
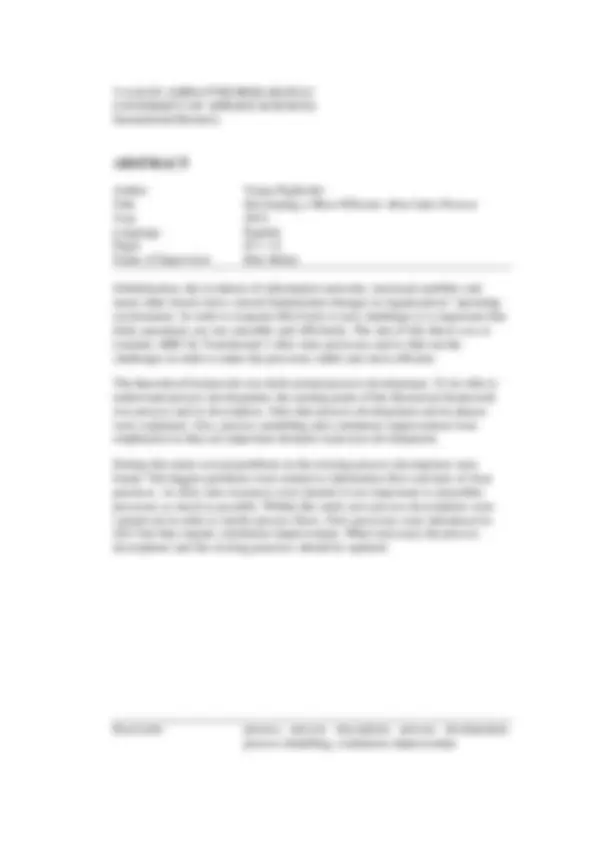
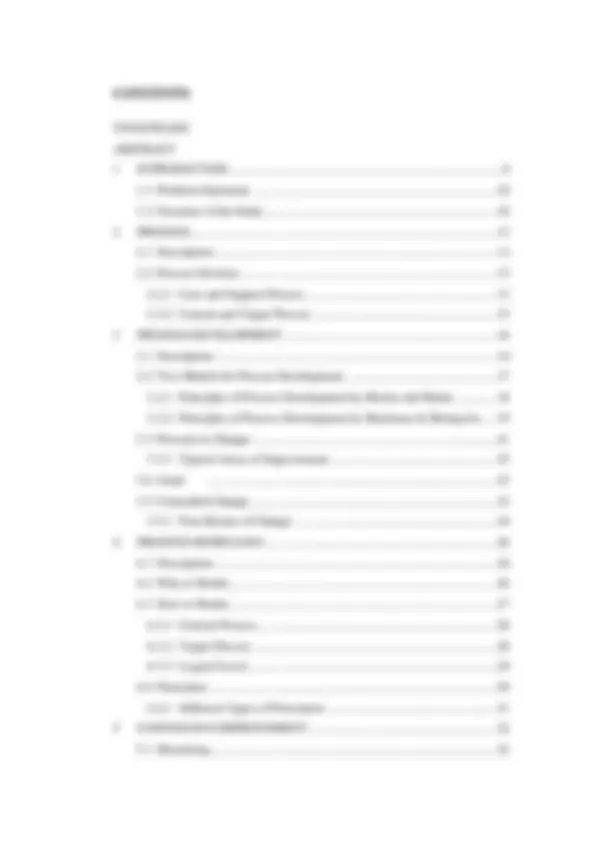

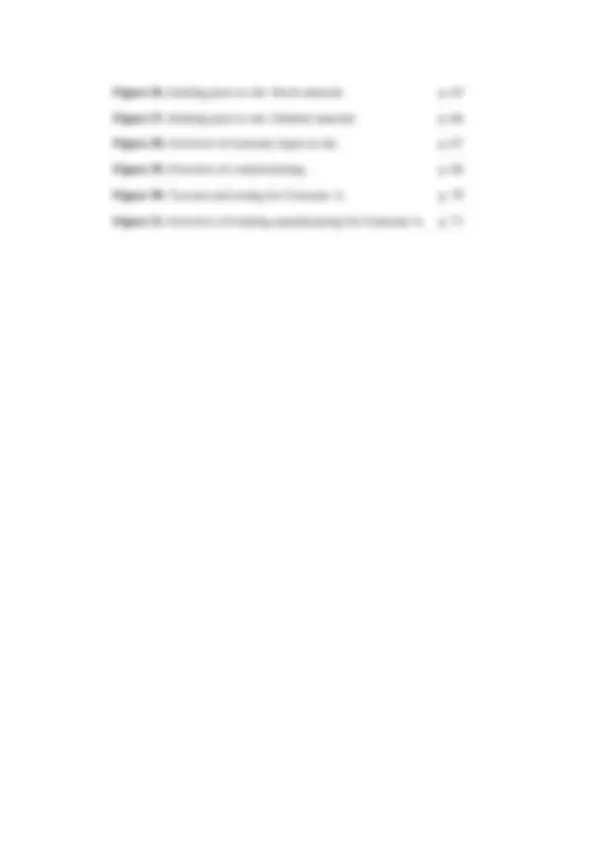
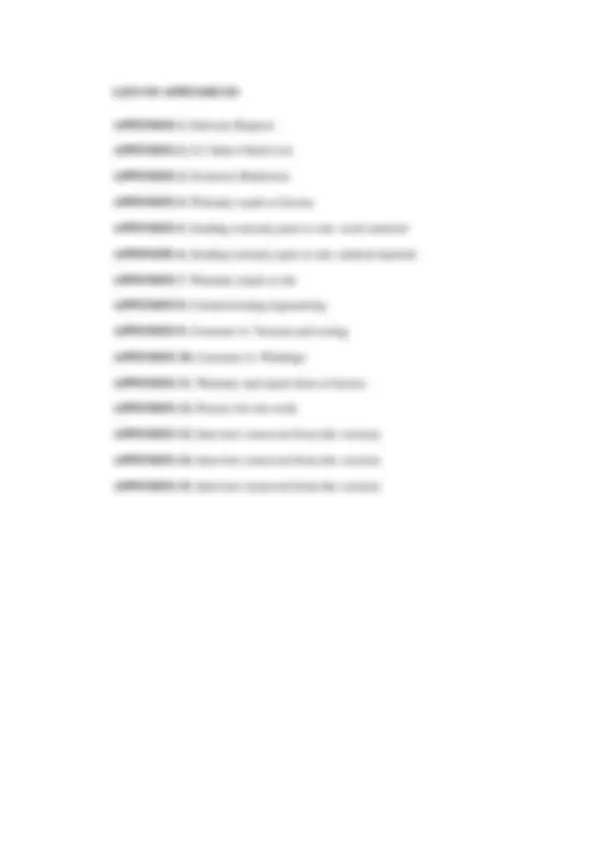
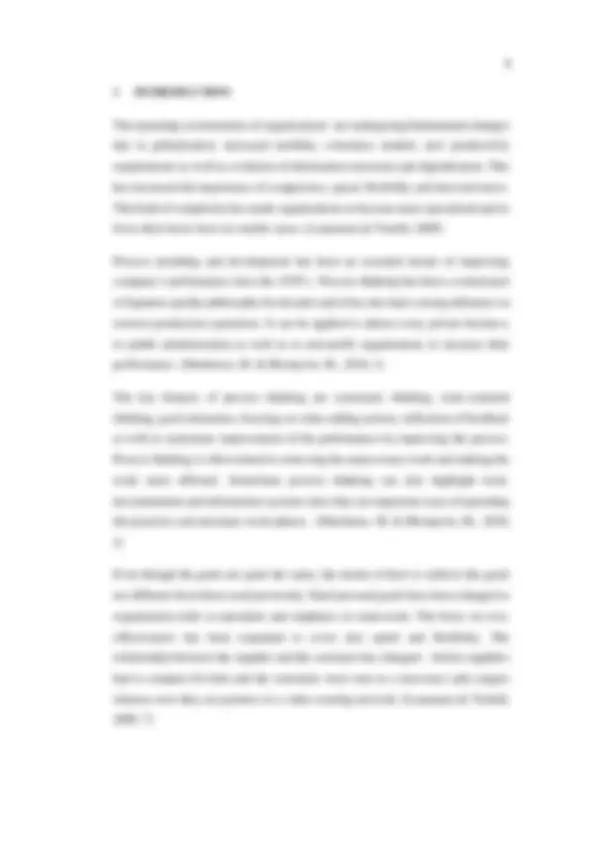
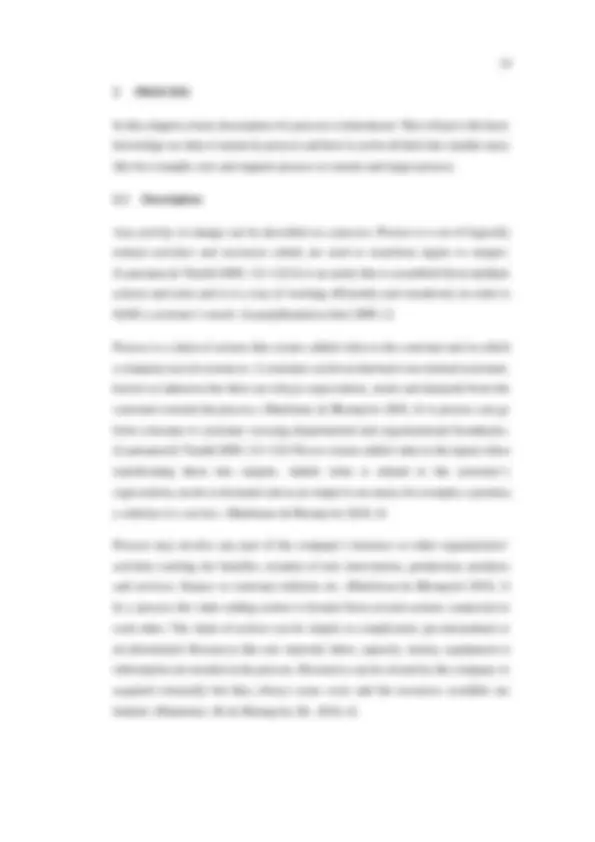
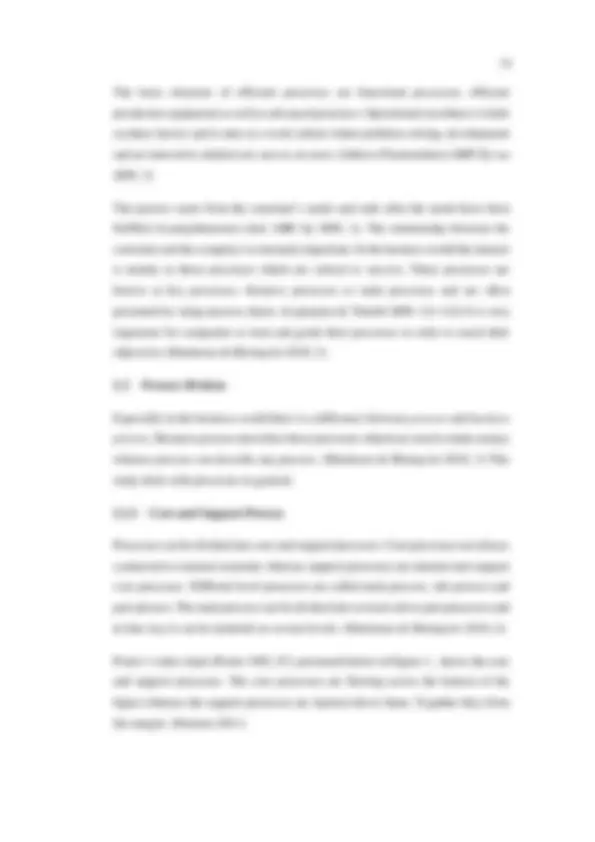
