
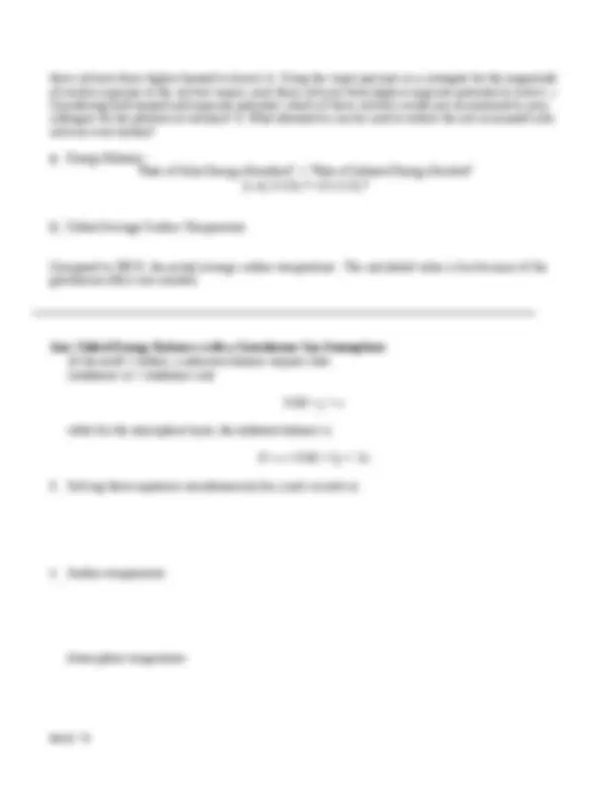
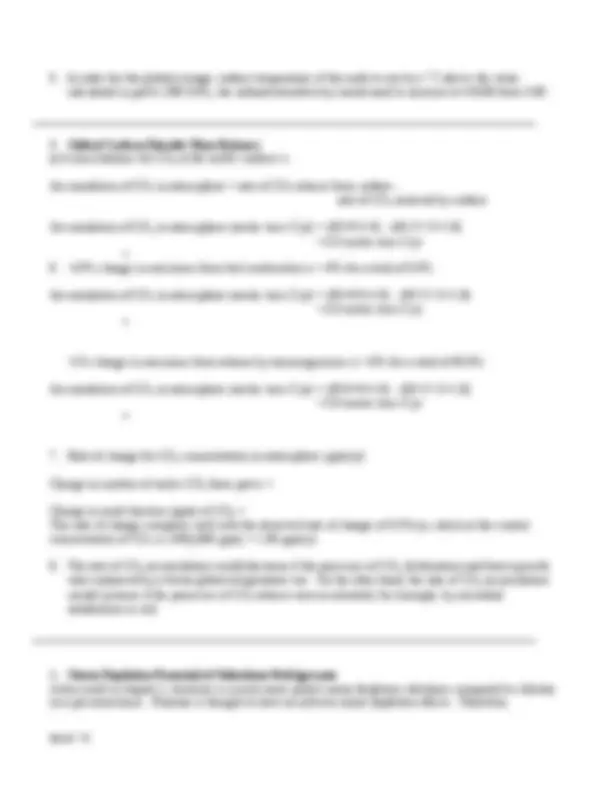
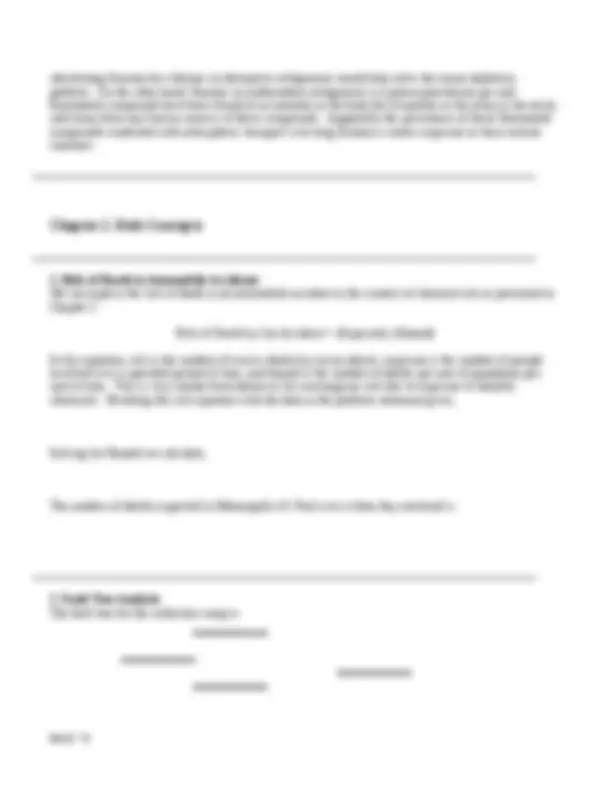
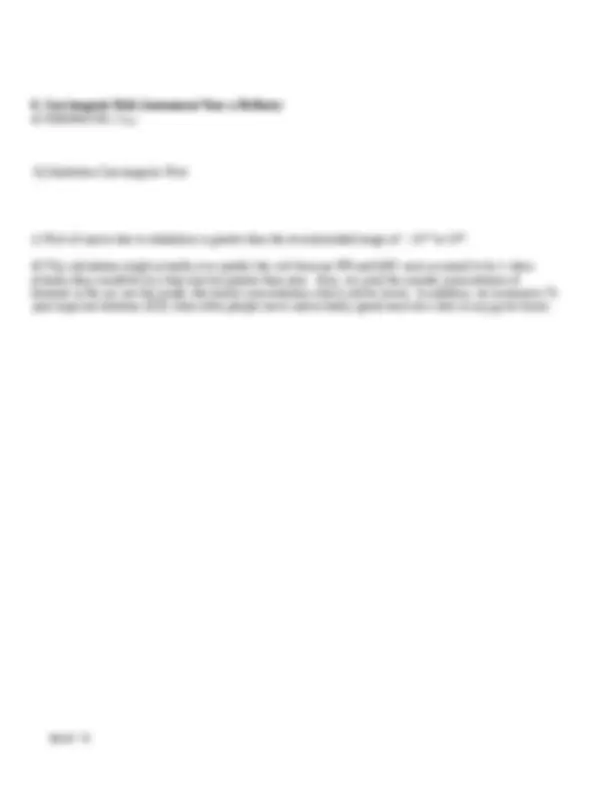
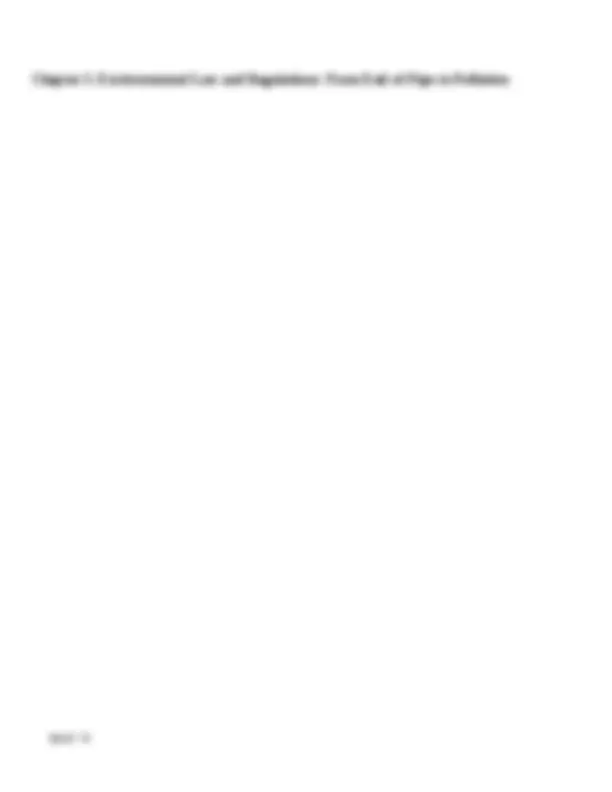
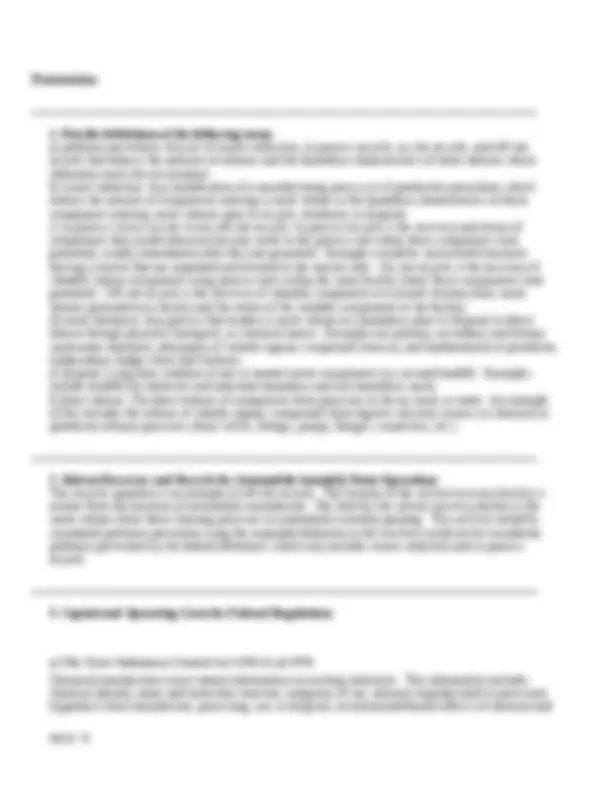
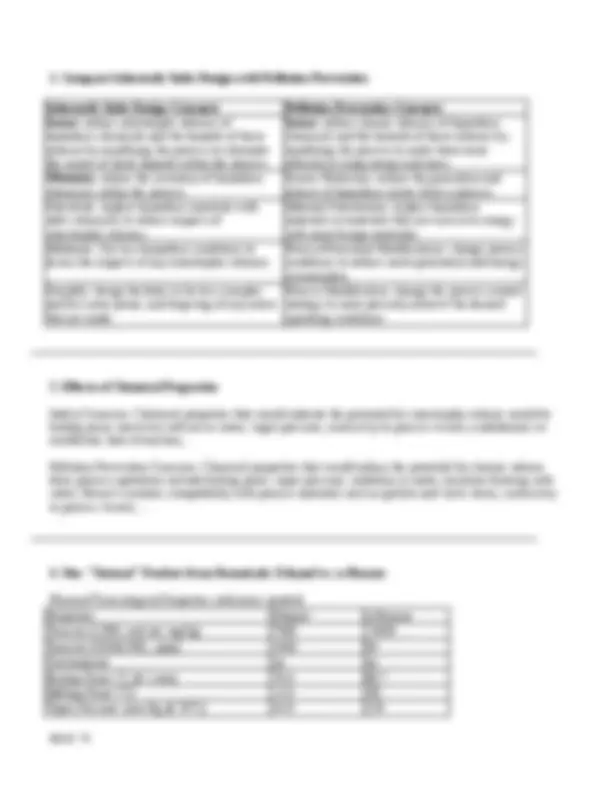
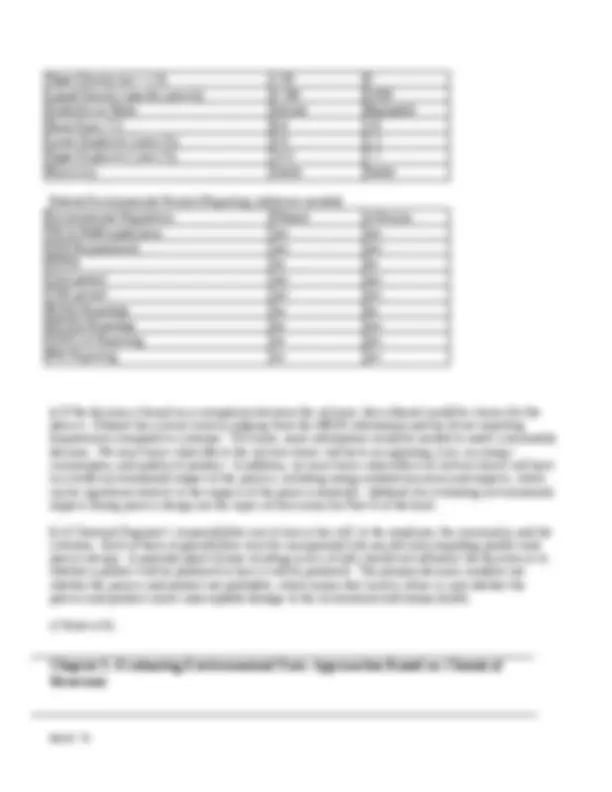
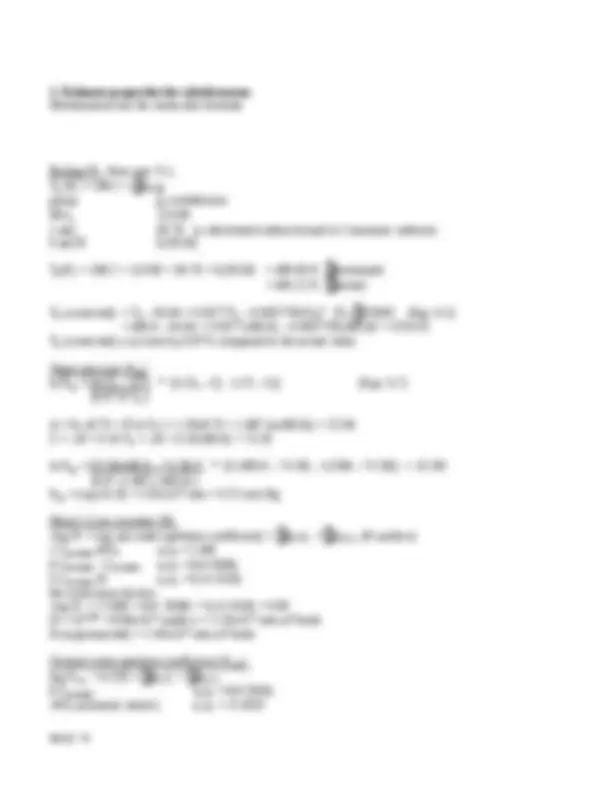
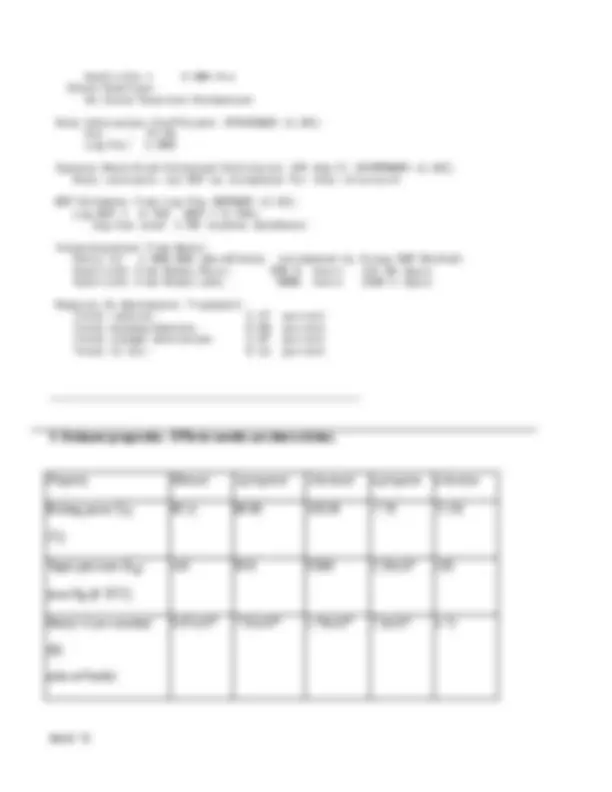
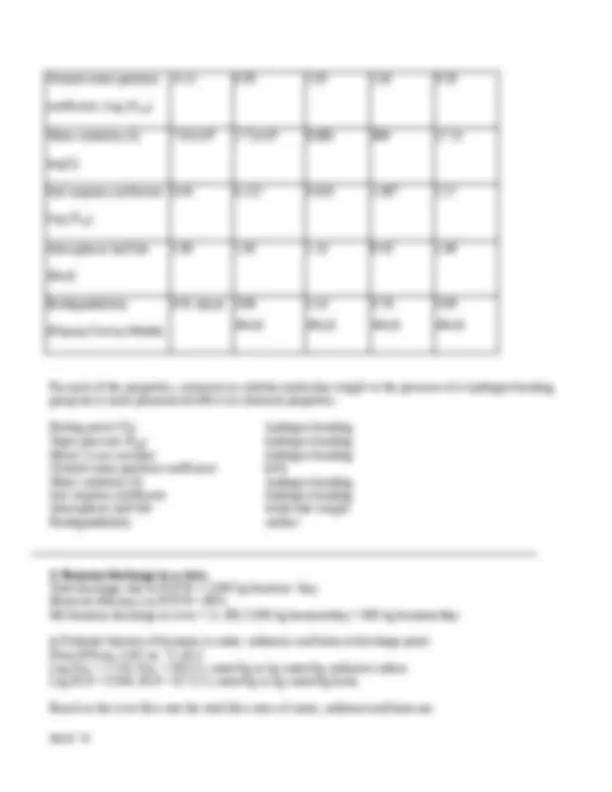
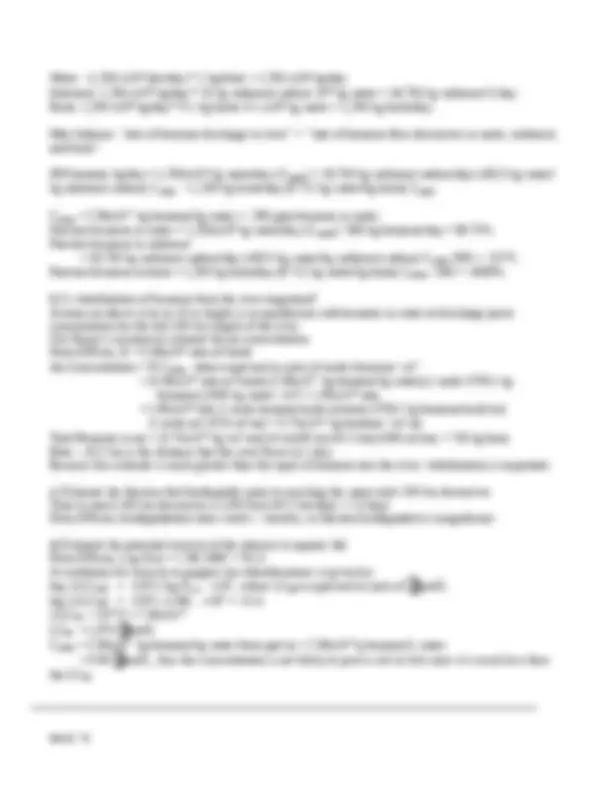
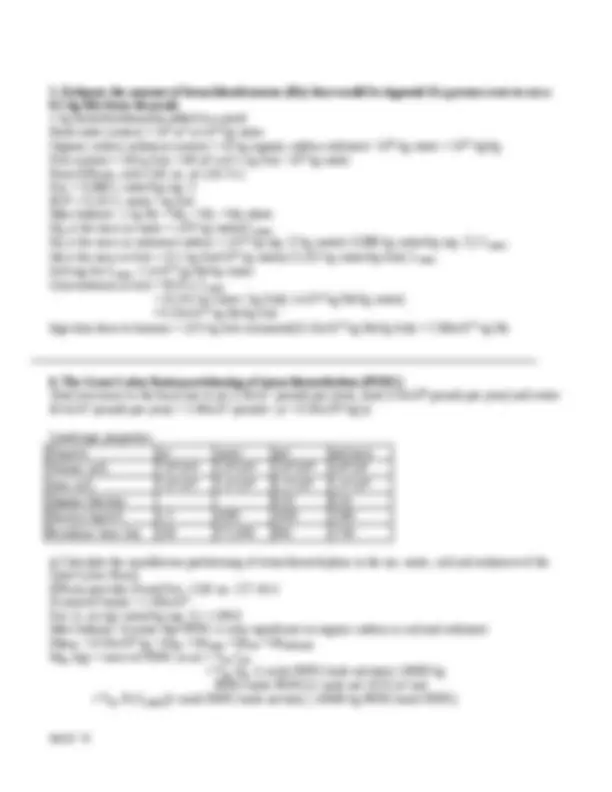
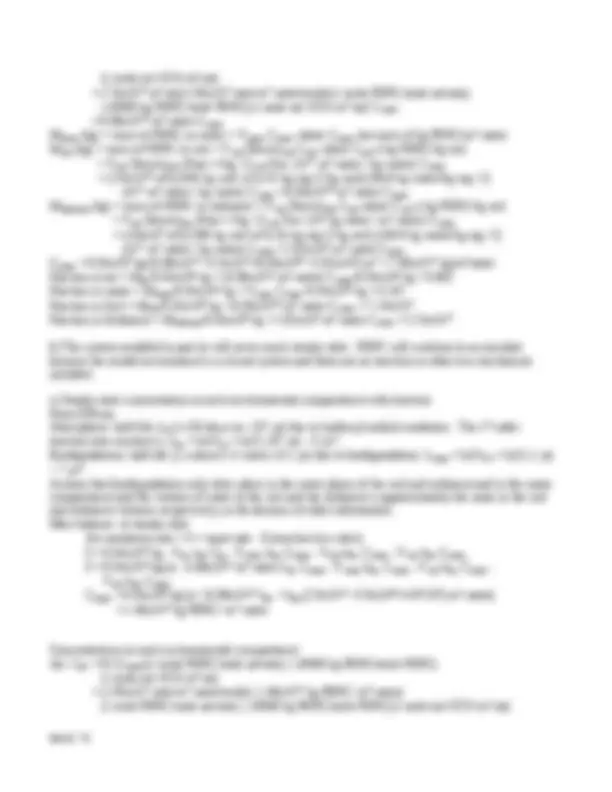
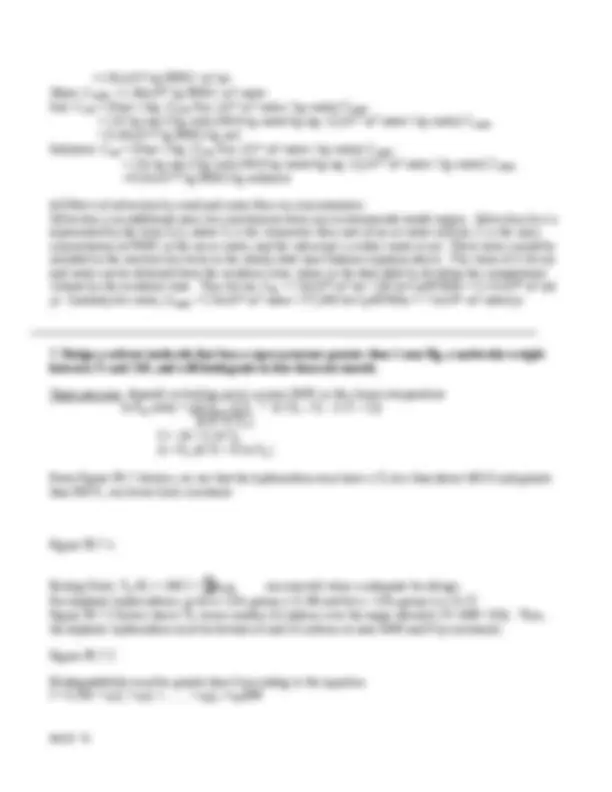
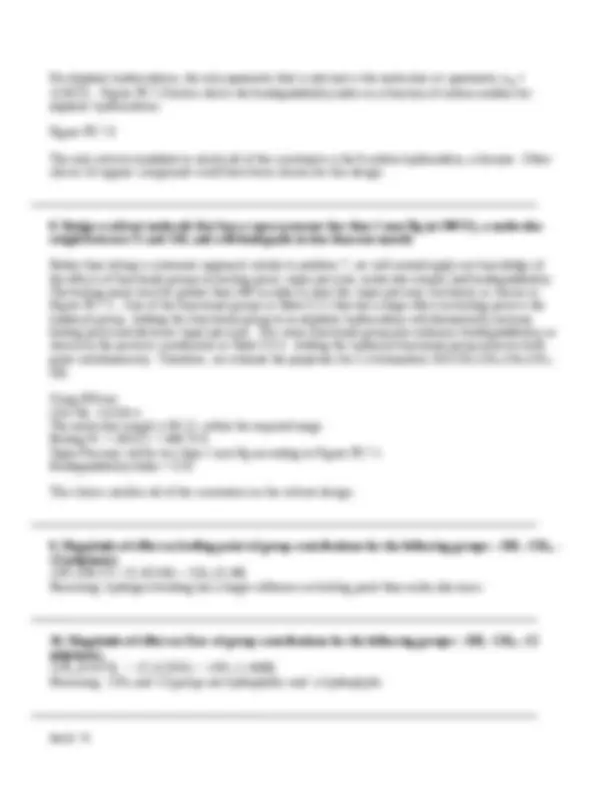
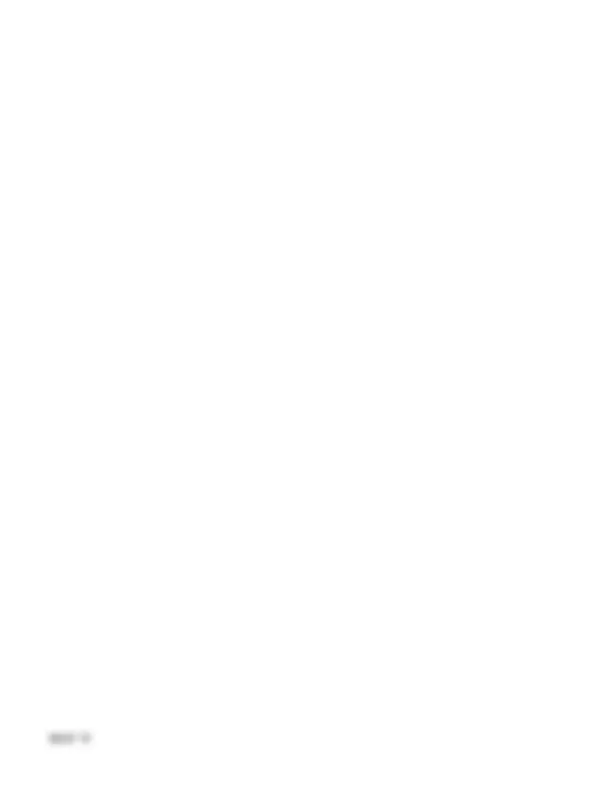
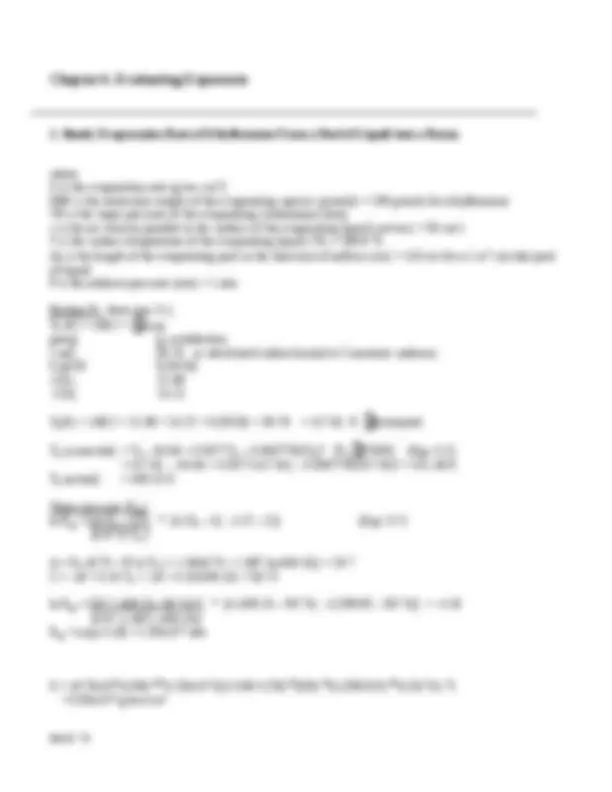
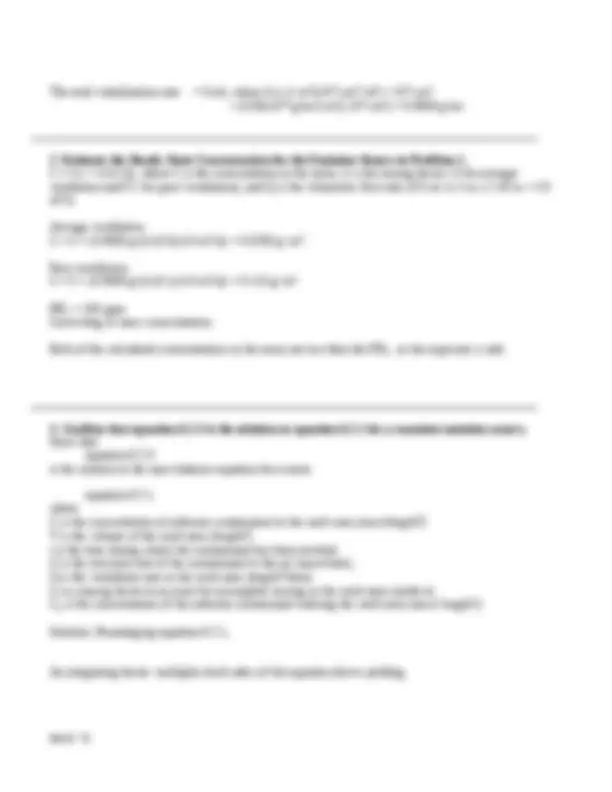
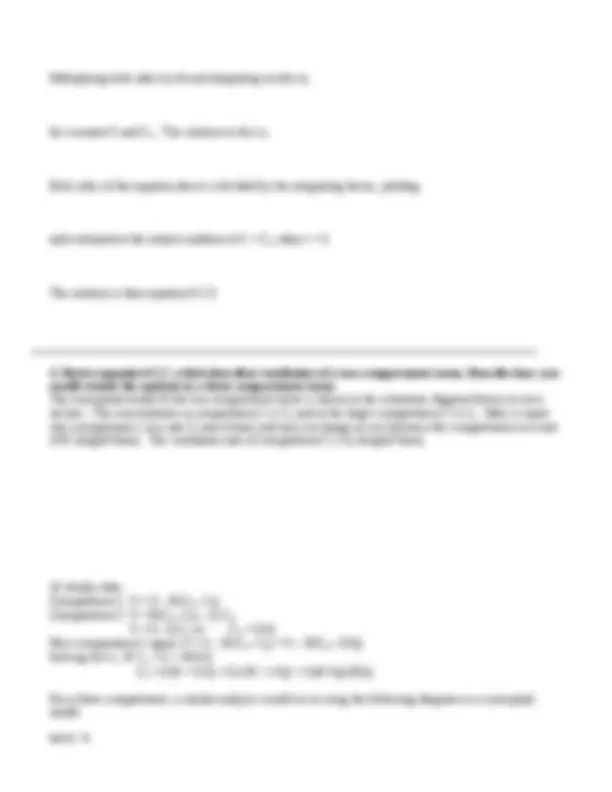
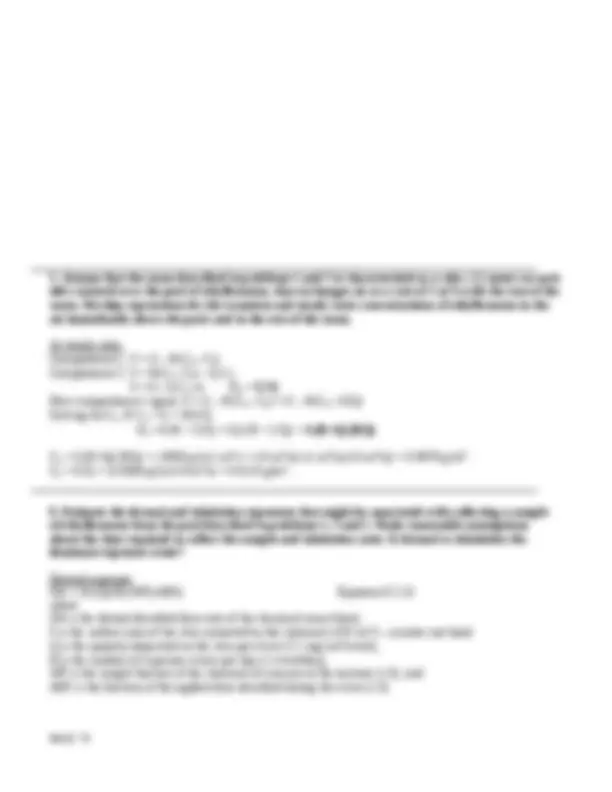
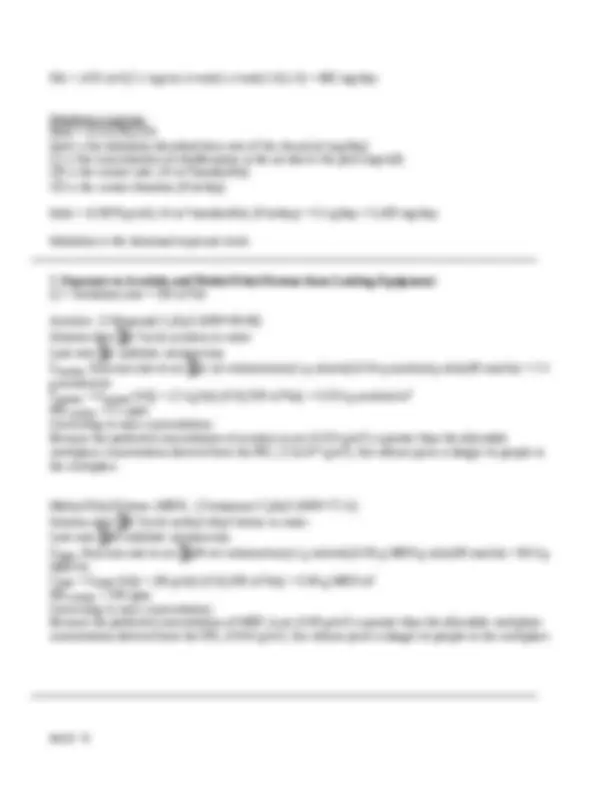
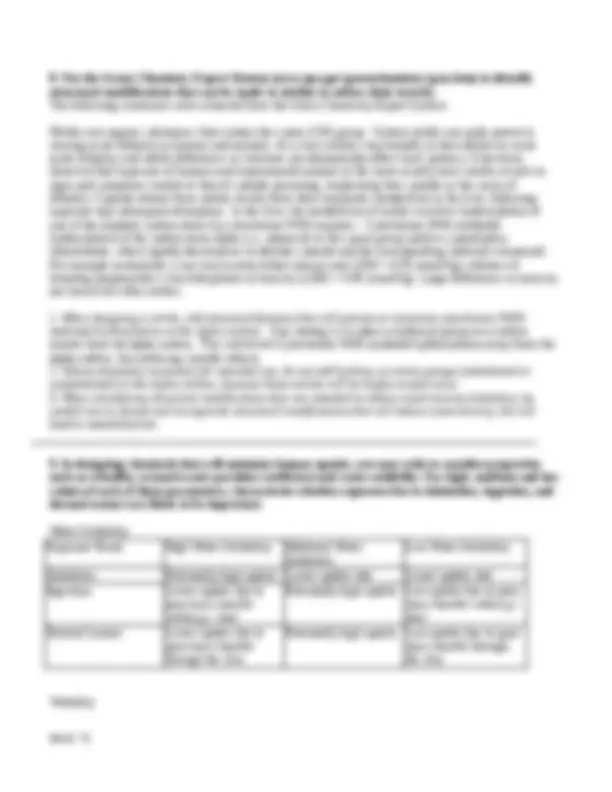
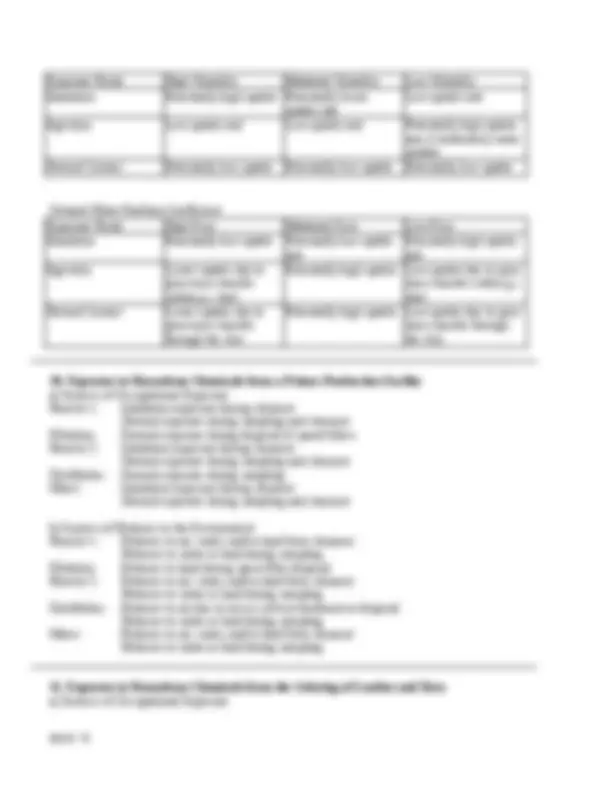
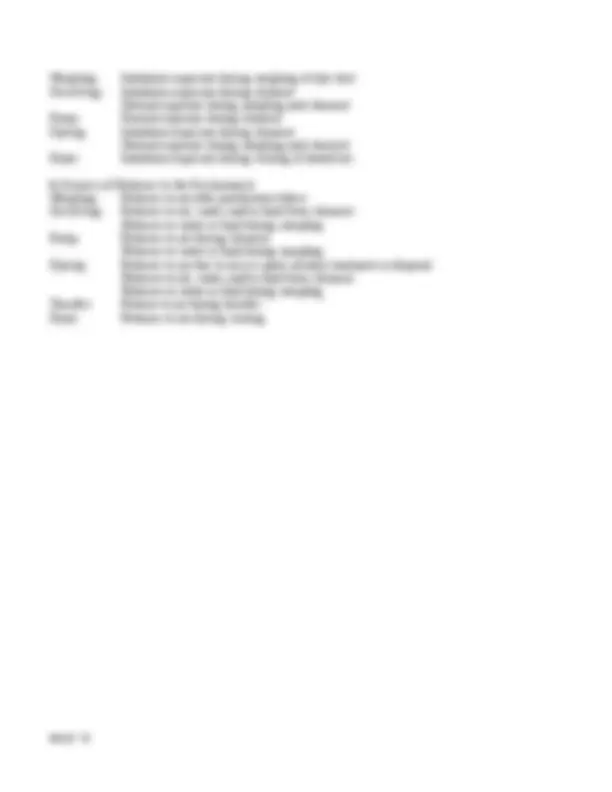
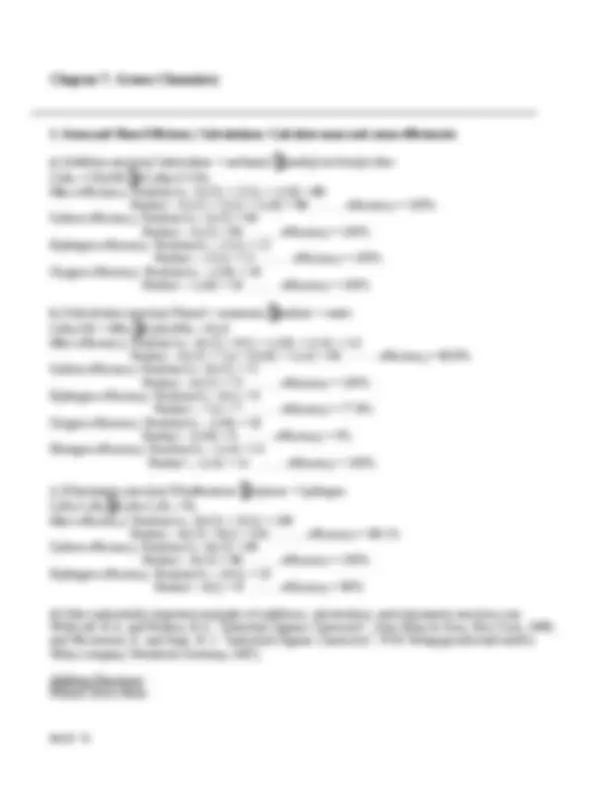
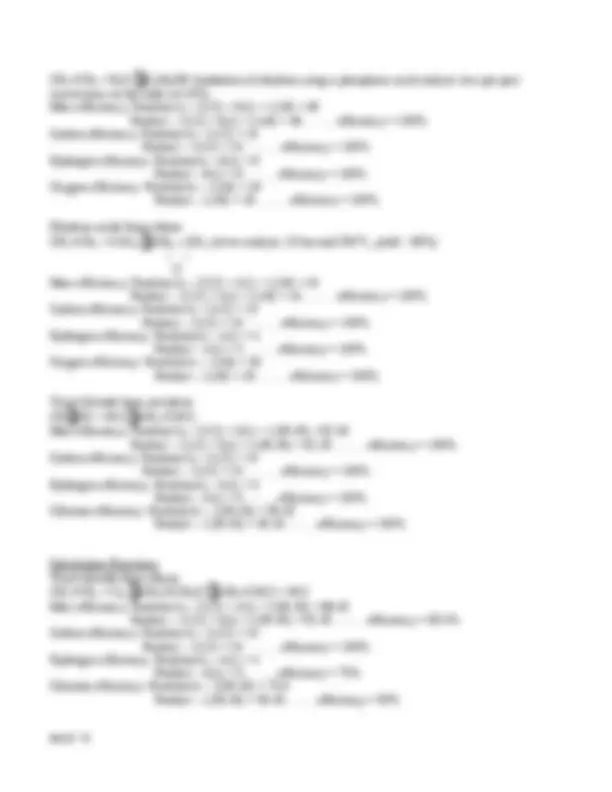
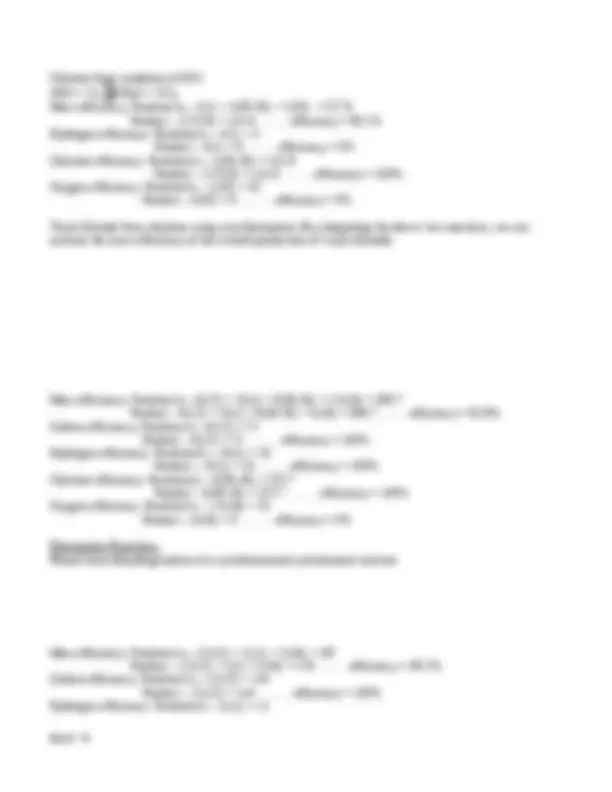
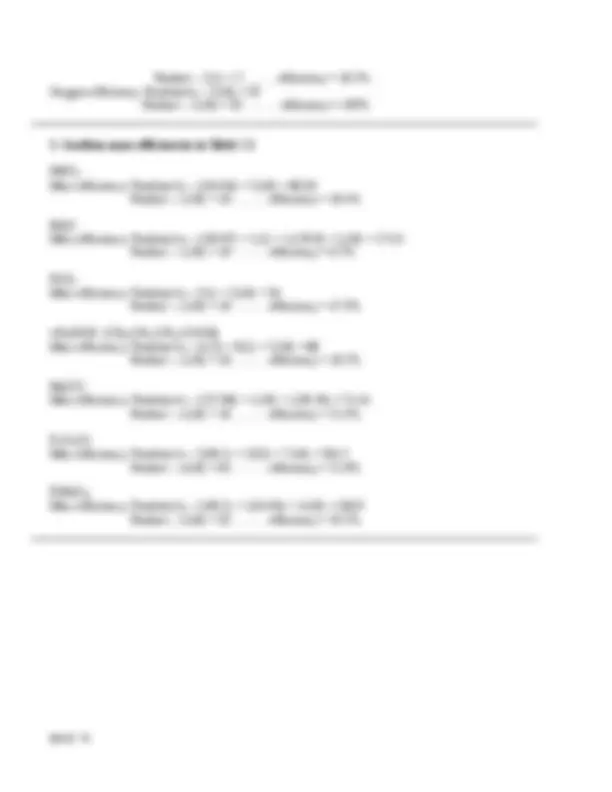
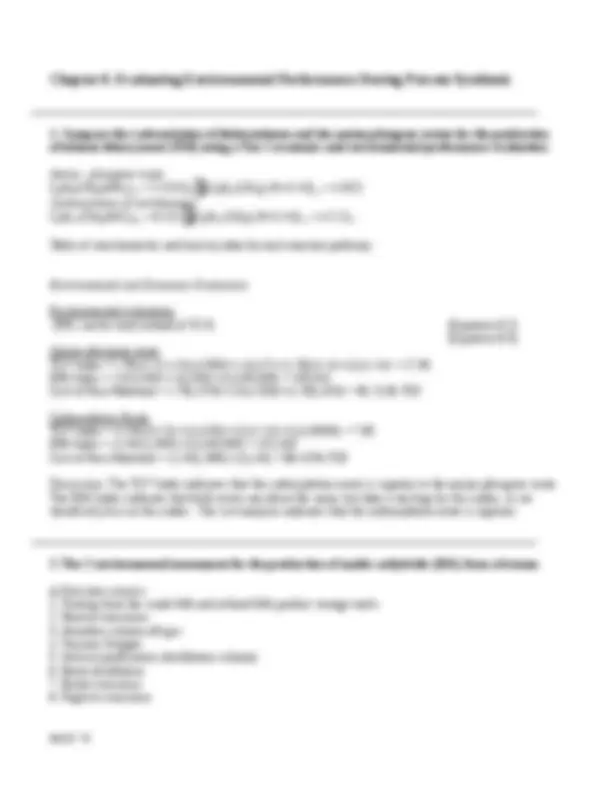
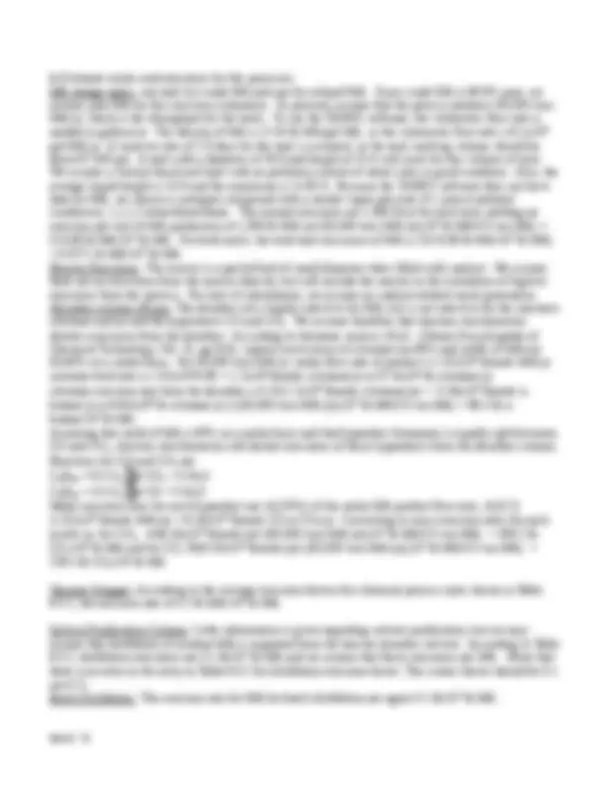
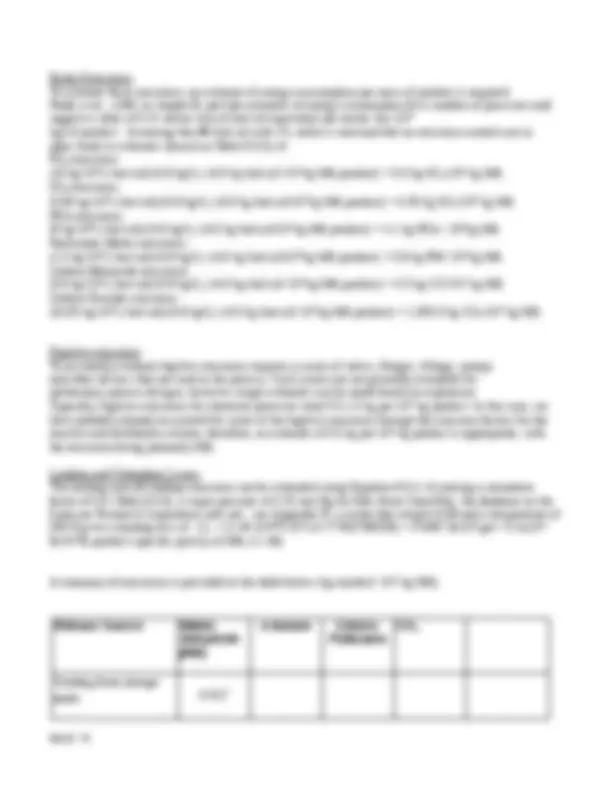
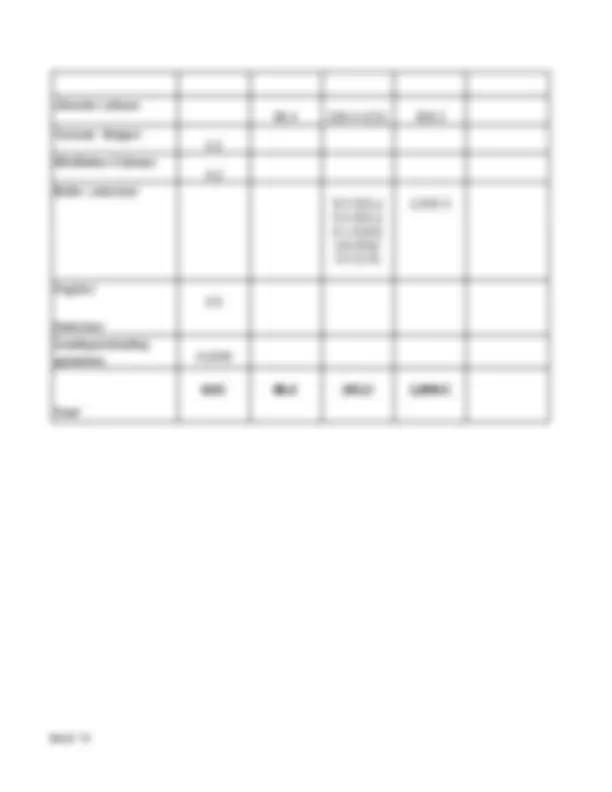
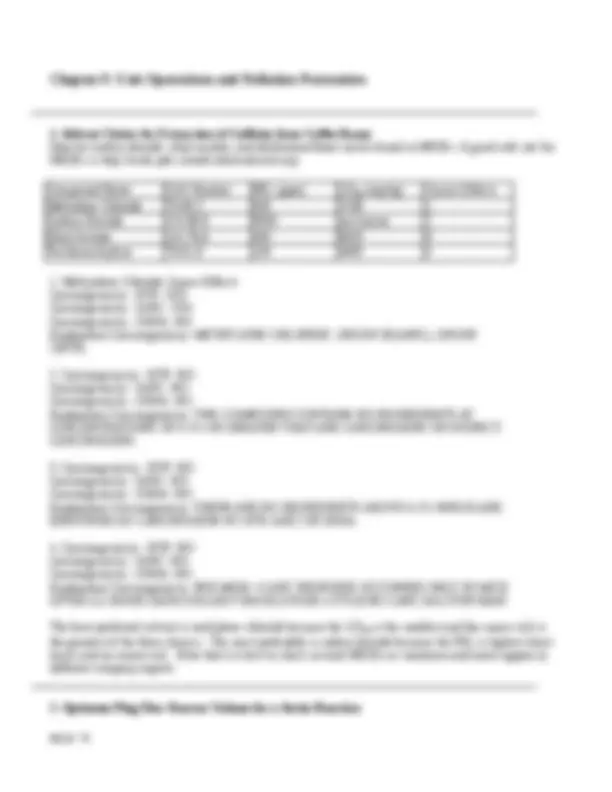
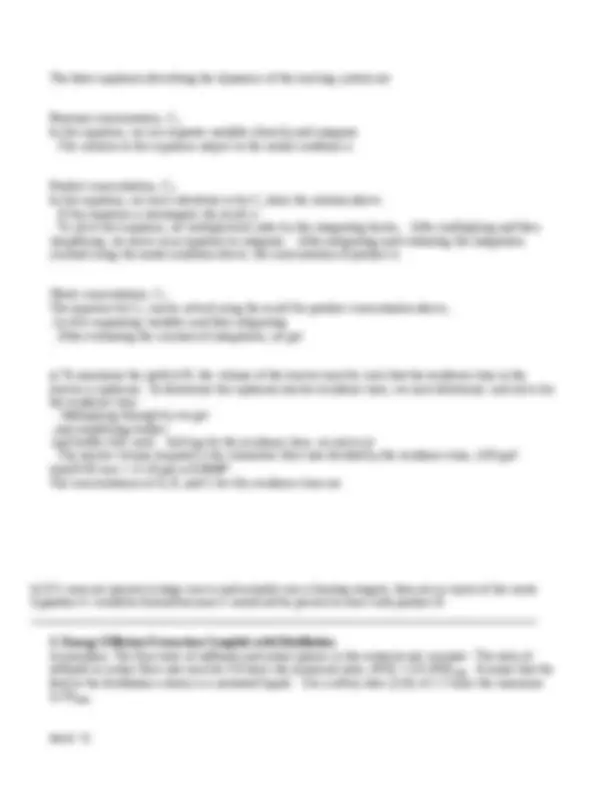
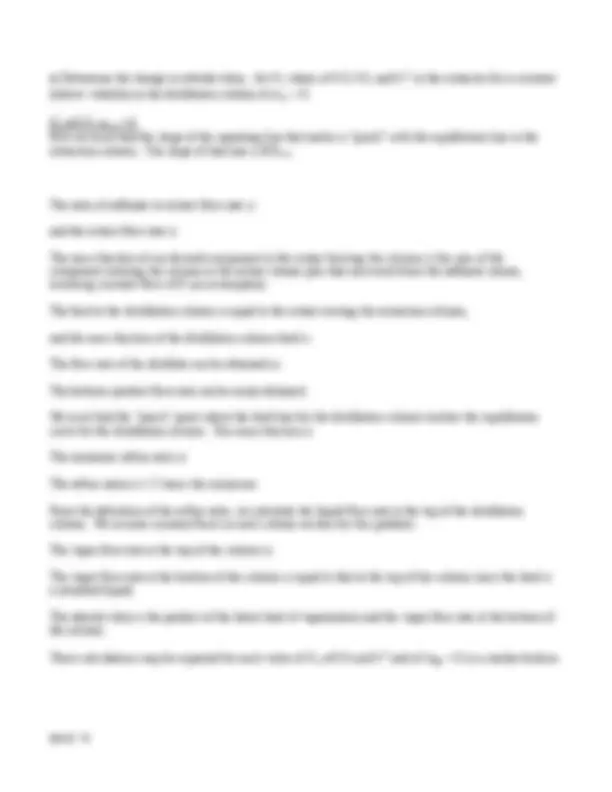
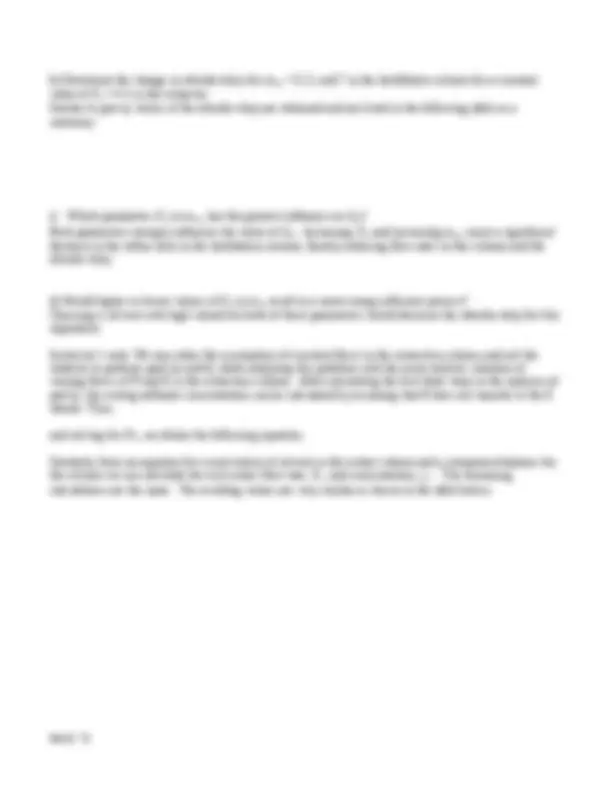
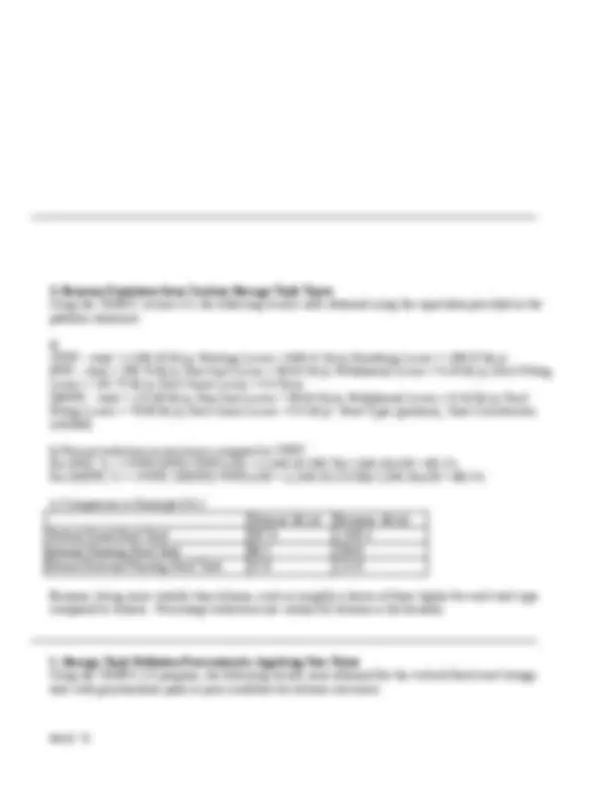
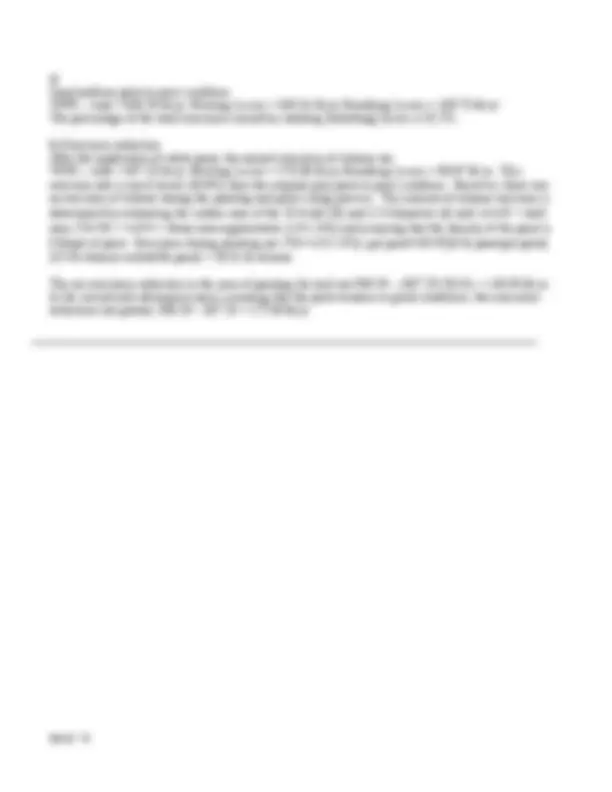
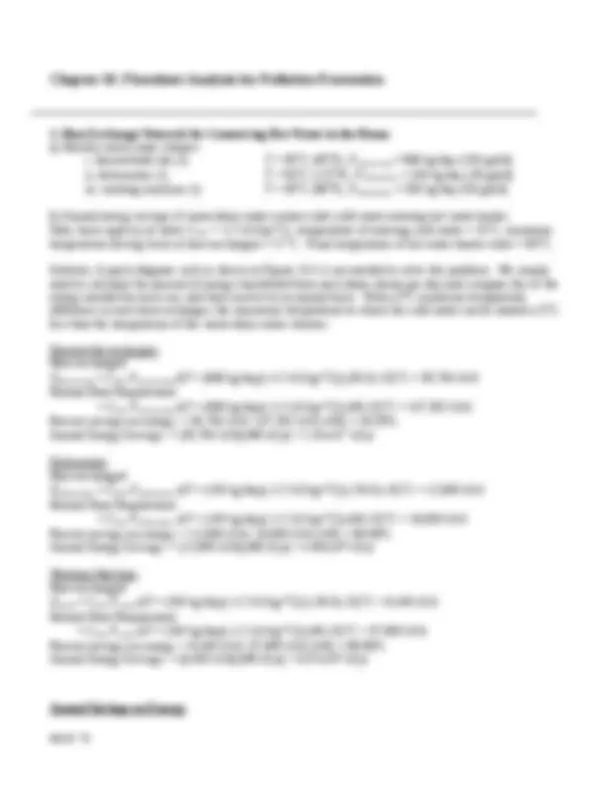
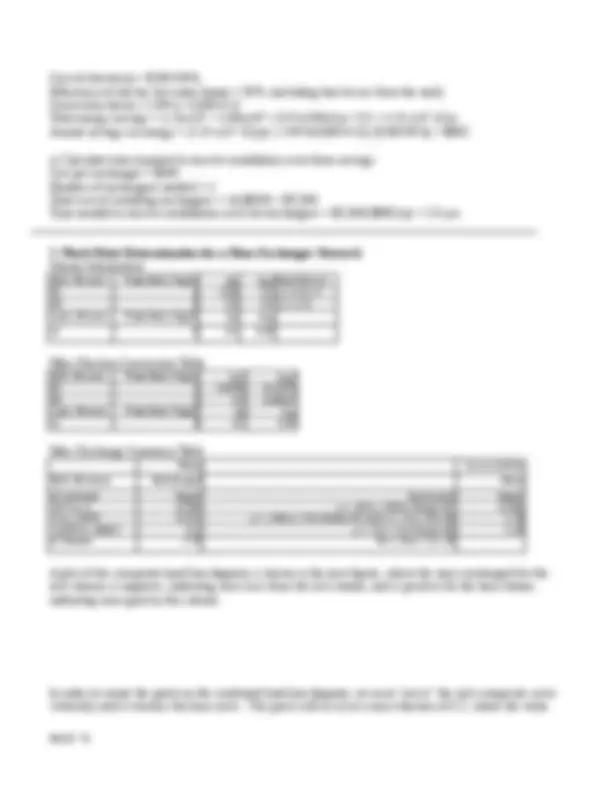
