
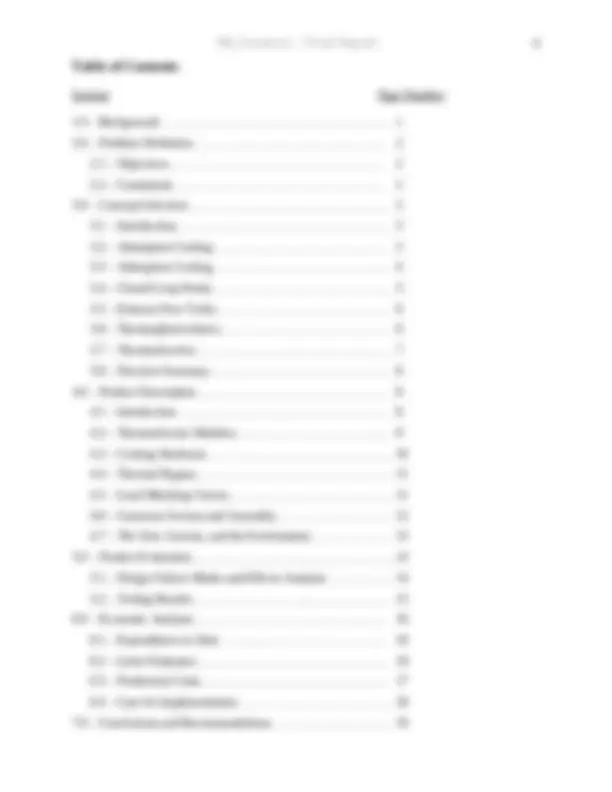
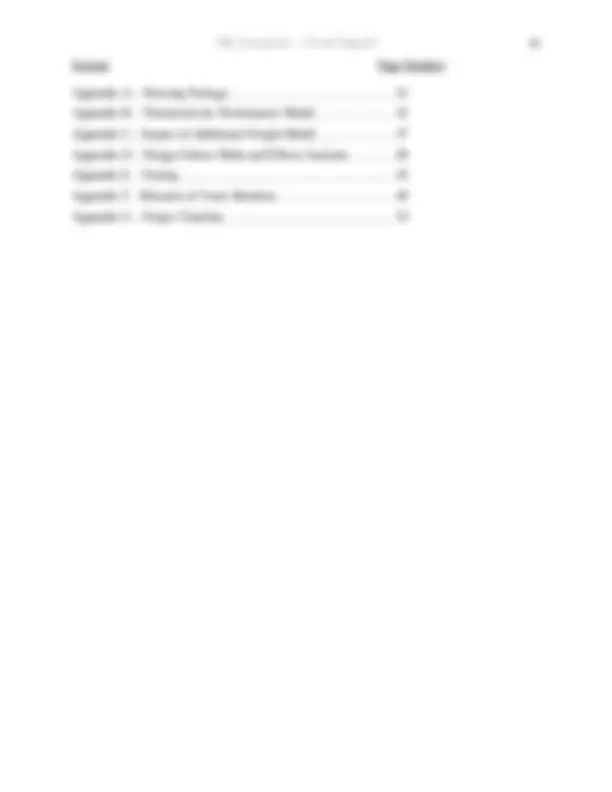
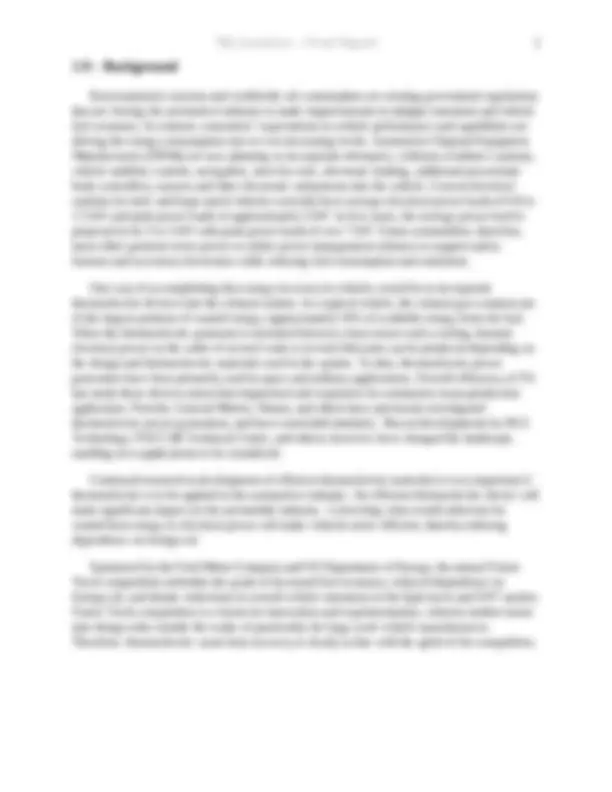
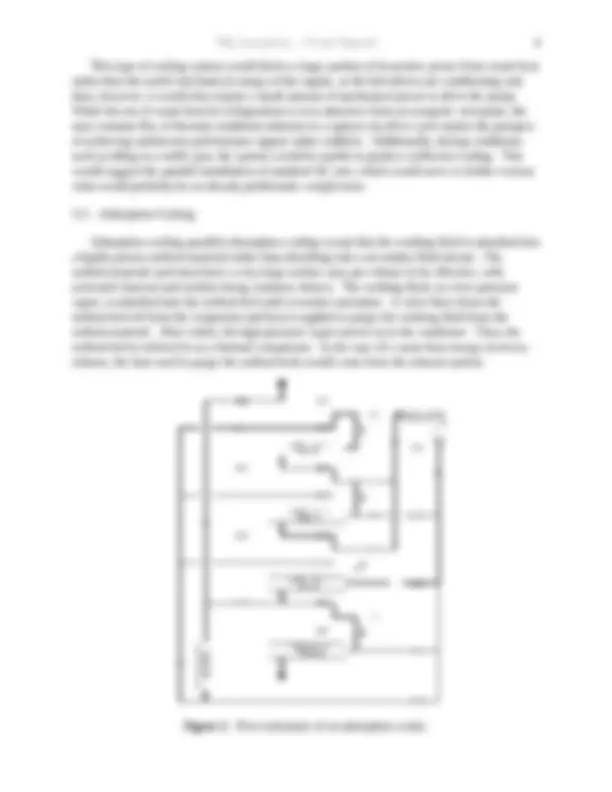
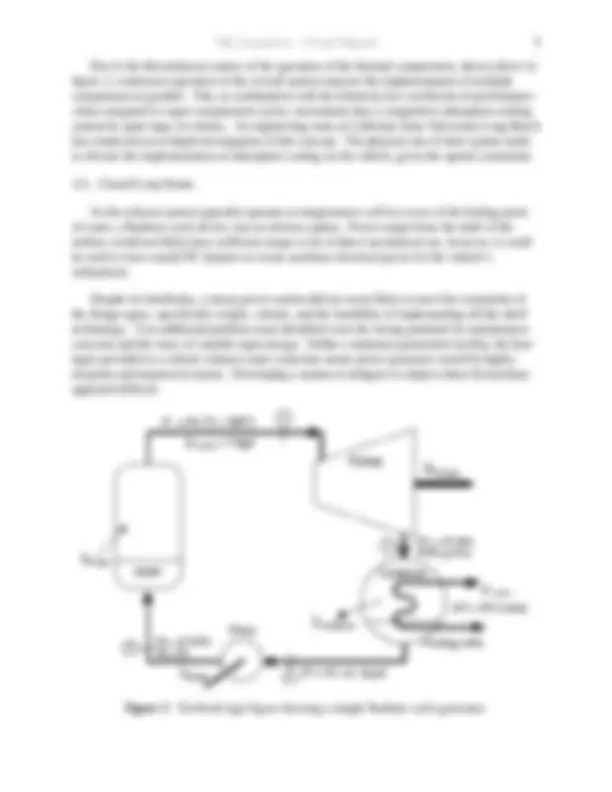
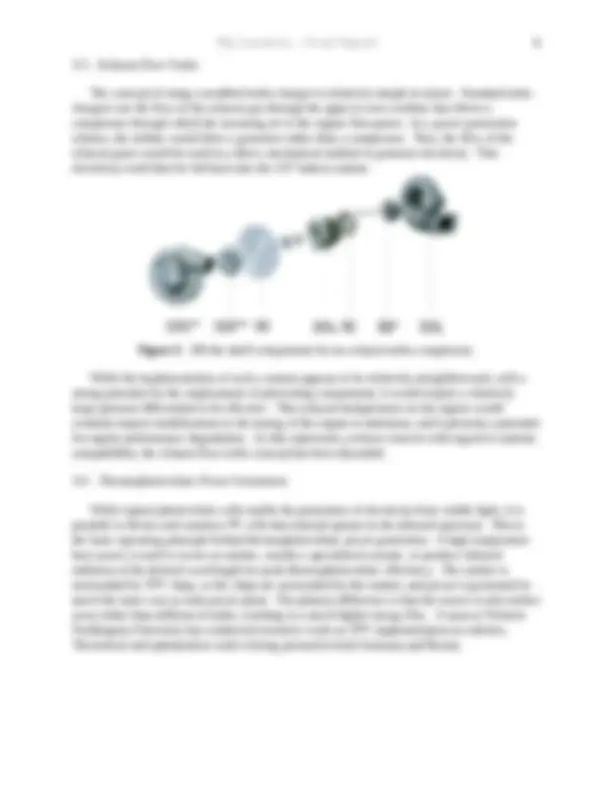
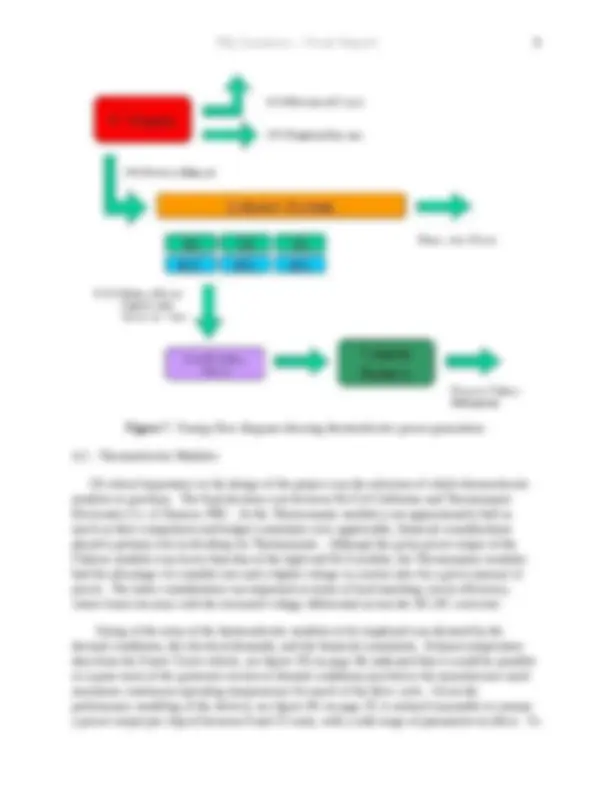
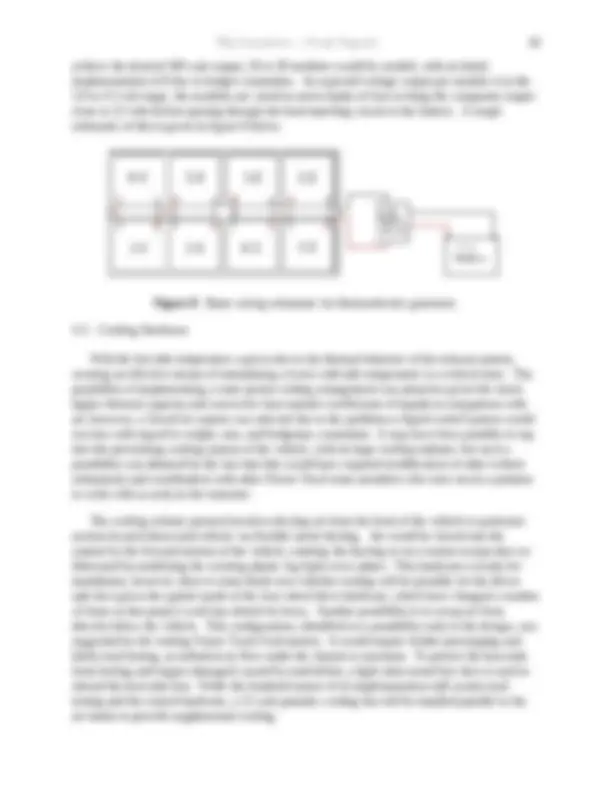
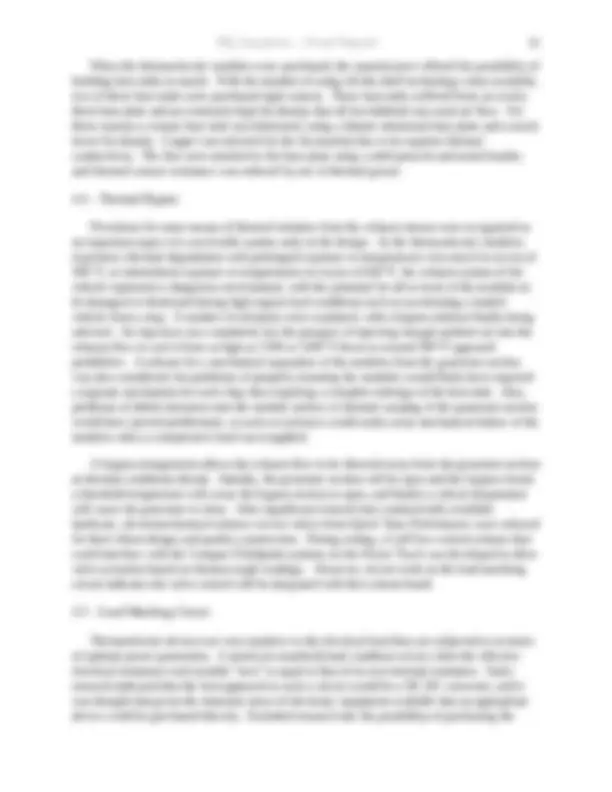
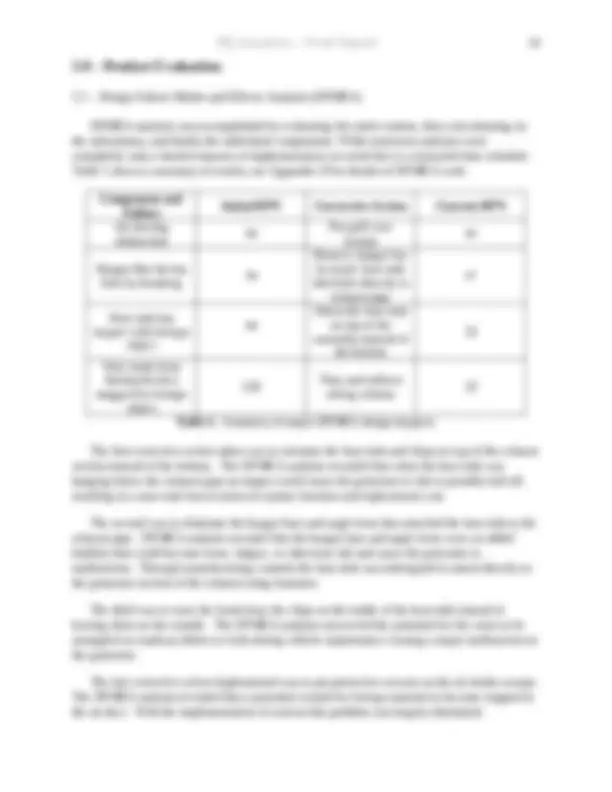
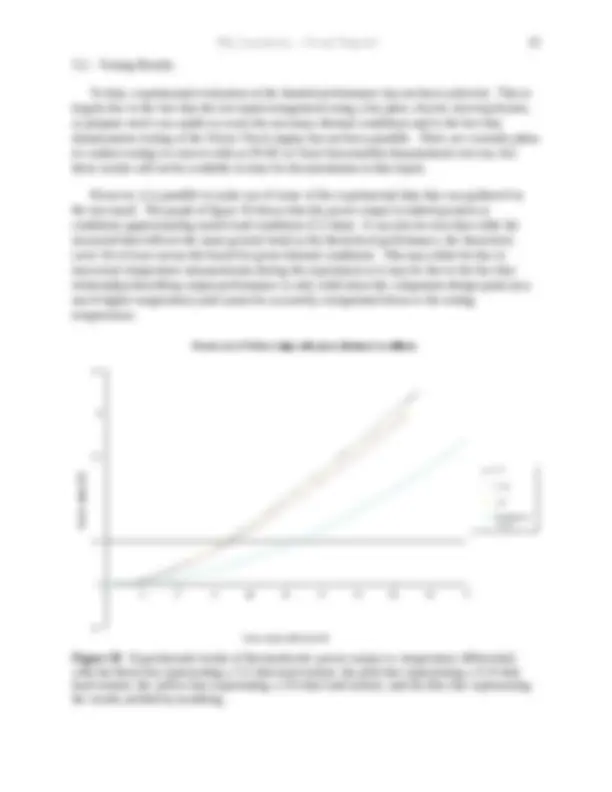
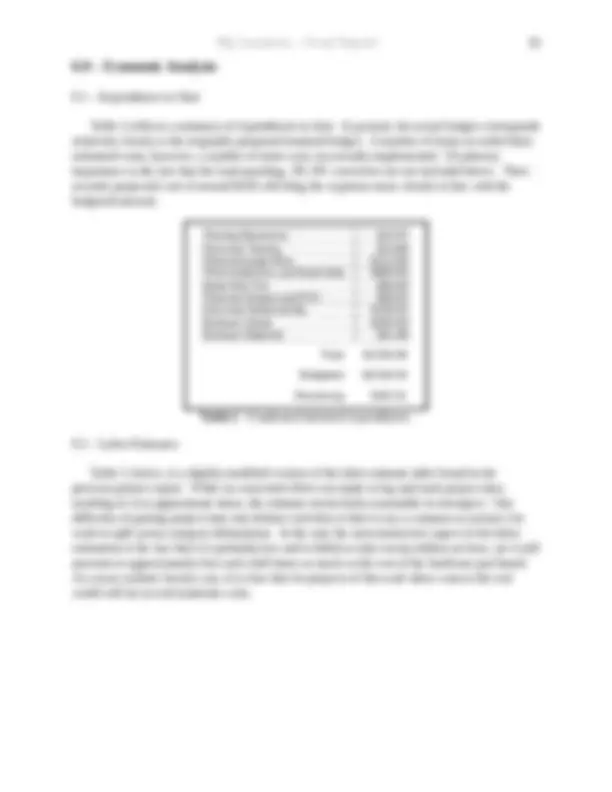
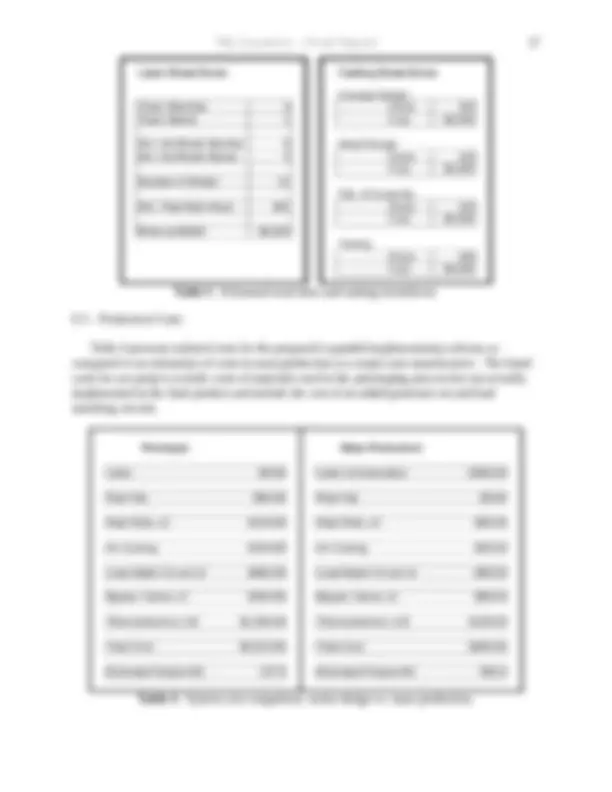
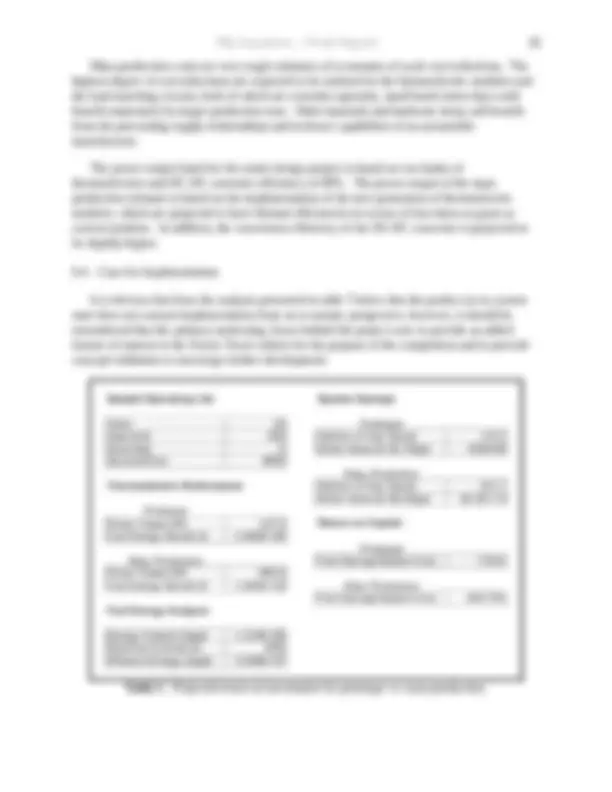
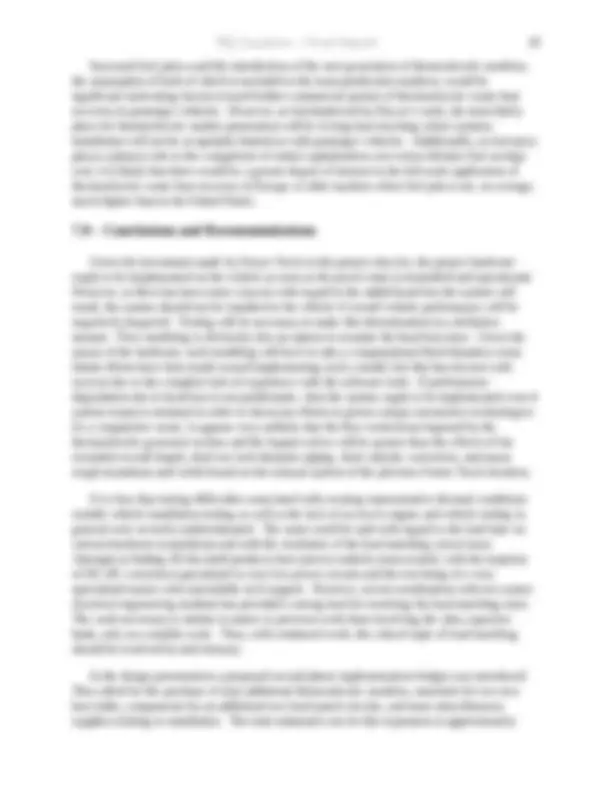
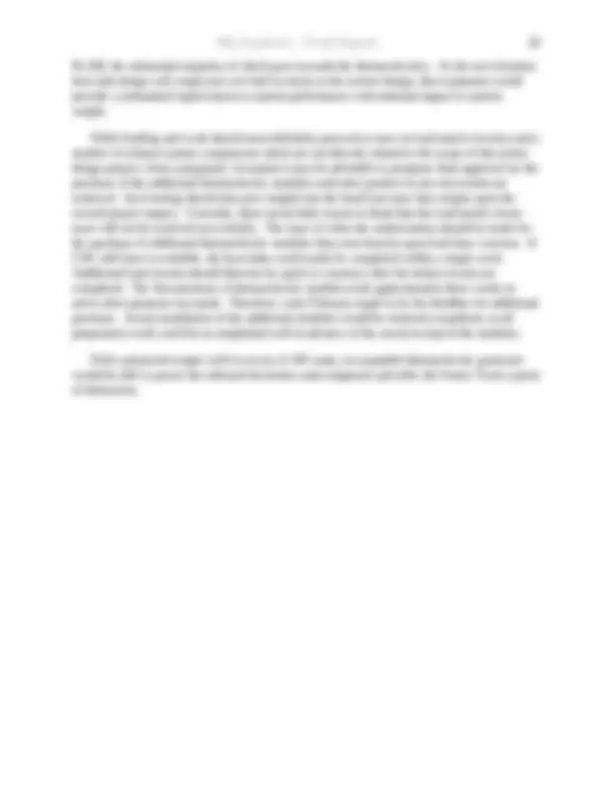
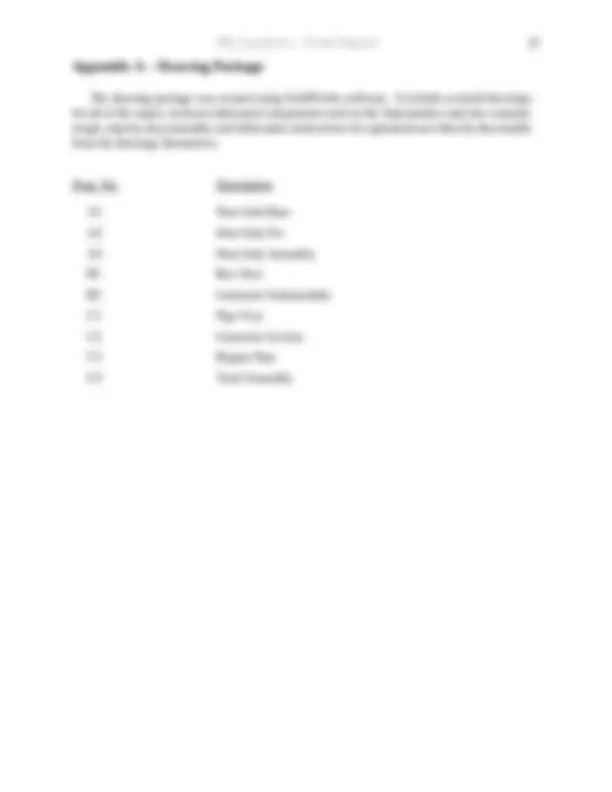
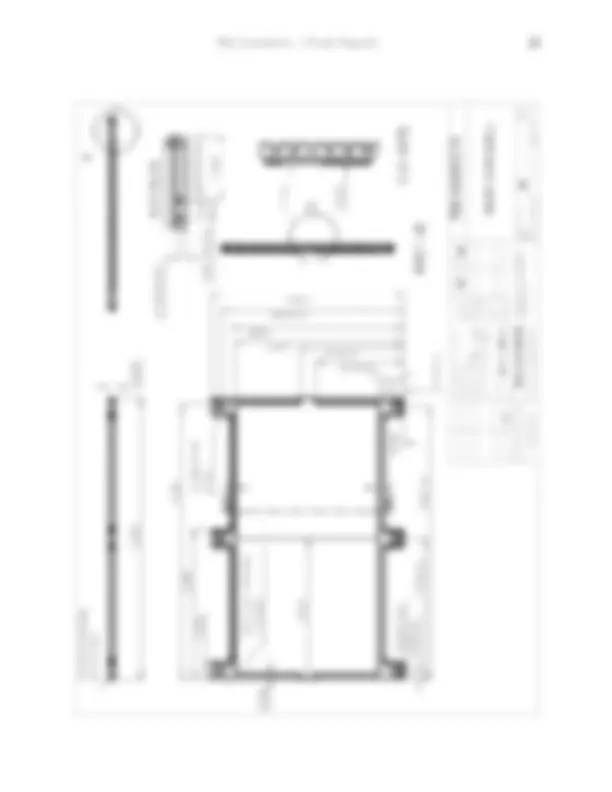
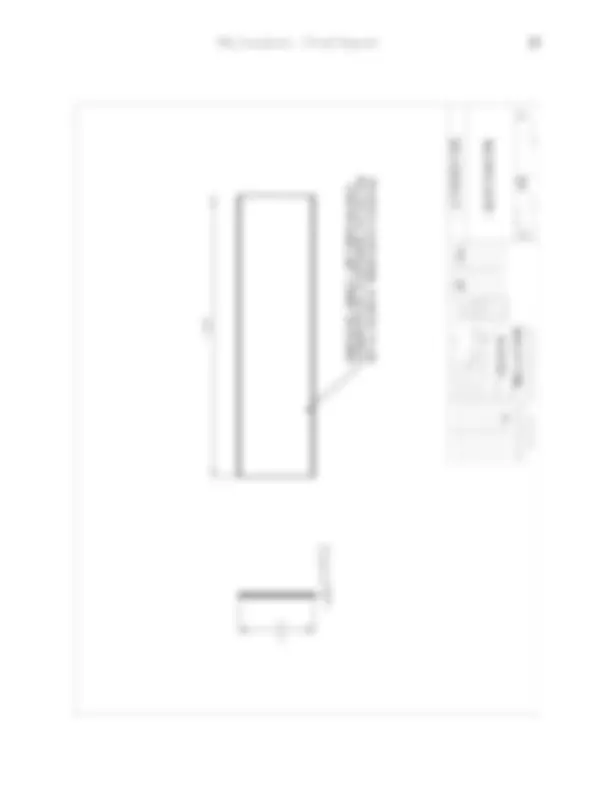
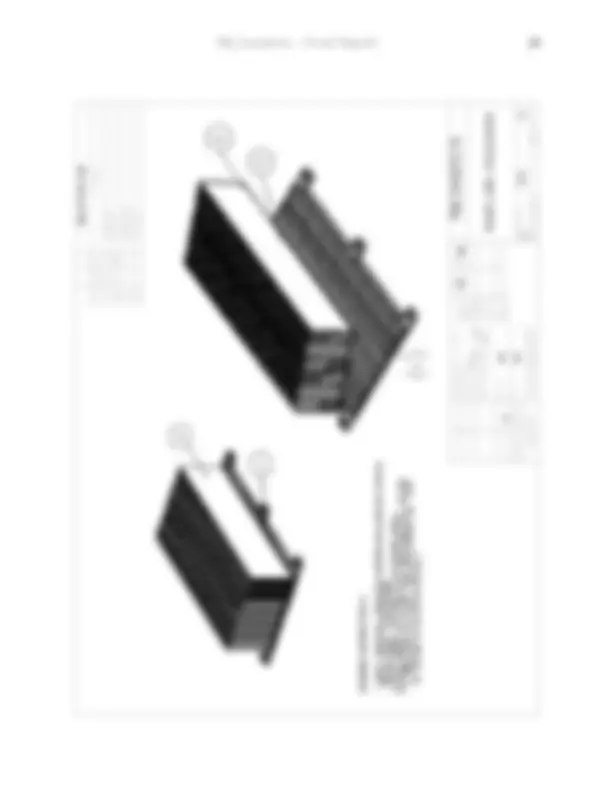
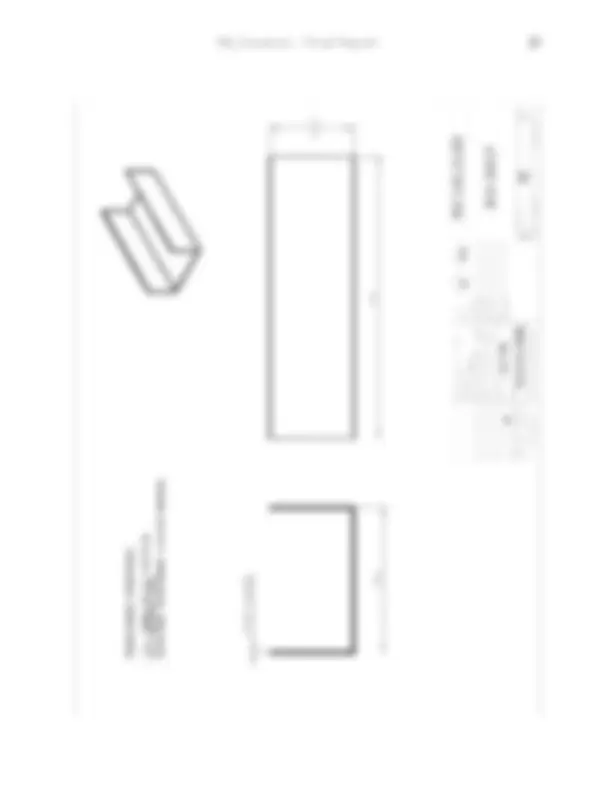
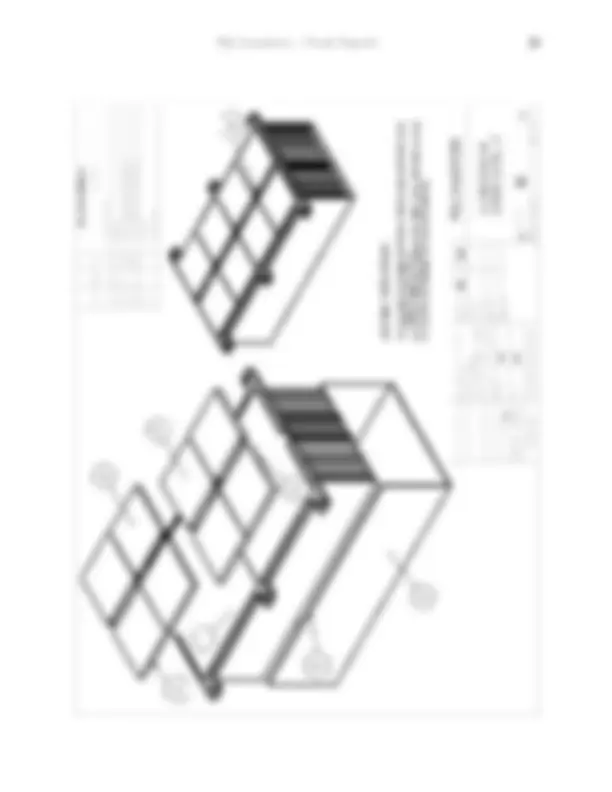
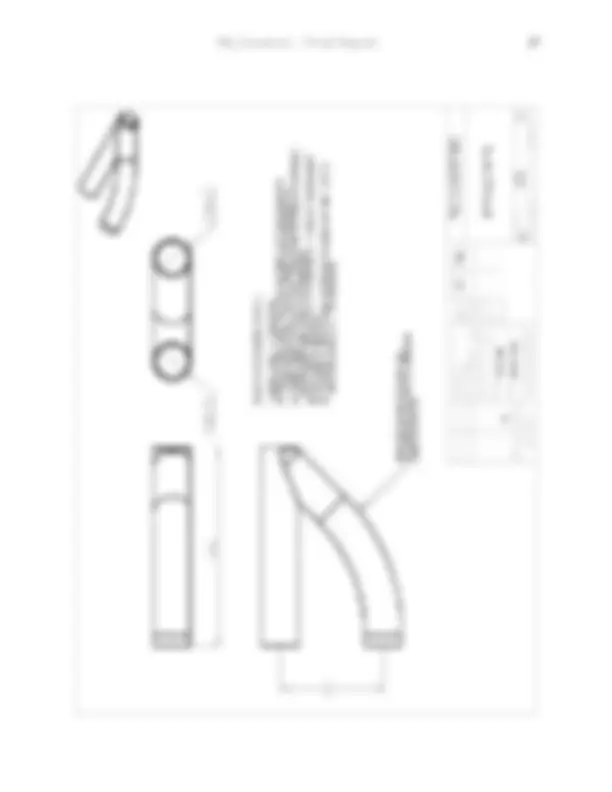
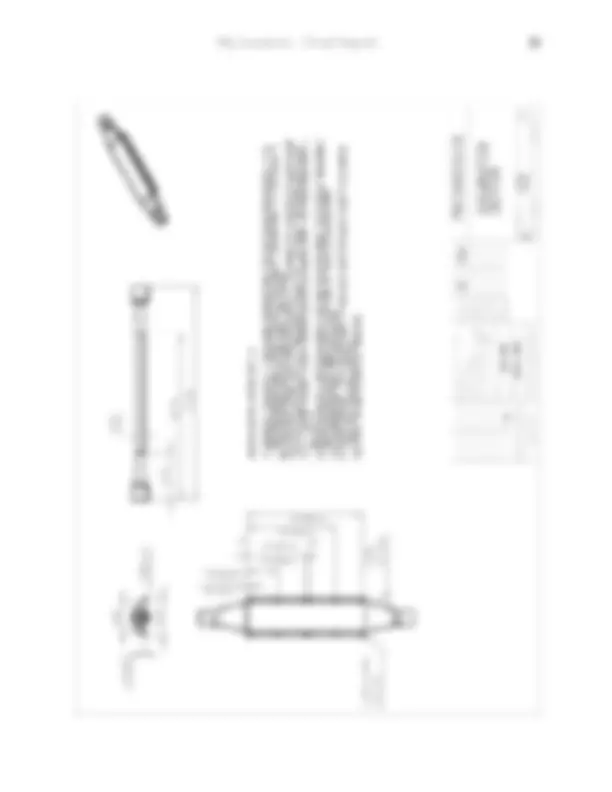
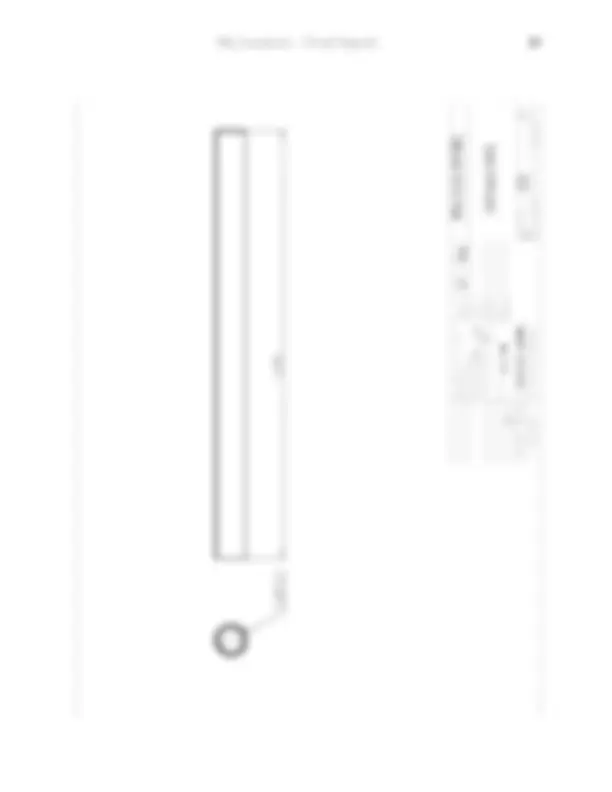
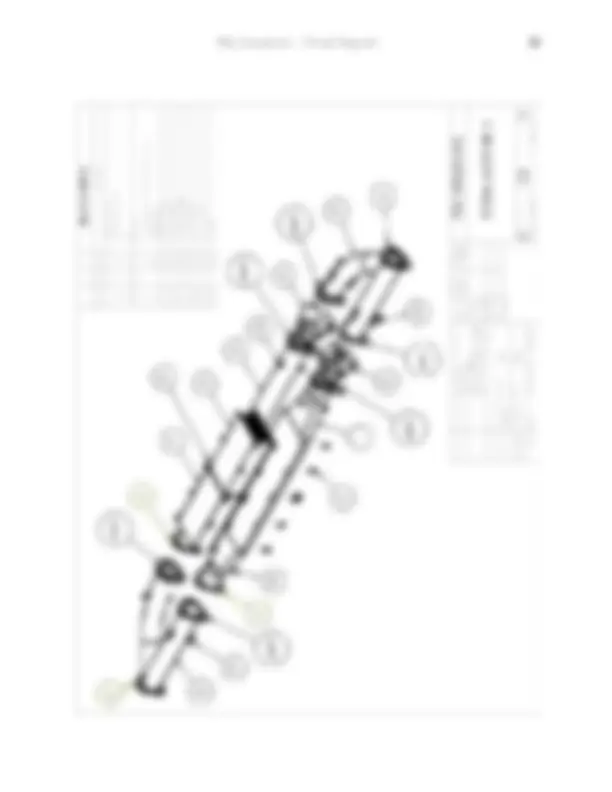
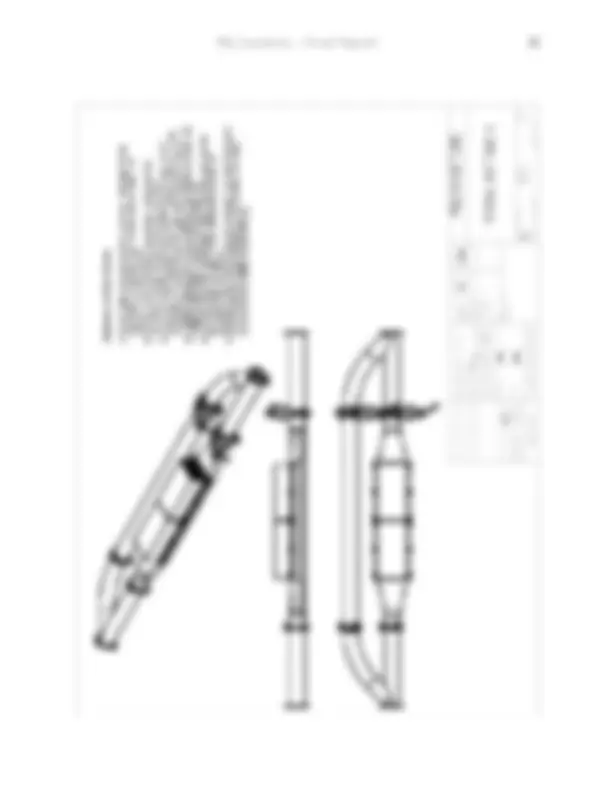
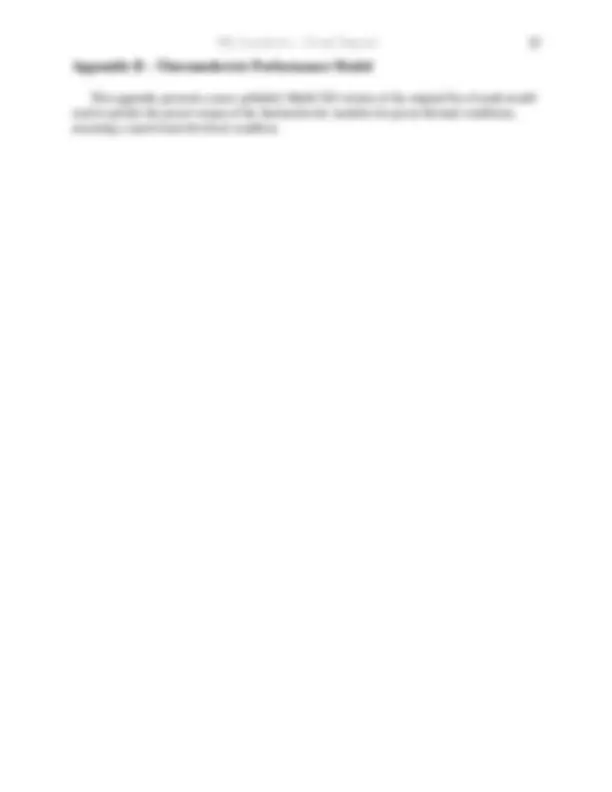
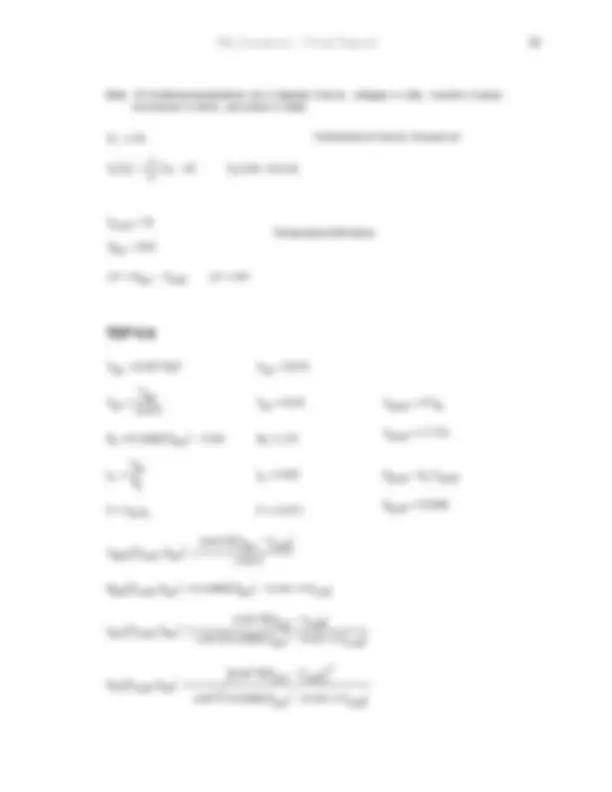
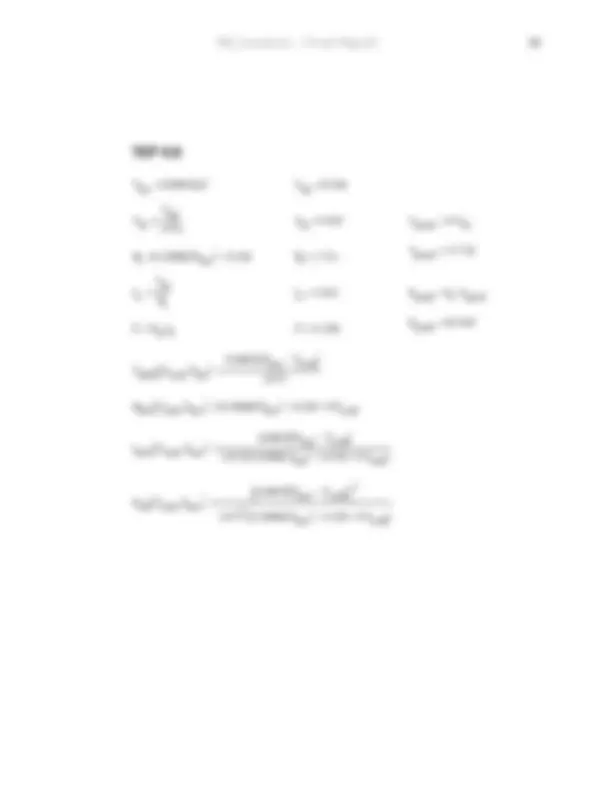
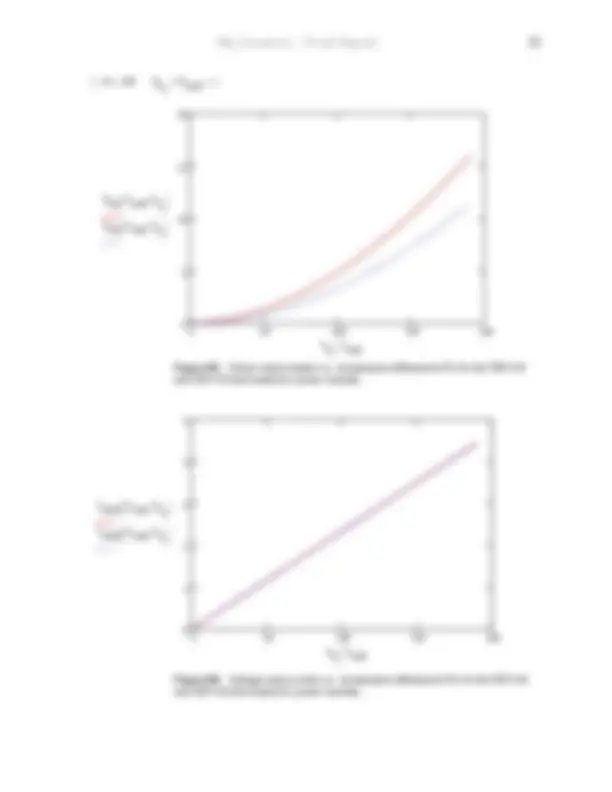
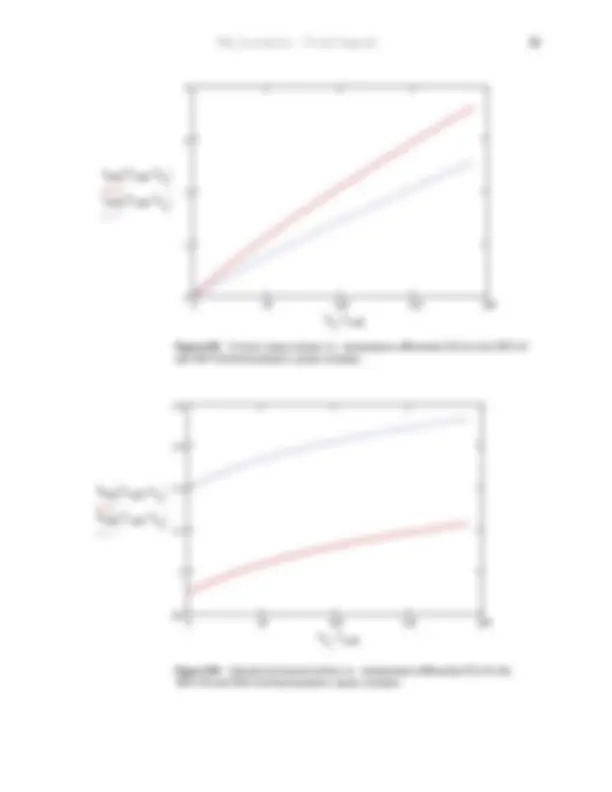
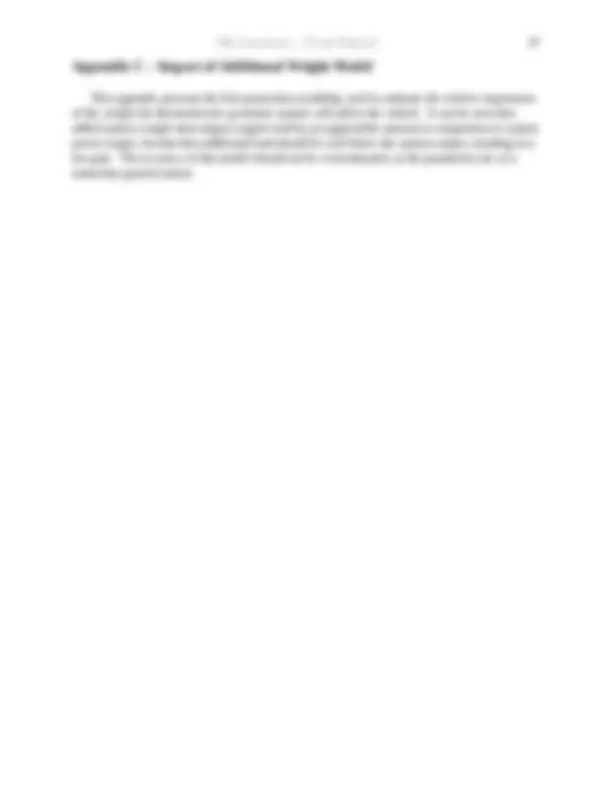
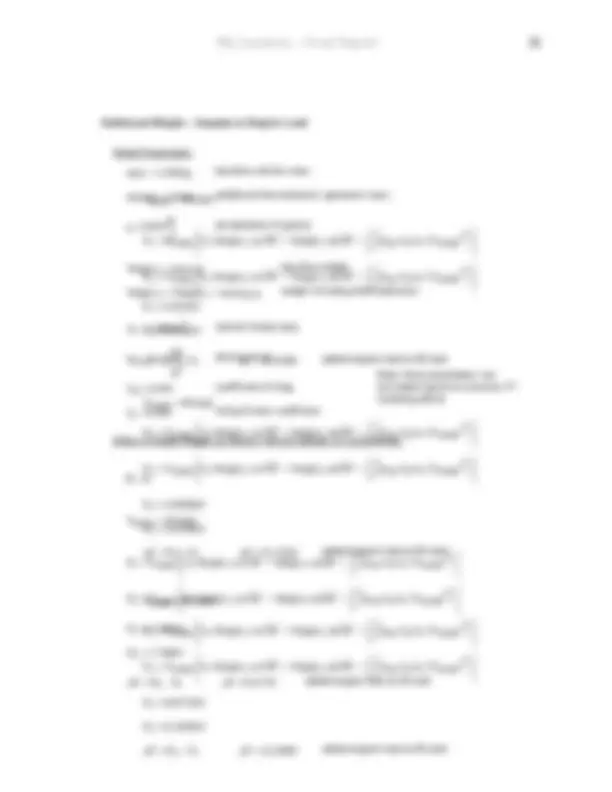
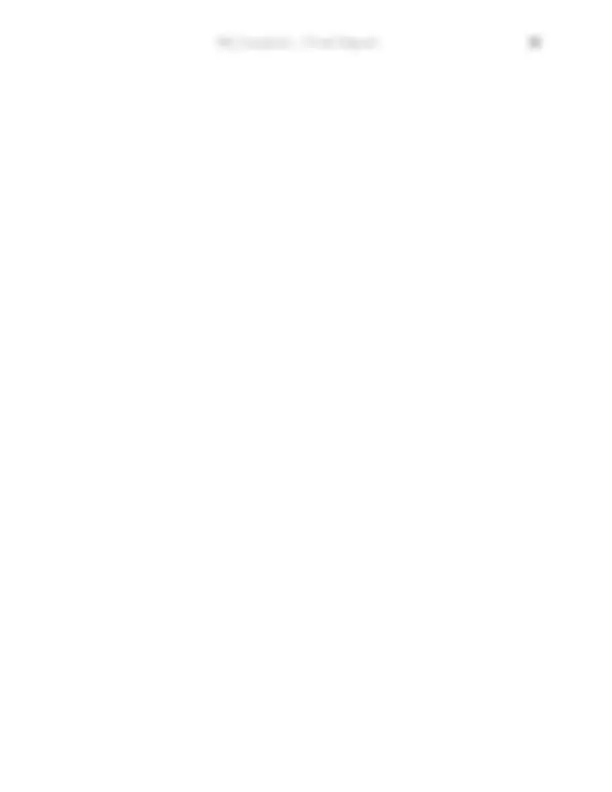
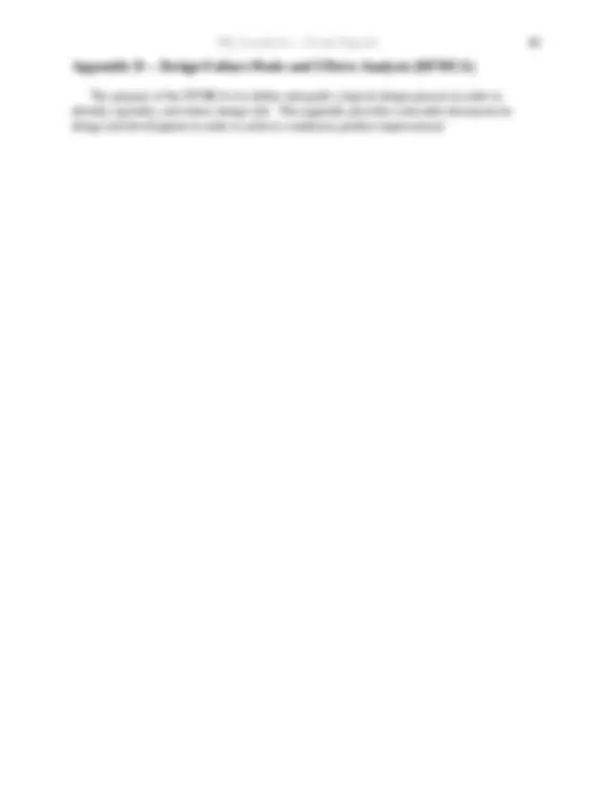
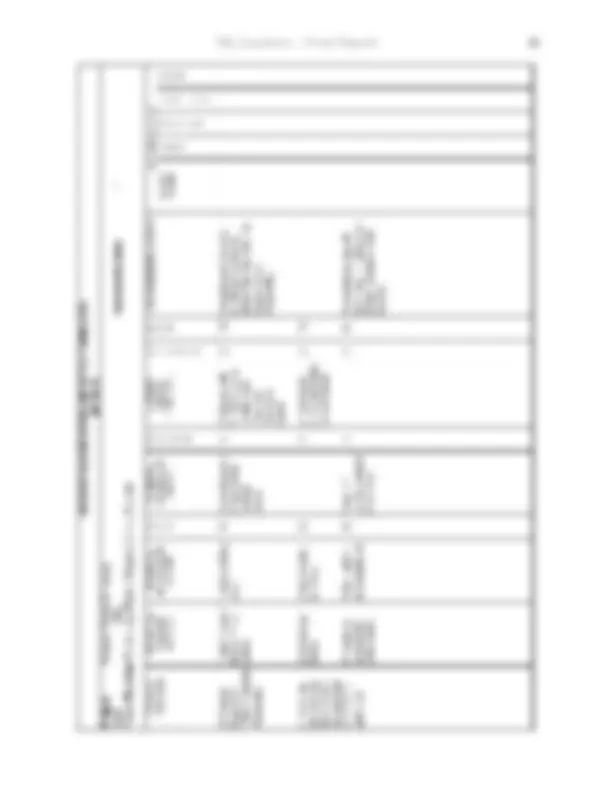
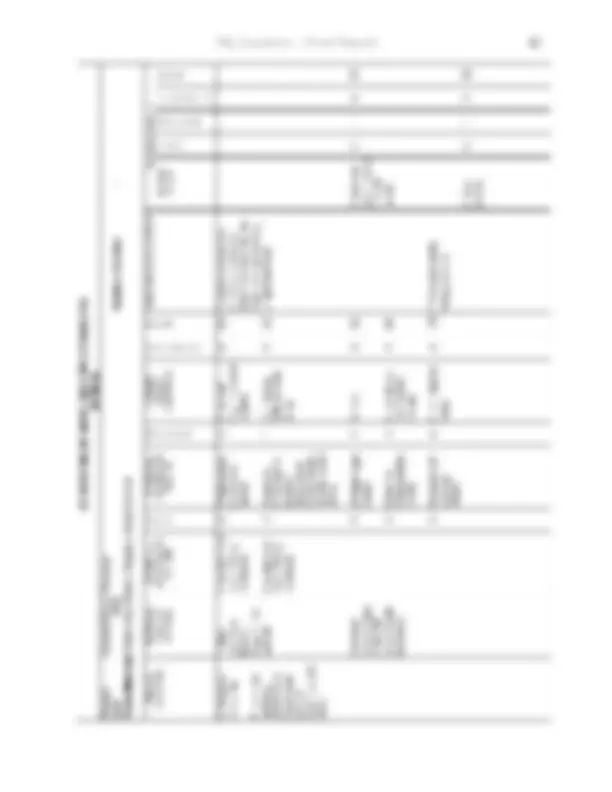
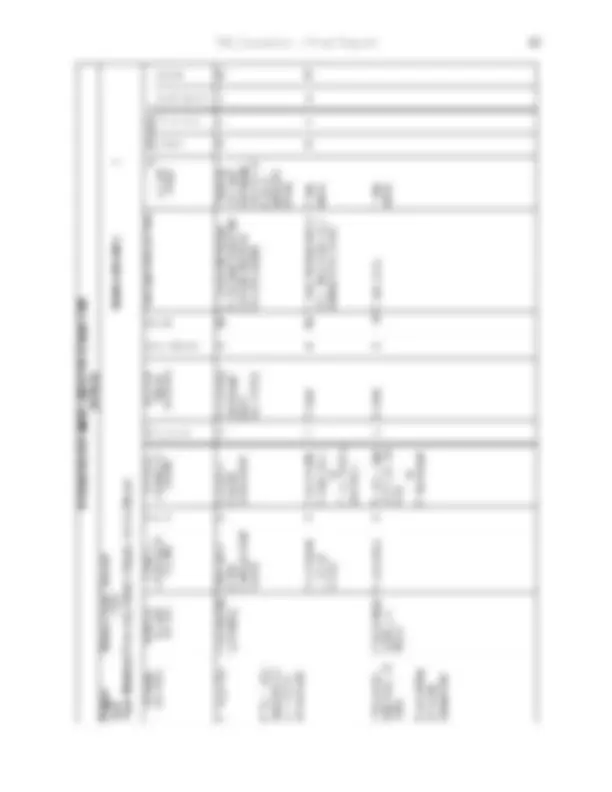
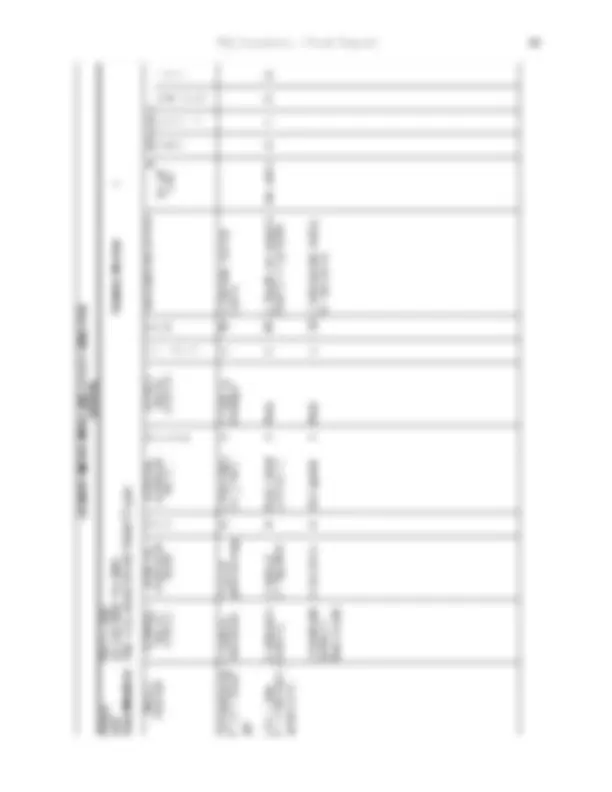
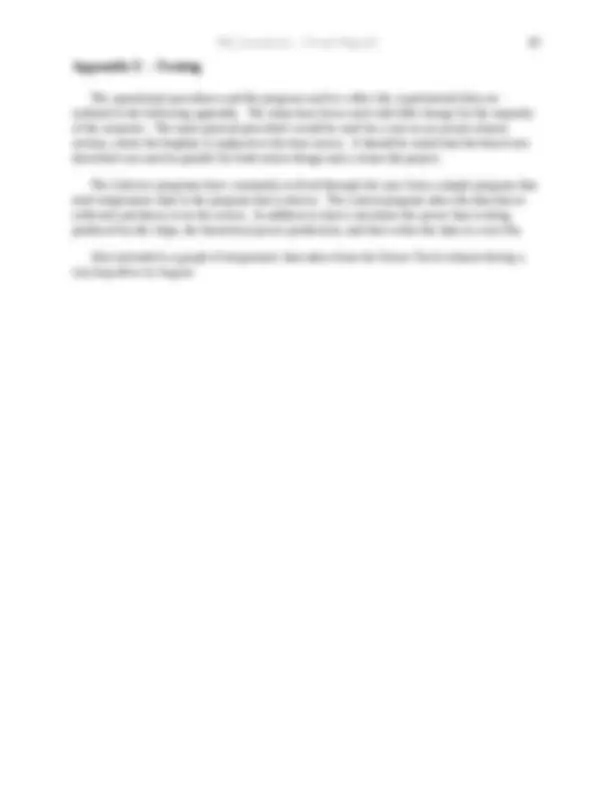
