
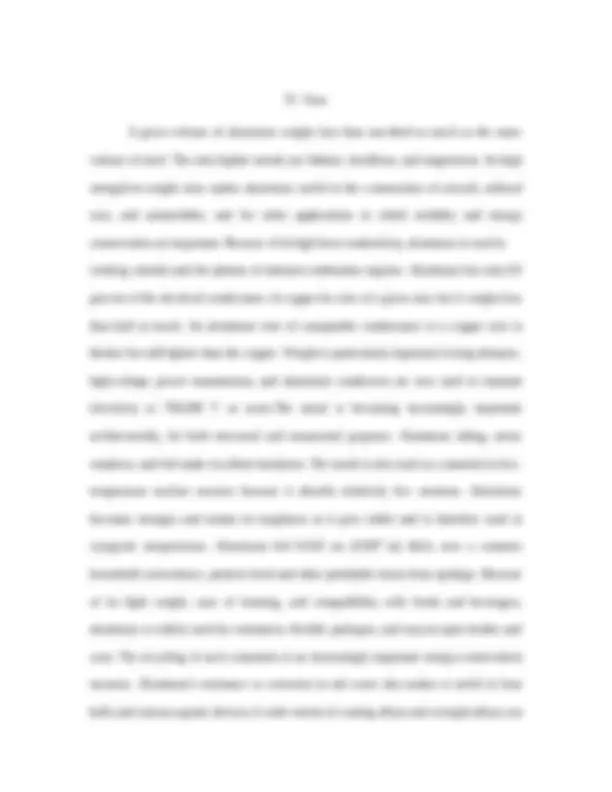
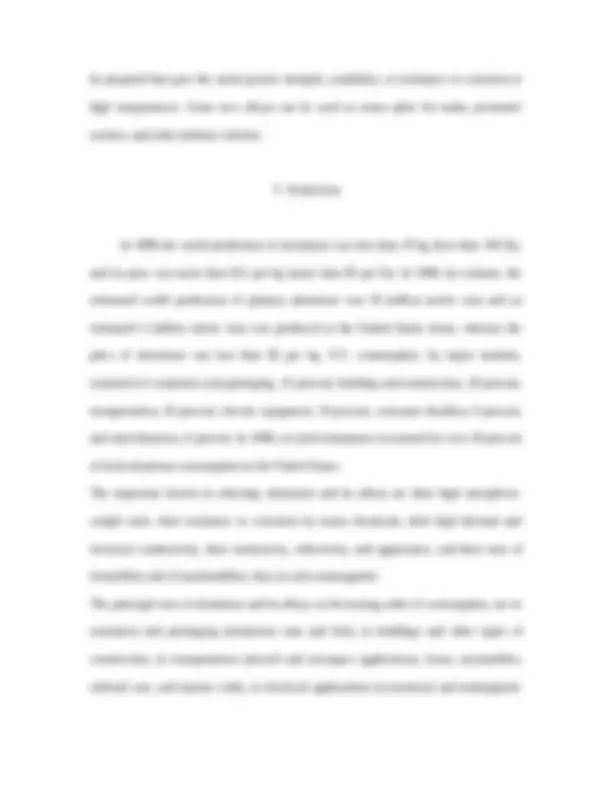

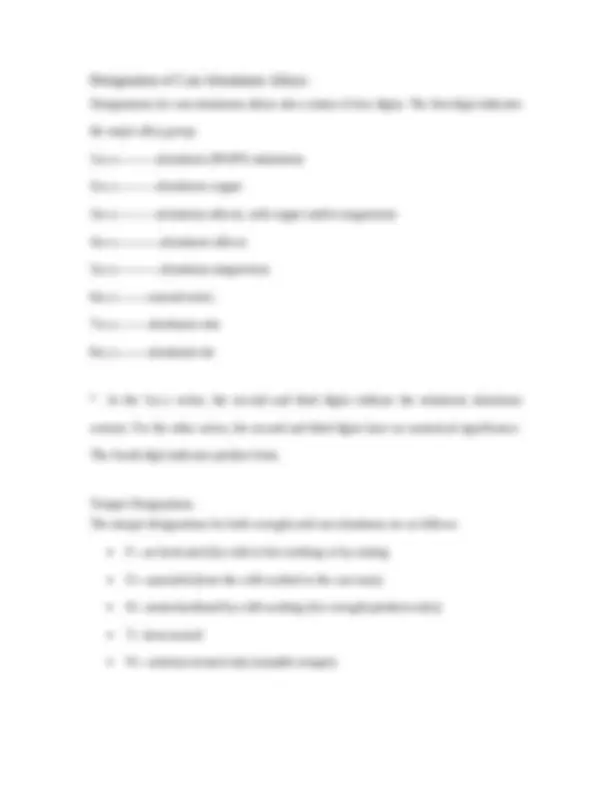
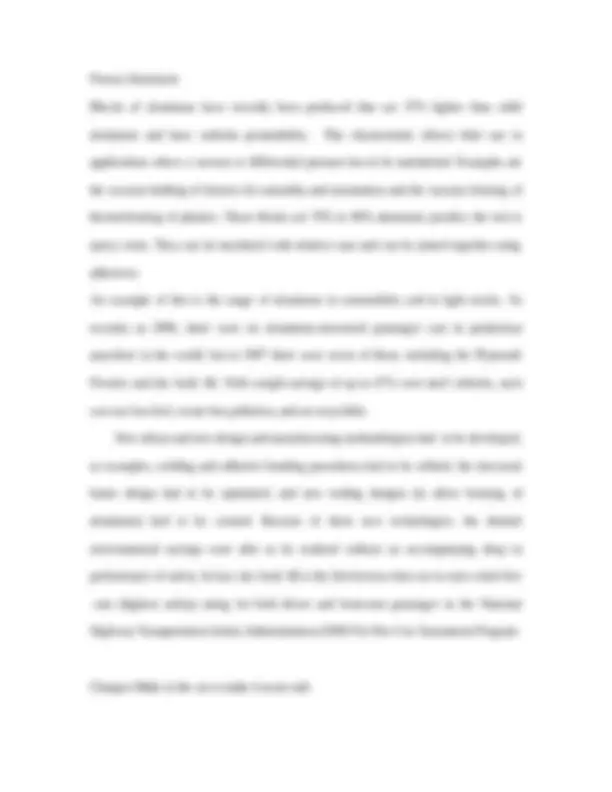
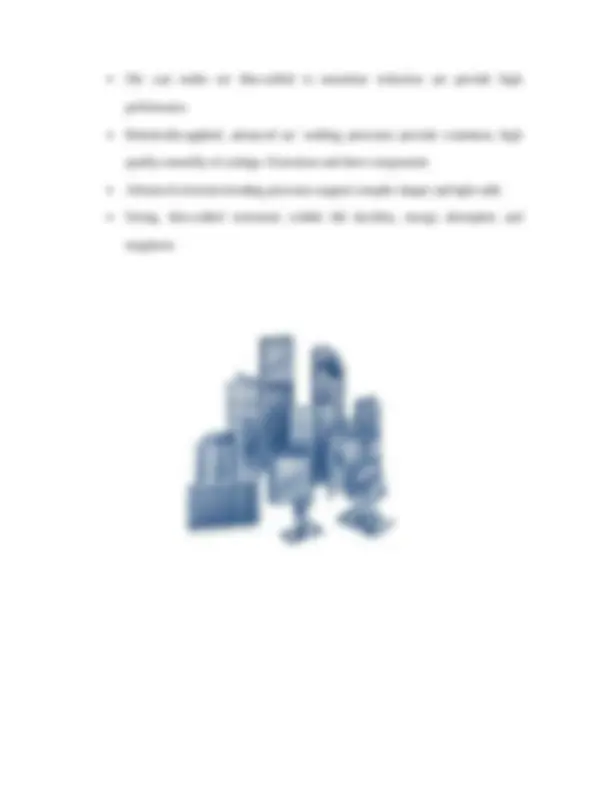
Study with the several resources on Docsity
Earn points by helping other students or get them with a premium plan
Prepare for your exams
Study with the several resources on Docsity
Earn points to download
Earn points by helping other students or get them with a premium plan
Community
Ask the community for help and clear up your study doubts
Discover the best universities in your country according to Docsity users
Free resources
Download our free guides on studying techniques, anxiety management strategies, and thesis advice from Docsity tutors
An in-depth look into the history of aluminum discovery, its properties, production methods, and various applications. Aluminum is a lightweight, highly reactive metal with a wide range of uses in industries such as construction, transportation, electrical applications, and consumer goods. Its isolation by hans christian oersted and henri sainte-claire deville, its atomic and physical properties, and its commercial production through the hall-héroult process. Uses of aluminum include its use in aircraft, cooking utensils, electrical conductors, and insulators.