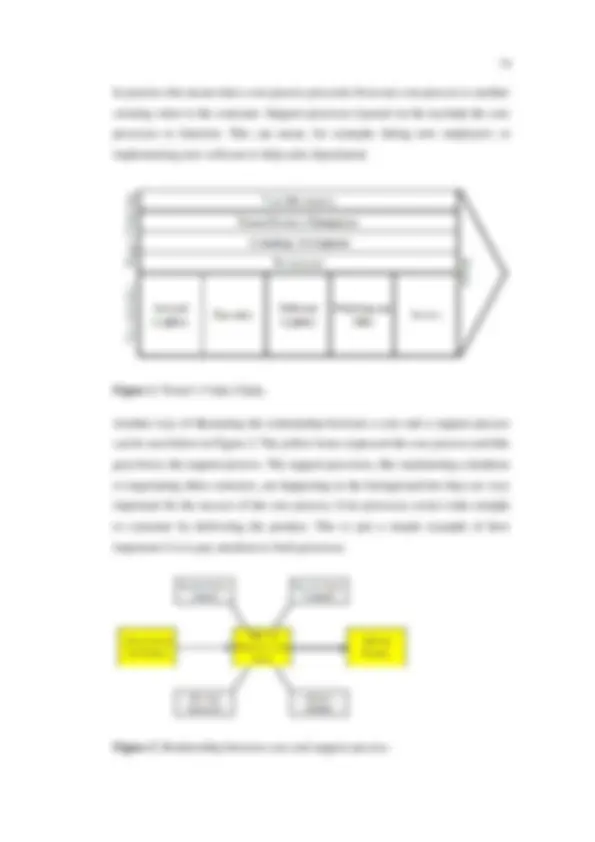
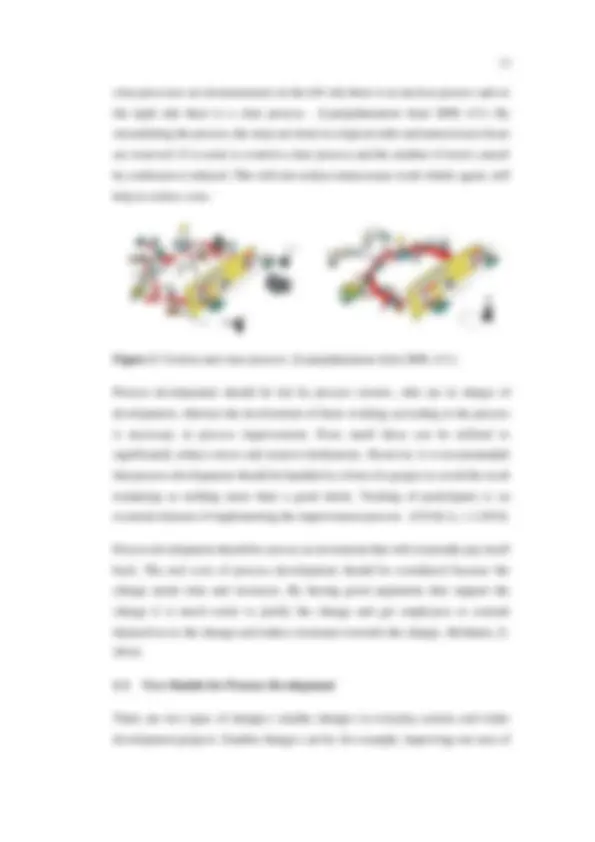
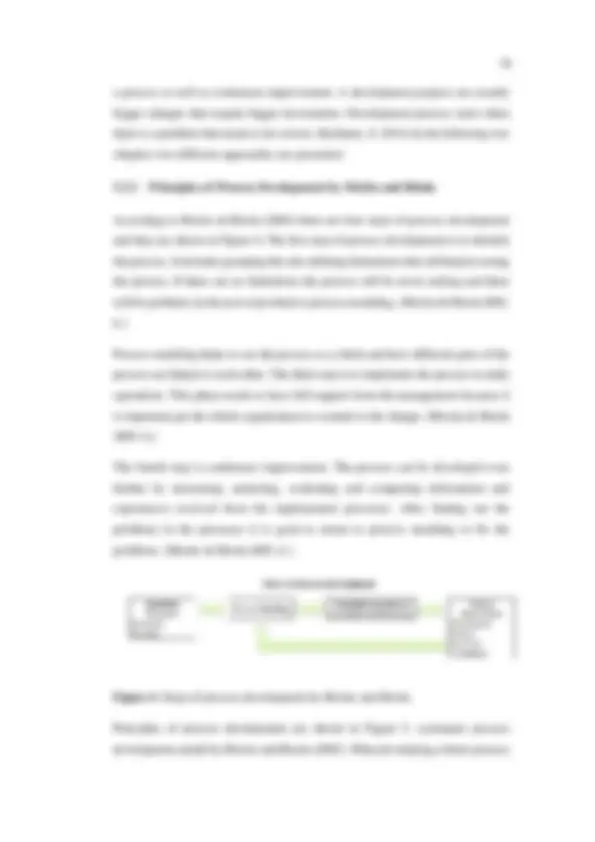
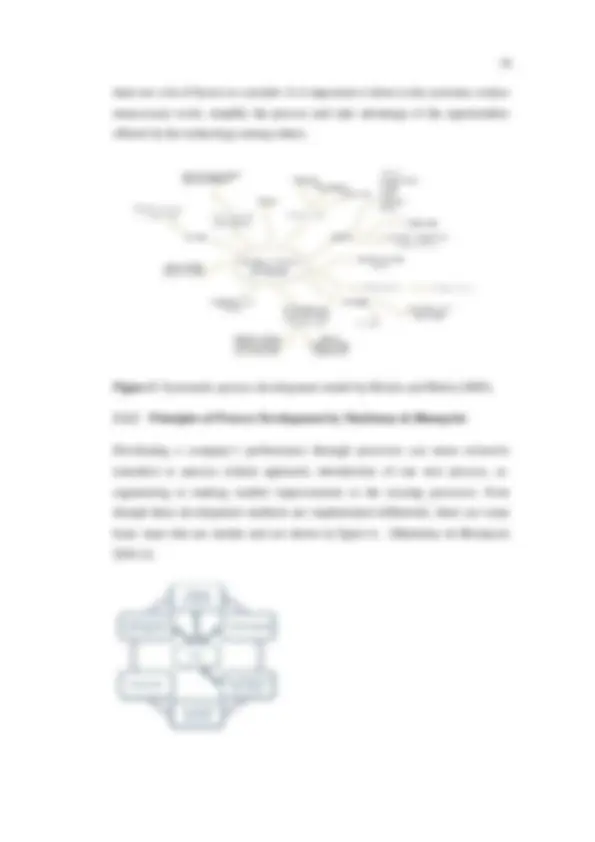

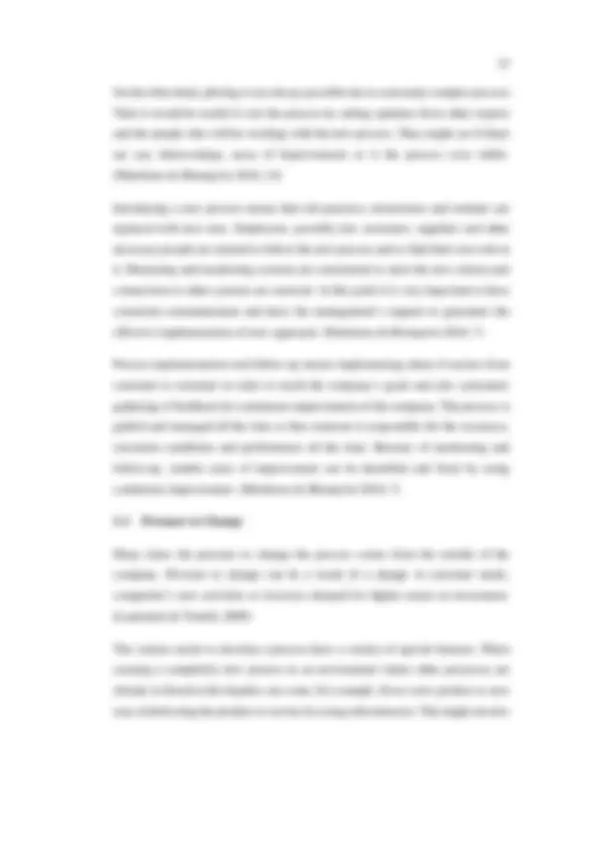
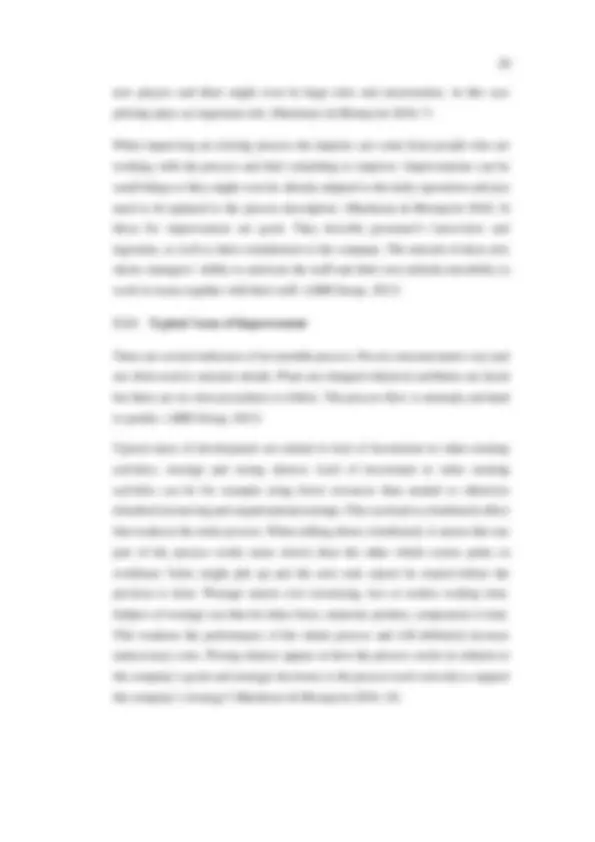
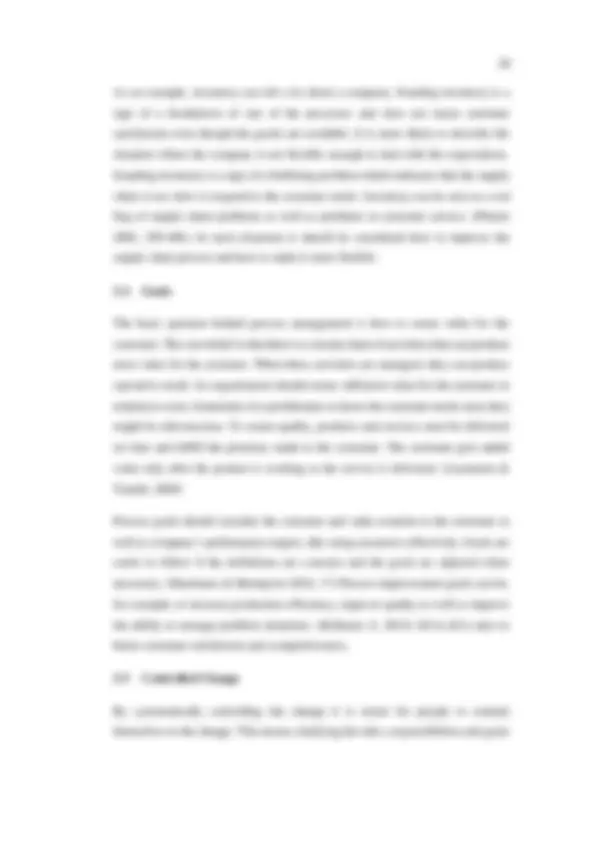
