
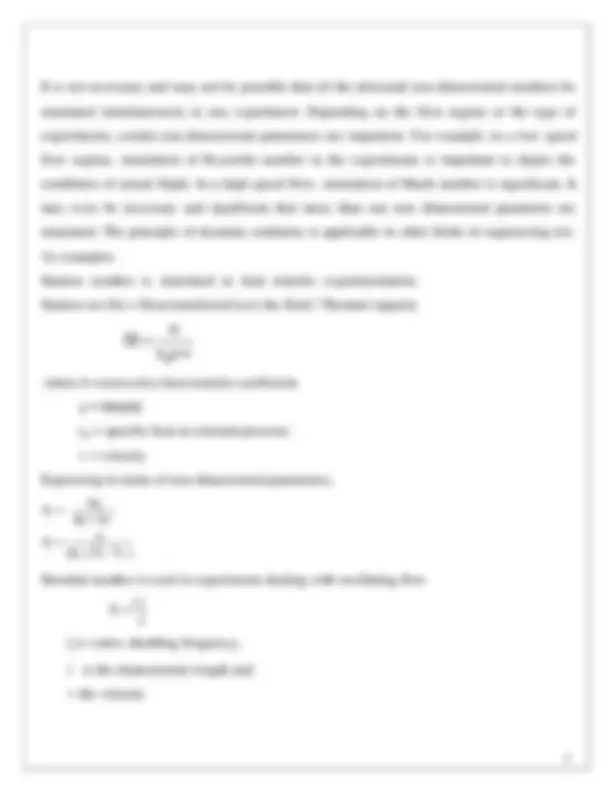
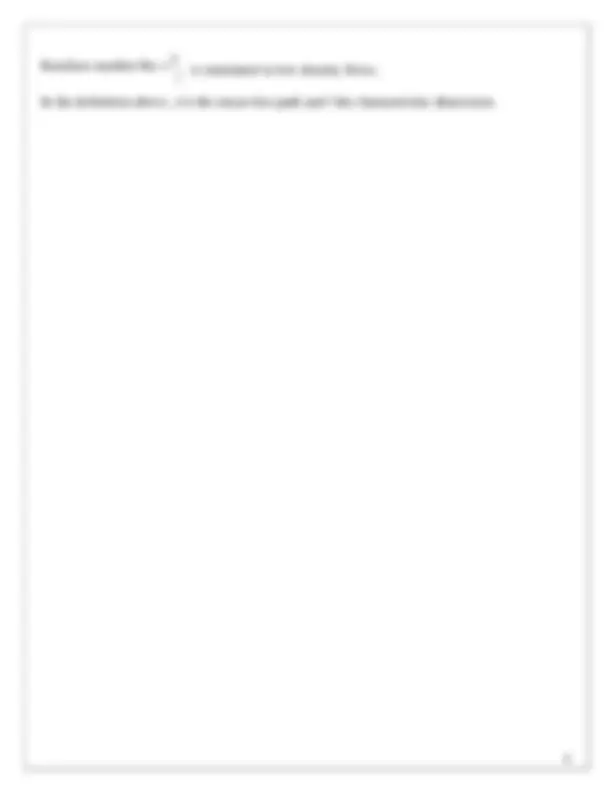
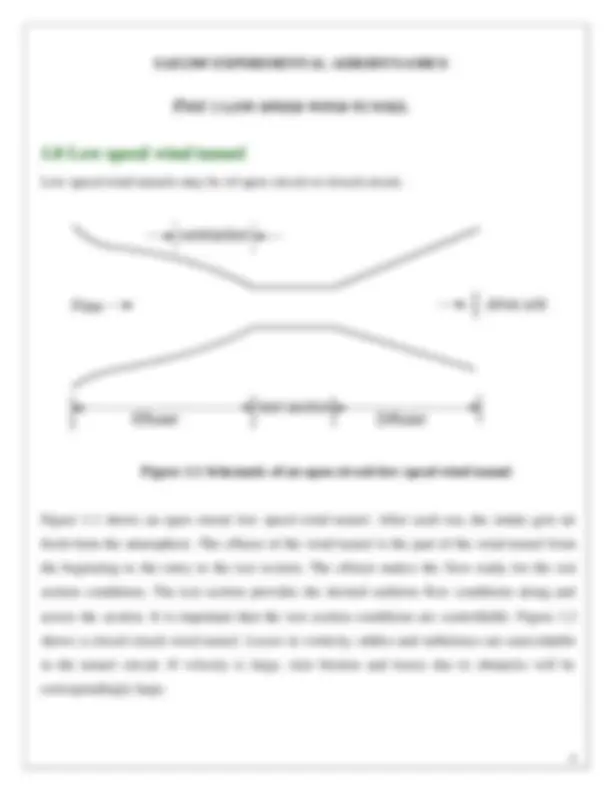
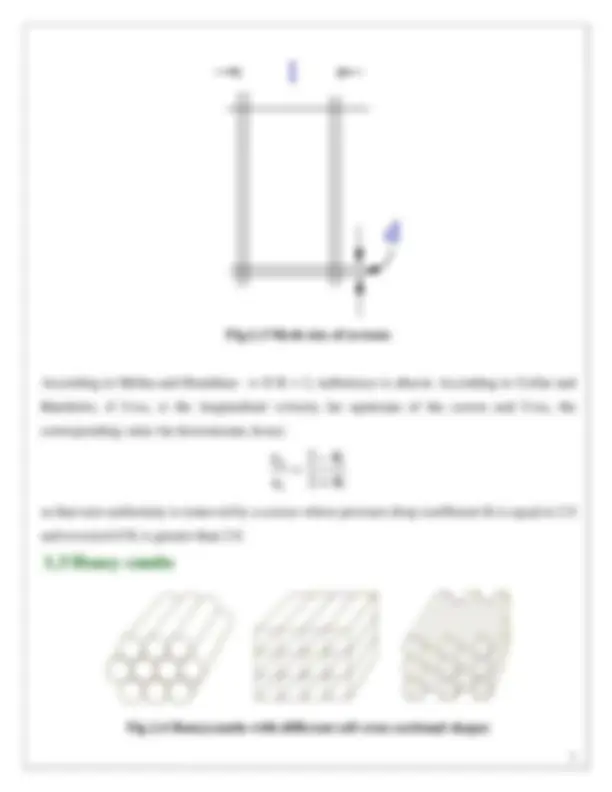
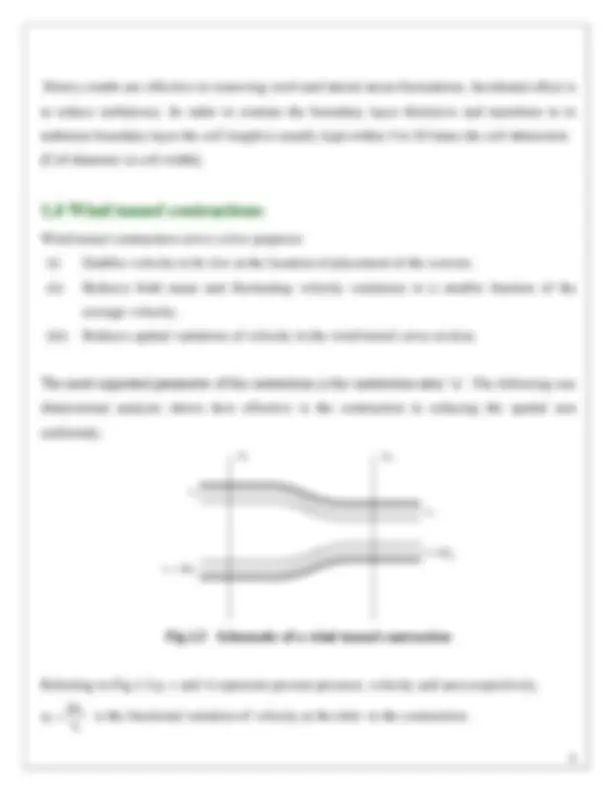
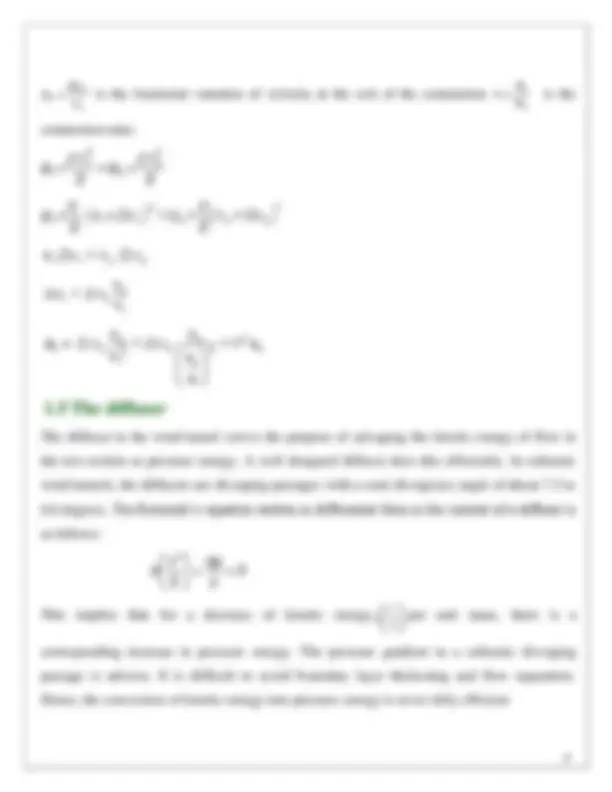
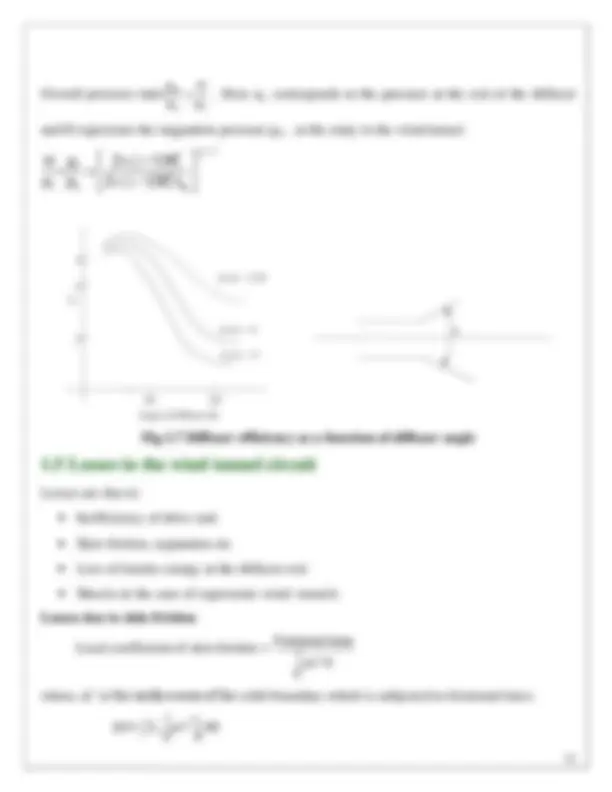
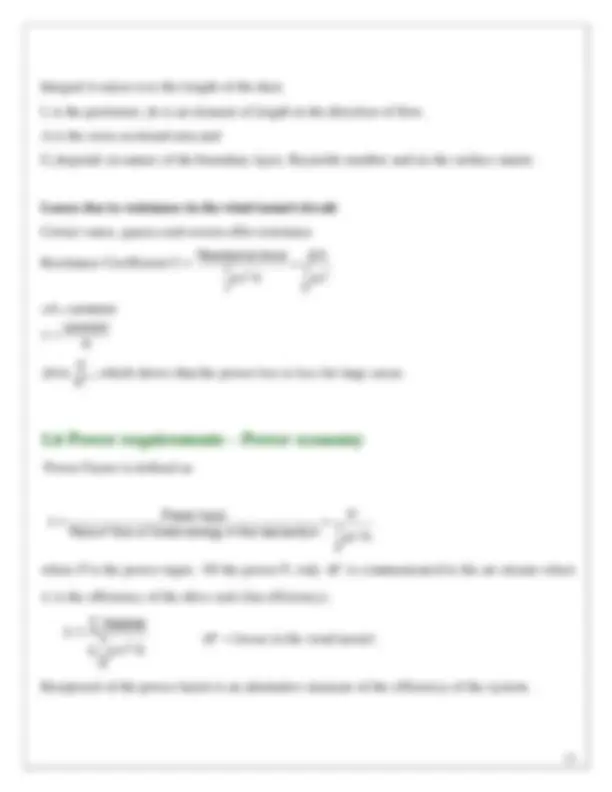
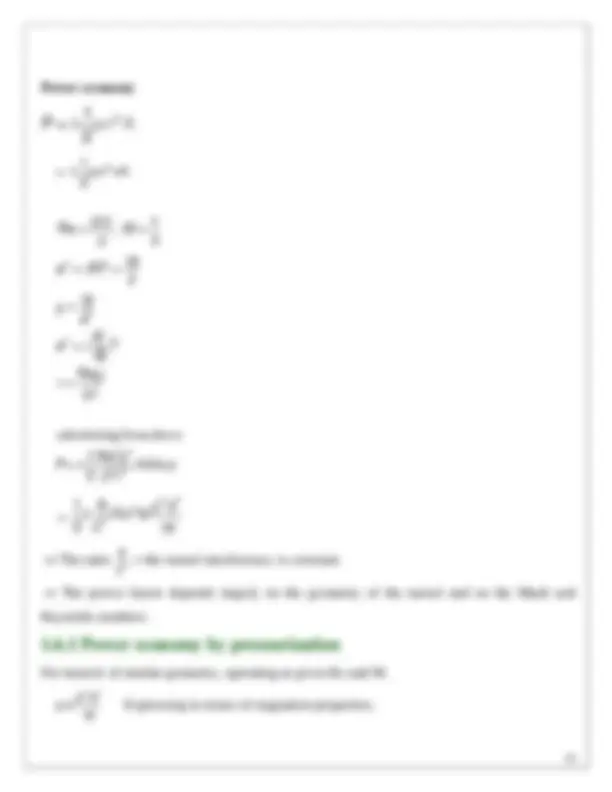
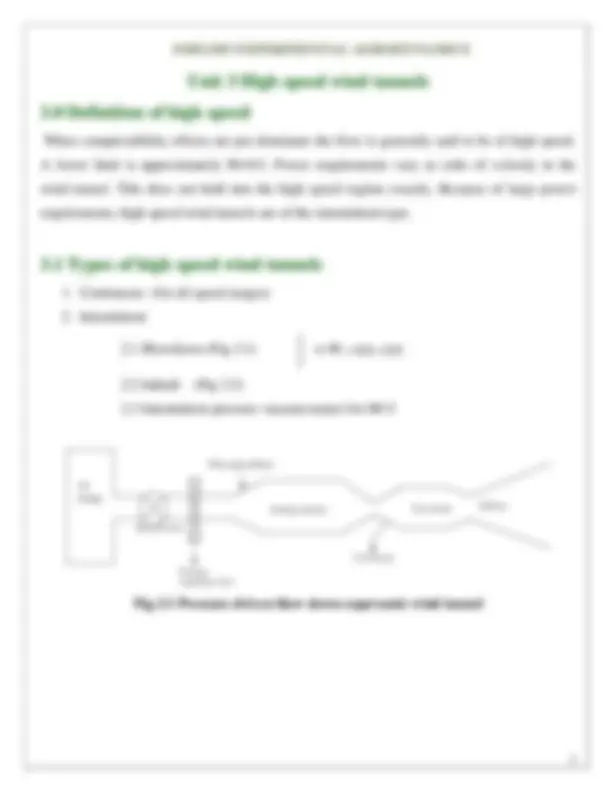
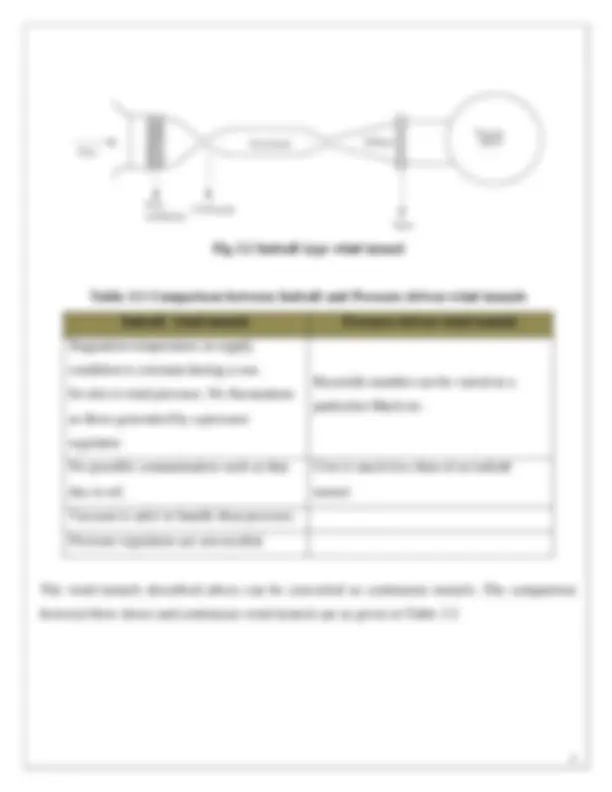
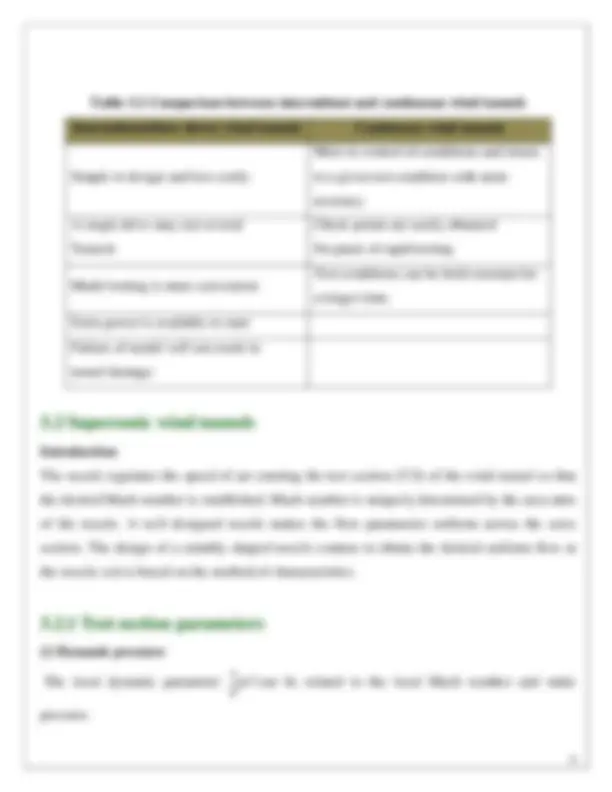
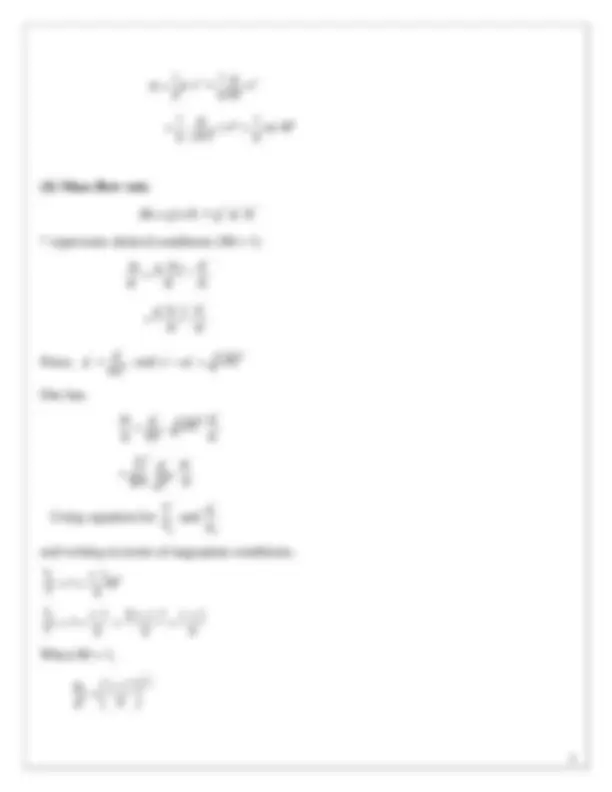
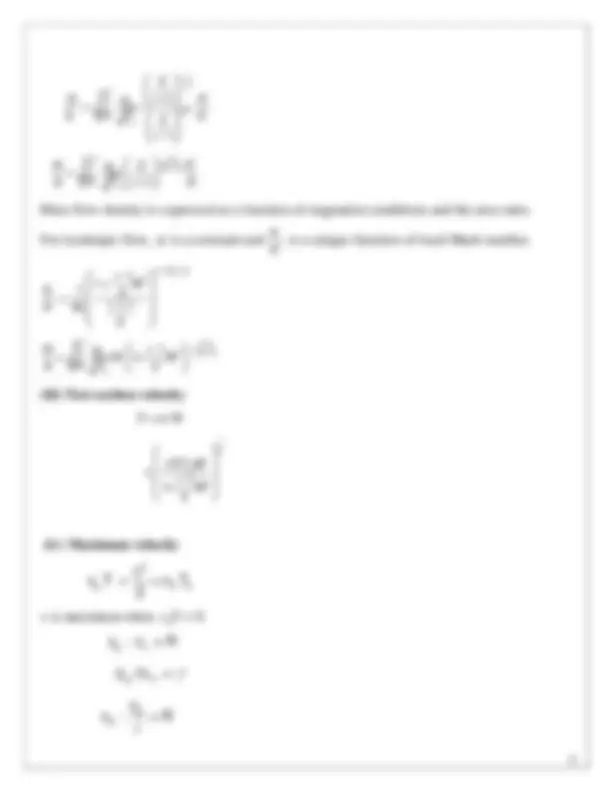
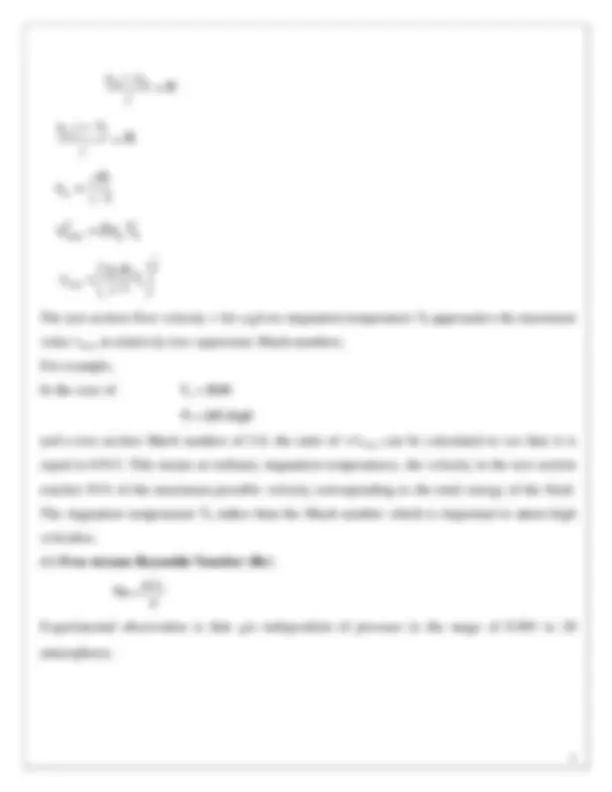
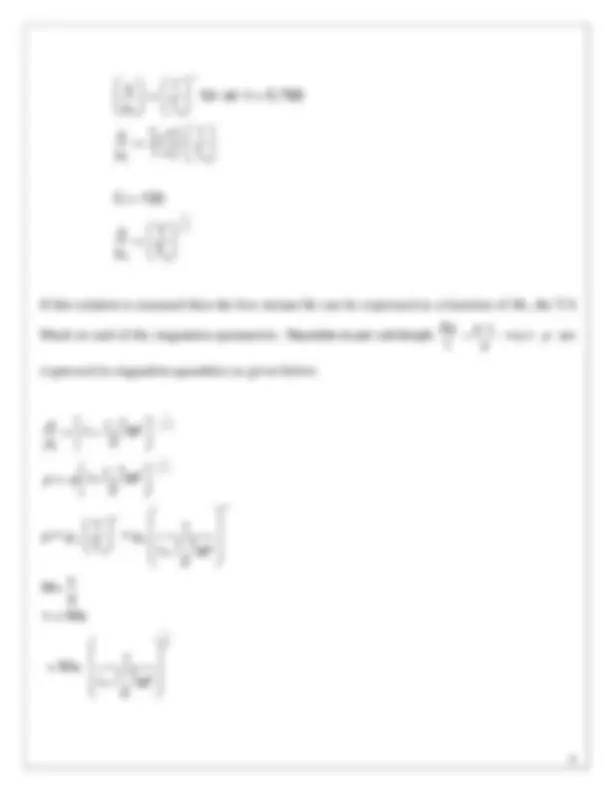
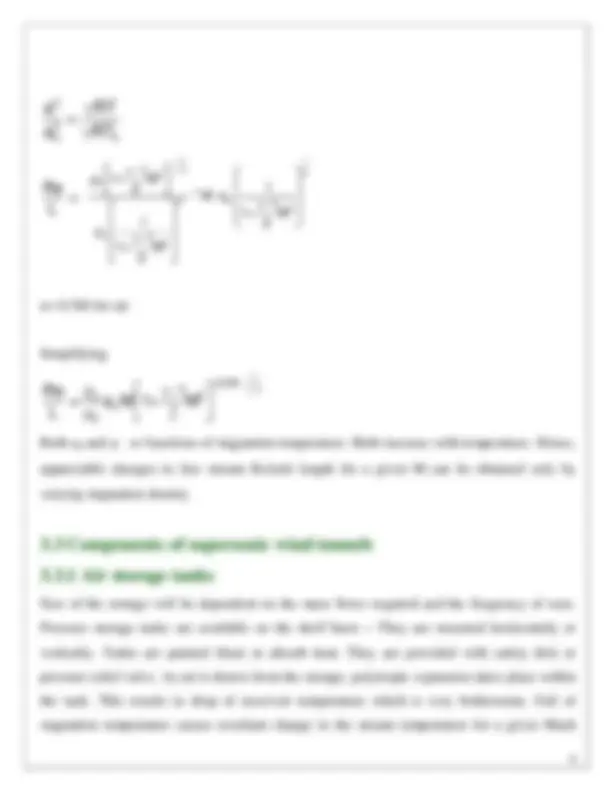
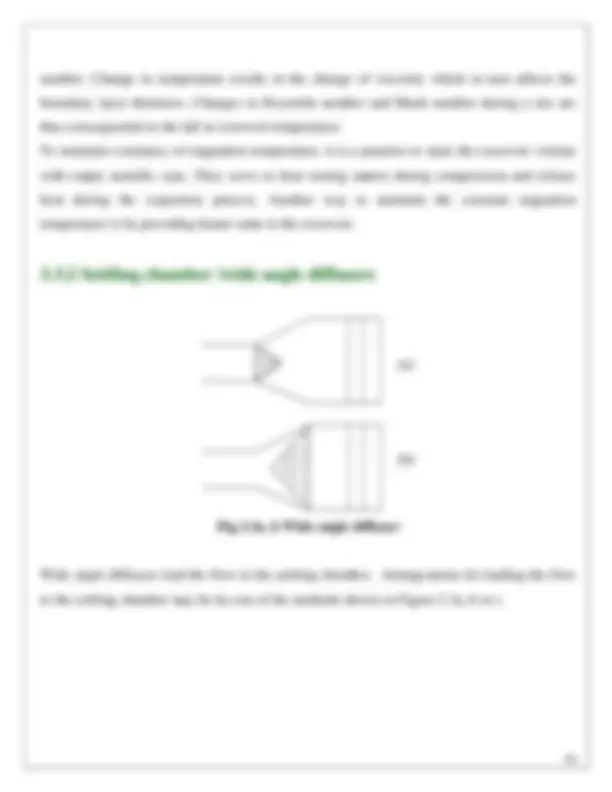
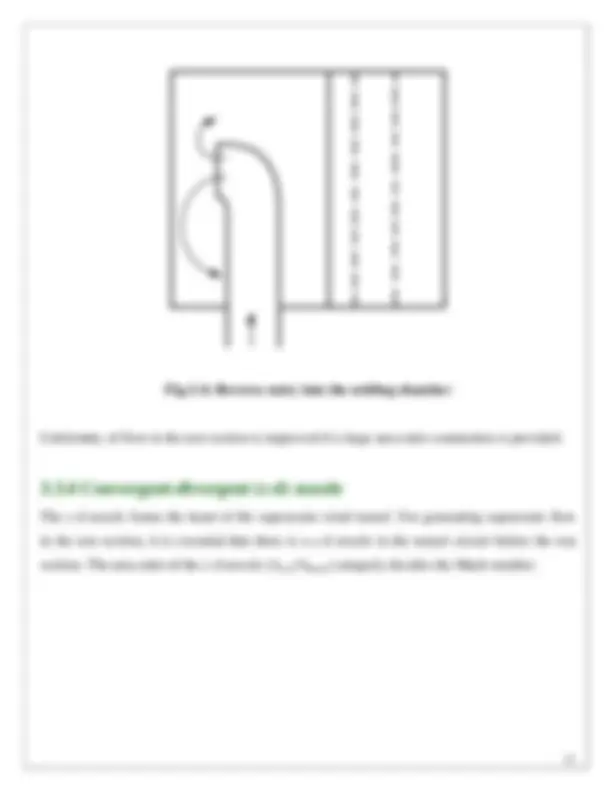
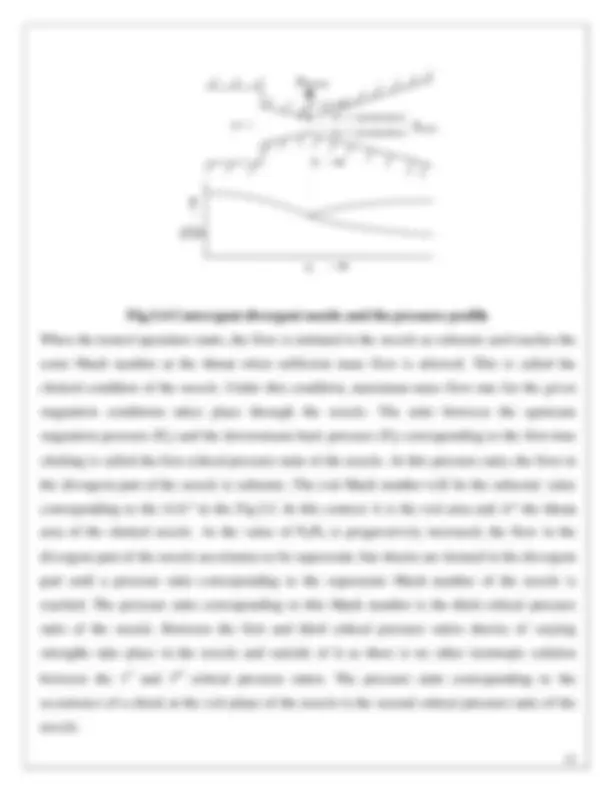
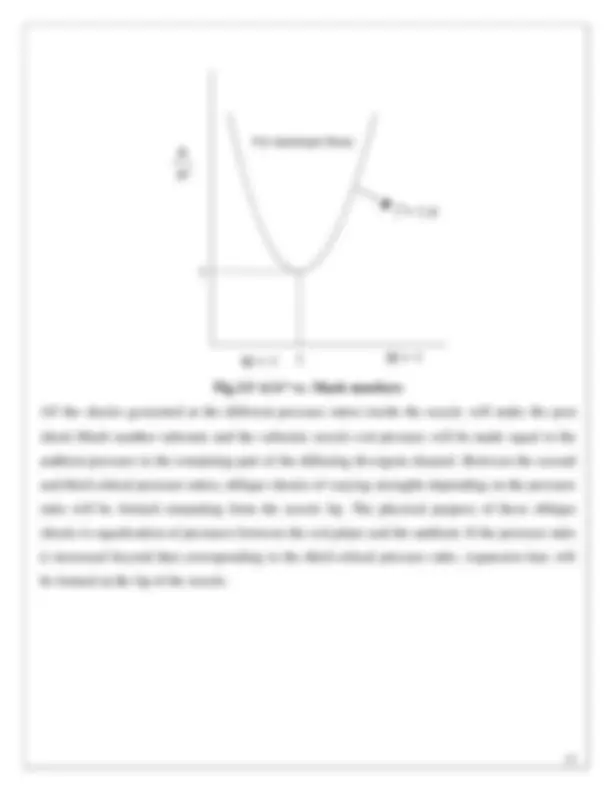
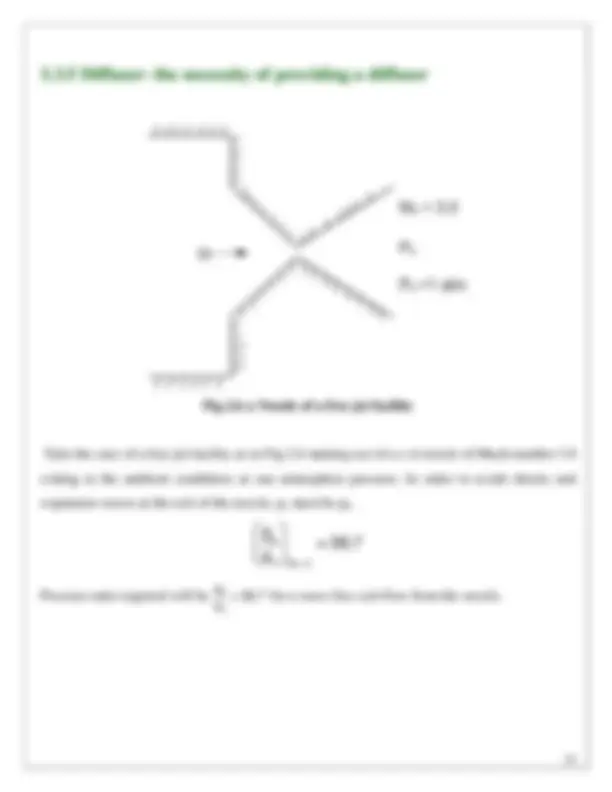
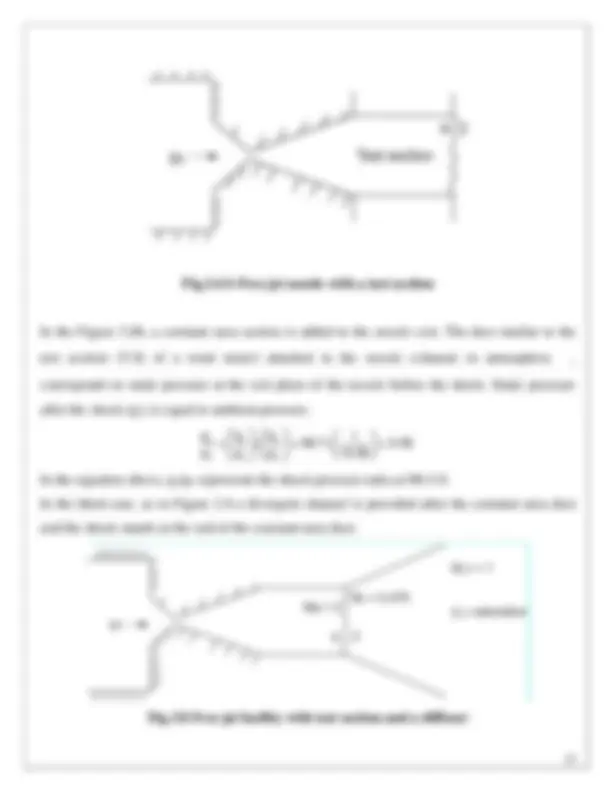
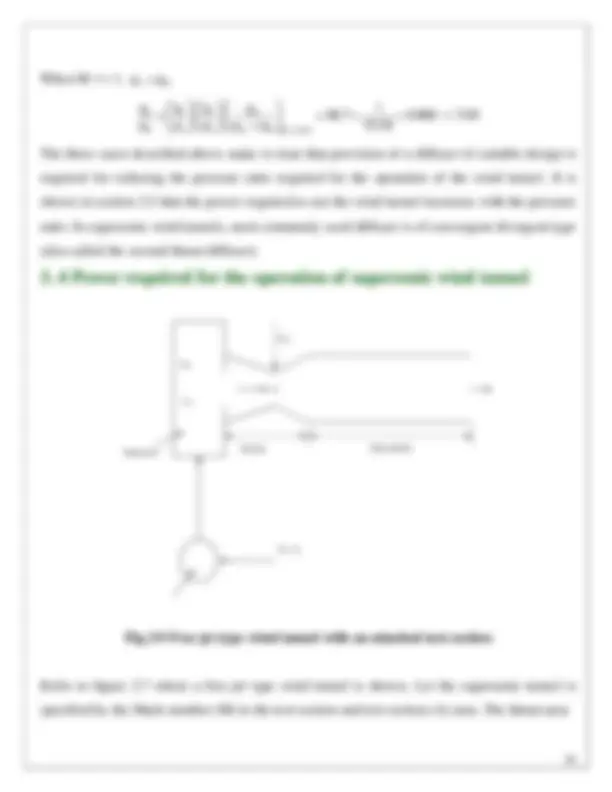
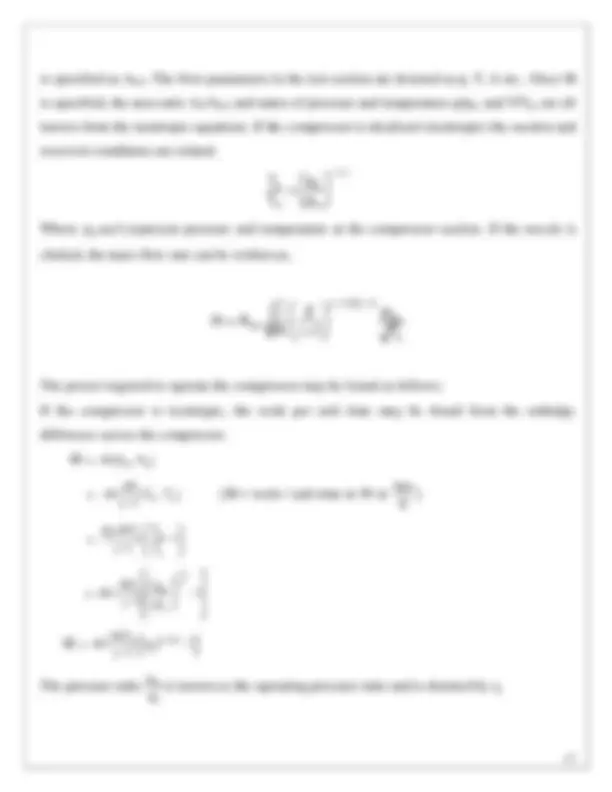
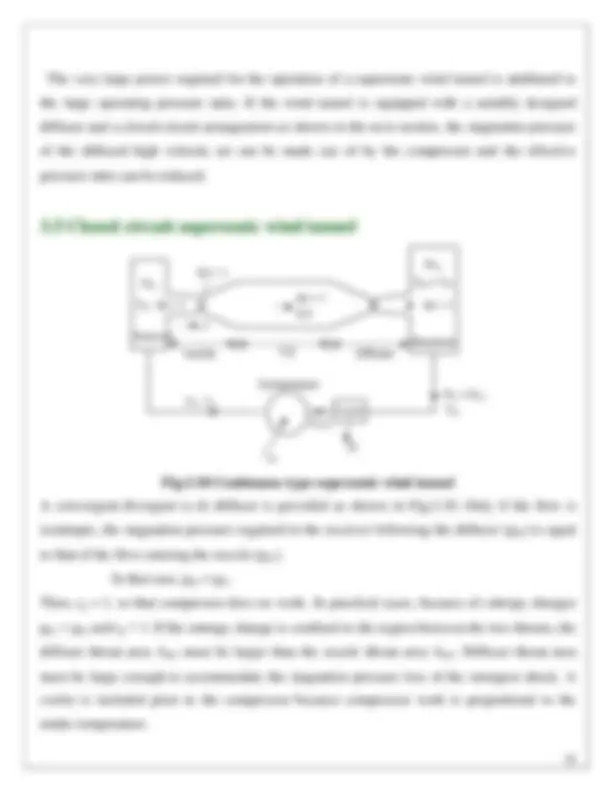
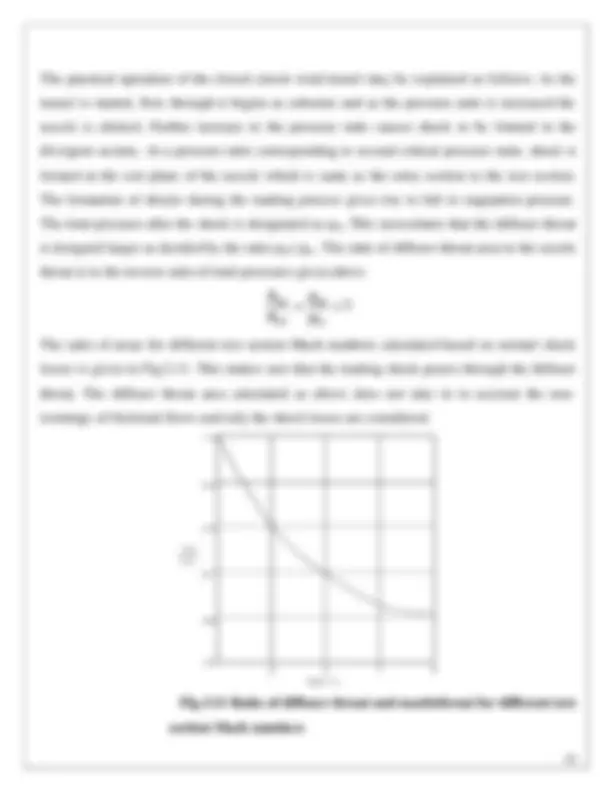
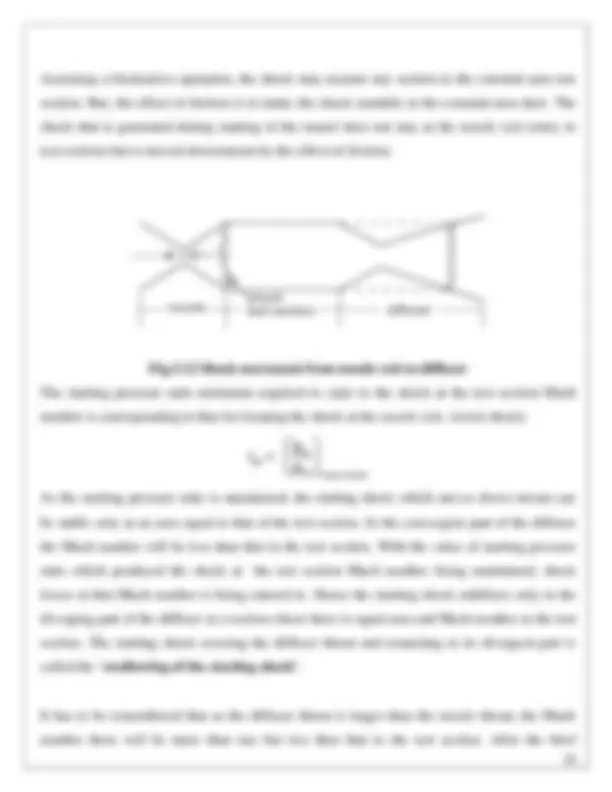
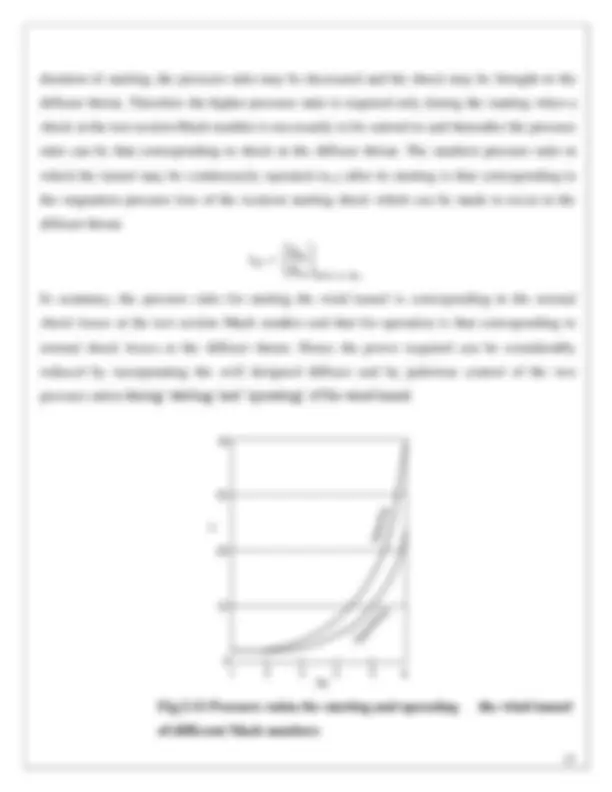
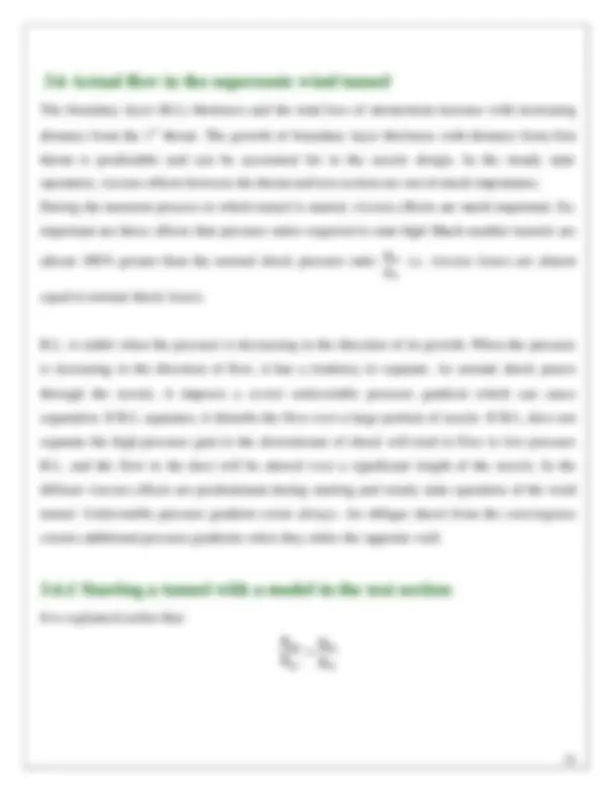
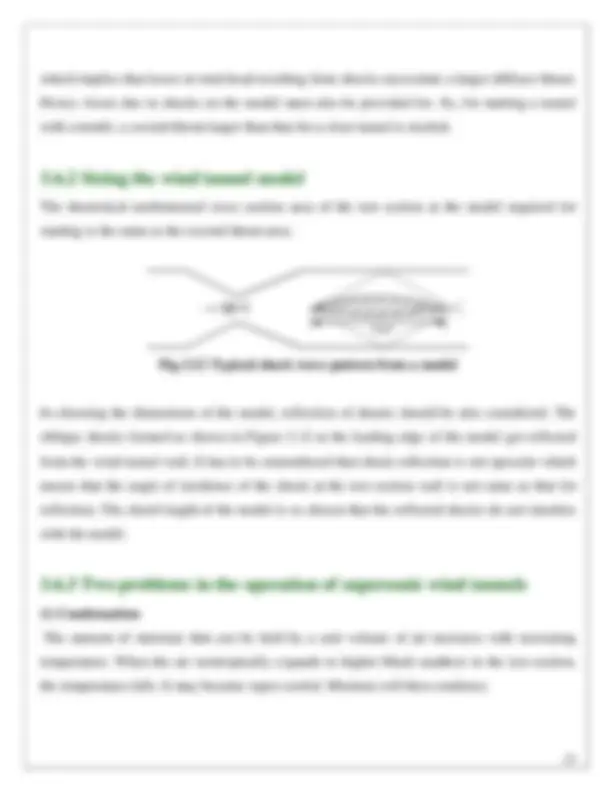
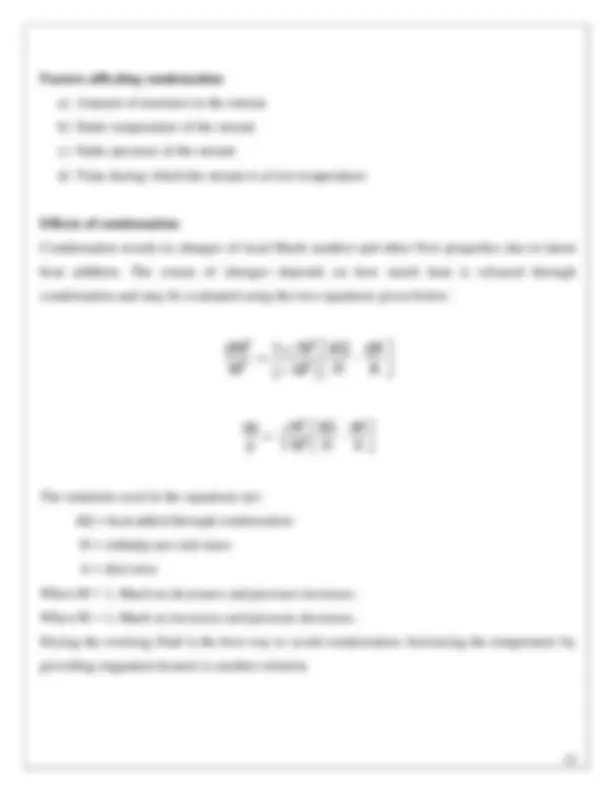
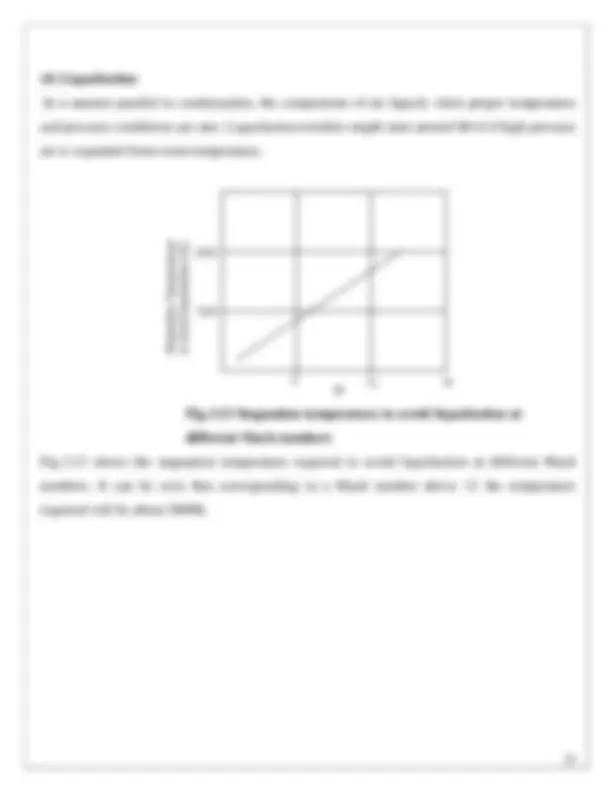
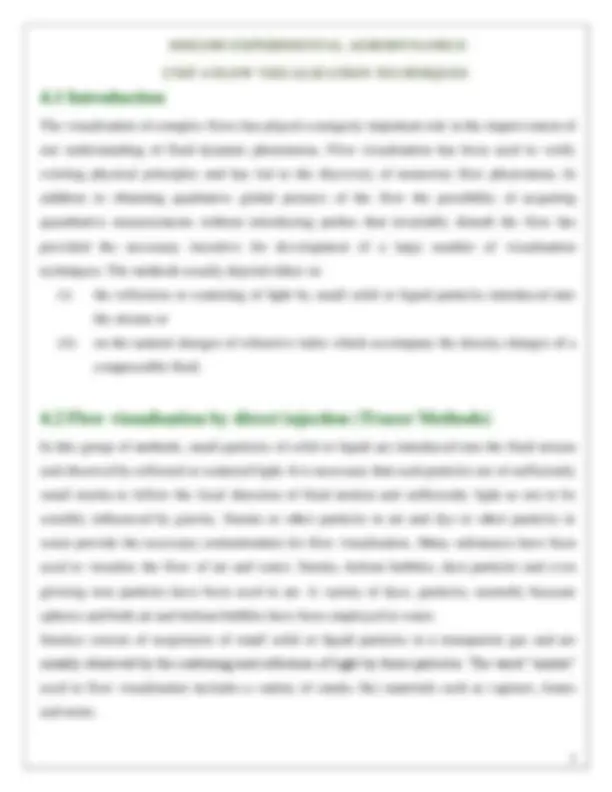
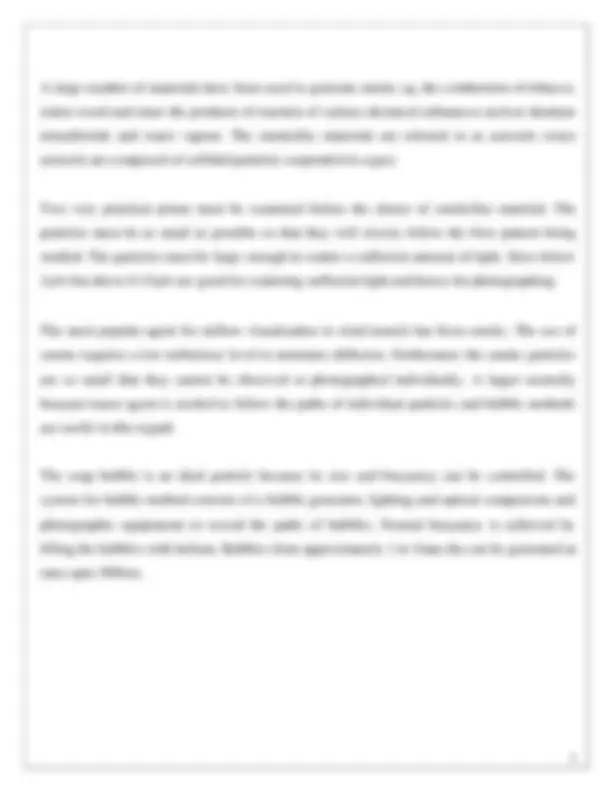
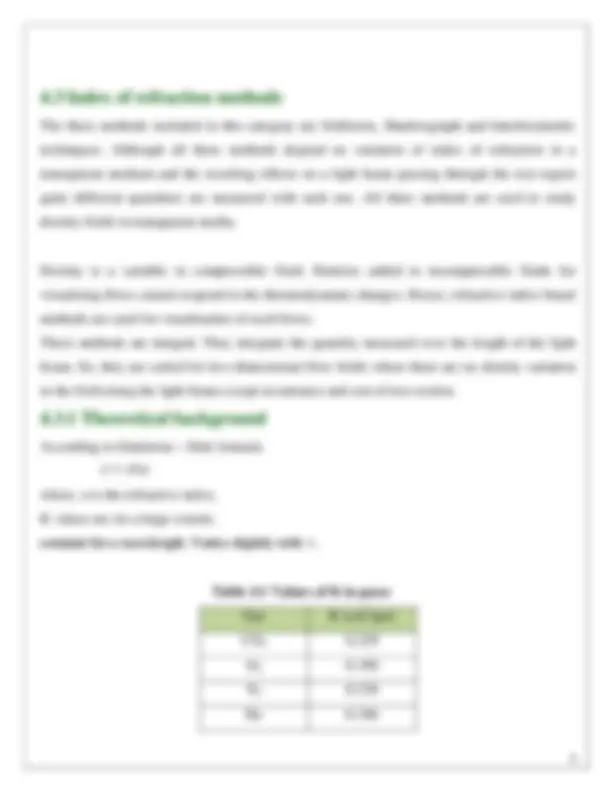
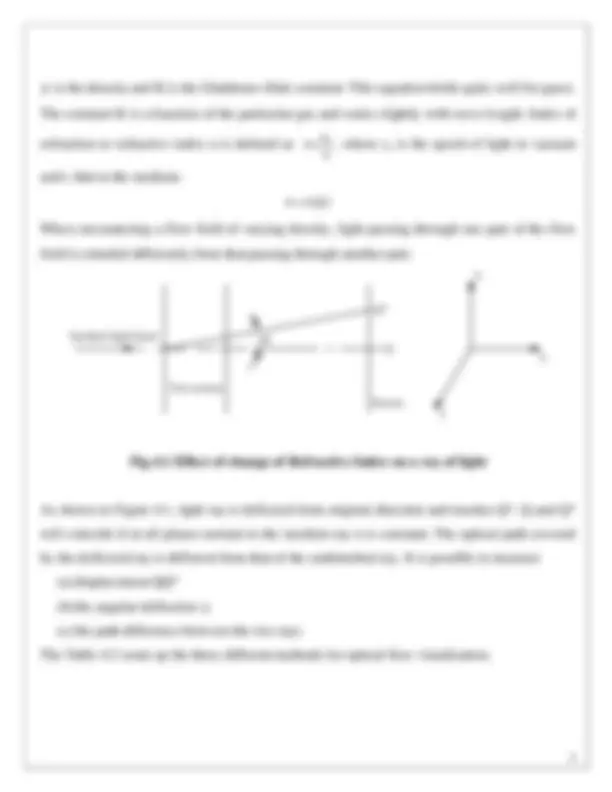
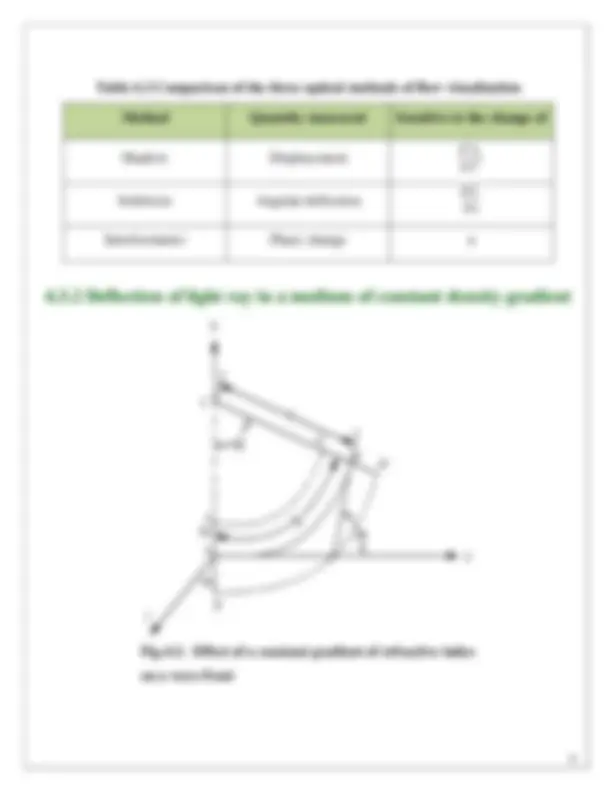
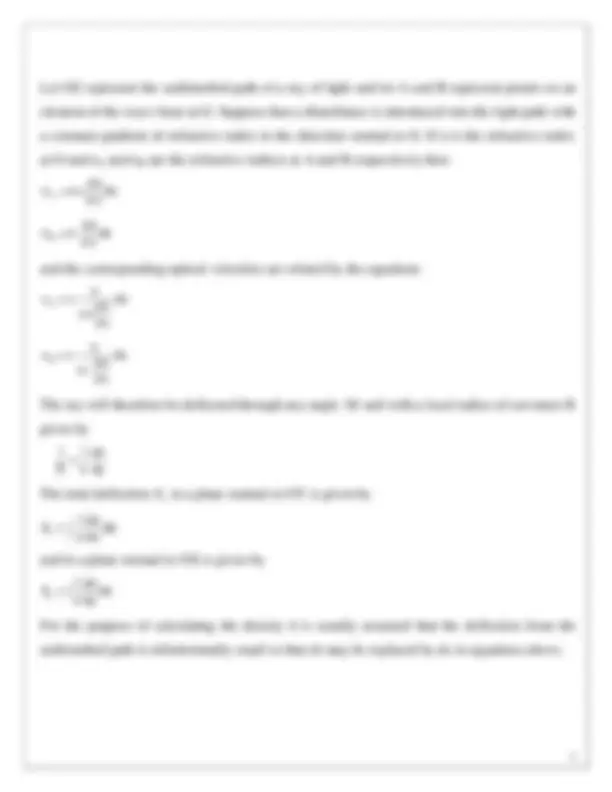
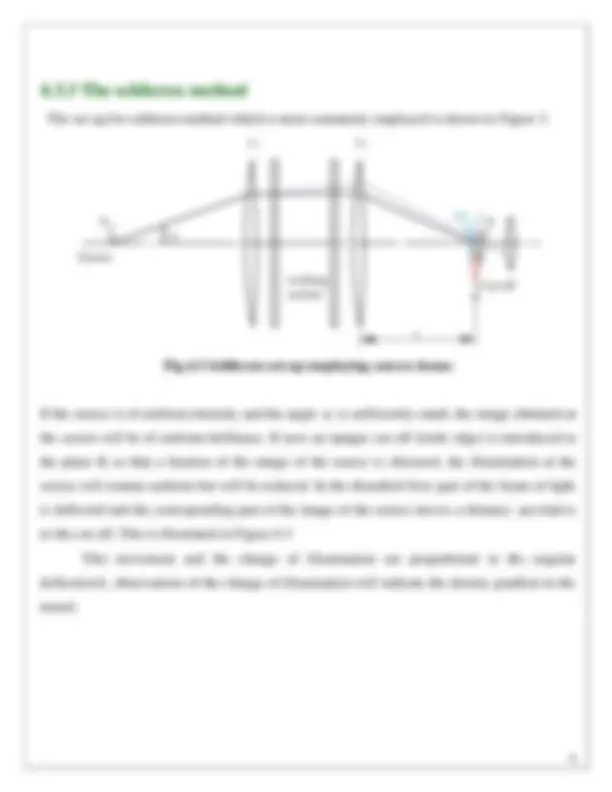
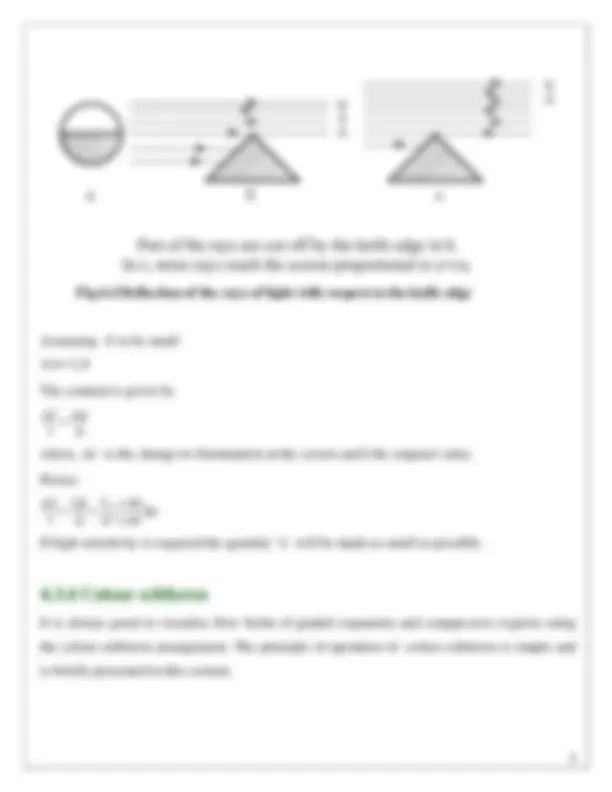
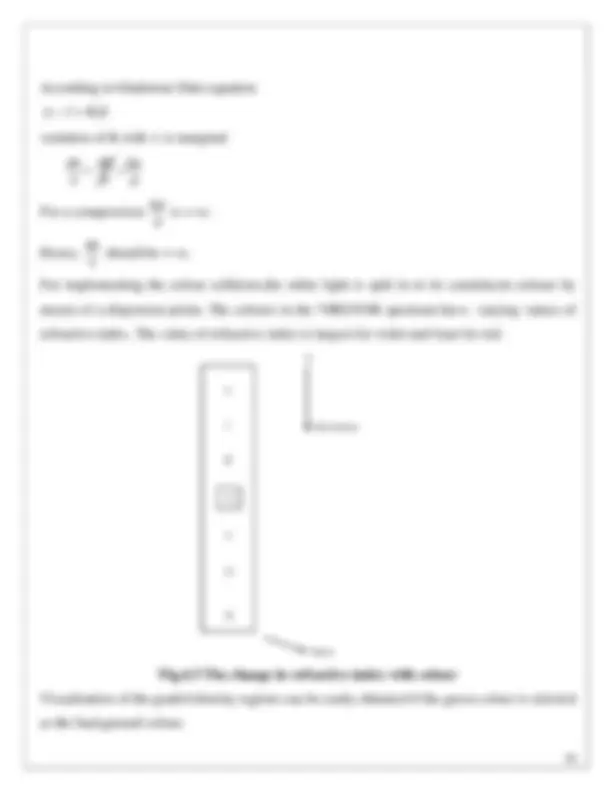
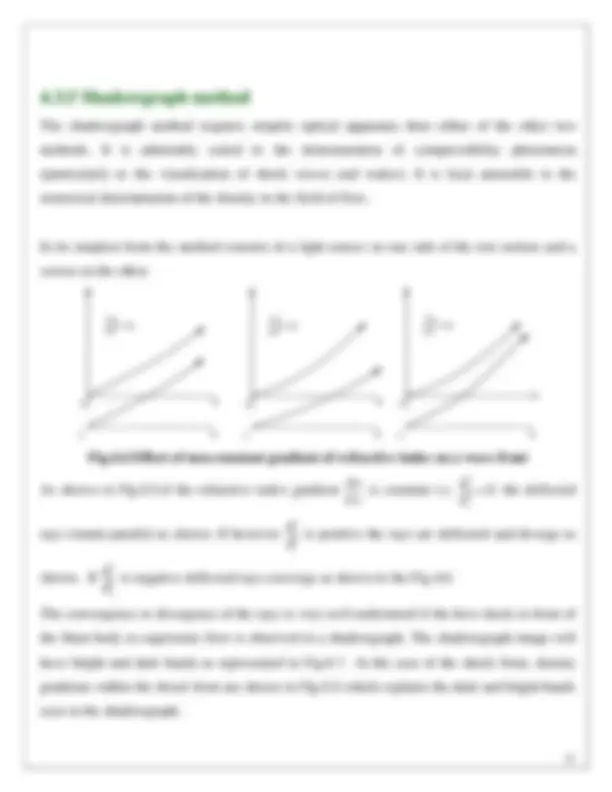
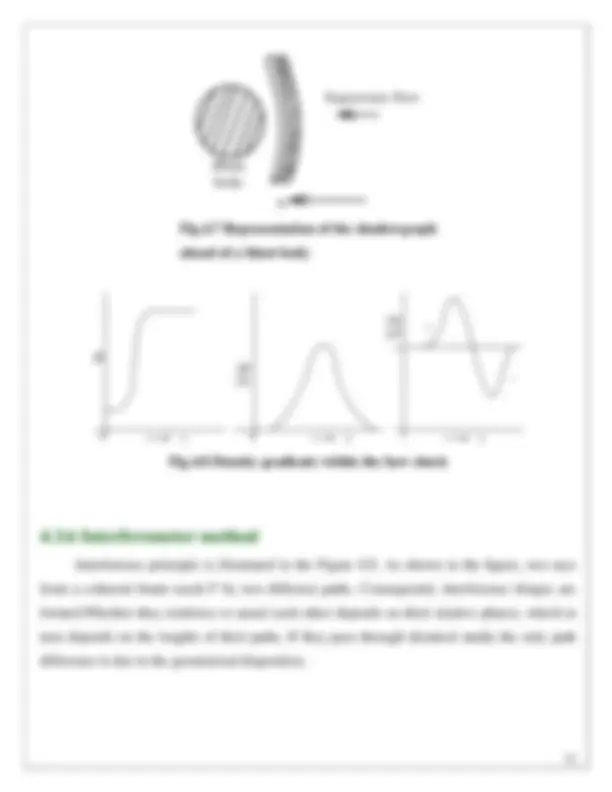

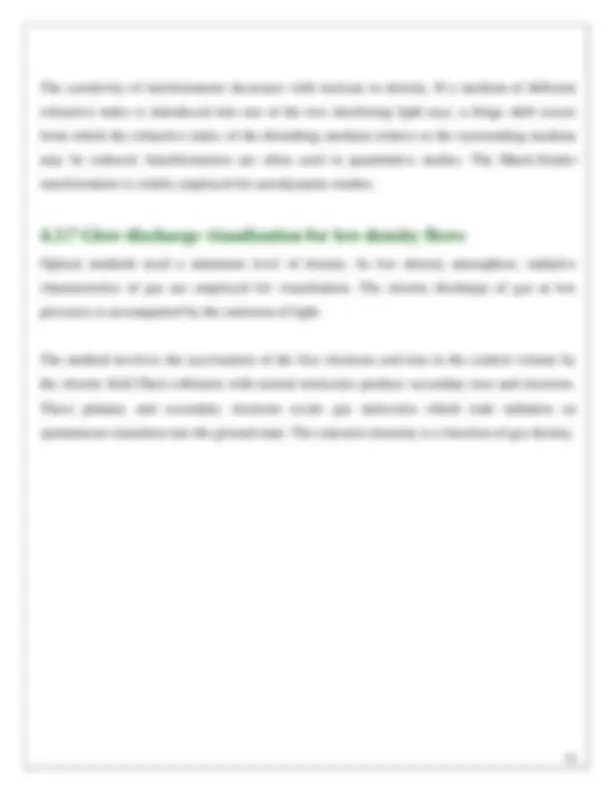
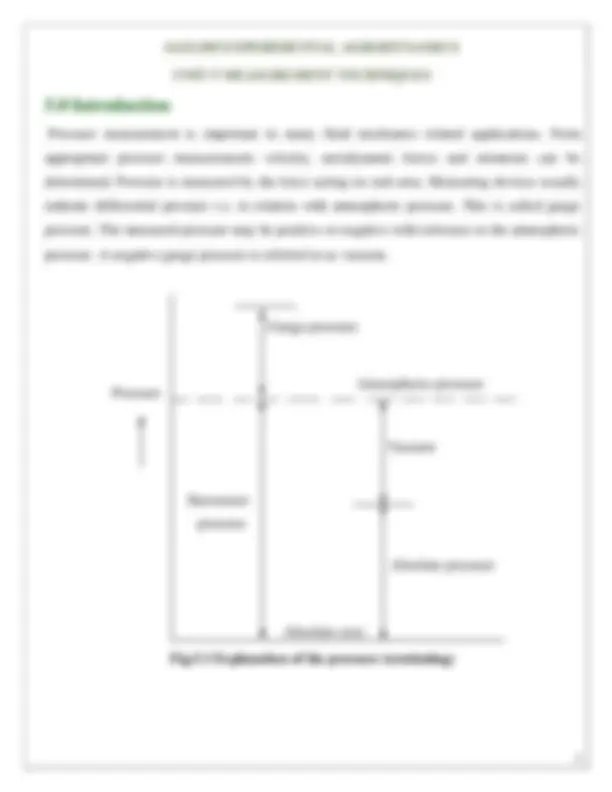
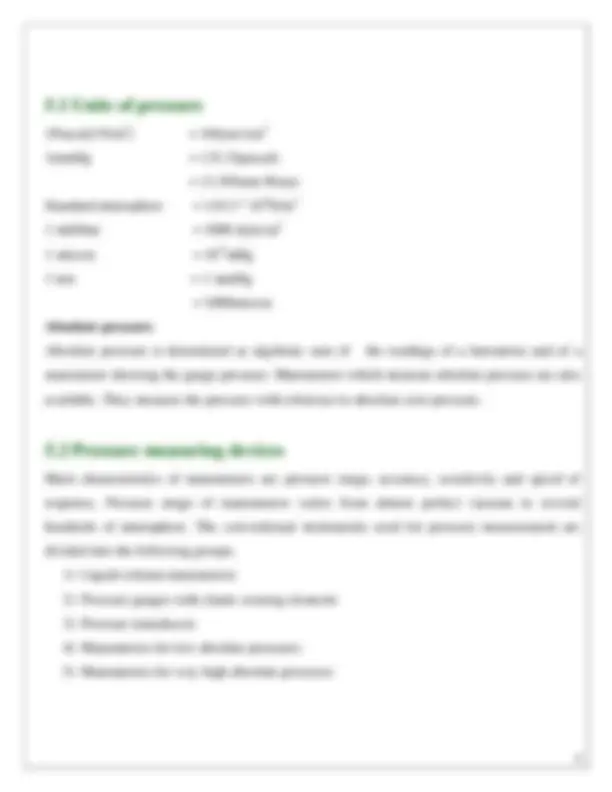
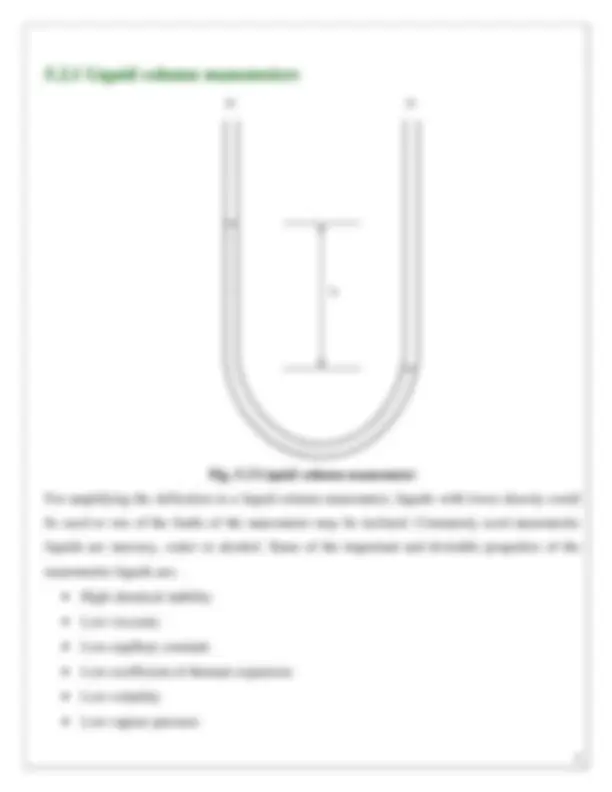