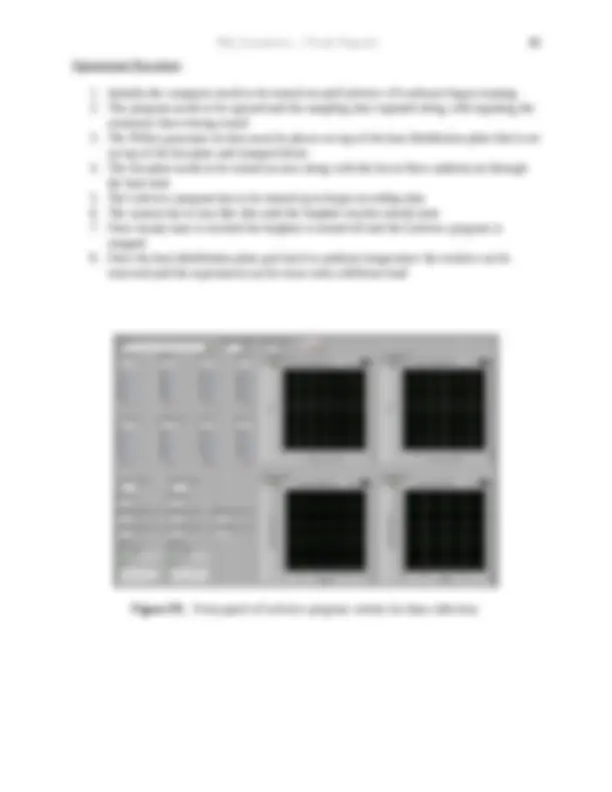
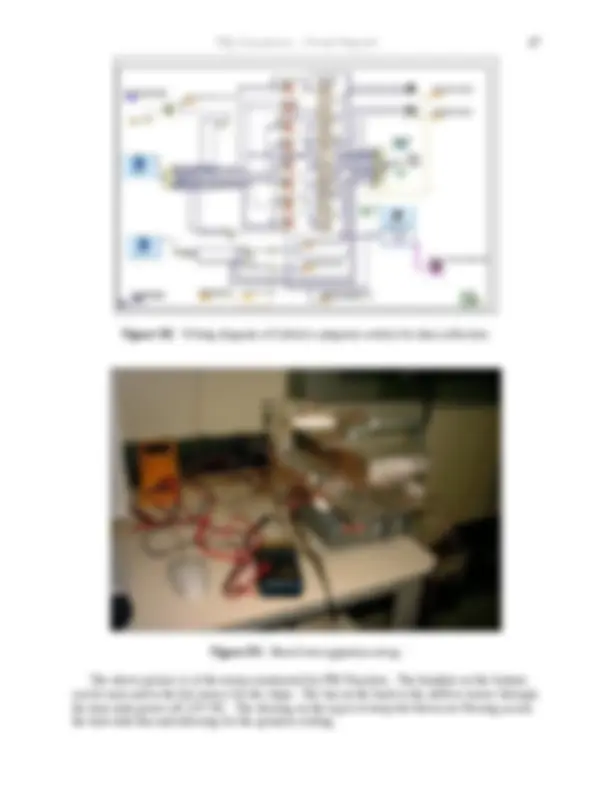
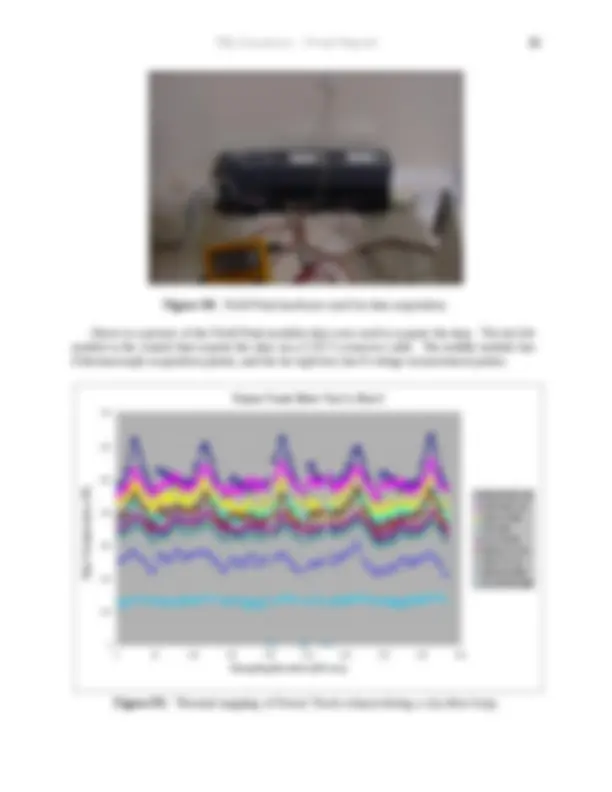
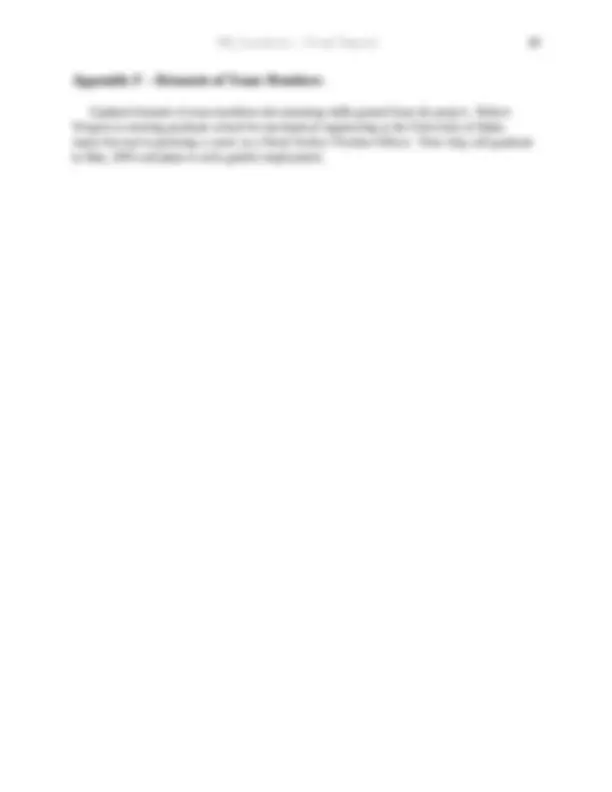
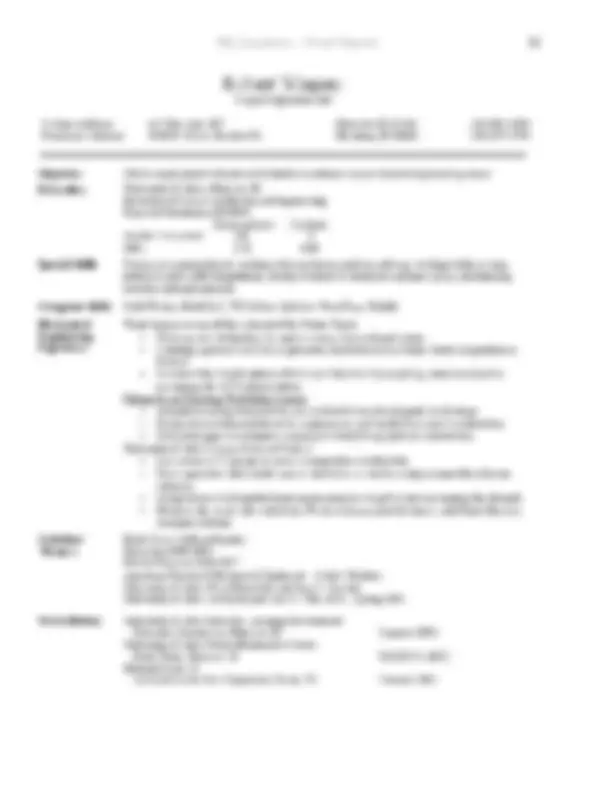
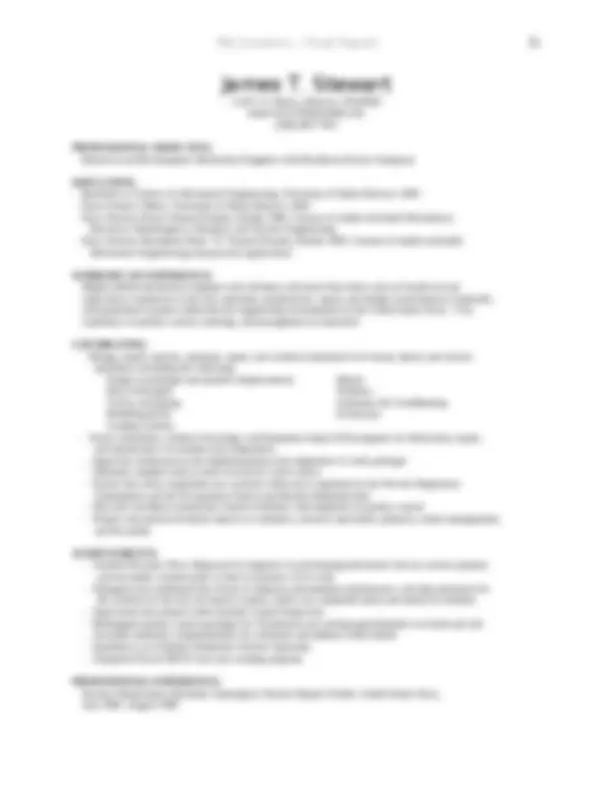
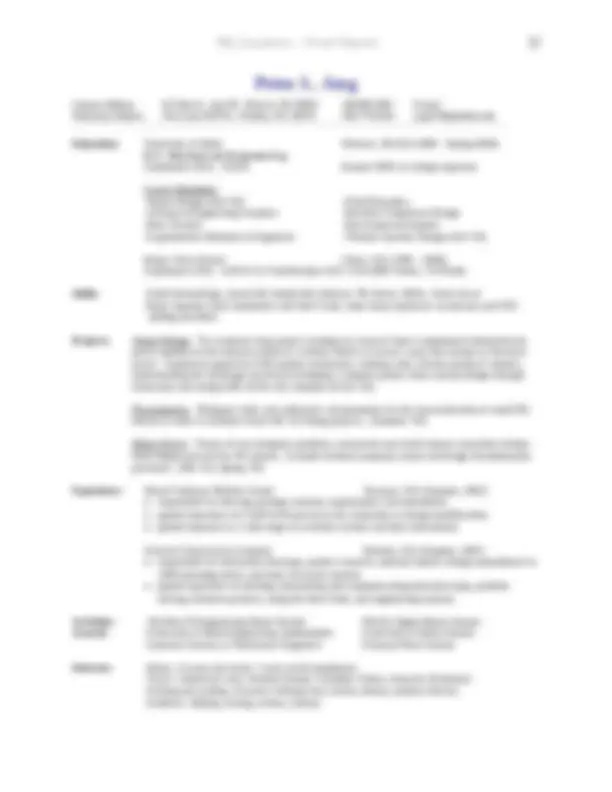
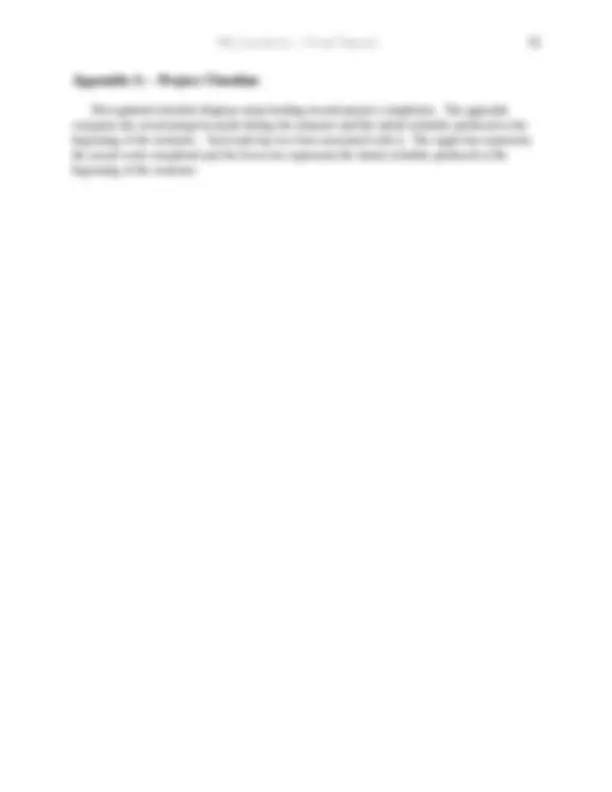
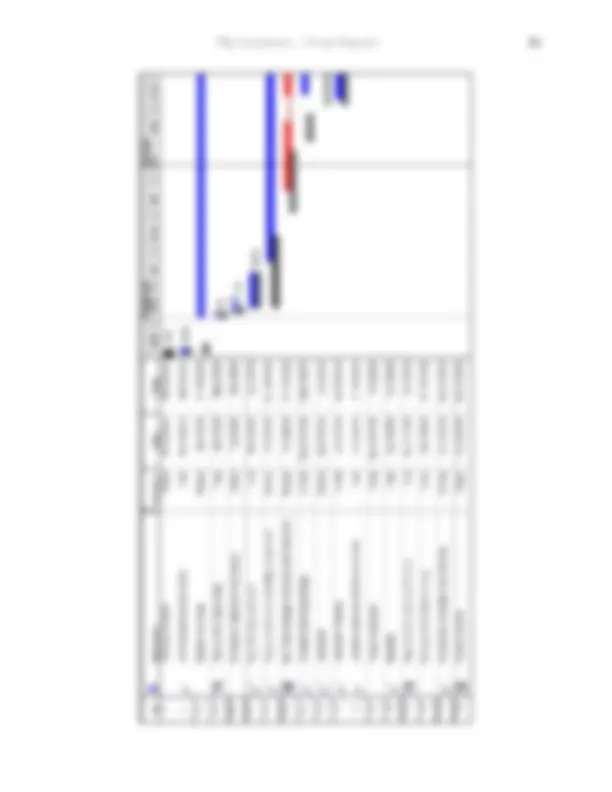
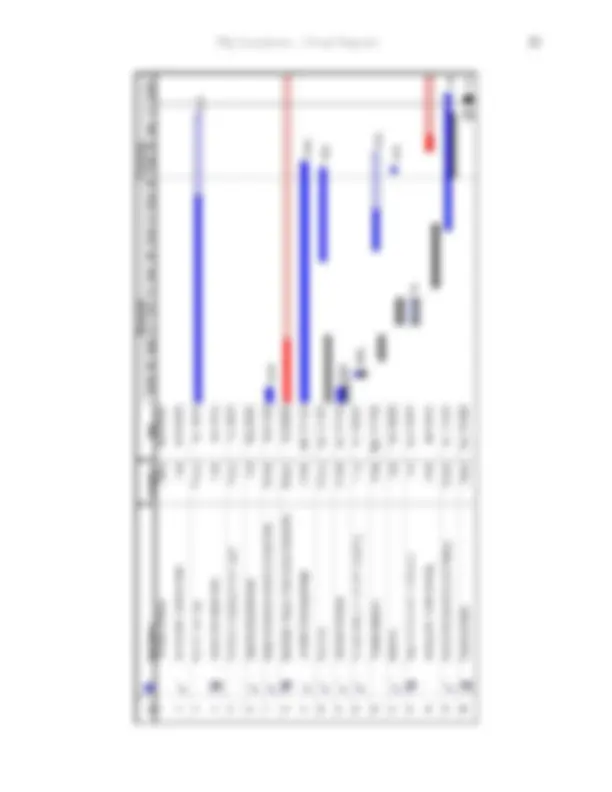
Study with the several resources on Docsity
Earn points by helping other students or get them with a premium plan
Prepare for your exams
Study with the several resources on Docsity
Earn points to download
Earn points by helping other students or get them with a premium plan
Community
Ask the community for help and clear up your study doubts
Discover the best universities in your country according to Docsity users
Free resources
Download our free guides on studying techniques, anxiety management strategies, and thesis advice from Docsity tutors
Material Type: Exam; Class: Mechanical Systems Design II; Subject: Mechanical Engineering; University: University of Idaho; Term: Fall 2003;
Typology: Exams
1 / 59
This page cannot be seen from the preview
Don't miss anything!
PBJ Xaustors – Final Report
Government regulations stemming from environmental concerns and worldwide oil consumption are forcing the automotive industry to make improvements in tailpipe emissions and vehicle fuel economy. In a typical vehicle, the exhaust gas contains one of the largest portions of wasted energy, approximately 34% of available energy from the fuel. As a result, we have constructed a thermoelectric generator to capture this waste heat energy