
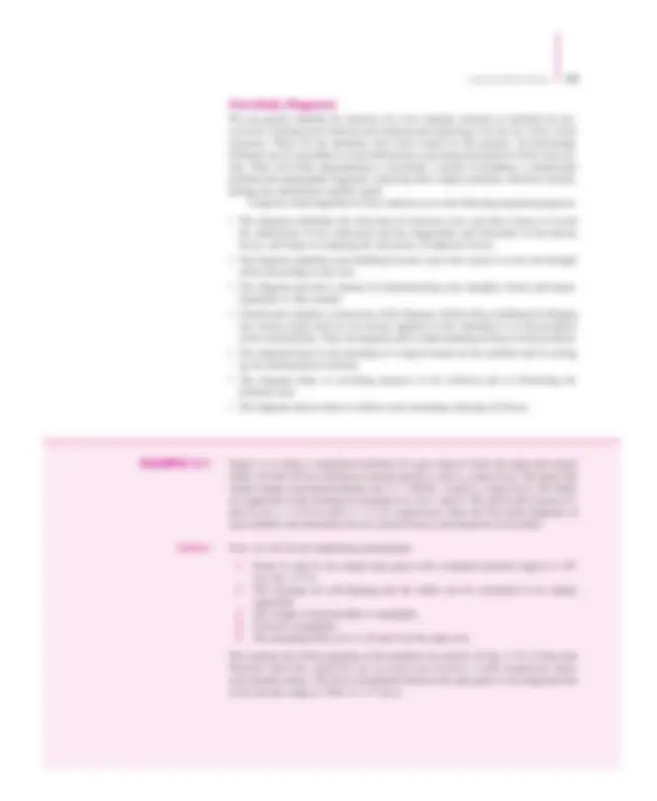
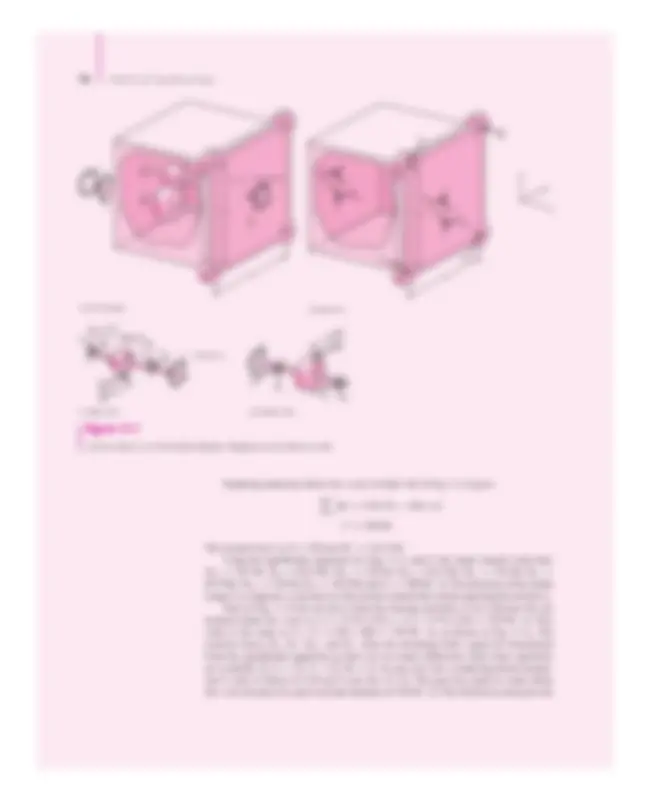
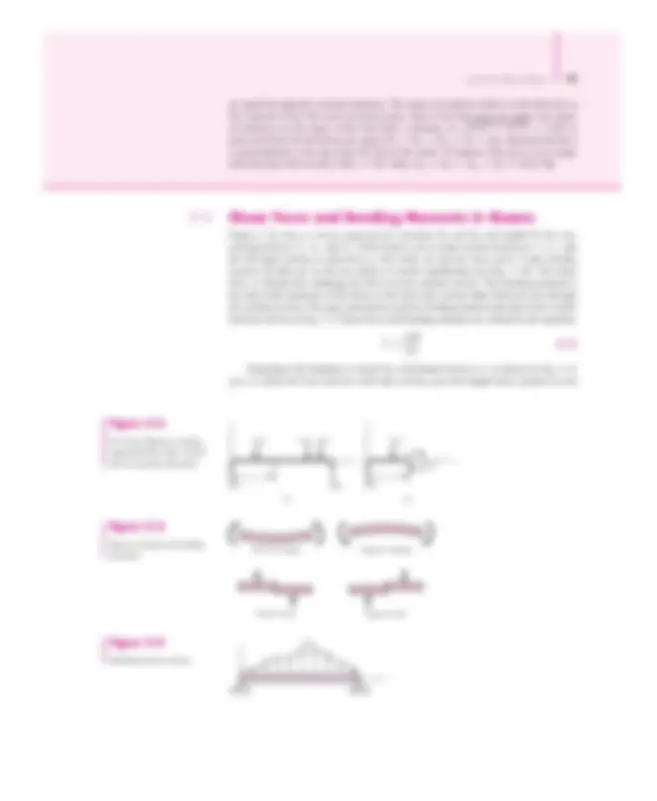
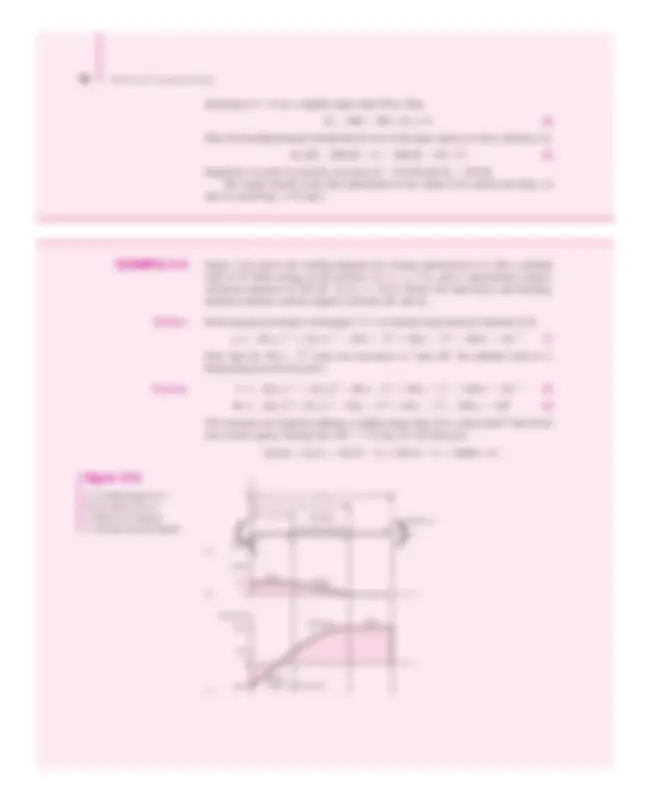
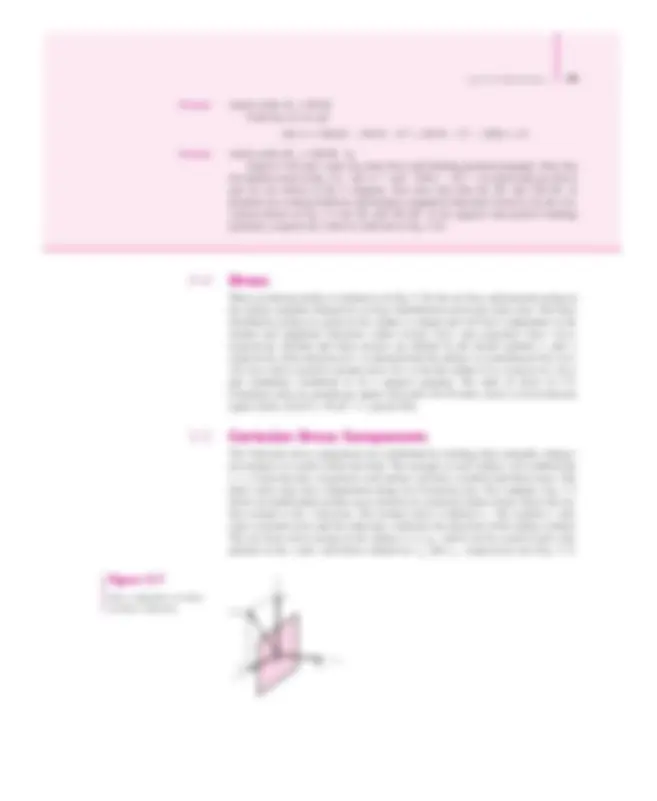
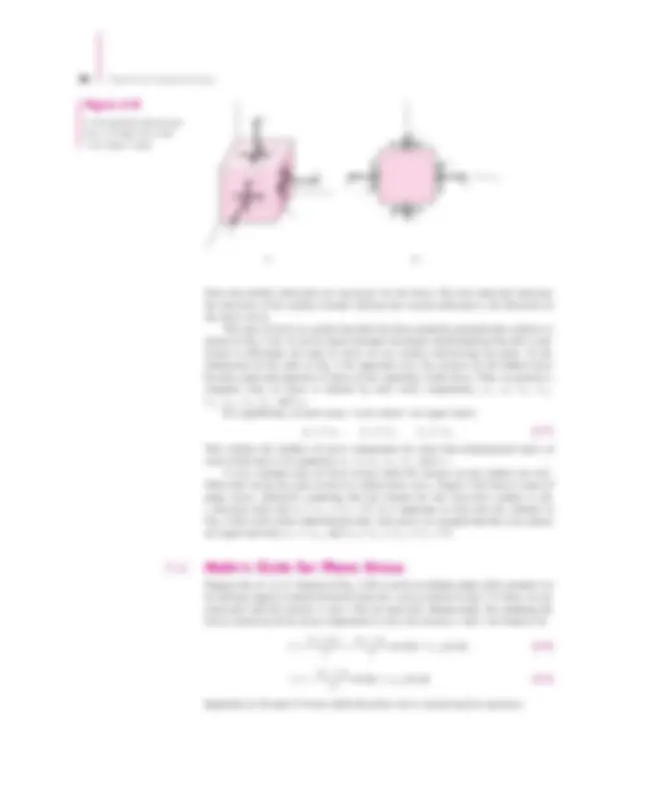
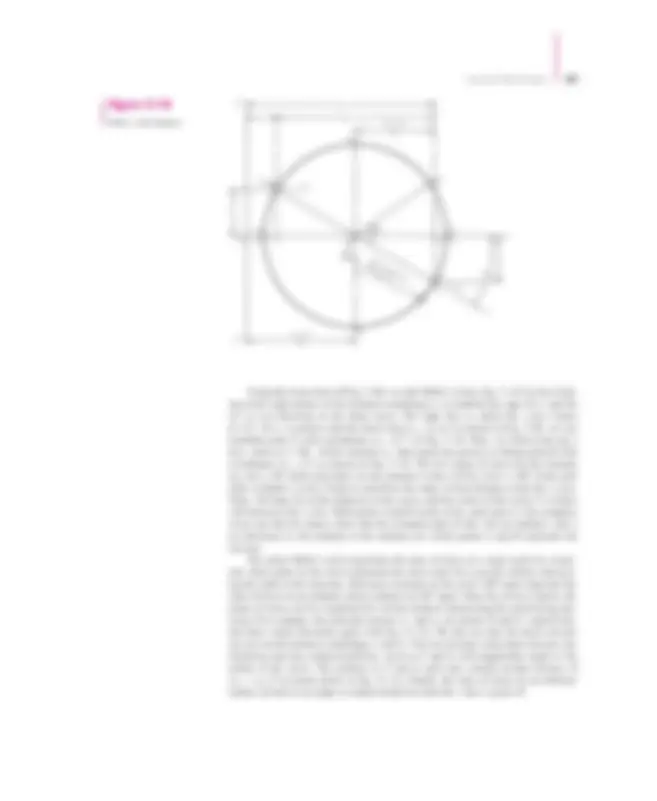
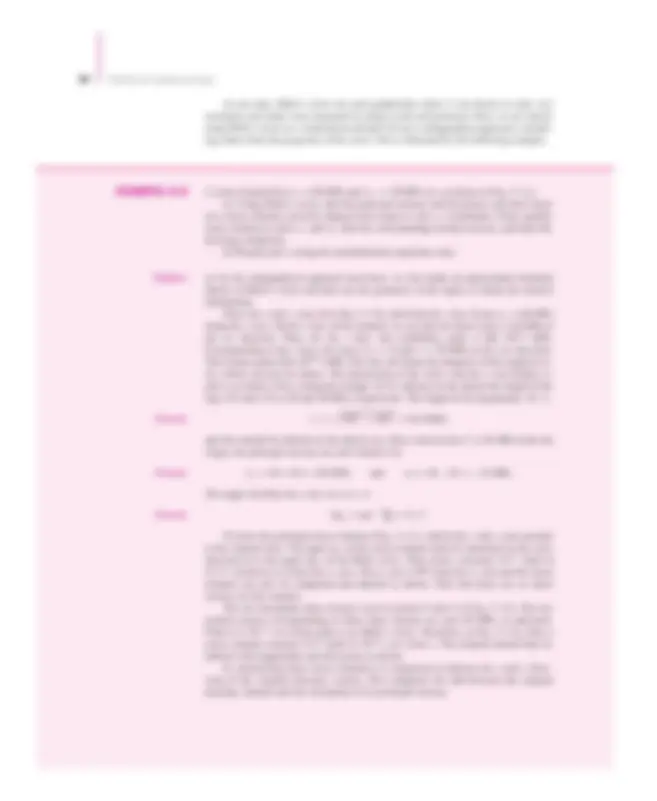
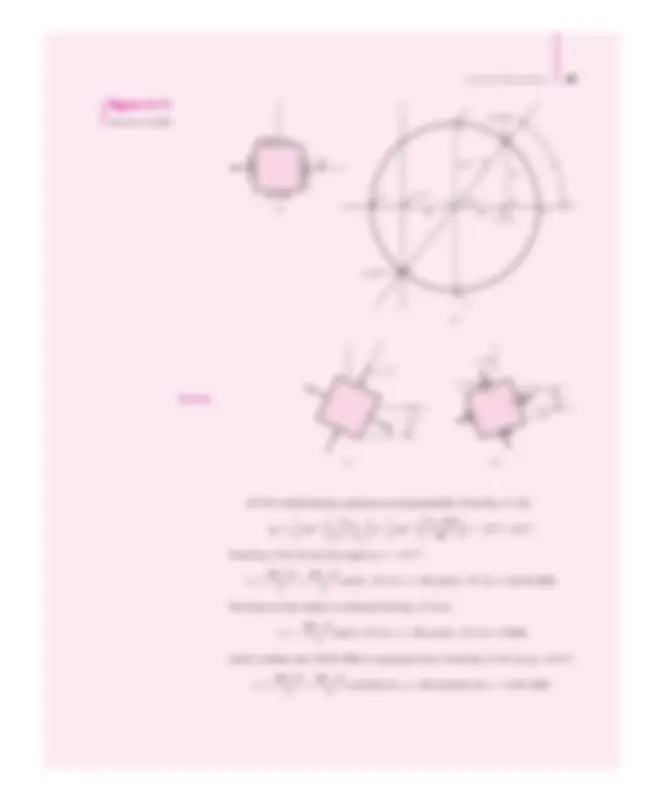
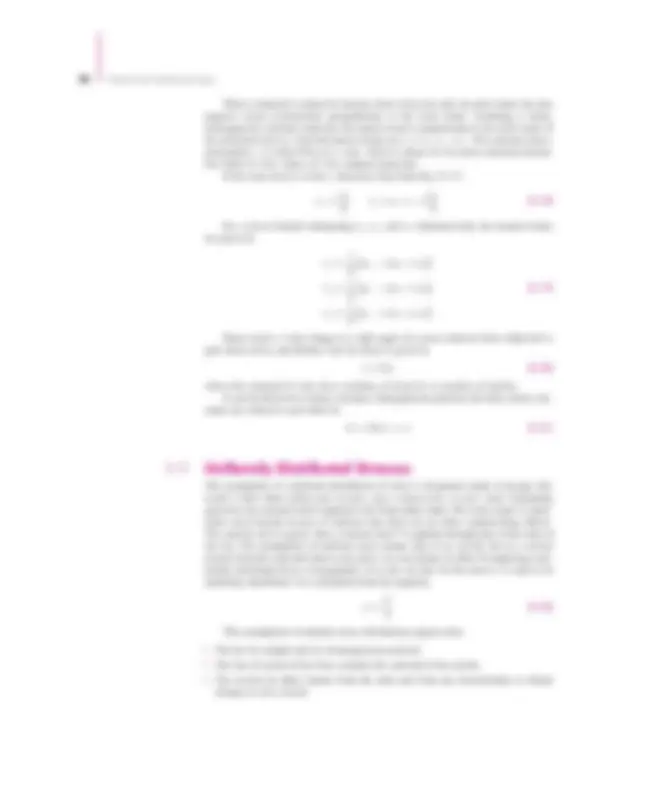
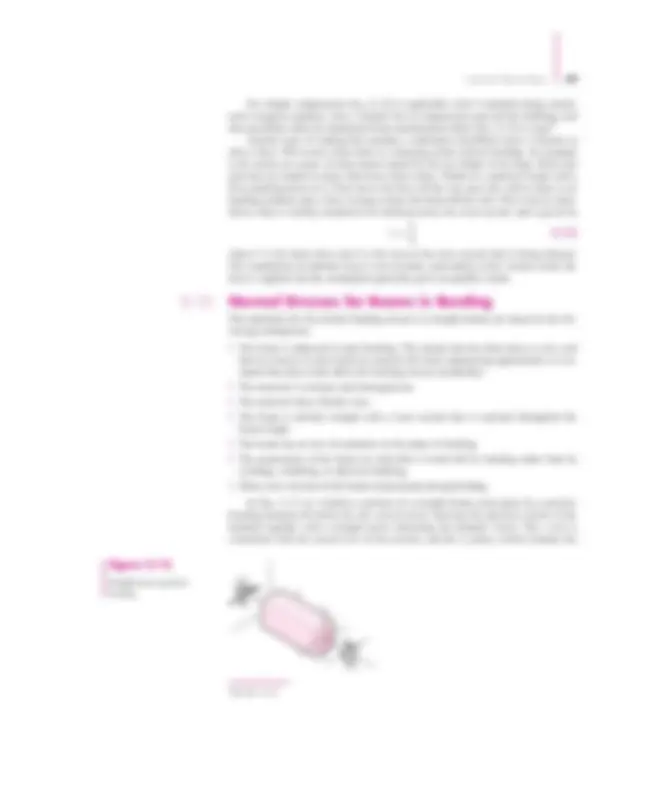
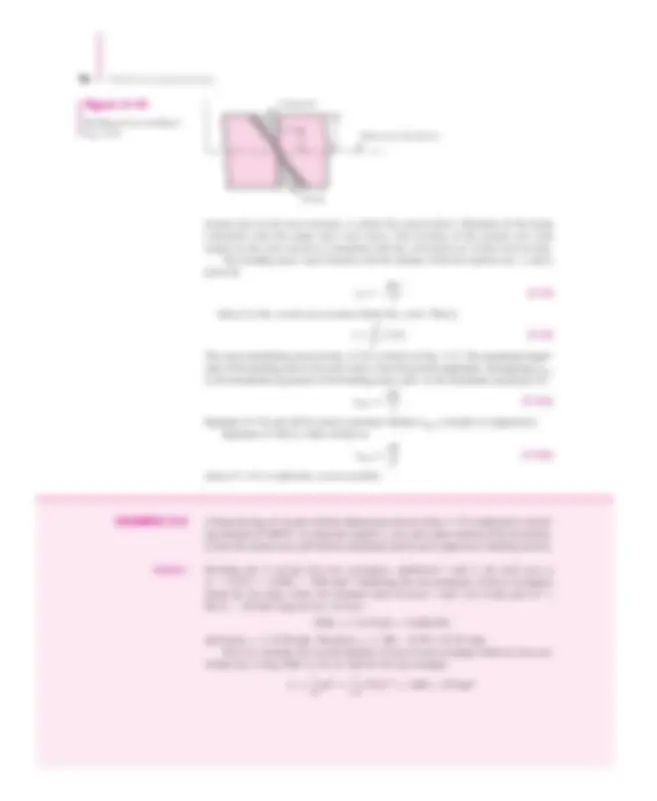
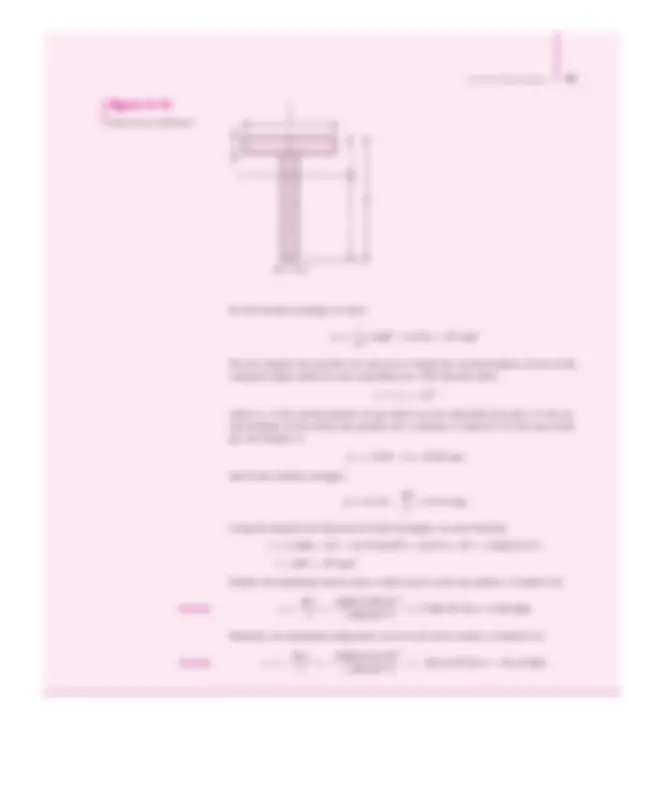
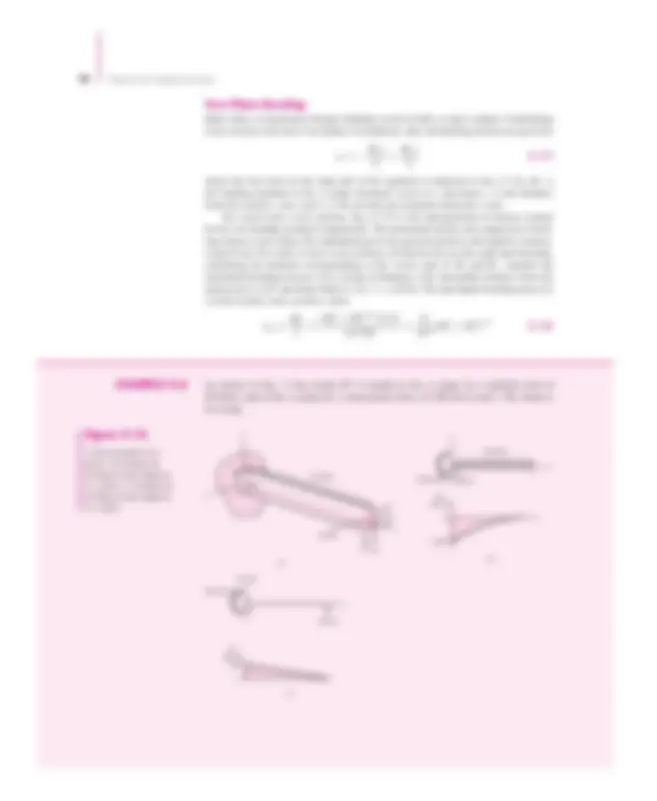
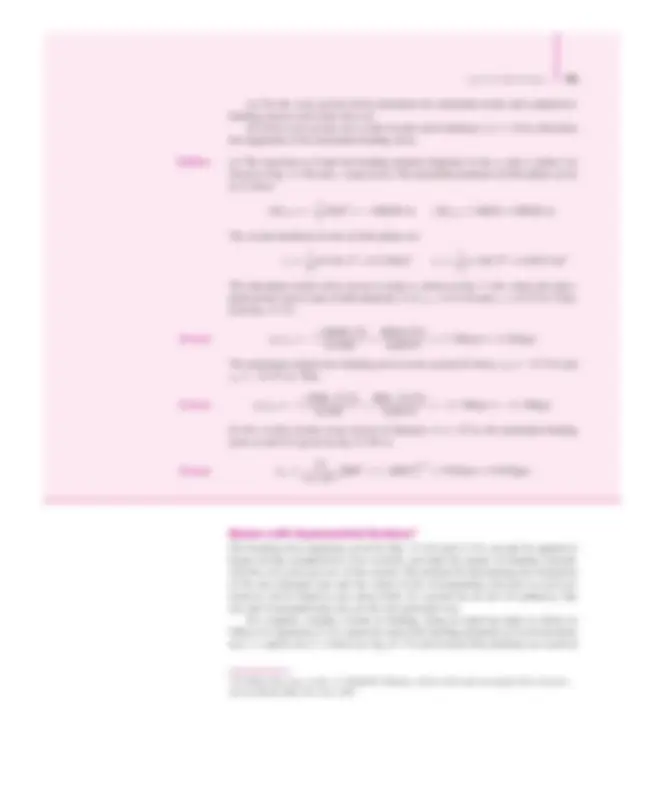
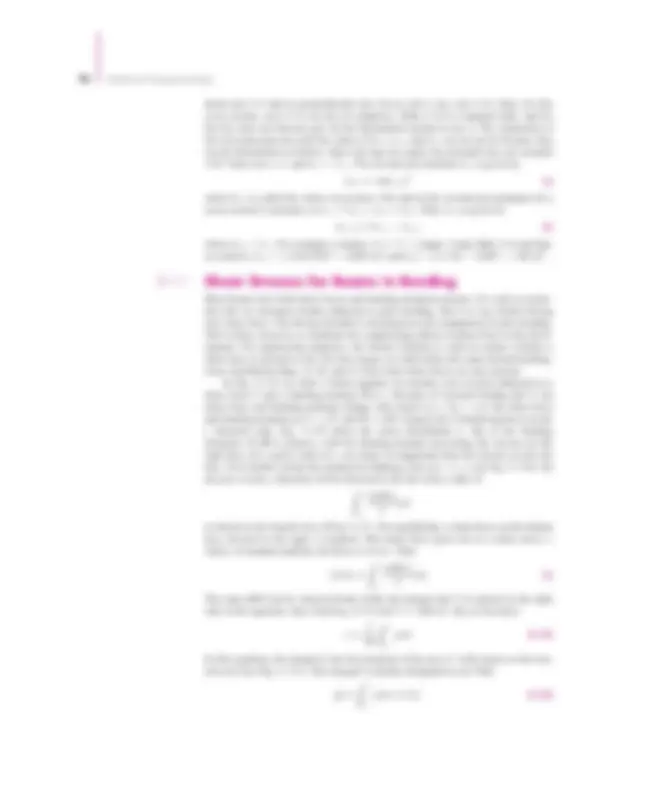
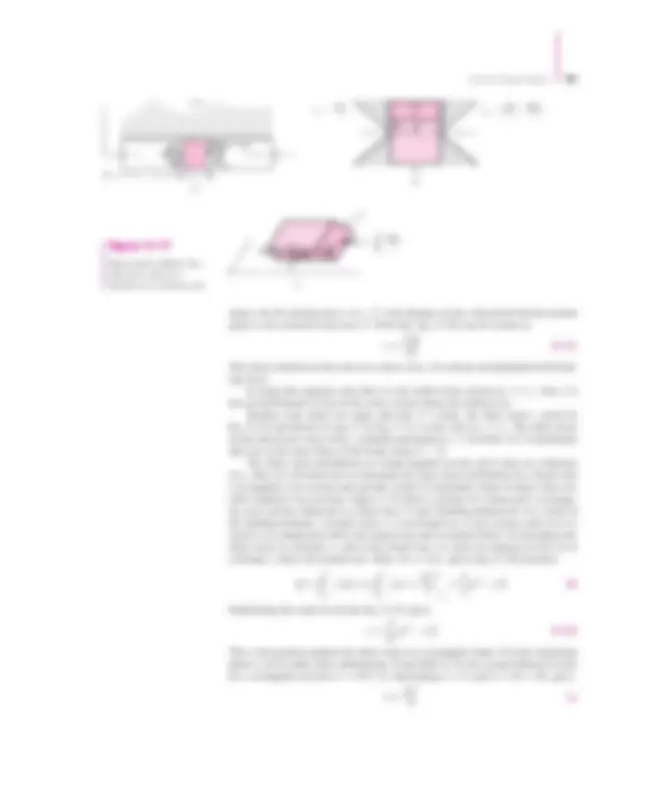
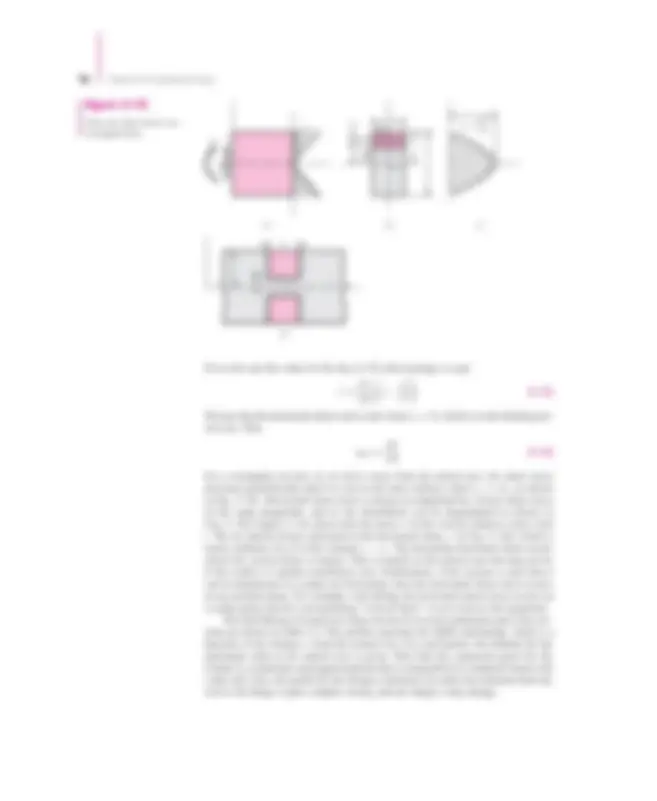
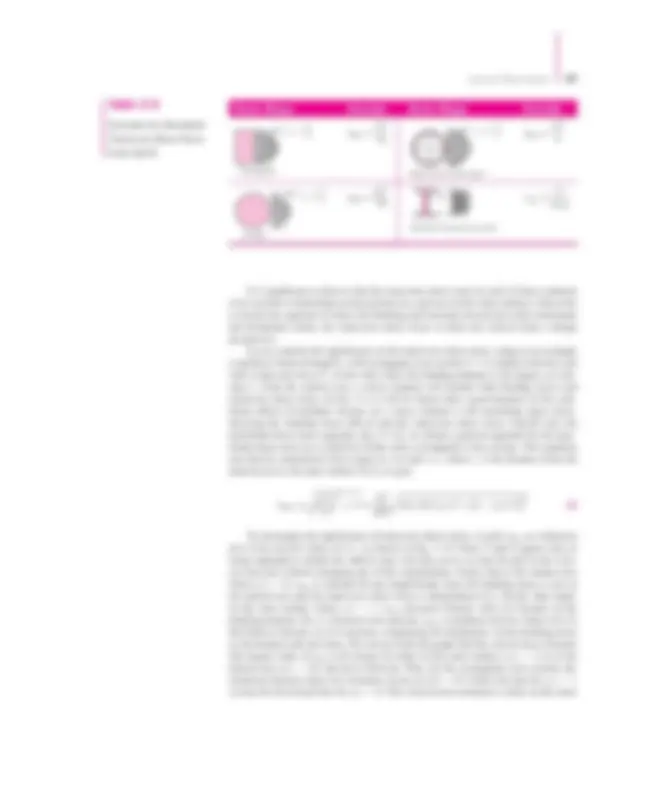
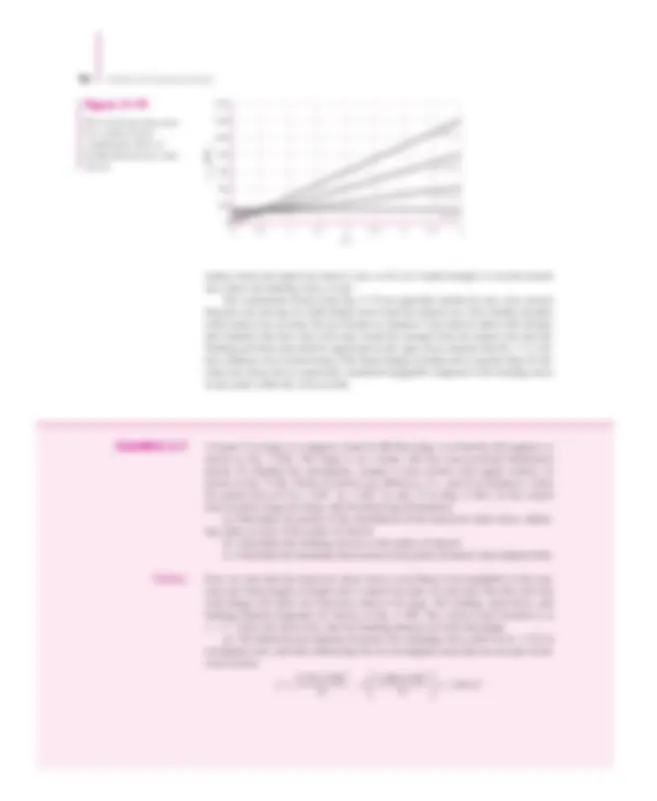
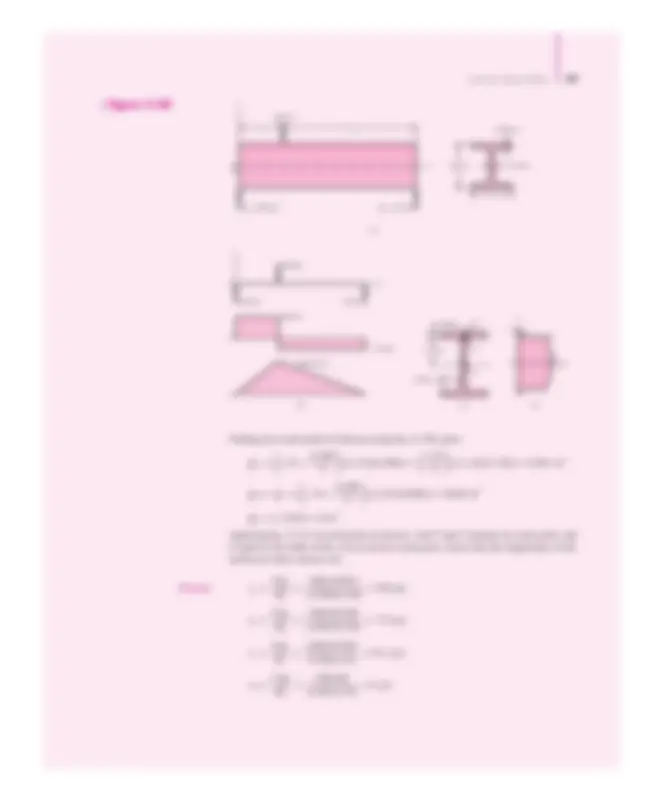
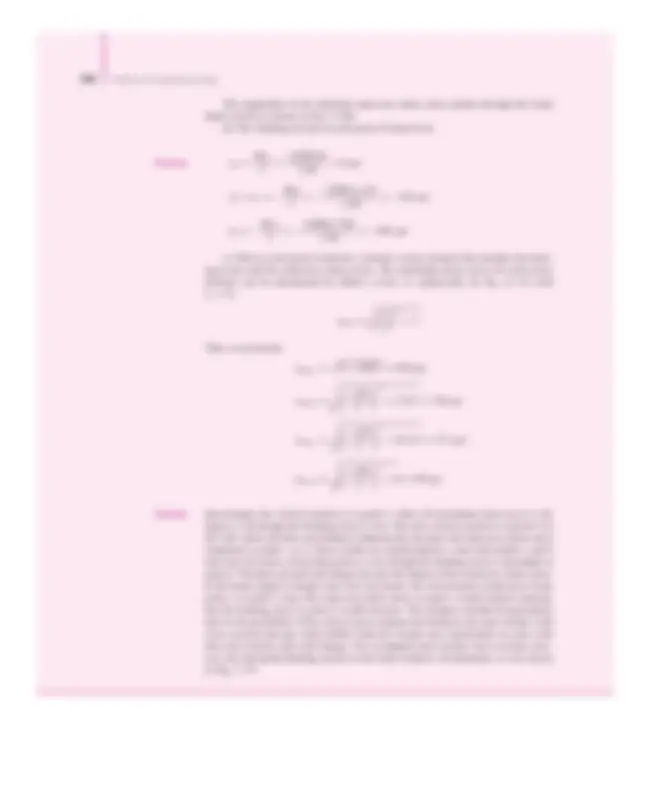
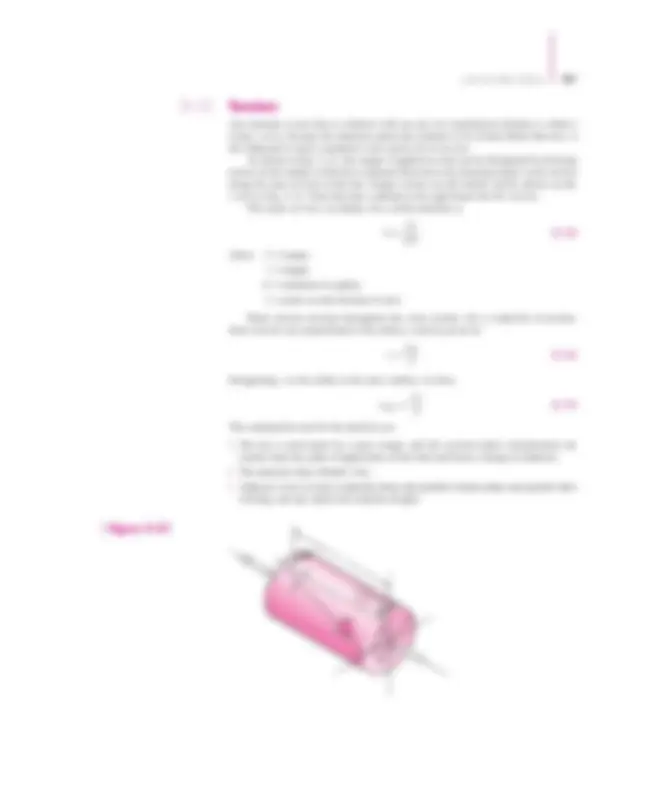
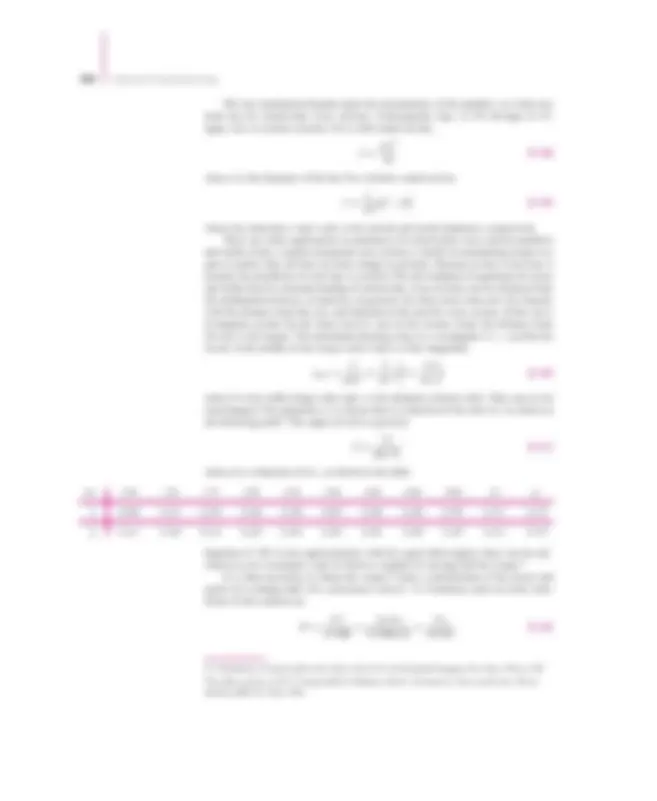
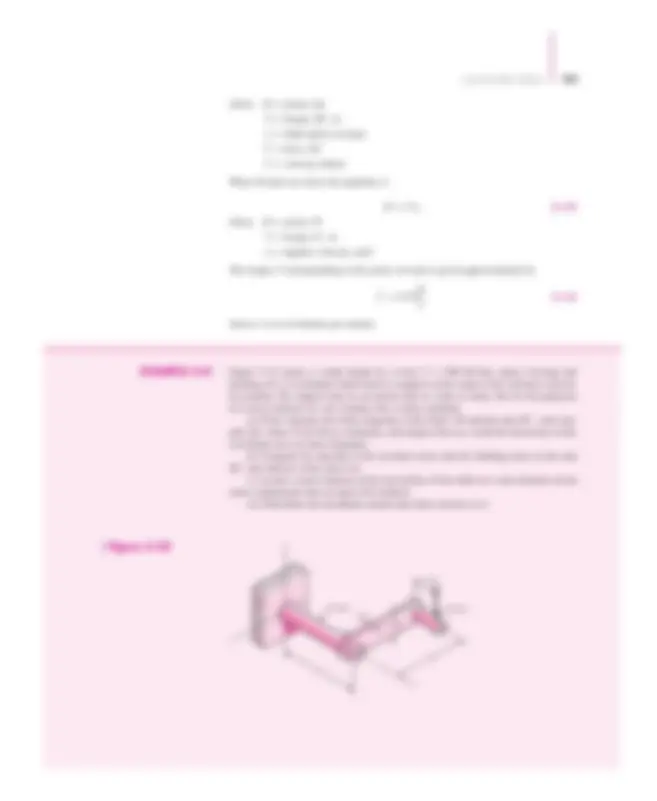
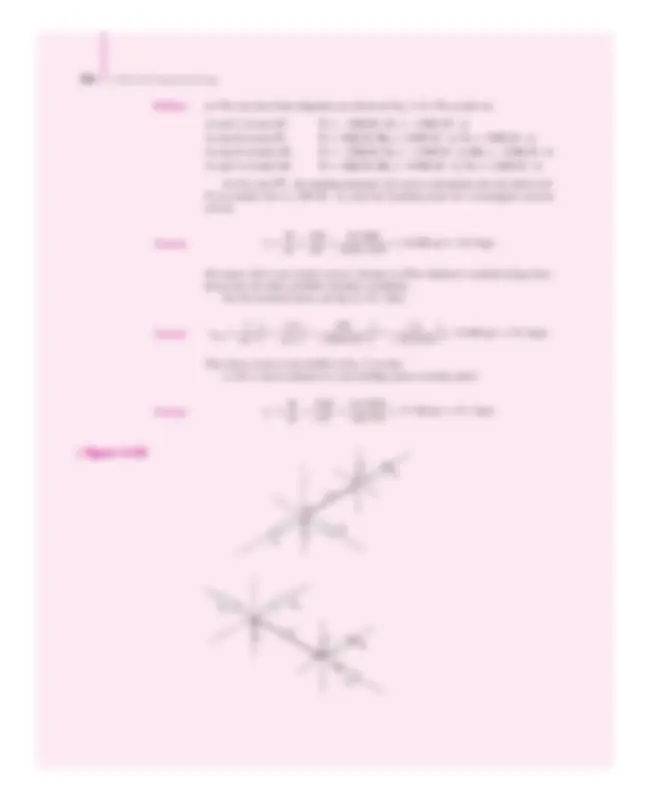
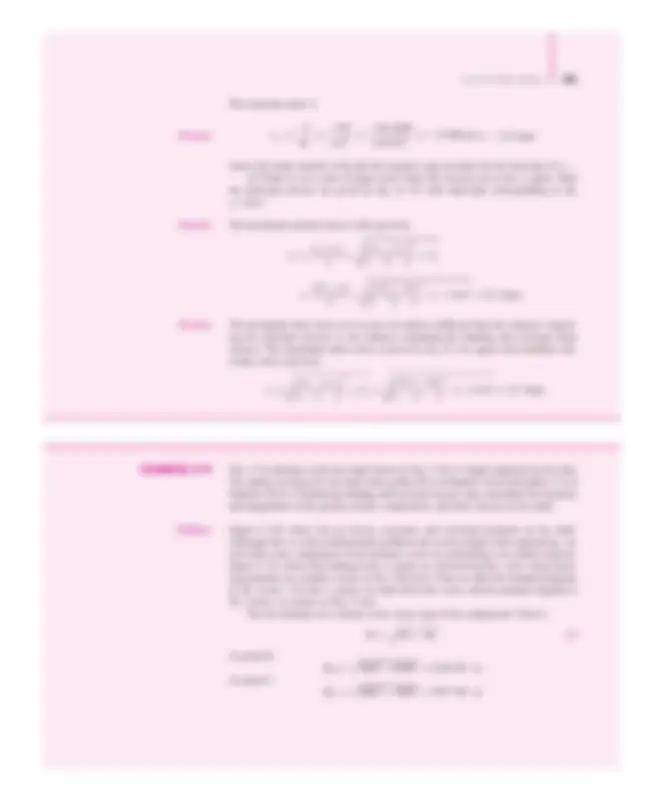
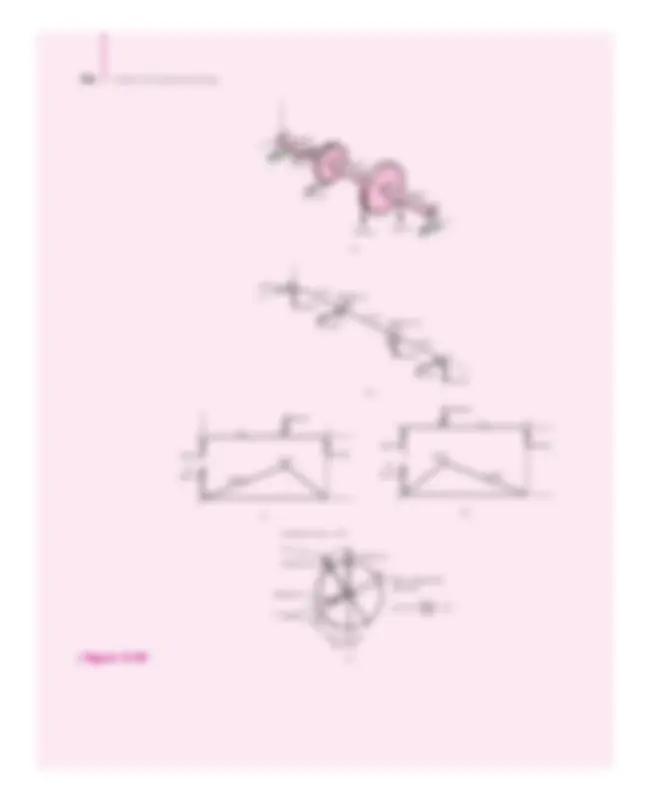
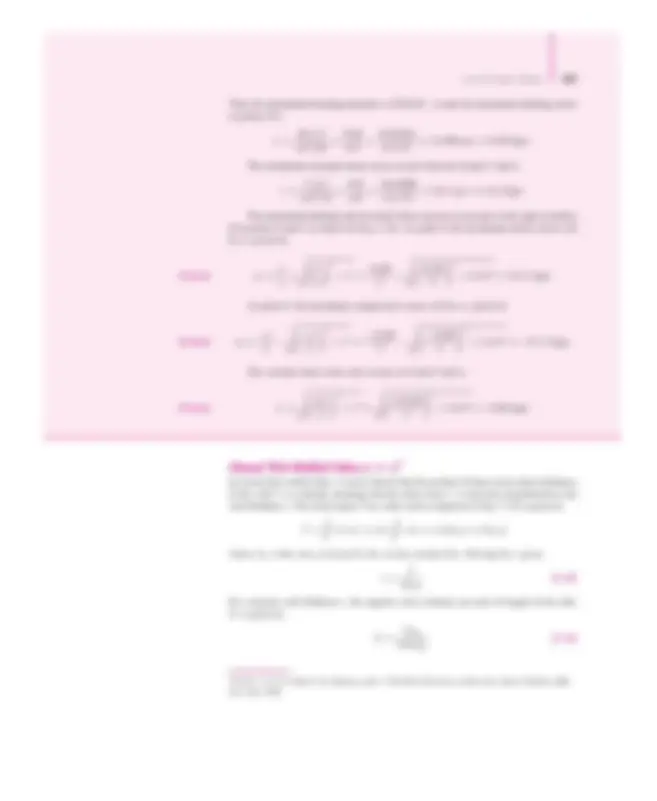
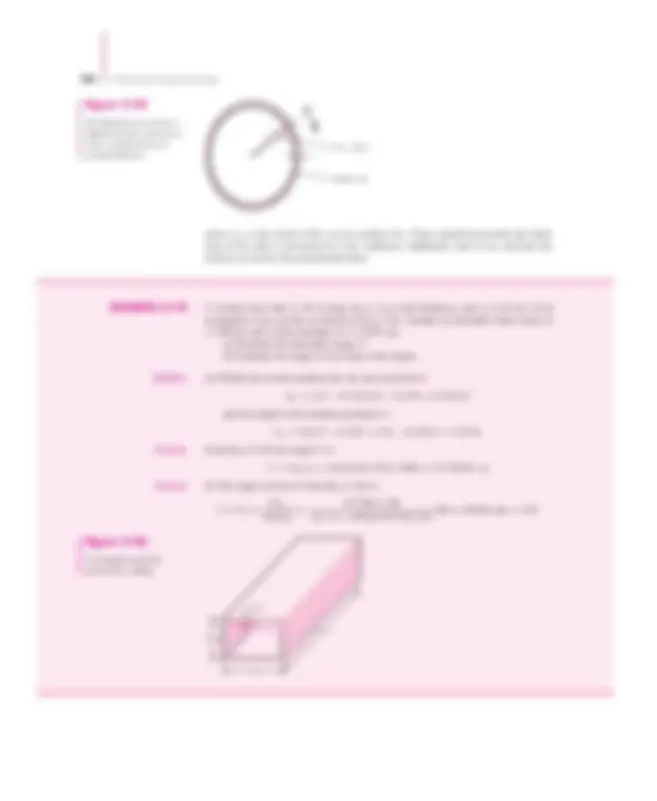
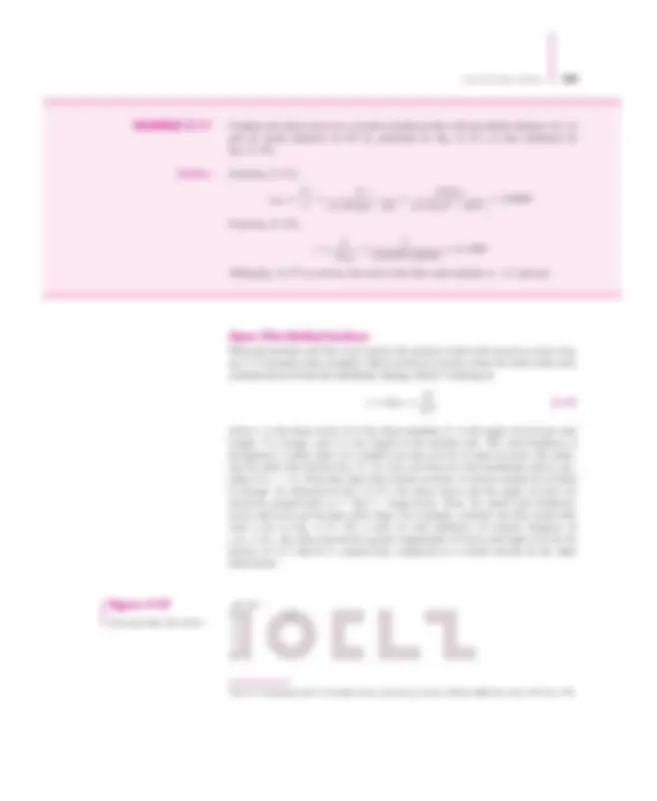
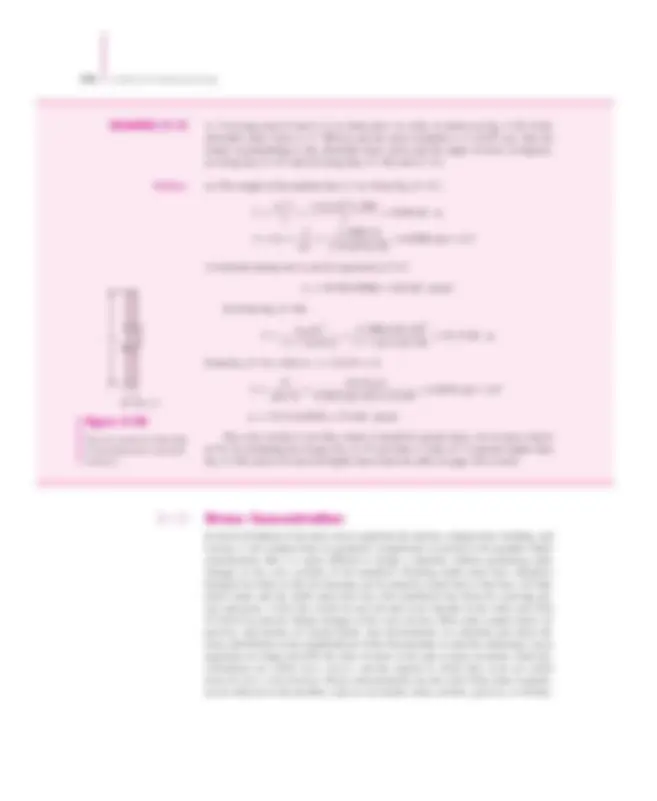
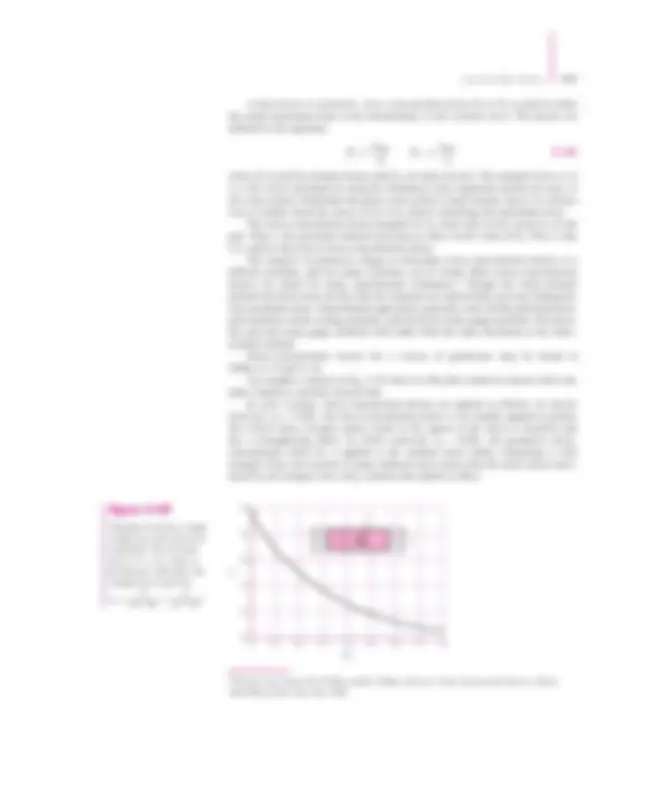
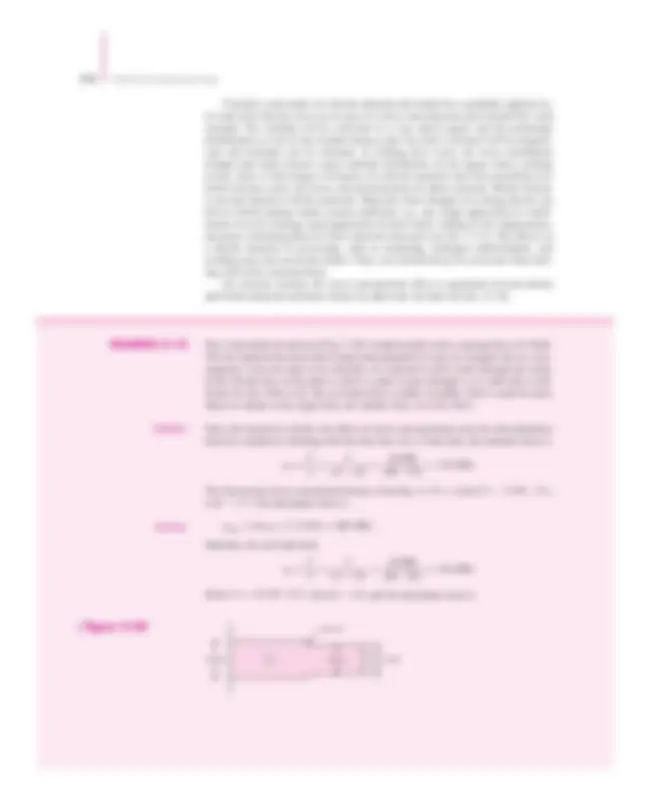
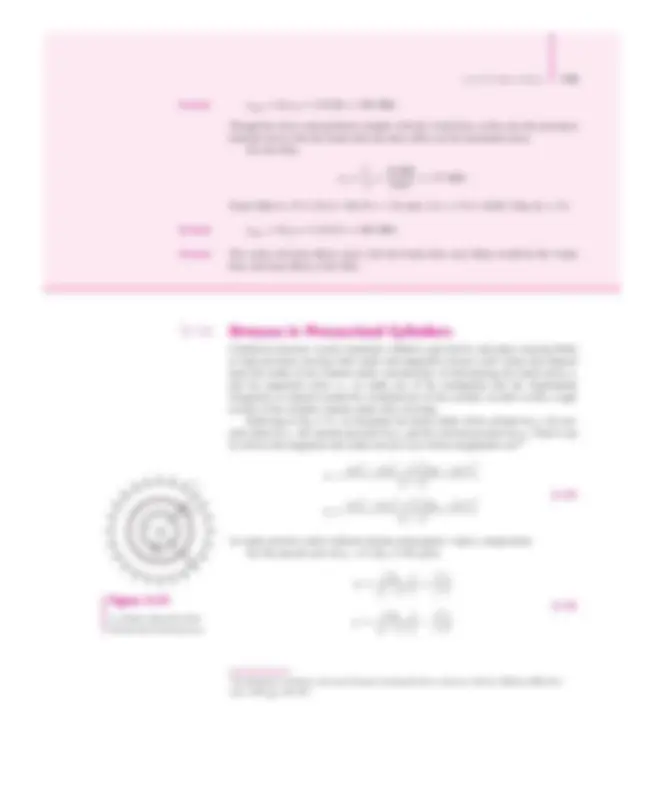
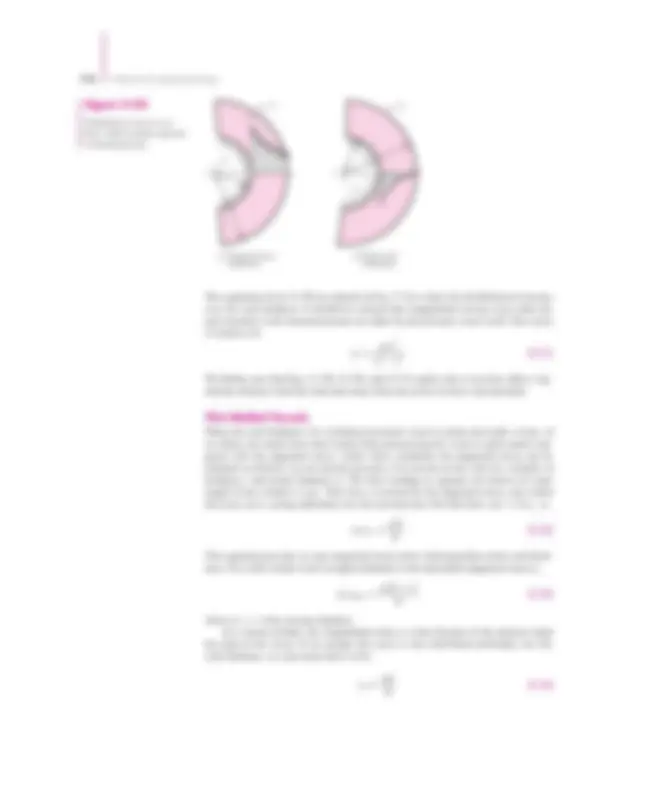
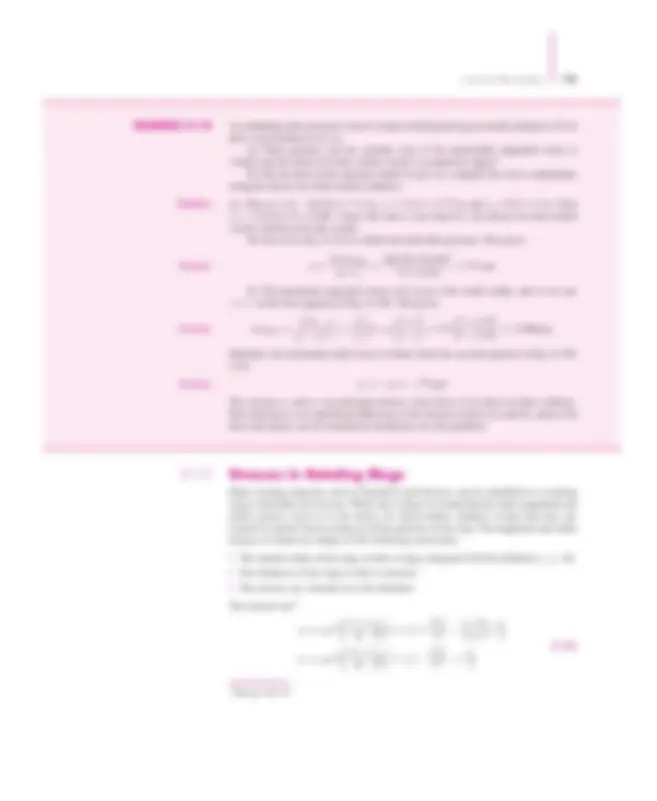
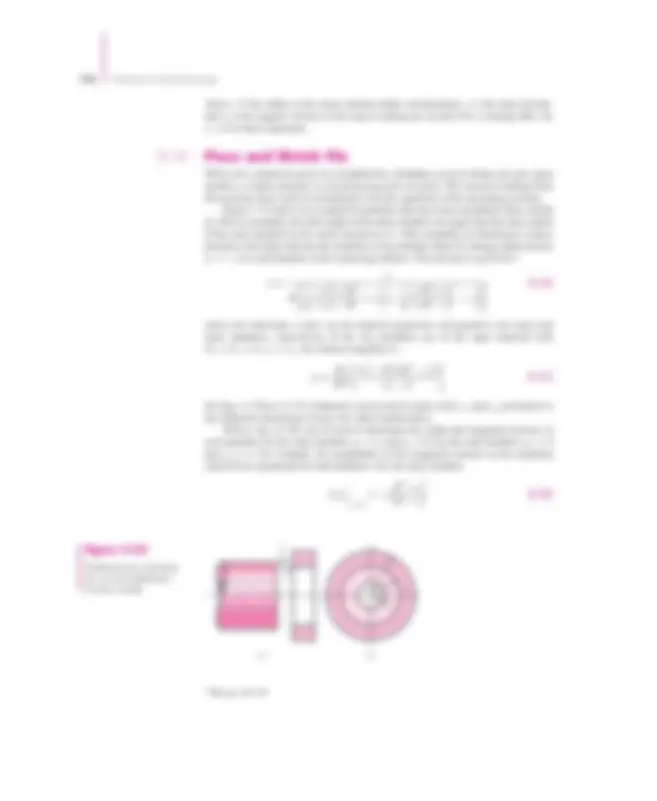
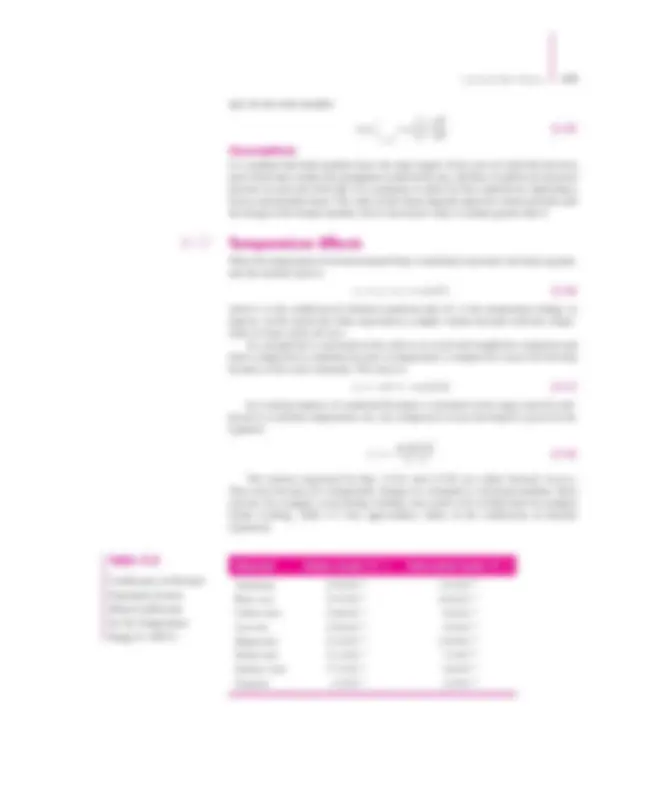
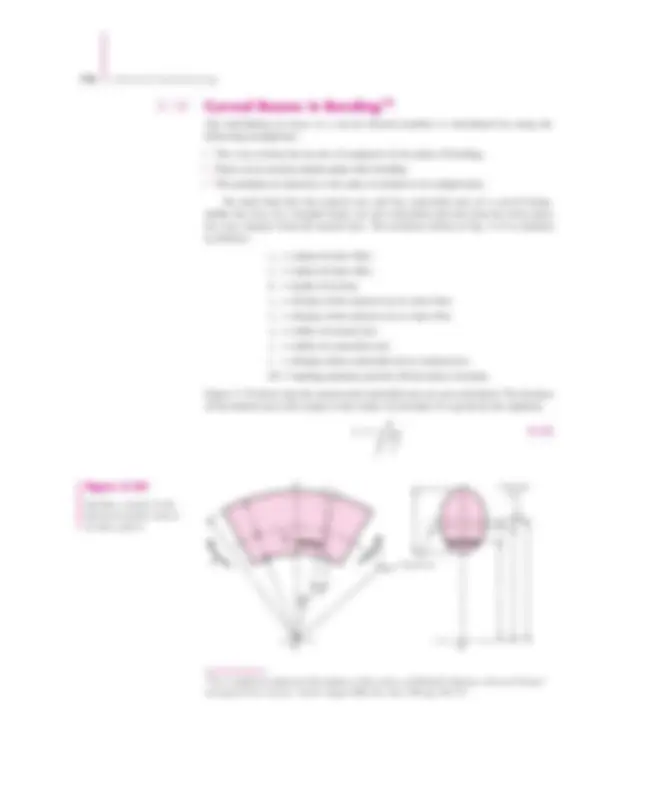
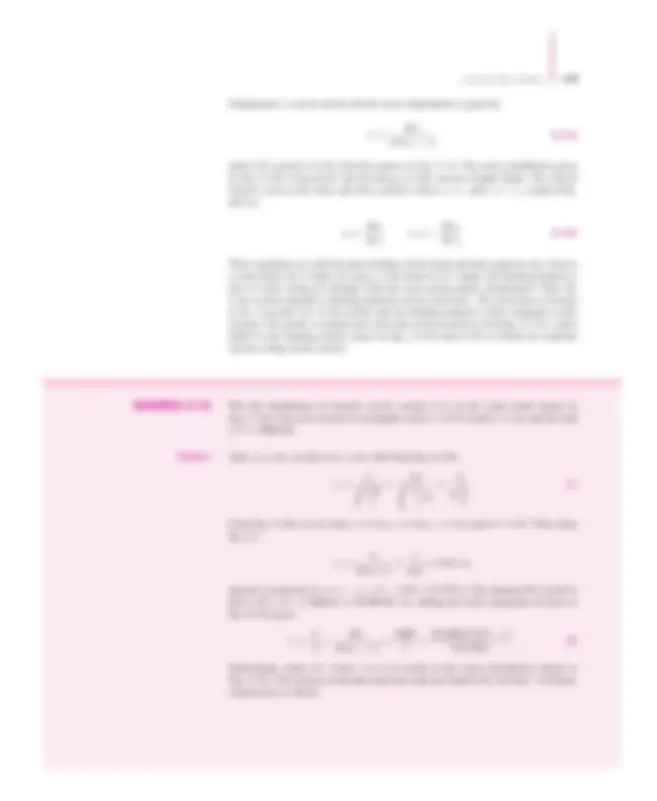
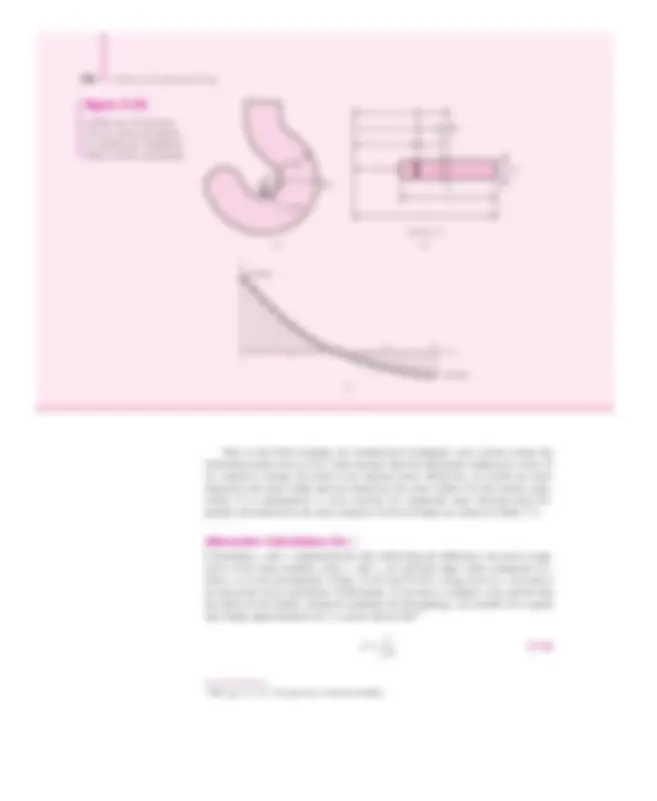
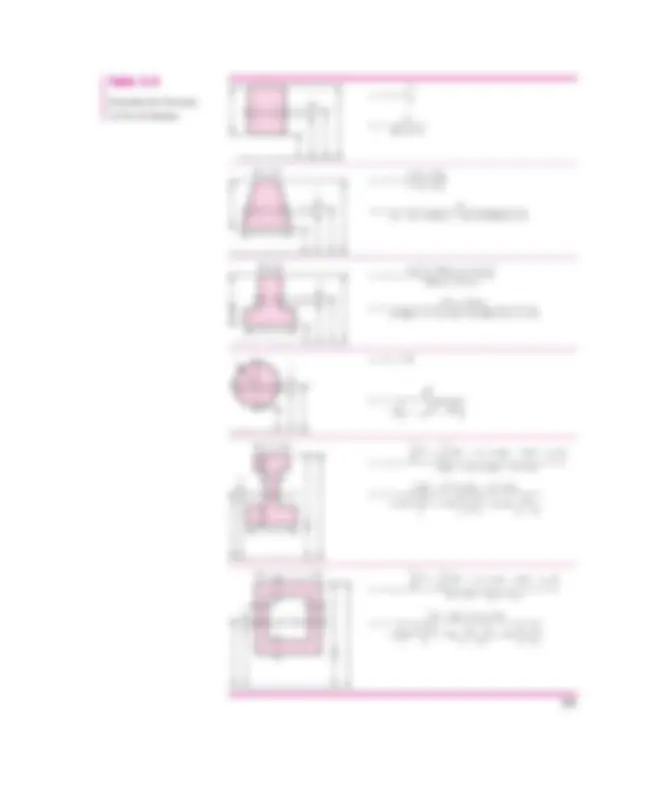
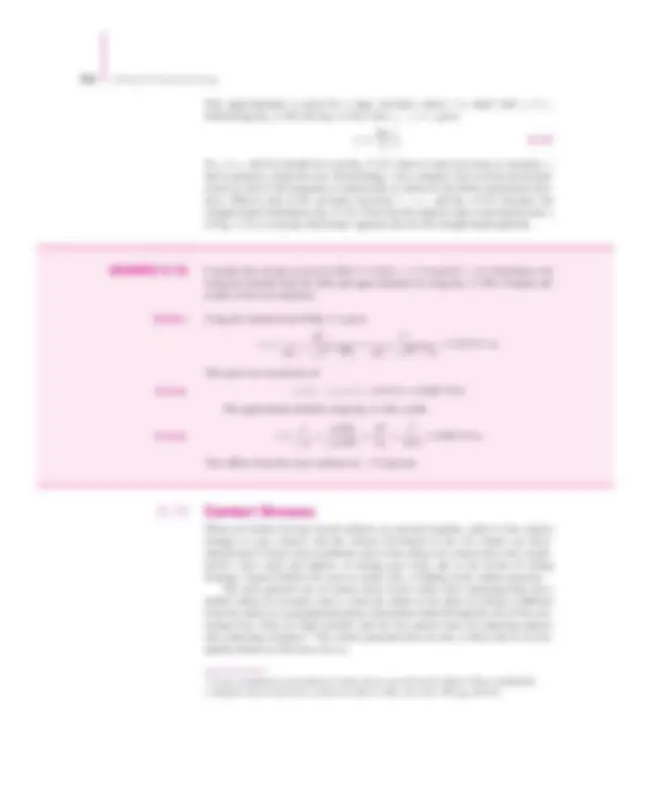
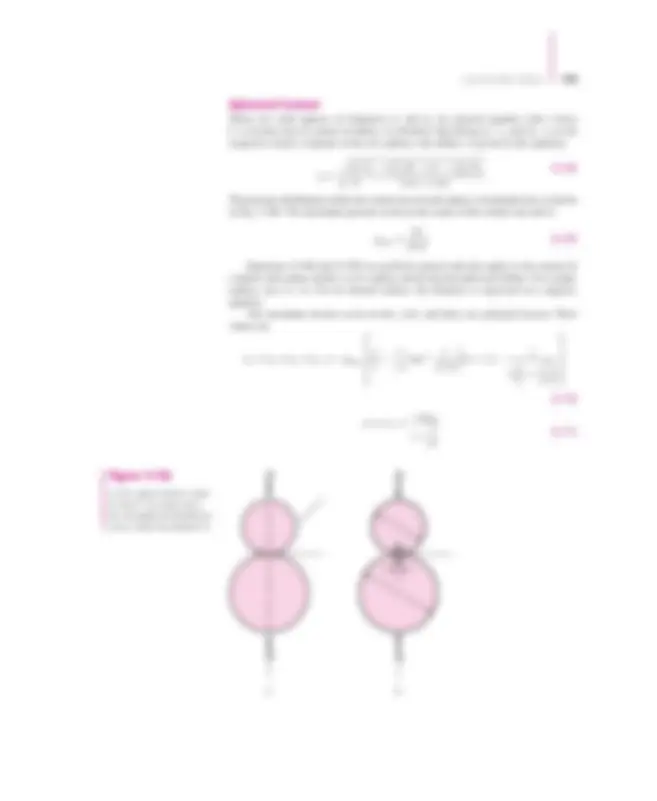
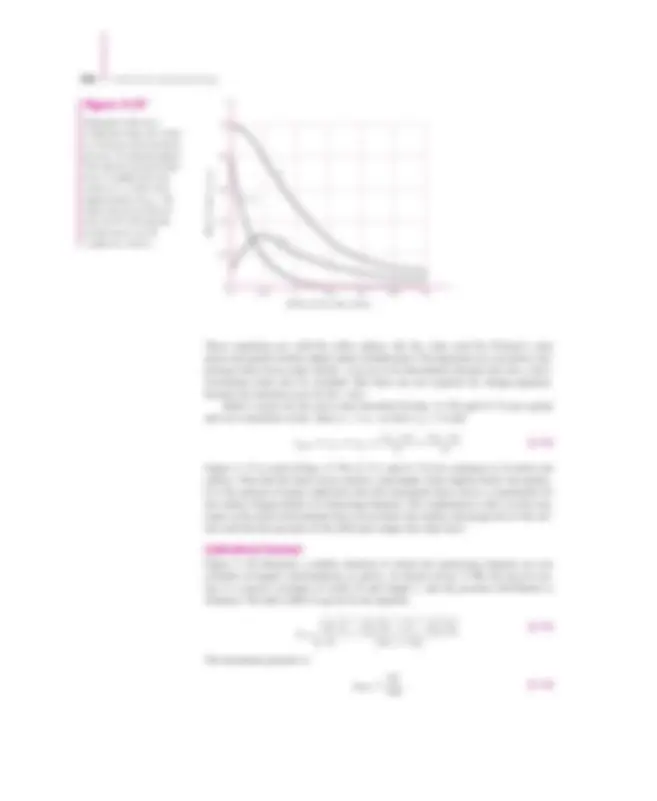
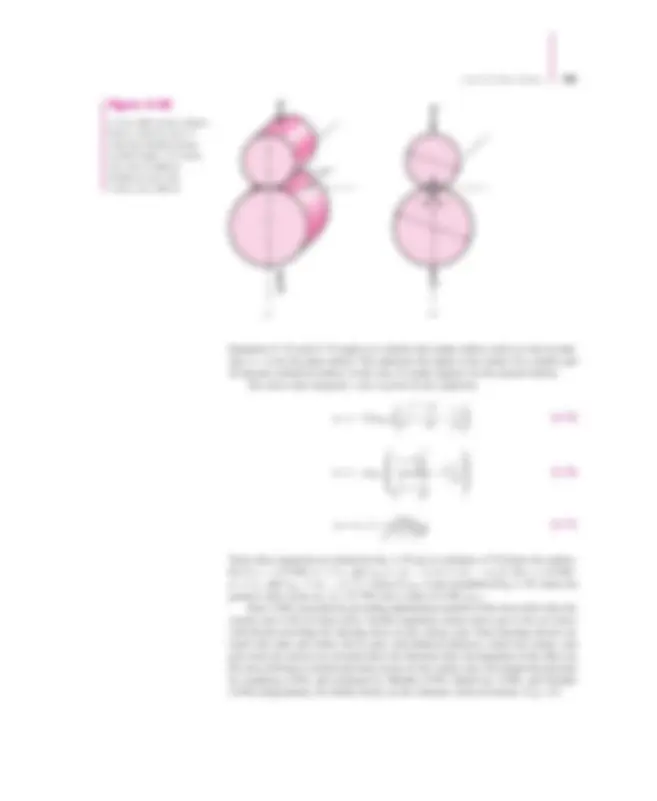

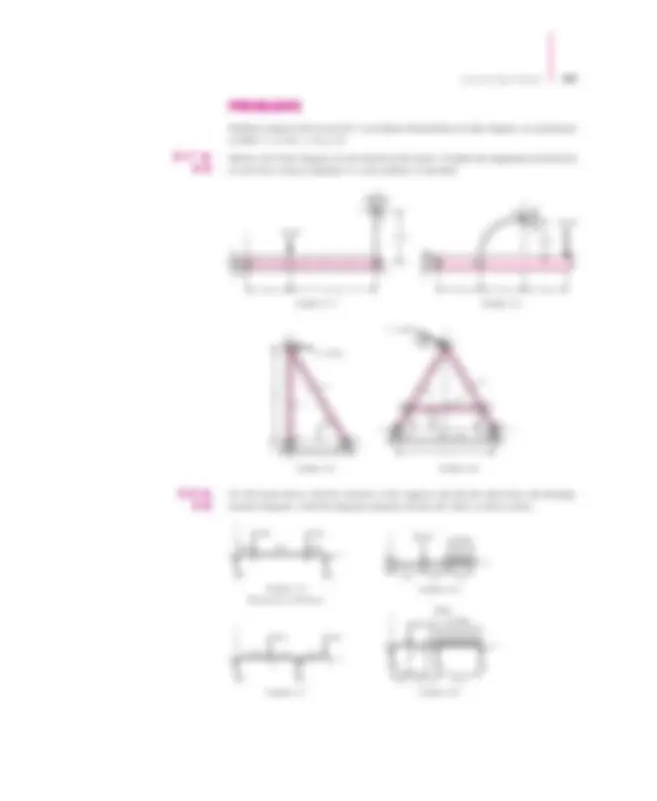
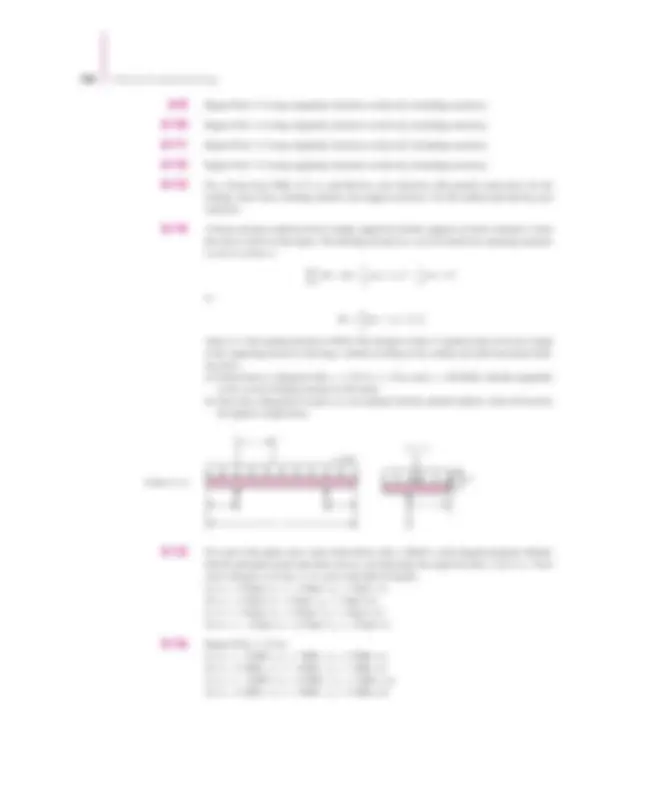
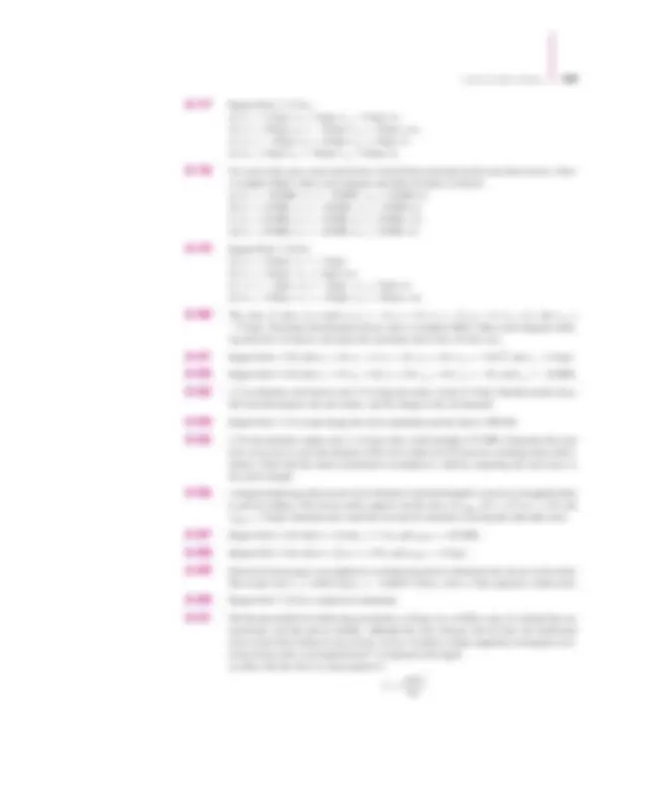
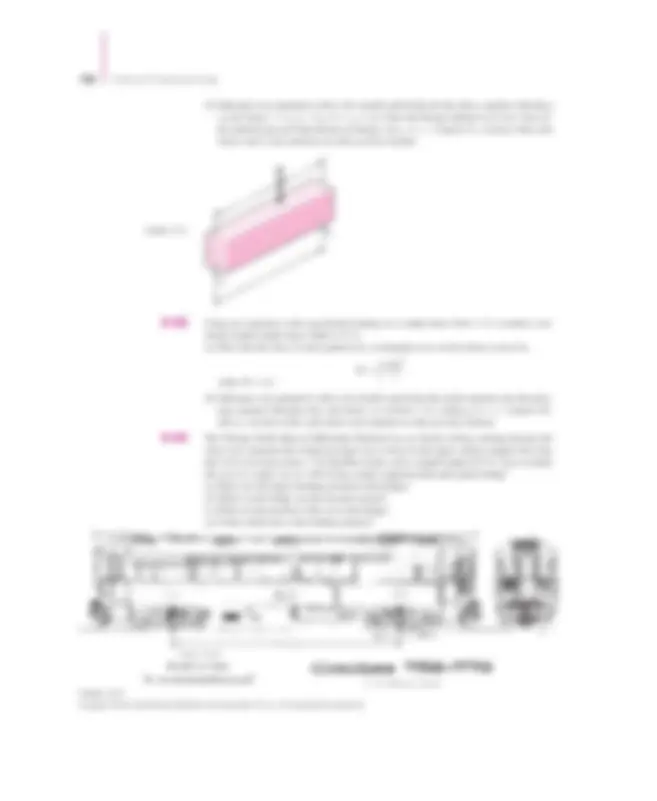
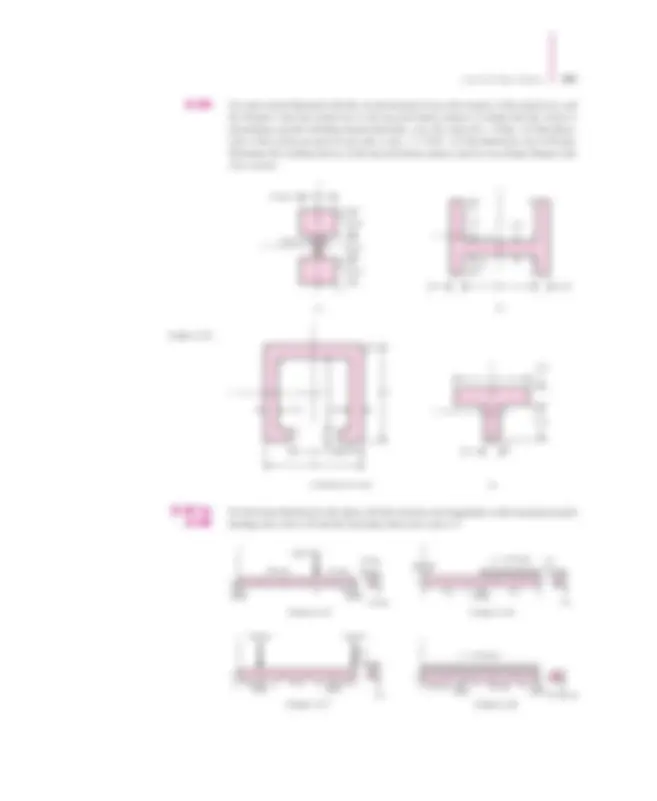
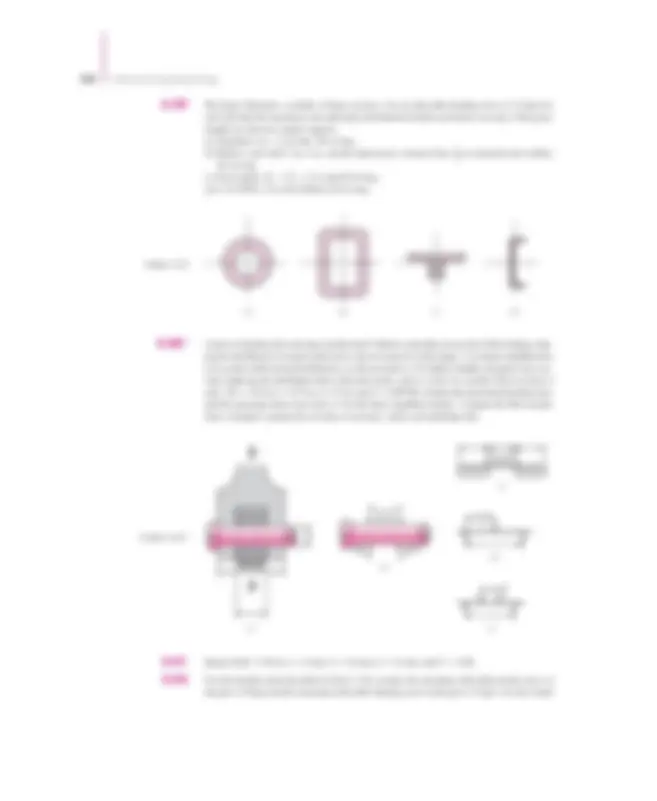
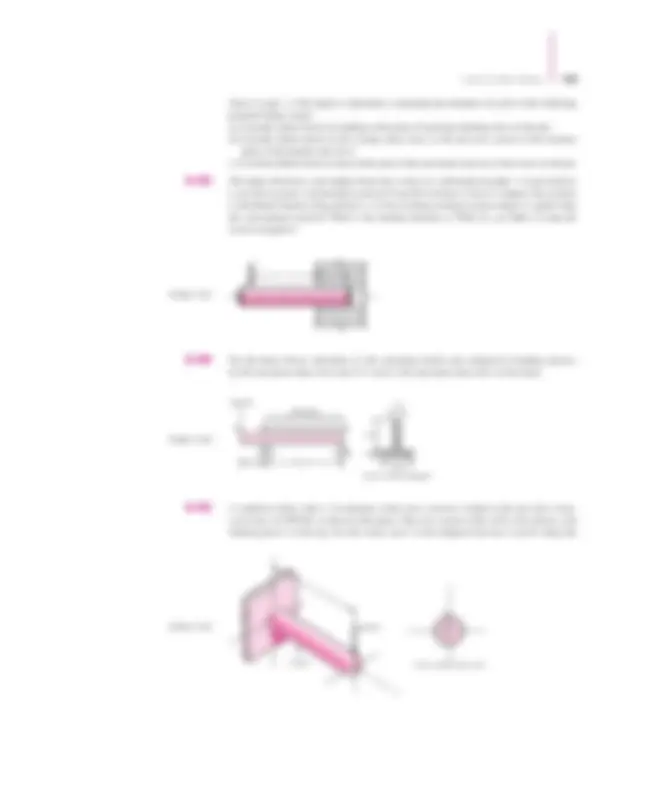
