
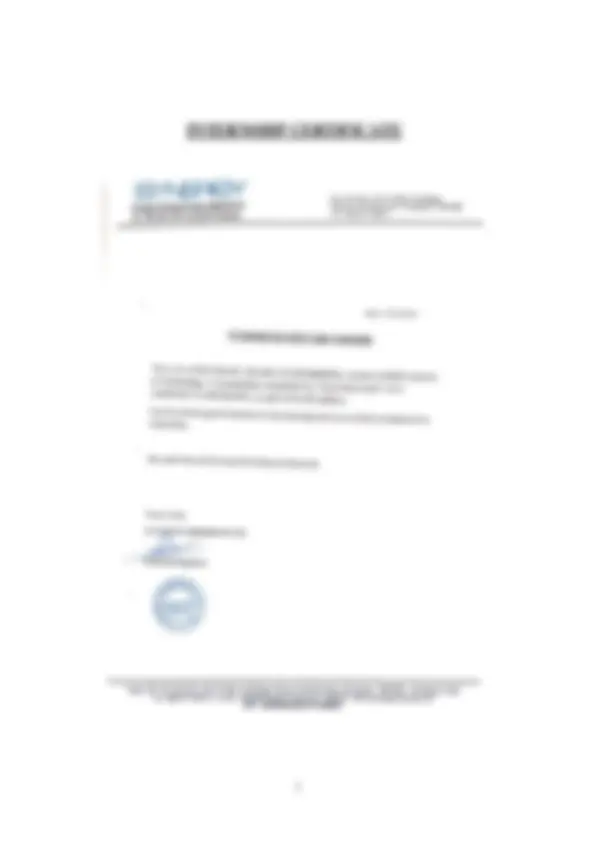
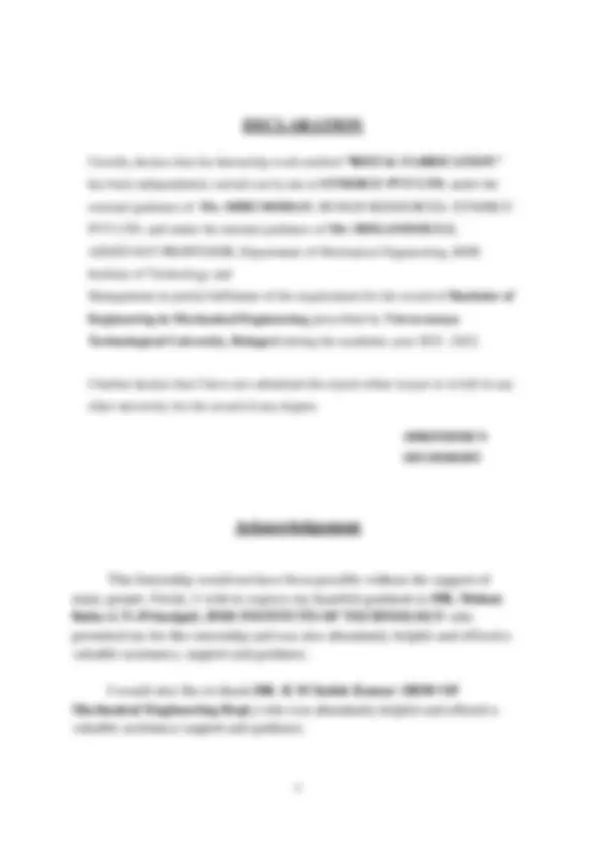
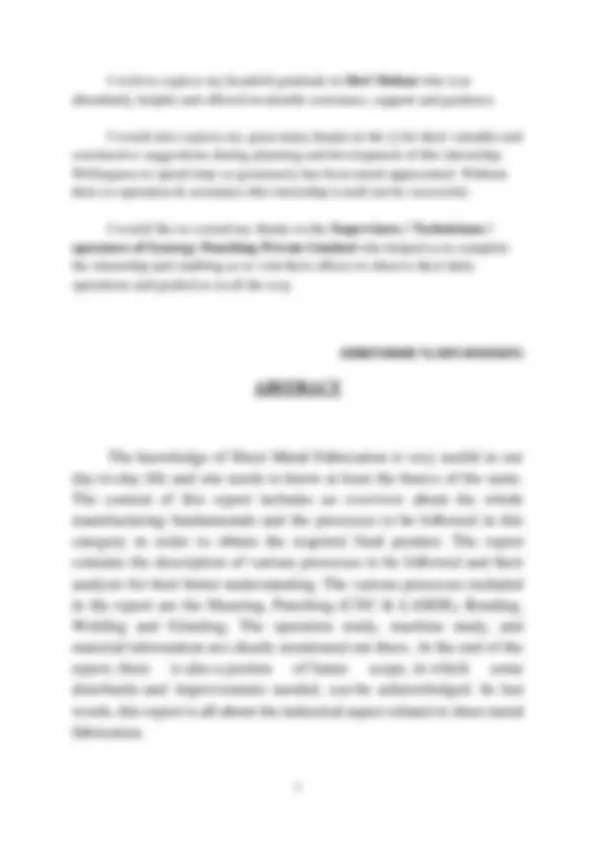
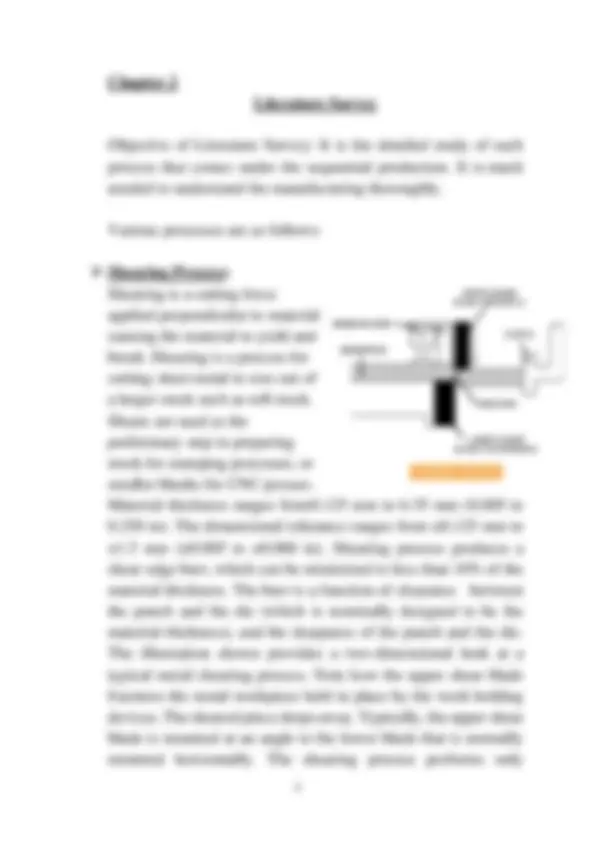
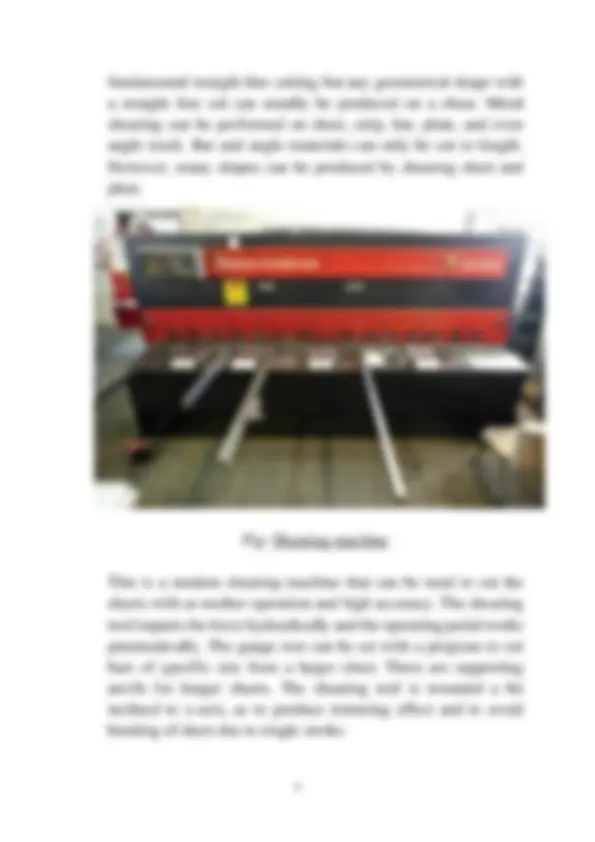
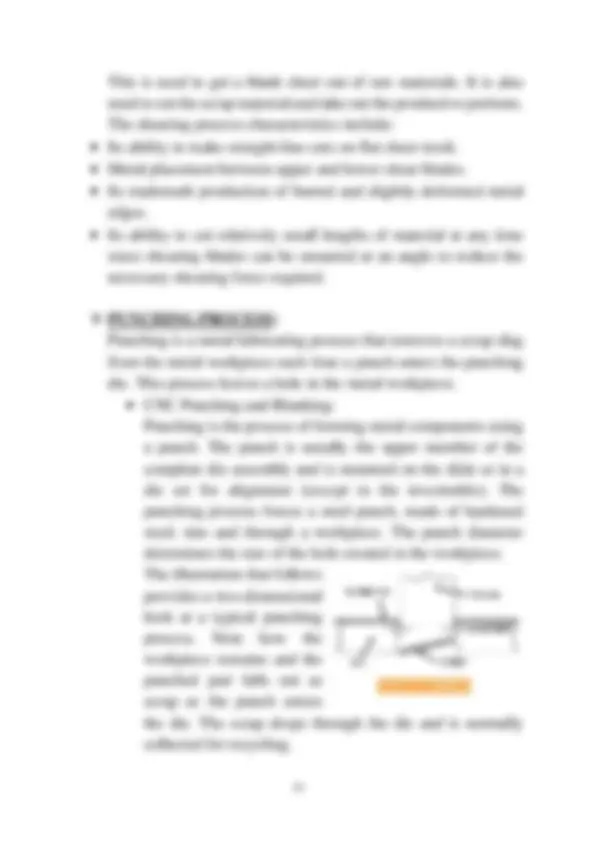
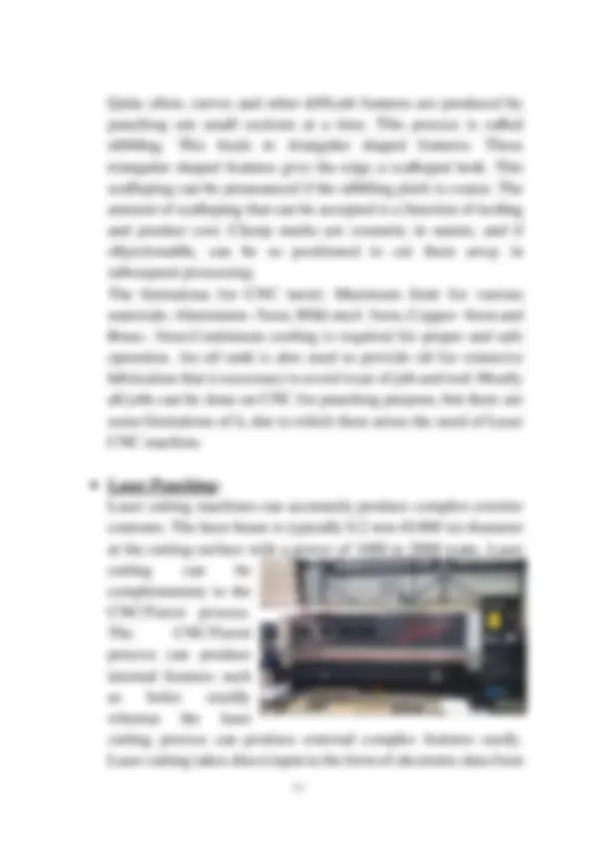
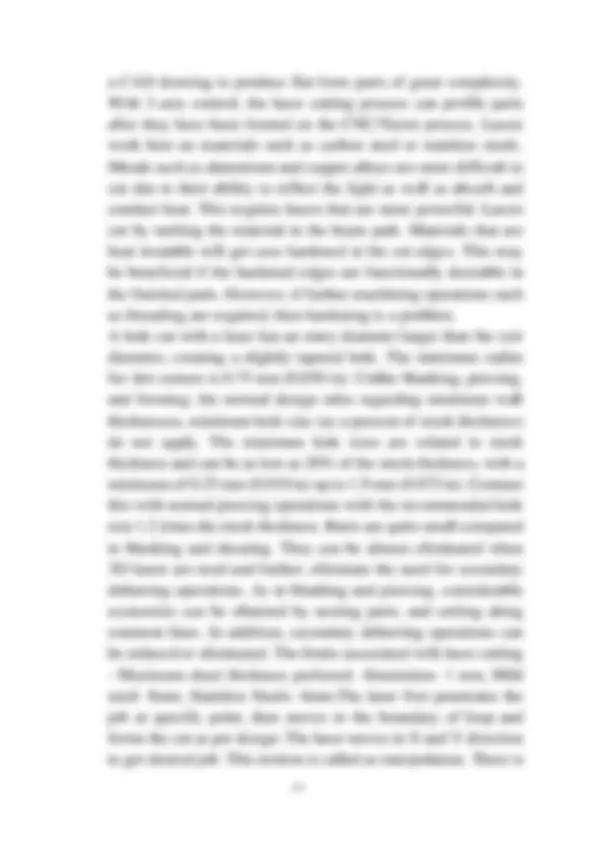
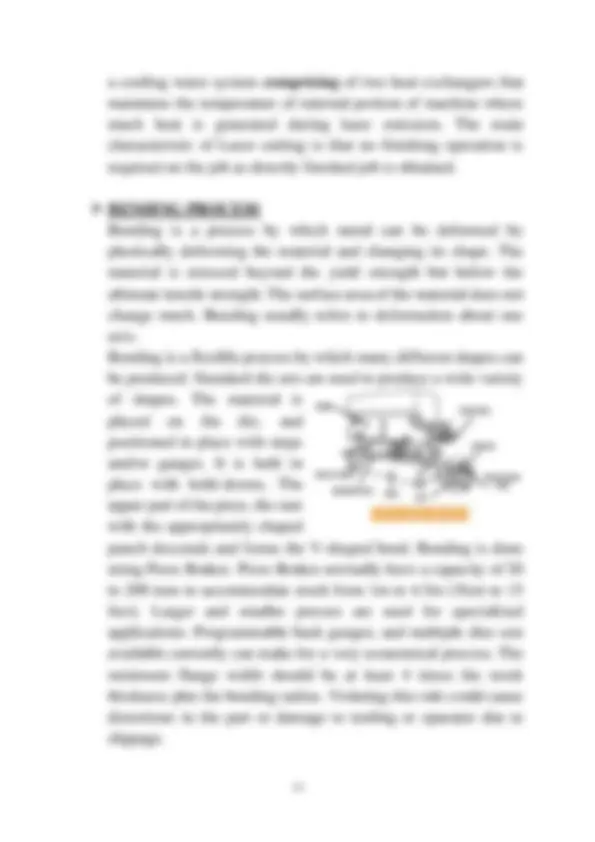
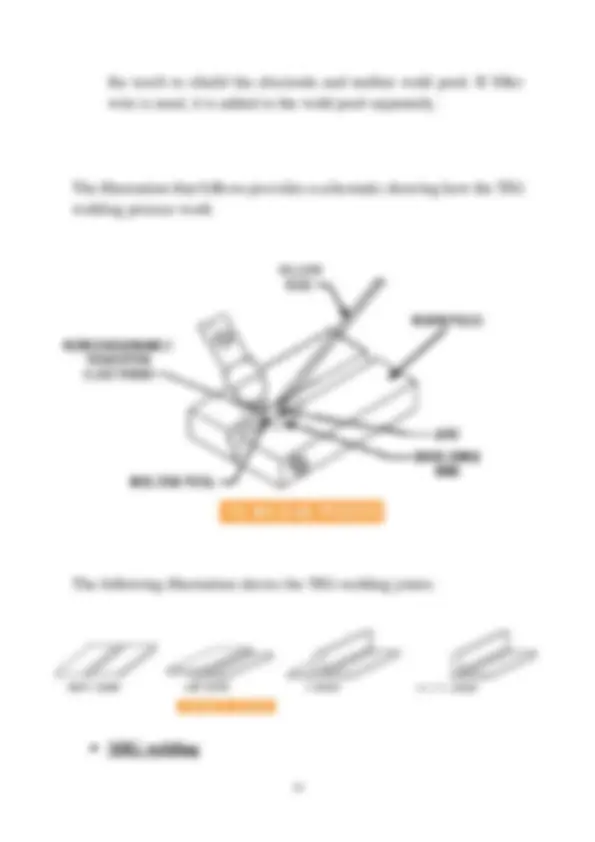
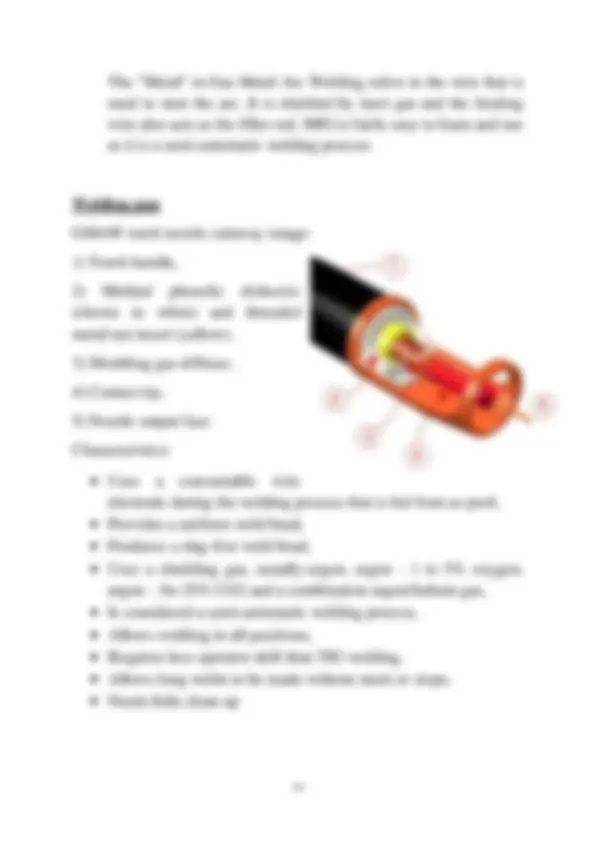
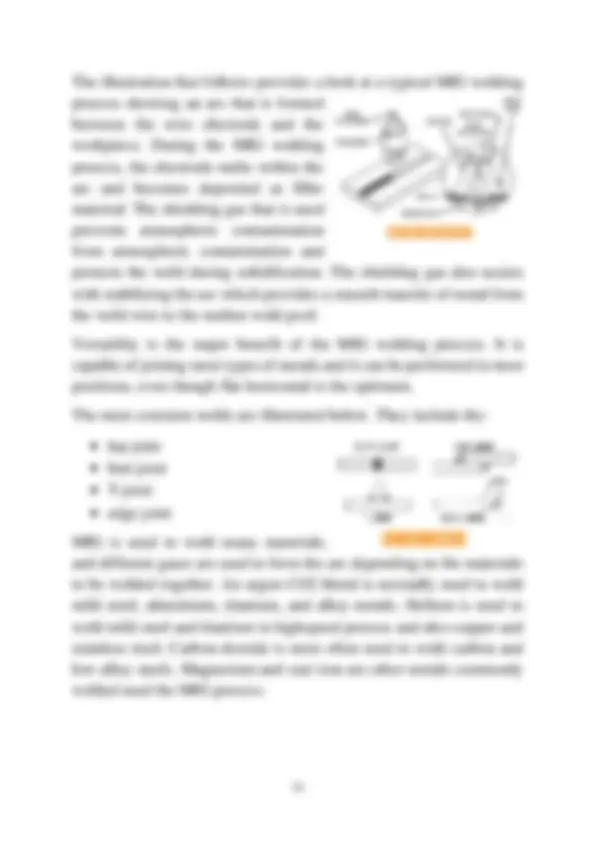
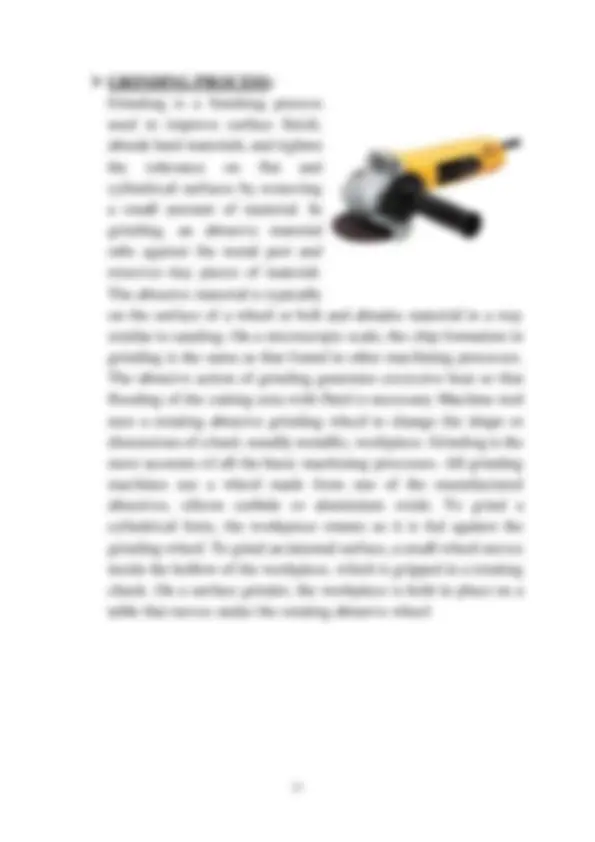
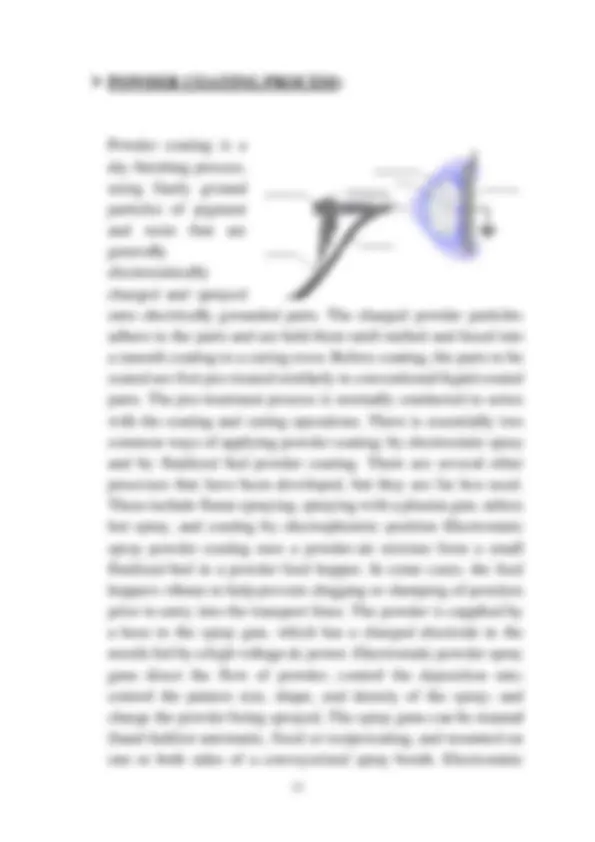
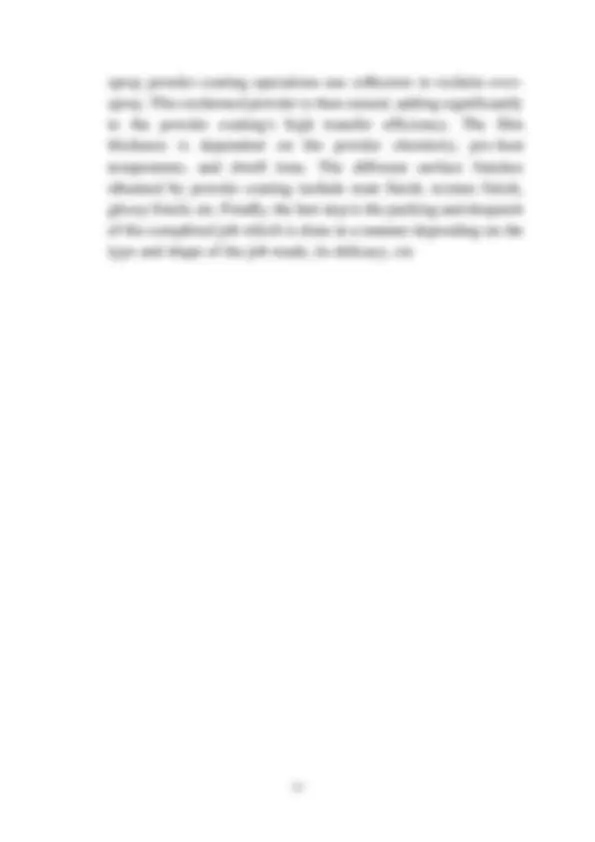
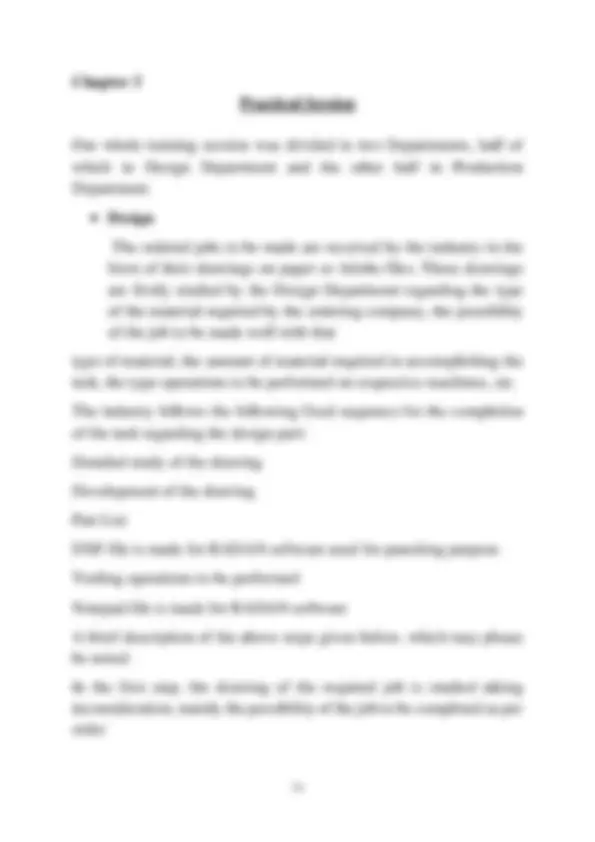
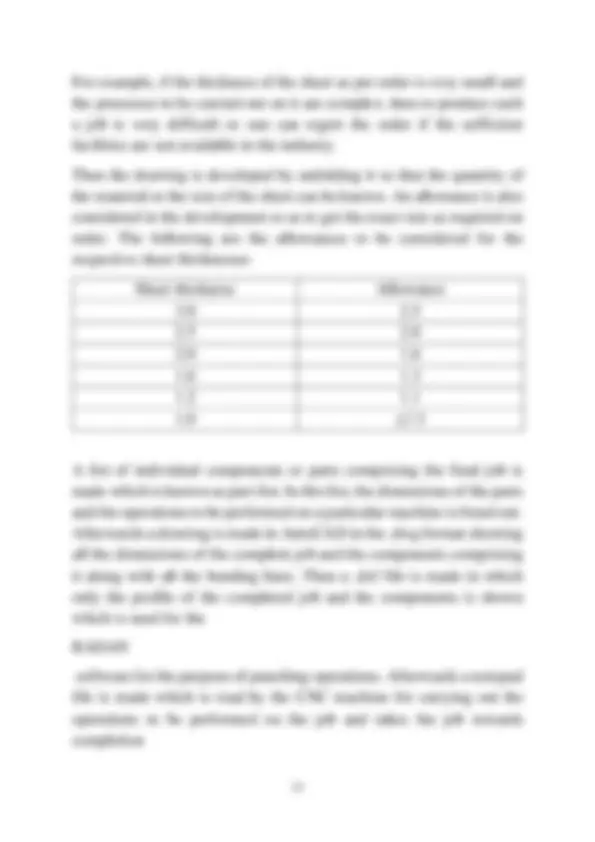
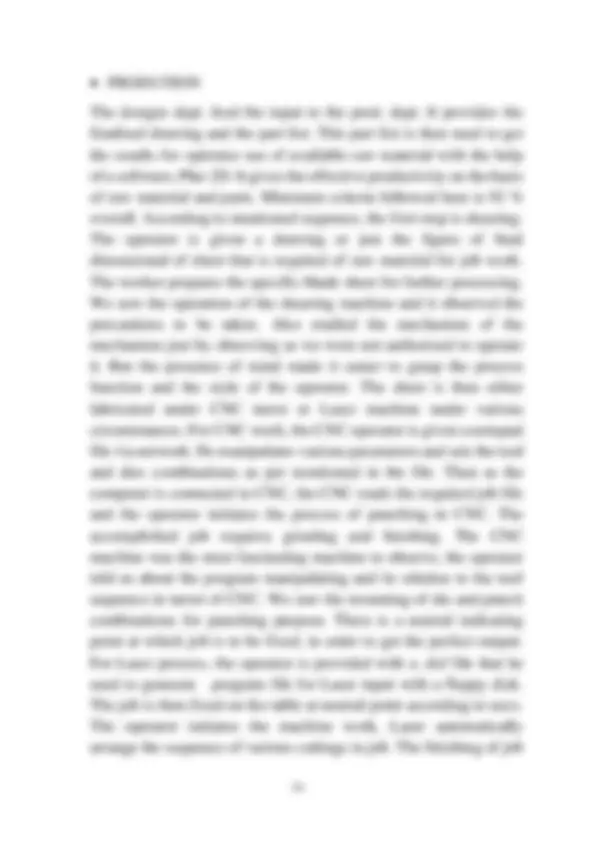
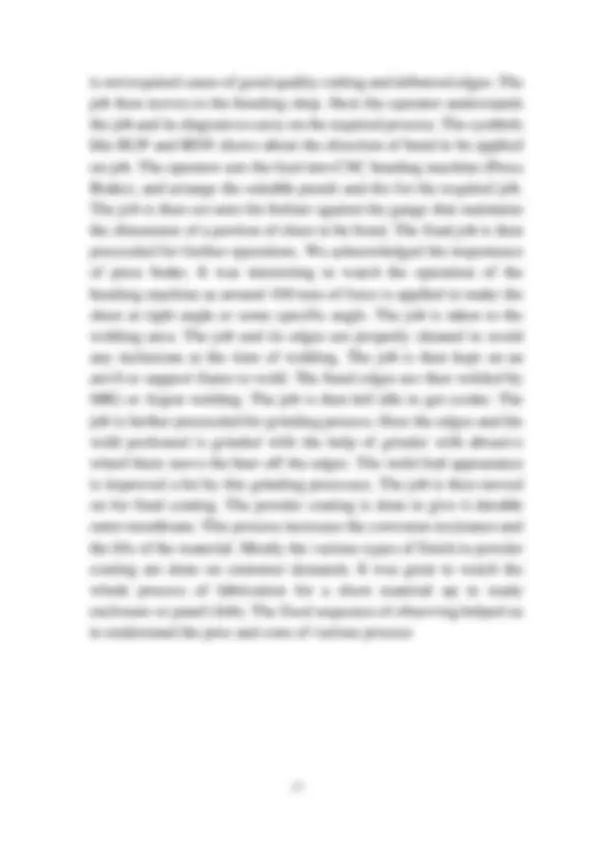
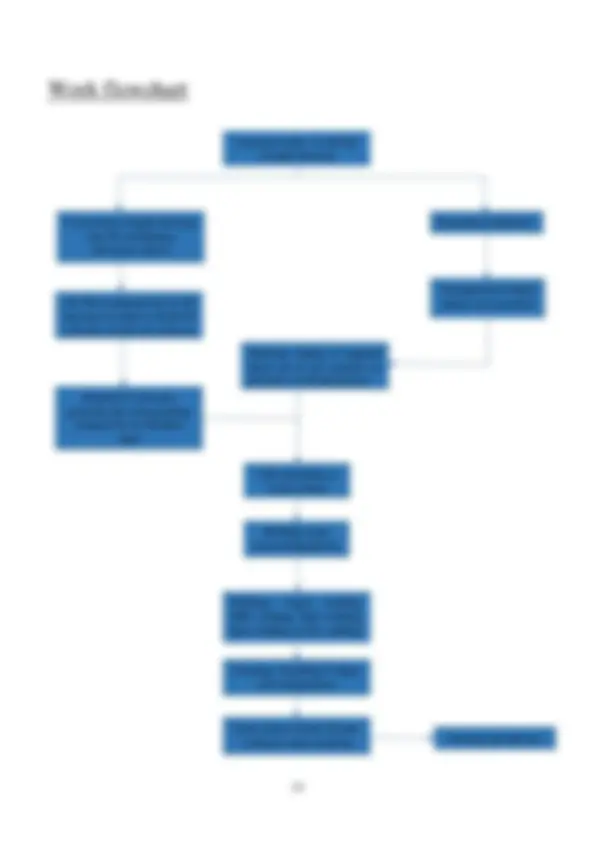
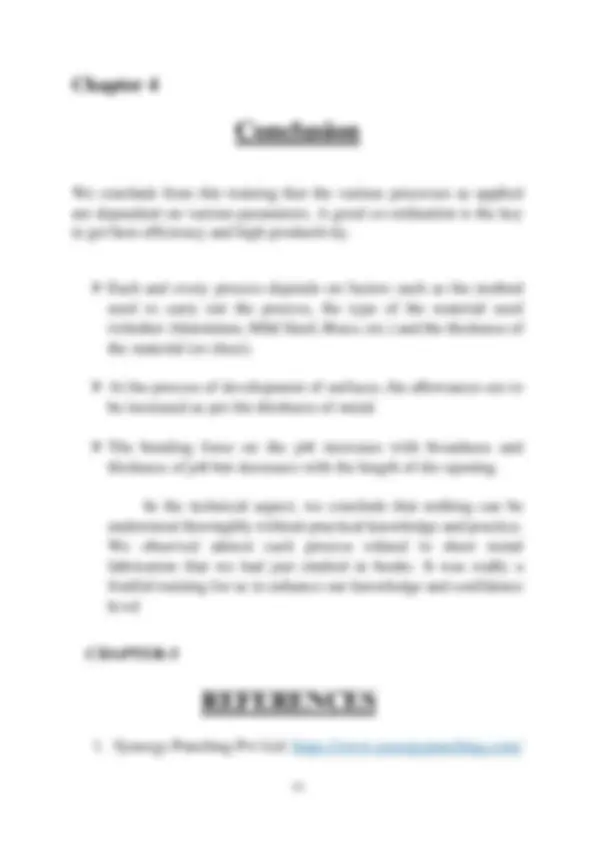
