
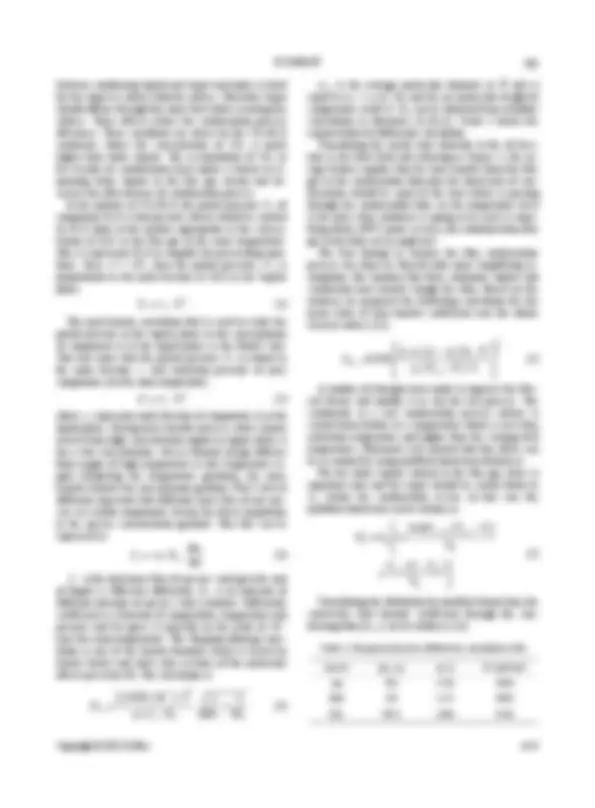
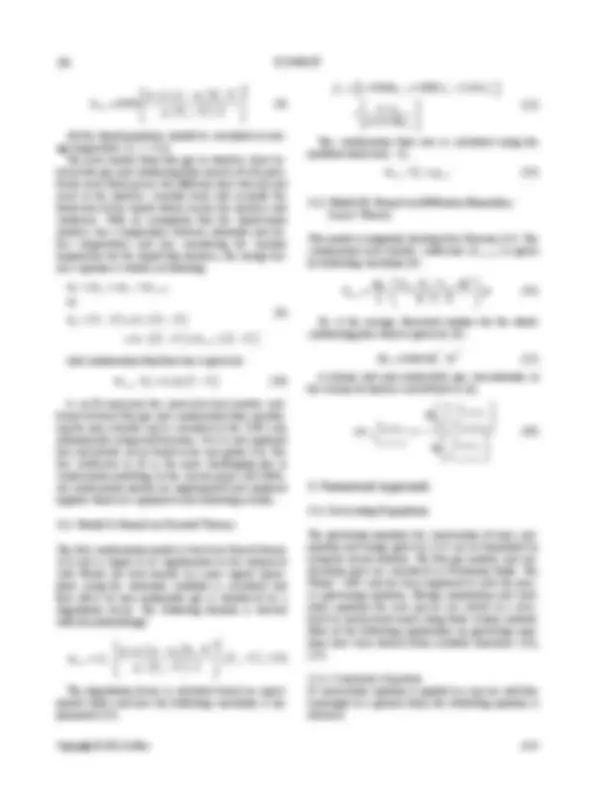
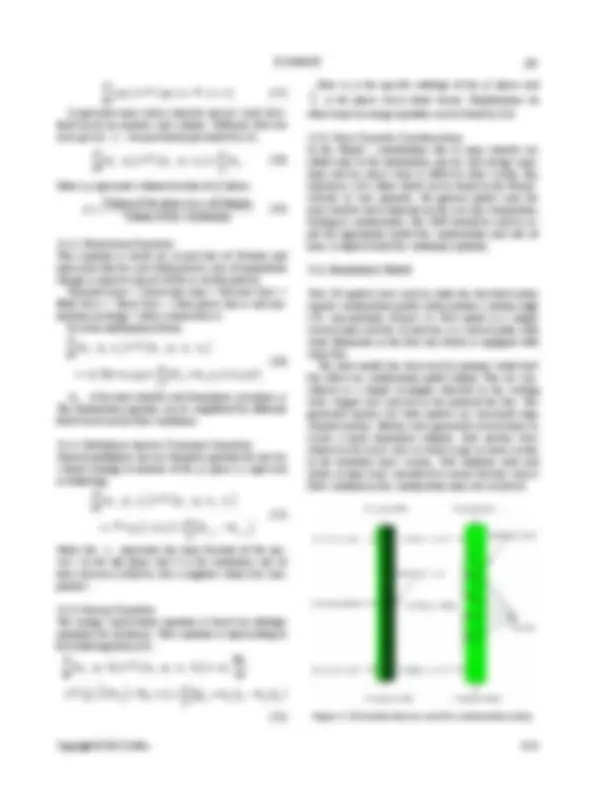
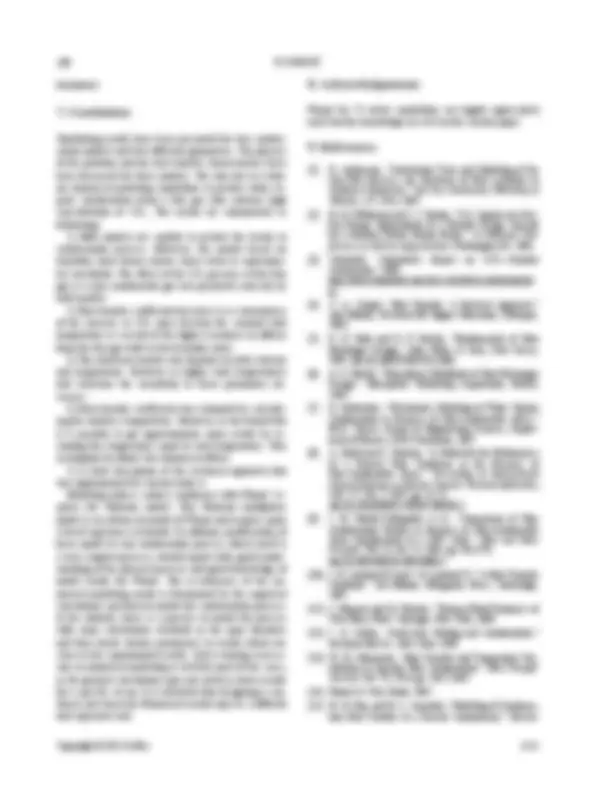
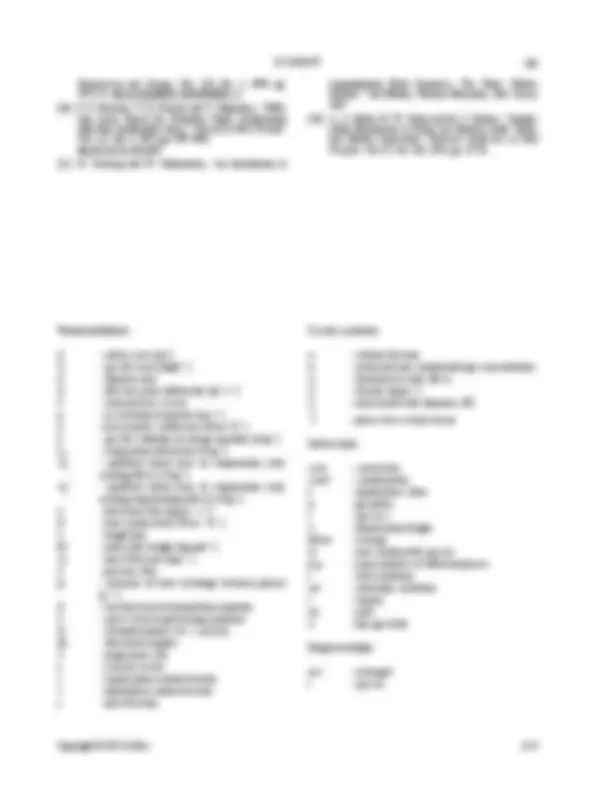
Study with the several resources on Docsity
Earn points by helping other students or get them with a premium plan
Prepare for your exams
Study with the several resources on Docsity
Earn points to download
Earn points by helping other students or get them with a premium plan
Community
Ask the community for help and clear up your study doubts
Discover the best universities in your country according to Docsity users
Free resources
Download our free guides on studying techniques, anxiety management strategies, and thesis advice from Docsity tutors
condensation of water vapor from a mixture of CO2/H2O is studied numerically
Typology: Study Guides, Projects, Research
1 / 9
This page cannot be seen from the preview
Don't miss anything!