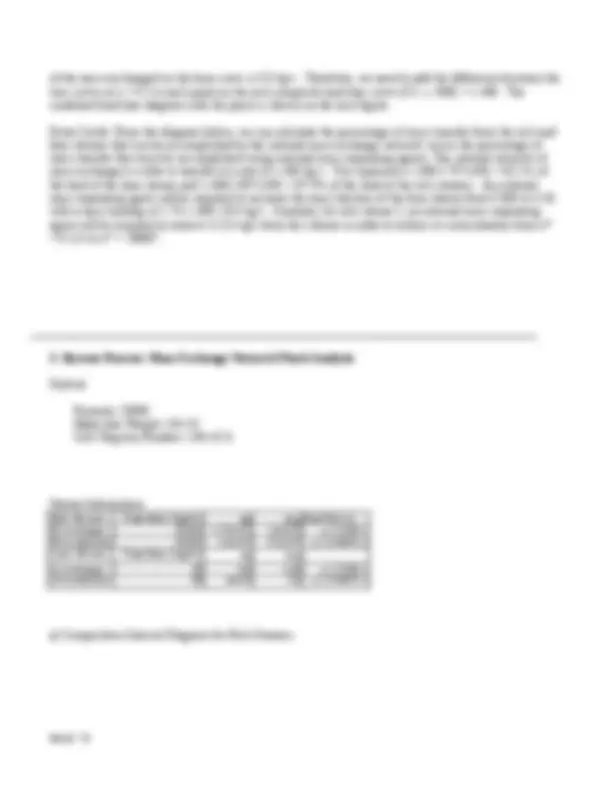
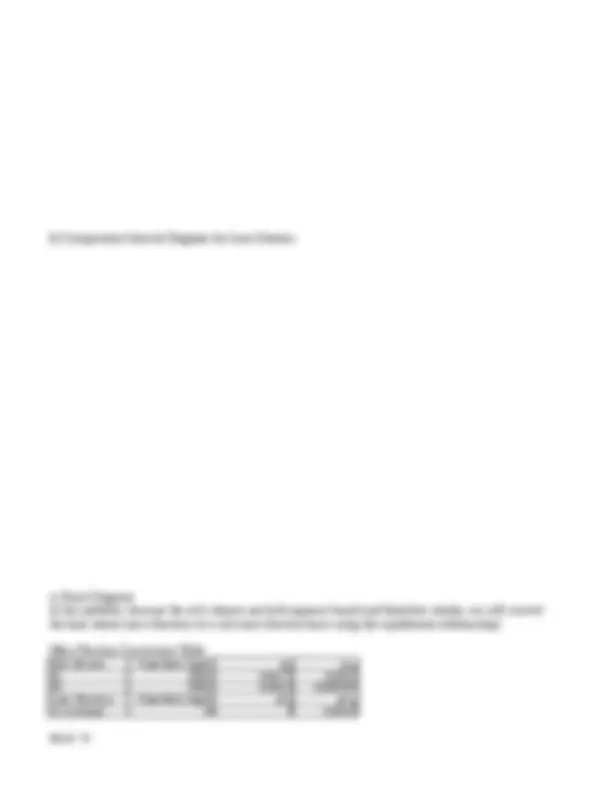
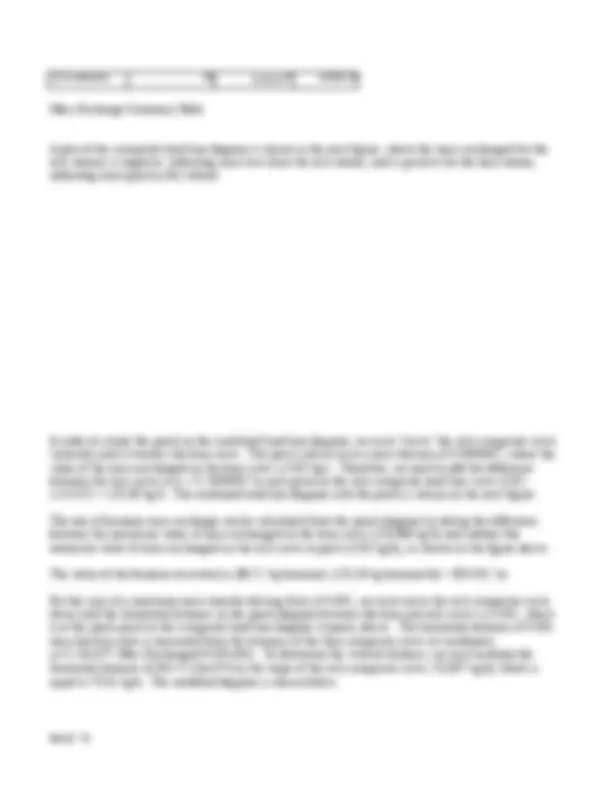
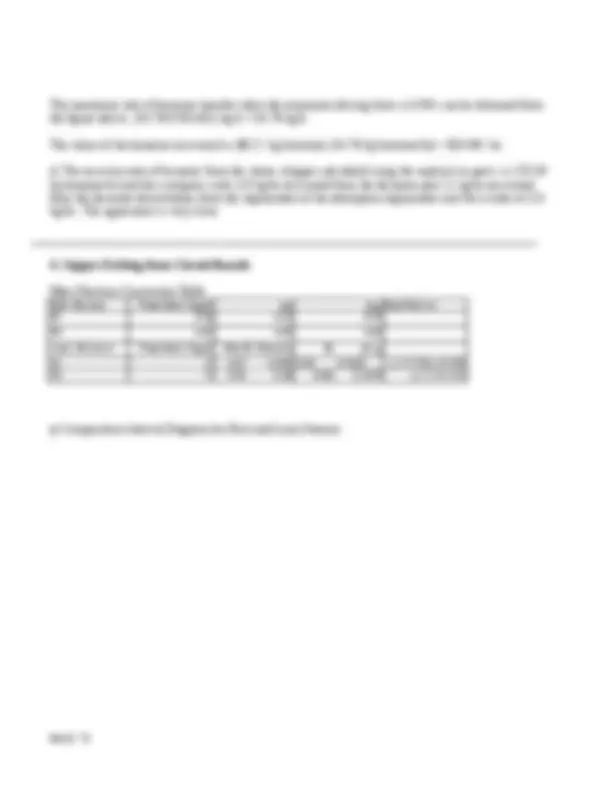
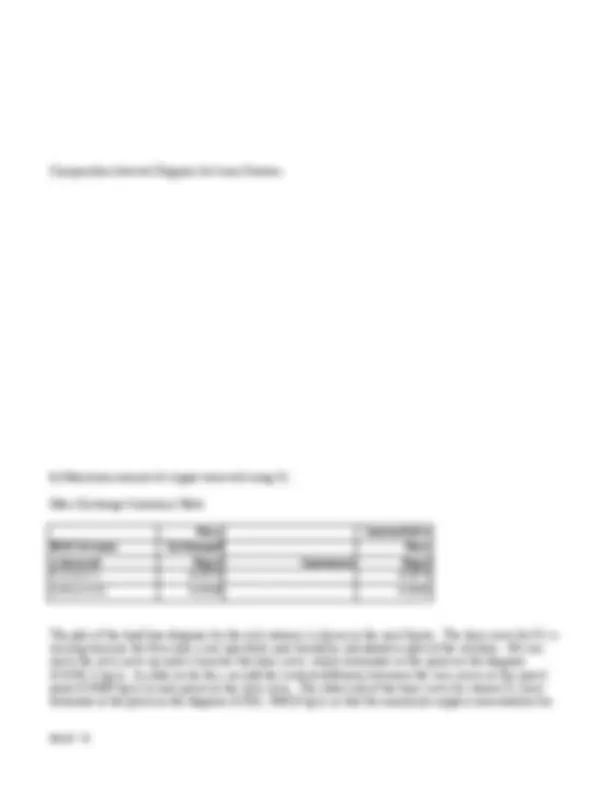
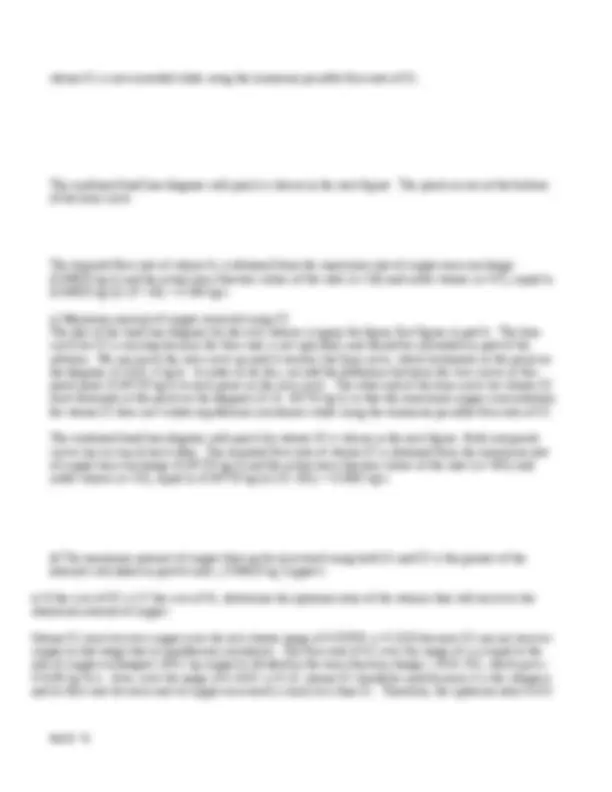
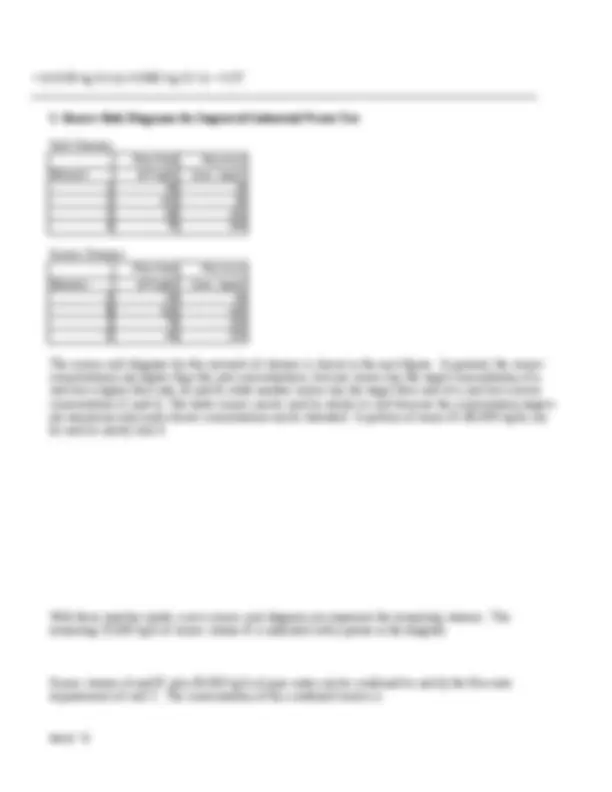
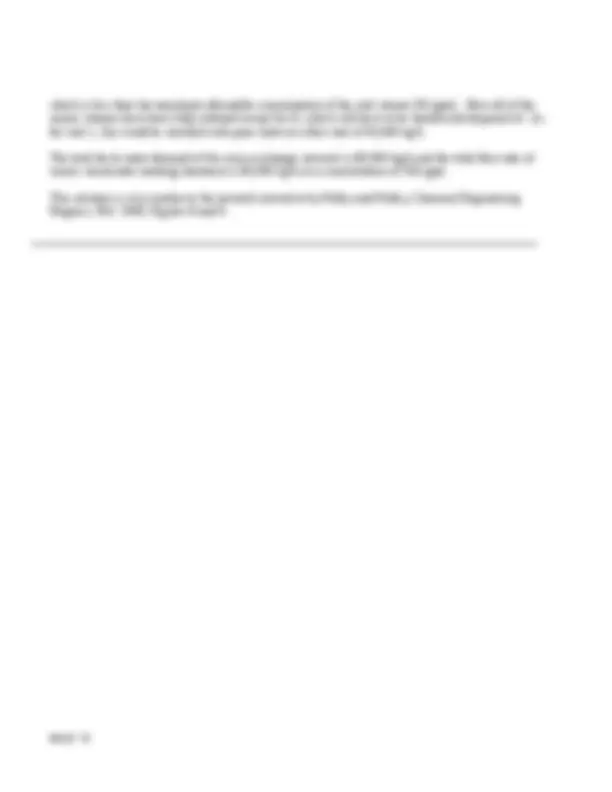
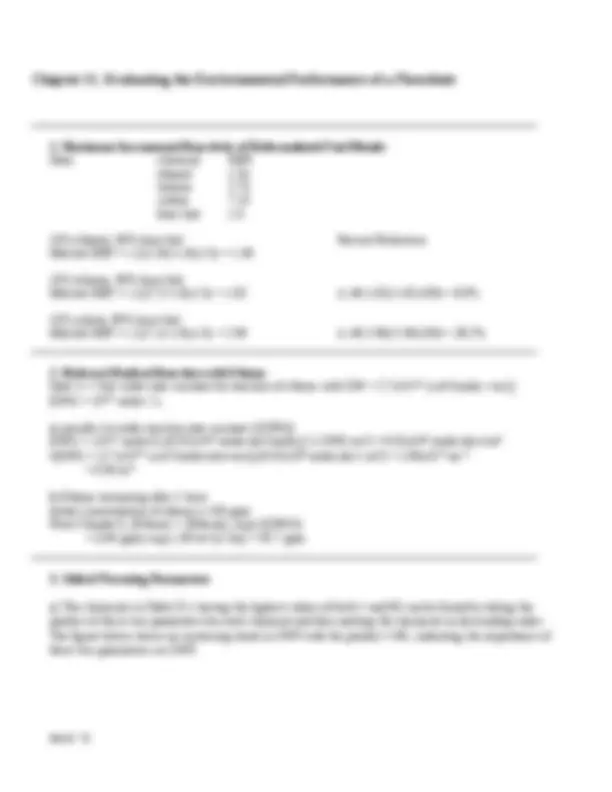
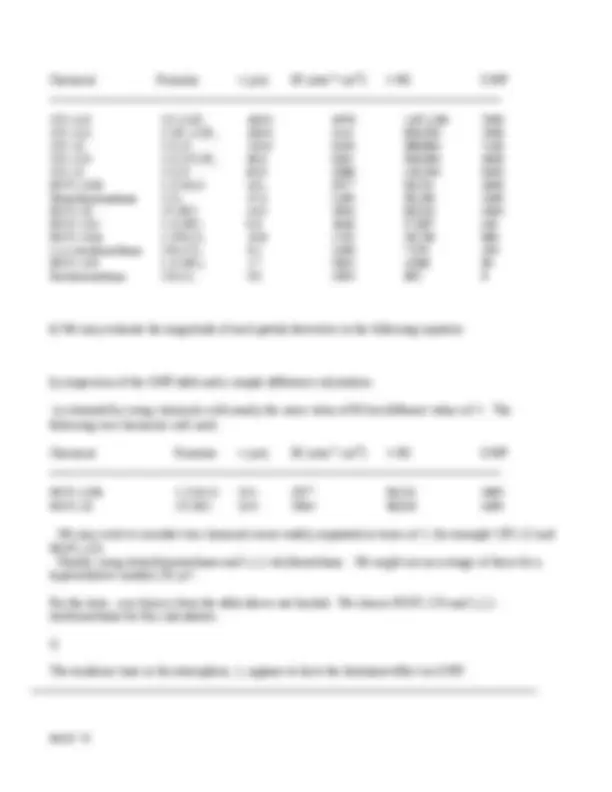
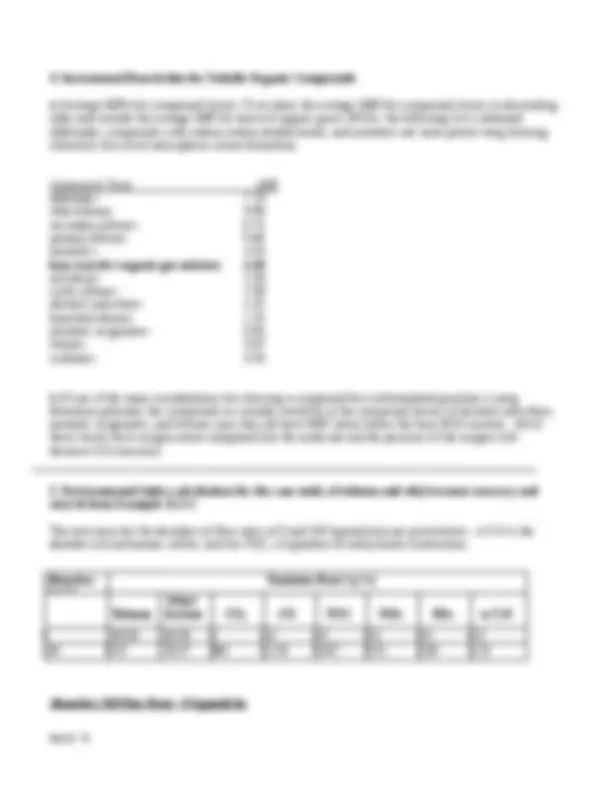
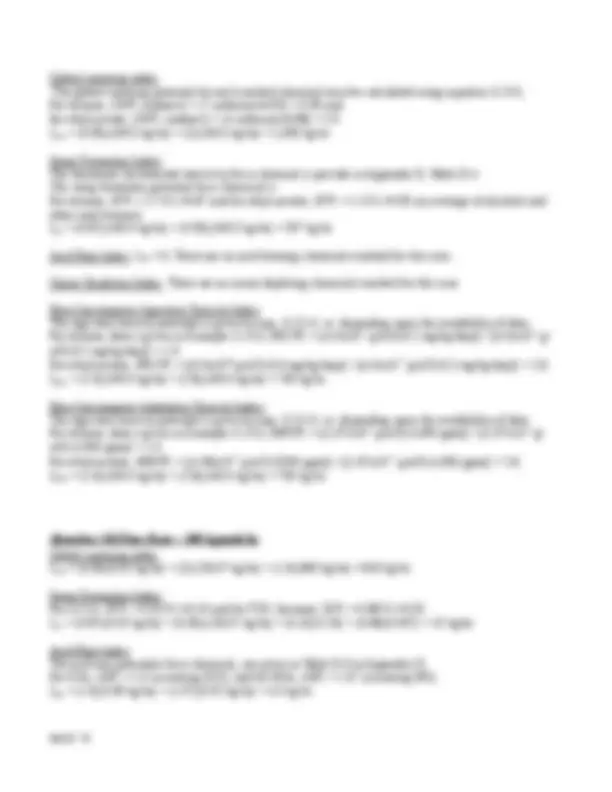
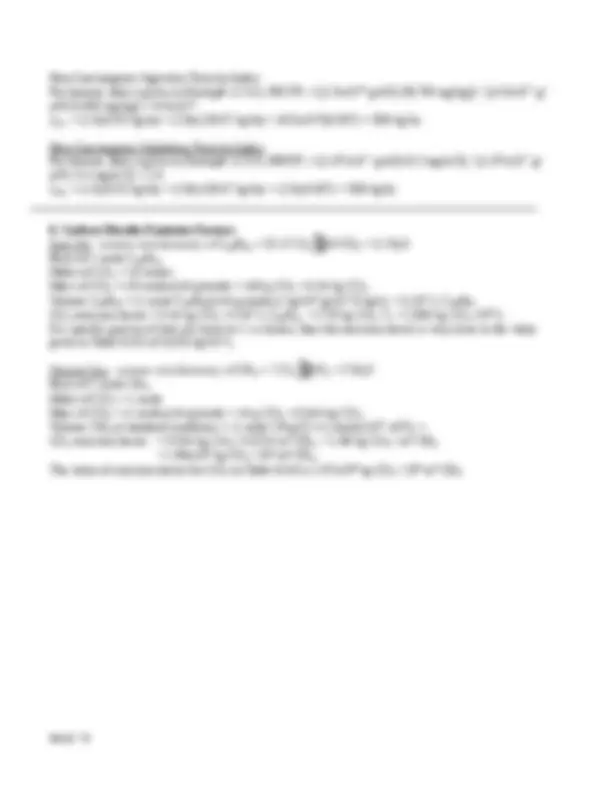
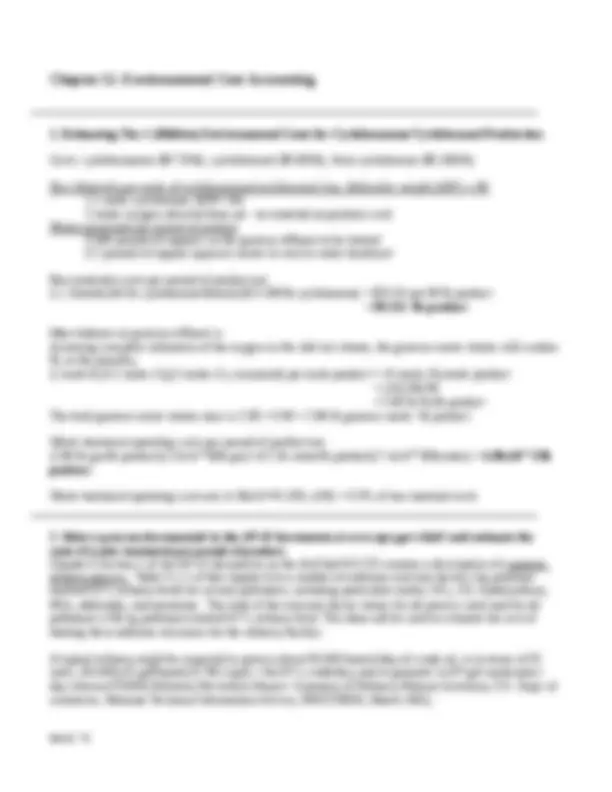
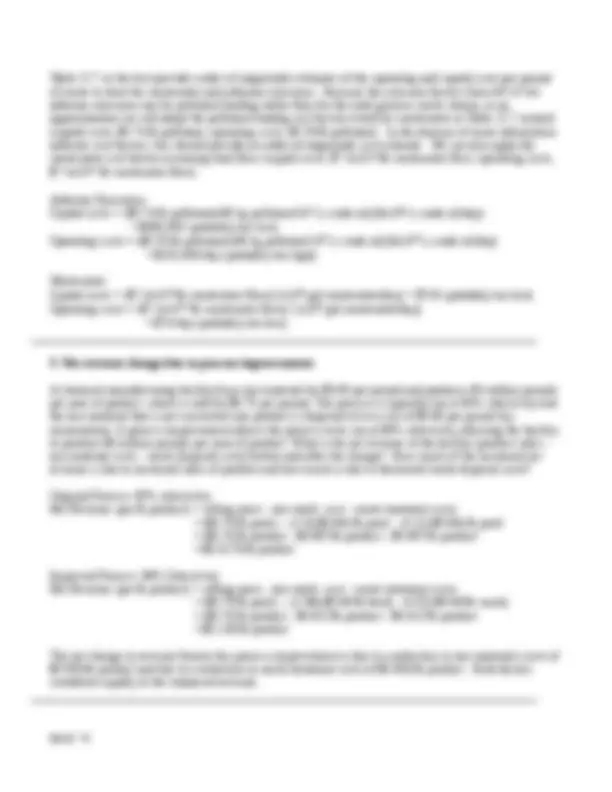
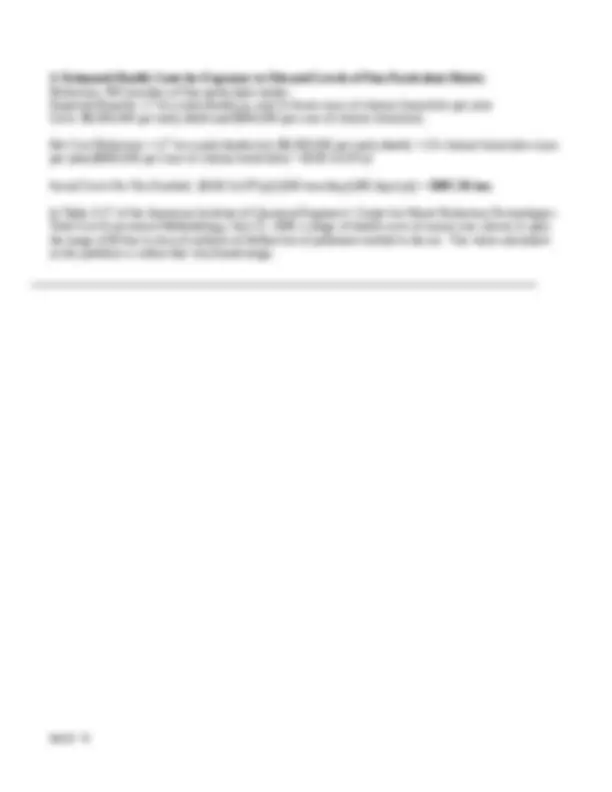
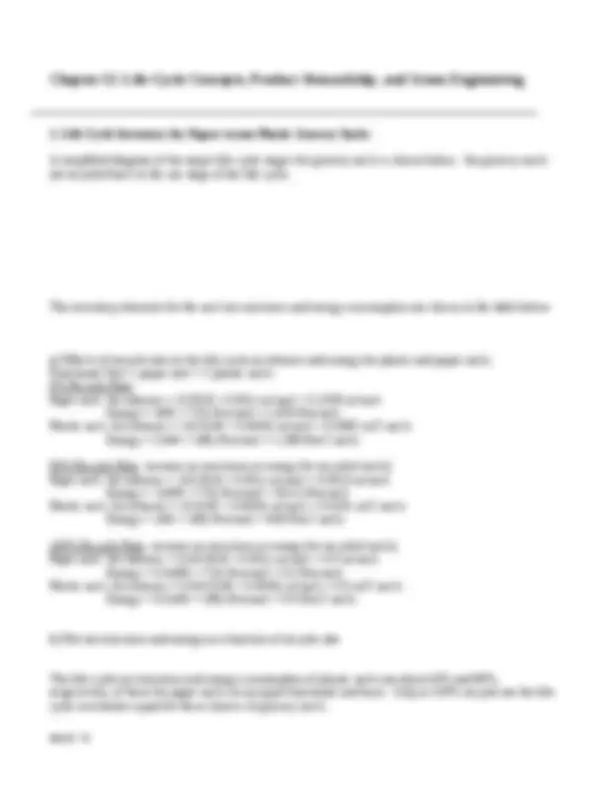
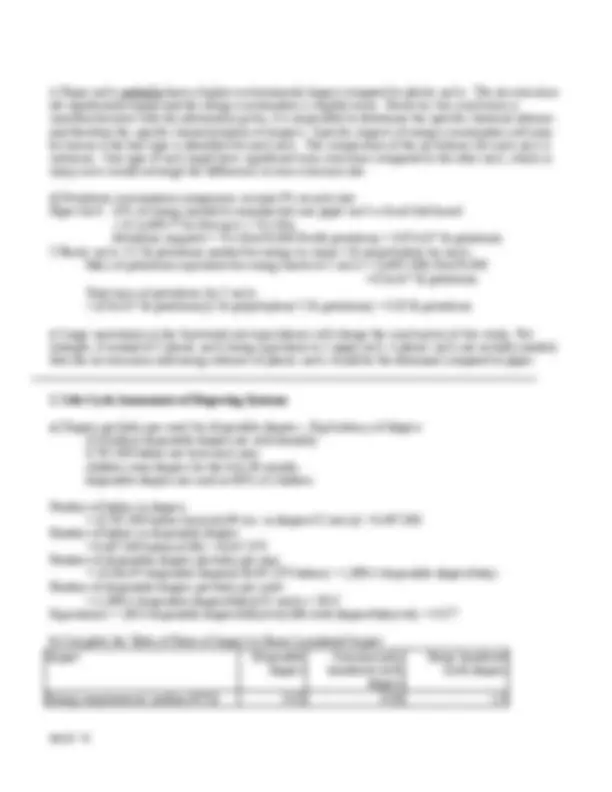
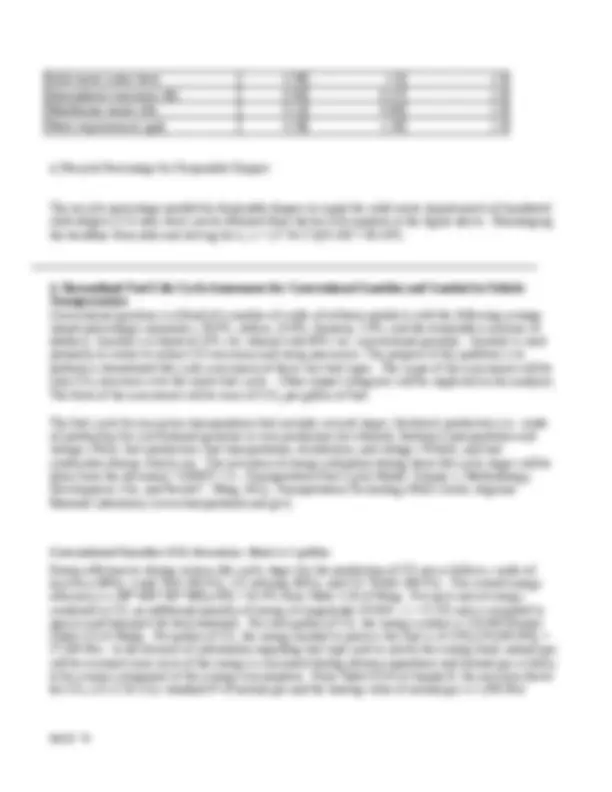
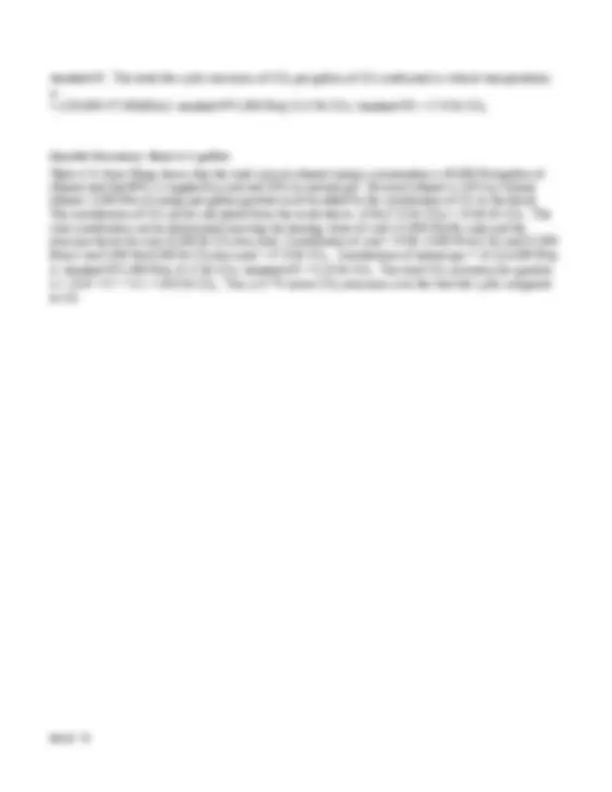
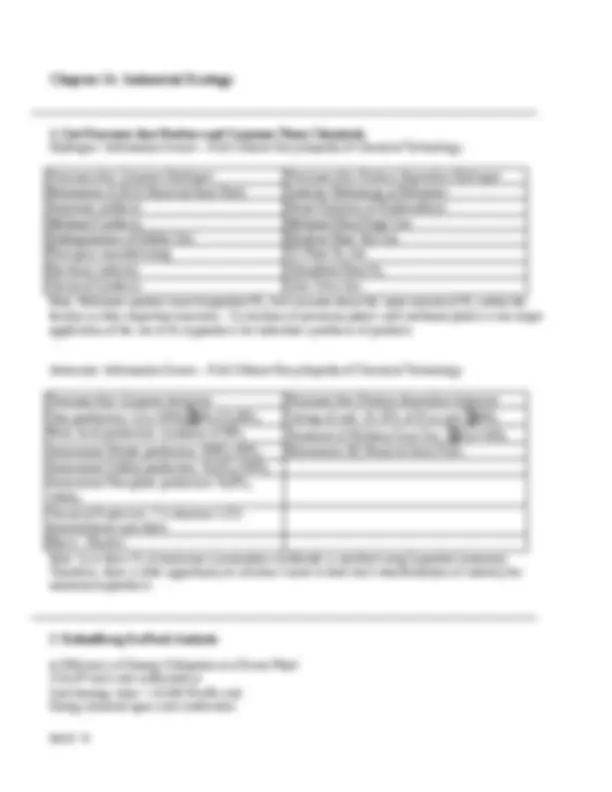
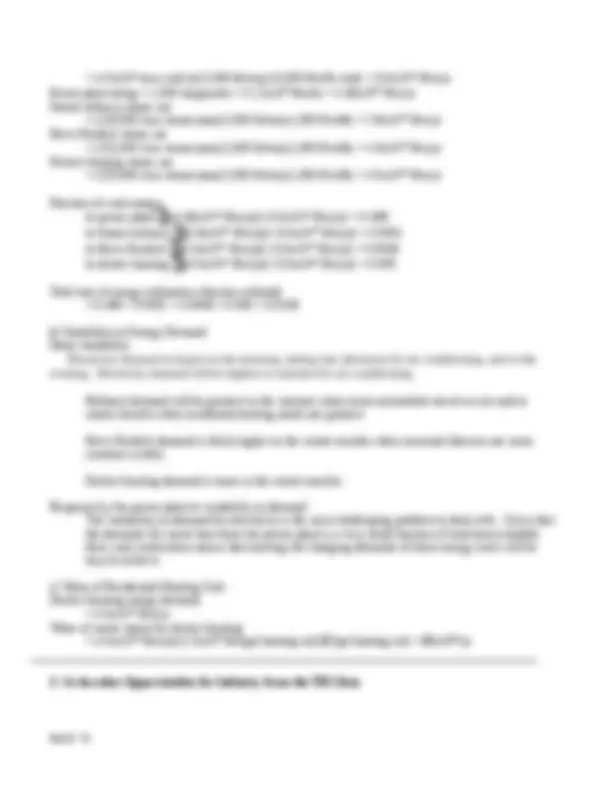
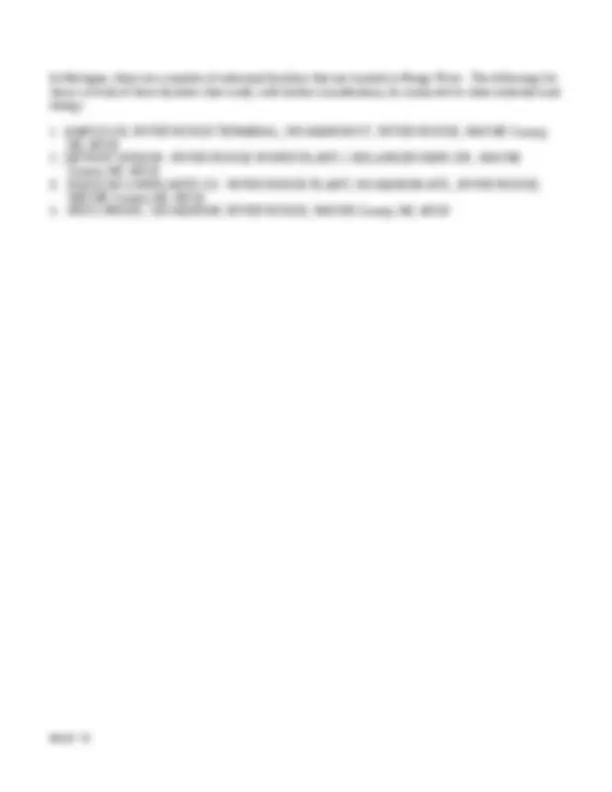
Study with the several resources on Docsity
Earn points by helping other students or get them with a premium plan
Prepare for your exams
Study with the several resources on Docsity
Earn points to download
Earn points by helping other students or get them with a premium plan
Community
Ask the community for help and clear up your study doubts
Discover the best universities in your country according to Docsity users
Free resources
Download our free guides on studying techniques, anxiety management strategies, and thesis advice from Docsity tutors
maths - maths
Typology: Exams
1 / 72
This page cannot be seen from the preview
Don't miss anything!
On special offer
