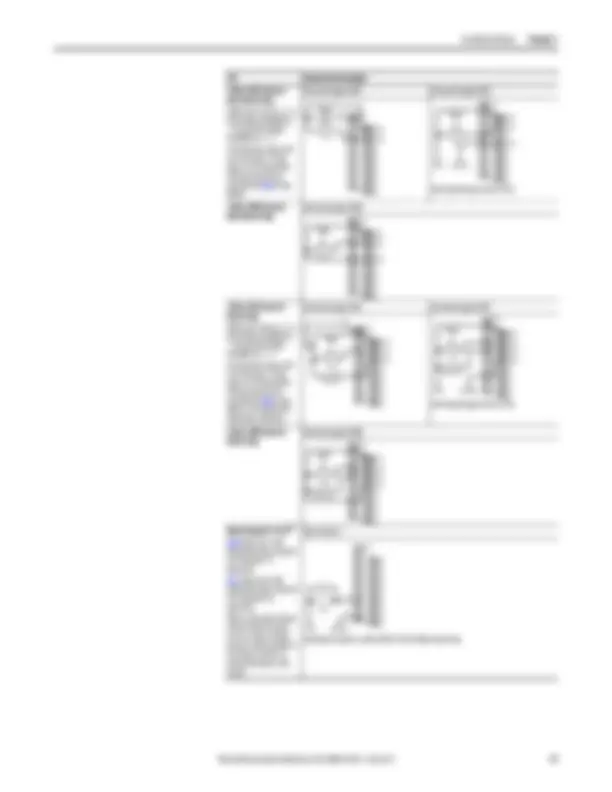
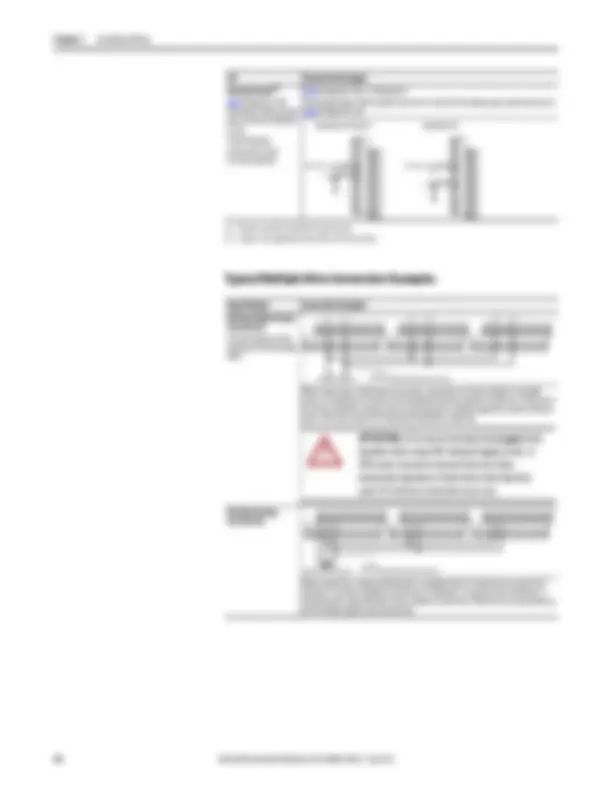
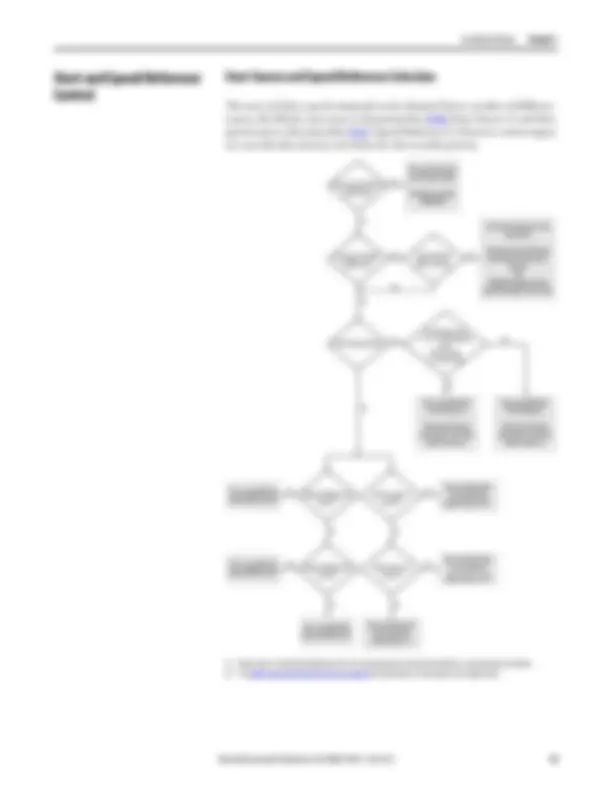
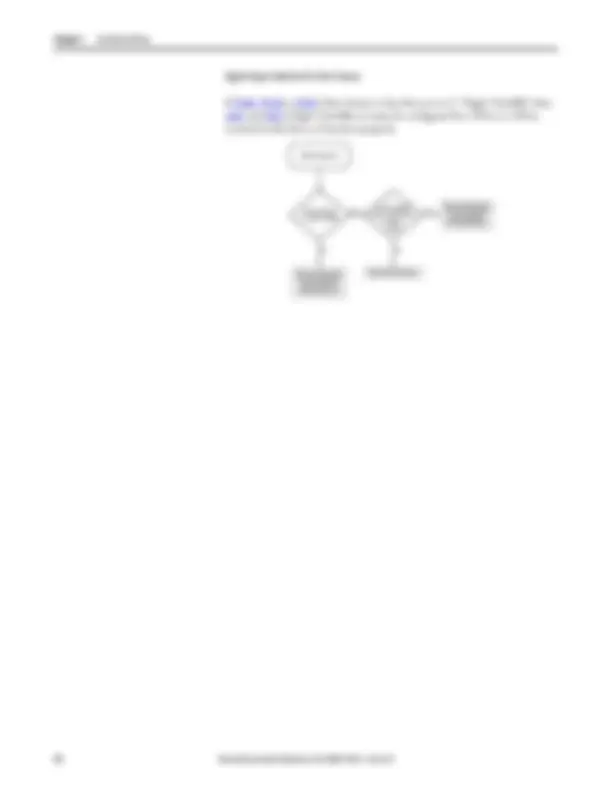
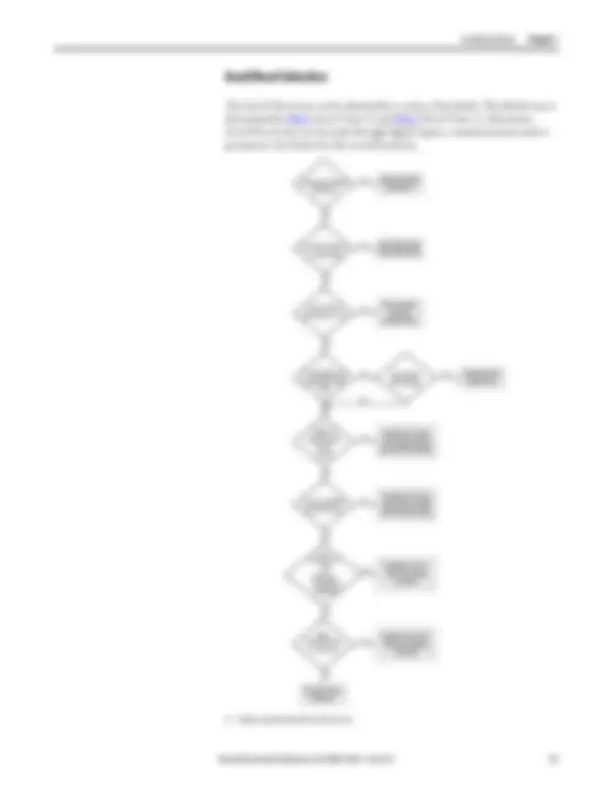
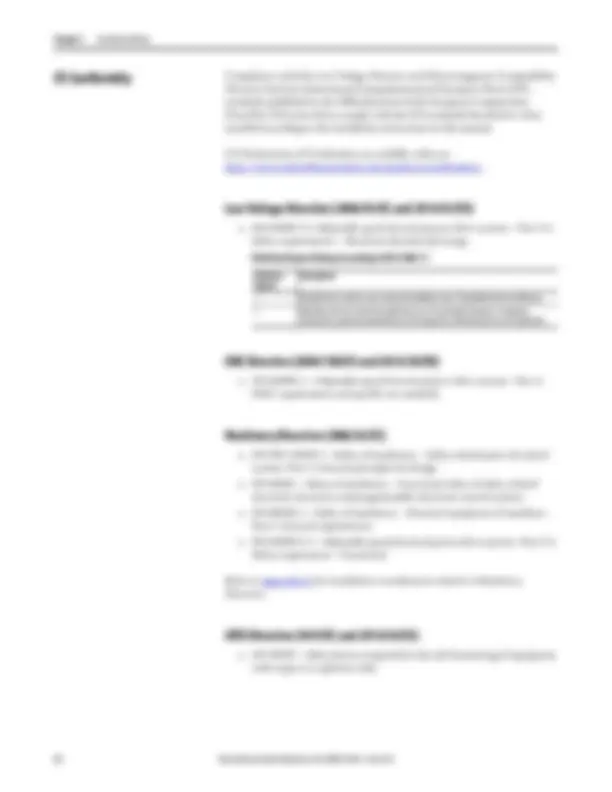
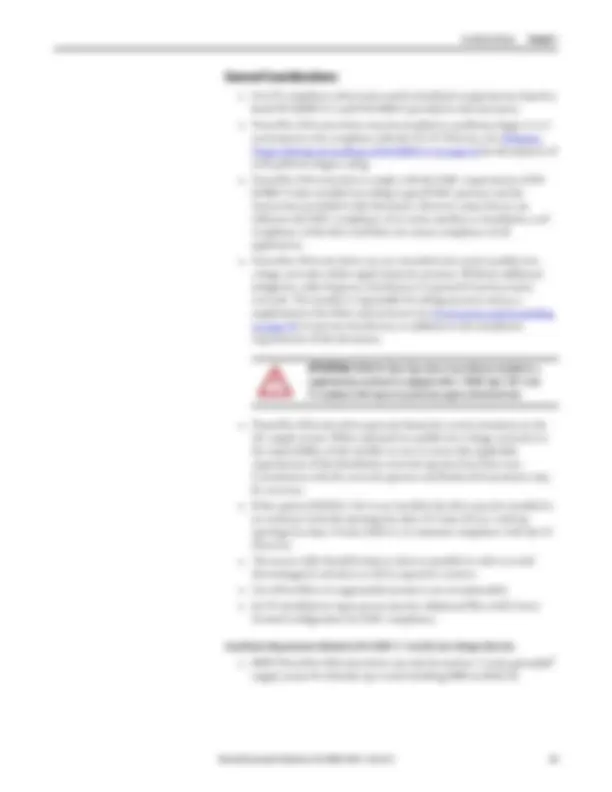
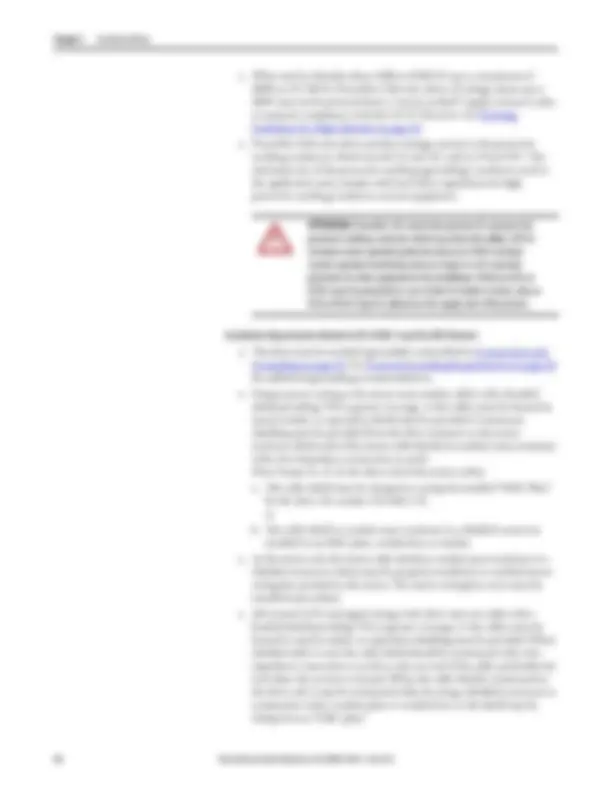
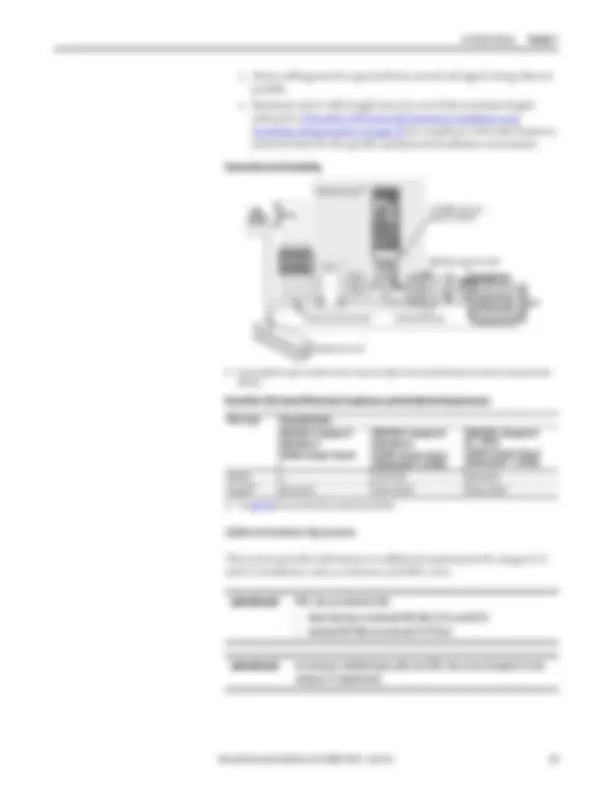
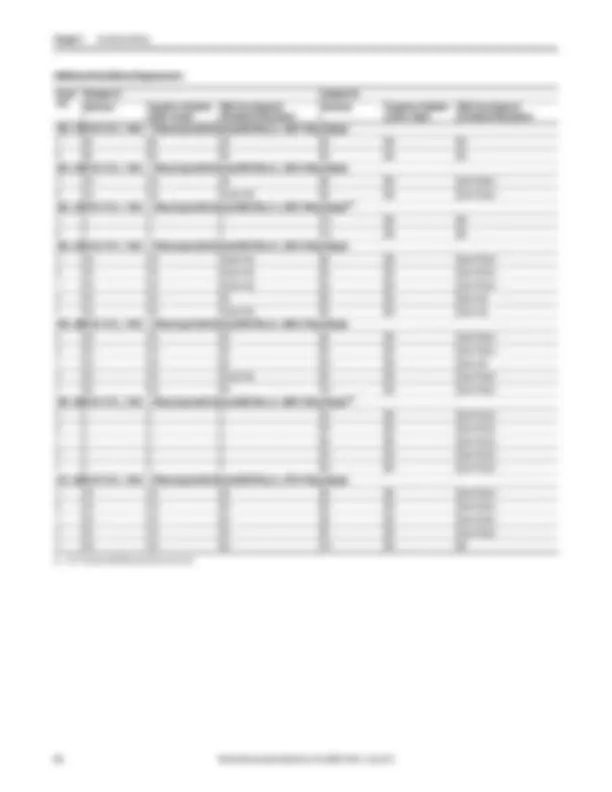
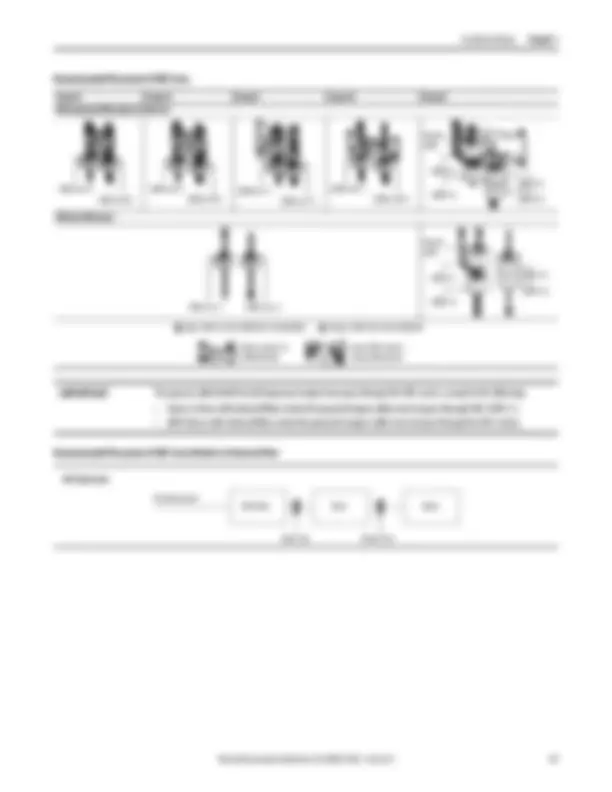
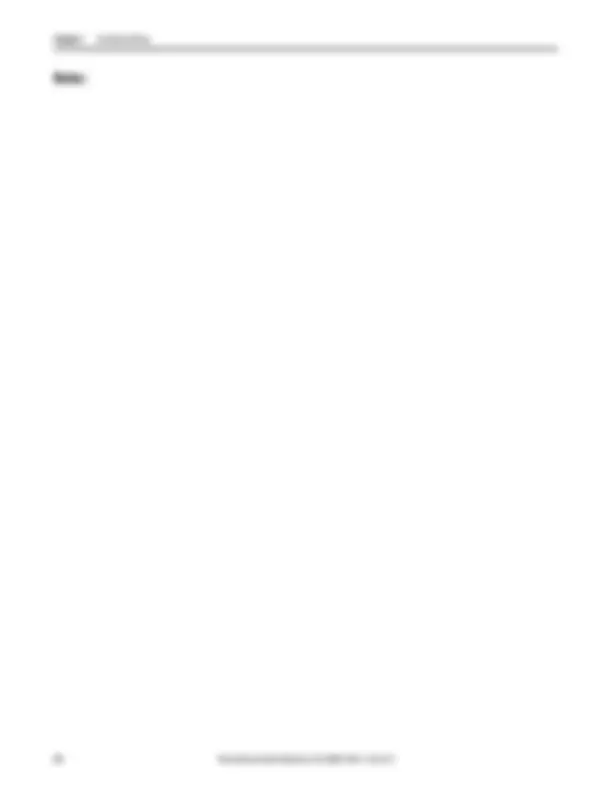
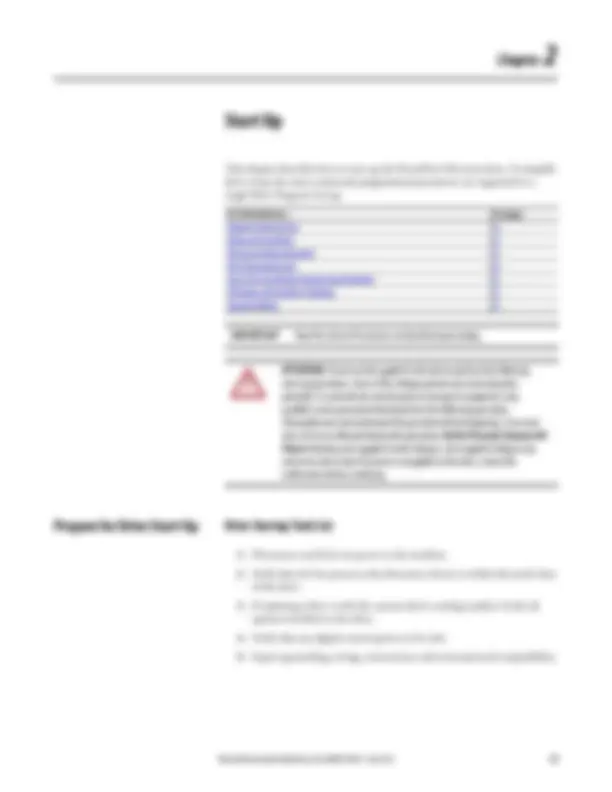
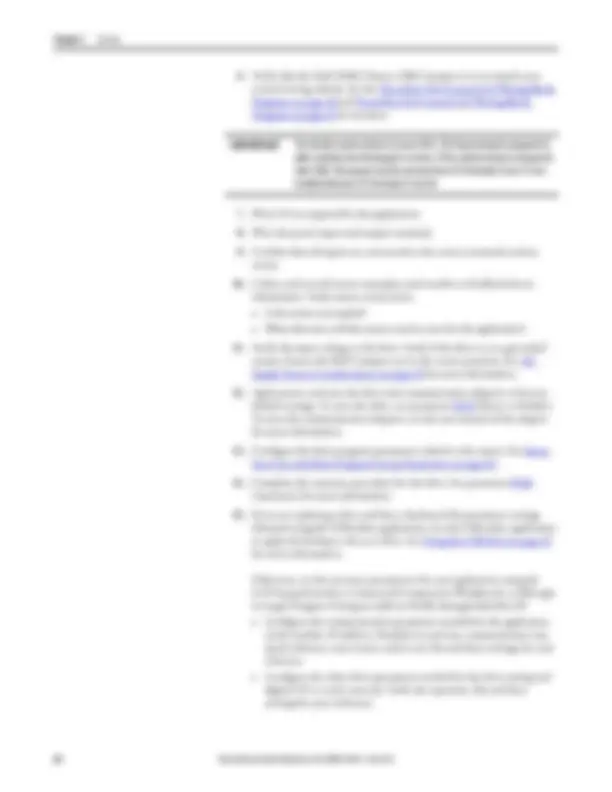
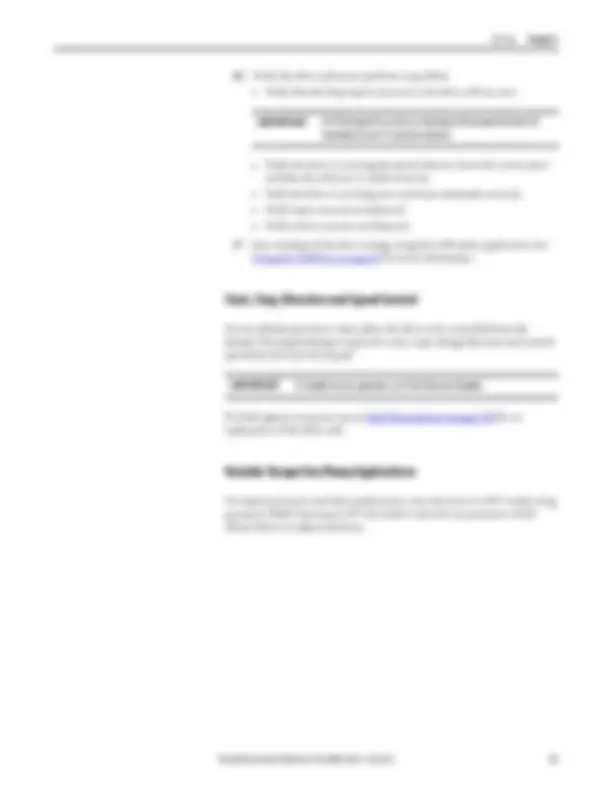
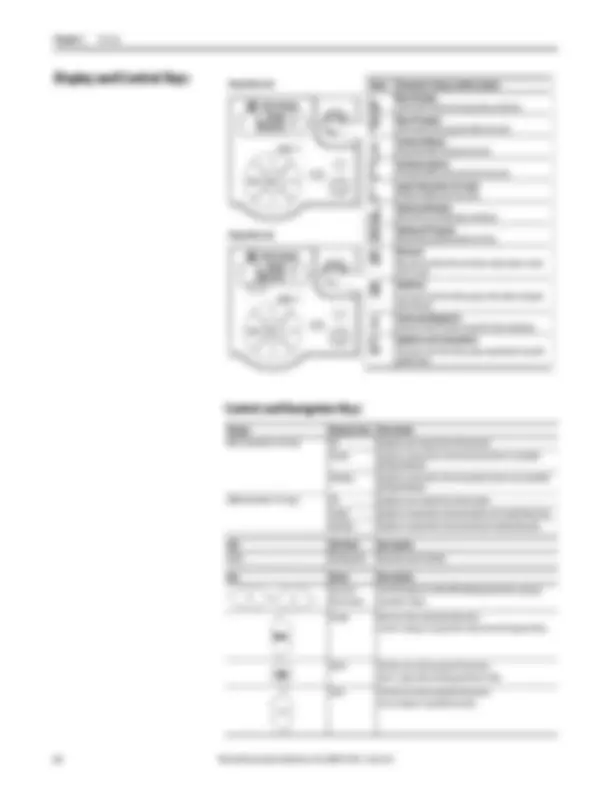
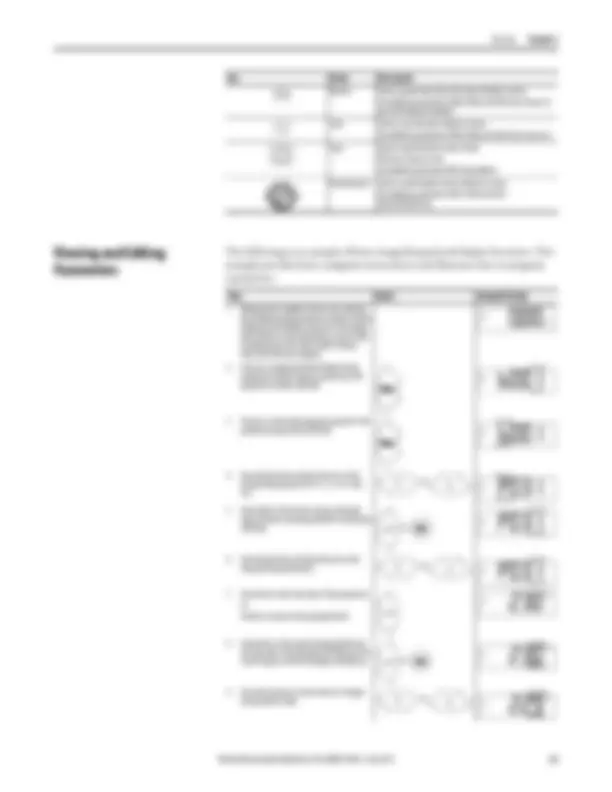
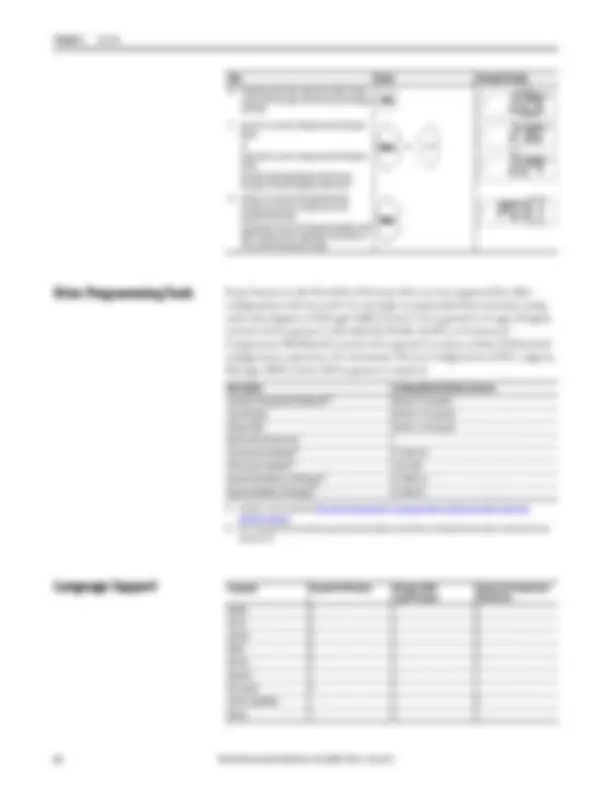
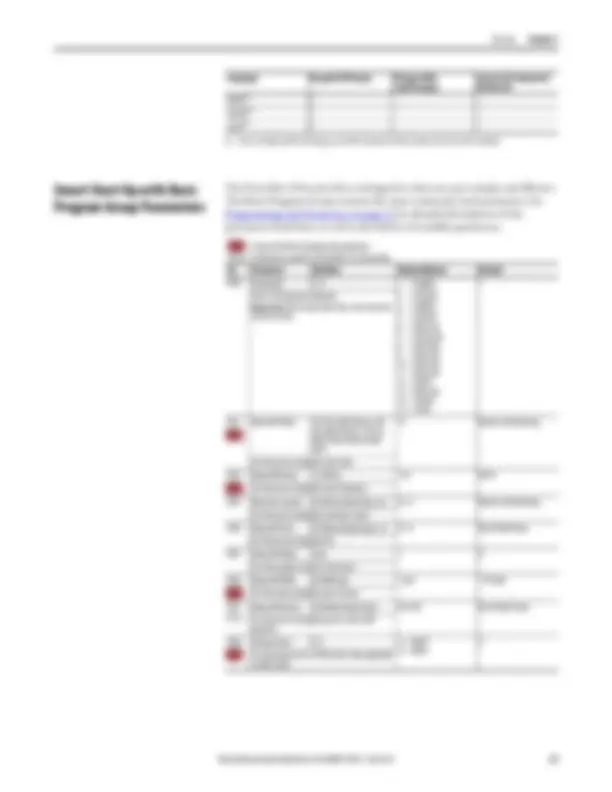
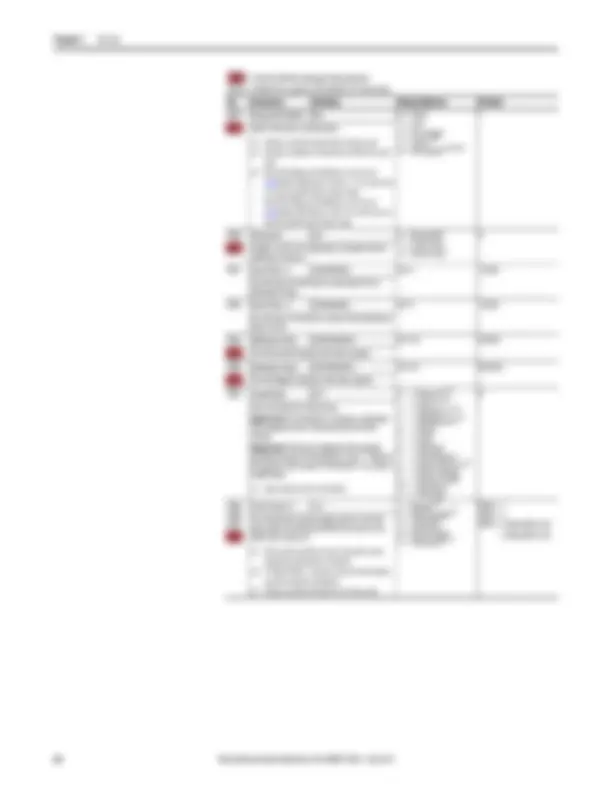