Energy and Power Engineering , 2011, 3, 181- doi:10.4236/epe.2011.32023 Published Online May 2011 (http://www.SciRP.org/journal/epe)
School of Sustainable Development of Society and Technology , Mälardalen University , Västerås , Sweden E-mail : hamid.nabati@gmail.com Received February 2, 2011; revised April 7, 2011; accepted April 11, 2011
Abstract
1. Introduction
Oxy-fuel power plants are one of the recently promising processes for clean energy production with CO 2 captur- ing and condensers for separation of water vapour from flue gas are essential components in these new proposed power plants. As the combustion process in the oxy-fuel power plants is performed with fuel and pure oxygen, the re- sulting flue gas consists mostly of H 2 O and CO (^) 2.The water vapour separation process from the flue gas im- pacts the thermal efficiency of the plant and the opera- tional cost; thus the precise design of such CO (^) 2/H 2 O condenser systems is a vital demand in the industry [1-3]. Currently there are commercialized condensers in the market that most of them are installed for separation of air and water or for condensation of nearly pure water steams and thus far the condensers for separation of wa- ter vapor and CO 2 are not off the shelf products yet. Considering the specific characteristics of such condens- ers for application in the CO 2 /H (^) 2O separation, makes them as special process heat exchangers in the industry. Despite of wide referring to this kind of condenser in different proposed Oxy fuel cycles, the required design data are not available yet and there is a demand for more studies to achieve the desired efficiency for CO 2 captur- ing and steam separation and basic studies on condensa-
tion of water vapour from a flue gas with high CO 2 con- centration could provide such useful technical data for designers. Naturally, condensation happens whenever the vapour temperature is decreased by cooling until it reaches the saturation temperature T (^) sat at the operational pressure and usually this takes place when vapor is brought into con- tact with a solid surface whose temperature T (^) s is less than saturation temperature of the vapor. However condensa- tion can also occur in a gas or on the interface of a liquid and a gas. When condensation occurs in a gas, the liquid droplets usually suspend in the gas. As it is more com- mon in the industry to operate and control surface con- tacts condensers and also based on what is shown for oxy-fuel CO 2 capturing, in the current study the conden- sation on solid surfaces with focus on film condensation is considered. It is a common practice in the literatures to accept film condensation in heat exchanger design [4-6]. In this process, the condensate forms a liquid film is formed on the solid surface. This liquid film slips down under the influence of gravity. The thickness of the liquid film in- creases gradually with more vapors condensation on the film in the flow direction. Liquid covers the surface and eventually a liquid film takes place between vapour and solid surface. This liquid film resists against heat transfer flow. It means that released heat from vapour condensa-
tion at the vapour-liquid interface must transmit through this layer before it approaches the cooling solid surface. Moreover, the presence of even a small quantity of non-condensable gas significantly affects the heat trans- fer resistance in the region of the vapour-liquid interface. Experimental studies show that the non-condensable gases existence in the mixture has an unfavorable con- sequence on condensation process [7,8]. As an example, the presence of less than 1 percent (by mass) of air in steam decreases the condensation heat transfer coefficient more than half [4]. Vapour carries the non-condensable gas towards the vapour-liquid interface and it accumu- lates there. Thus special consideration should be applied when condensation from CO (^) 2/H 2 O mixture is studied. In this case a large portion of gas stream is occupied by CO 2 which is a non-condensable gas in the normal con- dition. This is one of the cases that are referred as multi-component ( n > 2) mixture condensation where n represents the number of components. The CO (^) 2/H (^) 2O flue gas is a binary ( n = 2) mixture that its phase equilibrium characteristics is important in flue gas condenser design and operation. Condensation of water vapor from CO (^) 2/H 2 O flue gas mixture on a vertical smooth surface is shown schemati- cally in the Figure 1. Referring to this figure, the condensation behavior can be explained as the following: When water vapor starts to condense, only the non- condensable gas part in the mixture remains in the vicin- ity of the interface surface. This gas layer acts as an ob- stacle between vapor and surface, and makes it difficult for the vapor to penetrate and reach the surface. Conse- quently, the efficiency of the condensation process is reduced. There are limited works about surface condensation which have been performed either experimentally or numerically. Recently, some studies have been per- formed on vapour condensation from mixture of non- condensable gases and steam. However, nowadays, the main idea is to use available tools (like numerical meth- ods) to develop robust and reliable methods which can be used to simulate the heat and mass transfer in condensa- tion process. Three main categories of condensation models are available: models with experimental correlations, models using Nusselt theory (based on heat and mass transfer analogy) and mechanistic models based on the boundary layer equations [9]. The main advantage of the first group models is their simplicity and therefore they can be easily adopted for numerical modeling. Also they can be used for initial verification of CFD condensation modeling. However they are bounded to a very limited set of data. The second group models are also suitable to
Figure 1. Water vapour condensation on a smooth vertical plane from a mixture containing non-condensable gas.
