
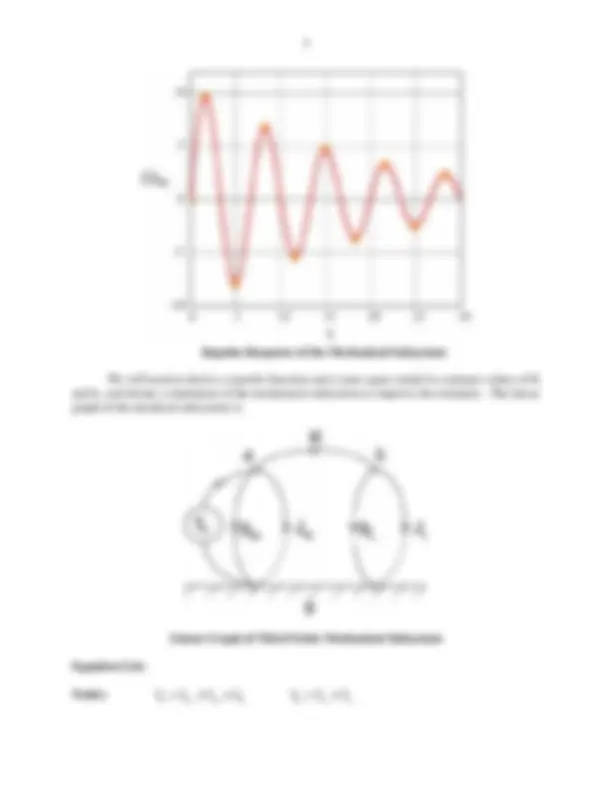
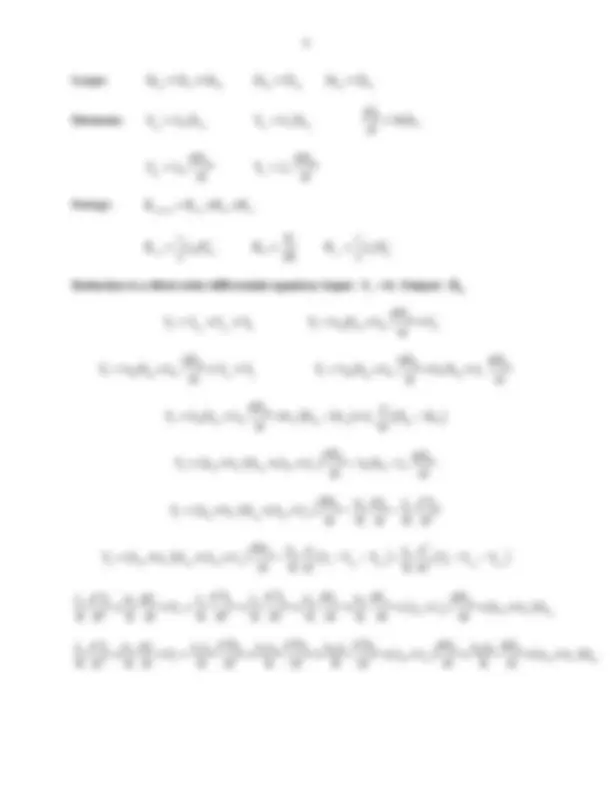
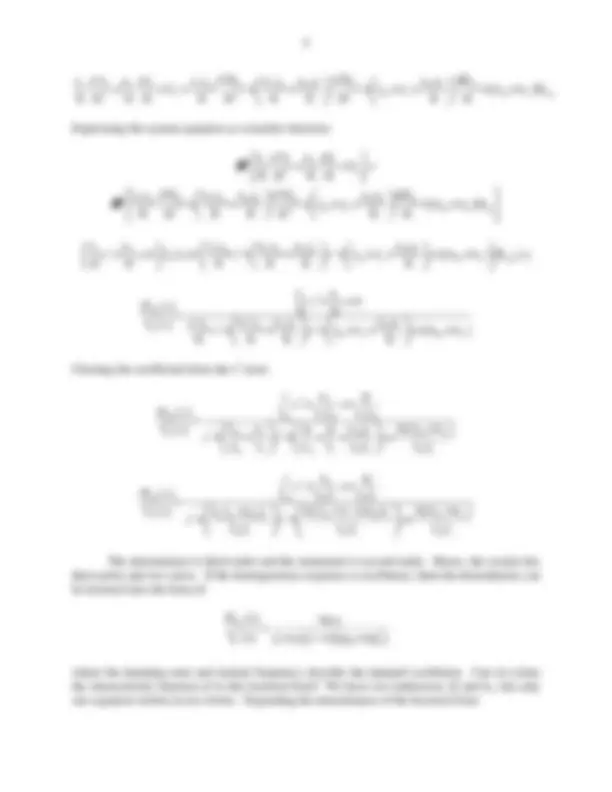
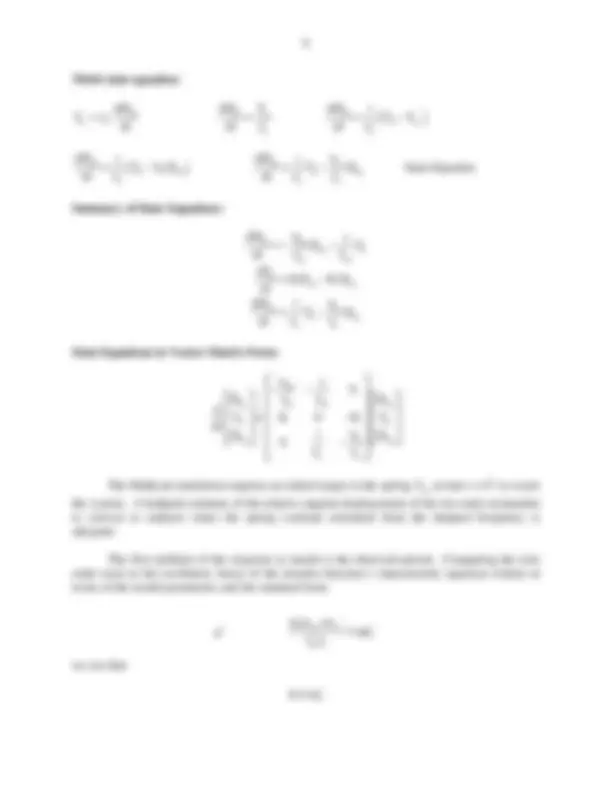
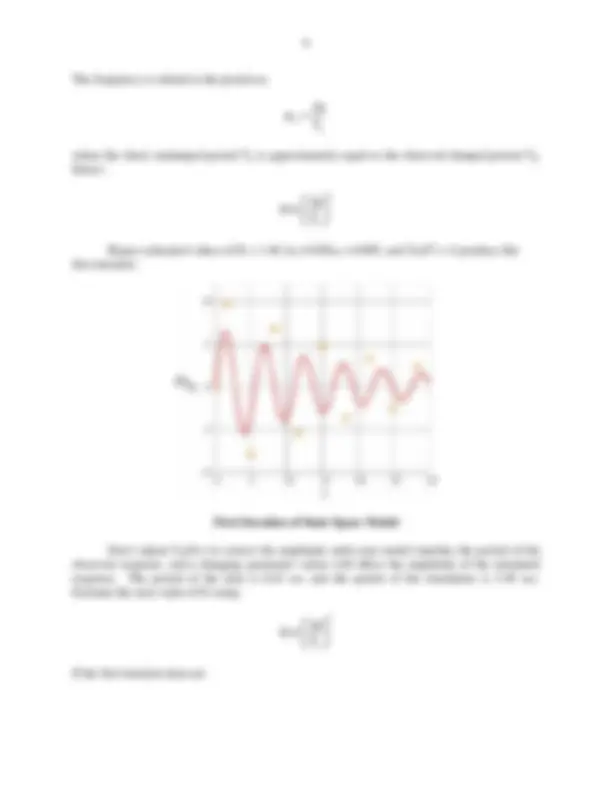
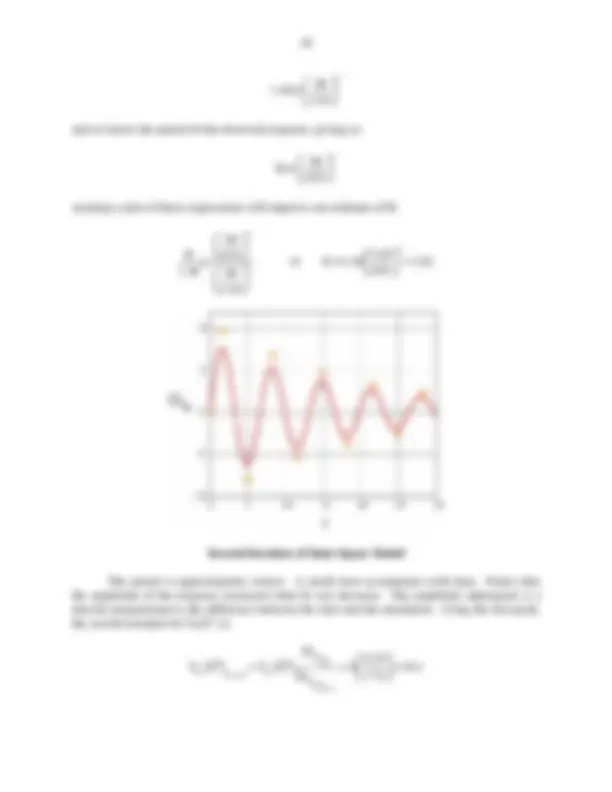
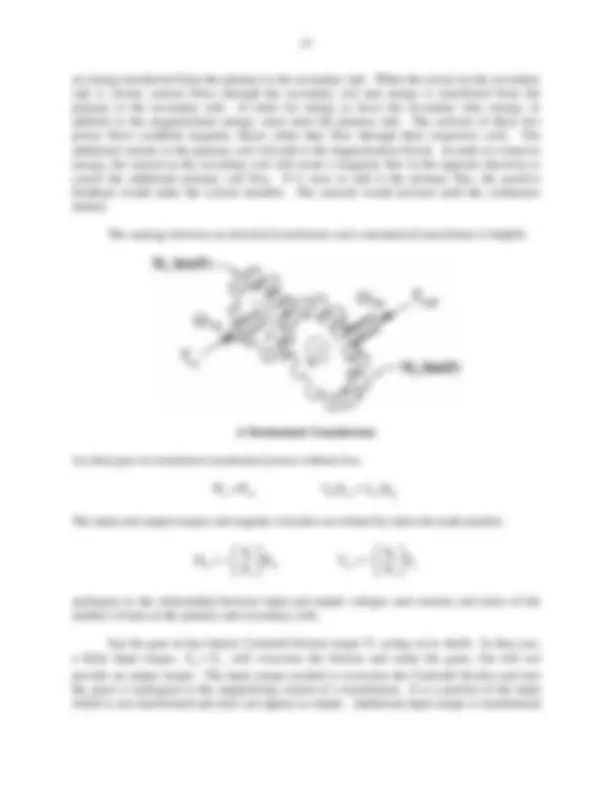
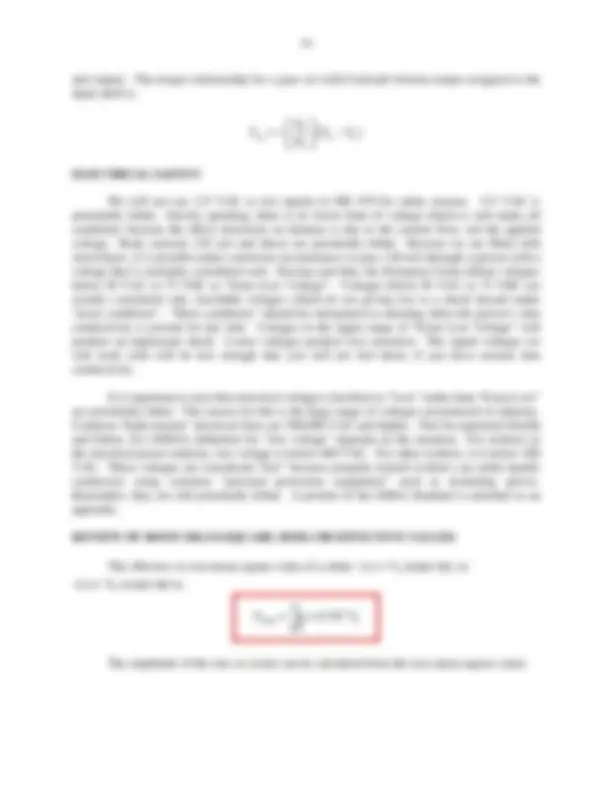
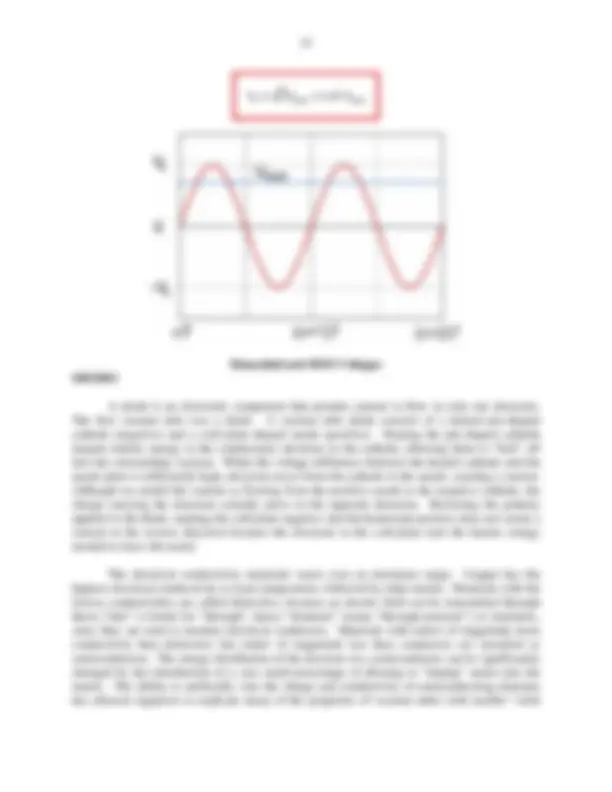
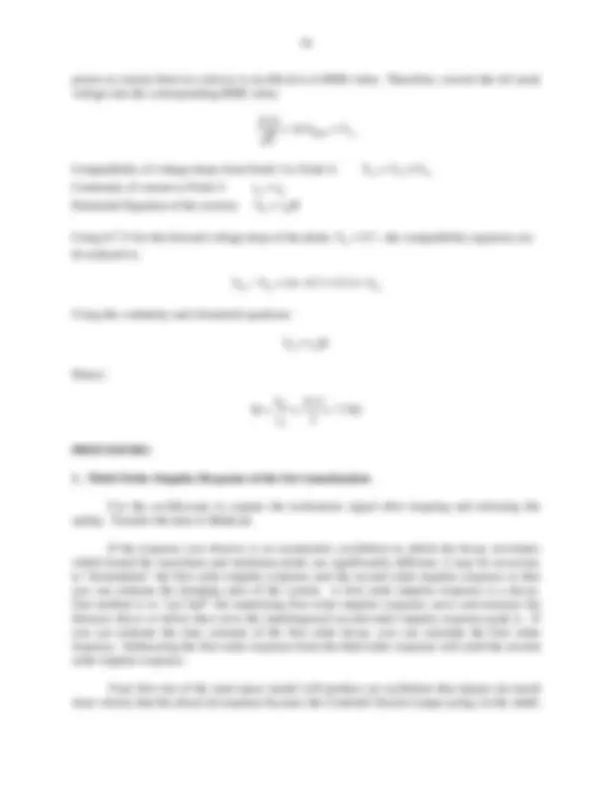
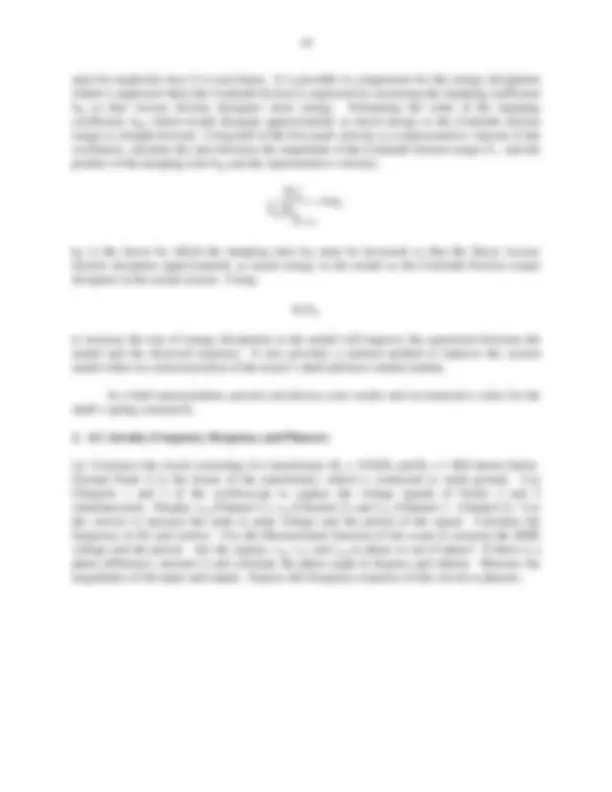
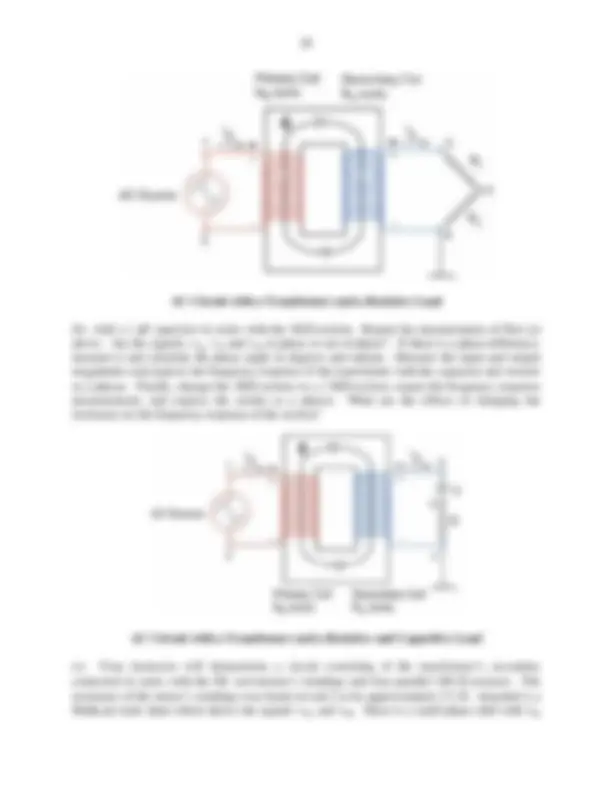
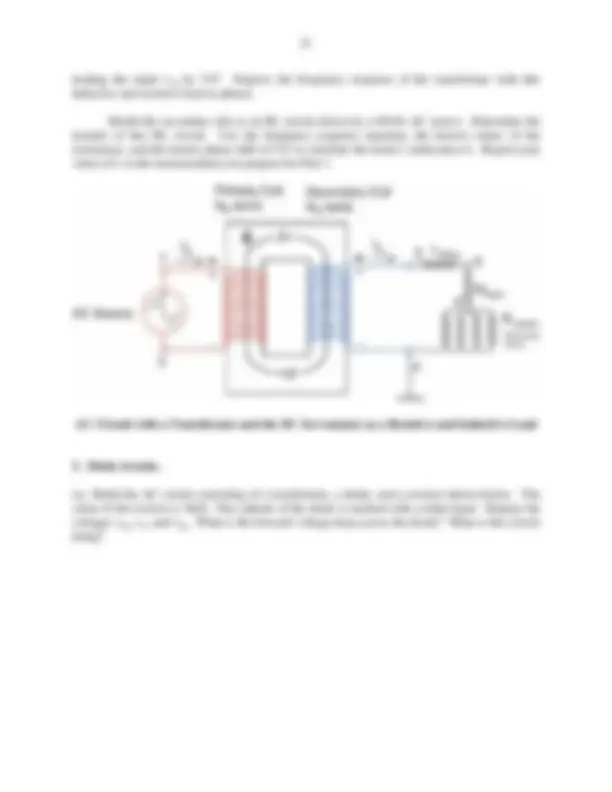
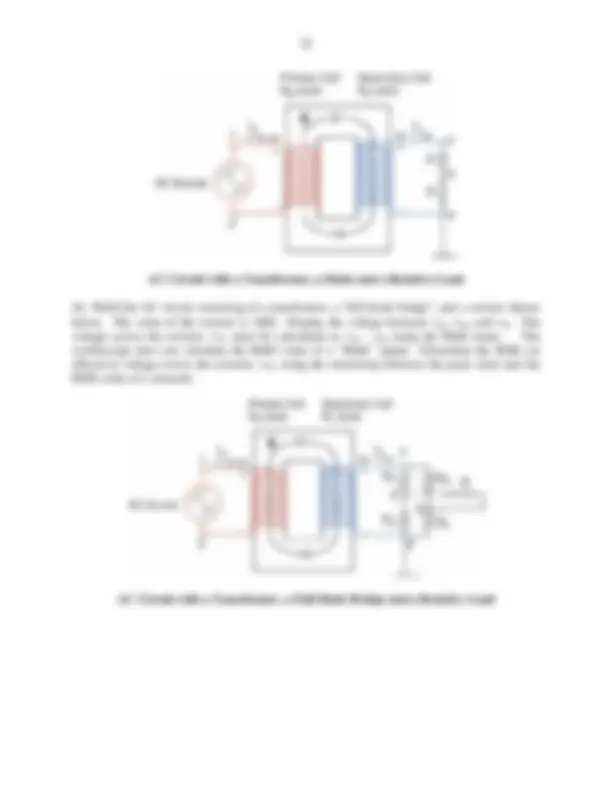
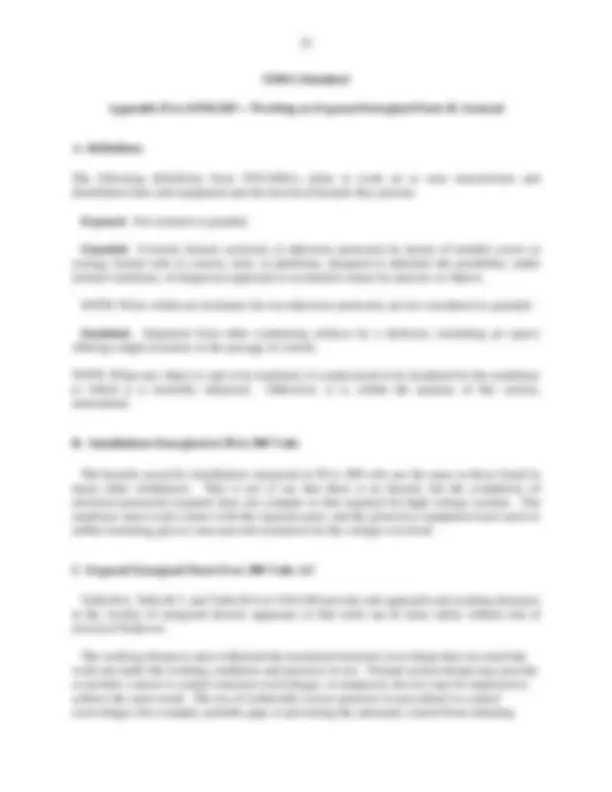