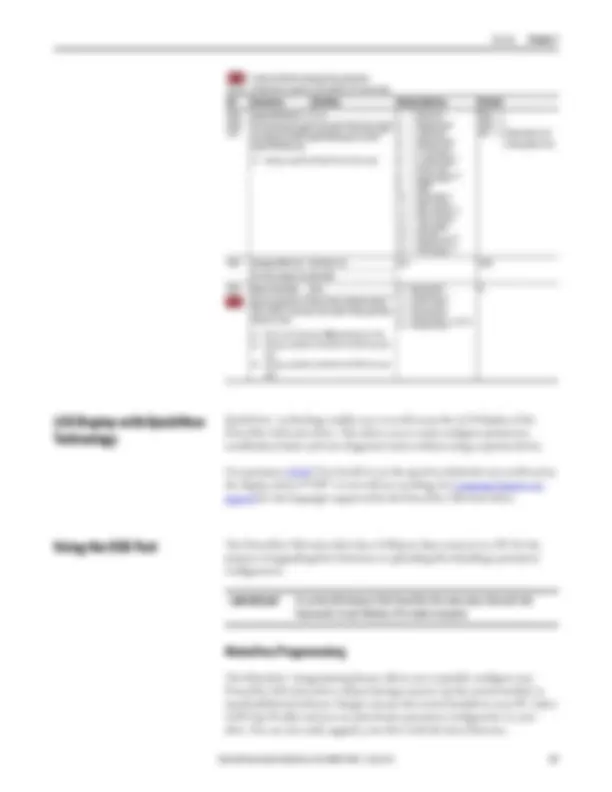
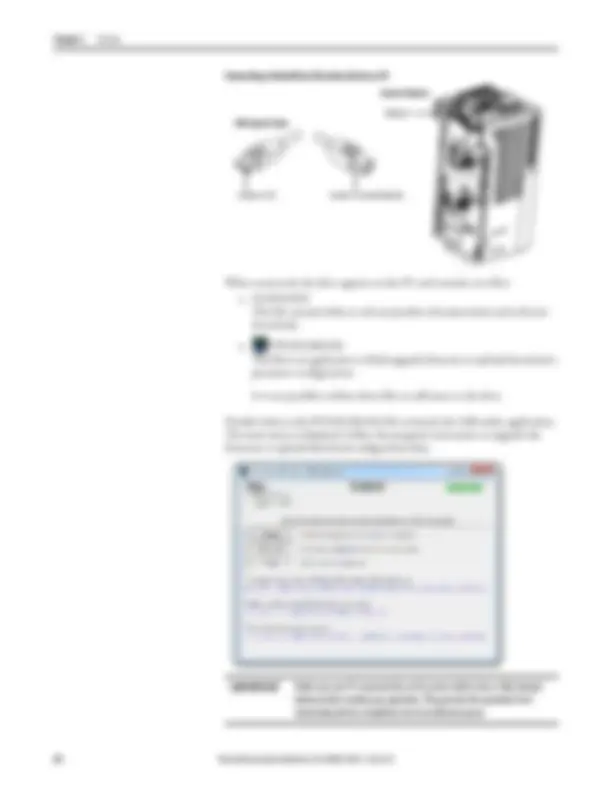
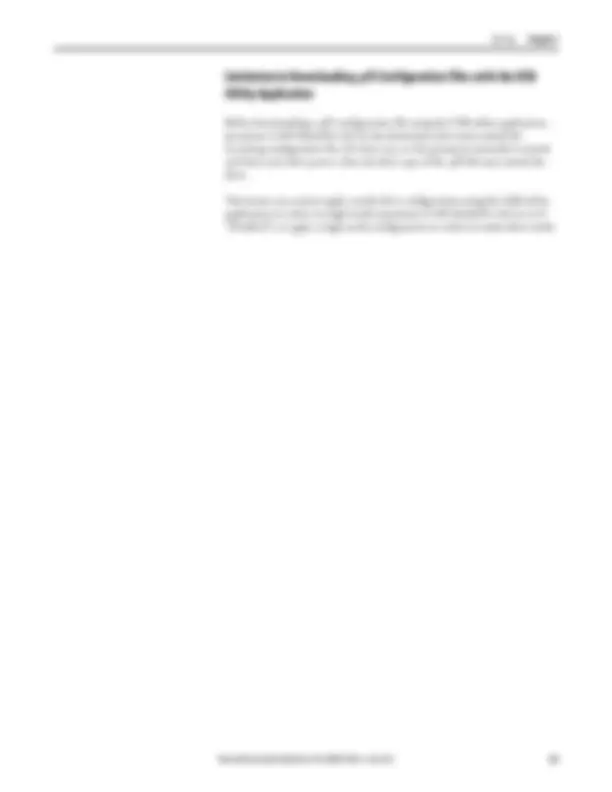
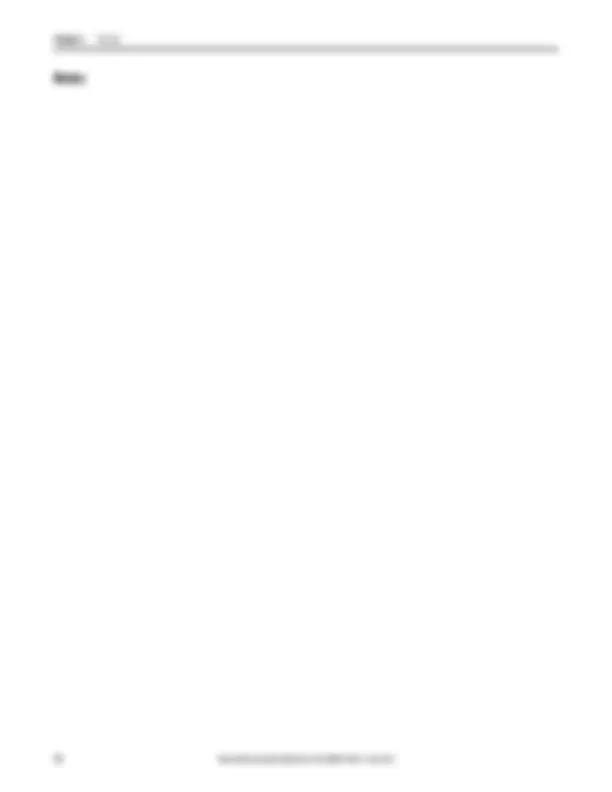
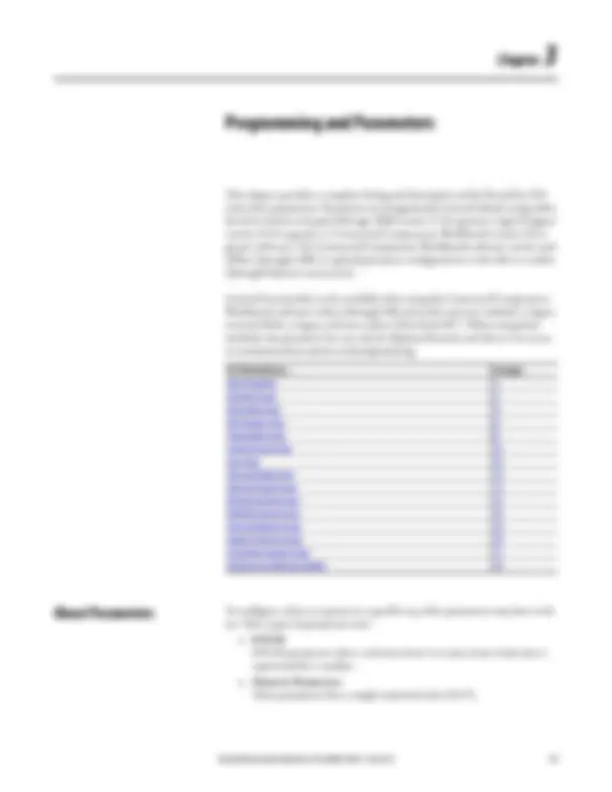
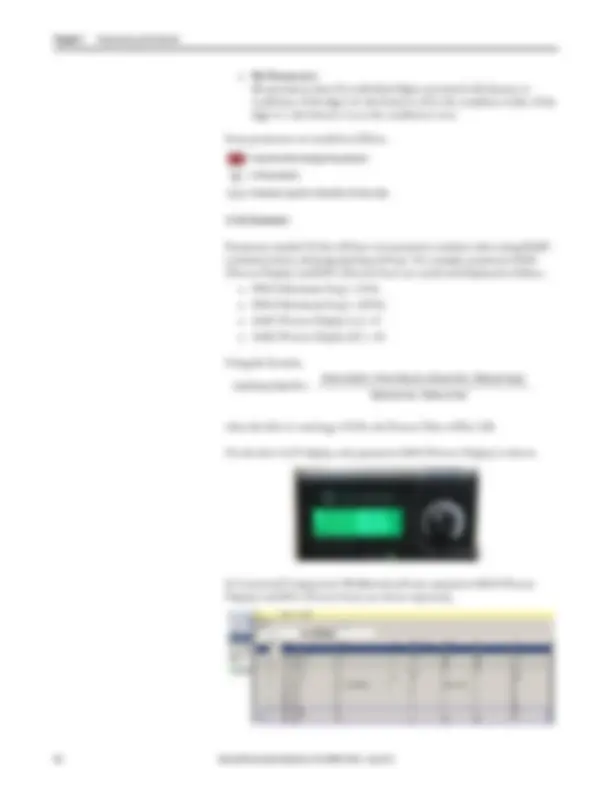
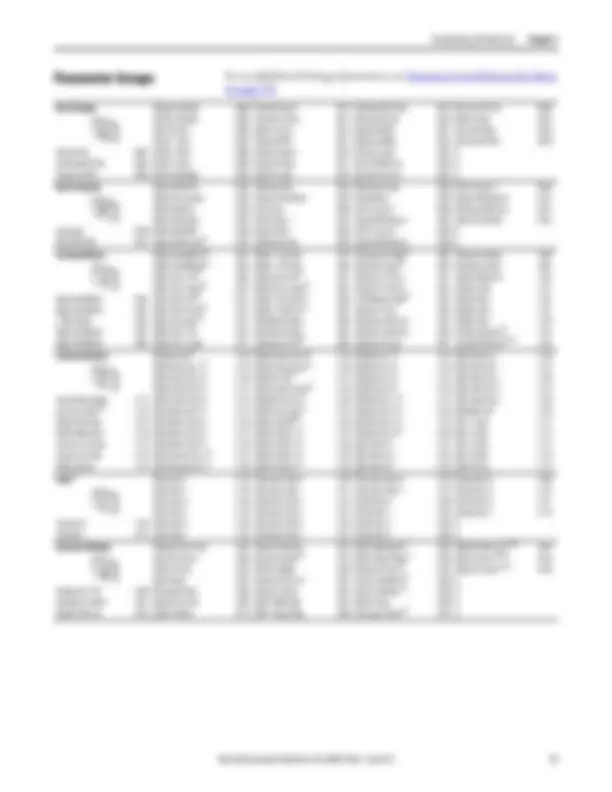
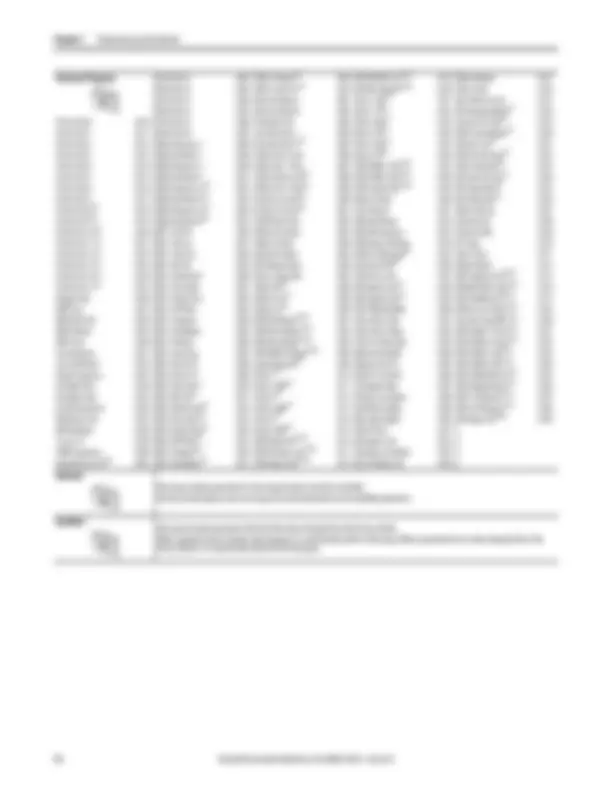
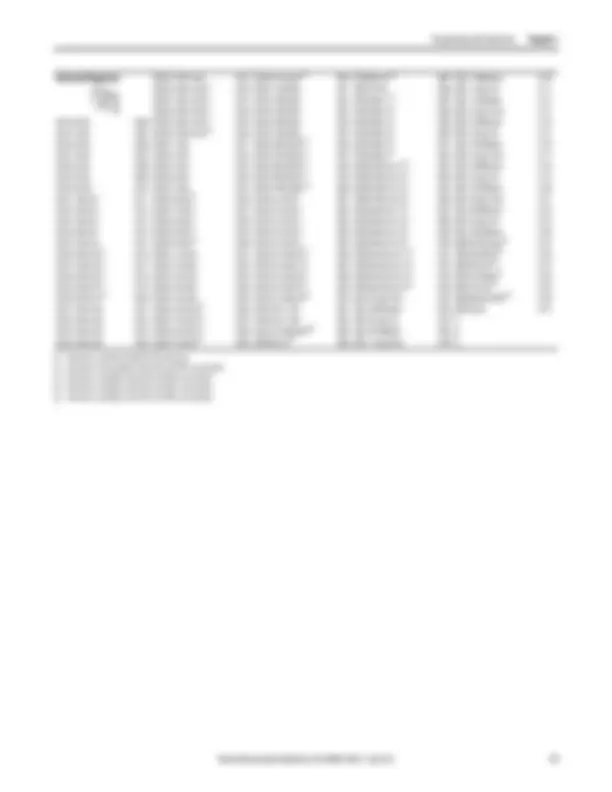
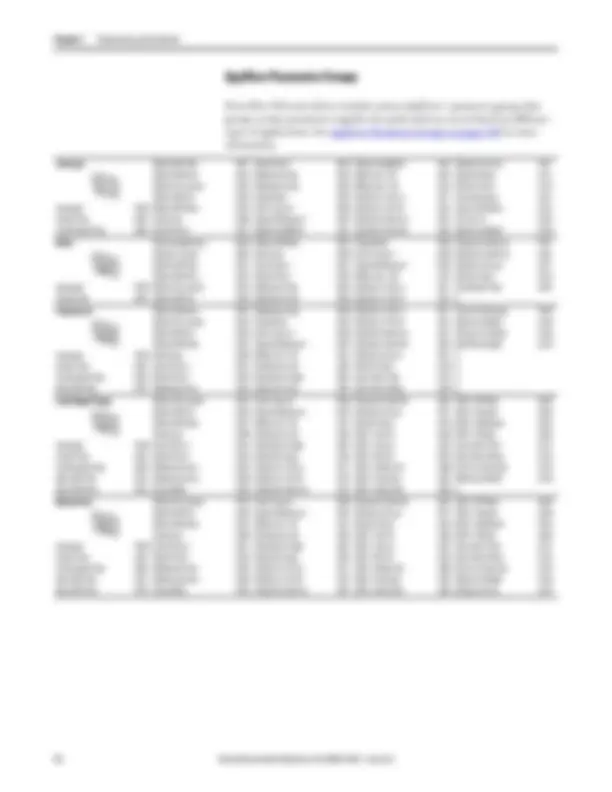
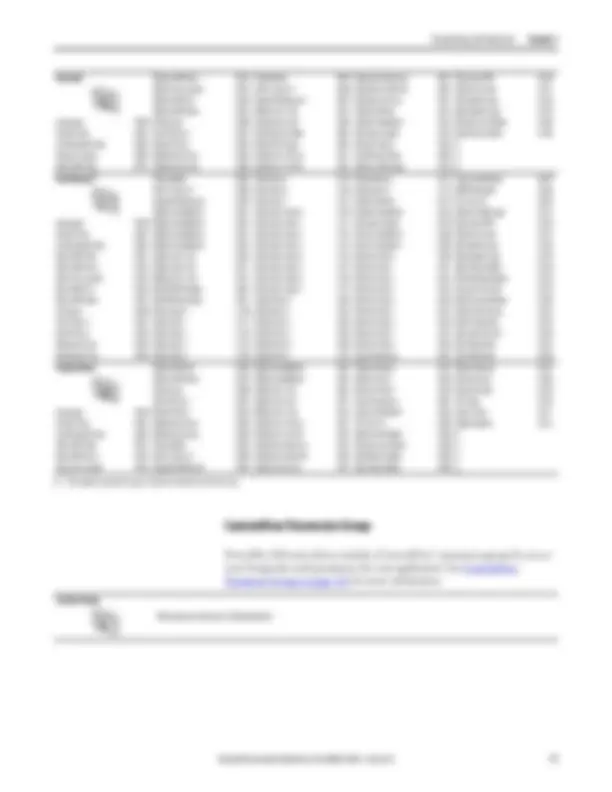
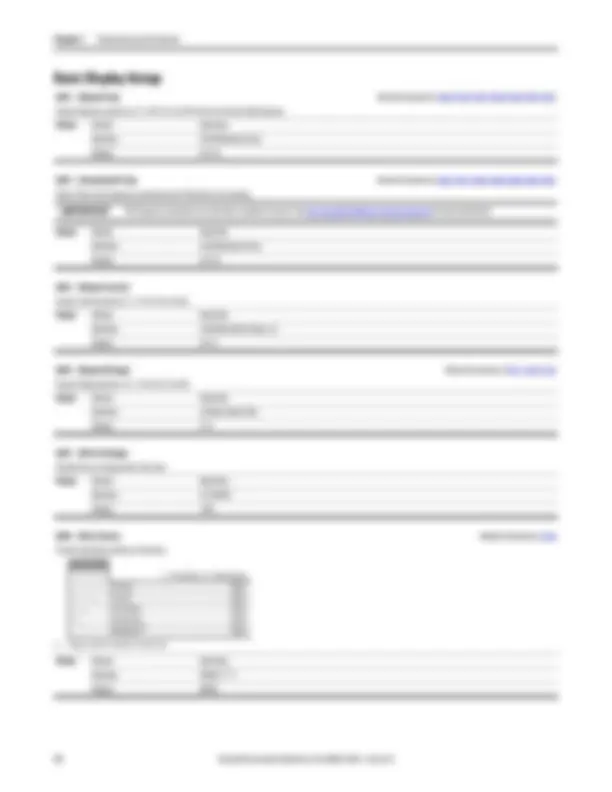
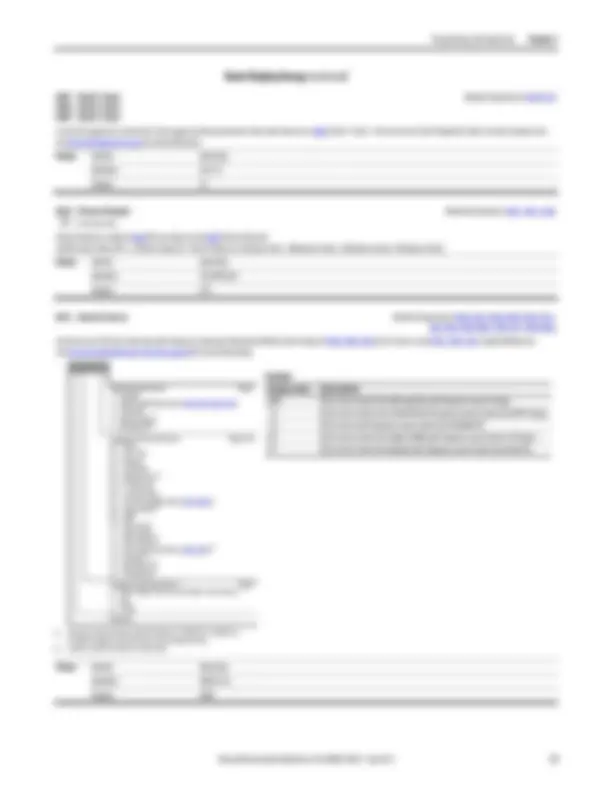
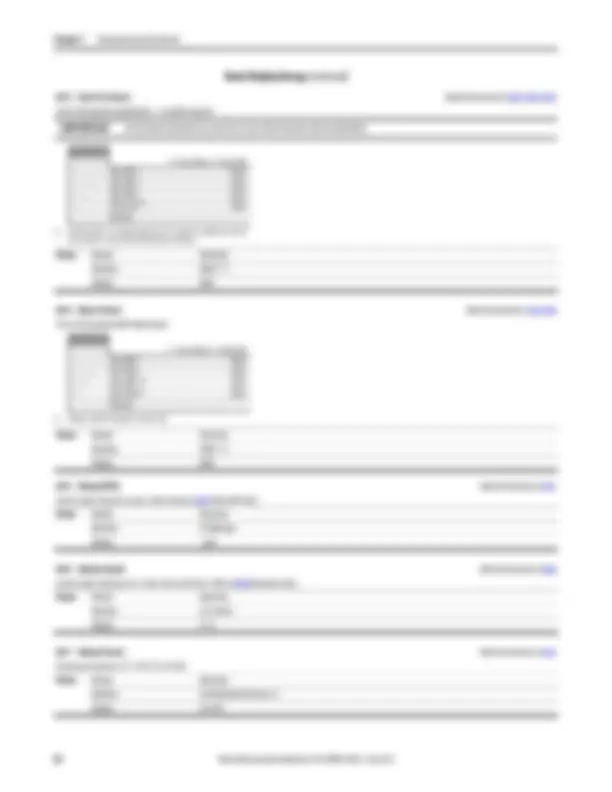
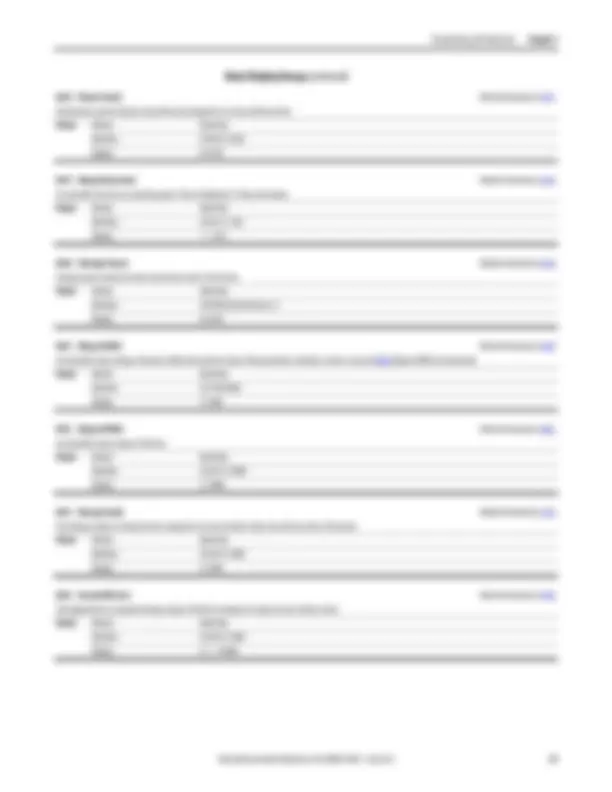
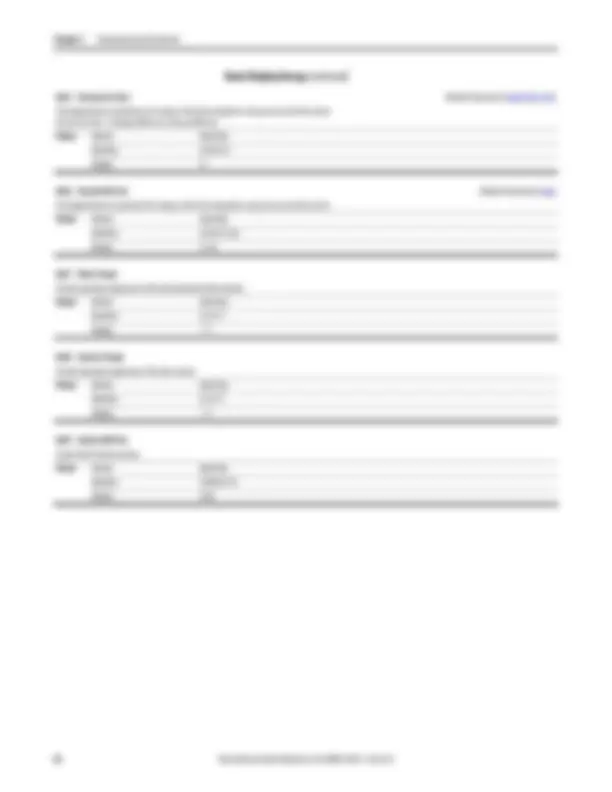
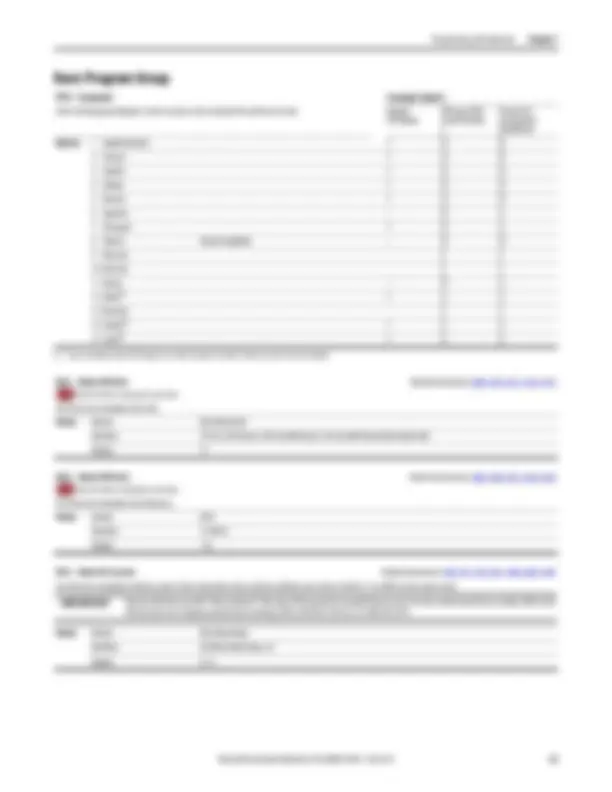
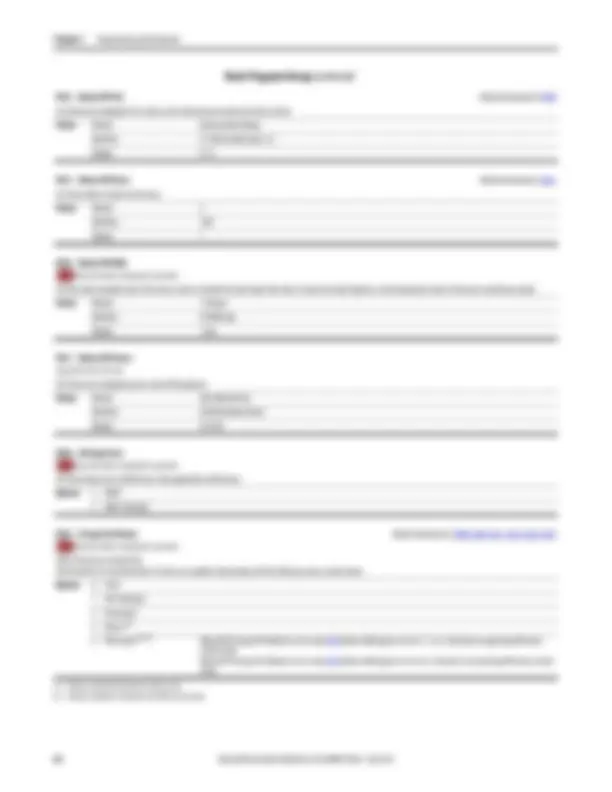
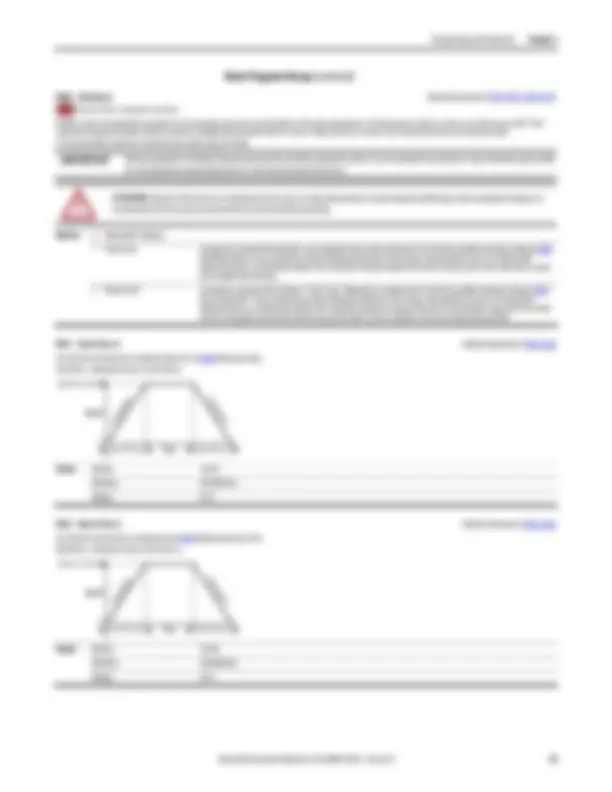
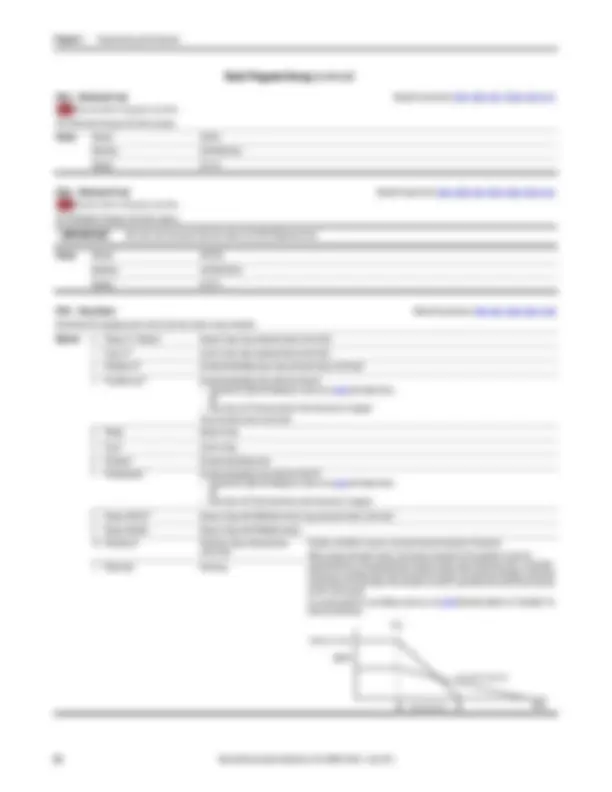
