
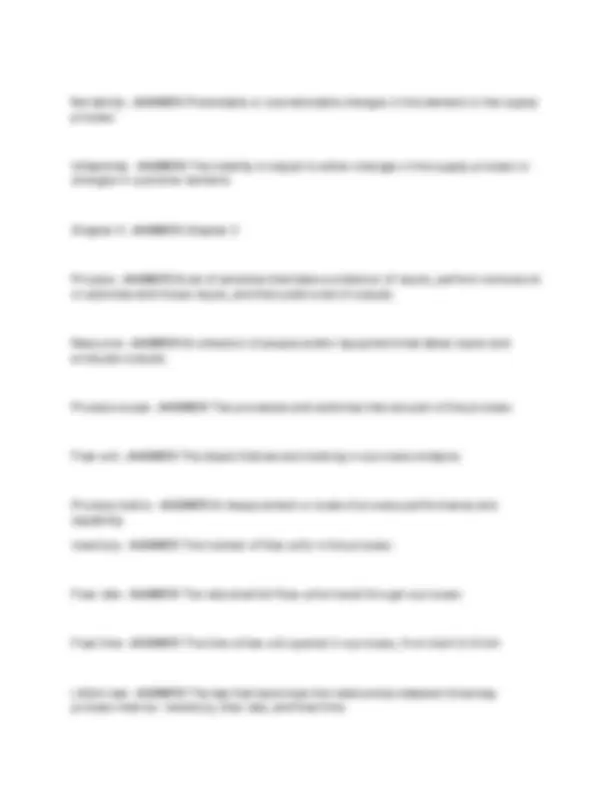
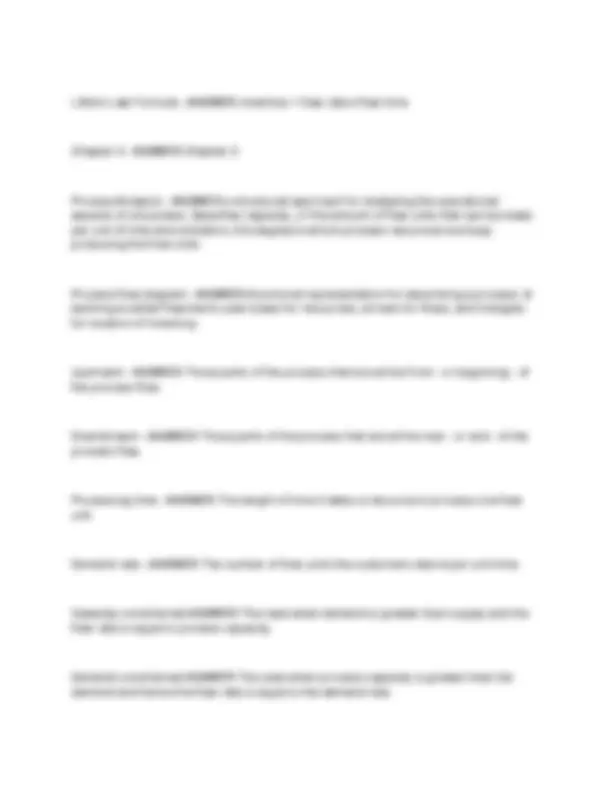
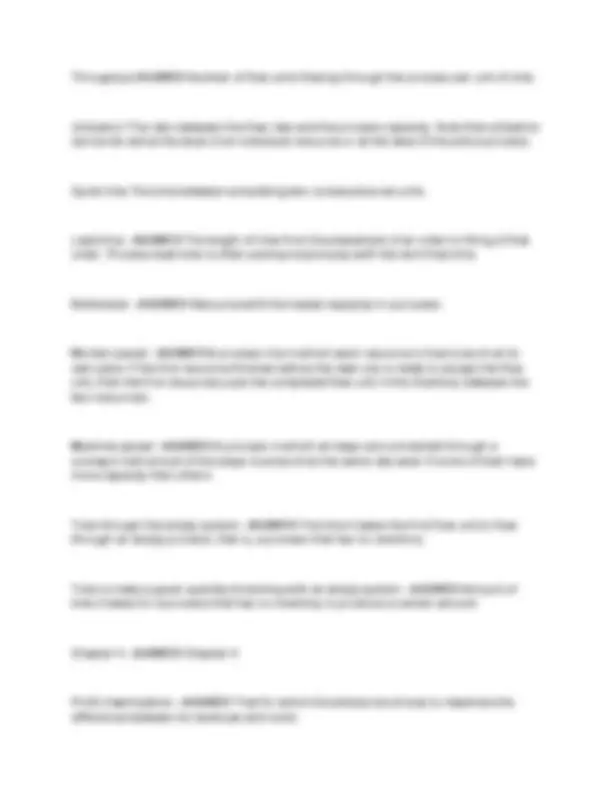
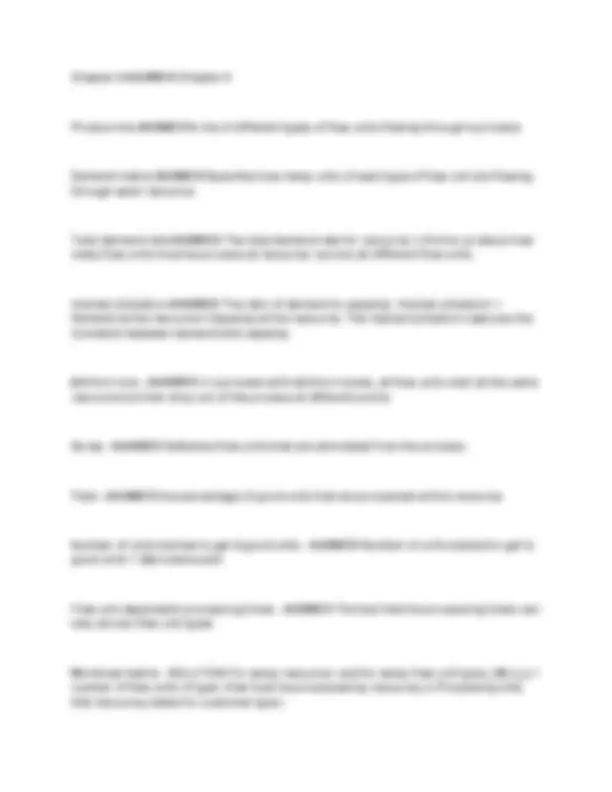
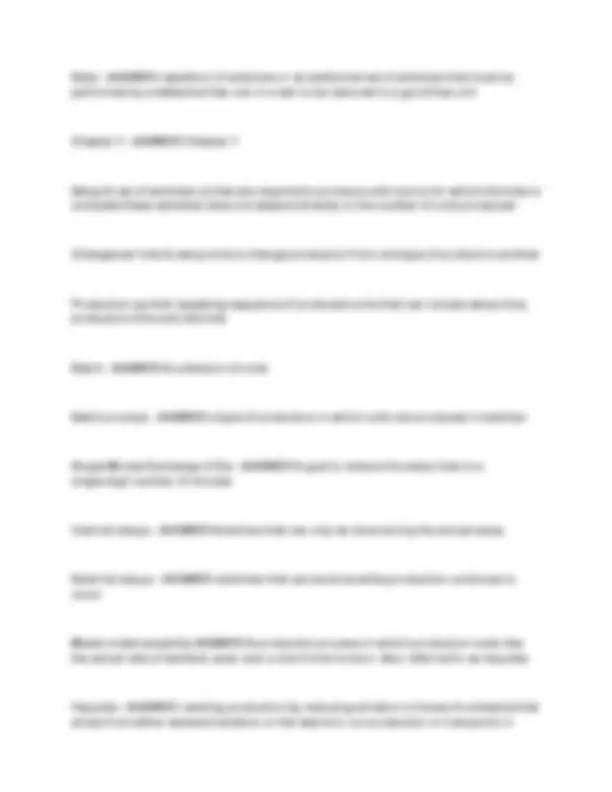
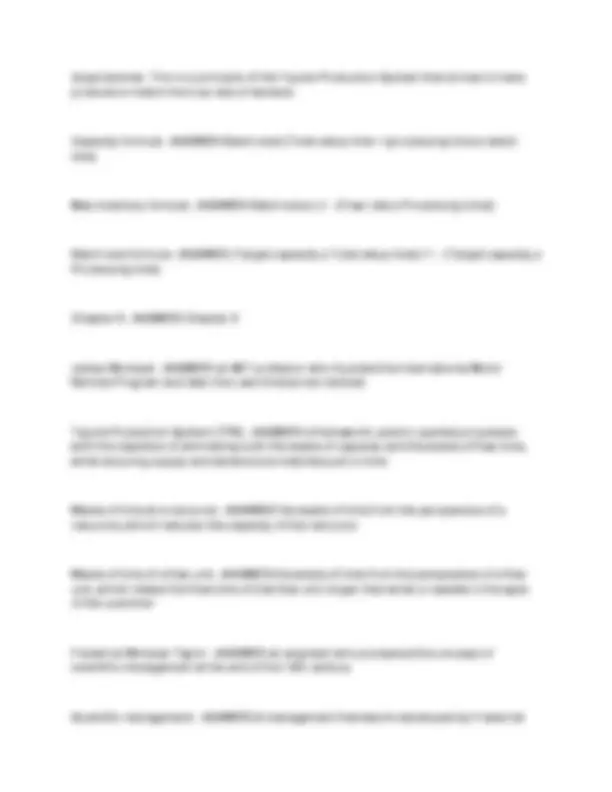
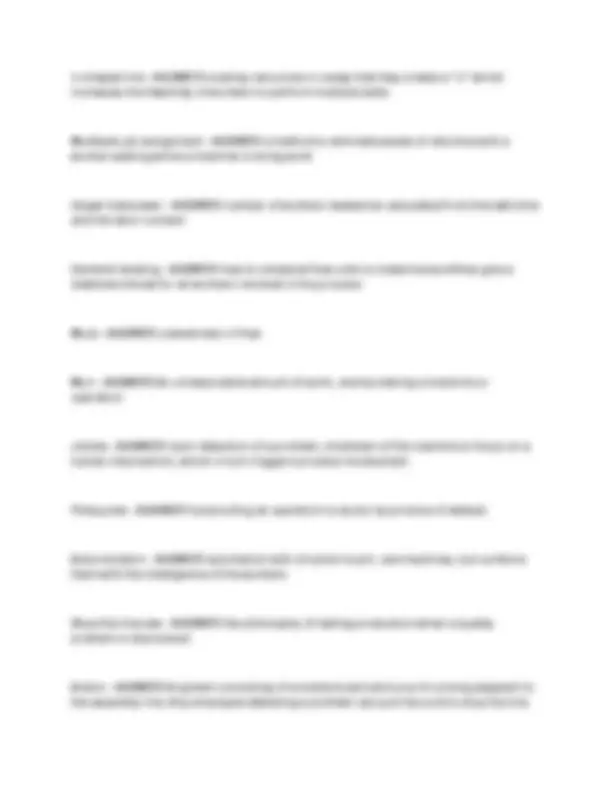