Q. Chapter 1 Sample Homework Problem Electric Vehicles: Effects on Industrial Production of Fuels Replacing automobiles having internal combustion engines with vehicles having electric motors is seen by some as the best solution to urban smog and tropospheric ozone. Write a short report (1-2 pages double spaced) on the likely effects of this transition on industrial production of fuels. Assume for this analysis that the amount of energy required per mile trav eled is roughly the same for each kind of vehicle. Consider the environmental impacts of using different kinds of fuel for the electricity generation to satisfy the demand from electric vehicles. This analysis does not include the loss of power over the lines/grid.
CO decrease by about 80%, NOx would increase by about 60%, and SO 2 would increase by about 240%.
Accumulation of CO 2 in atmosphere = rate of CO 2 release from surface - rate of CO 2 removal by surface
Accumulation of CO 2 in atmosphere (metric tons C/yr) = (60+6+1.6) - (60+2+.5+1.8) = 3.3 metric tons C/yr =
Accumulation of CO 2 in atmosphere (metric tons C/yr) = (60+6.6+1.6) - (60+2+.5+1.8) = 3.9 metric tons C/yr =
+1% change in emissions from release by microorganisms is +.6% for a total of 60.6%
Accumulation of CO 2 in atmosphere (metric tons C/yr) = (60.6+6+1.6) - (60+2+.5+1.8) = 3.9 metric tons C/yr =
Change in number of moles CO 2 from part a =
Change in mole fraction (ppm) of CO 2 =
This rate of change compares well with the observed rate of change of 0.5%/yr, which at the current concentration of CO 2 is (.005)(360 ppm) = 1.80 ppm/yr.
substituting fluorine for chlorine on alternative refrigerants would help solve the ozone depletion
