
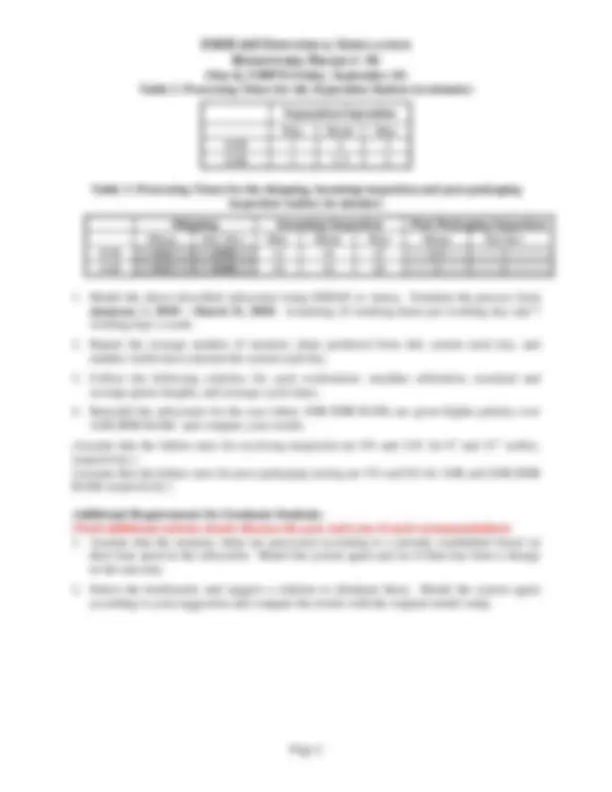
Study with the several resources on Docsity
Earn points by helping other students or get them with a premium plan
Prepare for your exams
Study with the several resources on Docsity
Earn points to download
Earn points by helping other students or get them with a premium plan
Community
Ask the community for help and clear up your study doubts
Discover the best universities in your country according to Docsity users
Free resources
Download our free guides on studying techniques, anxiety management strategies, and thesis advice from Docsity tutors
HW1 Material Type: Notes; Professor: Wu; Class: Indus Simulation; Subject: Industrial and Manufacturing Systems Engineering; University: Kansas State University; Term: Fall 2010;
Typology: Study notes
1 / 2
This page cannot be seen from the preview
Don't miss anything!
(Due by 5:00PM Friday, September 24) Page 1 A computer memory packaging facility consists of six workstations: one inspection/testing station, one die separation station, two Integrated Circuit packaging stations, a backup packaging station, and a shipping station. Wafers of two different sizes of 8-inch (for 1GB DDR RAMs) and 12-inch (for 2BG DDR RAMs) supplied by two upstream wafer manufacturers are tested, cutted, and packaged using the same facility. The first upstream wafer factory sends parts for 8” wafers to the subsystem 10 sets at a time and the inter-arrival times are exponentially distributed with a mean of 12 hours. The second upstream wafer factory sends 12” wafers to the subsystem 20 sets at a time, and the inter-arrival time follows a normal distribution with the mean of 36 hours and the standard deviation of 6 hours. The wafers for both sizes are tested upon arrival at the inspection/testing station. The inspection station tests the parts for any damage during manufacturing and shipping. If the wafer are confirmed good, it is sent to the die separation station, otherwise the wafer for the model is discarded. The Die Separation Station separates an 8” wafer to 4 dies (of 1GB DDR RAM chips), and an 12” wafer to 8 dies (of 2GB DDR RAM chips). The processing times of the separation and inspection stations follow triangular distributions and the corresponding parameters are given in Tables 2 and 3. The separated dies are then forwarded to the packaging stations for wire bonding and plastic packaging operations. The die packaging process consists of two packaging workstations that put the die into an plastic package, bond the golden wires to the die and sealed with packaging material. Dies for 2GB DDR must go to the packaging station 1, and then to the packaging station 2. Dies for 1GB DDR must go to the packaging station 2 and then to the packaging station 1. Packaging station 2 has only 128 buffer spaces. If the packaging station 2 runs out of buffer spaces, the parts are re- routed to another backup station. The processing time for the backup station is the same both memory chips and is distributed uniformly between 0.5 to 15 minutes. After the chips have been packaged, they are sent to the inspection/testing station. Then, the inspection station tests the functionalities of the packaged memory chips. If a chip is confirmed as a good product, the chip will be sent to the shipping department and then the chip departs the system. If the memory chip is considered as a non-confirmed product, it will be discarded. If the memory chips goes through the backup assembly station, it is considered to be inspected on-line and does not need to be re-inspected at the inspection station. It would directly go to the shipping station. The processing times for the two packaging stations, separation station and the incoming inspection station follow triangular distributions. The processing times for the shipping station, and the post-packaging inspection is based on normal distribution. The corresponding parameters are given below: Table 1. Processing Times for the Packaging Stations (in minutes) Packaging 1 Packaging 2 Min. Mode Max. Min. Mode Max. 2GB 1.0 2.0 3.0 1.0 2.5 4. 1GB 1.0 1.5 4.0 0.5 2.0 3.
(Due by 5:00PM Friday, September 24) Page 2 Table 2. Processing Times for the Separation Station (in minutes) Separation Operation Min. Mode Max. 2GB 1 2 3 1GB 1 1.5 2 Table 3. Processing Times for the shipping, incoming inspection and post-packaging inspection station (in minutes) Shipping Incoming Inspection Post-Packaging Inspection Mean. Std. Dev. Min. Mode Max Mean Std Dev 2GB 0.2 0.05 12 18 25 2.5 1 1GB 0.2 0.06 10 16 20 2 2