

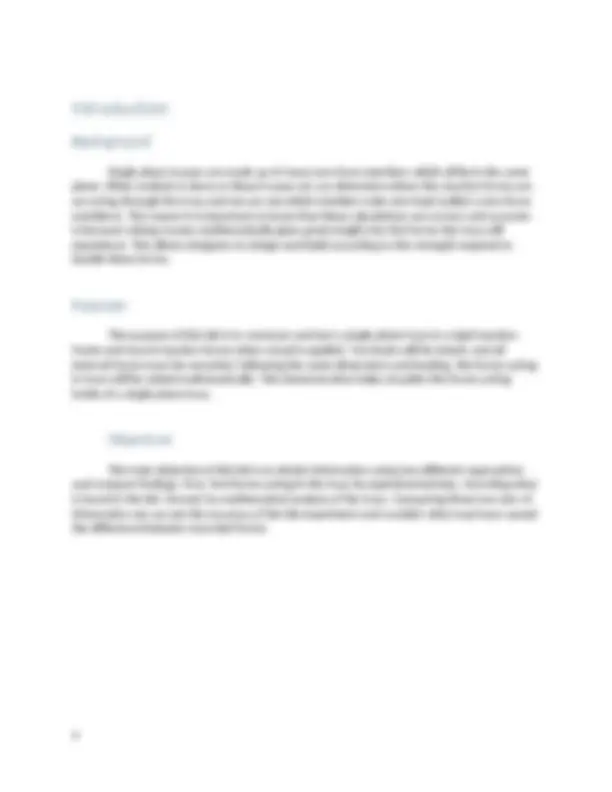
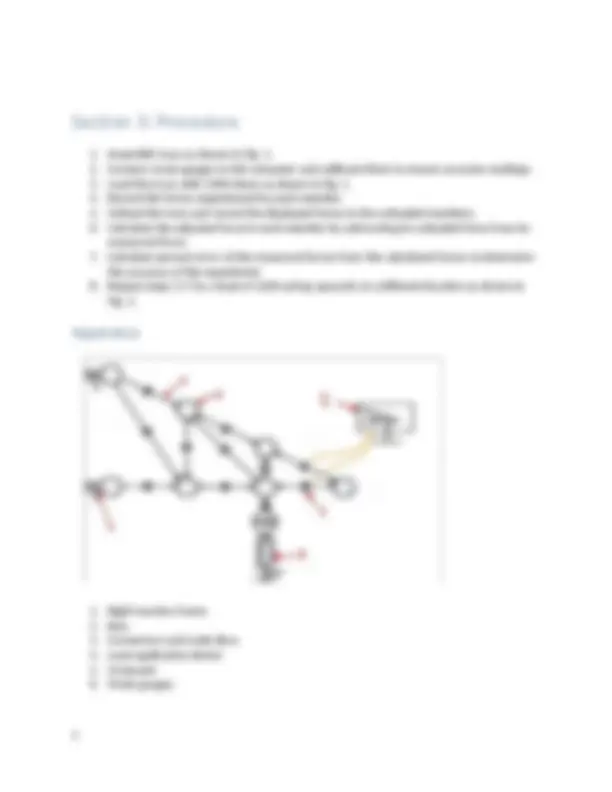
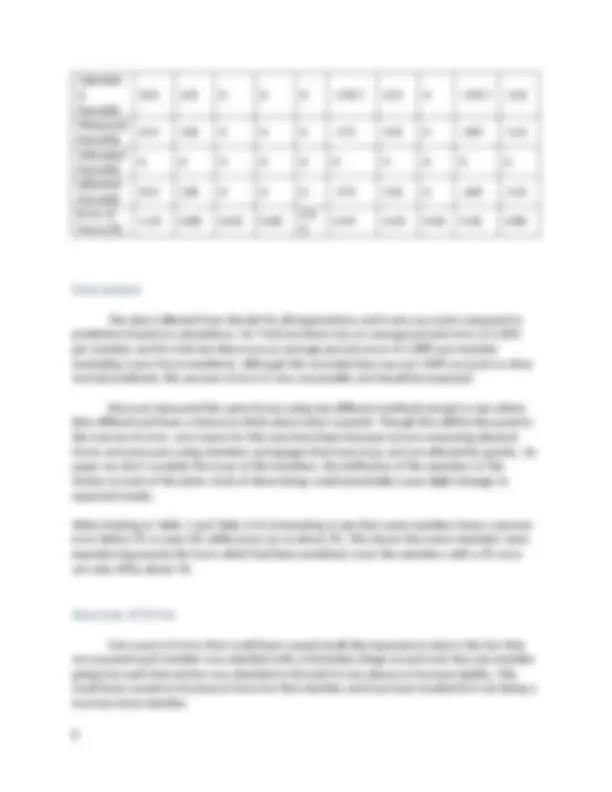
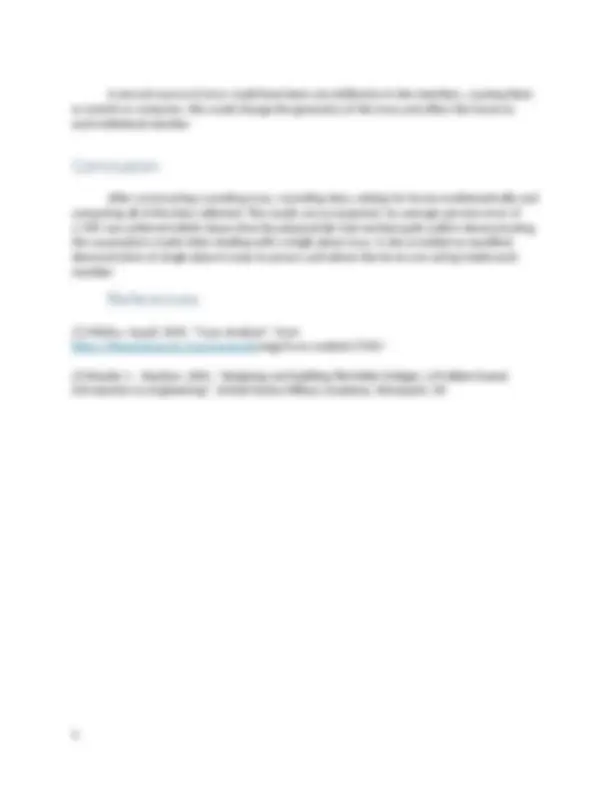
Study with the several resources on Docsity
Earn points by helping other students or get them with a premium plan
Prepare for your exams
Study with the several resources on Docsity
Earn points to download
Earn points by helping other students or get them with a premium plan
Community
Ask the community for help and clear up your study doubts
Discover the best universities in your country according to Docsity users
Free resources
Download our free guides on studying techniques, anxiety management strategies, and thesis advice from Docsity tutors
Report for lab 1, has everything except an appendix
Typology: Lab Reports
1 / 9
This page cannot be seen from the preview
Don't miss anything!
Lab 1: Forces in Single Plane Truss Section: B TA: Talaz Baral Jackson Pankratz February 22, 2021
This experiment focused on examining how a single plane truss reacts under multiple loading scenarios and what forces each member experiences. To achieve this, individual members were assembled into a truss structure and installed into a rigid reaction frame. All members are equipped with strain gauges to monitor the forces being experienced. A load was then attached to at one of the joints. This was done to view the individual forces acting in each member of the truss. From the experiment, the measured values were extremely close to the expected mathematical values. Trial 1 with a 130N downward load had an average percent error of 2.64%, Trial 2 with a 125N Upward load had an average percent error of 2.88%. This concludes that our experiment and theory are very accurate and work well together.
Single plane trusses are made up of many two-force members which all lie in the same plane. When analysis is done on these trusses we can determine where the reaction forces are occurring through the truss and we can see which members take zero load (called a zero-force members). The reason it is important to know that these calculations are correct and accurate is because solving trusses mathematically gives great insight into the forces the truss will experience. This allows designers to design and build according to the strength required to handle these forces.
The purpose of this lab is to construct and test a single plane truss in a rigid reaction frame and record reaction forces when a load is applied. Two loads will be tested, and all internal forces must be recorded. Following the same dimensions and loading, the forces acting in truss will be solved mathematically. This demonstration helps visualize the forces acting inside of a single plane truss.