problem. On the other hand, fluorine on hydrocarbon refrigerants is a potent greenhouse gas and fluorinated compounds have been found to accumulate in the body fat of animals as far away as the arctic, well away from any known sources of these compounds. Apparently the persistence of these fluorinated compounds combined with atmospheric transport over long distances creates exposure to these remote creatures.
1. Risk of Death in Automobile Accidents We can express the risk of death in an automobile accident in the context of chemical risk as presented in Chapter 2.
Risk of Death by Car Accident = (Exposure) (Hazard)
In this equation, risk is the number of excess deaths by car accidents, exposure is the number of people involved over a specified period of time, and hazard is the number of deaths per unit of population per unit of time. This is very similar formulation as for carcinogenic risk due to exposure to harmful chemicals. Restating this risk equation with the data in the problem statement gives,
Solving for Hazard we calculate,
The number of deaths expected in Minneapolis-St. Paul over a three-day weekend is
2. Fault Tree Analysis
The fault tree for the collection sump is
ethylene glycol 50
n-butyl acetate 150 methyl ethyl ketone 200 ethyl acetate 400
b) Rank from higher to lower exposure potential using vapor pressure
Vapor Press. (kPa @ 25˚C)
diethylemine 30. ethyl acetate 12. methyl ethyl ketone 12. monomethyl ether 1. n-butyl acetate 1. furfuryl alcohol 0. ethylene glycol 0.
c) Considering hazard and exposure, rank from higher to lower risk If we take the inverse of the PEL as a measure of potential hazard and multiply by the vapor pressure (a measure of exposure), we could estimate the overall risk potential by inhalation.
