
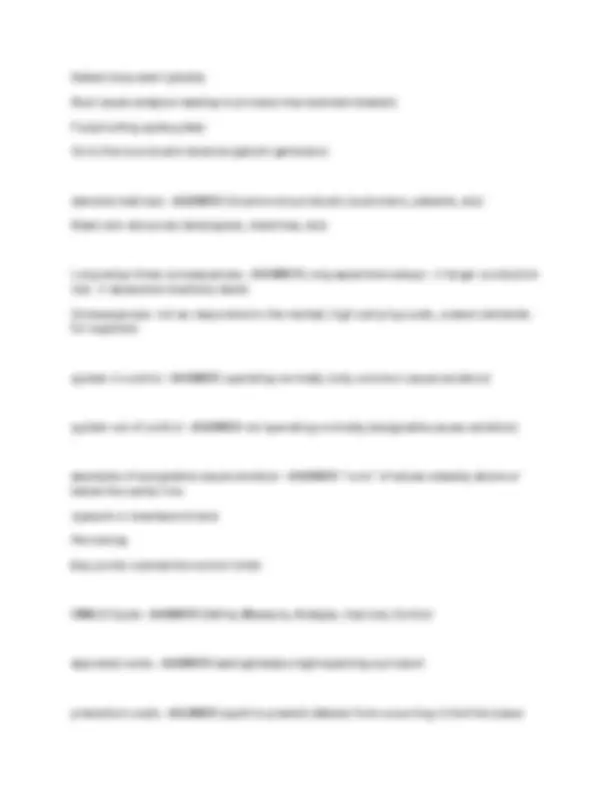
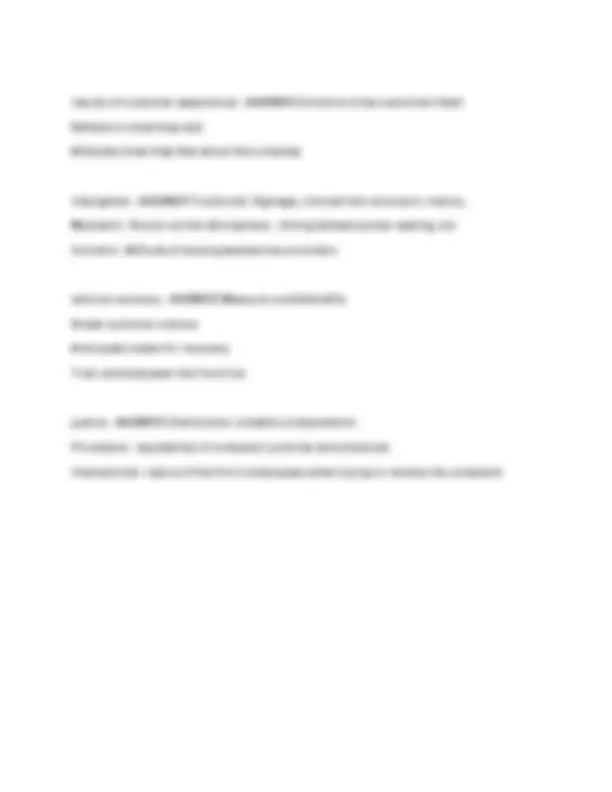
Study with the several resources on Docsity
Earn points by helping other students or get them with a premium plan
Prepare for your exams
Study with the several resources on Docsity
Earn points to download
Earn points by helping other students or get them with a premium plan
Community
Ask the community for help and clear up your study doubts
Discover the best universities in your country according to Docsity users
Free resources
Download our free guides on studying techniques, anxiety management strategies, and thesis advice from Docsity tutors
OTM 300 Exam 1 With Complete Solutions 100% Verified Latest Update
Typology: Exams
1 / 4
This page cannot be seen from the preview
Don't miss anything!
what drives consumption utility - ANSWER Performance ex: high quality grilled burger vs frozen patty Fit ex: vegetarians don't eat meat
three system inhibitors - ANSWER 1. Waste
three key process metrics - ANSWER inventory, flow rate, flow time
types of waste - ANSWER Waste of time of a resource: capacity is wasted because of idle time, also wasted by performing what we will define as waste and non-value-adding work Waste of time of a flow unit: Inventory = Flow rate x Flow time; shorter flow time is directly proportional to less inventory taylorism - ANSWER scientific management, encouraged the development of mass production techniques and the assembly line, led to a revolution in American education of social science.
two types of work - ANSWER Non-value-added work: movements that do not add value in the eyes of the customer but must be done under current process conditions to complete a unit (ex: worker moving between machines) Value-added work: movements valued by the customer as they are absolutely required to transform the flow unit into the output the customer wants
toyota's four principles - ANSWER Philosophy: a long term approach that favors quality and capabilities over short-term financial goals
Processes: continuous process flows that match supply with demand, aiming to reduce waste of flow time and capacity People and partners: respectful interactions with employees and partners emphasizing skill development and growth Problem solving: ongoing improvement of operations leveraging the experience of the front-line employees
single-unit flow - ANSWER operate at a flow of one unit at a time from one resource to the next rather than operating based on transfer batches
offloading the bottleneck (strategies) - ANSWER Line Balancing: reassigning activities to other resources that have more capacity Automating some of the activities consuming time at the bottleneck by using technology Outsourcing some of the activities consuming time at the bottleneck
natural variation - ANSWER variation occurring in a process due to pure randomness (aka common cause variation) ex: Never able to perfectly replicate signature 1,000 times
assignable cause variation - ANSWER variation arising due to a specific change in input or in environmental variables ex: Someone bumps your elbow while writing
key innovations for work flow - ANSWER Specialization of labor Moving assembly line
Toyota's 7 Wastes - ANSWER Overproduction, waiting time, material movement, inventory, over processing, worker movement, defective products
built-in-quality - ANSWER Workers responsible for quality
results of customer experience - ANSWER Emotions (how customers feel) Behaviors (how they act) Attitudes (how they feel about the company
intangibles - ANSWER Functional: Signage, line barriers at airport, menus, Mechanic: Round out the atmosphere ; dining tables/counter seating, tvs Humanic: Attitude of employees/service providers
service recovery - ANSWER Measure costs/benefits Break customer silence Anticipate needs for recovery Train and empower the front line
justice - ANSWER Distributive: suitable compensation Procedure : equitability of company's policies and practices Interactional: nature of the firm's employees when trying to resolve the complaint