The main objective of this lab is to obtain information using two different approaches and compare findings. First, find forces acting in the truss by experimental data, recording what is found in the lab. Second, by mathematical analysis of the truss. Comparing these two sets of information we can see the accuracy of the lab experiment and consider what may have caused the difference between recorded forces.
All of the forces that were solved and recorded have been added to these tables (one for each trial). Each table contains a summary of member forces at a load of 130N down and 125N up, respectively. Table 1: Summary of the member forces with a load of 130N down Summary of the Member forces at a Load F = 130 N (Down) Member No.
Calculate d Force(N)
Measured Force(N)
Unloaded Force(N)
Adjusted Force(N)
Error of Force (%)
Table 2: Summary of the member forces with a load of 125N up Summary of the Member forces at a Load F = 125 N (Up) Member No.
Calculate d Force(N)
Measured Force(N)
Unloaded Force(N)
Adjusted Force(N)
Error of Force (%)
The data collected from the lab fits all expectations and is very accurate compared to predictions based on calculations. For Trial one there was an average percent error of 2.64% per member and for trial two there was an average percent error of 2.88% per member (excluding 4 zero-force members). Although the recorded data was not 100% accurate to what we had predicted, this amount of error is very reasonable and should be expected. Since we measured the same forces using two different methods we get to see where they differed and have a chance to think about what caused it. Though this will be discussed in the sources of error, one reason for this may have been because we are measuring physical forces and pressures using members and gauges that have mass and are affected by gravity. On paper we don’t consider the mass of the members, the deflection of the members or the friction at each of the joints. Each of these things could potentially cause slight changes in expected results. When looking at Table 1 and Table 2 it is interesting to see that some members have a percent error below 1% or even 0% while many are at about 5%. This shows that some members were experiencing exactly the force which had been predicted, even the members with a 5% error are only off by about 7N.
One source of error that could have caused small discrepancies in data is the fact that we assumed each member was attached with a frictionless hinge at each end. But one member going into each intersection was attached to the joint in two places to increase rigidity. This could have caused an increase in force for that member and may have resulted in it not being a true two force member.