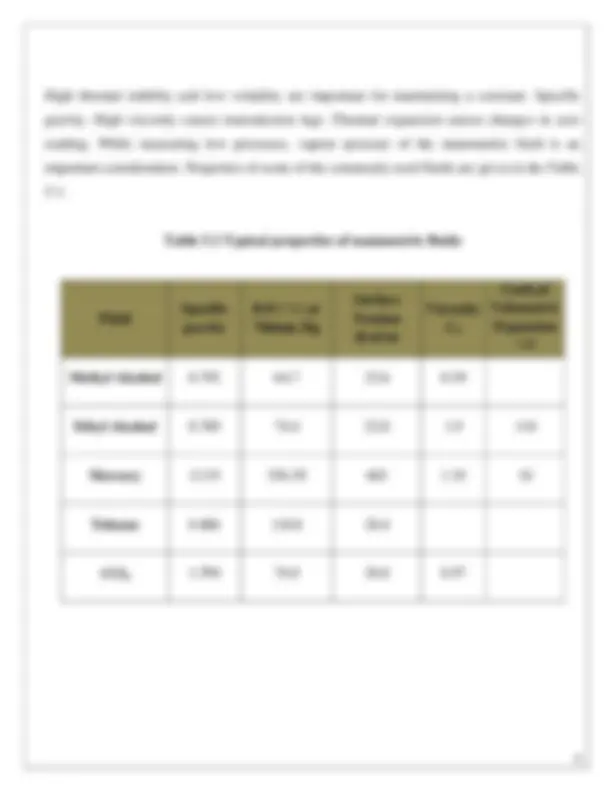
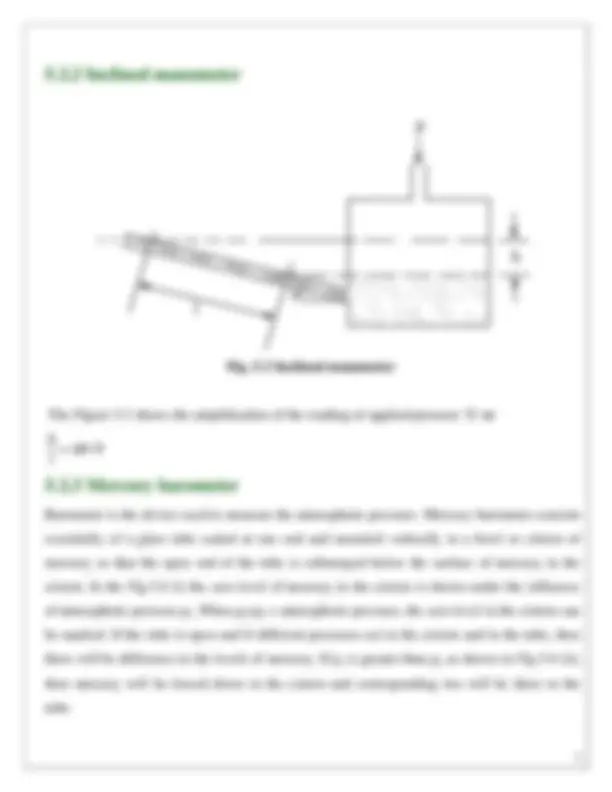
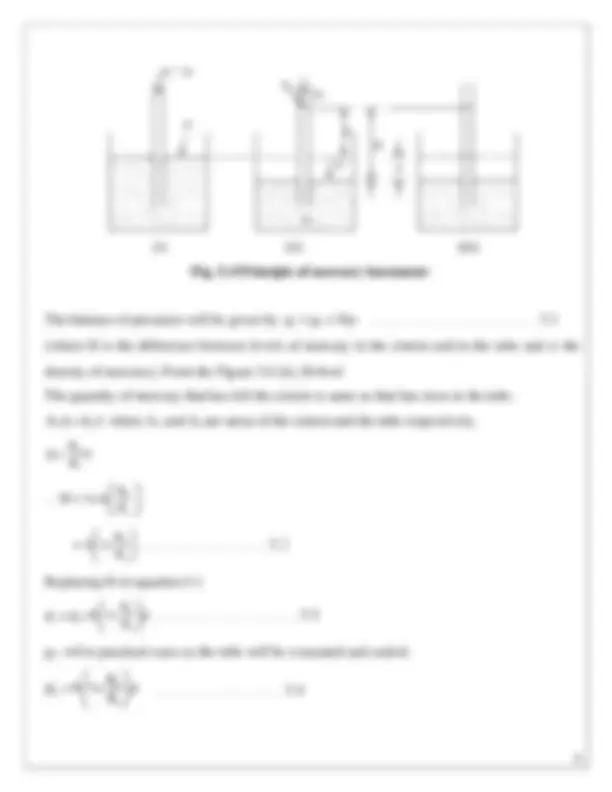
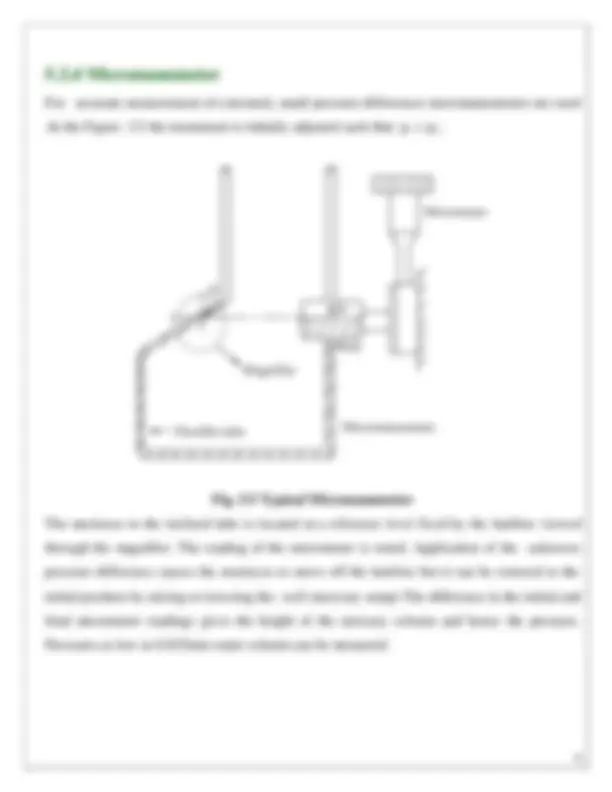
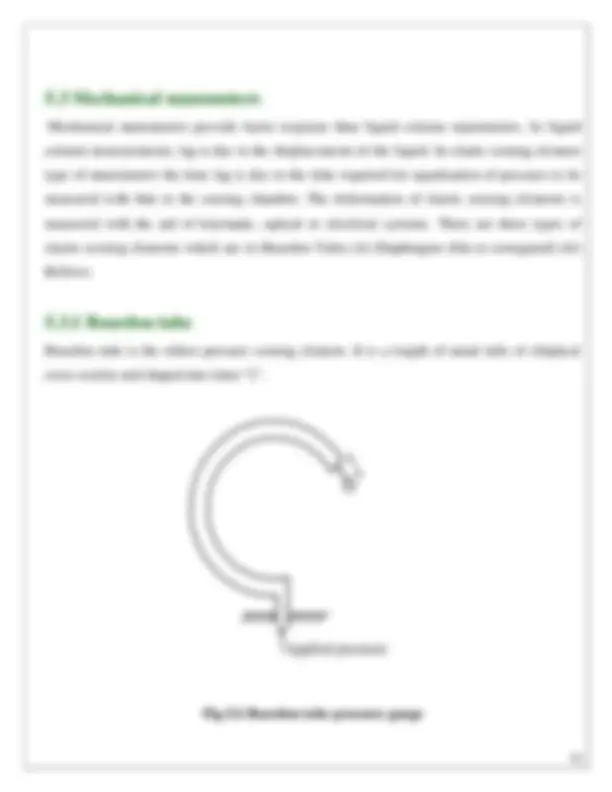
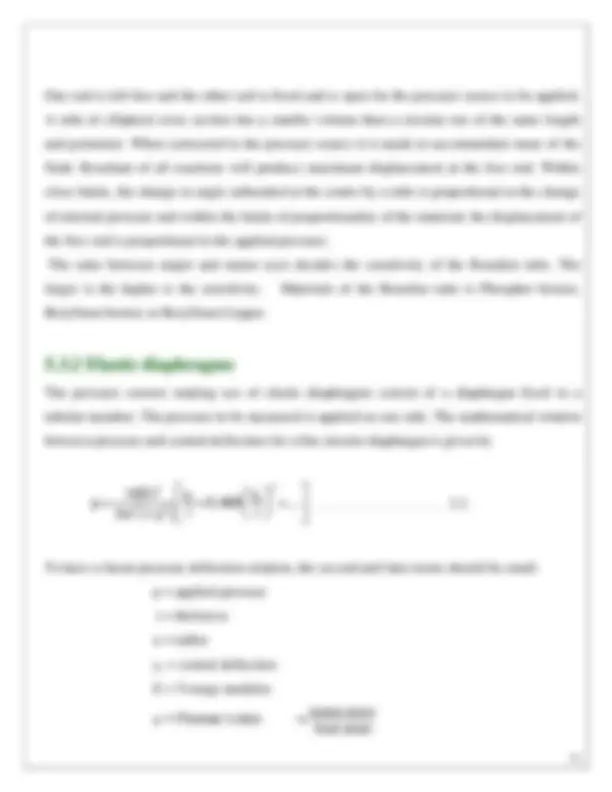
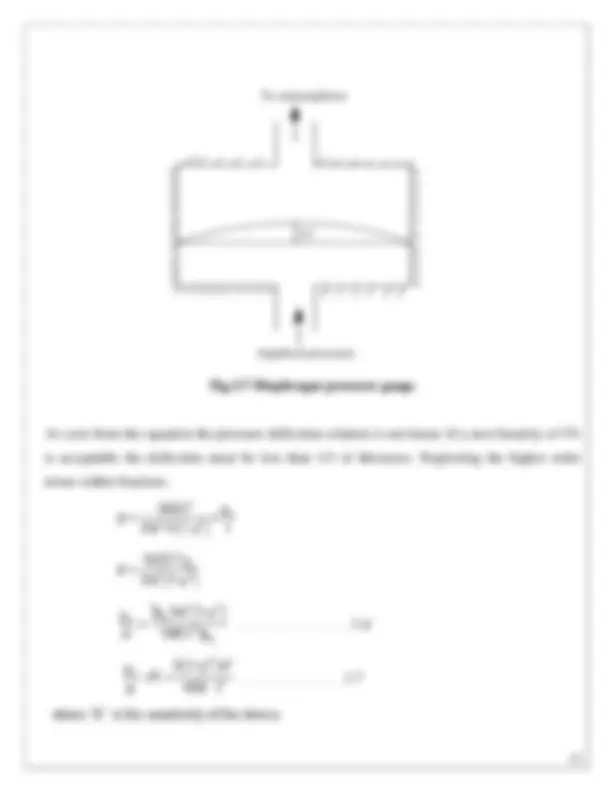
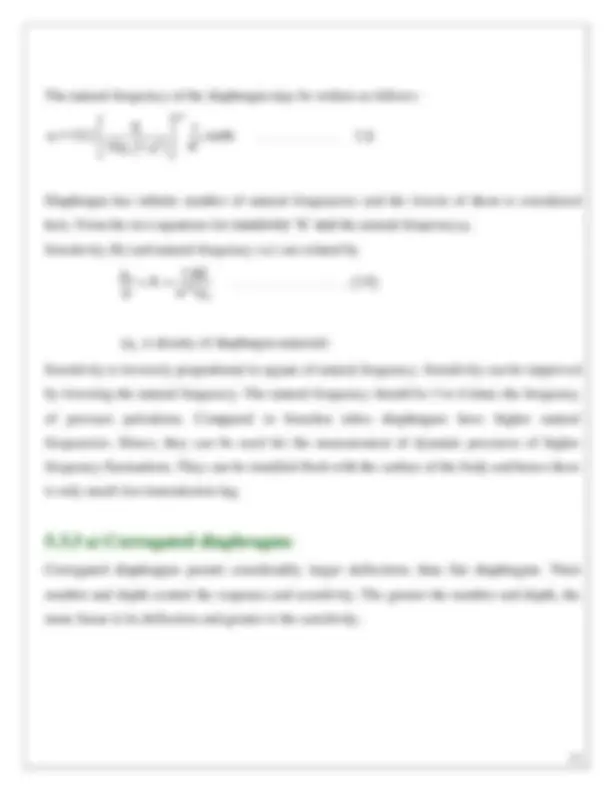
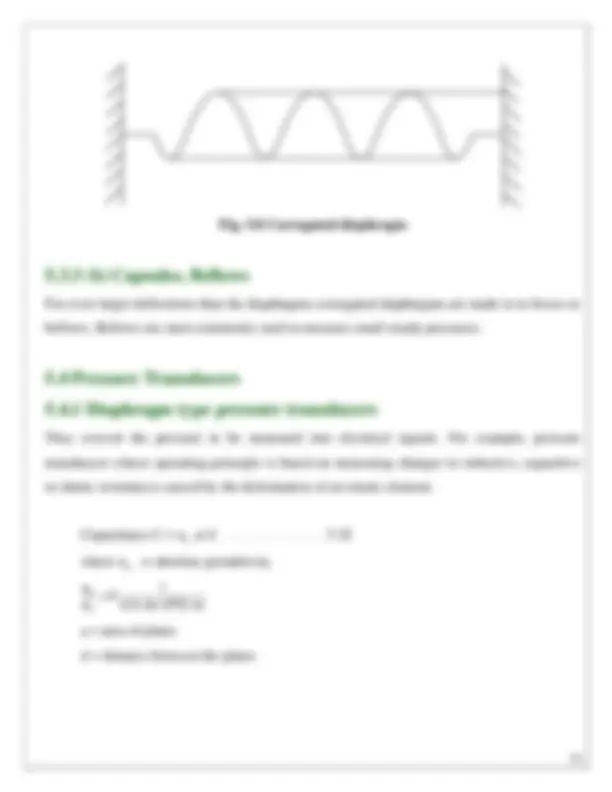
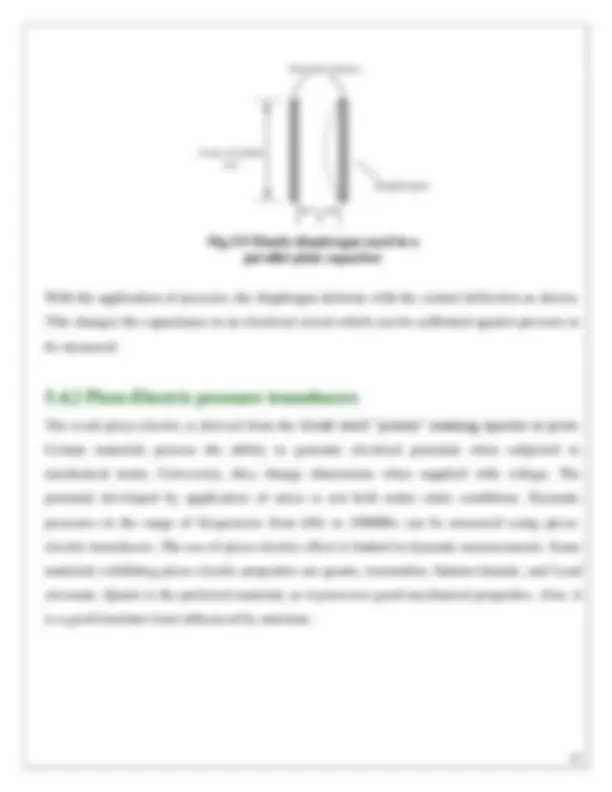
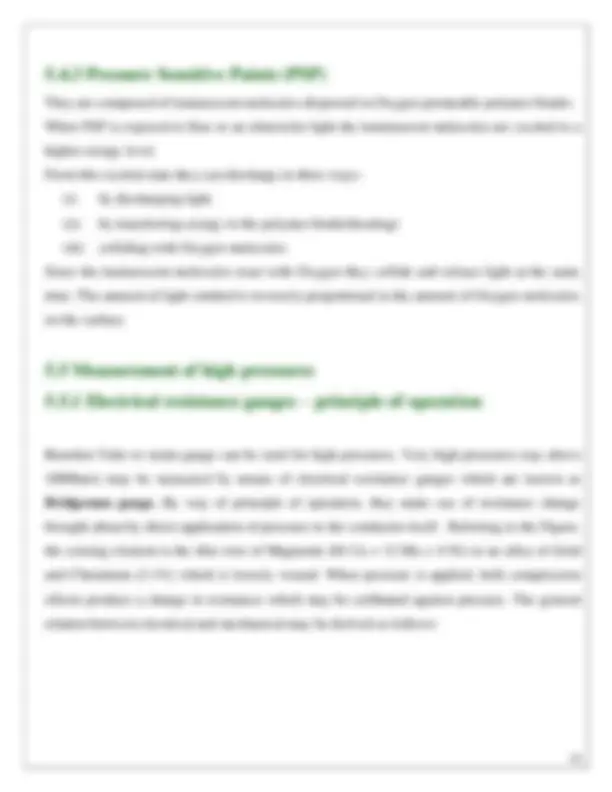
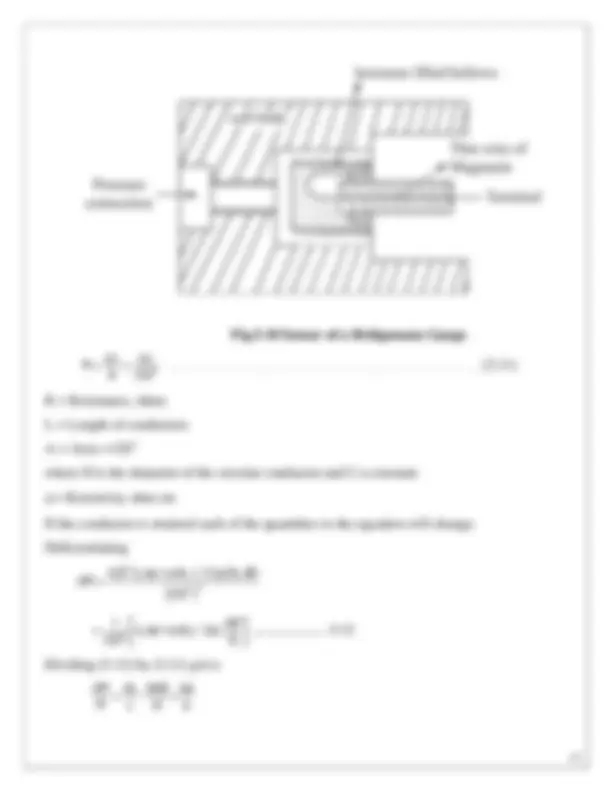
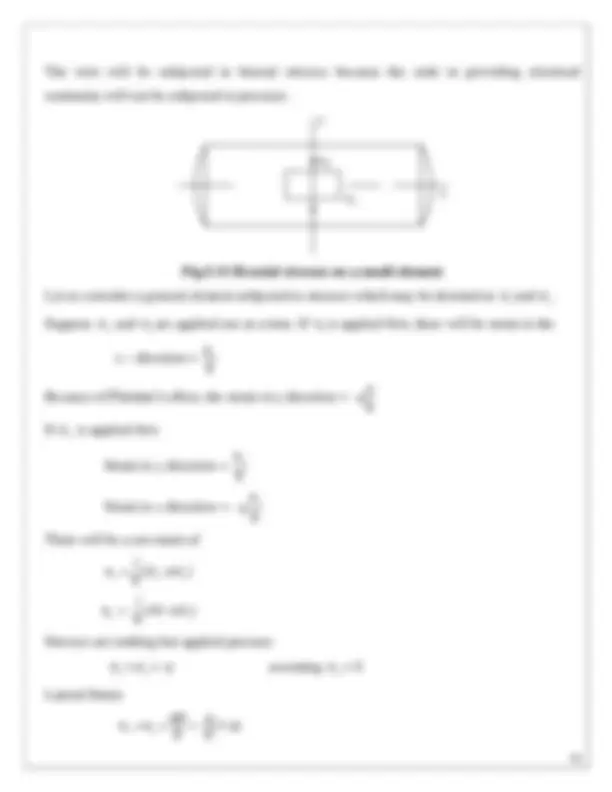
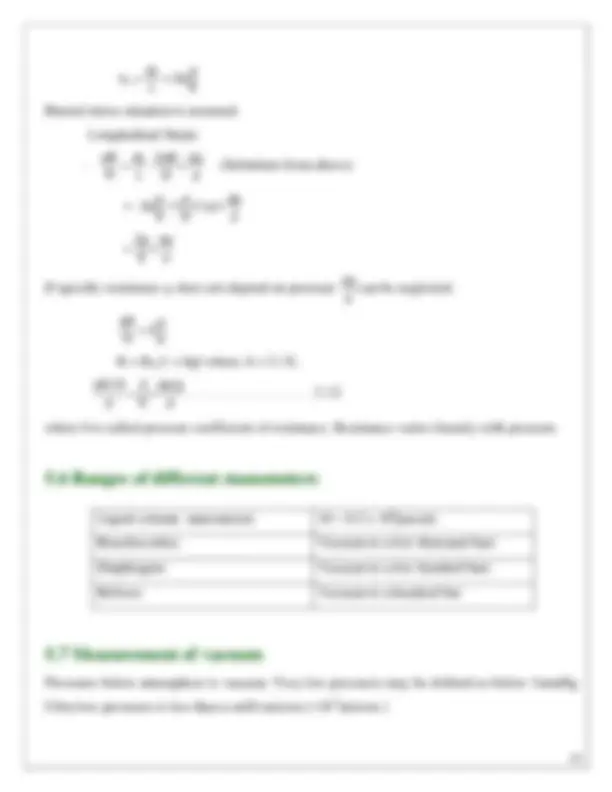
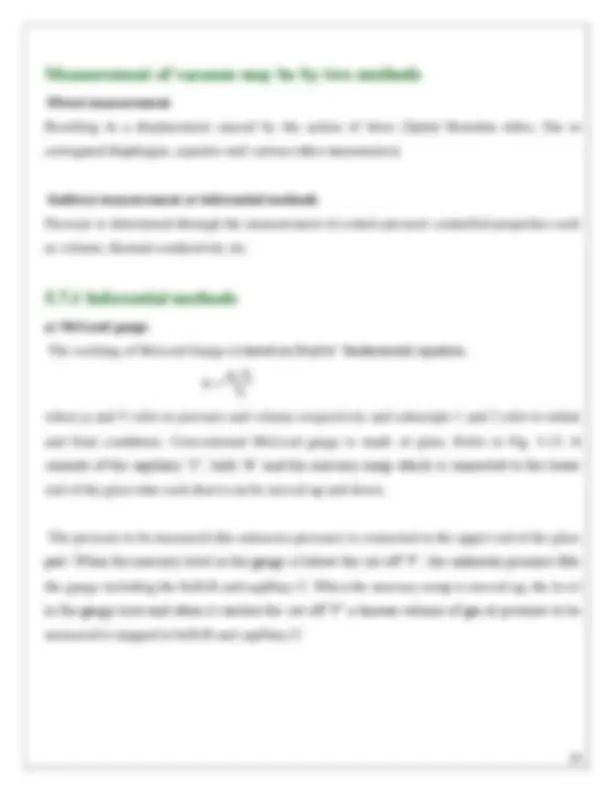
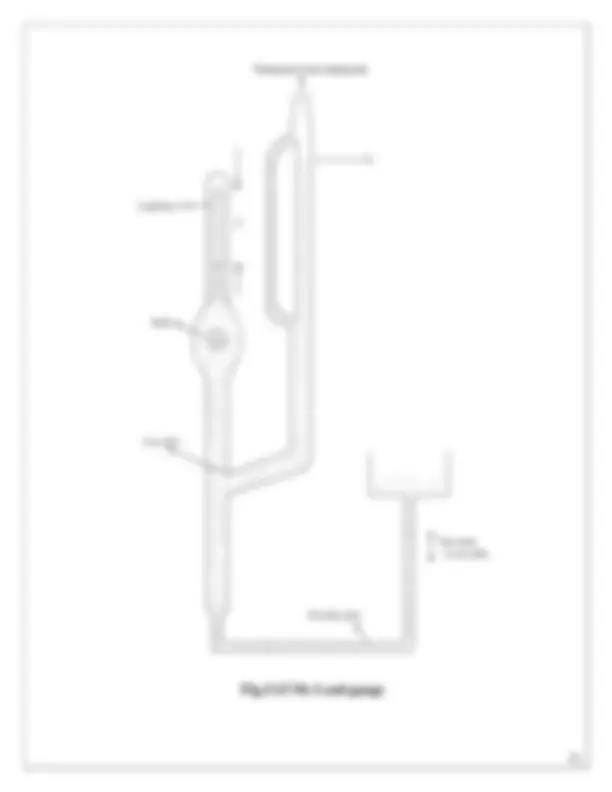
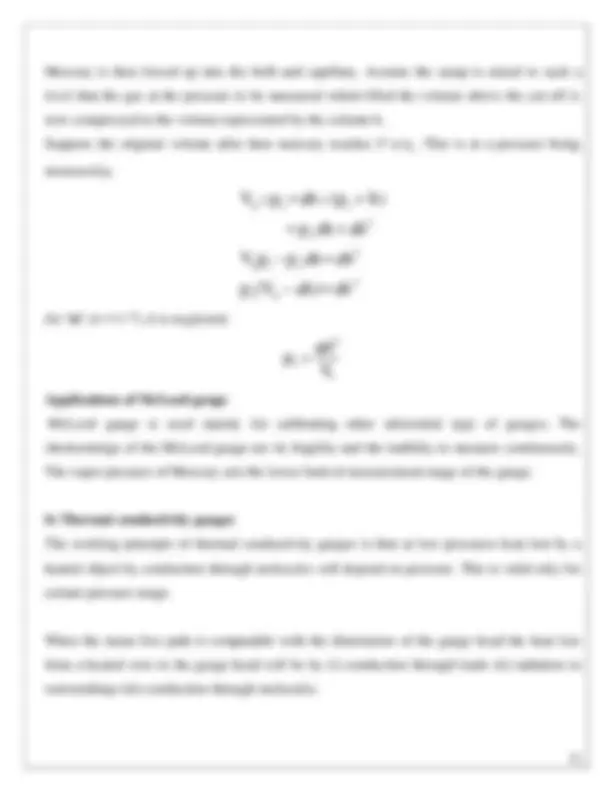
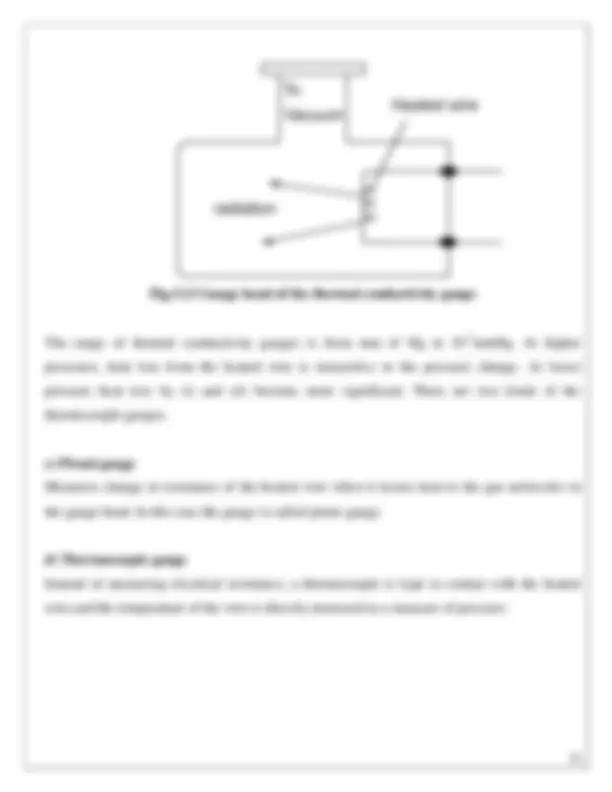
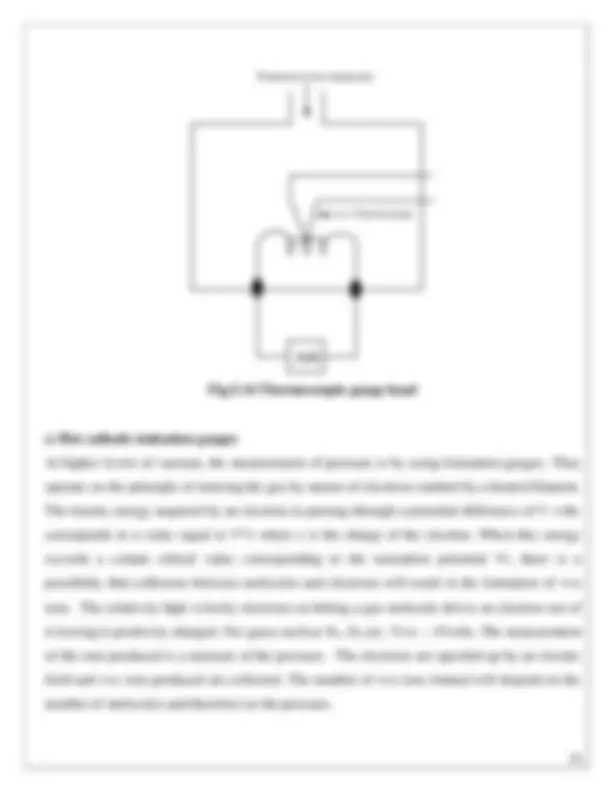
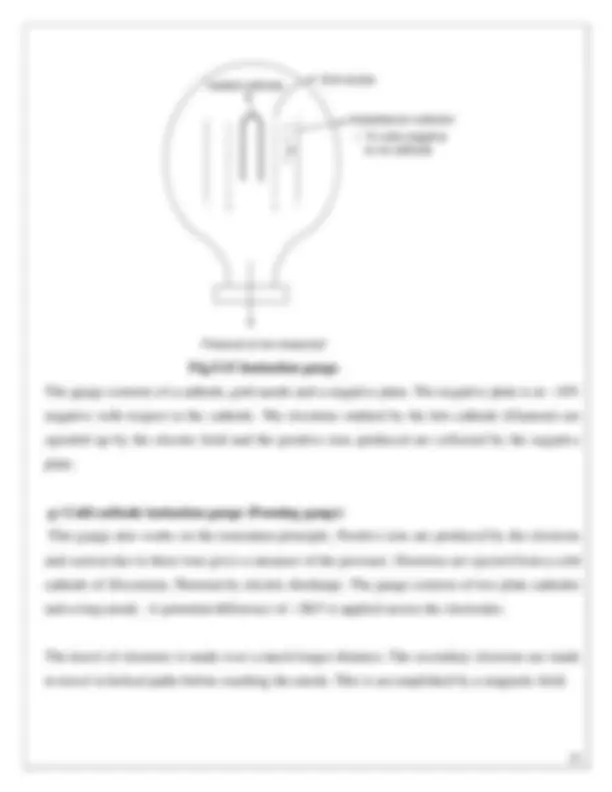
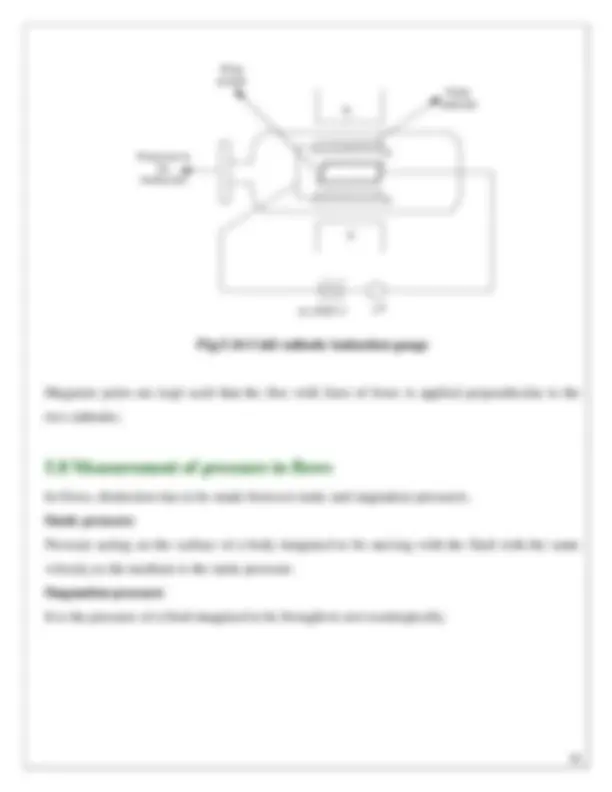
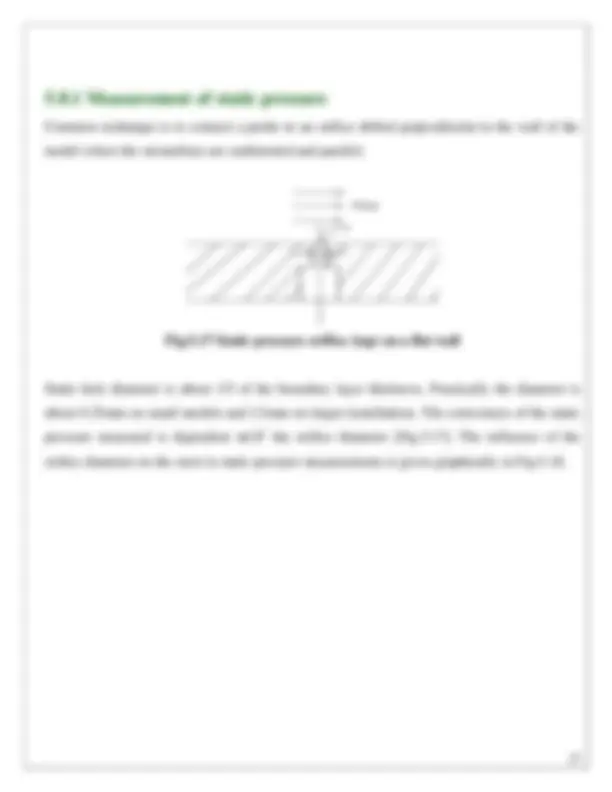
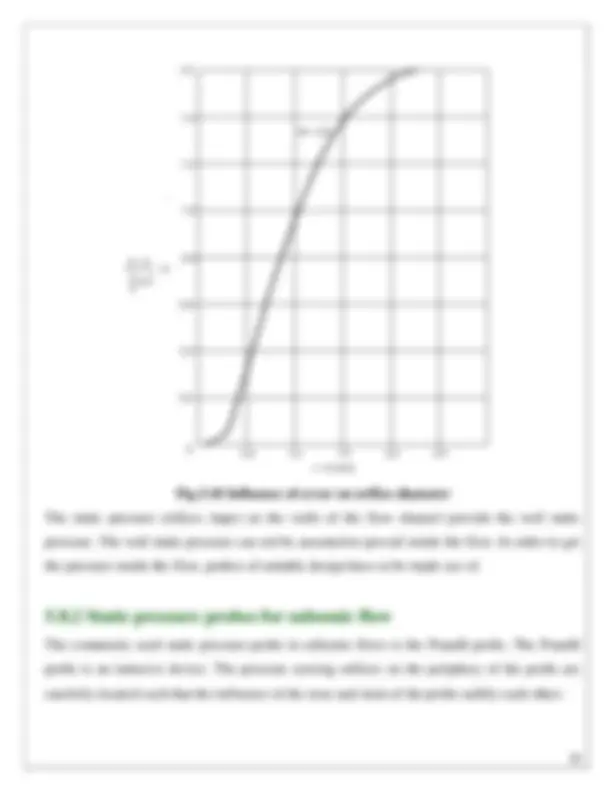
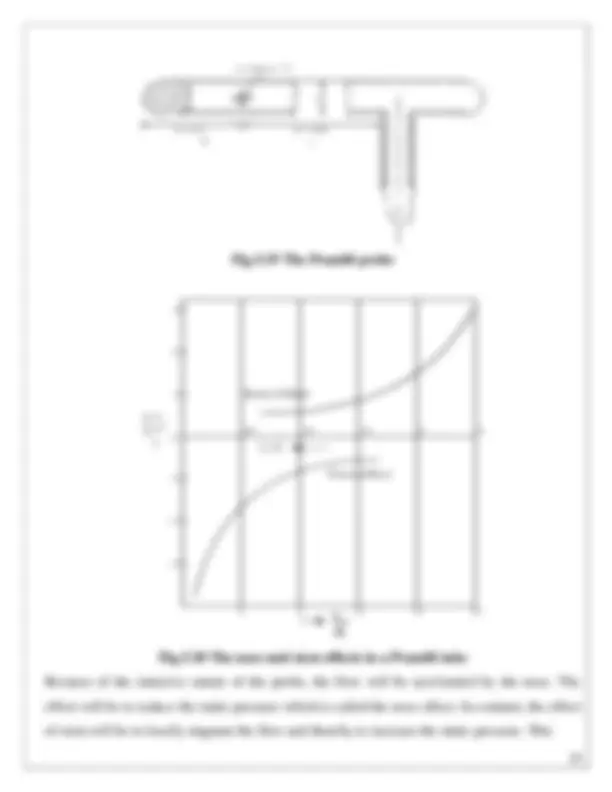
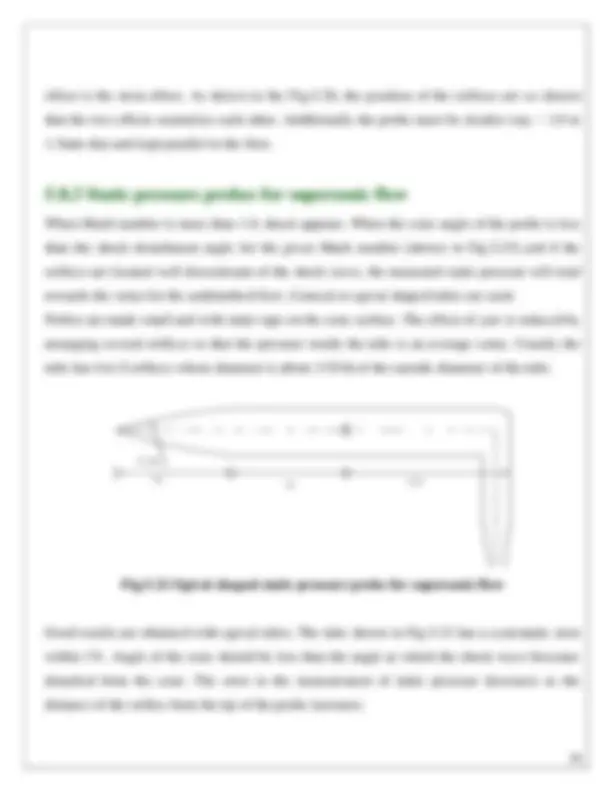
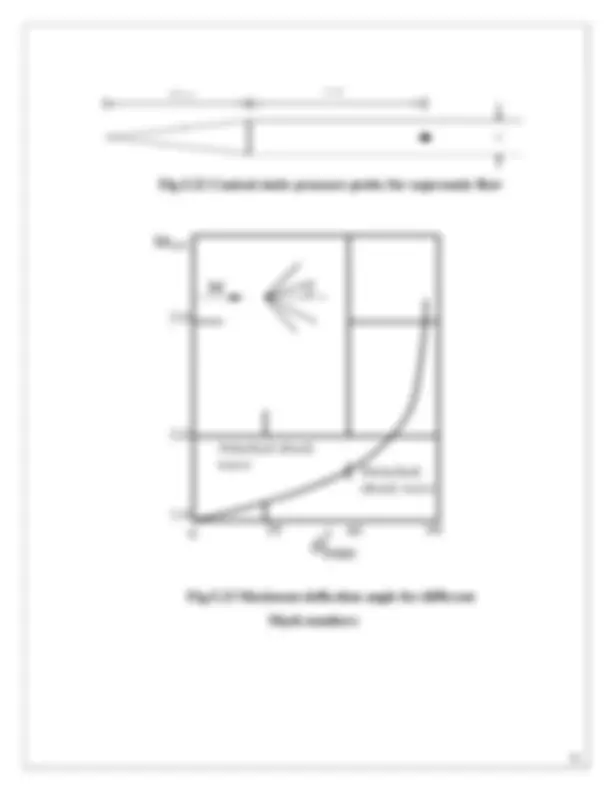
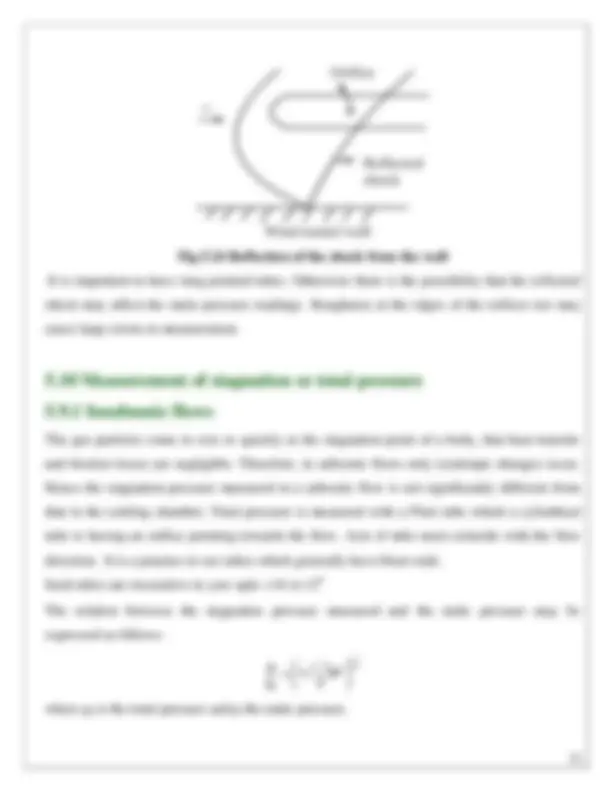
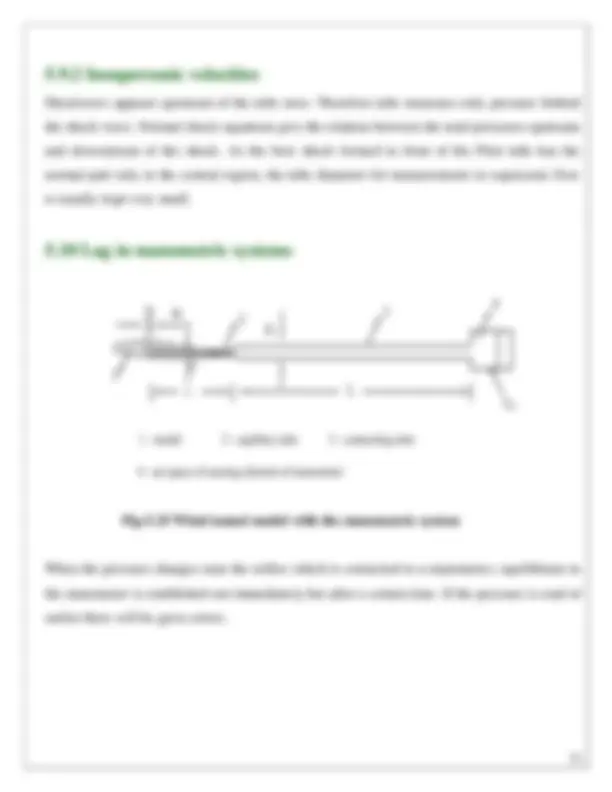
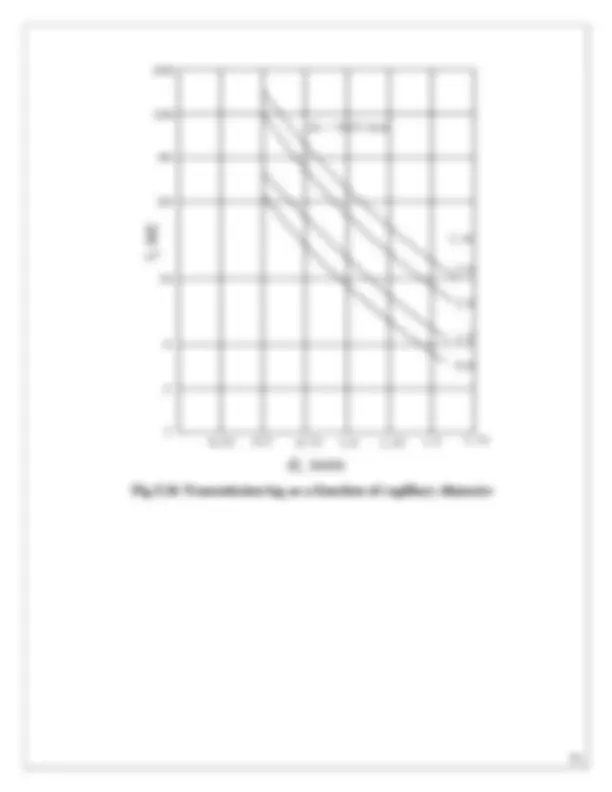
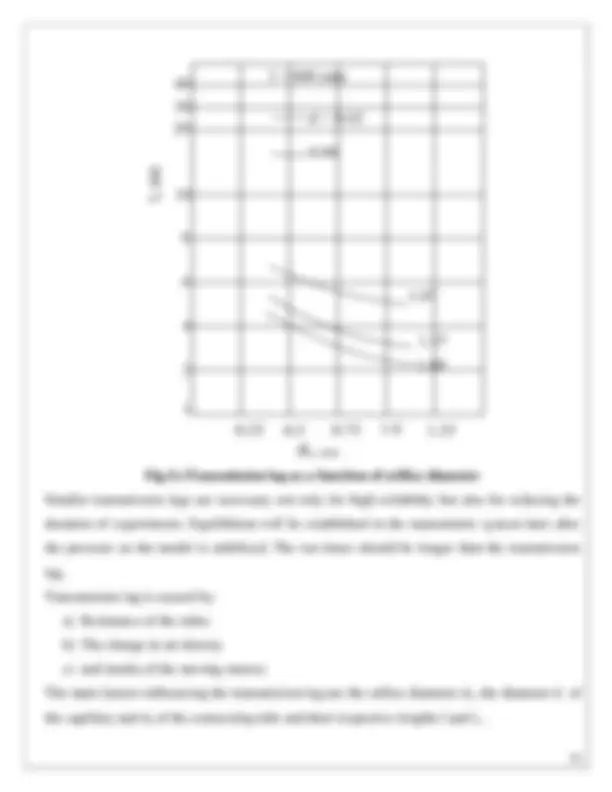
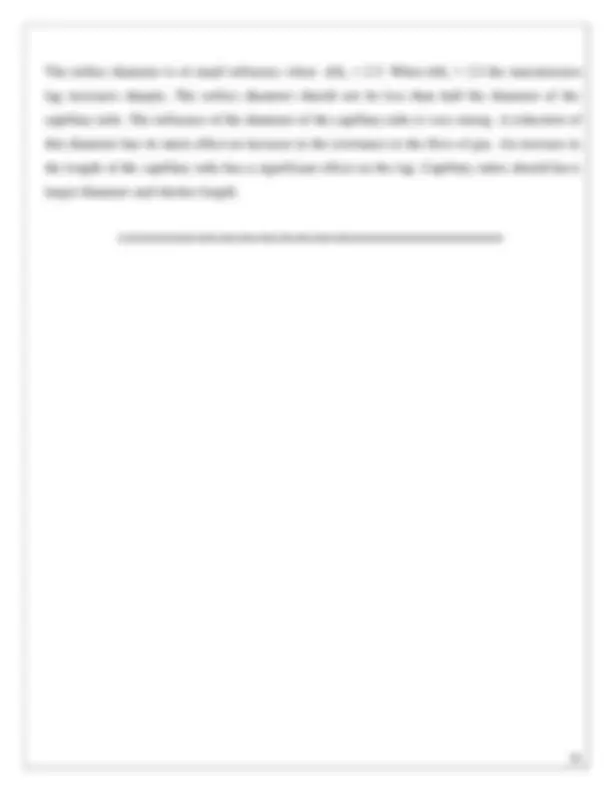
Study with the several resources on Docsity
Earn points by helping other students or get them with a premium plan
Prepare for your exams
Study with the several resources on Docsity
Earn points to download
Earn points by helping other students or get them with a premium plan
Community
Ask the community for help and clear up your study doubts
Discover the best universities in your country according to Docsity users
Free resources
Download our free guides on studying techniques, anxiety management strategies, and thesis advice from Docsity tutors