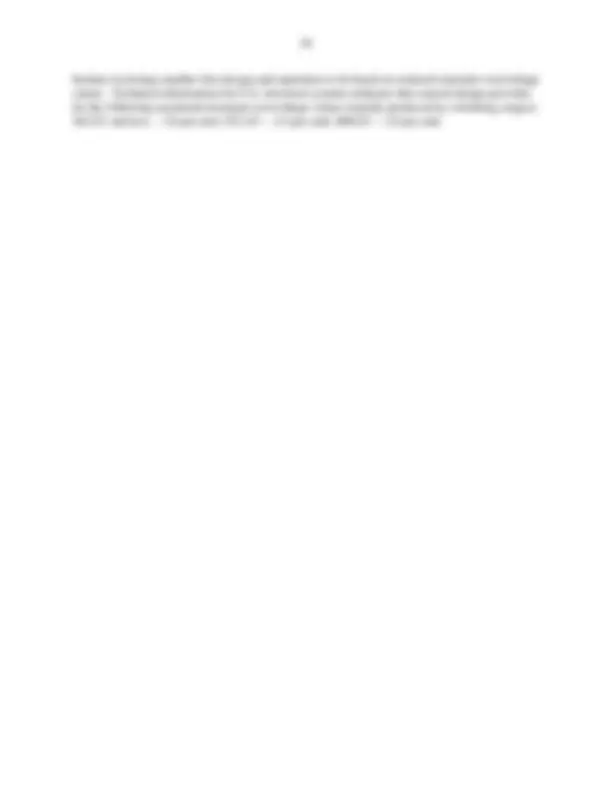
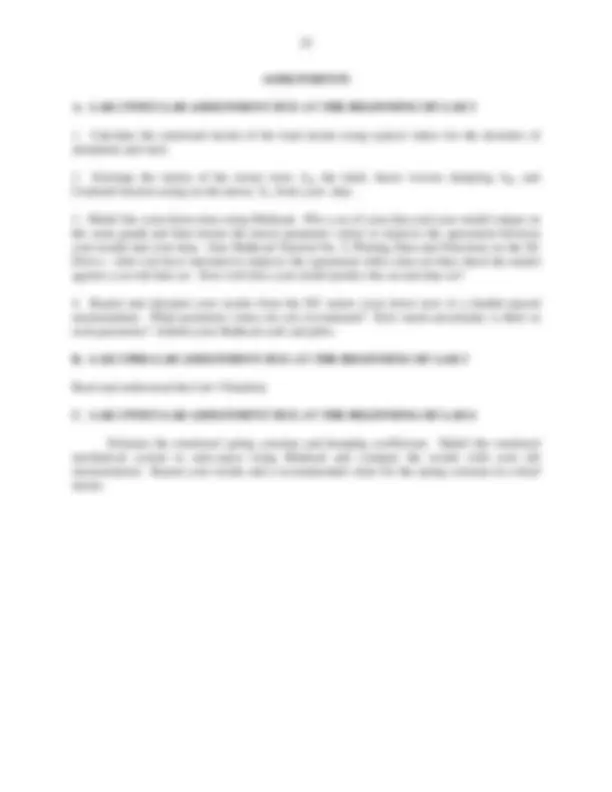
Study with the several resources on Docsity
Earn points by helping other students or get them with a premium plan
Prepare for your exams
Study with the several resources on Docsity
Earn points to download
Earn points by helping other students or get them with a premium plan
Community
Ask the community for help and clear up your study doubts
Discover the best universities in your country according to Docsity users
Free resources
Download our free guides on studying techniques, anxiety management strategies, and thesis advice from Docsity tutors
