
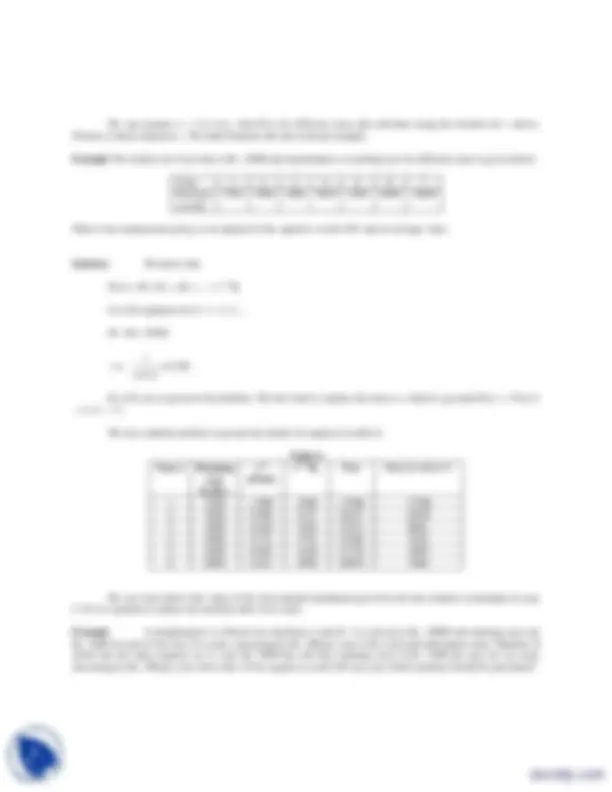
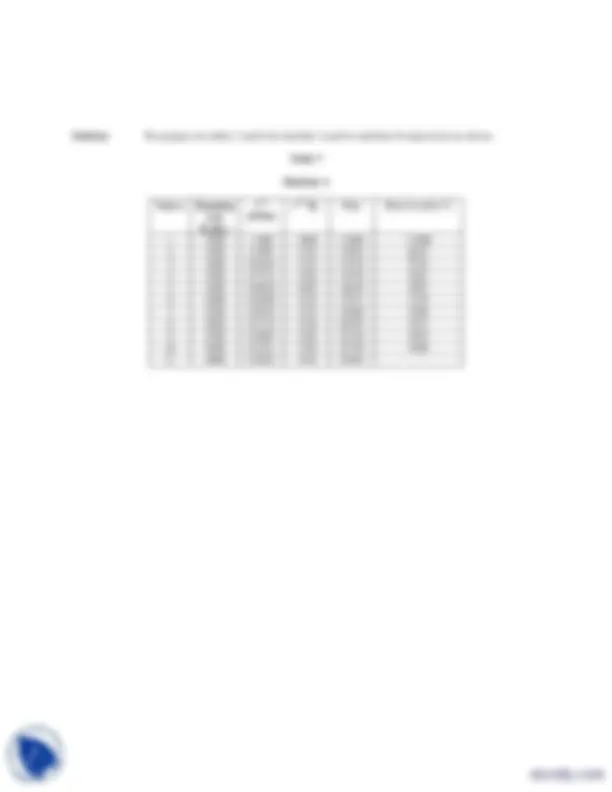
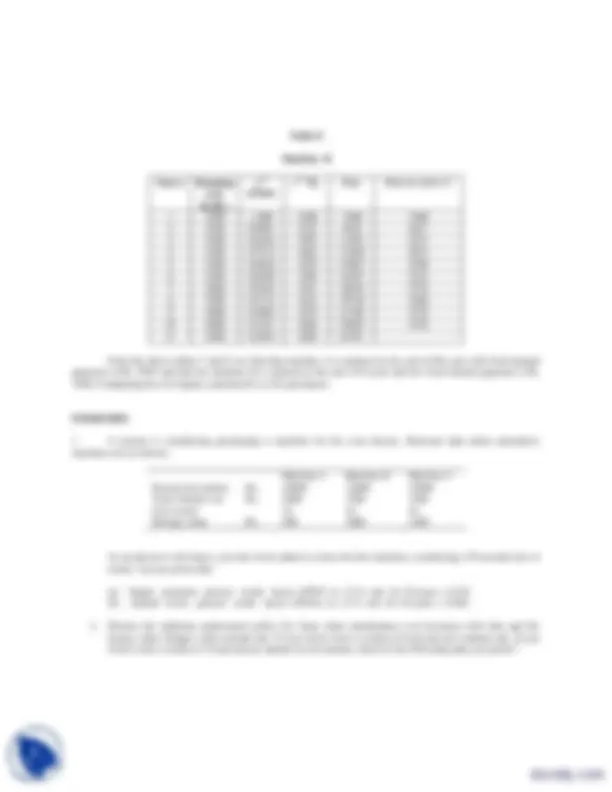
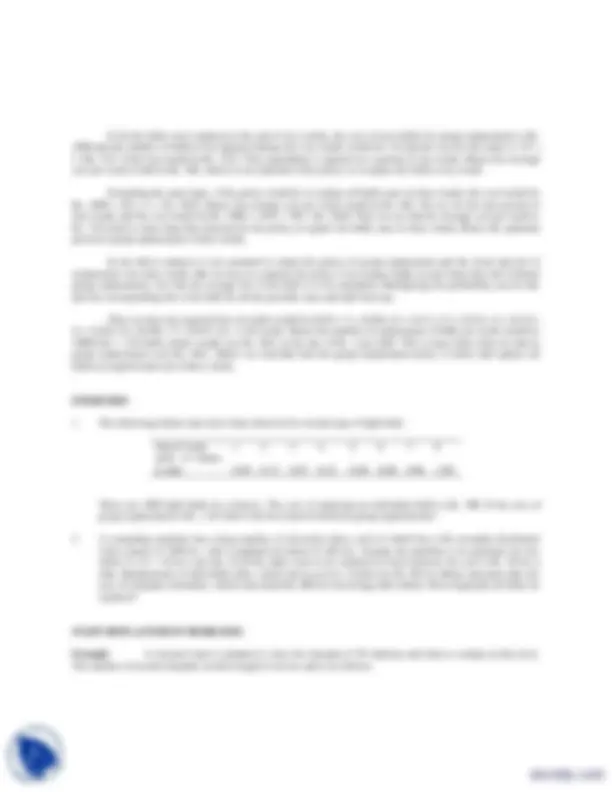
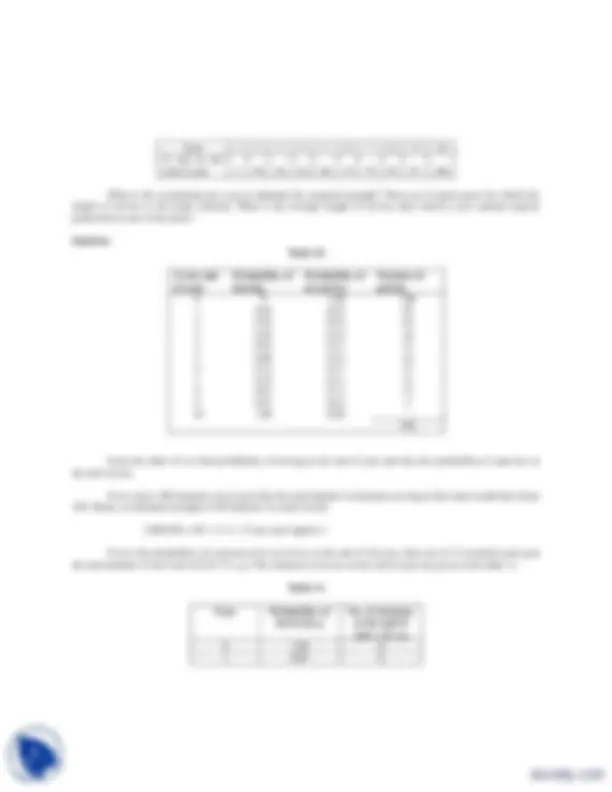
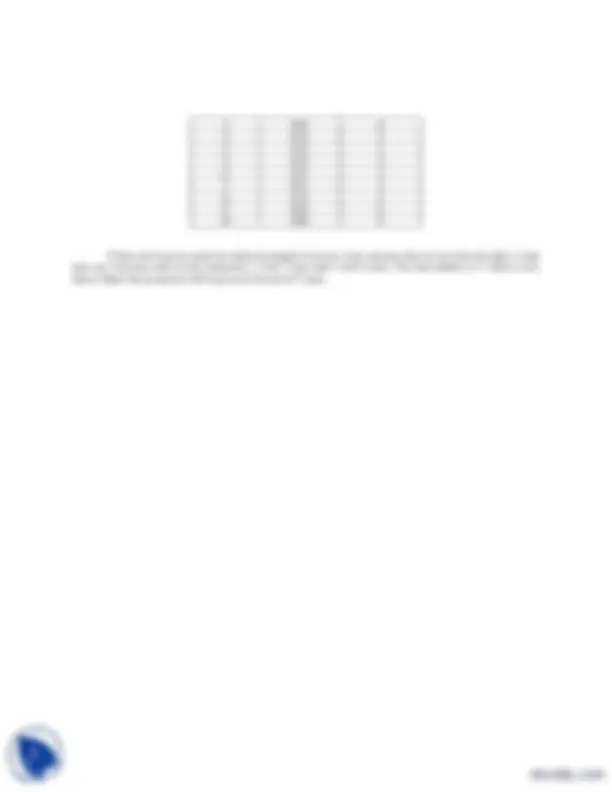
Study with the several resources on Docsity
Earn points by helping other students or get them with a premium plan
Prepare for your exams
Study with the several resources on Docsity
Earn points to download
Earn points by helping other students or get them with a premium plan
Community
Ask the community for help and clear up your study doubts
Discover the best universities in your country according to Docsity users
Free resources
Download our free guides on studying techniques, anxiety management strategies, and thesis advice from Docsity tutors
Operations Research (OR) refers to the science of decision making. This course elaborate like linear, nonlinear and discrete optimization. This lecture handout was provided by Sir Avikshit Gupte. It includes: Exercise, Maintainance, Found, Screap, Machine, Replaced, Experience, Determine, Replacement, Profitable
Typology: Exercises
1 / 10
This page cannot be seen from the preview
Don't miss anything!
Year 1 2 3 4 5 6 7 8 Maintenance cost (Rs.)
When should the machine be replaced?
Year 1 2 3 4 5 6 7 Cost of installation (Rs.)
Salvage value (Rs.)
Operating cost (Rs.)
Find an optimum replacement policy and the corresponding minimum cost.