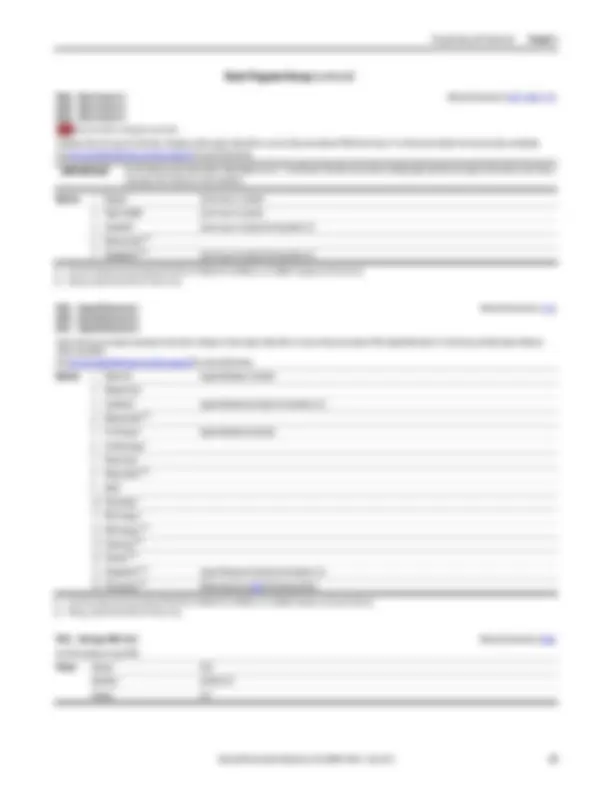

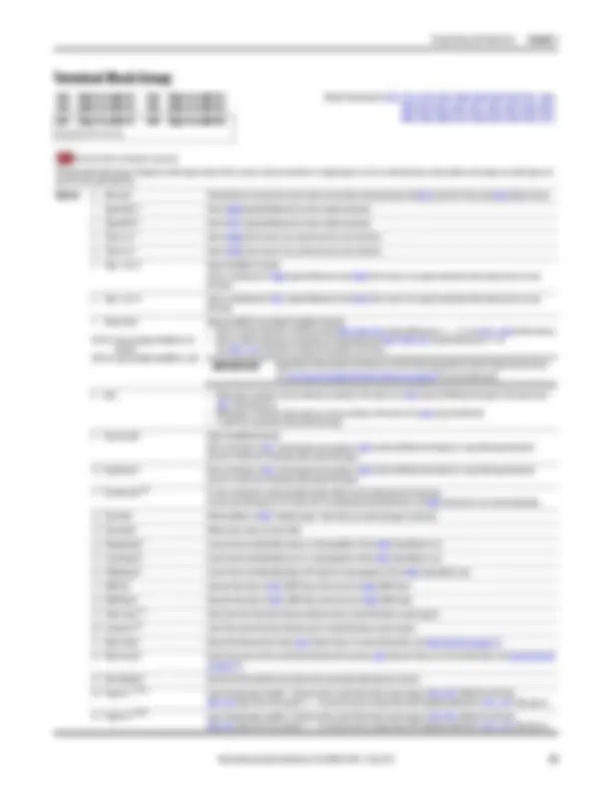
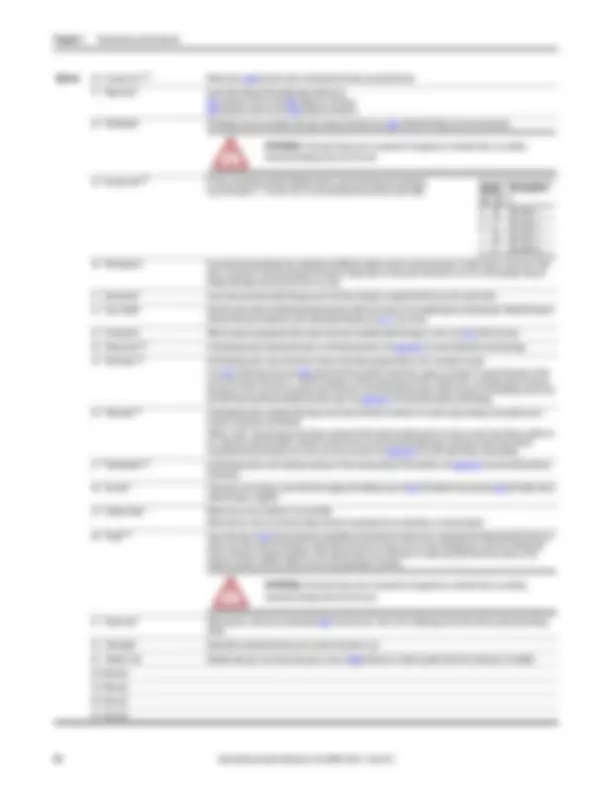
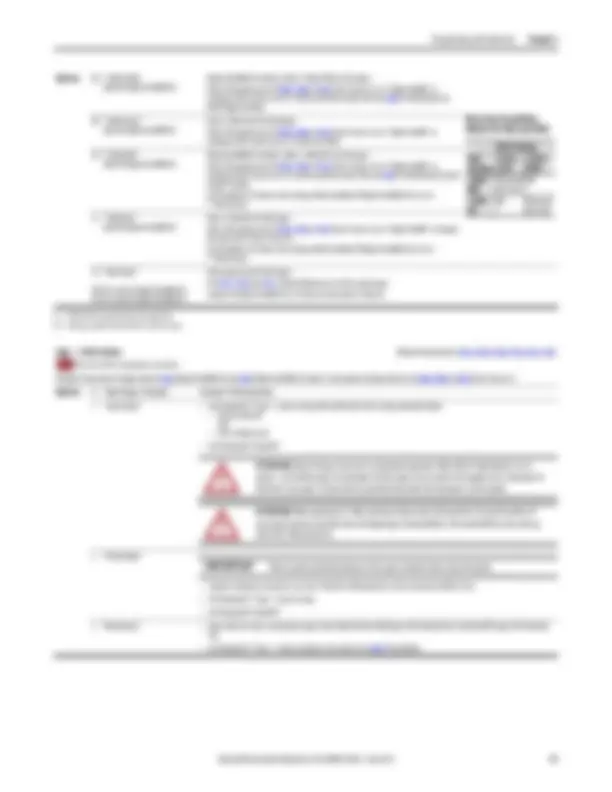
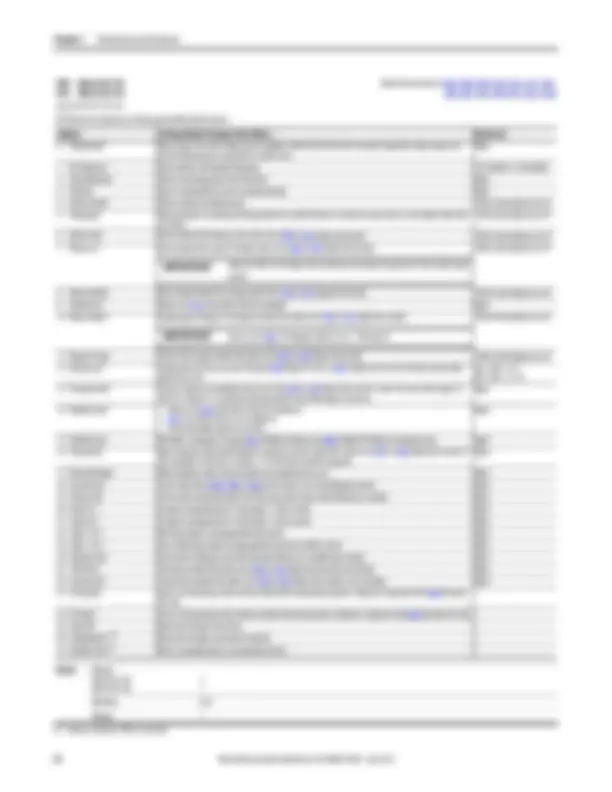
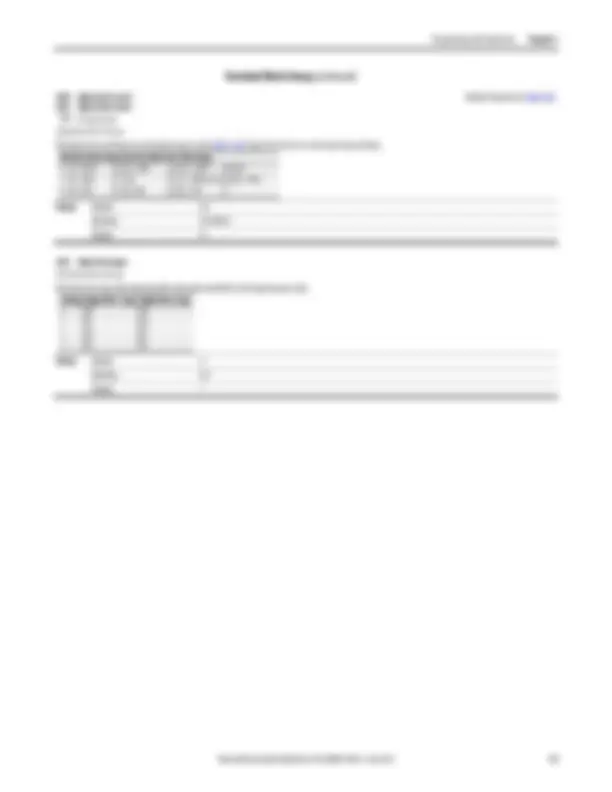
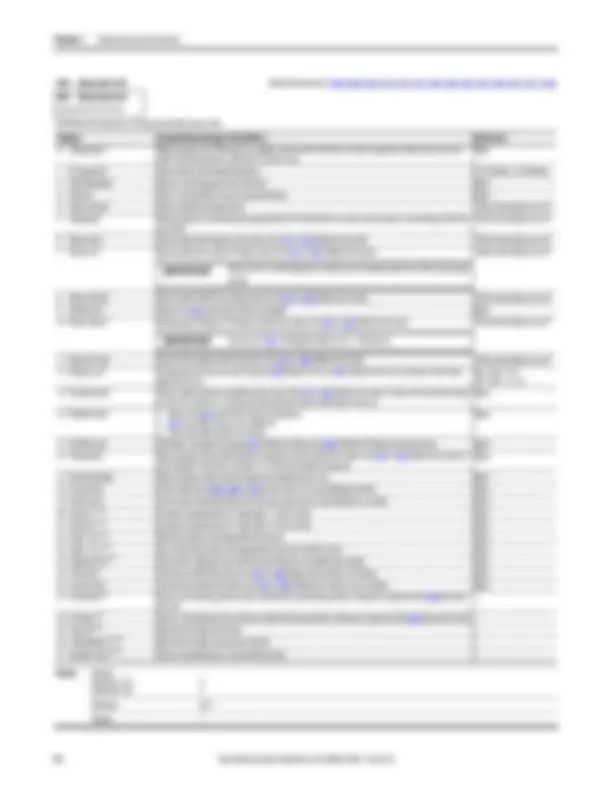
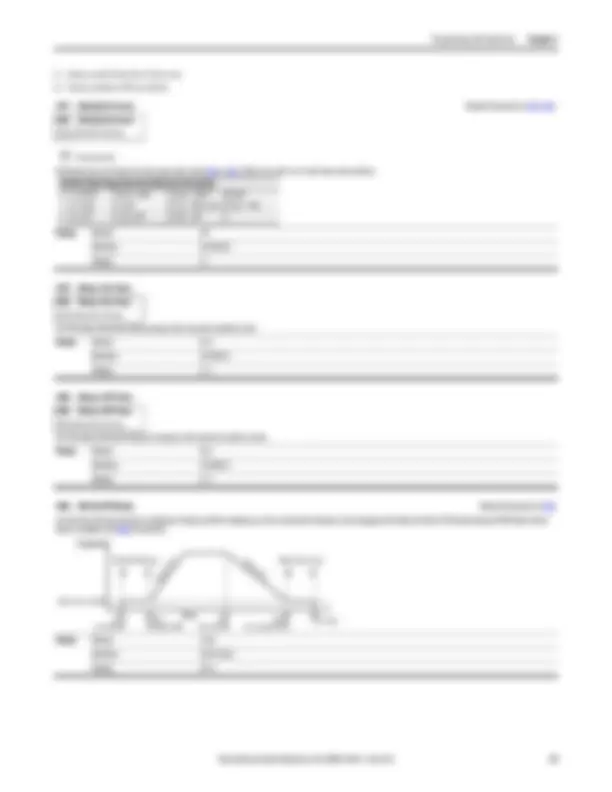
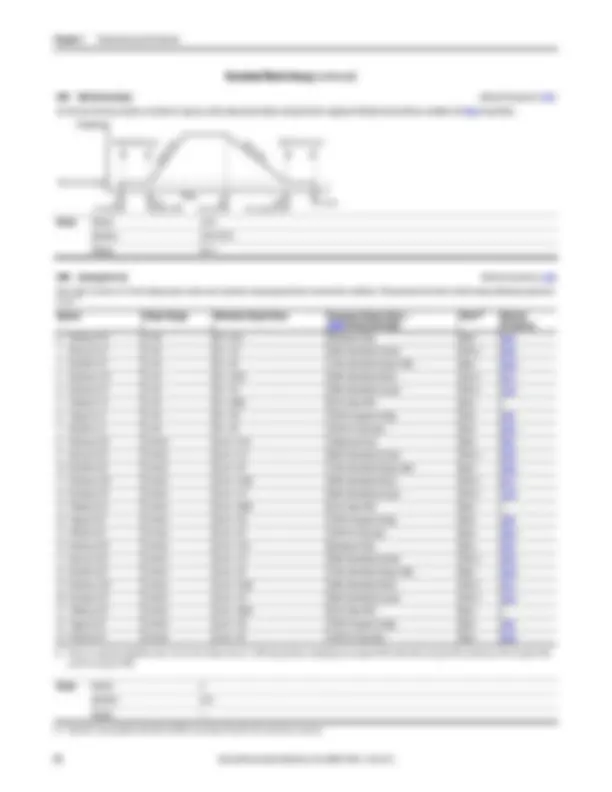
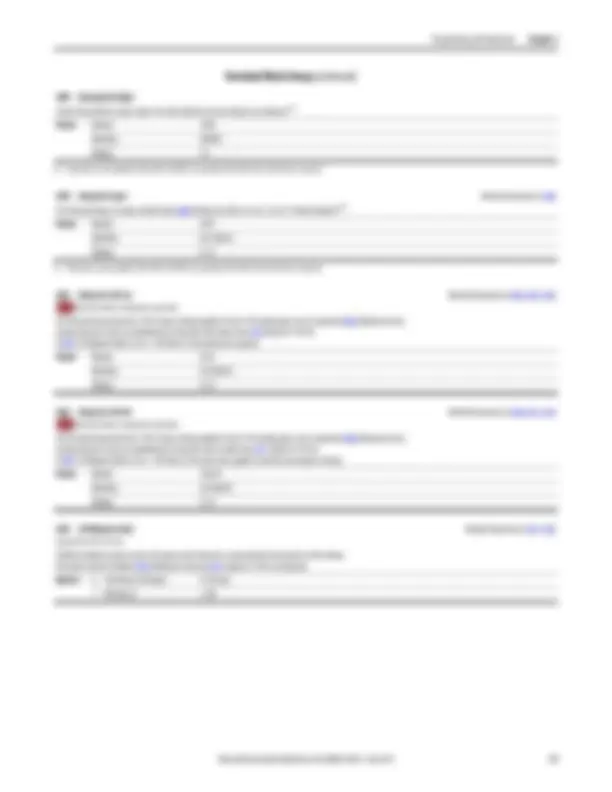
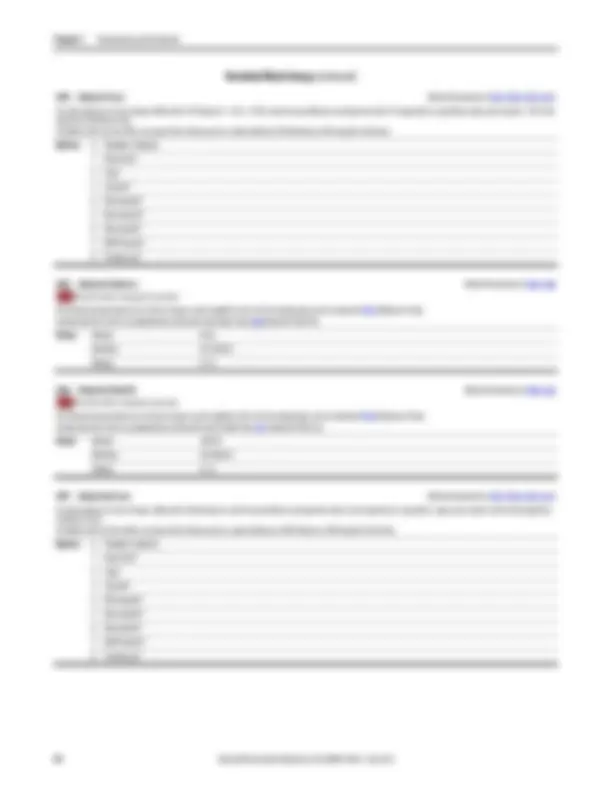
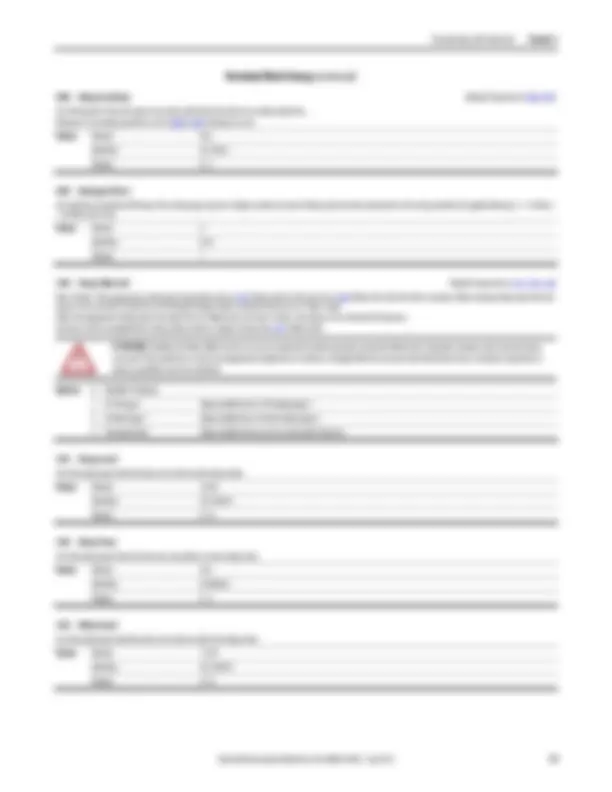
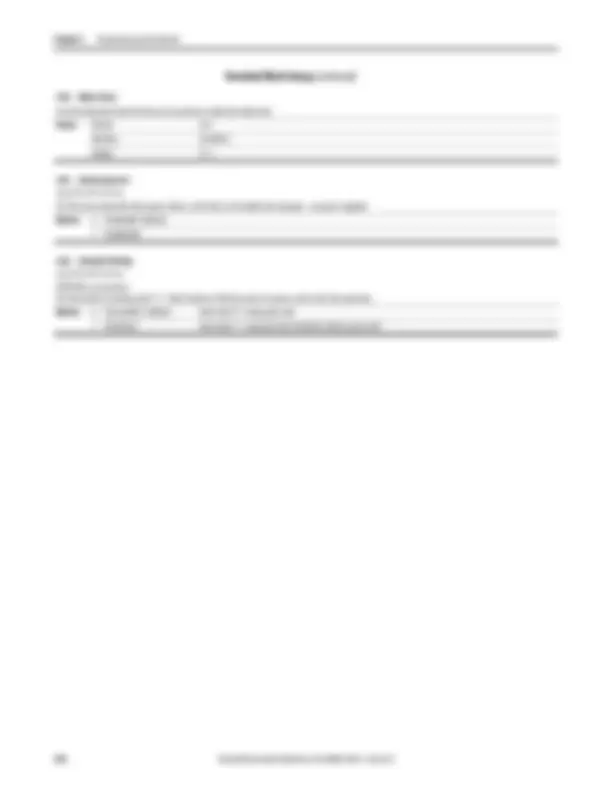
Study with the several resources on Docsity
Earn points by helping other students or get them with a premium plan
Prepare for your exams
Study with the several resources on Docsity
Earn points to download
Earn points by helping other students or get them with a premium plan
Community
