
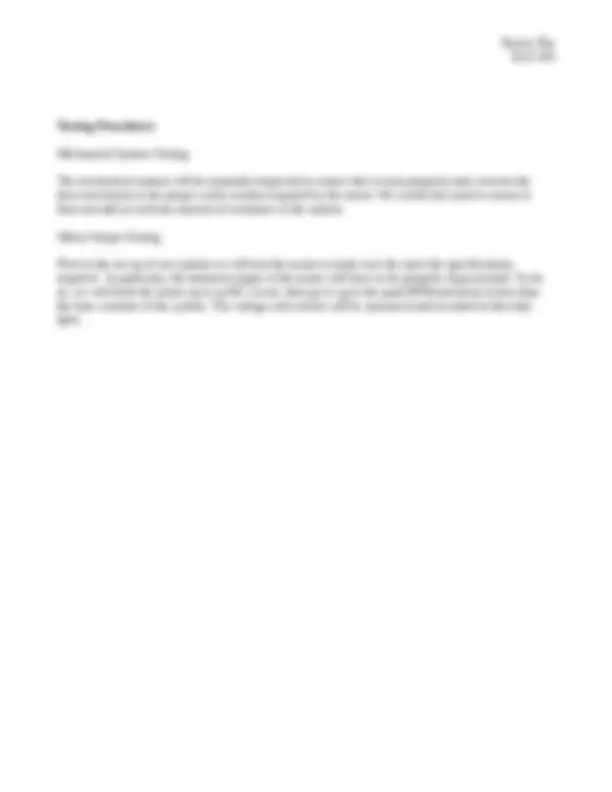
Study with the several resources on Docsity
Earn points by helping other students or get them with a premium plan
Prepare for your exams
Study with the several resources on Docsity
Earn points to download
Earn points by helping other students or get them with a premium plan
Community
Ask the community for help and clear up your study doubts
Discover the best universities in your country according to Docsity users
Free resources
Download our free guides on studying techniques, anxiety management strategies, and thesis advice from Docsity tutors
The process of calculating the power requirements for a motor used in a door automation system. The author, xavier zhu, from ece 445, explains how they determined the acceptable user load and the total available power from the user. They then use this information to select a motor with the appropriate torque and rpm. The document also includes details about the mechanical design and testing procedures.
Typology: Study Guides, Projects, Research
1 / 2
This page cannot be seen from the preview
Don't miss anything!
Xavier Zhu ECE 445 Power Calculation for Motor In our choice of motors the key aspect was making sure that the user could handle the load imposed upon him by the motor. The motor must be selected such as not to impede the user's convenience when it comes to opening and closing the door. To do so we first tried to determine what is an acceptable level we can harvest from the motion of opening a door. We used a spring scale and recorded the amount of force required to open a door as well as the average time it took. We measured the average force required to open an average household door as being approximately 0.4N, and the highest force required to open an large, heavy door to be about 2.5N. Our device will be installed on regular household doors, and we aim to increase the user load by an additional 1.2N. This is the maximal amount of effort we can get from the user without making the door overly taxing. Since the distance from the door knob to the hinge of a regular door is about 0.8m, and the average time taken to open it is about 1.0s, we have the ability to calculate the total available power from the user: Total Power Input = Fu d^ ^ d = (^) 1.2N 0.8m 0.25s-1=.24W Where Fu^ = Force applied by user, d is the distance from the knob to the hinge, and d^ is the angular velocity of the door in revolutions per second. A proportion of this power will be lost in the mechanical transfer between the door and the motor. Assuming an efficiency of 0.6 gives us 0.144W of power transferred to the motor. Due to the interrupted nature of our input, our system is constantly operating in the transient state. At this stage, the back emf of the motor is negligible, and since our load is merely a rectifier and a super- capacitor the load will not be high either – almost all power out of of the motor should be stored in the capacitor. Ideally, we would choose the motor such that its rated torque and RPM correspond to the available power. Tr (^) r = 0.144W With these numbers as a guide, we used the BDR-32-20- Motor from Anaheim Automation. It has a stall torque of 64.8 g-cm and a no-load RPM of 2700. This corresponds to a power input of 0.28W. This number drops to .045 at maximum efficiency at continuous torque, This indicates the motor operates at the correct range for our requirements. Mechanical Design Our mechanical design is essentially a gear train driving a series of pulleys step it up to the proper RPM for our motor. The entire system is mounted on top of the frame and does not impede the movement of the door. The diagram is attached.
Xavier Zhu ECE 445 Testing Procedures Mechanical System Testing The mechanical system will be manually inspected to ensure that it turns properly and converts the door movement to the proper cyclic motion required by the motor. We would also need to ensure it does not add an extreme amount of resistance to the system. Motor Output Testing Prior to the set up of our system we will test the motor to make sure the meet the specifications required. In particular, the transient output of the motor will have to be properly characterized. To do so, we will hook the motor up to an RC circuit, then get it up to the peak RPM and down in less than the time constant of the system. The voltage and current will be measured and recorded in this time span.