
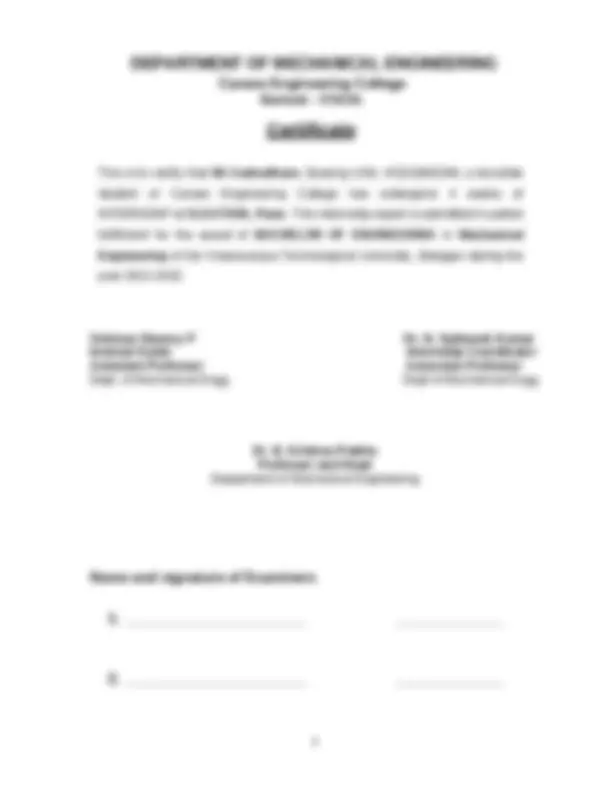
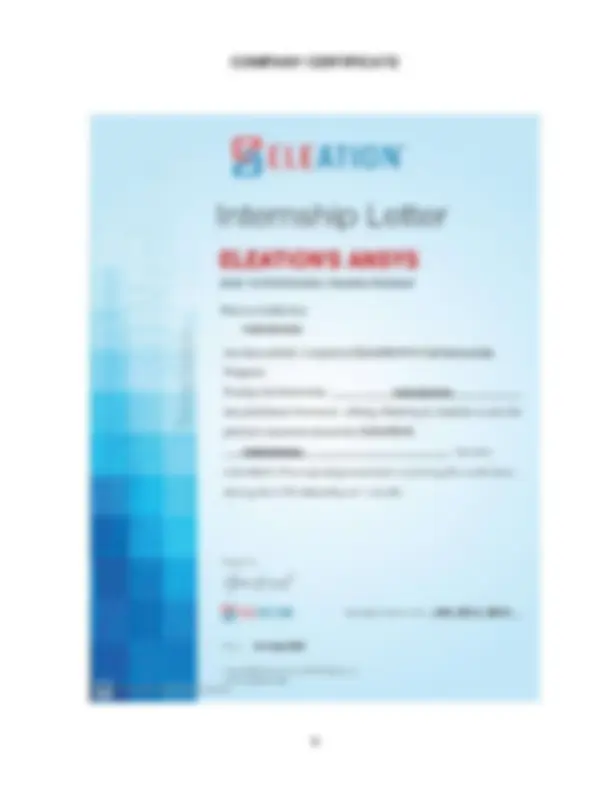
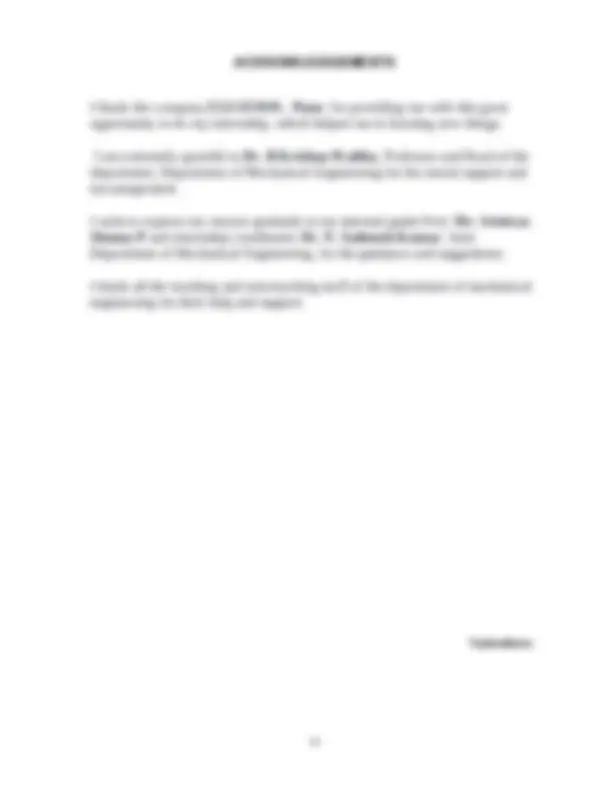
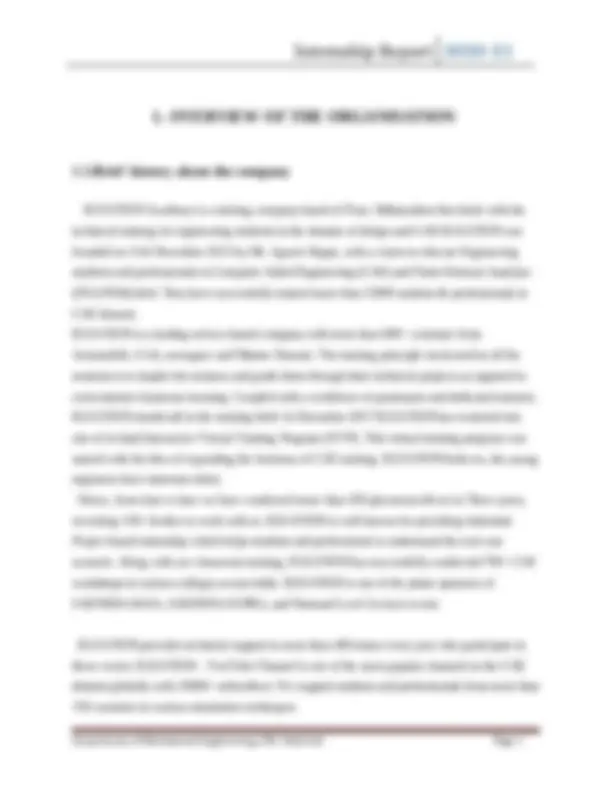
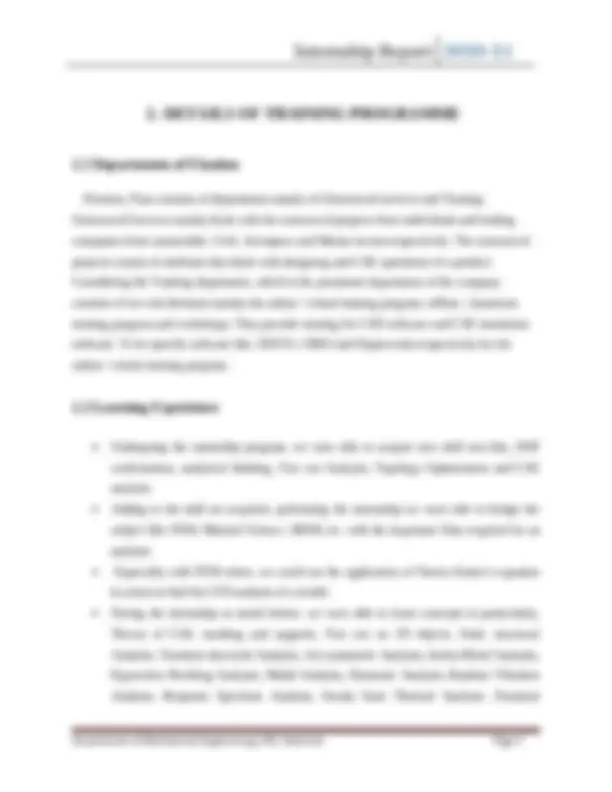

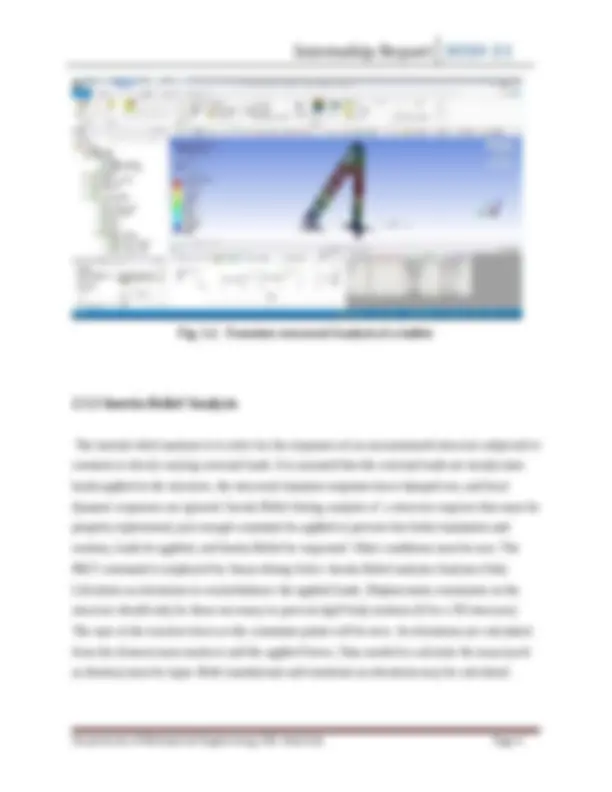
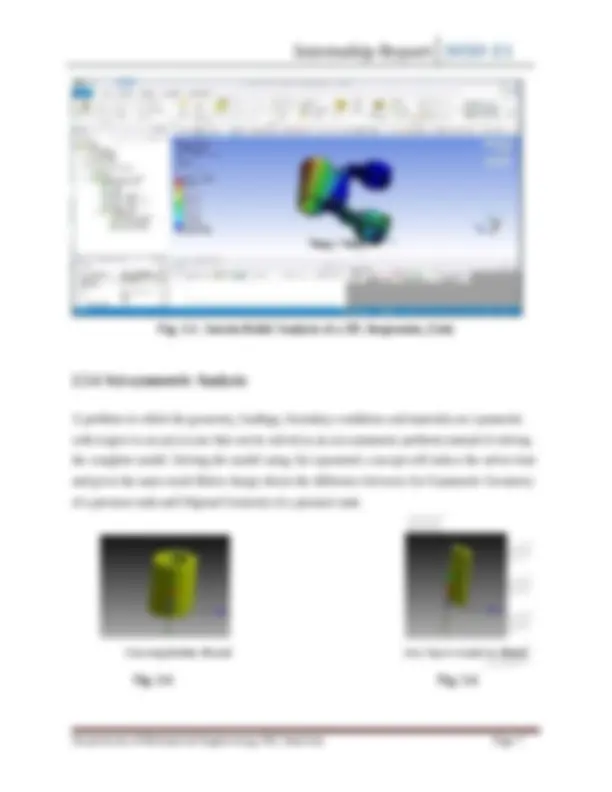
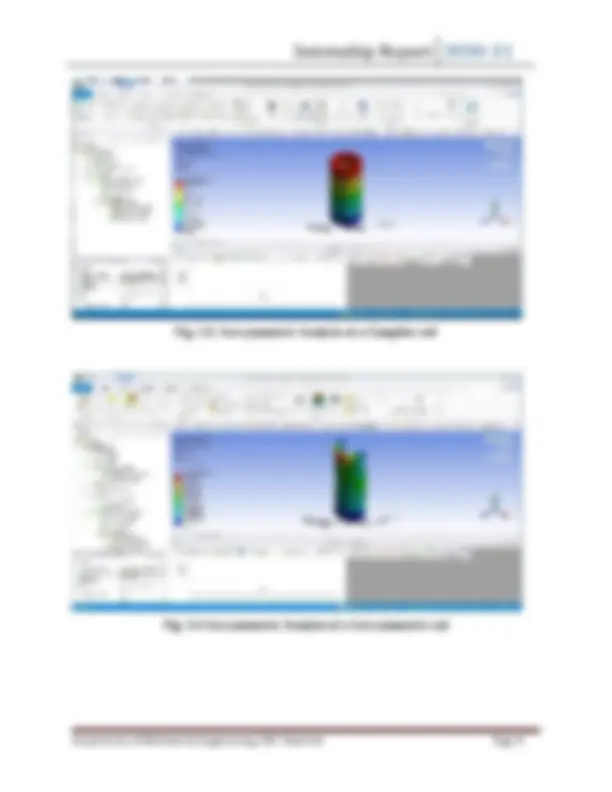
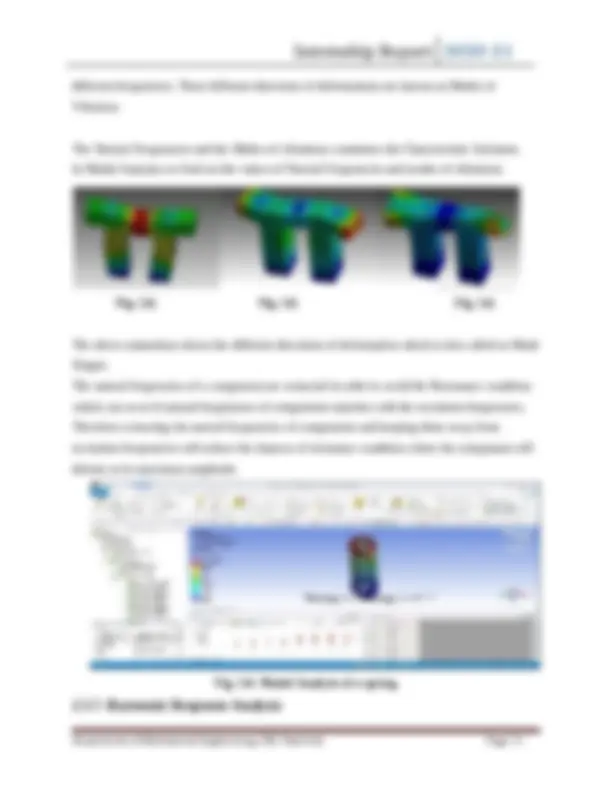
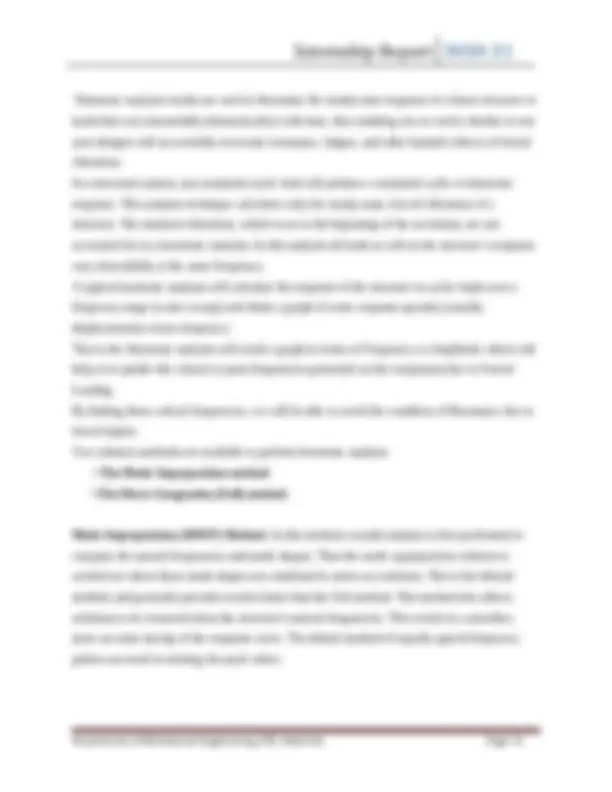
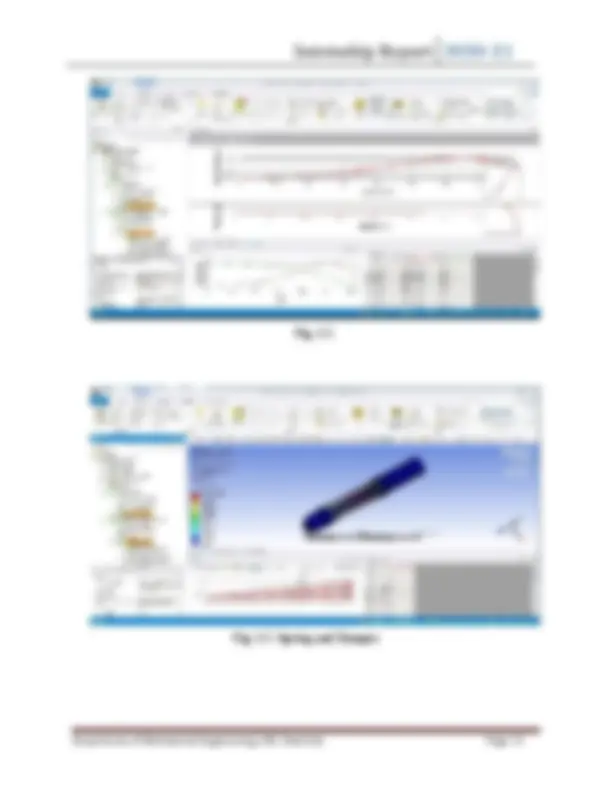
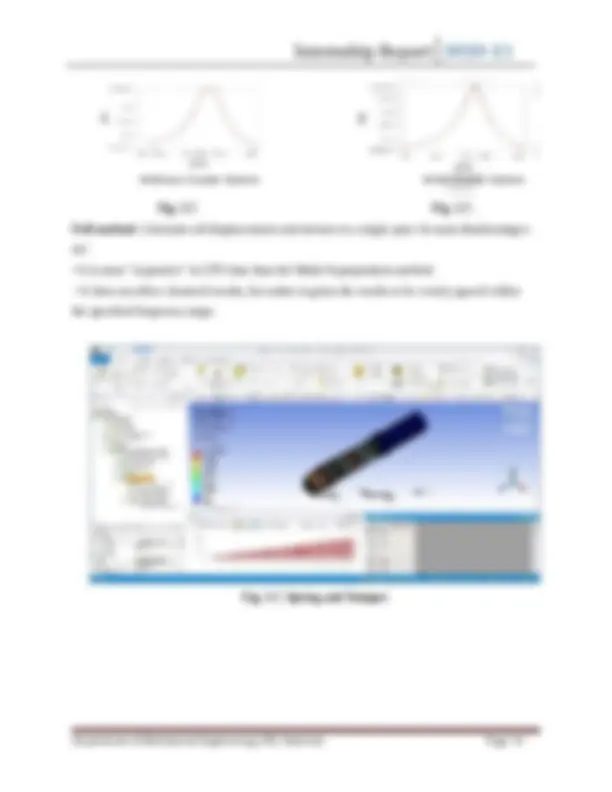
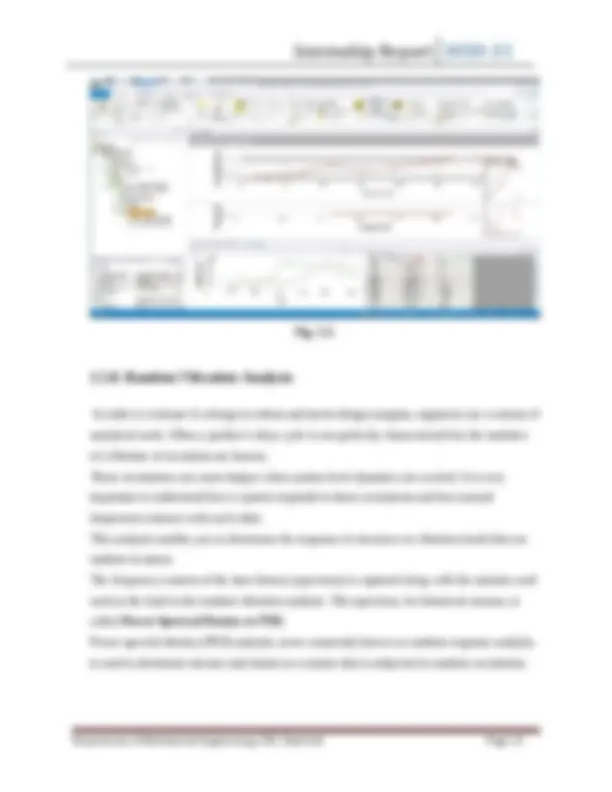
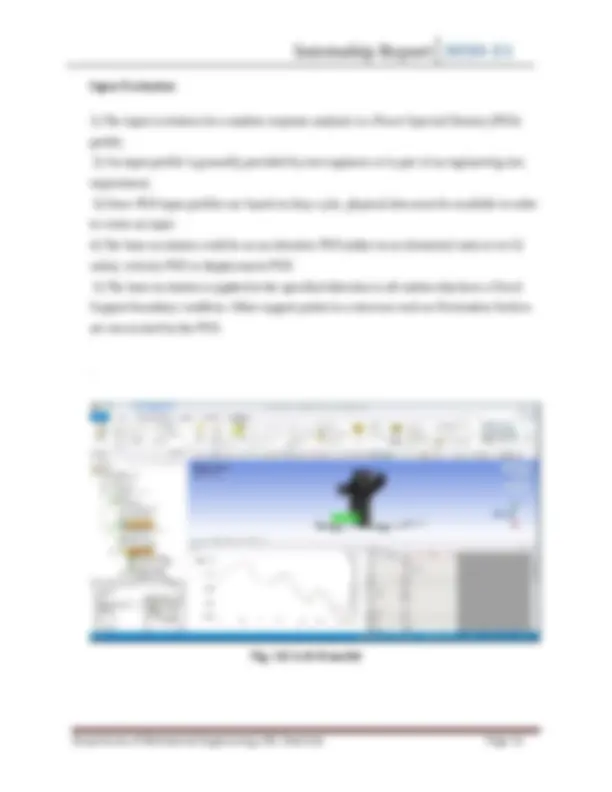
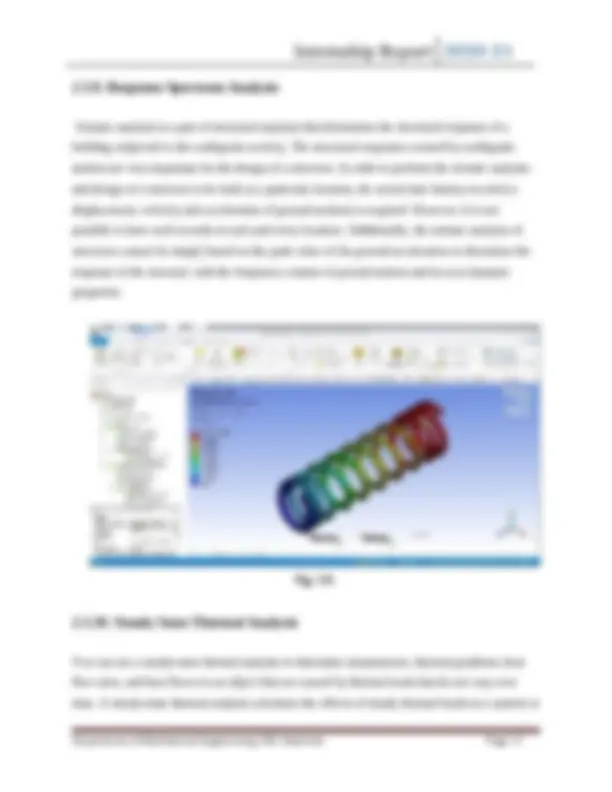
