
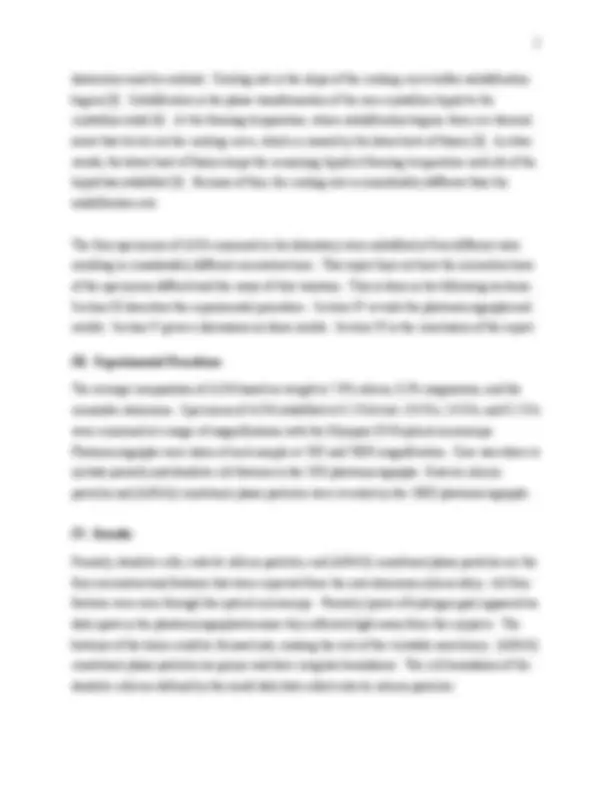
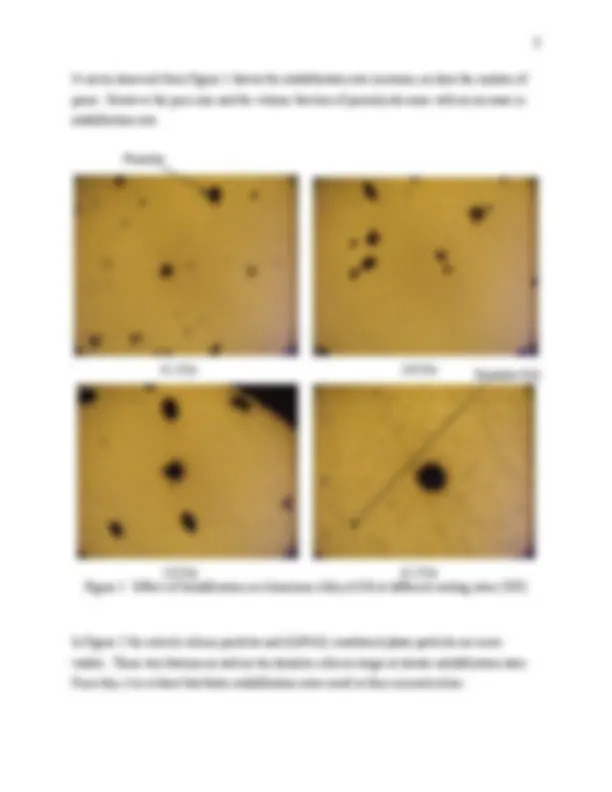
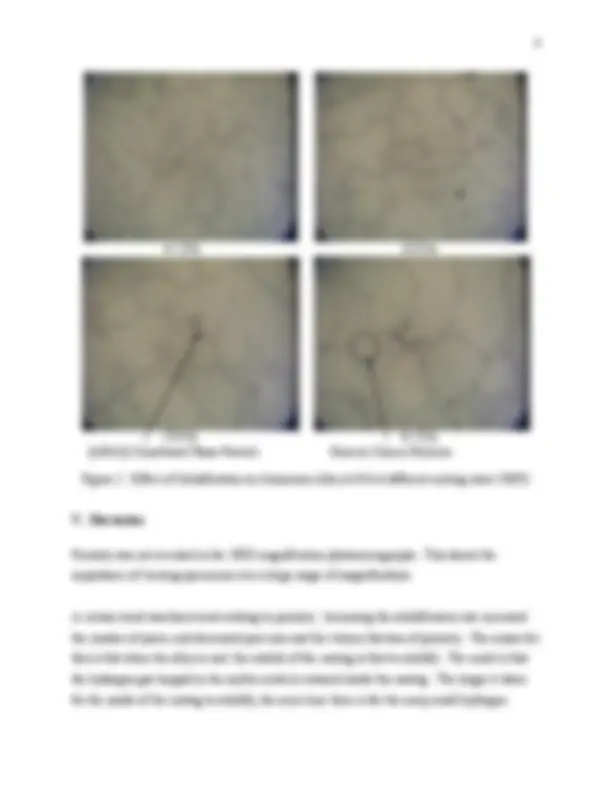
Study with the several resources on Docsity
Earn points by helping other students or get them with a premium plan
Prepare for your exams
Study with the several resources on Docsity
Earn points to download
Earn points by helping other students or get them with a premium plan
Community
Ask the community for help and clear up your study doubts
Discover the best universities in your country according to Docsity users
Free resources
Download our free guides on studying techniques, anxiety management strategies, and thesis advice from Docsity tutors
Material Type: Lab; Professor: Anyalebechi; Class: Materials Science and Engineering; Subject: Engineering; University: Grand Valley State University; Term: Spring 2005;
Typology: Lab Reports
1 / 6
This page cannot be seen from the preview
Don't miss anything!
