
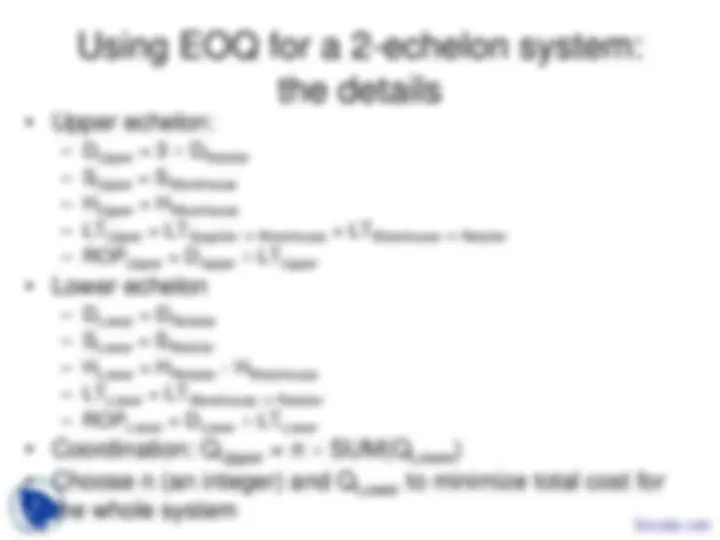
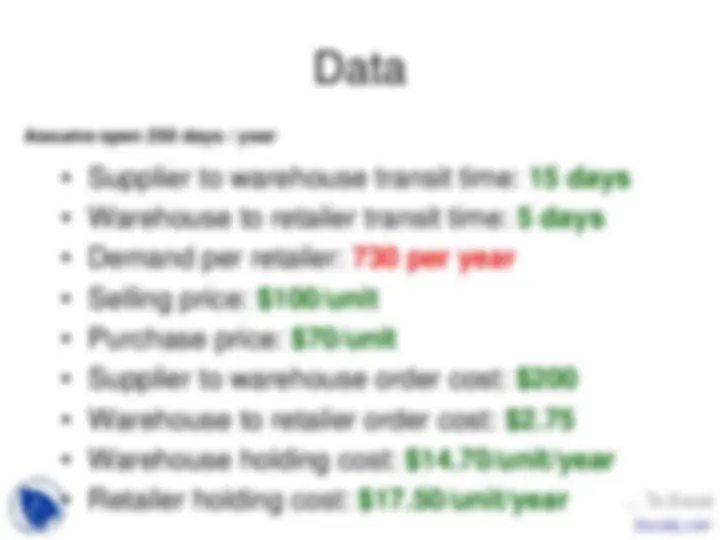
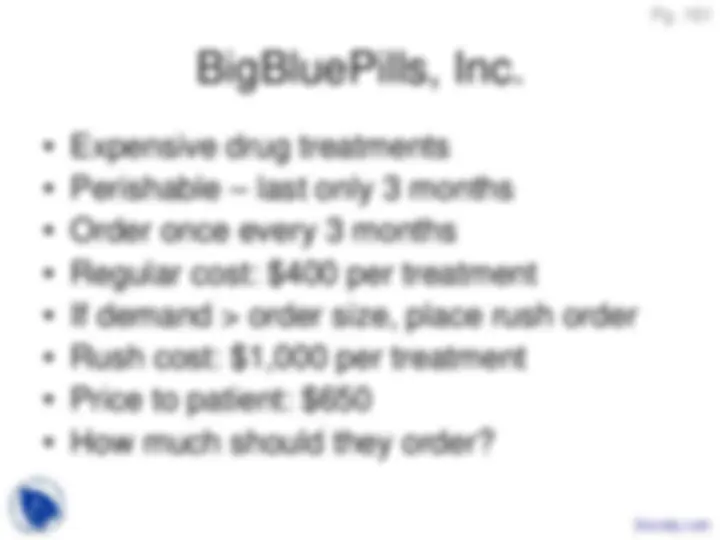


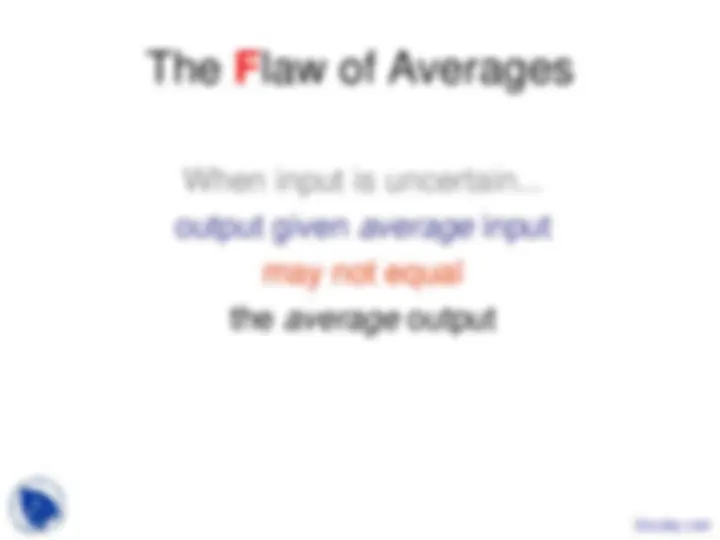
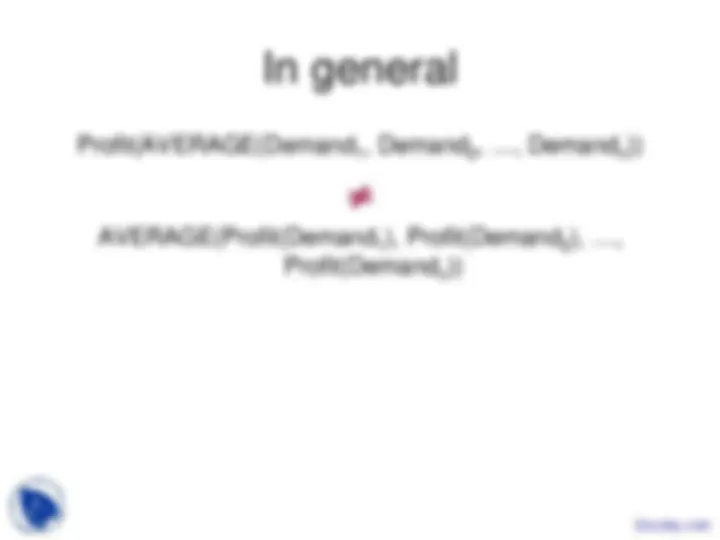
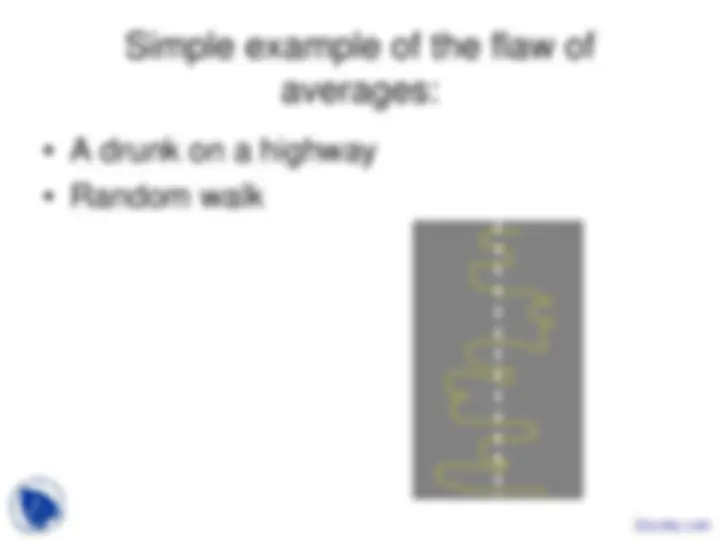
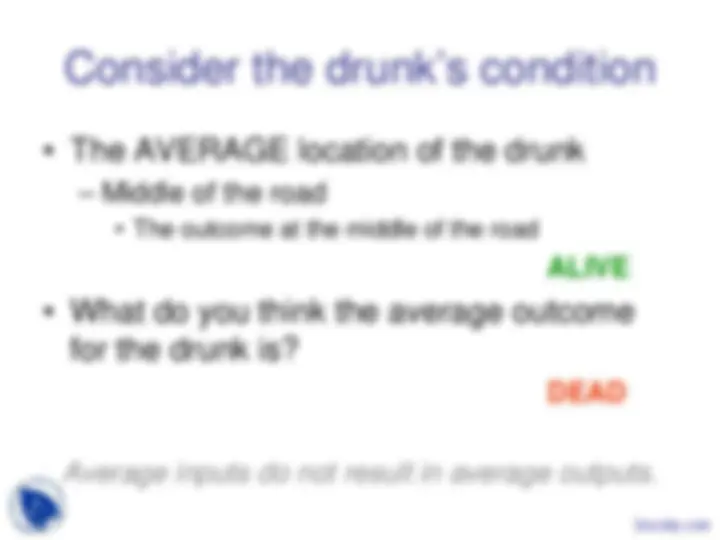
Study with the several resources on Docsity
Earn points by helping other students or get them with a premium plan
Prepare for your exams
Study with the several resources on Docsity
Earn points to download
Earn points by helping other students or get them with a premium plan
Community
Ask the community for help and clear up your study doubts
Discover the best universities in your country according to Docsity users
Free resources
Download our free guides on studying techniques, anxiety management strategies, and thesis advice from Docsity tutors
Methods for finding optimal inventory policies using simulation and eoq models. It covers the application of eoq in multi-echelon systems, coordination between echelons, and the importance of considering supplier and retailer transit times, demand data, and holding costs. The document also discusses the concept of the 'newsvendor problem' and the limitations of relying solely on average inputs.
Typology: Slides
1 / 15
This page cannot be seen from the preview
Don't miss anything!
A&E Noise example Methods for finding good inventory policies:
Assume open 250 days / year
… To Excel
Pg. 161
Average 18. Stdev 6. min 5. max 34.
Category bin Frequency <=5 5 1 6 - 10 10 3 11 - 15 15 3 16 - 20 20 5 21 - 25 25 6 26 - 30 30 1
30 1
0
1
2
3 4 5
6 7
<=5 6 - 10 11 - 1516 - 2021 - 2526 - 30> 30 Quarterly demand
Frequency
When input is uncertain... output given average input may not equal the average output
Profit(AVERAGE(Demand 1 , Demand 2 , …, Demand (^) n))
AVERAGE(Profit(Demand 1 ), Profit(Demand 2 ), …, Profit(Demand (^) n ))