Material Type: Lab; Professor: Seeler; Class: Control Design & Analysis; Subject: Mechanical Engineering; University: Lafayette College; Term: Fall 2004;
Typology: Lab Reports
1 / 25
This page cannot be seen from the preview
Don't miss anything!
© Dr. Seeler Department of Mechanical Engineering Fall 2004 Lafayette College
ME 479: Dynamic Systems, Controls and Mechatronics Laboratory
Lab 3: Third Order Systems, AC Circuits, and Diodes.
OBJECTIVES
Two parameters of the servomechanism remain to estimated, the spring constant K of the compliant shaft and the damping bL of the bearing which support the load inertia.
Lumped Parameter Model of the DC Motor Driving a Rotation Load Through a Compliant Shaft
The motor inertia and the load inertia are independent energy storages when they are separated by a spring which serves as a compliant shaft because they can have different angular velocities during a transient response of the system. We have estimated the rotational inertia of the motor and have calculated the rotational inertia of the load inertia (which includes the aluminum cylinder plus two jaws of the coupling and the hinged collar). We wish to determine the spring constant of the torsional spring. We will remove the electrical subsystem by not powering the DC motor. This reduces the servomechanism to a third order mechanical subsystem.
We will perform a dynamic test in which we torque the spring manually and then release it. The strain energy stored in the spring will create an oscillation in the system. We will
observe the motion of the system by capturing the tachometer voltage on the oscilloscope. From the damped oscillation, we can establish the damped frequency, damping ratio, ideal undamped natural frequency of the second order poles of the system.