This document delves into the fundamentals of low-speed wind tunnels, exploring their classification, operational modes, and key characteristics. It examines the irregularities of flow in these tunnels, including spatial non-uniformity and loss of total head in the diffuser action. The document also discusses the concept of isentropic efficiency and its relevance to wind tunnel performance. It provides a comparison between different types of wind tunnels, including in-draft and pressure-driven designs, and highlights the importance of mach number and reynolds number in wind tunnel experiments.
Typology: Schemes and Mind Maps
1 / 88
This page cannot be seen from the preview
Don't miss anything!
Need of experiments (i) Theory is incomplete and needs to be supplemented. (ii) Information of fundamental nature needed in many areas. Experimental information towards solving aerodynamic problems could be obtained in a number of ways. Flight tests, rocket flights, drop tests water tunnels, ballistic ranges and wind tunnels are some of the ways by which aerodynamic data can be generated. With the help of well performed experiments even information of fundamental nature could be derived.
Majority of experimental data needed in aerodynamics is generated using wind tunnels. Wind Tunnel is a device for producing airflow relative to the body under test. Wind tunnels provide uniform flow conditions in their test section.
Wind tunnels may be classified based on any of the following: (a) Speed, Mach no They are classified as of low speed or high speed wind tunnels .In wind tunnel parlance, high speed wind tunnels are those operating at speeds where compressibility effects are important. They are also classified based on the Mach number of operation as subsonic, transonic, supersonic or hypersonic wind tunnels. (b) Mode of operation (Pressure storage, in-draft or Pressure vacuum type.) (c) Kind of test section (T.S) - Open, Closed or Semi enclosed
_1. Aerodynamic applications