1/PEL • Vapor Press. diethylemine 1/25 • 30.1 = 1. methyl ethyl ketone 1/200 • 12.1 = 0. monomethyl ether 1/25 • 1.3 = 0. ethyl acetate 1/400 • 12.6 = 0. n-butyl acetate 1/150 • 1.3 = 0. furfuryl alcohol 1/50 • 0.1 = 0. ethylene glycol 1/50 • 0.008 = 0.
Ethylene glycol is the solvent with the lowest risk.
d) To lower the risk even more, process modifications could be placed on the integrated circuits fabrication process to reduce the amount of vapor generated and to collect and recover any vapors prior to exposure to workers.
6. Carcinogenic Risk Assessment Near a Refinery a) Inhalation dos, I (^) INH :
b) Inhalation Carcinogenic Risk
c) Risk of cancer due to inhalation is greater than the recommended range of < 10 -4^ to 10-^.
d) This calculation might actually over predict the risk because RR and ABS were assumed to be 1 when
actually they would be less than one but greater than zero. Also, we used the outside concentration of benzene in the air, not the inside (the home) concentration which will be lower. In addition, we assumed a 70 year exposure duration (ED) when often people move and actually spend much less time in any given home.
1. Provide definitions of the following terms a) pollution prevention: Any act of source reduction, in-process recycle, on-site recycle, and off-site recycle that reduces the amounts of releases and the hazardous characteristics of those releases which ultimately reach the environment. b) source reduction: Any modification of a manufacturing process or of production procedures which reduces the amount of components entering a waste stream or the hazardous characteristics of those components entering waste streams prior to recycle, treatment, or disposal. c) in-process versus on-site versus off-site