
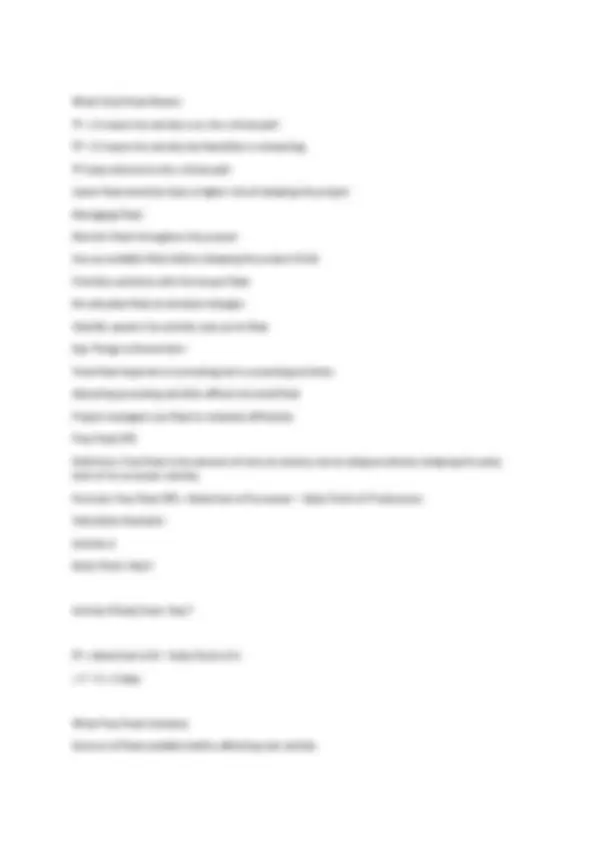
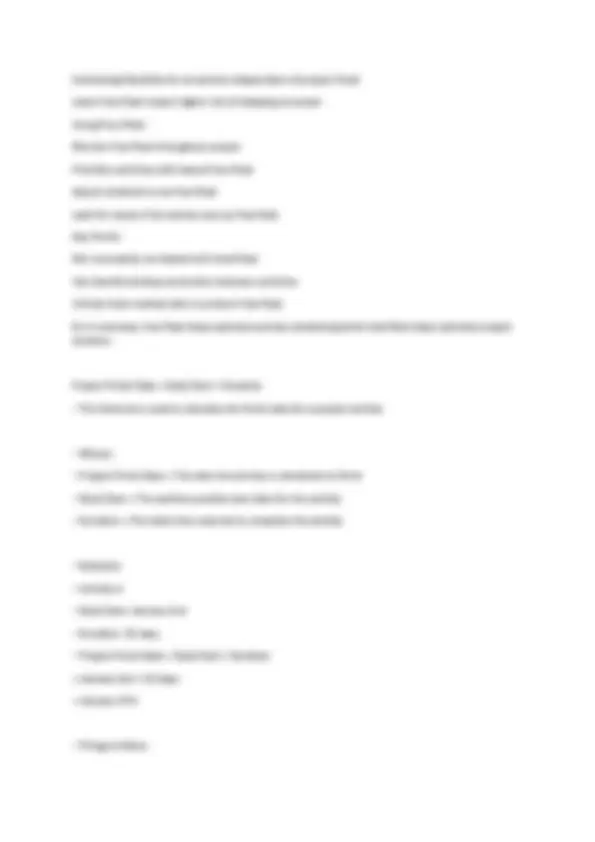
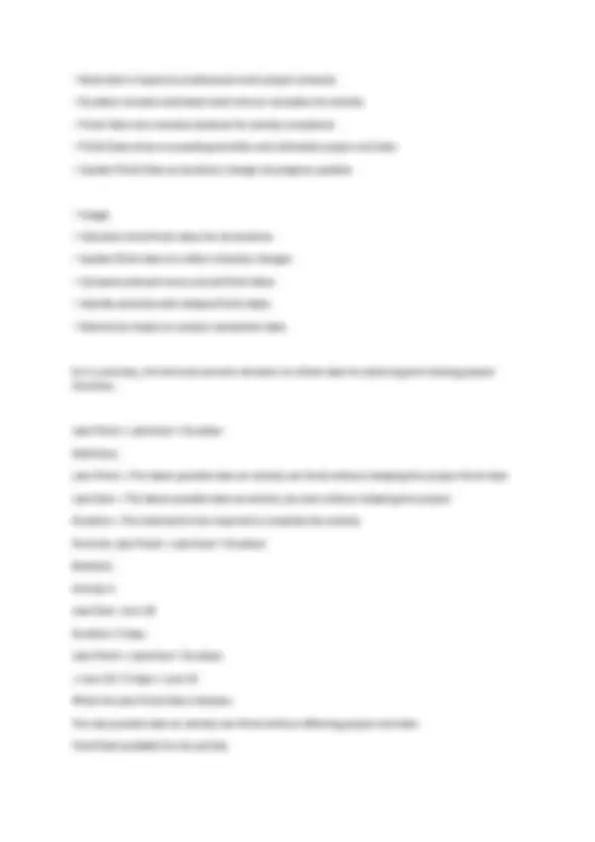
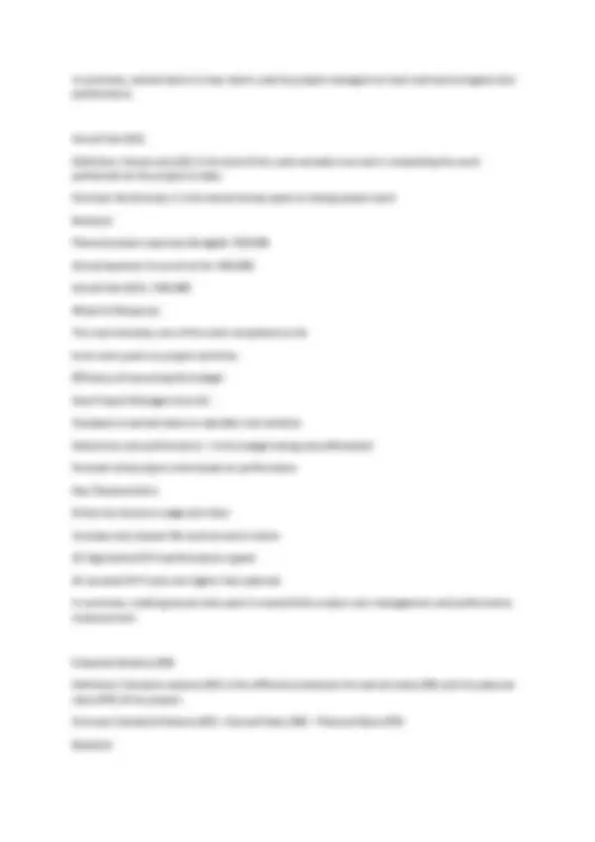
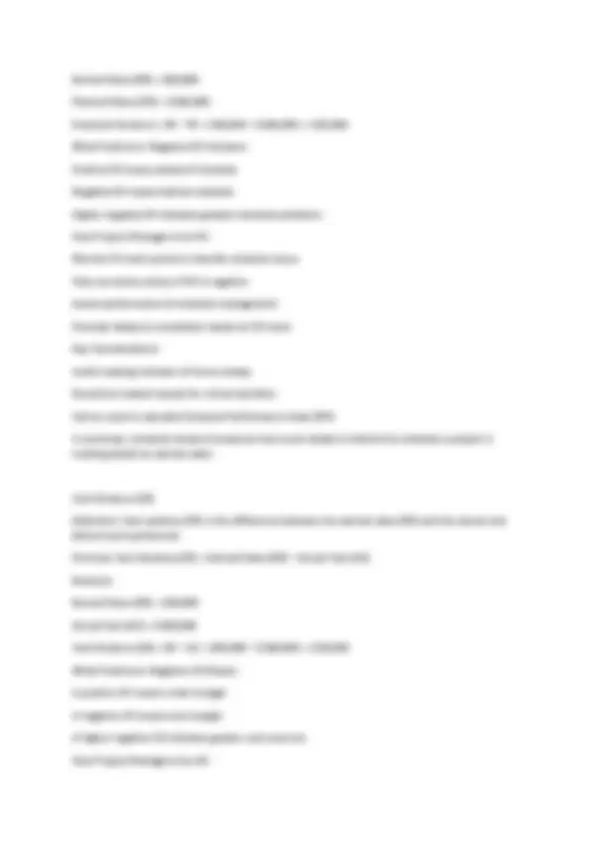
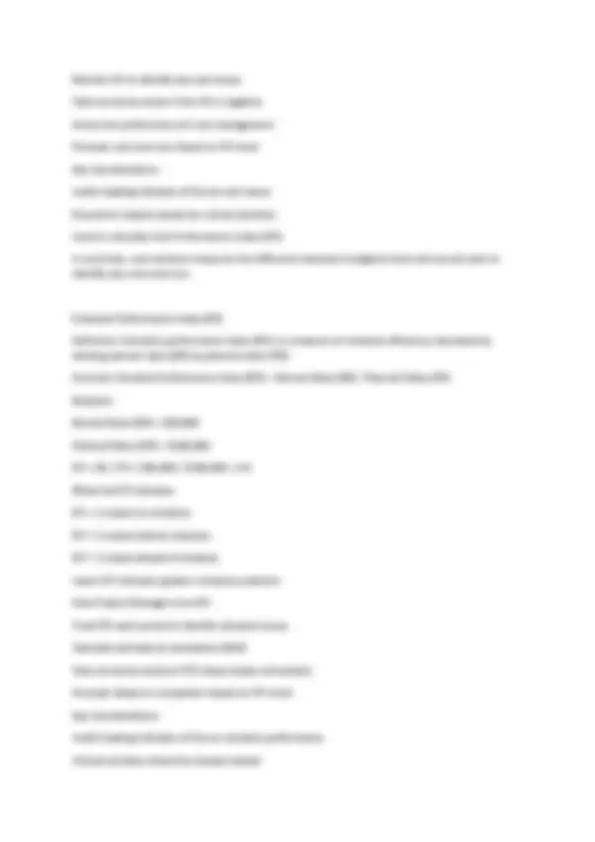
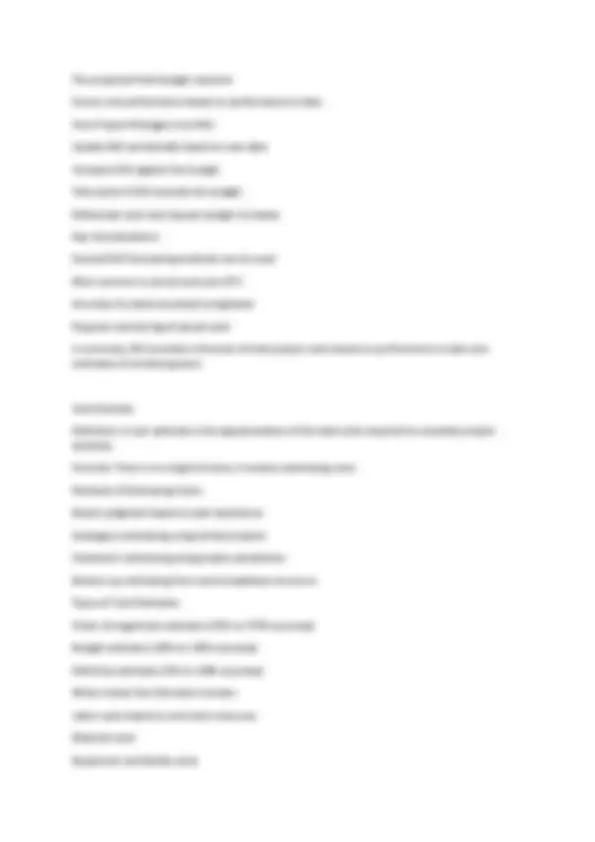