Effects of Solidification Rate on Porosity Formation and Cast Microstructure in Aluminum Alloy A
by
Dan VanderBoon
School of Engineering Padnos College of Engineering & Computing Grand Valley State University
Laboratory Module 3 EGR 250 – Materials Science & Engineering Section 2
Instructor: Dr. P. N. Anyalebechi
February 1, 2005
I. Abstract
The purpose of this report was to analyze the effects of solidification rate on the microstructure of the cast aluminum alloy A356. Four specimens of A356 that solidified at different rates were examined with an optical microscope. Photomicrographs of each specimen were taken at high and low magnifications. The photomicrographs revealed a trend in porosity formation. Decreasing solidification rate caused fewer pores, bigger pores, and more area of the photomicrograph was taken up by the pores. It was also observed that an increase in solidification rate resulted in finer microstructure. In other words, all the microstructure features (porosity, dendrite cells, eutectic silicon particles, and [AlFeSi] constituent phase particles) became smaller.
II. Introduction
Metallography is the science of evaluating metal structures [1]. This is done on the macro and micro levels. The optical microscope is useful on the micro level to provide extensive information about a materials microstructure. The class of the material involved, method of manufacturing, whether the material has been heat-treated or not, and other inferences can be gathered from an optical microscope [1]. In this laboratory, an optical microscope was used to examine the effects of solidification rate on the microstructure of aluminum alloy A356.
A356 is used for aircraft pump parts, automotive transmission cases, and water-cooled cylinder blocks [2]. Aluminum alloys are favorites of the transportation industry because they can decrease fuel consumption as a result of a high specific strength. High corrosion resistance, ductility, and electrical and thermal conductivity are other favorable properties of aluminum [2]. A356 is a cast, heat-treatable alloy [2]. It is subjected to a solution heat treatment followed by artificial aging [2]. This process is referred to as precipitation hardening [2]. In solution heat treatment all the solute atoms are dissolved to form a single-phase solid solution [2]. This is accomplished by heating the alloy to a temperature within a phase field and waiting for all other phases present to dissolve into that particular phase [2]. After this the solution is cooled.
The cooling step in the alloy treatment process affects the microstructure of A356. However, it is not the cooling rate but the solidification rate that is taken into account in this laboratory. This
It can be observed from Figure 1 that as the solidification rate increases, so does the number of pores. However the pore size and the volume fraction of porosity decrease with an increase in solidification rate.
6.2 K/s 3.8 K/s
2.0 K/s 0.2 K/s Figure 1: Effect of Solidification on Aluminum Alloy A356 at different cooling rates (50X)
In Figure 2 the eutectic silicon particles and [AlFeSi] constituent phase particles are more visible. These two features as well as the dendrite cells are larger at slower solidification rates. From this, it is evident that faster solidification rates result in finer microstructure.
Dendrite Cell
Porosity
6.2 K/s 3.8 K/s
2.0 K/s 0.2 K/s
Figure 2: Effect of Solidification on Aluminum Alloy A356 at different cooling rates (500X)
V. Discussion
Porosity was not revealed in the 500X magnification photomicrographs. This shows the importance of viewing specimens over a large range of magnifications.
A certain trend was discovered relating to porosity. Increasing the solidification rate increased the number of pores, and decreased pore size and the volume fraction of porosity. The reason for this is that when the alloy is cast, the outside of the casting is first to solidify. The result is that the hydrogen gas trapped in the molten metal is retained inside the casting. The longer it takes for the inside of the casting to solidify, the more time there is for the many small hydrogen
[AlFeSi] Constituent Phase Particle Eutectic Silicon Particles