
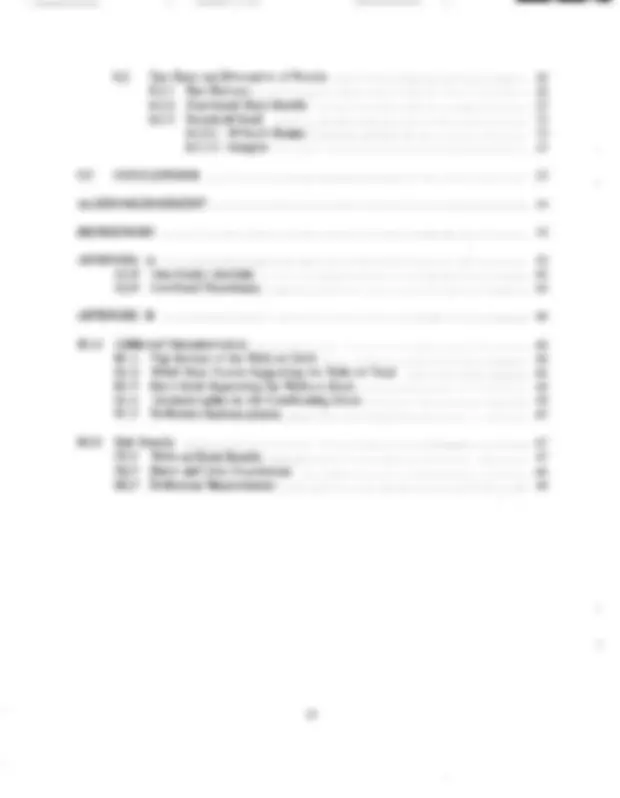
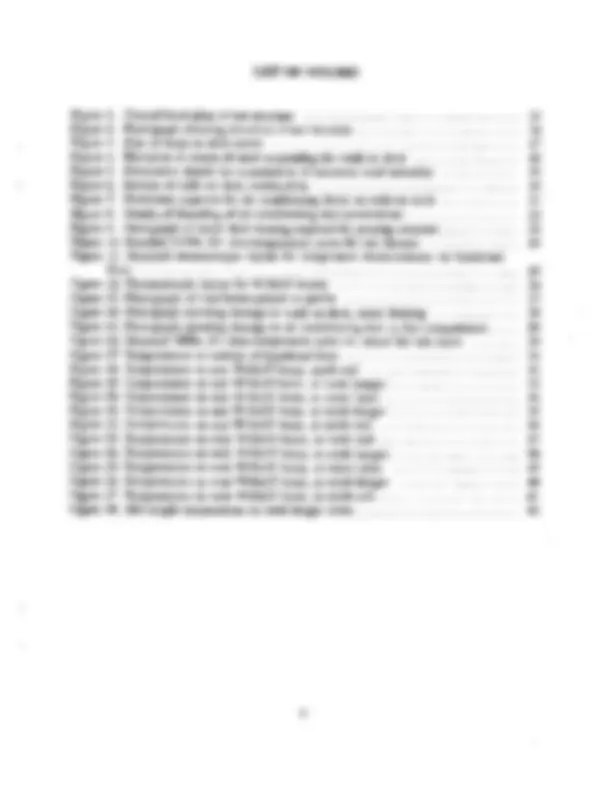

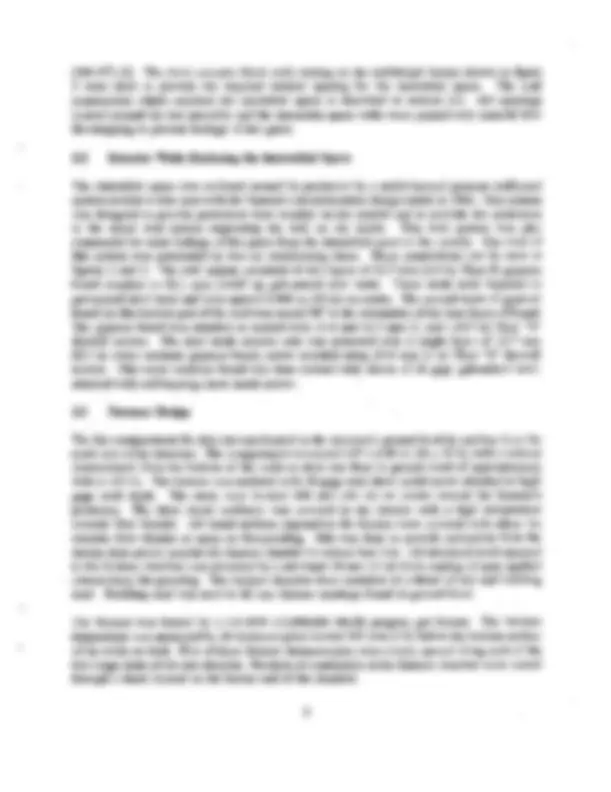
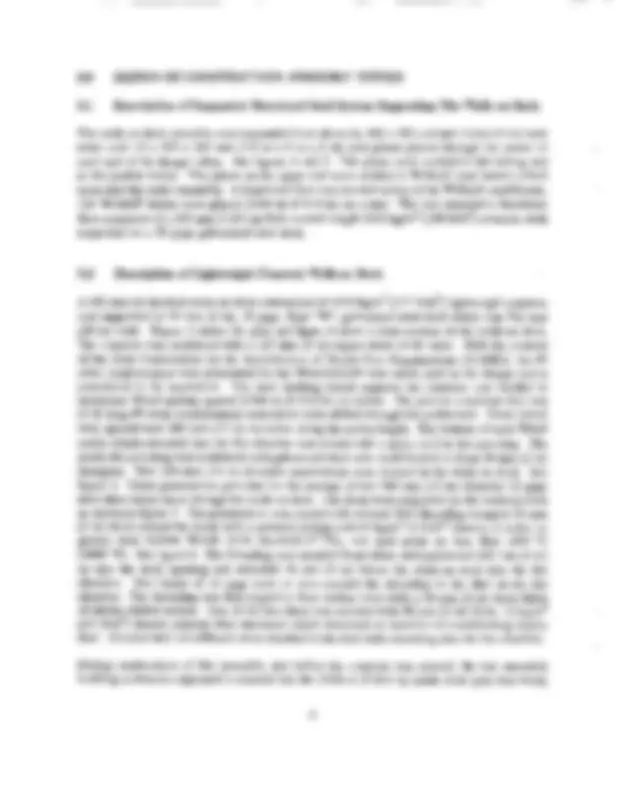
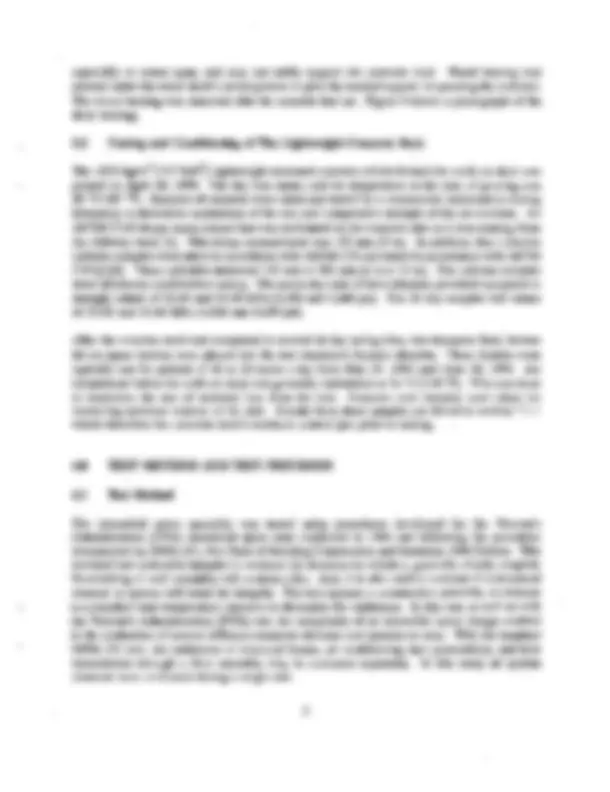
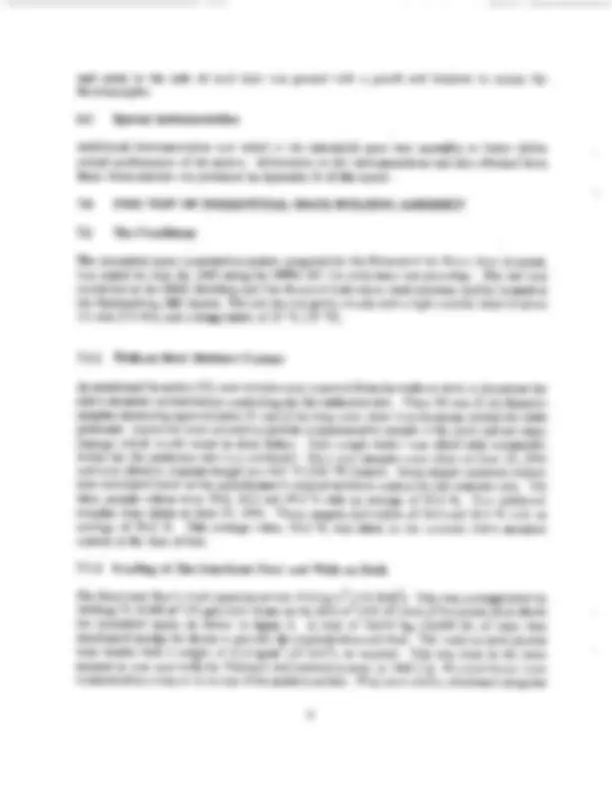
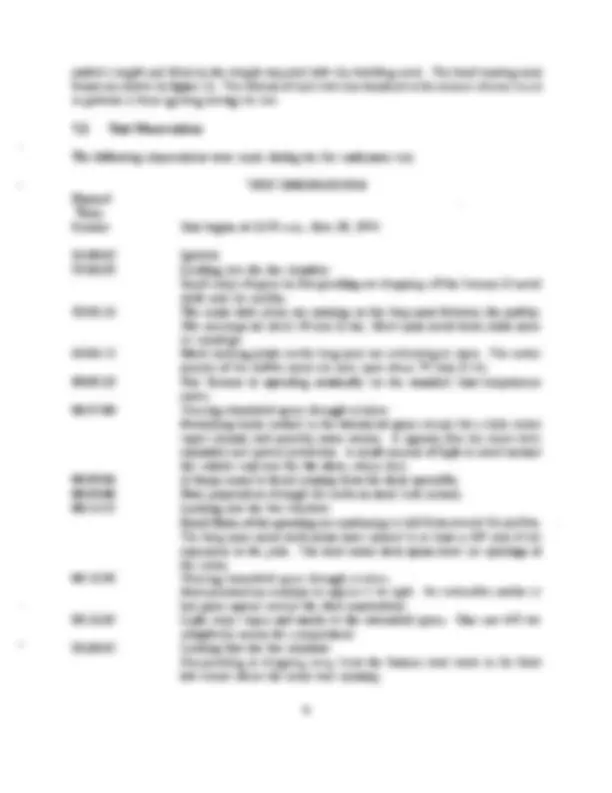

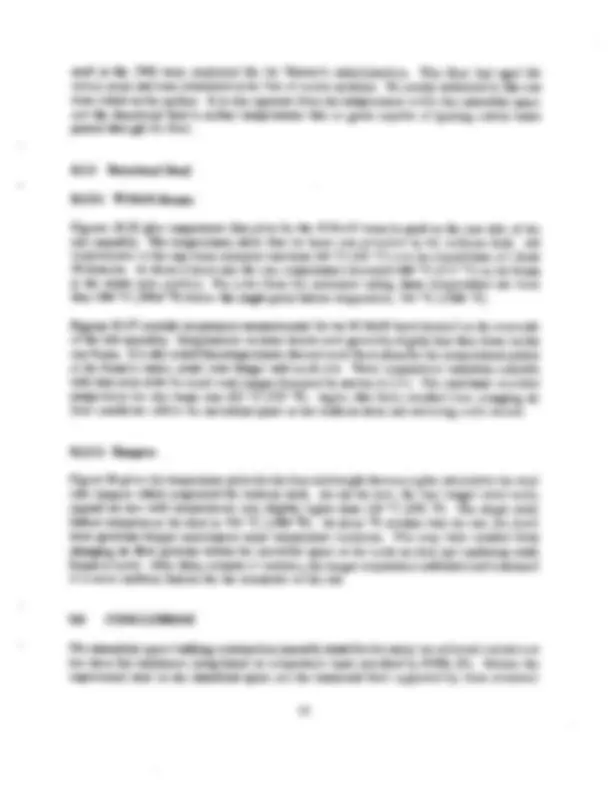
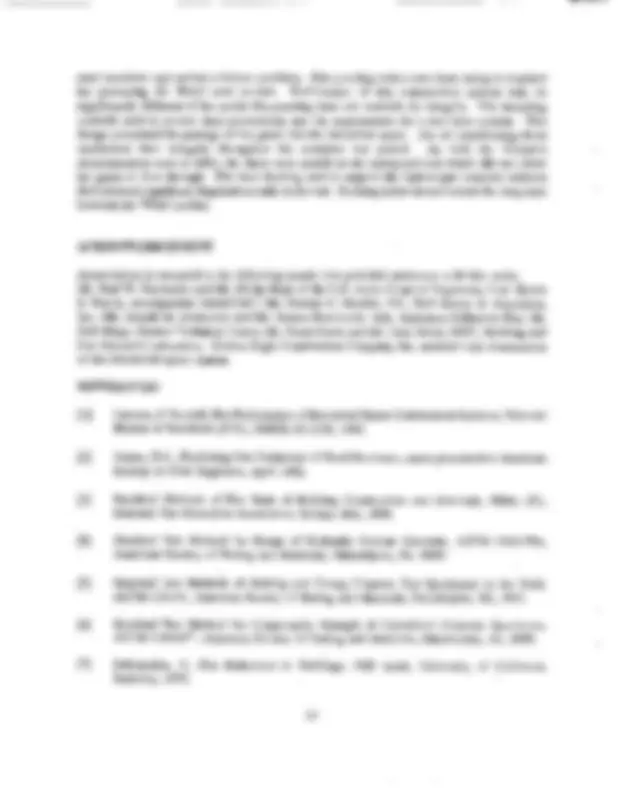
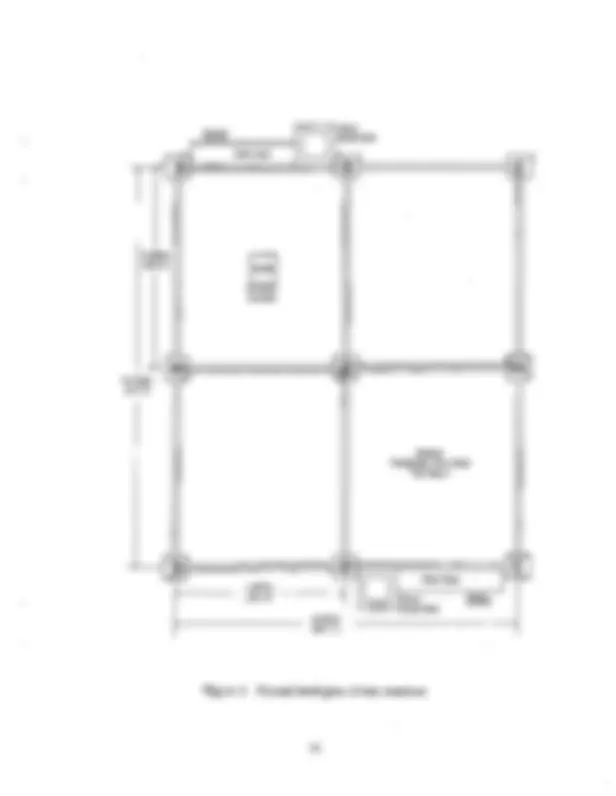
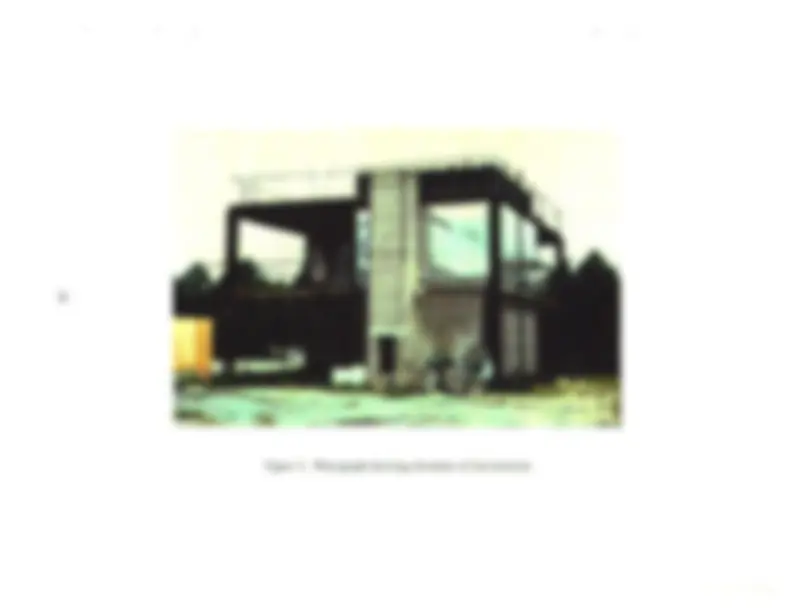
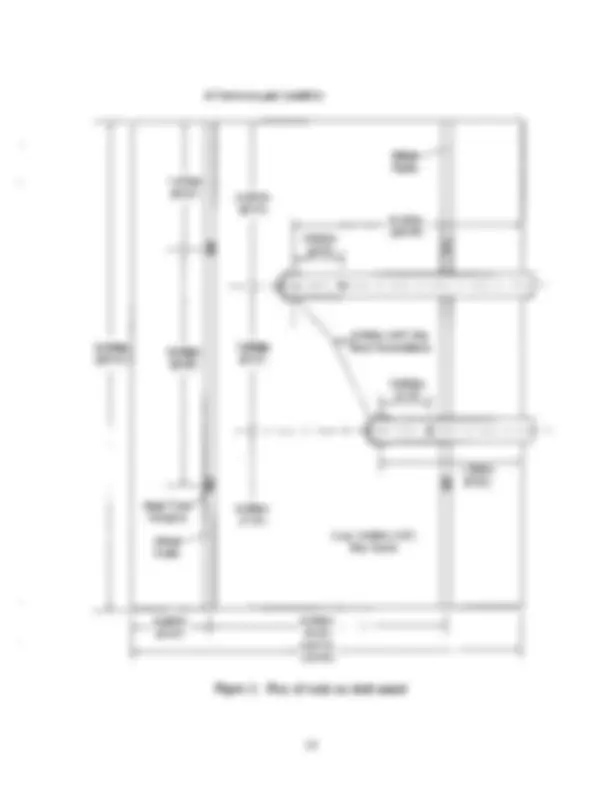
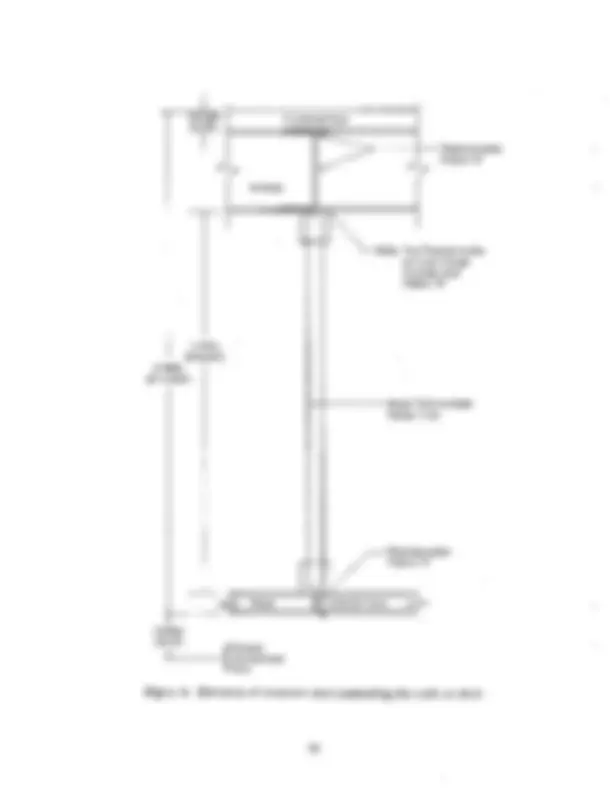
