
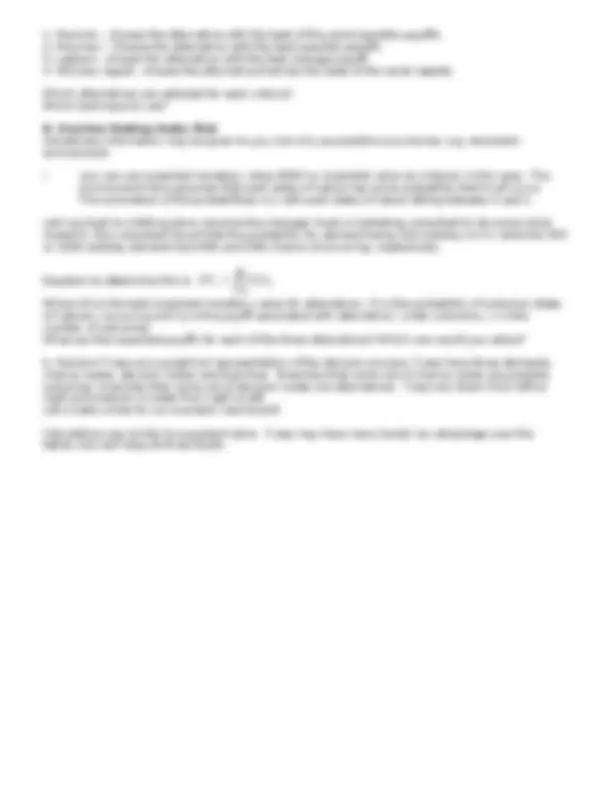
Study with the several resources on Docsity
Earn points by helping other students or get them with a premium plan
Prepare for your exams
Study with the several resources on Docsity
Earn points to download
Earn points by helping other students or get them with a premium plan
Community
Ask the community for help and clear up your study doubts
Discover the best universities in your country according to Docsity users
Free resources
Download our free guides on studying techniques, anxiety management strategies, and thesis advice from Docsity tutors
Material Type: Notes; Class: OPERATIONS MANAGEMENT; Subject: Management; University: Clark University; Term: Fall 2004;
Typology: Study notes
1 / 3
This page cannot be seen from the preview
Don't miss anything!
MGMT250 Notes September 7, 2004
1. Initial Stuff A. Schedule 1. Collect H.W. and briefly go over it (any volunteers to put their work on board?). 2. We will finish up Operations Strategy. 3. We will begin Decision Theory and how it helps to make decisions. 3. Case Analysis due week from Thursday. 4. Problems for Chapter 5S may be due next class (depending on how far we get today). 5. For next week read quality assignments. Will try to start Quality next time, if time allows.
Job Shop Batch Repetitive assembly Continuous Flow
3. Decision Theory A. Management means making decisions. There can be 7 steps to a typical decision process: 1. Identify the problem 2. Specify Objectives and the criteria for choosing a solution. 3. Develop alternatives. 4. Analyze and compare. 5. Select the best alternative. 6. Implement the chosen alternative. 7. Monitor the results and feedback. In this class steps 1-5 is focus. In reality all steps are important. B. The manager faces three types of decision environments. 1. Certainty. Deterministic and known values for all parameters. 2. Risk - have some information...statistical usually. 3. Uncertainty - no information on probabilities of occurrences of future events. C. Decision Theory can be used for a number of operations decisions. Works well for strategic..but tactical and operational decisions could be answered: Location, capacity planning, equipment…etc. D. You need to have three major pieces of information to apply decision theory process. 1. Future Conditions (states of nature). 2. Alternatives to choose from. 3. Payoffs for each alternative for a given conditions. This information may be supplemented with finding probabilities of occurrences. Then use decision criteria to evaluate alternatives. These first steps help form a “payoff table” (later we shall see these applied to a “decision tree.”) To complete the payoff table we also: 4. Determine likelihood of states of nature 5. Evaluate alternatives based on some “criteria”, (e.g. maximize profit) and make selection. Let us assume that we have a company a custom clothing store, is looking to its future. Business for this company has been good and it’s looking to build another store in another town. There are a number of alternatives available to them, they could build a facility with 2000 sq. ft, a facility with 10,000 sq. ft. or a 20,000 sq. ft. facility. They decided to have some estimation done and came up with the following preliminary numbers. If they built the 2000 sq. ft. facility and demand was low ( suits a day), then they could expect a net present value on the facility (over the life of the facility) of $5 million. Actually, this is true if demand is at 400 or 1000 suits per day (the other demand estimates). If they built the 10,000 sq. ft. facility they would make $3 million with the 100 suit/day demand, $10 million with the 400 suit/day demand and $16 million, for the 1000 suit/day demand. Yet, if they built the 20,000 sq. ft. facility, they could expect to lose $4 million over the life of the store if demand was 100 suit/day. If demand were 400 or 1000 suits/day his returns would be $2 million and $16 million respectively. How would you set up this problem? How do we read the payoff table? Let us use this table for evaluation in the three different environments. 1. Certainty We know for sure that next period’s demand is going to be high, which alternative do we select? Rather straight forward. If we have estimates available. 2. Uncertainty We have 4 possible analysis criteria (methods) which we can use. Let us put table on board.