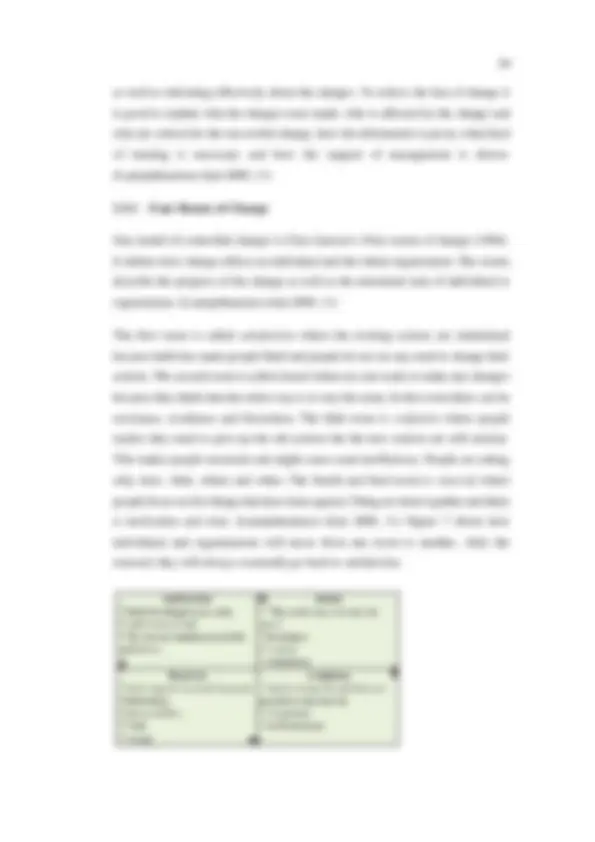
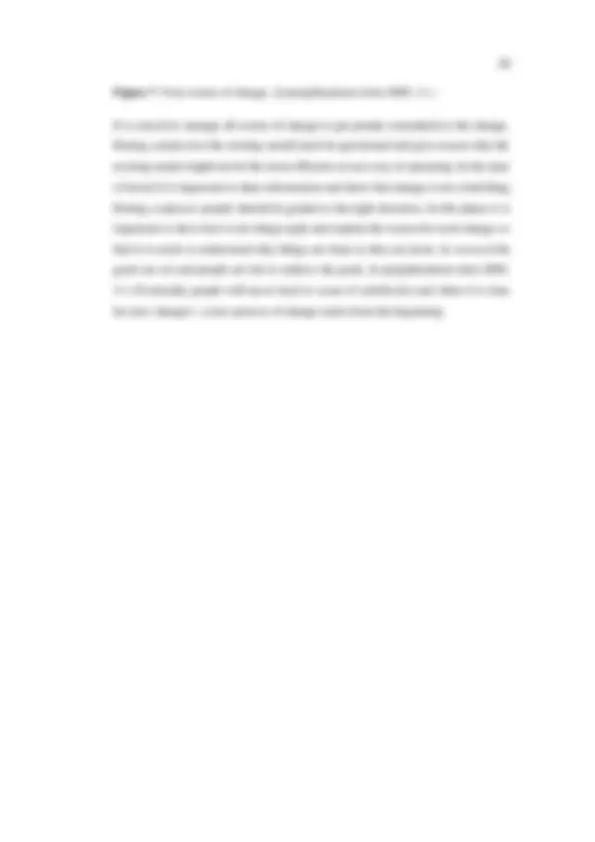
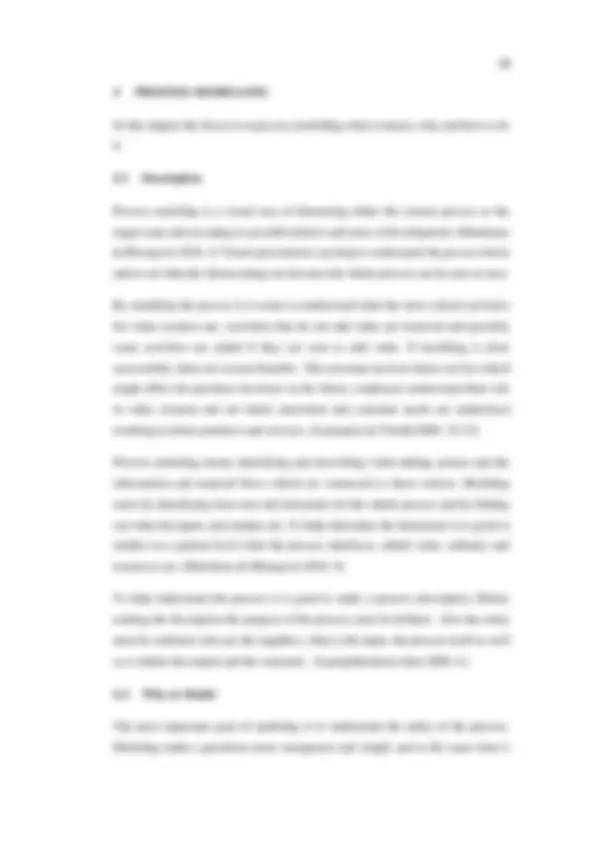
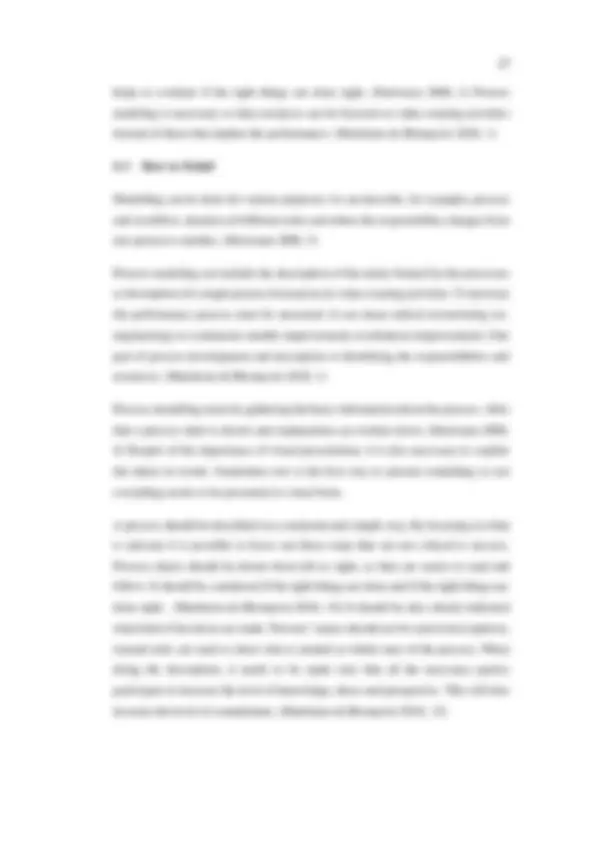
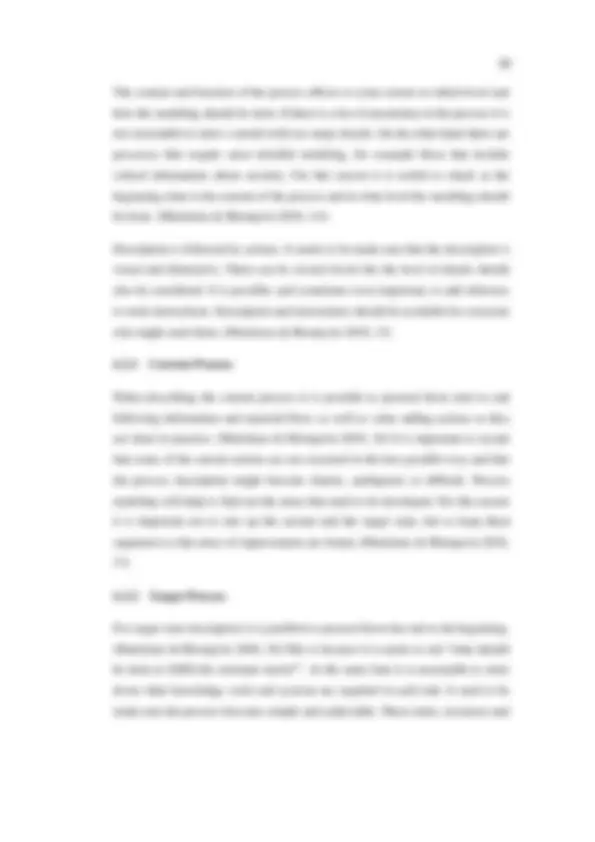
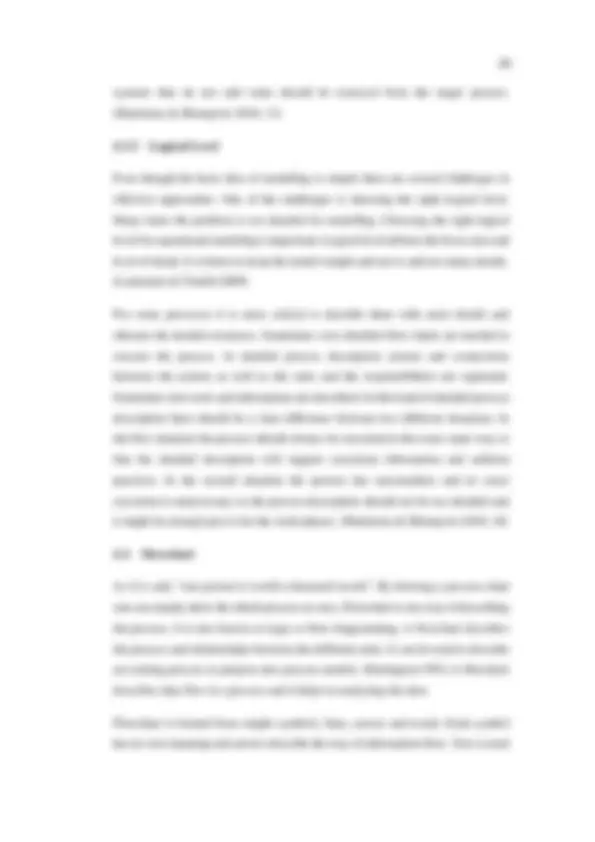
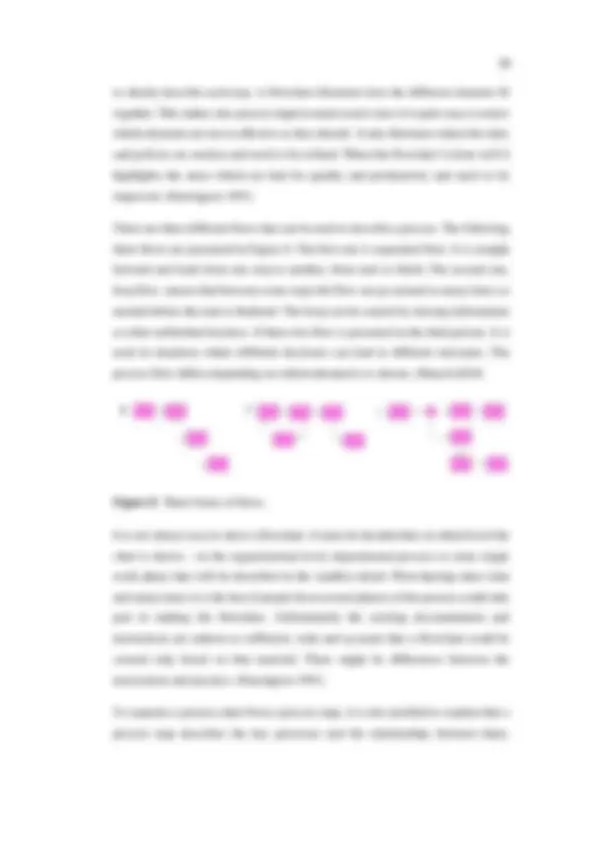

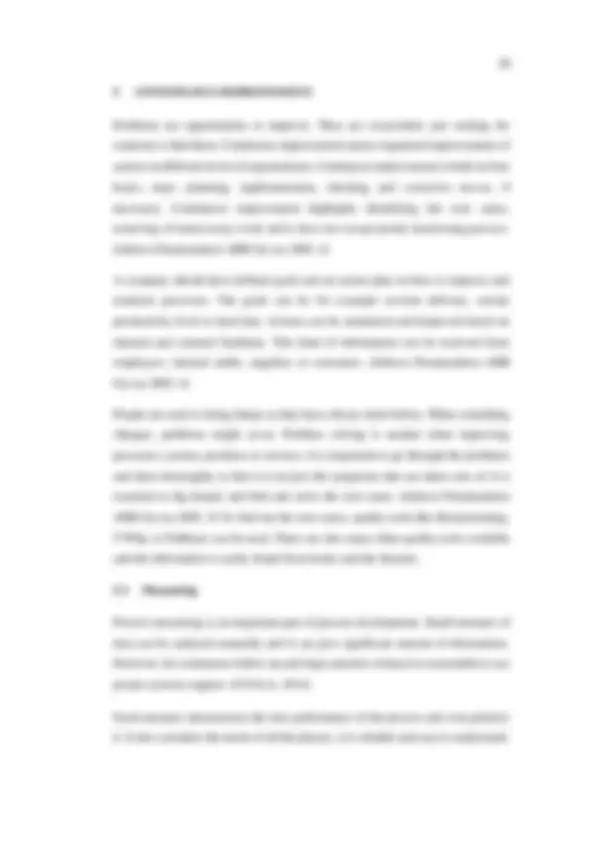