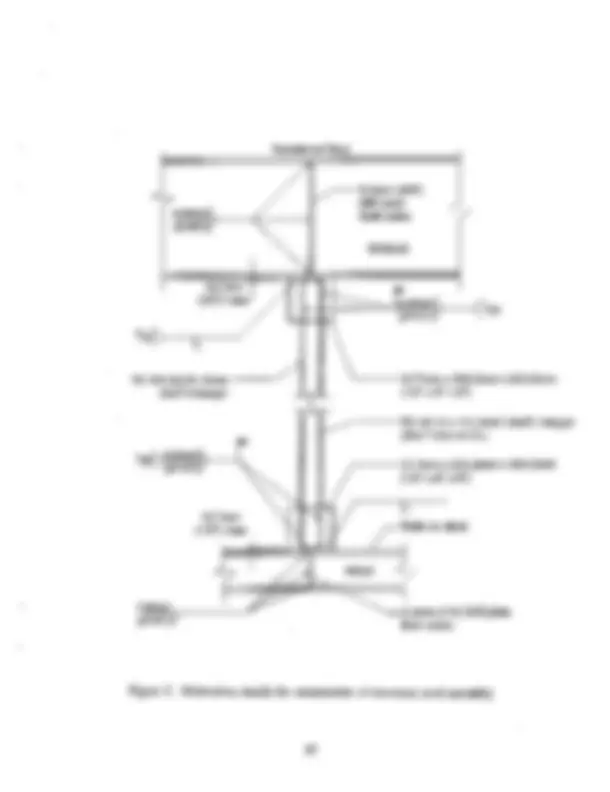
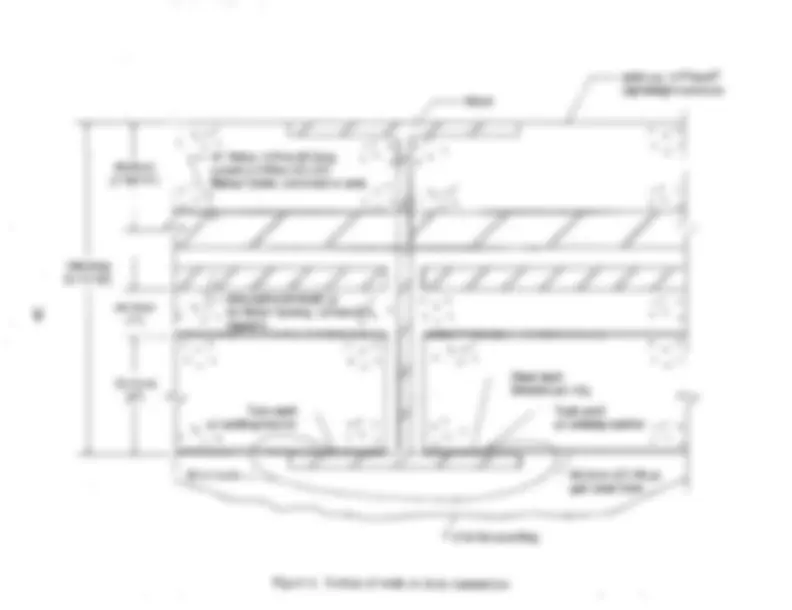
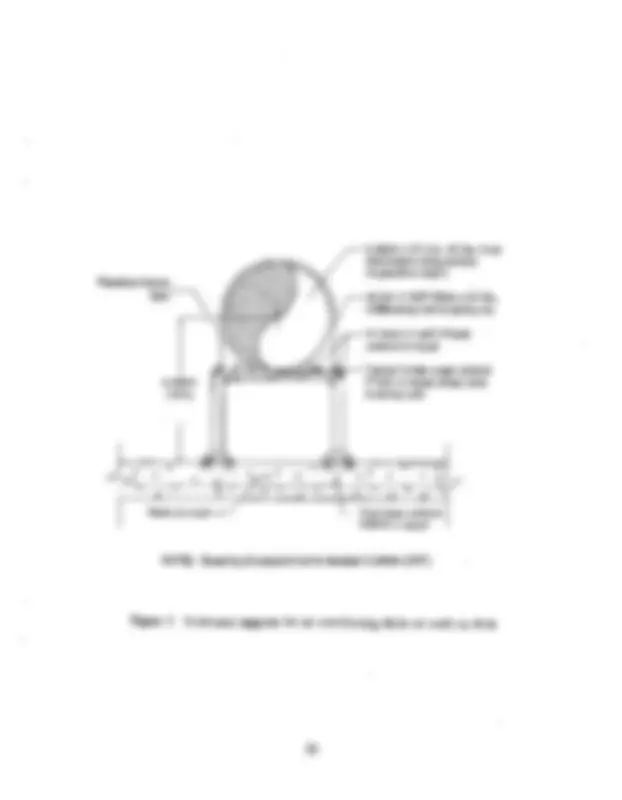
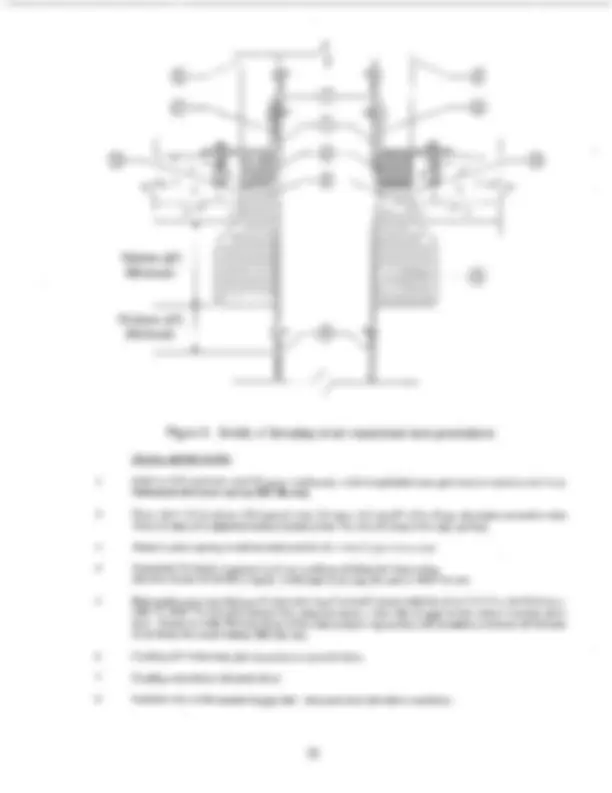
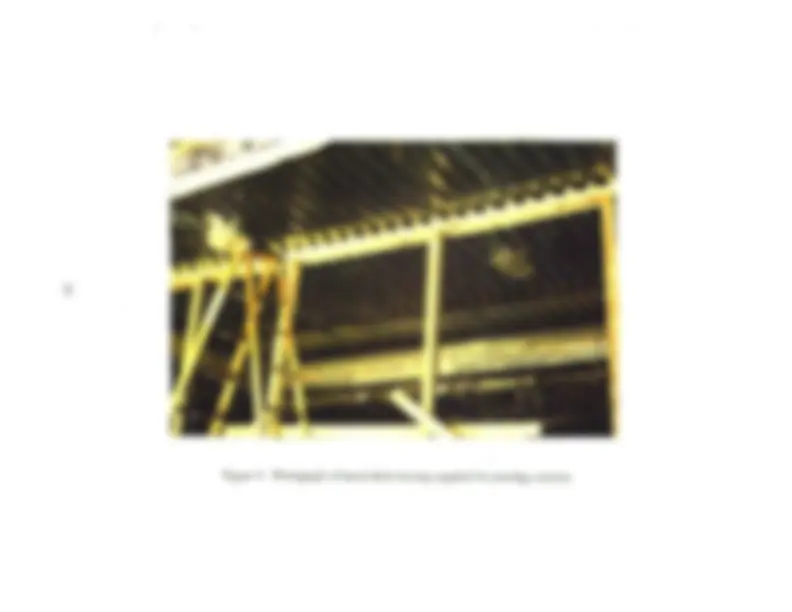
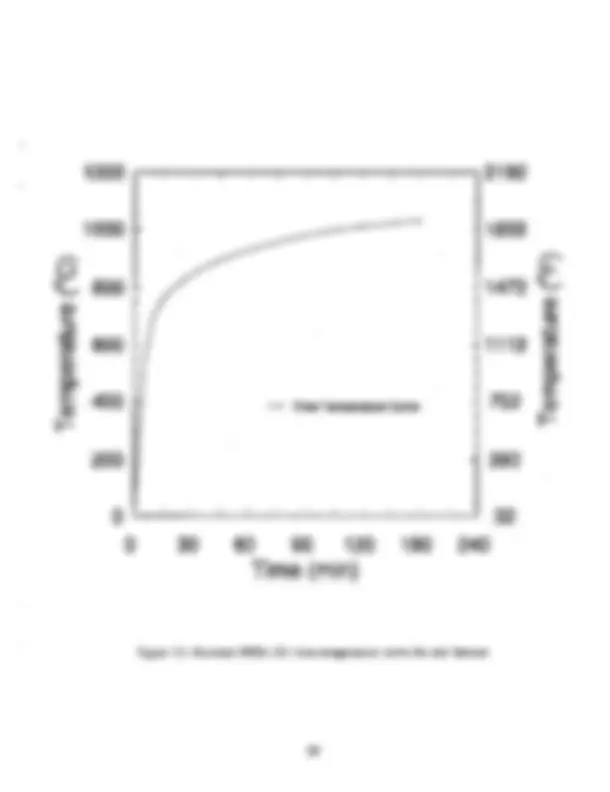
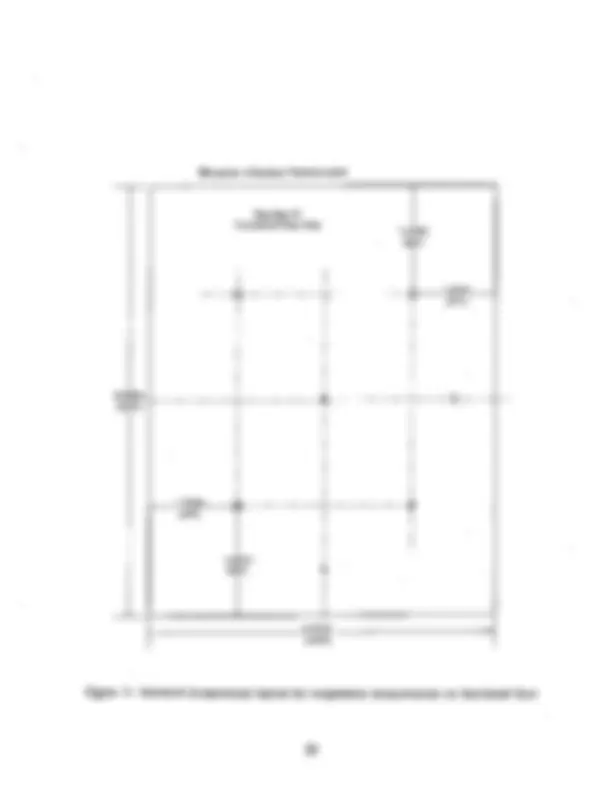
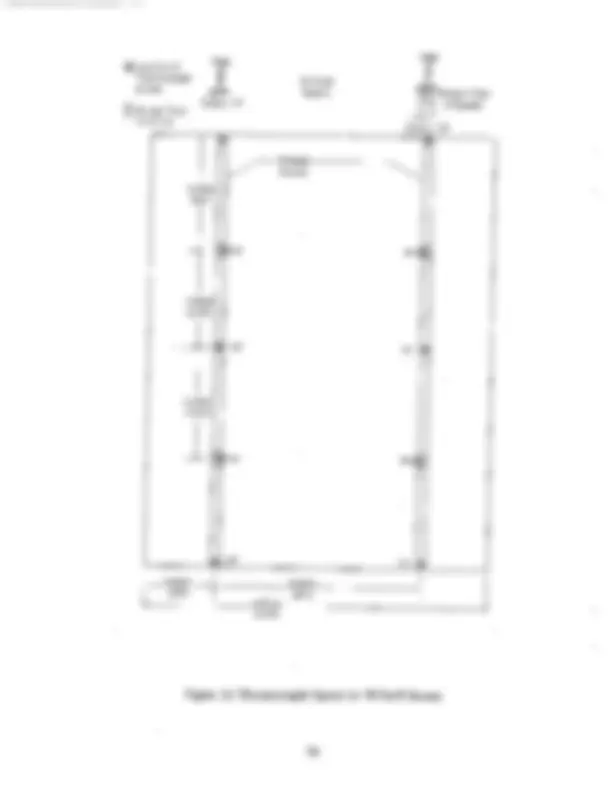
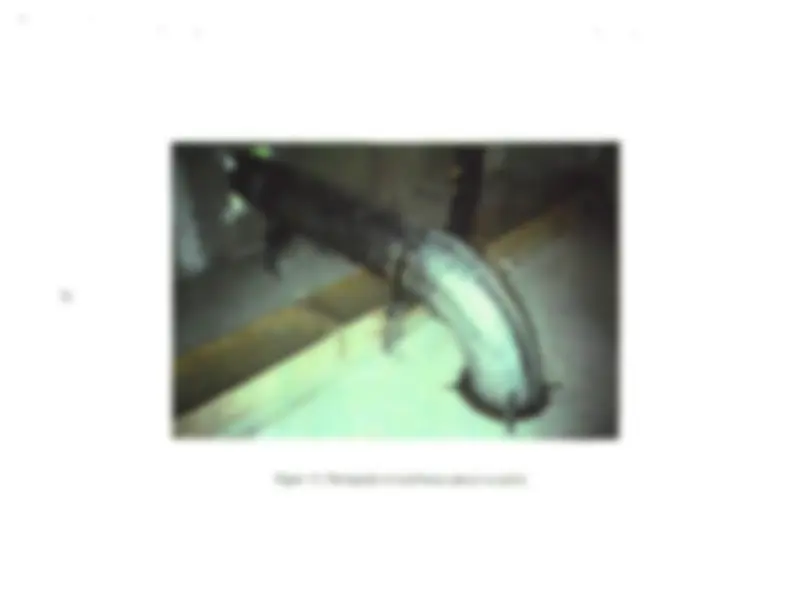
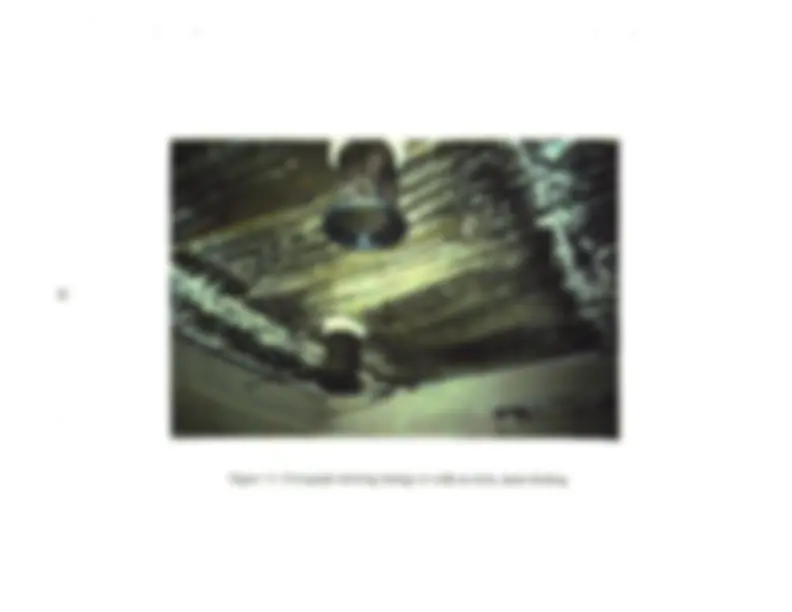
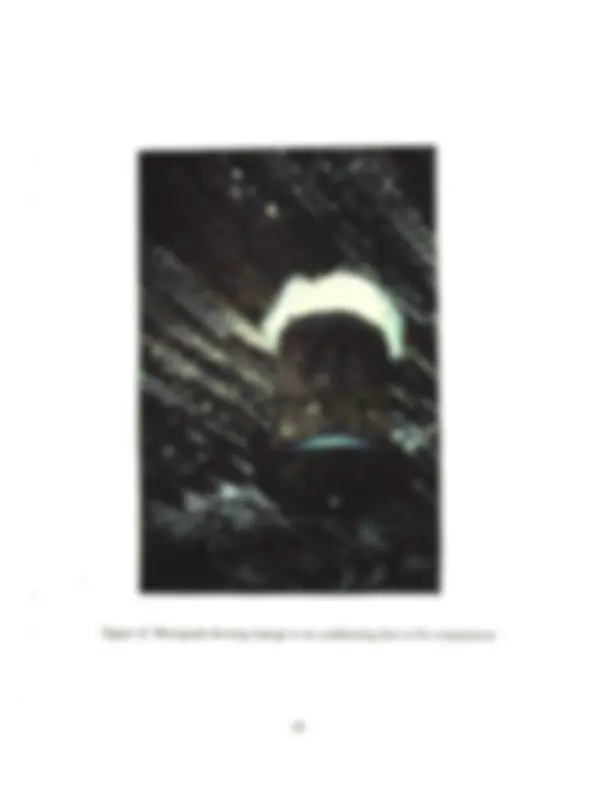
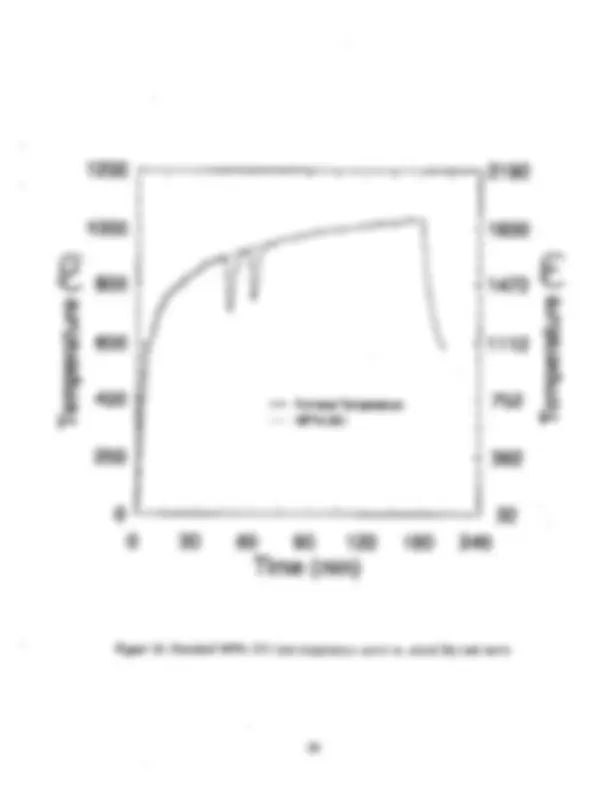