in the exhaust and turn it into useful electric energy. With the thermoelectric generator mounted between the exhaust stream and the cooling channel, the generator we have built is projected to have a power output in the range of 70 to 90 watts depending on driving conditions. However, system testing requires implementation of the customized DC-DC converter currently in development. The generator is designed to be passive system, fully integrated into the Future Truck exhaust stream, with no customer action required to operate. We have performed detailed experiments on the generator and our testing results lead us to recommend that additional funds be spent on an expanded implementation of the thermoelectric generator in order to achieve results that will positively impact the Future Truck performance at competition. We have accomplished our objective of capturing the exhaust waste heat and turning it into useful electrical power. The long term action should be to wait until second generation thermoelectric chips are available at a reasonable cost and then continue the construction of another generator with the new chips. Until then we recommend that the thermoelectric generator be installed into the Future Truck to showcase the talents and engineering abilities of the University of Idaho mechanical engineering students. i
PBJ Xaustors – Final Report Section: Page Number: Appendix A – Drawing Package………………………………….. 21 Appendix B – Thermoelectric Performance Model………………. 32 Appendix C – Impact of Additional Weight Model………………. 37 Appendix D – Design Failure Mode and Effects Analysis………... 40 Appendix E – Testing …………………………………………….. 45 Appendix F – Résumés of Team Members……………………….. 49 Appendix G – Project Timeline…………………………………… 53 iii
