
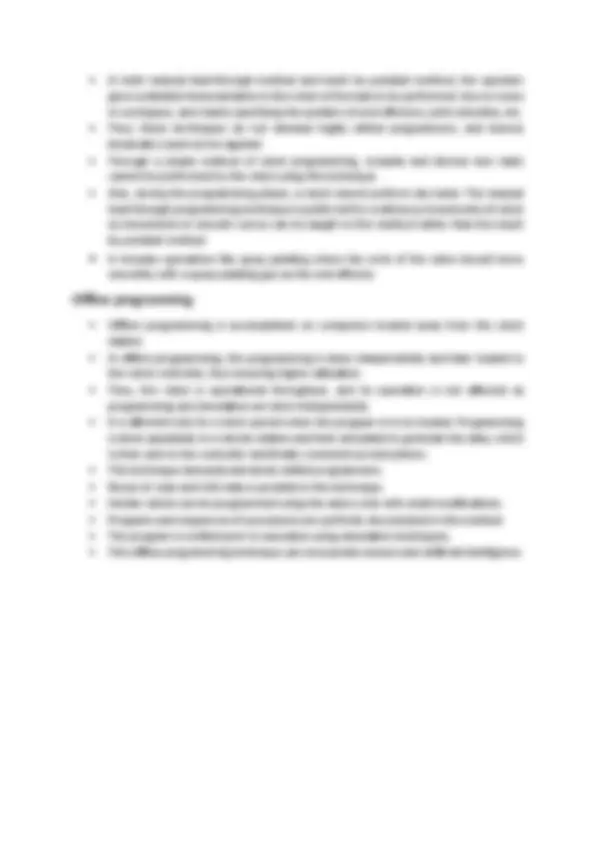
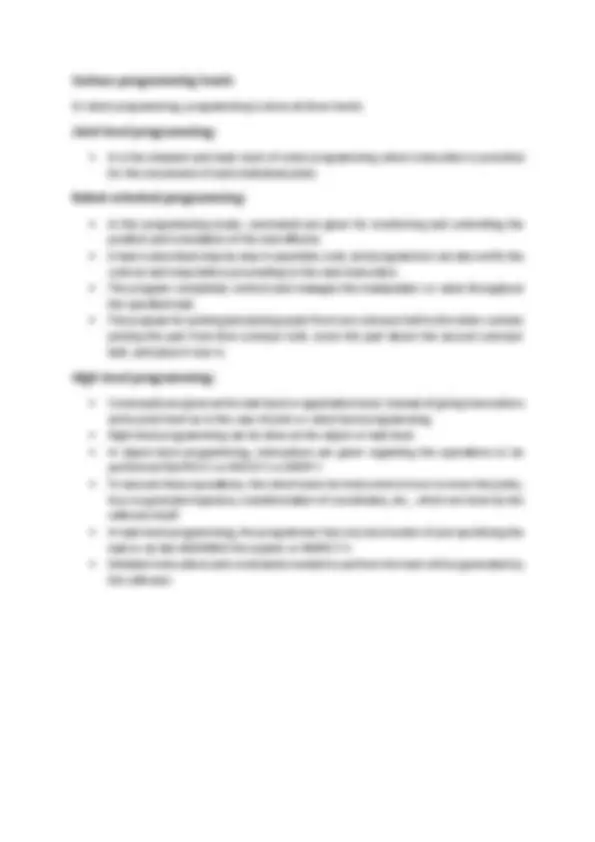
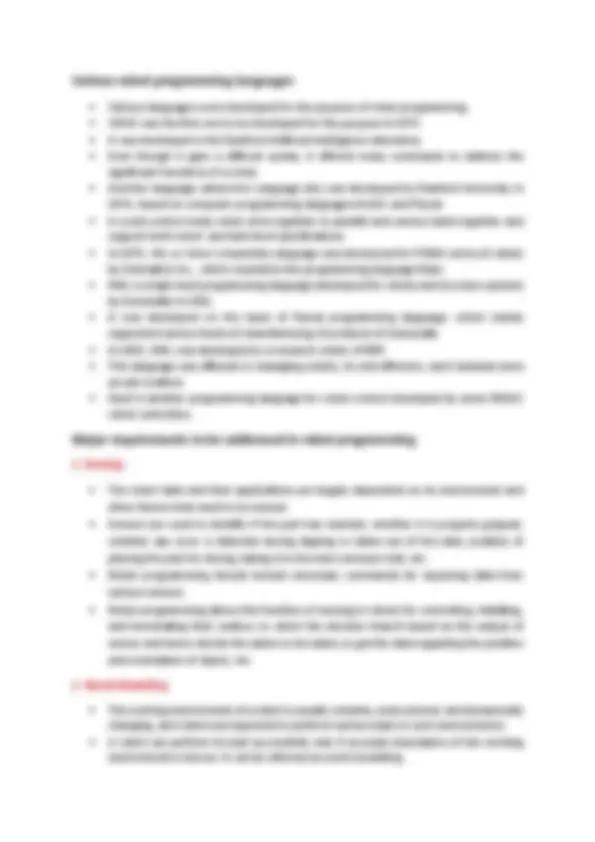
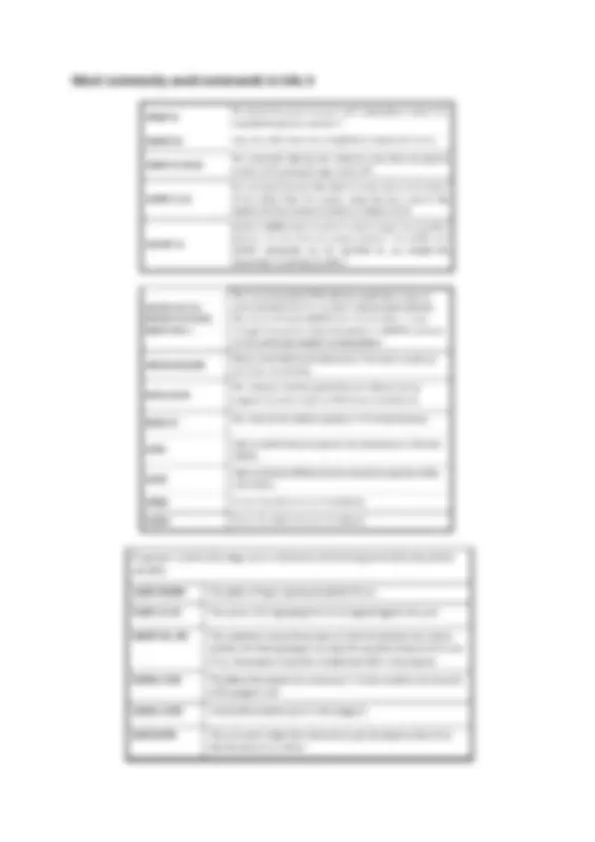
Study with the several resources on Docsity
Earn points by helping other students or get them with a premium plan
Prepare for your exams
Study with the several resources on Docsity
Earn points to download
Earn points by helping other students or get them with a premium plan
Community
Ask the community for help and clear up your study doubts
Discover the best universities in your country according to Docsity users
Free resources
Download our free guides on studying techniques, anxiety management strategies, and thesis advice from Docsity tutors
Introduction to robotics - Module 4
Typology: Study notes
1 / 8
This page cannot be seen from the preview
Don't miss anything!
Robot Programming: A robot program is a set of instructions given to the robot to define and control its actions. Robots are programmed to make them perform complex tasks, and these programs can be edited or changed when required. The various steps in robot programming include training the robot on the task to be performed, saving and executing the program, and debugging procedure to correct the code if needed. Robot programs can be simple or complex based on the actions to be performed. A simple program contains codes to tell the robot how to respond to a particular event that can be expected. Complex programs direct robots on how to perform when complex situations arise and are trained to learn from past series of events and to predict things that are yet to happen and respond accordingly. A robot program commands or instruct them to operate the end-effectors, grippers, etc. how to take a decision based on certain events, movement, etc. In online programming, a robot is manually trained or guided on the various configurations within the workspace, and various motions and positions using the lead-through method or using teach pendants. In offline programming, programs are written in one of the many robot programming languages. The series of actions that the robot needs to perform are listed in detail using these textural languages. The major types of robot programming methods are as follows:
In robot programming, programming is done at three levels:
1. Sensing: - The robot tasks and their applications are largely dependent on its environment and other factors that need to be sensed. - Sensors are used to identify if the part has reached, whether it is properly gripped, whether any error is detected during dipping or taken out of the tank, position of placing the part for drying, taking it to the next conveyor belt, etc. - Robot programming should include necessary commands for acquiring data from various sensors. - Robot programming allows the function of sensing in robots for controlling, initiating, and terminating their motion, to select the decision branch based on the output of sensor and hence decide the action to be taken, to get the data regarding the position and orientation of object, etc.
Motion commands, speed control commands, sensor commands (SIGNAL, WAIT, DELAY) end effector commands, react commands (Refer class notes)