Ask the community for help and clear up your study doubts
Discover the best universities in your country according to Docsity users
Free resources
Download our free guides on studying techniques, anxiety management strategies, and thesis advice from Docsity tutors
A section of the Rockwell Automation Publication 520-UM001I-EN-E, focusing on the installation and wiring of PowerFlex 520-Series Drives. It includes information on fuses and circuit breakers, digital input terminals, and various frame sizes. The document also provides notes and a list of parameters for programming and parameters.
Typology: Lecture notes
1 / 137
This page cannot be seen from the preview
Don't miss anything!
User Manual
Original Instructions
Important User Information
Allen-Bradley, Rockwell Automation, Rockwell Software, PowerFlex, Connected Components Workbench, Studio 5000, Studio 5000 Logix Designer, DriveTools SP, AppView, CustomView, QuickView, MainsFree Programming, PointStop, and TechConnect are trademarks of Rockwell Automation, Inc. Trademarks not belonging to Rockwell Automation are property of their respective companies.
Table of Contents
Velocity StepLogic Using Timed Steps............................ 210 Velocity StepLogic Using Basic Logic Functions................... 210 Timer Function................................................. 211 Counter Function............................................... 212 Velocity StepLogic Parameters................................... 213
Encoder and Pulse Train Usage................................... 215 Wiring Notes................................................... 216 Determine Encoder Pulse Per Revolution (PPR) Specification Based on Speed Resolution................................................ 217 Positioning Overview............................................ 218 Common Guidelines for All Applications......................... 218 Positioning Operation........................................... 220 Homing Routine................................................ 223 Encoder and Position Feedback.................................. 224 Use Over Communications...................................... 225 Setup Notes..................................................... 226
PID Reference and Feedback..................................... 229 Analog PID Reference Signals.................................... 230
EC Type Examination Certification.............................. 236 EMC Instructions............................................... 236 Using PowerFlex 525 Safe-Torque-Off............................ 236 Safety Concept.................................................. 237 Enabling PowerFlex 525 Safe-Torque-Off......................... 239 Wiring......................................................... 239 PowerFlex 525 Safe-Torque-Off Operation....................... 239 Verify Operation................................................ 240 Connection Examples........................................... 241 PowerFlex 525 Certification for Safe-Torque-Off.................. 245
Ground Connections for EtherNet/IP Networks.................. 248
Summary of Changes
New and Updated
Information
Topic Page Added footnote to indicate that circuit breaker selection is not available for certain drive ratings.