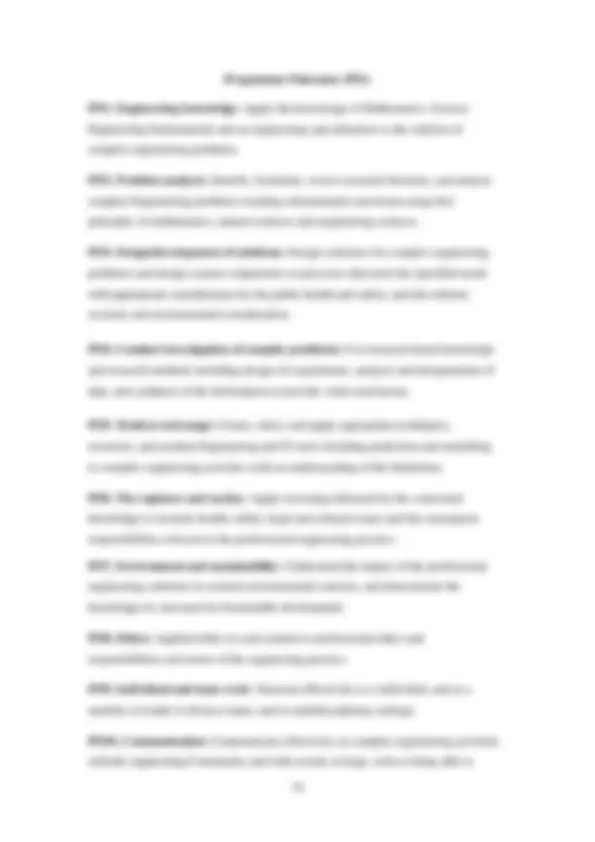
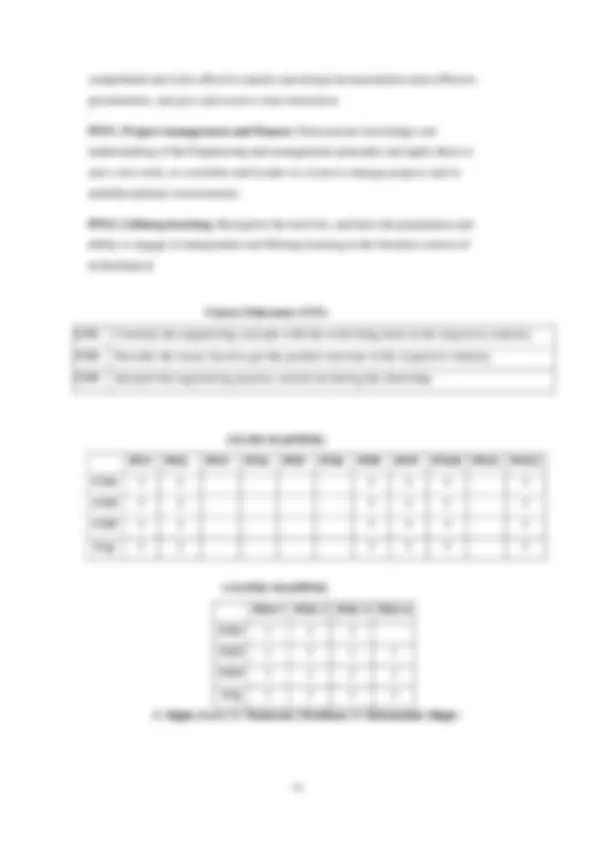
Study with the several resources on Docsity
Earn points by helping other students or get them with a premium plan
Prepare for your exams
Study with the several resources on Docsity
Earn points to download
Earn points by helping other students or get them with a premium plan
Community
Ask the community for help and clear up your study doubts
Discover the best universities in your country according to Docsity users
Free resources
Download our free guides on studying techniques, anxiety management strategies, and thesis advice from Docsity tutors
A certification of completion for an internship report on various metal fabrication processes, including shearing, punching (CNC & Laser), bending, welding, grinding, and powder coating. The report covers the processes' principles, characteristics, and limitations. It