
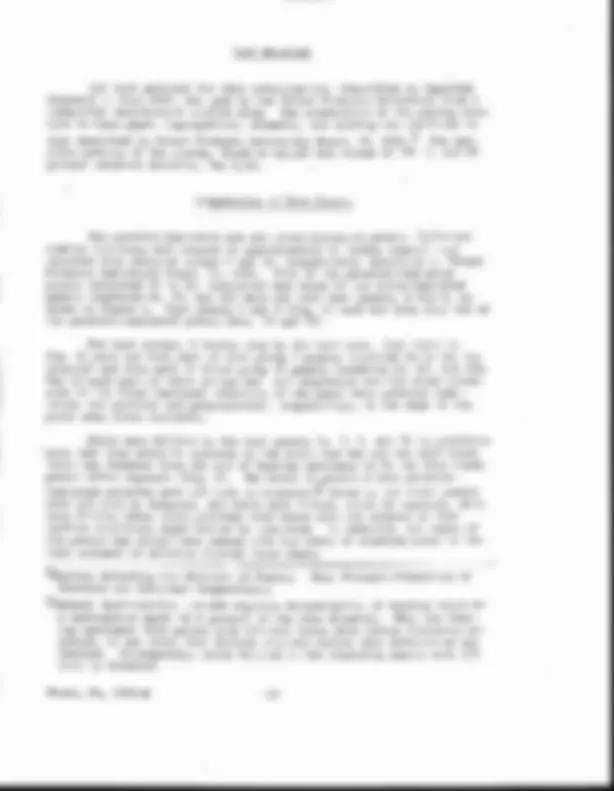
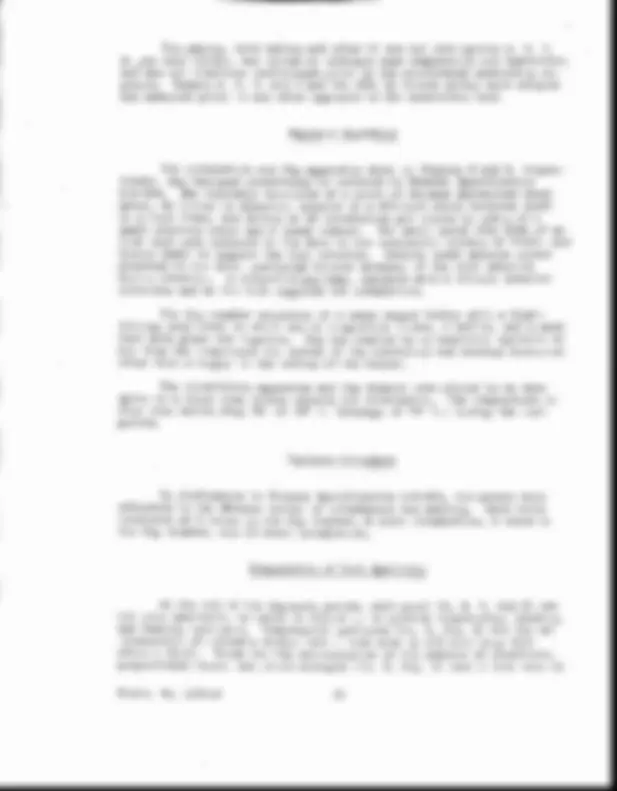
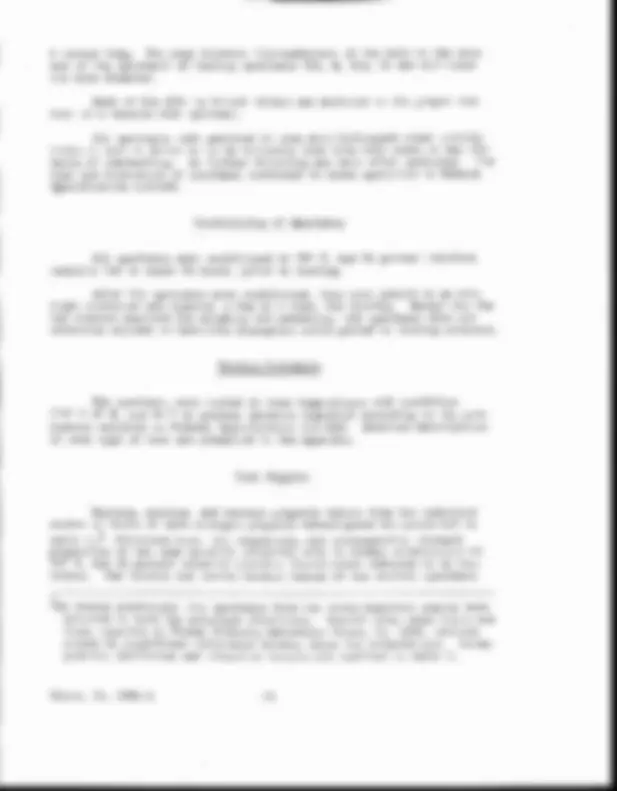
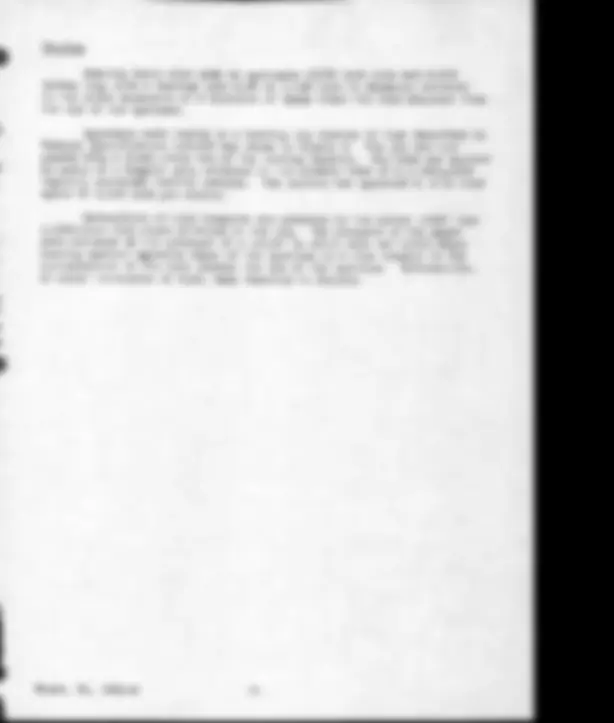
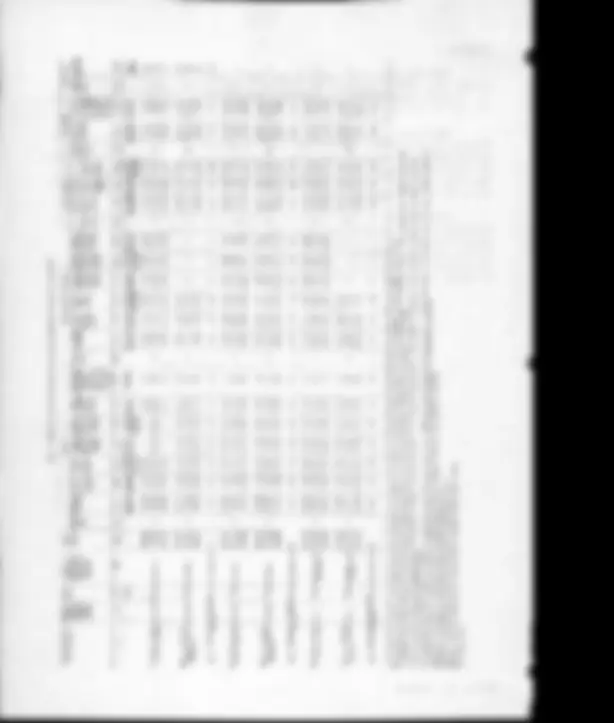
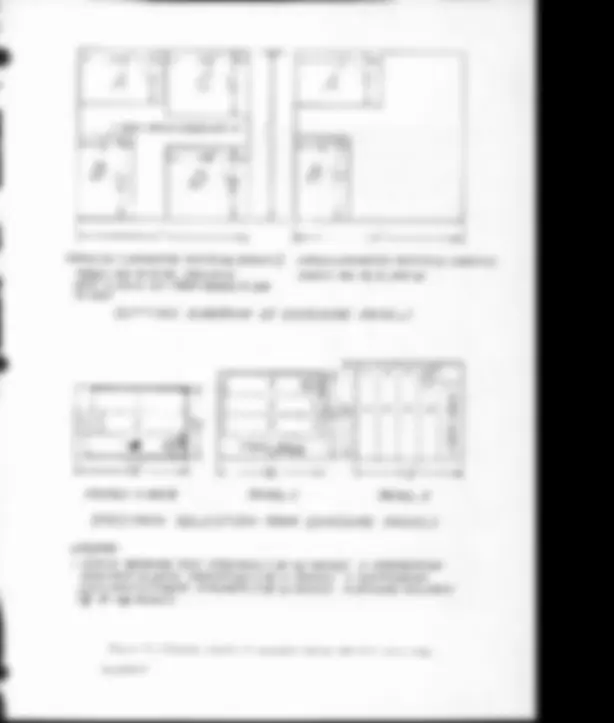
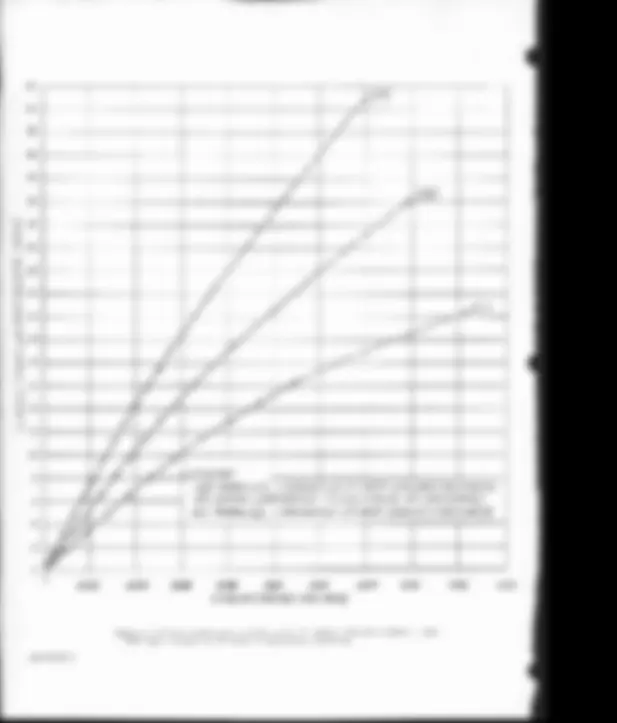
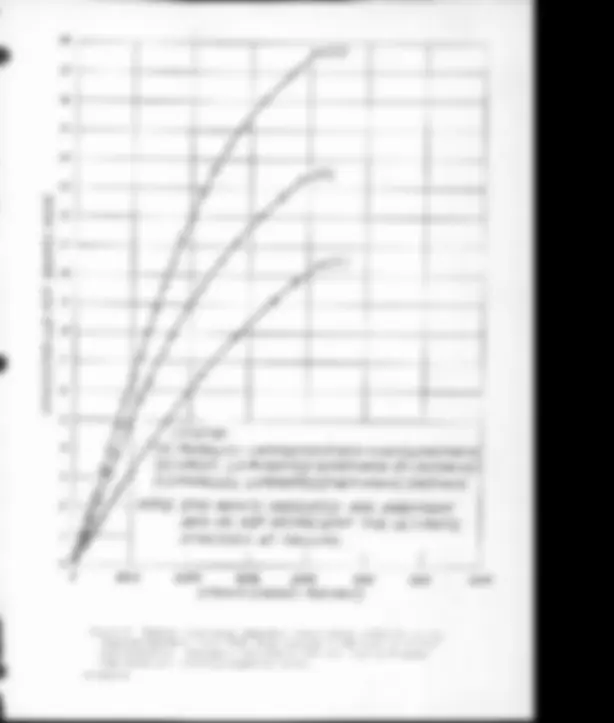
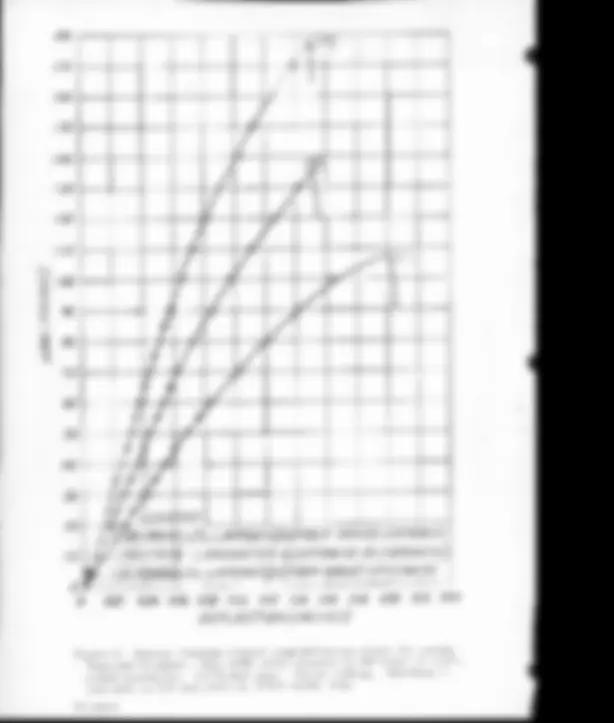
Study with the several resources on Docsity
Earn points by helping other students or get them with a premium plan
Prepare for your exams
Study with the several resources on Docsity
Earn points to download
Earn points by helping other students or get them with a premium plan
Community
Ask the community for help and clear up your study doubts
