
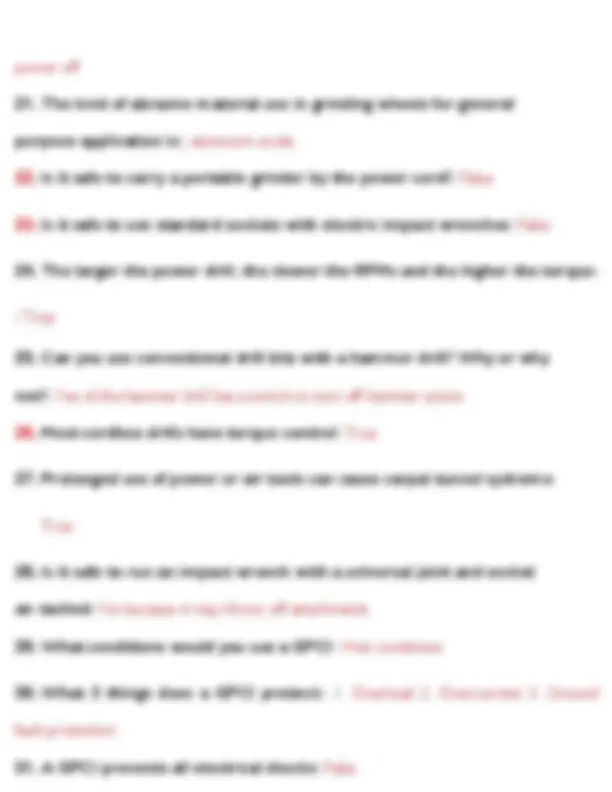

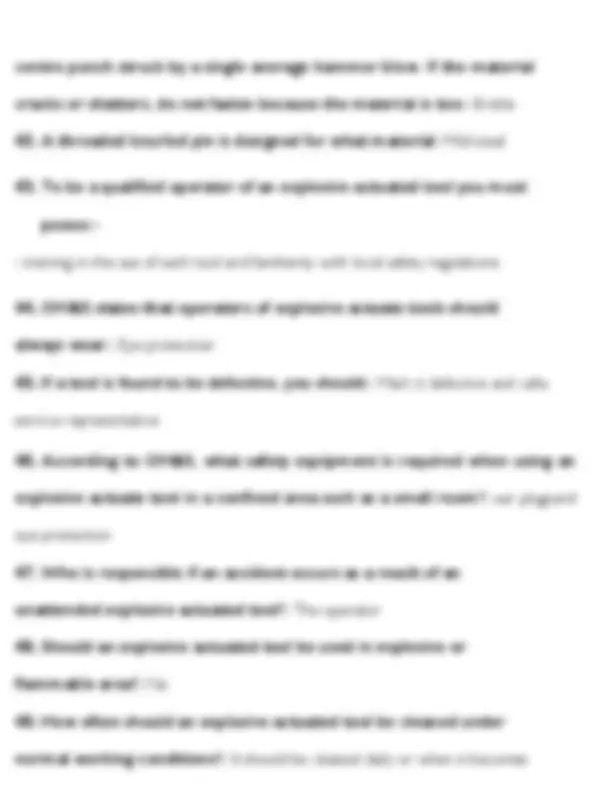
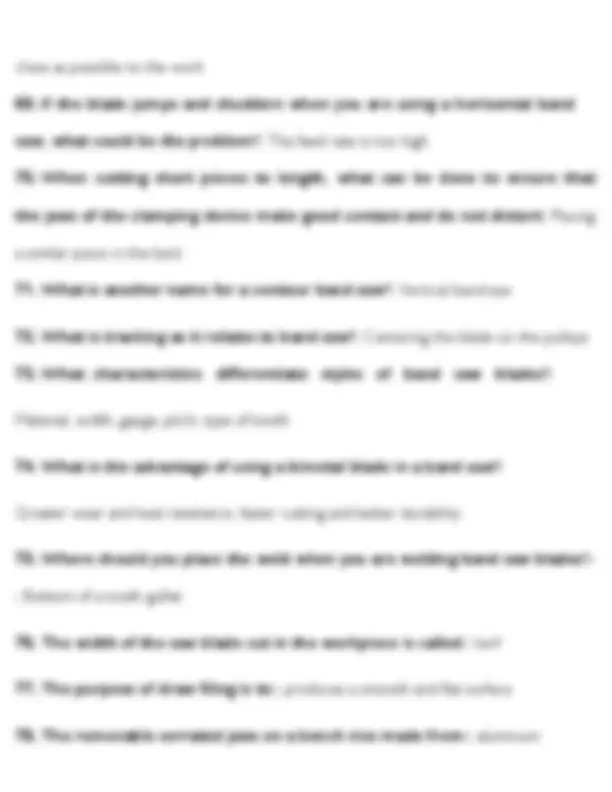
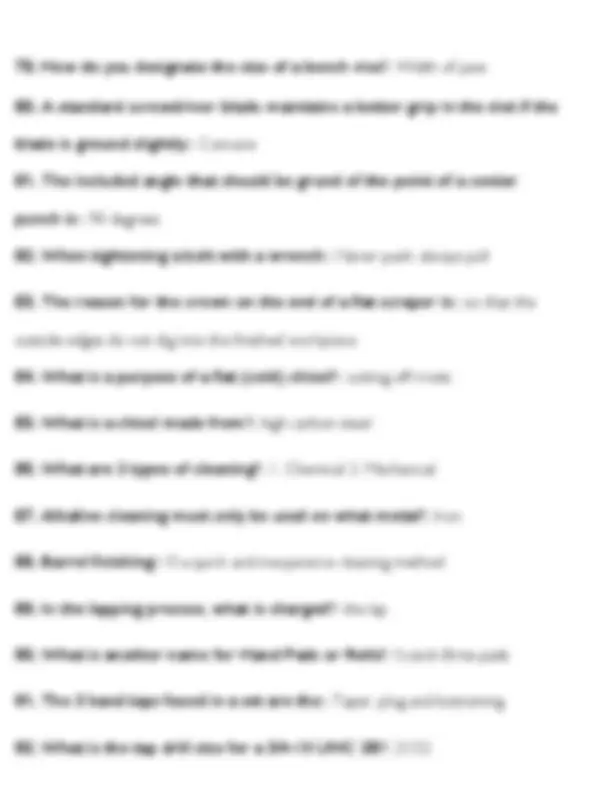
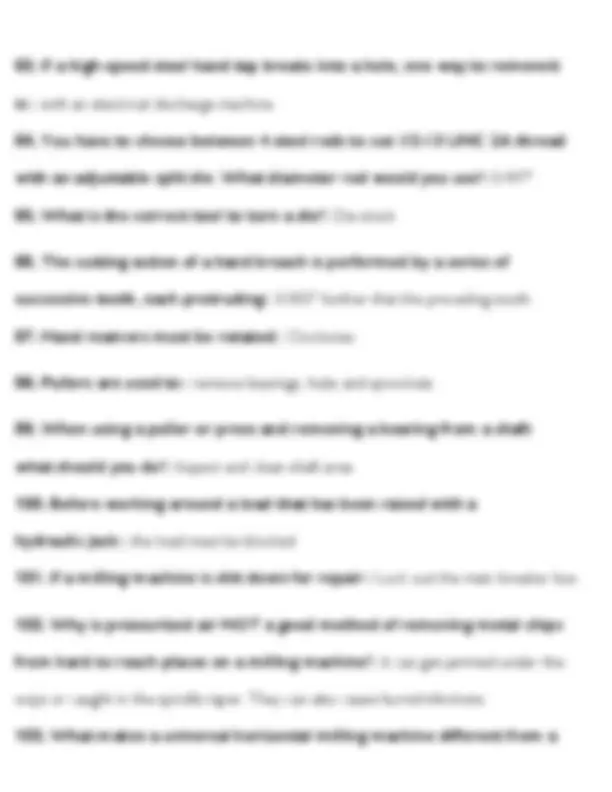
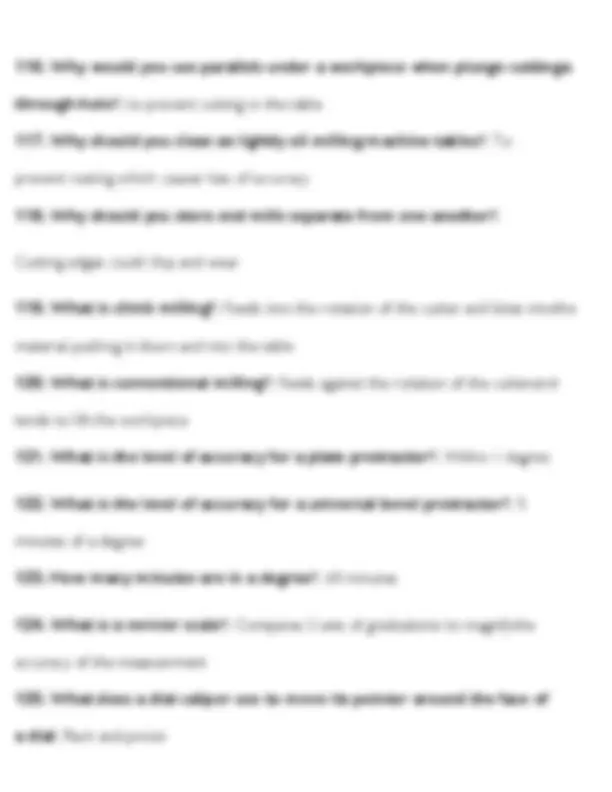
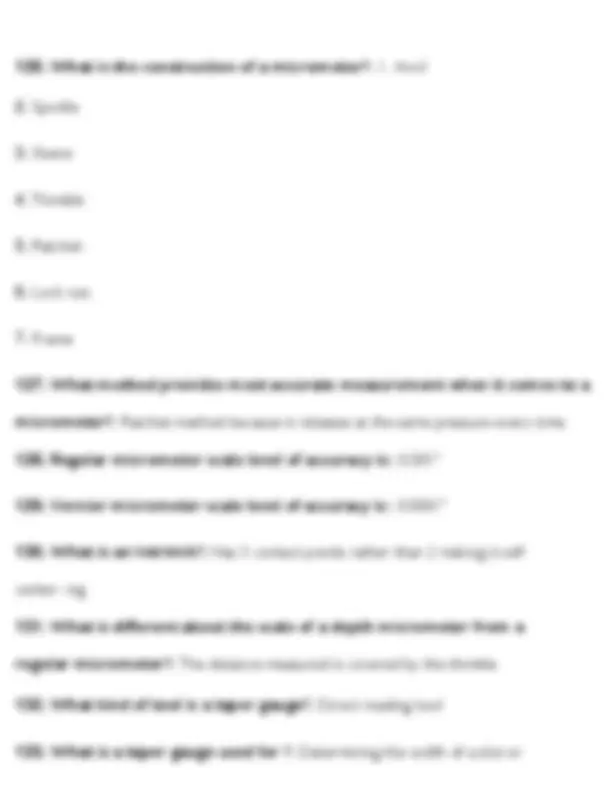
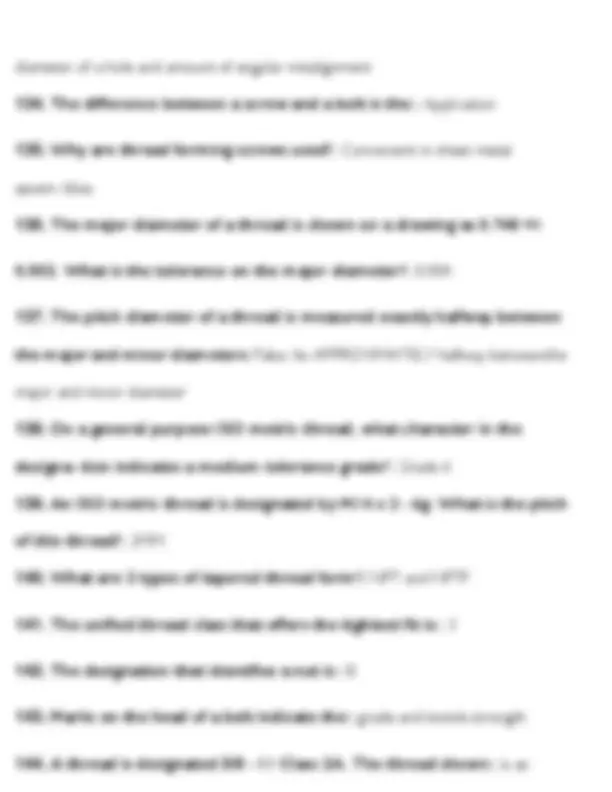
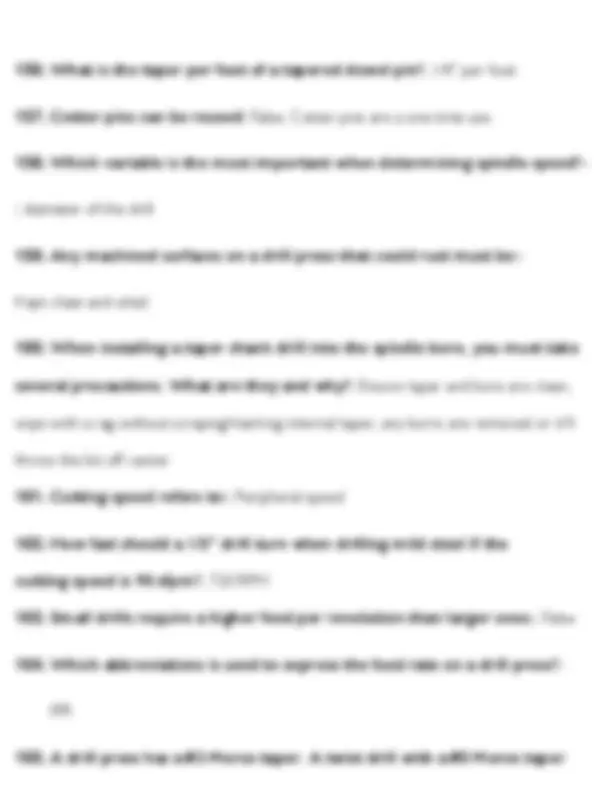
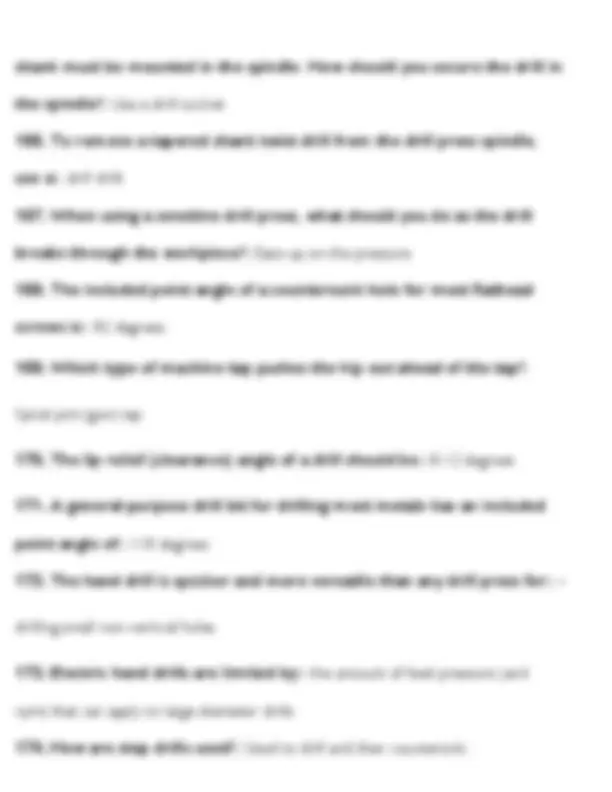
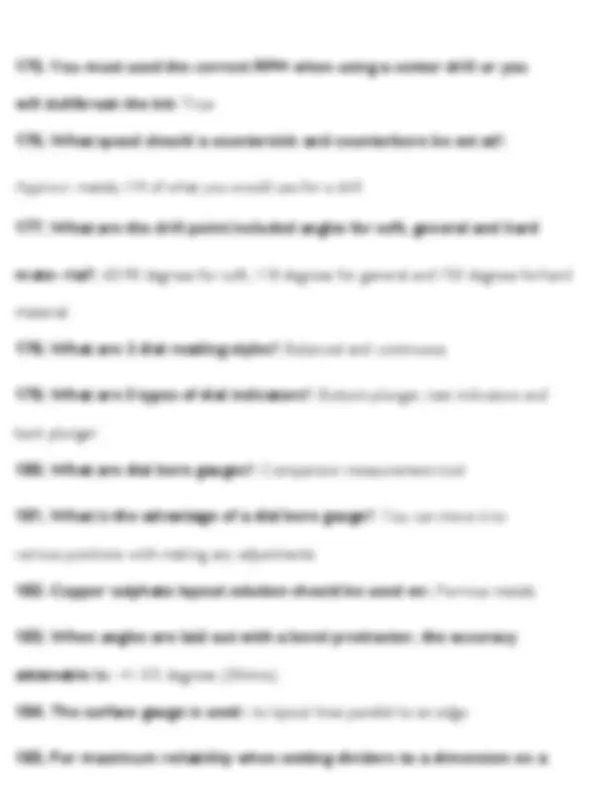
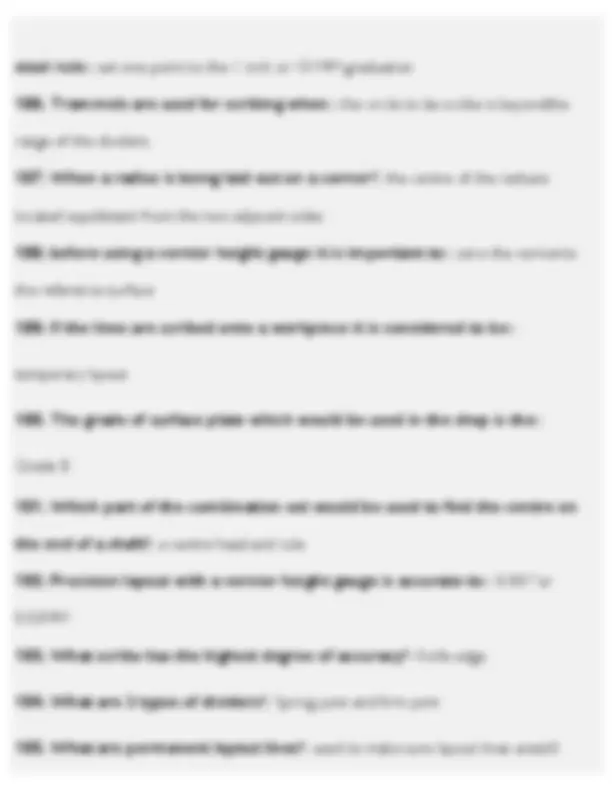
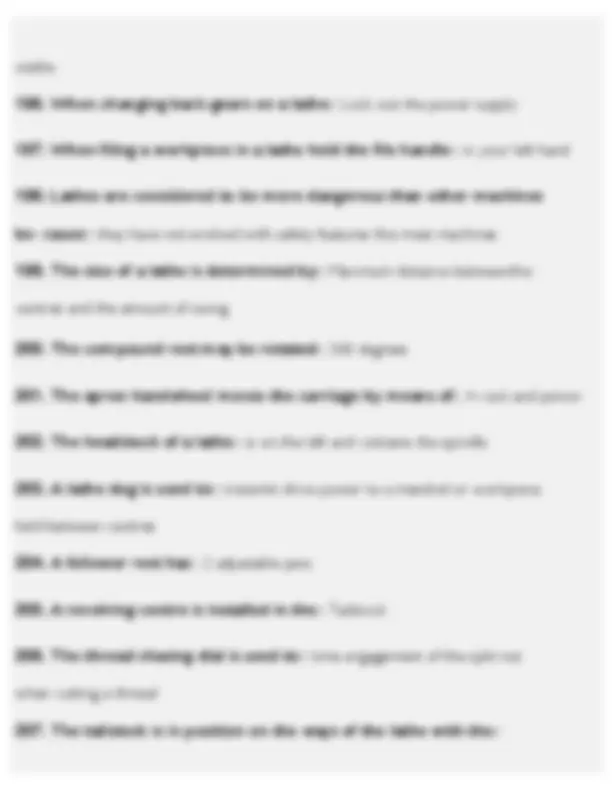
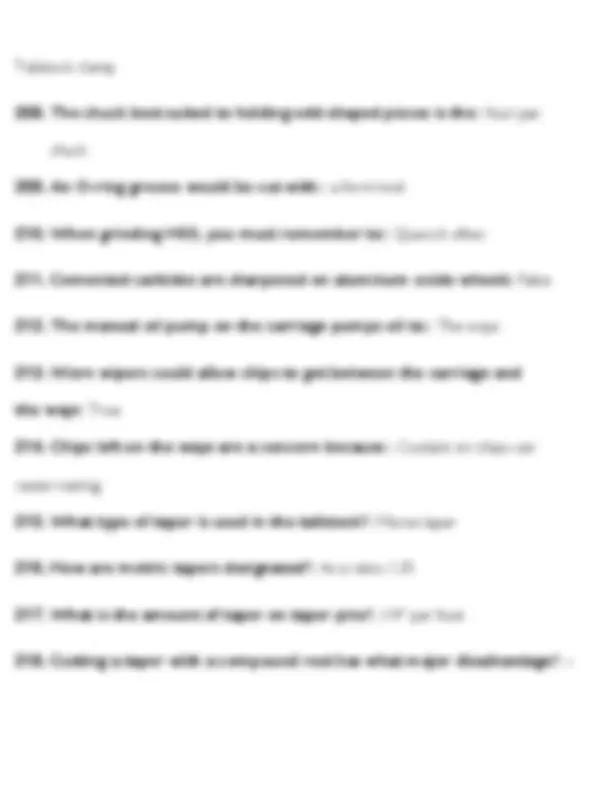
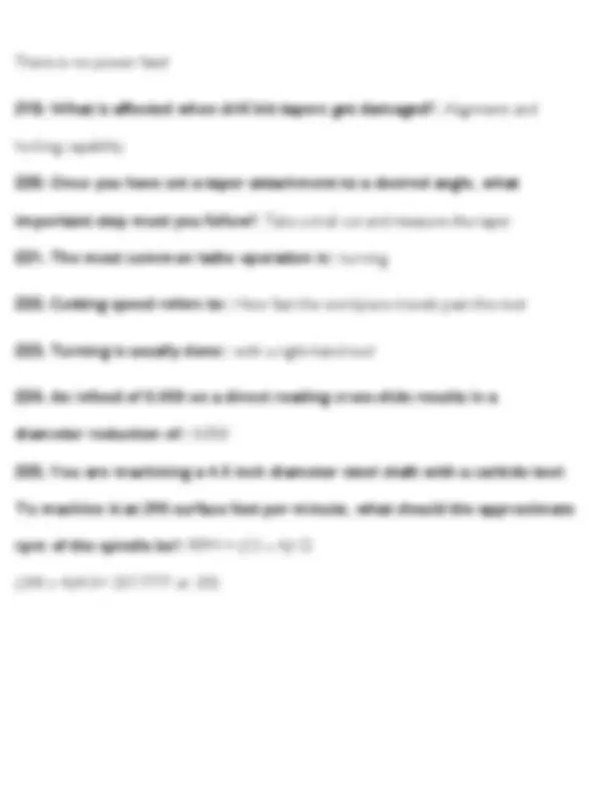
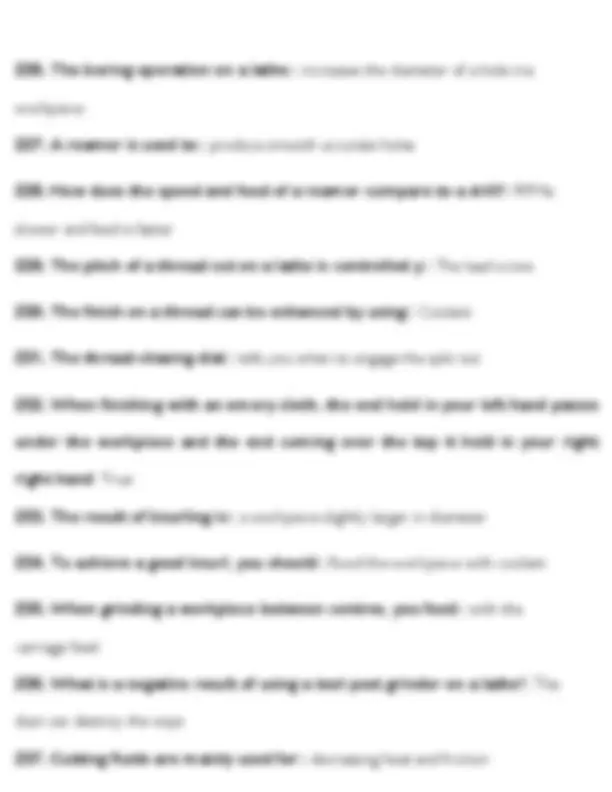
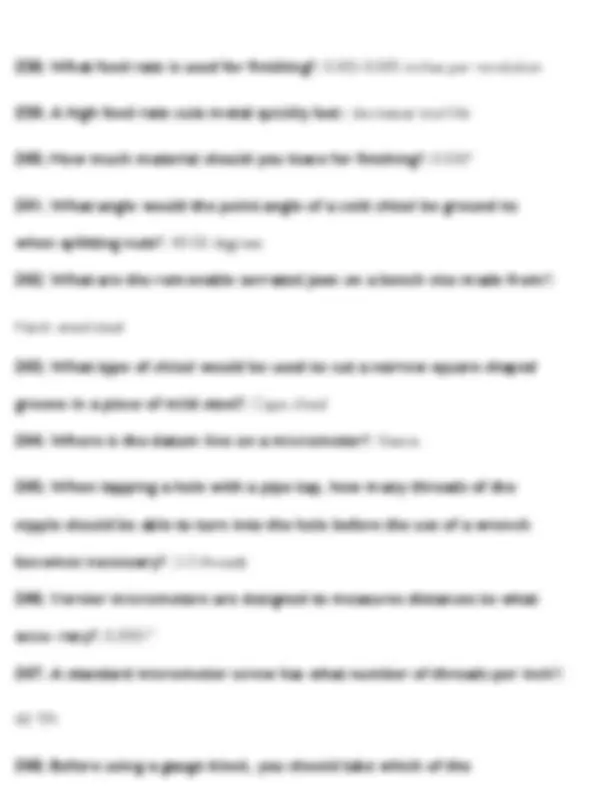
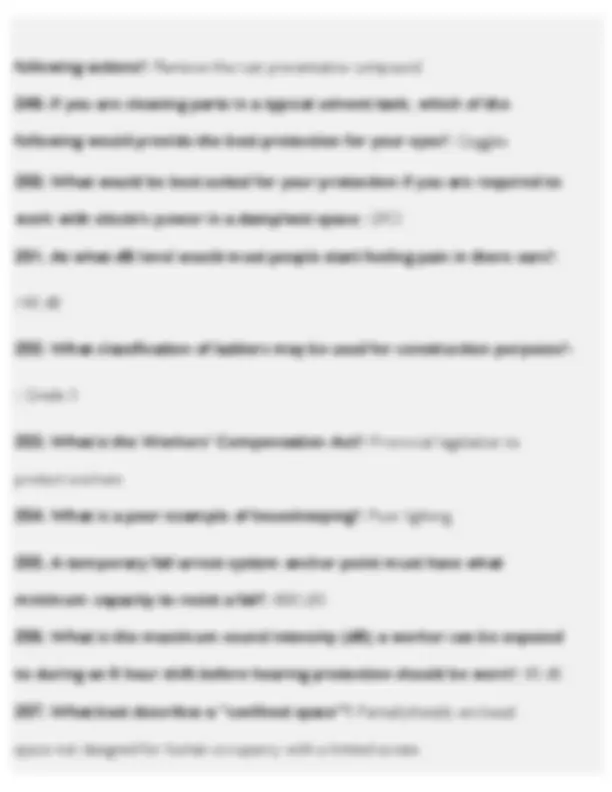
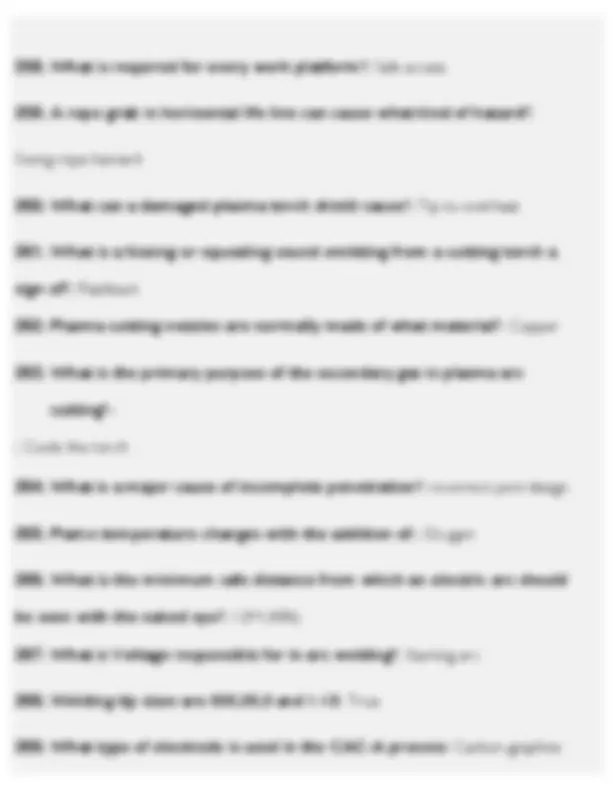
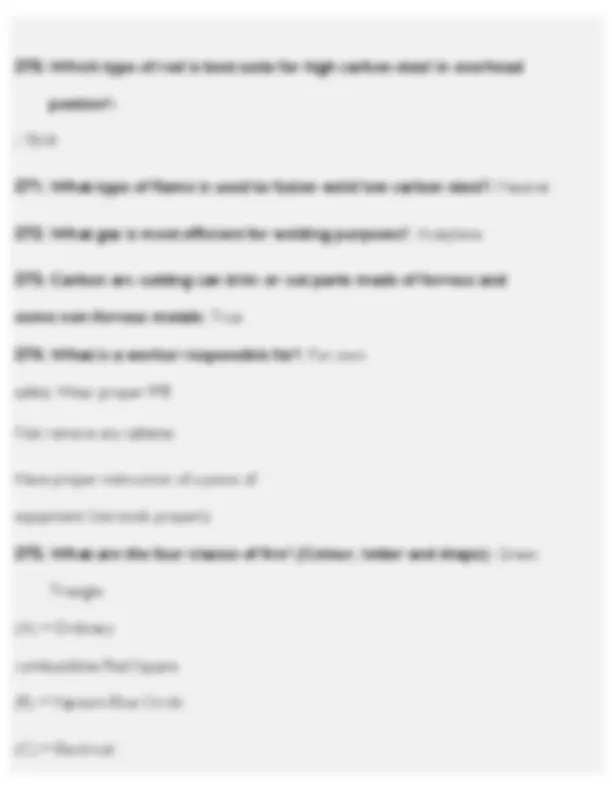
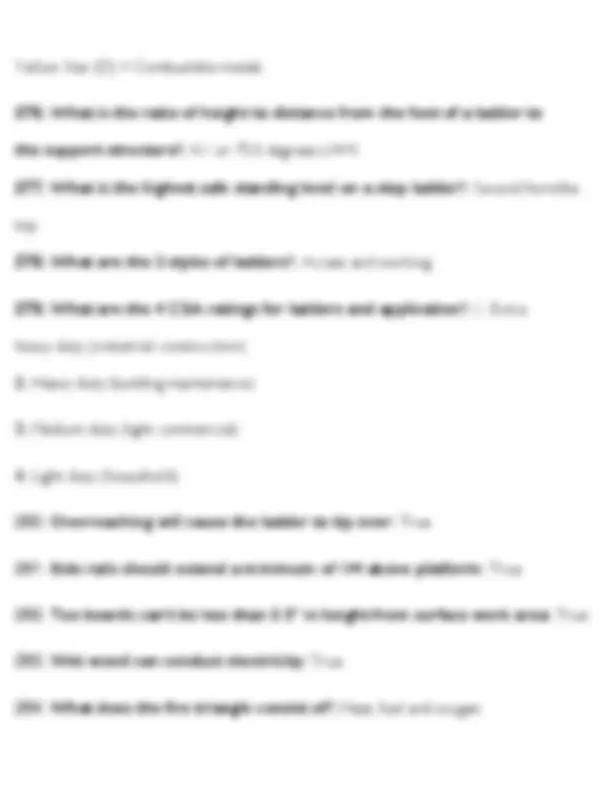

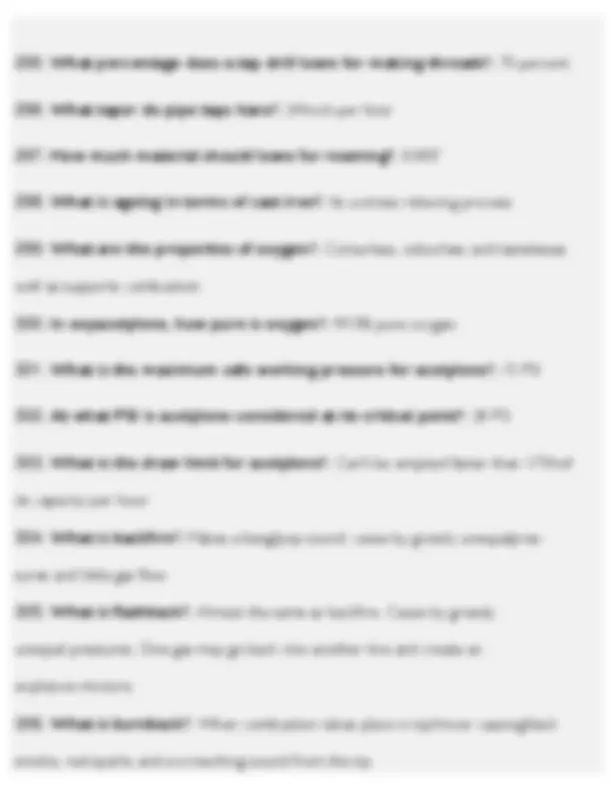
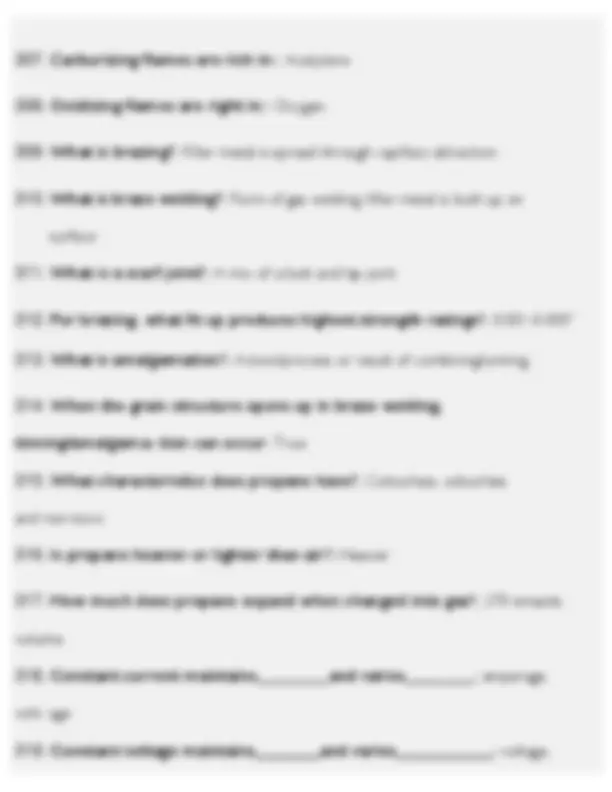
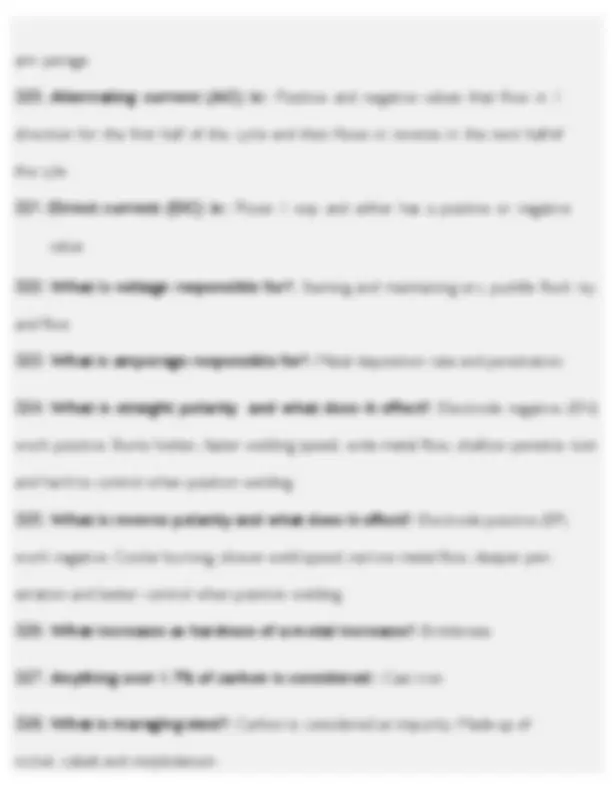

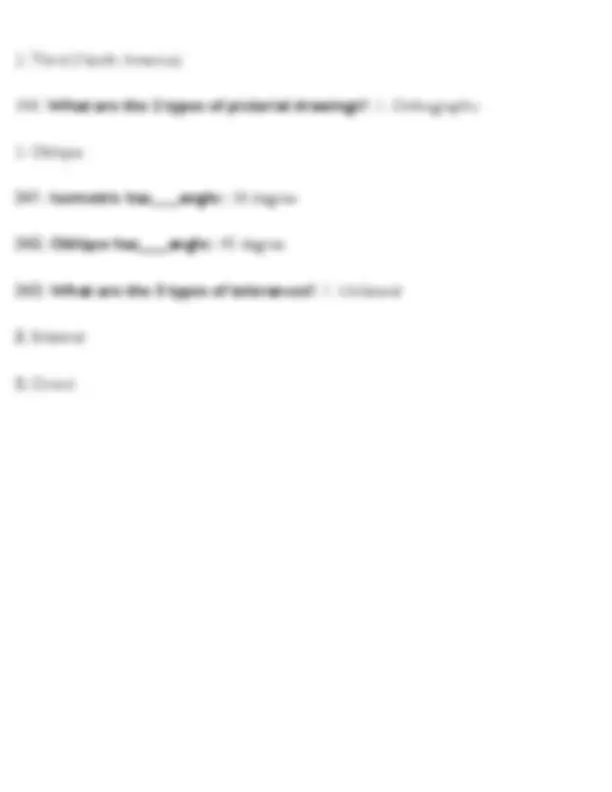
Study with the several resources on Docsity
Earn points by helping other students or get them with a premium plan
Prepare for your exams
Study with the several resources on Docsity
Earn points to download
Earn points by helping other students or get them with a premium plan
Community
Ask the community for help and clear up your study doubts
Discover the best universities in your country according to Docsity users
Free resources
Download our free guides on studying techniques, anxiety management strategies, and thesis advice from Docsity tutors
A comprehensive set of questions and answers for a millwright level 1 final exam. it covers various topics including grinding wheels, abrasive materials, power tools, and explosive actuated tools. The detailed explanations make it a valuable resource for students preparing for similar exams. The questions assess understanding of safety procedures, tool operation, and material properties.
Typology: Exams
1 / 36
This page cannot be seen from the preview
Don't miss anything!
1. On a pedestal grinder, the gap between the grinding wheel and work rest should not exceed:: ✓✓✓1/8 inch 2. The kind of abrasive material used in grinding wheels for general purpose applications is:: aluminum oxide 3. A blotter is used on a grinding wheel to:: ✓✓✓ protect the flanges from the abrasize grit, display information about the wheel and compensate for the unevensurfaces on the wheel 4. Flanges should at least be:: ✓✓✓ 1/3 the diameter of the wheel 5. The best wheel to use for cleaning scale and dirt off a workpiece is the:: wire wheel 6. What is a natural abrasive?: ✓✓✓ made of natural material rather than synthetic 7. Under properties of abrasives, to what does the term hardness refer?: ✓✓✓ ability of a material to scratch or penetrate another material 8. The is the part of the wheel that holds the grains together: bond
2 / 15
9. Markings for the wheel identification can be found on the : ✓✓✓ Blotter 10. What is the recommended speed to run a grinding wheel?: Never runit faster that the max RPM of the grinding wheel 11. How should you start a grinder?: Stand off to the side and wait a full minute 12. Is 46 or 60 the coarser grit?: 46 13. What are the 2 most commonly used abrasive materials?: Aluminum oxide and silicone carbide 14. For what purpose is the diamond dresser used?: When a very fine finishis required 15. What is the purpose of ring test?: to check for cracks 16. If a grinding wheel makes a ringing sound what does that mean?: wheelis not cracked 17. What is the purpose of truing a grinding wheel?: Restores the shape ofthe wheel and makes the outer surface of the wheel concentric with its bore 18. An out of balance wheel:: vibrates 19. Belt grinders are useful for:: quickly deburring and chamfering a workpiece 20. What is the purpose of a GFCI?: Senses drop in current and switches
32. Higher voltage on a battery means:: Greater power of tool 33. What type of power load must be used in the low velocity tool? Why?: Pow- er load with a crimped end must be used cause high power load would get lodged in the tool 34. 6 colours ranging from lowest strength to highest strength for power load are:: 1. Grey 2. Brown 3. Green 4. Yellow 5. Red 6. Purple 35. Power loads should not be carried loosely in pockets or aprons. Why?: - Could be set off causing serious injury or death 36. Fasteners used in explosive actuated tools are:: Manufactured from special steel and tempered 37. A drive pin is a fastener used to:: Permanently attach one material toanother 38. What is base material?: Material which the fastener shank is driven into 39. To determine the sustainability of a base material, use a fastener asa centre punch struck by a single average hammer blow. If the fastener is blunted ( meaning it can't fasten) the material is too:: Hard 40. To determine the sustainability of a base material, use a fastener as a cen- tre punch struck by a single average hammer blow. If the fastener penetrates easily, do not fasten because the material is too:: Soft 41. To determine the sustainability of a base material, use a fastener as a
centre punch struck by a single average hammer blow. If the material cracks or shatters, do not fasten because the material is too:: Brittle