Added PowerFlex 523 series B to Control I/O Wiring Block Diagram. 38 Added PowerFlex 523 series B to Control I/O Terminal Designations. 40 Added PowerFlex 523 series B I/O wiring examples for analog input and analog output. 45 Added note to PowerFlex 525 I/O wiring example for pulse train input. 46 Added footnote to enum “4” for P053 [Reset to Defalts] under Smart Start-Up with Basic Program Group Parameters.
Added new sub topic for 32-bit parameters. 72 Added footnotes to parameters that are available in PowerFlex 523 FRN 3.xxx and later. Chapter 3 Updated descriptions for parameters that are available in PowerFlex 523 FRN 3.xxx and later. Added formula for calculating scaled process value to parameter b010 [Process Display]. 79 Added recommendation to perform rotate tune when using VVC mode to parameter P [Autotune].
Added footnote to indicate which settings are PowerFlex 525 only for parameter d394 [Dig Out Status].
Updated descriptions for parameters A465 [PID 1 Deadband] and A477 [PID 2 Deadband]. 123 Added corrective action to fault F114 (uC Failure). 162 Added analog output to PowerFlex 523 drives. 171 Added new topic “Determine Encoder Pulse Per Revolution (PPR) Specification Based on Speed Resolution” to Appendix E.
Updated information to verify operation of the safety inputs in Appendix G. 240 General maintenance updates. Throughout manual
Summary of Changes
Notes:
Preface Overview
Manual Conventions •^ In this manual we refer to PowerFlex 520-Series Adjustable Frequency AC
Title Publication PowerFlex 525 Embedded EtherNet/IP Adapter 520COM-UM PowerFlex 25-COMM-D DeviceNet Adapter 520COM-UM PowerFlex 25-COMM-E2P Dual-Port EtherNet/IP Adapter 520COM-UM PowerFlex 25-COMM-P PROFIBUS DPV1 Adapter 520COM-UM
P 031 [Motor NP Volts]
Name Number Group b P t C L d A N M f G = Basic Display = Basic Program = Terminal Blocks = Communications = Logic = Advanced Display = Advanced Program = Network = Modified = Fault and Diagnostic = AppView and CustomView
Words Meaning Can Possible, able to do something Cannot Not possible, not able to do something May Permitted, allowed Must Unavoidable, you must do this Shall Required and necessary Should Recommended Should Not Not Recommended
Overview Preface
Drive Frame Sizes Similar PowerFlex 520-series drive sizes are grouped into frame sizes to simplify
Overview Preface
Catalog Number Explanation
Code Type 25A PowerFlex 523 25B PowerFlex 525
25B – B 2P3 N 1 1 4 – – Drive Dash Voltage Rating Rating Enclosure Reserved Emission Class Reserved Dash Dash
Output Current @ 1 Phase, 100...120V Input Code Amps Frame ND HD HP kW HP kW 1P6 (1)^ 1.6 A 0.25 0.2 0.25 0. 2P5 2.5 A 0.5 0.4 0.5 0. 4P8 4.8 B 1.0 0.75 1.0 0. 6P0 6.0 B 1.5 1.1 1.5 1. Output Current @ 1 Phase, 200...240V Input Code Amps Frame ND HD HP kW HP kW 1P6 (1)^ 1.6 A 0.25 0.2 0.25 0. 2P5 2.5 A 0.5 0.4 0.5 0. 4P8 4.8 A 1.0 0.75 1.0 0. 8P0 8.0 B 2.0 1.5 2.0 1. 011 11.0 B 3.0 2.2 3.0 2. Output Current @ 3Phase, 200...240V Input Code Amps Frame ND HD HP kW HP kW 1P6 (1)^ 1.6 A 0.25 0.2 0.25 0. 2P5 2.5 A 0.5 0.4 0.5 0. 5P0 5.0 A 1.0 0.75 1.0 0. 8P0 8.0 A 2.0 1.5 2.0 1. 011 11.0 A 3.0 2.2 3.0 2. 017 17.5 B 5.0 4.0 5.0 4. 024 24.0 C 7.5 5.5 7.5 5. 032 32.2 D 10.0 7.5 10.0 7. 048 (2)^ 48.3 E 15.0 11.0 10.0 7. 062 (2)^ 62.1 E 20.0 15.0 15.0 11.
Output Current @ 3 Phase, 380...480V Input Code Amps Frame ND HD HP kW HP kW 1P4 1.4 A 0.5 0.4 0.5 0. 2P3 2.3 A 1.0 0.75 1.0 0. 4P0 4.0 A 2.0 1.5 2.0 1. 6P0 6.0 A 3.0 2.2 3.0 2. 010 10.5 B 5.0 4.0 5.0 4. 013 13.0 C 7.5 5.5 7.5 5. 017 17.0 C 10.0 7.5 10.0 7. 024 24.0 D 15.0 11.0 15.0 11. 030 (2)^ 30.0 D 20.0 15.0 15.0 11. 037 (2)^ 37.0 E 25.0 18.5 20.0 15. 043 (2)^ 43.0 E 30.0 22.0 25.0 18. Output Current @ 3 Phase, 525...600V Input Code Amps Frame ND HD HP kW HP kW 0P9 0.9 A 0.5 0.4 0.5 0. 1P7 1.7 A 1.0 0.75 1.0 0. 3P0 3.0 A 2.0 1.5 2.0 1. 4P2 4.2 A 3.0 2.2 3.0 2. 6P6 6.6 B 5.0 4.0 5.0 4. 9P9 9.9 C 7.5 5.5 7.5 5. 012 12.0 C 10.0 7.5 10.0 7. 019 19.0 D 15.0 11.0 15.0 11. 022 (2)^ 22.0 D 20.0 15.0 15.0 11. 027 (2)^ 27.0 E 25.0 18.5 20.0 15. 032 (2)^ 32.0 E 30.0 22.0 25.0 18.
Code Voltage Phase V 120V AC 1 A 240V AC 1 B 240V AC 3 D 480V AC 3 E 600V AC 3
Code Enclosure N IP20 NEMA / Open
Code Interface Module 1 Standard
Code EMC Filter 0 No Filter 1 Filter
Code Braking 4 Standard
(1) This rating is only available for PowerFlex 523 drives. (2) Normal and Heavy Duty ratings are available for this drive.
Preface Overview
Notes:
Chapter 1 Installation/Wiring
(1) For Frame E with Control Module Fan Kit only, clearance of 95 mm (3.7 in.) is required. (2) For Frame E with Control Module Fan Kit only, clearance of 12 mm (0.5 in.) is required.
25 mm (1.0 in.)
25 mm (1.0 in.) (2)
(2)
25 mm (1.0 in.)
50 mm (2.0 in.)
50 mm (2.0 in.)(1)^
50 mm (2.0 in.)(1)
50 mm (2.0 in.)(1)
50 mm (2.0 in.)
50 mm (2.0 in.)
50 mm (2.0 in.)
Esc Sel Esc Sel Esc Sel Esc Sel
50 mm (2.0 in.)
50 mm (2.0 in.)
50 mm (2.0 in.)
50 mm (2.0 in.)
Esc (^) Sel
Esc (^) Sel
50 mm (2.0 in.)
50 mm (2.0 in.) 50 mm (2.0 in.) (^) (2.0 in.)50 mm
50 mm (2.0 in.) (1)
Esc (^) Sel
Esc (^) Sel
Esc Sel Esc Sel Esc Sel Esc Sel
Vertical, Zero Stacking No clearance between drives.
Horizontal, Zero Stacking with Control Module Fan Kit No clearance between drives.
Vertical Vertical, Zero Stacking with Control Module Fan Kit No clearance between drives.
Vertical with Control Module Fan Kit
Horizontal with Control Module Fan Kit
Installation/Wiring Chapter 1
Mounting Enclosure Rating(1)^ Ambient Temperature Minimum Maximum (No Derate) Maximum (Derate) (2)^ Maximum with Control Module Fan Kit (Derate) (3)(5) Vertical IP 20/Open Type
IP 30/NEMA 1/UL Type 1 45 °C (113 °F) 55 °C (131 °F) – Vertical, Zero Stacking IP 20/Open Type 45 °C (113 °F) 55 °C (131 °F) 65 °C (149 °F) IP 30/NEMA 1/UL Type 1 40 °C (104 °F) 50 °C (122 °F) – Horizontal with Control Module Fan Kit(4)(5)^
IP 20/Open Type 50 °C (122 °F) – 70 °C (158 °F)
Horizontal, Zero Stacking with Control Module Fan Kit(4)(5)^
IP 20/Open Type (^45) °C (113 °F) – 65 °C (149 °F)
(1) IP 30/NEMA 1/UL Type 1 rating requires installation of the PowerFlex 520-Series IP 30/NEMA 1/UL Type 1 option kit, catalog number 25-JBAx. (2) For catalogs 25x-D1P4N104 and 25x-E0P9N104, the temperature listed under the Maximum (Derate) column is reduced by 5 °C (9 °F) for all mounting methods. (3) For catalogs 25x-D1P4N104 and 25x-E0P9N104, the temperature listed under the Maximum with Control Module Fan Kit (Derate) column is reduced by 10 °C (18 °F) for vertical and vertical with zero stacking mounting methods only. (4) Catalogs 25x-D1P4N104 and 25x-E0P9N104 cannot be mounted using either of the horizontal mounting methods. (5) Requires installation of the PowerFlex 520-Series Control Module Fan Kit, catalog number 25-FANx-70C.
Ambient Temperature (°C)
40
100 90
110
120
80 70 60 50 Percentage of Rated Current (%) 30 35 404550 5560 65 70 75 80
(^) IP 30/NEMA 1 with Control Module Fan Kit
IP 20/Open Type
Ambient Temperature (°C)
40
100 90
110
120
80 70 60 50 Percentage of Rated Current (%) 30 35 4045505560 65 70 75 80
(^) IP 30/NEMA 1 with Control Module Fan Kit
IP 20/Open Type
Single Drive Zero Stacking
Ambient Temperature (°C)
40
100 90
120 110
80 70 60 50 Percentage of Rated Current (%) 30 35 40 4550 5560 6570 75 80
with Control Module Fan Kit
IP 20/Open Type
Ambient Temperature (°C)
40
100 90
120 110
80 70 60 50 Percentage of Rated Current (%) 30 35 40 4550 5560 6570 75 80
(^) with Control Module Fan Kit
IP 20/Open Type
Single Drive Zero Stacking
Installation/Wiring Chapter 1
AC Supply Source
Considerations
Disconnecting MOVs
Power Module
R/L S/L T/L 1 2 3 4
Three-Phase AC Input
Jumper
Chapter 1 Installation/Wiring
General Grounding
Requirements
Input Power Condition Corrective Action Low Line Impedance (less than 1% line reactance) • Install Line Reactor(2)
- or Isolation Transformer
(2) See Appendix B for accessory ordering information.
Greater than 120 kVA supply transformer Line has power factor correction capacitors • Install Line Reactor(2) Line has frequent power interruptions^ •^ or Isolation Transformer Line has intermittent noise spikes in excess of 6000V (lightning) Phase to ground voltage exceeds 125% of normal line to line voltage • Remove MOV jumper to ground.
- or Install Isolation Transformer with Ungrounded distribution system grounded secondary if necessary. B-phase grounded distribution system 240V open delta configuration (stinger leg)(1) (1) For drives applied on an open delta with a middle phase grounded neutral system, the phase opposite the phase that is tapped in the middle to the neutral or earth is referred to as the “stinger leg,” “high leg,” “red leg,” etc. This leg should be identified throughout the system with red or orange tape on the wire at each connection point. The stinger leg should be connected to the center Phase B on the reactor. See Bulletin 1321-3R Series Line Reactors on page 183 for specific line reactor part numbers. - Install Line Reactor(2)
SHLD
U/T V/T W/T
R/L S/L T/L
Esc Sel