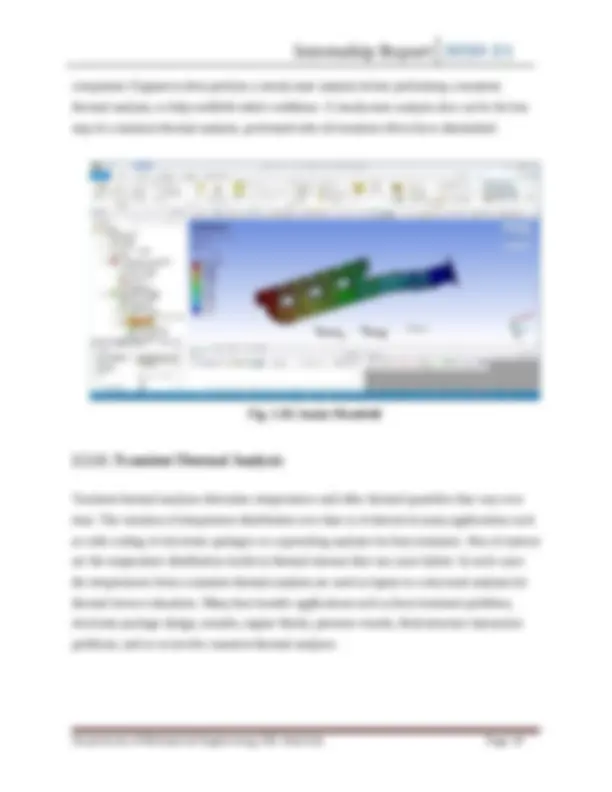
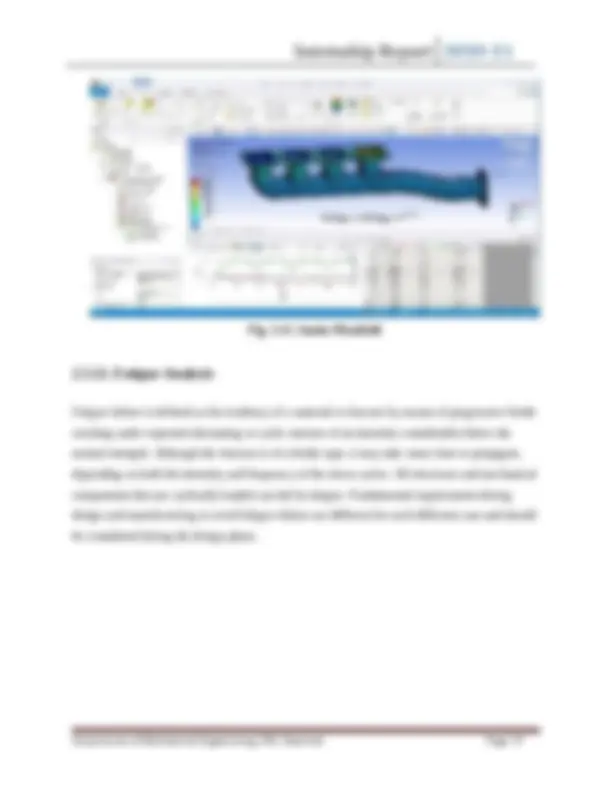
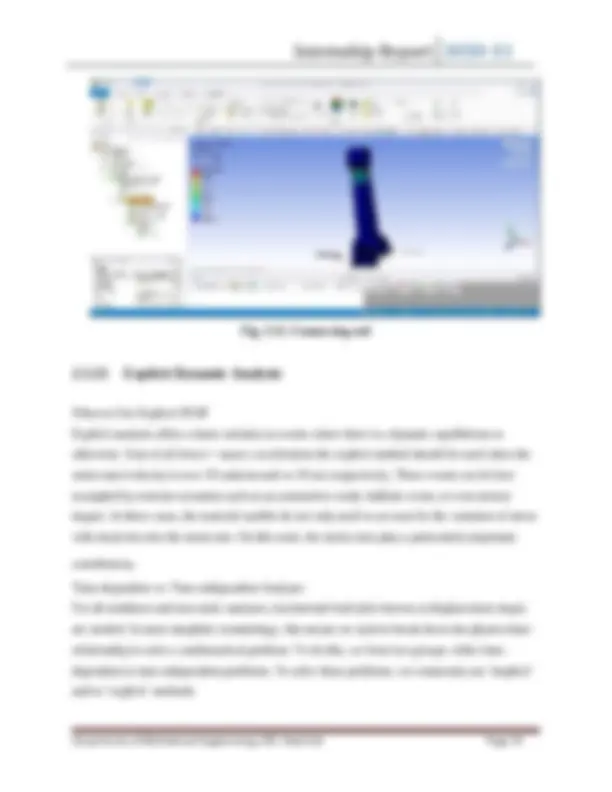
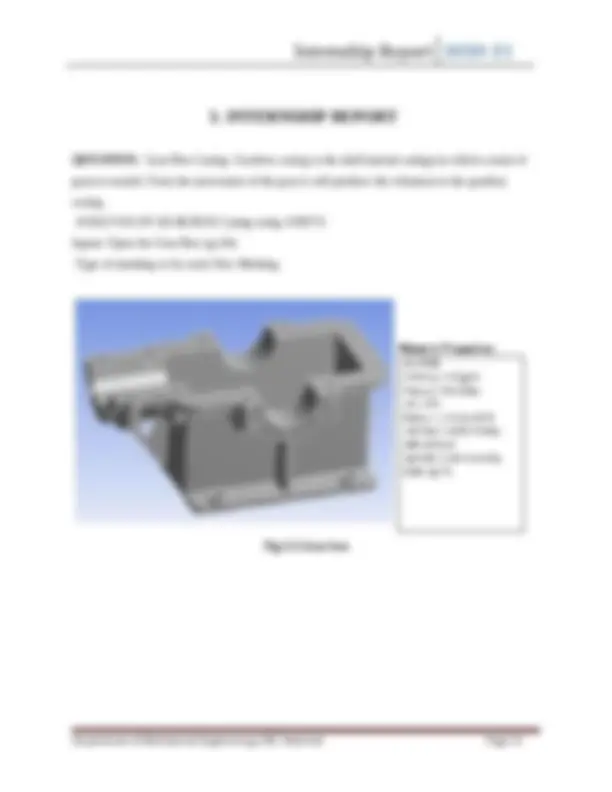
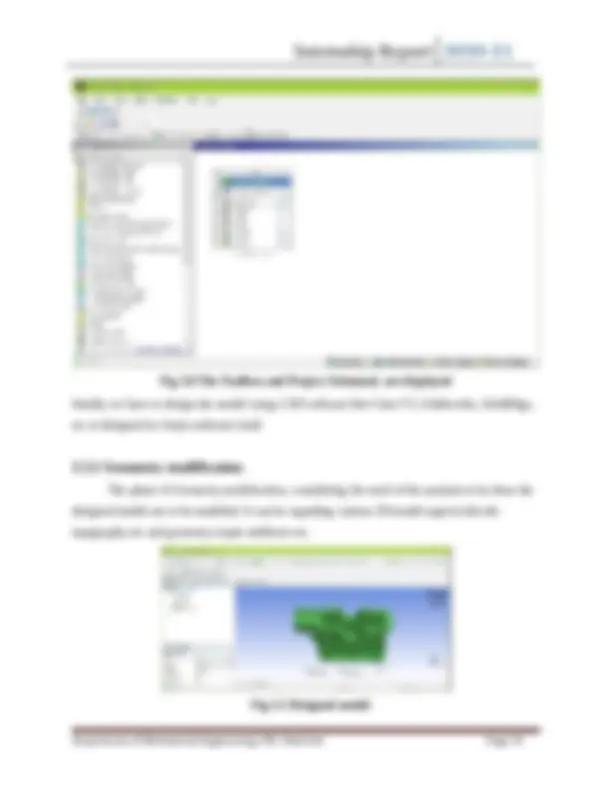
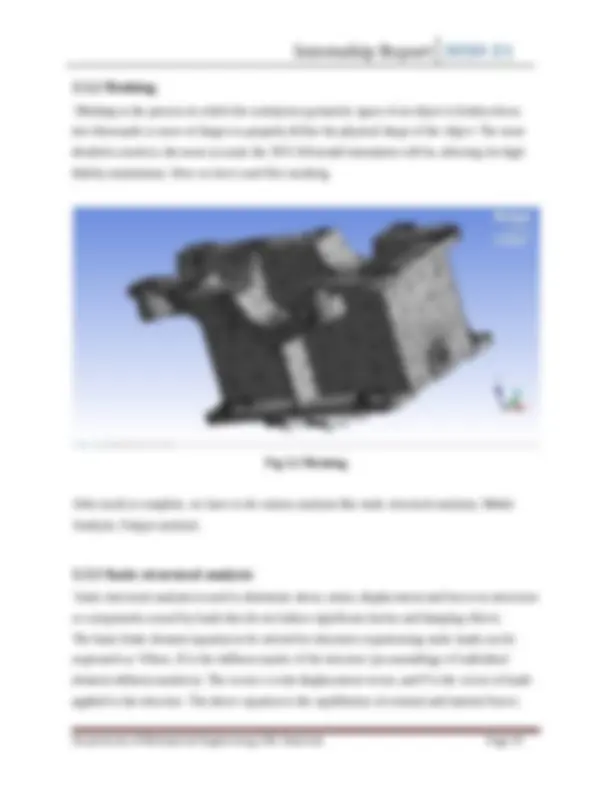
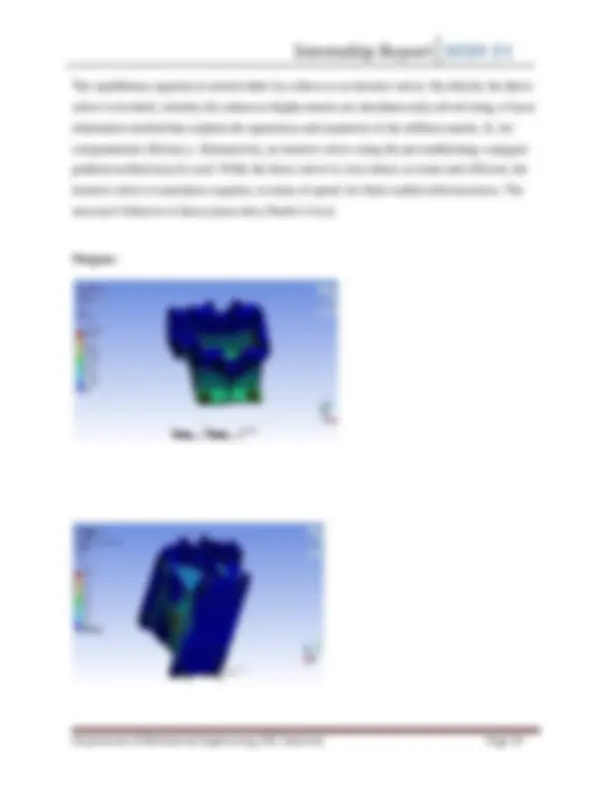
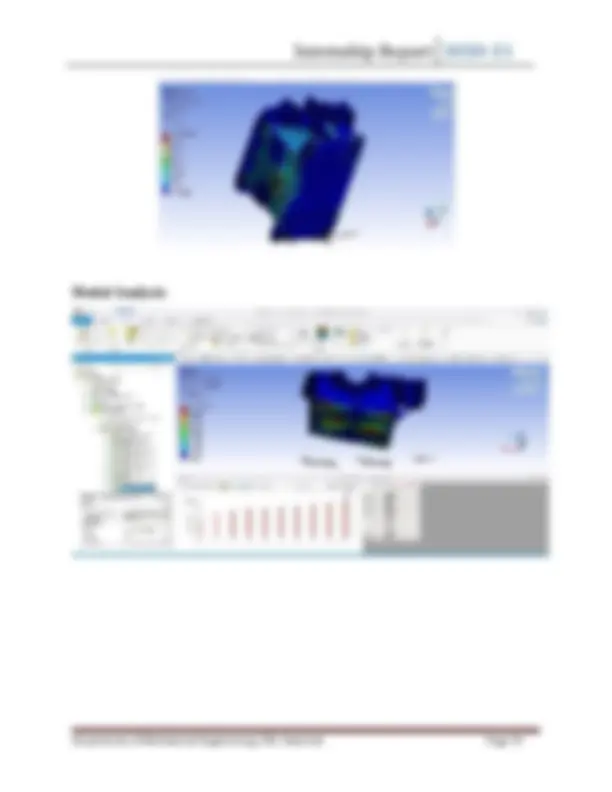
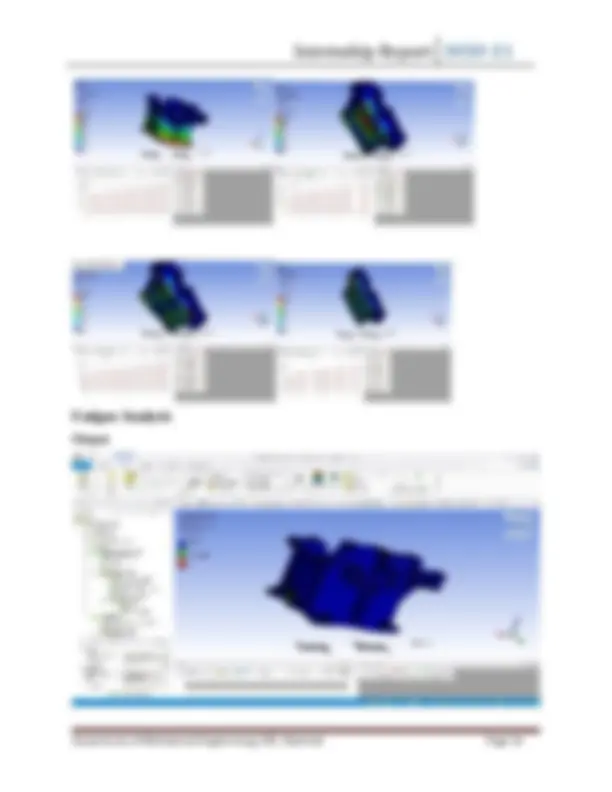
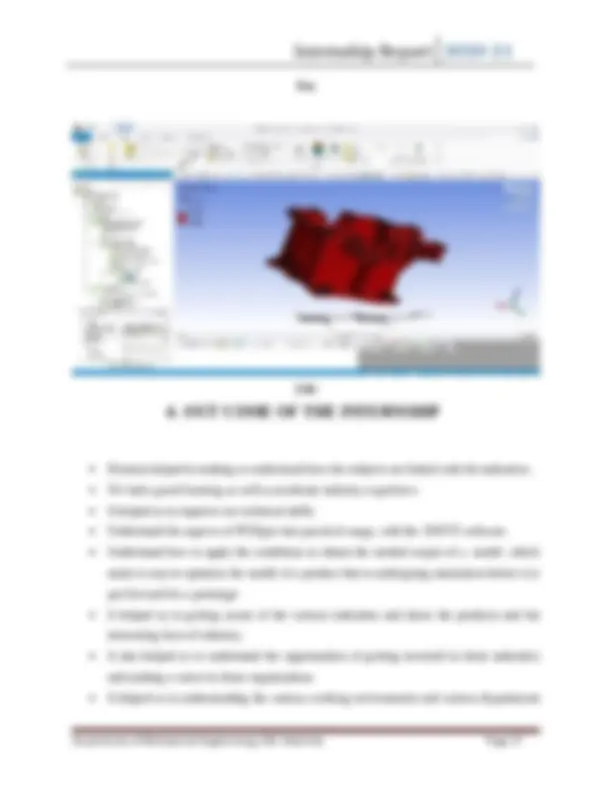
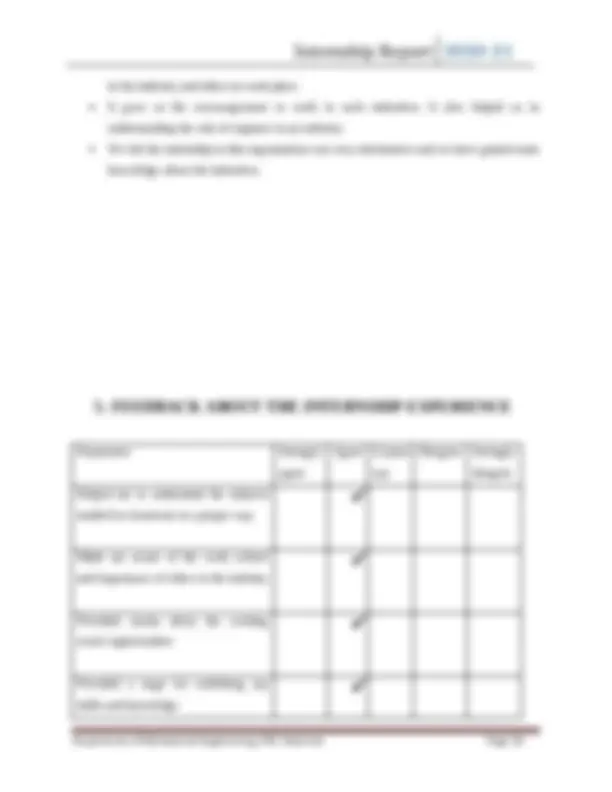
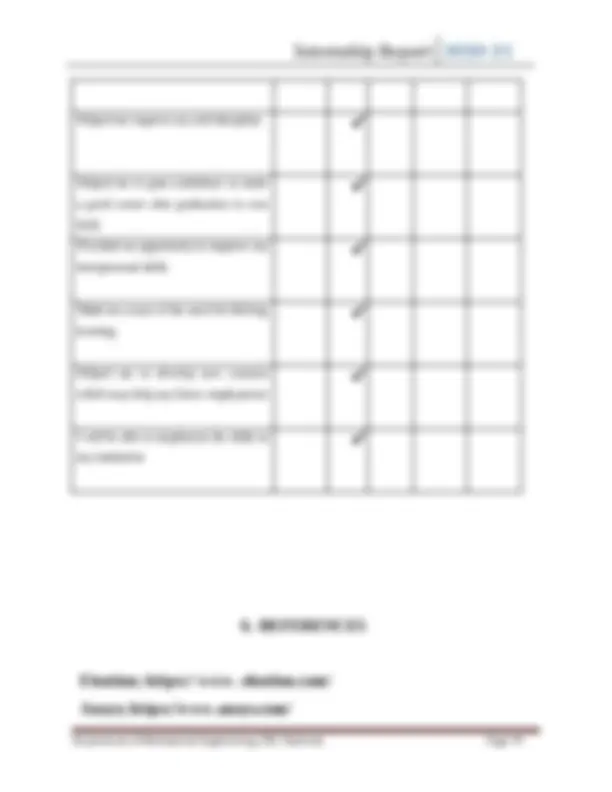
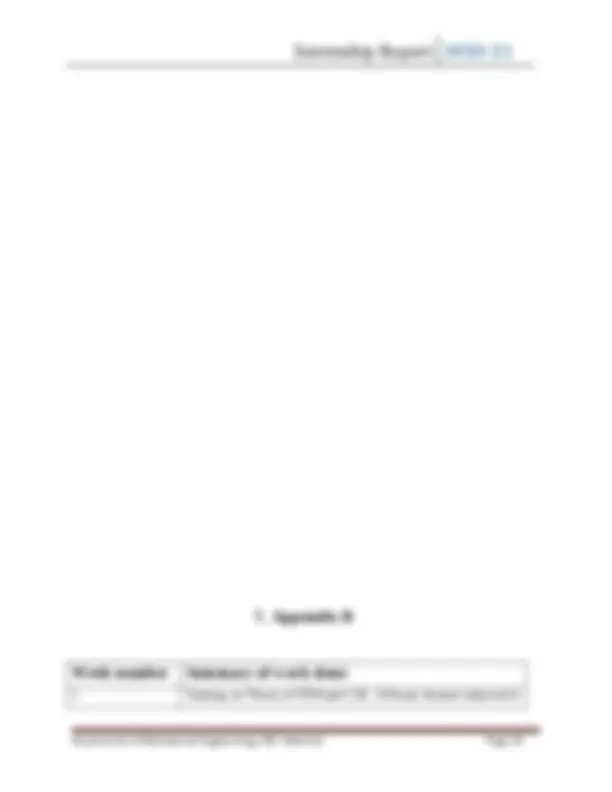
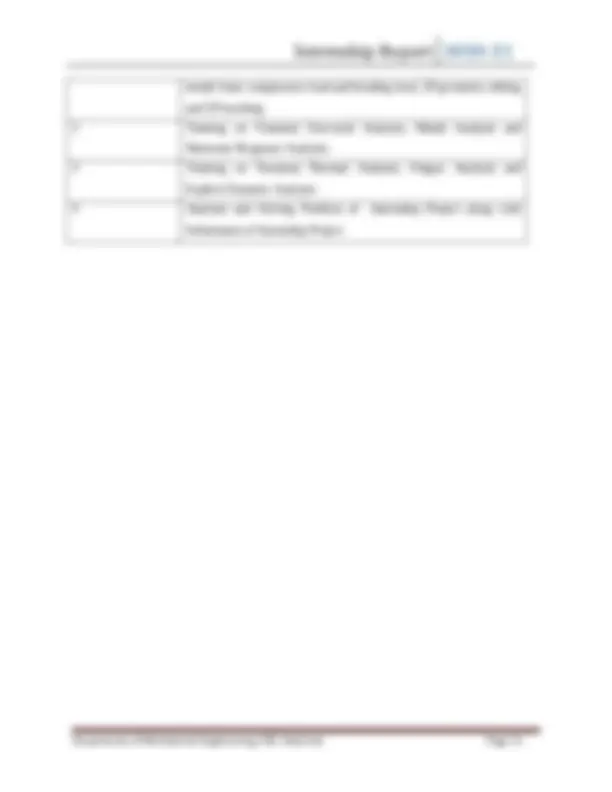
Study with the several resources on Docsity
Earn points by helping other students or get them with a premium plan
Prepare for your exams
Study with the several resources on Docsity
Earn points to download
Earn points by helping other students or get them with a premium plan
Community
Ask the community for help and clear up your study doubts
Discover the best universities in your country according to Docsity users
Free resources
Download our free guides on studying techniques, anxiety management strategies, and thesis advice from Docsity tutors
It is a internship report on the eleation
Typology: Study Guides, Projects, Research
1 / 38
This page cannot be seen from the preview
Don't miss anything!
On special offer
Submitted for the award of the degree of
By
Canara Engineering College Bantwal – 574219, Karnataka, India. 2021-
Submitted for the award of the degree of
By
Canara Engineering College Bantwal – 574219, Karnataka, India.
i
iii
Yashodhara iv
vi
Internship Report 2020-
1. OVERVIEW OF THE ORGANISATION
ELEATION Academy is a training company based of Pune, Maharashtra that deals with the technical training for engineering students in the domain of design and CAE.ELEATION was founded on 11th November 2015 by Mr. Apoorv Bapat, with a vision to educate Engineering students and professionals in Computer Aided Engineering (CAE) and Finite Element Analysis (FEA/FEM) field. They have successfully trained more than 15000 students & professionals in CAE domain. ELEATION is a leading service-based company with more than 600+ customer from Automobile, Civil, aerospace and Marine Domain. The training principle inculcated in all the sessions is to inspire the trainees and guide them through their technical projects as opposed to conventional classroom learning. Coupled with a workforce of passionate and dedicated trainers, ELEATION stands tall in the training field. In December 2017 ELEATION has ventured into one of its kind Interactive Virtual Training Program (IVTP). This virtual training program was started with the idea of expanding the horizons of CAE training. ELEATION believes, the young engineers have immense talent. Hence, from time to time we have conducted more than 450 placement drives in Three years, recruiting 150+ fresher to work with us. ELEATION is well known for providing Industrial Project based internship which helps students and professional to understand the real case scenario. Along with our classroom training, ELEATION has successfully conducted 700+ CAE workshops in various colleges across India. ELEATION is one of the prime sponsors of SAEINDIA BAJA, SAEINDIA SUPRA, and National Level Go-kart events. ELEATION provides technical support to more than 400 teams every year who participate in these events. ELEATION – YouTube Channel is one of the most popular channels in the CAE domain globally with 10000+ subscribers. We support students and professionals from more than 150 countries in various simulation techniques Department of Mechanical Engineering, CEC, Bantwal. Page 1
Internship Report 2020- Thermal Analysis ,Fatigue Analysis ,Explicit Dynamic Analysis and Computational Fluid Dynamics (CFD).
Engineering simulation software “Ansys” was founded by software engineer John Swanson.This was developed in a range of computer-aided engineering (CAE) Products, it is perhaps best known for its ANSYS mechanical and ANSYS multi-physics products.Ansys mechanical and ANSYS multi-physics software are non exportable analysis tools, so these cannot be used without a licence and also the software certain minimum requirement for executing.These are general purpose finite element modeling packages for numerically solving mechanical problems, including static/dynamic structural analysis both linear/non linear, heat transfer and fluid problems. 2.4 Workflow Preprocessing Workflow Department of Mechanical Engineering, CEC, Bantwal. Page 3
Internship Report 2020-
Analysis can be defined as a process of analyzing a structure to the externally applied loads like Pressure, Force and Temperature. And with Ansys simulation software providing 14 specific types of analysis as follows: Static structural Analysis Transient structural Analysis Axi-symmetric Analysis Inertia Relief Analysis Eigenvalue Buckling Analysis Modal Analysis Harmonic Analysis Random Vibration Analysis Response Spectrum Analysis Steady State Thermal Analysis Transient Thermal Analysis Fatigue Analysis Explicit Dynamic Analysis
A static structural analysis determines the displacements, stresses, strains, and forces in structures or components caused by loads that do not induce significant inertia and damping effects. Steady loading and response conditions are assumed; that is, the loads and the structure’s response are assumed to vary slowly with respect to time. A static structural load can be performed using the ANSYS. Department of Mechanical Engineering, CEC, Bantwal. Page 4
Internship Report 2020- Fig. 5.2. Transient structural Analysis of a ladder
The inertial relief analysis is to solve for the responses of an unconstrained structure subjected to constant or slowly varying external loads. It is assumed that the external loads are steady-state loads applied to the structure, the structural transient responses have damped out, and local dynamic responses are ignored. Inertia Relief during analysis of a structure requires that mass be properly represented, just enough constraint be applied to prevent free body translation and rotation, loads be applied, and Inertia Relief be requested. Other conditions must be met. The IRLF command is employed by Ansys during Solve. Inertia Relief analysis Analyses Only Calculates accelerations to counterbalance the applied loads. Displacement constraints on the structure should only be those necessary to prevent rigid body motions (6 for a 3D structure). The sum of the reaction forces at the constraint points will be zero. Accelerations are calculated from the element mass matrices and the applied forces. Data needed to calculate the mass (such as density) must be input. Both translational and rotational accelerations may be calculated. Department of Mechanical Engineering, CEC, Bantwal. Page 6
Internship Report 2020- Fig. 5.3. Inertia Relief Analysis of a 3D_Suspension_Link
A problem in which the geometry, loadings, boundary conditions and materials are symmetric with respect to an axis is one that can be solved as an axi-symmetric problem instead of solving the complete model. Solving the model using Axi-symmetric concept will reduce the solver time and gives the same result Below Image shows the difference between Axi Symmetric Geometry of a pressure tank and Original Geometry of a pressure tank. Fig. 5.4. Fig. 5.4. Department of Mechanical Engineering, CEC, Bantwal. Page 7
Internship Report 2020-
Buckling is an instability that leads to Structural Failure. When a structure is subjected to compressive axial Loading, buckling may occur. Buckling is characterized by a sudden sideways deflection of a structural member. This may occur even though the stresses that develop in the structure are well below those needed to cause failure of the material of which the structure is composed. As an applied axial load is increased on a member, such as a column, it will ultimately become large enough to cause the member to become unstable and it is said to have buckled. Generally, there is confusion between the terms Tension, Compression, Shearing, Torsion, Bending and buckling. This can be cleared from the below animation, Fig. 5.5. A linear-buckling analysis (also called eigenvalue-based buckling analysis), which is in many ways similar to modal analysis. Linear buckling is the most common type of analysis and is easy to execute. Linear-buckling analysis calculates buckling load magnitudes that cause buckling and associated buckling modes. FEA programs provide calculations of a large number of buckling modes and the associated buckling-load factors (BLF). The BLF is expressed by a number which the applied load must be multiplied by (or divided — depending on the particular FEA package) to obtain the buckling-load magnitude. That means after performing Eigenvalue buckling Analysis software provides buckling load factor (i.e. a number) you have to multiple that number Department of Mechanical Engineering, CEC, Bantwal. Page 9
Internship Report 2020- with the load you have applied on the structure / component / part / assembly to find out at which load the component / structure / part / assembly might buckle. If you know the load and deformation pattern, i.e. at which load the component will buckle and in which direction it is going to buckle then you can decide the criticality of load and damage caused by the buckled component on other components / parts. Fig. 5.5. Eigenvalue Buckling Analysis of a Spring
Certain properties of a component does not change with respect to the changes in the Initial conditions of the component. Such properties can be termed as Characteristics Solutions. They are;
Internship Report 2020- Harmonic analysis results are used to determine the steady-state response of a linear structure to loads that vary sinusoidally (harmonically) with time, thus enabling you to verify whether or not your designs will successfully overcome resonance, fatigue, and other harmful effects of forced vibrations. In a structural system, any sustained cyclic load will produce a sustained cyclic or harmonic response. This analysis technique calculates only the steady-state, forced vibrations of a structure. The transient vibrations, which occur at the beginning of the excitation, are not accounted for in a harmonic analysis. In this analysis all loads as well as the structure’s response vary sinusoidally at the same frequency. A typical harmonic analysis will calculate the response of the structure to cyclic loads over a frequency range (a sine sweep) and obtain a graph of some response quantity (usually displacements) versus frequency. That is the Harmonic analysis will result a graph in terms of Frequency vs Amplitude which will help us to predict the critical or peak frequencies generated on the component due to Forced Loading. By finding these critical frequencies, we will be able to avoid the condition of Resonance due to forced inputs. Two solution methods are available to perform harmonic analysis:
**- The Mode-Superposition method
Internship Report 2020- Fig. 5.7. Fig. 5.7. Spring and Damper Department of Mechanical Engineering, CEC, Bantwal. Page 13