42. A threaded knurled pin is designed for what material: Mild steel 43. To be a qualified operator of an explosive actuated tool you must posses:- : training in the use of each tool and familiarity with local safety regulations 44. OH&S states that operators of explosive actuate tools should always wear:: Eye protection 45. If a tool is found to be defective, you should:: Mark it defective and calla service representative 46. According to OH&S, what safety equipment is required when using an explosive actuate tool in a confined area such as a small room?: ear plugsand eye protection 47. Who is responsible if an accident occurs as a result of an unattended explosive actuated tool?: The operator 48. Should an explosive actuated tool be used in explosive or flammable area?: No 49. How often should an explosive actuated tool be cleaned under normal working conditions?: It should be cleaned daily or when it becomes
59. What is another name for a power saw?: Reciprocating saw 60. What determines the size (capacity) of a power hacksaw?: Largest square piece that can be cut 61. Why is the pressure removed from the blade of a power hack saw on the return stroke?: To prevent damage to the blade 62. How is the speed of a power hacksaw expressed?: Strokes per minute 63. Describe the characteristics of a bimetal power hacksaw blade: High speed tooth edge with a tough alloy steel back 64. How does the blade set differ from the blade kerf?: Kerf is the width the blade cuts and set is the way individual teeth are bent out of line with the body 65. What are the limitations of a horizontal band saw as it relates to cutting curves or round corners?: It can only cut straight 66. How is feed rate controlled on a horizontal band saw?: An adjustablehy- draulic