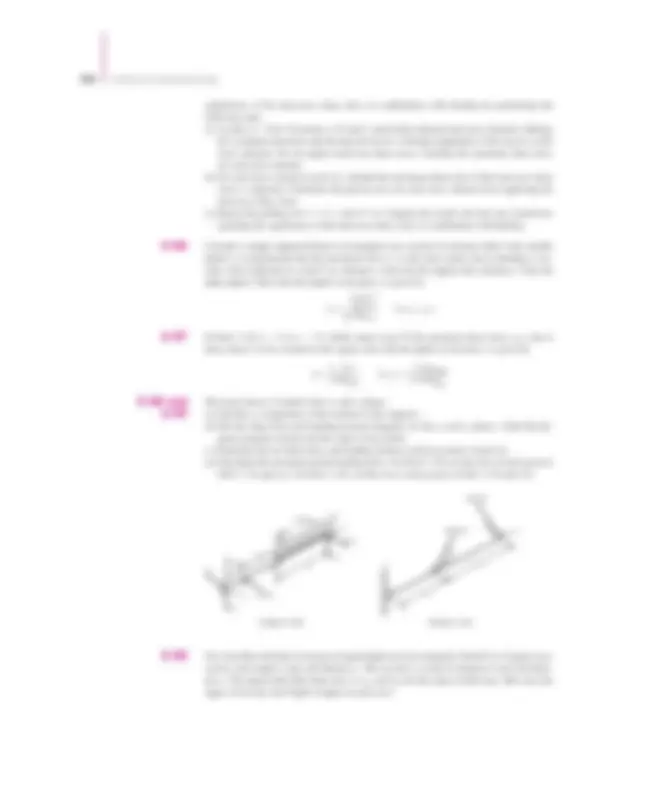
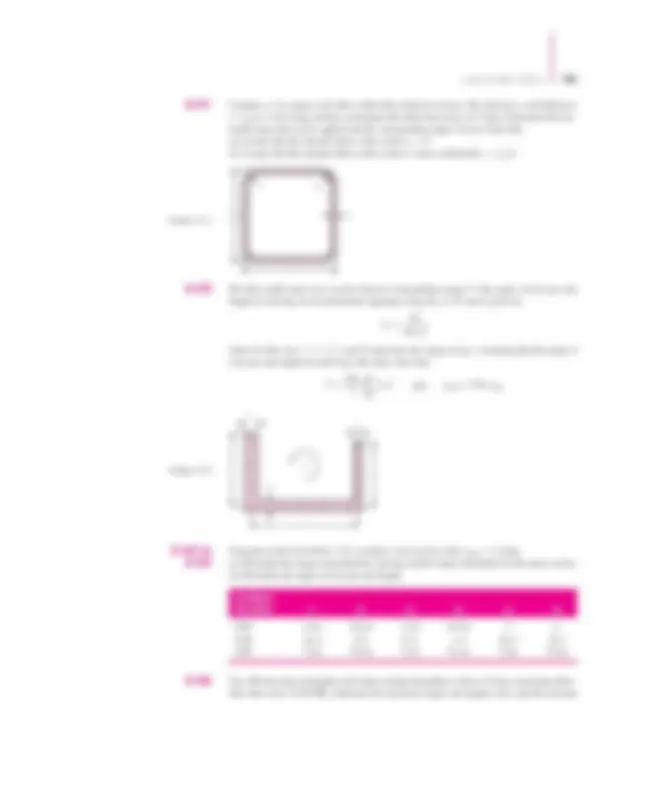

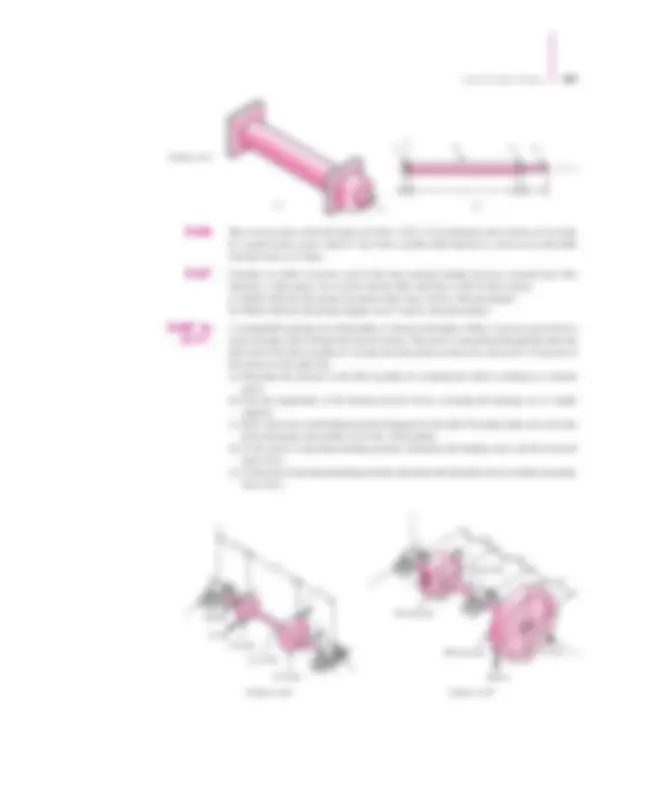
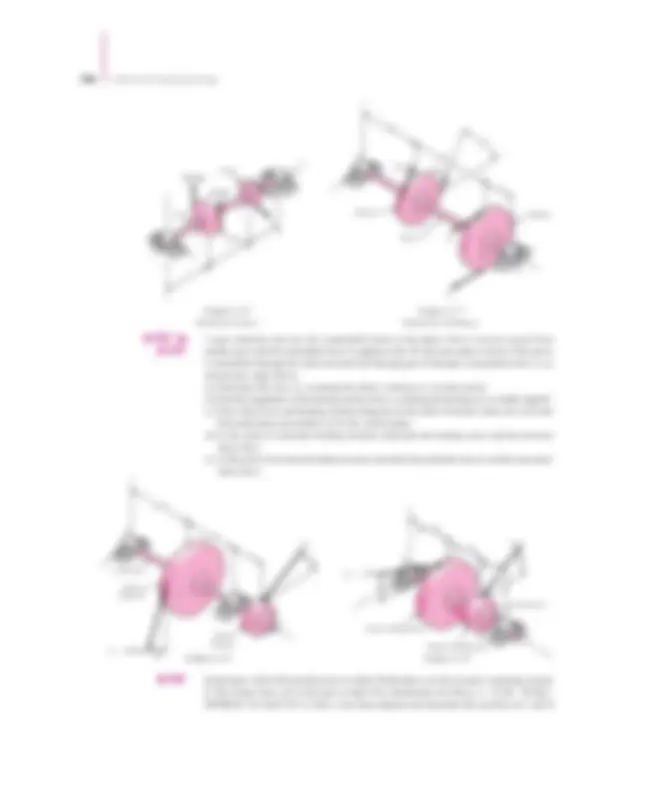
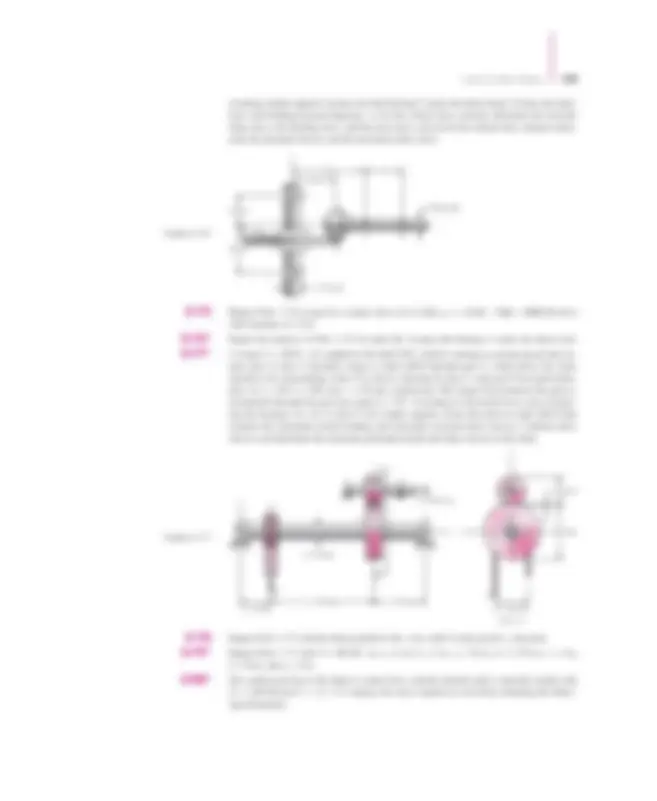
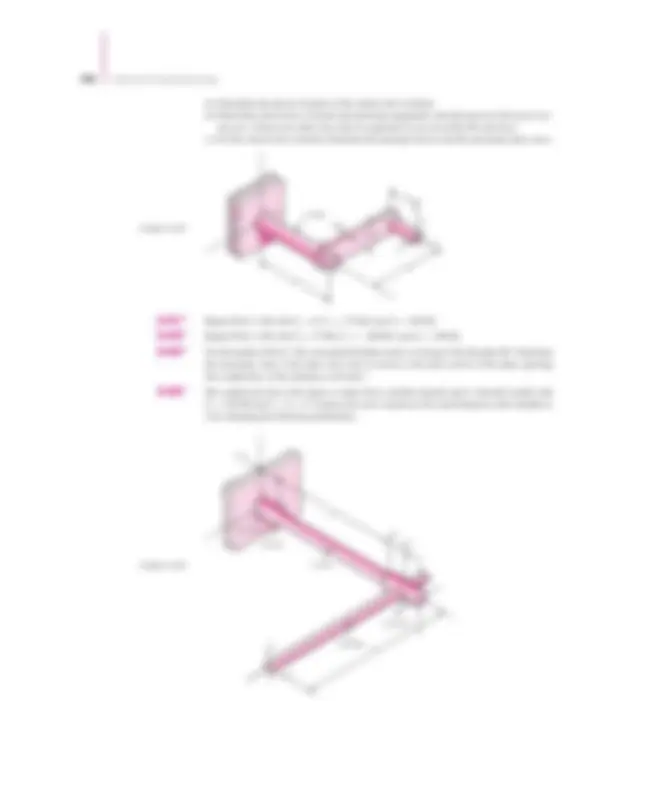
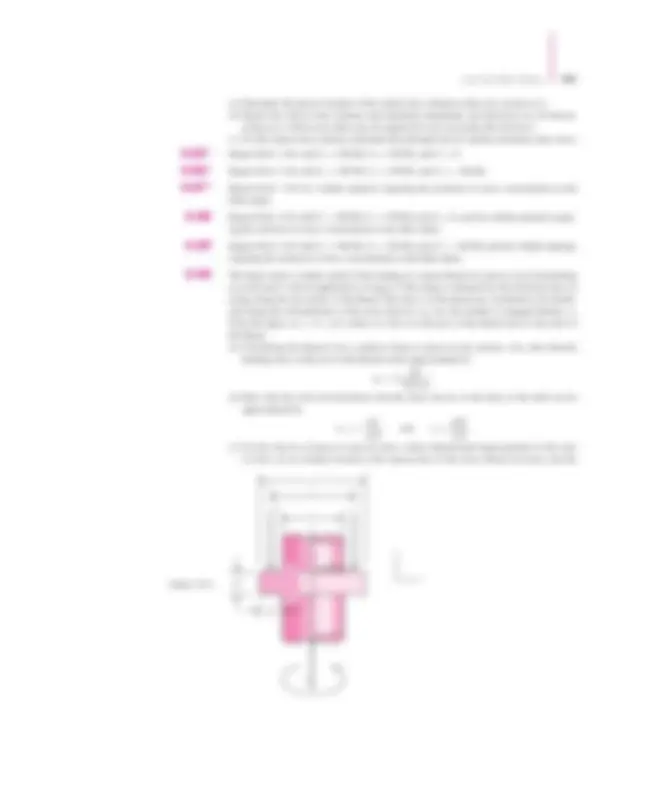
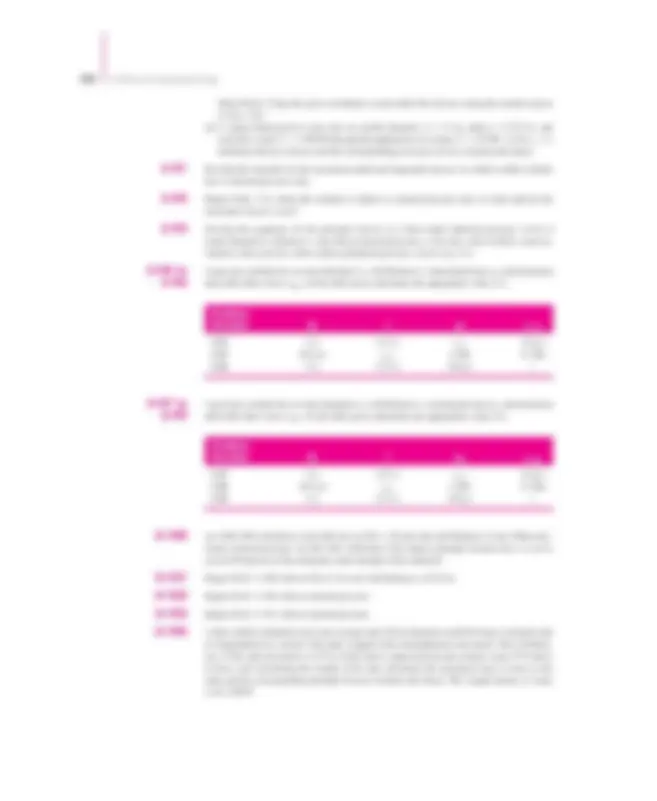
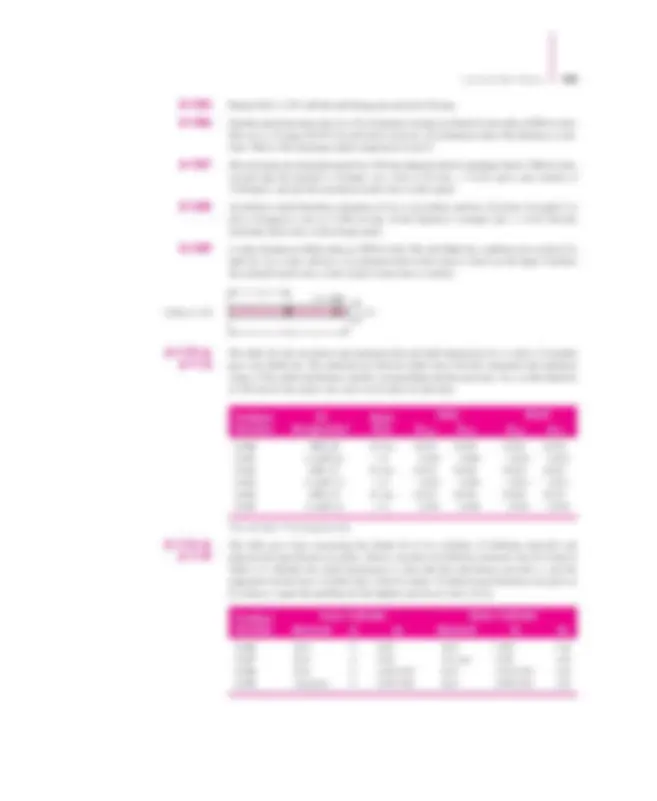
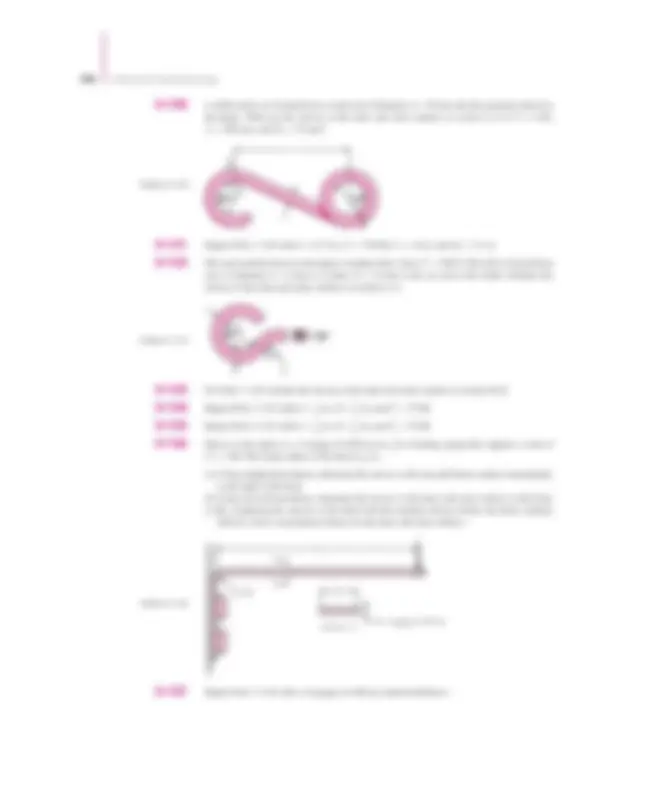
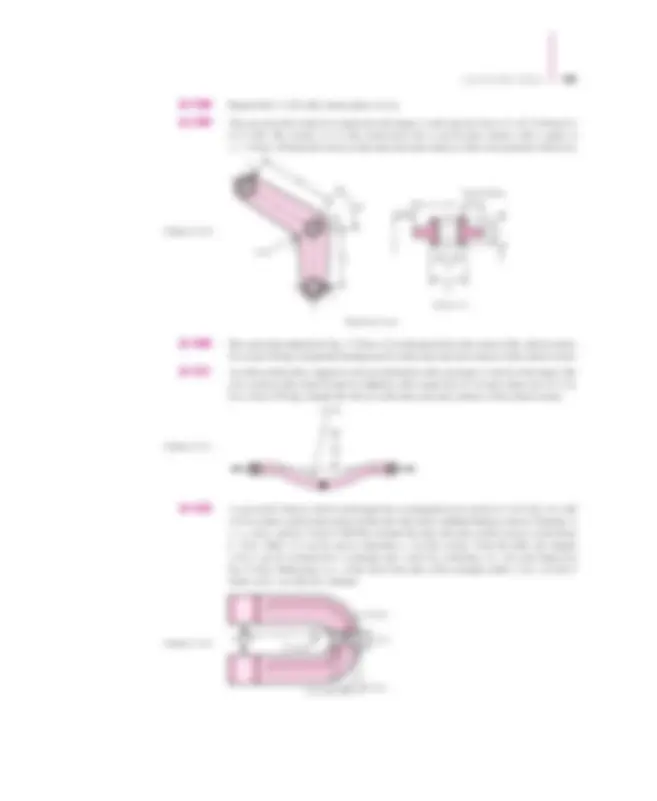
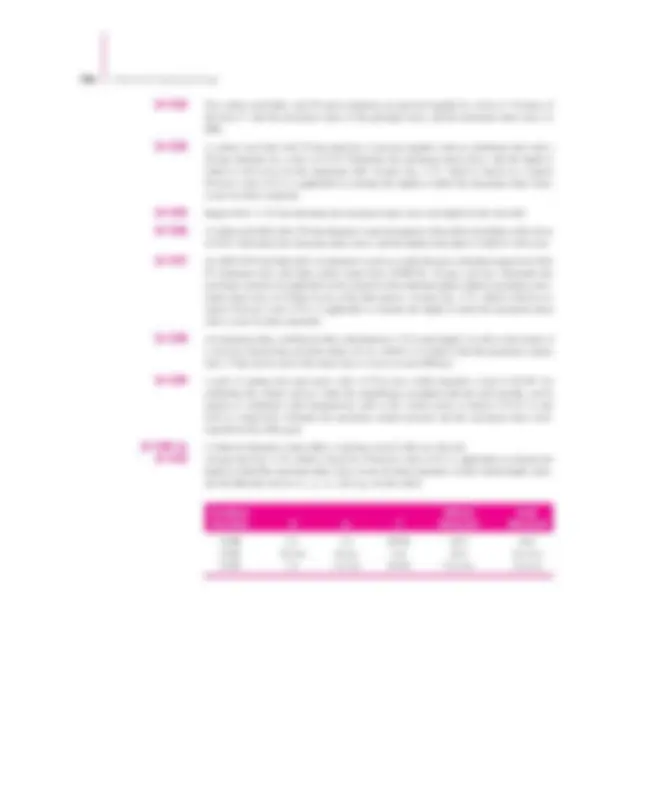
Study with the several resources on Docsity
Earn points by helping other students or get them with a premium plan
Prepare for your exams
Study with the several resources on Docsity
Earn points to download
Earn points by helping other students or get them with a premium plan
Community
Ask the community for help and clear up your study doubts
Discover the best universities in your country according to Docsity users
Free resources
Download our free guides on studying techniques, anxiety management strategies, and thesis advice from Docsity tutors
This Mechanical Engineering chapter has addressed the description of stress analysis. Insights into the textbook Shigley’s Mechanical Engineering Design - 9th ed.
Typology: Lecture notes
1 / 76
This page cannot be seen from the preview
Don't miss anything!
72 Mechanical Engineering Design
One of the main objectives of this book is to describe how specific machine components function and how to design or specify them so that they function safely without failing structurally. Although earlier discussion has described structural strength in terms of load or stress versus strength, failure of function for structural reasons may arise from other factors such as excessive deformations or deflections. Here it is assumed that the reader has completed basic courses in statics of rigid bodies and mechanics of materials and is quite familiar with the analysis of loads, and the stresses and deformations associated with the basic load states of simple prismatic elements. In this chapter and Chap. 4 we will review and extend these topics briefly. Complete derivations will not be presented here, and the reader is urged to return to basic textbooks and notes on