Servomechanism Configured as a Third Order System
We will use state-space to model the third order mechanical system. The three state variables are the angular velocities of the two inertias, Ω4g and Ω5g, and the torque in the spring, TK. As we discussed in Lab 2, the system’s damping is the property most difficult to characterize. We estimated the damping coeffiecient bM and Coulomb friction torque TC which act on the motor’s shaft from the coast-down test data. We will include the damping bM in our third order model, but we will not be able to include the Coulomb friction torque TC because the motor inertia will change direction, back and forth, as the system oscillates. The Coulomb friction torque would also have to change direction, which we cannot accomplish in our linear model. If it were necessary to improve the accuracy of our model, we would use dynamic simulation software, such as VisSim or Matlab, which include non-linear elememts. Alternatively, we could break our linear simulation into pieces corresponding to the sign of the motor inertia’s velocity. We would use the values of the state variables at the moment when the velocity changed sign as the initial conditions for the next period of the simulation, change the sign on the Coulomb friction torque, and continue the simulation.
We are interested in the second order aspect of the step response because its frequency is a function of the rotational spring constant K. Finding the period and the damping ratio of the second order impulse response is straight forward. The response will resemble the trace shown below:
Loops: Ω4g = Ω 45 + Ω5g Ω4g = Ω (^) 4g Ω5g = Ω5g
Elements: Tb (^) M = bM Ω (^) 4g Tb (^) L = bL Ω5g K 45
dT K dt
M
4g J M
d T J dt
= (^) JL L 5g
d T J dt
Energy: (^) Esystem = E (^) J (^) M + EK +EJL
M
2 J M
E = Ω4g
2 K K
2 5g
Reduction to a third order differential equation: Input: TC = 0, Output: Ω 4g
TC = Tb (^) M + TJ (^) M+ TK 4g C M 4g M
d T b J T dt K
L
4g C M 4g M b J
d T b J T T dt
= Ω + + + (^) L C M 4g M 4g^ L 5g L 5g
d d T b J b J dt dt
4g C M 4g M L 4g 45 L 4g 45
d (^) d T b J b J dt dt
4g (^45) C M L 4g M L L 45 L
d (^) d T b b J J b J dt dt
2 4g (^) L K L K C M L 4g M L (^2)
d (^) b dT J d T T b b J J dt K dt K dt
( ) ( ) (^) ( (^) M M ) ( (^) M M)
2 4g (^) L L C M L 4g M L C b J 2 C b J
d (^) b d J d T b b J J T T T T T T dt K dt K dt
2 2 2 L C L C L J^ L b^ L J^ L b^ 4g 2 C^2 2 M^ L^ M^ L^4
J d T b dT J d T^ J d T^ b dT^ b dT^ d T J J K dt K dt K dt K dt K dt K dt dt
2 3 2 2 L C L C L M 4g^ L M 4g^ M L 4g^ 4g^ M L 4g 2 C^3 2 2 M^ L^ M^ L^4
J d T b dT J J d^ b J d^ b J d^ d^ b b d T J J K dt K dt K dt K dt K dt dt K dt
2 3 2 L C L C L M 4g^ L M M L 4g^ M L 4g 2 C^3 2 M^ L
J d T b dT J J d^ b J b J d^ b b d T J J K dt K dt K dt K K dt K dt
Ω (^) ⎛ ⎞ Ω (^) ⎛ ⎞ Ω
bM bL Ω4g
Expressing the system equation as a transfer function:
2 L C L C 2 C
J d T b dT T K dt K dt
3 2 L M 4g^ L M M L 4g^ M L 4g 3 2 M^ L^ M^ L^ 4g
J J d^ b J b J d^ b b d J J b b K dt K K dt K dt
J b J J b J b J b b s s 1 T s s s J J s b b K K K K K K
⎛ ⎞ ⎛^ ⎛ ⎞ ⎛ ⎞ ⎞ ⎜ +^ +^ ⎟ =^ ⎜ +^ ⎜ +^ ⎟ +^ ⎜ +^ +^ ⎟ +^ +^ ⎟Ω ⎝ ⎠ (^) ⎝ ⎝ ⎠ ⎝ ⎠ ⎠
L 2 L 4g C L^ M^3 L^ M^ M^ L^2 M^ L M L M L
J b s s^ s^1 K K T s J J^ b J^ b^ J^ b^ b s s J J s K K K K
b b
Clearing the coefficient from the s^3 term:
(^2) L 4g (^) M L M L M C (^3) M L 2 M L M L M L M L M L M L
1 b K s s s (^) J J J J J T s (^) b b K K b b K b b s s s J J J J J J J J
(^2) L 4g (^) M M L M L C (^3) L M M L 2 M L M L M L M L M L M L
1 b K s s s (^) J J J J J T s (^) b J b J K J J b b K b b s s s J J J J J J
The denominator is third order and the numerator is second order. Hence, the system has three poles and two zeros. If the homogeneous response is oscillatory, then the denominator can be factored into the form of:
4g 2 2 C (^) n n
s (^) N(s) T s (^) s a s 2 s
where the damping ratio and natural frequency describe the damped oscillation. Can we relate the characteristic function of to this factored form? We have two unknowns, K and bL, but only one equation written in two forms. Expanding the denominator of the factored form:
ζ < 0.
We can simplify the approximation of the spring constant K by neglecting the second term in the denominator:
M L^2 n M L
≈ (^) ⎜ ⎟ω ⎝ + ⎠
Although we neglected bL in order to estimate K, we need an initial value for bL to begin the iteration. We have observed that the damping of the load bearings is “small” relative to the friction losses in the motor. Consequenlty, as an initial estimate, we will arbitrarily assign bL a “small” fraction of the value of bM, say:
IMPORTANT: Keep in mind that each of the parameter values is uncertain to some degree. Any multiplicative relationship increases the uncertainty of the result. Also, we estimated K and bL using contradictory assumptions. Finally, we neglect the Coulomb friction torque so that we can use a linear model. Consequently, do not be distressed if your initial simulation results indicate significant error in both K and bL. We will adjust our model’s parameters iteratively using repeated simulation until we reproduce the observed response as well as possible.
