
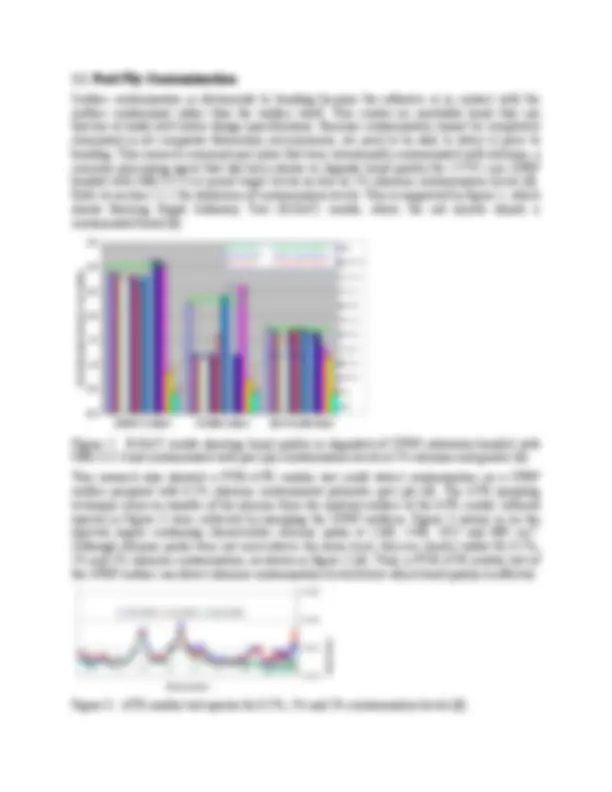
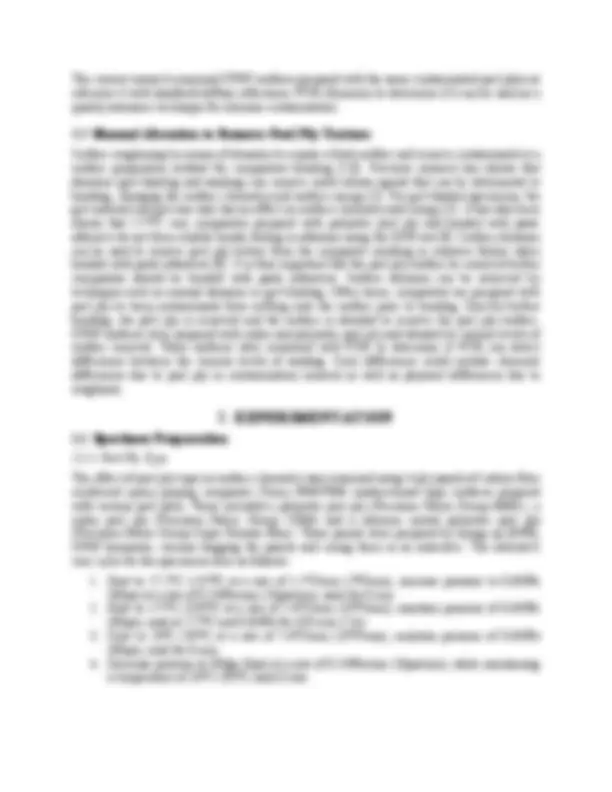
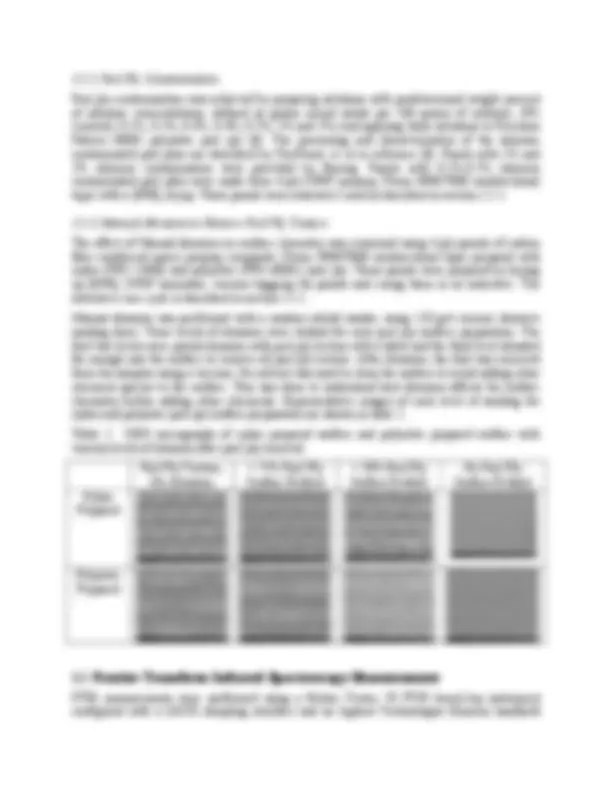
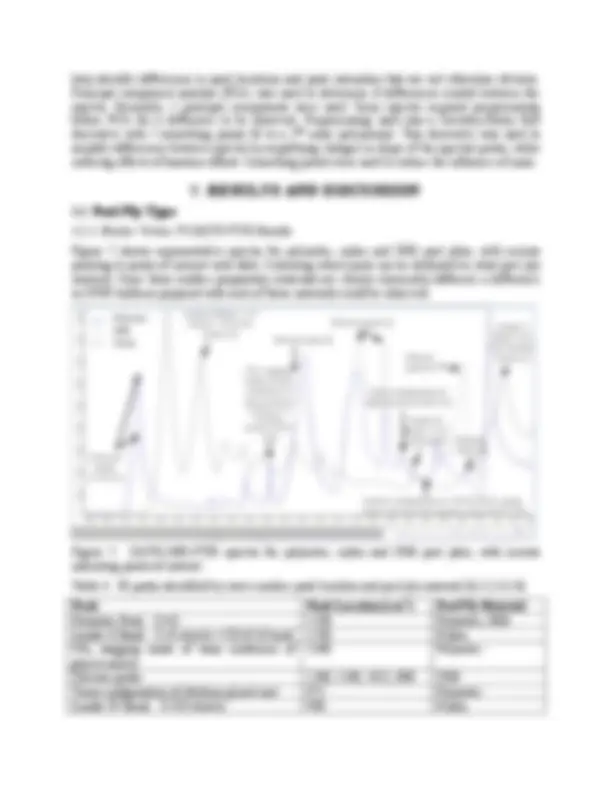
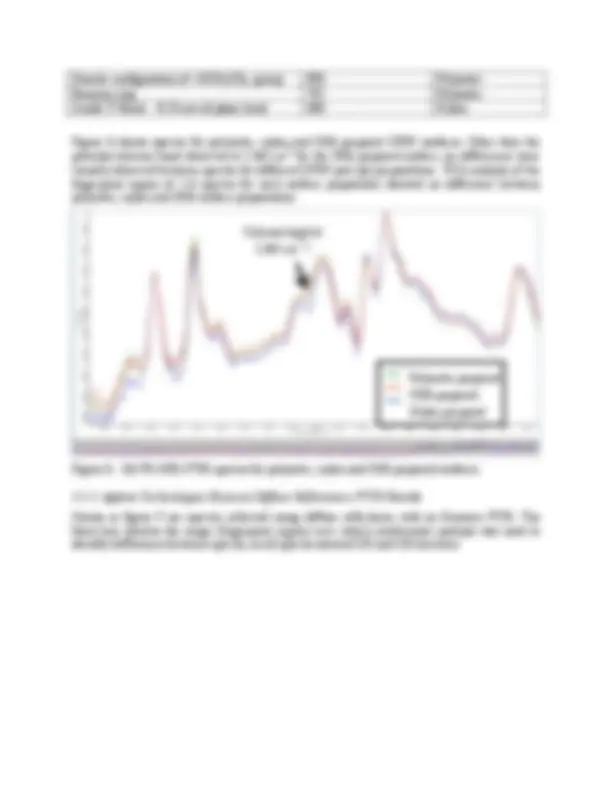
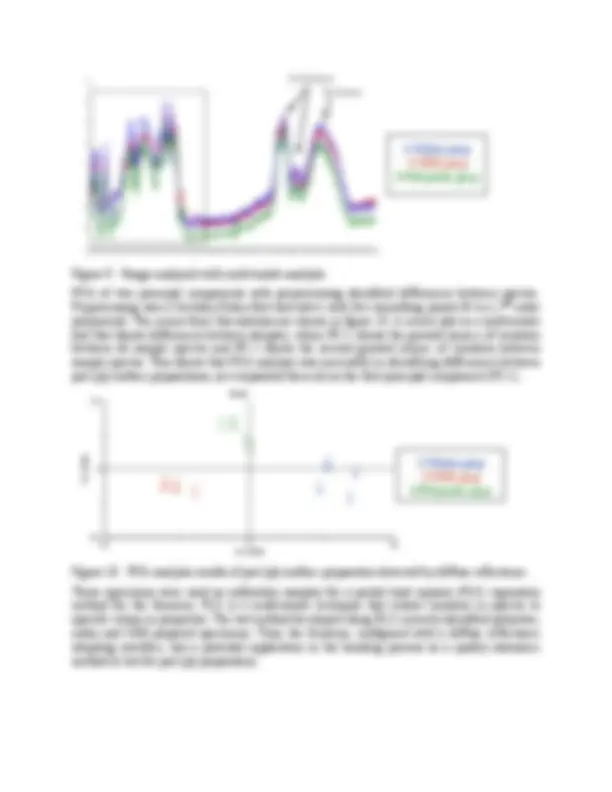
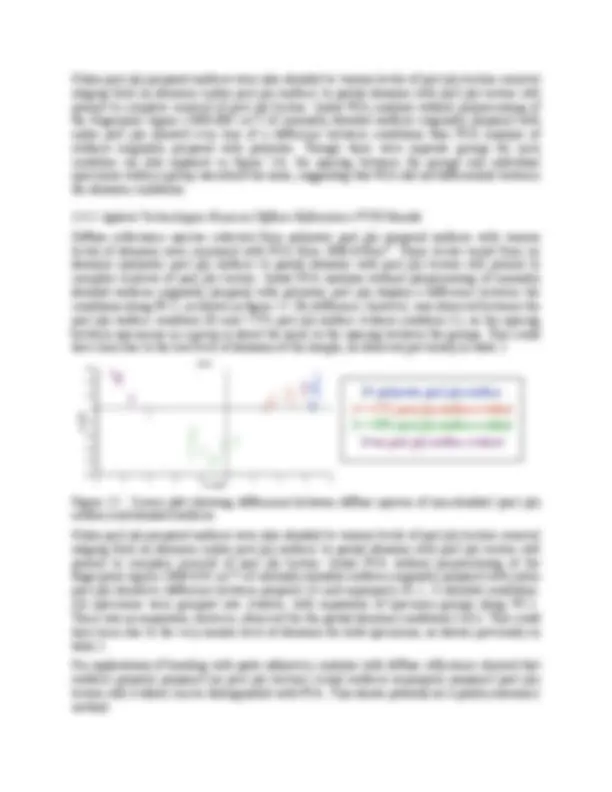
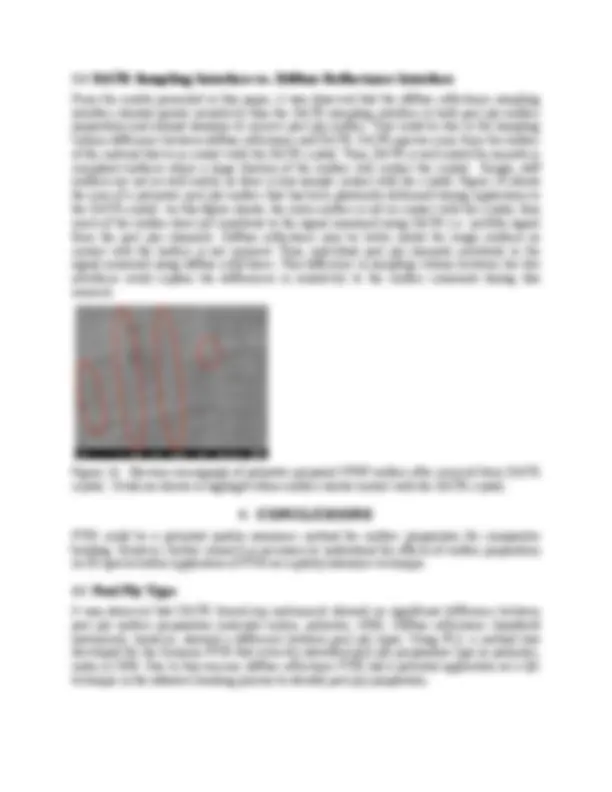
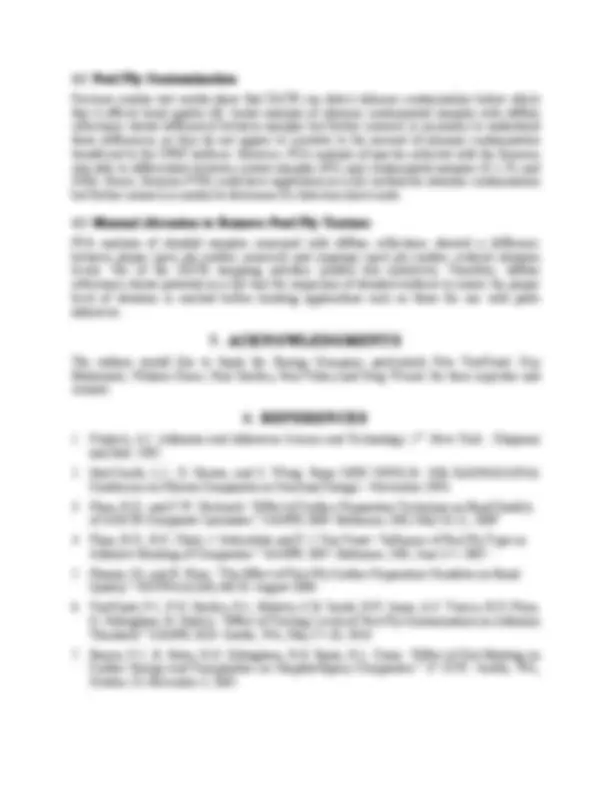
Study with the several resources on Docsity
Earn points by helping other students or get them with a premium plan
Prepare for your exams
Study with the several resources on Docsity
Earn points to download
Earn points by helping other students or get them with a premium plan
Community
Ask the community for help and clear up your study doubts
Discover the best universities in your country according to Docsity users
Free resources
Download our free guides on studying techniques, anxiety management strategies, and thesis advice from Docsity tutors
This research evaluates Fourier transform infrared spectroscopy measurement methods as a potential technique to monitor surface preparation processes for adhesive bonding of composite substrates. The study examines the capabilities of FTIR as a potential technique for surface preparation inspection. the sensitivity of both devices and references surface preparation and bond quality data. The paper also discusses processing conditions that can affect infrared spectroscopy measurements.
Typology: Study notes
1 / 16
This page cannot be seen from the preview
Don't miss anything!
Ashley C. Tracey, Brian D. Flinn University of Washington Materials Science and Engineering Department 302 Roberts Hall, Box 352120 Seattle, WA 98195 - 2120
The purpose of this research is to evaluate Fourier transform infrared spectroscopy measurement methods (FTIR) as a potential technique to monitor surface preparation processes for adhesive bonding of composite substrates. The recent availability of handheld FTIR instruments enables application of infrared spectroscopy in manufacturing or repair environments. This motivates research to understand the capabilities of FTIR as a potential technique for surface preparation inspection. Infrared spectroscopy can be used to identify chemical bonds on a composite surface prepared for secondary bonding. This information can help understand one requirement of adhesion: the formation of primary chemical bonds between the adherend and adhesive as well as the identification of contaminants. Mid-infrared spectroscopy measurements are made using a bench-top infrared spectrometer (Bruker Vertex 70) and a handheld infrared spectrometer (Agilent Technologies Exoscan). The bench-top FTIR is configured with a single-bounce diamond crystal attenuated total reflectance (DATR) sampling interface. The handheld FTIR uses a diffuse reflectance sampling interface. The materials examined are 177 °C cure carbon fiber reinforced epoxy laminates prepared with various surface preparation methods, including peel ply preparation and manual abrasion. Infrared spectroscopy measurements characterized surfaces with various surface preparations and contaminants. The sensitivity of both devices will be discussed and referenced to surface preparation and bond quality data.