these subjects. This chapter begins with a review of equilibrium and free-body diagrams associated with load-carrying components. One must understand the nature of forces before attempting to perform an extensive stress or deflection analysis of a mechanical com- ponent. An extremely useful tool in handling discontinuous loading of structures employs Macaulay or singularity functions. Singularity functions are described in Sec. 3–3 as applied to the shear forces and bending moments in beams. In Chap. 4, the use of singularity functions will be expanded to show their real power in handling deflections of complex geometry and statically indeterminate problems. Machine components transmit forces and motion from one point to another. The transmission of force can be envisioned as a flow or force distribution that can be fur- ther visualized by isolating internal surfaces within the component. Force distributed over a surface leads to the concept of stress, stress components, and stress transforma- tions (Mohr’s circle) for all possible surfaces at a point. The remainder of the chapter is devoted to the stresses associated with the basic loading of prismatic elements, such as uniform loading, bending, and torsion, and topics with major design ramifications such as stress concentrations, thin- and thick-walled pressurized cylinders, rotating rings, press and shrink fits, thermal stresses, curved beams, and contact stresses.
Equilibrium The word system will be used to denote any isolated part or portion of a machine or structure—including all of it if desired—that we wish to study. A system, under this definition, may consist of a particle, several particles, a part of a rigid body, an entire rigid body, or even several rigid bodies. If we assume that the system to be studied is motionless or, at most, has constant velocity, then the system has zero acceleration. Under this condition the system is said to be in equilibrium. The phrase static equilibrium is also used to imply that the system is at rest. For equilibrium, the forces and moments acting on the system balance such that ∑ F = 0 (3–1) ∑ M = 0 (3–2)
which states that the sum of all force and the sum of all moment vectors acting upon a system in equilibrium is zero_._