Geometric similarity One of the most important requirements of models is that there should be geometric similarity between the model and the prototype. By geometric similarity it is meant that ratios of corresponding dimensions in the model and the prototype should be the same.
Dynamic similarity Equally important as the geometric similarity is the requirement of dynamic similarity. In an actual flight, when the body moves through a medium, forces and moments are generated because of the viscosity of the medium and also due to its inertia, elasticity and gravity. The inertia, viscous, gravity and elastic forces generated on the body in flight can be expressed in terms of fundamental units. The important force ratios can be expressed as non dimensional numbers. For example,
Knudsen number Kn = λ l is simulated in low density flows. In the definition above, is the mean free path and l the characteristic dimension.
Low speed wind tunnels may be of open circuit or closed circuit.
Figure 1.1 shows an open circuit low speed wind tunnel. After each run, the intake gets air fresh from the atmosphere. The effuser of the wind tunnel is the part of the wind tunnel from the beginning to the entry to the test section. The effuser makes the flow ready for the test section conditions. The test section provides the desired uniform flow conditions along and across the section. It is important that the test section conditions are controllable. Figure 1. shows a closed circuit wind tunnel. Losses in vorticity, eddies and turbulence are unavoidable in the tunnel circuit. If velocity is large, skin friction and losses due to obstacles will be correspondingly large.
Figure 1.1 Schematic of an open circuit low speed wind tunnel
Intensity of turbulence = ^ ^ 0 0 0
u (^) or v (^) or w (^) V V V where, V 0 is the mean of U, V, W
Scale of turbulence 0
L = (^) R dy y
where R is the coefficient of co-relation between the longitudinal component of turbulent velocity at A and that at another point B distant y from it.
y^ A^ B A B
R =^ u u u u
1