Environmental concerns and worldwide oil consumption are creating government regulations that are forcing the automotive industry to make improvements in tailpipe emissions and vehicle fuel economy. In contrast, consumers’ expectations in vehicle performance and capabilities are driving the energy consumption rate to ever-increasing levels. Automotive Original Equipment Manufacturers (OEMs) are now planning to incorporate telematics, collision avoidance systems, vehicle stability controls, navigation, steer-by-wire, electronic braking, additional powertrain/ body controllers, sensors and other electronic subsystems into the vehicle. Current electrical systems for mid- and large-sized vehicles currently have average electrical power loads of 0.8 to 1.5 kW and peak power loads of approximately 2 kW. In five years, the average power load is projected to be 3 to 5 kW with peak power loads of over 7 kW. Future automobiles, therefore, must either generate more power or utilize power management schemes to support safety features and accessory electronics while reducing fuel consumption and emissions. One way of accomplishing this energy recovery in vehicles would be to incorporate thermoelectric devices into the exhaust system. In a typical vehicle, the exhaust gas contains one of the largest portions of wasted energy, approximately 34% of available energy from the fuel. When the thermoelectric generator is mounted between a heat source and a cooling channel, electrical power on the order of several watts to several kilowatts can be produced depending on the design and thermoelectric materials used in the system. To date, thermoelectric power generators have been primarily used in space and military applications. Overall efficiency of 5% has made these devices somewhat impractical and expensive for automotive mass-production application. Porsche, General Motors, Nissan, and others have previously investigated thermoelectric power generation, and have concluded similarly. Recent developments by HI-Z Technology, PACCAR Technical Center, and others, however, have changed the landscape, enabling new applications to be considered. Continued research in development of efficient thermoelectric materials is very important if thermoelectric is to be applied in the automotive industry. An efficient thermoelectric device will make significant impact on the automobile industry. Converting what would otherwise be wasted heat energy to electrical power will make vehicles more efficient, thereby reducing dependence on foreign oil. Sponsored by the Ford Motor Company and US Department of Energy, the annual Future Truck competition embodies the goals of increased fuel economy, reduced dependence on foreign oil, and drastic reductions in overall vehicle emissions in the light truck and SUV market. Future Truck competition is a forum for innovation and experimentation, wherein student teams take design risks outside the realm of practicality for large scale vehicle manufacturers. Therefore, thermoelectric waste heat recovery is clearly in line with the spirit of the competition.
