
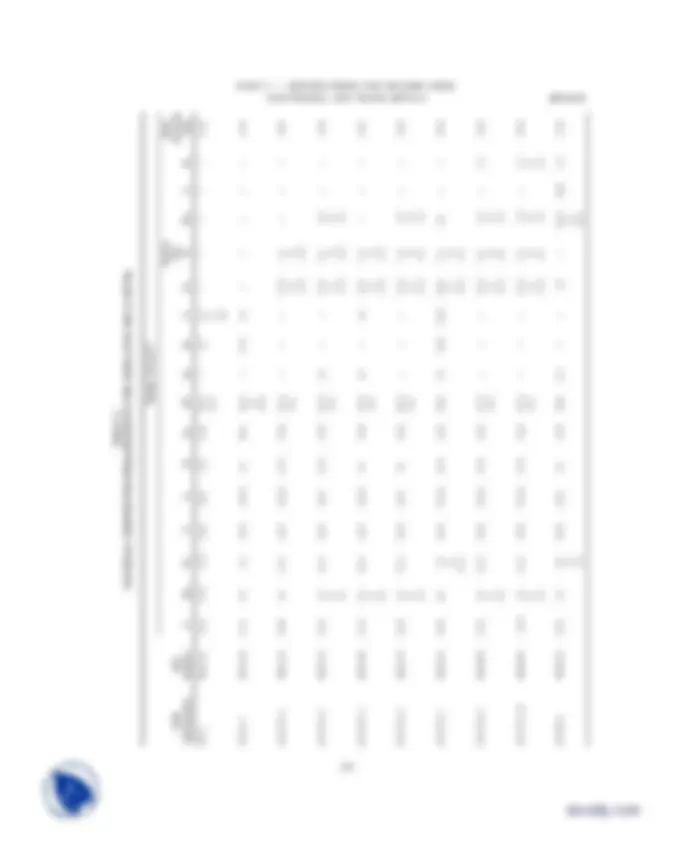
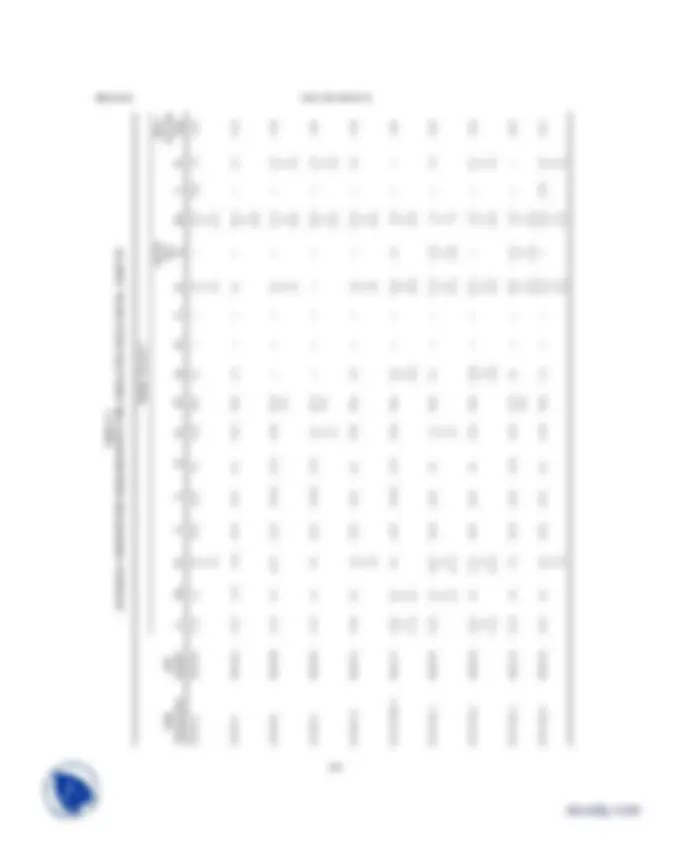

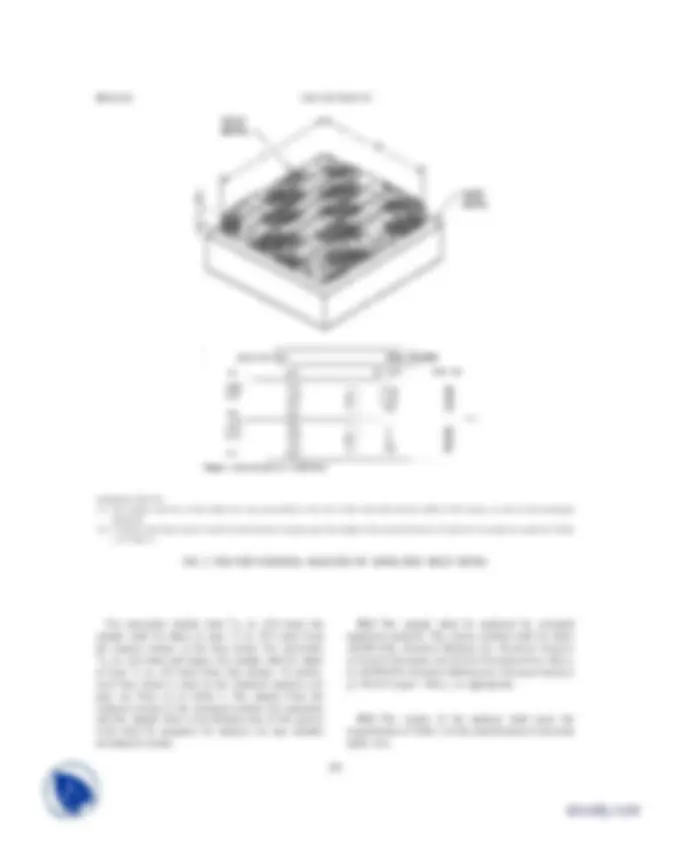
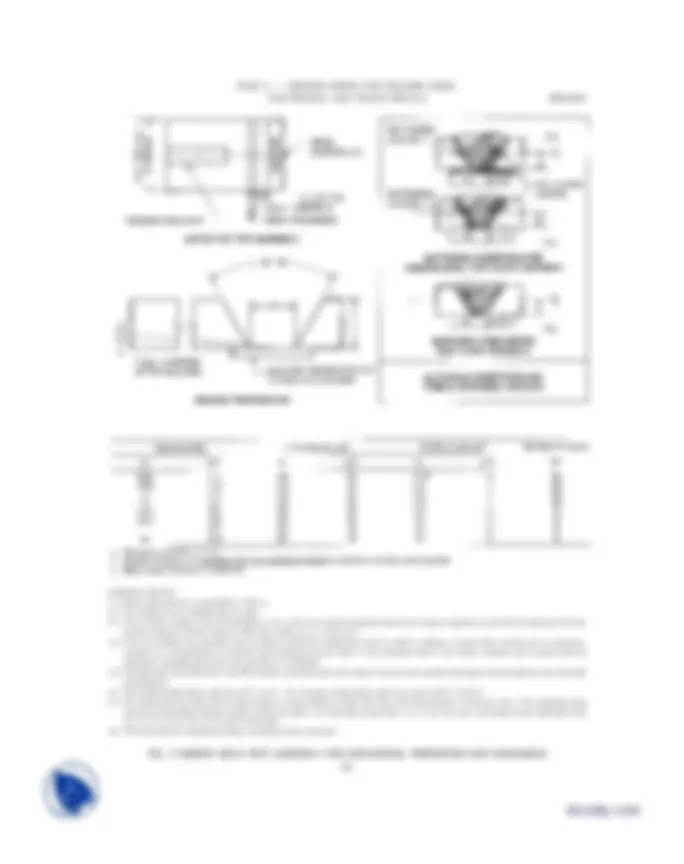
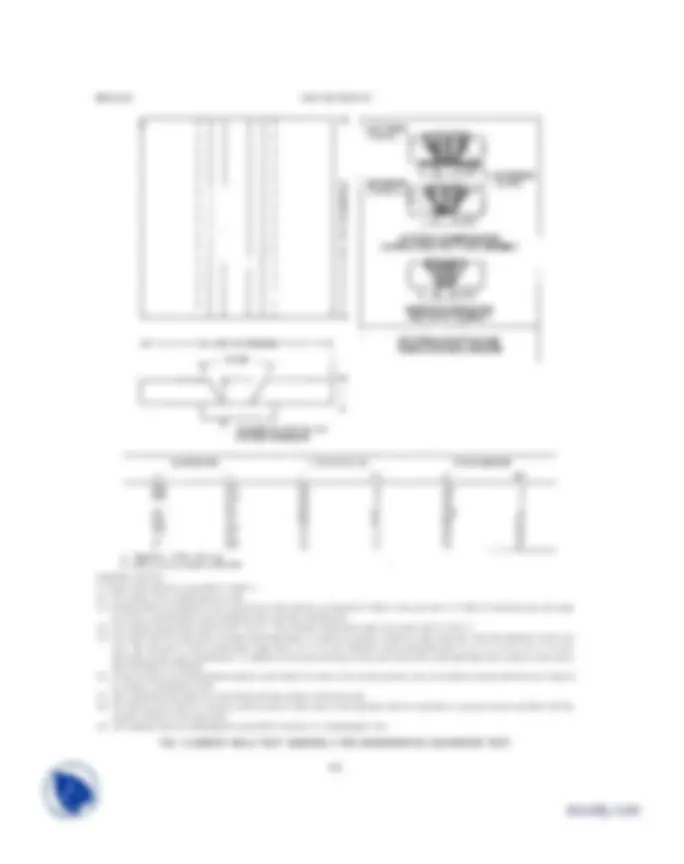
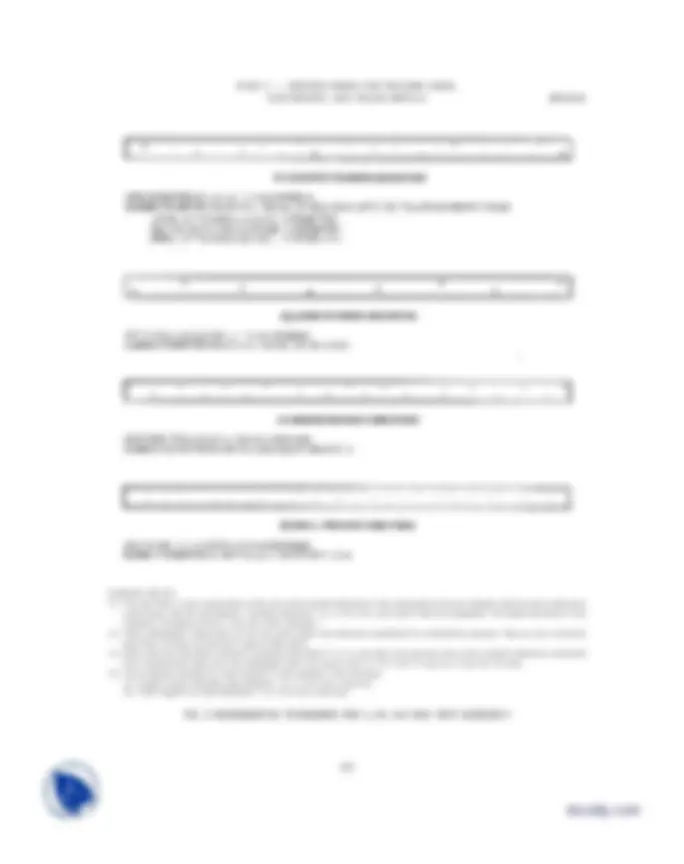
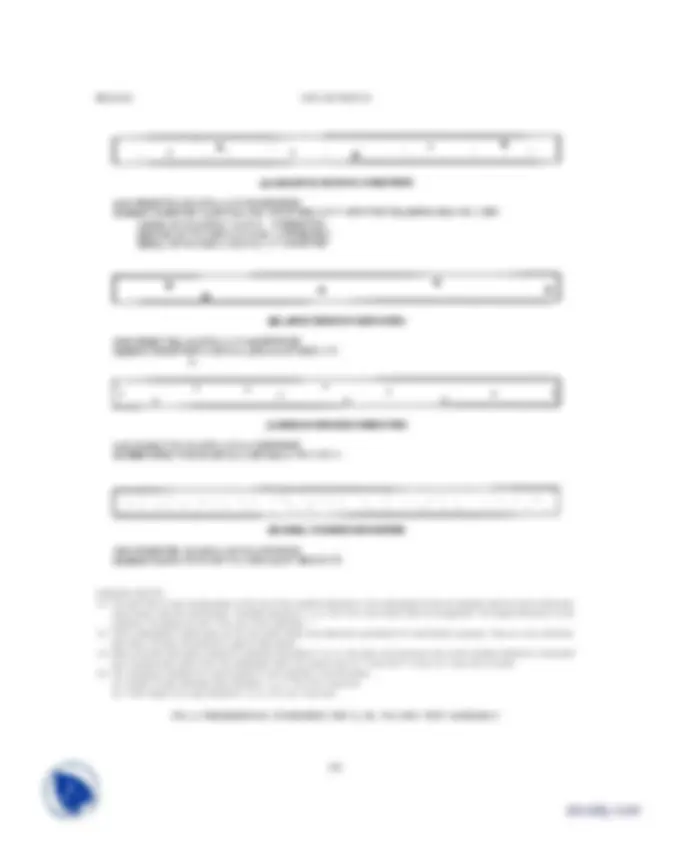
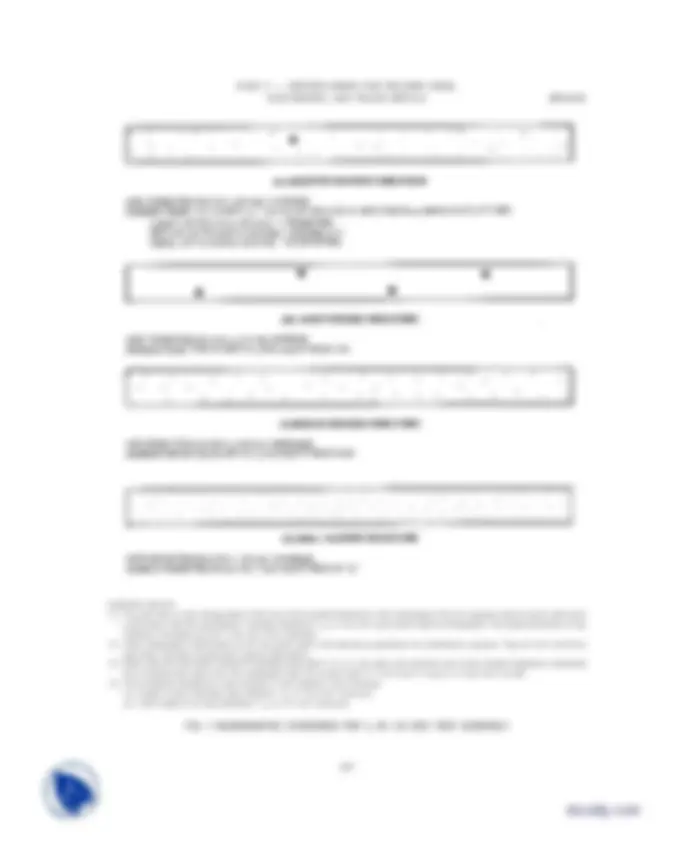
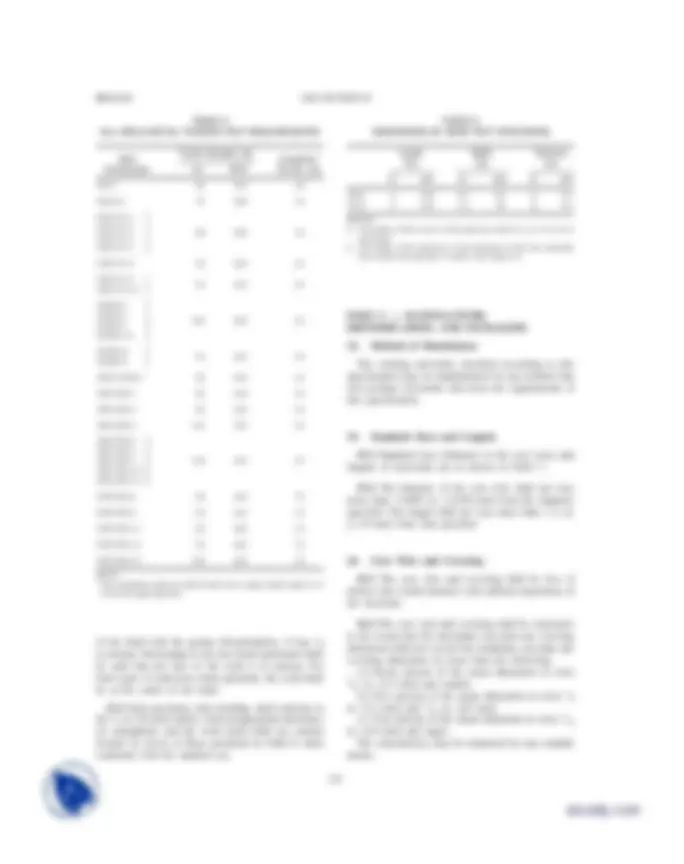
