
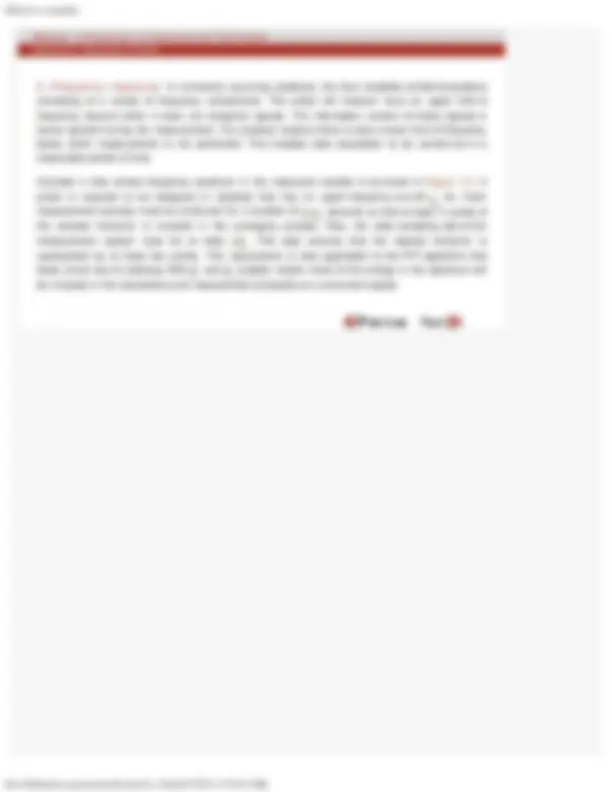
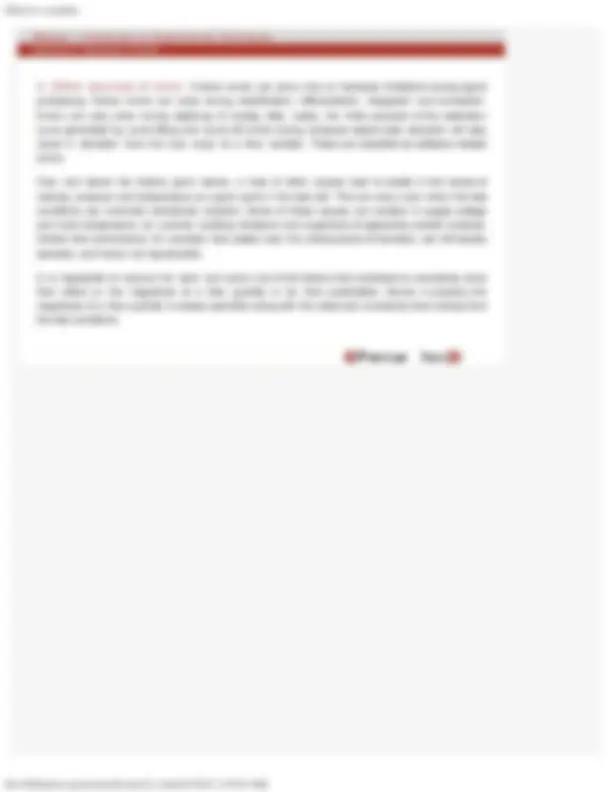
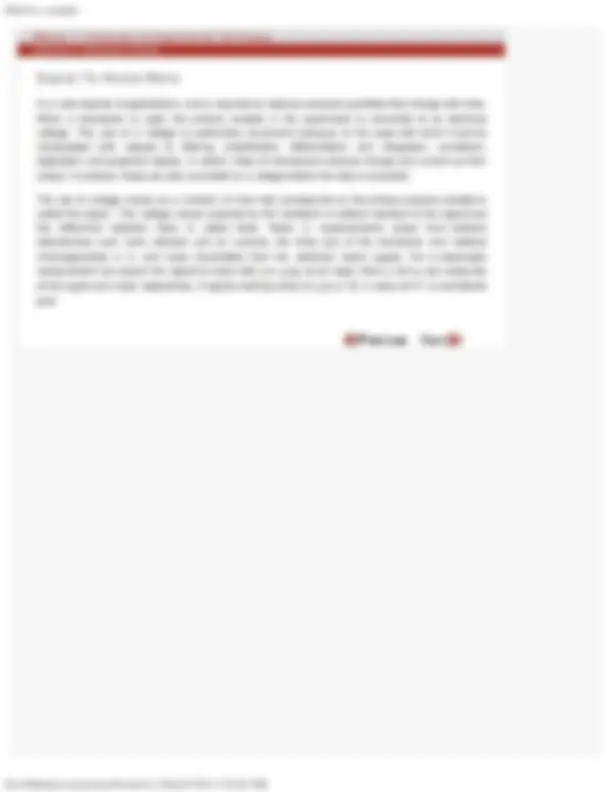
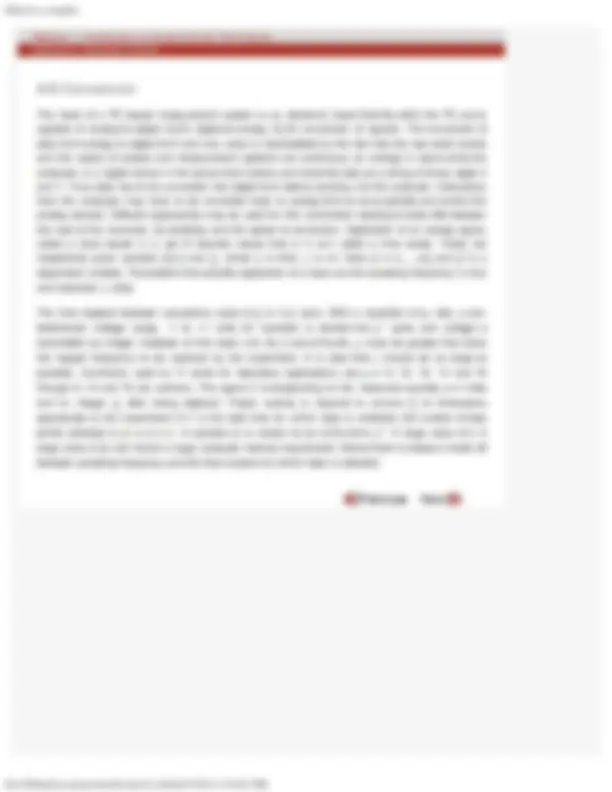
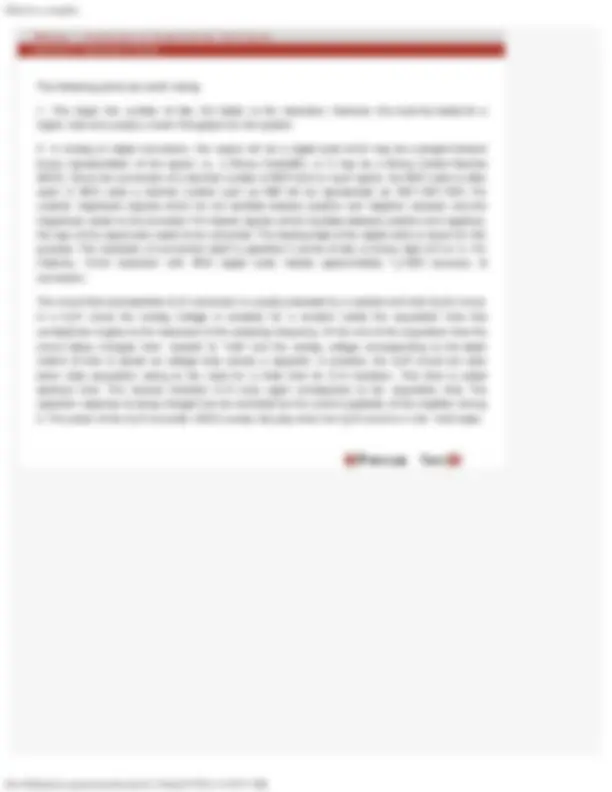
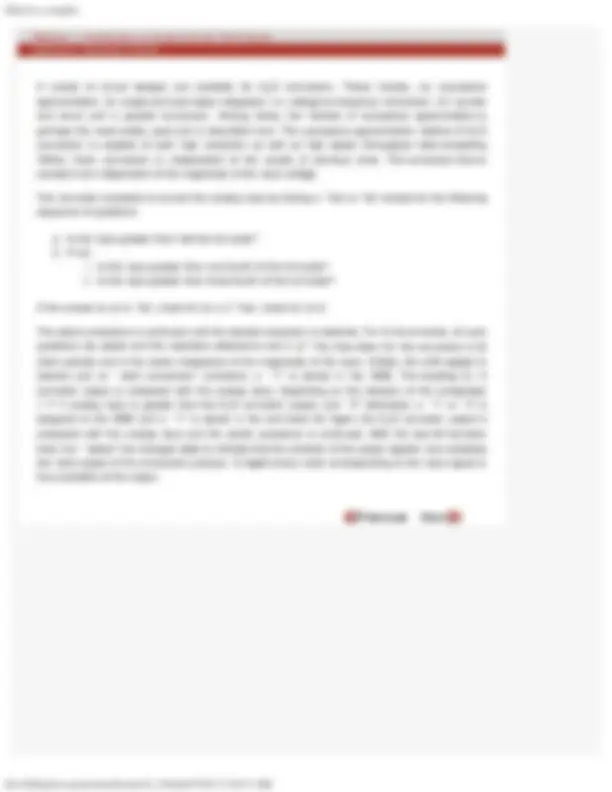
Study with the several resources on Docsity
Earn points by helping other students or get them with a premium plan
Prepare for your exams
Study with the several resources on Docsity
Earn points to download
Earn points by helping other students or get them with a premium plan
Community
Ask the community for help and clear up your study doubts
Discover the best universities in your country according to Docsity users
Free resources
Download our free guides on studying techniques, anxiety management strategies, and thesis advice from Docsity tutors
A part of an optical measurement lecture series, focusing on sources of error in measurement. It covers topics such as signal-to-noise ratio and analog-to-digital conversion, discussing their importance in measurement systems and the impact of errors in these processes. The document also provides information on various circuit designs for analog-to-digital conversion and their resolutions.