Discover the best universities in your country according to Docsity users
Free resources
Download our free guides on studying techniques, anxiety management strategies, and thesis advice from Docsity tutors
This report explores the effect of accelerated weathering on the tensile, compressive, flexure, bearing, and hardness properties of papreg. The study is part of a series of investigations to determine how aircraft service conditions influence papreg's strength. The research employed an accelerated weathering test to simulate the effects of sun and moisture in a short period.
Typology: Papers
1 / 17
This page cannot be seen from the preview
Don't miss anything!
Madison, Wisconsin In Cooperation with the University of Wisconsin
FACTORS AFFECTING THE STRENGTH OF PAPREG1 ' 3
bearing, and hardness properties of papreg. It covers one of a (^) series of
The papreg, both before and after it. was cut into panels A, B, C, D, and test strips, was stored at ordinary room temperature and humidities, and was not otherwise conditioned prior to the accelerated weathering ex- posure. Panels A, B, C, and D and the 3/4- by 9-inch strips were weighed and measured prior to and after exposure to the weathering test.
Exposure Apparatus
The irradiation and fog apparatus shown in figures 2 and 3, respec- tively, was designed essentially as outlined in Federal Specification L-P-406. The turntable consisted of a piece of 16-gage galvanized sheet
in a wood frame, and driven at 35 revolutions per minute by means of a small electric motor and a speed reducer. Two sheet metal ribs 3/16 of an inch high were soldered to the disc in two concentric circles of 3-3/4- and 6-inch radii to support the test material. Several small machine screws attached to the disc, prevented lateral movement of the test material during rotation. A commercial sun lamp, equipped with a 15-inch diameter reflector and an S-1 bulb supplied the irradiation.
The fog chamber consisted of a large topper boiler with a tight- fitting wood cover in which was an inspection window, a baffle, and a wood rack with glass rod supports. Fog was created by an aspirator operated by air from the compressed air system of the Laboratory and drawing distilled water from a supply in the bottom of the boiler.
The irradiation apparatus and fog chamber were placed in an open space in a large room having natural air circulation. The temperature in
period.
Exposure Procedure
In conformance to Federal Specification L-.P-406, the panels were subjected to ten 24-hour cycles of irradiation and wetting. Each cycle consisted of 2 hours in the fog chamber, 2 hours irradiation, 2 hours in the fog chamber, and 18 hours irradiation.
Preparation of Test Specimens
At the end of the exposure period, each panel (A, B, 0, and D) was cut into specimens, as shown in figure 1, to provide compression, bending, and bearing specimens. Compression specimens (No. 3, fig. 1) for the de- termination of ultimate stress were 1 inch wide by 1/2 inch long (1/r ratio = 13.9). Those for the determination of the modulus of elasticity, proportional limit, and yield strength (No. 2, fig. 1) were 1 inch wide by
Mimeo. No. 1521-A 3
4 inches long. The edge distance (circumference of the hole to the near end of the specimen) of bearing specimens (No. 4, fig. 1) was 2.5 times the hole diameter.
Each of the 3/4- by 9-inch strips was machined to the proper con- tour of a tension test specimen.
All specimens were machined to size with high-speed steel cutting tools in such a manner as to be virtually free from tool marks or any evi- dence of overheating. No further finishing was done after machining. The type and dimensions of specimens conformed to those specified in Federal Specification L-P-406.
Conditioning of Specimens
All specimens were conditioned at 75° F. and 50 percent relative humidity for at least 48 hours, prior to testing,
After the specimens were conditioned, they were placed in an air- tight container and removed, a few at a time, for testing. Except for t'he few minutes required for weighing and measuring, the specimens were not otherwise exposed to test-room atmosphere until placed in testing machines.
Testing Procedure
The specimens were tested at room temperatures and humidities (78° J.- 30 F. and 46 ± 10 percent relative humidity) according to the pro- cedures outlined in Federal Specification L-P-406. Detailed descriptions of each type of test are presented in the appendix.
Test Results
Maximum, minimum, and average property values from the indicated number of tests of each strength property investigated are presented in
table 1. 2 Presented also, for comparison, are corresponding strength
75° F. and 50 percent relative humidity (hereinafter referred to as con- trols). The tensile and static bending values of the control specimens
-As stated previously, the specimens from the cross-laminated papreg were oriented in both the principal directions. Results from these tests and those reported in Forest Products Laboratory Mimeo. No. 1319, revised, showed no significant difference between these two orientations. Conse- quently, lengthwise and crosswise results are combined in table 1.
Mimeo. No. 1521-A (^) -4-
Appendix
Tension, compression, bending, and bearing tests were conducted as hereafter described.
Tension
Tension specimens were tested in self-aligning Templin grips in a motor-driven, 10,000-pound capacity, universal testing machine. Theilaa-
mately 75 percent of ultimate load, during which time (^) load-elongation data were obtained, and then increased to 0.157 inch per minute and maintained at this rate until failure. A 2,-inch gage length separable nonaveraging type extensometer, equipped with a spiral staff type 0.0001-inch dial, was used to measure elongation.
Compression
Compression tests to determine ultimate stress were made on speci- mens 1 inch wide by 1/2 inch long. To overcome the difficulty in accu- rately placing a single specimen of such small dimensions in position to assure axial loading, two specimens placed 1 inch apart and parallel to
10,000-pound capacity universal testing machine. The machine was operated at a no load speed of 0.023 inch per minute.
Specimens 1 inch wide by 4 inches long were tested in compression as a laterally supported column by means of the pack apparatus shown in
table of a 10,000-pound capacity hydraulic testing machine. The machine speed was constant at 0,012 inch per minute. Deformations, to approxi- mately 0.02-inch strain, were measured at equal increments of load with a 2-inch gage length Martens mirrors compressometer attached to the ma- chined edges of the specimen.
Bending
Specimens 1 inch wide by 4-1/2 inches long were tested flatwise in a bending jig adjusted to a 2-1/2-inch span (span-specimen thickness ratio of 20:1). The load was applied at the center of the span by means of a loading block attached to the cross head of a 30,000-pound universal test-
machine was operated at a no load speed of 0.049 inch per minute until ap- proximately 50 percent of the maximum load was reached and then increased to 0.146 inch per minute, Deflections at the center of the span were measured with a 0.001-inch dial gage.
Mimeo. No. 1521-A (^) -6-
Bearing
Bearing tests were made on specimens 15/16 inch wide and 4-3/ inches long with a (^) bearing hole 0.25 or 0.125 inch in diameter centered in the width dimension at a (^) distance of three times the hole diameter from the end of the specimen.
Specimens were tested in a bearing jig similar to that described in Federal Specification L-P-406 and shown in figure 8. The jig was sus- pended from (^) a (^) fixed cross arm of the testing machine. The load was applied by means of a Templin grip attached to the movable head of a 1,000-pound capacity universal testing machine. The machine was operated at a no load speed of 0.016 inch per minute.
Deformation of hole diameter was measured by two spiral (^) staff type 0.0001-inch dial gages attached to the jig. The plungers of the gages were actuated by the movement of (^) a (^) collar in which were set knife edges bearing against opposite edges of the specimen in a line tangent to the circumference of the hole nearest the end of the specimen. Deformations, at equal increments of load, were observed to failure.
Mimeo. No. 1521-4 (^) -7-
ry C
FIBER GRAIN DIRECTION—w-
PARALLEL-LAMINATED MATER /AL (GROUP I) CROSS-LAMINATED MATERIAL (GROUP a)
PANELS N05.7670 82, INCLUSIVE (^) PANELS N05. 58,59, AND 60 NOTE: C AND D CUT FROM PANELS 78 AND 79 ONLY
CUTTING DIAGRAM Of EXPOSURE PANELS
SIN
I
4 ,46,
4. (^) 0 1 4 'gni,.
10 1 0 10 I
Id
I I 4 1
1
1^4 4.
I I (^) tI I 13 I I^ I^1 I -0-- 51-
PANELS A AND 8 (^) PANEL C (^) PANEL D
SPEC/MEN (^) SELECT/ON FROM EXPOSURE PANELS
I. STATIC BENDING TEST SPECIMEN ( (^) I BY 41. INCHES) Z. COMPRESSION SPEC/MEN-ELASTIC PROPERTIES (^) (/BY 4 INCHES) 3. COMPRESS/ON SPEC/MEN-I/LT/MATE STRENGTH (/ BY r INCHES) 4. (^) BEARING SPEC/MEN BY 4i- INCHES)
Figure 1.--Typical layout of exposure panels and test specimens.
Z M 57140 F
30
-
c • t 26
(r)^0^24
cZ=i • /
/ tr) / F- /
/
6
42
40
Figure 4.--Typical tensile stress-strain curves for papreg (Improved Standard - June
/
/
- /
/
(^1615) LEGEND: i
(B) CR055 (^) LAM/NATED-(LENGTHWISE OR CROSSWISE)
GRAIN) CROSSWISE
(^0002) 0.004 (^0006 0008) 00/0 00/2 00/ STRAIN (INCHES PER INCH)
Figure 5.--Typical compression (edgewise) stress-strain curves for papreg (Improved Standard - June 1943) after exposure to 240 hours of acceler- ated weathering. S pecimen 1 inch wide by 1/8 inch thick by 4 inches long tested as a laterally supported column. Z M 57142 F
Figure 7.--Specimen ready for test in the apparatus used for the laterally supported column compression test: C, clips to hold the lower gage points of the gage; F, spring-steel fingers to provide lateral restraint to specimen; M, Marten's mirror gages; S, specimen; Y, yokes.
Z 477.75 I?'
Figure 8.-j9lPparatus assembly for bearing test of papreg (tensile loading): A, Templin grip; B, dial gage; C, collar; D, knife edge; E, specimen; F, 1/8 inch diameter steel pin.
Z M 58910 r