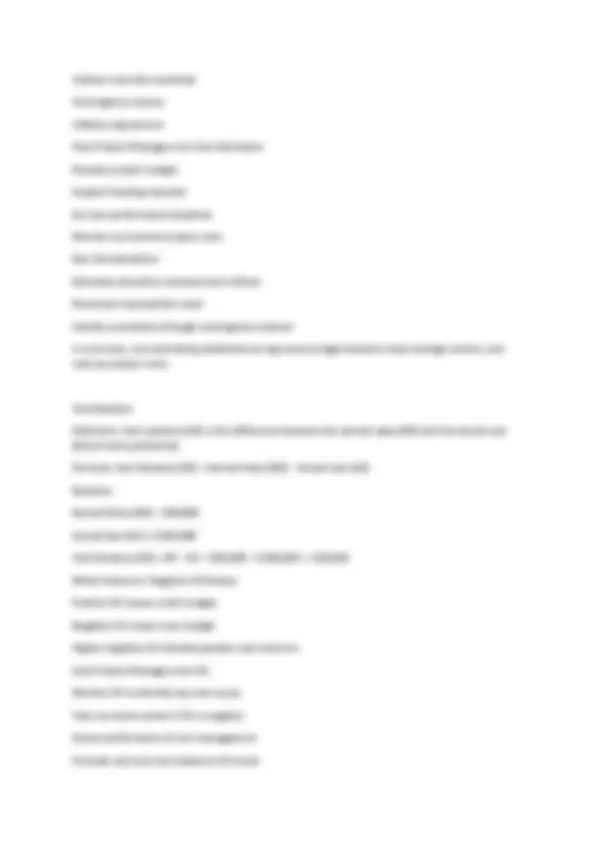
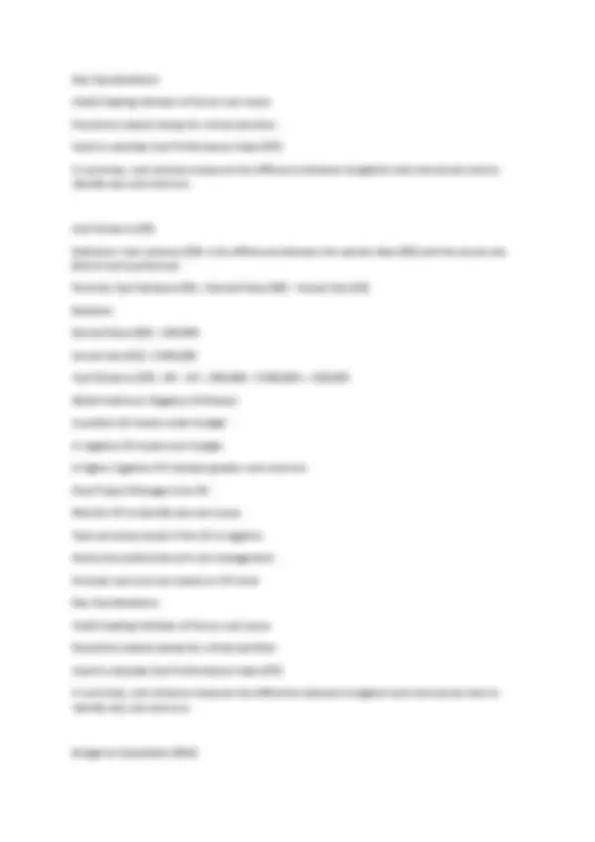
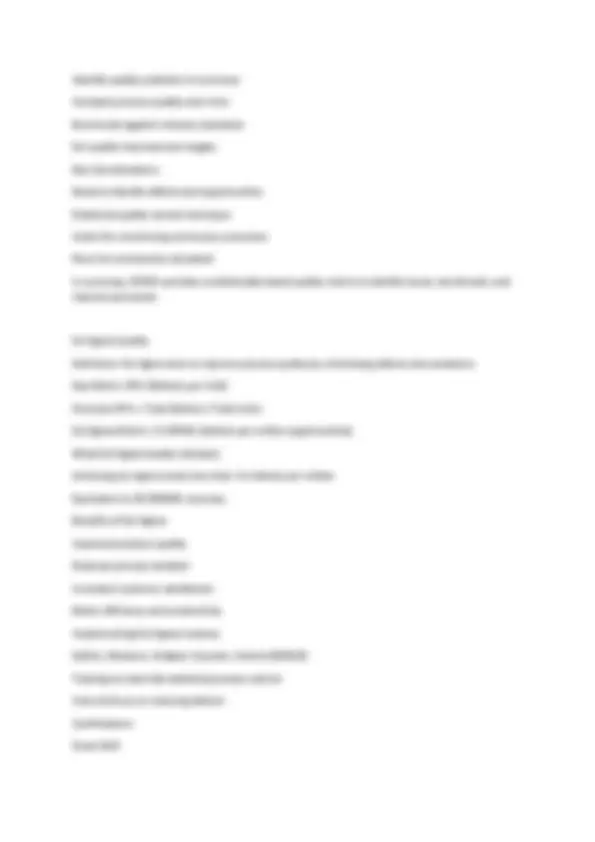
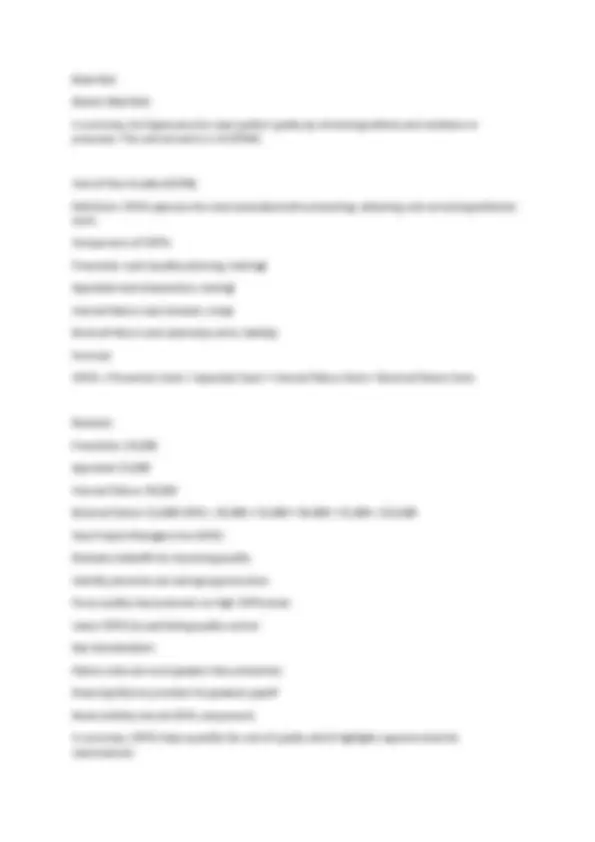
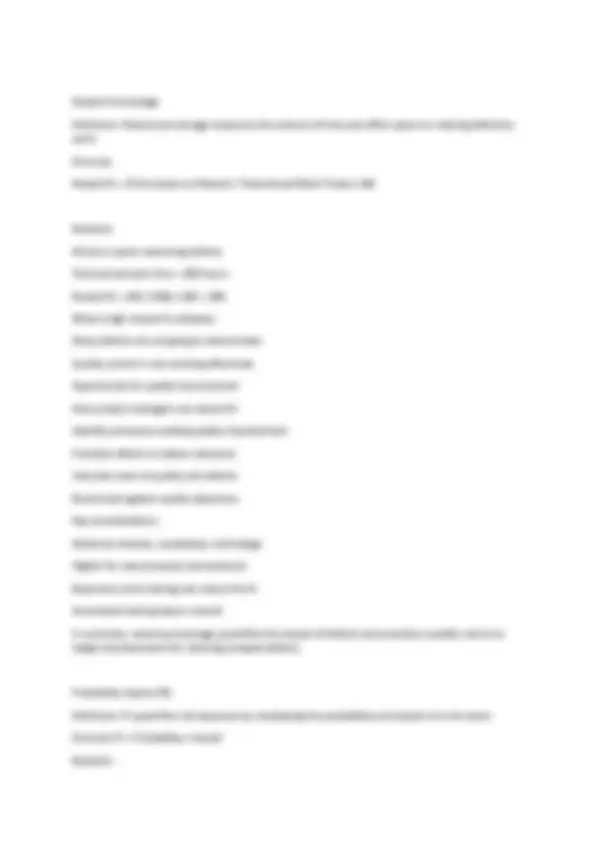
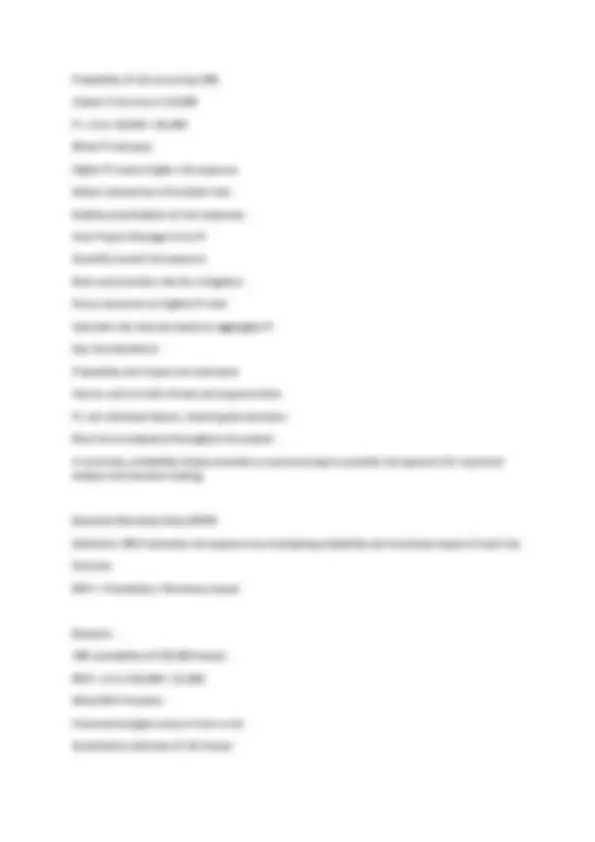
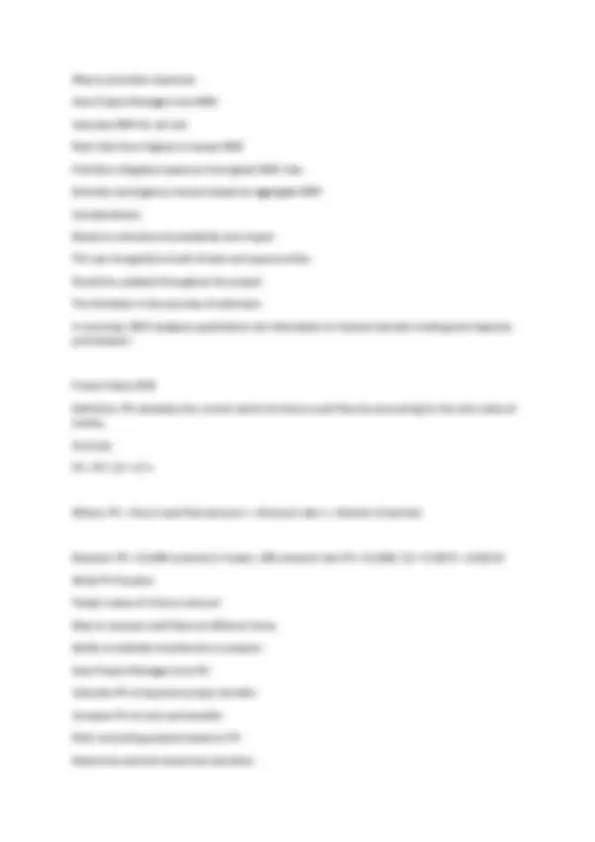
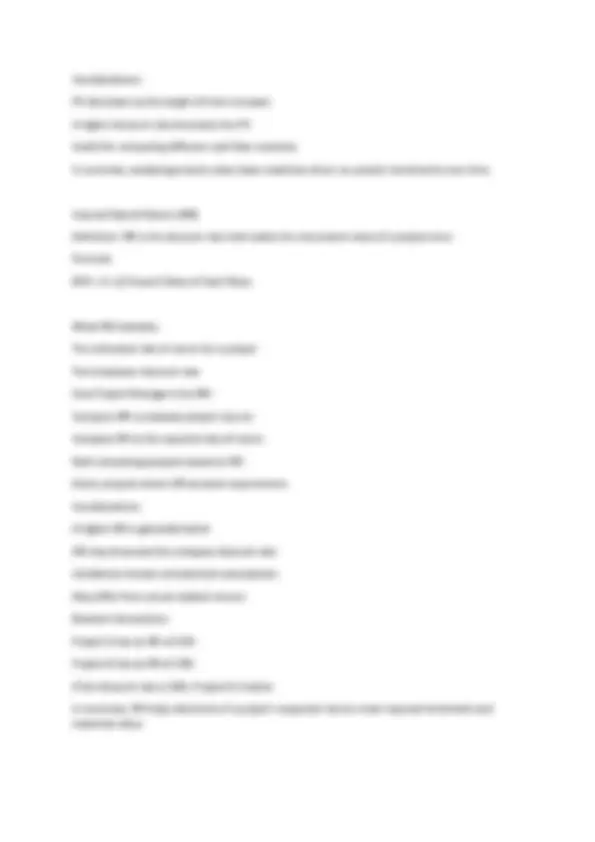