cylinder 67. IS it necessary to turn a horizontal band saw off manually after completing a cutting operation? Why or Why not?: No because a switch is automatically activated by the downward motion of the upper frame 68. What re the saw guides and where should you place them when you are using a horizontal band saw?: They guide the blade and should be adjusted to as
close as possible to the work
69. If the blade jumps and shudders when you are using a horizontal band saw, what could be the problem?: The feed rate is too high 70. When cutting short pieces to length, what can be done to ensure that the jaws of the clamping device make good contact and do not distort: Placing a similar piece in the back 71. What is another name for a contour band saw?: Vertical band saw 72. What is tracking as it relates to band saw?: Centering the blade on the pulleys 73. What characteristics differentiate styles of band saw blades?: Material, width, gauge, pitch, type of tooth 74. What is the advantage of using a bimetal blade in a band saw?: Greater wear and heat resistance, faster cutting and better durability 75. Where should you place the weld when you are welding band saw blades?- : Bottom of a tooth gullet 76. The width of the saw blade cut in the workpiece is called:: kerf 77. The purpose of draw filing is to:: produces a smooth and flat surface 78. The removable serrated jaws on a bench vise made from:: aluminum
93. If a high-speed steel hand tap breaks into a hole, one way to remove it is:: with an electrical discharge machine 94. You have to choose between 4 steel rods to cut 1/2- 13 UNC 2A thread with an adjustable split die. What diameter rod would you use?: 0.497" 95. What is the correct tool to turn a die?: Die stock 96. The cutting action