74 Mechanical Engineering Design
Summing moments about the x axis of shaft AB in Fig. 3–1 d gives ∑ M (^) x = F ( 0. 75 ) − 240 = 0
F = 320 lbf
The normal force is N = 320 tan 20° = 116.5 lbf. Using the equilibrium equations for Figs. 3–1 c and d , the reader should verify that: R (^) Ay = 192 lbf, R (^) Az = 69 .9 lbf, R (^) By = 128 lbf, R (^) Bz = 46 .6 lbf, R (^) C y = 192 lbf, R (^) Cz = 69 .9 lbf, R (^) Dy = 128 lbf, R (^) Dz = 46 .6 lbf, and To = 480 lbf · in. The direction of the output torque To is opposite ω o because it is the resistive load on the system opposing the motion ω o. Note in Fig. 3–1 b the net force from the bearing reactions is zero whereas the net moment about the x axis is (1.5 + 0.75) (192) + (1.5 + 0.75) (128) = 720 lbf · in. This value is the same as Ti + To = 240 + 480 = 720 lbf · in, as shown in Fig. 3–1 a. The reaction forces R (^) E , R (^) F , R (^) H , and R (^) I , from the mounting bolts cannot be determined from the equilibrium equations as there are too many unknowns. Only three equations are available,
Fy =
Fz =
M (^) x = 0. In case you were wondering about assump- tion 5, here is where we will use it (see Sec. 8–12). The gear box tends to rotate about the x axis because of a pure torsional moment of 720 lbf · in. The bolt forces must provide
( a ) Gear reducer
5 in
4 in
C
A
I
E B
D
F
H
G 2
G 1
o
To i , Ti 240 lbf in
( c ) Input shaft
B (^) G 1 T^ i^ ^ 240 lbf^ ^ in r 1
RBz RBy
1.5 in 1 in
N
A F
RAz RAy
( d ) Output shaft
D
G 2
r 2
T 0
RDz RDy
N F
C
RCy RCz
( b ) Gear box
z y
5 in x
4 in
C
A
I
E
D
F
H
B
R (^) Dy
RBy R (^) Bz RDz
R (^) Cy
R (^) Ay R (^) Az
RF
RH
RCz
RI
RE
Figure 3– ( a ) Gear reducer; ( b–d ) free-body diagrams. Diagrams are not drawn to scale.
Load and Stress Analysis 75
an equal but opposite torsional moment. The center of rotation relative to the bolts lies at the centroid of the bolt cross-sectional areas. Thus if the bolt areas are equal: the center of rotation is at the center of the four bolts, a distance of