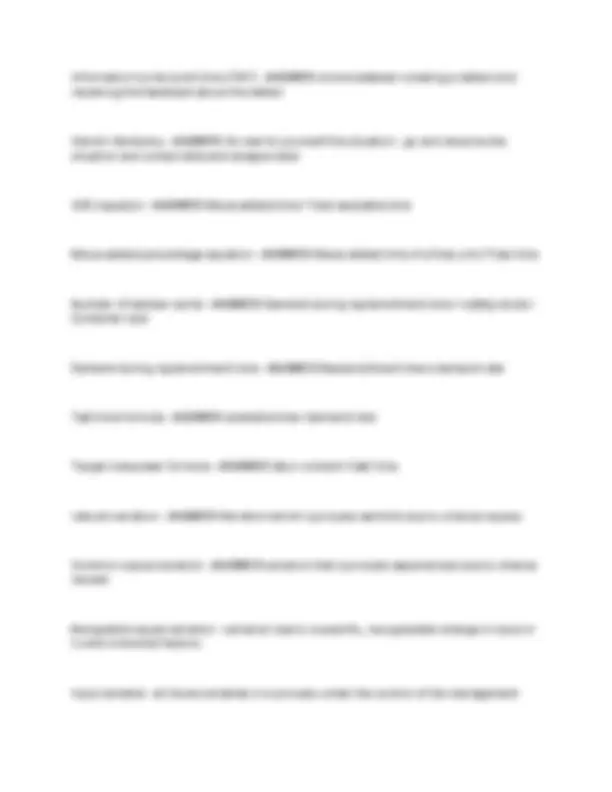
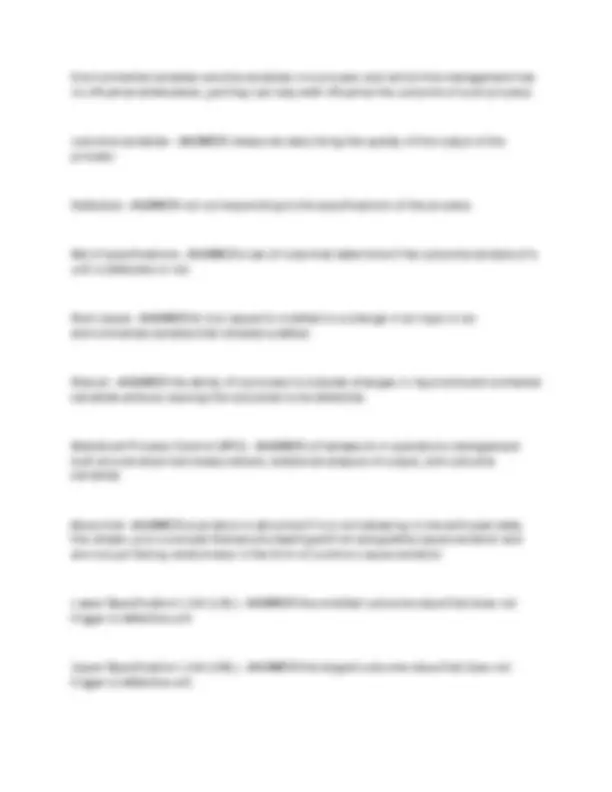
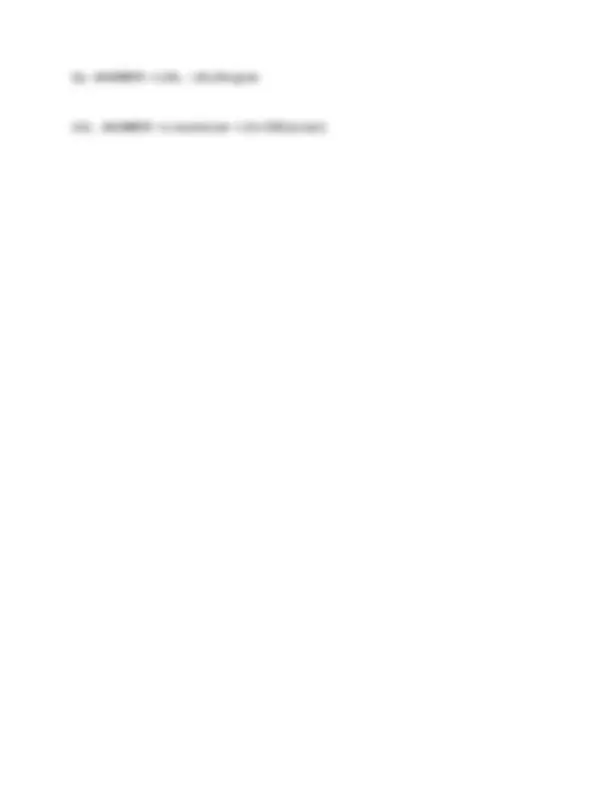
Study with the several resources on Docsity
Earn points by helping other students or get them with a premium plan
Prepare for your exams
Study with the several resources on Docsity
Earn points to download
Earn points by helping other students or get them with a premium plan
Community
Ask the community for help and clear up your study doubts
Discover the best universities in your country according to Docsity users
Free resources
Download our free guides on studying techniques, anxiety management strategies, and thesis advice from Docsity tutors
OTM 300 Midterm UW-Madison Exam With Accurate Solutions 100% Verified
Typology: Exams
1 / 18
This page cannot be seen from the preview
Don't miss anything!