With the advent of the Boeing 787 and Airbus A350, adhesive bonds are now being used extensively for large aerospace structures. In comparison to mechanical fasteners, bonding reduces weight, eliminates stress concentrations and eliminates the need for sealants to protect against environmental damage. The purpose of this research was to evaluate infrared spectroscopy techniques as a possible inspection method for pre-bond surface preparations. The most important step in the formation of adhesive bonds is surface preparation to create chemically active surfaces that maximize bond strength and to prevent or remove contaminants that can adversely affect bonding. Adhesive bonding predominantly depends on the formation of primary chemical bonds and less on mechanical factors, thus surfaces must be properly prepared for formation of strong adhesive bonds [1, 2]. The surface preparation methods of focus for this research were peel ply and manual abrasion with use of a random orbital sander. A peel ply is a polymer fabric, such as polyester or nylon. It
is the last layer applied to a composite part before cure and is removed directly before bonding. Figure 1 displays the removal of a peel ply and the resulting surface. Infrared spectroscopy techniques examined used the Bruker Vertex 70, a desktop instrument, and the Agilent Technologies Exoscan, a handheld device. The Vertex 70, configured with attenuated total reflectance (ATR), was used to measure the surface chemistry of composite substrates for comparison with the Exoscan, configured with diffuse reflectance. Surface characterization is important in the aerospace industry, where adhesive bonding of composites is desired, because it can aide in the understanding of adhesion. This paper will discuss processing conditions that can affect infrared spectroscopy measurements: peel ply type, peel ply contamination and manual abrasion of peel ply surfaces. Figure 1: Removal of peel ply from a carbon fiber reinforced epoxy composite (CFRP). 1.1 Peel Ply Type Traditional peel ply surface preparation is material system (prepreg and adhesive) specific [3, 4]. Certain peel ply, composite and adhesive systems result in strong bonds whereas others result in weak bonds. For example, previous research shows that polyester peel ply prepared 177°C cure CFRP shows cohesive failure and a GIC = 812±35 J/m 2 when bonded with MB1515-3 adhesive [5]. However, when this same CFRP material is prepared with nylon peel ply and bonded with MB1515-3, adhesion failure is observed with resulting GIC = 122±15 J/m^2 [5]. Similarly, when this CFRP is prepared with Super Release Blue (SRB) release ply (polyester peel ply coated with siloxane) and bonded with MB1515-3, adhesion failure and GIC < 94 J/m^2 are observed [5]. Table 1 shows the failure modes for the combinations of substrate, surface preparation and adhesive discussed [5]. The mode I strain energy release rates (GIC) and failure modes were determined using Mode I Double Cantilever Beam (DCB) testing [5]. Because different peel ply fabrics may appear visually very similar, we need to be able to detect the peel ply preparation material prior to bonding. One aspect of this research examined common peel ply materials (polyester and nylon) used for bonding, as well as a release ply (SRB) known to cause poor adhesion. Table 1: DCB fracture surfaces of peel ply surfaces bonded with MB1515-3 adhesive [5]. Polyester Prepared Nylon Prepared SRB Prepared Failure Mode Cohesive Adhesion Adhesion GIC 812±35 J/m^2 122±15 J/m^2 < 94 J/m^2 Table 2 Fracture surfaces of tested laminates (Sample Width = 12.7 mm) Polyester Prepared Nylon Prepared SRB Prepared AF Failure Mode Cohesive Cohesive & Interlaminar Adhesion MB1515- 3 Failure Mode Cohesive Adhesion Adhesion The measure of bond quality for our purposes is the critical strain energy release rate of the bonded laminate, determined by Mode I DCB Testing. As can be seen in Figure 8 , surfaces prepared with SRB displayed consistently poor bonding. Samples prepared with polyester peel ply had the best