( 4 / 2 )^2 + ( 5 / 2 )^2 = 3 .202 in from each bolt; the bolt forces are equal ( R (^) E = R (^) F = R (^) H = R (^) I = R ), and each bolt force is perpendicular to the line from the bolt to the center of rotation. This gives a net torque from the four bolts of 4 R ( 3. 202 ) = 720. Thus, R (^) E = R (^) F = R (^) H = R (^) I = 56 .22 lbf.
Figure 3–2 a shows a beam supported by reactions R 1 and R 2 and loaded by the con- centrated forces F 1 , F 2 , and F 3. If the beam is cut at some section located at x = x 1 and the left-hand portion is removed as a free body, an internal shear force V and bending moment M must act on the cut surface to ensure equilibrium (see Fig. 3–2 b ). The shear force is obtained by summing the forces on the isolated section. The bending moment is the sum of the moments of the forces to the left of the section taken about an axis through the isolated section. The sign conventions used for bending moment and shear force in this book are shown in Fig. 3–3. Shear force and bending moment are related by the equation
d M dx
(3–3)
Sometimes the bending is caused by a distributed load q ( x ), as shown in Fig. 3–4; q ( x ) is called the load intensity with units of force per unit length and is positive in the
Figure 3–
Free-body diagram of simply- supported beam with V and M shown in positive directions.
Figure 3–
Sign conventions for bending and shear.
Figure 3–
Distributed load on beam.
Positive bending
Positive shear Negative shear
Negative bending
x
y q^ ( x )
x 1 x 1
y y
F 1 F 2 F 3 F 1
x x
R 1 R 2 R 1
V M
( a ) ( b )
Load and Stress Analysis 77
The four singularity functions defined in Table 3–1, using the angle brackets 〈 〉, consti- tute a useful and easy means of integrating across discontinuities. By their use, general expressions for shear force and bending moment in beams can be written when the beam is loaded by concentrated moments or forces. As shown in the table, the concentrated moment and force functions are zero for all values of x not equal to a. The functions are undefined for values of x = a. Note that the unit step and ramp functions are zero only for values of x that are less than a. The integration properties shown in the table con- stitute a part of the mathematical definition too. The first two integrations of q ( x ) for V ( x ) and M ( x ) do not require constants of integration provided all loads on the beam are accounted for in q ( x ). The examples that follow show how these functions are used.
EXAMPLE 3–2 Derive the loading, shear-force, and bending-moment relations for the beam of Fig. 3–5 a.
Solution Using Table 3–1 and q ( x ) for the loading function, we find
Answer q = R 1 〈 x 〉−^1 − 200 〈 x − 4 〉−^1 − 100 〈 x − 10 〉−^1 + R 2 〈 x − 20 〉−^1 (1) Integrating successively gives
Answer V =
q dx = R 1 〈 x 〉^0 − 200 〈 x − 4 〉^0 − 100 〈 x − 10 〉^0 + R 2 〈 x − 20 〉^0 (2)
Answer M =
V dx = R 1 〈 x 〉^1 − 200 〈 x − 4 〉^1 − 100 〈 x − 10 〉^1 + R 2 〈 x − 20 〉^1 (3)
Note that V M 0 at x 0 . The reactions R 1 and R 2 can be found by taking a summation of moments and forces as usual, or they can be found by noting that the shear force and bending moment must be zero everywhere except in the region 0 ≤ x ≤ 20 in. This means that Eq. (2)
Figure 3–
( a ) Loading diagram for a simply-supported beam. ( b ) Shear-force diagram. ( c ) Bending-moment diagram.
20 in
4 in 10 in
200 lbf 100 lbf
y
R 1 R 2
O
O
( c ) O
V (lbf)
( b )
( a )
900
210 10
840
x
x
x
M (lbf (^) in)
78 Mechanical Engineering Design
should give V = 0 at x slightly larger than 20 in. Thus R 1 − 200 − 100 + R 2 = 0 (4) Since the bending moment should also be zero in the same region, we have, from Eq. (3), R 1 ( 20 ) − 200 ( 20 − 4 ) − 100 ( 20 − 10 ) = 0 (5) Equations (4) and (5) yield the reactions R 1 210 lbf and R 2 90 lbf. The reader should verify that substitution of the values of R 1 and R 2 into Eqs. (2) and (3) yield Figs. 3–5 b and c.
( a )
( b )
D A B C
y
q
x
10 in 7 in 3 in
R 1 M 1
20 lbf/in (^) 240 lbf in
x
V (lbf)
O
Step (^) Ramp
( c )
x
M (lbf in)
O
80
Parabolic Step
80
240
Ramp Slope = 80 lbf in/in
Figure 3– ( a ) Loading diagram for a beam cantilevered at A. ( b ) Shear-force diagram. ( c ) Bending-moment diagram.
EXAMPLE 3–3 Figure 3–6 a shows the loading diagram for a beam cantilevered at A with a uniform load of 20 lbf/in acting on the portion 3 in ≤ x ≤ 7 in, and a concentrated counter- clockwise moment of 240 lbf · in at x = 10 in. Derive the shear-force and bending- moment relations, and the support reactions M 1 and R 1.