Chapter 1 - Chapter 1 Supply - ANSWER Products or services a business offers to its customers Demand - ANSWER Simply, the set of products and services our customers want. Utility - ANSWER A measure of the strength of customer preferences for a given productor service. Customers buy the product or service that maximizes utility.
Consumption Utility - ANSWER A measure of how much you like a product or service,ignoring the effects of price and of the inconvenience of obtaining the product or service. Performance - ANSWER A subcomponent of the consumption utility that captures howmuch an average consumer desires a product or service.
Fit A subcomponent of the consumption utility that captures how well the product orservice matches with the unique characteristics of a given consumer.
Heterogeneous preferences The fact that not all consumers have the same utilityfunction.
Price The total cost of owning the product or receiving the service. Inconvenience - ANSWER The loss of utility that arises from the time and effort of
obtaining the product or service. Transaction costs - ANSWER A synonym for inconvenience of obtaining a product orservice.
Location - ANSWER Where the consumer can obtain a good or service. Timing - ANSWER The period of time that elapses between the consumer ordering aproduct or service and the consumer obtaining the product or service.
Marketing - ANSWER The academic discipline that is about understanding andinfluencing how customers derive utility from products or services.
Capabilities - ANSWER The dimensions of the customer's utility function a firm is able tosatisfy.
Trade-offs - ANSWER The need to sacrifice one capability in order to increase anotherone.
Market segments - ANSWER A set of customers who have similar utility functions. Pareto dominated - ANSWER A firm's product or service is inferior to one or multiplecompetitors on all dimensions of the customer utility function.
Efficient frontier - ANSWER The set of firms that are not Pareto dominated Inefficiency - ANSWER The gap between a firm and the efficient frontier. Waste - ANSWER The consumption of inputs and resources that do not add value to thecustomer.
Little's Law Formula - ANSWER inventory = flow rate x flow time Chapter 3 - ANSWER Chapter 3 Process Analysis - ANSWER a structured approach for analyzing the operationalaspects of a business. Specifies capacity, or the amount of flow units that can be made per unit of time and utilization, the degree to which process resources are busyproducing the flow units.
Process flow diagram - ANSWER A pictorial representation for describing a process. Atechnique called flowcharts uses boxes for resources, arrows for flows, and triangles for location of inventory. Upstream - ANSWER Those parts of the process that are at the front - or beginning - ofthe process flow.
Downstream - ANSWER Those parts of the process that are at the rear - or end - of theprocess flow.
Processing time - ANSWER The length of time it takes a resource to process one flowunit.
Demand rate - ANSWER The number of flow units the customers desire per unit time. Capacity-constrained ANSWER The case when demand is greater than supply and theflow rate is equal to process capacity.
Demand-constrained ANSWER The case when process capacity is greater than thedemand and hence the flow rate is equal to the demand rate.
Throughput ANSWER Number of flow units flowing through the process per unit of time. Utilization The ratio between the flow rate and the process capacity. Note that utilizationcan be de ned at the level of an individual resource or at the level of the entire process.
Cycle time The time between completing two consecutive ow units. Lead time - ANSWER The length of time from the placement of an order to filling of thatorder. Process lead time is often used synonymously with the term flow time.
Bottleneck - ANSWER Resource with the lowest capacity in a process. Worker-paced - ANSWER A process line in which each resource is free to work at itsown pace: if the first resource finishes before the next one is ready to accept the flow unit, then the first resources puts the completed flow unit in the inventory between thetwo resources.
Machine-paced - ANSWER A process in which all steps are connected through aconveyor belt and all of the steps must work at the same rate even if some of them have more capacity than others. Time through the empty system - ANSWER The time it takes the first flow unit to flowthrough an empty process; that is, a process that has no inventory.
Time to make a given quantity X starting with an empty system - ANSWER Amount oftime it takes for a process that has no inventory to produce a certain amount
Chapter 4 - ANSWER Chapter 4 Profit maximization - ANSWER That for which the enterprise strives to maximize thedifference between its revenues and costs.
specialization increases efficiency by elimination setups Reduction of processing times due to learning - ANSWER the fact that specializationincreases efficiency by providing more practice to the operator in the execution of a particular activity Lower-skilled labor - ANSWER labor that is not able to master multiple activities andthus can only work as a resource with very short processing times
Equipment replication The necessity to provide additional equipment to nonspecializedlabor at resources often results in a low level of equipment utilization.
