
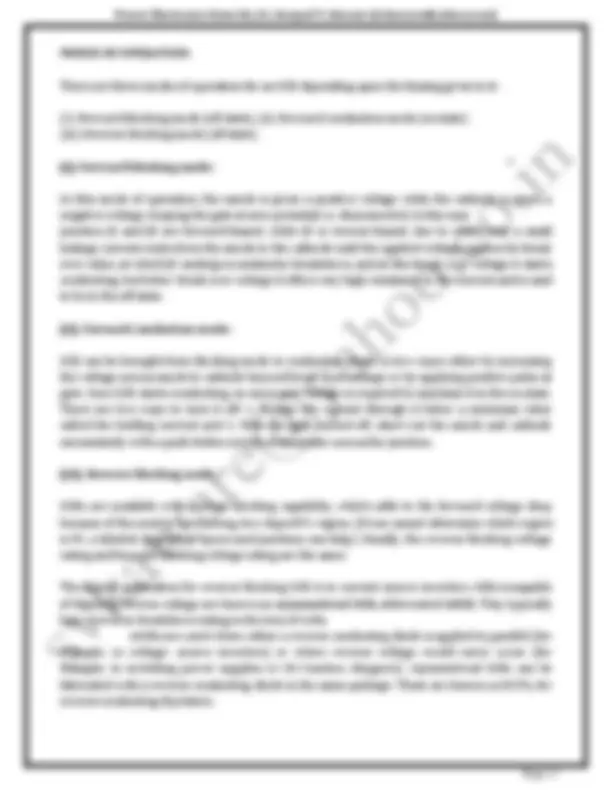
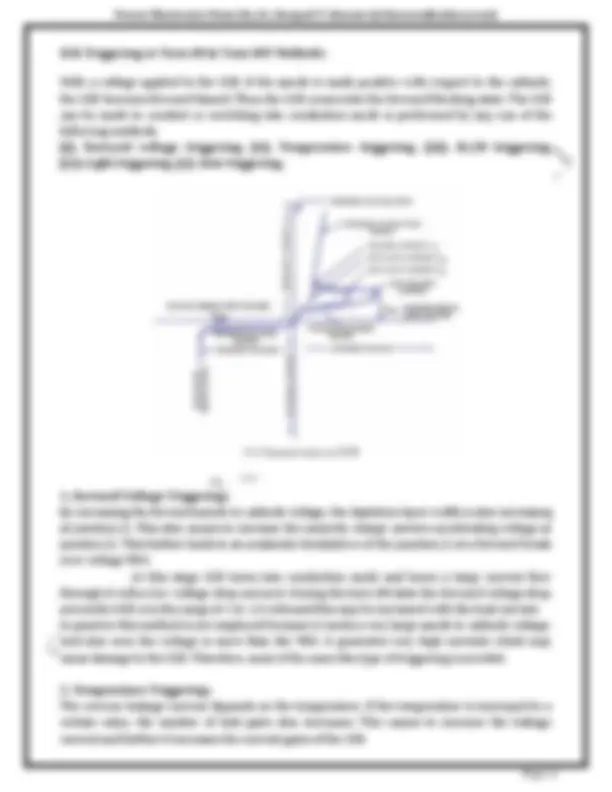
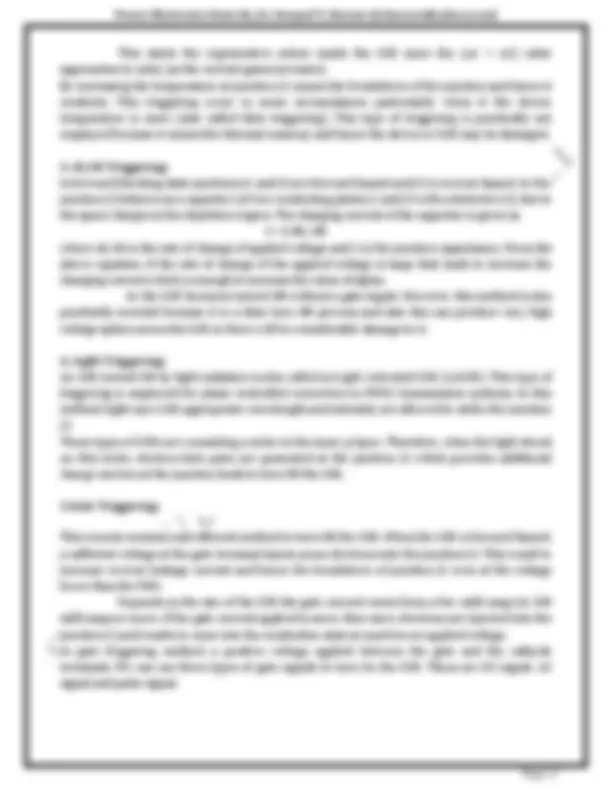
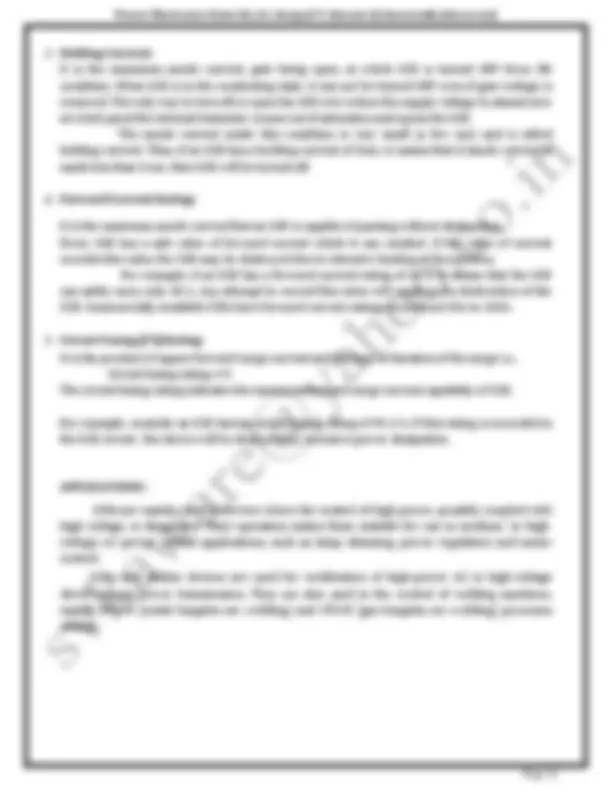
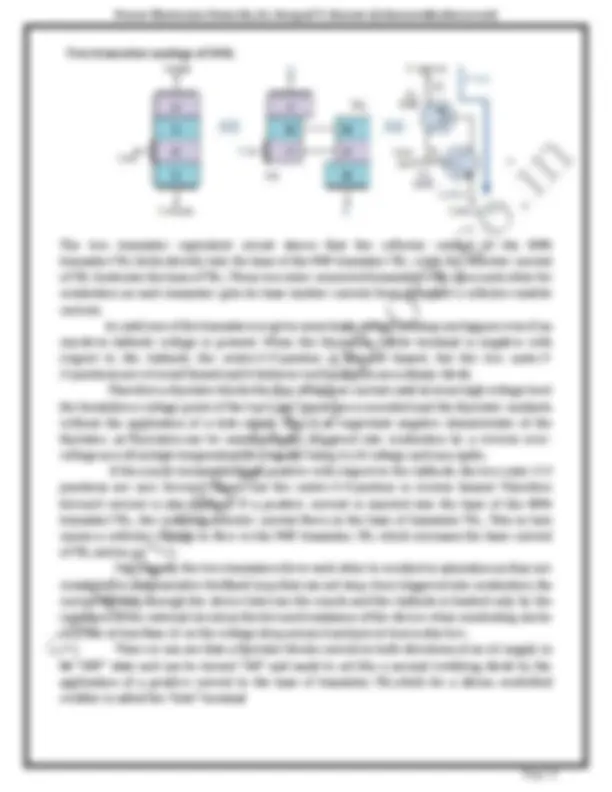
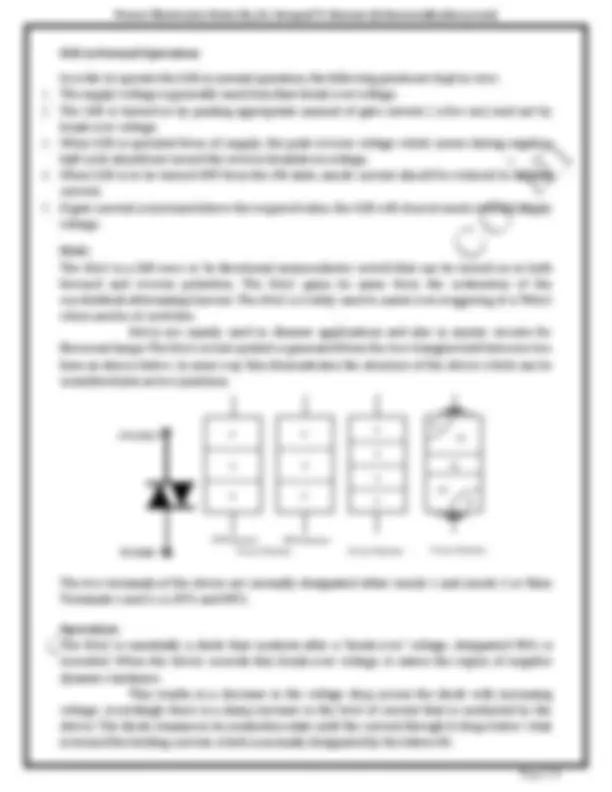
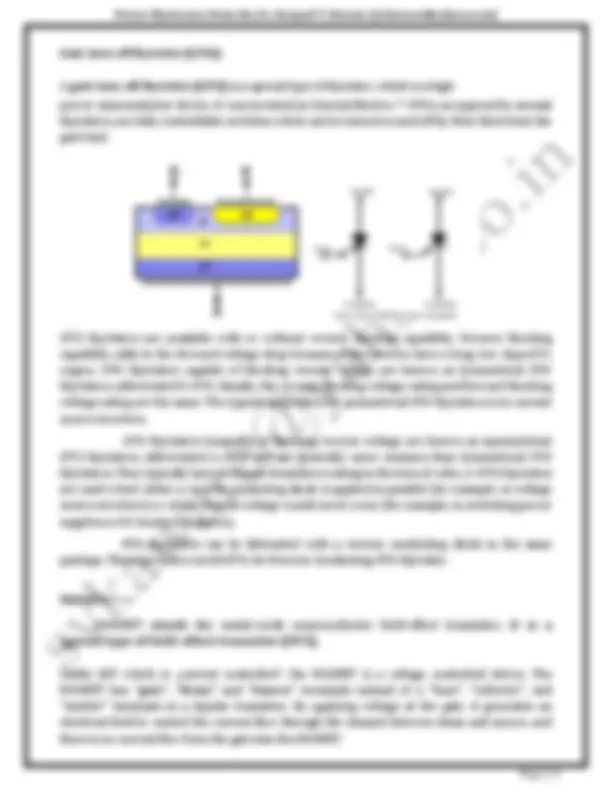
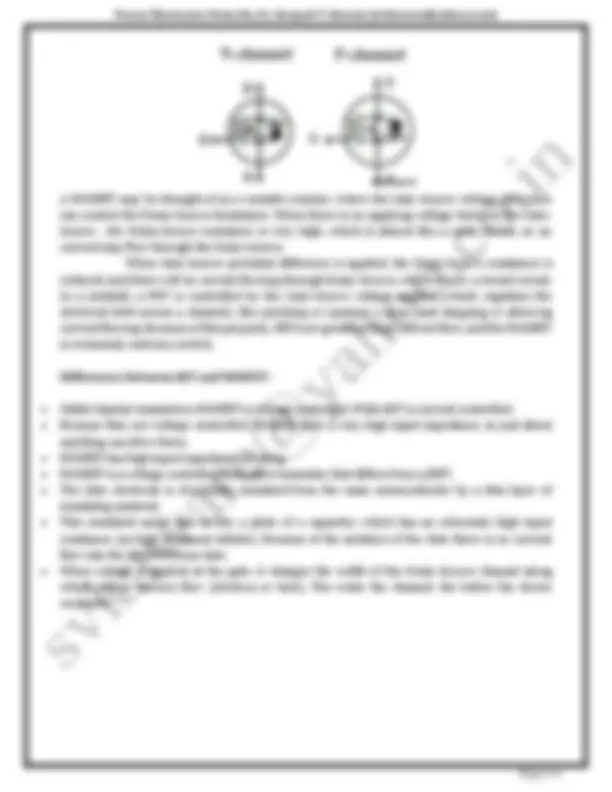
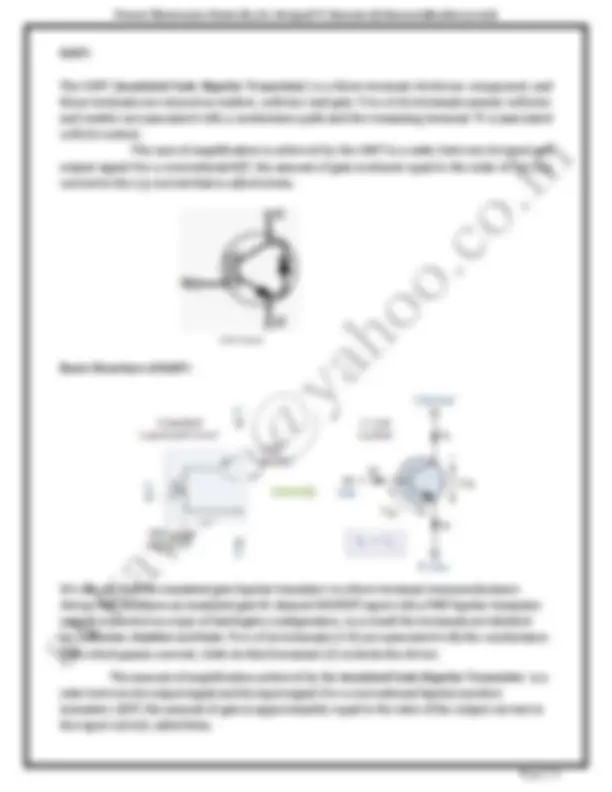
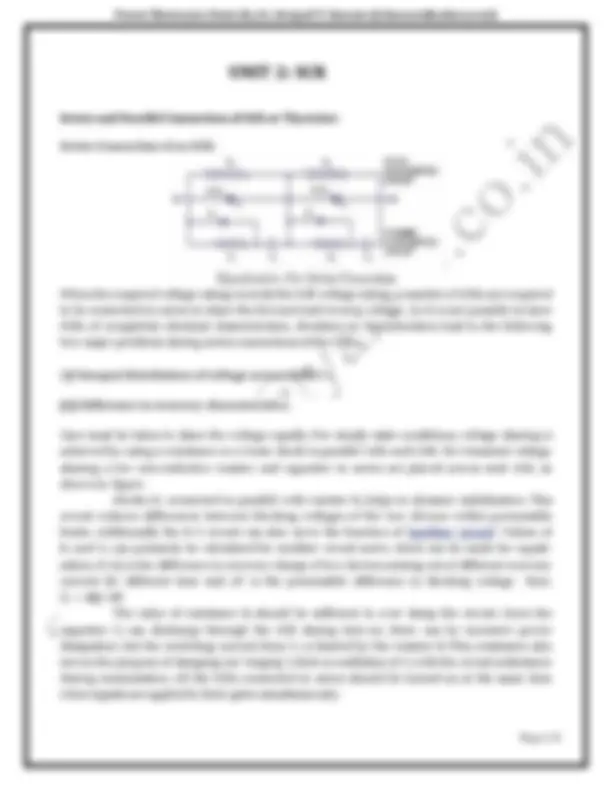
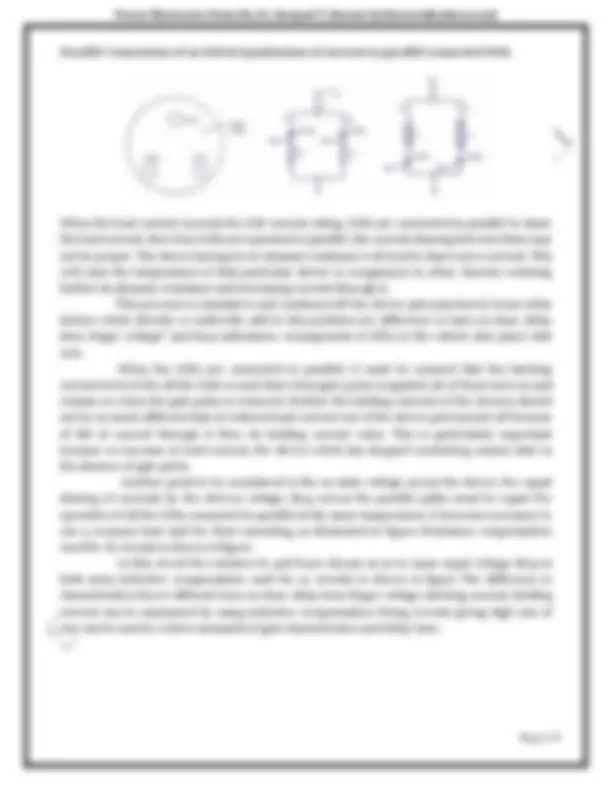
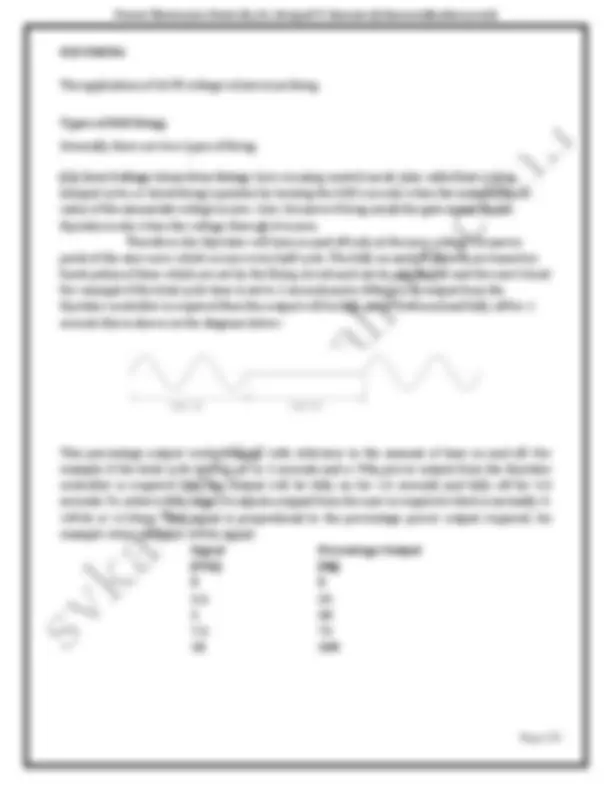