Solution Following the procedure of Example 3–2, we find the load intensity function to be q = − M 1 〈 x 〉−^2 + R 1 〈 x 〉−^1 − 20 〈 x − 3 〉^0 + 20 〈 x − 7 〉^0 − 240 〈 x − 10 〉−^2 (1) Note that the 20〈 x − 7 〉^0 term was necessary to “turn off” the uniform load at C. Integrating successively gives
Answers V = − M 1 〈 x 〉−^1 + R 1 〈 x 〉^0 − 20 〈 x − 3 〉^1 + 20 〈 x − 7 〉^1 − 240 〈 x − 10 〉−^1 (2) M = − M 1 〈 x 〉^0 + R 1 〈 x 〉^1 − 10 〈 x − 3 〉^2 + 10 〈 x − 7 〉^2 − 240 〈 x − 10 〉^0 (3) The reactions are found by making x slightly larger than 10 in, where both V and M are zero in this region. Noting that 〈 10 〉−^1 = 0, Eq. (2) will then give − M 1 ( 0 ) + R 1 ( 1 ) − 20 ( 10 − 3 ) + 20 ( 10 − 7 ) − 240 ( 0 ) = 0
80 Mechanical Engineering Design
Note that double subscripts are necessary for the shear. The first subscript indicates the direction of the surface normal whereas the second subscript is the direction of the shear stress. The state of stress at a point described by three mutually perpendicular surfaces is shown in Fig. 3–8 a. It can be shown through coordinate transformation that this is suf- ficient to determine the state of stress on any surface intersecting the point. As the dimensions of the cube in Fig. 3–8 a approach zero, the stresses on the hidden faces become equal and opposite to those on the opposing visible faces. Thus, in general, a complete state of stress is defined by nine stress components, σ x , σ y , σ z , τ x y , τ x z , τ yx , τ yz , τ zx , and τ zy. For equilibrium, in most cases, “cross-shears” are equal, hence τ yx = τ x y τ zy = τ yz τ x z = τ zx (3–7) This reduces the number of stress components for most three-dimensional states of stress from nine to six quantities, σ x , σ y , σ z , τ x y , τ yz , and τ zx. A very common state of stress occurs when the stresses on one surface are zero. When this occurs the state of stress is called plane stress. Figure 3–8 b shows a state of plane stress, arbitrarily assuming that the normal for the stress-free surface is the z direction such that σ z = τ zx = τ zy = 0. It is important to note that the element in Fig. 3–8 b is still a three-dimensional cube. Also, here it is assumed that the cross-shears are equal such that τ yx = τ x y , and τ yz = τ zy = τ x z = τ zx = 0.