Work cells An organization of work where small teams of employees perform a job,complete a flow unit, from beginning to end
Fixed costs Those costs that a firm has to pay anyway, independent of how much itproduces and sells.
Variable costs - ANSWER Those costs that increase in direct proportion to the quantity afirm produces and sells.
Gross margin - ANSWER The ratio of profits to revenues Profits equation - ANSWER flow rate x (Average price - Average cost) Costs of direct labor equation - ANSWER Wages per unit of time / Flow rate takt time equation - ANSWER available time / required quantity Average labor utilization formula ANSWER Labor content / Labor content + Idle time
Chapter 5 ANSWER Chapter 5 Product mix ANSWER A mix of different types of flow units flowing through a process Demand matrix ANSWER Specifies how many units of each type of flow unit are flowingthrough each resource.
Total demand rate-ANSWER The total demand rate for resource i informs us about howmany flow units must be process at resource i across all different flow units.
Implied Utilization-ANSWER The ratio of demand to capacity: Implied utilization =Demand at the resource / Capacity at the resource. The implied utilization captures the mismatch between demand and capacity. Attrition loss - ANSWER In a process with attrition losses, all flow units start at the sameresource but then drop out of the process at different points.
Scrap - ANSWER Defective flow units that are eliminated from the process. Yield - ANSWER the percentage of good units that are processed at this resource Number of units started to get Q good units - ANSWER Number of units started to get Qgood units = Q/process yield
Flow unit-dependent processing times - ANSWER The fact that the processing times canvary across flow unit types
Workload matrix - SOLUTION For every resource i and for every flow unit type j, WL(i,j) =number of flow units of type i that must be processed by resource j x Processing time that resource j takes for customer type i.
large batches. This is a principle of the Toyota Production System that strives to haveproduction match the true rate of demand.
Capacity formula - ANSWER Batch size/ (Total setup time + (processing time x batchsize)
Max inventory formula - ANSWER Batch size x (1 - (Flow rate x Processing time)) Batch size formula - ANSWER (Target capacity x Total setup time) / 1 - (Target capacity xProcessing time)
Chapter 8 - ANSWER Chapter 8 James Womack - ANSWER an MIT professor who founded the International MotorVehicle Program and later the Lean Enterprise Institute
Toyota Production System (TPS) - ANSWER a framework used to operate processeswith the objective of eliminating both the waste of capacity and the waste of flow time, while ensuring supply and demand are matched just in time Waste of time at a resource - ANSWER the waste of time from the perspective of aresource, which reduces the capacity of the resource
Waste of time of a flow unit - ANSWER the waste of time from the perspective of a flowunit, which makes the flow time of that flow unit longer than what is needed in the eyes of the customer Frederick Winslow Taylor - ANSWER an engineer who pioneered the concept ofscientific management at the end of the 19th century
Scientific management - ANSWER A management framework developed by Frederick
Winslow Taylor that focuses on efficiency and optimization Taiichi Ohno - ANSWER an engineer who developed the Toyota Production System,which is based on waste reduction principles
Non-value-added work - ANSWER Those activities that do not add value in the eyes ofthe customer but must be performed given the existing constraints of the process to make a unit Value-added work - ANSWER Those operations valued by the customer because theyare absolutely required to transform the flow unit from its inputs to being the output the customer wants. Total available time - ANSWER the amount of time a resource has available to fulfilldemand
Overall equipment effectiveness - ANSWER the percentage of the total available timethat is used in a way that adds value to the customer
Kaizen - ANS the process of making small changes to the process with the goal ofeliminating waste.