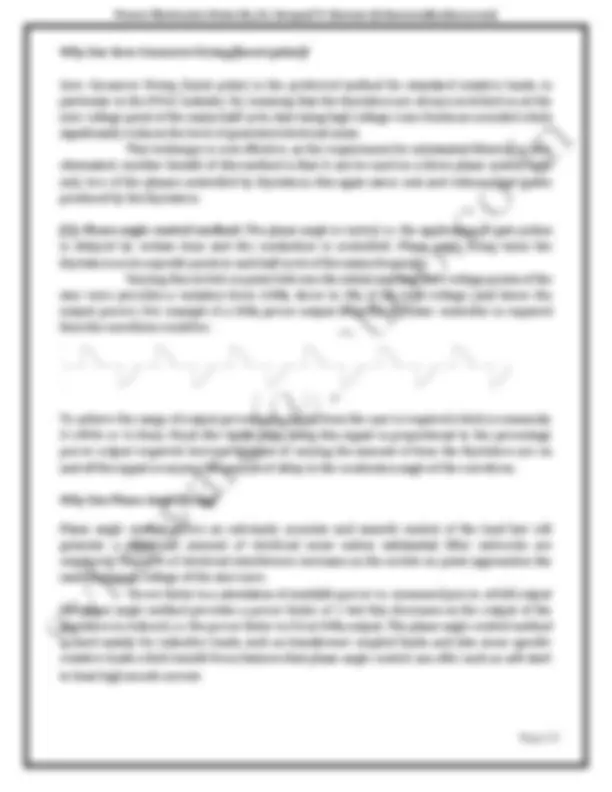
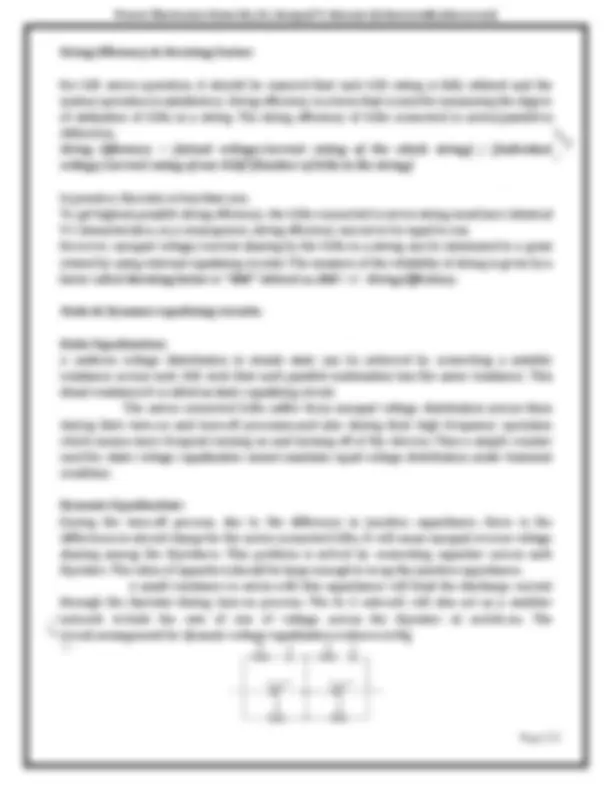
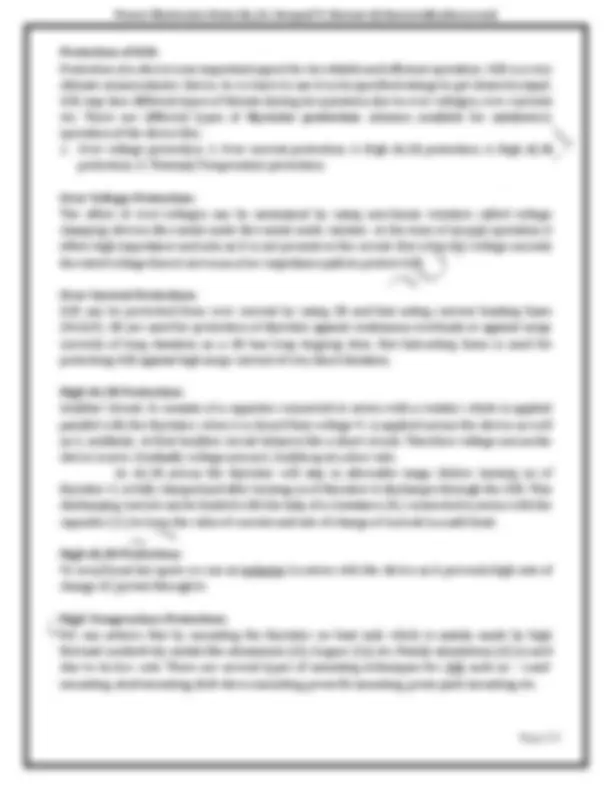
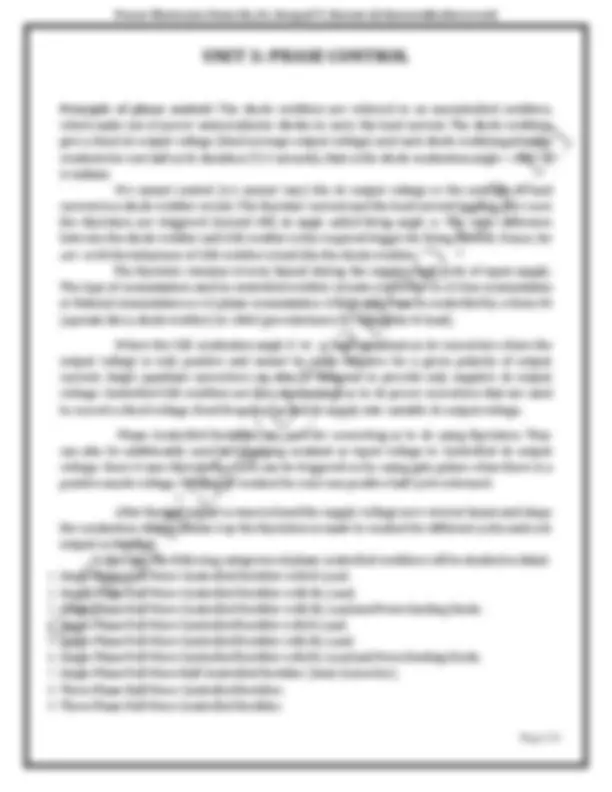
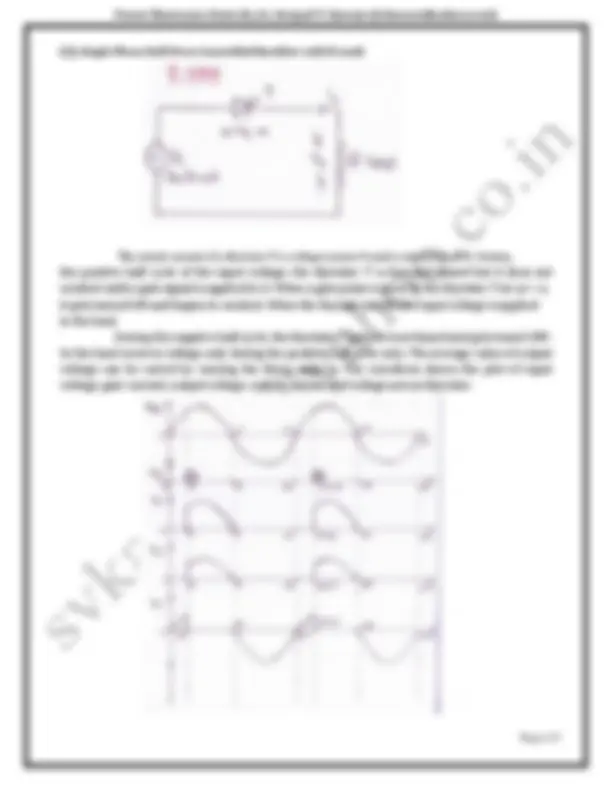
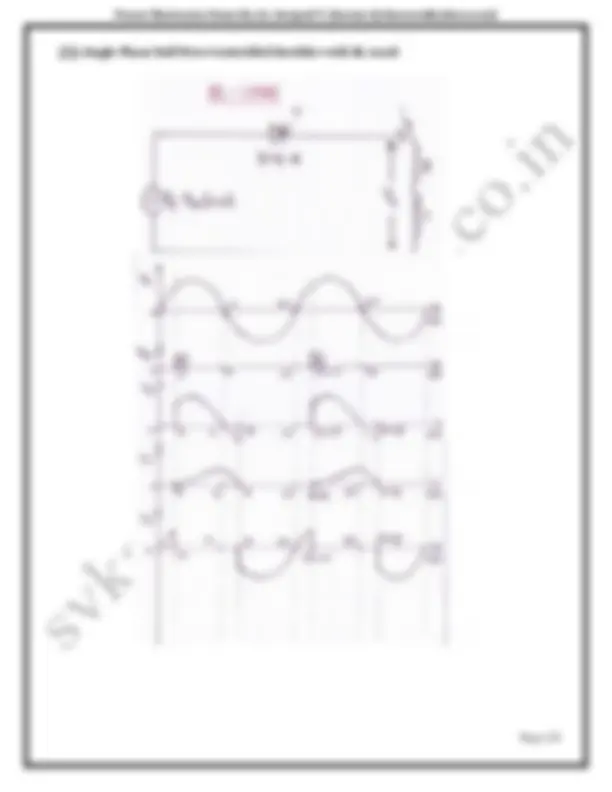
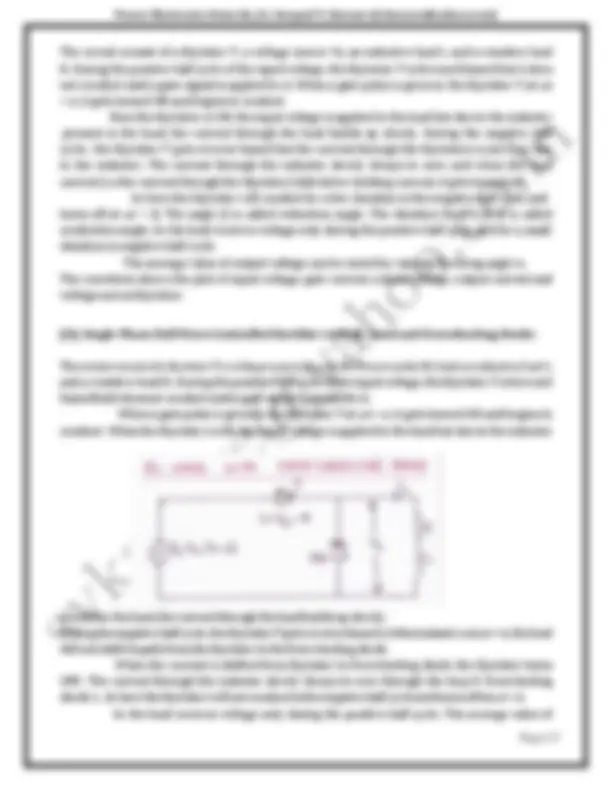

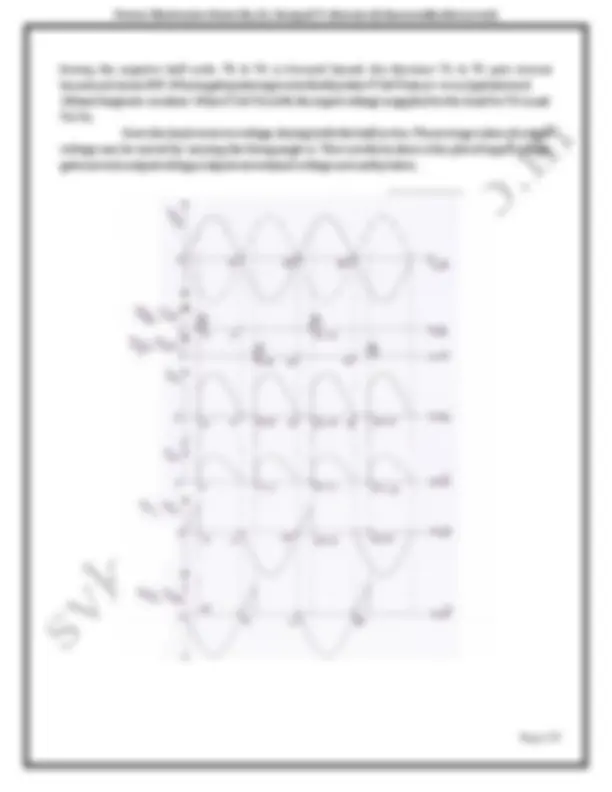
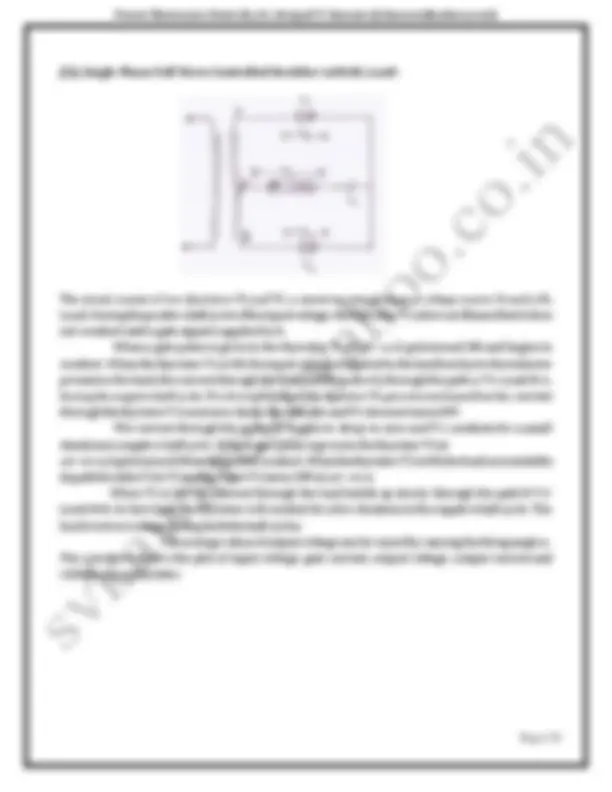
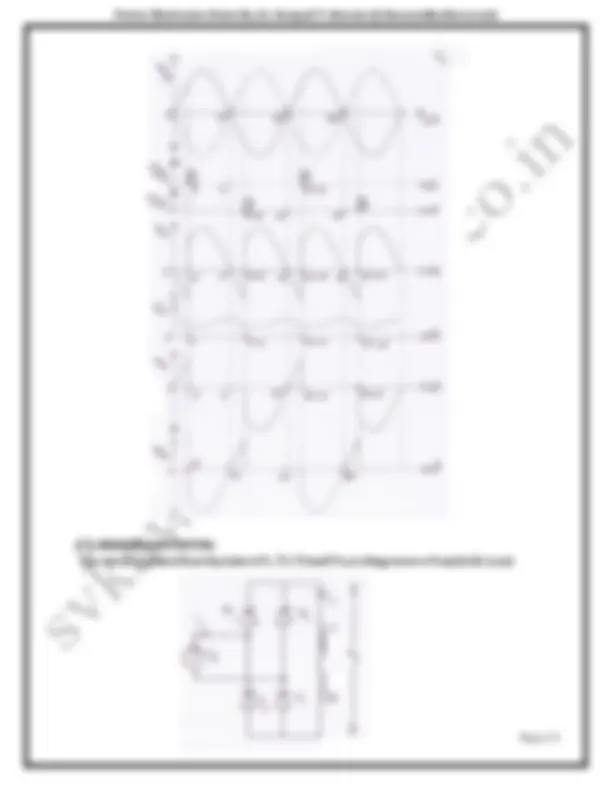
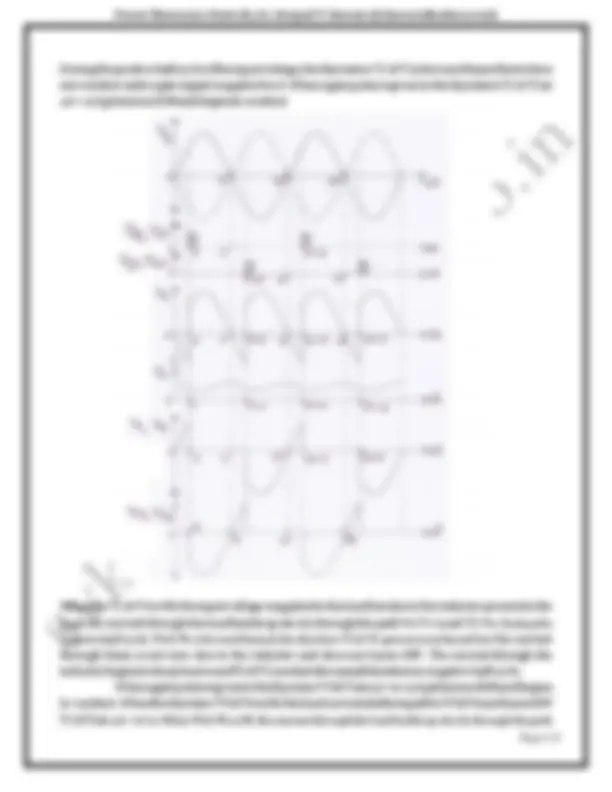
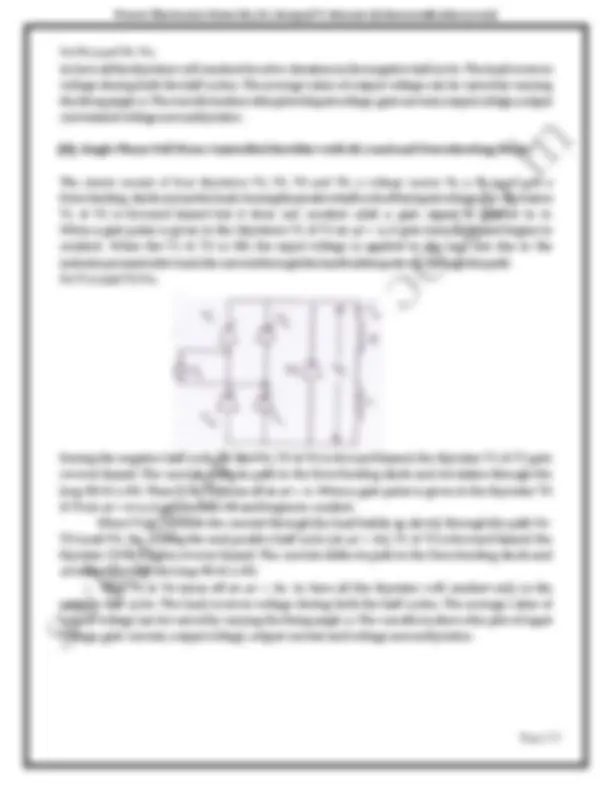
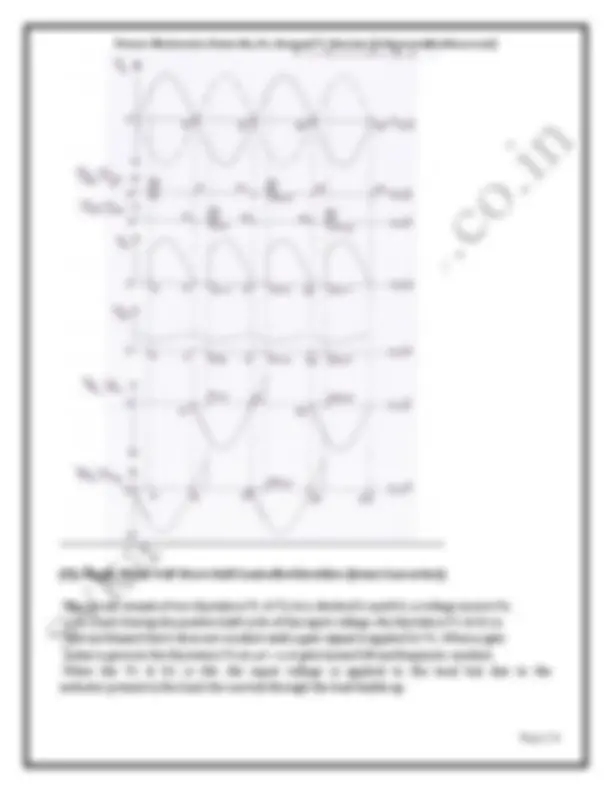