Typology: Slides
1 / 12
This page cannot be seen from the preview
Don't miss anything!
A/D Conversion Digitalization Errors due to A/D Conversion
The process of measurement involves locating the probe in the flow field, an act that invariably changes the flow itself. Hence the measured quantity is only an approximation of the local value of interest. Besides this, other sources of error are:
over a finite volume. The issue of probe size becomes crucial in micro-environments; examples are flows set up in electronic circuit boards for the purpose of cooling, and micro-electro-mechanical systems.
time for the probe to fully sense the new state. Hence any reading taken in finite time is really a cut- off value. The transients depend on the inertia and damping present in the probe and the measurement system. They could be monotonic or oscillatory. Typical probe responses are shown in Figure 1.4.
processing. Hence errors can arise during amplification, differentiation, integration and correlation. Errors can also arise during digitizing of analog data. Lastly, the finite precision of the calibration curve generated by curve-fitting and round-off errors during computer-based data reduction will also result in deviation from the true value of a flow variable. These are classified as software-related errors.
Over and above the factors given above, a host of other causes lead to scatter in the values of velocity, pressure and temperature at a given point in the test cell. This can occur even when the test conditions are nominally maintained constant. Some of these causes are variation in supply voltage and room temperature, air currents, building vibrations and roughness of apparently smooth surfaces. Certain flow phenomena, for example, flow states near the critical points of transition, are intrinsically sporadic, and hence not reproducible.
It is impossible to account for each and every one of the factors that contribute to uncertainty since their effect on the magnitude of a flow quantity is far from predictable. Hence, in practice, the magnitude of a flow quantity is always specified along with the observed uncertainty level arising from the test conditions.
In a vast majority of applications, one is required to measure physical quantities that change with time. When a transducer is used, the primary variable in the experiment is converted to an electrical voltage. The use of a voltage is particularly convenient because of the ease with which it can be manipulated with respect to filtering, amplification, differentiation and integration, correlation, digitization and graphical display. A certain class of transducers produce charge and current as their output. In practice, these are also converted to a voltage before the data is recorded.
The set of voltage values as a function of time that corresponds to the primary process variable is called the signal. The voltage values acquired by the hardware is seldom identical to the signal and the difference between them is called noise. Noise in measurements arises from ambient disturbances such room vibration and air currents, the finite size of the transducer and material inhomogeneities in it, and noise transmitted from the electrical mains supply. For a meaningful measurement we require the signal-to-noise ratio to be large. Here and are measures of the signal and noise respectively. A typical working value of is 10; a value of 0.1 is considered poor.
Physical processes are continuous functions of time and space and manual approaches to measurements of these parameters are cumbersome. In applications such as atmospheric flow patterns, turbulence and combustion, a large volume of data has to be collected in a short span of time. In yet another class of problems, nuclear power plants, process industries and material processing and metal forming operations, for example, process variables must be continuously monitored with the help of a centralized control room to ensure product quality, high efficiency and to prevent accidents. These requirements have necessitated the development of Data Acquisition Systems (DAS).
A variety of general-purpose as well as special-purpose, stand-alone DAS units are commercially available. However, such units are costly and may not be flexible in their configuration. Their primary use pertains to situations wherein a large number of sensors and hence process variables are employed. For typical laboratory-scale applications, the number of sensors is limited (to say 8 or 16) and low cost DAS can be configured. With rapid advances in the technology of microprocessors, desk-top (personal) computers (PC) and associated peripherals and interfaces, such units have become attractive alternatives to a stand-alone system. The flexibility in configuration is very high for these PC-based DAS and hence a host of options and expansion possibilities are available.
With a properly configured DAS, a variety of tasks can be accomplished through software alone. These include, a collection of probe data as a function time, (b) collection of data simultaneously from a set of probes, (c) post processing of sensor data to extract meaningful information, and (d) generation of control action that would alter the state of the process itself. Step (c) requires that the DAS additionally posses adequate computing power and memory.
The heart of a PC-based measurement system is an electronic board that fits within the PC and is capable of analog-to-digital (A D) digital-to-analog (D A) conversion of signals. The conversion of data from analog to digital form and vice versa is necessitated by the fact that the real-world events and the output of probes and measurement systems are continuous (or analog) in nature while the computer is a digital device in the sense that it stores and transmits data as a string of binary digits 0 and 1. Thus data has to be converted into digital form before sending it to the computer. Instructions from the computer may have to be converted back to analog form so as to operate and control the analog devices. Different approaches may be used for this converstion leading to trade-offs between the cost of the converter, its simplicity and the speed of conversion. Digitization of an analog signal, called a trace results in a set of discrete values that is in turn called a time series. These are respectively given symbols and , where is time, is an index and is a dependent variable. Parameters that quantify digitization of a trace are the sampling frequency (Hz) and resolution (bits)
The time elapsed between successive value of is 1 (sec). With a resolution of -bits, a pre- determined voltage range, -1 to +1 volts for example is divided into parts and voltage is transmitted as integer multiples of this basic unit. As a rule-of-thumb, must be greater than twice the largest frequency to be resolved by the experiment. It is clear that should be as large as possible. Commonly used A D cards for laboratory applications use 8, 10, 12, 14 and 16 through 8, 12 and 16 are common. The signal corresponding to the measured quantity is in Volts and an integer after being digitized. Proper scaling is required to convert to dimensions appropriate to the experiment. If is the total time for which data is collected, the number of data points collected is. In practice is chosen to be of the form. A large value of A large value of and hence a large computer memory requirement. Hence there is always a trade-off between sampling frequency and the time duration for which data is collected.
A variety of circuit designs are available for A D conversion. These include, (a) successive approximation, (b) single-and dual-slope integration, (c) voltage-to-frequency conversion, (d) counter and servo and e parallel conversion. Among these, the method of successive approximation is perhaps the most widely used and is described here. The successive approximation method of A D conversion is capable of both high resolution as well as high speed (throughput rates exceeding 1MHz). Each conversion is independent of the results of previous ones. The conversion time is constant and independent of the magnitude of the input voltage.
The converter proceeds to convert the analog input by finding a Yes' or
No' answer for the following sequence of questions:
a. Is the input greater than half the full scale? b. If not i. Is the input greater than one-fourth of the full scale? ii. Is the input greater than three-fourth of the full scale?
If the answer to (a) is No', check for (b-i); if
Yes', check for (b-ii)
The above procedure is continued until the desired resolution is obtained. For bit converter,^ such questions are asked and the resolution obtained is one in The time taken for the conversion is clock periods and is the same irrespective of the magnitude of the input. Initially, the shift register is cleared and on start conversion" command, a
1" is stored in the MSB. The resulting D A converter output is compared with the analog input. Depending on the decision of the comparator (1" if analog input is greater than the D A converter output, and
0" otherwise), a 1" or
0" is assigned to the MSB and a 1" is stored in the next lower bit. Again, the D A converter output is compared with the analog input and the earlier procedure is continued. After the last bit has been tried, the
status" line changes state to indicate that the contents of the output register now constitute the valid output of the conversion process. A digital binary code corresponding to the input signal is thus available at the output.
In most circumstances, the signal from the probe is analog and it is digitized either in a digital measuring instrument or with the help of an ADC DAC card, before being acquired by the PC through appropriate interfaces and software. One of the major source of errors during data acquisition is the A D conversion process itself. In this section, a quantitative estimate of the digitization error is provided. Analog to digital conversion proceeds at a finite rate and during this period of conversion changes that take place in the input voltage level are ignored in S H circuit. If is the number of points into which the voltage range is discretized by the A D converter, then the average discretization error in measuring a voltage in this range of. For a -bit converter. The discretization error spread over the period for which data is collected is equivalent to a noise signal. If the analog signal has a variance and the noise signal has a variance it is desirable that the signal-to-noise ratio be as large as possible. Let be the probability density function of the input signal. Let be the total number of points in the digitized signal. We may then estimate and as follows:
The function can be assumed to be a constant in the small integration interval. Hence,
Since can be assumed to be a constant , the value of is nearly.
The magnitude of however, will depend on the form of function. Table 1 summarizes the value of for a variety of input signals and bit converters.
Gaussian Sine wave White noise 4 16 9 18 14 8 24 147 311 24