Seven sources of production waste - ANS waiting, overproduction, inventory, transport,overprocessing, rework, and unnecessary motions
Just-in-time - ANS Supplying a unit of demand when and where it is needed, thusavoiding unnecessary inventory
Value-added percentage - ANS the percentage of flow time used for value-added work 4Ps of Toyota - ANSWER business principles espoused by Toyota that are comprised of
U-shaped line - ANSWER locating resources in a way that they create a "U" whichincreases the flexibility of workers to perform multiple tasks
Mulittask job assignment - ANSWER a method to eliminate waste of idle time with aworker waiting while a machine is doing work
target manpower - ANSWER number of workers needed as calculated from the takt timeand the labor content
Demand leveling - ANSWER how to schedule flow units to make the workflow give astable workload for all workers involved in the process
Mura - ANSWER unevenness in flow Muri - ANSWER An unreasonable amount of work, overburdening a machine oroperation
Jidoka - ANSWER Upon detection of a problem, shutdown of the machine to focus on ahuman intervention, which in turn triggers process involvement.
Poka-yoke - ANSWER foolproofing an operation to avoid recurrence of defects Autonomation - ANSWER automation with a human touch; use machines, but combinethem with the intelligence of the workers
Stop-the-line-see - ANSWER the philosophy of halting production when a qualityproblem is discovered
Andon - ANSWER A system consisting of a visible board and a cord running adjacent tothe assembly line. Any employee detecting a problem can pull the cord to stop the line.
Information turnaround time (ITAT) - ANSWER a time between creating a defect andreceiving the feedback about the defect
Genchi Genbutsu - ANSWER Go see for yourself the situation - go and observe thesituation and collect data and analyze data
OEE equation - ANSWER Value-added time / Total available time Value-added percentage equation - ANSWER Value-added time of a flow unit / Flow time Number of kanban cards - ANSWER Demand during replenishment time + safety stock /Container size
Demand during replenishment time - ANSWER Replenishment time x demand rate Takt time formula - ANSWER available time / demand rate Target manpower formula - ANSWER labor content / takt time natural variation - ANSWER Variation which a process exhibits due to chance causes Common cause variation - ANSWER variation that a process experiences due to chancecauses
Assignable cause variation - variation due to a specific, recognizable change in input orin environmental factors.
Input variable - all those variables in a process under the control of the management
Process capability index - ANSWER The ratio between the width of the specificationinterval of the outcome variable and the variation of the outcome variable. Tells us how many standard deviations we can move away from the statistical mean before causing adefect
Six-sigma program - ANSWER a process that has 6 standard deviation on either side ofthe mean and the specification limit
Defect probability - ANSWER the statistical probability with which a randomly chosenflow unit does not meet specifications
Parts per million - ANSWER the expected number of defective parts in a random sampleof one million
Target variationgiven defect probability the biggest amount of variation in a process that does not exceed a
control chartsoutcome variable on y - axis. Also has long run center line, which is average across all visual representation of variation in the process. Time on x - axis and an points. Also has UCL and LCL. X-bar charts - ANSWER a special control chart in which we track the mean of a sample X - bar - ANSWER the average of a sample Lower Control Limit (LCL) - ANSWER a line in a control chart that provides the smallestvalue that is still acceptable without being labeled an abnormal variation
Upper Control Limit (UCL) - ANSWER A line in a control chart that provides the largestvalue that is still acceptable without being labeled an abnormal variation.
x double bar - ANSWER the average of a set of sample averages Estimated standard deviation of all parts - ANSWER the standard deviation that iscomputed across all parts
Estimated standard deviation for X-bar - ANSWER the standard deviation of an individualsample mean, x-bar
Fishbone diagram - ANSWER A structured brainstorming tool used to help animprovement team list possible causes of a specific effect.
Five Whys - ANSWER A brainstorming technique that helps employees to find the rootcause of a problem. In order to avoid stopping too early and not having found the real root cause employees are encouraged to ask, "Why did this happen?" at least five times Pareto diagram - ANSWER A graphical way to identify the most important causes ofprocess defects
robust process - ANSWER a process that is robust can tolerate variation in inputvariables and environmental variable without leading to a defect
Event tree - ANSWER A graphical representation of yes/no outcome variables. It aids thedefect probability calculations by linking the defects in the process with an overall outcome measure. p-chart - ANSWER a type of control chart for attributes that is employed to monitorsample proportions
Attribute-based control chart - ANSWER Special control chart for dealing with binaryoutcomes