p -p 1/2ρv
where p 1 and p 2 are values of pressure up and downstream of the screen. K depends also on β,
Re, θ. Re the Reynolds number and θis the flow incidence angle measured from normal to the
screen βis the open area ratio and is defined as ^ d^2 β =^ 1-^ l ‘l’ and ‘d’ are marked on Figure 2.
pressure drop coefficient.
velocity regions where the Re is the least. Effect of screen on turbulence depends on K, the
keeping the screens at the beginning of the tunnel circuit is to ensure that they are at the low
screens. The eddies are practically absent when the Re is < 40.One of the important reasons for
The scale of eddies depends on the flow Re based on wire diameter of the flow through the
intensity.
down to smaller ones and the smaller ones decay rapidly. Multiple screens reduce turbulence
usually made of metal, nylon or polyester. With the use of screens, larger eddies are broken
mesh size are used. They are kept as far upstream of the test section as possible. Screens are
Use of wire meshes (also called as gauzes or screens) is very common. Screens of very fine
Effect of screens on turbulence
Fig.1.3 Mesh size of screens
According to Mehta and Bradshaw If K = 2, turbulence is absent. According to Collar and Batchelor, if U+u 1 is the longitudinal velocity far upstream of the screen and U+u 2 the corresponding value far downstream, hence
2 1
u 2 K u 2 K
Fig.1.4 Honeycombs with different cell cross sectional shapes
and reversed if K is greater than 2.0.
so that non-uniformity is removed by a screen whose pressure drop coefficient K is equal to 2.
2 2 2 a = Δv v is the fractional variation of velocity at the exit of the contraction
1 2 n =^ A (^) A is the
contraction ratio.
12 22 1 2
2 2 1 1 1 2 2 2
1 2 2 1
Δv = Δ v v v
1 2 2 2 2 2 2 2 12 2
v 2 dp d ^2 + (^) ρ = 0
This implies that for a decrease of kinetic energyd ^ v 22
per unit mass, there is a