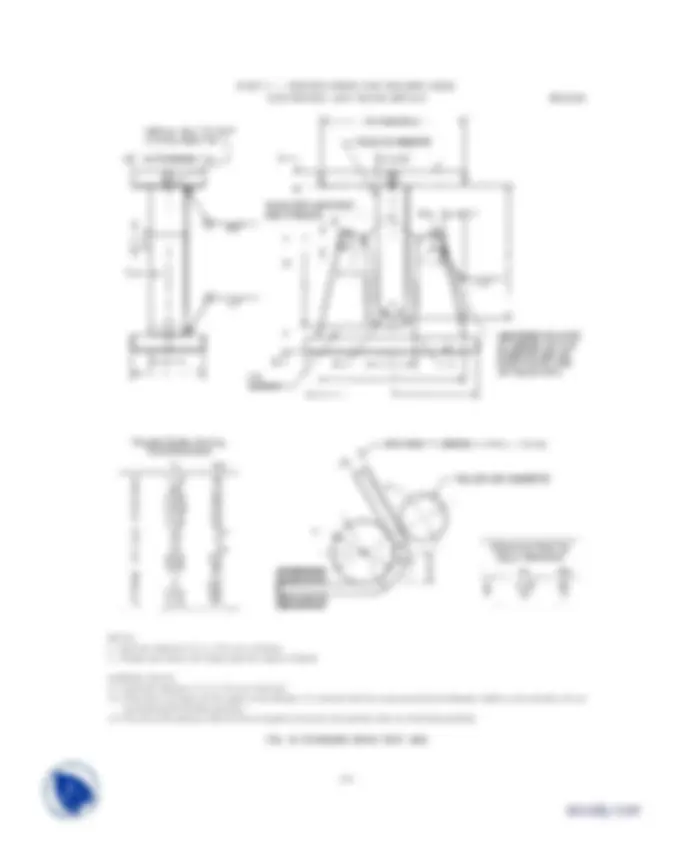

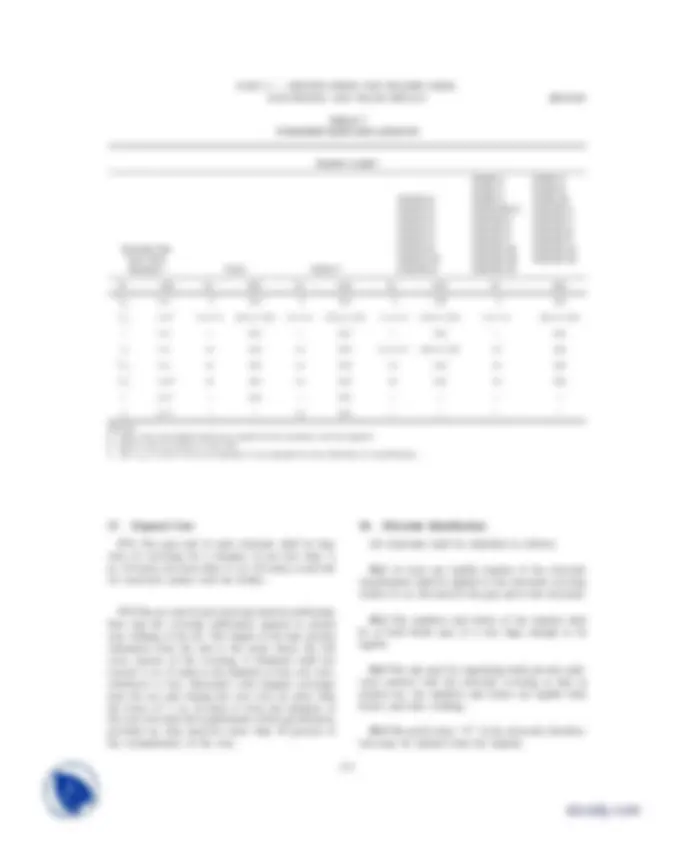
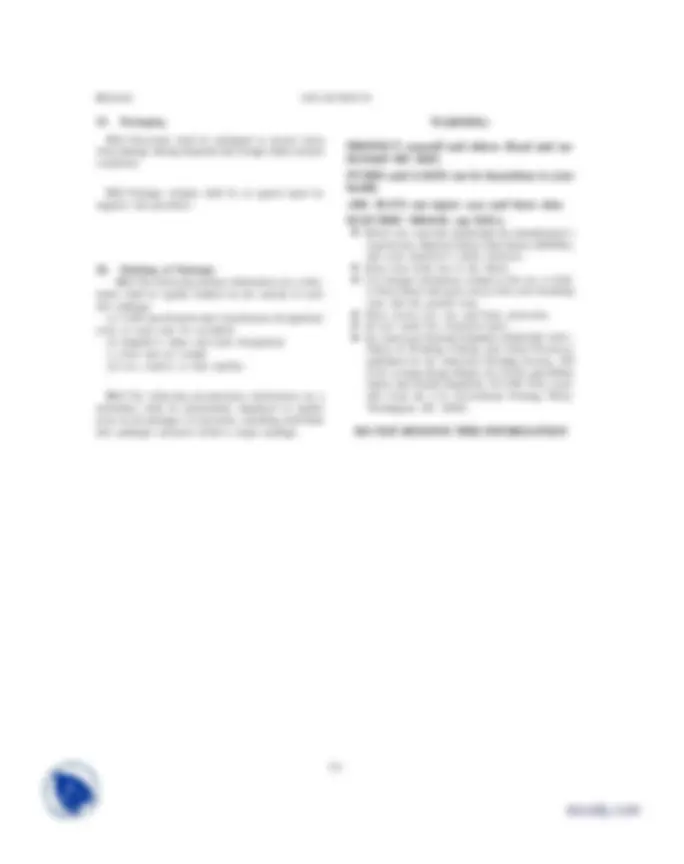
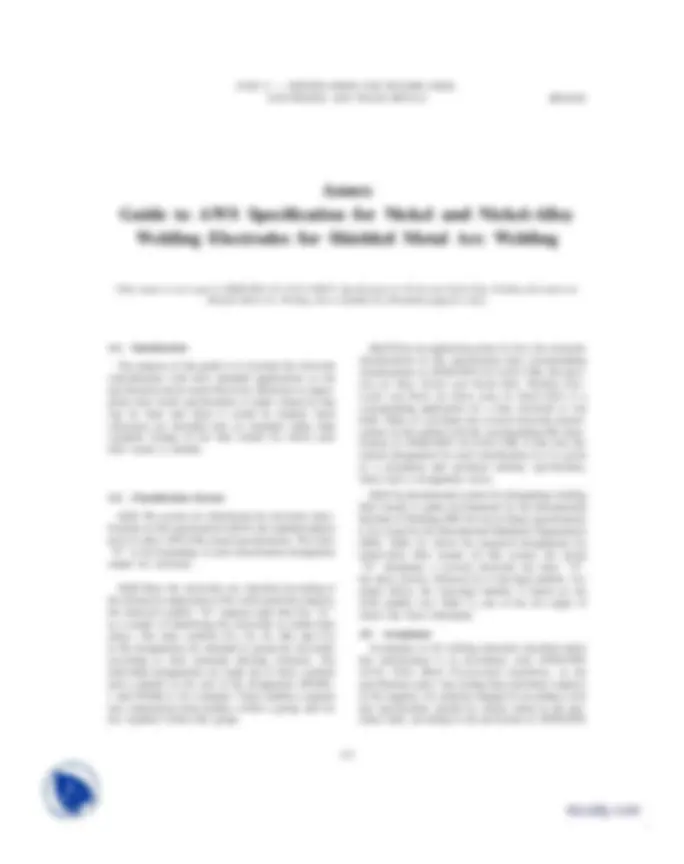
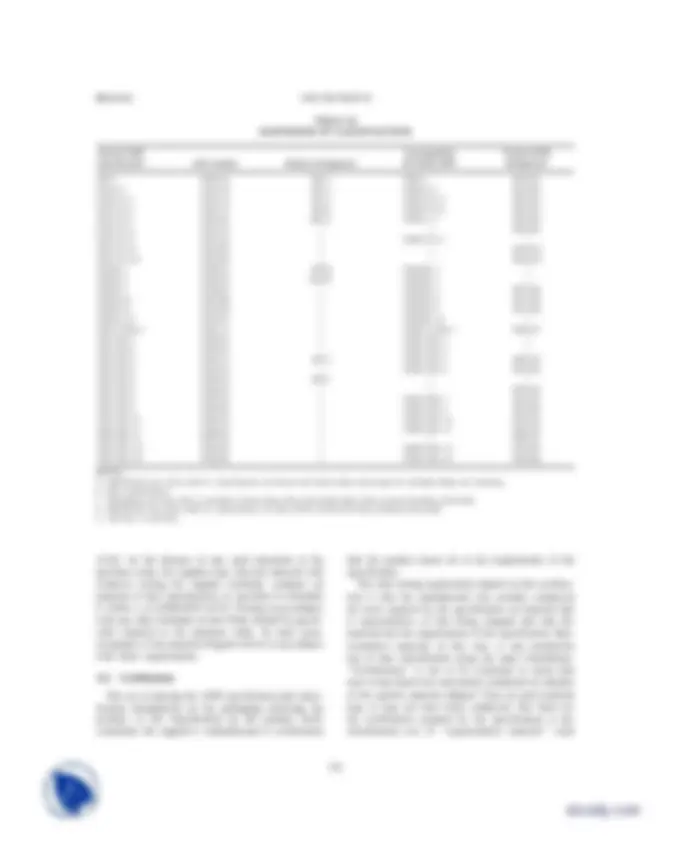
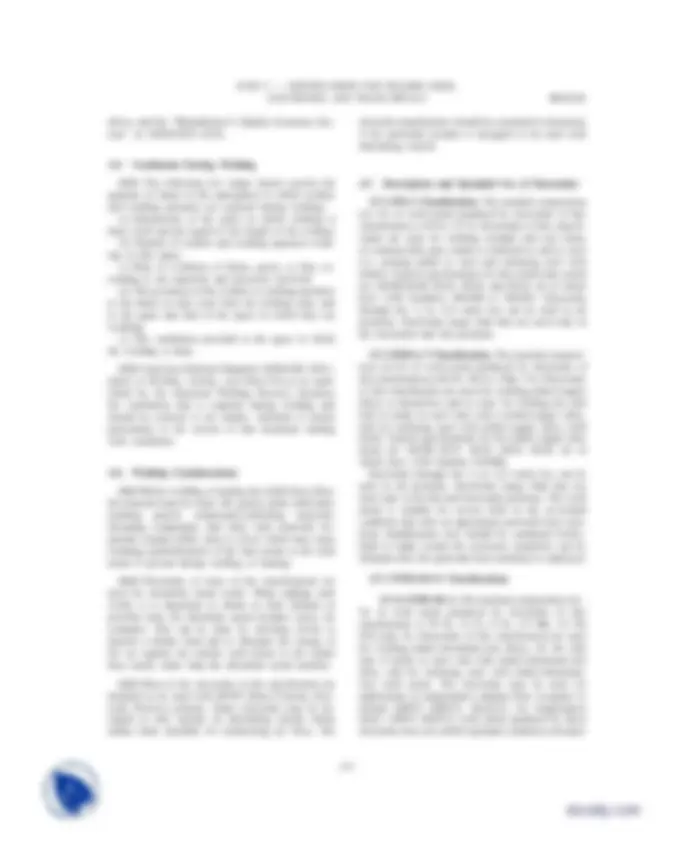
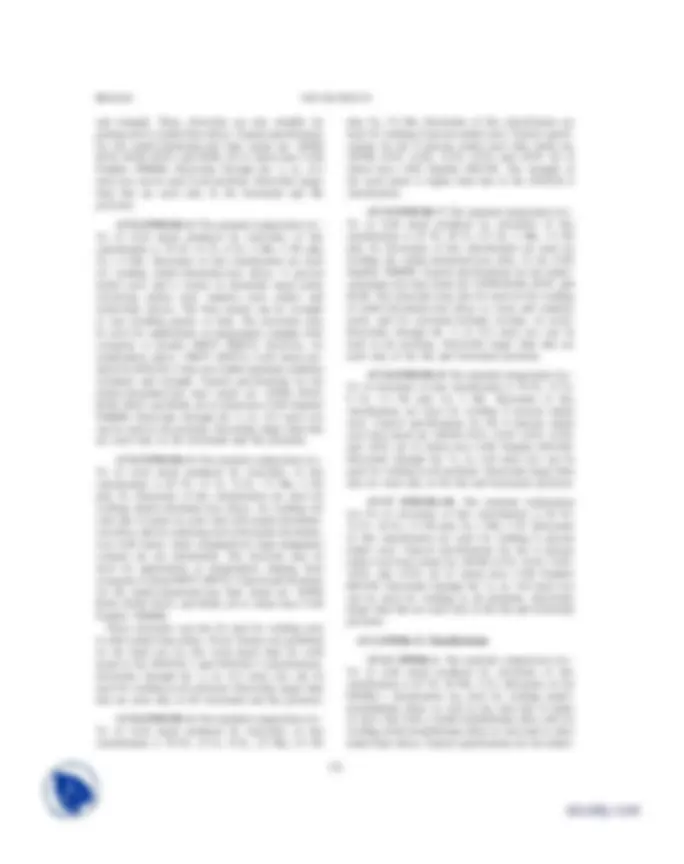
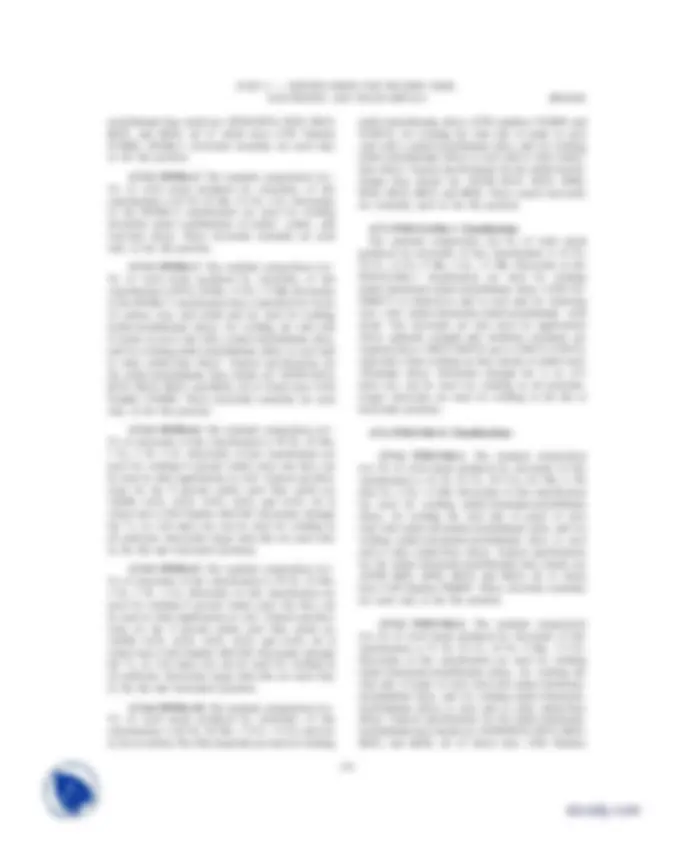
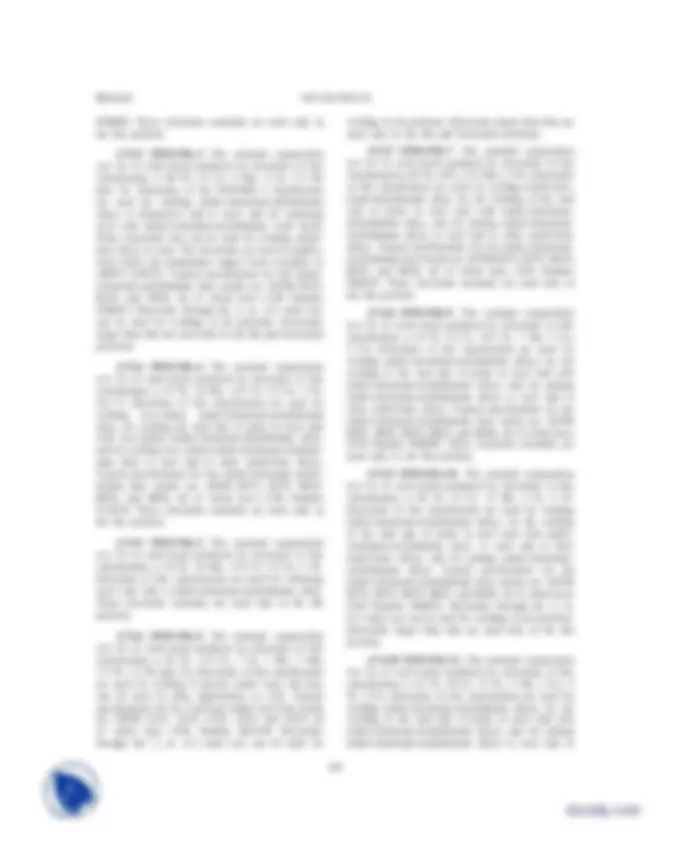
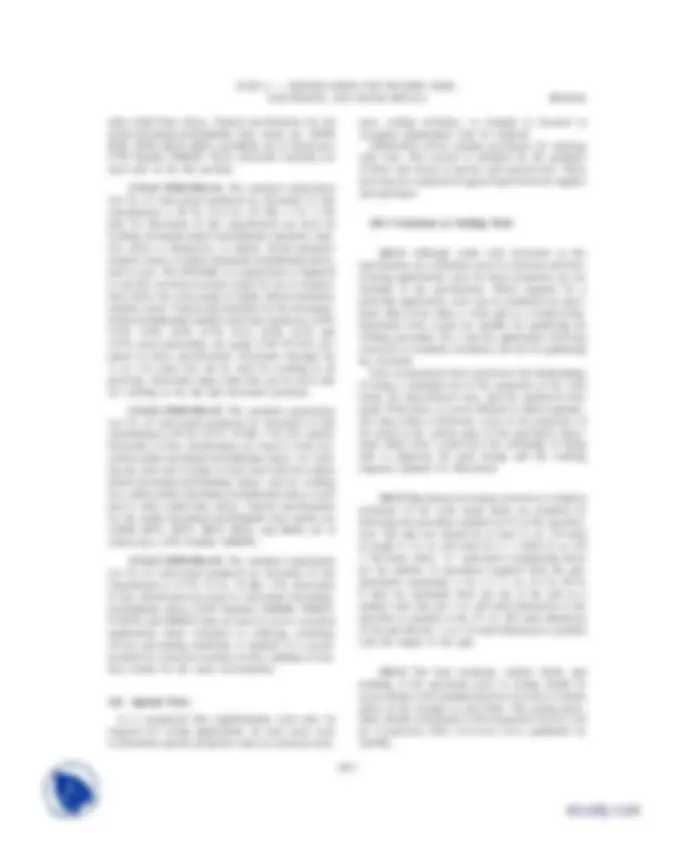
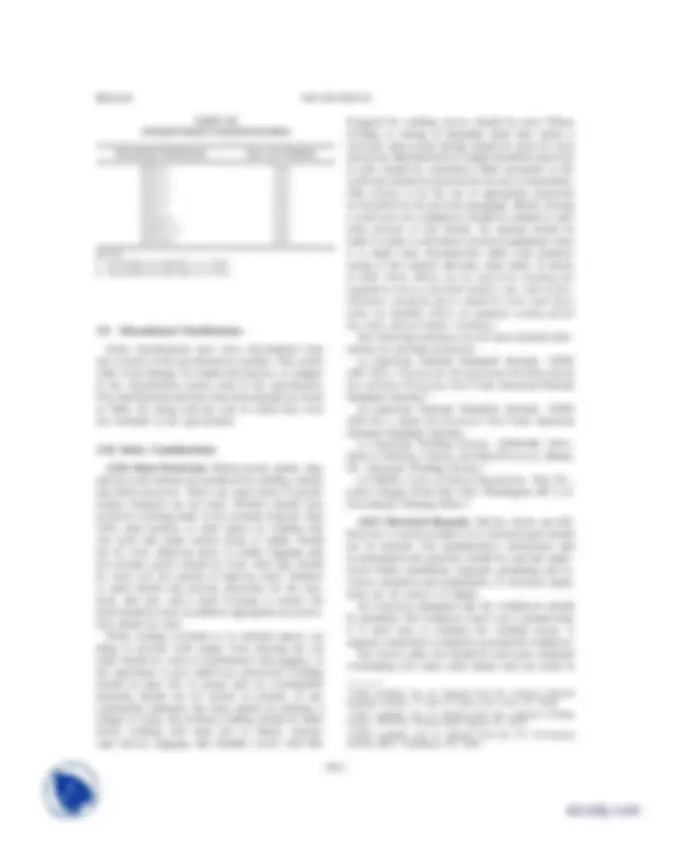
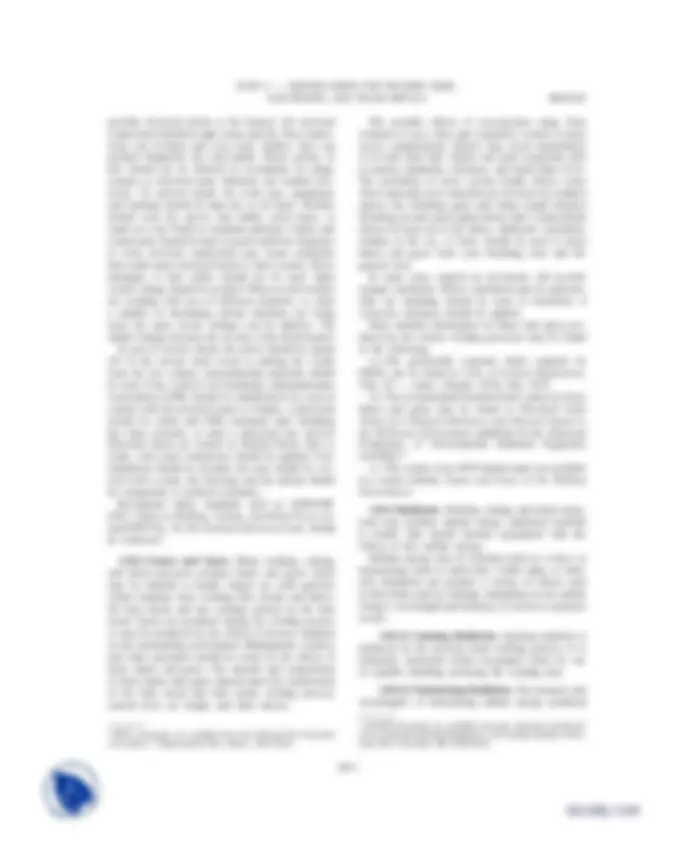
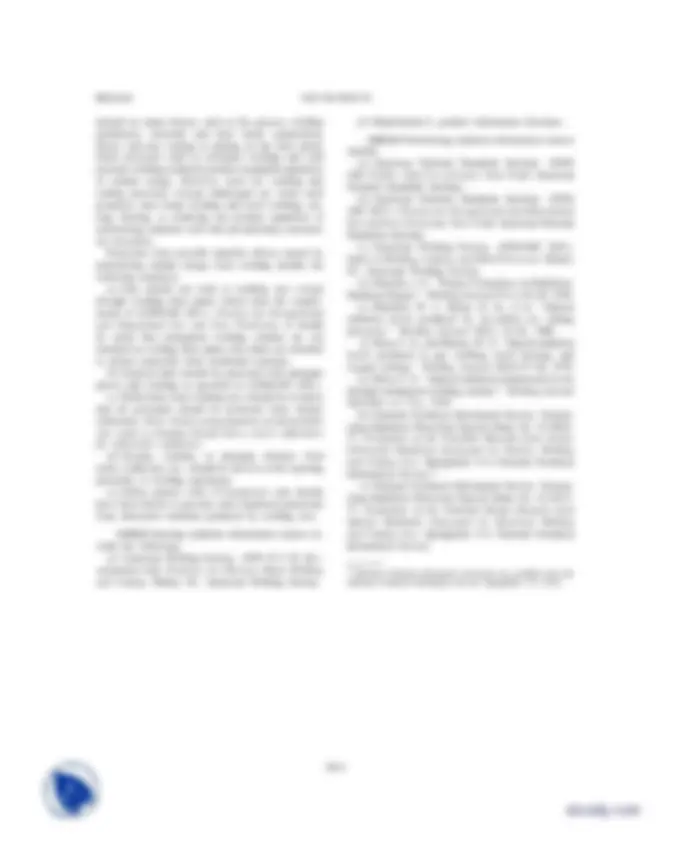
Study with the several resources on Docsity
Earn points by helping other students or get them with a premium plan
Prepare for your exams
Study with the several resources on Docsity
Earn points to download
Earn points by helping other students or get them with a premium plan
Community
Ask the community for help and clear up your study doubts
Discover the best universities in your country according to Docsity users
Free resources
Download our free guides on studying techniques, anxiety management strategies, and thesis advice from Docsity tutors
Dr. Ajitabh Sai delivered this lecture at Baba Farid University of Health Sciences for Mechanical and Materials Engineering Specifications course. It includes: Specification, Nickel, Nickel-alloy, Bare, Rods, Electrodes, Welding, Test, Requirements, Procedures
Typology: Exercises
1 / 32
This page cannot be seen from the preview
Don't miss anything!
1. Scope
This specification prescribes requirements for the
classification of nickel and nickel-alloy covered elec-
trodes for shielded metal arc welding. It includes those
compositions in which the nickel content exceeds that
of any other element. 1
PART A — GENERAL REQUIREMENTS
2. Normative References
2.1 The following ANSI/AWS standards 2 are refer-
enced in the mandatory sections of this document:
(a) ANSI/AWS A1.1, Metric Practice Guide for the
Welding Industry
(b) ANSI/AWS A5.01, Filler Metal Procurement Guidelines
(c) ANSI/AWS B4.0, Standard Methods for Mechan-
ical Testing of Welds
2.2 The following ASTM and ISO standards 3 are
referenced in the mandatory sections of this document:
(^1) Nickel-base covered electrodes for welding cast irons are treated
separately in ANSI/AWS A5.15, Specification for Welding Electrodes and Rods for Cast Iron. This specification is available from the American Welding Society, 550 N.W. LeJeune Road, Miami, FL
(^2) AWS standards can be obtained from the American Welding Society,
550 N.W. LeJeune Road, Miami, FL 33126. (^3) ASTM standards can be obtained from the American Society for
Testing and Materials, 100 Barr Harbor Drive, West Conshohocken, PA 19428-2959. ISO standards are available from American National Standards Institute, ANSI, 11 West 42nd Street, 13th Floor, New York, NY 10036.
(a) ASTM A 131/A 131M, Standard Specification for Structural Steel for Ships (b) ASTM A 240/A 240M, Standard Specification for Heat-Resisting Chromium and Chromium-Nickel Stainless Steel Plate, Sheet, and Strip for Pressure Vessels (c) ASTM A 285/A 285M, Standard Specification for Pressure Vessel Plates, Carbon Steel, Low- and Intermediate-Tensile Strength (d) ASTM A 515/A 515M, Standard Specification for Pressure Vessel Plates, Carbon Steel, for Intermedi- ate- and Higher-Temperature Service (e) ASTM B 127, Standard Specification for Nickel- Copper Alloy (UNS N04400) Plate, Sheet, and Strip (f) ASTM B 160, Standard Specification for Nickel Rod and Bar (g) ASTM B 162, Standard Specification for Nickel Plate, Sheet, and Strip (h) ASTM B 164, Standard Specification for Nickel- Copper Alloy Rod, Bar, and Wire (i) ASTM B 166, Standard Specification for Nickel- Chromium-Iron Alloys (UNS N06600, N06601, N06690, N06025, and N06045) and Nickel-Chromium-Cobalt- Molybdenum Alloy (UNS N06617) Rod, Bar, and Wire (j) ASTM B 167, Standard Specification for Nickel- Chromium-Iron Alloys (UNS N06600, N06601, N06690, N06025, and N06045) Seamless Pipe and Tube (k) ASTM B 168, Standard Specification for Nickel- Chromium-Iron Alloys (UNS N06600, N06601, N06690, N06025, and N06045) and Nickel-Chromium-Cobalt- Molybdenum Alloy (UNS N06617) Plate, Sheet, and Strip (l) ASTM B 333, Standard Specification for Nickel- Molybdenum Alloy Plate, Sheet, and Strip
(m) ASTM B 435, Standard Specification for UNS
N06002, UNS N06230, UNS N12160, and UNS R
Plate, Sheet, and Strip (n) ASTM B 443, Standard Specification for Nickel-
Chromium-Molybdenum-Columbium Alloy (UNS
N06625) Plate, Sheet, and Strip
(o) ASTM B 446, Standard Specification for Nickel-
Chromium-Molybdenum-Columbium Alloy (UNS
N06625) Rod and Bar
(p) ASTM B 575, Standard Specification for Low-
Carbon Nickel-Molybdenum-Chromium, Low-Carbon
Nickel-Chromium-Molybdenum, and Low-Carbon
Nickel-Chromium-Molybdenum-Tungsten Alloy Plate,
Sheet, and Strip
(q) ASTM B 582, Standard Specification for Nickel-
Chromium-Iron-Molybdenum-Copper Alloy Plate, Sheet,
and Strip
(r) ASTM E 29, Standard Practice for Using Signifi-
cant Digits in Test Data to Determine Conformance
with Specifications
(s) ASTM E 38, Standard Methods for Chemical
Analysis of Nickel-Chromium and Nickel-Chromium-
Iron Alloys
(t) ASTM E 76, Standard Methods for Chemical
Analysis of Nickel-Copper Alloys
(u) ASTM E 142, Methods for Controlling Quality
of Radiographic Testing (v) ISO 544, Filler Metals for Manual Welding —
Size Requirements
3. Classification
3.1 The welding electrodes covered by the A5.11/
A5.11M specification are classified using a system
that is independent of U.S. Customary Units and the
International System of Units (SI). Classification is
according to the chemical composition of their undiluted
weld metal, as specified in Table 1.
3.2 Electrodes classified under one classification shall
not be classified under any other classification in this
specification.
4. Acceptance
Acceptance 4 of the electrodes shall be in accordance
with the provisions of ANSI/AWS A5.01, Filler Metal
Procurement Guidelines.
(^4) See Section A3, Acceptance (in the Annex), for further information concerning acceptance and testing of the material shipped, as well as ANSI/AWS A5.01, Filler Metal Procurement Guidelines.
5. Certification
By affixing the AWS specification and classification designation to the packaging, or the classification to the product, the manufacturer certifies that the product meets the requirements of this specification. 5
6. Units of Measure and Rounding-Off Procedure
6.1 This specification makes use of both U.S. Custom- ary Units and the International System of Units (SI). The measurements are not exact equivalents; therefore each system must be used independently of the other without combining values in any way. The specification with the designation A5.11 uses the U.S. Customary Units. Specification A5.11M uses SI Units. The latter are shown in appropriate columns in tables and in figures, and within brackets [] when used in the text.
6.2 For purposes of determining conformance with this specification, an observed or calculated value shall be rounded to the nearest 1000 psi [10 MPa] used in expressing the limiting value for other quantities in accordance with the rounding-off method given in ASTM E29, Standard Practice for Using Significant Digits in Tests to Determine Conformance with Specifi- cations.
PART B — TESTS, PROCEDURES, AND REQUIREMENTS
7. Summary of Tests
The tests required for classification are specified in Table 2. The purpose of these tests is to determine the chemical composition, the mechanical properties and soundness of the weld metal, and the usability of the electrode. The base metal for the weld test assem- blies, the welding and testing procedures to be em- ployed, and the results required are given in Section 9, Weld Test Assemblies, through Section 13, Bend Test.
8. Retest
If the results of any test fail to meet the requirement, that test shall be repeated twice. The results of both retests shall meet the requirement. Specimens for retest may be taken from the original test assembly, or from one or two new test assemblies. For chemical analysis,
(^5) See Section A4, Certification (in the Annex), for further information concerning certification and the testing called for to meet this requirement.
Weight Percent
a,b
Nb(Cb)
Other
Plus
Elements
Classification
Number
c^
Mn
Fe
Si
Cu
Ni
d^
Co
Al
Ti
Cr
Ta
Mo
Total
ENiMo-
Rem
to
to
to
ENiMo-
Rem
to30.
ENiMo-
min.
to
to
to
ENiMo-
to
min.
to
to
ENiMo-
Rem
to
to
to
ENiCrCoMo-
Rem
to
to
to
to
to
ENiCrMo-
Rem
to
to
to
to
to
to
ENiCrMo-
Rem
to
to
to
to
to
to
ENiCrMo-
(e)
min.
to
to
to
ENiCrMo-
Rem
to
to
to
to
Weight Percent
a,b
Nb(Cb)
Other
Plus
Elements
Classification
Number
c^
Mn
Fe
Si
Cu
Ni
d^
Co
Al
Ti
Cr
Ta
Mo
Total
ENiCrMo-
Rem
to
to
to
to
ENiCrMo-
to
min.
to
to
to
to
ENiCrMo-
Rem
to
to
ENiCrMo-
Rem
to
to
to
to
ENiCrMo-
Rem
to
to
to
to
ENiCrMo-
Rem
to
to
to
to
to
to
ENiCrMo-
g^
Rem
to
to
to
ENiCrMo-
Rem
to
to
ENiCrMo-
Rem
to
to
to
NOTES:a. The weld metal shall be analyzed for the specific elements for which values are shown in this table. If the presence of other elements is indicated in the course of the work, the amount of
those elements shall be determined to ensure that their total does not exceed the limit specified for ‘‘Other Elements, Total’’ in the last column of the table. b. Single values are maximum, except where otherwise specified. Rem
p
remainder.
c. ASTM/SAE Unified Numbering System for Metals and Alloys.d. Includes incidental cobalt. Rem
p
remainder.
e. Cobalt — 0.12 maximum, when specified by the purchaser.f. Tantalum — 0.30 maximum, when specified by the purchaser.g. UNS number formerly was W86040.
retest need be only for those specific elements that
failed to meet the test requirement.
If the results of one or both retests fail to meet the requirement, the material under test shall be considered
as not meeting the requirements of this specification
for that classification.
In the event that, during preparation or after comple-
tion of any test, it is clearly determined that prescribed
or proper procedures were not followed in preparing
the weld test assembly or test specimen(s) or in conduct-
ing the test, the test shall be considered invalid, without
regard to whether the test was actually completed, or
whether test results met, or failed to meet, the require-
ment. That test shall be repeated, following proper
prescribed procedures. In this case, the requirement for
doubling of the number of test specimens does not
apply.
9. Weld Test Assemblies
9.1 To perform all required tests as specified in
Table 2, a minimum of one weld test assembly is
required. Two, or even three, may be necessary (ac-
cording to the classification, size, and manner in which
the testing is conducted, i.e., with respect to alternative
options).
The weld test assemblies are identified as follows: (1) The weld pad in Fig. 1 for chemical analysis of
the undiluted weld metal
(2) The groove weld in Fig. 2 for mechanical proper-
ties and soundness
(3) The groove weld in Fig. 3 for radiographic
soundness.
The sample for chemical analysis may be taken from
a low dilution area in the groove weld in Fig. 2, or
from the reduced section of the fractured tension test
specimen, thereby avoiding the need to make the weld
pad. In case of dispute, the weld pad shall be the
referee method.
9.2 Preparation of each weld test assembly shall be
as prescribed in 9.3, 9.4.1, and 9.4.2. The base metal
for each assembly shall meet the requirements of the
appropriate ASTM specification shown in Table 3 or
an equivalent specification. Testing of the assemblies
shall be as prescribed in Section 10, Chemical Analysis,
Section 11, Radiographic Test, Section 12, Tension
Test, and Section 13, Bend Test.
9.3 Weld Pad. A weld pad shall be prepared as
specified in Table 2 and shown in Fig. 1, except when one of the alternatives in 9.1 (taking the sample from
the weld metal in the groove or from the tension test
specimen) is selected. Base metal of any convenient
size, of the type specified in Table 3, shall be used as the base for the weld pad. The surface of the base metal on which the filler metal is deposited shall be clean. The pad shall be welded in the flat position with multiple beads and layers to obtain undiluted weld metal. The type of current and range of amperage used for welding shall be as recommended by the manufacturer. The preheat temperature shall be not less than 60°F [16°C] and the interpass temperature shall not exceed 300°F [150°C]. The slag shall be removed after each pass. The pad may be quenched in water (temperature above 60°F [16°C]) between passes. The dimensions of the completed pad shall be as shown in Fig. 1 for each size of electrode. Testing of this assembly shall be as specified in Section 10, Chemical Analysis.
9.4 Groove Weld
9.4.1 Mechanical Properties and Soundness. A test assembly shall be prepared and welded as specified in Fig. 2 and Table 2 using base metal of an appropriate type in Table 3. Testing of this assembly shall be as specified in Section 12, Tension Test, and Section 13, Bend Test. Additionally, this assembly may be used to satisfy the requirements of the flat position radio- graphic test (Note c to Table 2). In that case, the assembly shall be radiographed as required in Section 11, Radiographic Test. The assembly shall be tested in the as-welded condition.
9.4.2 Radiographic Soundness. A test assembly shall be prepared for electrodes of all classifications and welded as shown in Fig. 3, using base metal of the appropriate type specified in Table 3. The welding position shall be as specified in Table 2 for the different electrode sizes and classifications. Testing of the assem- bly shall be as specified in Section 11, Radiographic Test. The groove weld in Fig. 2 may be radiographed (for those classifications for which the radiographic test is welded in the flat position), thus eliminating the need to make the groove weld in Fig. 3, in those cases.
10. Chemical Analysis
10.1 The sample for analysis shall be taken from weld metal obtained from the weld pad, the reduced section of the fractured tension test specimen, or a low-dilution area of the groove weld in Fig. 2. The top surface of the pad described in 9.3 and shown in Fig. 1 (when the pad is used), shall be removed and discarded. A sample for analysis shall be obtained from the underlying metal by any appropriate mechanical means. The sample shall be free of slag.
(1) The number and size of the beads will vary according to the size of the electrode and the width of the weave, as well as the amperage employed. (2) If carbon steel base metal is used for the chemical analysis pad, the height of the pad (dimension H) shall be increased as required in Note 1 of Table 3.
For electrodes smaller than 5 ⁄ 32 in. [4.0 mm], the
sample shall be taken at least 3 ⁄ 8 in. [9.5 mm] from
the nearest surface of the base metal. For electrodes (^5) ⁄ 32 in. [4.0 mm] and larger, the sample shall be taken at least 3 ⁄ 4 in. [19 mm] from that surface. If carbon-
steel base metal is used in the chemical analysis test
pad, see Note (1) in Table 3. The sample from the
reduced section of the fractured tension test specimen and the sample from a low-dilution area of the groove
weld shall be prepared for analysis by any suitable
mechanical means.
10.2 The sample shall be analyzed by accepted analytical methods. The referee method shall be either ASTM E38, Standard Methods for Chemical Analysis of Nickel-Chromium and Nickel-Chromium-Iron Alloys , or ASTM E76, Standard Methods for Chemical Analysis of Nickel-Copper Alloys , as appropriate.
10.3 The results of the analysis shall meet the requirements of Table 1 for the classification of electrode under test.
(1) Base metal shall be as specified in Table 3. (2) The surface to be welded shall be clean. (3) Welding shall be conducted in the vertical-up or flat position, as required in Table 2 (also see note c in Table 2) using the type and range of current, and technique recommended by the electrode manufacturer. (4) The preheat temperature shall be 60°F [16°C]. The interpass temperature shall not exceed 300°F [150°C]. (5) The welds shall be made with a stringer bead technique or a weave to produce a bead no wider than four times the diameter of the core wire. The root layer in tests of electrodes larger than 1 ⁄ 8 in. [3.2 mm] diameter may be deposited with 3 ⁄ 32 or 1 ⁄ 8 in. [2.4, 2.5 or 3.2 mm] electrodes of that same classification. In addition to the start and stop at the ends of the weld, each bead shall also contain a start and a stop somewhere in between. (6) A small amount of grinding between beads is permissible for welds in the vertical position, but an inordinate amount should not be required to produce a satisfactory weld. (7) The completed weld shall be at least flush with the surface of the test plate. (8) The backing strip shall be removed, and the weld on both sides of the assembly shall be machined or ground smooth and flush with the original surfaces of the base plate. (9) The assembly shall be radiographed as specified in Section 11, Radiographic Test.
AWS Classification Material a,b^ ASTM Specifications c^ UNS Number
ENi-1 Nickel B160, B162 N02200, N
ENiCu-7 Nickel-Copper Alloy B127, B164 N
ENiCrFe-1, 2, 3, 4, 9 ,10 Nickel-Chromium-Iron Alloy B166, B168 N
ENiCrFe-7 Nickel-Chromium-Iron Alloy B166, B167, B168 N
ENiMo-1, 3, 7, 8, 9, 10 Nickel-Molybdenum Alloy B333 N10001, N10665, N
ENiCrCoMo-1 Nickel-Chromium-Cobalt-Molybdenum Alloy B166, B168 N
ENiCrMo-1, 9, 11 Nickel-Chromium-Molybdenum Alloy B582 N06007, N06985, N
ENiCrMo-2 Nickel-Chromium-Molybdenum Alloy B435 N
ENiCrMo-3 Nickel-Chromium-Molybdenum Alloy B443, B446 N
ENiCrMo-4, 5, 7, 10, 13, 14 Low-Carbon Nickel-Chromium-Molybdenum B575 N10276, N06455, N06022, Alloy N06059, N
ENiCrMo-6 Nickel-Chromium-Molybdenum Alloy B166, B168 N
ENiCrMo-12 Chromium-Nickel-Molybdenum Alloy A240 S (Austenitic Stainless Steel)
NOTES: a. Either the base metals specified or carbon steel (A131, A285, A515) may be used. If carbon steel is used, two layers of buttering shall be applied to the surface and backing strip if appropriate. For chemical analysis, base metals other than those specified may be used as the base for the undiluted weld pad provided that, for electrodes of the 1 ⁄ 8 in. [3.2 mm] size and smaller, the minimum height shown in Figure 1 is (^3) ⁄ 4 in. [19 mm] and the sample for analysis is taken at least 5 ⁄ 8 in. [16 mm] from the nearest surface of the base metal. For electrode sizes (^5) ⁄ 32 in. [4 mm] through 1 ⁄ 4 in. [6.4 mm], these dimensions are 1 in. [25 mm] and 7 ⁄ 8 in. [22 mm], respectively.
b. All specified base metals shall be in the annealed condition prior to welding. c. Equivalent material specifications may be used.
