
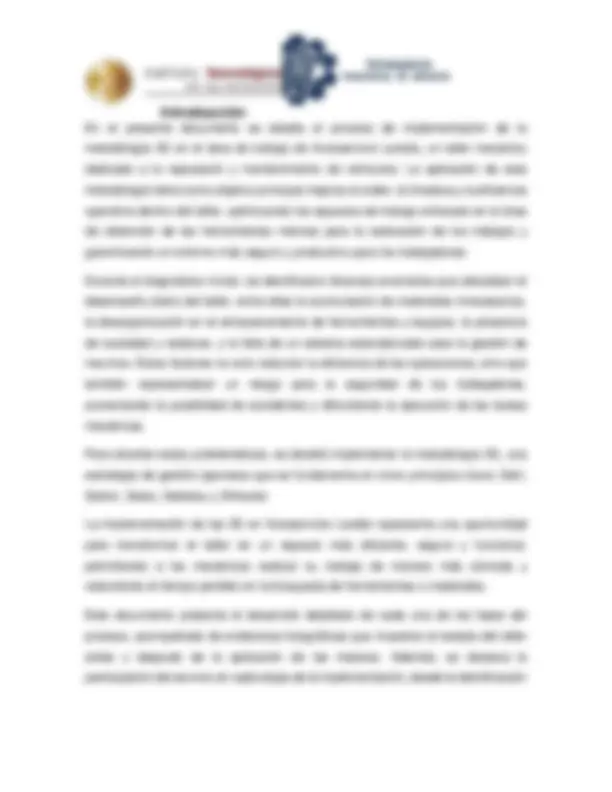
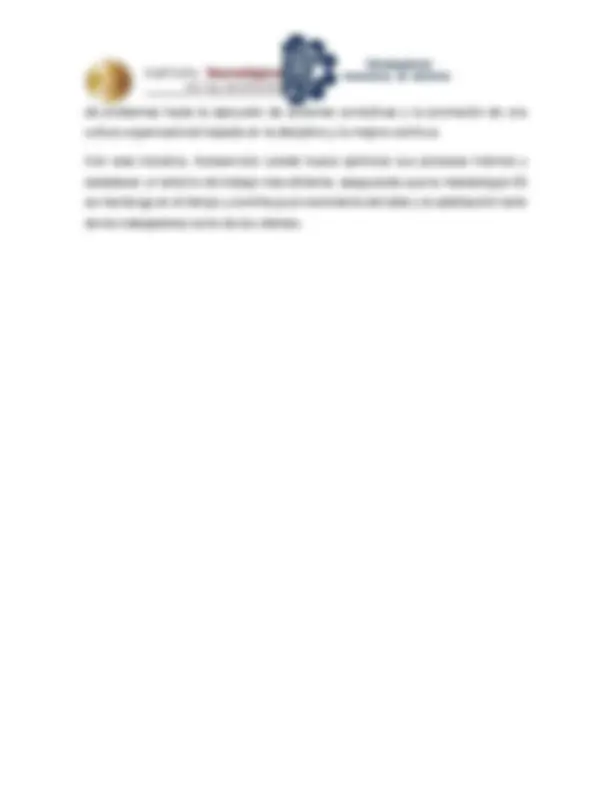

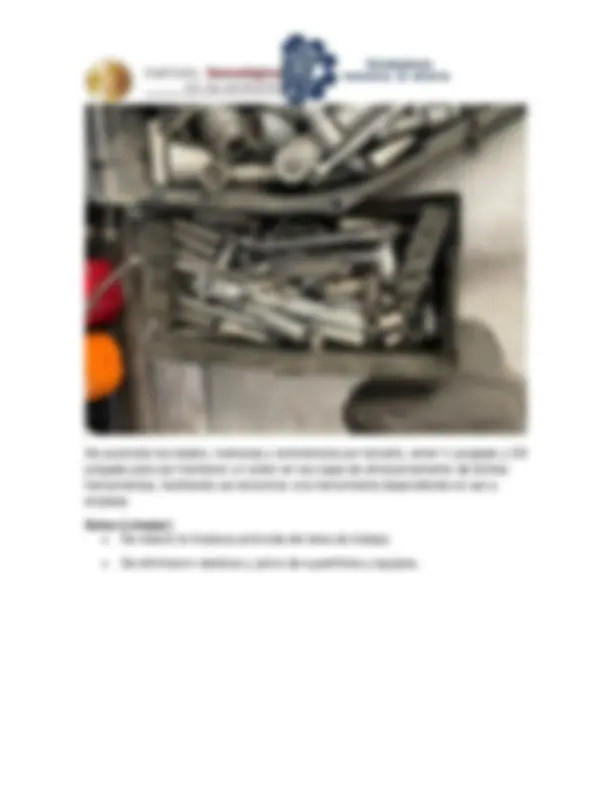
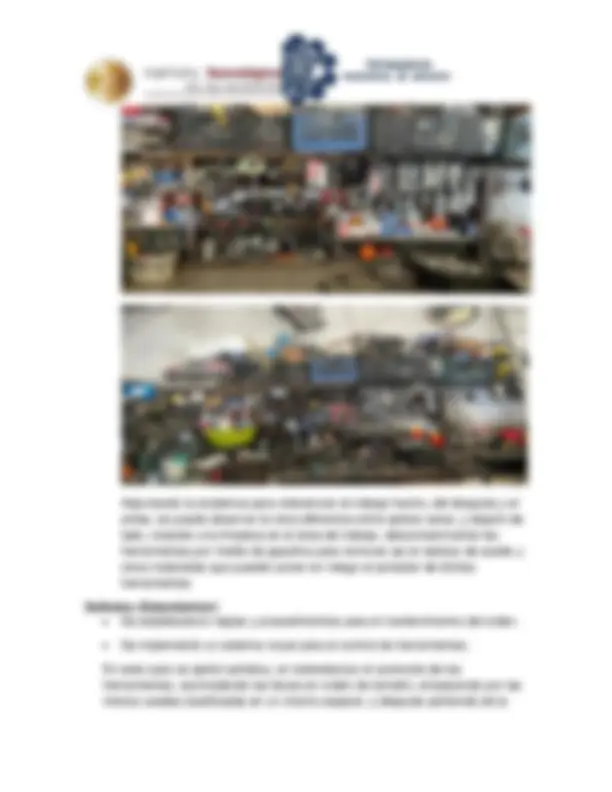
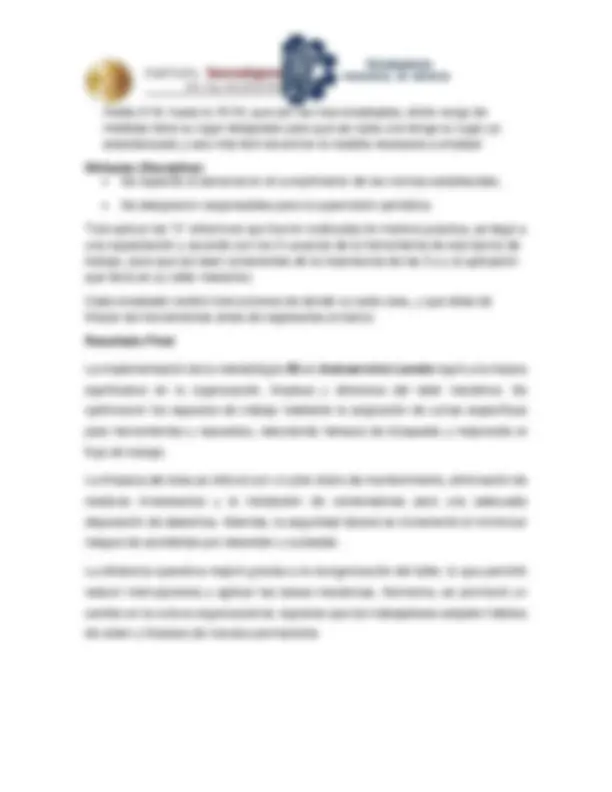
Study with the several resources on Docsity
Earn points by helping other students or get them with a premium plan
Prepare for your exams
Study with the several resources on Docsity
Earn points to download
Earn points by helping other students or get them with a premium plan
Community
Ask the community for help and clear up your study doubts
Discover the best universities in your country according to Docsity users
Free resources
Download our free guides on studying techniques, anxiety management strategies, and thesis advice from Docsity tutors
Un caso práctico de la implementación de la metodología 5s en un taller mecánico, autoservicio laredo. Se describe el proceso de diagnóstico inicial, donde se identificaron problemas como desorden, falta de organización y suciedad. Luego, se detalla la aplicación de cada uno de los principios de las 5s: seiri (clasificar), seiton (ordenar), seiso (limpiar), seiketsu (estandarizar) y shitsuke (disciplina). Se incluyen evidencias fotográficas que muestran el estado del taller antes y después de la aplicación de las mejoras. Finalmente, se destaca la participación del alumno en cada etapa del proceso y se analizan los resultados obtenidos.
Typology: Study notes
1 / 12
This page cannot be seen from the preview
Don't miss anything!
Docente: MAE. José Luis Lara Cruz Equipo G: Erick Eduardo Cardona Delgado 21150205 Carlos Brandon Estrada Mora 22151093 Andrea Cristina De La Cruz Hernández 23150919 Fecha: 06 / 02 /20 25
de problemas hasta la ejecución de acciones correctivas y la promoción de una cultura organizacional basada en la disciplina y la mejora continua. Con esta iniciativa, Autoservicio Laredo busca optimizar sus procesos internos y establecer un entorno de trabajo más eficiente, asegurando que la metodología 5S se mantenga en el tiempo y contribuya al crecimiento del taller y la satisfacción tanto de los trabajadores como de los clientes.
Diagnóstico Inicial Tras una evaluación del área de trabajo, se han identificado diversas anomalías que afectan la eficiencia operativa, la seguridad y la productividad. A continuación, se detallan los principales problemas detectados: Desorden y acumulación de materiales innecesarios Se ha observado que en el banco de almacen de las herramientas, que va de la mano con el área de trabajo hay una acumulación excesiva de materiales que no tienen un uso inmediato o que han quedado obsoletos. Esta acumulación no solo ocupa un espacio valioso, sino que también dificulta el acceso a los elementos realmente necesarios para las operaciones diarias. Además, la presencia de materiales en exceso puede generar riesgos de seguridad, como tropiezos o caídas, y afectar la circulación dentro del área de trabajo. Falta de organización en herramientas y equipos Las herramientas y equipos utilizados en el área de trabajo no cuentan con un sistema de almacenamiento eficiente, lo que provoca pérdidas de tiempo al momento de buscarlos y dificulta su correcta conservación. La falta de señalización y de un lugar específico para cada herramienta genera confusión entre los trabajadores, incrementando el tiempo de ejecución de las tareas y aumentando el riesgo de accidentes debido a la manipulación inadecuada de los equipos. Presencia de suciedad y residuos Se detectó un nivel considerable de suciedad en las instalaciones, con acumulación de polvo, restos de materiales, empaques y otros desechos. La falta de limpieza y mantenimiento periódico no solo deteriora la imagen del lugar de trabajo, sino que también puede representar riesgos para la salud de los trabajadores, afectando la calidad del ambiente laboral. La acumulación de residuos en ciertas áreas también
Seiton (Ordenar)
Se acomodo los dados, matracas y extensiones por tamaño, entre ½ pulgada y 3/ pulgada para asi mantener un orden en las cajas de almacenamiento de dichas herramientas, facilitando asi encontrar una herramienta dependiendo el uso a emplear Seiso (Limpiar)
media 5/16, hasta la 15/16, que son las mas empleadas, dicho rango de medidas tiene su lugar designado para que asi cada una tenga su lugar ya estandarizado y sea más fácil encontrar la medida necesaria a emplear Shitsuke (Disciplina)
La implementación de la metodología 5S permitió optimizar el espacio de trabajo, mejorando la productividad y seguridad. Se recomienda continuar con auditorías periódicas para asegurar la sostenibilidad de los cambios realizados. La participación del alumno fue clave para el éxito del proyecto. Estas anomalías identificadas requieren una intervención inmediata para mejorar la eficiencia del área de trabajo. La implementación de metodologías de organización, como las 5S, puede ser una estrategia eficaz para abordar estos problemas, optimizar el uso del espacio y mejorar las condiciones laborales.
La aplicación de las 5S en un taller mecánico mejora la organización, seguridad y eficiencia en el área de trabajo. Al reducir el desorden y estandarizar procesos, se optimiza el tiempo, se minimizan riesgos y se eleva la calidad del servicio. Además, fomenta un ambiente más profesional y motivador para el personal. Para su éxito, es clave el compromiso continuo y auditorías periódicas. En resumen, las 5S generan un impacto positivo en la productividad y satisfacción tanto de trabajadores como de clientes.
Las 5S son una metodología que busca mejorar la organización y eficiencia en el trabajo a través de cinco principios: Seiri (Clasificar), Seiton (Ordenar), Seiso (Limpiar), Seiketsu (Estandarizar) y Shitsuke (Disciplina). Son importantes porque aumentan la productividad, reducen riesgos laborales y mejoran el ambiente de trabajo.
Personalmente, creo que aplicar las 5S va más allá de mejorar la apariencia del lugar; se trata de cultivar una mentalidad orientada a la excelencia y al trabajo en