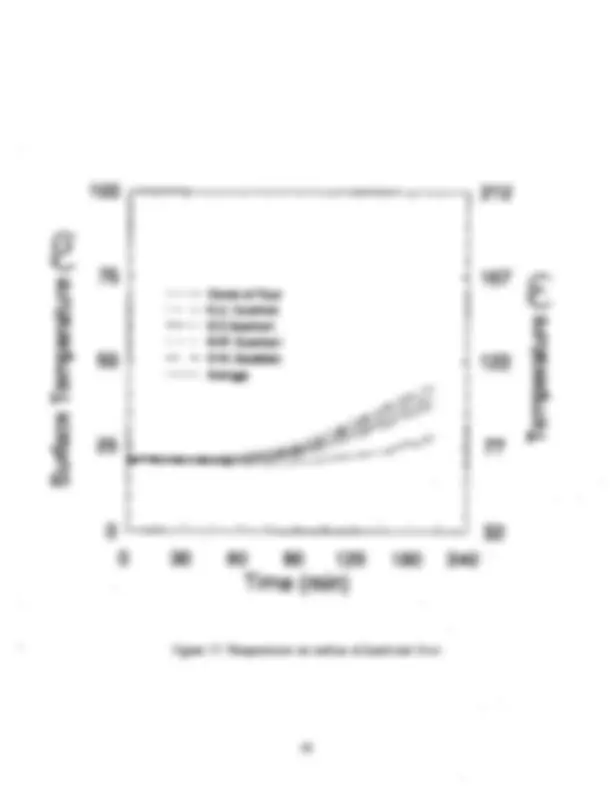
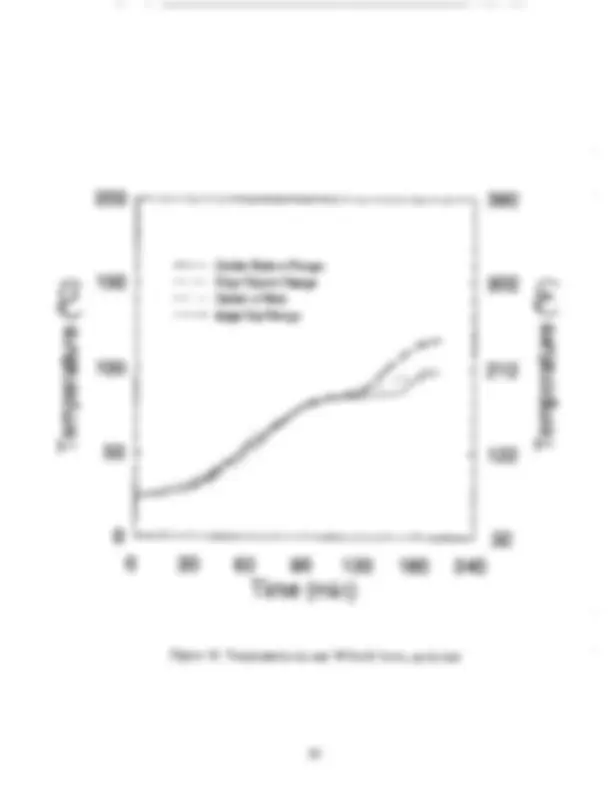
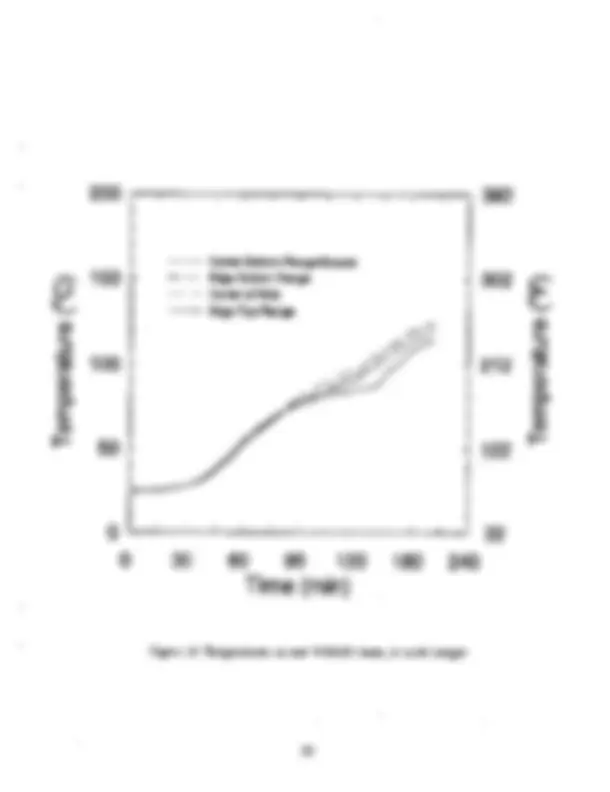
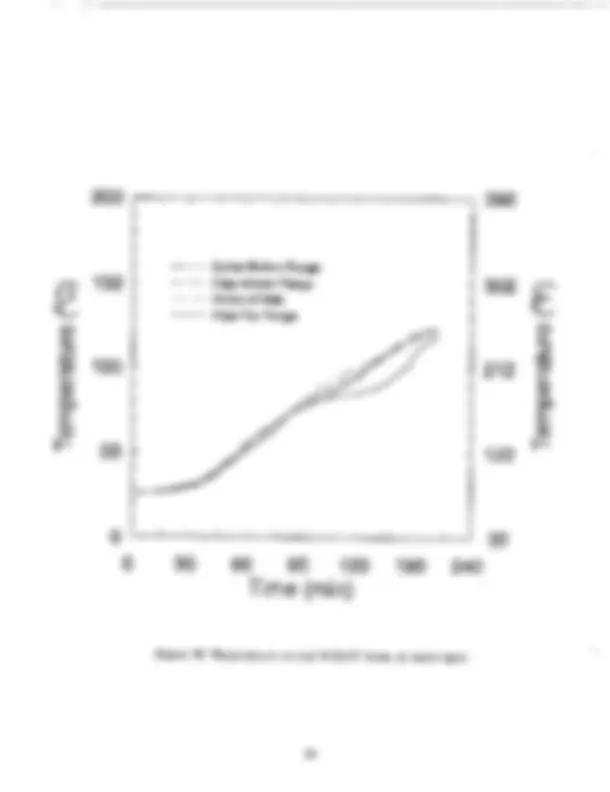
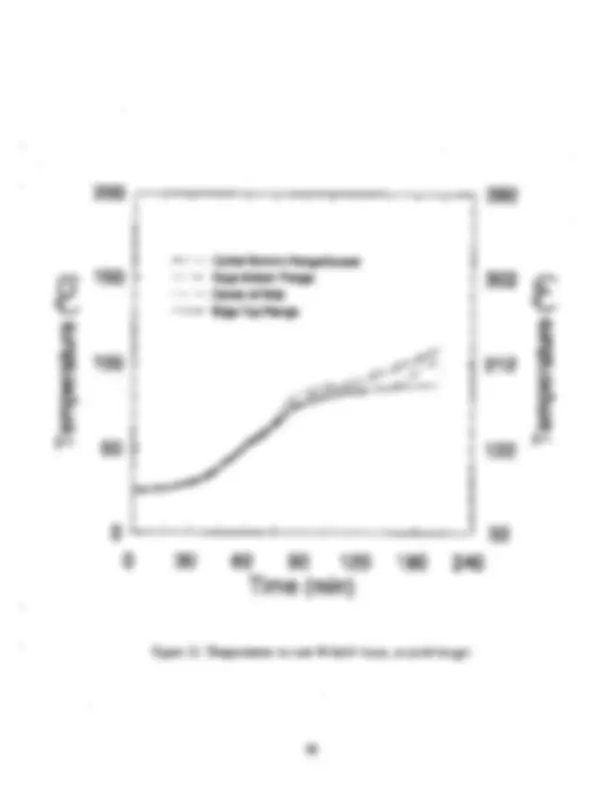
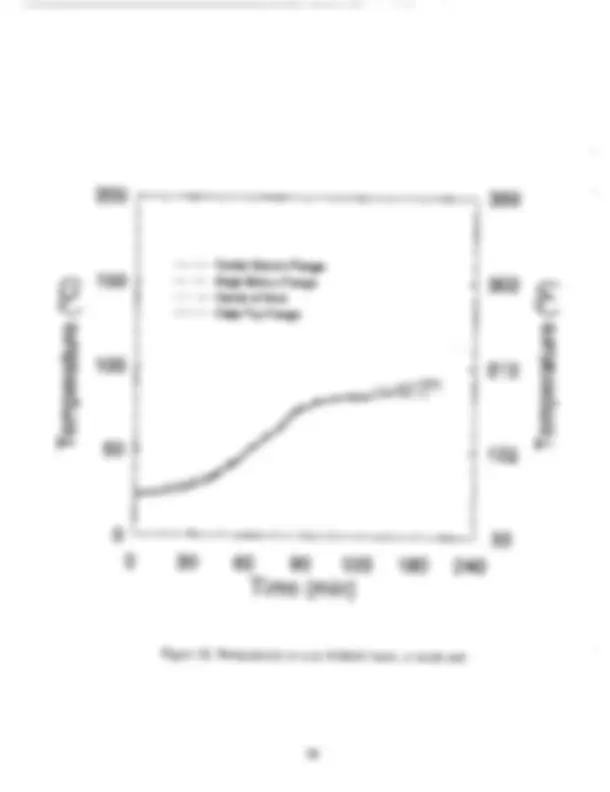
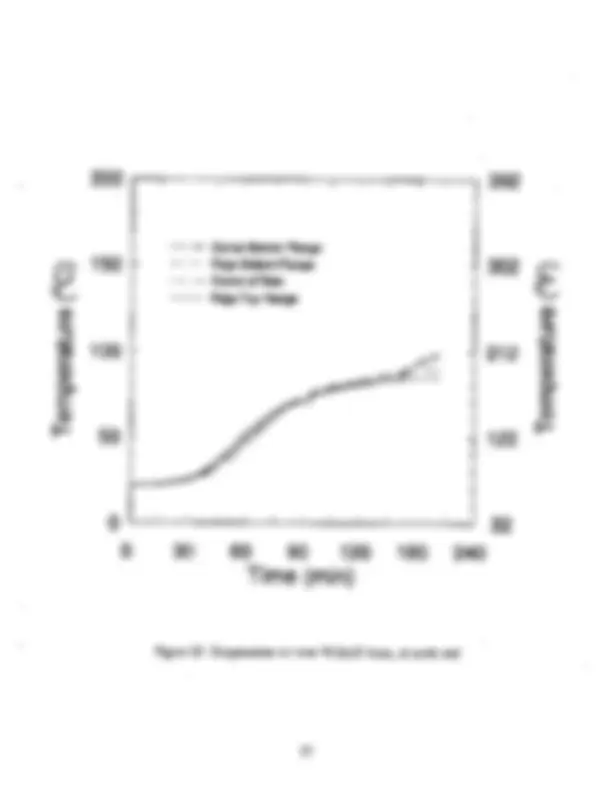
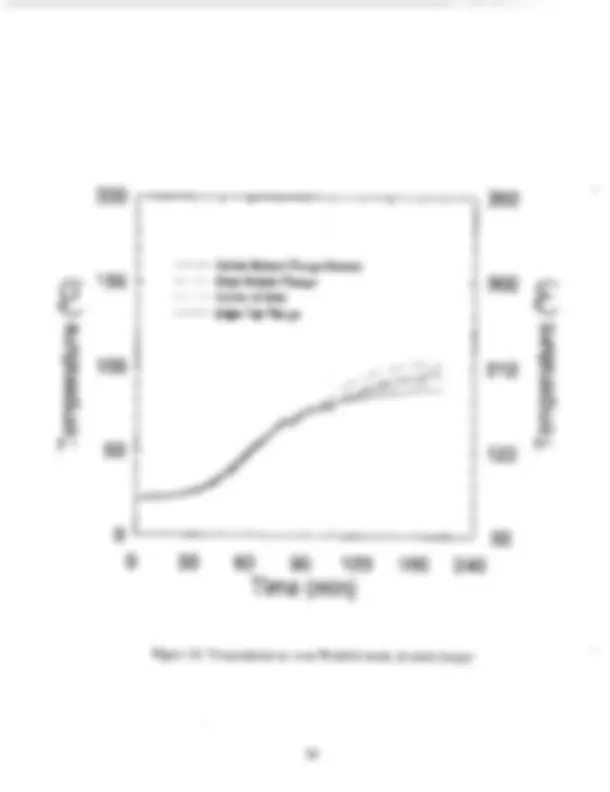
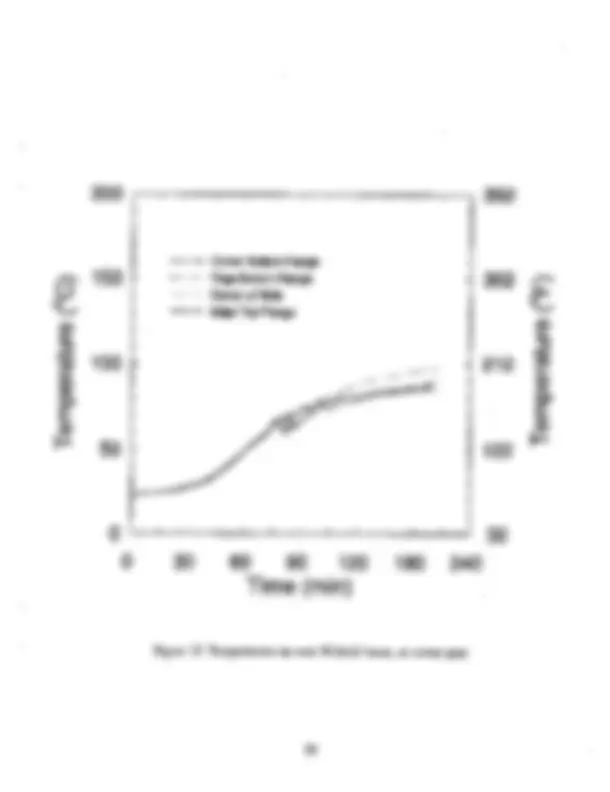
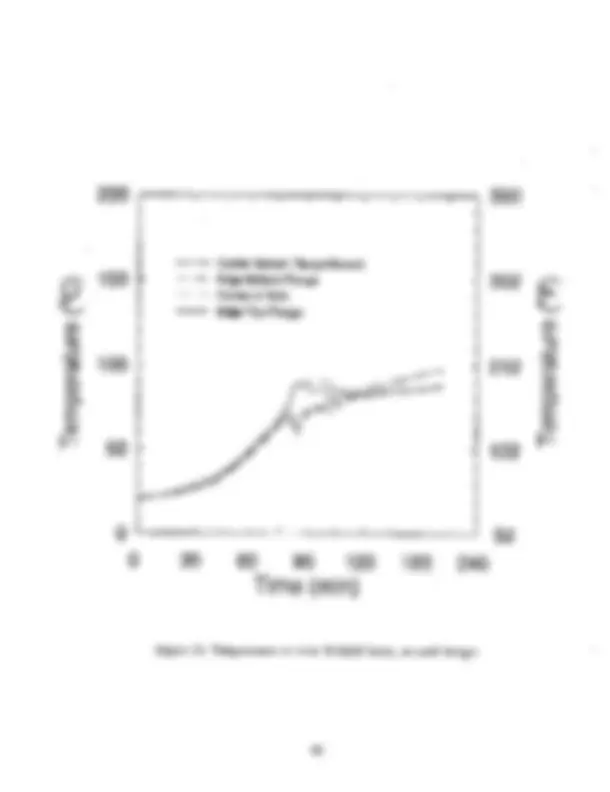

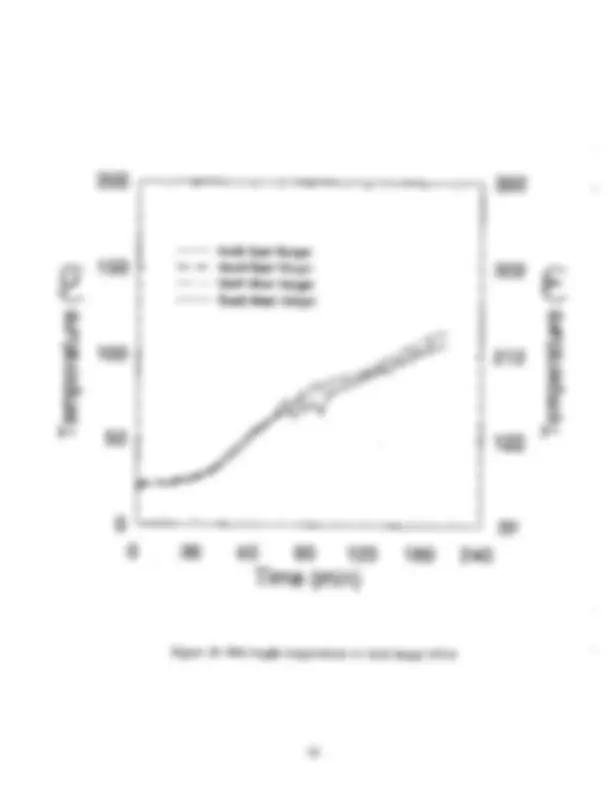
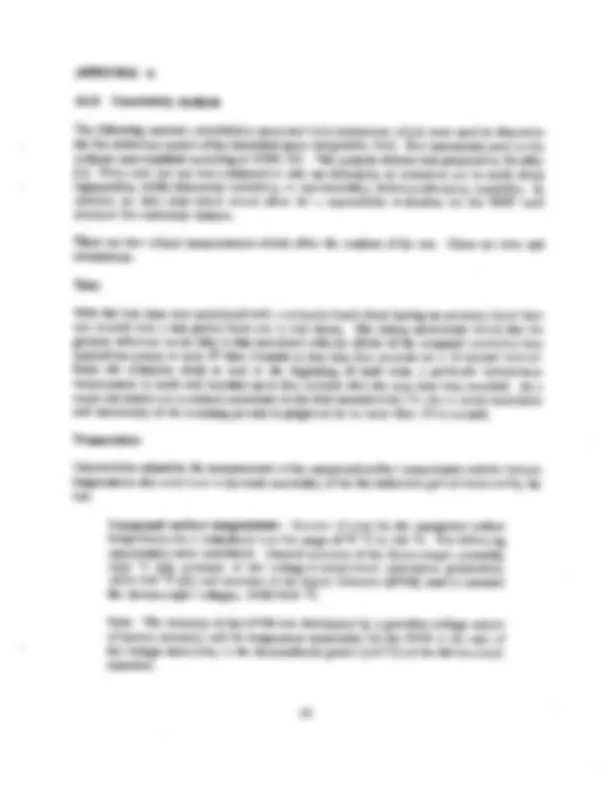
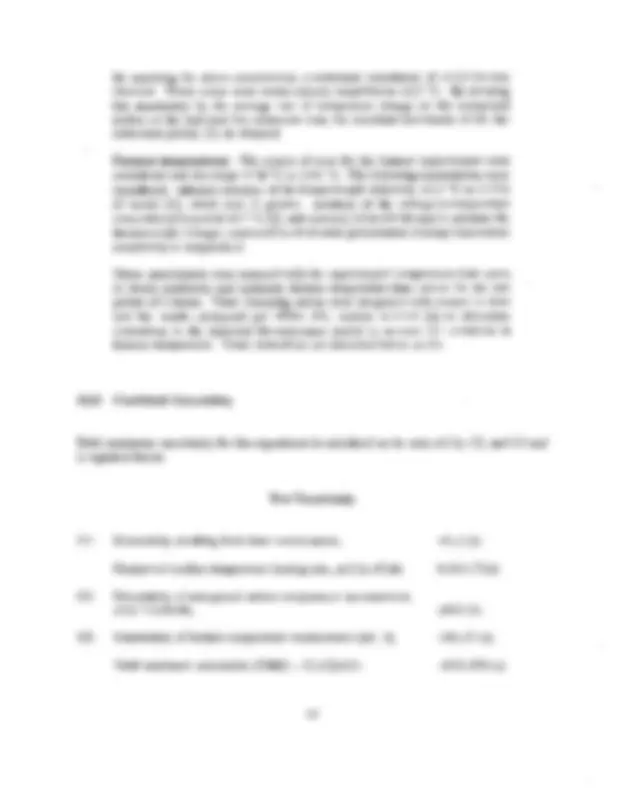