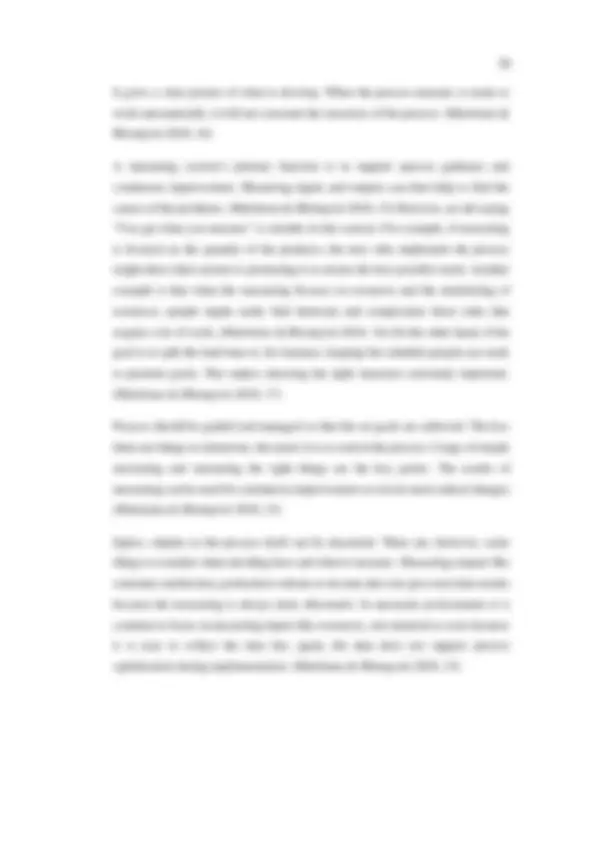
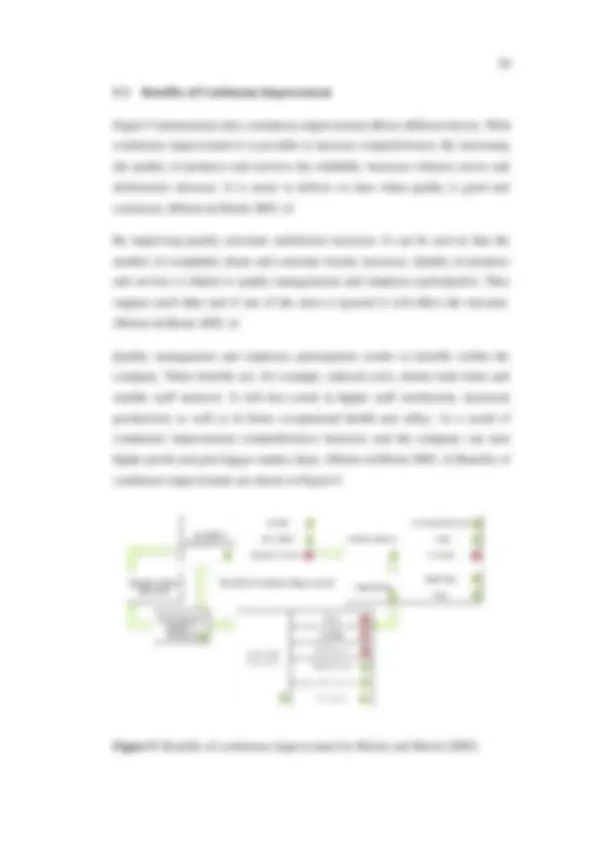
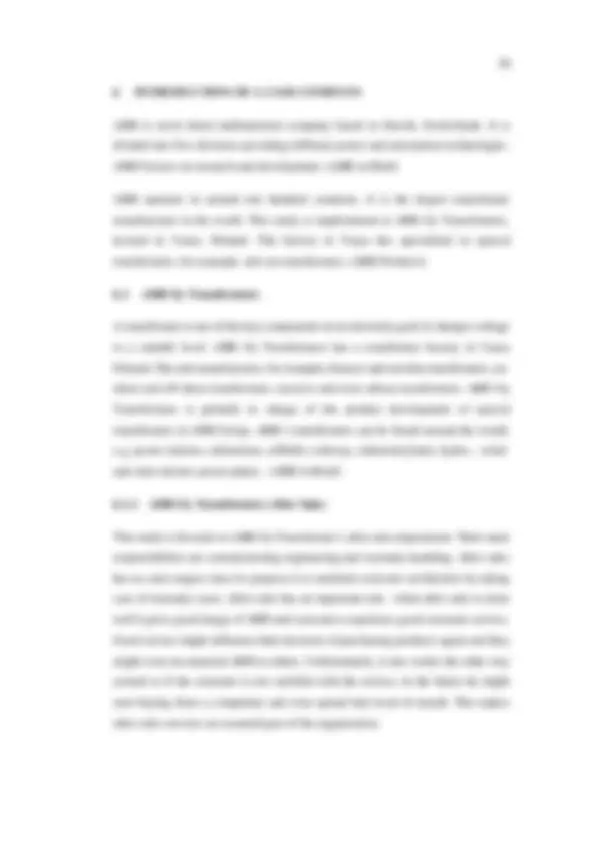
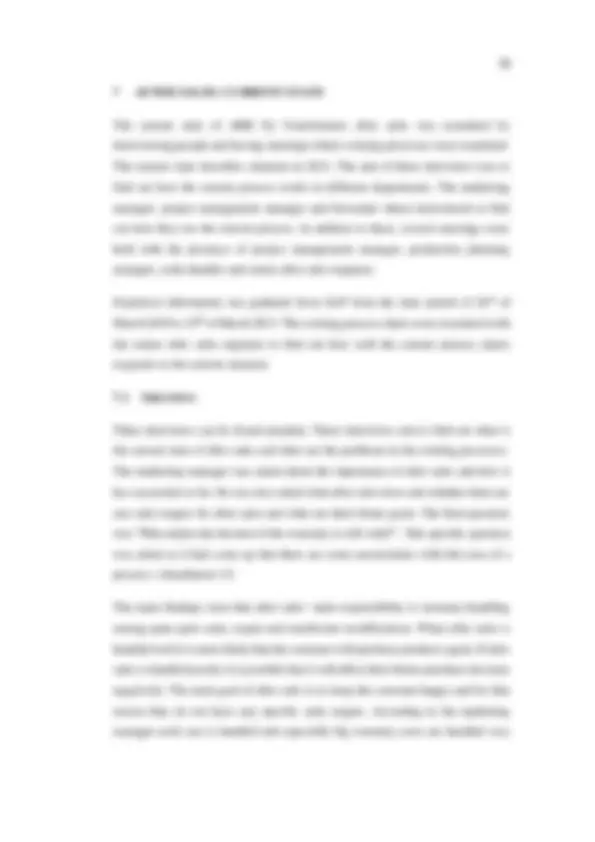
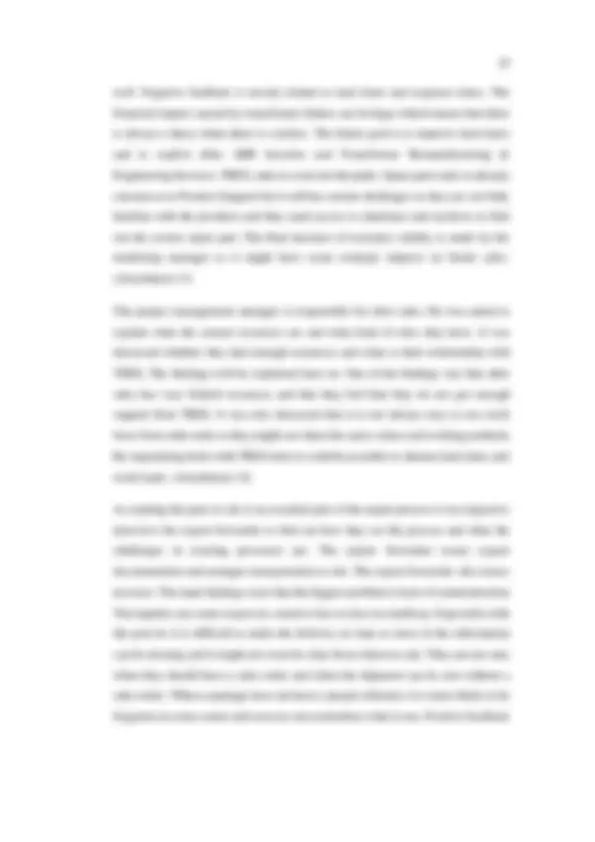
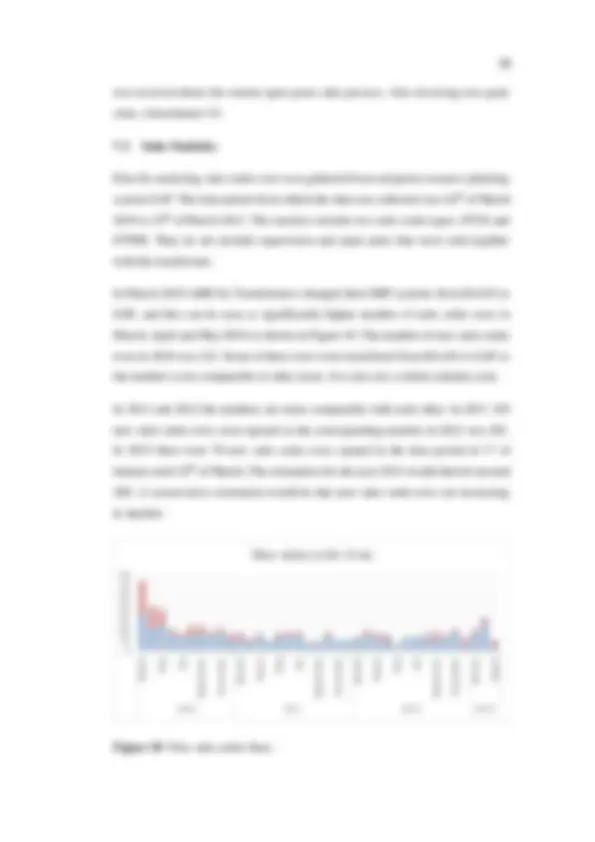
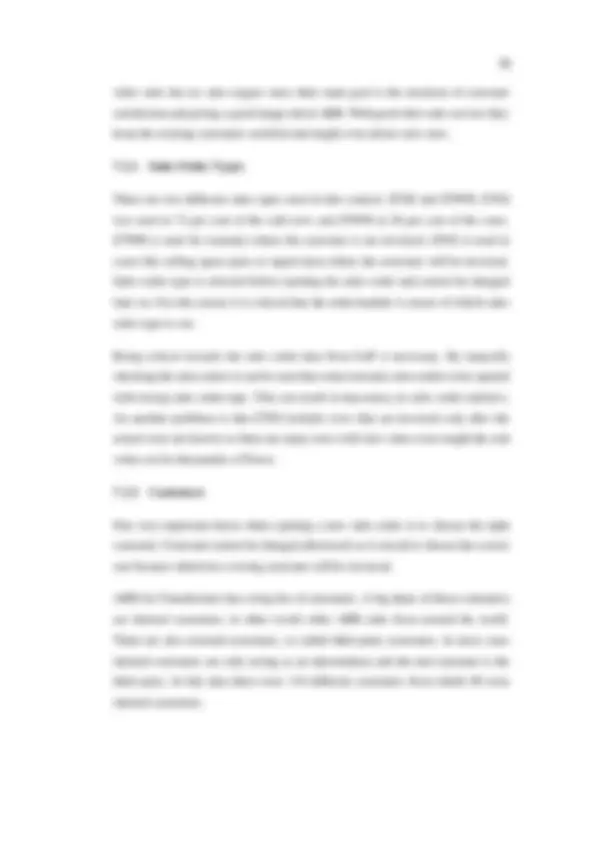
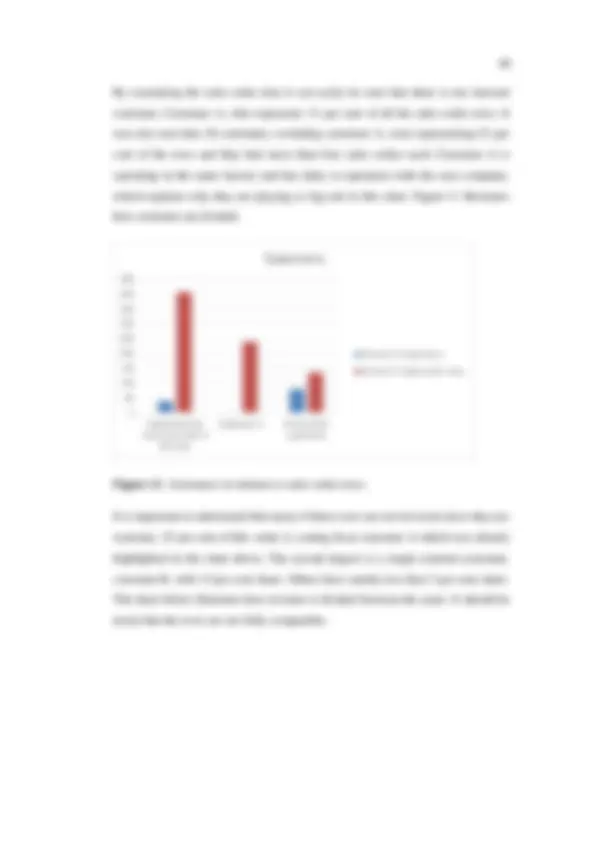
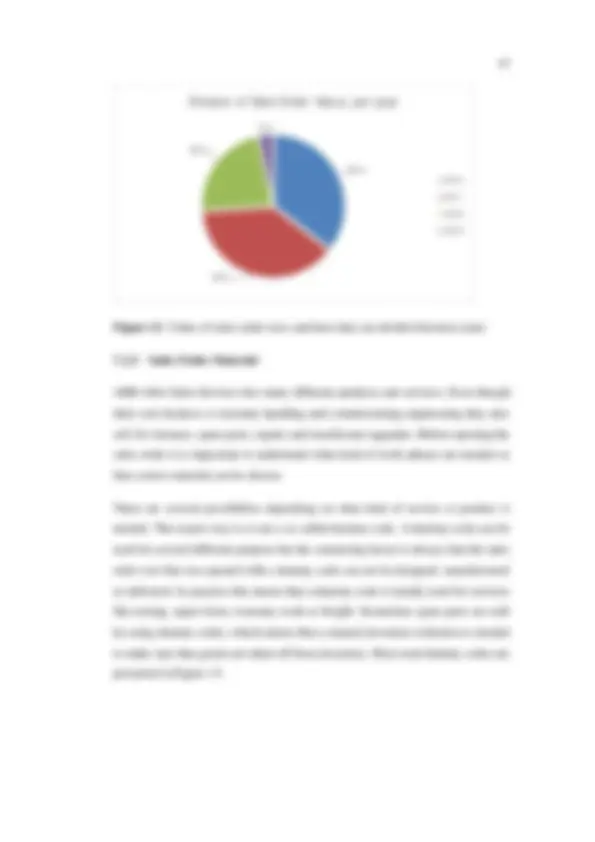
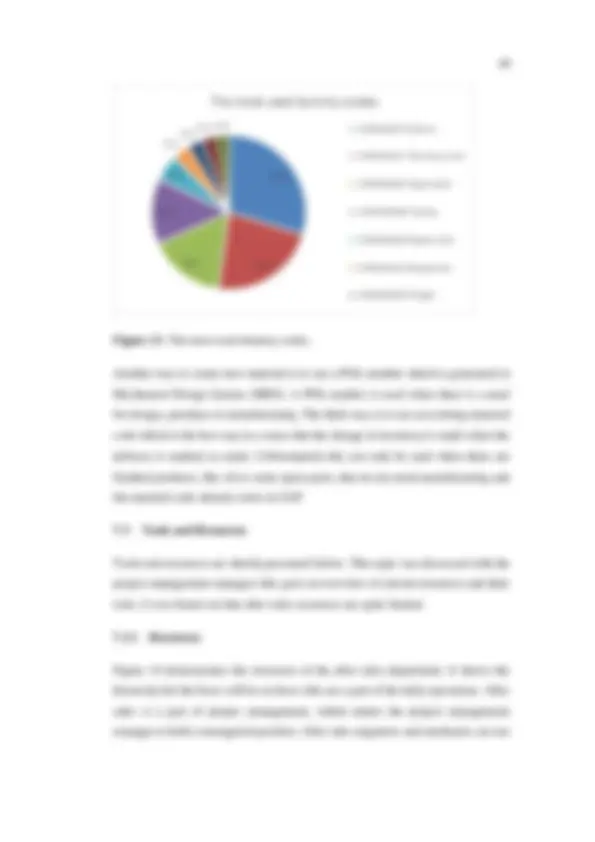
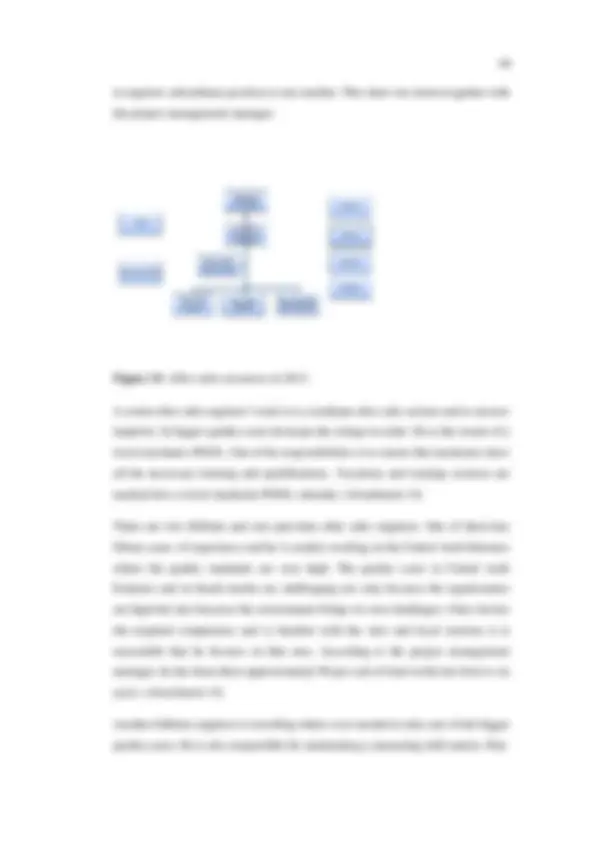
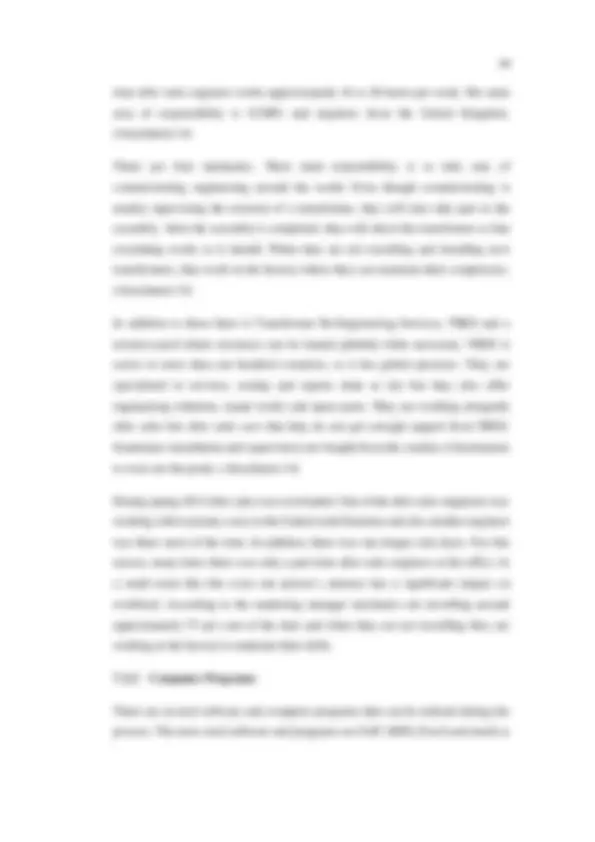
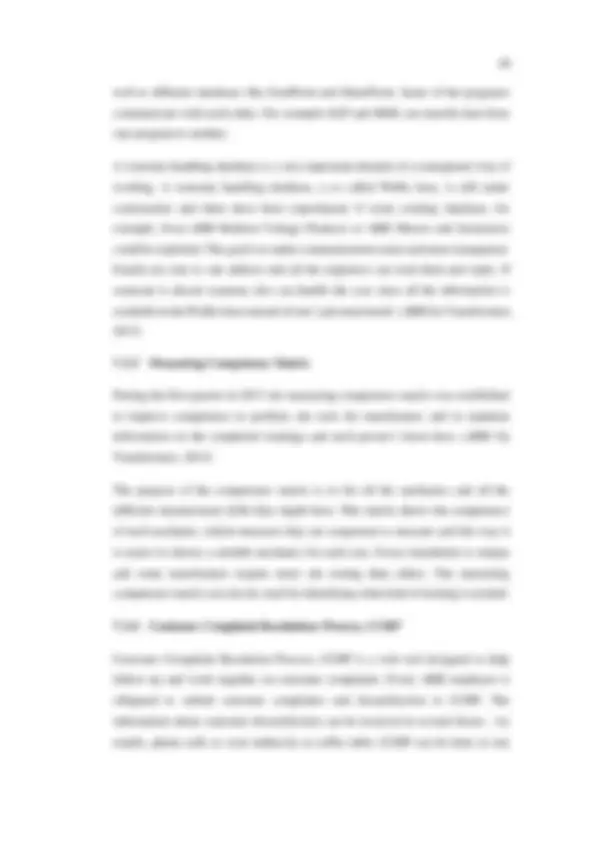
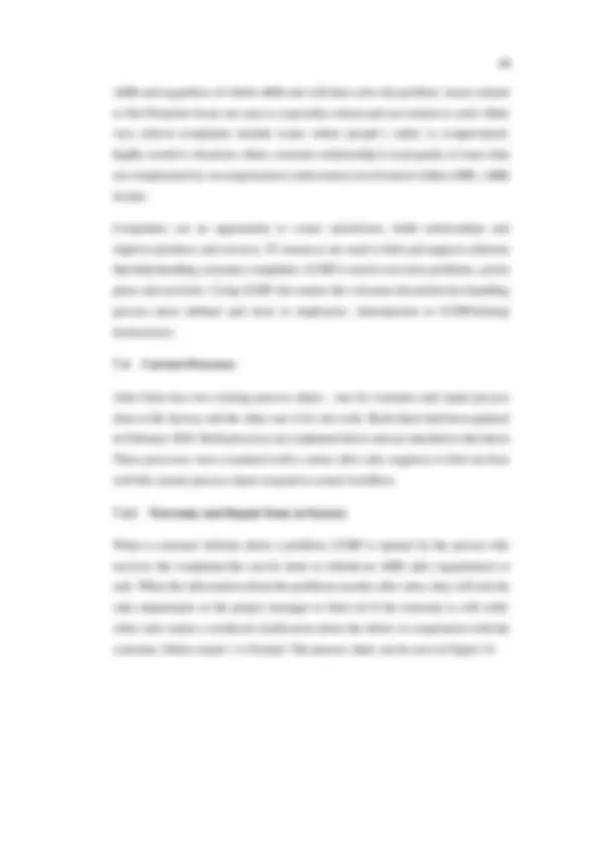
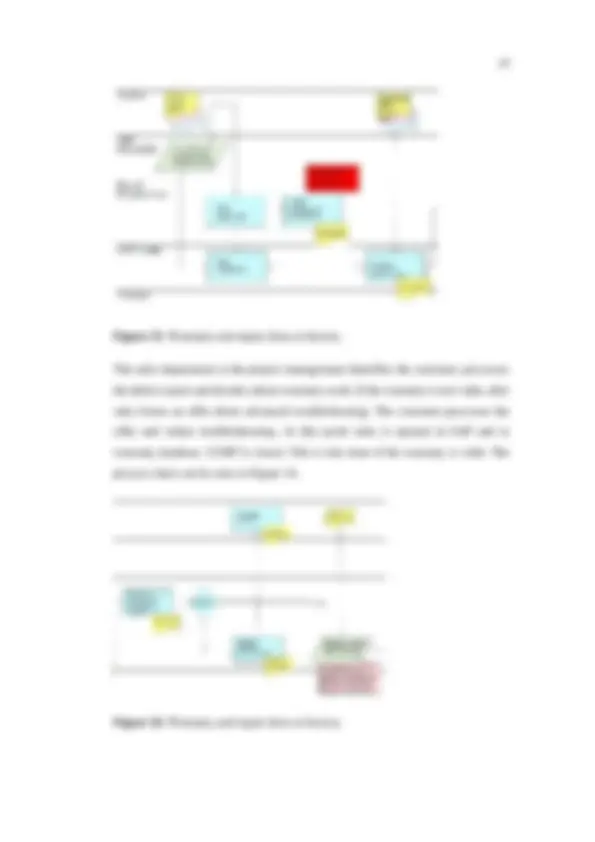
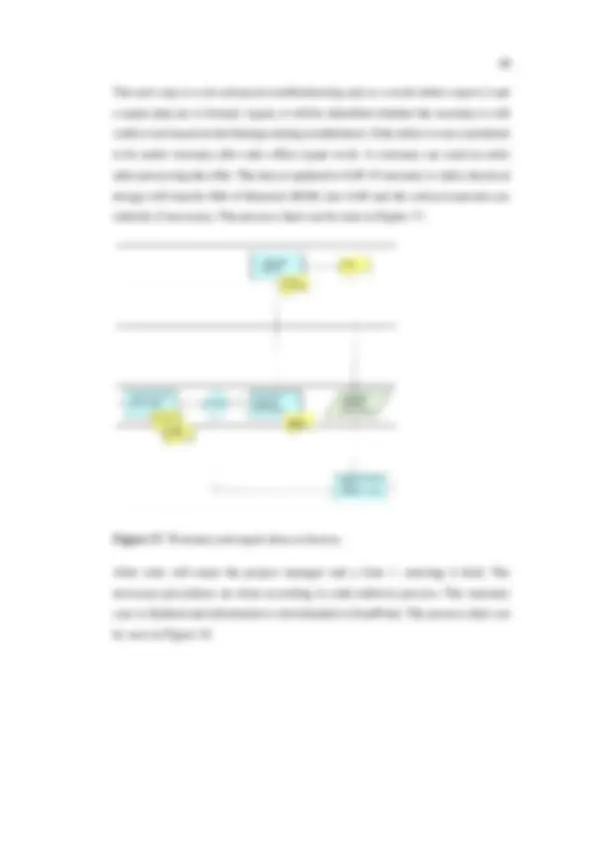
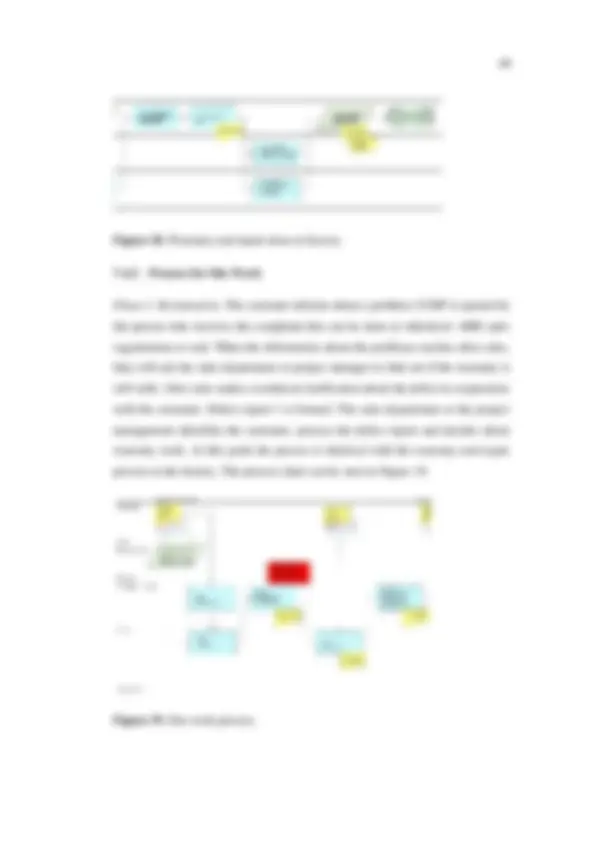
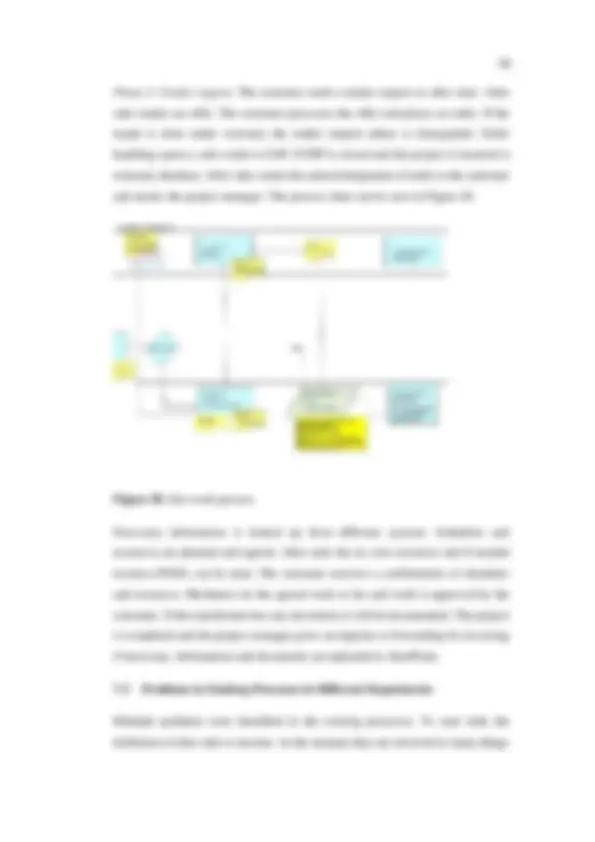
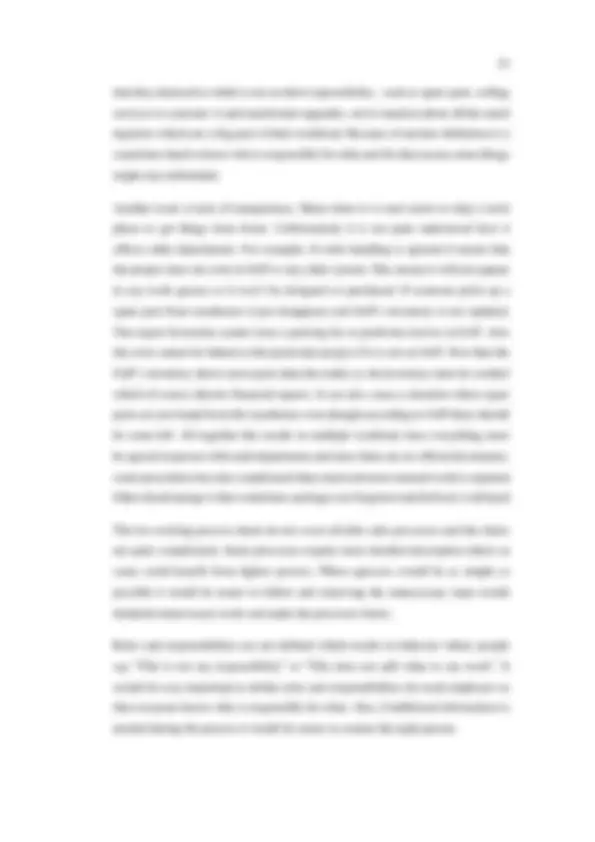
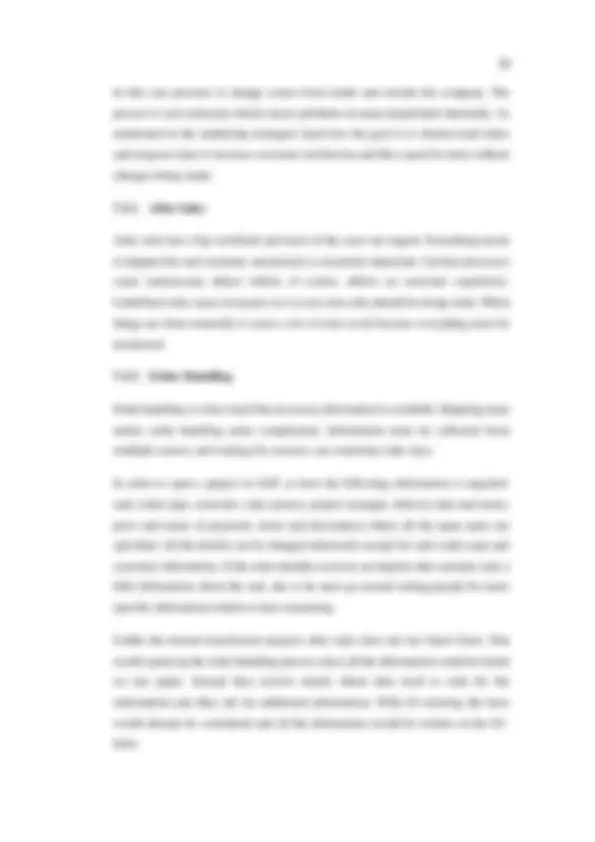
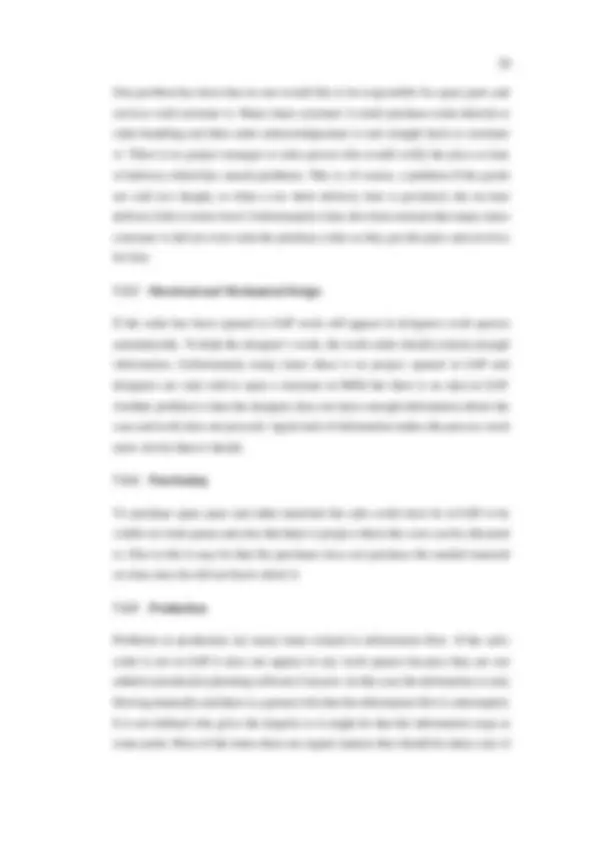
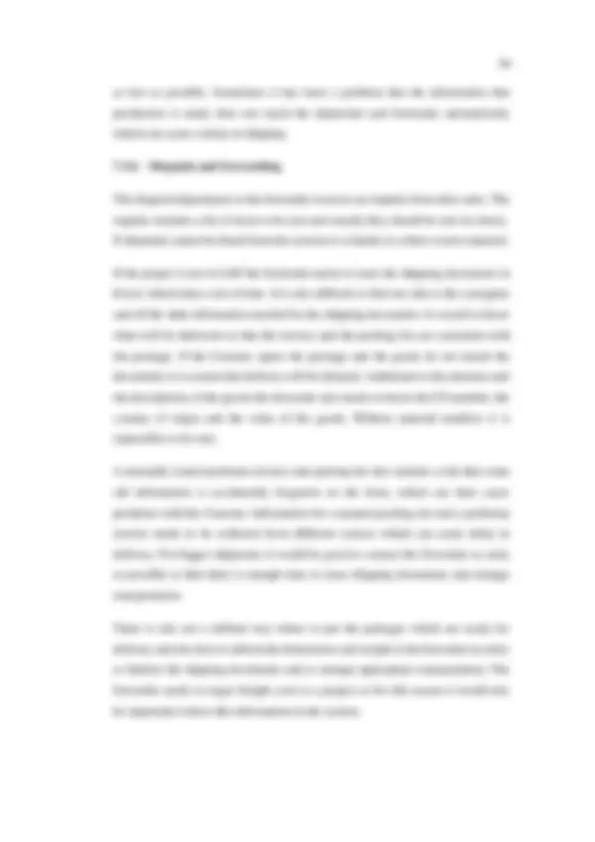
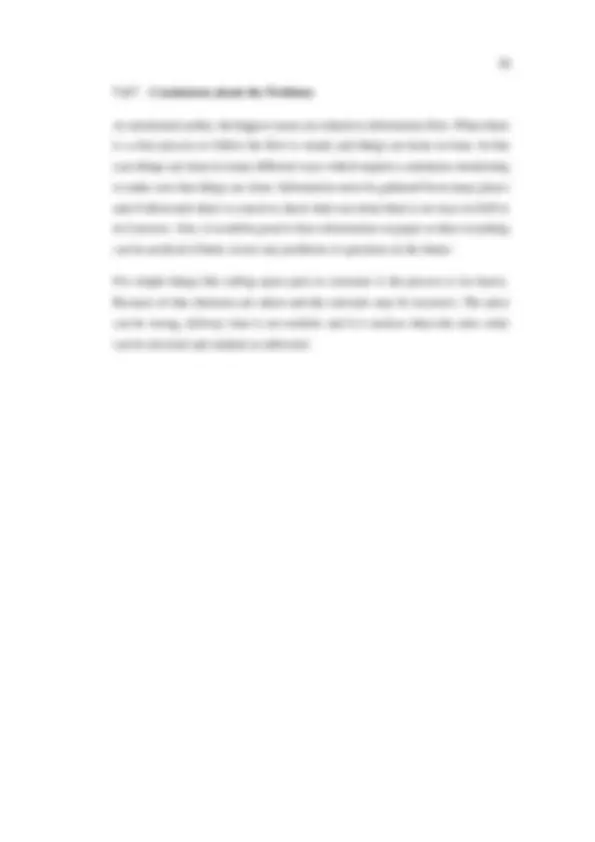
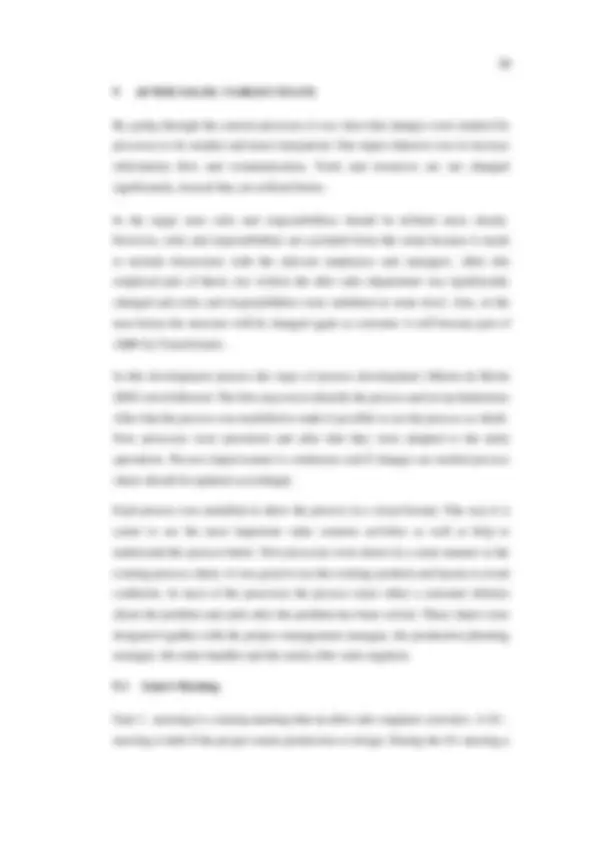
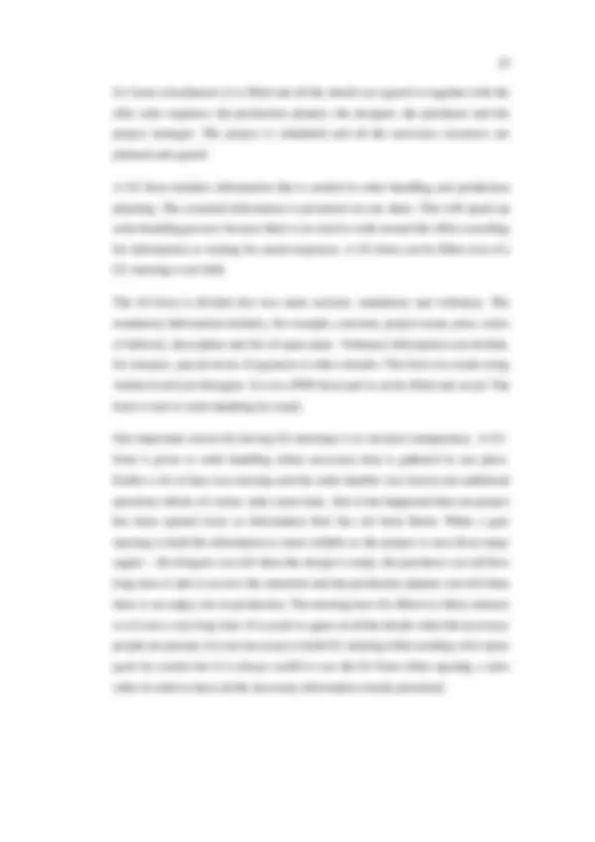
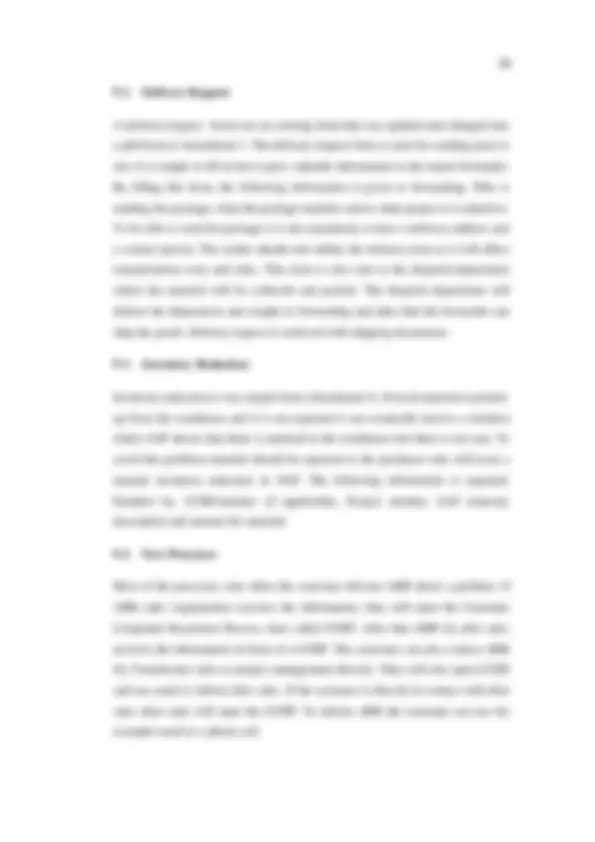
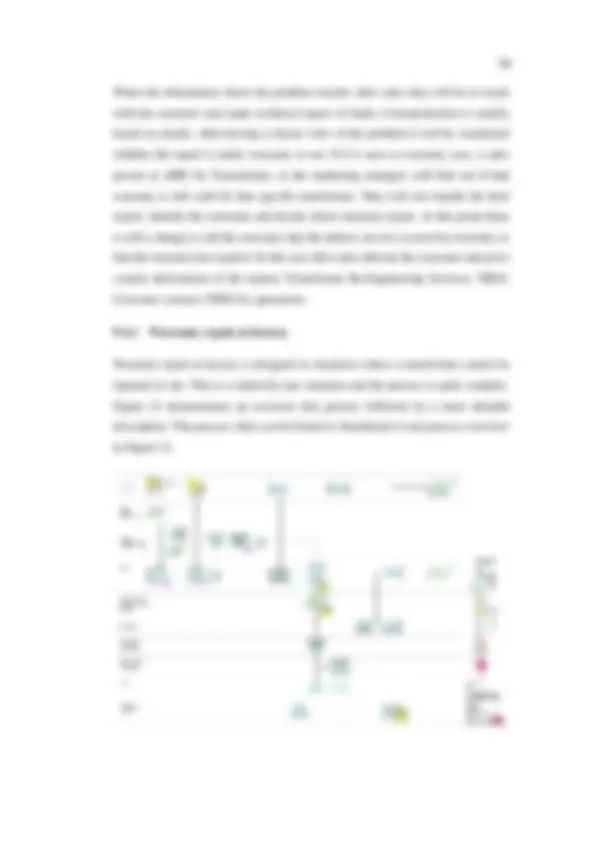

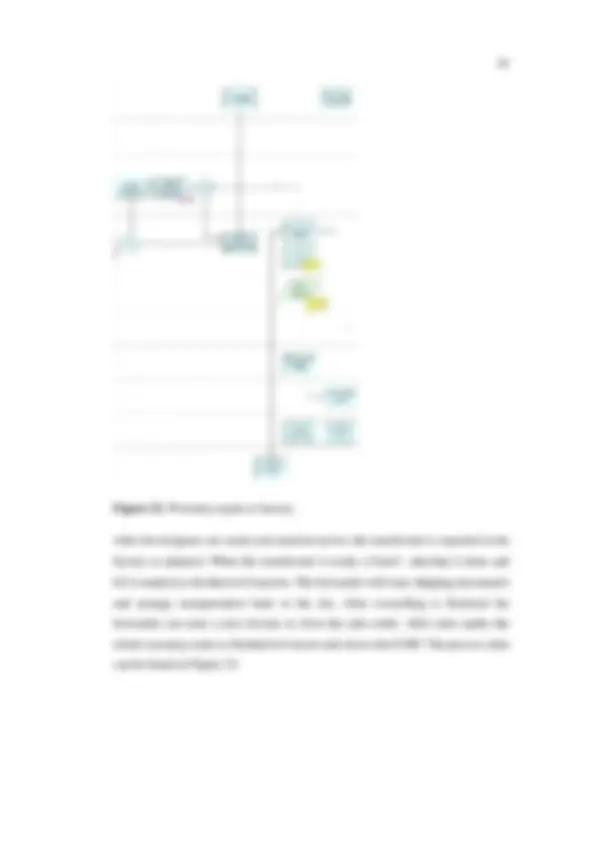
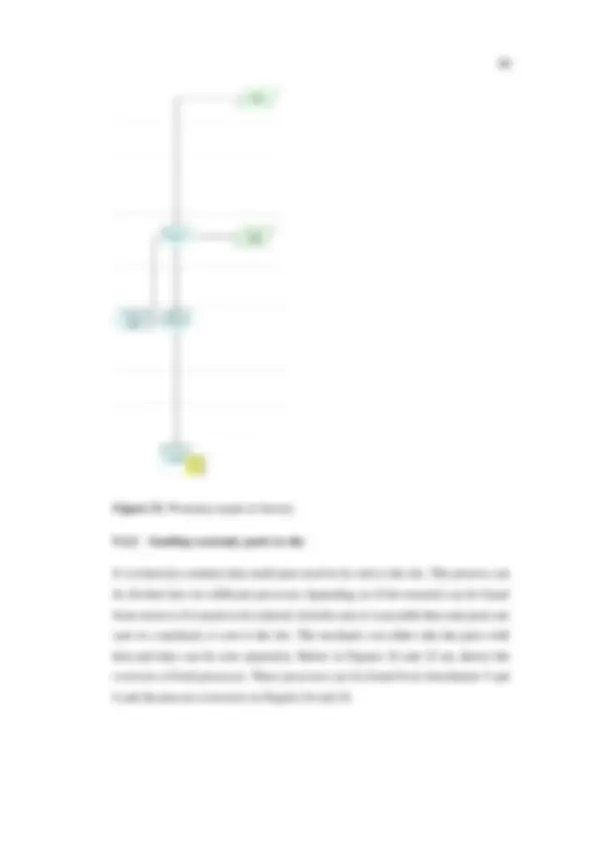