In the previous section we did not take the interest for the money invested, the running costs and resale value. If the effect of time value of money is to be taken into account, the analysis must be based on an equivalent cost. This is done with the present value or present worth analysis.
For example, suppose the interest rate is given as 10% and Rs. 100 today would amount to Rs. 110 after a year's time. In other words the expenditure of Rs. 110 in year's time is equivalent to Rs. 100 today. Likewise one rupee a year from now is equivalent to (1.1)-1^ rupees today and one-rupee in ' n ' years from now is equivalent to (1.1)-n^ rupees today. This quantity (1.1)-n^ is called the present value or present worth of one rupee spent 'n' years from now.
We can establish an algebraic formula for the present worth value.
Let M = purchase price of an item. Rn = running cost in year n. r = rate of interest
The present worth of a rupee to be spent after a year is denoted by v and given by
v = 1/(1 + r )
v is called the discount rate. Let the item be replace after n years, and that the expenditure can be considered to take place at the beginning of each year. Then the present worth of expenditure denoted by
P(n) = M + R 1 + vR 2 + v^2 R 3 + ... + vn-^1 Rn
We note that P ( n ) increases as n increases.
The present worth of expenditure incurred for n years including the capital cost is obtained from a money lending institution and we repay the loan by fixed annual installments throughout the life of the machine. The present worth of this fixed annual installment x for n years is
= x + vx + v^2 x + ... + vn -1 x
= x (1 + v + v^2 + ... + vn -1) 1 ( ) 1
v^ n P n x v
(using the formula for a geometric series)
Since this is the sum repaid, we equate the present worth of expenditure to the present worth or repayment. Then,
( ).
1 n^
P n
v x v
So, the best period at which to replace the machine is the period n which minimizes x. Since (1 - v ) is constant, it is enough if we minimize P ( n )/(1 - vn ). The best period at which to replace the machine is the period n which minimizes P ( n ) / (1 - vn ) = F ( n ) (say).
The value of n is not continuous but discrete and hence we are not in a position to employ differentiation to find the optimum period.
Solution We prepare two tables 7 and 8 for machine A and for machine B respectively as shown.
Table 7
Machine A
Year n Running cost, Rn (Rs.)
vn -^1 (PWF)
vn -^1 Rn P ( n ) P ( n ) (1- v )/(1- vn )
Table 8
Machine B
Year n Running cost, Rn (Rs.)
vn -^1 (PWF)
vn -^1 Rn P ( n ) P ( n ) (1- v )/(1- vn )
From the above tables 7 and 8 we find that machine A is replaced at the end of 9th year with fixed annual payment of Rs. 5503 and that the machine B is replaced at the end of 8 years and the fixed annual payment is Rs.
Machine A Machine B Machine C Present investment Rs. 10000 12000 15000 Total Annual cost Rs. 2000 1500 1200 Life (years) 10 10 10 Salvage value Rs. 500 1000 1200
As an adviser to the buyer, you have been asked to select the best machine, considering 12% normal rate of return. You are given that:
(a) Single payment present worth factor (PWF) at 12 % rate for 10 years = 0.322. (b) Annual series present worth factor (PWFs) at 12 % rate for 10 years = 5.650.
Percentage failure by end of week 5 13 25 43 68 88 96 100
There are 1000 bulbs in a factory and it costs Rs. 400 to replace and individual bulb, which has burnt out. If all bulbs were replaced simultaneously, it would cost Re. 1 per bulb. It is proposed to replace all bulbs at fixed intervals, whether or not they have burnt out, and to continue replacing burnt out bulbs as they fail. At what intervals should all the bulbs be replaced?
Solution: We make two assumptions in solving the problem.
(1) The bulbs that fail during a week are replaced before the end of the week.
(2) The actual probability of failures during a week for a subpopulation of the bulbs with the same age is the same as the probability of failure during the week for that sub-population.
Let Pi be the probability that a bulb newly installed fails during the i th week of its life. This can be obtained from mortality table shown below in table 9.
Table 9
End of the week 1 2 3 4 5 6 7 8 Probability of failure during the i th week
Now, we calculate the number of bulbs that fail during a particular week and require replacement.
Let ni be the number of replacement made at the end of the i th week if all 1000 bulbs were new initially with the assumptions made above. We obtain,
n 0 = n 0 = 1000
n 1 = n 0 p 1 = 50
n 2 = n 0 p 2 + n 1 p 1 = 80 + 3 = 83
n 3 = n 0 p 3 + n 1 p 2 + n 2 p 1 = 120 + 4 + 4 = 128
n 4 = n 0 p 4 + n 1 p 3 + n 2 p 2 + n 3 p 1 = 180 + 6 + 7 + 6 = 199
n 5 = n 0 p 5 + n 1 p 4 + n 2 p 2 + n 3 p 2 + n 4 p 1 = 250+9+10+10+10 = 289
If the policy is to replace all the bulbs simultaneously every week the cost of installation of 1000 bulbs at the rate of Re. 1 per bulb is rate of Rs. 4 per bulb. Then the cost of replaced bulbs = Rs. 200. Total cost per week = Rs. 1200.
If all the bulbs were replaced at the end of two weeks, the cost of new bulbs for group replacement is Rs. 1000 and the number of bulbs to be replaced during first two weeks would be 133 and the cost for the same is 133 x 4 =Rs. 532. Total cost would be Rs. 1532. This expenditure is spread over a period of two weeks. Hence the average cost per week would be Rs. 766, which is less than that if the policy is to replace the bulbs every week.
Extending the same logic, if the policy would be to replace all bulbs once in three weeks, the cost would be Rs. 1000 + 261 x 4 = Rs. 2044. Hence the average cost per week would be Rs. 681. We try for the time period of four weeks and the cost would be Rs. 1000 + 1044 + 796 = Rs. 2840. Thus we see that the average cost per week is Rs. 710 which is more than that incurred for the policy to replace the bulbs once in three weeks. Hence the optimum period of group replacement is three weeks.
In the above analysis it was assumed to adopt the policy of group replacement and the fixed interval of replacement was three weeks. But we have to examine the policy if we replace bulbs as and when they fail (without group replacement). For this the average life of the bulb is to be calculated. Multiplying the probability can do this and the corresponding life of the bulb for all the possible cases and add them up.
Thus we have the expected life of a bulb would be (0.05 x 1) + (0.08 x 2) + (0.12 x 3) + (0.18 x 4) + (0.25 x
End of week 1 2 3 4 5 6 7 8 prob. of failure to date 0.05 0.13 0.25 0.43 0.68 0.88 0.96 1.
There are 1000 light bulbs in a factory. The cost of replacing an individual bulb is Rs. 500. If the cost of group replacement is Rs. 1.20 what is the best interval between group replacements?
Example A research team is planned to raise the strength of 50 chemists and then to remain at that level. The number of recruits depends on their length of service and is as follows.
If there are 8 service posts for which the length of service is the criterion, then we see from the table 11 that there are 3 persons with 6 years experience, 2 with 7 years and 2 with 8 years. The total number is 7, which is less than 8. Hence the promotion will be given at the end of 5 years.