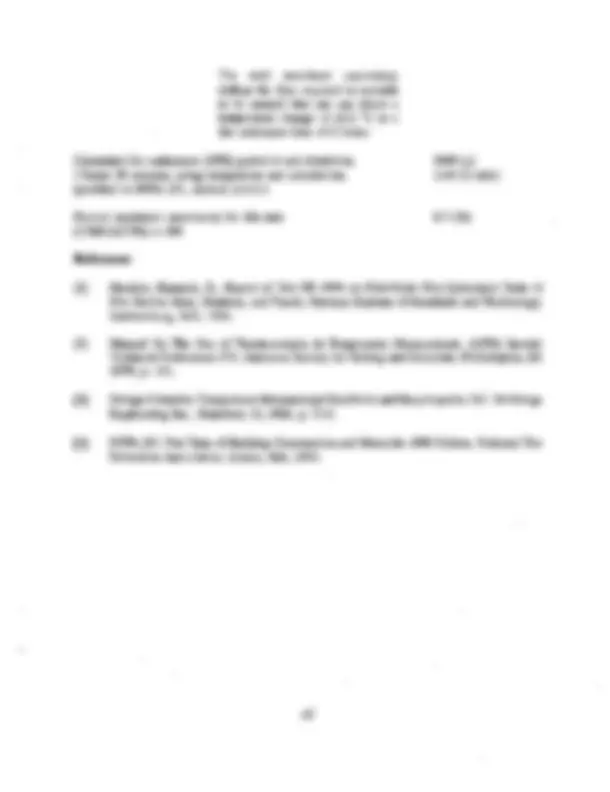
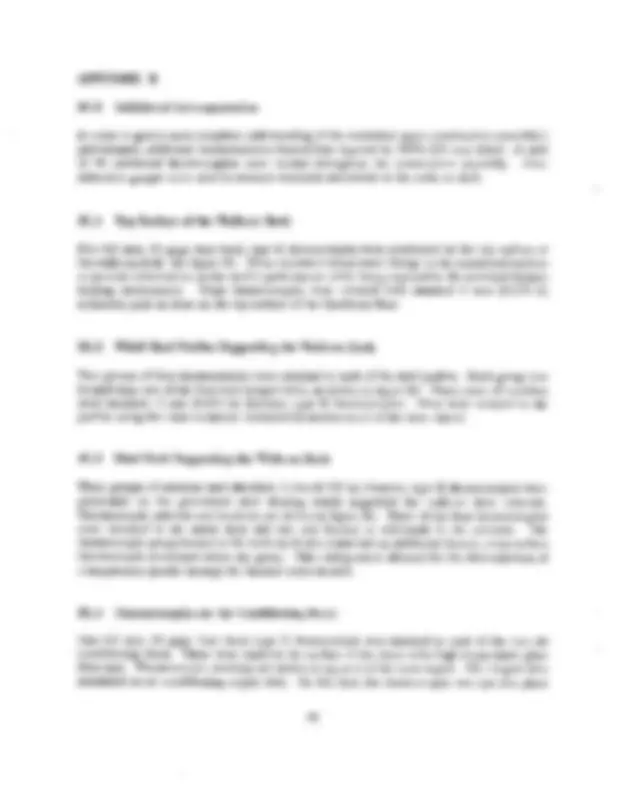
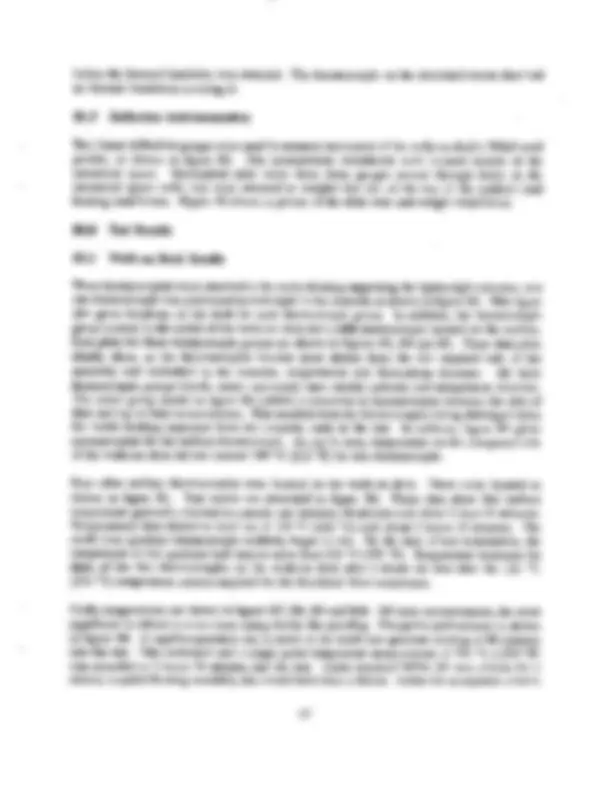
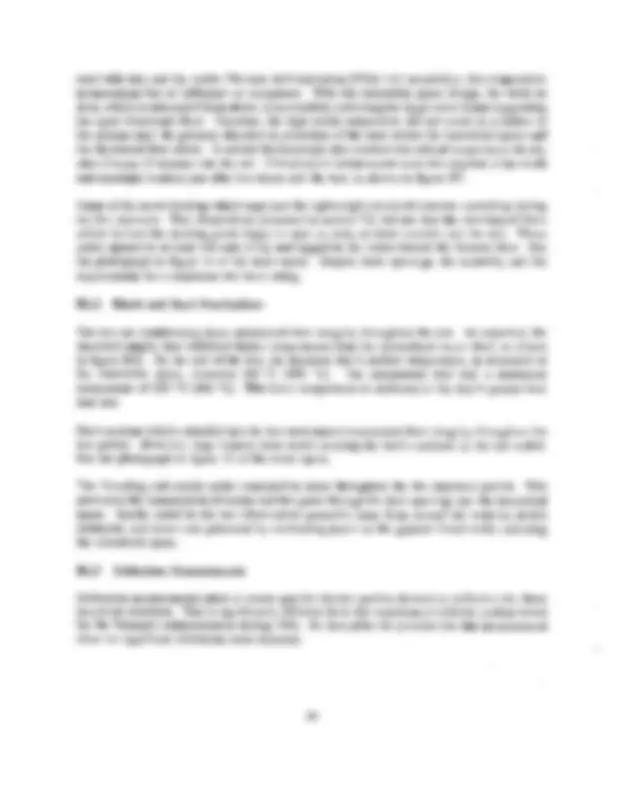
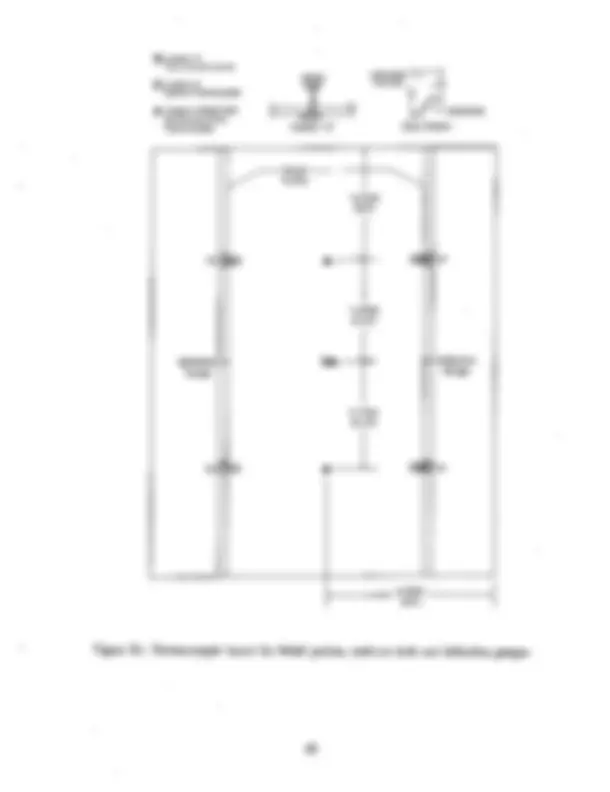
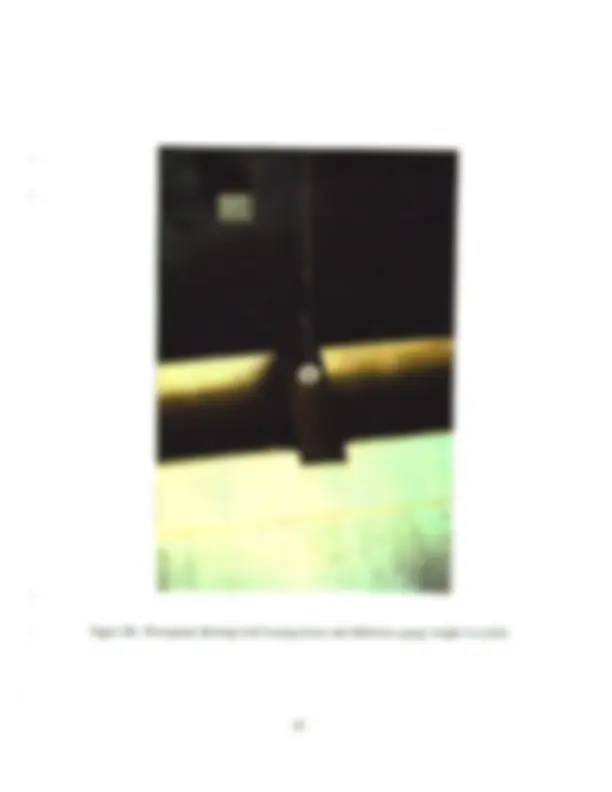
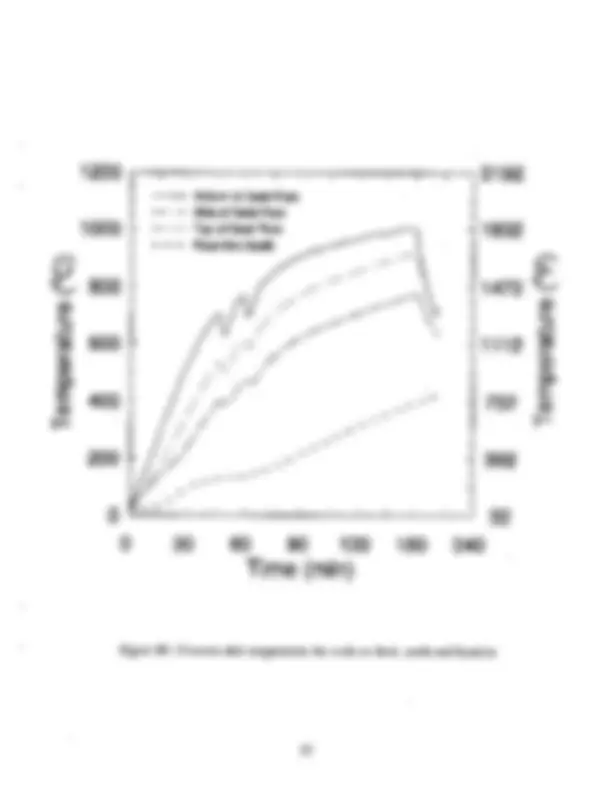
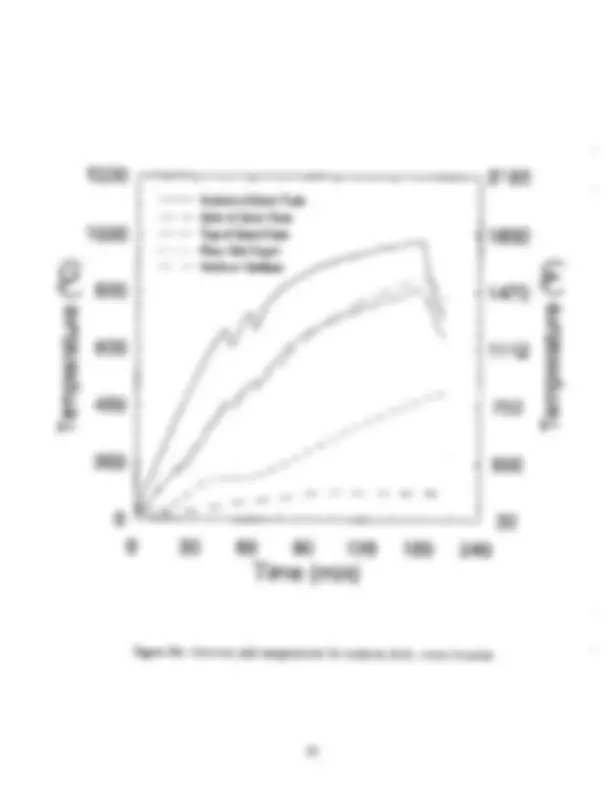
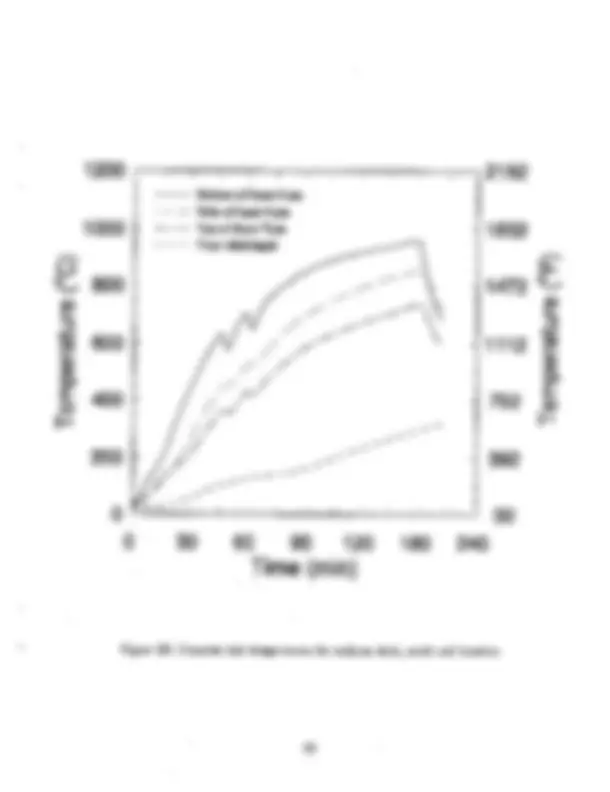
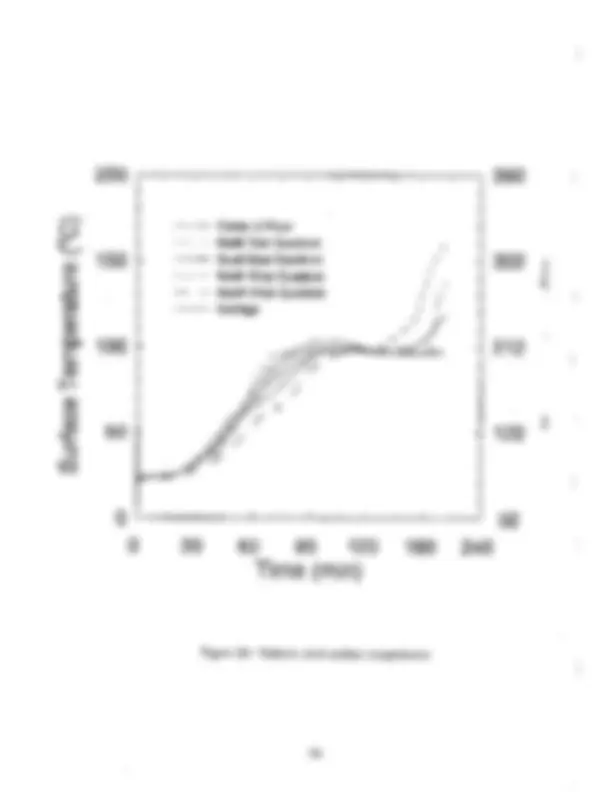
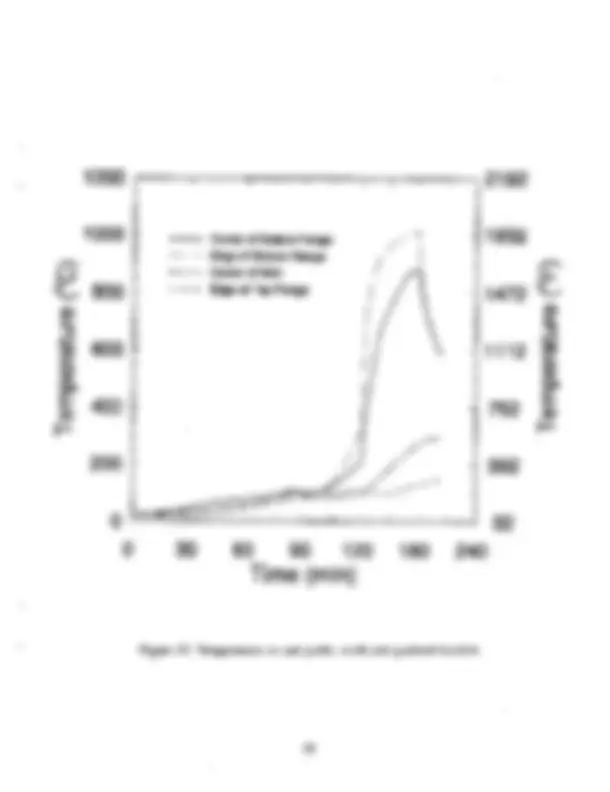
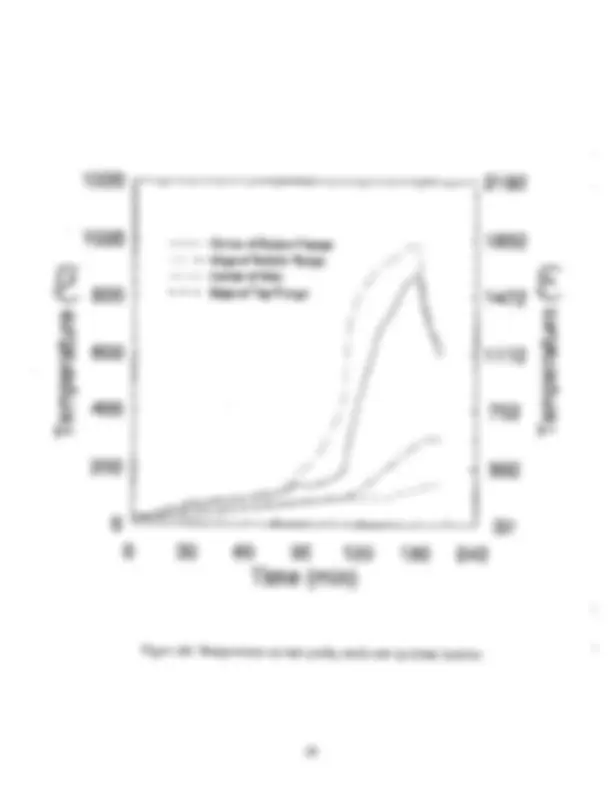
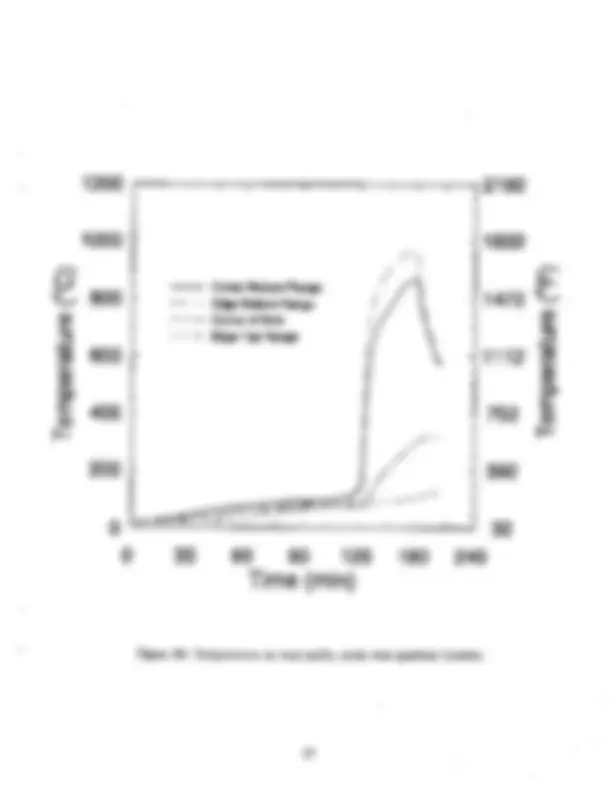
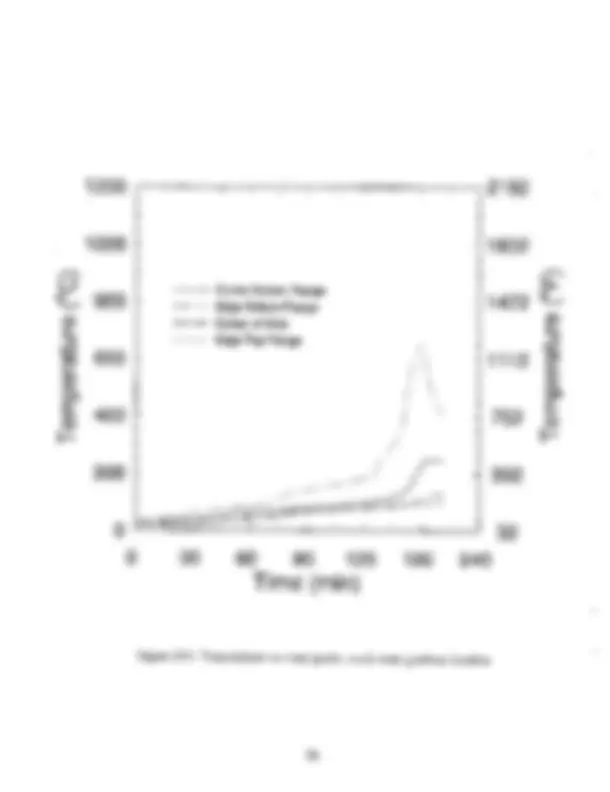
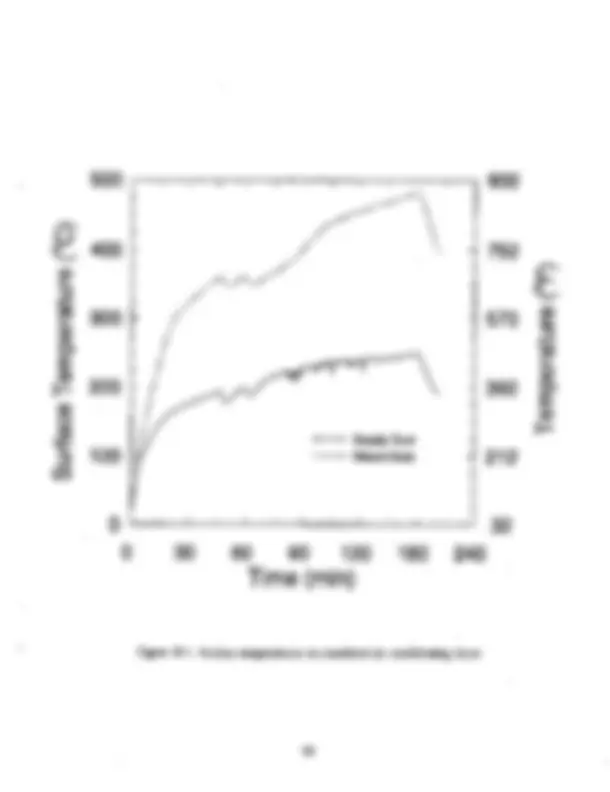
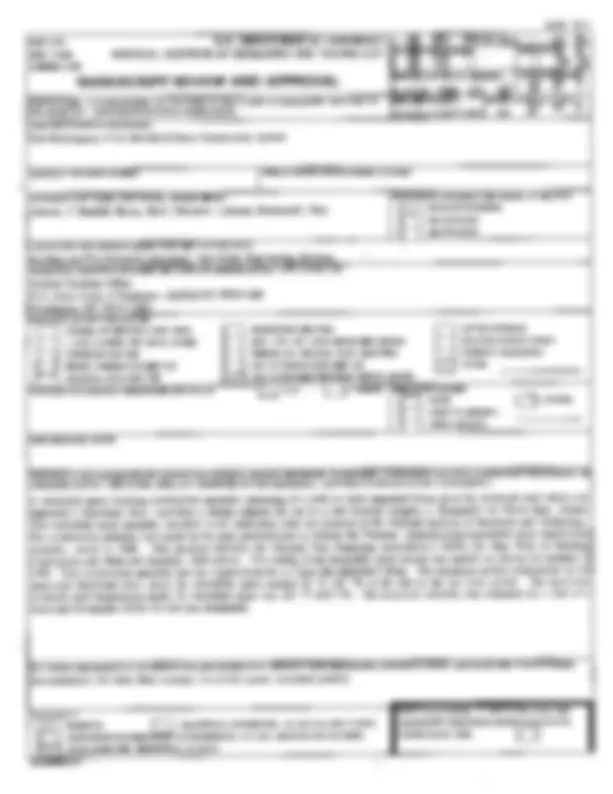
Study with the several resources on Docsity
Earn points by helping other students or get them with a premium plan
Prepare for your exams
Study with the several resources on Docsity
Earn points to download
Earn points by helping other students or get them with a premium plan
Community
Ask the community for help and clear up your study doubts
Discover the best universities in your country according to Docsity users
Free resources
Download our free guides on studying techniques, anxiety management strategies, and thesis advice from Docsity tutors
Details of a fire endurance test conducted on an interstitial space assembly, including temperature measurements on various components such as beams, purlins, and concrete slabs. The document also discusses the uncertainties associated with the time and temperature measurements used in the test. The test was carried out in accordance with NFPA 251 standards.