3.1 – Introduction Work on concept development paralleled the formulation of project goals. The original mandate of the project was to recovery energy from the exhaust flow of the vehicle that would have otherwise been wasted in an effort to improve overall vehicle efficiency. Thus the original concept development was broader than the final goal statement would suggest, including as it did ideas for heat driven cooling systems in addition to power generation schemes. The methodology of concept development centered around brainstorming with regard to the nature of the energy available and the possible means of utilizing it, followed by largely internet based research to determine the degree to which such concepts had already been developed as well as the commercial availability of necessary subsystems or components. Given the project scope and resources, the challenge was not to develop a unique process or technology but to select an appropriate technology and tailor it to the system constraints. 3.2 – Absorption Cooling As the exhaust energy recovery was not originally limited to electrical power generation, a number of cooling schemes were investigated as a means of replacing the vehicle’s current air conditioning system, which constitutes a significant power draw. The ammonia absorption refrigeration cycle was considered as inspired by the propane-powered refrigerator. Rather than burning fuel to drive dissolved ammonia (other chemicals such as lithium bromide would also be potential options) out of the water stream, waste heat from the combustion of fuel in the vehicle’s engine would instead be employed, as is shown in figure 1. Figure 1. Schematic representation of automotive absorption cooler.
This type of cooling system would derive a large portion of its motive power from waste heat rather than the useful mechanical energy of the engine, as the belt-driven air conditioning unit does, however, it would also require a small amount of mechanical power to drive the pump. While the use of waste heat for refrigeration is very attractive from an exergetic viewpoint, the near constant flux of thermal conditions inherent to a typical city drive cycle makes the prospect of achieving satisfactory performance appear rather unlikely. Additionally, during conditions such as idling in a traffic jam, the system would be unable to produce sufficient cooling. This would suggest the parallel installation of standard AC unit, which would serve to further worsen what would probably be an already problematic weight issue. 3.3 – Adsorption Cooling Adsorption cooling parallels absorption cooling except that the working fluid is adsorbed into a highly porous sorbent material rather than absorbing into a secondary fluid stream. The sorbent material used must have a very large surface area per volume to be effective, with activated charcoal and zeolites being common choices. The working fluid, as a low-pressure vapor, is adsorbed into the sorbent bed until it reaches saturation. A valve then closes the sorbent bed off from the evaporator and heat is applied to purge the working fluid from the sorbent material. After which, the high-pressure vapor moves on to the condenser. Thus, the sorbent bed is referred to as a thermal compressor. In the case of a waste heat energy recovery scheme, the heat used to purge the sorbent beds would come from the exhaust system. Figure 2. Flow schematic of an adsorption cooler.