of a hand broach is performed by a series of successive teeth, each protruding:: 0.003" further that the preceding tooth 97. Hand reamers must be rotated:: Clockwise 98. Pullers are used to:: remove bearings, hubs and sprockets 99. When using a puller or press and removing a bearing from a shaft what should you do?: Inspect and clean shaft area 100. Before working around a load that has been raised with a hydraulic jack:: the load must be blocked 101. If a milling machine is shit down for repair:: Lock out the main breaker box 102. Why is pressurized air NOT a good method of removing metal chips from hard to reach places on a milling machine?: It can get jammed under the ways or caught in the spindle taper. They can also cause burns/infections 103. What makes a universal horizontal milling machine different from a
plain horizontal milling machine: The table can be swivelled
104. When would you tighten the backlash eliminator: When climb milling 105. As a general rule, the maximum depth of cut for an endmill is equal to:: 1/2 the diameter of the endmill 106. You can use V-blocks on a milling machine: True 107. The purpose of the overarm is to support the , which in turn supports the : arbor supports, free end of arbor
116. Why would you use parallels under a workpiece when plunge cutting a through-hole?: to prevent cutting in the table 117. Why should you clean an lightly oil milling machine tables?: To prevent rusting which causes loss of accuracy 118. Why should you store end mills separate from one another?: Cutting edges could chip and wear 119. What is climb milling?: Feeds into the rotation of the cutter and bites into the material pushing it down and into the table 120. What is conventional milling?: Feeds against the rotation of the cutter and tends to lift the workpiece 121. What is the level of accuracy for a plate protractor?: Within 1 degree 122. What is the level of accuracy for a universal bevel protractor?: 5 minutes of a degree 123. How many minutes are in a degree?: 60 minutes 124. What is a vernier scale?: Compares 2 sets of graduations to magnify the accuracy of the measuerment 125. What does a dial caliper use to move its pointer around the face of a dial: Rack and pinion
126. What is the construction of a micrometer?: 1. Anvil
external thread
145. The thread angle from an American National Acme Thread is:: 29 degress 146. A no go ring gauge is easliy identified by:: annular ring on the knurled surface 147. Thread comparison gauges use as a basis for thread size: -
Pitch diameter
148. Rolled threads are advantageous over machined threads because:: They have increased tensile strength They produce a burnished thread finish They have better wear resistance which reduces fatigue and shear problems 149. What does API stand for: American Petroleum Institue 150. What kind of threads do Acme threads have?: 29 degree angle and the root and crests are flat 151. Hex set screws may sometimes be doubled up: True 152. What are cap screws made of?: High tensile steel 153. How is a Woodruff key sized?: First 2 numbers are multiplied by 1/32"and second set of numbers are multiplied by 1/8" 154. A rivet is:: a permanent fastener 155. What is the taper per foot of a tapered gib head key?: 1/8" per foot
shank must be mounted in the spindle. How should you secure the drill in the spindle?: Use a drill socket