Typology: Exams
1 / 65
This page cannot be seen from the preview
Don't miss anything!
,-
.
Fire Performance of an Interstitial Space
Construction System
J. R. Lawson, E. Braun, L. DeLauter and G. Roadarmel
February 1995 Building and Fire Research Laboratory National Institute of Standards and Technology Gaithersburg, MD 20899
U.S. Department of Commerce (^) Sponsored by: Ronald H. Brown, Secretary Technology Administration (^) Medical Facilities Office Mary L. Good, Under Secretary for Technology (^) U.S. Army Corps of Engineers National Institute of Standards and Technology (^) HQUSACE CEMP-EM Arati Prabhakar, Director (^) Washington, DC 20314-
page LIST OF FIGURES................................................. V .
- INTRODUCI’ION s - SUPPORTING TEST STRUCTURE AND FIRE TEST FURNACE - 2.1 Test Structure - Exterior Walls Enclosing the Interstitial Space - 2.3 FurnaceDesig n - DESIGN OF CONSTRUCTION ASSEMBLY TESTED - Deck 3.1 DescriptionofSuspended Structural Steel System SupportingTheWalk-on - 3.2 Description of Lightweight Concrete Walk-on Deck - 3.3 Curing and Conditioning ofThe Lightweight Concrete Deck - TEST METHOD AND TEST PRECISION - 4.1 Test Method - 4.2 Test Method Uncertainty - ACCEPTANCE CRITERIA - INTERSTITIAL SPACE ASSEMBLY INSTRUMENTA~ON - 6.1 Thermocouple Locations Specified by NFPA - 6.1.1 Top Surface ofthe Functional Floor - 6.1.2 Steel Beams Supporting the Functional Floor and Walk-on Deck - 6.2 Special Instrumentation - FIRE TEST OF INTERSTITIAL SPACE BUILDING ASSEMBLY - 7.1 Test Conditions - 7.1.1 Walk-on Deck Moisture Content - 7.1.2 Loading of The Functional Floor and Walk-on Deck - 7.2 Test Obsemations - TEST RESULTS - 8.1 Post Test Observations - ,,!
Figure 1. Figure 2.
. Figure 3. Figure 4. Figure 5. d (^) Figure 6.
Figure 7. Figure 8. Figure 9.
Ground level plan oftest structure............................... 15 Photograph showing elevation of test structure....................... 16 Plan ofwalk-on deck tested.................................... 17 Elevation of structural steel suspending the walk-on deck............... 18 Fabrication details for construction of structural steel assembly........... 19 Section ofwalk-on deck construction............................. 20 Horizontal supports for air conditioning ducts on walk-on deck........... 21 Details of firesafing of air conditioning duct penetrations................ 22 Photograph of metal deck bracing required for pouring concrete........... 23 Figure 10. Standard NFPA 251 time-temperature curve for test furnace............. 24 Figure 11. Standard thermocouple layout for temperature measurements on functional floor....................................................... 25 Figure 12. Figure 13. Figure 14. Figure 15. Figure 16. Figure 17. Figure 18. Figure 19. Figure 20. Figure 21. Figure 22. Figure 23.
Thermocouple layout for W18x35 beams.......................... 26 Photograph ofloadboxes placed on purlin......................... 27 Photograph showing damage to walk-on deck, metal decking............ 28 Photograph showing damage to air conditioning duet in fire compartment.... 29 Standard NFPA 251 time-temperature curve vs. actual fire test curve....... 30 Temperatures onsurface of functional floor......................... 31 Temperatures on east W18X35 beam, north end...................... 32 Temperatures on east W18X35 beam, at north hanger.................. 33 Temperatures on east W18X35 beam, at center span................... 34 Temperatures on east W18X35 beam, at south hanger.................. 35 Temperatures on east W18X35 beam, at south end.................... 36 Temperatures on west W18X35 beam, at north end.................... 37 Figure 24. Temperatures on west W18X35 beam, at north hanger.................. 38 Figure 25. Temperatures on west W18X35 beam, at center span.................. 39 Figure 26. Temperatures on west W18X35 beam, at south hanger................. 40 Figure 27. Temperatures on west W18X35 beam, at south end.................... 41 Fi@re 28. Mid-height temperatures on deck hanger tubes....................... 42
LIST OF FIGUmS - APPENDIX B
Figure
Figure
Figure Figure Figure Figure Figure Figure Figure Figure Figure
B1. Thermocouple layout for W6X9 purlins, walk-on deck and deflection gauges..................................................... 49 B2. Photograph showing load bearing boxes and deflection gauge weight on purlin.............. ..a..................................... 50 B3. Concrete slab temperatures forwalk-on deck, north end location.......... 51 B4. Concrete slab temperatures for walk-on deck, center location............ 52 B5. Concrete slab temperatures for walk-on deck, south end location.......... 53 B6. Walk-on deck surface temperatures.............................. 54 B7. Temperatures on east purlin, north east quadrant location............... 55 B8. Temperatures on east purlin, south east quadrant location............... 56 B9. Temperatures on west purlin, north west quadrant location.............. 57 B1O. Temperatures on west purlin, south west quadrant location............. 58 B1l. Surface temperatures on simulated air conditioning ducts.............. 59
vi
This study was initiated as a result of modifications to the original Veteran’s Administration design. Some of the significant changes were the larger size of structural steel members and increased spacing between the structural members. The suspension system which supports the walk-on deck also differs, and the new design used lightweight structural concrete instead of lightweight insulating concrete. Penetrations through the walk-on deck were also somewhat different. These alterations in the original design required that the new building assembly be tested to insure that it would successfully provide a 2 hour fire endurance rating. Design work on this project was coordinated through the Medical Facilities Design Office of the United States Army Corps of Engineers, in Washington, DC. Also, the Joint Commission for the Accreditation of Health Care Organizations (JCAHO) provided guidance on acceptable design criteria for the system. The United States Air Force provided funds for the study through the Corps of Engineers and monitored progress of the project. (^) Original work on the new design and modifications was carried out by Anderson DeBartolo Pan and Rolf Jensen & Associates, Inc. 1 The National Institute of Standards and Technology, Building and Fire Research Laboratory assisted with design issues, constructed the test assembly and conducted the fire endurance test.
2.0 SUPPORTING TEST STRUCTURE AND FIRE TEST FUWACE
2.1 Test Structure
The steel structure used in evaluating the fire endurance of the new Elmendorf AFB hospital interstitial space design was the same structure used to test the Veteran’s Administration (DVA) interstitial design during 1983 [1]. This test structure was originally built to replicate a corner section of a mid-height twenty story steel frame building. It was built to provide an experimental structure for a series of tests conducted by the American Iron and Steel Institute (AKN) and the National Bureau of Standards (NBS and currently NIST) [2]. A ground level plan of the structure is shown in figure 1, and the elevation is shown in the photograph of figure 2. Note: For all figures showing a plan design or instrumentation layout, north is located at the top of the drawing. The structure consists of three levels. In this test, the ground level served as the fire compartment and represented a patient floor. (^) The second level, figure 3, consisted of the suspended walk-on deck system which formed the lower part of the interstitial space enclosure. The top level represented the functional floor which would be a patient floor in the medical facility.
This test was conducted with the fire in Test Bay #l, as shown in figure 1. The walk-on deck had a 28.8 mz (320 ft2) surface exposed to the fire compartment. The National Fire Protection Association, NFPA 251 method requires that a test floor surface area not be less than 16.2 m
lCertain businesses, commercial equipment, instmments, or materials are identified in this paper in order to adequately specify the experimental procedure. Such identification does not imply recommendation or endorsement by the National Institute of Standards and Technology, nor does it imply that the materials or equipment identified are necessarily the best available for the purpose.
2
.
(180 ft2) [3]. The short concrete block walls resting on the mid-height beams shown in figure 2 were used to provide the required vertical spacing for the interstitial space. The wall construction which enclosed the interstitial space is described in section 2.2. All openings located around the test assembly and the interstitial space walls were packed with mineral fiber fire-stopping to prevent leakage of hot gases.
2.2 Exterior Walls Enclosing the Interstitial Space
. (^) The interstitial space was enclosed around its perimeter by a multi-layered gypsum wallboard
system similar to that used with the Veteran’s Administration design tested, in 1984. This system was designed to provide protection from weather on the outside and to provide fire protection to the metal stud system supporting the wall on the inside. This wall system was also constructed to resist leakage of hot gases from the interstitial space to the outside. One wall of this system was penetrated by two air conditioning ducts. These penetrations can be seen in figures 2 and 3. The wall system consisted of two layers of 12.7 mm (0.5 in) Type-X gypsum board attached to 92.1 mm (3.625 in) galvanized steel studs. These studs were fastened to galvanized steel track and were spaced 0.406 m (16 in) on center. The second layer of gypsum board on this interior part of the wall was turned 90° to the orientation of the base layer of board. The gypsum board was attached as needed with 25.4 and 41.3 mm (1 and 1.625 in) Type “S” drywall screws. The steel studs exterior side was protected with a single layer of 12.7 mm (0.5 in) water resistant gypsum board, screw attached using 25.4 mm (1 in) Type “S” drywall screws. This water resistant board was then covered with sheets of 28 gage galvanized steel, attached with self-tapping sheet metal screws.
23 Furnace Design
.
The fire compartment for this test was located at the structure’s ground level in test bay 1 on the south end of the structure. The compartment measured 4.87 x 6.09 m (16 x 20 ft) with a vertical measurement from the bottom of the walk-on deck test floor to ground level of approximately 3.66 m (12 ft). The fiu-nace was enclosed with 20 gage steel sheet metal screw attached to light gage steel studs. The studs were located 406 mm (16 in) on center around the furnace’s perimeter. The sheet metal enclosure was covered on the interior with a high temperature ceramic fiber blanket. All metal surfaces exposed to the furnace were covered with either the ceramic fiber blanket or spray on fire-proofing. This was done to provide protection from the intense heat and to insulate the furnace chamber to reduce heat loss. All structural steel exposed to the fbrnace chamber was protected by a minimum 50 mm (2 in) thick coating of spay applied cementitious fire-proofing. The furnace chamber floor consisted of a blend of soil and building sand. Building sand was used to fill any furnace openings found at ground level.
The furnace was heated by a 4.4 MW (15,000,000 Btu/h) propane gas burner. The furnace temperature was measured by 10 thermocouples located 305 mm (1 ft) below the bottom surface of the walk-on deck. Five of these furnace thermocouples were evenly spaced along each of the two longs sides of the test chamber. Products of combustion in the furnace chamber were vented through a stack located on the burner end of the chamber.
.
.
especially at center span, and may not safely support the concrete load. Wood bracing was erected under the metal deck’s center portion to give the needed support for pouring the concrete. The wood bracing was removed after the concrete had set. Figure 9 shows a photograph of the deck bracing.
303 Curing and Conditioning of The Lightweight Concrete Deck
The 1874 kg/m3 (117 lb/ft~ lightweight structural concrete which formed the walk-on deck was poured on April 20, 1994. The day was sunny, and the temperature at the time of pouring was 20 “C (68 “F). Samples of concrete were taken and tested by a commercial independent testing laboratory to determine consistency of the mix and compressive strength of the set concrete. An ASTM C143 slump measurement test was performed on the concrete mix as it was coming from the delivery truck [4]. This slump measurement was 152 mm (6 in). In addition, four concrete cylinder samples were taken in accordance with ASTM C31 and tested in accordance with ASTM C39 [5][6]. These cylinders measured 152 mm x 305 mm (6 in x 12 in). The cylinder samples were laboratory cured before testing. The seven day tests of two cylinders provided compressive strength values of 22.68 and 23.30 MPa (3,290 and 3,380 psi). The 28 day samples had values of 33.92 and 33.44 MPa (4,920 and 4,850 psi).