Typology: Assignments
1 / 12
This page cannot be seen from the preview
Don't miss anything!
Introduction Aluminum (in Canada and Europe, aluminium), symbol Al, the most abundant metallic element in the earth's crust. The atomic number of aluminum is 13; the element is in group 13 (IIIa) of the periodic table. Hans Christian Oersted, a Danish chemist, first isolated aluminum in 1825, using a chemical process involving potassium amalgam. Between 1827 and 1845, Friedrich Wöhler, a German chemist, improved Oersted's process by using metallic potassium. He was the first to measure the specific gravity of aluminum and show its lightness. In 1854 Henri Sainte-Claire Deville, in France, obtained the metal by reducing aluminum chloride with sodium. Aided by the financial backing of Napoleon III, Deville established a large- scale experimental plant and displayed pure aluminum at the Paris Exposition of 1855. II. Properties Aluminum is a lightweight, silvery metal. The atomic weight of aluminum is 26.9815; the element melts at 660° C (1220° F), boils at 2467° C (4473° F), and has a specific gravity of 2.7. Aluminum is a strongly electropositive metal and extremely reactive. In contact with air, aluminum rapidly becomes covered with a tough, transparent layer of aluminum oxide that resists further corrosive action. For this reason, materials made of aluminum do not tarnish or rust. The metal reduces many other metallic compounds to their base metals. For example, when thermite (a mixture of from
the iron; the heat of powdered iron oxide and aluminum) is heated, the aluminum rapidly removes the oxygen the reaction is sufficient to melt the iron. This phenomenon is used in the thermite process for welding iron.The oxide of aluminum is amphoteric—showing both acidic and basic properties. The most important compounds include the oxide, hydroxide, sulfate, and mixed sulfate compounds (see Alum). Anhydrous aluminum chloride is important in the oil and synthetic-chemical industries. Many gemstones—ruby and sapphire, for example—consist mainly of crystalline aluminum oxide. III. Occurrence Aluminum is the most abundant metallic constituent in the crust of the earth; only the nonmetals oxygen and silicon are more abundant. Aluminum is never found as a free metal; commonly as aluminum silicate or as a silicate of aluminum mixed with other metals such as sodium, potassium, iron, calcium, and magnesium. These silicates are not useful ores, for it is chemically difficult, and therefore an expensive process, to extract aluminum from them. Bauxite, an impure hydrated aluminum oxide, is the commercial source of aluminum and its compounds.In 1886 Charles Martin Hall in the United States and Paul L. T. Héroult in France independently and almost simultaneously discovered that alumina, or aluminum oxide, would dissolve in fused cryolite (Na3AlF6) and could then be decomposed electrolytically to a crude molten metal. A low-cost technique, the Hall-Héroult process, is still the major method used for the commercial production of aluminum, although new methods are under study. The purity of the product has been increased until a commercially pure ingot is 99.5 percent pure aluminum; it can be further refined to 99.99 percent.
be prepared that give the metal greater strength, castability, or resistance to corrosion or high temperatures. Some new alloys can be used as armor plate for tanks, personnel carriers, and other military vehicles. V. Production In 1886 the world production of aluminum was less than 45 kg (less than 100 lb), and its price was more than $11 per kg (more than $5 per lb). In 1989, by contrast, the estimated world production of primary aluminum was 18 million metric tons and an estimated 4 million metric tons was produced in the United States alone, whereas the price of aluminum was less than $2 per kg. U.S. consumption, by major markets, consisted of containers and packaging, 31 percent; building and construction, 20 percent; transportation, 24 percent; electric equipment, 10 percent; consumer durables, 9 percent; and miscellaneous, 6 percent. In 1989, recycled aluminum accounted for over 20 percent of total aluminum consumption in the United States. The important factors in selecting aluminum and its alloys are their high strength-to- weight ratio, their resistance to corrosion by many chemicals, their high thermal and electrical conductivity, their nontoxicity, reflectivity, and appearance, and their ease of formability and of machinability; they are also nonmagnetic. The principal uses of aluminum and its alloys, in decreasing order of consumption, are in containers and packaging (aluminum cans and foil), in buildings and other types of construction, in transportation (aircraft and aerospace applications, buses, automobiles, railroad cars, and marine craft), in electrical applications (economical and nonmagnetic
electrical conductor), in consumer durables (appliances, cooking utensils, and furniture), and in portable tools. Nearly all high-voltage transmission wiring is made of aluminum. In its structural (load-bearing) components, 82% of a Boeing 747 aircraft and 79% of a Boeing 757 aircraft is aluminum. Properties of Selected Aluminum Alloys at Room Temperature Alloy Temper Ultimate tensile Yield Strength Elongation Strength (Mpa) (Mpa) in 50 mm (%) 1100 0 90 35 33- 1100 H14 125 120 9- 2024(A92024) O 190 75 20- 2024 t4 470 325 19- 3003(930030) O 110 40 30- 3003 H14 150 145 8- Manufacturing Properties and Typical Applications of Selected Wrought Aluminum Alloys Alloy Corrosion Mechanability Weldability Typical Application 1100 A C-D A Sheet metal work, hollow ware, tin stock 2024 C B-C B-C Truck wheels, screw machine products, aircraft
can be hardened by cold-working and are not heat –treatable, and alloys that can be hardened by heat treatment. Wrought – aluminum alloys are identified by four digits and by a temper designation that shows the condition of the material. The major alloying element is identified by the first dight. 1xxx – commeercially pure aluminum-excellent corrosion resistance/ high electrical and thermal conductivity: good workability: low strength: not heat treatable. 2xxx --copper------high strength-to-weight ratio: low resistance to corrosion: heat treatable. 3xxx---manganese---good workability: moderate strength: not generally heat-treatable. 4xxx---silicon---lower melting point; forms an oxide film of a dark-gray to charcoal color; not generally heat-treatable. 5xxx---magnesium---good corrosion resistance and weldability: moderate to high strength: not heat treatable. 6xxx---magnesium and silicon---medium strength; good formability, machinability, weldability, and corrosion resistance; heat treatable. 7xxx---zinc---moderate to very high strength; heat treatable.
Designations for cast aluminum alloys also consist of four digits. The first digit indicates the major alloy group. 1xx.x----------aluminum (99.00% minimum) 2xx.x----------aluminum-copper 3xx.x----------aluminum-silicon, with copper and/or magnesium 4xx.x-----------aluminum-silicon 5xx.x-----------aluminum-magnesium 6xx.x--------unused series 7xx.x--------aluminum-zinc 8xx.x--------aluminum-tin
Die cast nodes are thin-walled to maximize reduction yet provide high performance. Robotically-applied, advanced arc welding processes provide consistent, high quality assembly of castings. Extrusions and sheet components Advanced extrusion bending processes support complex shaper and tight radii Strong, thin-walled extrusions exhibit hih ductility, energy absorption and toughness
References url: http://www.encarta.msn.com/find/search.asp? search=aluminum Kalpakjian, Serope, and Steven R. Schmid. “Manufacturing Engineering and Technology. 4th^ ed. New Jersey. November 2000.