corresponding increase in pressure energy. The pressure gradient in a subsonic diverging passage is adverse. It is difficult to avoid boundary layer thickening and flow separation. Hence, the conversion of kinetic energy into pressure energy is never fully efficient.
as follows:
8.0 degrees. The Bernoulli’s equation written in differential form in the context of a diffuser is
wind tunnels, the diffusers are diverging passages with a semi divergence angle of about 7.5 to
the test section as pressure energy. A well designed diffuser does this efficiently. In subsonic
The diffuser in the wind tunnel serves the purpose of salvaging the kinetic energy of flow in
The efficiency of the diffuser is best understood in physical terms when the efficiency term is included in the Bernoulli’s equation as below: 2 D η dv^ + dp= 0 2 ρ
^ where ƞD is the diffuser efficiency
Pressure changes in expanding passages may be examined by referring to the Fig.1.6 to elucidate the statement above.
Fig.1.6 Exit pressure profile of jet through different passages
There are two definitions of diffuser efficiency (a) Polytrophic efficiency (ƞD)
D 2 1 12 22
η = p -p (^1) ρv - 1 ρv 2 2 Use continuity equation to write the above equation as
Overall pressure ratio^01 2 2
p (^) =H (^) p p. Here p 2 corresponds to the pressure at the exit of the diffuser
and H represents the stagnation pressure p 01 at the entry to the wind tunnel.
2 /^ - 1 21 1 2 1 σ
H (^) × p =^ 2+^ -1 M p p 2+ -1 M η
Fig.1.7 Diffuser efficiency as a function of diffuser angle
Losses are due to: Inefficiency of drive unit Skin friction, separation etc Loss of kinetic energy at the diffuser exit Shocks in the case of supersonic wind -tunnels Losses due to skin friction
Local coefficient of skin friction =^ Frictional force (^12) 2 ρv A where, A’ is the surface area of the solid boundary which is subjected to frictional force.
ΔH = Cf 1 ρv^2 LdS
Integral is taken over the length of the duct. L is the perimeter, ds is an element of length in the direction of flow. A is the cross sectional area and Cf depends on nature of the boundary layer, Reynolds number and on the surface nature.
