

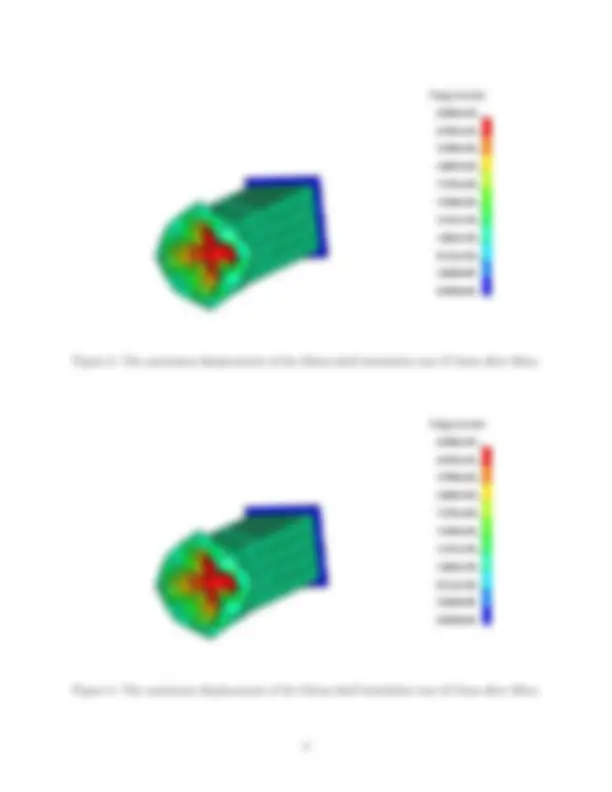
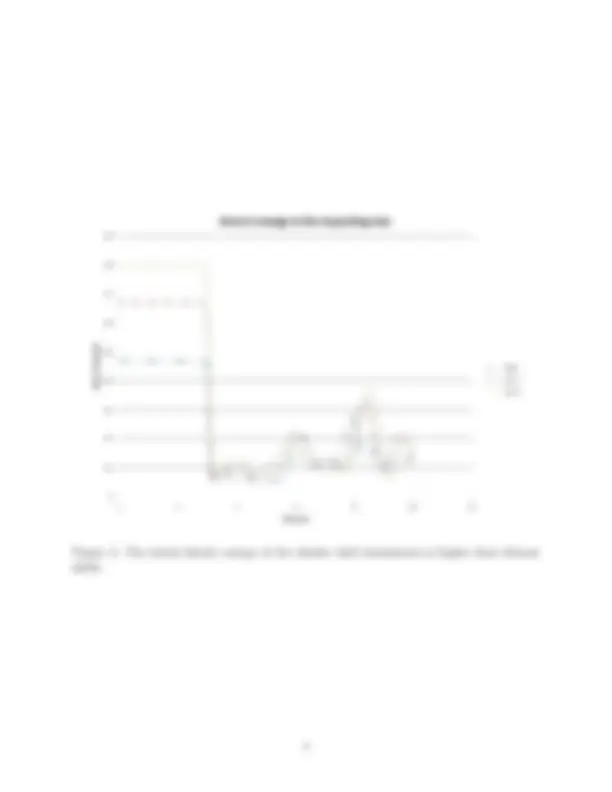
Study with the several resources on Docsity
Earn points by helping other students or get them with a premium plan
Prepare for your exams
Study with the several resources on Docsity
Earn points to download
Earn points by helping other students or get them with a premium plan
Community
Ask the community for help and clear up your study doubts
Discover the best universities in your country according to Docsity users
Free resources
Download our free guides on studying techniques, anxiety management strategies, and thesis advice from Docsity tutors
Material Type: Project; Professor: Chaphalkar; Class: Materials Failure Analysis; Subject: Engineering; University: Grand Valley State University; Term: Fall 2008;
Typology: Study Guides, Projects, Research
1 / 5
This page cannot be seen from the preview
Don't miss anything!
EGR 680 – Impact Analysis Instructor: Dr. Chaphalkar
School of Engineering Padnos College of Engineering and Computing Grand Valley State University
November 3, 2008
1 Introduction
The purpose of this simulation was to determine the effects of shell thickness on the deformation of a tube impacting a rigid wall. A tube was modeled in LS-Dyna and given an initial velocity. A rigid wall was placed in the model to provide the contact for collision. The thickness of the shell elements was varied from 0.7mm to 1.2mm and the simulation results were compared. The model with the thickest shell elements shows lower total deflections but higher kinetic energies than the thinner models.
2 Simulation Setup
A 10mm x 10mm x 75mm box was meshed in LS-Dyna using the box-shell element type. The box was given an initial velocity of 5m/s. A rigid wall was included in the model 15mm from the end of the box to provide a surface for impact. Additionally, 9 point masses of 5kg apiece were placed at the nine nodes in the center of the model on the surface opposite the rigid wall. Figure 1 shows the setup of the box/rigid wall model in LS-PrePost.
Figure 1: A rigid wall, denoted as a blue plane, was placed 15mm from the end of the box with 9 point masses placed at the opposite end of the box.
The material properties chosen for all of the simulations were those of steel. The thickness of the shell elements used for each simulation were 0.7mm, 1.0mm, and 1.2mm respectively. The simulation time used for each simulation was 10ms.
Figure 3: The maximum displacement of the 10mm shell simulation was 47.2mm after 10ms.
Figure 4: The maximum displacement of the 12mm shell simulation was 45.7mm after 10ms.
Figure 5: The initial kinetic energy of the thicker shell simulations is higher than thinner shells.