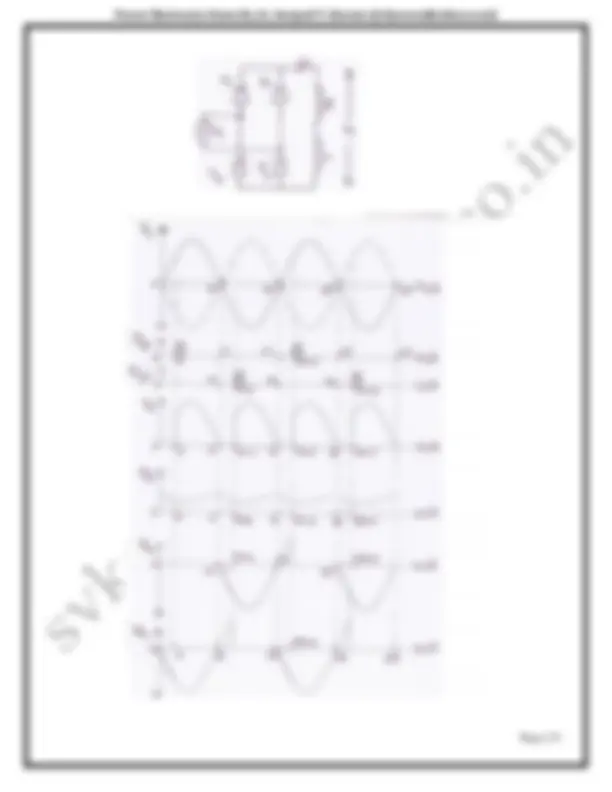
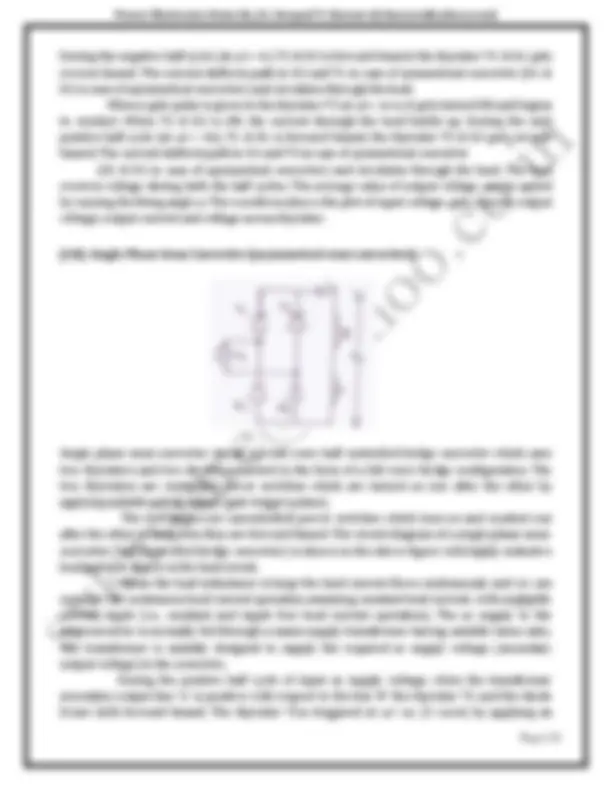
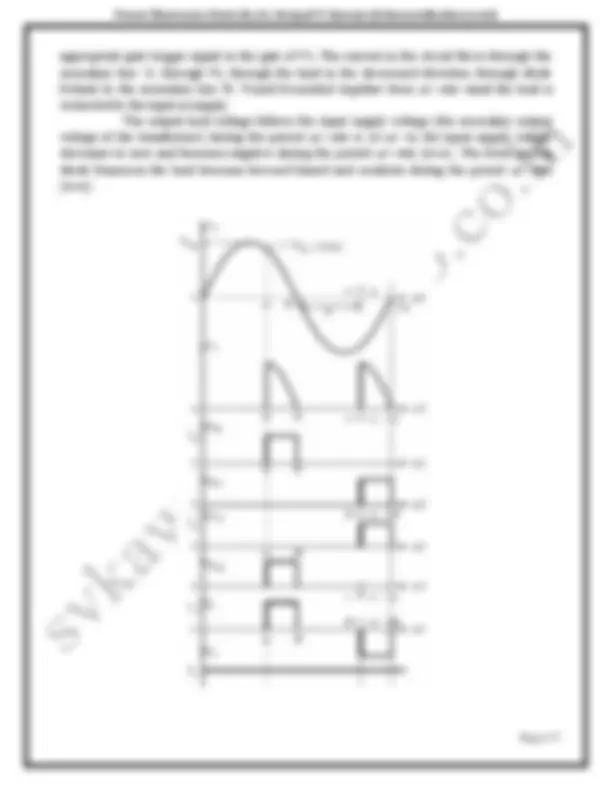
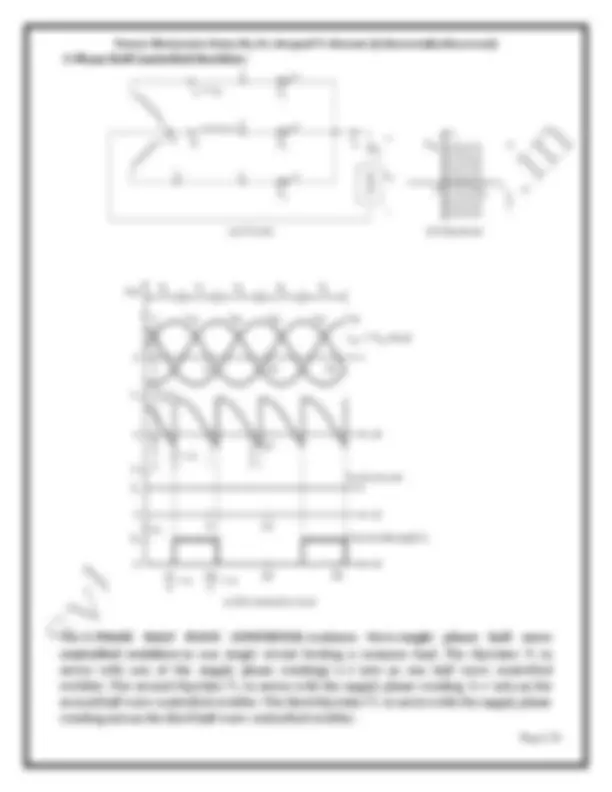
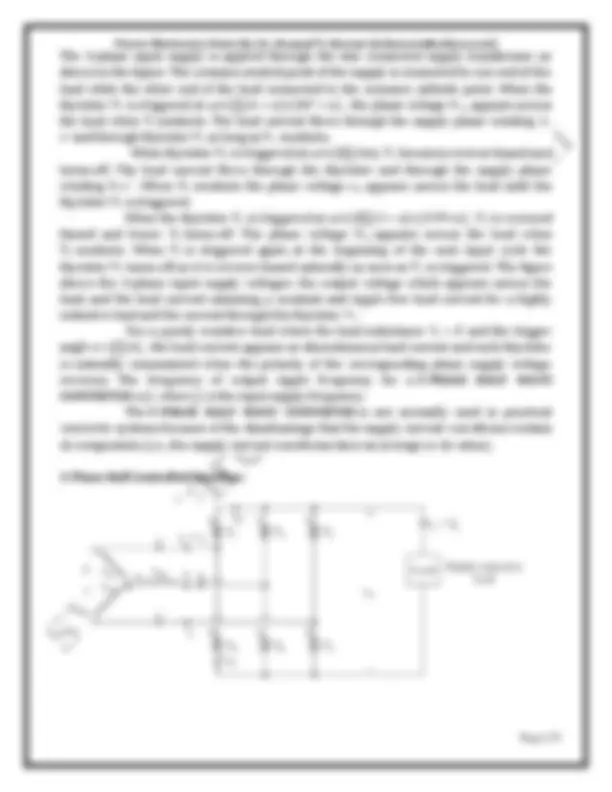
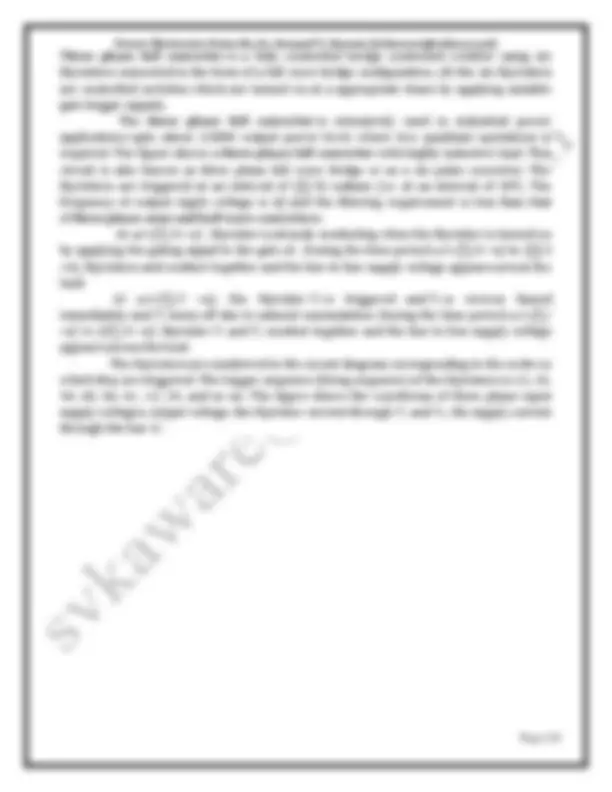
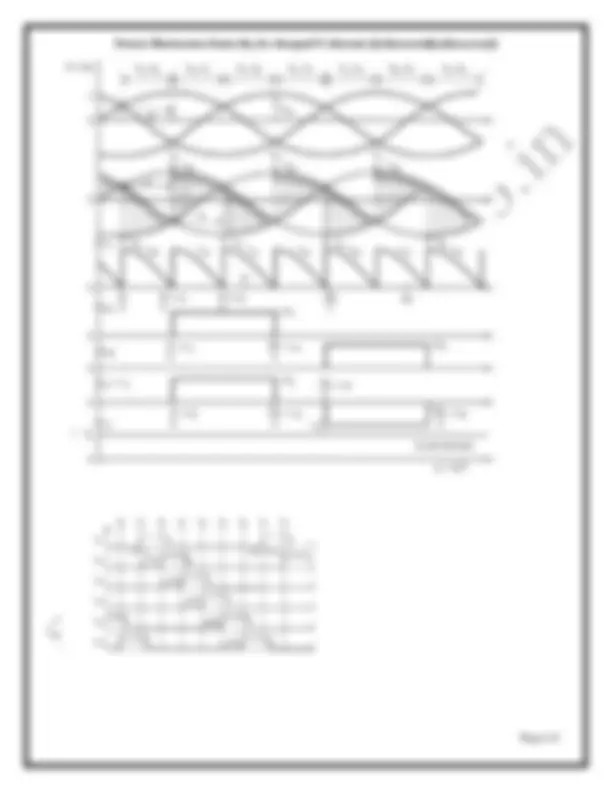
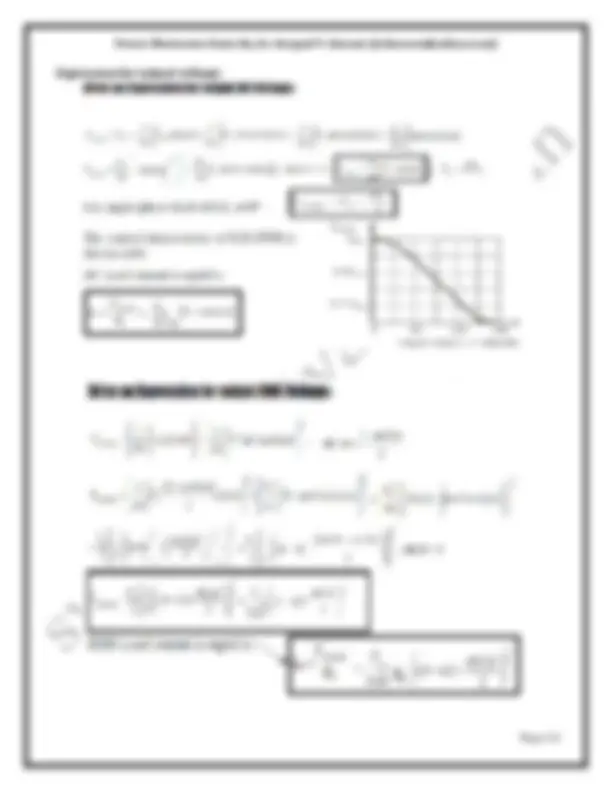
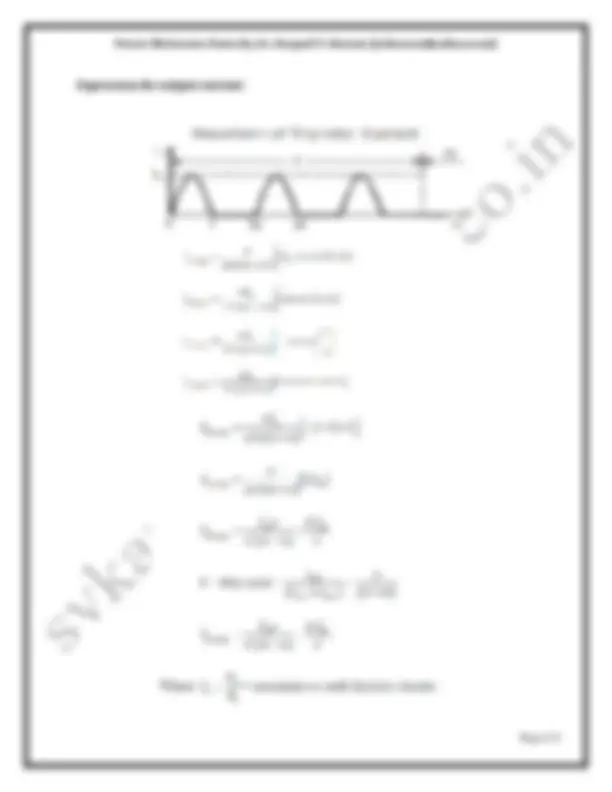
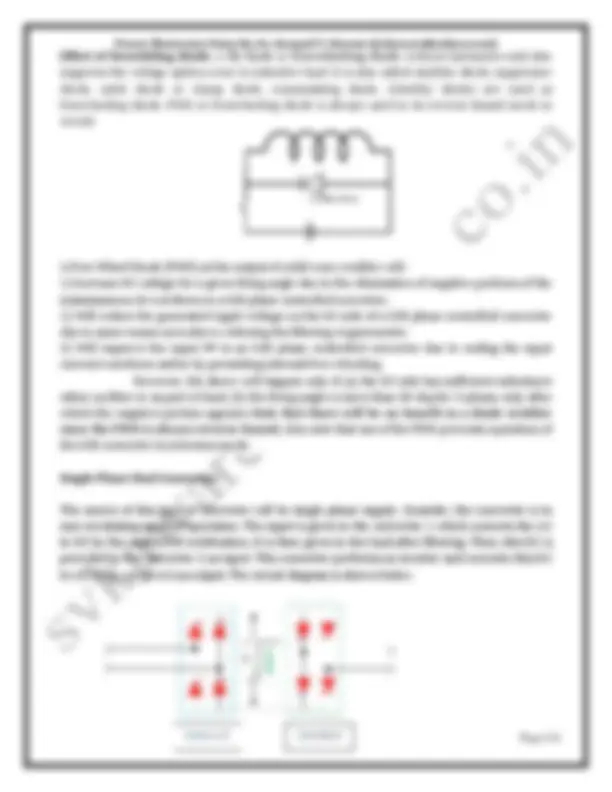
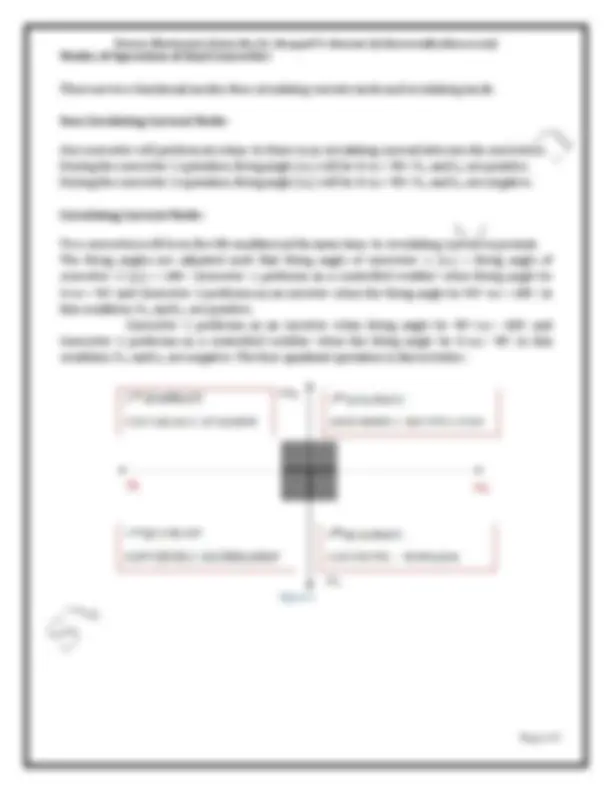
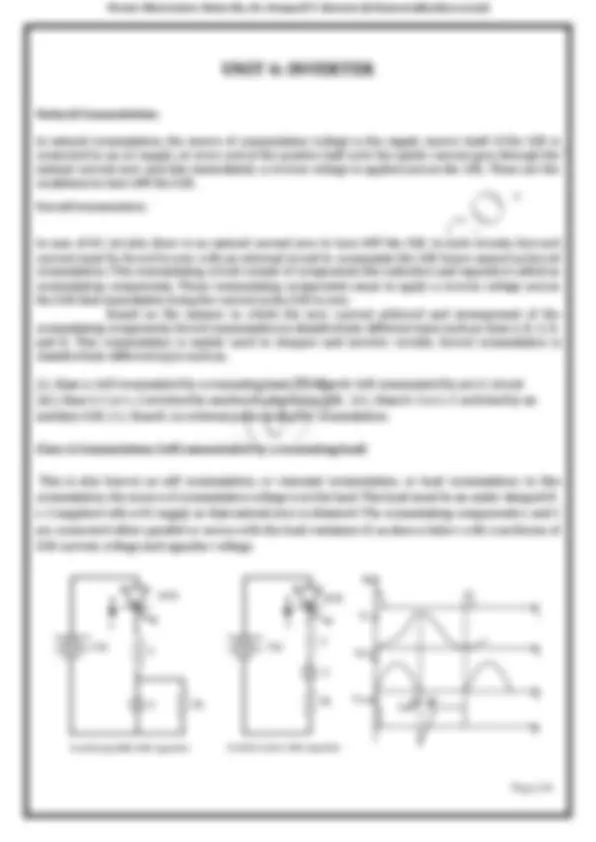