is a partial fulfillment of a Bachelor of Engineering in Mechanical Engineering degree at B.M.S. Institute of Technology and Management, under the guidance of Mr. Sriganesh.T.G.
What you will learn
Typology: Summaries
1 / 31
This page cannot be seen from the preview
Don't miss anything!
VISVESVARAYA TECHNOLOGICAL UNIVERSITY JNANASANGAMA, BELAGAVI - 590018, KARNATAKA An Internship Report on METAL FABRICATION Submitted in partial fulfillment of the requirement for the award of degree BACHELOR OF ENGINEERING IN MECHANICAL ENGINEERING Submitted by: SHRINIDHI N 1BY18ME0 55 VIII Semester Internship carried at SYNERGY PUNCHING PVT LTD. #A3 & A4, 14th A Cross,, Peenya, Bengaluru, Karnataka 560058 Internal Guide External Guide Mr. Sriganesh T. G Mr.Shri Mohan Assistant Professor Human resources Director Mechanical Department Synergy Punching Pvt Ltd BMS Institute of Technology & Management
(Affiliated to Visvesvaraya Technological University, Belagavi, Karnataka) #6443, Doddaballapura Main Road, Avalahalli, Yelahanka, Bengaluru- 560064 DEPARTMENT OF MECHANICAL ENGINEERING CERTIFICATE This is to certify that the Internship Report on “MATAL FABRICATION” submitted by SHRINIDHI N bearing USN:1BY18ME 055 respectively is a bonafide student of B.M.S. Institute of Technology And Management, has successfully completed the Internship programme in partial fulfillment for the award of Bachelor of Engineering in Mechanical Engineering prescribed by Visvesvaraya Technological University, Belagavi during the academic year 2021
I hereby declare that the Internship work entitled “METAL FABRICATION” has been independently carried out by me at SYNERGY PVT LTD , under the external guidance of Mr. SHRI MOHAN , HUMAN RESOURCES, SYNERGY PVT LTD. and under the internal guidance of Mr. SRIGANESH.T.G , ASSISTANT PROFFESOR, Department of Mechanical Engineering, BMS Institute of Technology and Management in partial fulfilment of the requirement for the award of Bachelor of Engineering in Mechanical Engineering prescribed by Visvesvaraya Technological University, Belagavi during the academic year 2021 - 2022. I further declare that I have not submitted this report either in part or in full in any other university for the award of any degree. SHRINIDHI N 1BY18ME0 55 Acknowledgement This Internship would not have been possible without the support of many people. Firstly, I wish to express my heartfelt gratitude to DR. Mohan Babu G N (Principal), BMS INSTITUTE OF TECHNOLOGY who permitted me for this internship and was also abundantly helpful and offered a valuable assistance, support and guidance. I would also like to thank DR. K M Satish Kumar (HOD OF Mechanical Engineering Dept.) who was abundantly helpful and offered a valuable assistance support and guidance.
I wish to express my heartfelt gratitude to Shri Mohan who was abundantly helpful and offered invaluable assistance, support and guidance. I would also express my great many thanks to the [] for their valuable and constructive suggestions during planning and development of this internship. Willingness to spend time so generously has been much appreciated. Without their co-operation & assistance this internship would not be successful. I would like to extend my thanks to the Supervisors / Technicians / operators of Synergy Punching Private Limited who helped us to complete the internship and enabling us to visit their offices to observe their daily operations and guided us in all the way. SHRINIDHI N(1BY18ME055) ABSTRACT The knowledge of Sheet Metal Fabrication is very useful in our day-to-day life and one needs to know at least the basics of the same. The content of this report includes an overview about the whole manufacturing fundamentals and the processes to be followed in this category in order to obtain the required final product. The report contains the description of various processes to be followed and their analysis for their better understanding. The various processes included in the report are the Shearing, Punching (CNC & LASER), Bending, Welding and Grinding. The operation study, machine study, and material information are clearly mentioned out there. At the end of the report, there is also a portion of future scope, in which some drawbacks and improvements needed, can be acknowledged. In last words, this report is all about the industrial aspect related to sheet metal fabrication.