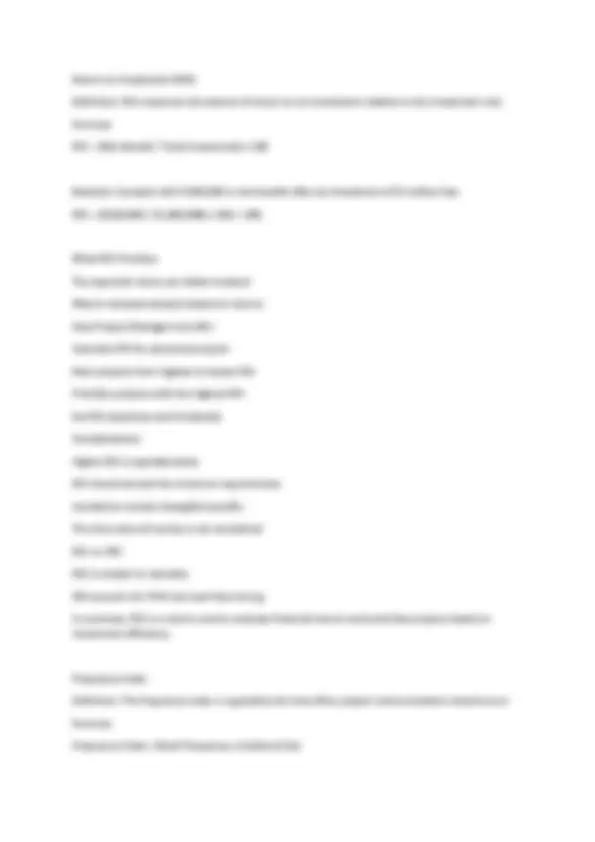
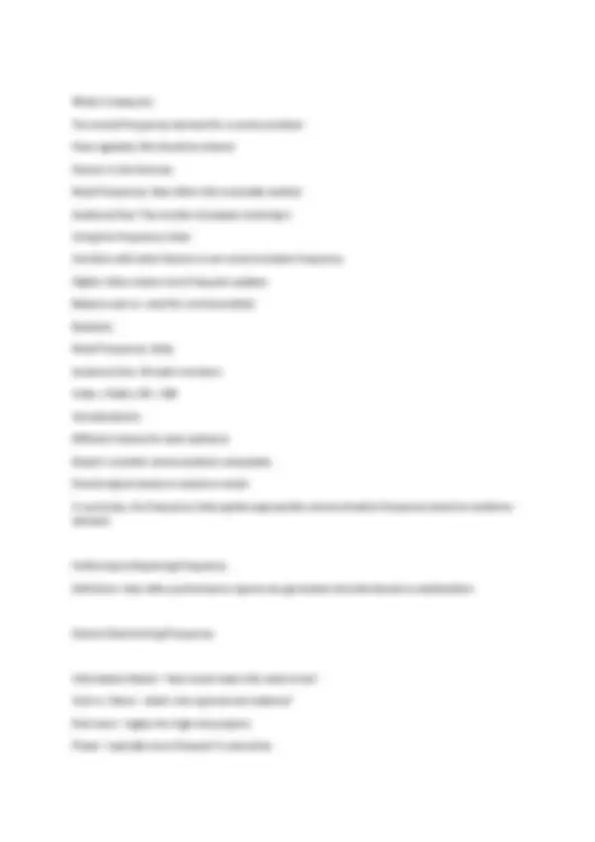
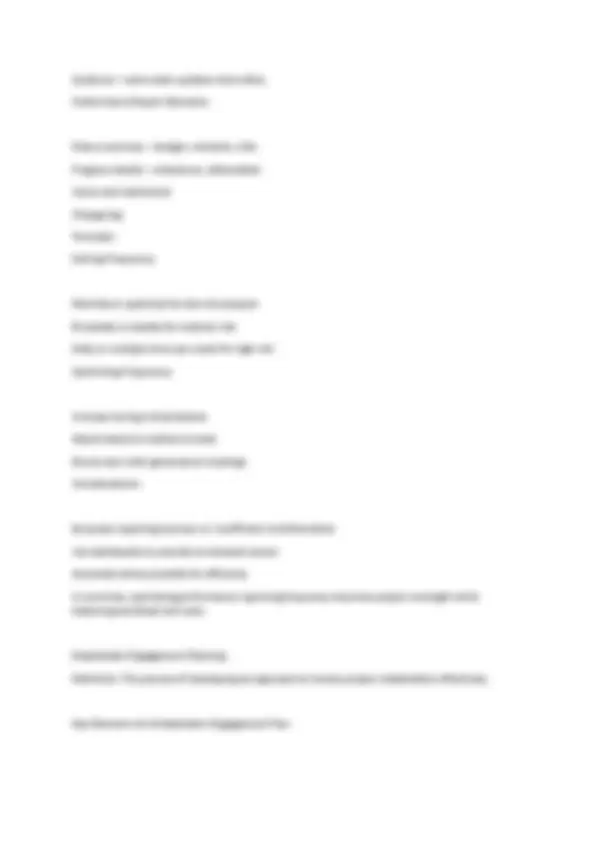
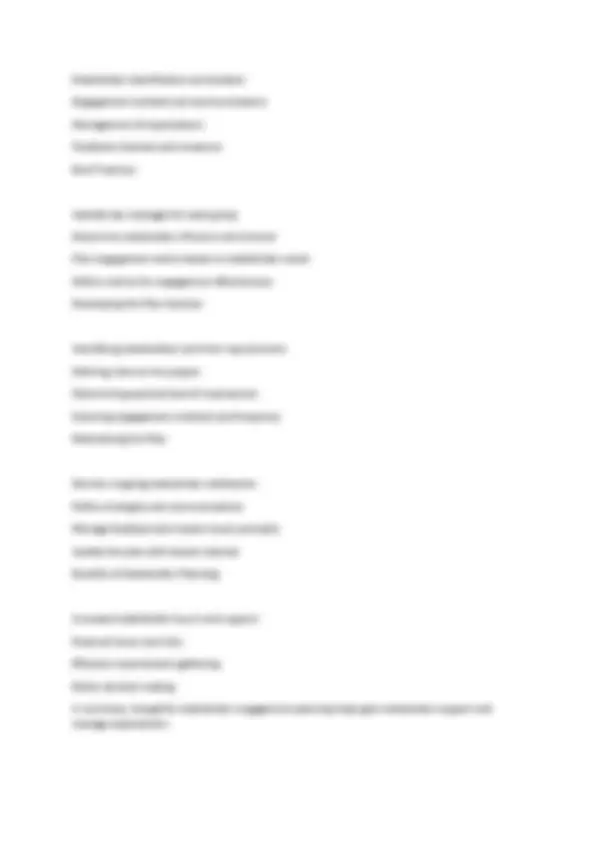
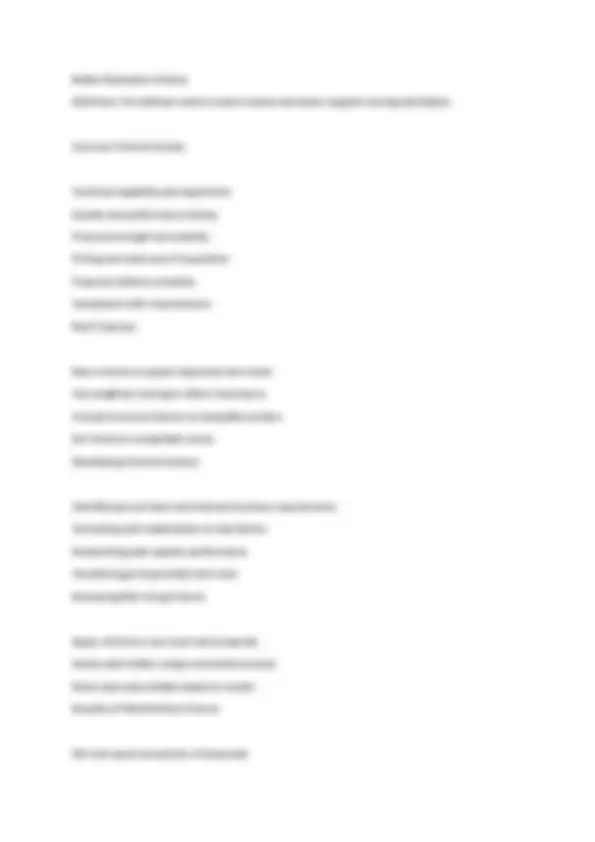
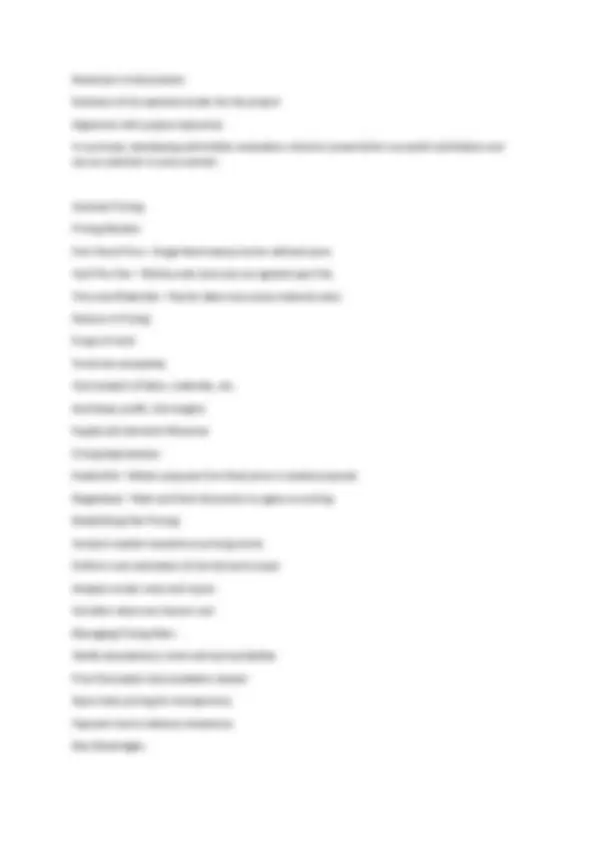
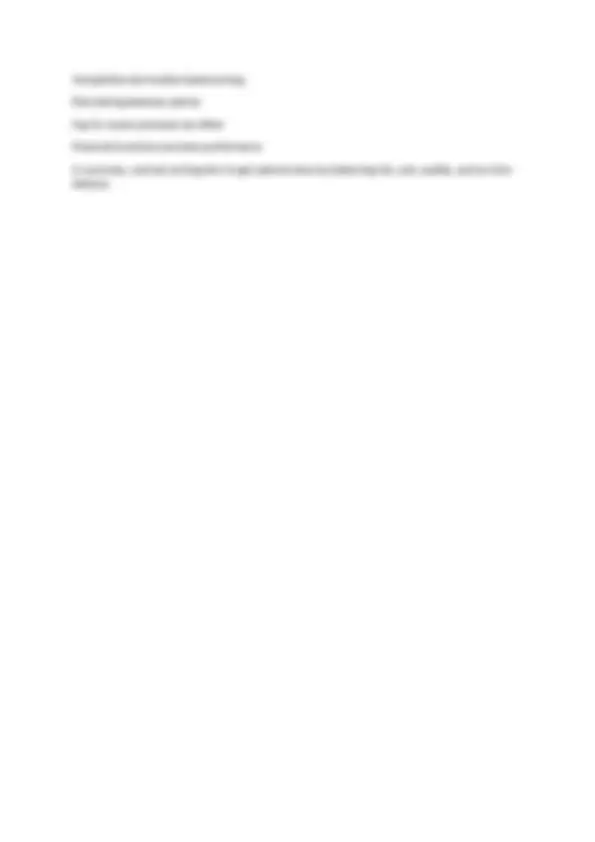
Study with the several resources on Docsity
Earn points by helping other students or get them with a premium plan
Prepare for your exams
Study with the several resources on Docsity
Earn points to download
Earn points by helping other students or get them with a premium plan
Community
Ask the community for help and clear up your study doubts
Discover the best universities in your country according to Docsity users
Free resources
Download our free guides on studying techniques, anxiety management strategies, and thesis advice from Docsity tutors
A comprehensive overview of key pmp formulas, including critical path, total float, free float, project finish date, late finish, planned value, earned value, actual cost, and schedule variance. Each formula is explained in detail with examples and key considerations for effective project management. A valuable resource for individuals preparing for the pmp certification exam.
Typology: Exams
1 / 30
This page cannot be seen from the preview
Don't miss anything!
[COMPANY NAME] [Company address]
34 PMP Formulas in Detail Critical Path (CP) Definition: The critical path is the sequence of project network activities that represents the longest path through the project. It determines the minimum time required to complete the project. How to Calculate: To find the critical path, identify all the activities in the project and create a network diagram showing the dependencies and durations. The critical path includes activities with zero total float. Add up the durations of the critical path activities to calculate the overall project duration. Formula: Critical Path = Longest sequence of activities in terms of duration Calculation Example: Activity A has a 5-day duration Activity B has a 3-day duration Activity C has a 7-day duration Activity D has a 5-day duration The network diagram shows A - > B - > C - > D as the longest path. Therefore: Critical Path = A + B + C + D = 5 + 3 + 7 + 5 = 20 days Key Things to Know: The critical path determines the shortest time to complete the project. Any delays on the critical path will delay the project. Critical path activities have zero floats. Improving estimates on the critical path can help shorten the project timeline. Re-calculating the critical path is key as the project progresses. Total Float (TF) Definition: Total float is the amount of time an activity can be delayed without delaying the overall project finish date. Formula: Total Float (TF) = Late Finish โ Early Finish Calculation Example: Activity A Early Finish: Day 5 Late Finish: Day 7 TF = Late Finish โ Early Finish = 7 โ 5 = 2 days
Scheduling flexibility for an activity independent of project finish Lower free float means higher risk of delaying successor Using Free Float: Monitor free float throughout project Prioritize activities with lowest free float Adjust schedule to use free float Look for causes if an activity uses up free float Key Points: Not necessarily correlated with total float Can identify binding constraints between activities Critical chain method aims to protect free float So in summary, free float helps optimize activity scheduling while total float helps optimize project duration. Project Finish Date = Early Start + Duration
If PV < EV, the project is ahead of schedule Key Points: PV changes over time as per planned schedule Used to calculate schedule variance (SV = EV โ PV) Delays relative to baseline appear as negative SV A key metric for tracking project performance In summary, planned value measures the budgeted work scheduled to be completed at any given point in the project. Earned Value (EV) Definition: Earned value (EV) is the measurement of the amount of work actually completed, expressed in terms of the approved budget. Formula: Earned Value (EV) = Actual % Complete x Budget at Completion (BAC) Example: BAC = $100, Actual % complete = 20% EV = 20% x $100, = $20, What EV Measures: The dollar value of work completed at a point in time Actual physical work progress on deliverables Performance relative to budget How Project Managers Use EV: Compare to planned value to determine schedule variance Compare to actual costs to determine cost variance Monitor EV over time to track budgeted work performed Key Characteristics: EV increases as work gets completed Negative EV variances indicate problems Used to forecast final project cost and completion More reliable than % complete estimates
In summary, earned value is a key metric used by project managers to track real work progress and performance. Actual Cost (AC) Definition: Actual cost (AC) is the total of the costs actually incurred in completing the work performed on the project to date. Formula: No formula, it is the actual money spent on doing project work Example: Planned project expenses (budget): $50,00 0 Actual expenses incurred so far: $40, Actual Cost (AC) = $40, What AC Measures: The real monetary cost of the work completed so far Sunk costs spent on project activities Efficiency of executing the budget How Project Managers Use AC: Compare to earned value to calculate cost variance Determine cost performance โ Is the budget being used efficiently? Forecast total project costs based on performance Key Characteristics: Driven by resource usage and rates Increase over project life cycle as work is done AC lags behind EV if performance is good AC exceeds EV if costs are higher than planned In summary, tracking actual costs spent is essential for project cost management and performance measurement. Schedule Variance (SV) Definition: Schedule variance (SV) is the difference between the earned value (EV) and the planned value (PV) of the project. Formula: Schedule Variance (SV) = Earned Value (EV) โ Planned Value (PV) Example:
Monitor CV to identify any cost issues Take corrective action if the CV is negative Assess the performance of cost management Forecast cost overruns based on CV trend Key Considerations: Useful leading indicator of future cost issues Should be tracked closely for critical activities Used to calculate Cost Performance Index (CPI) In summary, cost variance measures the difference between budgeted costs and actual costs to identify any cost overruns. Schedule Performance Index (SPI) Definition: Schedule performance index (SPI) is a measure of schedule efficiency calculated by dividing earned value (EV) by planned value (PV). Formula: Schedule Performance Index (SPI) = Earned Value (EV) / Planned Value (PV) Example: Earned Value (EV) = $80, Planned Value (PV) = $100, SPI = EV / PV = $80,000 / $100,000 = 0. What the SPI Indicates: SPI = 1 means on schedule SPI < 1 means behind schedule SPI > 1 means ahead of schedule Lower SPI indicates greater schedule problems How Project Managers Use SPI: Track SPI each period to identify schedule issues Calculate estimate at completion (EAC) Take corrective actions if SPI drops below a threshold Forecast delays to completion based on SPI trend Key Considerations: Useful leading indicator of future schedule performance Critical activities should be closely tracked
Changes in SPI indicate efficiency improvements or deterioration In summary, SPI measures schedule efficiency and provides an early warning signal of project delays. Cost Performance Index (CPI) Definition: Cost performance index (CPI) measures the cost efficiency of work completed by comparing earned value to actual costs. Formula: Cost Performance Index (CPI) = Earned Value (EV) / Actual Cost (AC) Example: Earned Value (EV) = $80, Actual Cost (AC) = $100, CPI = EV / AC = $80,000 / $100,000 = 0. What CPI Indicates: CPI > 1 means under budget CPI = 1 means on budget CPI < 1 means over budget Lower CPI indicates greater cost overruns How Project Managers Use CPI: Monitor CPI to identify any cost issues Calculate estimate at completion (EAC) Take corrective action if CPI drops below a threshold Forecast cost overruns based on CPI trend Key Considerations: Leading indicator of future cost performance Critical activities should be closely tracked Changes in CPI show efficiency improvements or deterioration In summary, CPI measures how efficiently the budget is being spent and helps forecast final project costs. Estimate to Complete (ETC) Definition: Estimate to complete (ETC) is the estimated cost required to complete the remaining project work.