Since we are working with a third order system, we will use a state-space model for the simulation rather than perform the partial fraction expansion necessary to yield a time domain response from the third order transfer function.
Reduction to State-Space: Input: TC = 0, State-variables: Ω 4g, TK, Ω 5g
First state equation:
M
4g J M
d T J dt
= 4g JM M
d (^1) T dt J
= 4g C M
d (^1) T dt J
= (^) ( − Tb (^) M −TK)
4g M 4g K M
d (^1) b T dt J
= − Ω − 4g^ M 4g K M M
d (^) b 1 T dt J J
= − Ω − State Equation
Second state equation:
K 45
dT K dt
dT K dt
= Ω − Ω K 4g 5g
dT K K dt
= Ω − Ω State Equation
Third state equation:
L
5g J L
d T J dt
= 5g JL L
d T dt J
= 5g ( (^) K bL) L
d (^1) T T dt J
5g K L 5g L
d (^1) T b dt J
= − Ω 5g^ K L 5 L L
d (^1) b T dt J J g
= − Ω State Equation
Summary of State Equations:
4g (^) M 4g K M M
d (^) b 1 T dt J J
K 4g 5g
dT K K dt
5g (^) L K 5 L L
d (^1) b T dt J J g
State Equations in Vector-Matrix Form:
M 4g M M 4g K K 5g L 5g L L
b 1 0 J J d T K 0 K T dt 1 b 0 J J
The Mathcad simulation requires an initial torque in the spring TK 0 at time t = 0+^ to excite
the system. A ballpark estimate of the relative angular displacement of the two ends (remember to convert to radians) times the spring constant estimated from the damped frequency is adequate.
The first attribute of the response to match is the observed period. Comparing the zero order term in the oscillatory factor of the transfer function’s characteristic equation written in terms of the model parameters and the standard form:
s^0
n M L
K b b a J J
= ω
we see that:
2 K ∝ ωn
2 2
⎛ π ⎞ ∝ ⎜ ⎟ ⎝ ⎠
and we know the period of the observed response, giving us:
2 2 K
⎛ π ⎞ ∝ ⎜ ⎟ ⎝ ⎠
creating a ratio of these expressions will improve our estimate of K:
2
2
⎛ π ⎞ ⎜ ⎟ ∝ ⎝^ ⎠ ⎛ π ⎞ ⎜ ⎟ ⎝ ⎠
2
K 1.48 1.
Second Iteration of State-Space Model
The period is approximately correct. A small error accumulates with time. Notice that the amplitude of the response increased when K was decrease. The amplitude adjustment is a directly proportional to the difference between the data and the simulation. Using the first peak, the second estimate for TK(0+) is:
PeakData
SimulationPeak
4g K (^) revised K 4g
Third Iteration of State-Space Model
This looks pretty good, but these “data” were generated by a linear model. You will not achieve as good a fit between your data, which include the effect of the Coulomb friction torque, and your model, which doesn’t. This is an opportunity to estimate the value of the damping coefficient, bM, which would dissipate approximately as much energy as the Coulomb friction torque, which we must neglect. The procedure is straight-foreward. Using as an representative velocity of the oscillation, half of the first peak velocity, calculate the ratio between the magnitude of the Coulomb friction torque TC and the product of the damping ratio bM and the represenative velocity:
C C M 4g half max
b
≡ α Ω
αC is the factor by which the damping ratio bM must be increased so that the linear viscous friction dissipates approximately as much energy in the model as the Coulomb friction torque dissipates in the actual system. Using:
α C bM
to increase the rate of energy dissipation in the model will improve the agreement between the model and the observed response.
ELECTRICAL TRANSFORMERS
A schematic of a “core” type transformer is shown below:
no energy transferred from the primary to the secondary side. When the circuit on the secondary side is closed, current flows through the secondary coil and energy is transferred from the primary to the secondary side. In order for energy to leave the secondary side, energy, in addition to the magnetization energy, must enter the primary side. The currents of these two power flows establish magnetic fluxes when they flow through their respective coils. The additional current in the primary coil will add to the magnetization flux φ. In order to conserve energy, the current in the secondary coil will create a magnetic flux in the opposite direction to cancel the additional primary coil flux. If it were to add to the primary flux, the positive feedback would make the system unstable. The currents would increase until the conductors melted.
The analogy between an electrical transformer and a mechanical transformer is helpful.
A Mechanical Transformer
An ideal gear set transforms mechanical power without loss.
P in =Pout Tin Ω1g = Tout Ω2g
The input and output torques and angular velocities are related by ratios the teeth number:
1 2g 1g 2
2 out in 2
analogous to the relationship between input and output voltages and currents and ratios of the number of turns in the primary and secondary coils.
Say the gear set has kinetic Coulomb friction torque TC acting on its shafts. In that case, a finite input torque, , will overcome the friction and rotate the gears, but will not
provide an output torque. The input torque needed to overcome the Coulomb friction and turn the gears is analogous to the magnetizing current of a transformer. It is a portion of the input which is not transformed and does not appear as output. Additional input torque is transformed
T in =TC
and output. The torque relationship for a gear set with Coulomb friction torque assigned to the input shaft is:
2
We will not use 115 VAC as test signals in ME 479 for safety reasons. 115 VAC is potentially lethal. Strictly speaking, there is no lower limit of voltage which is safe under all conditions because the effect electricity on humans is due to the current flow, not the applied voltage. Body currents 120 mA and above are potentially lethal. Because we are filled with electrolytes, it is possible under contrived circumstances to pass 120 mA through a person with a voltage that is normally considered safe. Having said that, the European Union define voltages below 50 VAC or 75 VDC as “Extra Low Voltage”. Voltages below 50 VAC or 75 VDC are usually considered safe, touchable voltages which do not giving rise to a shock hazard under “most conditions”. “Most conditions” should be interpreted as meaning when the person’s skin conductivity is normal for dry skin. Voltages in the upper range of “Extra Low Voltage” will produce an unpleasant shock. Lower voltages produce less sensation. The signal voltages we will work with will be low enough that you will not feel them, if you have normal skin conductivity.
