
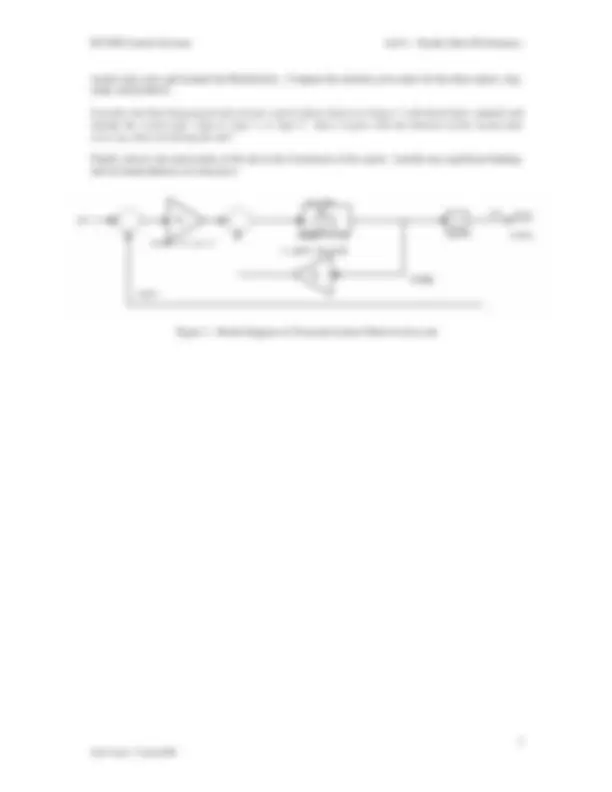
Study with the several resources on Docsity
Earn points by helping other students or get them with a premium plan
Prepare for your exams
Study with the several resources on Docsity
Earn points to download
Earn points by helping other students or get them with a premium plan
Community
Ask the community for help and clear up your study doubts
Discover the best universities in your country according to Docsity users
Free resources
Download our free guides on studying techniques, anxiety management strategies, and thesis advice from Docsity tutors
The procedure for lab 4 of the ec2300 control systems course, focusing on steady-state performance. Students will investigate the steady-state error of a control plant using step, ramp, and parabolic inputs. They will use the ecp software to execute the lab and analyze the results in matlab. The report should include the theory behind steady-state error, observations, and comparisons of error plots, identification of system type, and conclusions.
What you will learn
Typology: Slides
1 / 3
This page cannot be seen from the preview
Don't miss anything!
The steady-state error is the difference between the output (actual state) and the input (commanded state) after the transient response has passed. The primary source of steady-state error is due simply to the type of input (step, ramp, or parabola) that stimulates the control plant. Another cause is attributed to the system type as defined by the form of the transfer function G(s). The effects of these error sources will be observed during this lab procedure.
2.1 Steady-State Error of the Control Plant with Step Input For the first part of this lab, the control plant will be excited with a step input, and the steady-state error determined.
2.1.1 Setup the Control Plant. The torsion system will be set up with two (2 each) weights loaded on the bottom disk only. The weights are secured 180 degrees apart from each other such that the outside edge of each weight is tangent to the 9-cm radius line (last line on the disk).
2.1.2 Start the ECP software program.
2.1.3 Record the ECP Station Number, as each ECP station will have slightly different system characteristics.
2.1.4 Energize the control system by pushing the “ON” button on the ECP controller.
WARNING The system is now energized and will rotate at potentially high speeds when a control voltage is applied to the motor of the torsional system. At any point the motion of the system can be stopped by pressing the OFF (red) button on the ECP controller box.
2.1.5 Setup the ECP Program a. Set the system units to degrees: Setup‡User Units, select degrees b. Select Setup‡Control Algorithm.
e. Utility ‡ Zero Position (to reset encoders to zero)
2.1.6 Select Command ‡Execute, Normal Data Sampling. Click Run to load and execute the program. With the trajectory set up as described above, the disk should rotate 180 degrees very rapidly and hold this position for 3 seconds before relaxing to its rest position.
2.1.7 Plot Data: Select Plotting ‡ Setup Plot. For the left axis choose Commanded Position and Encoder 1 Position. Select Plot Data.
2.1.8 Export the raw data and plot the data in Matlab. Using the Matlab subplot command, make two plots: 1) In the first subplot window, show the commanded position and the actual position of the disk with time on the horizontal axis. 2) In the second subplot window, show the error. This is just the difference between the commanded and the actual position, also with time on the horizontal axis.
2.2 Steady-State Error for a Ramp Input For this part of the lab procedure, you will utilize the ramp input of the ECP program to explore the steady- state error.
2.2.1. Select the following in the ECP program window: Select Command‡Trajectory a. Select Ramp and Unidirectional moves. Click Setup. o Distance (degrees)= o Velocity (degrees/sec) = 720 o Dwell Time (msec) = 0 o Number of reps = 1 b. Utility ‡ Zero Position (to reset encoders to zero) c. Command ‡ Execute. Click Run.
2.2.3 Plot the Data: Select Plotting ‡ Plot Data.
2.2.4 Save and Plot the Data in Matlab.
2.3 Steady-State Error for a Parabolic Input For this part of the lab procedure, you will utilize the parabolic input of the ECP program to explore the steady-state error.
2.3.2. Select the following in the ECP program window: a. Command‡Trajectory. Select Parabolic and Unidirectional moves. Click Setup. o Distance (degrees)= o Velocity (degrees/sec) = 900 o Accel Time (msec) = 2500 o Dwell Time (msec) = 0 o Number of reps = 1 b. Utility ‡ Zero Position (to reset encoders to zero) c. Command ‡ Execute. Click Run.
2.3.3 Plot the Data: Select Plotting ‡ Plot Data.
2.3.4 Save and Plot the Data in Matlab.
Submit a report in the standard format for this class. In the Introduction discuss the relevant theory that was presented and explored during the lab. In the Results and Analysis discuss your observations of the