

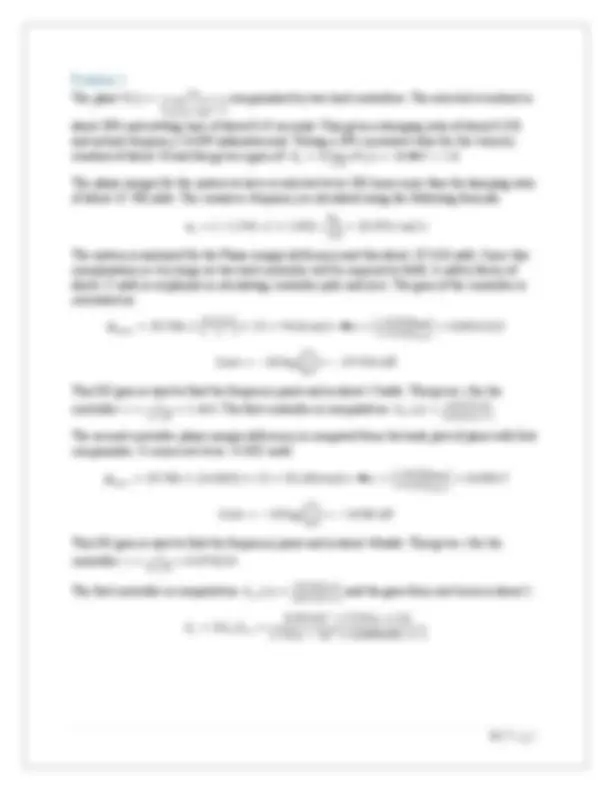
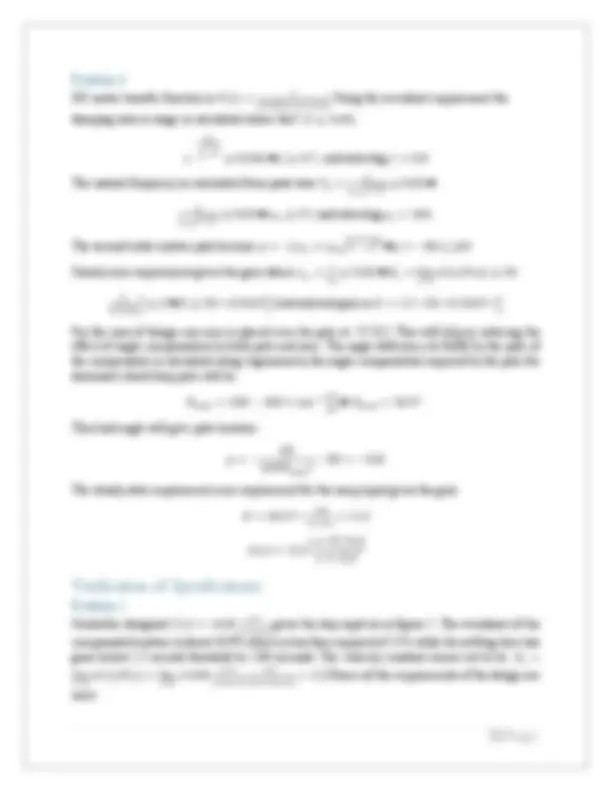
Study with the several resources on Docsity
Earn points by helping other students or get them with a premium plan
Prepare for your exams
Study with the several resources on Docsity
Earn points to download
Earn points by helping other students or get them with a premium plan
Community
Ask the community for help and clear up your study doubts
Discover the best universities in your country according to Docsity users
Free resources
Download our free guides on studying techniques, anxiety management strategies, and thesis advice from Docsity tutors
A final project on compensator design for achieving desired specifications from a known plant of a system. The project employs techniques such as root locus, pole placement, step response and others to design lead and lag compensators. The compensators are designed to fulfill requirements such as overshoot, settling time, steady state errors fulfillment and others. three problems with their respective plants and required specifications, and the design of compensators to meet those specifications.