Losses due to resistance in the wind tunnel circuit Corner vanes, gauzes and screen offer resistance
Resistance Coefficient C = 2
2 2
Resistance force (^) = ΔH (^1) ρv A 1 ρv 2 vA = constant v = constant A 2 ΔH α C A^ ,^ which shows that the power loss is less for large areas.
Power Factor is defined as
3 λ = Power Input^ = P Rate of flow of kinetic energy in the test section (^1) ρv A 2 where P is the power input. Of the power P, only ηPis communicated to the air stream where
η is the efficiency of the drive unit (fan efficiency).
3
ηP = losses in the wind tunnel.
Reciprocal of the power factor is an alternative measure of the efficiency of the system.
(^20 ) 0 α μ a p
0 p α 1 p Power is inversely proportional to p^0.
Objections to power economy by pressurization
Aerodynamic forces on the model are proportional to^12 ρv 2 ^ ^21 p M^2
which for given M is proportional to p 0
For a given pressure μ a^20
p α
At constant temperature ^ 3 3/ a 0 α (^) M
3 R T*^ 3/ a = (^) M
μ 0 falls as the number of atoms in a molecule increases. = 2n+ 2n+1 where n is the number of atoms in the molecule. falls when n increases. 20 1/ 3/ p α μ M
Power economy can be achieved by working fluid of higher molecular weight.
Limitations Complete dynamic similarity can be got with only the same . Boiling point of higher molecular weight fluids is high. Hence, to keep the working fluid in gaseous state, the temperature should be high.
Table 1.1 Power required with a different working substance T 0 = 288 K
Fluid
Boiling Point K
Power relative to air
Air 90 a0 SF6 / a0Air = 0.395μ
μ0SF6/ μ0Air =0.
The Table 1.1 above shows that the power required when SF 6 is used as the working fluid is only 1/50 of that while using air.
For a given working fluid, p 0 , , M and Re. P α μ a^20
a 0 α T 0 1/ 0 3/ μ 0 α (^) T0ref T+C C is a constant.
0 9/ 0ref^2
