
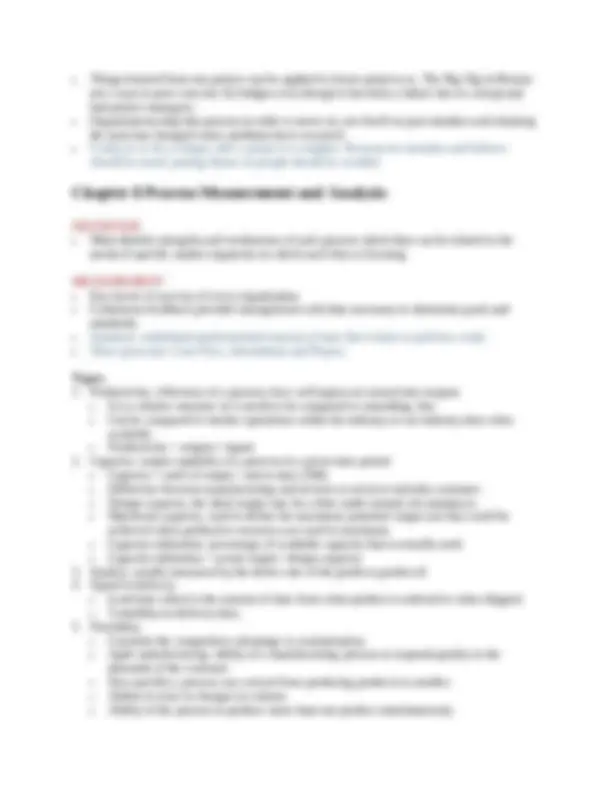
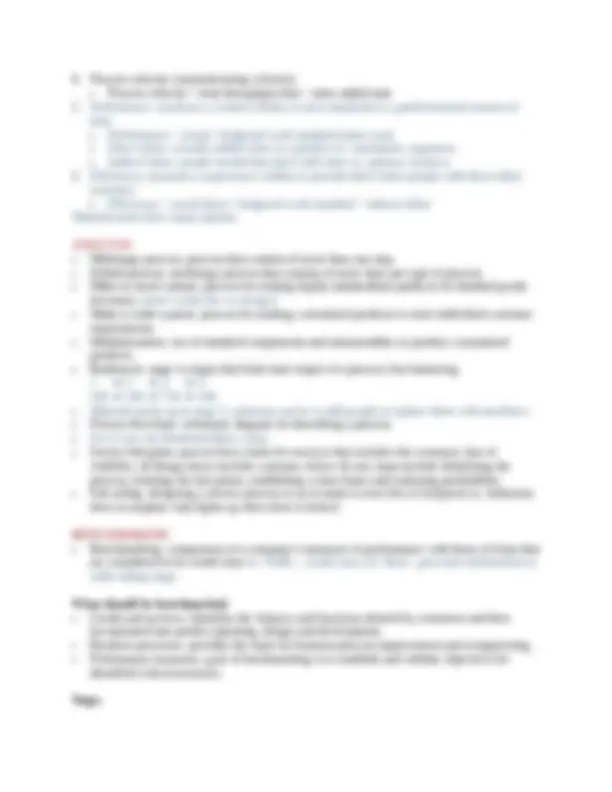
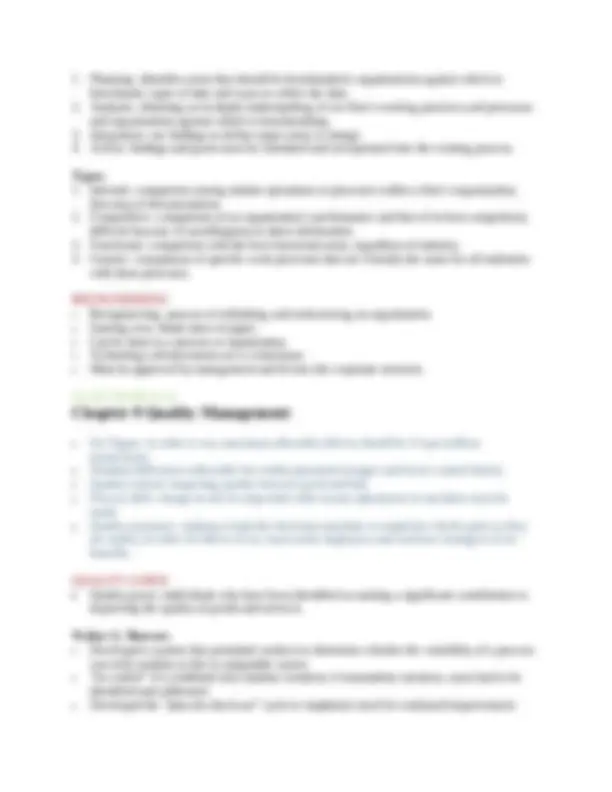
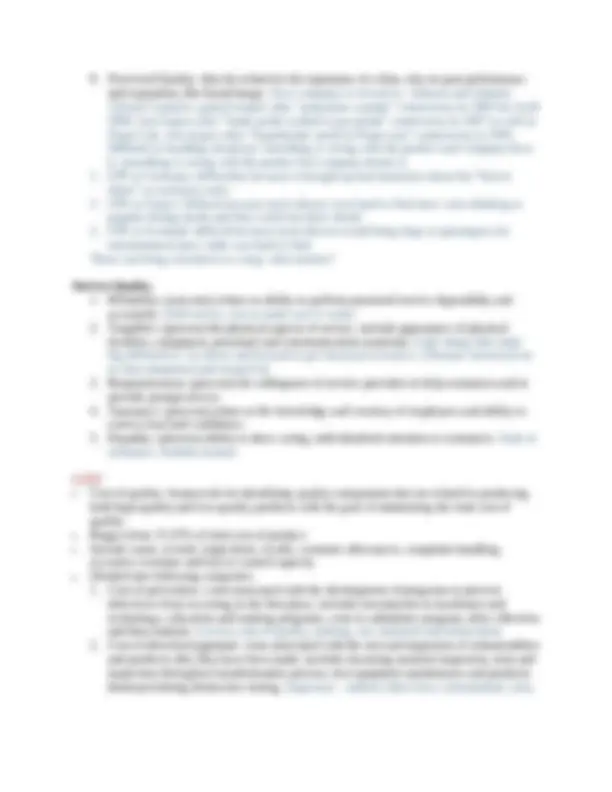
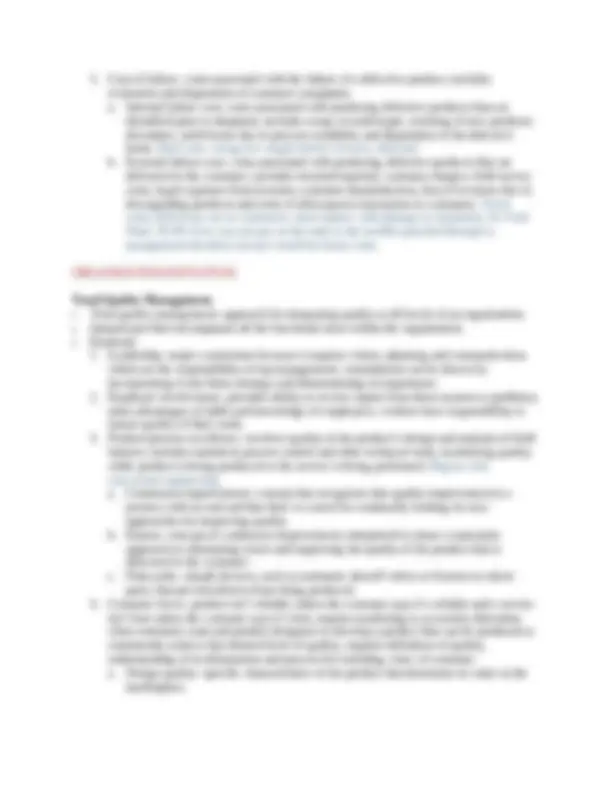
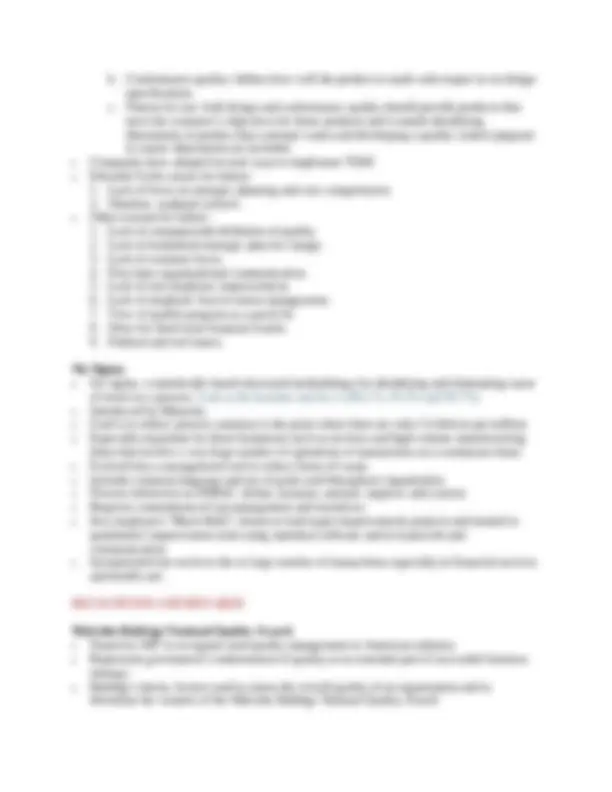
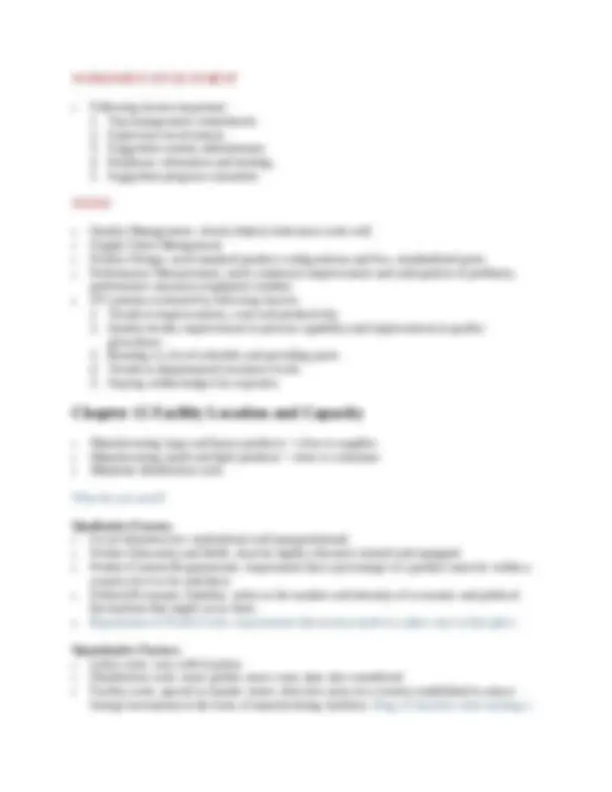
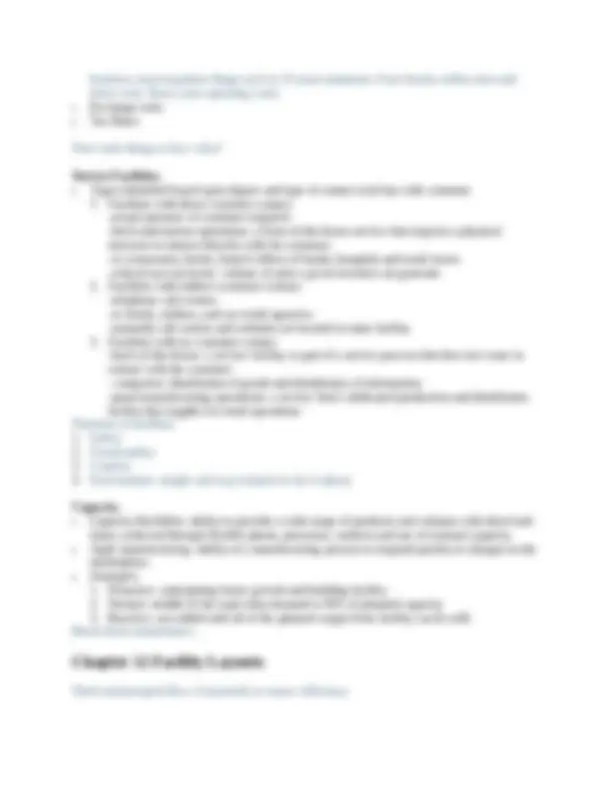
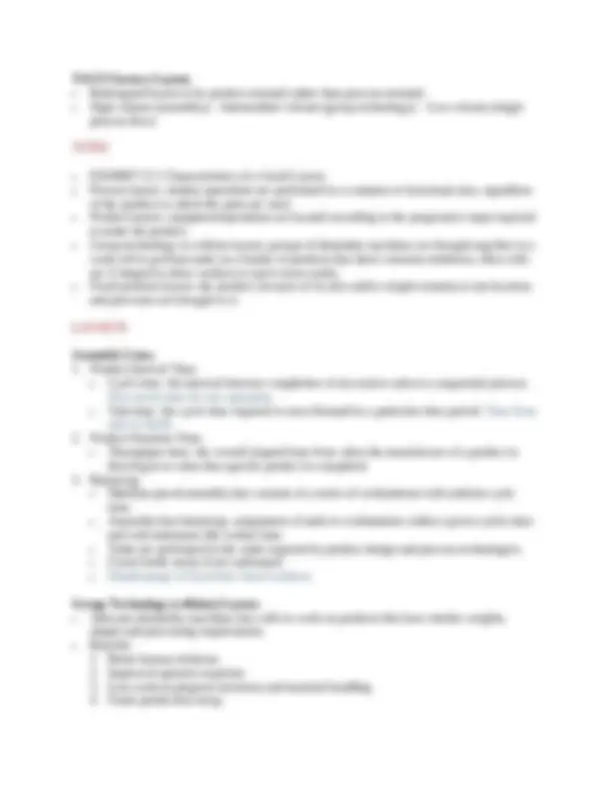
Study with the several resources on Docsity
Earn points by helping other students or get them with a premium plan
Prepare for your exams
Study with the several resources on Docsity
Earn points to download
Earn points by helping other students or get them with a premium plan
Community
Ask the community for help and clear up your study doubts
Discover the best universities in your country according to Docsity users
Free resources
Download our free guides on studying techniques, anxiety management strategies, and thesis advice from Docsity tutors
Material Type: Notes; Professor: Jefferson; Class: Operations Management; Subject: Management; University: Bryant University; Term: Fall 2009;
Typology: Study notes
1 / 16
This page cannot be seen from the preview
Don't miss anything!
Project- series of related jobs or tasks focused on the completion of an overall objective, doing a unique thing Ex. contractor building a house. Project management- involves the planning, directing and controlling resources (people, equipment, material) to meet the technical, cost and time constraints of the project. Differences between managing ongoing processes and managing projects: organizational structure, types of tasks (effective project management requires constant monitoring, updating, and re-planning throughout the life). Project starts out as a statement of work- written as a description of the objectives to be achieved. Program- synonym for a project, although it can consist of several interrelated projects Ex. introduction of a new healthcare system. -tasks or activities are subdivisions of a project, not longer than several months and performed by one group or organization. -subtask may be used if needed to further subdivide the project. -work package is a group of activities combined to be assignable to a single organizational unit. Milestones- specific major events to be completed at certain times in the project. Work Breakdown Structure. Work breakdown structure- method by which a project is divided into tasks and subtasks. A good structure: allows activities to be worked on independently, makes activities manageable in size, gives authority to carry out the program, monitors and measures the program and provides the required resources. Steps to making something successfully with number one being defining what you want. CONSIDERATIONS Role of the Project Manager. Have a unique role within the traditional organization structure. Involve people with a wide variety of skills from different organizational units. Must create a collaborative work environment. Keep a team motivated and resolve team conflicts. Development Stages of Teamwork.
High Team Performance. Most work in modern times is done in teams. Following factors are critical for a successful project team:
Six Sigma- in order to run, maximum allowable defects should be 3.4 per million transactions. Nominal differences allowable but within parameters (upper and lower control limits). Quality control- inspecting quality between good and bad. Process shift- change in size in sequential order means adjustment to machines must be made. Quality assurance- making it right the first time (machine or employee checks parts as they are made); in order for this to occur, must teach employees and convince managers of its benefits. QUALITY GURUS Quality gurus- individuals who have been identified as making a significant contribution to improving the quality of goods and services. Walter A. Shewart. Developed a system that permitted workers to determine whether the variability of a process was truly random or due to assignable causes. “In control” if it exhibited only random variation; if nonrandom variation, cause had to be identified and addressed. Developed the “plan-do-check-act” cycle to emphasize need for continued improvement.
Can reduce total overall cost by improving quality of processes. Costs estimated as 25% of revenues for manufacture and 40% of operating expenses for service. Could be less than 2.5% of sales. Genichi Taguchi. Refinement of quality management philosophy and development of quality tools. Engineering approach: focusing on design of experiments to improve yield and performance. Emphasized minimal variation to reduce costs to firma and society. External failure (Juran) must include cost to firm that ships defective product and firm that accepts it, customer that buys and uses it etc. Engineering-philosophical perspective shows how much is lost when products doesn’t meet specifications. Kaoru Ishikawa. Son of founder and first chairman of Japanese Union of Scientists and Engineers. Developed problem solving tools: cause-and-effect diagram. Father of quality circles. Written about differences between Eastern and Western cultures. “To practice quality control is to develop, design, produce and service a quality product which is most economical, useful and satisfactory to customer. DEFINITION After WWII, quality viewed as defensive function. Emphasis was on quality control: reducing customer complaints. Reliance on identifying poor quality through inspection rather than preventing. Cost incurring, therefore the assumption was that high quality is more costly. Today, companies recognize strategic importance of quality. Can identify new markets and increase market share. Goods Quality. Dimensions of quality- elements of quality as perceived by customers by David Garvin.
b. Conformance quality- defines how well the product is made with respect to its design specifications. c. Fitness for use- both design and conformance quality should provide products that meet the customer’s objectives for those products and it entails identifying dimensions of product that customer wants and developing a quality control program to ensure dimensions are included. Companies have adopted several ways to implement TQM. Edwards Fuchs causes for failure:
Evaluated on three dimensions: the soundness of the approach or system, the deployment or integration of those systems throughout the entire organization and the results generated by those systems. Baldrige criteria used to: help and design a total quality system, evaluate ongoing internal relationships among departments, divisions and functional units within an organization, assess and assist outside suppliers of goods and services to a company and assess customer satisfaction. ISO 9000 International Organization for Standardization published first standards in 1986. ISO 9000 series quality standards- international set of standards for documenting the processes that an organization uses to produce goods and services. Purpose to satisfy customer organization’s assurance requirements and increase level of confidence of customer organizations in suppliers. Revisions made in 2000 to quality management systems. First party, second party and third party certifications. Say what you do (document everything and do a pre-audit), do what you say (follow your process guidelines) Get provisional certification: 6 month, 1 year and 2 year. European business plans: be certified. Keep it up: can’t explain if it is lost. A skill that is in demand.
Deadly wastes:
Following factors important:
Manufacturing large and heavy products = close to supplier. Manufacturing small and light products = close to consumer. Minimize distribution costs. What do you need? Qualitative Factors. Local infrastructure- institutional and transportational. Worker Education and Skills- must be highly educated, trained and equipped. Product Content Requirements- requirement that a percentage of a product must be within a country for it to be sold there. Political/Economic Stability- refers to the number and intensity of economic and political fluctuations that might occur there. Repatriation of Profits Costs- requirements that money made in a place stay in that place. Quantitative Factors. Labor costs- vary with location. Distribution costs- more global, more costs; time also considered. Facility costs- special economic zones- duty-free areas in a country established to attract foreign investment in the form of manufacturing facilities. King of situation when starting a
business; must negotiate things such as 10 years minimum of tax breaks, utility rates and labor costs. Know your operating costs. Exchange rates Tax Rates Don’t take things at face value! Service Facilities. Types identified based upon degree and type of contact each has with customer.
Need uninterrupted flow of materials to ensure efficiency.
Steps of shifting from process to GT cellular layout: