
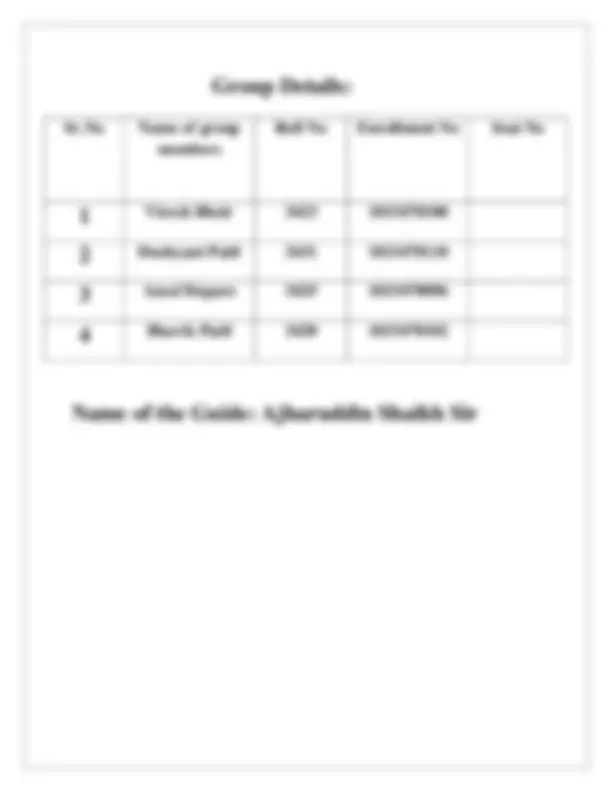
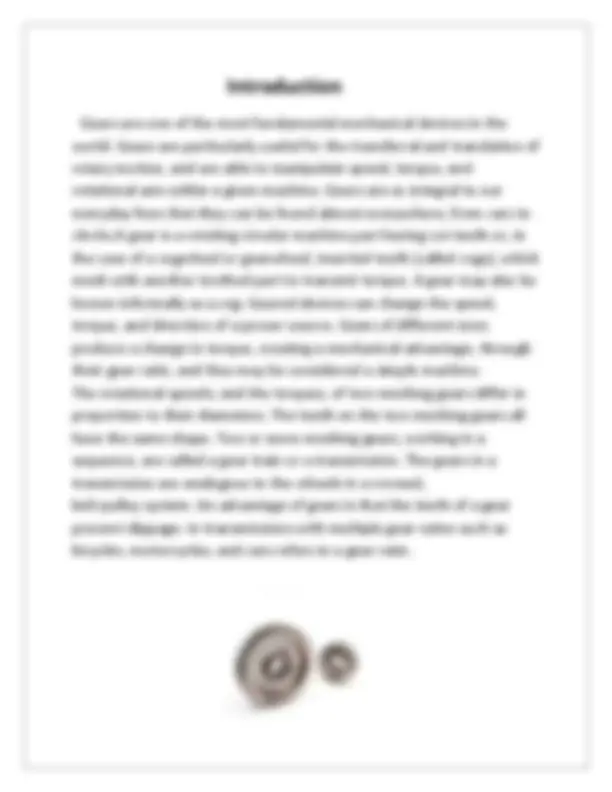
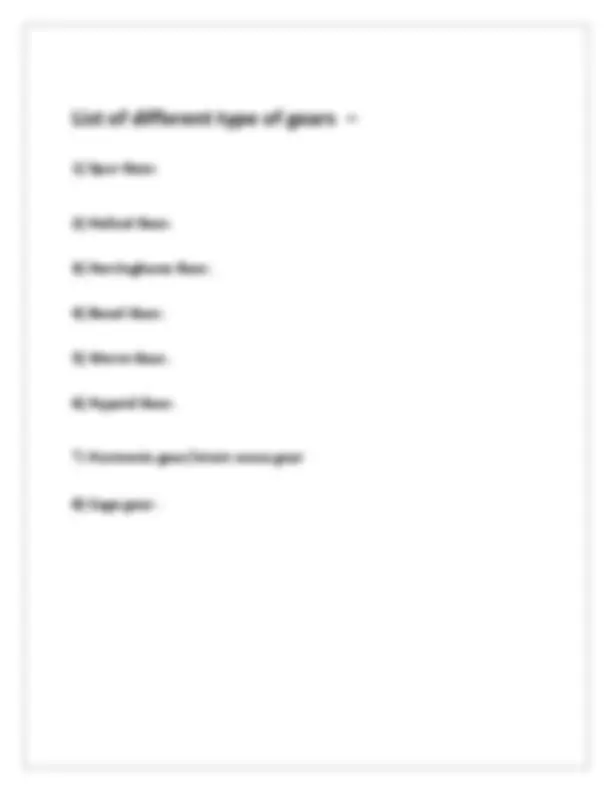
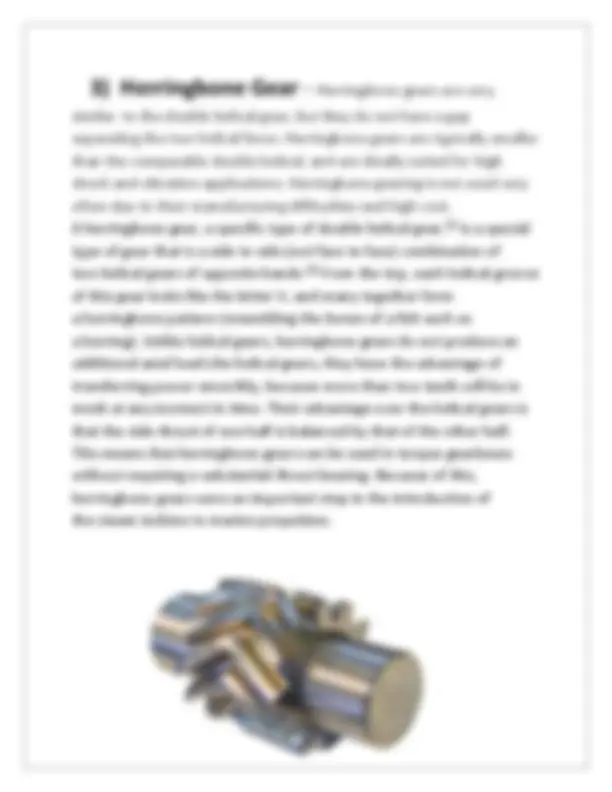
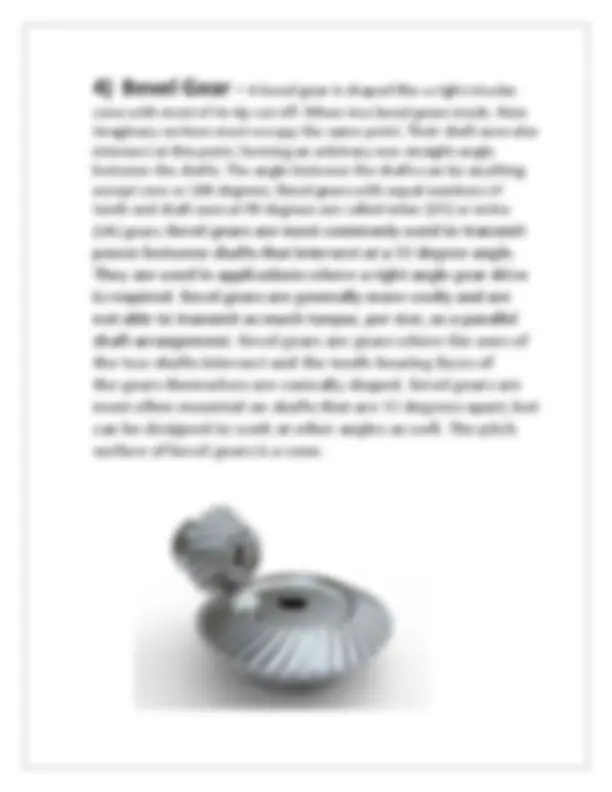
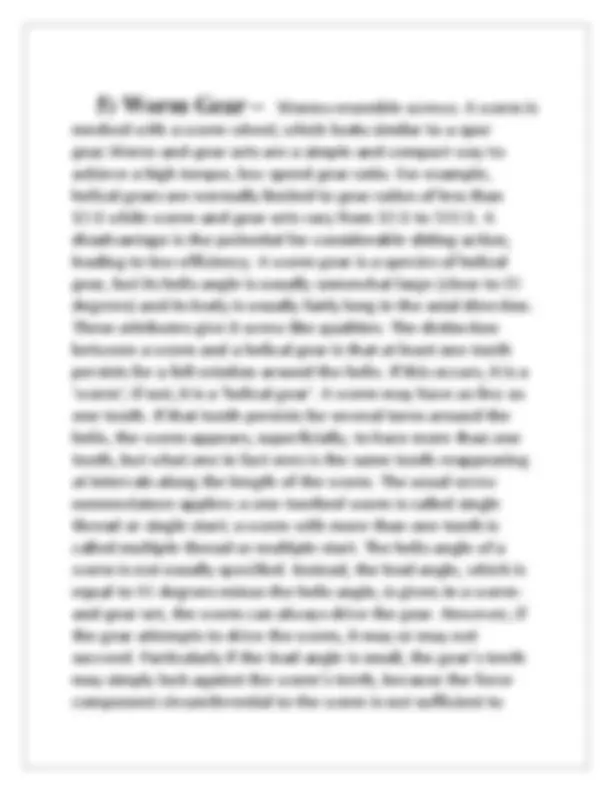
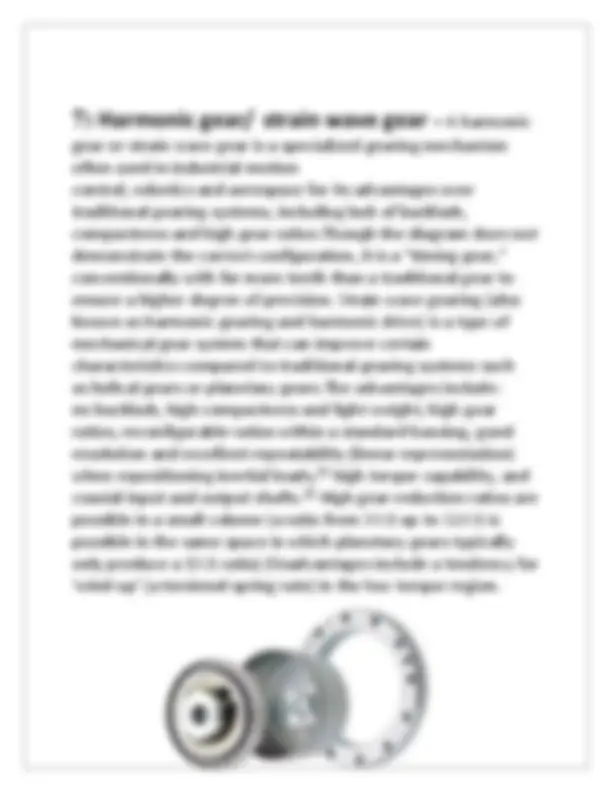

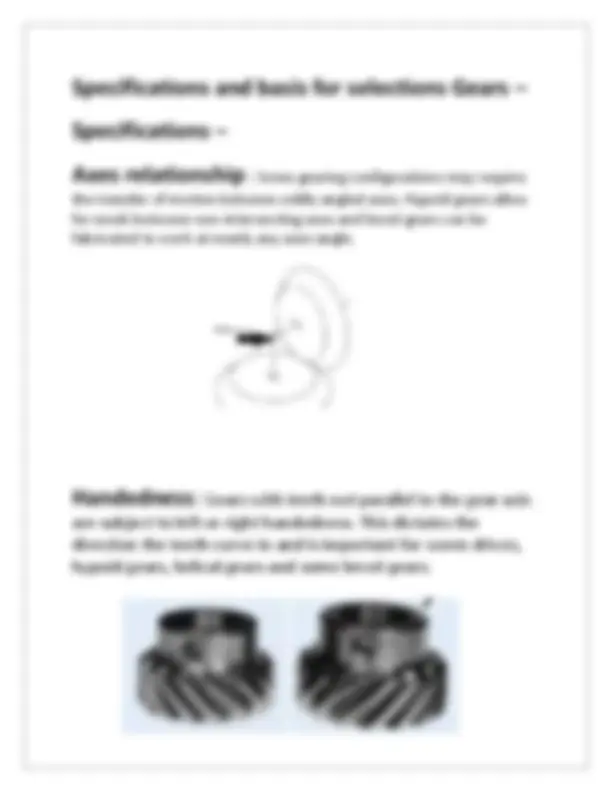
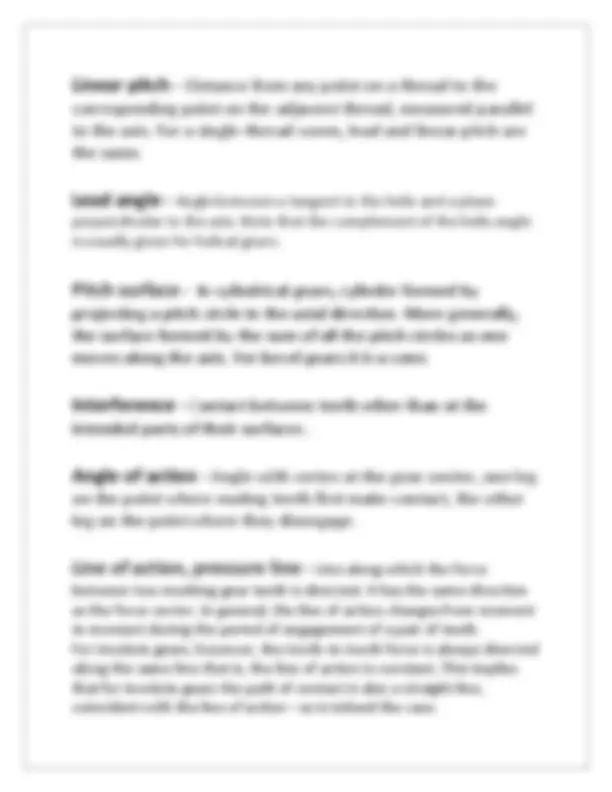
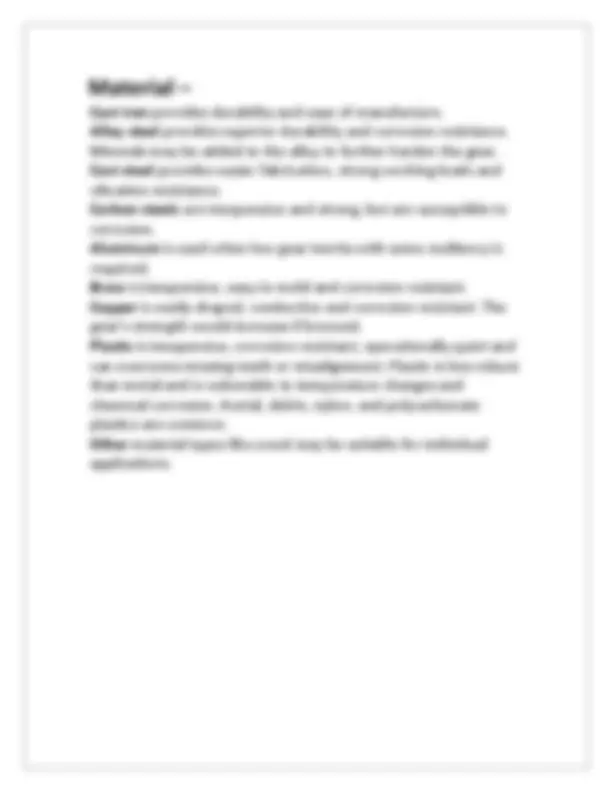
Study with the several resources on Docsity
Earn points by helping other students or get them with a premium plan
Prepare for your exams
Study with the several resources on Docsity
Earn points to download
Earn points by helping other students or get them with a premium plan
Community
Ask the community for help and clear up your study doubts
Discover the best universities in your country according to Docsity users
Free resources
Download our free guides on studying techniques, anxiety management strategies, and thesis advice from Docsity tutors
diploma emd micro project to study and udrstand concept
Typology: Cheat Sheet
1 / 19
This page cannot be seen from the preview
Don't miss anything!
On special offer
MAHARASHTRA STATE BOARD OF TECHNICAL EDUCATION
Academic year: 20 20 - 21
MAHARASHTRA STATE BOARD OF TECHNICAL EDUCATION Certificate This is to certify that Mr. /Ms. Viresh Bhoir, Dushyant Patil, Amol Dupare, Bhavik patil Roll No. 23,31,20,25 of 5 th^ Semester of Diploma in Mechanical Engeernering of Institute, Government Polytechnic, Vikramgad (Code: 1547) has completed the Micro Project satisfactorily in Subject - ( 22564 ) for the academic year 2019- 2020 as prescribed in the curriculum. Place: Vikramgad Enrollment No: ………………………………… Date: ……………………… Exam. Seat No: ………………………………… Subject Teacher Head of the Department Principal
Introduction Gears are one of the most fundamental mechanical devices in the world. Gears are particularly useful for the transferral and translation of rotary motion, and are able to manipulate speed, torque, and rotational axis within a given machine. Gears are so integral to our everyday lives that they can be found almost everywhere, from cars to clocks.A gear is a rotating circular machine part having cut teeth or, in the case of a cogwheel or gearwheel, inserted teeth (called cogs), which mesh with another toothed part to transmit torque. A gear may also be known informally as a cog. Geared devices can change the speed, torque, and direction of a power source. Gears of different sizes produce a change in torque, creating a mechanical advantage, through their gear ratio, and thus may be considered a simple machine. The rotational speeds, and the torques, of two meshing gears differ in proportion to their diameters. The teeth on the two meshing gears all have the same shape. Two or more meshing gears, working in a sequence, are called a gear train or a transmission. The gears in a transmission are analogous to the wheels in a crossed, belt pulley system. An advantage of gears is that the teeth of a gear prevent slippage. In transmissions with multiple gear ratios such as bicycles, motorcycles, and cars refers to a gear ratio.
**List of different type of gears – 1 ) Spur Gear.
2) Helical Gear - Helical gears have teeth that are oriented at an angle to the shaft, unlike spur gears which are parallel. This causes more than one tooth to be in contact during operation and helical gears are capable of carrying more load than spur gears. Due to the load sharing between teeth, this arrangement also allows helical gears to operate smoother and quieter than spur gears. Helical gears produce a thrust load during operation which needs to be considered when they are used. Most enclosed gear drives use helical gears Helical or "dry fixed" gears offer a refinement over spur gears. The leading edges of the teeth are not parallel to the axis of rotation, but are set at an angle. Since the gear is curved, this angling makes the tooth shape a segment of a helix. Helical gears can be meshed in parallel or crossed orientations. The former refers to when the shafts are parallel to each other; this is the most common orientation. In the latter, the shafts are non-parallel, and in this configuration the gears are sometimes known as "skew gears".The angled teeth engage more gradually than do.
3) Herringbone Gear - Herringbone gears are very similar to the double helical gear, but they do not have a gap separating the two helical faces. Herringbone gears are typically smaller than the comparable double helical, and are ideally suited for high shock and vibration applications. Herringbone gearing is not used very often due to their manufacturing difficulties and high cost. A herringbone gear, a specific type of double helical gear,[1]^ is a special type of gear that is a side to side (not face to face) combination of two helical gears of opposite hands.[2]^ From the top, each helical groove of this gear looks like the letter V, and many together form a herringbone pattern (resembling the bones of a fish such as a herring). Unlike helical gears, herringbone gears do not produce an additional axial load.Like helical gears, they have the advantage of transferring power smoothly, because more than two teeth will be in mesh at any moment in time. Their advantage over the helical gears is that the side-thrust of one half is balanced by that of the other half. This means that herringbone gears can be used in torque gearboxes without requiring a substantial thrust bearing. Because of this, herringbone gears were an important step in the introduction of the steam turbine to marine propulsion.
5) Worm Gear – Worms resemble screws. A worm is
[27][30]
[31]
7) Harmonic gear/ strain wave gear – A harmonic
[1]
[2]
Internal gears : Some gears may have an inverted tooth
Lubrication : Most gearing arrangements require lubrication
Gear Nomenclature Specifications – Pitch Diameter - A predefined diametral position on the gear where the circular tooth thickness, pressure angle and helix angles are defined. The standard pitch diameter is a design dimension and cannot be measured, but is a location where other measurements are made. Face Width - FACE WIDTH is the length of the teeth in an axial plane. FILLET RADIUS is the radius of the fillet curve at the base of the gear tooth. FULL DEPTH TEETH are those in which the working depth equals 2.000 divided by the normal diametral pitch. Gear, wheel - The larger of two interacting gears or a gear on
Material – Cast iron provides durability and ease of manufacture. Alloy steel provides superior durability and corrosion resistance. Minerals may be added to the alloy to further harden the gear. Cast steel provides easier fabrication, strong working loads and vibration resistance. Carbon steels are inexpensive and strong, but are susceptible to corrosion. Aluminum is used when low gear inertia with some resiliency is required. Brass is inexpensive, easy to mold and corrosion resistant. Copper is easily shaped, conductive and corrosion resistant. The gear's strength would increase if bronzed. Plastic is inexpensive, corrosion resistant, operationally quiet and can overcome missing teeth or misalignment. Plastic is less robust than metal and is vulnerable to temperature changes and chemical corrosion. Acetal, delrin, nylon, and polycarbonate plastics are common. Other material types like wood may be suitable for individual applications.