The projected final budget required Future cost performance based on performance to date How Project Managers Use EAC: Update EAC periodically based on new data Compare EAC against the budget Take action if EAC exceeds the budget Reforecast costs and request budget increases Key Considerations: Several EAC forecasting methods can be used Most common is actual costs plus ETC Accuracy increases as project progresses Requires monitoring of actual costs In summary, EAC provides a forecast of total project costs based on performance to date and estimates of remaining work. Cost Estimate Definition: A cost estimate is the approximation of the total costs required to complete project activities. Formula: There is no single formula, it involves estimating costs Methods of Estimating Costs: Expert judgment based on past experience Analogous estimating using similar projects Parametric estimating using project parameters Bottom-up estimating from work breakdown structure Types of Cost Estimates: Order of magnitude estimate (-25% to +75% accuracy) Budget estimate (-10% to +25% accuracy) Definitive estimate (-5% to +10% accuracy) What a Good Cost Estimate Includes: Labor costs based on work and resources Material costs Equipment and facility costs
Indirect costs like overhead Contingency reserve Inflation adjustment How Project Managers Use Cost Estimates: Develop project budget Support funding requests Set cost performance baselines Monitor and control project costs Key Considerations: Estimates should be reviewed and refined Document assumptions used Handle uncertainty through contingency reserves In summary, cost estimating establishes an approved budget baseline helps manage control, and reduces project costs. Cost Baseline Definition: Cost variance (CV) is the difference between the earned value (EV) and the actual cost (AC) of work performed. Formula: Cost Variance (CV) = Earned Value (EV) โ Actual Cost (AC) Example: Earned Value (EV) = $80, Actual Cost (AC) = $100, Cost Variance (CV) = EV โ AC = $80,000 โ $100,000 = - $20, What Positive or Negative CV Means: Positive CV means under budget Negative CV means over budget Higher negative CV indicates greater cost overruns How Project Managers Use CV: Monitor CV to identify any cost issues Take corrective action if CV is negative Assess performance of cost management Forecast cost overruns based on CV trend
Definition: BAC is the total authorized budget for completing all work to deliver the project scope. Formula: No formula, it is the approved total budget Example: A project has the following cost estimates: Labor: $80, Materials: $50, Equipment: $20, Total budget = $80,000 + $50,000 + $20,000 = $150, Therefore, BAC = $150, What BAC Represents: The approved budget baseline Total expected costs for all project work Funding required to complete the project How Project Managers Use BAC: Compare against Earned Value to calculate variances Use as basis for performance measurement Approve changes that impact BAC Request additional funding if needed Key Points: Set at the beginning but can change Increase requires change control process Cost baselines sum to BAC at the project level Used to track cost performance In summary, the budget at completion represents the total approved budget and is a key performance measurement baseline. To-Complete Performance Index (TCPI) Definition: TCPI calculates the cost performance required on remaining work to meet the budget at completion (BAC). Formula: TCPI = (BAC โ EV) / (BAC โ AC) Example: BAC = $100,
What TCPI Indicates: The CPI needed on remaining work If less than 1, need better performance If greater than 1, cost overrun likely How Project Managers Use TCPI: Identify if major improvements in CPI are feasible Determine if the project can meet the BAC Support re-planning or requesting more funds Provide an early warning signal Key Considerations: TCPI changes as project progresses Used along with other EVM metrics Considers both past and future performance Signals unachievable economic goals In summary, TCPI compares the performance achieved versus whatโs required to meet the approved budget. Defects per Million Opportunities (DPMO) Definition: DPMO measures process performance by quantifying the number of defects per million opportunities. Formula: DPMO = Number of Defects / Opportunities for Defects x 1,000, Example: 200 defects in a process with 300,000 opportunities for defects DPMO = 200 / 300,000 x 1,000,000 = 67, What DPMO Indicates: The higher the DPMO, the poorer the quality Allows comparison across processes Shows quality deterioration or improvement over time How Project Managers Use DPMO:
Black Belt Master Black Belt In summary, Six Sigma aims for near-perfect quality by minimizing defects and variations in processes. The central metric is 3.4 DPMO. Cost of Poor Quality (COPQ) Definition: COPQ captures the costs associated with preventing, detecting, and correcting defective work. Components of COPQ: Prevention costs (quality planning, training) Appraisal costs (inspections, testing) Internal failure costs (rework, scrap) External failure costs (warranty work, liability) Formula: COPQ = Prevention Costs + Appraisal Costs + Internal Failure Costs + External Failure Costs Example: Prevention: $5, Appraisal: $3, Internal Failure: $4, External Failure: $1,000 COPQ = $5,000 + $3,000 + $4,000 + $1,000 = $13, How Project Managers Use COPQ: Evaluate tradeoffs for improving quality Identify potential cost savings opportunities Focus quality improvements on high COPQ areas Lower COPQ by optimizing quality control Key Consideration: Failure costs are much greater than prevention Reducing failures provides the greatest payoff Need visibility into all COPQ components In summary, COPQ helps quantify the cost of quality which highlights opportunities for improvement.
Rework Percentage Definition: Rework percentage measures the amount of time and effort spent on redoing defective work. Formula: Rework % = (Time Spent on Rework / Total Actual Work Time) x 100 Example: 40 hours spent reworking defects Total actual work time = 200 hours Rework % = (40 / 200) x 100 = 20% What a high rework % indicates: Many defects are escaping to downstream Quality control is not working effectively Opportunity for quality improvement How project managers use rework %: Identify processes needing quality improvement Prioritize efforts on defect reduction Calculate costs of quality and defects Benchmark against quality objectives Key considerations: Varies by industry, complexity, technology Higher for new processes and products Experience and training can reduce the % Automated testing lowers rework In summary, rework percentage quantifies the impact of defects and provides a quality metric to target improvements for reducing escaped defects. Probability Impact (PI) Definition: PI quantifies risk exposure by multiplying the probability and impact of a risk event. Formula: PI = Probability x Impact Example: