
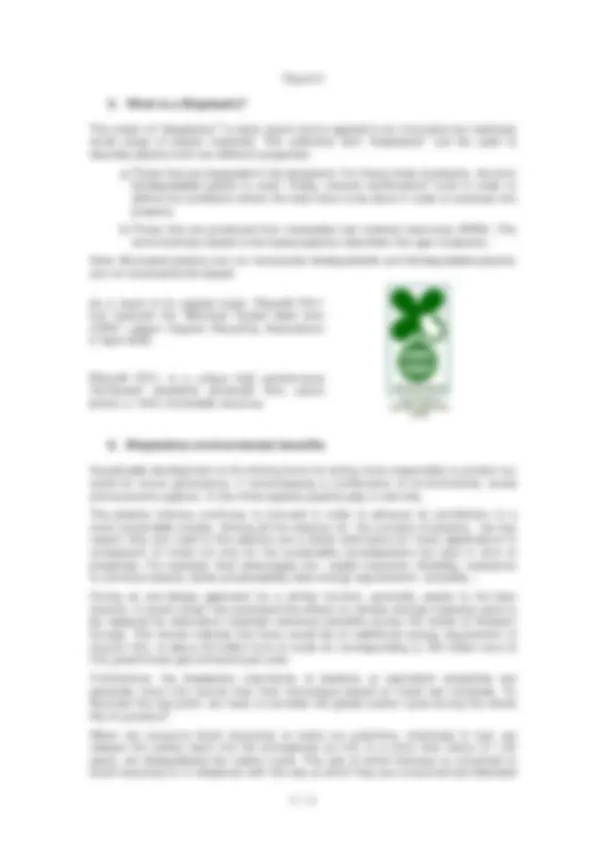
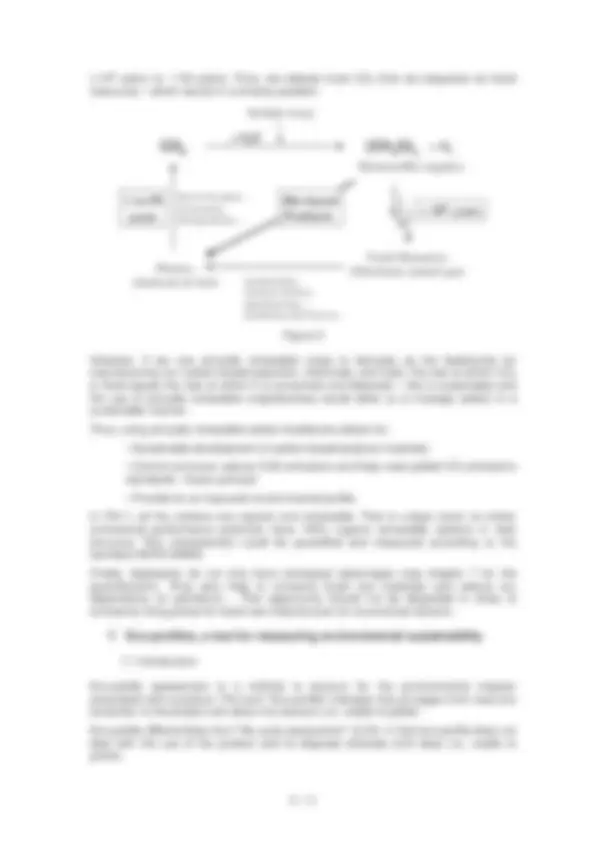
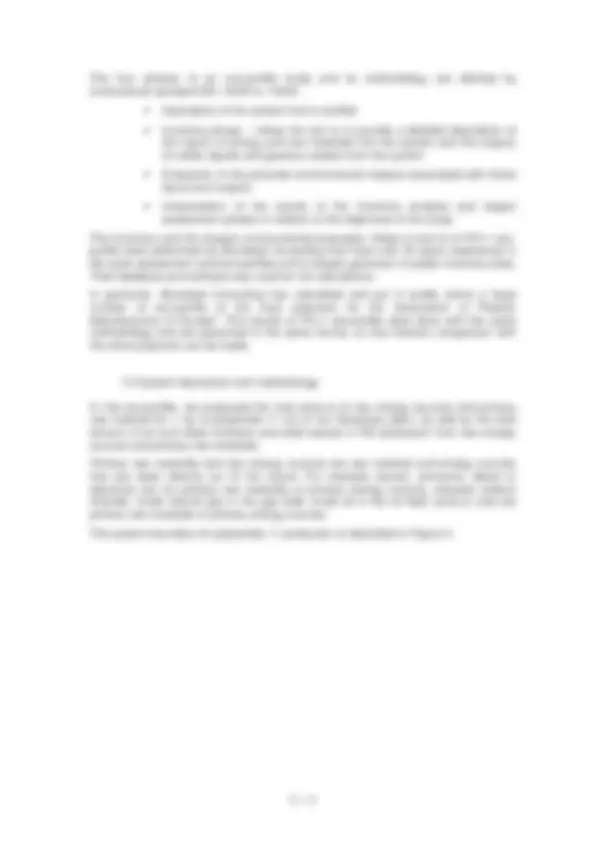
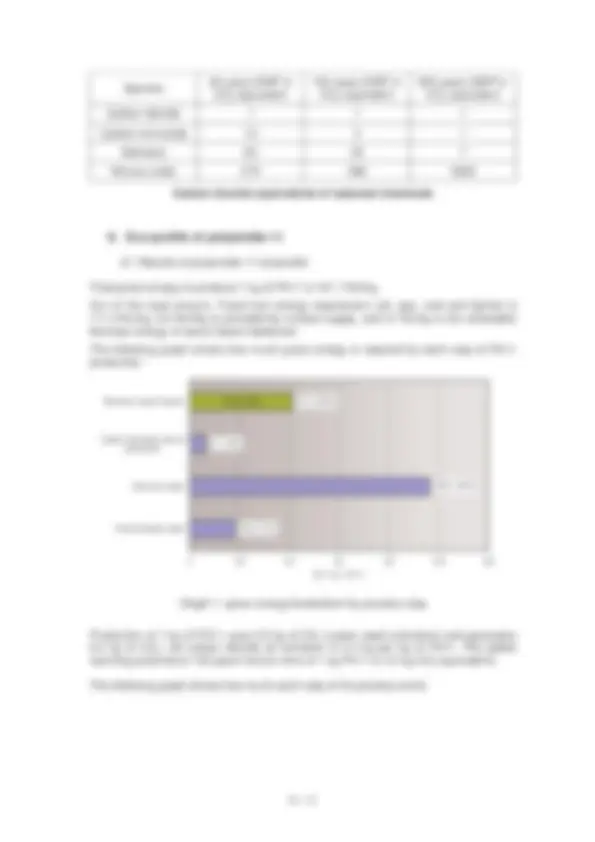
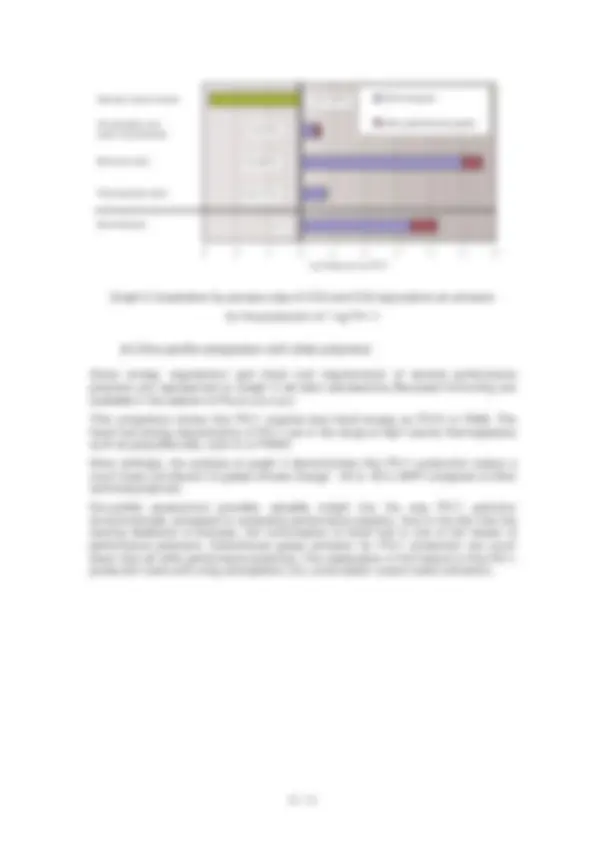
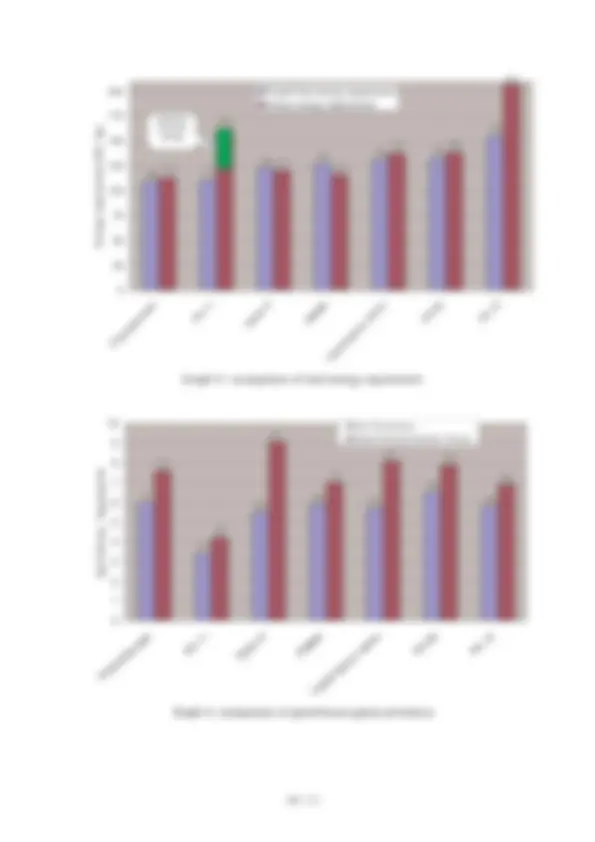
Study with the several resources on Docsity
Earn points by helping other students or get them with a premium plan
Prepare for your exams
Study with the several resources on Docsity
Earn points to download
Earn points by helping other students or get them with a premium plan
Community
Ask the community for help and clear up your study doubts
Discover the best universities in your country according to Docsity users
Free resources
Download our free guides on studying techniques, anxiety management strategies, and thesis advice from Docsity tutors
The properties of Polyamide 11
Typology: Essays (university)
1 / 11
This page cannot be seen from the preview
Don't miss anything!
On special offer
Jean-François Devaux, Guillaume Lê*, Bernard Pees****
*Arkema C.R.R.A. - Rue Henri Moissan, BP 63, 69493 PIERRE-BENITE Cedex, FRANCE ** Arkema CERDATO - Route du Rilsan, BP 19, 27470 SERQUIGNY, FRANCE
Polyamide-11 (PA11) is a high performance, lightweight bioplastic (plastic produced with 100% of the carbons coming from plant based renewable resources) with a unique combination high performance properties. Compared to other high performance and engineering plastics, PA11 delivers an outstanding level of chemical, thermal and impact resistance over a wide range of flexibility. PA11 is widely used in applications where safety, durability and versatility are critical. Polyamide 11 is therefore frequently used as a cost effective replacement for metal or rubber in highly technical applications.
PA11 is produced from renewable castor seeds and is commercialized by ARKEMA under the Rilsan® brand^1.
The purpose of this article is to present new data regarding the environmental benefits of PA11 as compared to other high performance polymers.
PA11 exhibits superior high temperature and cold impact resistance, has a lower moisture pick-up and exhibits superior ageing resistance compared to conventional high performance polyamides. This unique combination of properties allows to use Rilsan® B in a wide variety of highly demanding applications, including packaging, automotive and truck (ex. air brake tubes and fuel lines), oil and gas (ex. Offshore flexible pipes), sporting equipment (ex. soles for sports shoes, ski top layers), medical devices, cable and electrical components.
Some recent applications examples:
Rotomolding applications
Rilsan® CC for ski top layers
Multi-Layer Technology: Rilperm®
Conductive Rilsan in tubes applications
The history of PA11 development began in 1938 when Joseph Zeltner and Michel Genas envisioned the possibility to prepare the monomer of PA11 from undecenoic acid, obtained from castor oil cracking. Development of this process progressed sporadically through the wartime years. A pilot production finally began in 1944. An industrial monomer plant started in 1955 in Marseille (France) and supplied a polymerisation plant in Serquigny (France).
Today Rilsan® PA11 is produced in France (Serquigny), USA (Birdsboro, PA) and in China (Changshu).
PA11 life cycle starts with the castor bean plant named Ricinus Communis. Castor oil, which is extracted from its seeds, is the raw material for further transformations into PA11. All free energy consumed by this biological system arises from solar energy that is trapped by the process of photosynthesis. All the carbon atoms, that compose castor oil, as well as PA11 have their origin in the carbon dioxide that are absorbed by the castor plant. After harvesting, the seeds are treated in a similar manner than most oil seeds. The seeds are transported to a castor mill, where the oil is separated from the meal by crushing and/or solvent extraction. Because of its high nitrogen content, castor meal is recycled as fertilizer. Crude castor oil is further refined and then transported to our Marseille (France) monomer plant. Castor seed contains nearly 50% castor oil. Castor oil is a unique triacylglycerol, that is composed of 85 to 90% 12-hydroxyoleic acid, also known as ricinoleic acid. At Marseille plant, castor oil undergoes five chemical steps that are represented on Figure 1. Ricinoleate triglyceride is first transesterified with methanol to methyl ricinoleate (see Figure 1 - ) along with glycerin co-product. Cracking of methyl ricinoleate leads to heptaldehyde and methyl undecylenate (). After hydrolysis, undecylenic acid is obtained along with methanol, which is recycled to the first step (). The following step is an addition on hydrogen bromide () followed by a nucleophilic substitution with ammonia to form 11-aminoundecanoic acid (), which is PA11 monomer.
C
O O
OH
C
O O
OH
C
O O
OH^ +^
CH 3 OH
C
O OCH 3
OH
1/
HO OH OH
C
O OCH 3
O H
methyl ricinoleate
glycerin
methyl undecylenate (^) heptaldehyde
COOH +^ CH^3 OH + undecylenic acid
cracking
C
O Br OH
O H 2 N OH 11-aminoundecanoic acid
C
O O
OH
C
O O
OH
C
O O
OH^ +^
CH 3 OH
C
O OCH 3
OH
1/
HO OH OH
C
O OCH 3
O H
methyl ricinoleate
glycerin
methyl undecylenate (^) heptaldehyde
COOH +^ CH^3 OH + undecylenic acid
cracking
C
O Br OH
O H 2 N OH 11-aminoundecanoic acid
Figure 1
Aminoundecanoic acid is then sent to one of our polymerization plants where it is transformed into PA11 according to Figure 2.
C
O H 2 N (^) OH
O NH n Polymerization^ Polyamide 11
n
(>10^6 years vs. 1-50 years). Thus, we release more CO 2 than we sequester as fossil resources – which results in a kinetics problem.
CO 2
Sunlight energy
(CH 2 O)x + O 2
> 10^6 years
transportation, chemical industry, manufacturing,.., distribution and final use
1 to 50 years
End of life phase : incineration, biodegradation…
Bio-based Products
Figure 3
However, if we use annually renewable crops or biomass as the feedstocks for manufacturing our carbon based polymers, chemicals, and fuels, the rate at which CO 2 is fixed equals the rate at which it is consumed and liberated – this is sustainable and the use of annually renewable crops/biomass would allow us to manage carbon in a sustainable manner.
Thus, using annually renewable carbon feedstocks allows for:
In PA11, all the carbons are organic and renewable. That is unique since no others commercial performance polymers have 100% organic renewable carbons in their structure. This characteristic could be quantified and measured according to the standard ASTM D6866.
Finally, bioplastics do not only have ecological advantages (see chapter 7 for the quantification). They also help to conserve fossil raw materials and reduce our dependency on petroleum. , This opportunity should not be disgarded in times of constantly rising prices for fossil raw material even for economical reasons.
7.1 Introduction
Eco-profile assessment is a method to account for the environmental impacts associated with a product. The term “Eco-profile” indicates that all stages from resource extraction to the product are taken into account (i.e. cradle to pellet).
Eco-profile differentiates from “life cycle assessment” (LCA), in that eco-profile does not deal with the use of the product and its disposal whereas LCA does (i.e. cradle to grave).
The four phases of an eco-profile study and its methodology are defined by international standard ISO 14040 to 14043:
The inventory and the impacts environmental evaluation (Steps 2 and 3) of PA11 eco- profile were performed by Boustead Consulting that have over 35 years experience in life cycle assessment and eco-profiles and is largest generator of public inventory data. Their database and software was used for the calculations.
In particular, Boustead Consulting has calculated and put in public arena a large number of eco-profile of the main polymers for the Association of Plastics Manufacturers of Europe^7. The results of PA11 eco-profile were done with the same methodology and are presented in the same format, so that relevant comparison with the other polymers can be made.
7.2 System description and methodology
In this eco-profile, we evaluated the total amount of raw energy sources and primary raw material for 1 kg of polyamide 11 out of our Serquigny plant, as well as the total amount of air and water emission and solid wastes in this production from raw energy sources and primary raw materials.
Primary raw materials and raw energy sources are raw material and energy sources that are taken directly out of the nature. For example caustic, ammonia, diesel or electricity are not primary raw materials or primary energy sources, whereas sodium chloride, crude natural gas in the gas field, crude oil in the oil field, wind or coal are primary raw materials or primary energy sources.
The system boundary for polyamide 11 production is described in Figure 4.
production of PA-11, we have for example two co-products: glycerin and heptaldehyde. With the co-product allocation procedure, they take on part of the burden of the inputs and outputs.
The allocation has been made on a mass basis at the stage of undecylenic acid plant.
More precisely:
7.5 Impact assessment
One of the objectives of these eco-profile studies is to be able to compare different materials for a specific use on an environmental point of view.
This article focuses on two categories of impacts that have an increasing importance around the word today.
Species 20 years GWP inCO 2 equivalent
100 years GWP in CO 2 equivalent
500 years GWP in CO 2 equivalent Carbon dioxide 1 1 1
Carbon monoxide 10 3 1 Methane 62 23 7 Nitrous oxide 275 296 5200
Carbon dioxide equivalents of selected chemicals
8.1 Results of polyamide-11 ecoprofile
Total gross energy to produce 1 kg of PA11 is 161.7 MJ/kg.
Out of this total amount, Fossil fuel energy requirement (oil, gas, coal and lignite) is 111.4 MJ/kg, 9.3 MJ/Kg is provided by nuclear supply, and 41 MJ/kg is the renewable biomass energy of castor beans feedstock.
The following graph shows how much gross energy is required by each step of PA production.
18,0 (11%)
6,1 (4%)
41,0 (25%)
96,6 (60%)
0 20 40 60 80 100 120
Biomass (castor beans)
Castor cultivation and oil production
Monomer plant
Polymerisation plant
MJ / kg PA
Renewable
Graph 1: gross energy breakdown by process step
Production of 1 kg of PA11 uses 2.8 kg of CO 2 (castor seed cultivation) and generates 6.2 kg of CO 2 : net carbon dioxide air emission is 3.4 kg per kg of PA11. The global warming potential at 100 years horizon time of 1 kg PA11 is 4.2 kg CO 2 equivalents.
The following graph shows how much each step of the process emits.
109 111
123 127
132 133
155
113
162
(^121 )
137 139
207
0
25
50
75
100
125
150
175
200
Polycarbonate
PA 11 Nylon 6 PMMA
Liquid epoxy resins
PA 66 PA 12
Energy requirement (MJ / kg)
Fossil Fuel energy requirement Gross energy requirement feedstock biomass energy
Graph 3 : comparison of total energy requirement
6
3,
5,
5,9 (^) 5,
6, 5,
7,
4,
9,
7,
8,1 (^) 7,
6,
0
1
2
3
4
5
6
7
8
9
10
Polycarbonate
PA 11 Nylon 6 PMMA
Liquid epoxy resins
PA 66 PA 12
kg CO2 eq. / kg polymer
Net CO2 emission Global Warming Potential 100 year
Graph 3: comparison of greenhouse gases emissions
Arkema endorses Responsible Care®, a voluntary undertaking by the chemical industry to improve safety and the protection of health and the environment, under the aegis of the International Council of Chemical Associations (ICCA) worldwide and of the European Chemical Industry Council (CEFIC) at European level.
Reducing greenhouse gas emissions is a priority. As a major energy consumer directly concerned about carbon dioxide emissions, Arkema is continuously improving the energy efficiency of its installations. Since 1990, the baseline year for the Kyoto Protocol establishing improvement targets for industrialized nations, Arkema has cut greenhouse gas emissions by a factor of three.
In this same spirit, ARKEMA is looking forward to developing and commercializing more products with improved environmental performance. Bio-based products development is one of the four-top priorities of ARKEMA Research and Development teams.
As described in this article, one of these products, Rilsan® (Polyamide-11) contributes to sustainable development in that:
(^1) See PA11 and PA12 technical center in the OMNEXUS website : http://omnexus.com/tc/pa11- pa12/index.aspx
(^2) German IK association position paper “Bioplastics, chances and opportunities” published in January 2006
(^3) EN13432 , ASTM 6400 or GreenPla in Japan – See ADEME website for more information about biodegradable plastics : http://www2.ademe.fr/servlet/getDoc?id=11433&m=3cid=
(^4) JORA website : http://www.jora.jp/eng/
(^5) David Cadogan, ECPI, Plasttekniske Dager, “The future belongs to plastics and plastics belong to the
future”, Oslo, 8-9 November 2006
(^6) Pr. Narayan, National ACS Symposium hed in San Diego, in june 2006
(^7) Plastics Europe website : http://www.plasticseurope.org
The EcoProfile of PA11 described in this technical memo has been set up by Boustead Consulting Ltd on the basis of information collected by the authors. For any additional information plse contact: : info.rilsan@arkema.com