Typology: Papers
1 / 7
This page cannot be seen from the preview
Don't miss anything!
The controller or compensator design is used to achieve desired specifications from a known plant
of a system. The compensator designed used techniques such as root locus, pole placement, step
response and other.
There are primarily two types of compensators designed in this project the lead compensator and
the lag compensator. The lead compensator has a pole further from the zero and thus adding phase
to the system. This makes the systemโs root locus mover more towards the left half plane and gives
more stability.
The lag compensator is designed for fulfilling the margins in frequency domains such as phase
margin and gain margin. The zero is placed further in the system than the pole of the compensator
and tends to mover system more to the right.
The design of each of the compensator are carried out to fulfill requirements such as overshoot,
settling time, steady state errors fulfillment and others.
The standard design scheme of the negative feedback system incorporated with the compensator
is shown in figure 1. For each of the three systems in this project this particular scheme will be
employed to fulfill the requirements.
Figure 1 - Closed loop control system with compensator.
The Plant for this problem is ๐
!.#
$($&#)($&()
and is a stable plant with all the poles ๐ =
0 , โ 1 , โ 4 in the left half plane. This is a type 1 system with an integrator so the steady state error
for the step input for open loop response will be zero. The uncompensated closed loop system has
percentage overshoot of 27.7% while the settling time is about 11 seconds. The steady state error
when in a closed loop is about 27%. The uncompensated system velocity constant is about 1. The
required specifications are about ๐. ๐ โค 11% and๐ $
โค 2. 5 ๐ ๐๐๐๐๐๐ . So to make the system follow
such specifications a lead compensator will be employed to reduce the overshoot and the settling
time. The gain of the controller will computed to fulfill the velocity constant requirement of๐พ )
the left half plane.
The Plant for the second problem is ๐(๐ ) =
#!
$*
!
"
#".%&'
&
!
().*
&#+
and is a stable plant with all the poles
๐ = 0 , โ 0. 1016 ยฑ 3. 1536 ๐ the left half plane. This is a type 1 system with an integrator so the
steady state error for the step input for open loop response will be zero. The uncompensated closed
loop system has a very high percentage overshoot of 357240% while the system never properly
settles within a 1000 seconds frame. The steady state error when in a closed loop is 0. The
uncompensated system velocity constant is about 1. The required specifications are about ๐. ๐ โค
35% and๐ $
โค 0. 75 ๐ ๐๐๐๐๐๐ . So to make the system follow such specifications a lead compensator
will be employed to reduce the overshoot and the settling time. The gain of the controller will
computed to fulfill the velocity constant requirement of๐พ )
โฅ 15. The frequency domain technique
will be used to design two lead controller in series thus overall a second order compensator.
DC motor system control is the third problem to compensate. The input is in terms of voltage and
output in terms of position in radians. The estimated transfer function of the motor is
)($)
,($)
$(!.!!-.$&!./.0-)
. The analysis of the transfer function reveals a stable system with two poles
and no zero. The pole locations are๐ = 0 , โ 57. 7312. The step response of the closed loop of the
DC motor gives a peak time of 3.8 seconds. This time shows that the DC motor is not fast enough
The plant ๐(๐ ) =
#!
$*
!
"
#".%&'
&
!
().*
&#+
compensated by two lead controllers. The selected overshoot is
about 30% and settling time of about 0.45 seconds. This gives a damping ratio of about 0.
and natural frequency 24.839 radians/second. Taking a 20% increased value for the velocity
constant of about 18 and this gives a gain of: ๐พ 8
= ๐พ lim
$โ!