recycle: In-process recycle is the recovery and return of components that would otherwise become waste to the process unit where these components were generated, usually immediately after they are generated. Examples would be unconverted reactants leaving a reactor that are separated and returned to the reactor inlet. On-site recycle is the recovery of valuable stream components using process units within the same facility where those components were generated. Off-site recycle is the recovery of valuable components at a remote location from waste streams generated at a facility and the return of the valuable components to the facility. d) waste treatment: Any process that renders a waste stream less hazardous prior to disposal or direct release through physical, biological, or chemical means. Examples are primary, secondary, and tertiary wastewater treatment, adsorption of volatile organic compounds from air, and landtreatment of petroleum hydrocarbon sludges from tank bottoms. e) disposal: Long-term isolation of raw or treated waste components in a secured landfill. Examples include landfills for domestic and industrial hazardous and non-hazardous waste. f) direct release: The direct release of components from processes to the air, land, or water. An example of this includes the release of volatile organic compounds from fugitive emission sources in chemical or petroleum refinery processes (from valves, fittings, pumps, flanges, connectors, etc.). 2. Solvent Recovery and Recycle for Automobile Assembly Paint Operations This recycle operation is an example of off-site recycle. The location of the solvent recovery facility is remote from the locations of automobile manufacture. The feed for the solvent recovery facility is the waste streams from these cleaning processes in automobile assembly painting. This activity would be considered pollution prevention using the expanded definition in this text but would not be considered pollution prevention by the federal definition, which only includes source reduction and in-process recycle. 3. Capital and Operating Costs for Federal Regulations
a) The Toxic Substances Control Act (TSCA) of 1976 Chemical manufacturers must submit information on existing chemicals. This information includes chemical identity, name and molecular structure, categories of use, amounts manufactured or processed, byproducts from manufacture, processing, use, or disposal, environmental/health effects of chemical and
byproducts, and exposure information. Companies must also keep records of any incidents involving the
chemical that resulted in adverse health effects or environmental damage. Chemical manufacturers, importers, and processors are required to notify EPA within 90 days of introducing a new chemical into commerce by submitting a Premanufacturing Notice (PMN).
b) The Federal Insecticide, Fungicide, and Rodenticide Act (FIFRA) of 1972
The decision by EPA to register a pesticide is based on the data submitted by the pesticide manufacturer in the registration application. The data in the registration application is difficult and expensive to develop. A registration is valid for five years, upon which time it automatically expires unless a re- registration petition is received. FIFRA requires older pesticides that were never subject to the current
registration requirements to be registered if their use is to continue.
c) The Occupational Safety and Health Act (OSH Act) of 197 0 The OSH Act’s Hazard Communication Standard requires that several standards be met by manufacturers or importers of chemicals and also for the subsequent users of them. These requirements include the development of hazard assessment data, the labeling of chemical substances, and the informing and training of employees in the safe use of chemicals. This information must be assembled in a material
safety data sheet (MSDS) in accordance with OSH Act standards and accompany any sale or transfer of the chemical. Employers must also develop a written hazards communication plan which outlines the implementation plan for informing and training employees on the safe handling of chemicals in the workplace. Employers must keep records of all steps taken to comply with OSH Act requirements and employers must keep records of all work-related injuries and deaths and report them periodically to OSHA.
d) Clean Air Act (CAA) of 1970 Prior to the completion of new facilities or additions to existing facilities, a permit must be obtained from the state air quality authority. Manufacturers must comply with the state-mandated source-specific emission limits on mobile and stationary sources at a sufficient level to assure compliance with federal quality standards. Meeting these requirements is achieved by installing pollution control equipment on waste streams leaving the process or by modifying the process to eliminate the waste streams.
e) The Clean Water Act (CWA) of 1972 The National Pollutant Discharge Elimination System (NPDES) permit program requires any point source of pollution to obtain a permit. NPDES permits contain effluent limits, either requiring the installation of specific pollutant treatment technologies or adherence to specified numerical discharge limits. NPDES permit holders must monitor discharges, collect data, and keep records of the pollutant levels of their effluents. These records must be submitted to the agency that granted the NPDES permit in order to assure that the point source is not exceeding the effluent discharge limits. A permit must be obtained from the United States Army Corp of Engineers before any discharge of dredge or fill materials occurs into navigable waterways, including wetlands.
f) Resource Conservation and Recovery Act (RCRA) of 1976 A generator of hazardous waste must obtain an EPA identification number within 90 days of the initial generation of the waste. RCRA requires generators to properly package hazardous waste for shipment off-site and to use approved labeling and shipping containers. Generators must maintain records of the quantity of hazardous waste generated, where the waste was sent to for treatment, storage, or disposal,
1. Compare Inherently Safer Design with Pollution Prevention
Inherently Safer Design Concepts Pollution Prevention Concepts
Intent : reduce catastrophic releases of hazardous chemicals and the hazards of those releases by modifying the process to eliminate the source of those hazards within the process.
Intent : reduce chronic releases of hazardous chemicals and the hazards of those releases by modifying the process to make them more efficient at using energy and mass.
Minimize : reduce the inventory of hazardous
chemicals within the process.
Source Reduction: reduce the generation and release of hazardous wastes from a process. Substitute: replace hazardous materials with safer chemicals to reduce impacts of catastrophic releases.
Material Substitution: replace hazardous materials or materials that use excessive energy with more benign materials.
Moderate: Use less hazardous conditions to lessen the impacts of any catastrophic releases.
Process/Procedure Modifications: change process conditions to reduce waste generation and energy consumption.
Simplify: design facilities to be less complex and less error prone, and forgiving of any errors that are made.
Process Modification: change the process control strategy to more precisely achieve the desired operating conditions.
2. Effects of Chemical Properties
Safety Concerns: Chemical properties that would indicate the potential for catastrophic release would be boiling point, reactivity with air or water, vapor pressure, corrosivity to process vessels, endothermic or exothermic heat of reaction, ..
Pollution Prevention Concerns: Chemical properties that would reduce the potential for chronic release from process operations include boiling point, vapor pressure, solubility in water, emulsion forming with water, Henry's constant, compatibility with process materials such as gaskets and valve stems, corrosivity to process vessels, …
3. New "Natural" Product from Botanicals: Ethanol vs. n-Hexane
Physical/Toxicological Properties (reference needed)
Properties Ethanol n-Hexane
Toxicity (LD50, oral rat, mg/kg) 7060 >
Toxicity (OSHA PEL, ppm) 1000 50
Carcinogenic no no
Boiling Point (˚C @ 1 atm) 78.3 68.
Melting Point (˚C) -114 -
Vapor Pressure (mm Hg @ 20˚C) 44.6 129
Vapor Density (air = 1.0) 1.59 3
Liquid Density (specific gravity) 0.789 0.
Solubility in Water Infinite Negligible
Flash Point (˚C) 8.9 -
Lower Explosive Limit (%) 3.3 1.
Upper Explosive Limit (%) 24.5 7.
Reactivity Stable Stable
Federal Environmental Permits/Reporting (reference needed)
Environmental Regulation Ethanol n-Hexane
TSCA PMN application yes yes
OSH Requirements yes yes
FIFRA no no
CAA permit yes yes
CWA permit yes yes
RCRA Reporting no no
EPCRA Reporting no yes
CERCLA Reporting no yes
PPA Reporting no yes
a) If the decision is based on a comparison between the solvents, then ethanol would be chosen for the process. Ethanol has a lower toxicity judging from the MSDS information and has fewer reporting requirements compared to n-hexane. Of course, more information would be needed to make a reasonable decision. We must know what effects the solvent choice will have on operating costs, on energy consumption, and quality of product. In addition, we must know what effects of solvent choice will have on overall environmental impact of the process, including energy-related emissions and impacts, which can be significant relative to the impacts of the process materials. Methods for evaluating environmental impacts during process design are the topics of discussion for Part II of the book.
b) A Chemical Engineer’s responsibilities are to him or her self, to the employer, the community, and the customer. Each of these responsibilities must be incorporated into any decision regarding product and process design. A potential plant closure resulting in loss of jobs should not influence the decision as to whether a product will be produced or how it will be produced. The primary decision variables are whether the process and product are profitable, which means that society values it, and whether the process and product causes unacceptable damage to the environment and human health.
c) Same as b).
No corrections factors log K ow = 0.229 + 6(0.2940) + -0.1823 = 1. K (^) ow = 10^ 1.81^ = 64. log K (^) ow (experimental) = 1.
Water solubility (S): (S in mole/L)
log S = 0.796 – 0.854 log K (^) ow - 0.00728(MW) +^ F 05 3 hj (used when melting pt. not available) Corrections factors h (^) j = -.390 (aromatic nitro group)
log S = 0.796 – 0.854(1.85) - 0.00728(123.11) + -.390 = -2. S = 10-2.07^ =8.51x10 -3^ moles/L = 1.05 g/L = 1,047.5 mg/L
Soil sorption coefficient (K (^) oc): log K (^) oc = 0.53^1 F 06 3 + 0.62 + F 05 3 njP (^) j (K (^) oc is ratio of μg/g carbon to μg/ml solution) 1 F 0 6 3 =^
F 0 5 3(^
F 0 6 4i^ *^
F 0 6 4j)^
-0.5 (^) , the first order molecular connectivity index F 0 6 4i^ ,the connectedness of carbon or other heteroatom i) Bond connectedness ( F 06 4i* F 06 4j)
(N-O) (N=O) (N-C) 2(C-C) 4(C-C) (3,1) (3,1) (3,3) 2(3,2) 4(2,2) 1 F 06 3 = F 05 3( F 06 4i * F 06 4j) -0. 1 F 0 6 3 = = 4. log K (^) oc = 0.53(4.305) + 0.62 - 0.632 = 2. K (^) oc = 10^ 2.27^ = 186
Atmospheric half life: The only significant reaction is addition to aromatic ring = 0.2437x10-12^ cm 3 /molecule-sec.
t1/2½ = ln (2) / (k [OH. ]) = 0.693/((0.2437x10-12^ cm^3 /molecule-sec)(1.5x10^6 molecules/ cm^3 )) t1/2½ = 1.896x10^6 sec = 22 days.
Biodegradability: I = 3.199 + a (^) 1f 1 + a2f 2 +…… + a (^) nf (^) n + amMW Unsubstituted phenyl group a = 0. Aromatic (NO (^) 2)^ a^ = -.134 (used aromatic amine as substitute) Molecular weight a = -0. I = 3.199 + 0.022 - .134 + 123.11(-0.00221) = 2.81 (weeks to a month)
2. Estimate properties for 2-Chloroaniline From the EPIWIN software, enter the CAS Number of 95-51-2. The following summary is obtained with the software output listed directly below.
Boiling point (Tb) 216.05 ˚C Vapor pressure (Pvp) at 300 K^ 0.16 mm Hg @ 25˚C Henry’s Law constant (H) 1.41x10 -6^ atm-m^3 /mole using bond method Octanol-water partition coefficient (Kow ) Log K (^) ow = 1.
Bioconcentration Factor (BCF) Log BCF = 0.763 using BCFwin Water solubility (S) 2241 mg/L - no melting pt. formula used. Soil sorption coefficient (K (^) oc) Log K (^) oc = 1. Atmospheric half life 0.340 Days (12-hr day; 1.5E6 OH/cm 3 ) Biodegradability 2.5757 (weeks-months)
SMILES : Nc(c(ccc1)CL)c CHEM : Benzenamine, 2-chloro- CAS NUM: 000095-51- MOL FOR: C6 H6 CL1 N MOL WT : 127. ------------------------------ EPI SUMMARY (v2.40) -------------------------- Physical Property Inputs: Water Solubility (mg/L): ------ Vapor Pressure (mm Hg) : ------ Henry LC (atm-m3/mole) : ------ Log Kow (octanol-water): ------ Boiling Point (deg C) : ------ Melting Point (deg C) : ------
Log Octanol-Water Partition Coef (SRC): Log Kow (KOWWIN v1.60 estimate) = 1. Log Kow (Exper. database match) = 1.
Boiling Pt, Melting Pt, Vapor Pressure Estimations (MPBPWIN v1.28): Boiling Pt (deg C): 216.05 (Adapted Stein & Brown method) Melting Pt (deg C): 24.41 (Mean or Weighted MP) VP(mm Hg,25 deg C): 0.16 (Mean VP of Antoine & Grain methods)
Water Solubility Estimate from Log Kow (WSKOW v1.30): Water Solubility at 25 deg C (mg/L): 2241 log Kow used: 1.90 (expkow database) no-melting pt equation used
ECOSAR Class Program (ECOSAR v0.99b): Class(es) found: Aromatic Amines
Henrys Law Constant (25 deg C) [HENRYWIN v3.00]: Bond Method : 1.41E-006 atm-m3/mole Group Method: 1.86E-006 atm-m3/mole
Probability of Rapid Biodegradation (BIOWIN v3.63): Linear Model : 0. Non-Linear Model : 0. Expert Survey Biodegradation Results: Ultimate Survey Model: 2.5757 (weeks-months) Primary Survey Model : 3.3900 (days-weeks )
Atmospheric Oxidation (25 deg C) [AopWin v1.87]: Hydroxyl Radicals Reaction: OVERALL OH Rate Constant = 31.4297 E-12 cm3/molecule-sec Half-Life = 0.340 Days (12-hr day; 1.5E6 OH/cm3)
Octanol-water partition
coefficient, Log (Kow )
Water solubility (S)
(mg/L)
7.92x105^ 2.72x105^ 6,885 369 17.
Soil sorption coefficient
Log (K (^) oc)
Atmospheric half life
(days)
Biodegradability
(Primary Survey Model)
3.91 (days) 3.
(days)
(days)
(days)
(days)
For each of the properties, comment on whether molecular weight or the presence of a hydrogen bonding group has a more pronounced effect on chemical properties.
Boiling point (Tb) hydrogen bonding Vapor pressure (Pvp)^ hydrogen bonding Henry’s Law constant hydrogen bonding Octanol-water partition coefficient both Water solubility (S) hydrogen bonding Soil sorption coefficient hydrogen bonding Atmospheric half life molecular weight Biodegradability neither
4. Benzene discharge to a river. Total discharge rate to POTW = 2,000 kg benzene / day Removal efficiency in POTW = 85% Net benzene discharge to river = (1-.85) 2,000 kg benzene/day = 300 kg benzene/day
a) Estimate fraction of benzene in water, sediment, and biota at discharge point. From EPIwin, CAS no. 71-43- Log Koc = 2.219, Koc = 165.5 L water/kg or kg water/kg sediment carbon Log BCF = 0.940, BCF = 8.712 L water/kg or kg water/kg biota
Based on the river flow rate the total flow rates of water, sediment and biota are:
Water: (1,250 x10 6 liter/day * 1 kg/liter) = 1,250 x10^6 kg/day Sediment: 1,250 x10 6 kg/day * 15 kg sediment carbon/ 10^6 kg water = 18,750 kg sediment C/day Biota: 1,250 x10^6 kg/day * 0.1 kg biota/ 0.1 x10^6 kg water = 1,250 kg biota/day
Mass balance: “rate of benzene discharge to river” = “rate of benzene flow downriver in water, sediment, and biota”.
300 benzene kg/day = 1,250x10 6 kg water/day (Cwater ) + 18,750 kg sediment carbon/day (165.5 kg water/ kg sediment carbon) Cwater + 1,250 kg biota/day (8.712 kg water/kg biota) Cwater
C (^) water = 2.39x10-7^ kg benzene/kg water = .239 ppm benzene in water. Fraction benzene in water = 1,250x10^6 kg water/day (C^ water) / 300 kg benzene/day = 99.75% Fraction benzene in sediment = 18,750 kg sediment carbon/day (165.5 kg water/kg sediment carbon) C water /300 = .247% Fraction benzene in biota = 1,250 kg biota/day (8.712 kg water/kg biota) Cwater / 300 = .0009%
b) Is volatilization of benzene from the river important? Assume air above river to 10 m height is in equilibrium with benzene in water at discharge point concentration for the full 100 km length of the river. Use Henry’s constant to estimate the air concentration From EPIwin, H = 5.39x10-3^ atm-m^3 /mole
Air Concentration = H Cwater when expressed in units of moles benzene / m 3 = (5.39x10 -3^ atm-m 3 /mole)(2.39x10-7^ kg benzene/kg water)(1 mole/.07811 kg benzene)(1000 kg water / m 3 ) = 1.65x10^ -5^ atm = 1.65x10 -5^ atm (1 mole benzene/mole air•atm)(.07811 kg benzene/mole bz) (1 mole air/.0224 m^3 air) = 5.75x10^ -5^ kg benzene / m^3 air Total Benzene in air = (5.75x10 -5^ kg /m 3 air)(10 m)(30 m)(43.2 km)(1000 m/km) = 745 kg benz
Note – 43.2 km is the distance that the river flows in 1 day. Because this estimate is much greater than the input of benzene into the river, volatilization is important.
c) Estimate the fraction that biodegrades prior to reaching the water inlet 100 km downriver. Time to reach 100 km downriver is (100 km)/(43.2 km/day) = 2.3 days From EPIwin, biodegradation takes weeks – months, so fraction biodegraded is insignificant.
d) Estimate the potential toxicity of the releases to aquatic life From EPIwin, Log Kow = 1.99, MW = 78. A correlation for toxicity to guppies for chlorobenzenes is given by log (1/LC (^) 50) = 0.871 log K (^) ow - 4.87, where LC50is expressed in units of F 06 Dmol/L.
log (1/LC (^) 50) = 0.871 (1.99) - 4.87 = -3. 1/LC 50 = 10-3.14^ = 7.30x10^ - LC 50 = 1,370 F 06 Dmol/L C (^) water = 2.39x10-7^ kg benzene/kg water from part a) = 2.39x10 -4^ g benzene/L water = 3.06 F 06 Dmol/L, thus this concentration is not likely to pose a risk to fish since it is much less than the LC (^) 50.