
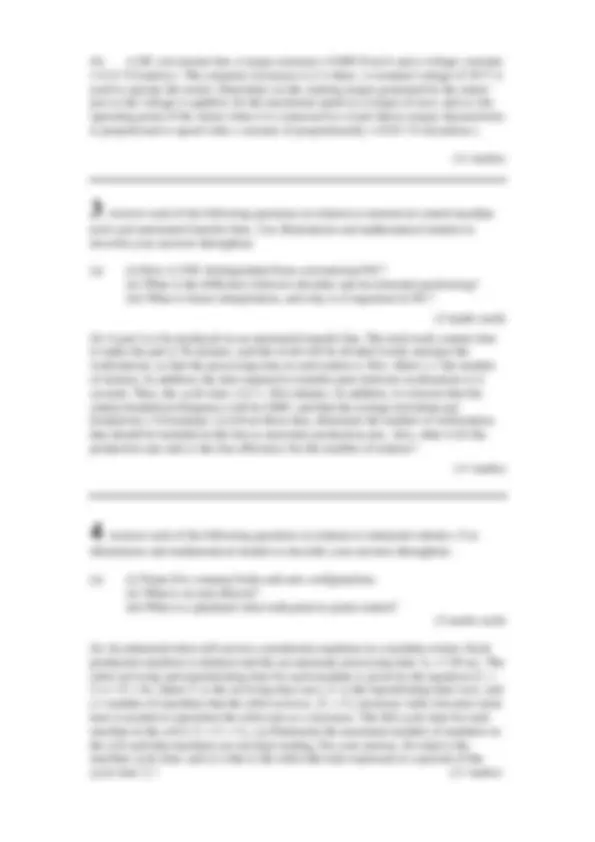
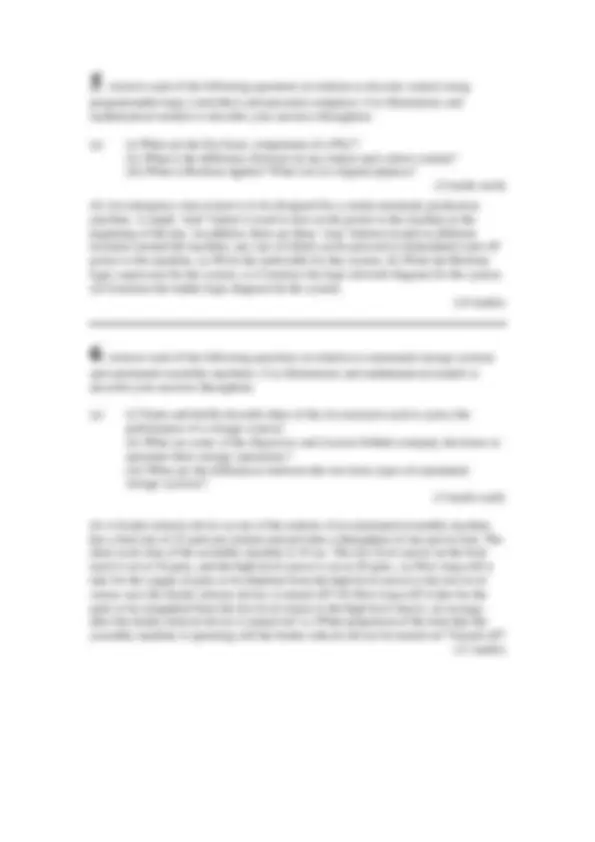
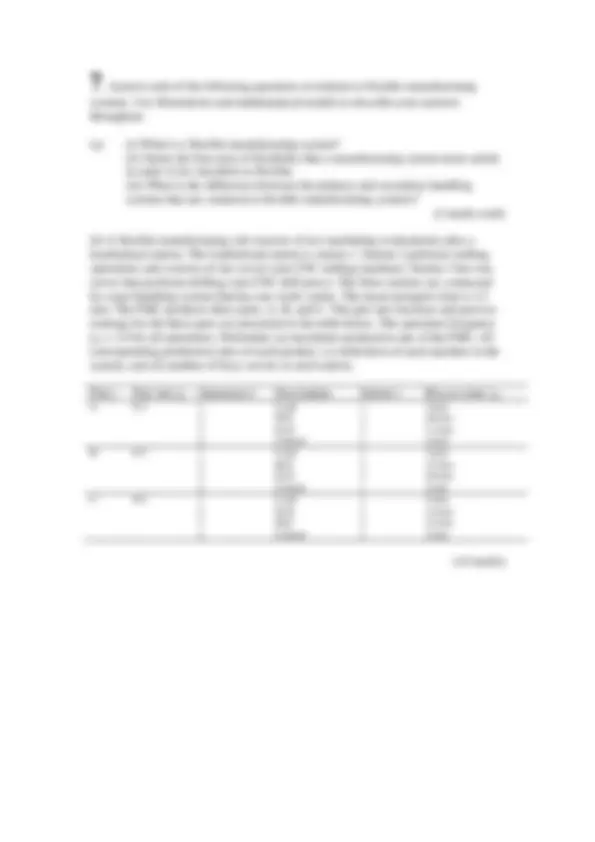
Study with the several resources on Docsity
Earn points by helping other students or get them with a premium plan
Prepare for your exams
Study with the several resources on Docsity
Earn points to download
Earn points by helping other students or get them with a premium plan
Community
Ask the community for help and clear up your study doubts
Discover the best universities in your country according to Docsity users
Free resources
Download our free guides on studying techniques, anxiety management strategies, and thesis advice from Docsity tutors
Main points of this past exam are: Industrial Control, Integrated Manufacturing, Over Automation, Determine the Average, Programmable Machines, Plant Capacity, Forward Control, Linear Interpolation, End Effector, Down Counter
Typology: Exams
1 / 5
This page cannot be seen from the preview
Don't miss anything!
Exam Code(s) 3BI1, 1EM Exam(s) B.E. Degree in Industrial Engineering
Module Code(s) IE Module(s) Computer Integrated Manufacturing
Paper No. 1 Repeat Paper
External Examiner(s) Prof. J Antony Internal Examiner(s) Dr. David O’Sullivan Dr. Ke Ning
All questions will be marked equally. Use a separate answer book for each section.
Duration (^) 3 Hours
No. of Pages Cover + 4 pages Department(s) Industrial Engineering Course Co-ordinator(s) Dr. David O’Sullivan
Requirements: MCQ Handout Statistical Tables Graph Paper Log Graph Paper Other Material
manufacturing and related mathematical models and metrics. Use illustrations and mathematical models to describe your answers throughout.
(a) (i) What is computer integrated manufacturing? (ii) Identify three situations where manual labour is preferred over automation. (iii) What is programmable automation and what are some of its features? (3 marks each)
(b) A certain job shop specializes in one-of-a-kind orders dealing with parts of medium-to-high complexity. A typical part is processed sequentially through ten machines in batch sizes of one. The shop contains a total of eight conventional machine tools and operates 35 hours per week of production time. The machine tools are interchangeable in the sense that they can be set up for any operation required on any of the parts. Average time values on the part are: machining time per machine = 0.5 hour, work handling time per machine = 0.3 hour, tool change time per machine = 0.2 hour, setup time per machine = 6 hours, and nonoperation time per machine = 12 hours. A new programmable machine has been purchased by the shop that is capable of performing all ten operations in a single setup. The programming of the machine for this part will require 20 hours; however, the programming can be done off-line, without tying up the machine. The setup time will be 10 hours. The total machining time will be reduced to 80% of its previous value due to advanced tool control algorithms; the work handling time will be the same as for one machine; and the total tool change time will be reduced by 50% because it will be accomplished automatically under program control. For the one machine, nonoperation time is expected to be 12 hours. (a) Determine the manufacturing lead time for the traditional method and for the new method. (b) Compute the plant capacity for the following alternatives: (i) a job shop containing the eight traditional machines, and (ii) a job shop containing two of the new programmable machines. Assume the typical jobs are represented by the data given above. (c) Determine the average level of work-in-process for the two alternatives in part (b), if the alternative shops operate at full capacity. (11 marks)
and hardware for automation and process control. Use illustrations and mathematical models to describe your answers throughout.
(a) (i) What is industrial control? (ii) What is the difference between a continuous control system and a discrete control system? (iii) What is feed forward control?
(3 marks each)
Question 2 continued overleaf …
programmable logic controllers and personal computers. Use illustrations and mathematical models to describe your answers throughout.
(a) (i) What are the five basic components of a PLC? (ii) What is the difference between an up counter and a down counter? (iii) What is Boolean algebra? What was its original purpose? (2 marks each)
(b) An emergency stop system is to be designed for a certain automatic production machine. A single "start" button is used to turn on the power to the machine at the beginning of the day. In addition, there are three ‘stop’ buttons located at different locations around the machine, any one of which can be pressed to immediately turn off power to the machine. (a) Write the truth table for this system. (b) Write the Boolean logic expression for the system. (c) Construct the logic network diagram for the system. (d) Construct the ladder logic diagram for the system. (14 marks)
and automated assembly machines. Use illustrations and mathematical models to describe your answers throughout.
(a) (i) Name and briefly describe three of the six measures used to assess the performance of a storage system? (ii) What are some of the objectives and reasons behind company decisions to automate their storage operations? (iii) What are the differences between the two basic types of automated storage systems? (3 marks each)
(b) A feeder-selector device at one of the stations of an automated assembly machine has a feed rate of 25 parts per minute and provides a throughput of one part in four. The ideal cycle time of the assembly machine is 10 sec. The low level sensor on the feed track is set at 10 parts, and the high level sensor is set at 20 parts. (a) How long will it take for the supply of parts to be depleted from the high level sensor to the low level sensor once the feeder-selector device is turned off? (b) How long will it take for the parts to be resupplied from the low level sensor to the high level sensor, on average, after the feeder-selector device is turned on? (c) What proportion of the time that the assembly machine is operating will the feeder-selector device be turned on? Turned off? (11 marks)
systems. Use illustrations and mathematical models to describe your answers throughout.
(a) (i) What is a flexible manufacturing system? (ii) Name the four tests of flexibility that a manufacturing system must satisfy in order to be classified as flexible. (iii) What is the difference between the primary and secondary handling systems that are common in flexible manufacturing systems? (2 marks each)
(b) A flexible manufacturing cell consists of two machining workstations plus a load/unload station. The load/unload station is station 1. Station 2 performs milling operations and consists of one server (one CNC milling machine). Station 3 has one server that performs drilling (one CNC drill press). The three stations are connected by a part handling system that has one work carrier. The mean transport time is 2. min. The FMC produces three parts, A, B, and C. The part mix fractions and process routings for the three parts are presented in the table below. The operation frequency fijk = 1.0 for all operations. Determine (a) maximum production rate of the FMC, (b) corresponding production rates of each product, (c) utilization of each machine in the system, and (d) number of busy servers at each station.
Part j Part mix pj Operation k Description Station i Process time tijk A 0.2 1 Load 1 3 min 2 Mill 2 20 min 3 Drill 3 12 min 4 Unload 1 2 min B 0.3 1 Load 1 3 min 2 Mill 2 15 min 3 Drill 3 30 min 4 Unload 1 2 min C 0.5 1 Load 1 3 min 2 Drill 3 14 min 3 Mill 2 22 min 4 Unload 1 2 min
(14 marks)