11. Radiographic Test
11.1 The radiographic soundness test weld described
in 9.4.2 and shown in Fig. 3 (or the groove weld
described in 9.4.1 and shown in Fig. 2, when that is
desired and is permitted by Note (3) of Table 2), shall
be radiographed to evaluate the usability of the electrode.
In preparation for radiography, the backing shall be
removed, and both surfaces of the weld shall be ma-
chined or ground smooth and flush with the original
surfaces of the base metal. Both surfaces of the test
assembly, in the area of the weld, shall be smooth
enough to avoid difficulty in interpreting the radiograph.
11.2 The weld shall be radiographed in accordance
with ASTM E142, Standard Method for Controlling
Quality of Radiographic Testing. The quality level of
inspection shall be 2-2T.
11.3 The electrode meets the requirements of this specification if the radiograph shows the following:
(a) No cracks, no incomplete fusion, and no incom-
plete penetration
(b) No slag inclusions in excess of those permitted by Note 4 to the radiographic standards in Figs. 4 through 8, according to the size of the electrode (c) No rounded indications in excess of those permit- ted by the radiographic standards in Figs. 4 through 8, according to the thickness of the test assembly, or the alternative method of evaluation in 11.3. In evaluating the radiograph, 1 in. [25 mm] of the weld on each end of the test assembly shall be disregarded.
11.3.1 The alternative method of evaluation in- volves calculation of the total area of the rounded indications as they appear on the radiograph. This total area shall not exceed 1 percent of the thickness of the test assembly multiplied by the length of the weld used in the evaluation (length of the weld in the test assembly minus 1 in. [25 mm] on each end). The value given in Note 3 to each of the figures (4 through 8) has been calculated for 6 in. [150 mm] of weld (an 8-in. [200-mm] long test assembly). The value for weld
(1) The chart that is most representative of the size of the rounded indications in the radiograph of the test assembly shall be used to determine conformance with this specification. Rounded indications 1 ⁄ 64 in. [0.4 mm] and smaller shall be disregarded. The largest dimension of the indication (including any tail) is the size of the indication. (2) These radiographic requirements are for test welds made in the laboratory specifically for classification purposes. They are more restrictive than those normally encountered in general fabrication. (3) When using the alternative method of evaluation described in 11.3.1, the total cross-sectional area of the rounded indications (calculated from measurements taken from the radiograph) shall not exceed 0.015 in.^2 [9.7 mm 2 ] in any 6 in. [150 mm] of weld. (4) The acceptance standard for slag inclusions in this assembly is the following: (a) Length of each individual slag indication: 5 ⁄ 32 in. [4.0 mm] maximum (b) Total length of all slag indications: 1 ⁄ 4 in. [6.4 mm] maximum
(1) The chart that is most representative of the size of the rounded indications in the radiograph of the test assembly shall be used to determine conformance with this specification. Rounded indications 1 ⁄ 64 in. [0.4 mm] and smaller shall be disregarded. The largest dimension of the indication (including any tail) is the size of the indication. (2) These radiographic requirements are for test welds made in the laboratory specifically for classification purposes. They are more restrictive than those normally encountered in general fabrication. (3) When using the alternative method of evaluation described in 11.3.1, the total cross-sectional area of the rounded indications (calculated from measurements taken from the radiograph) shall not exceed 0.023 in.^2 [14.8 mm 2 ] in any 6 in. [150 mm] of weld. (4) The acceptance standard for slag inclusions in this assembly is the following: (a) Length of each individual slag indication: 7 ⁄ 32 in. [5.6 mm] maximum (b) Total length of all slag indications: 3 ⁄ 8 in. [9.5 mm] maximum
(1) The chart that is most representative of the size of the rounded indications in the radiograph of the test assembly shall be used to determine conformance with this specification. Rounded indications 1 ⁄ 64 in. [0.4 mm] and smaller shall be disregarded. The largest dimension of the indication (including any tail) is the size of the indication. (2) These radiographic requirements are for test welds made in the laboratory specifically for classification purposes. They are more restrictive than those normally encountered in general fabrication. (3) When using the alternative method of evaluation described in 11.3.1, the total cross-sectional area of the rounded indications (calculated from measurements taken from the radiograph) shall not exceed 0.045 in.^2 [29.0 mm 2 ] in any 6 in. [150 mm] of weld. (4) The acceptance standard for slag inclusions in this assembly is the following: (a) Length of each individual slag indication: 5 ⁄ 16 in. [7.9 mm] maximum (b) Total length of all slag indications: 15 ⁄ 32 in. [11.9 mm] maximum
(1) Dimensions C and G shall be as shown, but the ends may be of any shape required to fit the testing machine, as long as the load is kept axial. (2) The diameter of the specimen (dimension D) within the gage length (dimension G) shall be slightly smaller at the center than at the ends (controlling dimension). The difference shall not exceed 1 percent of the diameter. (3) The finish of the surface within the C dimension shall be no rougher than 63 min. [1.6 mm].
GENERAL NOTES: (1) Specimen thickness is 3 ⁄ 8 in. [9.5 mm] minimum. (2) Dimensions not shown are the option of the designer; it is essential that the wrap-around jig has adequate rigidity so the assembly will not spring during the bending operation. (3) One end of the specimen shall be firmly clamped to the jig so the specimen does not slide during bending.
Fissures Permitted
Electrode Size Maximum Length c
Maximum AWS Classification in. mm Numberb^ in. mm (^5) ⁄ 64 2.
6
d 3 1 ⁄ 8 3 — 2. ENi-1 1 ⁄ 8 3. (^5) ⁄ 32 4. 6
d (^4 1) ⁄ 8 3 — 5. (^5) ⁄ 64 2.
6
(^3) ⁄ 32 2.4 d 3 3 ⁄ 32 2. — 2. ENiCu-7 1 ⁄ 8 3. (^5) ⁄ 32 4.
6
(^3) ⁄ 16 4.8 d 4 3 ⁄ 32 2. — 5. (^1) ⁄ 4 6.4 d
ENiMo-1 ENiMo-3 (^) ENiMo-7 ENiMo-8 (^)
6
ENiMo-9 ENiMo-10 (^) ENiCrFe-1 ENiCrFe-2 (^) ^5 ⁄ 64 2. ENiCrFe-4 ENiCrFe-7 (^) ^3 ⁄ 32 2.4 d ENiCrFe-9 ENiCrFe-10 (^) — 2. ENiCrCoMo-1 ENiCrMo-1 (^) ^1 ⁄ 8 3.2 3 3 ⁄ 32 2.
5 ENiCrMo-2 ENiCrMo-3 (^) ^5 ⁄ 32 4. ENiCrMo-4 ENiCrMo-5 (^) ^3 ⁄ 16 4.8 d ENiCrMo-6 ENiCrMo-7 (^) — 5. ENiCrMo-9 ENiCrMo-10 (^) ENiCrMo-11 ENiCrMo-12 (^) ENiCrMo-13 ENiCrMo-14 (^)
(^5) ⁄ 64 2. (^3) ⁄ 32 2.^ d
6
ENiCrFe-3 1 ⁄ 8 3.2 2 3 ⁄ 32 2. (^5) ⁄ 32 4. (^3) ⁄ 16 4.8 d — 5.
NOTES: a. These requirements apply to both side and face-bend specimens. b. The value shown is the maximum number of fissures permitted in the weld metal on the tension side of each bend specimen. The sizes of the fissures are defined in Note c. c. The number of fissures referred to in Note b, is for fissures between 1 ⁄ 64 in. [0.4 mm] and the length shown in the last column of the table. Those less than 1 ⁄ 64 in. [0.4 mm] in length and those on the corners of the specimens shall be disregarded. Bend specimens with fissures longer than the length shown do not meet the requirements of this specification. d. Metric sizes not shown in ISO 544.