P α^ T T +C
Objections Reducing stagnation temperature brings down the flow temperature too. Boiling point is one consideration. Severe metallurgical problems at low temperatures.
Indraft wind tunnels Pressure driven wind tunnels Stagnation temperature at supply condition is constant during a run. So also is total pressure. No fluctuations as those generated by a pressure regulator.
Reynolds number can be varied at a particular Mach no.
No possible contamination such as that due to oil.
Cost is much less than of an indraft tunnel. Vacuum is safer to handle than pressure. Pressure regulators are not needed.
Fig 3.2 Indraft type wind tunnel
Table 3.1 Comparison between Indraft and Pressure driven wind tunnels
between blow down and continuous wind tunnels are as given in Table 3.
The wind tunnels described above can be converted as continuous tunnels. The comparison
Intermittent(blow down) wind tunnels Continuous wind tunnels
Simple to design and less costly
More in control of conditions and return to a given test condition with more accuracy. A single drive may run several Tunnels
Check points are easily obtained No panic of rapid testing
Model testing is more convenient Test conditions can be held constant for a longer time. Extra power is available to start Failure of model will not result in tunnel damage
The local dynamic parameter 12 ρv^2 can be related to the local Mach number and static
pressure.
Table 3.2 Comparison between intermittent and continuous wind tunnels
(i) Dynamic pressure
the nozzle exit is based on the method of characteristics.
section. The design of a suitably shaped nozzle contour to obtain the desired uniform flow at
of the nozzle. A well designed nozzle makes the flow parameters uniform across the cross
the desired Mach number is established. Mach number is uniquely determined by the area ratio
The nozzle regulates the speed of air entering the test section (T.S) of the wind tunnel so that
Introduction