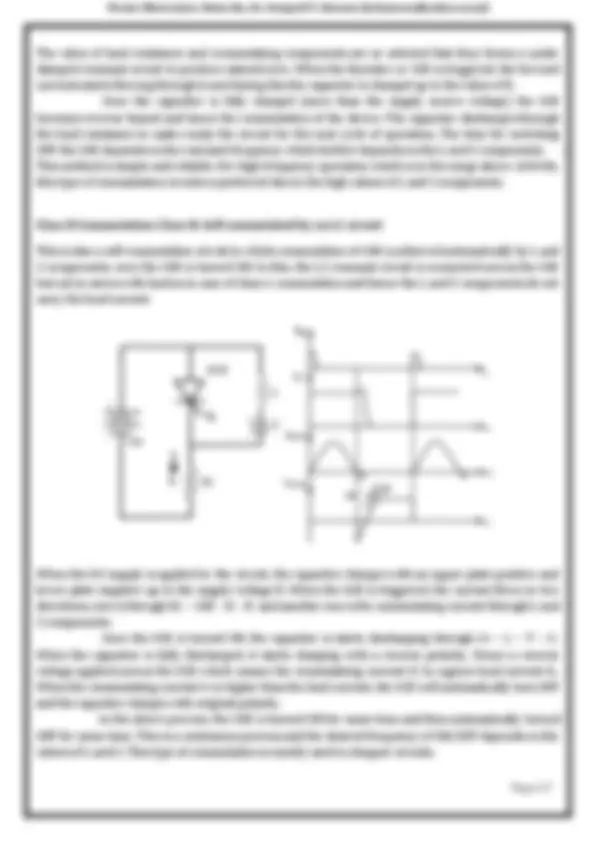
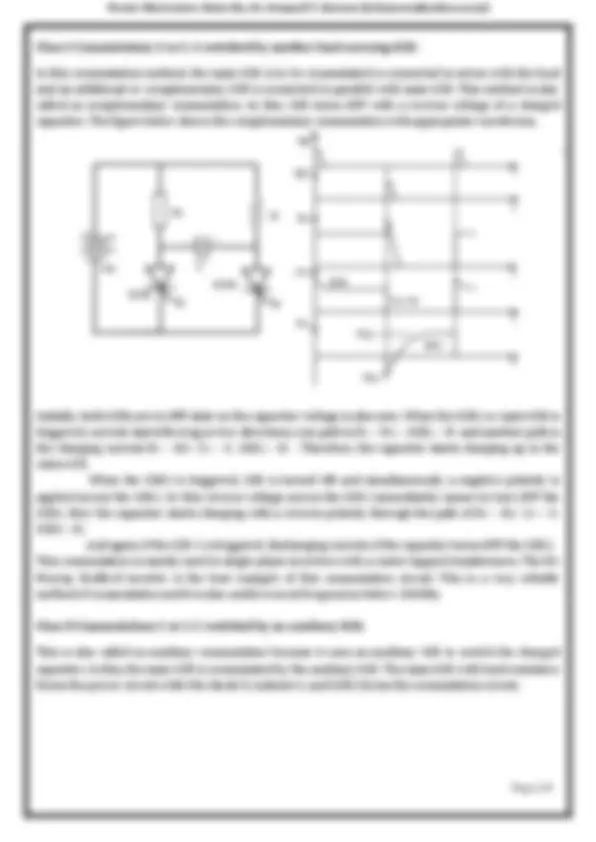
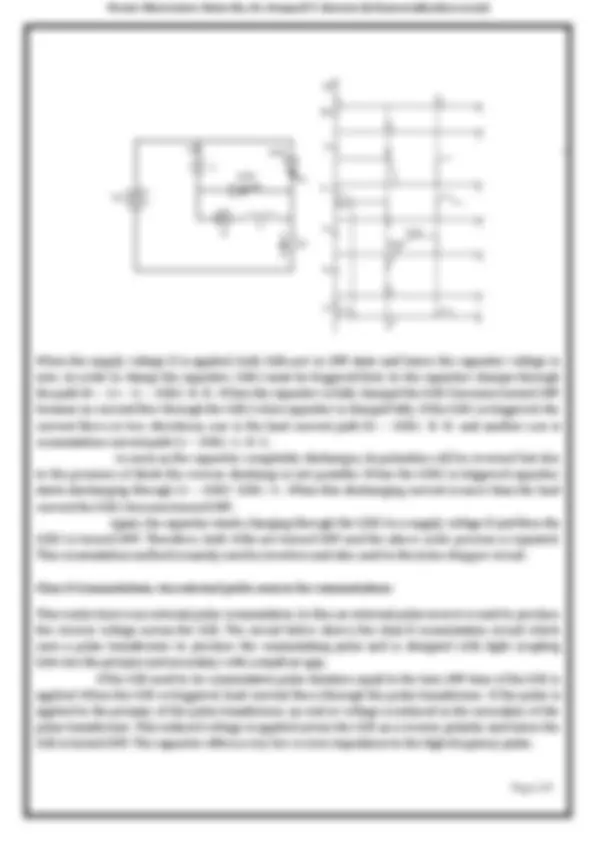
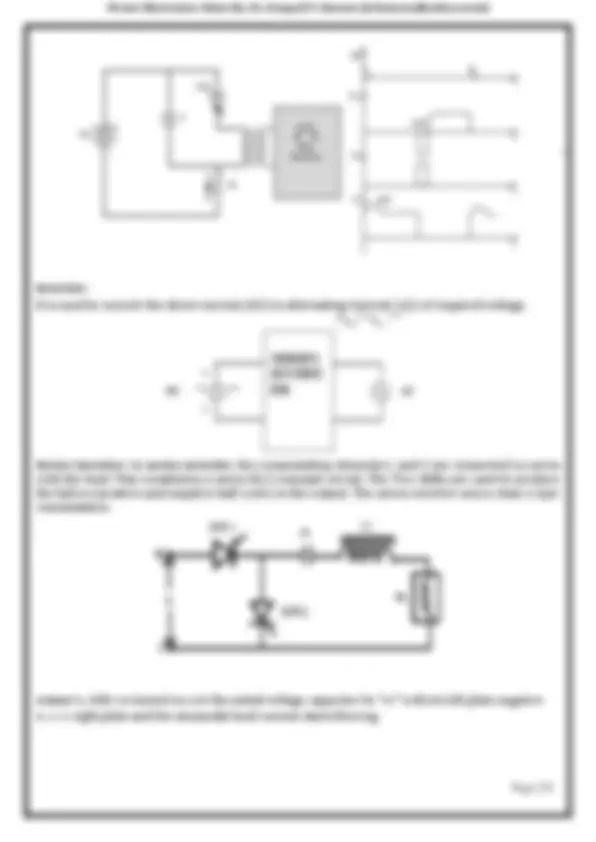
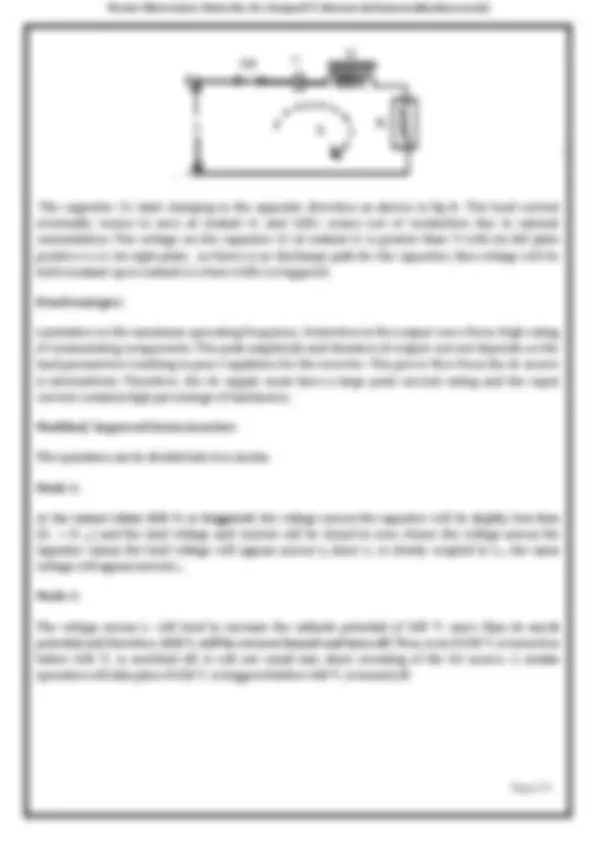
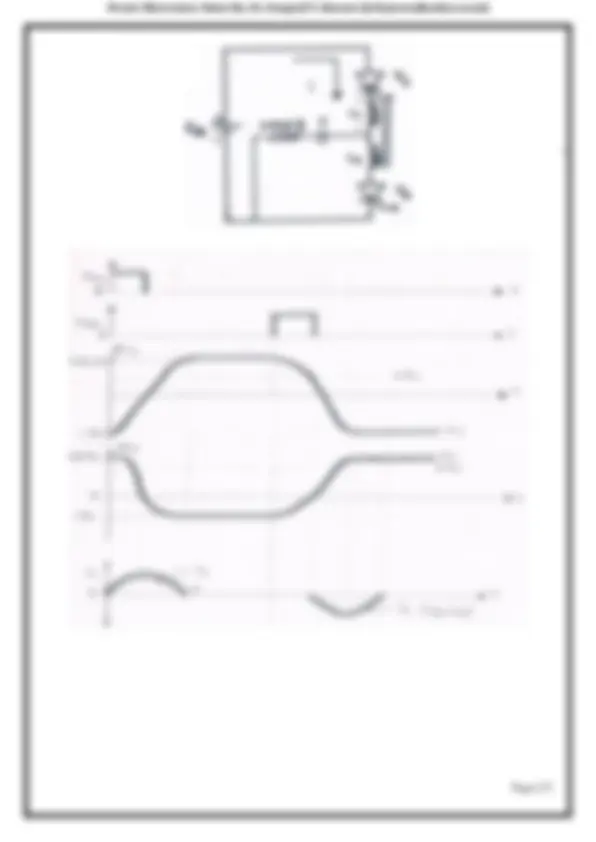
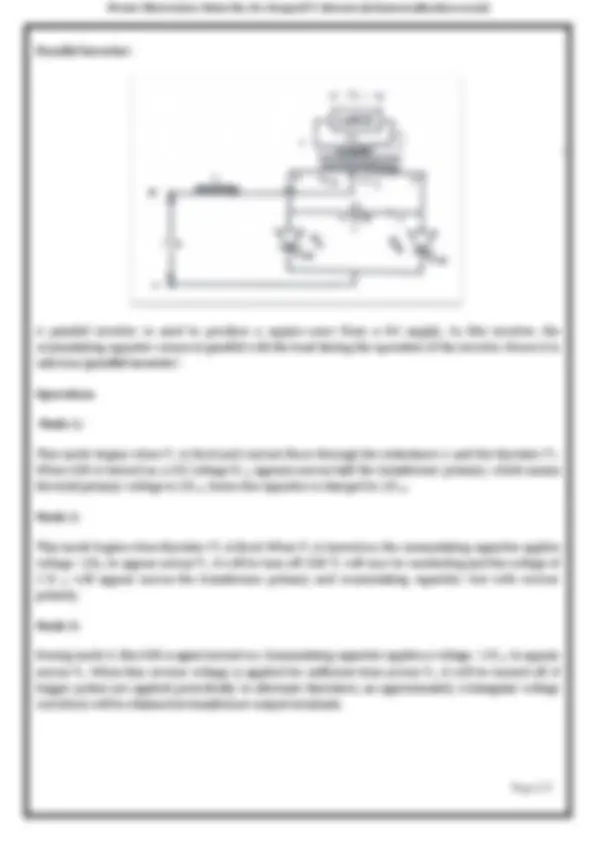
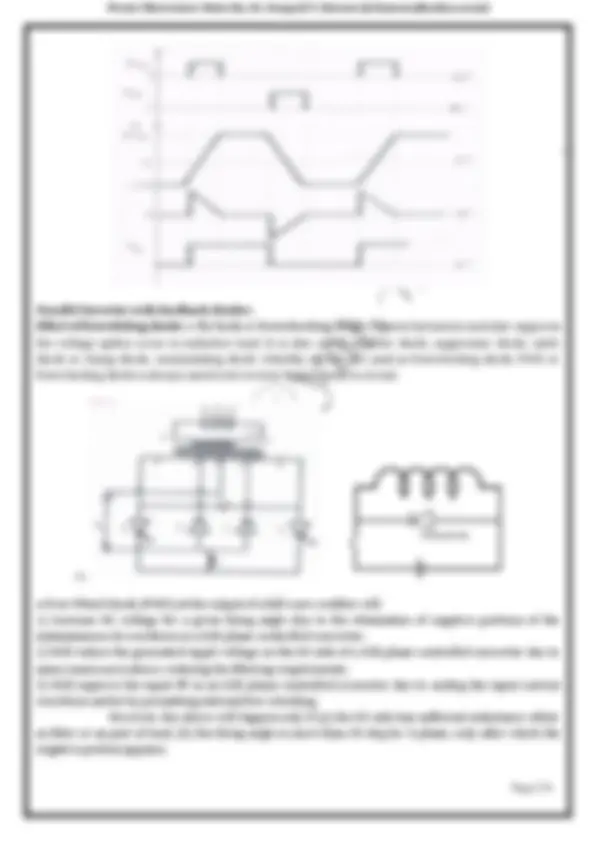
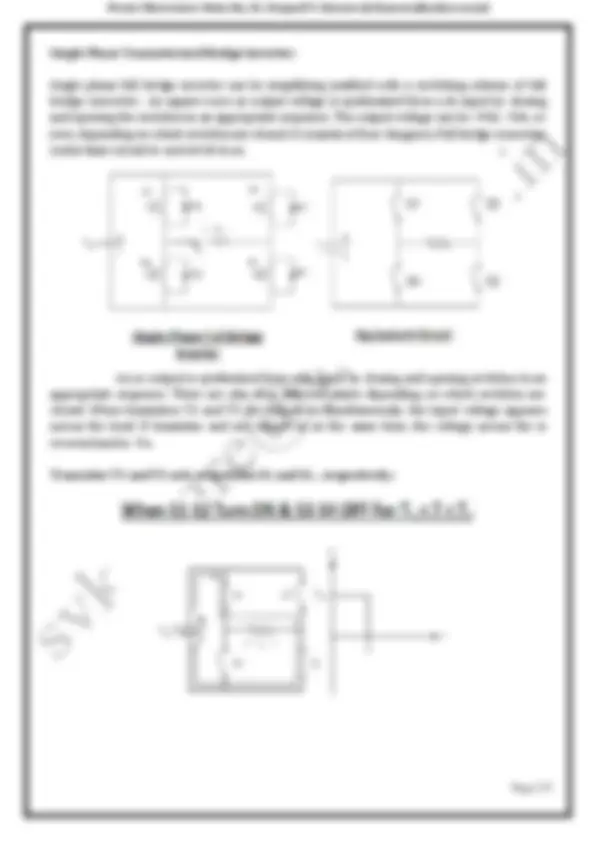

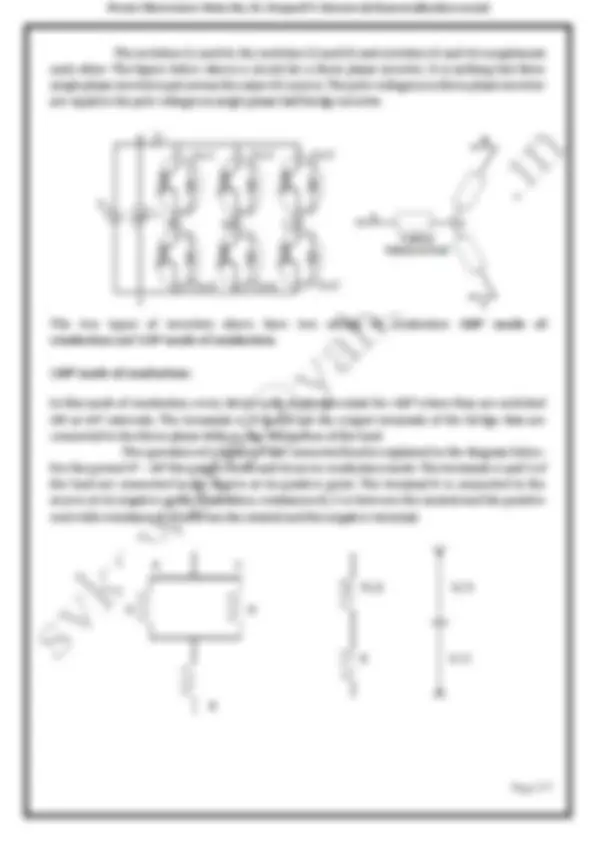
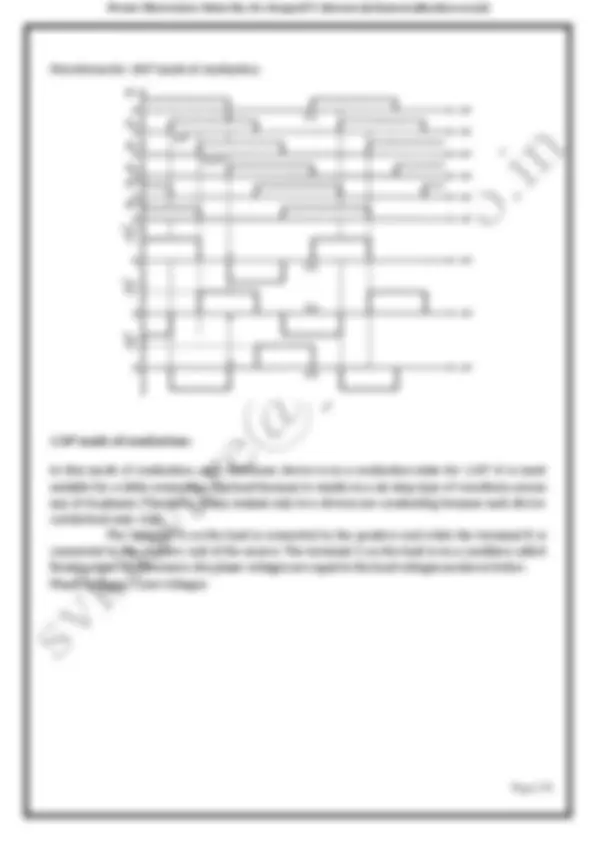
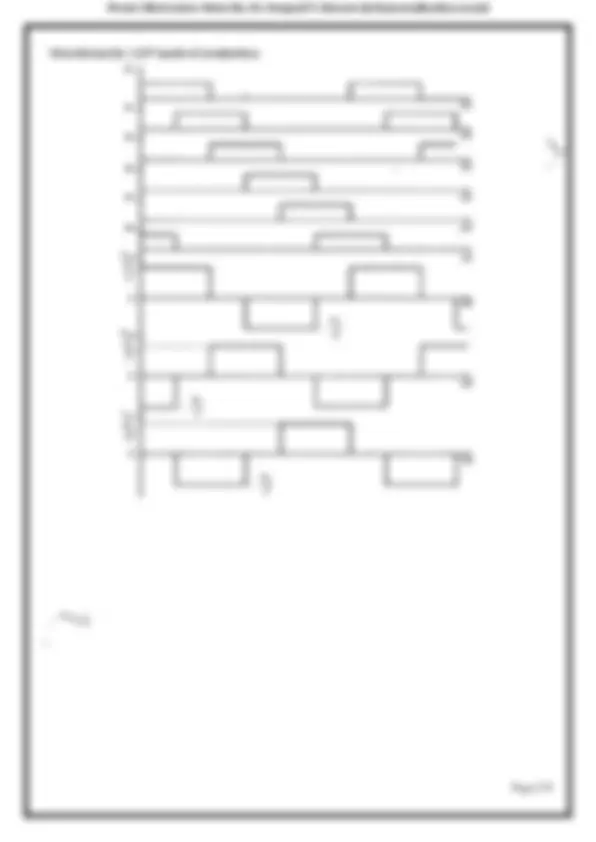
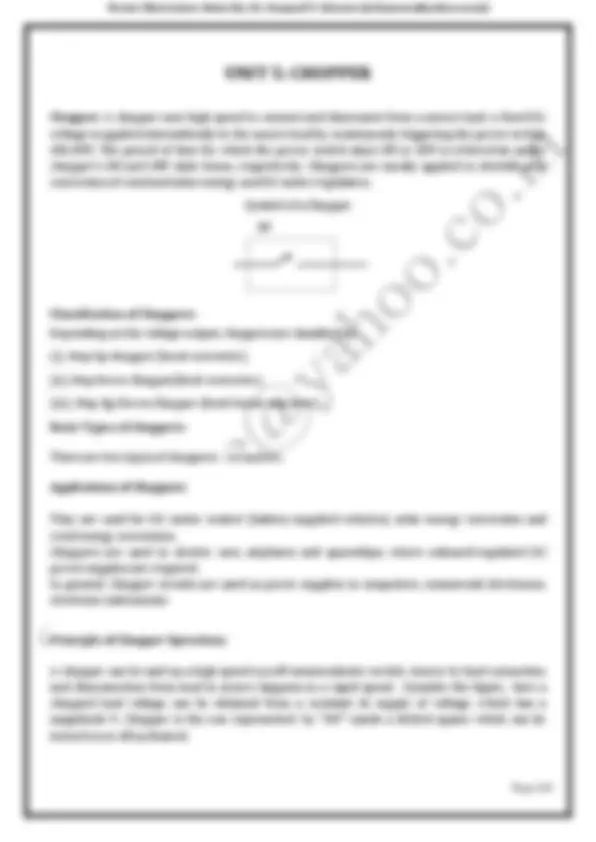
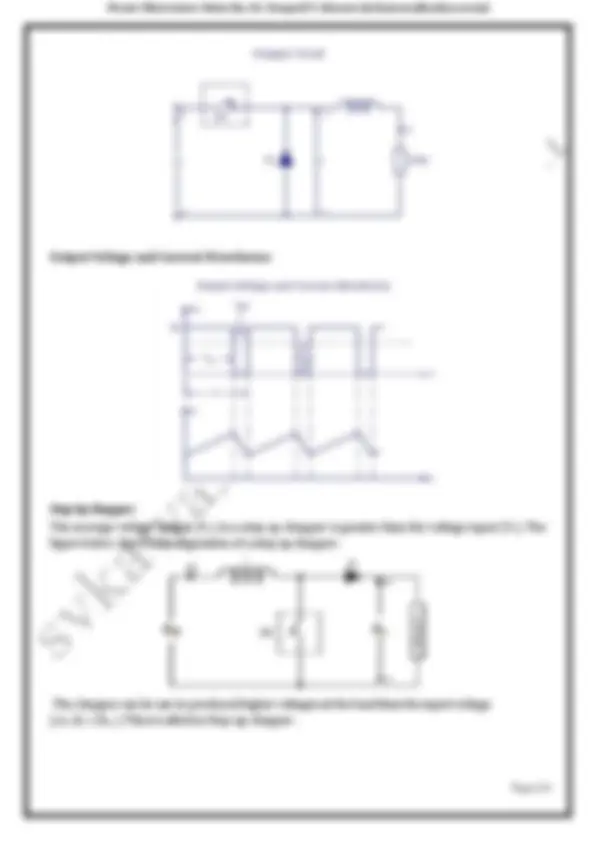
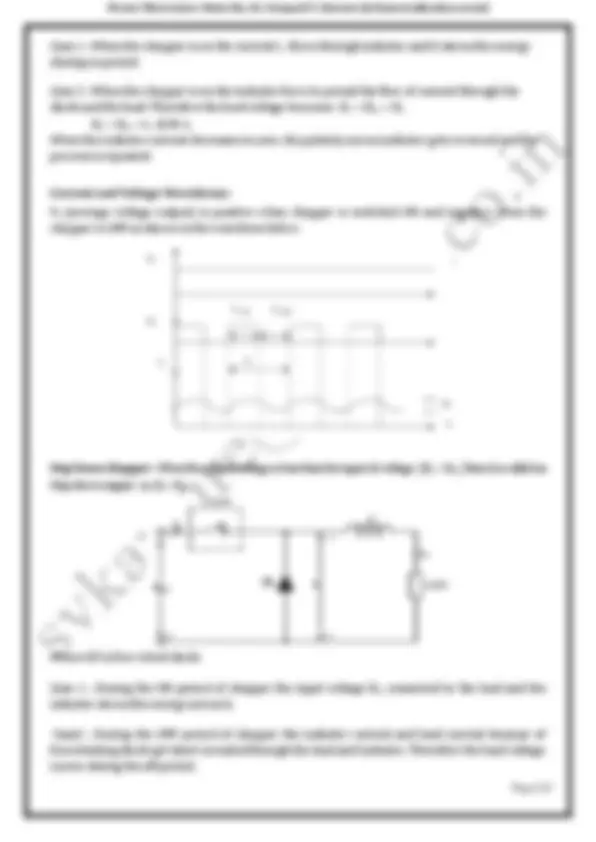
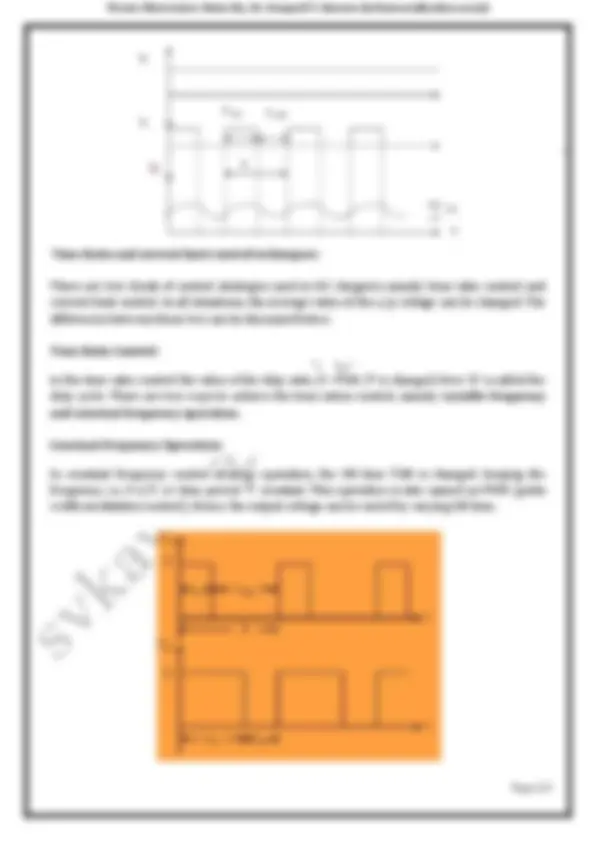
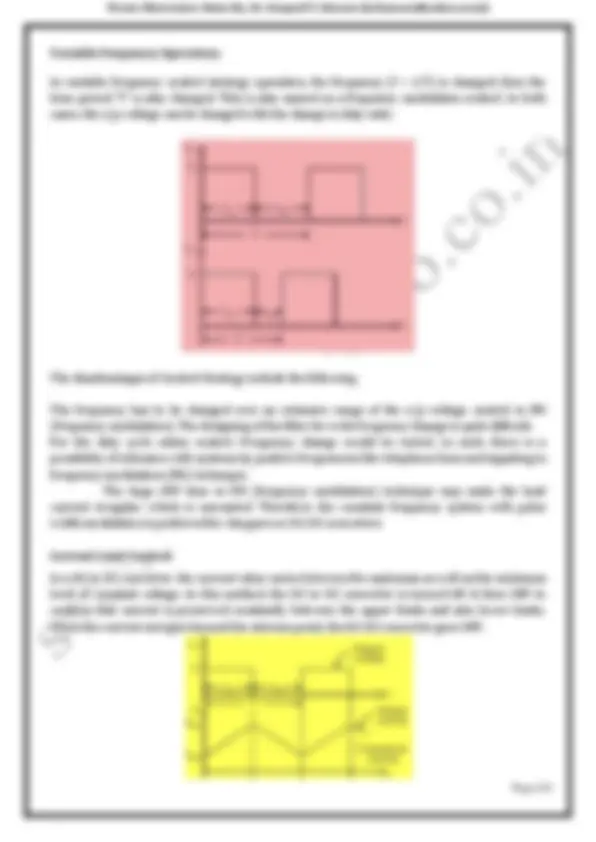
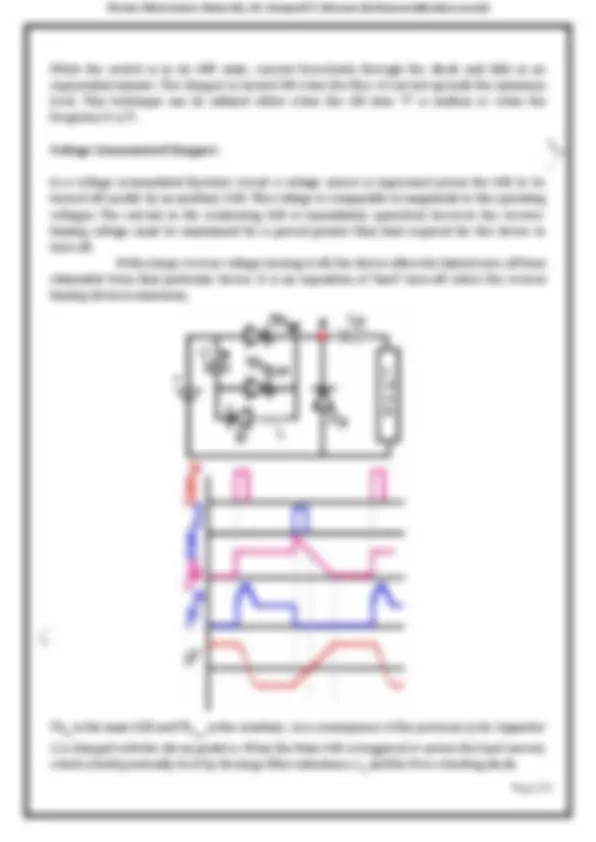
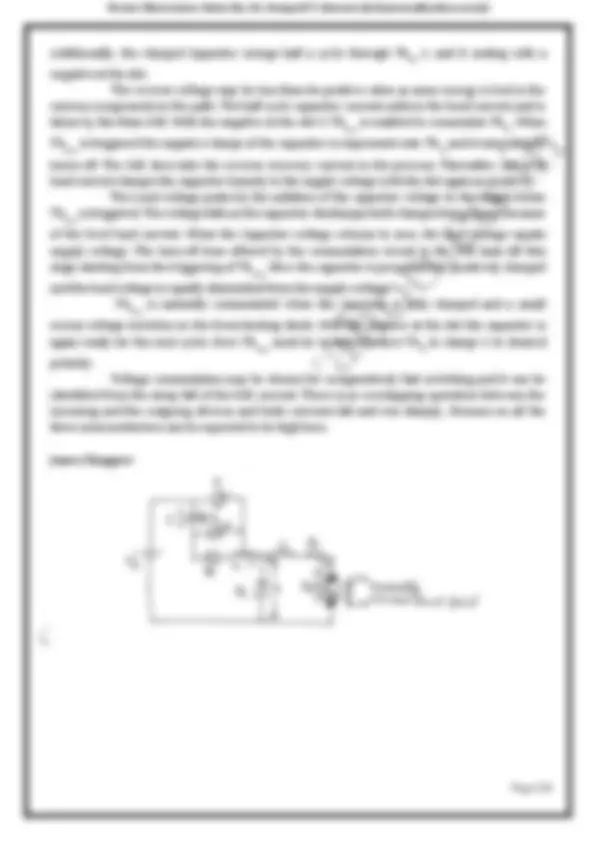
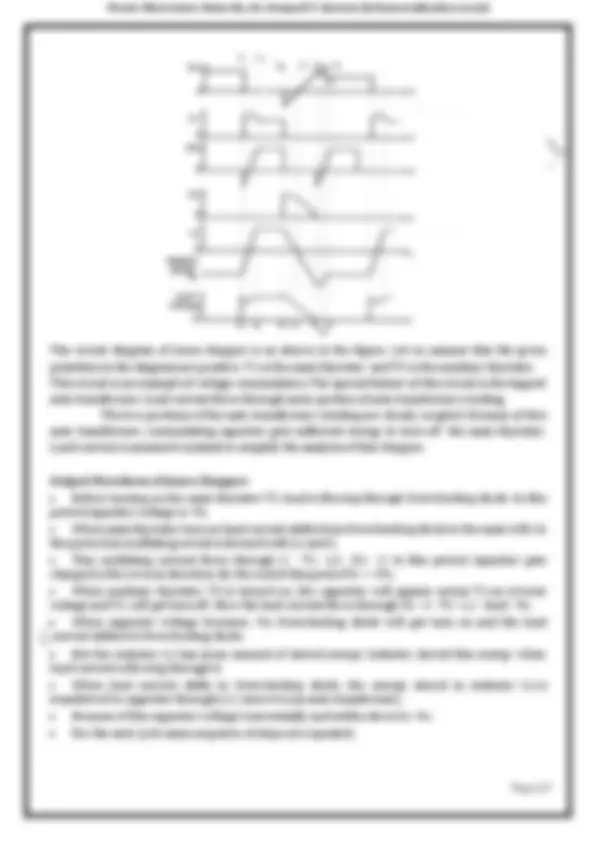

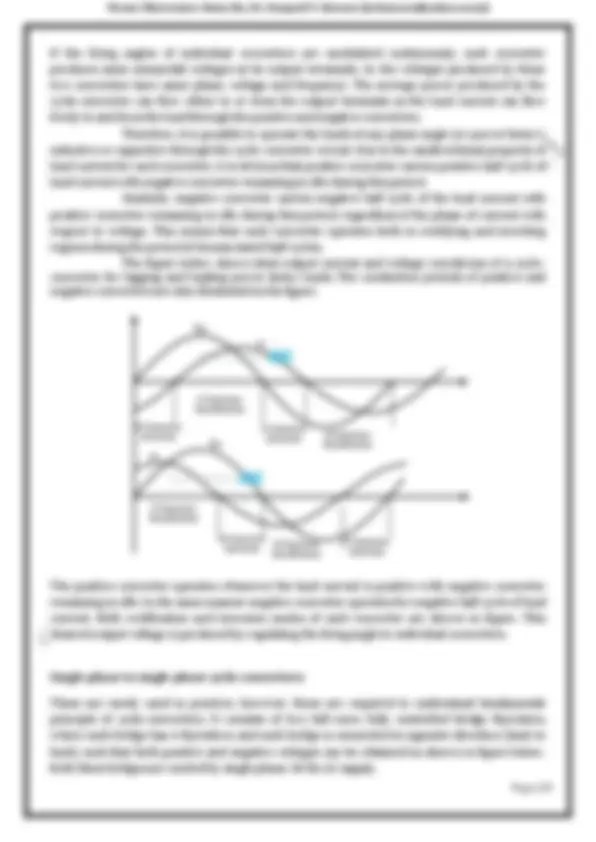
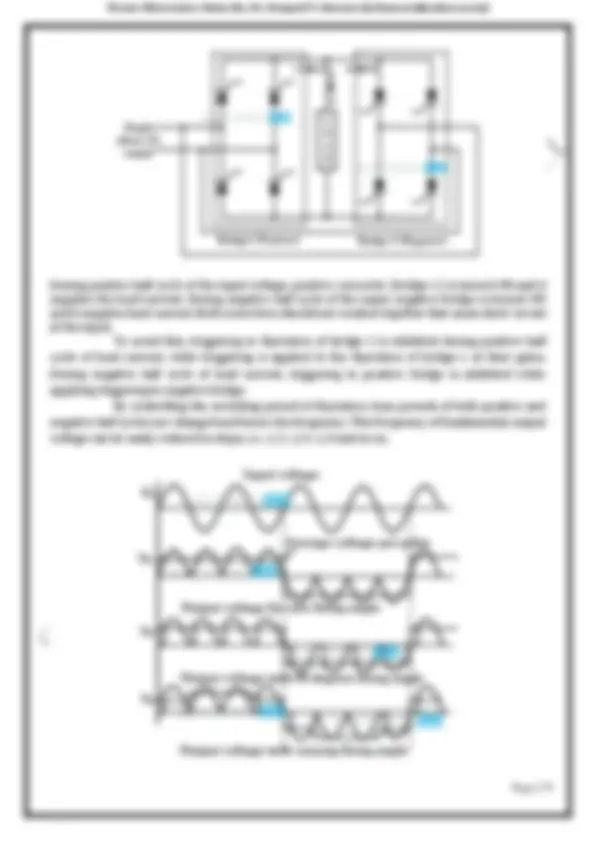
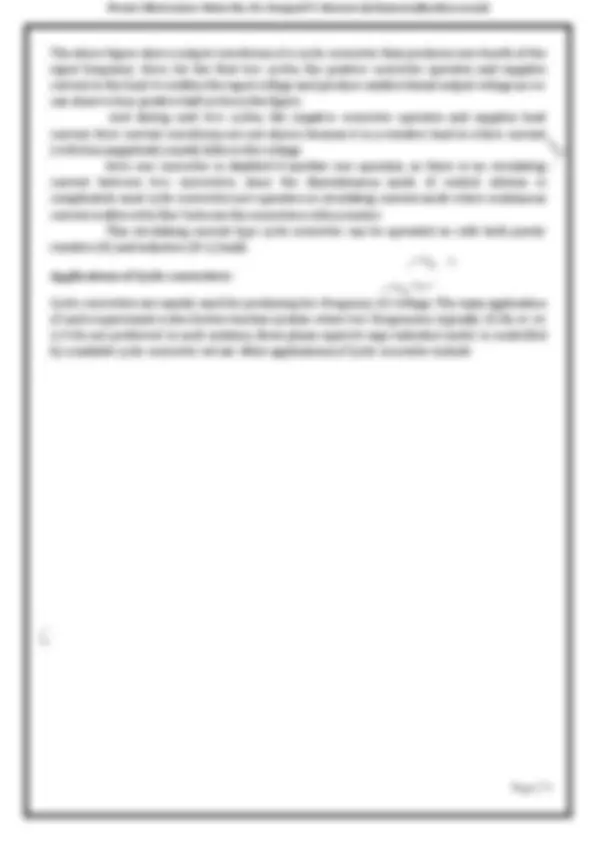
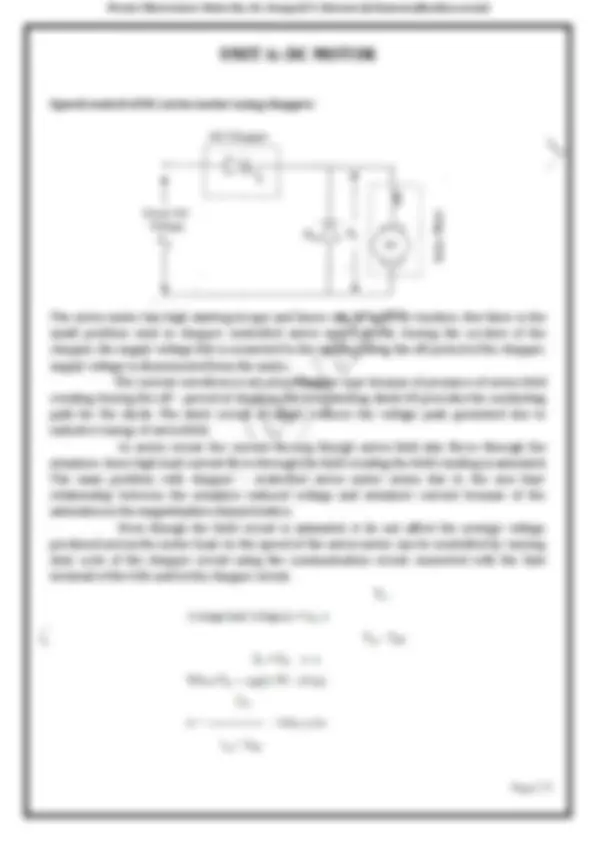
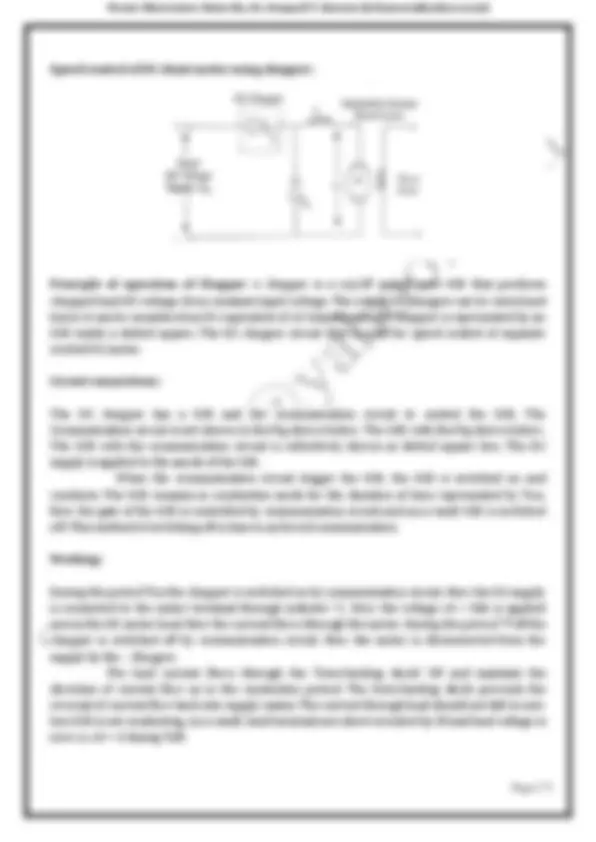