be implemented in the numerical simulation and they give more realistic results. The last group models are consistent with the numerical treatment of governing equations. But at the moment, implementation of such models requires high expenses because of their high de- gree of complexity. These are the best models that probably will be implemented in high accuracy CFD codes in future. This work evaluates two condensation models through a numerical simulation and propose the optimum model based on available two-phase flow mod- els and apply it in a numerical scheme with the help of Fluent©^ software to study water vapour condensation from a mixture containing mainly H (^) 2O and CO 2. Also effect of fin installation on the condensation surface is partly studied.
2. Physical Model for Binary System Condensation
As it was stated before, if any quantity of non-condensable gas exists in the mixture, there would be major effects on the heat and mass transfer resistance in the liquid-vapour interface. The non-condensable gas is carried towards the interface and accumulates there. This accumulation causes the partial pressure of gas at the interface became greater than its partial pressure in the binary mixture. This effect produces a driving force for non-condensable gas to diffuse again toward the bulk. This diffusive mo- tion is contrary to water vapour diffusion toward liq- uid-vapour interface. Also when the vapor which is mixed with a non-condensable gas is condensing, only the non-condensable gas remains in the vicinity of the liquid-gas surface. This gas layer forms a resisting wall
1 (^34)
f f fg f ilm f
k T T L
All the liquid properties should be calculated at aver- age temperature ( T (^) sat + T (^) s )/2. The heat transfer from flue gas to interface tween flue gas and condensing film consists of two parts: fir
g h g
h f sat ^ S
layer be-
stly, heat which passes the diffusion layer directly and reach to the interface (sensible heat) and secondly the latent heat of the vapour which reaches the interface and condenses. With an assumption that the liquid-vapor interface has a temperature between saturation and sur- face temperatures and also considering the constant temperature for the liquid film interface, the energy bal- ance equation is written as following:
(^)
or
tot film conv condens
tot s f f s h (^) (^) T (^) Tf (^) hcond (^) T Tf
q q q q
h T (^) T h T T
And condensation film flow rate is given by:
mcond hfg h Af s (^) Tf Ts (10)
sfer coef- fic der- ing the mass transfer and is calculated automatically using wall functions. So it is he
2] and is simple to be implemented in the numerical our atmos- here using the saturation condition is calculated and
h ∞ in (9) represents the convective heat tran ient between flue gas and condensation film consi in the CFD code not explained re and details can be found in the user guide [13]. The last coefficient in (9) is the most challenging part in condensation modeling. In the current paper, two differ- ent condensation models are implemented and compared together which are explained in the following sections.
The first condensation model is based on Nusselt theory [ code Firstly, the heat transfer in a pure vap p then effect of non-condensable gas is introduced by a degradation factor. The following formula is derived with this methodology:
1 (^3 ) f f g fg 1 cond nc sat f f
g h k q f T T T T L
nc nc nc nc
nc nc
f y y
y y
y
(^)
The condensation flow rate is calculated using the modified latent heat, hf g ^ : m cond h (^) fg qcond
nsf oefficient ( h ) is given by following correlation [4]:
This model is originally developed by Peterson [15]. The condensation heat tra er c (^) condens
2 2 L AB^ fg^ p g^ ,^ v cond
Sh h L R (^) v T (^) f T
D h C M
Sh (^) L is the average Sherwood number for the whole condensing plate which is given by [4]: 1 1 Sh 0.664 R^23 L eL^ ^ Sc (15)
the vicinity of interface and defined as [4]:
entration in
, , ,
ln 1
nc mean nc mean nc int
x x x
, ln
erface xsteam mean (^) xnc x
The governing equations for conversation of mass, mo- mentum and energy given by [17] can be formulated by sing the tensor notation. The flue gas mixture and con- Newtonian fluids. The ployed to solve the proc- , momentum and conti- ies are solved in a struc-
, mean (^) nc interface ,
3. Numerical Approach
u densation layer are considered as Fluent©^ CFD code has been em ess governing equations. Energy nuity equations for each spec
sat f (^)
The degradation factor is calculated based on experi- mental works and here the following correlation is im- plemented [15]:
tured or unstructured mesh using finite volume method. Most of the following explanations on governing equa- tions have been derived from available literatures [14], [17].
3.1.1. Continuity Equation If conservation equation is applied to a species and then rearranged in a general form, the following equation is obtained:
yi yi i Si t
S (^) i represents mass source term for species i and calcu- lated based on mixture unitvolume. Diffusive flux for each species J (^) i was previously presented by (3).
n
p 1
where αq represents volume fraction of q th^ phase:
Volume of the phase in a cell domain Volume of the cell domain
3.1.2. Momentum Equation This equation is based on second law of N represents that for each fluid particle, rate of momentum . Transient term + Convection term = Pressure force + Body force + Shear force + Inter-phase forces mentum exchange + other external forces Or in the mathematical form:
ewton and
change is equal to sum of all forces on that particle
and mo-
q q q q q q q n q q q pq pq q q q q
t
p R m
u u u
g u F
p 1
m (^) pq is the mass transfer rate from phase q to phase p. The momentum equation can be simplified for different flo ns.
3.1.3. Multiphase Species Transport Equation General multiphase species transport equation for s i which belongs to mixture of the q th^ phase is expressed as following:
ws based on the flow conditio
pecies
i i q q q q q q q
i n
y y t
u (21)
p 1 p q^ q^ p
3.1.4. Energy Equation The energy conservation equation is based on enthalpy equations for all phases. This equation is representing in g
where the yiq represents the mass fraction of the spe- cies i in the qth phase and S (^) i is the volumetric rate of mass increase (could be also a negative value) for com- ponent i.
the followin form [14]:
1
n q (^) q pq pq pq qp qp p
q q q q q q q q q
p h h t t
u
q q q
Here h (^) q is the specific enthalpy of the q th^ phase and
other terms in energy equation can be found in [14].
3.1.5. Mass Transfer Considerations In the Fluent©, contributions due to mass transfer are added only to the momentum, species and energy equa- tions and no source term is added to other scalars tu w ma in- ut the appropriate model for condensation and sink of tion.
The later model has been used to primary study how model output. Fins are con- idered as a simple rectangles attached to the cooling
dary layer section. Two adiabatic inlet and ou
like rbulence [14]. More detail can be found in the Fluent© ebsite or user manuals. No general model exist for ss transfer and it depends on the case like evaporation, boiling or condensation, The UDF should be used to p mass is imposed into the continuity equa
Two 2D models were used to study the described water vapour condensation model, when mixture contains high CO 2 concentration ( Figure 2 ). First model is a simple vertical plate and the second one is a vertical plate with same dimension as the first one which is equipped with some fins.
fins affect on condensation s wall. Copper was selected as the material for fins. The generated meshes for both models are structured map element meshes. Meshes were generated several times to assure a mesh dependent solution. Also meshes were refined in the areas close to walls to get accurate results in the boun tlet sections were considered to ensure that the correct flow condition in the condensation zone was achieved.
Figure 2. 2D models that are used for condensation study.
Figure 4. Comparison of two condensing models in mean heat transfer coefficient prediction (CO2/H (^) 2O mixture).
Figure 5. Comparison of condensation rate for two con- densation models.
rate decreases more sharply. The reason is that firstl
ecame more difficult. Results also showed that average heat transfer coeffi- cient is more sensitive to inlet velocity at low speeds. Figure 6 shows the results that are obtained with model based on diffusion boundary layer theory. It can be seen that at velocities more than 1.5 m/s, the velocity effects is negligible. However, when the CO 2 mass fraction is lower at the inlet, velocity can be an affecting parameter as well. The trend was found to be same for lower CO (^2) fractions. Effect of flue gas inlet temperature on mean heat transfer coefficient is depicted in Figure 7. Also here for higher inlet temperatures, rate of heat transfer coefficien
ature with less heat removal. Subse- uently the rate of condensation would be higher at
mparison of total heat transfer co
y there is less water content in the flow gas and secondly the diffusion of water vapour toward the cooling surface b
t change is less. It is natural, as water vapour reach to saturation temper q lower inlet temperature. Second case that was considered in this study was a vertical plate which was equipped with some pin fins. Figure 8 shows the co efficient in the simple condensing plate and surface
Figure 6. Average heat transfer coefficient vs inlet flue gas.
Figure 7. Relation between inlet temperature and total heat transfer coefficient.
Figure 8. Comparison of total heat transfer coefficient be- tween simple case and pin-finned surface
ible. It means that models that are eveloped here are not really accurate to predict the ex- act heat transfer coefficient in more complicate geome- tries. The reason is that the model just look into the cell adjacent to wall and the geometry is not accounted at all. Especially the correlations that were implemented are developed for vertical case and some surfaces of pins are
with pin fins. Figure shows that the difference in coeffi- cient values is neglig d
horizontal.
7. Conclusions
Simulating results have been presented for two conden- sation models and two different geometries. The physics of the problem and the heat transfer characteristics have been discussed for these models. The aim was to evalu- ate numerical modeling capabilities to predict water va- pour condensation from a flue gas that contains high concentration of CO2. The results are summarized as followings:
e to experimen-
ture. However at higher inlet temperatures nd velocities the sensitivity to these parameters de-
oefficient was estimated by calculat-
ppreciated an
9.
n
b tal correlation. The effect of the CO 2 presence in the flue gas as a non-condensable gas was predicted correctly by both models.
8. Acknowledgements
Fluent Inc.’S solver capabilities are highly a d I hereby knowledge use of it in the current paper.
References
[1] K. Andersson, “Combustion Tests and Modeling of the Oxy-Fuel Process—An Overview of R&d Activities at Chalmers University,” 2 nd Oxy-Combustion Workshop at Windsor , CT, USA, 2007. [2] M. B. Wilkinson and J. C. Boden, “CO 2 Capture via Oxy- fuel Firing: Optimization of a Retrofit Design Concept for a Refinery Power Station Boiler,” 1 st National Con- ference on Carbon Sequestration , Washington DC, 2001. [3] Vattenfall, “Vattenfall’s Project on CCS—Oxyfuel Combustion,” 2009. http://www.vattenfall.com/en/ccs/oxyfuel-combustion.ht m. [4] Y. A. Cengel, “Heat Transfer: A Practical Approach,” 2nd Edition, McGraw-Hil Higher Education, Dubuque,
[5] R. K. Shah and D. P. Sekulic, “Fundamentals of Heat Exchanger Design,” John Wiley & Sons, New Jersey,
Handbook of Heat Exchanger blishing Corporation, Bristol,
s,” Ph.D. Thesis, School of Engineering Sciences, Depart- s, KTH. Stockholm, 2007. ] A. Dehbi and S. Guentay, “A Model for the Performance
-52.
[7] K. Karkoszka, “Mechanistic Modeling of Water Vapour Condensation in Presence of Non-Condensable Gase
ment of Physic [ of a Vertical Tube Condenser in the Presence of Non-Condensable Gases,” Proceeding of International Topical Meeting on Nuclear Reactor Thermal-Hydraulics , Vol. 177, No. 7, 1997, pp. 41 doi:10.1016/S0029-5493(97)00184- [9] J. M. Martín-Valdepeñas et al. , “Comparison of Film Condensation Models in Presence of Non-Condensable Gases Implemented in a CFD Code,” Heat and Mass Transfer , Vol. 41, No. 11, 2005, pp. 961-976. doi:10.1007/s00231-004-0606- [10] J. H. Lienhard IV and J. H. Lienhard V, “A Heat Transfe Tex
r tbook,” 3rd Edition, Phlogiston Press, Cambridge,
hase Flow,” Springer, New York, 2006.
nd Temperature Dis-
6.2 User Guide, 2005.
200 5. [11] I. Mamoru and H. Takashi, “Thermo-Fluid Dynamics of Two-P [12] J. G. Collier, “Convective Boiling and Condensation,” McGraw-Hill Co., New York, 1980. [13] W. M. Rohsenow, “Heat Transfer a tribution in Laminar Film Condensation,” Heat Transfer Journal , Vol. 78, 1956, pp. 1645-1648. [14] Fluent [15] M. H. Kim and M. L. Corradini, “Modeling of Condensa- tion Heat Transfer in a Reactor Containment,” Nuclear