Suppose the dx dy dz element of Fig. 3–8 b is cut by an oblique plane with a normal n at an arbitrary angle φ counterclockwise from the x axis as shown in Fig. 3–9. Here, we are concerned with the stresses σ and τ that act upon this oblique plane. By summing the forces caused by all the stress components to zero, the stresses σ and τ are found to be
σ =
σ x + σ y 2
σ x − σ y 2
cos 2φ + τ x y sin 2φ (3–8)
τ = −
σ x − σ y 2
sin 2φ + τ x y cos 2φ (3–9)
Equations (3–8) and (3–9) are called the plane-stress transformation equations.
y y
x
y
yx
xy
x y
xy
x y
xy
x z
x x
y
x
y
z
x
z
y z
z y
z x
( a ) ( b )
Figure 3– ( a ) General three-dimensional stress. ( b ) Plane stress with “cross-shears” equal.
Load and Stress Analysis 81
Differentiating Eq. (3–8) with respect to φ and setting the result equal to zero maximizes σ and gives
tan 2φ p =
2 τ x y σ x − σ y
(3–10)
Equation (3–10) defines two particular values for the angle 2φ p , one of which defines the maximum normal stress σ 1 and the other, the minimum normal stress σ 2. These two stresses are called the principal stresses, and their corresponding directions, the princi- pal directions. The angle between the two principal directions is 90°. It is important to note that Eq. (3–10) can be written in the form σ x − σ y 2
sin 2φ p − τ x y cos 2φ p = 0 ( a )
Comparing this with Eq. (3–9), we see that τ = 0, meaning that the perpendicular sur- faces containing principal stresses have zero shear stresses. In a similar manner, we differentiate Eq. (3–9), set the result equal to zero, and obtain
tan 2φ s = −
σ x − σ y 2 τ x y
(3–11)
Equation (3–11) defines the two values of 2φ s at which the shear stress τ reaches an extreme value. The angle between the two surfaces containing the maximum shear stresses is 90°. Equation (3–11) can also be written as σ x − σ y 2
cos 2φ p + τ x y sin 2φ p = 0 ( b )
Substituting this into Eq. (3–8) yields
σ =
σ x + σ y 2
(3–12)
Equation (3–12) tells us that the two surfaces containing the maximum shear stresses also contain equal normal stresses of (σ x + σ y )/ 2. Comparing Eqs. (3–10) and (3–11), we see that tan 2φ s is the negative reciprocal of tan 2φ p. This means that 2φ s and 2φ p are angles 90° apart, and thus the angles between the surfaces containing the maximum shear stresses and the surfaces contain- ing the principal stresses are ± 45 ◦. Formulas for the two principal stresses can be obtained by substituting the angle 2φ p from Eq. (3–10) in Eq. (3–8). The result is
σ 1 , σ 2 =
σ x + σ y 2
σ x − σ y 2
x
n
y
x xy dsdx
dy
^
xy y
dx
dy ds
Figure 3–
Using the stress state of Fig. 3–8 b , we plot Mohr’s circle, Fig. 3–10, by first look- ing at the right surface of the element containing σ x to establish the sign of σ x and the cw or ccw direction of the shear stress. The right face is called the x face where φ = 0 ◦. If σ x is positive and the shear stress τ x y is ccw as shown in Fig. 3–8 b , we can establish point A with coordinates (σ x , τ (^) x y ccw ) in Fig. 3–10. Next, we look at the top y face, where φ = 90 ◦, which contains σ y , and repeat the process to obtain point B with coordinates (σ y , τ (^) x y cw ) as shown in Fig. 3–10. The two states of stress for the element are φ = 90 ◦^ from each other on the element so they will be 2φ = 180 ◦^ from each other on Mohr’s circle. Points A and B are the same vertical distance from the σ axis. Thus, AB must be on the diameter of the circle, and the center of the circle C is where AB intersects the σ axis. With points A and B on the circle, and center C , the complete circle can then be drawn. Note that the extended ends of line AB are labeled x and y as references to the normals to the surfaces for which points A and B represent the stresses. The entire Mohr’s circle represents the state of stress at a single point in a struc- ture. Each point on the circle represents the stress state for a specific surface intersect- ing the point in the structure. Each pair of points on the circle 180° apart represent the state of stress on an element whose surfaces are 90° apart. Once the circle is drawn, the states of stress can be visualized for various surfaces intersecting the point being ana- lyzed. For example, the principal stresses σ 1 and σ 2 are points D and E , respectively, and their values obviously agree with Eq. (3–13). We also see that the shear stresses are zero on the surfaces containing σ 1 and σ 2. The two extreme-value shear stresses, one clockwise and one counterclockwise, occur at F and G with magnitudes equal to the radius of the circle. The surfaces at F and G each also contain normal stresses of (σ x + σ y )/2 as noted earlier in Eq. (3–12). Finally, the state of stress on an arbitrary surface located at an angle φ counterclockwise from the x face is point H.
Load and Stress Analysis 83
x y ( x – y )
O
x + y 2
x – y F^2
( y , xy^ cw)
( x , ccw)
y (^) B
C
G
D
H
E
xy
2^ y x^ 1^
2
A^2 p
xy
x
cw
ccw
x – y (^2) + (^) xy 2
2 xy
Figure 3–
Mohr’s circle diagram.
84 Mechanical Engineering Design
At one time, Mohr’s circle was used graphically where it was drawn to scale very accurately and values were measured by using a scale and protractor. Here, we are strictly using Mohr’s circle as a visualization aid and will use a semigraphical approach, calculat- ing values from the properties of the circle. This is illustrated by the following example.
EXAMPLE 3–4 A stress element has σ x = 80 MPa and τ x y = 50 MPa cw, as shown in Fig. 3–11 a. ( a ) Using Mohr’s circle, find the principal stresses and directions, and show these on a stress element correctly aligned with respect to the x y coordinates. Draw another stress element to show τ 1 and τ 2 , find the corresponding normal stresses, and label the drawing completely. ( b ) Repeat part a using the transformation equations only.
Solution ( a ) In the semigraphical approach used here, we first make an approximate freehand sketch of Mohr’s circle and then use the geometry of the figure to obtain the desired information. Draw the σ and τ axes first (Fig. 3–11 b ) and from the x face locate σ x = 80 MPa along the σ axis. On the x face of the element, we see that the shear stress is 50 MPa in the cw direction. Thus, for the x face, this establishes point A (80, 50cw) MPa. Corresponding to the y face, the stress is σ = 0 and τ = 50 MPa in the ccw direction. This locates point B (0, 50ccw) MPa. The line AB forms the diameter of the required cir- cle, which can now be drawn. The intersection of the circle with the σ axis defines σ 1 and σ 2 as shown. Now, noting the triangle AC D , indicate on the sketch the length of the legs AD and C D as 50 and 40 MPa, respectively. The length of the hypotenuse AC is
Answer τ 1 =
( 50 )^2 + ( 40 )^2 = 64 .0 MPa
and this should be labeled on the sketch too. Since intersection C is 40 MPa from the origin, the principal stresses are now found to be
Answer σ 1 = 40 + 64 = 104 MPa and σ 2 = 40 − 64 = −24 MPa
The angle 2φ from the x axis cw to σ 1 is
Answer 2 φ p = tan−1 50 40 = 51. 3 ◦
To draw the principal stress element (Fig. 3–11 c ), sketch the x and y axes parallel to the original axes. The angle φ p on the stress element must be measured in the same direction as is the angle 2φ p on the Mohr circle. Thus, from x measure 25.7° (half of 51.3°) clockwise to locate the σ 1 axis. The σ 2 axis is 90° from the σ 1 axis and the stress element can now be completed and labeled as shown. Note that there are no shear stresses on this element. The two maximum shear stresses occur at points E and F in Fig. 3–11 b. The two normal stresses corresponding to these shear stresses are each 40 MPa, as indicated. Point E is 38.7° ccw from point A on Mohr’s circle. Therefore, in Fig. 3–11 d , draw a stress element oriented 19.3° (half of 38.7°) ccw from x. The element should then be labeled with magnitudes and directions as shown. In constructing these stress elements it is important to indicate the x and y direc- tions of the original reference system. This completes the link between the original machine element and the orientation of its principal stresses.
86 Mechanical Engineering Design
Substituting φ p = 64. 3 ◦^ into Eq. (3–9) again yields τ = 0 , indicating that −24.03 MPa is also a principal stress. Once the principal stresses are calculated they can be ordered such that σ 1 ≥ σ 2. Thus, σ 1 = 104 .03 MPa and σ 2 = − 24 .03 MPa.
Answer
Since for σ 1 = 104 .03 MPa, φ p = − 25. 7 ◦, and since φ is defined positive ccw in the transformation equations, we rotate clockwise 25.7° for the surface containing σ 1. We see in Fig. 3–11 c that this totally agrees with the semigraphical method. To determine τ 1 and τ 2 , we first use Eq. (3–11) to calculate φ s :
φ s =
tan−^1
σ x − σ y 2 τ x y
tan−^1
For φ s = 19. 3 ◦, Eqs. (3–8) and (3–9) yield
Answer σ =
cos[2( 19. 3 )] + (− 50 ) sin[2( 19. 3 )] = 40 .0 MPa
τ = −
sin[2( 19. 3 )] + (− 50 ) cos[2( 19. 3 )] = − 64 .0 MPa
Remember that Eqs. (3–8) and (3–9) are coordinate transformation equations. Imagine that we are rotating the x , y axes 19.3° counterclockwise and y will now point up and to the left. So a negative shear stress on the rotated x face will point down and to the right as shown in Fig. 3–11 d. Thus again, results agree with the semigraphical method. For φ s = 109. 3 ◦, Eqs. (3–8) and (3–9) give σ = 40 .0 MPa and τ = + 64 .0 MPa. Using the same logic for the coordinate transformation we find that results again agree with Fig. 3–11 d.
As in the case of plane stress, a particular orientation of a stress element occurs in space for which all shear-stress components are zero. When an element has this particular ori- entation, the normals to the faces are mutually orthogonal and correspond to the prin- cipal directions, and the normal stresses associated with these faces are the principal stresses. Since there are three faces, there are three principal directions and three prin- cipal stresses σ 1 , σ 2 , and σ 3. For plane stress, the stress-free surface contains the third principal stress which is zero. In our studies of plane stress we were able to specify any stress state σ x , σ y , and τ x y and find the principal stresses and principal directions. But six components of stress are required to specify a general state of stress in three dimensions, and the problem of determining the principal stresses and directions is more difficult. In design, three-dimensional transformations are rarely performed since most maxi- mum stress states occur under plane stress conditions. One notable exception is con- tact stress, which is not a case of plane stress, where the three principal stresses are given in Sec. 3–19. In fact, all states of stress are truly three-dimensional, where they might be described one- or two-dimensionally with respect to specific coordi- nate axes. Here it is most important to understand the relationship among the three principal stresses. The process in finding the three principal stresses from the six
Load and Stress Analysis 87
stress components σ x , σ y , σ z , τ x y , τ yz , and τ zx , involves finding the roots of the cubic equation 1 σ 3 − (σ x + σ y + σ z )σ 2 +
σ x σ y + σ x σ z + σ y σ z − τ (^) x y^2 − τ (^) yz^2 − τ (^) zx^2
σ −
σ x σ y σ z + 2 τ x y τ yz τ zx − σ x τ (^) yz^2 − σ y τ (^) zx^2 − σ z τ (^) x y^2
In plotting Mohr’s circles for three-dimensional stress, the principal normal stresses are ordered so that σ 1 ≥ σ 2 ≥ σ 3. Then the result appears as in Fig. 3–12 a. The stress coordinates σ , τ for any arbitrarily located plane will always lie on the bound- aries or within the shaded area. Figure 3–12 a also shows the three principal shear stresses τ 1 / 2 , τ 2 / 3 , and τ 1 / 3.^2 Each of these occurs on the two planes, one of which is shown in Fig. 3–12 b. The fig- ure shows that the principal shear stresses are given by the equations
τ 1 / 2 =
σ 1 − σ 2 2
τ 2 / 3 =
σ 2 − σ 3 2
τ 1 / 3 =
σ 1 − σ 3 2
(3–16)
Of course, τmax = τ 1 / 3 when the normal principal stresses are ordered (σ 1 > σ 2 > σ 3 ), so always order your principal stresses. Do this in any computer code you generate and you’ll always generate τmax.
Normal strain is defined and discussed in Sec. 2–1 for the tensile specimen and is given by Eq. (2–2) as = δ/ l , where δ is the total elongation of the bar within the length l. Hooke’s law for the tensile specimen is given by Eq. (2–3) as σ = E (3–17) where the constant E is called Young’s modulus or the modulus of elasticity.
1/
1/
2/
3 2 1^
( a ) ( b )
1/
1
2
Figure 3–
Mohr’s circles for three- dimensional stress.
(^1) For development of this equation and further elaboration of three-dimensional stress transformations see: Richard G. Budynas, Advanced Strength and Applied Stress Analysis, 2nd ed., McGraw-Hill, New York, 1999, pp. 46–78. (^2) Note the difference between this notation and that for a shear stress, say, τ x y. The use of the shilling mark is not accepted practice, but it is used here to emphasize the distinction.
Load and Stress Analysis 89
For simple compression, Eq. (3–22) is applicable with F normally being consid- ered a negative quantity. Also, a slender bar in compression may fail by buckling, and this possibility must be eliminated from consideration before Eq. (3–22) is used. 3 Another type of loading that assumes a uniformly distributed stress is known as direct shear. This occurs when there is a shearing action with no bending. An example is the action on a piece of sheet metal caused by the two blades of tin snips. Bolts and pins that are loaded in shear often have direct shear. Think of a cantilever beam with a force pushing down on it. Now move the force all the way up to the wall so there is no bending moment, just a force trying to shear the beam off the wall. This is direct shear. Direct shear is usually assumed to be uniform across the cross section, and is given by
τ =
(3–23)
where V is the shear force and A is the area of the cross section that is being sheared. The assumption of uniform stress is not accurate, particularly in the vicinity where the force is applied, but the assumption generally gives acceptable results.
The equations for the normal bending stresses in straight beams are based on the fol- lowing assumptions.
- The beam is subjected to pure bending. This means that the shear force is zero, and that no torsion or axial loads are present (for most engineering applications it is as- sumed that these loads affect the bending stresses minimally). - The material is isotropic and homogeneous. - The material obeys Hooke’s law. - The beam is initially straight with a cross section that is constant throughout the beam length. - The beam has an axis of symmetry in the plane of bending. - The proportions of the beam are such that it would fail by bending rather than by crushing, wrinkling, or sidewise buckling. - Plane cross sections of the beam remain plane during bending. In Fig. 3–13 we visualize a portion of a straight beam acted upon by a positive bending moment M shown by the curved arrow showing the physical action of the moment together with a straight arrow indicating the moment vector. The x axis is coincident with the neutral axis of the section, and the xz plane, which contains the
(^3) See Sec. 4–11.
Figure 3–
Straight beam in positive bending.
M
M
x
y
z
90 Mechanical Engineering Design
neutral axes of all cross sections, is called the neutral plane. Elements of the beam coincident with this plane have zero stress. The location of the neutral axis with respect to the cross section is coincident with the centroidal axis of the cross section. The bending stress varies linearly with the distance from the neutral axis, y , and is given by
σ x = −
M y I
(3–24)
where I is the second-area moment about the z axis. That is,
I =
y^2 d A (3–25)
The stress distribution given by Eq. (3–24) is shown in Fig. 3–14. The maximum magni- tude of the bending stress will occur where y has the greatest magnitude. Designating σmax as the maximum magnitude of the bending stress, and c as the maximum magnitude of y
σmax =
Mc I
(3–26 a )
Equation (3–24) can still be used to ascertain whether σmax is tensile or compressive. Equation (3–26 a ) is often written as
σmax =
(3–26 b )
where Z = I/c is called the section modulus.
EXAMPLE 3–5 A beam having a T section with the dimensions shown in Fig. 3–15 is subjected to a bend- ing moment of 1600 N · m, about the negative z axis, that causes tension at the top surface. Locate the neutral axis and find the maximum tensile and compressive bending stresses.
Solution Dividing the T section into two rectangles, numbered 1 and 2, the total area is A 12(75) 12(88) 1956 mm 2. Summing the area moments of these rectangles about the top edge, where the moment arms of areas 1 and 2 are 6 mm and (12 88 /2) 56 mm respectively, we have 1956 c 1 = 12 ( 75 )( 6 ) + 12 ( 88 )( 56 ) and hence c 1 = 32 .99 mm. Therefore c 2 = 100 − 32. 99 = 67 .01 mm. Next we calculate the second moment of area of each rectangle about its own cen- troidal axis. Using Table A–18, we find for the top rectangle
I 1 =
bh^3 =
( 75 ) 123 = 1. 080 × 104 mm^4
Compression
Neutral axis, Centroidal axis
Tension
x
c
y
y
Figure 3– Bending stresses according to Eq. (3–24).