It is important to note that electrical voltages classified as “Low” rather than “Extra Low” are potentially lethal. The reason for this is the huge range of voltages encountered in industry. Common “high tension” electrical lines are 500,000 VAC and higher. The Occupational Health and Safety Act (OSHA) definition for “low voltage” depends on the situation. For workers in the electrical power industry, low voltage is below 600 VAC. For other workers, it is below 300 VAC. These voltages are considered “low” because properly trained workers can safely handle conductors using common “personal protection equipment” such as insulating gloves. Remember, they are still potentially lethal. A portion of the OSHA Standard is attached as an appendix.
REVIEW OF ROOT-MEAN-SQUARE (RMS) OR EFFECTIVE VALUES
The effective or root-mean-square value of a either v(t) = V sin( 0 ω + φt ) or v(t) = V cos( 0 ω +t φ)is:
0 RMS 0
The amplitude of the sine or cosine can be calculated from the root-mean-square value:
state” devices. Although vacuum tubes are still used, most diodes today are semiconductor devices made of silicon or germanium. Depending on the doping atom used, regions of the semiconductor can develop net positive or negative charges. The diodes we will work with in lab are “junction” type, where the flow of current through the semiconductor is governed by the voltage established at the junction between negative and positive regions.
Diode Symbol and Current Flow Direction
Diode Voltage – Current Plot
Although the actual behavior of diodes is nonlinear, we will use an idealized linear model for our engineering calculations. Our diode model will allow current flow only from the anode
to the cathode, regardless of the polarity of the applied voltage. No current will flow if the applied voltage in the “forward” direction (from anode to cathode) is less than approximately 0. volts. (You will establish a more accurate value in lab). When the forward voltage drop (which electrical engineers call the “forward bias”) of the diode equals 0.7 volts, the diode conducts with negligiblely small resistance. We will need to provide an impedance in the circuit to limit the current flow through the diode because real diodes cannot conduct infinite current. If the impedance is a resistor added to the circuit only to limit the current through the diode, then that resistor is called a “ballast” resistor.
Often the allowable current through a semiconductor device is expressed as the maximum power the device can dissipate. The power dissipated by a diode is the product of its forward voltage drop times the current through the diode. The magnitude of the impedance needed to limit the current through the diode to an allowable value is calculated summing voltages around the loop containing the diode, using the diode’s forward voltage as its voltage drop.
Example: The diode D in the circuit shown below has an allowable working current of 2 A. The AC on the secondary side of the transformer has a peak voltage of 22.6 volts. Calculate the minimum “ballast” resistance R needed.
Since we are working with an AC circuit, we need to decide whether the allowable current is an RMS value (the effective current) or the peak value. If not indicated otherwise, a
must be neglected since it is non-linear. It is possible to compensate for the energy dissipation which is neglected when the Coulomb friction is neglected by increasing the damping coefficient bM so that viscous friction dissipates more energy. Estimating the value of the damping coefficient, bM, which would dissipate approximately as much energy as the Coulomb friction torque is straight-forward. Using half of the first peak velocity as a representative velocity of the oscillation, calculate the ratio between the magnitude of the Coulomb friction torque TC and the product of the damping ratio bM and the representative velocity:
C C M 4g half max
b
≡ α Ω
αC is the factor by which the damping ratio bM must be increased so that the linear viscous friction dissipates approximately as much energy in the model as the Coulomb friction torque dissipates in the actual system. Using:
α C bM
to increase the rate of energy dissipation in the model will improve the agreement between the model and the observed response. It also provides a rational method to improve the system model when we control position of the motor’s shaft and have similar motion.
In a brief memorandum, present and discuss your results and recommend a value for the shaft’s spring constant K.
2. AC circuits, Frequency Response, and Phasors:
(a) Construct the circuit consisting of a transformer, R 1 = 10 KΩ, and R 2 = 1 KΩ shown below. Ground Node 4 to the frame of the transformer, which is connected to earth ground. Use Channels 1 and 2 of the oscilloscope to capture the voltage signals of Nodes 3 and 5 simultaneously. Display v3g (Channel 1), v5g (Channel 2), and v 35 (Channel 1 – Channel 2). Use the cursors to measure the peak to peak voltage and the period of the signal. Calculate the frequency in Hz and rad/sec. Use the Measurement function of the scope to measure the RMS voltage and the period. Are the signals, v3g, v 35 and v5g in phase or out of phase? If there is a phase difference, measure it and calculate the phase angle in degrees and radians. Measure the magnitudes of the input and output. Express the frequency response of this circuit as phasors.
AC Circuit with a Transformer and a Resistive Load
(b) Add a 1 μF capacitor in series with the 1KΩ resistor. Repeat the measurements of Part (a) above. Are the signals, v3g, v 35 and v5g in phase or out of phase? If there is a phase difference, measure it and calculate the phase angle in degrees and radians. Measure the input and output magnitudes and express the frequency response of the transformer with the capacitor and resistor as a phasor. Finally, change the 1KΩ resistor to a 1 MΩ resistor, repeat the frequency response measurements, and express the results as a phasor. What are the effects of changing the resistance on the frequency response of the system?
AC Circuit with a Transformer and a Resistive and Capacitive Load
(c) Your instructor will demonstrate a circuit consisting of the transformer’s secondary connected in series with the DC servomotor’s windings and four parallel 100 Ω resistors. The resistance of the motor’s windings was found in Lab 2 to be approximately 5.5 Ω. Attached is a Mathcad work sheet which shows the signals v3g, and v6g. There is a small phase shift with v6g