๐ ๐(๐ ) = 18 รจ๐พ = 1. 8
The phase margin for the system to have is selected to be 100 times more than the damping ratio
of about 35.786 rad/s. The crossover frequency is calculated using the following formula:
C
6
The system is analyzed for the Phase margin deficiency and this about - 87.626 rad/s. Since this
compensation is very large so two lead controller will be required to fulfil. A safety factor of
about 15 rad/s is employed in calculating controller pole and zero. The gain of the controller is
calculated as:
D<E
F>. 070
7
P + 15 = 94. 6 ๐๐๐/๐ รจ๐ผ =
425
)
#&$G6=(H
425
)
๐บ๐๐๐ = โ 10 log [
This DC gain is used to find the frequency point and is about 17rad/s. This gives ๐ for the
controller: ๐ =
#>โ โ
K
= 1. 465. The first controller is computed as: ๐บ
C#
7 .0.>$&#.F
!.!!7.07$&#
The second controller phase margin deficiency is computed from the bode plot of plant with first
compensator. It comes out to be - 4.4205 rad/s
D<E
= 35. 786 + ( 4. 4205 ) + 15 = 55. 206 ๐๐๐/๐ รจ๐ผ =
425
)
#&$G6=(H
425
)
๐บ๐๐๐ = โ 10 log [
This DC gain is used to find the frequency point and is about 43rad/s. This gives ๐ for the
controller: ๐ =
(.โโK
The first controller is computed as: ๐บ
C#
!.!>(77$&#
!.!!>7F>$&#
and the gain from root locus is about 2.
C
C#
C 7
7
7
DC motor transfer function is ๐(๐ ) =
$(!.!!-.$&!./.0-)
Using the overshoot requirement the
damping ratio is range is calculated where the๐. ๐ โค 4 .6%.
3
+,
"
โค 0. 046 รจ๐ โฅ 0. 7 , and selecting ๐ = 0. 8
The natural frequency is calculated from peak time:๐ 1
L
5
/
M# 34
"
โค 0. 05 รจ
L
5
/
M# 34
"
โค 0. 05 รจ๐
6
โฅ 97 , and selecting๐
6
The second order system pole become ๐ = โ๐๐ 6
6
7
รจ๐ = โ 80 ยฑ ๐ 60
Steady error requirement gives the gain where ๐
$$
N
6
โค 0. 02 รจ๐พ
8
= lim
$โ!
N
!./.0-
2
1
โฅ 2 รจ๐พ โฅ 50 โ 0. 5369
1
2
And selected gain is ๐พ = 1. 5 โ 50 โ 0. 5369 โ
1
2
For the ease of design one zero is placed over the pole at - 57.312. This will help in reducing the
effect of angle compensation by both pole and zero. The angle deficiency to fulfill by the pole of
the compensator is calculated using trigonometry the angle compensation required by the pole for
dominant closed loop pole will be:
:;<=
= 180 โ 180 + tan
3 #
0!
F!
รจ ๐
:;<=
?
This lead angle will give pole location:
tan
:;<=
The steady state requirement error requirement for the ramp input gives the gain:
#0!
/>..#
Controller designed ๐ถ
$&#
$�.#(
gives the step input as in figure 5. The overshoot of the
compensated system is about 10.9% which is less than required of 11% while the settling time has
gone below 2.5 second threshold to 2.09 seconds. The velocity constant comes out to be: ๐พ
8
lim
$โ!
๐ ๐ถ(๐ )๐(๐ ) = lim
$โ!
$&#
$�.#(
!.#
$($&#)($&()
= 2. 2 .Hence all the requirements of the design are
meet.
time is also reduced to 0.15 seconds. Whereas the required range was to be below 0.75 seconds.
The value of velocity constant comes out to be:
8
= ๐พ lim
$โ!
7
7
7
This is greater than the required value of 15. Thus all the requirements are fulfilled.
The compensator designed for the DC motor is: ๐ถ
$&/>..#
$&##
and the resulting response
for the compensated closed loop system is shown in figure below.
Figure 4 - DC Motor Response to Train of Steps
As seen the DC motor follows the train of steps successfully and with almost no delay. The step
response information for the compensated response is shown in the figure below.
Figure 5 - DC motor Compensated Step Response information
The peak time has gone below the threshold of 0.05 seconds to 0.042 seconds while the overshoot
is also below the threshold of 4.6% to about 3.48 %. This validates the designed controller to fulfil
the requirements.