3.5 – Exhaust Flow Turbo The concept of using a modified turbo charger is relatively simple in nature. Standard turbo chargers use the flow of the exhaust gas through the pipes to turn a turbine that drives a compressor through which the incoming air to the engine first passes. In a power generation scheme, the turbine would drive a generator rather than a compressor. Thus, the flow of the exhaust gases would be used in a direct, mechanical method to generate electricity. This electricity could then be fed back into the 12V battery system. Figure 4. Off-the-shelf components for an exhaust turbo-compressor. While the implementation of such a system appears to be relatively straightforward, with a strong potential for the employment of preexisting components, it would require a relatively large pressure differential to be effective. This exhaust backpressure on the engine would certainly require modifications to the tuning of the engine at minimum, and it presents a potential for engine performance degradation. As this represents a serious concern with regard to systems compatibility, the exhaust flow turbo concept has been discarded. 3.6 – Thermophotovoltaic Power Generation While typical photovoltaic cells enable the generation of electricity from visible light, it is possible to devise and construct PV cells that instead operate in the infrared spectrum. This is the basic operating principle behind thermophotovoltaic power generation. A high temperature heat source is used to excite an emitter, usually a specialized ceramic, to produce infrared radiation of the desired wavelength for peak thermophotovoltaic efficiency. The emitter is surrounded by TPV chips, or the chips are surrounded by the emitter, and power is generated in much the same way as solar power plant. The primary difference is that the source is only inches away rather than millions of miles, resulting in a much higher energy flux. A team at Western Washington University has conducted extensive work on TPV implementation in vehicles. Theoretical and optimization work is being pursued in both Germany and Russia.
Figure 5. Artist rendering and cut-away of a proposed thermophotovoltaic generator. This technology is attractive. However, there are a number of challenges to implementation in this project. The first issue is one of availability. While research is on-going, commercial application has not yet developed, thus acquiring the TPV cells might prove to be impractical or prohibitively expensive. The second issue is more fundamental. Just as a typical PV cell will not produce a flow of electrons no matter how much red light is applied, so too will the TPV cells not function if the spectral band is not correct. Vehicle testing has proven that exhaust system temperatures under normal operating conditions are well below the required excitation temperatures. For these reasons the thermophotovoltaic power generation concept has been dropped. 3.7 – Thermoelectric Power Generation Also referred to as thermionic devices, the function of thermoelectric devices is similar to the behavior of thermocouples, with the dissimilar metals replaced by the P and N zones of an array of semiconductors. A temperature differential across the junctions of a thermoelectric device induces a voltage potential. Early commercial interest in thermoelectrics was focused on solid- state cooling applications. When current is passed through a thermoelectric device, one side becomes hot and the other cold. Power generation is achieved by instead providing the temperature differential and allowing the current to flow into a circuit. For their gross power output, thermoelectric generators tend to develop relatively high amperage and low voltage in comparison with more typical generation methods. The performance of the devices is strongly impacted by the temperature differential maintained across the device, with total power output roughly exponentially proportional to power output. For a given temperature differential, higher efficiencies will be achieved with a lower cold side temperature. Also of concern is the maximum sustainable operating temperature of the devices, as thermal degradation becomes problematic for currently available devices at temperatures in
Figure 7. Energy flow diagram showing thermoelectric power generation. 4.2 – Thermoelectric Modules Of critical importance to the design of the project was the selection of which thermoelectric modules to purchase. The final decision was between Hi-Z of California and Thermonamic Electronics Co. of Xiamen, PRC. As the Thermonamic modules cost approximately half as much as their competitors and budget constraints were appreciable, financial considerations played a primary role in deciding for Thermonamic. Although the gross power output of the Chinese modules was lower than that of the high end Hi-Z module, the Thermonamic modules had the advantage of a smaller size and a higher voltage to current ratio for a given amount of power. The latter consideration was important in terms of load matching circuit efficiency, where losses increase with the increased voltage differential across the DC-DC converter. Sizing of the array of the thermoelectric modules to be employed was dictated by the thermal conditions, the electrical demands, and the financial constraints. Exhaust temperature data from the Future Truck vehicle, see figure D5 on page 48, indicated that it would be possible to expose most of the generator section to thermal conditions just below the manufacturer rated maximum continuous operating temperatures for much of the drive cycle. Given the performance modeling of the devices, see figure B1 on page 35, it seemed reasonable to assume a power output per chip of between 9 and 15 watts, with a wide range of parameters in effect. To
achieve the desired 180 watt output, 16 to 20 modules would be needed, with an initial implementation of 8 due to budget constraints. As expected voltage output per module is in the 3.0 to 4.5 volt range, the modules are wired in series banks of four to bring the composite output close to 12 volts before passing through the load matching circuit to the battery. A rough schematic of this is given in figure 8 below. Figure 8. Basic wiring schematic for thermoelectric generator. 4.3 – Cooling Hardware With the hot side temperature a given due to the thermal behavior of the exhaust system, creating an effective means of maintaining a lower cold side temperature is a critical issue. The possibility of implementing a water jacket cooling arrangement was attractive given the much higher thermal capacity and convective heat transfer coefficients of liquids in comparison with air; however, a forced air system was selected due to the problems a liquid cooled system would run into with regard to weight, size, and budgetary constraints. It may have been possible to tap into the preexisting cooling system of the vehicle, with its large rooftop radiator, but such a possibility was dimmed by the fact that this would have required modification of other vehicle subsystems and coordination with other Future Truck team members who were not in a position to work with us early in the semester. The cooling scheme pursued involves ducting air from the front of the vehicle to generator section located about mid-vehicle via flexible metal ducting. Air would be forced into the system by the forward motion of the vehicle, entering the ducting at two custom scoops that we fabricated by modifying the existing plastic fog light cover plates. This hardware is ready for installation; however, there is some doubt now whether routing will be possible for the driver side duct given the spatial needs of the four wheel drive hardware, which have changed a number of times as that project work has altered its focus. Another possibility is to scoop air from directly below the vehicle. This configuration, identified as a possibility early in the design, was suggested by the visiting Future Truck Ford mentor. It would require further prototyping and likely road testing, as turbulent air flow under the chassis is uncertain. To protect the heat sink from fouling and impact damaged caused by road debris, a light sheet metal box duct is used to shroud the heat sink fins. While the finalized nature of its implementation still awaits road testing and the control hardware, a 12 watt parasitic cooling fan will be installed parallel to the air intake to provide supplemental cooling.
desired hardware was unsuccessful, with no preexisting hardware capable of the necessary function found. All was not lost, however, as recent work with electrical engineering students Jeremy Forbes and Erik Cegnar is moving towards an in-house solution to the problem. Both Mr. Forbes and Mr. Cegnar are experienced practitioners of the electrical arts, with extensive experience with the hybrid systems of the Future Truck vehicle. In return for their assistance, we will be working on mechanical installation issues pursuant to electric hybrid systems. The load matching circuit will consist of a buck-boost converter, as system voltage is expected to both fall short of and exceed the nominal battery charge of 12 volts, and load matching is desired at a maximum range of operating conditions. A programmable microcontroller will be used to take thermocouple inputs and drive a pulse width modulation circuit that will serve as a switching regulator and control the performance of the DC-DC converter. The circuit components are currently in an early stage of prototyping and material lists are being compiled. Each bank of four thermoelectric modules in series will require a load matching circuit. There is some loss of precise load matching on a module by module basis in this arrangement, as each of the four modules will be at slightly different conditions. This is mitigated, however, by the facts that implementing a load matching circuit for each module would be almost four times as costly; instrumenting each module with thermocouples is impractical; and the conversion efficiency of a DC-DC converter to boost from a single module voltage to the desired 12 volt range would be much lower. 4.6 – Generator Section and Assembly The piping work and custom generator section, as they are currently fabricated, required a large amount of welding, cutting, grinding, and other labor intensive activities to complete. The drawing package, including rough fabrication and assembly instructions, can be found in Appendix A. Overall, the craftsmanship and attention to detail are of a high quality, and the product is both sturdy and safe to handle. Interior weld interfaces, where accessible, have been ground relatively smooth and likewise the transition sections are of a tapered rather than abrupt nature in order to reduce the sources of head loss inherent to the structure of the system. Despite efforts taken during fabrication to restrict the possibility of warping during welding, some warping of the base plate, to which the thermoelectric modules mate up, did occur. Judicious use of an acetylene torch and c-clamps was largely able to correct the problem, as it was primarily localized in one corner of the plate, however, it is evident that this fabrication challenge would be extremely difficult to mitigate with current techniques. If the design were to go into a mass production mode, the generator section would likely be assembled using extruded parts, thus greatly reducing the time and complication of excessive welding. The final product presented, see figure 9 below, is the sum total result of a number of previous prototyping operations and as such itself presents opportunities for a number of further improvements. There are currently plans to significantly reduce the weight of the heat sink to enable the addition of a second generator subassembly without excessive impact to system weight. Additionally, while the assembly fits lengthwise in its install location, the clearances are
less than optimal for installation troubleshooting. A set of relatively simple modifications will allow for a length reduction of an estimated 10 inches. Figure 9. Photo of assembled prototype. 4.7 – The User, Society, and the Environment Once installed with the operation of controls verified, the thermoelectric generator should have very little direct impact on the user, as no user input and only very minimal maintenance will be required. For the typical user it will be yet another unseen automotive component. For society the impact will be improved fuel economy and perhaps a heightened awareness of vehicle efficiency issues. Impact to the environment will come by way of reduced emissions per unit of vehicle performance. With the exception of the thermoelectric modules, the materials of the system are not unique and should not result in any increased disposal problems. If mass production is achieved, it is possible that the semiconductor materials in the thermoelectric modules could require special disposal attention, but a recycling program seems possible as well.
5.2 – Testing Results To date, experimental evaluation of the desired performance has not been achieved. This is largely due to the fact that the test stand arrangement using a hot plate, electric stovetop burner, or propane torch was unable to reach the necessary thermal conditions and to the fact that dynamometer testing of the Future Truck engine has not been possible. There are currently plans to conduct testing in concert with an FSAE or Clean Snowmobile dynamometer test run, but these results will not be available in time for documentation in this report. However, it is possible to make use of some of the experimental data that was gathered on the test stand. The graph of figure 10 shows that the power output is indeed greatest at conditions approximating match load conditions (5.2 ohm). It can also be seen that while the measured data follows the same general trend as the theoretical performance, the theoretical curve fit is lower across the board for given thermal conditions. This may either be due to inaccurate temperature measurements during the experiment or it may be due to the fact that relationship describing output performance is only valid about the component design point (at a much higher temperature) and cannot be accurately extrapolated down to the testing temperatures. Figure 10. Experimental results of thermoelectric power output vs. temperature differential, with the black line representing a 5.2 ohm load resistor, the pink line representing a 11.8 ohm load resistor, the yellow line representing a 3.8 ohm load resistor, and the blue line representing the results yielded by modeling.
6.1 – Expenditures to Date Table 2 reflects a summary of expenditures to date. In general, the actual budget corresponds relatively closely to the originally proposed itemized budget. A number of items exceeded their estimated costs, however, a number of items were not actually implemented. Of primary importance is the fact that the load matching, DC-DC converters are not included above. Their recently projected cost of around $250 will bring the expenses more closely in line with the budgeted amount. Testing Electronics $10. Airscoop Testing $10. Thermocouple Wire $112. Thermoelectrics and Heat Sinks $880. Heat Sink Fins $84. Thermal Grease and RTV $26. Airscoop Subassembly $138. Exhaust Valves $330. Exhaust Materials $41. Total: $1,634. Budgeted: $2,032. Remaining: $397. Table 2. Condensed itemized expenditures. 6.2 – Labor Estimates Table 3, below, is a slightly modified version of the labor estimate table found in the previous project report. While no concerted effort was made to log and track project time, resulting in very approximate times, the estimate seems fairly reasonable in retrospect. One difficulty of parsing project time into distinct activities is that it was a common occurrence for work to spill across category delineations. In the end, the most instructive aspect of the labor estimation is the fact that it is probably low and is billed at only twenty dollars an hour, yet it still amounts to approximately four and a half times as much as the cost of the hardware purchased. At a more realistic hourly cost, it is clear that for projects of this scale labor costs in the real world will far exceed materials costs.