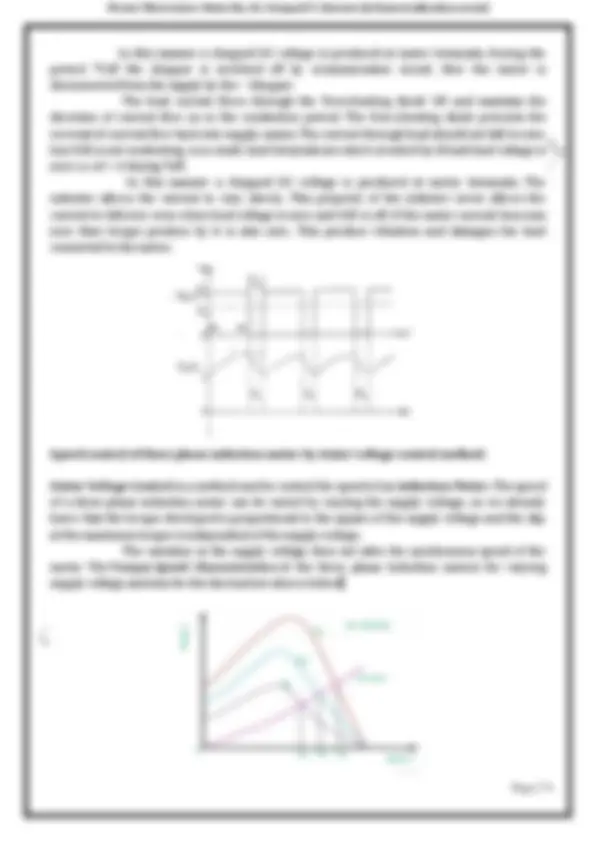
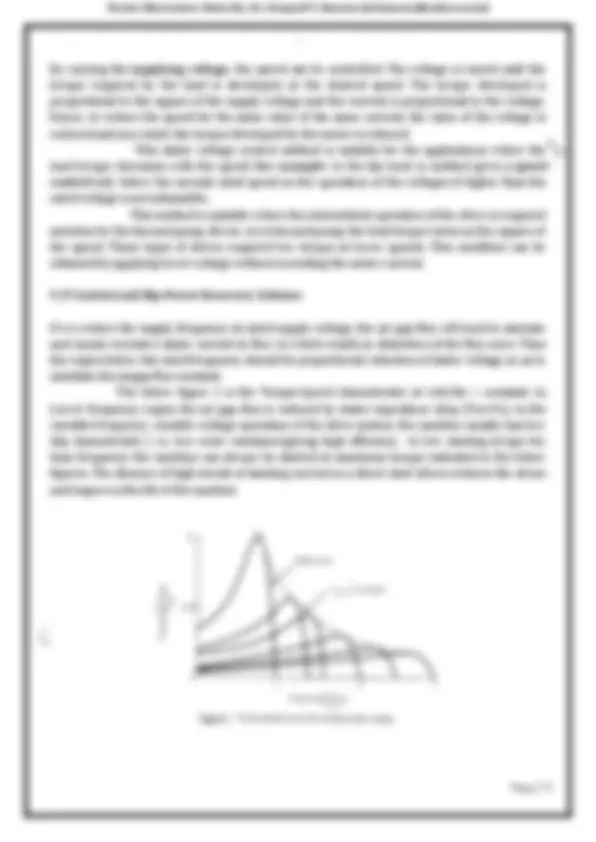
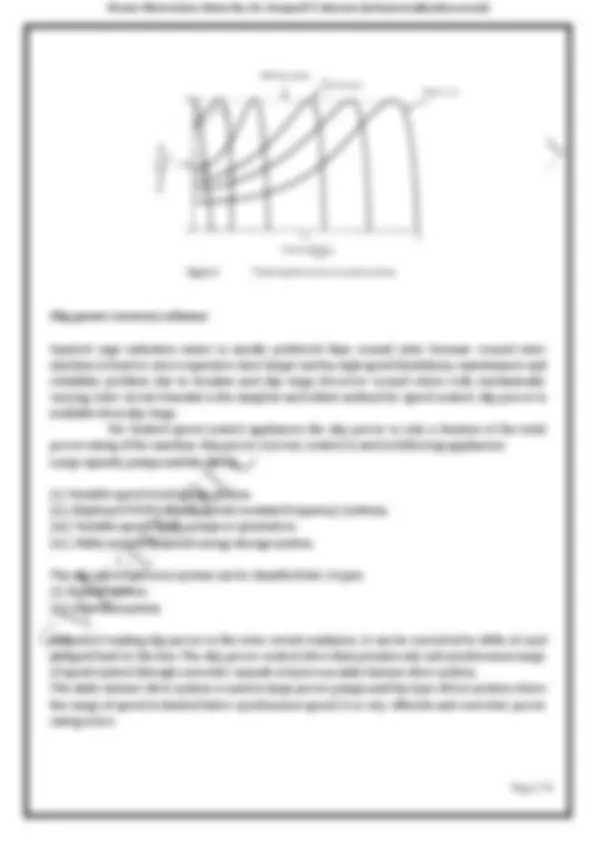
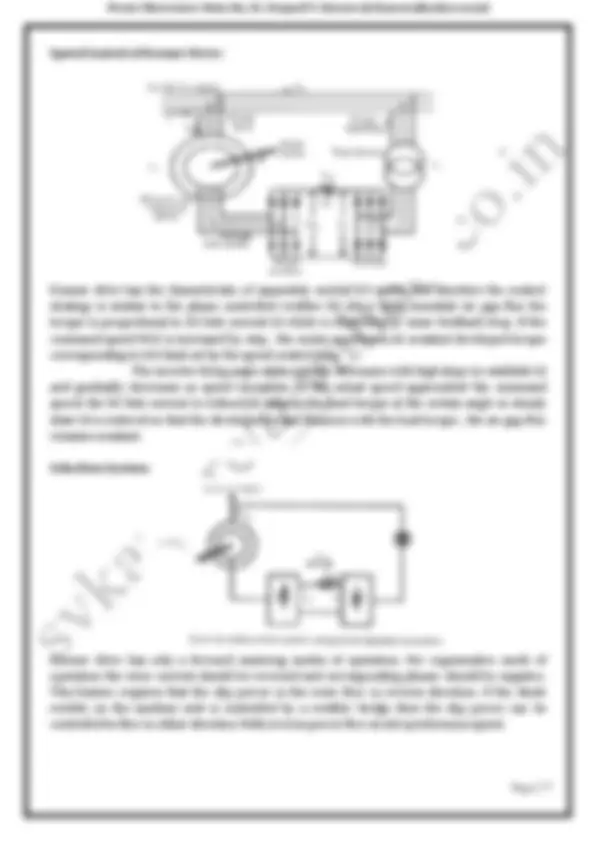
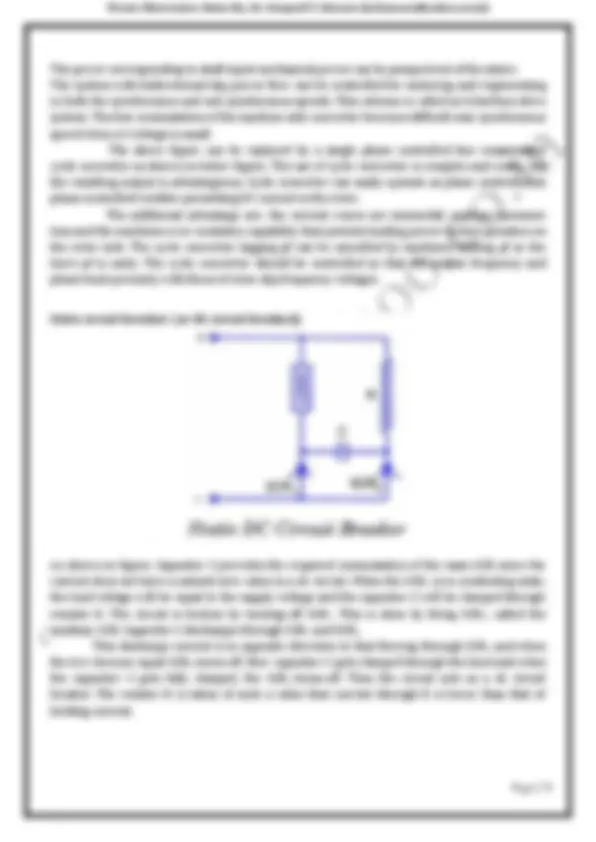

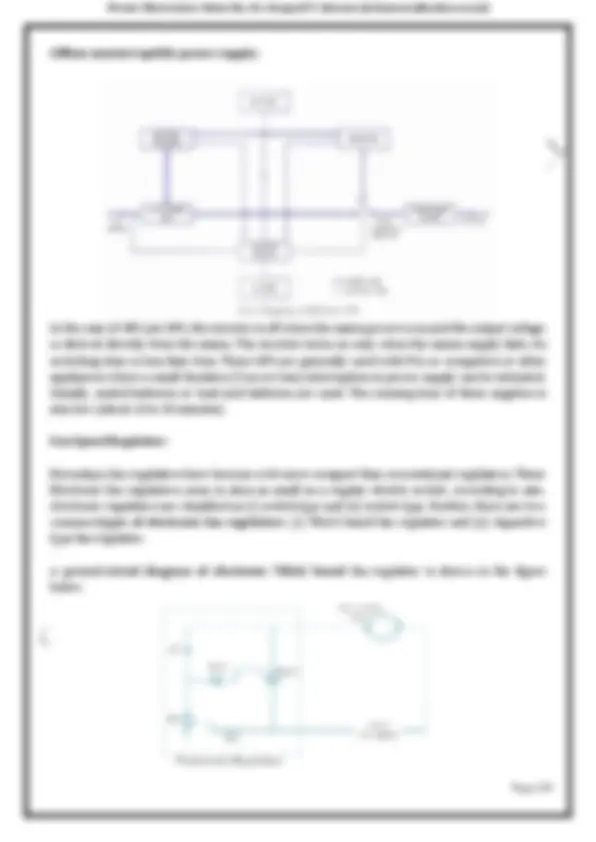
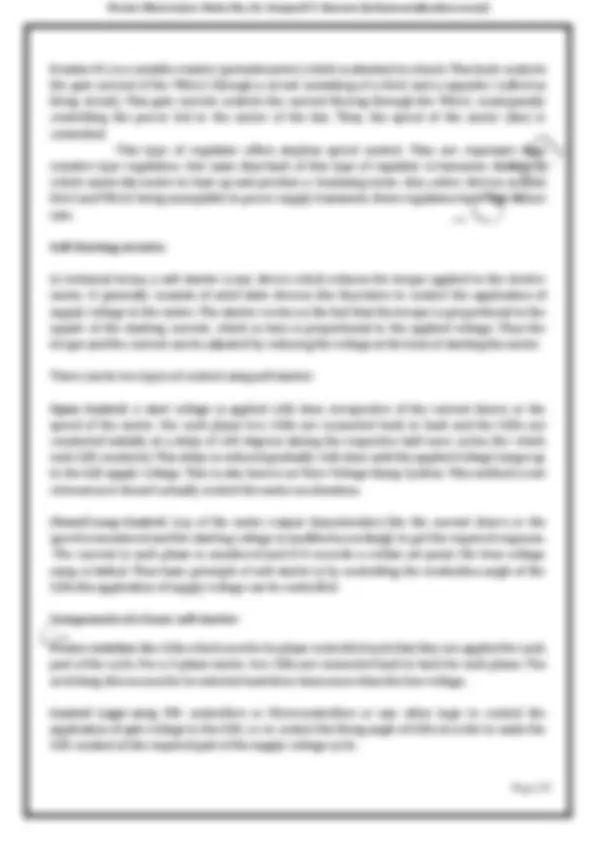
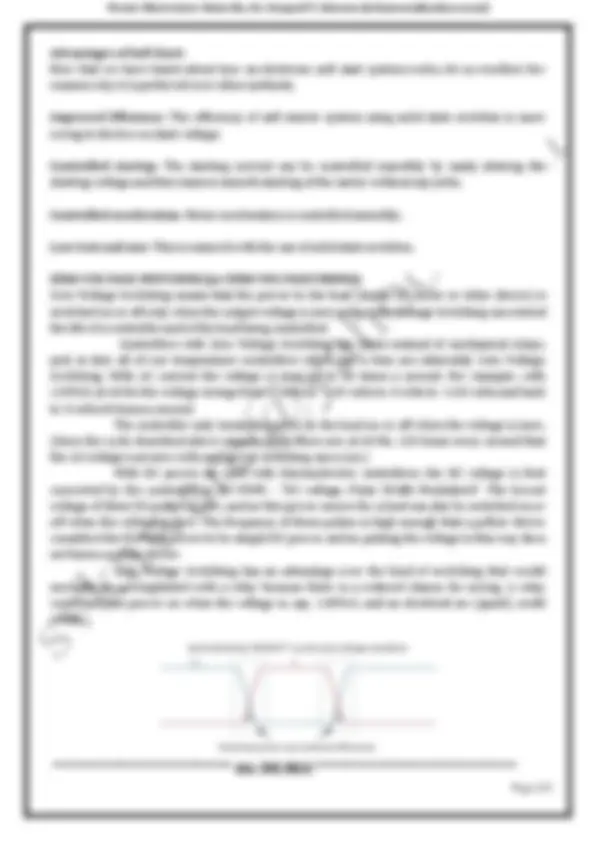
Study with the several resources on Docsity
Earn points by helping other students or get them with a premium plan
Prepare for your exams
Study with the several resources on Docsity
Earn points to download
Earn points by helping other students or get them with a premium plan
Community
Ask the community for help and clear up your study doubts
Discover the best universities in your country according to Docsity users
Free resources
Download our free guides on studying techniques, anxiety management strategies, and thesis advice from Docsity tutors
Power Electronics By Er. Swapnil V. Kaware
Typology: Study notes
1 / 82
This page cannot be seen from the preview
Don't miss anything!
UNIT 1: POWER SEMICONDUCTOR DEVICES Types of power semiconductor devices: SILICON CONTROLLED RECTIFIER: The silicon control rectifier (SCR) consists of four layers of semiconductors, which form NPNP or PNPN structures, having three P-N junctions labeled J1 , J2 and J3 , and three terminals. The anode terminal of an SCR is connected to the p-type material of a PNPN structure, and the cathode terminal is connected to the n-type layer, while the gate of the SCR is connected to the p-type material nearest to the cathode. An SCR consists of four layers of alternating p- and n-type semiconductor materials. Silicon is used as the intrinsic semiconductor, to which the proper dopants are added. The junctions are either diffused or alloyed (alloy is a mixed semiconductor or a mixed metal). The planar construction is used for low-power SCRs (and all the junctions are diffused). The mesa-type construction is used for high-power SCRs. In this case, junction J2 is obtained by the diffusion method, and then the outer two layers are alloyed to it, since the PNPN pellet is required to handle large currents. It is properly braced with tungsten or molybdenum plates to provide greater mechanical strength. One of these plates is hard-soldered to a copper stud, which is threaded for attachment of heat sink. The doping of PNPN depends on the application of SCR, since its characteristics are similar to those of the thyristor.
SCR Triggering or Turn ON & Turn OFF Methods: With a voltage applied to the SCR, if the anode is made positive with respect to the cathode, the SCR becomes forward biased. Thus, the SCR comes into the forward blocking state. The SCR can be made to conduct or switching into conduction mode is performed by any one of the following methods. (i). Forward voltage triggering. (ii). Temperature triggering. (iii). dv/dt triggering. (iv). Light triggering. (v). Gate triggering.
1. Forward Voltage Triggering: By increasing the forward anode to cathode voltage, the depletion layer width is also increasing at junction J2. This also causes to increase the minority charge carriers accelerating voltage at junction J2. This further leads to an avalanche breakdown of the junction J2 at a forward break over voltage VBO. At this stage SCR turns into conduction mode and hence a large current flow through it with a low voltage drop across it. During the turn ON state the forward voltage drop across the SCR is in the range of 1 to 1.5 volts and this may be increased with the load current. In practice this method is not employed because it needs a very large anode to cathode voltage. And also once the voltage is more than the VBO, it generates very high currents which may cause damage to the SCR. Therefore, most of the cases this type of triggering is avoided. 2. Temperature Triggering: The reverse leakage current depends on the temperature. If the temperature is increased to a certain value, the number of hole-pairs also increases. This causes to increase the leakage current and further it increases the current gains of the SCR.
This starts the regenerative action inside the SCR since the (α1 + α2) value approaches to unity (as the current gains increases). By increasing the temperature at junction J2 causes the breakdown of the junction and hence it conducts. This triggering occur in some circumstances particularly when it the device temperature is more (also called false triggering). This type of triggering is practically not employed because it causes the thermal runaway and hence the device or SCR may be damaged.
3. dv/dt Triggering: In forward blocking state junctions J1 and J3 are forward biased and J2 is reverse biased. So the junction J2 behaves as a capacitor (of two conducting plates J1 and J3 with a dielectric J2) due to the space charges in the depletion region. The charging current of the capacitor is given as I = C dv/ dt where dv/dt is the rate of change of applied voltage and C is the junction capacitance. From the above equation, if the rate of change of the applied voltage is large that leads to increase the charging current which is enough to increase the value of alpha. So the SCR becomes turned ON without a gate signal. However, this method is also practically avoided because it is a false turn ON process and also this can produce very high voltage spikes across the SCR so there will be considerable damage to it. 4. Light Triggering: An SCR turned ON by light radiation is also called as Light Activated SCR (LASCR). This type of triggering is employed for phase controlled converters in HVDC transmission systems. In this method, light rays with appropriate wavelength and intensity are allowed to strike the junction J2. These types of SCRs are consisting a niche in the inner p-layer. Therefore, when the light struck on this niche, electron-hole pairs are generated at the junction J2 which provides additional charge carriers at the junction leads to turn ON the SCR. 5.Gate Triggering: This is most common and efficient method to turn ON the SCR. When the SCR is forward biased, a sufficient voltage at the gate terminal injects some electrons into the junction J2. This result to increase reverse leakage current and hence the breakdown of junction J2 even at the voltage lower than the VBO. Depends on the size of the SCR the gate current varies from a few milli-amps to 200 milli amps or more. If the gate current applied is more, then more electrons are injected into the junction J2 and results to come into the conduction state at much lower applied voltage. In gate triggering method, a positive voltage applied between the gate and the cathode terminals. We can use three types of gate signals to turn On the SCR. Those are DC signal, AC signal and pulse signal.
So RE(MIN) = VBB – VE / IRE = VBB – VV / IV or for ensuring turn-off. RE > = VBB – VV / IV So, the range of resistor RE is given as VBB – VP / IP >RE > VBB – VV / IV The resistor R is chosen small enough so as to ensure that SCR is not turned on by voltage VR when emitter terminal E is open or IE = 0 The voltage VR = RVBB/R + RBB for open-emitter terminal. The capacitor C determines the time interval between triggering pulses and the time duration of each pulse. By varying RE, we can change the time constant RE C and alter the point at which the UJT fires. This allows us to control the conduction angle of the SCR, which means the control of load current. Important Terms In The V-I Characteristics of SCR:
**1. Break over voltage
3. Holding Current: It is the maximum anode current, gate being open, at which SCR is turned OFF from ON condition. When SCR is in the conducting state, it can not be turned OFF even if gate voltage is removed. The only way to turn off or open the SCR is to reduce the supply voltage to almost zero at which point the internal transistor comes out of saturation and opens the SCR. The anode current under this condition is very small (a few mA) and is called holding current. Thus, if an SCR has a holding current of 5mA, it means that if anode current is made less than 5 mA, then SCR will be turned off. 4. Forward Current Rating: It is the maximum anode current that an SCR is capable of passing without destruction. Every SCR has a safe value of forward current which it can conduct. If the value of current exceeds this value, the SCR may be destroyed due to intensive heating at the junction. For example, if an SCR has a forward current rating of 40 A, it means that the SCR can safely carry only 40 A. Any attempt to exceed this value will result in the destruction of the SCR. Commercially available SCRs have forward current ratings from about 30A to 100A. 5. Circuit Fusing (I^2 t) Rating: It is the product of square forward surge current and the time of duration of the surge i.e., Circuit fusing rating =I^2 t The circuit fusing rating indicates the maximum forward surge current capability of SCR. For example, consider an SCR having circuit fusing rating of 90 A^2 s. If this rating is exceeded in the SCR circuit , the device will be destroyed by excessive power dissipation. APPLICATIONS: SCRs are mainly used in devices where the control of high power, possibly coupled with high voltage, is demanded. Their operation makes them suitable for use in medium- to high- voltage AC power control applications, such as lamp dimming, power regulators and motor control. SCRs and similar devices are used for rectification of high-power AC in high-voltage direct-current power transmission. They are also used in the control of welding machines, mainly MTAW (metal tungsten arc welding) and GTAW (gas tungsten arc welding) processes similar.
SCR in Normal Operation: In order to operate the SCR in normal operation, the following points are kept in view:
Below the holding current, the DIAC reverts to its high-resistance (non-conducting) state. Its behaviour is bi-directional and therefore its operation occurs on both halves of an alternating cycle. TRIAC: Construction And Operation The triac is another three-terminal ac switch that is triggered into conduction when a low- energy signal is applied to its gate terminal. Unlike the SCR, the triac conducts in either direction when turned on. The triac also differs from the SCR in that either a positive or negative gate signal triggers it into conduction. Thus the triac is a three terminal, four layer bidirectional semiconductor device that controls ac power whereas an SCR controls dc power or forward biased half cycles of ac in a load. Because of its bidirectional conduction property, the triac is widely used in the field of power electronics for control purposes. Triacs of 16 kW rating are readily available in the market. “Triac” is an abbreviation for three terminal ac switch. „Tri‟-indicates that the device has three terminals and „ac‟ indicates that the device controls alternating current or can conduct in either direction. Construction of a Triac: As mentioned above, triac is a three terminal, four layer bilateral semiconductor device. It incorporates two SCRs connected in inverse parallel with a common gate terminal in a single chip device. The arrangement of the triac is shown in figure. As seen, it has six doped regions. The gate terminal G makes ohmic contacts with both the N and P materials. This permits trigger.
Gate turn-off thyristor (GTO): A gate turn-off thyristor (GTO) is a special type of thyristor, which is a high- power semiconductor device. It was invented at General Electric.[1]^ GTOs, as opposed to normal thyristors, are fully controllable switches which can be turned on and off by their third lead, the gate lead. GTO thyristors are available with or without reverse blocking capability. Reverse blocking capability adds to the forward voltage drop because of the need to have a long, low doped P region. GTO thyristors capable of blocking reverse voltage are known as Symmetrical GTO thyristors, abbreviated S-GTO. Usually, the reverse blocking voltage rating and forward blocking voltage rating are the same. The typical application for symmetrical GTO thyristors is in current source inverters. GTO thyristors incapable of blocking reverse voltage are known as asymmetrical GTO thyristors, abbreviated A-GTO, and are generally more common than Symmetrical GTO thyristors. They typically have a reverse breakdown rating in the tens of volts. A-GTO thyristors are used where either a reverse conducting diode is applied in parallel (for example, in voltage source inverters) or where reverse voltage would never occur (for example, in switching power supplies or DC traction choppers). GTO thyristors can be fabricated with a reverse conducting diode in the same package. These are known as RCGTO, for Reverse Conducting GTO thyristor. MOSFET: MOSFET stands for metal-oxide semiconductor field-effect transistor. It is a special type of field-effect transistor (FET). Unlike BJT which is „current controlled‟, the MOSFET is a voltage controlled device. The MOSFET has “ gate “, “ Drain ” and “ Source ” terminals instead of a “base”, “collector”, and “emitter” terminals in a bipolar transistor. By applying voltage at the gate, it generates an electrical field to control the current flow through the channel between drain and source, and there is no current flow from the gate into the MOSFET.
A MOSFET may be thought of as a variable resistor, where the Gate-Source voltage difference can control the Drain-Source Resistance. When there is no applying voltage between the Gate- Source , the Drain-Source resistance is very high, which is almost like a open circuit, so no current may flow through the Drain-Source. When Gate-Source potential difference is applied, the Drain-Source resistance is reduced, and there will be current flowing through Drain-Source, which is now a closed circuit. In a nutshell, a FET is controlled by the Gate-Source voltage applied (which regulates the electrical field across a channel), like pinching or opening a straw and stopping or allowing current flowing. Because of this property, FETs are great for large current flow, and the MOSFET is commonly used as a switch. Differences between BJT and MOSFET : Unlike bipolar transistors, MOSFET is voltage controlled. While BJT is current controlled. Because they are voltage controlled, MOSFET have a very high input impedance, so just about anything can drive them. MOSFET has high input impedance working. MOSFET is a voltage controlled field effect transistor that differs from a JFET. The Gate electrode is electrically insulated from the main semiconductor by a thin layer of insulating material. This insulated metal gate is like a plate of a capacitor which has an extremely high input resistance (as high as almost infinite). Because of the isolation of the Gate there is no current flow into the MOSFET from Gate. When voltage is applied at the gate, it changes the width of the Drain-Source channel along which charge carriers flow (electron or hole). The wider the channel, the better the device conducts.
For a metal oxide semiconductor field effect transistor or MOSFET, there is no input current as the gate is isolated from the main current carrying channel. Therefore, an FET’s gain is equal to the ratio of output current change to input voltage change, making it a transconductance device and this is also true of the IGBT. Then we can treat the IGBT as a power BJT whose base current is provided by a MOSFET. The Insulated Gate Bipolar Transistor can be used in small signal amplifier circuits in much the same way as the BJT or MOSFET type transistors. But as the IGBT combines the low conduction loss of a BJT with the high switching speed of a power MOSFET an optimal solid state switch exists which is ideal for use in power electronics applications IGBT Characteristics: Because the IGBT is a voltage-controlled device, it only requires a small voltage on the Gate to maintain conduction through the device unlike BJT’s which require that the Base current is continuously supplied in a sufficient enough quantity to maintain saturation. Also the IGBT is a unidirectional device, meaning it can only switch current in the “forward direction”, that is from Collector to Emitter unlike MOSFET’s which have bi-directional current switching capabilities (controlled in the forward direction and uncontrolled in the reverse direction). The principal of operation and Gate drive circuits for the insulated gate bipolar transistor are very similar to that of the N-channel power MOSFET. The basic difference is that the resistance offered by the main conducting channel when current flows through the device in its “ON” state is very much smaller in the IGBT. Because of this, the current ratings are much higher when compared with an equivalent power MOSFET. Snubber Citcuit of SCR: As we discussed above, the protection against high voltage reverse recovery transients and dv/dt is achieved by using an RC snubber circuit. This snubber circuit consists of a series combination of capacitor and resistor which is connected across the SCR. This also consist an inductance in series with the SCR to prevent the high di/dt. The resistance value is of few hundred ohms. The snubber network used for the protection of SCR is shown below.
When the switch closed, a sudden voltage appears across the SCR which is bypassed to the RC network. This is because the capacitor acts as a short circuit which reduces the voltage across the SCR to zero. As the time increases, voltage across the capacitor builds up at slow rate such that dv/dt across the capacitor is too small to turn ON the SCR. Therefore, the dv/dt across the SCR and the capacitor is less than the maximum dv/dt rating of the SCR. Normally, the capacitor is charged to a voltage equal the maximum supply voltage which is the forward blocking voltage of the SCR. If the SCR is turned ON, the capacitor starts discharging which causes a high current to flow through the SCR. This produces a high di/dt that leads to damage the SCR. And hence, to limit the high di/dt and peak discharge current, a small resistance is placed in series with the capacitor as shown in above. These snubber circuits can also be connected to any switching circuit to limit the high surge or transient voltages. Application of Power Electronics:
Parallel Connection of an SCR & Equalization of current in parallel connected SCR: When the load current exceeds the SCR current rating, SCRs are connected in parallel to share the load current. But when SCRs are operated in parallel, the current sharing between them may not be proper. The device having lower dynamic resistance will tend to share more current. This will raise the temperature of that particular device in comparison to other, thereby reducing further its dynamic resistance and increasing current through it. This process is cumulative and continues till the device gets punctured. Some other factors which directly or indirectly add to this problem are difference in turn-on time, delay time, finger voltage* and loop inductance. Arrangement of SCRs in the cubicle also plays vital role. When the SCRs are connected in parallel, it must be ensured that the latching current level of the all the SCRs is such that when gate pulse is applied, all of them turn-on and remain on when the gate pulse is removed. Further the holding currents of the devices should not be so much different that at reduced load current one of the device gets turned-off because of fall of current through it blow its holding current value. This is particularly important because on increase in load current, the device which has stopped conducting cannot start in the absence of gate pulse. Another point to be considered is the on-state voltage across the device. For equal sharing of currents by the devices voltage drop across the parallel paths must be equal. For operation of all the SCRs connected in parallel at the same temperature, it becomes necessary to use a common heat sink for their mounting, as illustrated in figure. Resistance compensation used for dc circuits is shown in figure. In this circuit the resistors Rx and R 2 are chosen so as to cause equal voltage drop in both arms. Inductive compensation used for ac circuits is shown in figure The difference in characteristics due to different turn-on time, delay time, finger voltage, latching current, holding current can be minimized by using inductive compensation. Firing circuits giving high rate of rise can be used to reduce mismatch of gate characteristics and delay time.
The application of GATE voltage is known as firing. Types of SCR firing: Generally there are two types of firing: (1). Zero Voltage Cross Over firing: Zero-crossing control mode (also called fast cycling, integral cycle, or burst firing) operates by turning the SCR’s on only when the instantaneous value of the sinusoidal voltage is zero. Zero Crossover Firing sends the gate signals to the thyristors only when the voltage through it is zero. Therefore, the thyristor will turn on and off only at the zero voltage crossover point of the sine wave which occurs every half cycle. The fully on and off periods are based on burst pulses of time which are set by the firing circuit and can be adjusted to suit the user’s load. For example if the total cycle time is set to 2 seconds and a 50% power output from the thyristor controller is required then the output will be fully on for 1 second and fully off for 1 second, this is shown in the diagram below: This percentage output works linearly with reference to the amount of time on and off. For example if the total cycle time is set to 2 seconds and a 75% power output from the thyristor controller is required then the output will be fully on for 1.5 seconds and fully off for 0. seconds. To achieve this range of outputs a signal from the user is required which is normally 0- 10Vdc or 4-20mA. This signal is proportional to the percentage power output required, for example when using a 0-10Vdc signal: Signal (Vdc) Percentage Output (%) 0 0 2.5 25 5 50 7.5 75 10 100