166. To remove a tapered shank twist drill from the drill press spindle, use a:: drill drift 167. When using a sensitive drill press, what should you do as the drill breaks through the workpiece?: Ease up on the pressure 168. The included point angle of a countersunk hole for most flathead screws is:: 82 degrees 169. Which type of machine tap pushes the hip out ahead of the tap?: Spiral pint (gun) tap 170. The lip relief (clearance) angle of a drill should be:: 8 - 12 degrees 171. A general-purpose drill bit for drilling most metals has an included point angle of:: 118 degrees 172. The hand drill is quicker and more versatile than any drill press for:: - drilling small non-vertical holes 173. Electric hand drills are limited by:: the amount of feed pressure (and rpm) that can apply to large-diameter drills 174. How are step drills used?: Used to drill and then countersink
175. You must used the correct RPM when using a center drill or you will dull/break the bit: True 176. What speed should a countersink and counterbore be set at?: Approxi- mately 1/4 of what you would use for a drill 177. What are the drill point included angles for soft, general and hard mate- rial?: 60 - 90 degrees for soft, 118 degrees for general and 150 degrees forhard material 178. What are 2 dial reading styles?: Balanced and continuous 179. What are 3 types of dial indicators?: Bottom plunger, test indicators and back plunger 180. What are dial bore gauges?: Comparison measurement tool 181. What is the advantage of a dial bore gauge?: You can move it to various positions with making any adjustments 182. Copper sulphate layout solution should be used on:: Ferrous metals 183. When angles are laid out with a bevel protractor, the accuracy attainable is:: +/- 0.5 degrees (30mins) 184. The surface gauge is used:: to layout lines parallel to an edge 185. For maximum reliability when setting dividers to a dimension on a