consistent bond quality. A dramatic change in fracture energy was observed when nylon-prepared surfaces were bonded with MB1515- 3 rather than AF555. The fracture mode also changed from cohesive (AF555) to adhesion (MB1515- 3 ) as shown in Table 2. The mode of failure (cohesive/interlaminar) seen in samples prepared with Table 2 Fracture surfaces of tested laminates (Sample Width = 12.7 mm) Polyester Prepared Nylon Prepared SRB Prepared AF Failure Mode Cohesive Cohesive & Interlaminar Adhesion MB1515- 3 Failure Mode Cohesive Adhesion Adhesion The measure of bond quality for our purposes is the critical strain energy release rate of the bonded laminate, determined by Mode I DCB Testing. As can be seen in Figure 8 , surfaces prepared with SRB displayed consistently poor bonding. Samples prepared with polyester peel ply had the best consistent bond quality. A dramatic change in fracture energy was observed when nylon-prepared surfaces were bonded with MB1515- 3 rather than AF555. The fracture mode also changed from cohesive (AF555) to adhesion (MB1515- 3 ) as shown in Table 2. The mode of failure (cohesive/interlaminar) seen in samples prepared with polyester peel ply and nylon peel ply bonded with AF555 is more desirable than the adhesion Table 2 Fracture surfaces of tested laminates (Sample Width = 12.7 mm) Polyester Prepared Nylon Prepared SRB Prepared AF Failure Mode Cohesive Cohesive & Interlaminar Adhesion MB1515- 3 Failure Mode Cohesive Adhesion Adhesion The measure of bond quality for our purposes is the critical strain energy release rate of the bonded laminate, determined by Mode I DCB Testing. As can be seen in Figure 8 , surfaces prepared with SRB displayed consistently poor bonding. Samples prepared with polyester peel ply had the best consistent bond quality. A dramatic change in fracture energy was observed when nylon-prepared surfaces were bonded with MB1515- 3 rather than AF555. The fracture mode also changed from cohesive (AF555) to adhesion (MB1515- 3 ) as shown in Table 2. The mode of failure (cohesive/interlaminar) seen in samples prepared with polyester peel ply and nylon peel ply bonded with AF555 is more desirable than the adhesion
The current research examined CFRP surfaces prepared with the same contaminated peel plies as reference 6 with handheld diffuse-reflectance FTIR (Exoscan) to determine if it can be used as a quality assurance technique for siloxane contamination. 1.3 Manual Abrasion to Remove Peel Ply Texture Surface roughening by means of abrasion to expose a fresh surface and remove contaminants is a surface preparation method for composites bonding [7,8]. Previous research has shown that abrasion (grit blasting and sanding) can remove mold release agents that can be detrimental to bonding, changing the surface chemistry and surface energy [7]. For grit blasted specimens, the grit material and grit size also has an affect on surface chemistry and energy [7]. It has also been shown that 177°C cure composites prepared with polyester peel ply and bonded with paste adhesive do not form reliable bonds, failing in adhesion using the DCB test [9]. Surface abrasion can be used to remove peel ply texture from the composite resulting in cohesive failure when bonded with paste adhesives [9]. It is thus important that the peel ply surface be removed before composites should be bonded with paste adhesives. Surface abrasion can be achieved by techniques such as manual abrasion or grit blasting. Often times, composites are prepared with peel ply to keep contaminants from settling onto the surface prior to bonding. Directly before bonding, the peel ply is removed and the surface is abraded to remove the peel ply surface. CFRP surfaces were prepared with nylon and polyester peel ply and abraded to various levels of surface removal. These surfaces were measured with FTIR to determine if FTIR can detect differences between the various levels of sanding. Such differences could include chemical differences due to peel ply or contamination removal as well as physical differences due to roughness.