Chapter 1 Company Profile A. Name: Synergy Punching Pvt. Ltd. B. Address: #A3 & A4, 14th A Cross, Peenya, Bengaluru, Karnataka-
C. Products: Sheet Metal components, Kiosk Enclosures, Lazer Cutting Services, Retail fixtures and ATM Enclosures. D. Dealing : The company deals with many industries all over India. Medha Servo Drives, BHEL Ltd., Electronic Stores (Samsung, Xiaomi, LG, Vivo etc.) E. Process sequence: The industry follows a fixed sequence in order to complete a job. There are some corresponding steps, as given below:
Chapter 2 Literature Survey Objective of Literature Survey: It is the detailed study of each process that comes under the sequential production. It is much needed to understand the manufacturing thoroughly. Various processes are as follows: ➢ Shearing Process: Shearing is a cutting force applied perpendicular to material causing the material to yield and break. Shearing is a process for cutting sheet metal to size out of a larger stock such as roll stock. Shears are used as the preliminary step in preparing stock for stamping processes, or smaller blanks for CNC presses. Material thickness ranges from0.125 mm to 6.35 mm (0.005 to 0.250 in). The dimensional tolerance ranges from ±0.125 mm to ±1.5 mm (±0.005 to ±0.060 in). Shearing process produces a shear edge burr, which can be minimized to less than 10% of the material thickness. The burr is a function of clearance between the punch and the die (which is nominally designed to be the material thickness), and the sharpness of the punch and the die. The illustration shown provides a two-dimensional look at a typical metal shearing process. Note how the upper shear blade fractures the metal workpiece held in place by the work holding devices. The sheared piece drops away. Typically, the upper shear blade is mounted at an angle to the lower blade that is normally mounted horizontally. The shearing process performs only
This is used to get a blank sheet out of raw materials. It is also used to cut the scrap material and take out the productive portions. The shearing process characteristics include:
Fig: CNC turret machine used for punching purpose The Computer Numerical Control (CNC) fabrication process offers flexible manufacturing runs without high capital expenditure dies and stamping presses. High volumes are not required to justify the use of this equipment. Tooling is mounted on a turret which can be as little as 10 sets to as much as100 sets. This turret is mounted on the upper part of the press, which can range in capacity from 10 tons to 100 tons in capacity. The turret travels on lead screws, which travel in the X and Y direction and are computer controlled. Alternatively, the workpiece can travel on the leadscrews, and move relative to the fixed turret. The tooling is located over the sheet metal, the punch is activated, and performs the operation, and the turret is indexed to the next location of the workpiece. After the first stage of tooling is deployed over the entire workpiece, the second stage is rotated into place and the whole process is repeated. This entire process is repeated until all the tooling positions of the turret are deployed.
Quite often, curves and other difficult features are produced by punching out small sections at a time. This process is called nibbling. This leads to triangular shaped features. These triangular shaped features give the edge a scalloped look. This scalloping can be pronounced if the nibbling pitch is coarse. The amount of scalloping that can be accepted is a function of tooling and product cost. Clamp marks are cosmetic in nature, and if objectionable, can be so positioned to cut them away in subsequent processing. The limitations for CNC turret: Maximum limit for various materials: Aluminium- 5mm, Mild steel- 3mm, Copper- 4mm and Brass- 3mm.Continuous cooling is required for proper and safe operation. An oil tank is also used to provide oil for extensive lubrication that is necessary to avoid wear of job and tool. Mostly all jobs can be done on CNC for punching purpose, but there are some limitations of it, due to which there arises the need of Laser CNC machine.
a CAD drawing to produce flat form parts of great complexity. With 3-axis control, the laser cutting process can profile parts after they have been formed on the CNC/Turret process. Lasers work best on materials such as carbon steel or stainless steels. Metals such as aluminium and copper alloys are more difficult to cut due to their ability to reflect the light as well as absorb and conduct heat. This requires lasers that are more powerful. Lasers cut by melting the material in the beam path. Materials that are heat treatable will get case hardened at the cut edges. This may be beneficial if the hardened edges are functionally desirable in the finished parts. However, if further machining operations such as threading are required, then hardening is a problem. A hole cut with a laser has an entry diameter larger than the exit diameter, creating a slightly tapered hole. The minimum radius for slot corners is 0.75 mm (0.030 in). Unlike blanking, piercing, and forming, the normal design rules regarding minimum wall thicknesses, minimum hole size (as a percent of stock thickness) do not apply. The minimum hole sizes are related to stock thickness and can be as low as 20% of the stock thickness, with a minimum of 0.25 mm (0.010 in) up to 1.9 mm (0.075 in). Contrast this with normal piercing operations with the recommended hole size 1.2 times the stock thickness. Burrs are quite small compared to blanking and shearing. They can be almost eliminated when 3D lasers are used and further, eliminate the need for secondary deburring operations. As in blanking and piercing, considerable economies can be obtained by nesting parts, and cutting along common lines. In addition, secondary deburring operations can be reduced or eliminated. The limits associated with laser cutting
Fig: Shows a hydraulic press (Bending machine) The machine has a stationary bed or anvil and a slide (ram or hammer) which has a controlled reciprocating motion toward and away from the bed surface and at right angle to it. The slide is guided in the frame of the machine to give a definite path of motion. A form of open-frame single-action press that is comparatively wide between the housings, with a bed designed for holding long, narrow forming edges or dies. Used for bending and forming strip, plate, and sheet (into boxes, panels, roof decks, and so on). Dies used in presses for bending sheet metal or wire parts into various shapes. The work is done by the punch pushing the stock into cavities or depressions of similar shape in the die or by auxiliary attachments operated by the descending punch. Various types
of machinery equipped with two or more rolls to form curved sheet and sections. ➢ WELDING PROCESS: Welding is the process of permanently joining two or more metal parts, by melting both materials. The molten materials quickly cool, and the two metals are permanently bonded. Mainly used welding types are Argon (TIG) welding and MIG welding.
The "Metal" in Gas Metal Arc Welding refers to the wire that is used to start the arc. It is shielded by inert gas and the feeding wire also acts as the filler rod. MIG is fairly easy to learn and use as it is a semi-automatic welding process Welding gun GMAW torch nozzle cutaway image:
The illustration that follows provides a look at a typical MIG welding process showing an arc that is formed between the wire electrode and the workpiece. During the MIG welding process, the electrode melts within the arc and becomes deposited as filler material. The shielding gas that is used prevents atmospheric contamination from atmospheric contamination and protects the weld during solidification. The shielding gas also assists with stabilizing the arc which provides a smooth transfer of metal from the weld wire to the molten weld pool. Versatility is the major benefit of the MIG welding process. It is capable of joining most types of metals and it can be performed in most positions, even though flat horizontal is the optimum. The most common welds are illustrated below. They include the: