
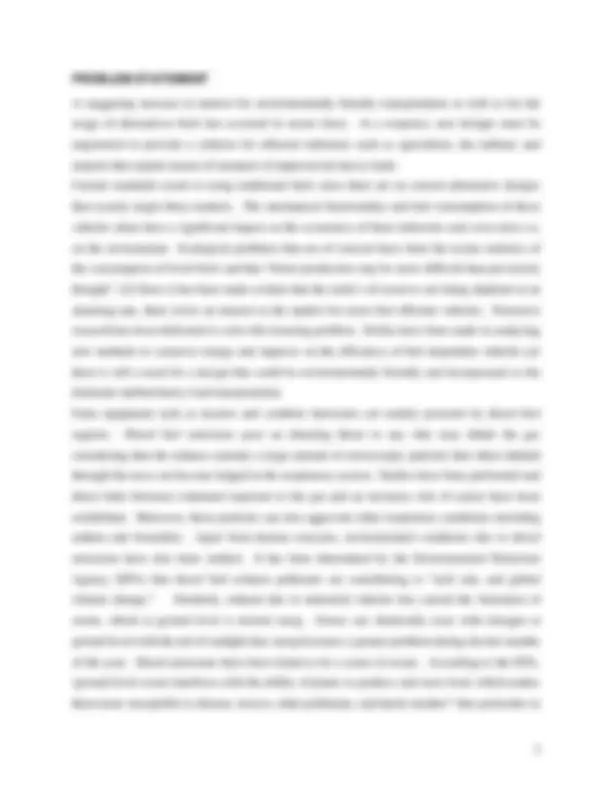
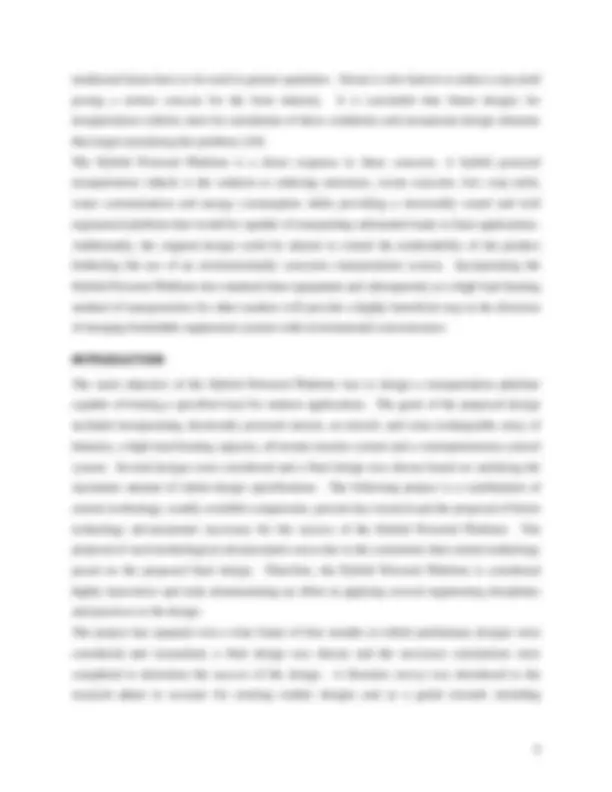
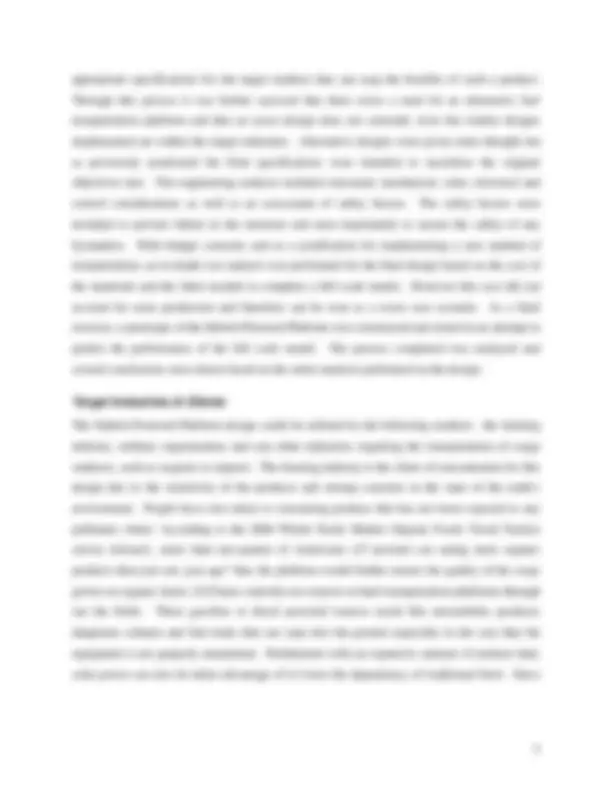
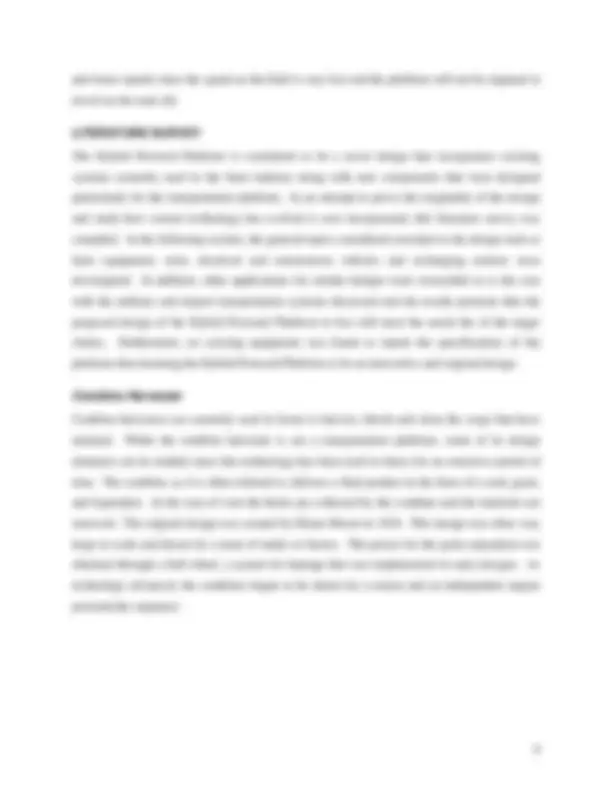
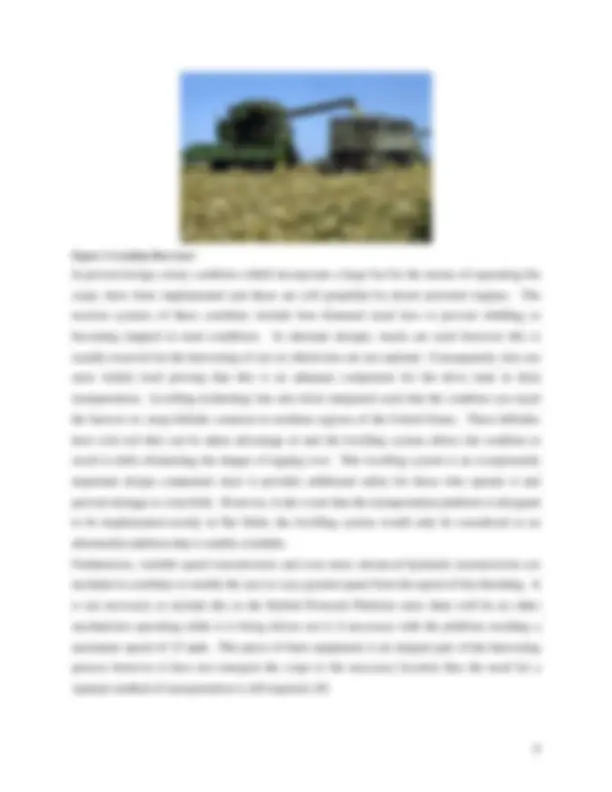
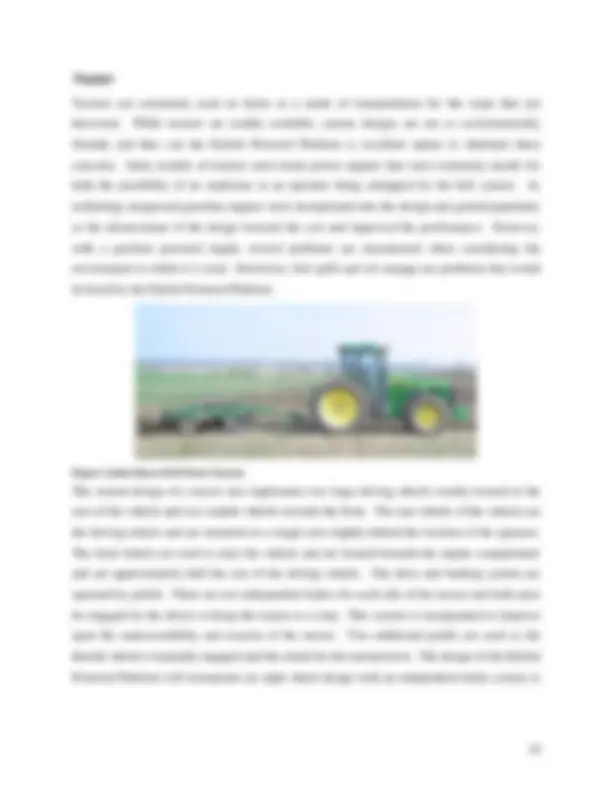
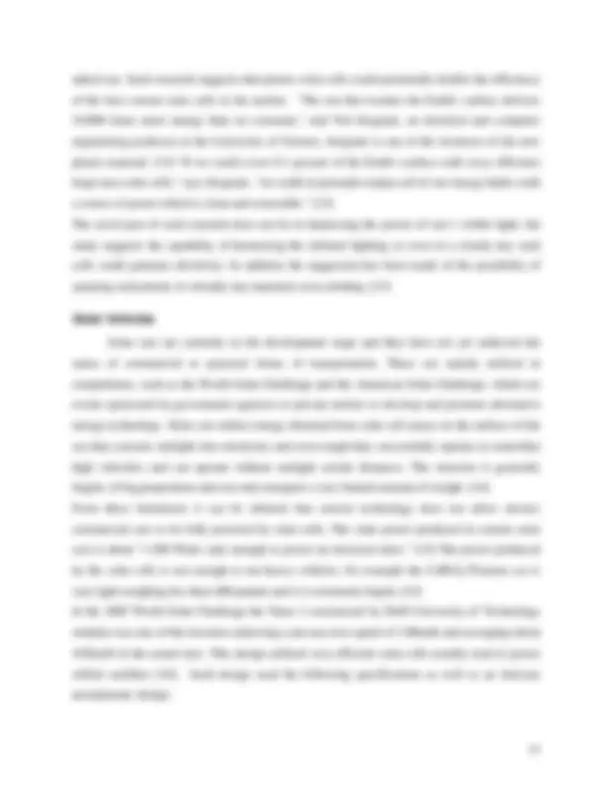
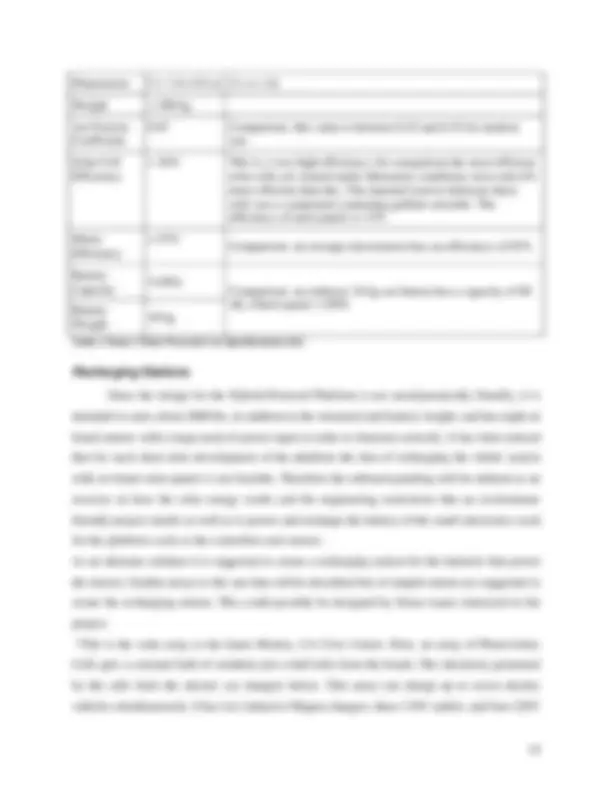
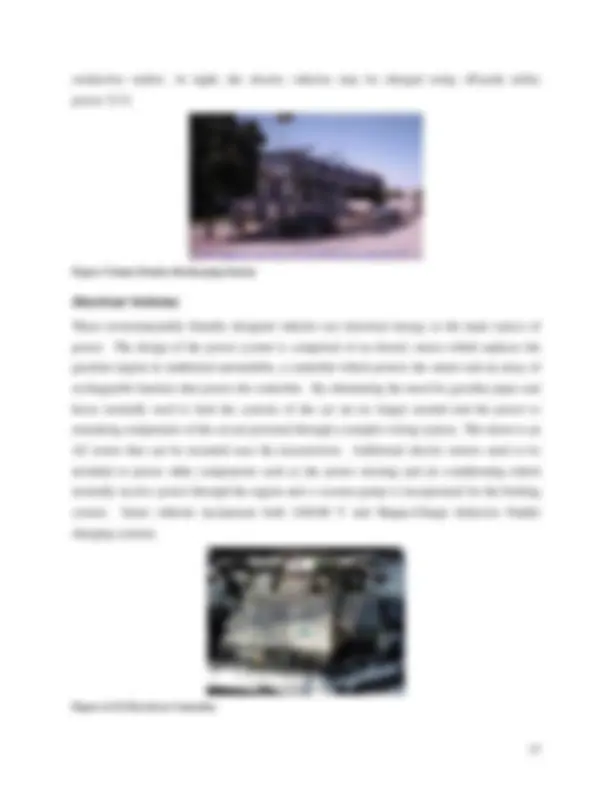
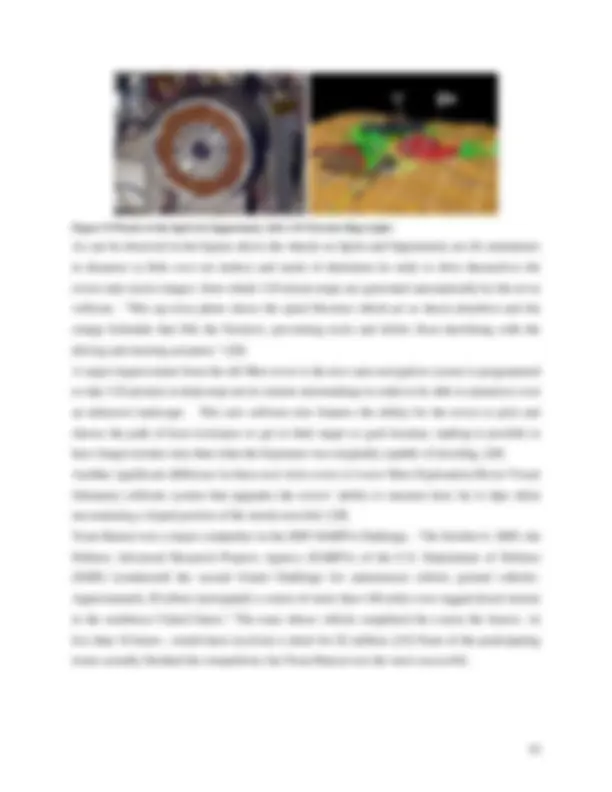
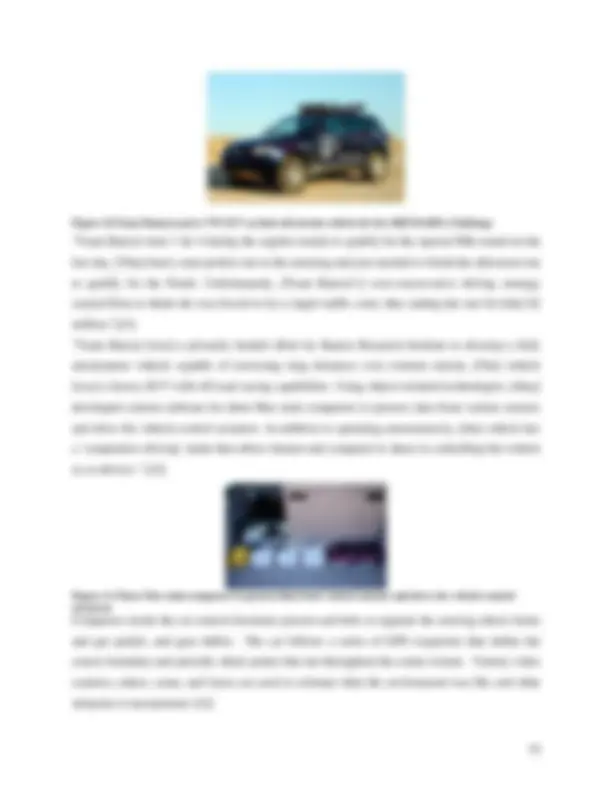
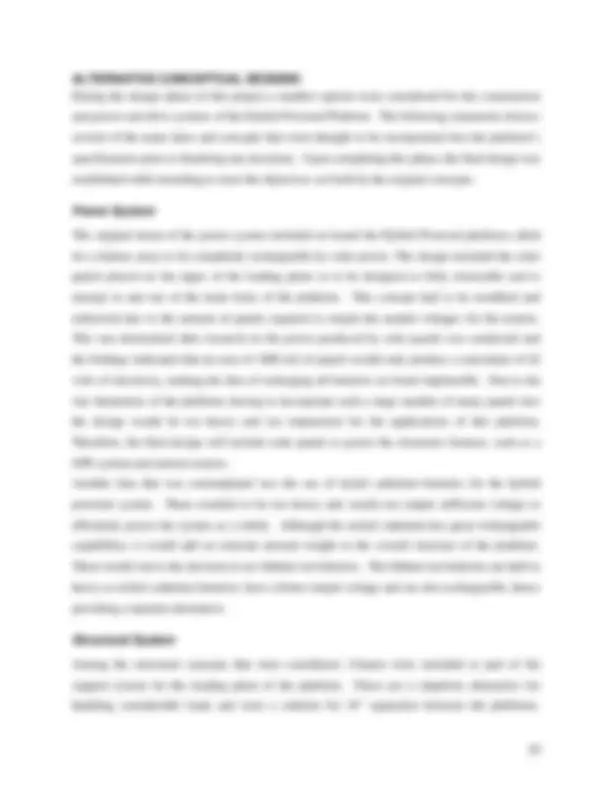
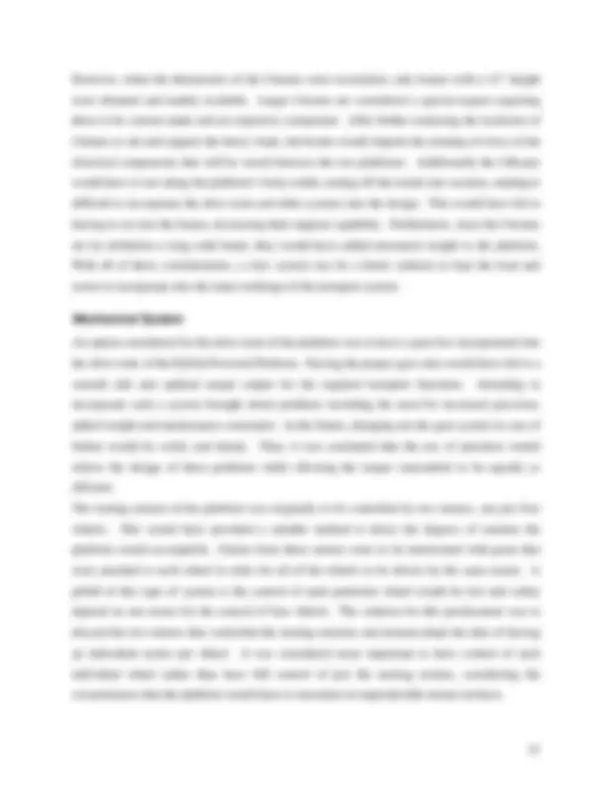
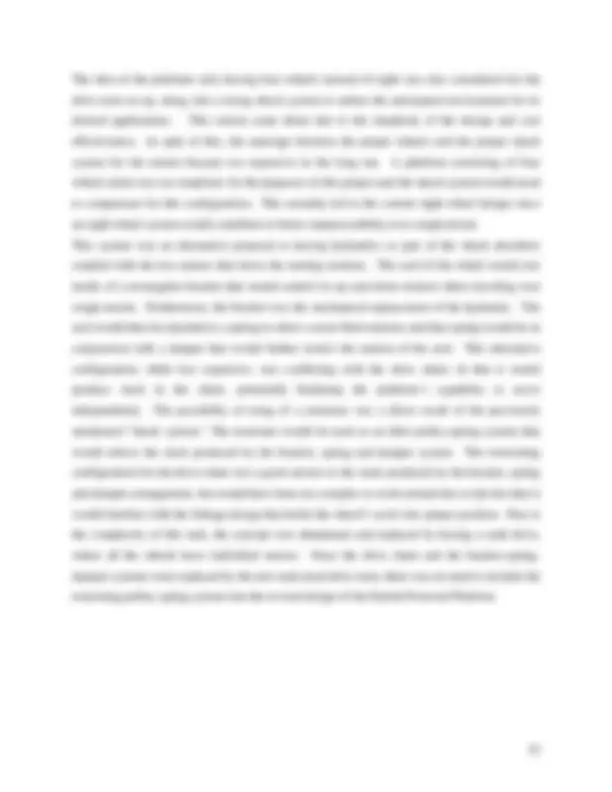
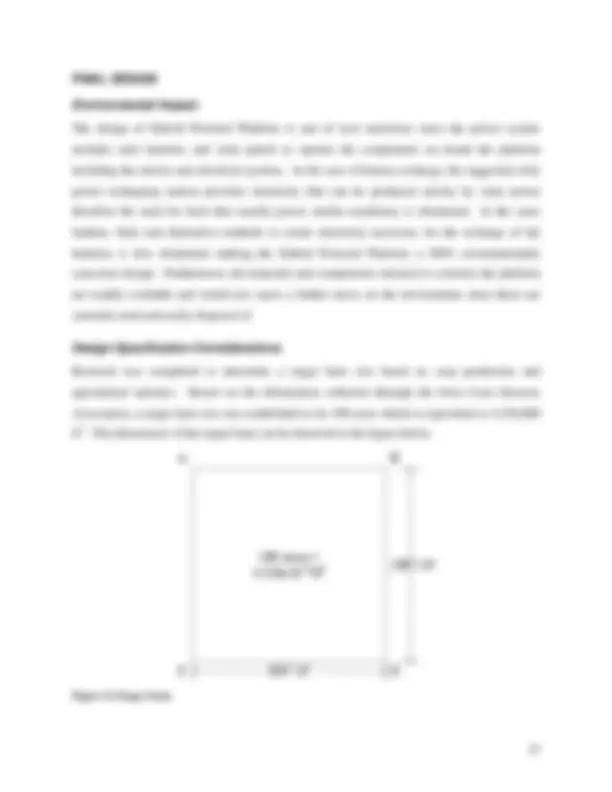
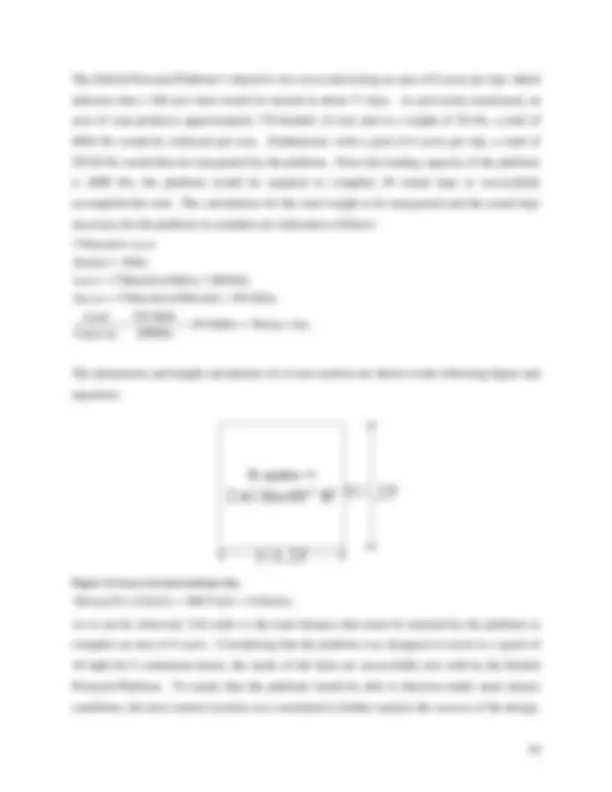
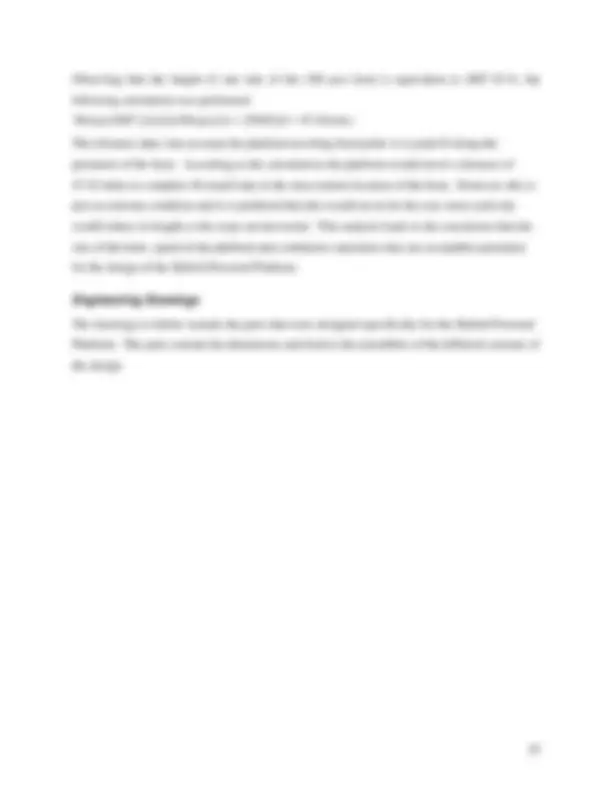
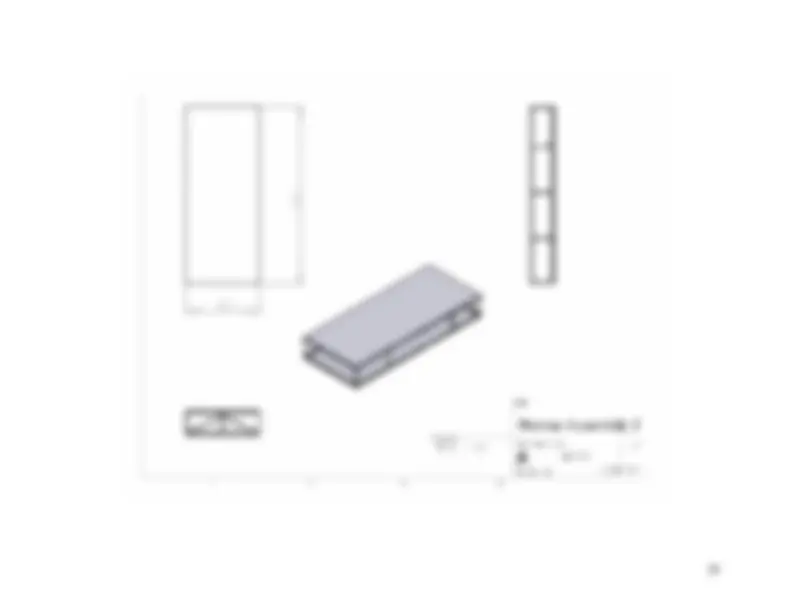
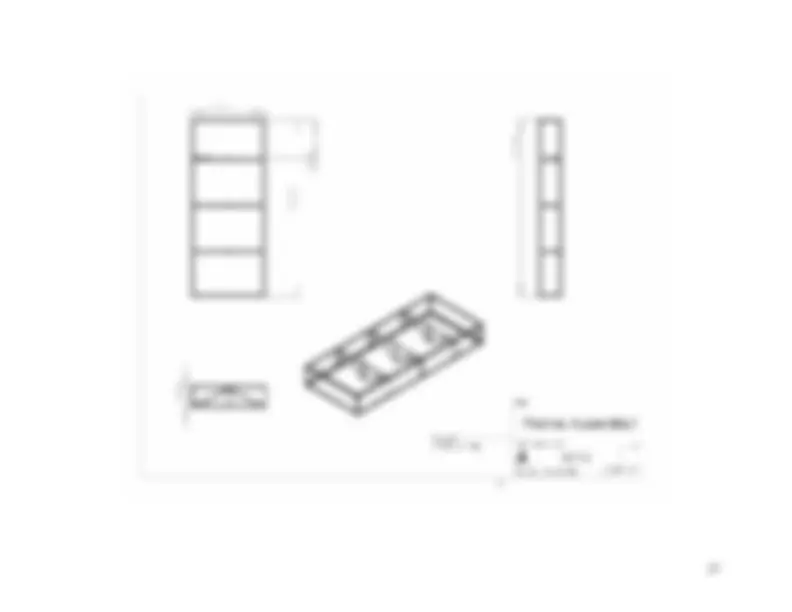
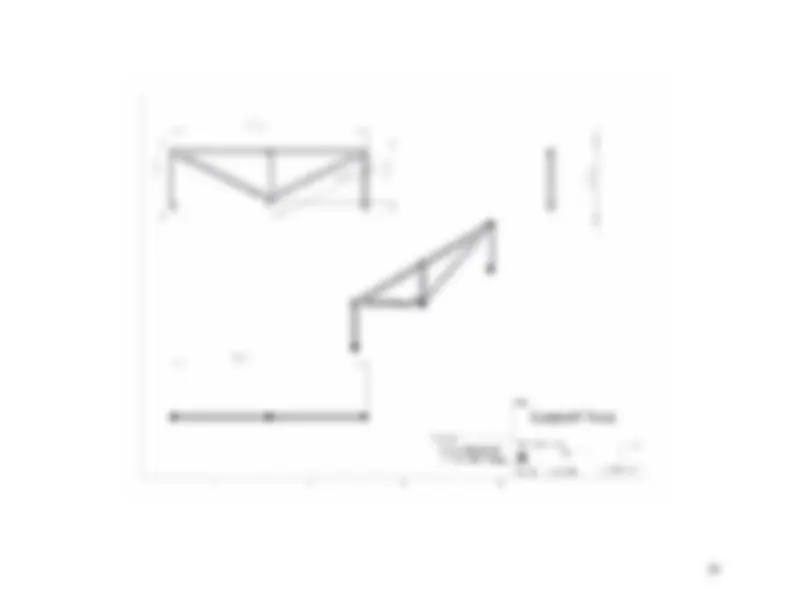
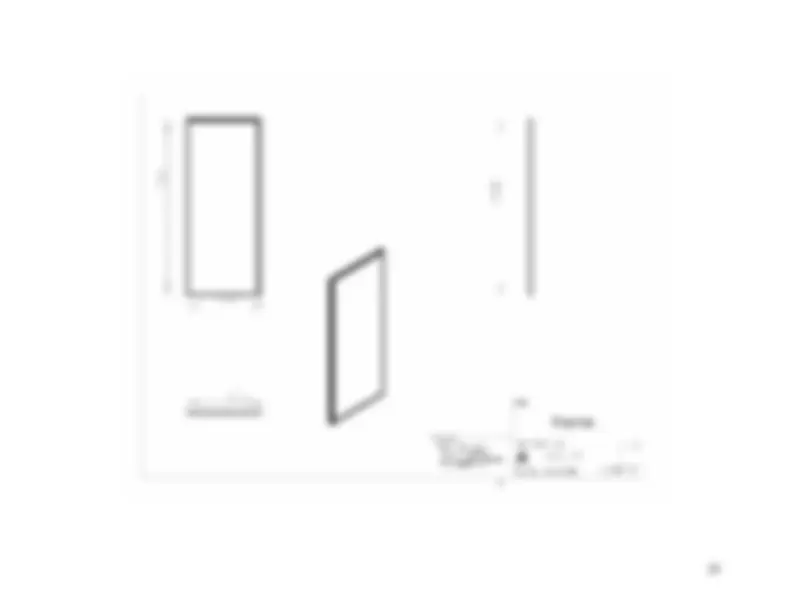
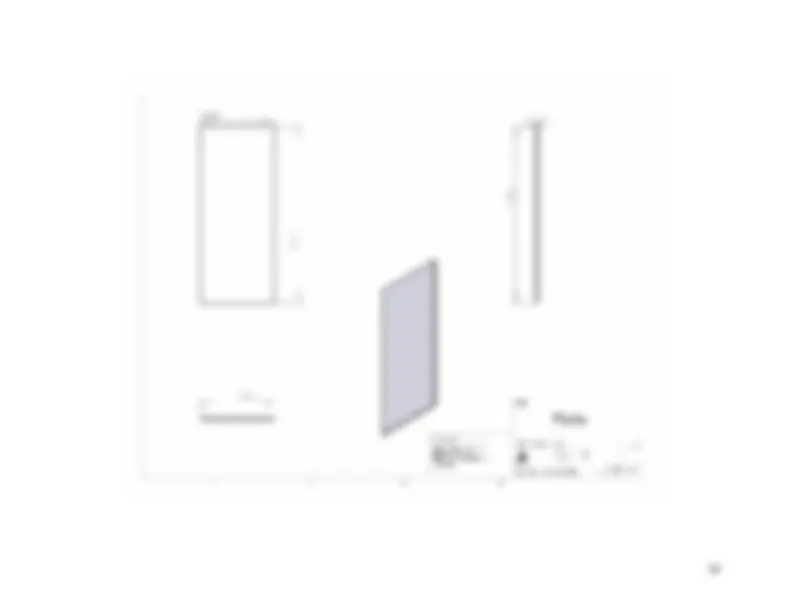
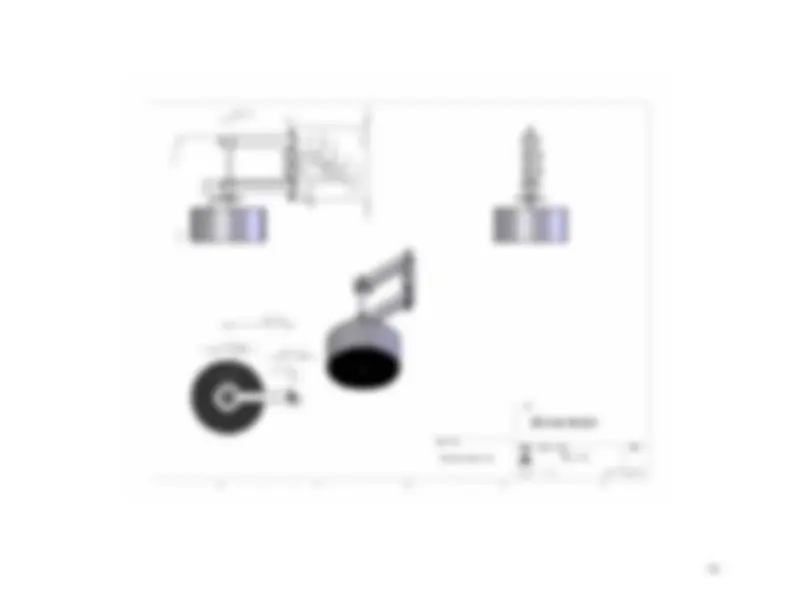
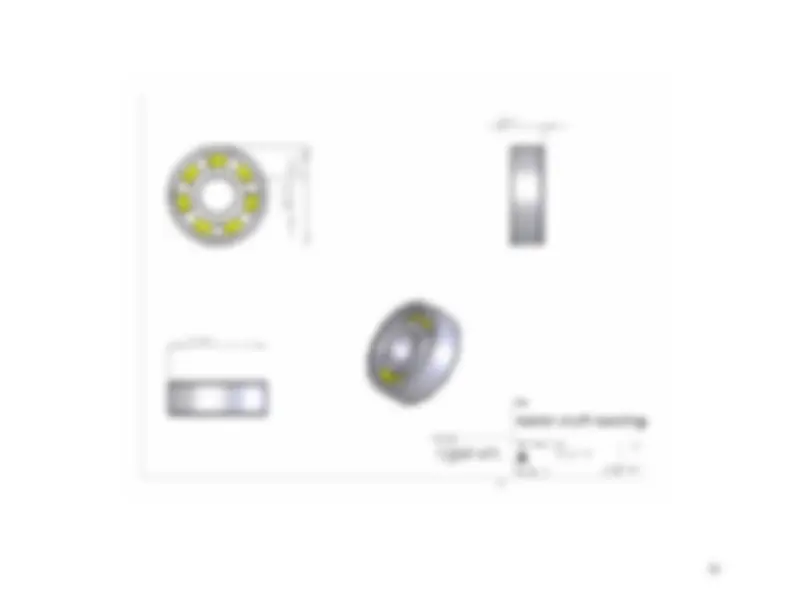
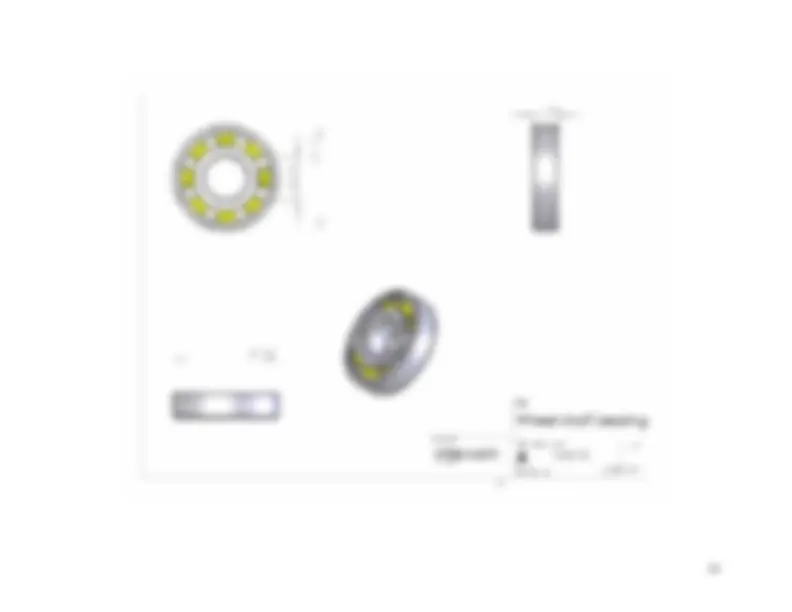
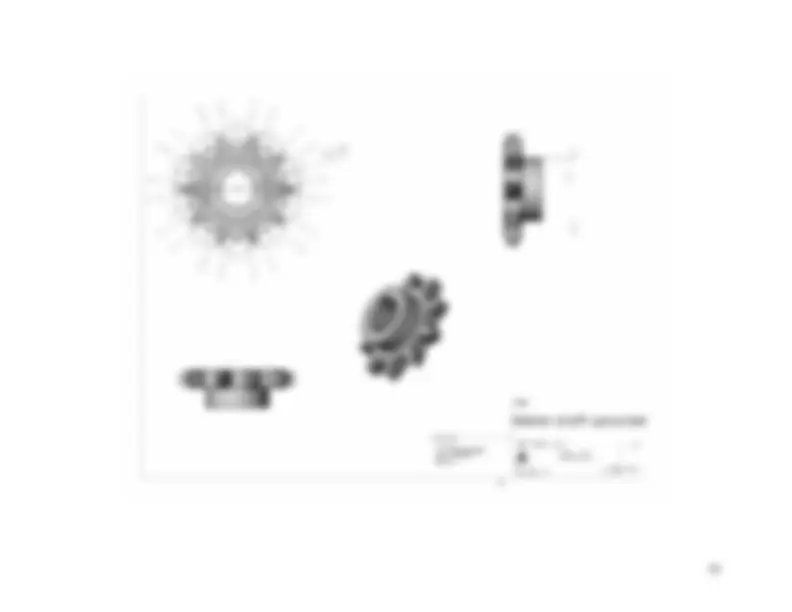
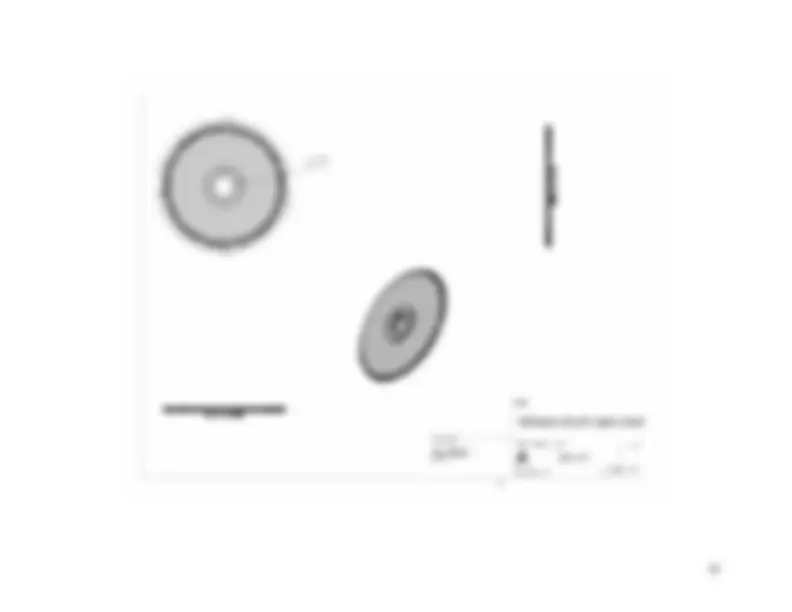
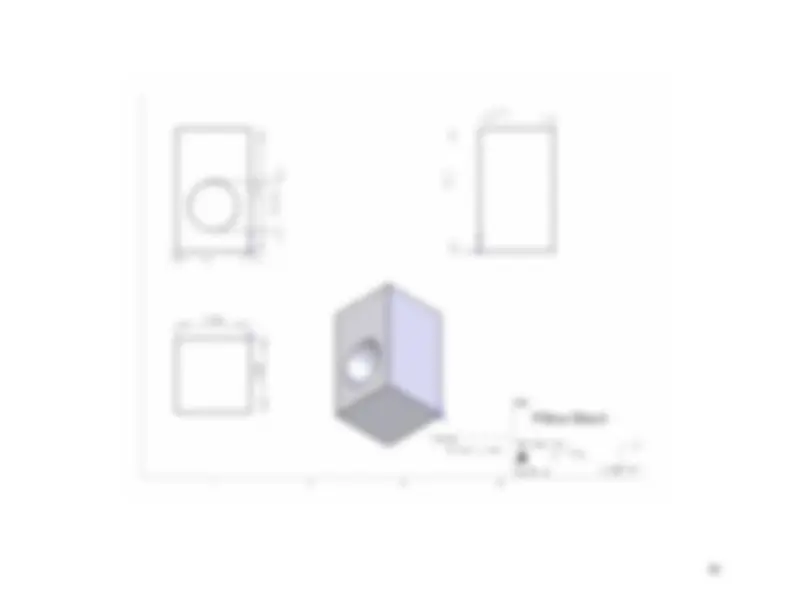
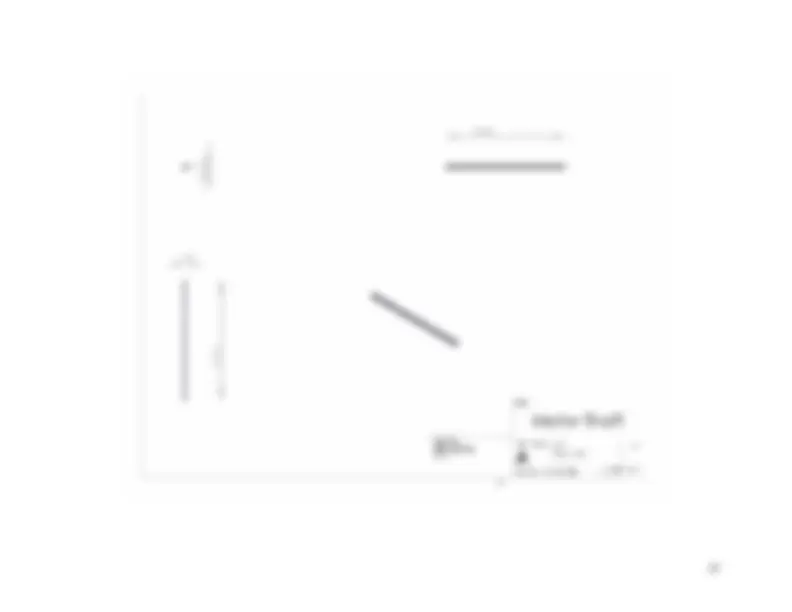
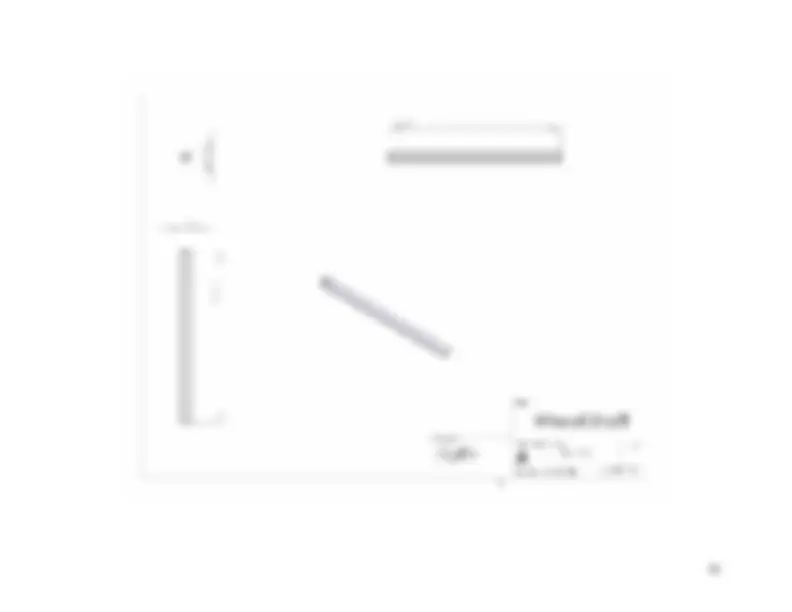
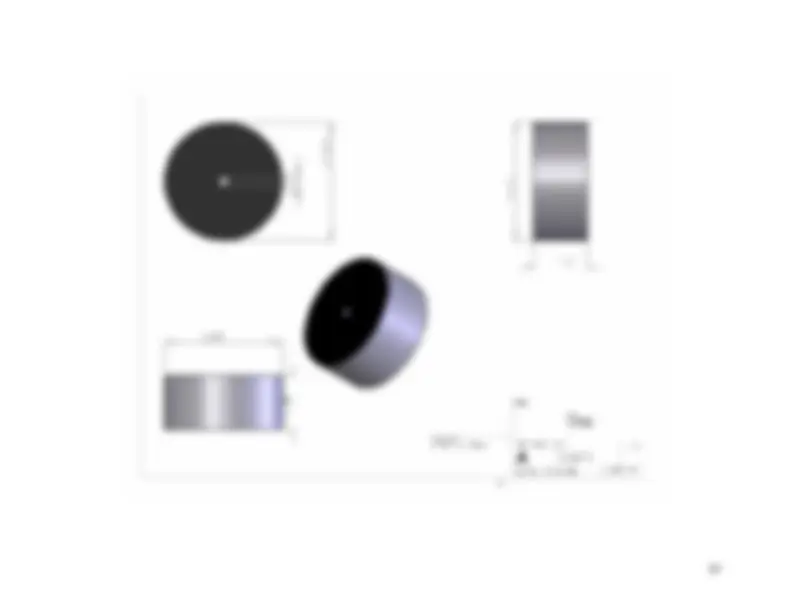
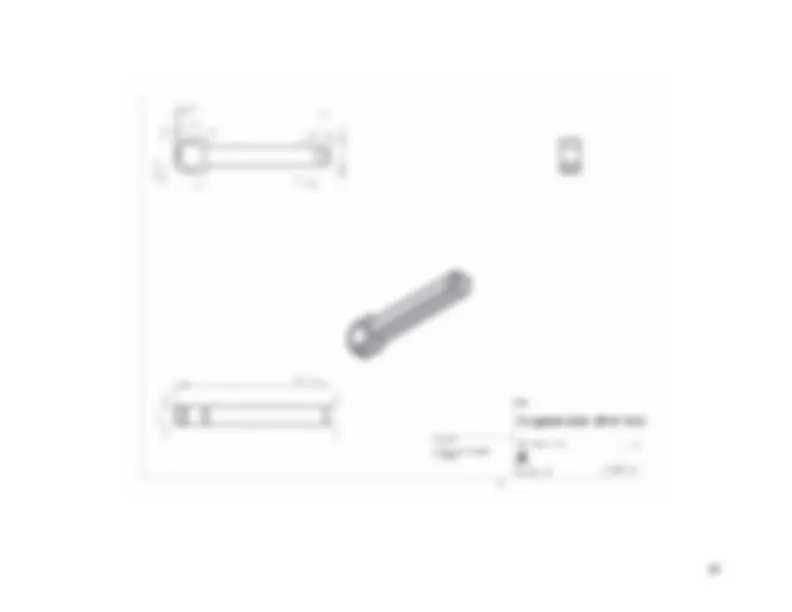
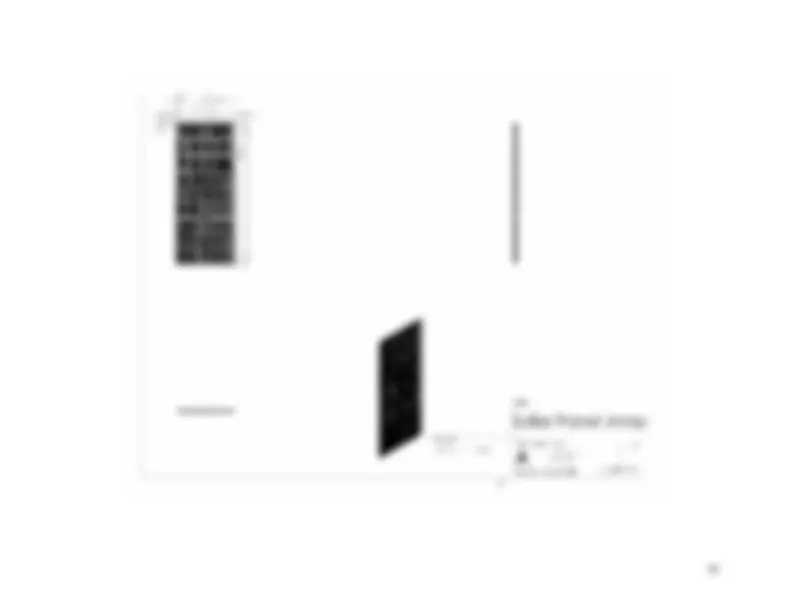
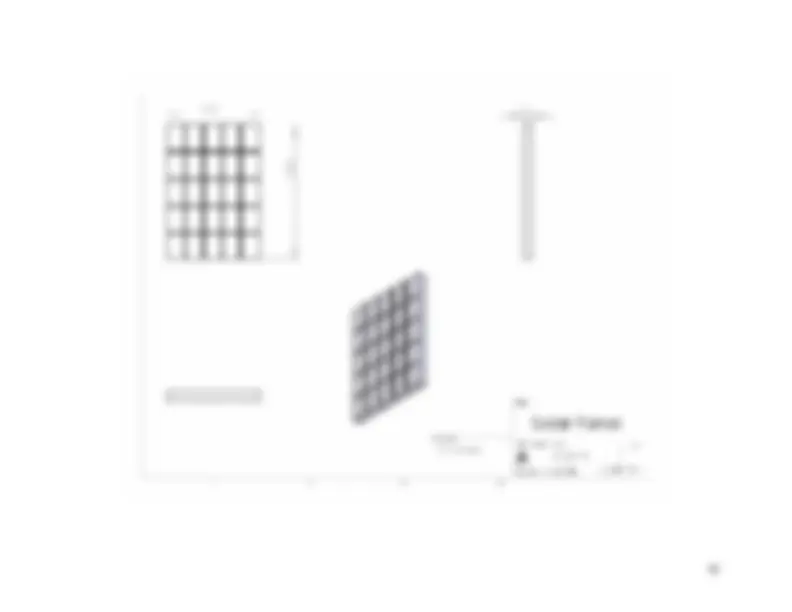
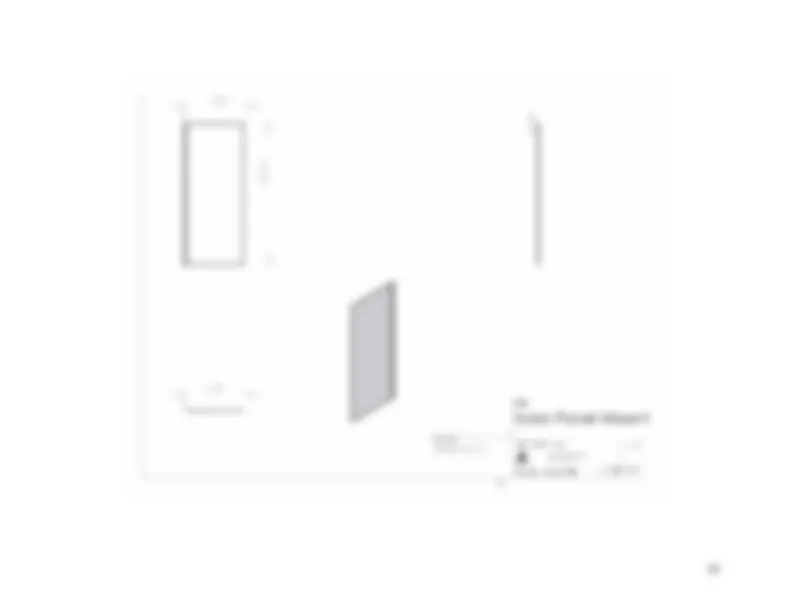
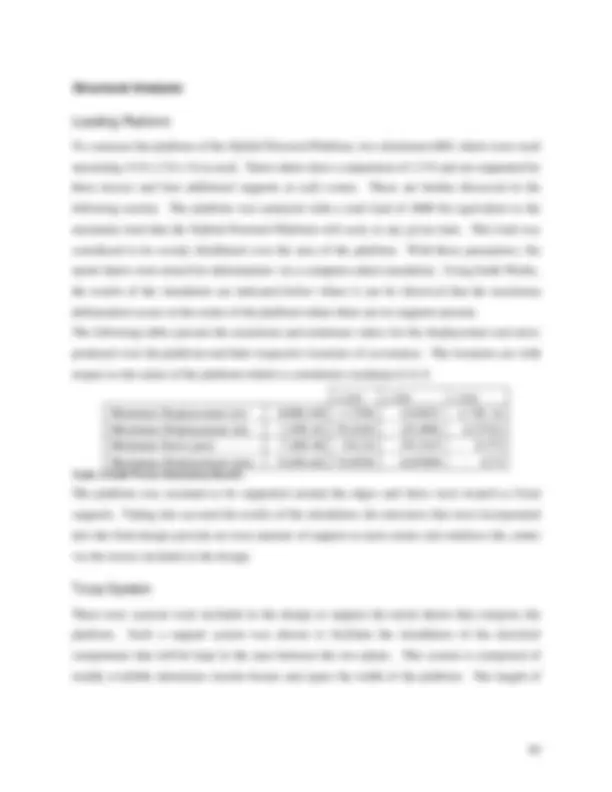
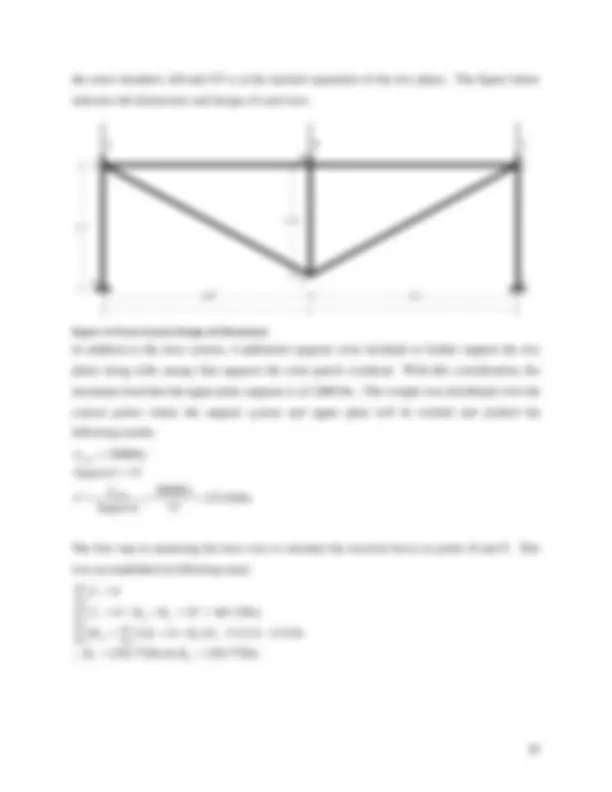
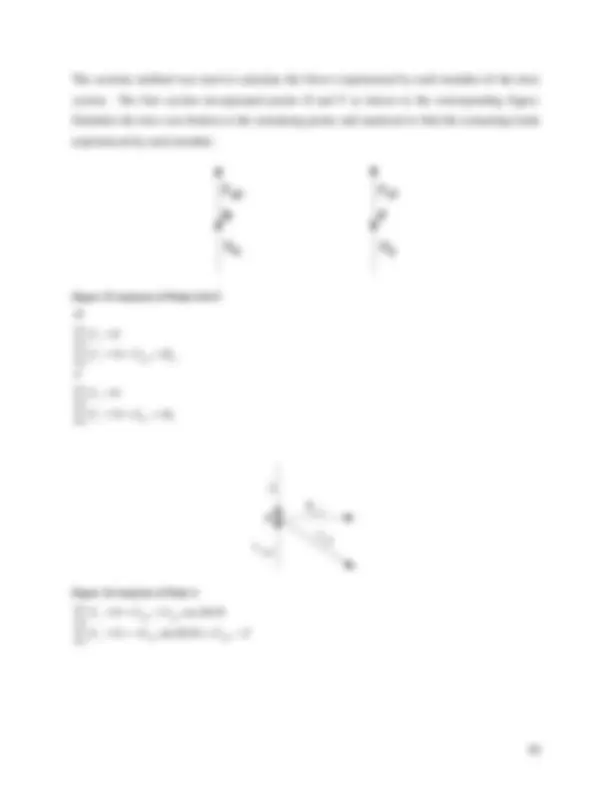
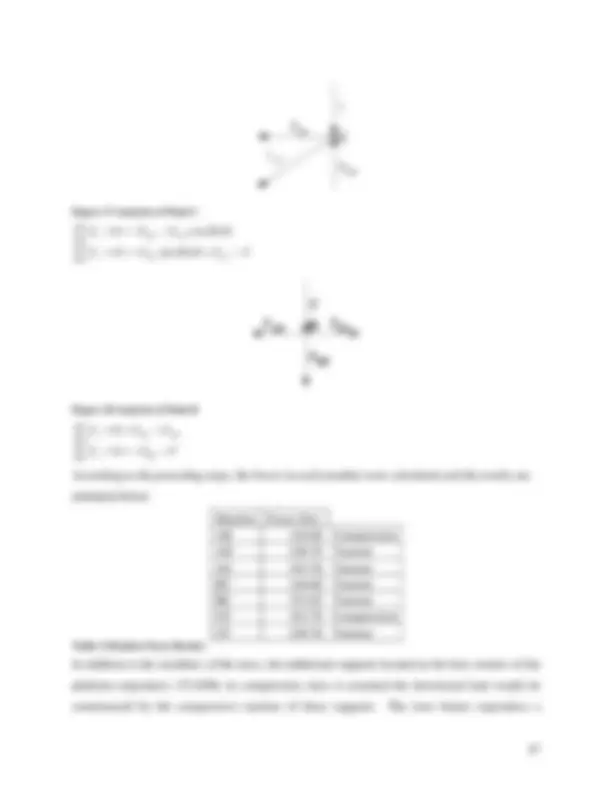
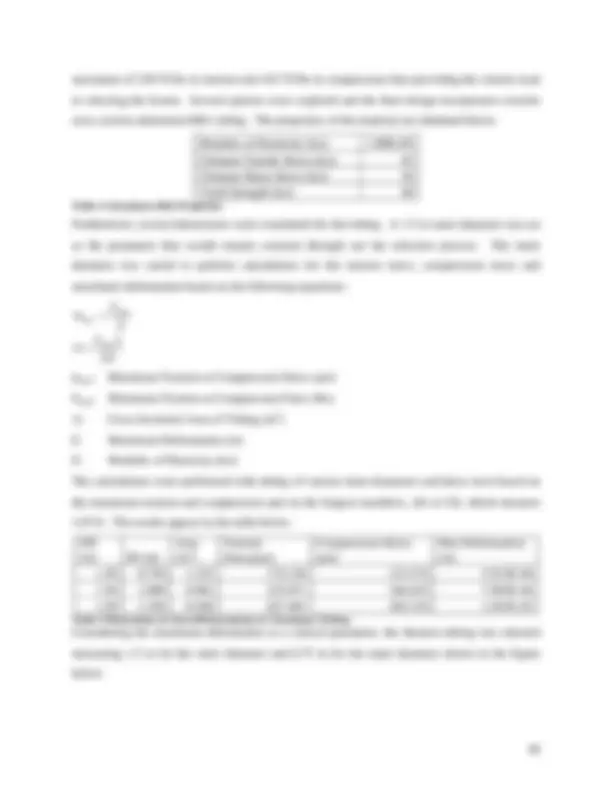
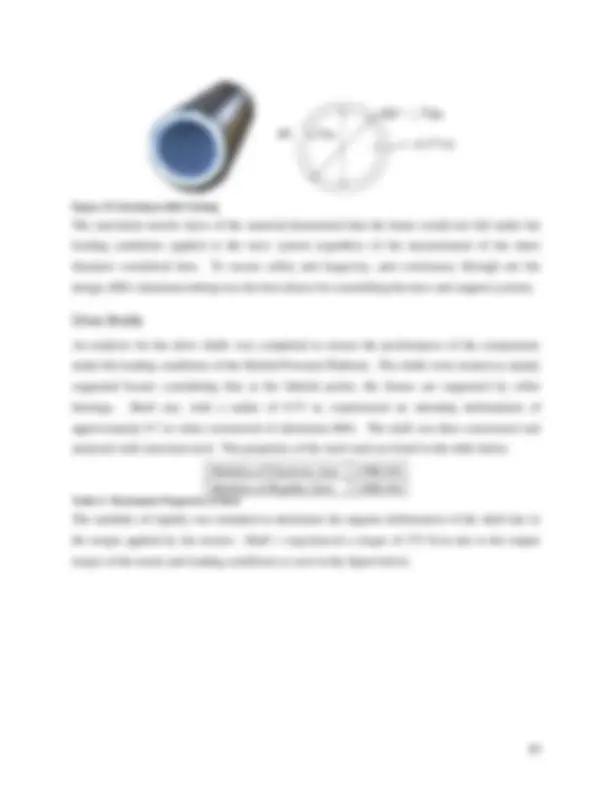
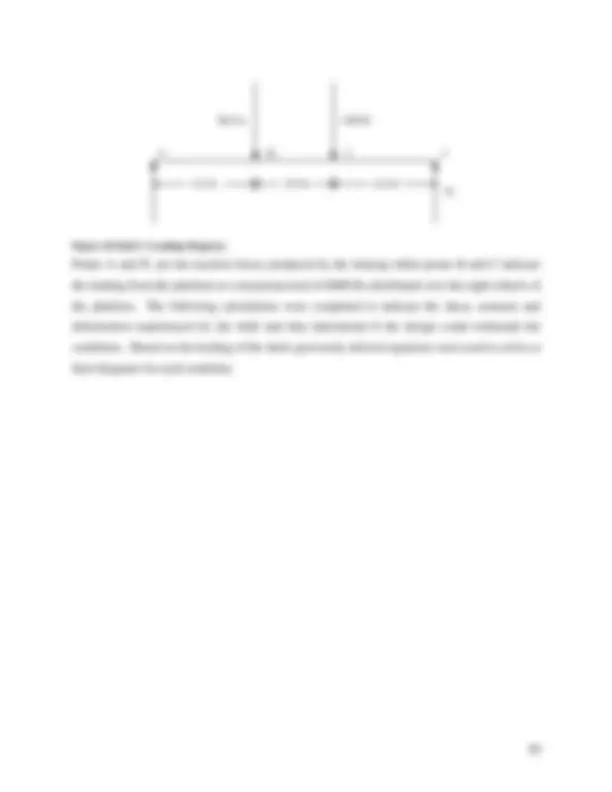
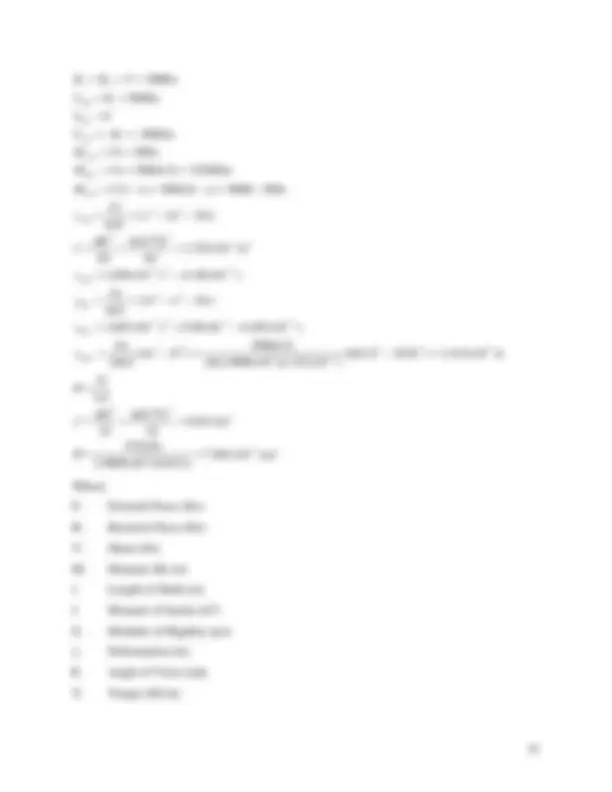
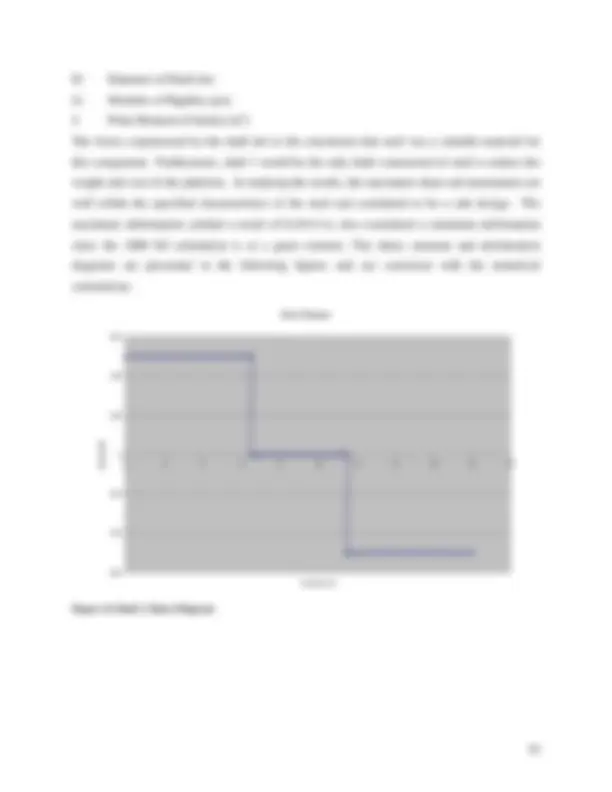
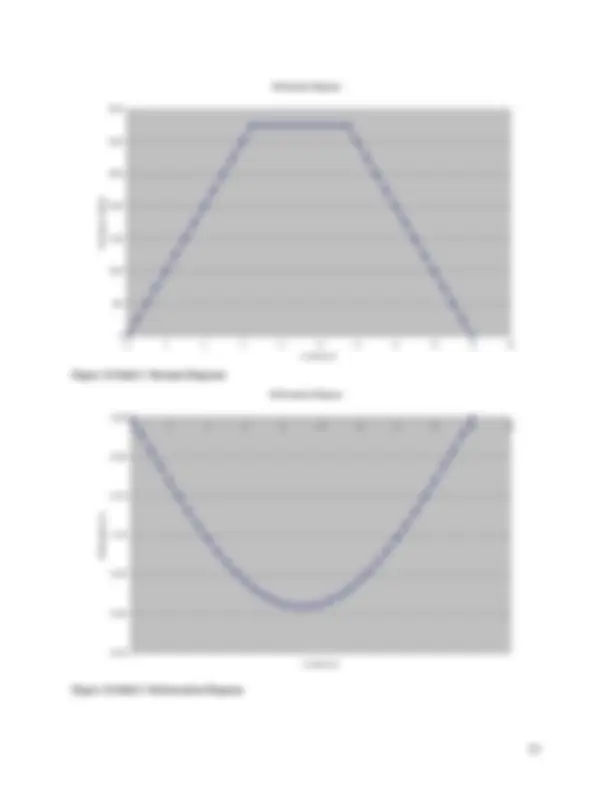
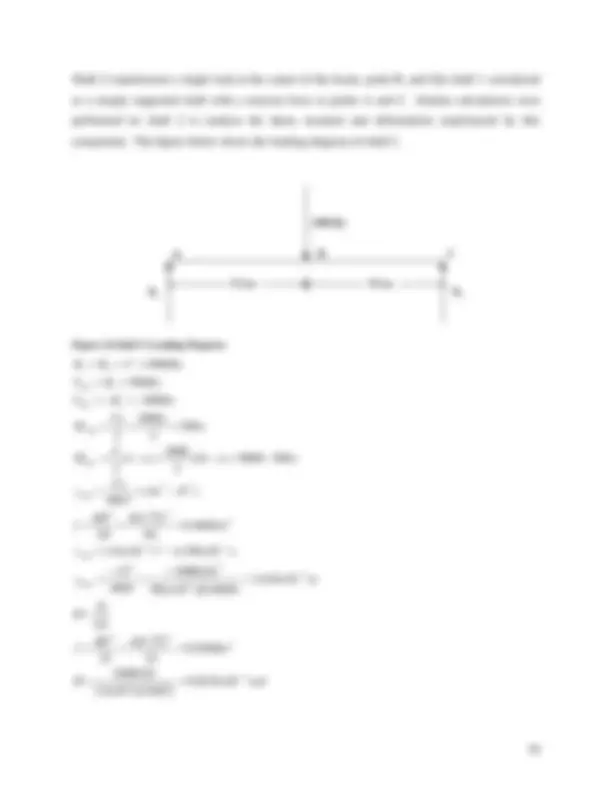
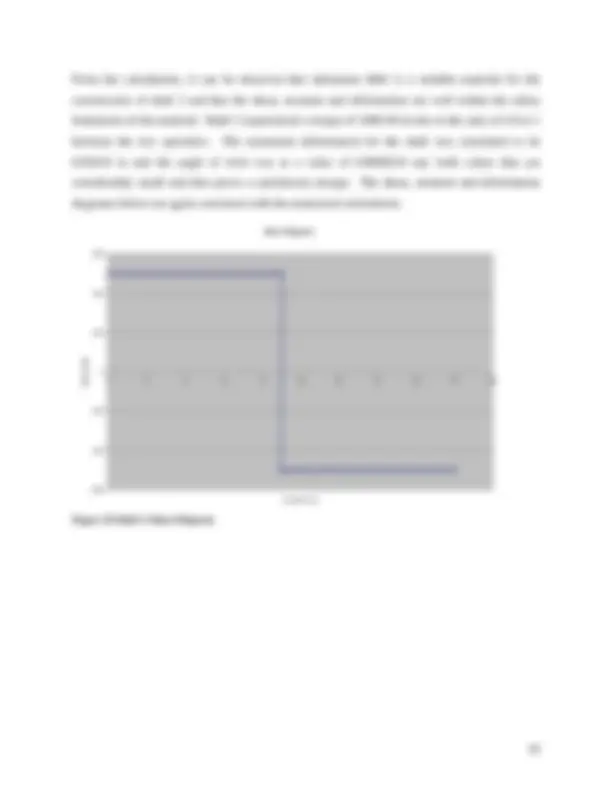
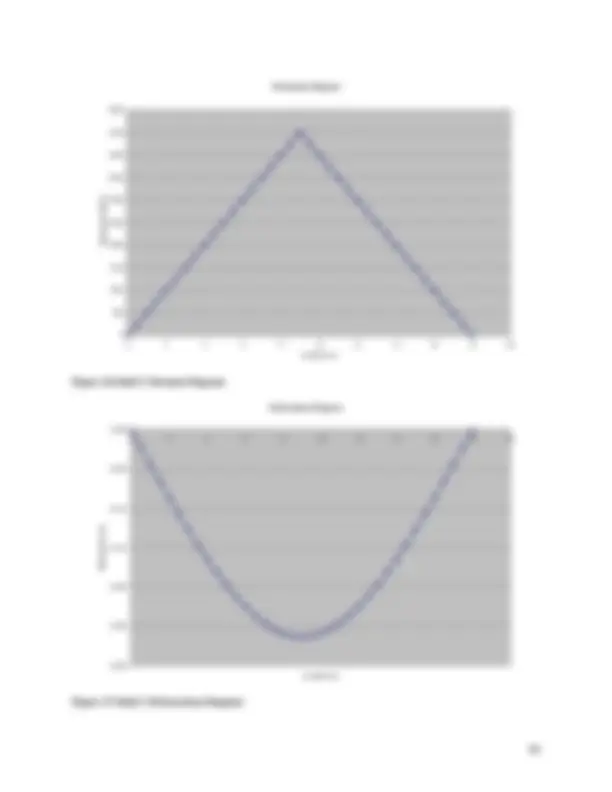
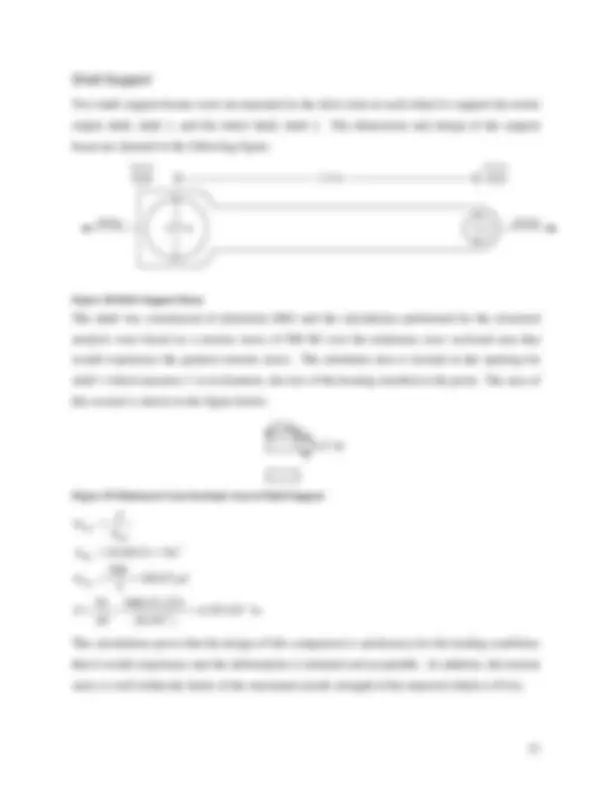
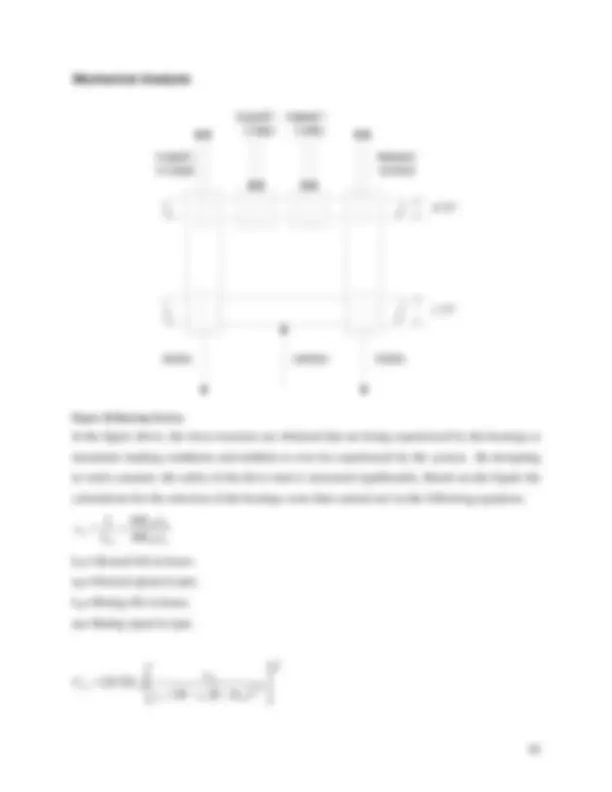
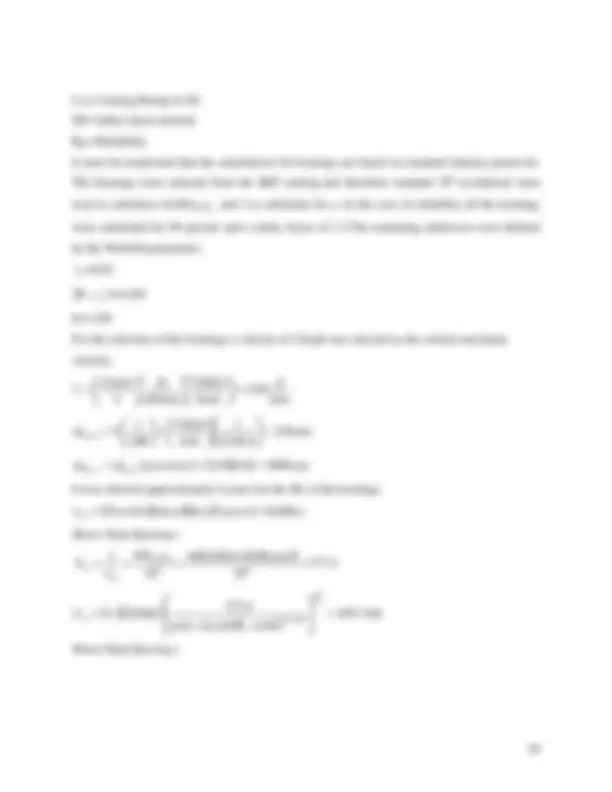
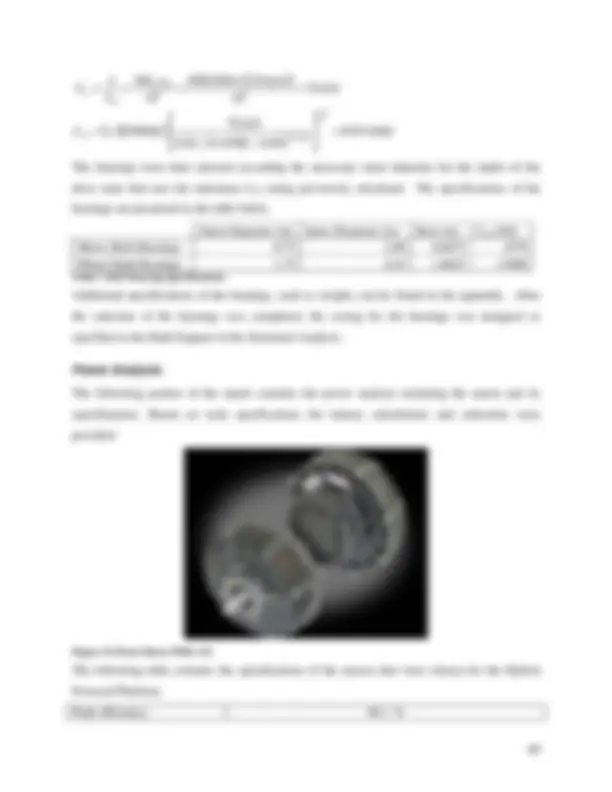
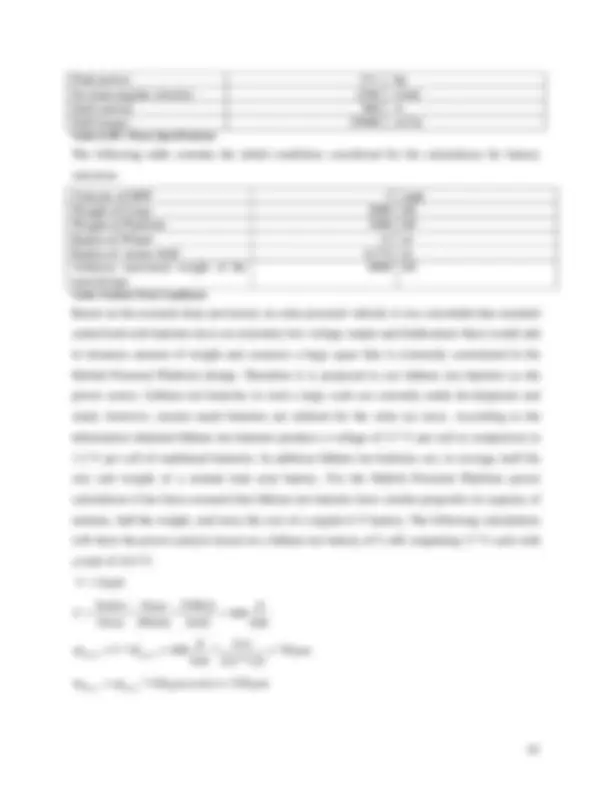
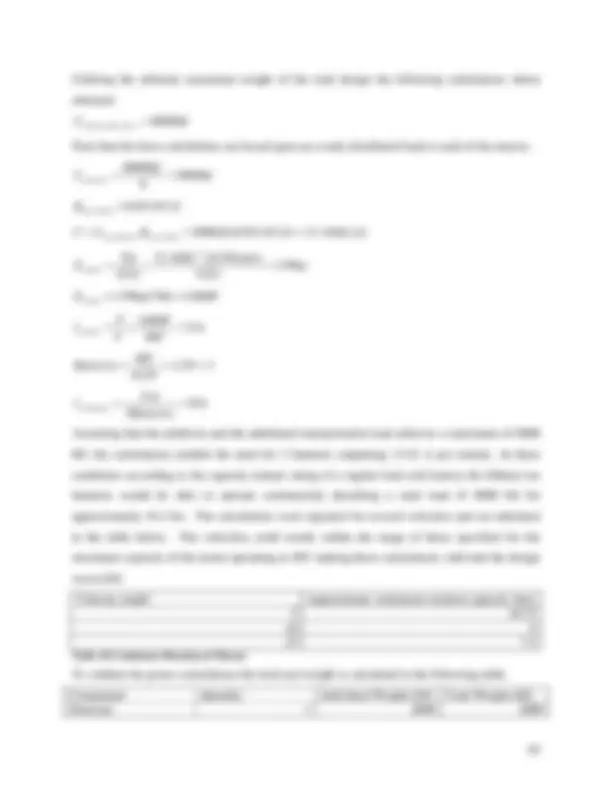
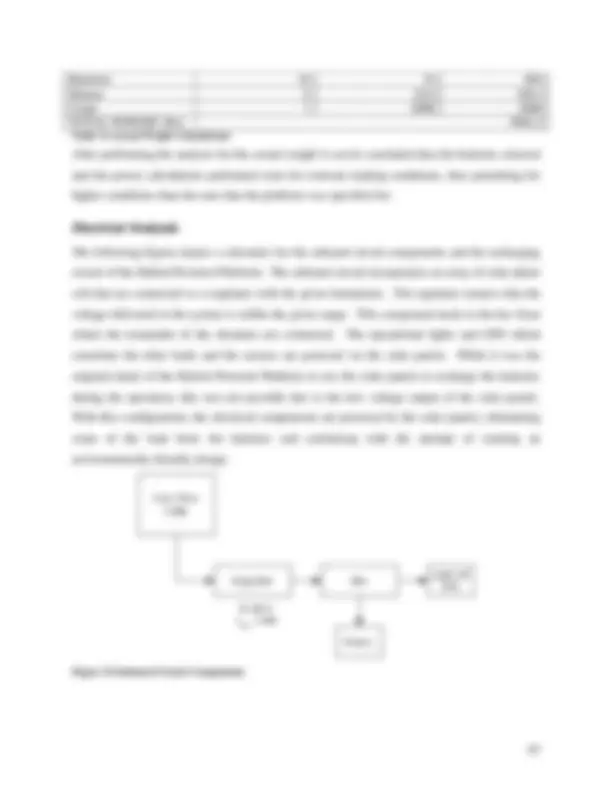
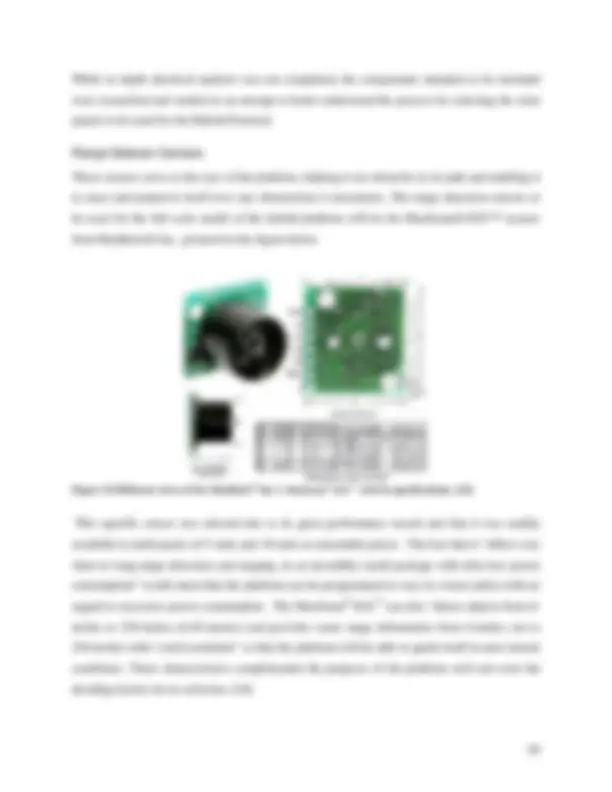
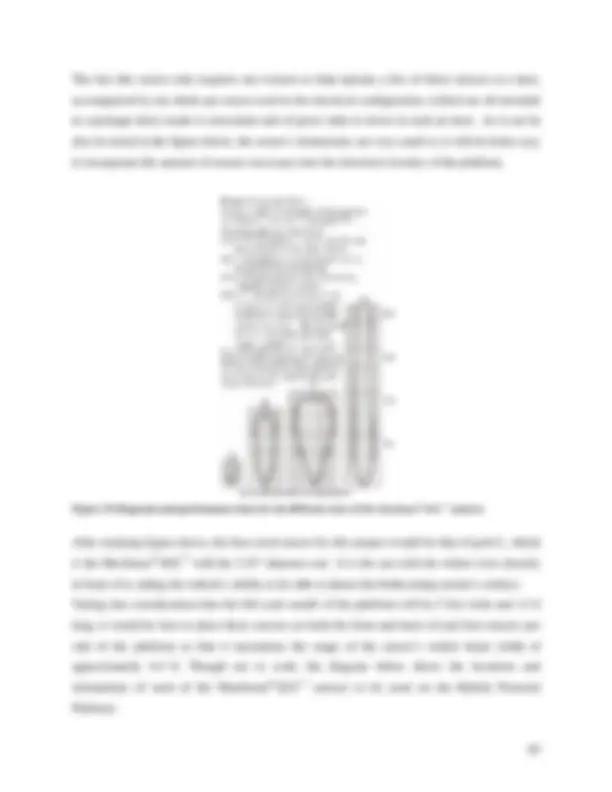
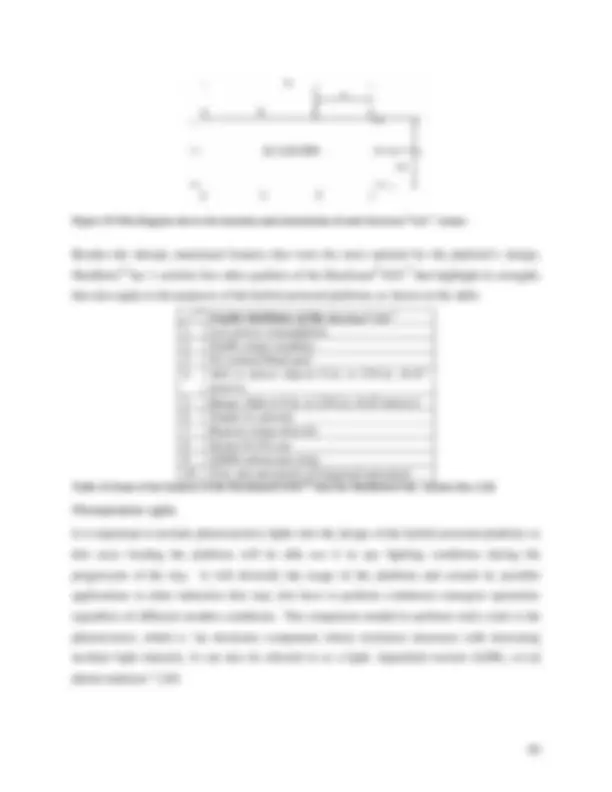
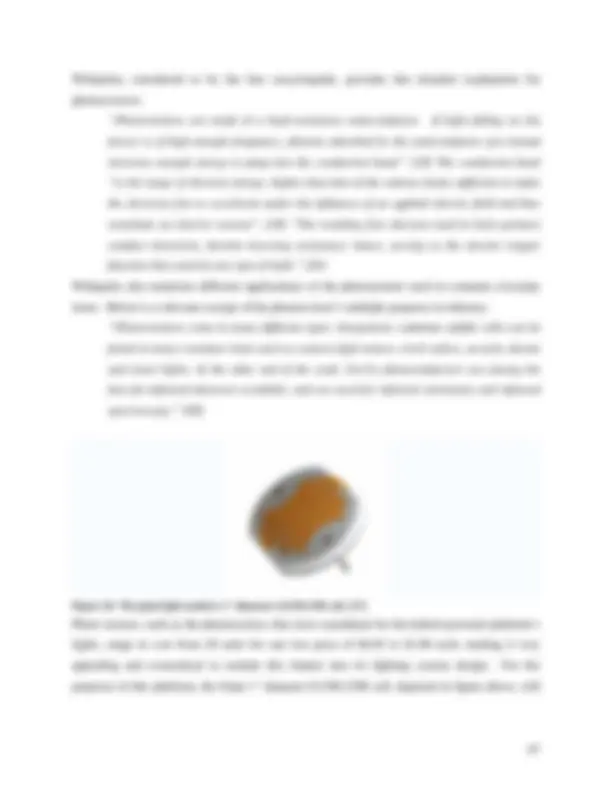
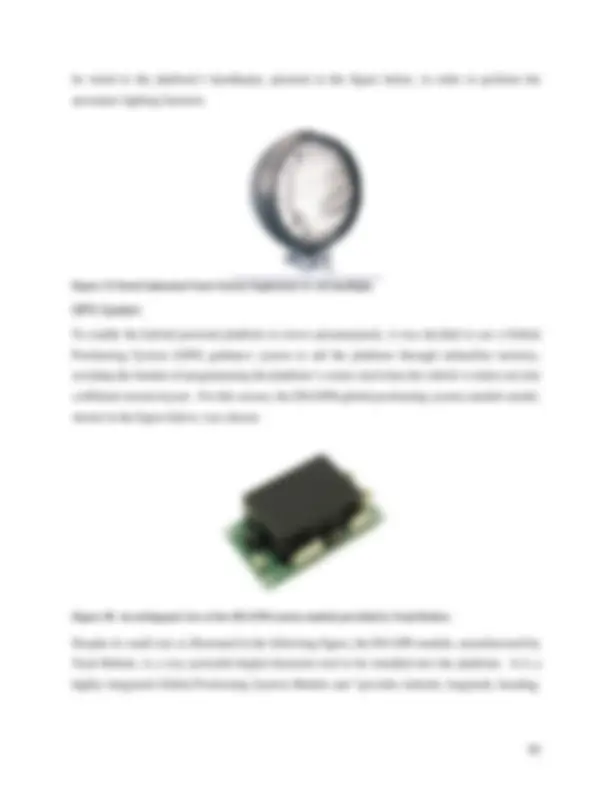
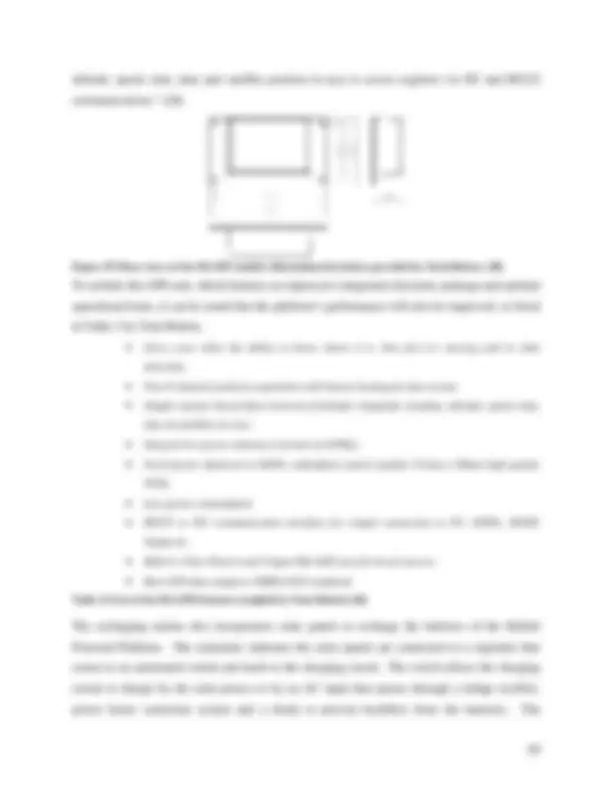
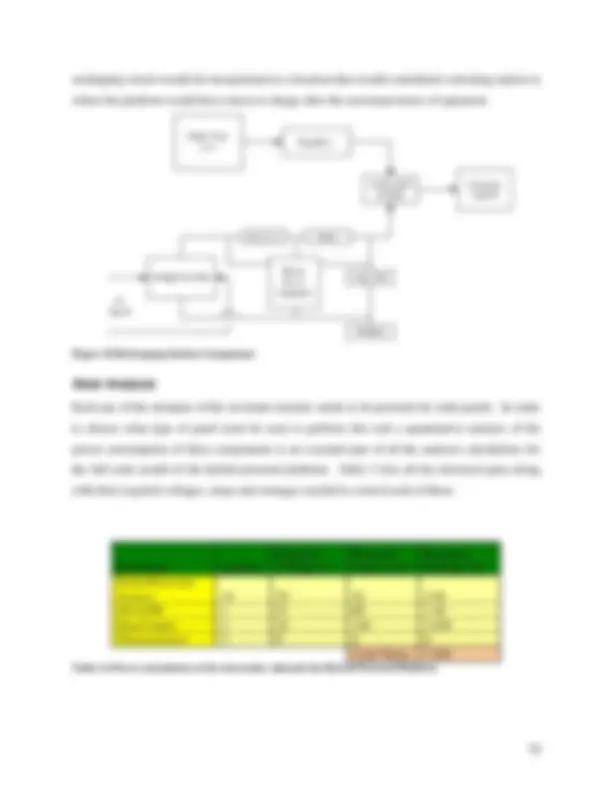
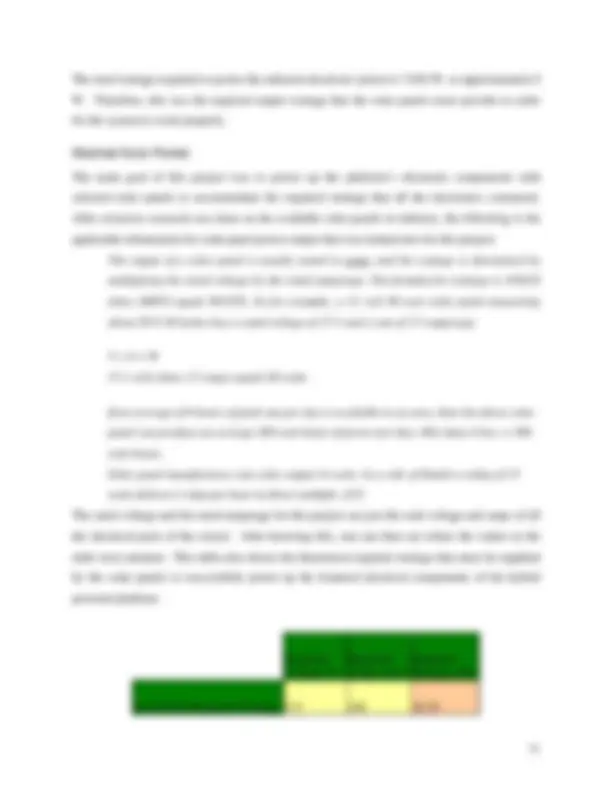
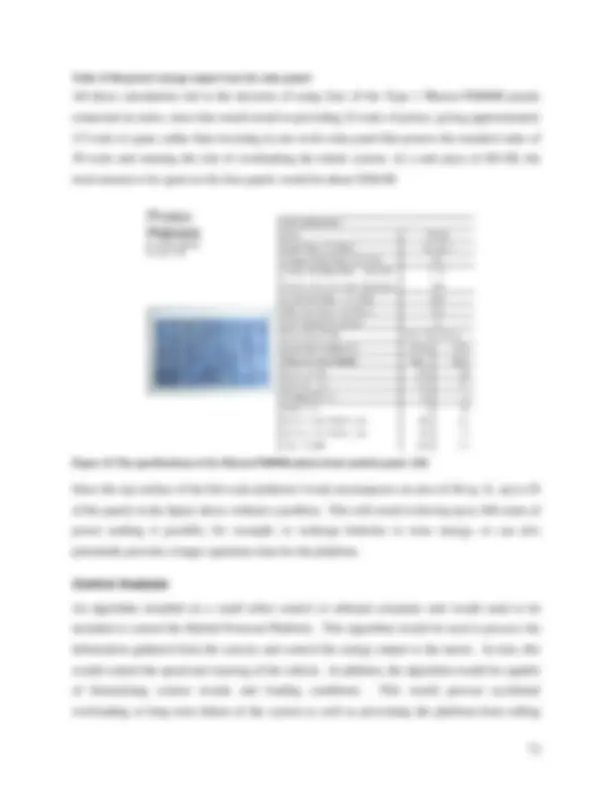
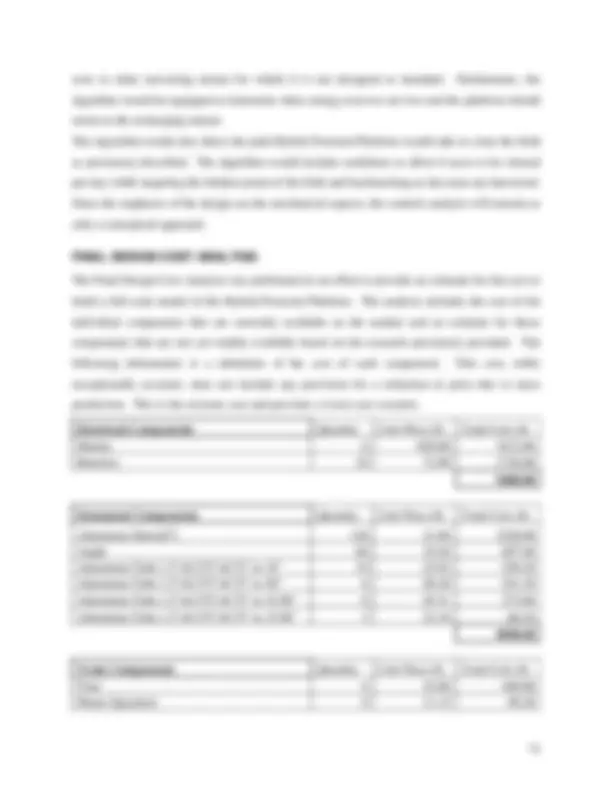
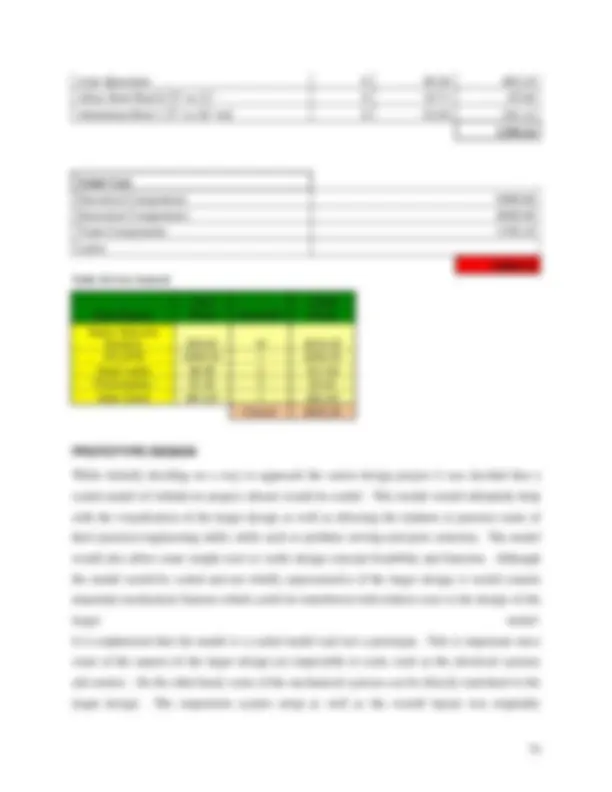
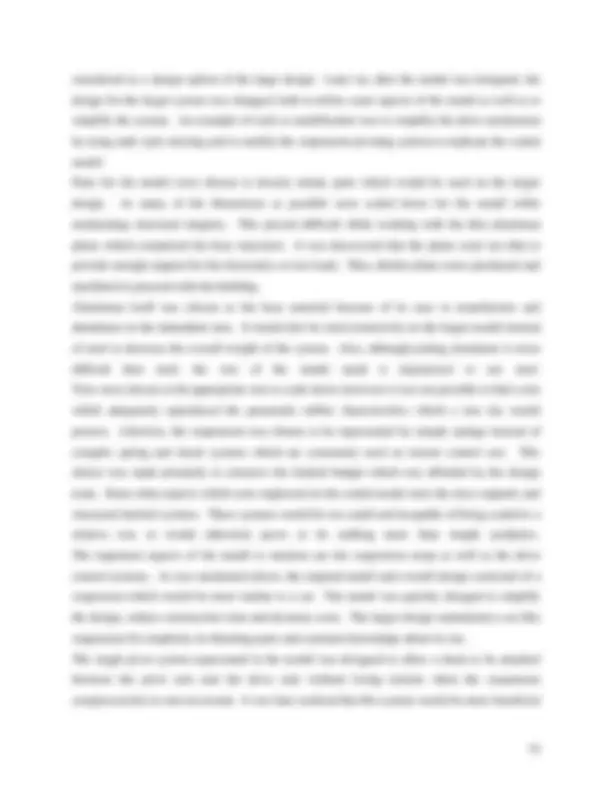
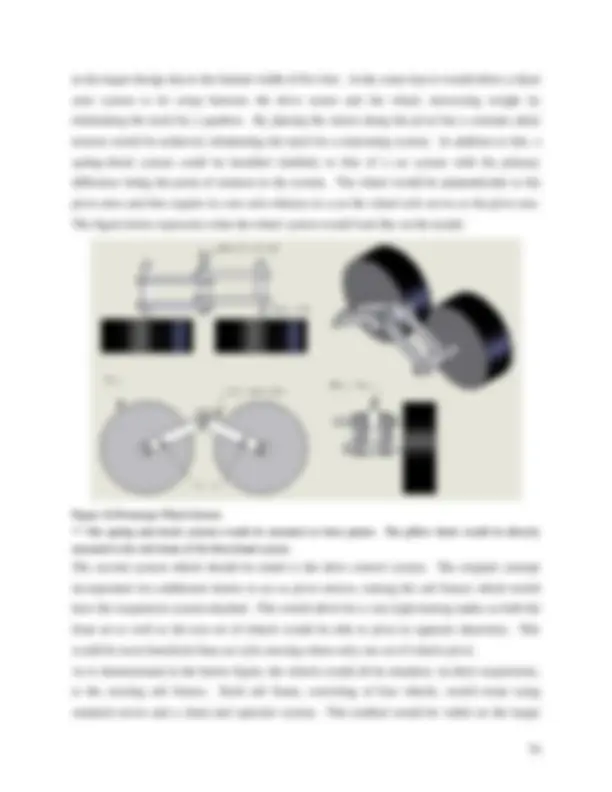
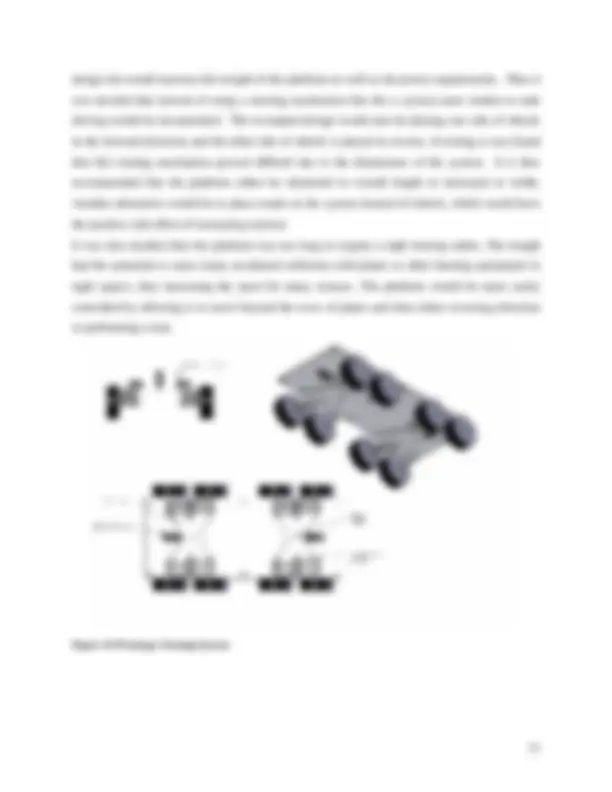
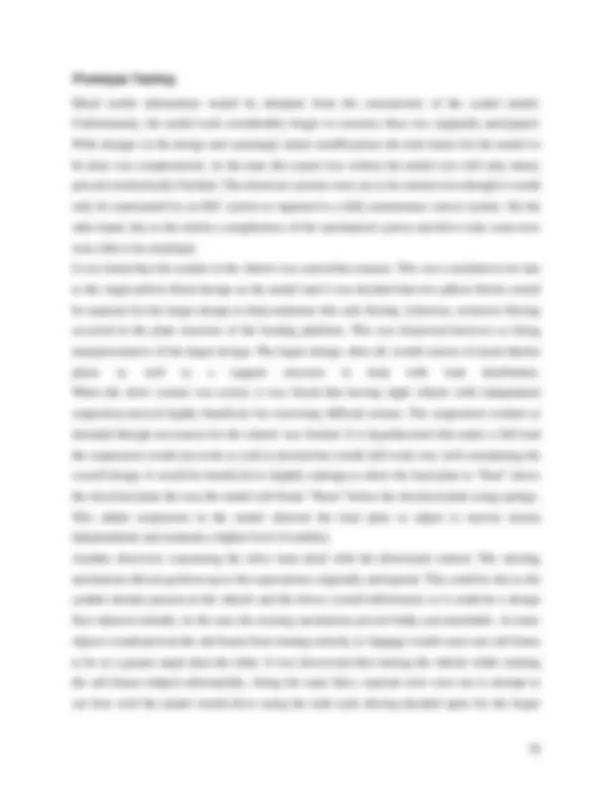
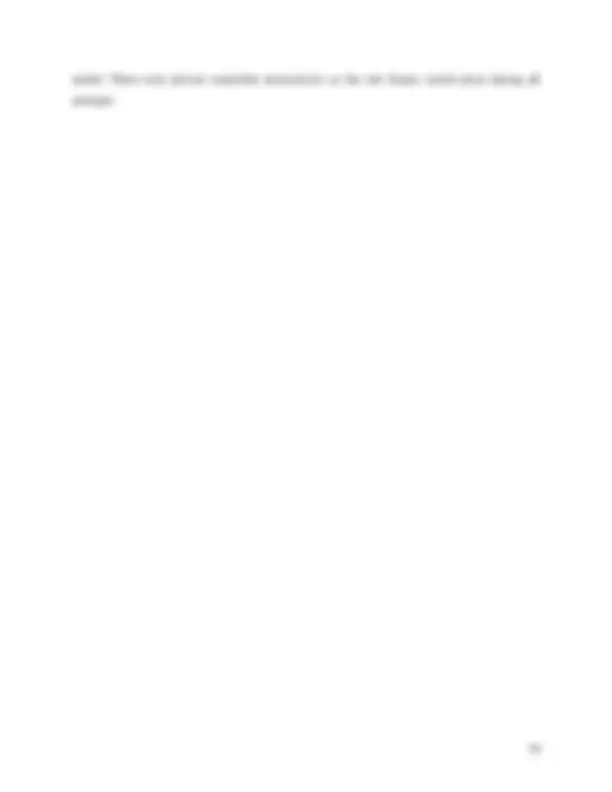
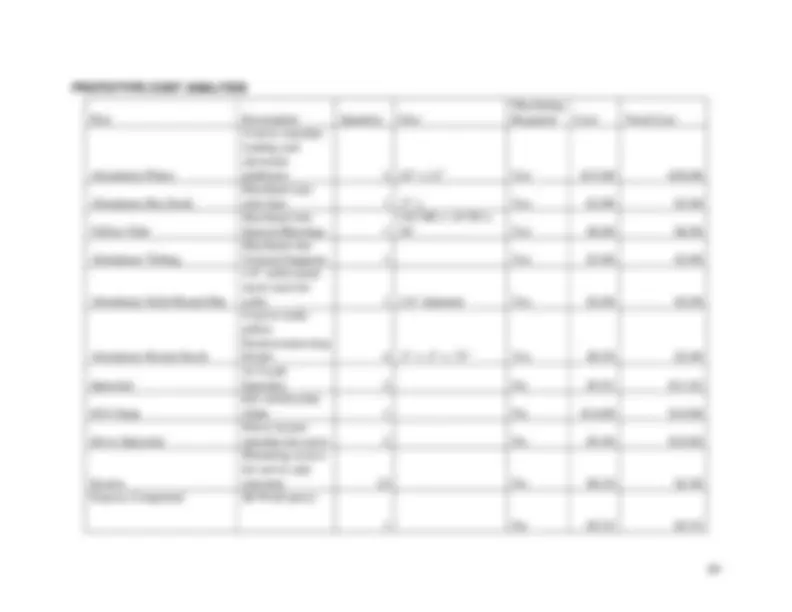
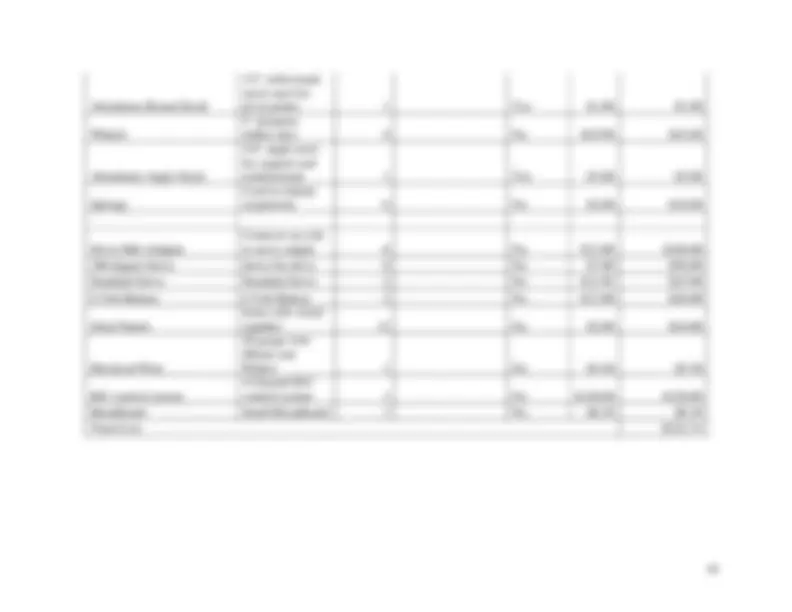
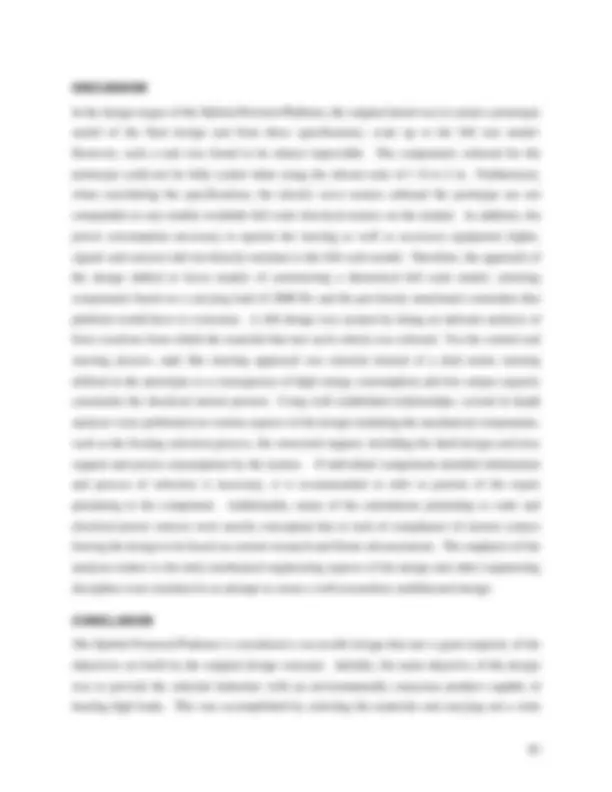
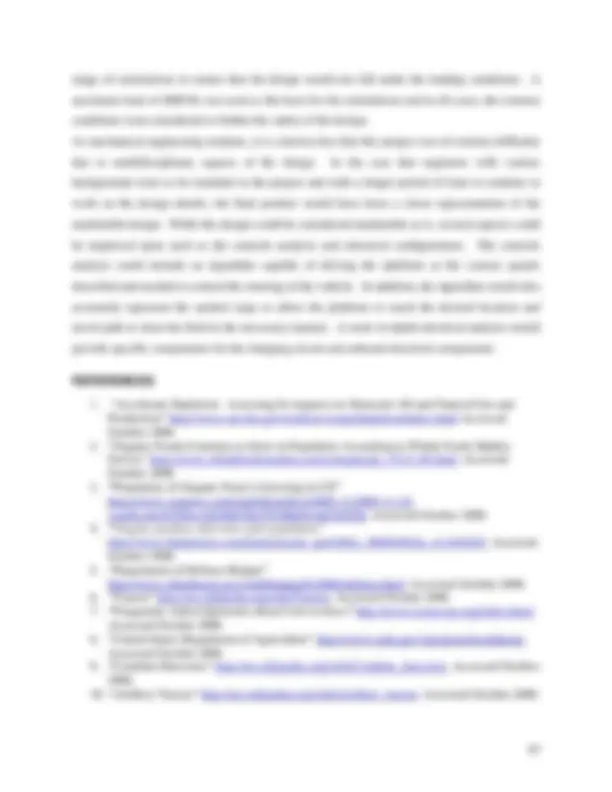
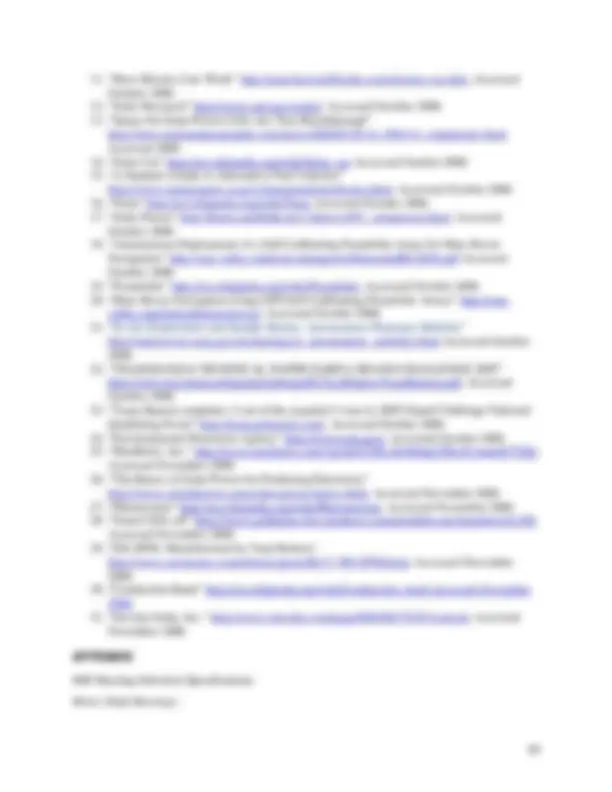
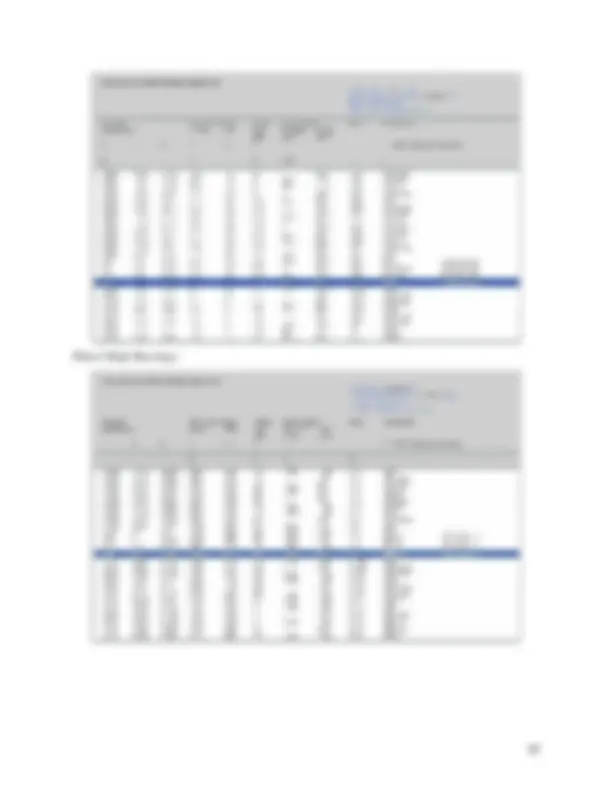
Study with the several resources on Docsity
Earn points by helping other students or get them with a premium plan
Prepare for your exams
Study with the several resources on Docsity
Earn points to download
Earn points by helping other students or get them with a premium plan
Community
Ask the community for help and clear up your study doubts
Discover the best universities in your country according to Docsity users
Free resources
Download our free guides on studying techniques, anxiety management strategies, and thesis advice from Docsity tutors
Material Type: Project; Professor: Tao; Class: Senior Design Proj; Subject: Engineering: Mechanical; University: Florida International University; Term: Unknown 1989;
Typology: Study Guides, Projects, Research
1 / 85
This page cannot be seen from the preview
Don't miss anything!
This report is written in partial fulfillment of the requirements in EML 4905. The contents represent the opinion of the authors and not the department of Mechanical and Materials Engineering.
traditional farms have to be used in greater quantities. Ozone is also known to reduce crop yield posing a serious concern for the farm industry. It is concluded that future designs for transportation vehicles must be considerate of these conditions and incorporate design elements that target remedying this problem. [24] The Hybrid Powered Platform is a direct response to these concerns. A hybrid powered transportation vehicle is the solution to reducing emissions, ozone concerns, low crop yield, water contamination and energy consumption while providing a structurally sound and well engineered platform that would be capable of transporting substantial loads in farm applications. Additionally, the original design could be altered to extend the marketability of the product furthering the use of an environmentally conscious transportation system. Incorporating the Hybrid Powered Platform into standard farm equipment and subsequently as a high load bearing method of transportation for other markets will provide a highly beneficial step in the direction of merging formidable engineered systems with environmental consciousness.
INTRODUCTION
The main objective of the Hybrid Powered Platform was to design a transportation platform capable of bearing a specified load for outdoor applications. The goals of the proposed design included incorporating electrically powered motors, an electric and solar rechargeable array of batteries, a high load bearing capacity, all terrain traction system and a semiautonomous control system. Several designs were considered and a final design was chosen based on satisfying the maximum amount of initial design specifications. The following project is a combination of current technology, readily available components, present day research and the proposal of future technology advancements necessary for the success of the Hybrid Powered Platform. The proposal of such technological advancements arose due to the constraints that current technology posed on the proposed final design. Therefore, the Hybrid Powered Platform is considered highly innovative and truly demonstrating an effort in applying several engineering disciplines and practices to the design. The project has spanned over a time frame of four months in which preliminary designs were considered and researched, a final design was chosen and the necessary calculations were completed to determine the success of the design. A literature survey was introduced to the research phase to account for existing similar designs and as a guide towards including
appropriate specifications for the target markets that can reap the benefits of such a product. Through this process it was further assessed that there exists a need for an alternative fuel transportation platform and that an exact design does not currently exist but similar designs implemented are within the target industries. Alternative designs were given some thought but as previously mentioned the final specifications were intended to maximize the original objectives met. The engineering analysis included structural, mechanical, solar, electrical and control considerations as well as an assessment of safety factors. The safety factors were included to prevent failure in the structure and most importantly to ensure the safety of any bystanders. With budget concerns and as a justification for implementing a new method of transportation, an in depth cost analysis was preformed for the final design based on the cost of the materials and the labor needed to complete a full scale model. However this cost did not account for mass production and therefore can be seen as a worst case scenario. As a final exercise, a prototype of the Hybrid Powered Platform was constructed and tested in an attempt to predict the performance of the full scale model. The process completed was analyzed and several conclusions were drawn based on the entire analysis performed on the design.
Target Industries & Clients
The Hybrid Powered Platform design could be utilized by the following markets: the farming industry, military organizations and any other industries requiring the transportation of cargo outdoors, such as seaports or airports. The farming industry is the client of concentration for this design due to the sensitivity of the products and arising concerns in the state of the earth’s environment. People have also taken to consuming produce that has not been exposed to any pollutants where “according to the 2004 Whole Foods Market Organic Foods Trend Tracker survey released…more than one-quarter of Americans (27 percent) are eating more organic products than just one year ago” thus the platform would further ensure the quality of the crops grown on organic farms. [2] Farms currently use tractors to haul transportation platforms through out the fields. These gasoline or diesel powered tractors much like automobiles produces dangerous exhaust and fuel leaks that can seep into the ground especially in the case that the equipment is not properly maintained. Furthermore with an expansive amount of outdoor land, solar power can also be taken advantage of to lower the dependency of traditional fuels. Since
would prevent the need for an operator consequently reducing the risk for loss of life. Under the conditions of current warfare solar power would be an ideal source of power and reduces the need for acquiring traditional sources of fuel. [5] Seaports and airports are another market that can be targeted by the Hybrid Powered Platform. This outdoor application would experience similar benefits to the previous industries but the design could be altered for a drive and traction system more suitable to an even terrain. Airports currently mobilize luggage using baggage trolleys. The design would eliminate the need for these and the platform could be automated not only to transport the baggage from the terminal to airplane but also between airplanes during layovers. The platform clearly has a wide marketability to formidable industries that could invest in this new environmentally friendly technology. With minor modifications, the platform can be utilized by a wide range of clientele seeking ground transportation.
Additional Initial Considerations In order to determine further specifications for the design, the following information was compiled to establish the load bearing capacities that are necessary the Hybrid Powered Platform. The staggering statistics for the amount of corn harvested previously mentioned proves that to design a platform capable of transporting the crop, the target design must accommodate these extreme conditions. The Iowa Corn Promotion Board/Iowa Corn Growers Association states the in 2005 farms produce 2.2 billion bushels of corn in 12.5 million acres of land per year. Using this basis it was determined that 176 bushels are produced for every acre of land per year while an acre is 43,560 square feet, almost the size of a standard football field. Using the conversion factor where 1 bushel is equivalent to 56 pounds, it was obtained that approximately 9856 pounds of corn are harvested in every acre. The specifications of our model allow for the transportation of 2000 pounds equivalent to 1 ton in each load. Further calculations will prove that the platform would be capable of providing and adequate method of transportation for small to large scale farms. [7] In selecting the maximum speed that the Hybrid Powered Platform should travel, the average traveling speed of a tractor was used as a guide for finalizing this design specification. A tractor travel usually at a speed of less than 1 mph to allow for the working of the land. Tractors reach a maximum speed of 25 mph when traveling on the road. As a result, the Hybrid Powered Platform will be designed for a maximum speed of 10 mph and studied over a range of higher
and lower speeds since the speed on the field is very low and the platform will not be required to travel on the road. [6]
LITERATURE SURVEY
The Hybrid Powered Platform is considered to be a novel design that incorporates existing systems currently used in the farm industry along with new components that were designed particularly for the transportation platform. In an attempt to prove the originality of the design and study how current technology has evolved is now incorporated, this literature survey was compiled. In the following section, the general topics considered essential to the design such as farm equipment, solar, electrical and autonomous vehicles and recharging stations were investigated. In addition, other applications for similar designs were researched as is the case with the military and airport transportation systems discussed and the results promote that the proposed design of the Hybrid Powered Platform in fact will meet the needs the of the target clients. Furthermore, no existing equipment was found to match the specifications of the platform thus deeming the Hybrid Powered Platform to be an innovative and original design.
Combine Harvester
Combine harvesters are currently used in farms to harvest, thresh and clean the crops that have matured. While the combine harvester is not a transportation platform, some of its design elements can be studied since this technology has been used in farms for an extensive period of time. The combine, as it is often referred to, delivers a final product in the form of a seed, grain, and byproduct. In the case of corn the husks are collected by the combine and the nutrients are removed. The original design was created by Hiram Moore in 1834. This design was often very large in scale and drawn by a team of mules or horses. The power for the grain separation was obtained through a bull wheel, a system for haulage that was implemented in early designs. As technology advanced, the combines began to be drawn by a tractor and an independent engine powered the separator.
Tractor
Tractors are commonly used on farms as a mode of transportation for the crops that are harvested. While tractors are readily available, current designs are not as environmentally friendly and thus can the Hybrid Powered Platform is excellent option to eliminate these concerns. Early models of tractors used steam power engines that were extremely unsafe for both the possibility of an explosion or an operator being entrapped by the belt system. As technology progressed gasoline engines were incorporated into the design and gained popularity as the advancement of the design lowered the cost and improved the performance. However, with a gasoline powered engine several problems are encountered when considering the environment in which it is used. Emissions, fuel spills and oil seepage are problems that would be faced by the Hybrid Powered Platform.
Figure 2-John Deere 8110 Farm Tractor The current design of a tractor also implements two large driving wheels usually located in the rear of the vehicle and two smaller wheels towards the front. The rear wheels of the vehicle are the driving wheels and are mounted on a single axle slightly behind the location of the operator. The front wheels are used to steer the vehicle and are located beneath the engine compartment and are approximately half the size of the driving wheels. The drive and braking system are operated by pedals. There are two independent brakes for each side of the tractor and both must be engaged by the driver to bring the tractor to a stop. This system is incorporated to improve upon the maneuverability and traction of the tractor. Two additional pedals are used as the throttle which is manually engaged and the clutch for the transmission. The design of the Hybrid Powered Platform will incorporate an eight wheel design with an independent brake system to
account for the various terrain conditions as a safety precaution that will be activated by light sensors. Modern tractors now use diesel engines ranging from 18 to 500 horsepower which enable the tractor to pull heavy loads and incorporate other attachments such as cutters and shredders. These tractors incorporate manual transmissions which allow the operator to vary the ground speed and power depending on the terrain that is encountered. Variable speed transmission further allows for more speed control to perform the necessary operations by the tractor. Tractors also have the ability to transfer power to external equipment as well electricity and hydraulic fluid. Tractors have also been equipped with rollover protection since this was a source of injuries among the operators of the tractors. These design specifications are not needed in the Hybrid Powered Platform since the dimension provide stability and there is no need for a transmission system [6]. In other applications, the military uses a version of a tractor for artillery transportation. The tractor is capable of towing artillery either as a wheeled or tracked tractor. This presents an alternate market for the Hybrid Powered Platform. Several models of artillery tractors include the White Scout Car, the Canadian Military Pattern Field Artillery Tractor and the Land Rover
Figure 3-US White Scout Cars (left) & Land Rover 101 (right) The aviation industry also incorporates outdoor transportation. As shown below a tractor pulls several baggage carts where passenger luggage is stored and transported from the terminal to the
naked eye. Such research suggests that plastic solar cells could potentially double the efficiency of the best current solar cells in the market. "The sun that reaches the Earth's surface delivers 10,000 times more energy than we consume," said Ted Sergeant, an electrical and computer engineering professor at the University of Toronto. Sergeant is one of the inventors of the new plastic material. [13] “If we could cover 0.1 percent of the Earth's surface with (very efficient) large-area solar cells," says Sergeant, "we could in principle replace all of our energy habits with a source of power which is clean and renewable." [13] The novel part of such research does not lie in harnessing the power of sun’s visible light; the study suggests the capability of harnessing the infrared lighting so even in a cloudy day such cells could generate electricity. In addition the suggestion has been made of the possibility of spraying such plastic in virtually any materials even clothing. [13]
Solar Vehicles
Solar cars are currently in the development stage and they have not yet achieved the status of commercial or practical forms of transportation. These are mainly utilized in competitions, such as the World Solar Challenge and the American Solar Challenge, which are events sponsored by government agencies or private entities to develop and promote alternative energy technology. Solar cars utilize energy obtained from solar cell arrays on the surface of the car that converts sunlight into electricity and even tough they successfully operate at somewhat high velocities and can operate without sunlight certain distances. The structure is generally fragile, of big proportions and can only transport a very limited amount of weight. [14] From these limitations it can be inferred that current technology does not allow electric commercial cars to be fully powered by solar cells. The solar power produced in current solar cars is about “1,500 Watts only enough to power an electrical drier.” [15] The power produced by the solar cells is not enough to run heavy vehicles, for example the CalPoly Pomona car is very light weighing less than 400 pounds and it is extremely fragile. [15] In the 2005 World Solar Challenge the Nuna 3 constructed by Delft University of Technology students was one of the favorites achieving a pre-race test speed of 130km/h and averaging about 103km/h in the actual race. This design utilized very efficient solar cells usually used to power orbital satellites [16]. Such design used the following specifications as well as an intricate aerodynamic design:
Dimensions 5 x 1.8 x 0.8 m (l x w x h) Weight < 200 kg Air Friction Coefficient
0.07 Comparison: this value is between 0.25 and 0.35 for modern cars Solar Cell Efficiency
26% This is a very high efficiency; for comparison the most efficient solar cells yet created under laboratory conditions were only 6% more efficient than this. The material used to fabricate these cells was a compound containing gallium arsenide. The efficiency of most panels is 15% Motor Efficiency
97% (^) Comparison: an average electromotor has an efficiency of 85%
Battery Capacity 5 kWh Battery Weight 30 kg
Comparison: an ordinary 24 kg car battery has a capacity of 80 Ah, which equals 1 kWh
Table 1-Nuna 3 Solar Powered Car Specifications [16]
Recharging Stations
Since the design for the Hybrid-Powered Platform is not aerodynamically friendly, it is intended to carry about 2000 lbs, in addition to the structural and battery weight, and has eight on board motors with a large need of power input in order to function correctly. It has been noticed that for such short term development of the platform the idea of recharging the whole system with on board solar panels is not feasible. Therefore the onboard paneling will be utilized as an exercise on how the solar energy works and the engineering restrictions that an environment friendly project entails as well as to power and recharge the battery of the small electronics used for the platforms such as the controllers and sensors. As an alternate solution it is suggested to create a recharging station for the batteries that power the motors. Similar arrays to the one that will be described but of simpler nature are suggested to create the recharging station. This could possibly be designed by future teams interested in the project. “This is the solar array at the Santa Monica, CA Civic Center. Here, an array of Photovoltaic Cells gets a constant bath of sunshine just a half mile from the beach. The electricity generated by the cells fuels the electric car chargers below. This array can charge up to seven electric vehicles simultaneously. It has two inductive Magna-chargers, three 110V outlets, and four 220V
Lithium ion batteries are the batteries of choice since they are light weight highly efficient. When the car is switched on the batteries deliver power to the motor which in turn powers the drive train of the vehicle and remaining components. Similar techniques will be applied to the Hybrid Powered Platform but in a more simplistic manner since the only the load for the batteries will be the six on board electric motor [11].
Autonomous Vehicles
The project Autonomous Deployment of a Self-Calibrating Pseudolite Array for Mars Rover Navigation project was founded and developed by the Aerospace Robotics Laboratory (ARL) at Stanford University to explore the advantages of self calibrating pseudolite array rover navigation, an alternative to the GPS navigation systems [19]. “Pseudolites are most often small transceivers that are used to create a local, ground-based GPS alternative. This is also known as a Local Area Augmentation System (LAAS).” [19] This technology will enable autonomous rovers to navigate themselves within a local environment rather than depending on the planetary constellations, allowing future rovers to be able to theoretically drive on any planet. “By utilizing bidirectional GPS transceivers (incorporating separate GPS pseudolites and GPS receivers) deployed in a ground-based array, the SCPA [Self-Calibrating Pseudolite Array] can provide all the benefits of satellite-based Carrier-phase Differential GPS (CDGPS), such as drift- free, centimeter-level, and three-dimensional positioning, without requiring a satellite constellation on Mars. Relative geometry change by moving the rover enables the SCPA to self- calibrate both the array locations and the rover trajectory to centimeter level accuracy. This self- calibration capability of the SCPA overcomes the difficulty of autonomous robotic deployment of the pseudolite-based navigation system on Mars, eliminating the need for accurate a priori position information or precise placement of the array.” [18] This specific article describes a trial run of the SCPA using the K9 Mars rover platform performed on the Marscape at NASA Ames Research Center. It was evident that they were able to successfully demonstrate that when the rover was “merged with an obstacle-avoidance system, the SCPA would support path planners for both short and long traverses, enabling the rovers to go precisely to and from any specific science targets, a critical capability for future sample-return missions. Its real-time continuous positioning would also be suitable for feedback-control systems, reducing the number of command cycles required to drive rovers…the SCPA is capable
of surveying autonomously the pseudolite locations after the deployment, thus eliminating the need for accurate a priori position…This self-calibration capability makes the SCPA literally “self-deployable,” overcoming the difficulty of autonomous robotic deployment of the pseudolite-based navigation system on Mars.” [18]
Figure 7-A Self-Calibrating Pseudolite Array (SCPA) deployed over a dry lakebed area in the “Marscape” at the NASA Ames Research Center
Figure 8-An illustration of the typical set up for the Self-Calibrating Pseudolite Array (SCPA) Twin rovers Spirit and Opportunity have been developed by NASA with the “Sojourner's "rocker-bogie" mobility system [that] was modified for the Mars Exploration Rover Mission. To account for the extreme difference in weight and center of gravity from Sojourner, the mobility system on the Mars Exploration Rovers is in the back of the vehicle. The wheels are, naturally, larger and have evolved in design. Each wheel is approximately 26 centimeters (about 10 inches) in diameter and has a unique spiral flecture pattern that connects the external part of the wheel with the spoke to absorb shock and prevent it from transferring to other parts of the rover.” [20]
Figure 10-Team Banzai used a VW SUV as their all terrain vehicle for the 2005 DARPA Challenge “Team Banzai went 1 for 4 during the regular rounds to qualify for the special fifth round on the last day. [They] had a near perfect run in the morning and just needed to finish the afternoon run to qualify for the Finals. Unfortunately, [Team Banzai’s] over-conservative driving strategy caused Dora to think she was boxed in by a single traffic cone, thus ending her run for [the] $ million.”[23] “Team Banzai [was] a privately funded effort by Banzai Research Institute to develop a fully autonomous vehicle capable of traversing long distances over extreme terrain. [The] vehicle [was] a luxury SUV with off-road racing capabilities. Using object-oriented technologies, [they] developed custom software for three Mac mini computers to process data from various sensors and drive the vehicle-control actuators. In addition to operating autonomously, [the] vehicle has a ‘cooperative driving’ mode that allows human and computer to share in controlling the vehicle as co-drivers.” [22]
Figure 11-Three Mac mini computers to process data from various sensors and drive the vehicle-control actuators Computers inside the car control electronic pistons and belts to regulate the steering wheel, brake and gas pedals, and gear shifter. The car follows a series of GPS waypoints that define the course boundary and periodic check points that ran throughout the course terrain. Various video cameras, radars, sonar, and lasers are used to estimate what the environment was like and what obstacles it encountered. [22]
During the design phase of this project a number options were considered for the construction and power and drive systems of the Hybrid Powered Platform. The following summaries discuss several of the main ideas and concepts that were thought to be incorporated into the platform’s specifications prior to finalizing any decisions. Upon completing this phase, the final design was established while intending to meet the objectives set forth by the original concepts.
Power System
The original intent of the power system included on board the Hybrid Powered platform called for a battery array to be completely rechargeable by solar power. The design included the solar panels placed on the edges of the loading plane or to be designed as fully retractable and to emerge in and out of the main body of the platform. This concept had to be modified and redirected due to the amount of panels required to output the needed voltages for the motors. This was determined after research on the power produced by solar panels was conducted and the findings indicated that an area of 1000 m2 of panels would only produce a maximum of 62 volts of electricity, making the idea of recharging all batteries on board implausible. Due to the size limitations of the platform, having to incorporate such a large number of many panels into the design would be too heavy and too impractical for the applications of this platform. Therefore, the final design will include solar panels to power the electronic features, such as a GPS system and motion sensors. Another idea that was contemplated was the use of nickel cadmium batteries for the hybrid powered system. These resulted to be too heavy and would not output sufficient voltage to efficiently power the system as a whole. Although the nickel cadmium has great rechargeable capabilities, it would add an extreme amount weight to the overall structure of the platform. These results led to the decision to use lithium ion batteries. The lithium ion batteries are half as heavy as nickel cadmium batteries, have a better output voltage and are also rechargeable, hence providing a superior alternative.
Structural System
Among the structural concepts that were considered, I-beams were included as part of the support system for the loading plane of the platform. These are a simplistic alternative for handling considerable loads and were a solution for 18” separation between the platforms.