2.1 Specimen Preparation 2.1.1 Peel Ply Type The effect of peel ply type on surface chemistry was examined using 4-ply panels of carbon fiber reinforced epoxy prepreg composite (Toray 3900/T800 unidirectional tape) surfaces prepared with various peel plies. These included a polyester peel ply (Precision Fabric Group 60001), a nylon peel ply (Precision Fabric Group 52006) and a siloxane coated polyester peel ply (Precision Fabric Group Super Release Blue). These panels were prepared by laying up [0/90]s CFRP laminates, vacuum bagging the panels and curing them in an autoclave. The autoclave cure cycle for the specimens were as follows:
2.1.2 Peel Ply Contamination Peel ply contamination was achieved by preparing solutions with predetermined weight percent of siloxane concentrations, defined as grams mixed solids per 100 grams of solution, (0% (control), 0.1%, 0.2%, 0.3%, 0.4%, 0.5%, 1% and 2%) and applying these solutions to Precision Fabrics 60001 polyester peel ply [6]. The processing and characterization of the siloxane contaminated peel plies are described by VanVoast, et. al in reference [6]. Panels with 1% and 2% siloxane contamination were provided by Boeing. Panels with 0.1%-0.5% siloxane contaminated peel plies were made from 4-ply CFRP prepreg (Toray 3900/T800 unidirectional tape) with a [0/90]s layup. These panels were autoclave cured as described in section 2.1.1. 2.1.3 Manual Abrasion to Remove Peel Ply Texture The effect of Manual abrasion on surface chemistry was examined using 4-ply panels of carbon fiber reinforced epoxy prepreg composite (Toray 3900/T800 unidirectional tape) prepared with nylon (PFG 52006) and polyester (PFG 60001) peel ply. These panels were prepared by laying up [0/90]s CFRP laminates, vacuum bagging the panels and curing them in an autoclave. The autoclave cure cycle is described in section 2.1.1. Manual abrasion was performed with a random orbital sander, using 120 grit ceramic abrasive sanding discs. Three levels of abrasion were studied for each peel ply surface preparation. The first two levels were partial abrasion with peel ply texture still evident and the third level abraded far enough into the surface to remove all peel ply texture. After abrasion, the dust was removed from the samples using a vacuum. No solvent was used to clean the surface to avoid adding other chemical species to the surface. This was done to understand how abrasion affects the surface chemistry before adding other chemicals. Representative images of each level of sanding for nylon and polyester peel ply surface preparation are shown in table 2. Table 2 : SEM micrographs of nylon prepared surface and polyester prepared surface with various levels of abrasion after peel ply removal. Peel Ply Texture, No Abrasion
75% Peel Ply Surface Evident < 50% Peel Ply Surface Evident No Peel Ply Surface Evident Nylon Prepared Polyester Prepared 2.2 Fourier Transform Infrared Spectroscopy Measurements FTIR measurements were performed using a Bruker Vertex 70 FTIR bench-top instrument configured with a DATR sampling interface and an Agilent Technologies Exoscan handheld
background spectrum was collected before each sample spectrum. The background was then ratioed to the specimen spectra. Data collected was 90 scans with 16 cm
help identify differences in peak locations and peak intensities that are not otherwise obvious. Principal component analysis (PCA) was used to determine if differences existed between the spectra. Generally, 2 principal components were used. Some spectra required preprocessing before PCA for a difference to be observed. Preprocessing used was a Savitsky-Golay first derivative with 5 smoothing points fit to a 2nd^ order polynomial. This derivative was used to amplify differences between spectra by amplifying changes in slope of the spectral peaks, while reducing effects of baseline offsets. Smoothing points were used to reduce the influence of noise.
3.1 Peel Ply Type 3.1.1 Bruker Vertex 70 DATR FTIR Results Figure 7 shows representative spectra for polyester, nylon and SRB peel plies, with arrows pointing to peaks of interest with table 3 showing which peak can be attributed to what peel ply material. Since these surface preparation materials are clearly chemically different, a difference in CFRP surfaces prepared with each of these materials could be observed. Figure 7: DATR-MIR-FTIR spectra for polyester, nylon and SRB peel plies, with arrows indicating peaks of interest. Table 3 : IR peaks identified by wave number peak location and peel ply material [6,1 2 ,1 3 ,1 4 ]. Peak Peak Location (cm-^1 ) Peel Ply Material Polyester Peak: C=O 1730 Polyester, SRB Amide II Band: C-N stretch + CO-N-H bend 1530 Nylon CH 2 wagging mode of trans conformer of glycol moiety 1340 Polyester Silicone peaks 1260, 1100, 1022, 800 SRB Trans configuration of ethylene glycol unit 975 Polyester Amide IV Band: C-CO stretch 930 Nylon
Figure 9: Range analyzed with multivariate analysis. PCA of two principal components with preprocessing identified differences between spectra. Preprocessing was a Savitsky-Golay first derivative with five smoothing points fit to a 2nd^ order polynomial. The scores from this analysis are shown in figure 10. A scores plot is a multivariate tool that shows differences between samples, where PC-1 shows the greatest source of variation between all sample spectra and PC-2 shows the second greatest source of variation between sample spectra. This shows that PCA analysis was successful in identifying differences between peel ply surface preparations, as it separated them all on the first principal component (PC-1). Figure 1 0 : PCA analysis results of peel ply surface preparation detected by diffuse reflectance. These specimens were used as calibration samples for a partial least squares (PLS) regression method for the Exoscan. PLS is a multivariate technique that relates variation in spectra to specific values or properties. The test method developed using PLS correctly identified polyester, nylon and SRB prepared specimens. Thus, the Exoscan, configured with a diffuse reflectance sampling interface, has a potential application in the bonding process as a quality assurance method to test for peel ply preparation. 1=Nylon prep 2=SRB prep 3=Polyester prep 1=Nylon prep 2=SRB prep 3=Polyester prep
3.2 Peel Ply Contamination 3.2.1 Hexane Extraction Results Silicone materials have characteristic IR peaks at 800, 1022, 1100 and 1260 cm
Nylon peel ply prepared surfaces were also abraded to various levels of peel ply texture removal ranging from no abrasion (nylon peel ply surface) to partial abrasion with peel ply texture still present to complete removal of peel ply texture. Initial PCA analysis without preprocessing of the fingerprint region (1800-600 cm-^1 ) of manually abraded surfaces originally prepared with nylon peel ply showed even less of a difference between conditions than PCA analysis of surfaces originally prepared with polyester. Though there were separate groups for each condition (as also apparent in figure 14), the spacing between the groups and individual specimens within a group was about the same, suggesting that PCA did not differentiate between the abrasion conditions. 3.3.2 Agilent Technologies Exoscan Diffuse Reflectance FTIR Results Diffuse reflectance spectra collected from polyester peel ply prepared surfaces with various levels of abrasion were examined with PCA from 2000- 65 0cm
3.4 DATR Sampling Interface vs. Diffuse Reflectance Interface From the results presented in this paper, it was observed that the diffuse reflectance sampling interface showed greater sensitivity than the DATR sampling interface to both peel ply surface preparation and manual abrasion to remove peel ply surface. This could be due to the sampling volume difference between diffuse reflectance and DATR. DATR spectra come from the surface of the material that is in contact with the DATR crystal. Thus, DATR is well suited for smooth or compliant surfaces where a large fraction of the surface will contact the crystal. Rough, stiff surfaces are not as well suited, as there is less sample contact with the crystal. Figure 16 shows the area of a polyester peel ply surface that has been plastically deformed during application to the DATR crystal. As this figure shows, the entire surface is not in contact with the crystal, thus much of the surface does not contribute to the signal measured using DATR (i.e. no/little signal from the peel ply channels). Diffuse reflectance may be better suited for rough surfaces as contact with the surface is not required. Thus, individual peel ply channels contribute to the signal measured using diffuse reflectance. This difference in sampling volume between the two interfaces could explain the differences in sensitivity to the surface examined during this research. Figure 16: Electron micrograph of polyester prepared CFRP surface after removal from DATR crystal. Ovals are drawn to highlight where surface shows contact with the DATR crystal.
FTIR could be a potential quality assurance method for surface preparation for composites bonding. However, further research is necessary to understand the effects of surface preparation on IR spectra before application of FTIR as a quality assurance technique. 4.1 Peel Ply Type It was observed that DATR (bench-top instrument) showed no significant difference between peel ply surface preparation materials (nylon, polyester, SRB). Diffuse reflectance (handheld instrument), however, showed a difference between peel ply types. Using PLS, a method was developed for the Exoscan FTIR that correctly identified peel ply preparation type as polyester, nylon or SRB. Due to this success, diffuse reflectance FTIR has a potential application as a QA technique in the adhesive bonding process to identify peel ply preparation.