After the concrete deck had completed its normal 28 day curing time, two kerosene fired, blower driven space heaters were placed into the test structure’s furnace chamber. These heaters were typically run for periods of 16 to 24 hours a day from May 19, 1994 until June 20, 1994. Air temperature below the walk-on deck was generally maintained at 54 “C (130 “F). This was done to accelerate the rate of moisture loss from the slab. Concrete core samples were taken for measuring moisture content of the slab. Results from these samples are found in section 7.1. which describes the concrete deck’s moisture content just prior to testing.
4.1 Test Method
The interstitial space assembly was tested using procedures developed for the Veteran’s Administration (DVA) interstitial space tests conducted in 1983 and following the procedure documented in, NFPA 251, Fire Tests of Building Construction and Materials 1990 Edition. This standard test method is intended to evaluate the duration for which a, generally closely coupled, floor/ceiling or wall assembly will contain a fire. And, it is also used to evaluate if a structural element or system will retain its integrity. The test exposes a construction assembly or element ~ (^) to a standard time-temperature exposure to determine fire endurance. In this test, as well as with the Veteran’s Administration (DVA) test, the complexity of an interstitial space design resulted in the evaluation of several different structural elements and systems at once. With the standard . NFPA 251 test, fire endurance of structural beams, air conditioning duct penetrations, and heat transmission through a floor assembly may be evaluated separately. In this study all system elements were evaluated during a single test.
The fire exposure for this test was provided by a single 4.4 MW (15,000,000 13tu/h)propane gas burner located in the fire compatiment below the walk-on deck floor. A plot of the standard time-temperature curve used in NFPA 251 is shown in figure 10. The same time-ternperature curve was used for evaluation of the Veterans Administration (DVA) interstitial space designs tested in 1983, reported in NBSIR 85-3158 “Fire Performance of Interstitial Space Construction Systems.” For this test, NIST used the same steel test structure and facilities as were reported in the Veterans Administration (DVA) tests.
4.2 (^) Twt Method Uncertainty
Even though NFPA 251 is a widely used test method and has been employed for several decades, no statement of expected precision has been prepared for the standard. This may be attributed to the fact that NFPA 251 tests are generally quite costly and replicate tests are not typically conducted. (^) Usually, only one test is conducted to evaluate a large construction assembly. Duplicate tests are typically run only to evaluate improvements to a design which may have failed an earlier test. In addition, little has been done to quantify the expected variability or accuracy of the systems used to conduct the test. For these reasons, the uncertainty statement for this study is limited to instrument uncertainty during the test. Additional information on the effects of changes in test design and conduct are discussed by Babrauskas [7].
Within the standard fire endurance test are two parameters which are measured for controlling the construction system’s thermal exposure. These are the measurement of time and temperature. Experimental uncertainty for NFPA 251 is related explicitly to the uncertainty of time measurement and implicitly to uncertainties associated with temperature measurements of critical assembly components and furnace temperatures.
TWObasic elements are identified as being significant in the assessment of instrument uncertainty with this test:
1. Time measurement - This is broken down into two components, computer clock accuracy and dati acquisition delay time associated with the time between reading the computer clock and reading a thermocouple output. 2. Temperature measurement - Three elements relate to uncertainty in temperature measurements were considered: Inherent accuracy of thermocouple matirials, mathematical accumcy of voltige to temperature convemion, and accursey of the instrument md to measure thermocouple voltig~.
.
Appendix A of this report contains an uncetiainty analysis for representative time and temperature measurements made during this test. From this analysis, it was determined that the mwimum instrument uncertainty for the total fire-endurance period of two how-s thirty minutes was 9 percent.
and metal to the side of each hole was peened with a punch and hammer to secure the thermocouples.
6.2 Speial Instrumenbtion
Additional instrumentation was added to the interstitial space test assembly to better define overall performance of the system. Information on this instrumentation and data obtained from these measurements are presented in Appendix B of this report.
‘7.0 mm TEST OF INTENTIT~L SPACE BUILDING ASSEMBLY
7.1 Test Conditions
The interstitial space construction system, proposed for the Elmendorf Air Force was tested on June 28, 1994 using the NFPA 251 fire endurance test procedure.
Base Hospital, The test was conducted at the NIST, Building and Fire Research Laboratory steel st~cture facility located at it’s Gaithersburg, MD Annex. The test day was pard y cloudy with a light variable wind of about 2.2 m/s (’7.3 fVs) and a temperature of 24 ‘C (75 “F).
As mentioned in section 3.3, core samples were removed from the walk-on deck to document the slab’s moisture content before conducting the fire endurance test. These 50 mm (2 in) diameter samples measuring approximately 50 mm (2 in) long were taken from locations around the slabs perimeter. Locations were selected to provide a representative sample of the deck and not cause damage which would result in deck failure. (^) Core sample holes were filled with vermiculite before the fire endurance test was conducted. Three core samples were taken on June 15, 1994 and were dried to constant weight in a 100 ‘C (212 ‘F) furnace. Deck sample moisture content was calculated based on the manufacturer’s original moisture content for the concrete mix. The three sample values were 70.0, 48.2 and 49.6 % with an average of 55.9 %. Two additional samples were taken on June 27, 1994. These smples had values of 54.0 and 58.4 70 with an average of 56.2 9Z0. This average value, 56.2 $Zo~was taken as content at the time of test.
7.1.2 hading Of ~he ~unctiona~ ~~oor and ~a]k-0~ kk
the concrete slab’s moisture
The functional floor’s load requirement was 45.4 kg/m2 (100 lb/ft2). This was accomplished by locating 75, 0.208 m3 (55 gal) steel drums on the 28.8 mz (320 ft2) area of functional floor above the interstitial space, as shown in figure 2. (^) A total of 14,515 kg (32,000 lb) of water was distributed among the drums to provide the required structural load. The walk-on deck purlins were loaded with a weight of 11.3 kg/m2 (25 lb/ft2), as required. This was done in the same manner as was used with the Veteran’s Administration tests, in 1983 [1]. Plywood boxes were constructed in a way to fit on top of the purlin’s surface. They were evenly positioned along the
purlin’s length and filled to the weight required with dry building sand. The load bearing sand boxes are shown in figure 13. The bottom of each box was insulated with calcium silicate board to prevent it from igniting during the test.
7.2 Test Observations
The following observations were made during the fire endurance test:
Elapsed Time, h:min:s
Test begins at 11:50 a.m., June 28, 1994
Ignition Looking into the fire chamber: Small chips of spray-on fire-proofing are dropping off the bottom of metal deck near the purlins. The metal deck joints are opening on the long span between the purlins. The openings are about 50 mm (2 in). Short span metal deck joints show no openings. Metal decking joints on the long span are continuing to open. The center section of the visible spans are now open about 75 mm (3 in). Test fbrnace is operating nominally on the standard time-temperature curve, Viewing interstitial space through window: Everything looks normal in the interstitial space except for a little water vapor (steam) and possibly some smoke. It appears that the ducts have expanded and moved somewhat. A small amount of light is noted around the outside wall seal for the short, return duct. A bump sound is heard coming from the deck assembly. Duct penetrations through the walk-on deck look normal. Looking into the fire chamber: Small flakes of fire-proofing are continuing to fall from around the purlins. The long span metal deck joints have opened to at least a 100 mm (4 in) separation at the joint. The short metal deck spans show no openings at the joints. Viewing interstitial space through window: Duct penetrations continue to appear to be tight. No noticeable smoke or hot gases appear around the duct penetrations. Light water vapor and smoke in the interstitial space. One can still see completely across the compartment. Looking into the fire chamber: Fire-proofing is dropping away from the furnace steel work in the front left corner above the stack vent opening.
9
.,
02:08:05 Fire-proofing continues to drop off of each purlin. Metal decking is still showing a 100 mm (4 in) opening between the joints. Short span metal deck sections show no joint openings. 02:10:00 West purlin shows approximately 3 m (9.9 ft) of exposed metal. 02:22:01 (^) Fire-proofing is still dropping off of the west purlin. The east purlin appears to have lost all of its fire-proofing. 02:25:00 West purlin is continuing to lose fire-proofing and some of the wire mesh is hanging from the purlin. 02:30:00 Burner is shut down. End of Test.
8.0 TEST RESULTS
8.1 (^) Post Tkst Observations
The following observations were made on June 30, 1994, two days after the fire test. Tfvo days were allowed for the test structure to cool so it could be safely entered.
Bottom of Walk-On Deck Exposed to Fire:
e (^) All of the 2.946 m (9 ft 8 in) steel metal decking had separated along the lapped joints. l (^) After cooling, the metal deck lap joints had generally returned to a position which showed openings of about a 25 mm (1 in). Figure 14. l (^) All 965 mm (3 ft 2 in) metal deck spans appeared to show little damage with no noted joint openings. l (^) All fire-proofing had dropped away from both purlins. Bare metal was exposed along the full length of each purlin. l (^) The duct work which extended into the fire chamber showed significant damage. Large blisters were seen on all surfaces not covered with firesafing. Figure 15. (^9) All firesafing around the ducts and in
Interstitial Space Observations:
l (^) No large cracks were apparent in the
the penetrations appeared to be in place.
walk-on deck inside the interstitial space. Small cracks were seen across the 2.946 m (9 ft 8 in) width of the concrete span. (^8) Firesafing and smoke barrier around the duct penetrations appeared to be in place. l (^) The purlins may have moved some, but appear to be straight. e (^) The walk-on deck slab appeared to have pulled away form its normal position toward the center. The deck appeared to be sagging in the center, and there was increased space around the edges of about 50 mm (2 in). l (^) The thermal insulation wrapped around the supply AC duct was discolored “brown” near the floor penetration. l (^) The 102 x 102 x 6.4 mm (4x4xl/4 in) steel hanger tubes and the W18X35 steel beams appear to be unaffected by the fire test.
e (^) Paper on the east gypsum board wall enclosing the interstitial space was burned away over about a 1.2 m (4 ft2) area near the walk-on deck supply duct. e (^) No fire exposure damage was noticeable at any of the five concrete core drill locations on the walk-on deck.
Functional
l (^) No
Floor Observations:
changes were noted in the functional floor relative to its pretest condition.
8.2 (^) Tat Data and Dhcussion of Resulk
This section contains information concerning operations and addresses the acceptance criteria Additional test results are presented in Appendix B of this report for instrumentation not directly related to the acceptance criteria.
requirements for successful NFPA 251 test for the interstitial space construction assembly.
8.2.1 Test Furnace
In accordance with section 2-2.3 of NFPA 251, the test assembly was exposed to an acceptable fire test environment required for a two hour rating. Figyme 16 shows the standard time- temperature curve along with the actual temperature curve as measured during the fire test. The total furnace exposure was for 2 hours and 30 minutes. The area under the curve for the test was 104,360 ‘C-rein as compared to the standard NFPA 251 area of 105,430 OC-min which was a difference of 1.01 percent. The main reason for the area differences resulted from two electrical failures during the test which caused the burner to shut down. These drops can be seen in figure
8.2.2 Functiona# Floor Resulti
Temperature measurements for the functional floor’s surface are shown in figure 17. These plots show that maximum temperature rise for the two hour test period was no greater than 33 “C (91 “F). No changes in floor temperature were noted until about 60 minutes into the test. At that point, temperatures generally began to rise across the deck. (^) The center position thermocouple temperature becomes less than the others at about 75 minutes into the test. This is attributed to heat losses to a structural steel member located near the thermocouple. The maximum temperature rise above ambient for the functional floor’s surface was 22 “C (72 “1?) at the end of 2 hours and 30 minutes. The fictional floor used in this test was the same one
steel members approached a failure condition. Fire-proofing with a two hour rating is required for protecting the W6X9 steel purlins. Performance^ of^ this^ construction^ system^ may^ be significantly different if the purlin fire-proofing does not maintain its integrity. The firesafing methods used to protect duct penetrations met the requirements for a two hour system. This ales@ prevented the passage of hot gases into the interstitial space. The air conditioning ducts maintained their integrity throughout the complete test period. As with the Veteran’s “ Administration tests in 1983, the ducts were sealed on the unexposed end which did not allow hot gases to flow through. The steel decking used to support the lightweight concrete walk-on deck showed significant degradation early in the test. Decking joints opened across the long span = between the W6X9 purlins.
ACmOWLEDGEMENT
Appreciation is extended to the following people that provided assistance with this study: Mr. Paul W. Hanreeder and Mr. Philip I-loge of the U.S. Army Corps of Engineers; Capt. Kevin S. Purvis, Headquarters USAF/CEC; Mr. Donald C. Moeller, P.E., Rolf Jensen & Associates, Inc.; Mr. Donald M. Drakulich and Mr. Vernon Rosamond, AIA, Anderson DeBartolo Pan; Mr. Rob Mapp, Genstar Technical Center; Mr. Frank Davis and Mr. John Gross, NR3T, Building and Fire Research Laboratory. Golden Eagle Construction Company, Inc. assisted with construction of the interstitial space system.
Lawson, J. Randall, Fire Performance of Interstitial Space Construction Systems, National Bureau of Standards (U.S.), NBSIR 85-3158, 1985.
Jeanes, D.C., Predicting Fire Endurance of Steel Structures, paper presented to American Society of Civil Engineers, April 1982.
Standard Methods of Fire Tests of Building Construction and Materials, NFPA 251, National Fire Protection Association, Quincy, MA, 1990.
Standard Test Method for Slump of Hydraulic Cement Concrete, ASTM C143-90a, American Society of Testing and Materials, Philadelphia, PA, 1990.
Standard Test Methods of Making and Curing Concrete Test Specimens in the Field, ASTM C31-91, American Society of Testing and Materials, Philadelphia, PA, 1991.
Standard Test Method for Compressive Strength of Cylindrical Concrete Specimens, ASTM C39-86el, American Society of Testing and Materials, Philadelphia, PA, 1990.
13abrauskas, V., Fire Endurance in Buildin~, PhD thesis, University of California, Berkeley, 1976.
L
;.096m [20’-0”)
12.192m (40’-0”)
J L
WI 4x Column
L
I r
-1 L
J L
Bottom FunctionalFloorArea Test Bay 1
1 r
A
Figure 1. Ground level plan of test structure