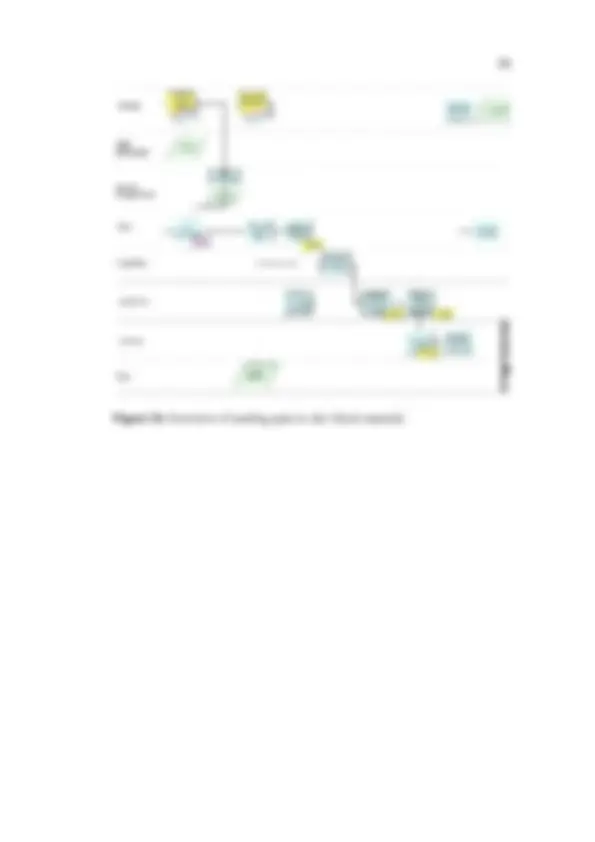
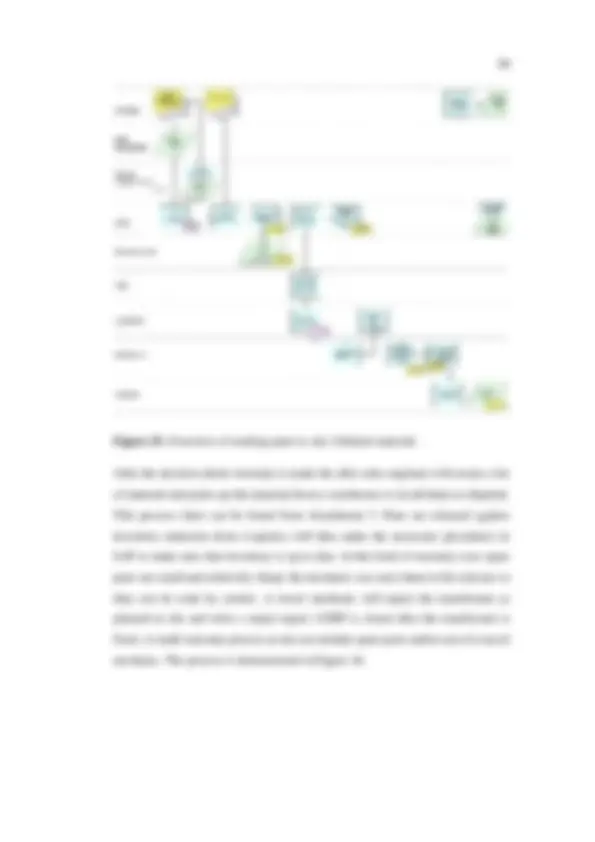
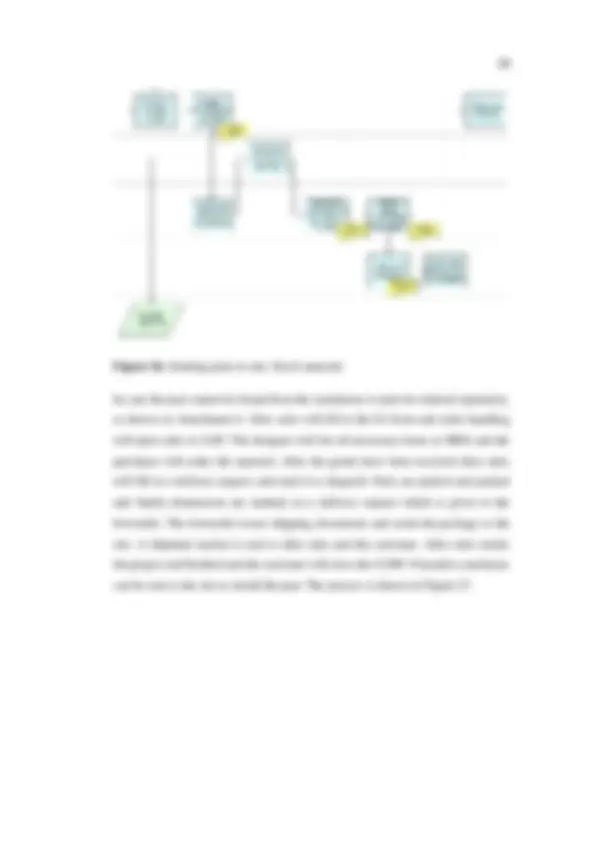
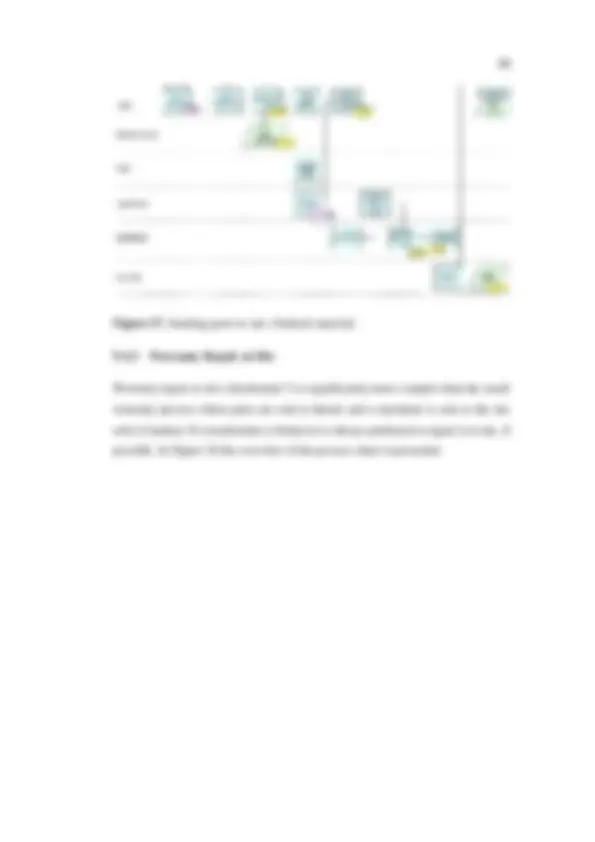
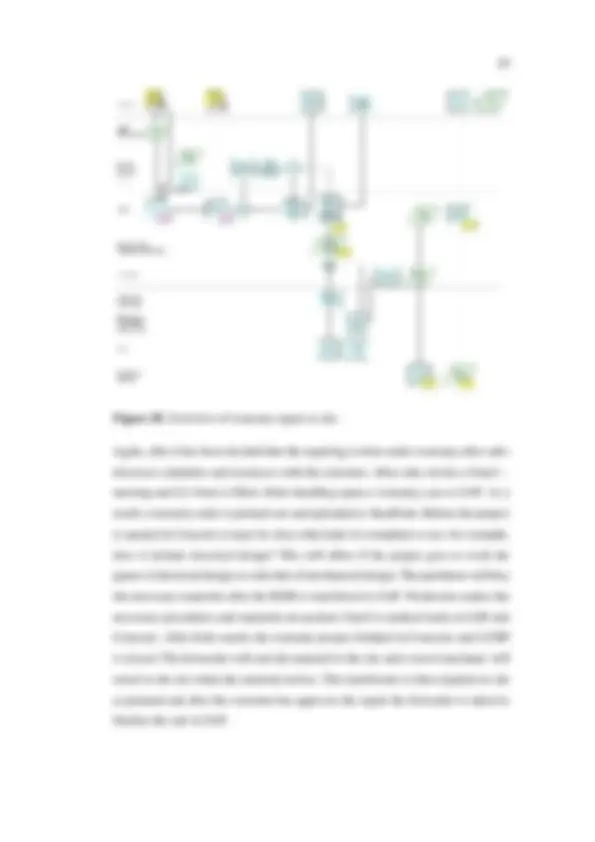
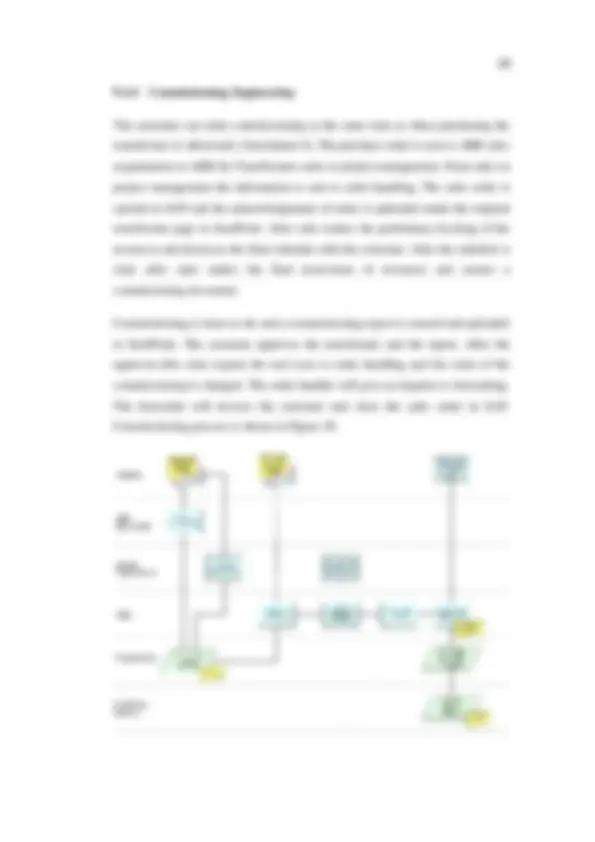
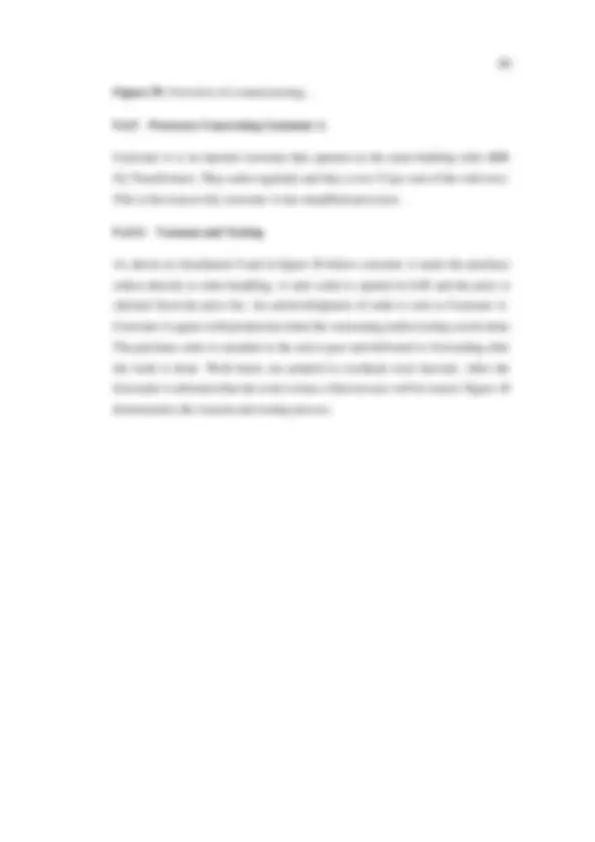
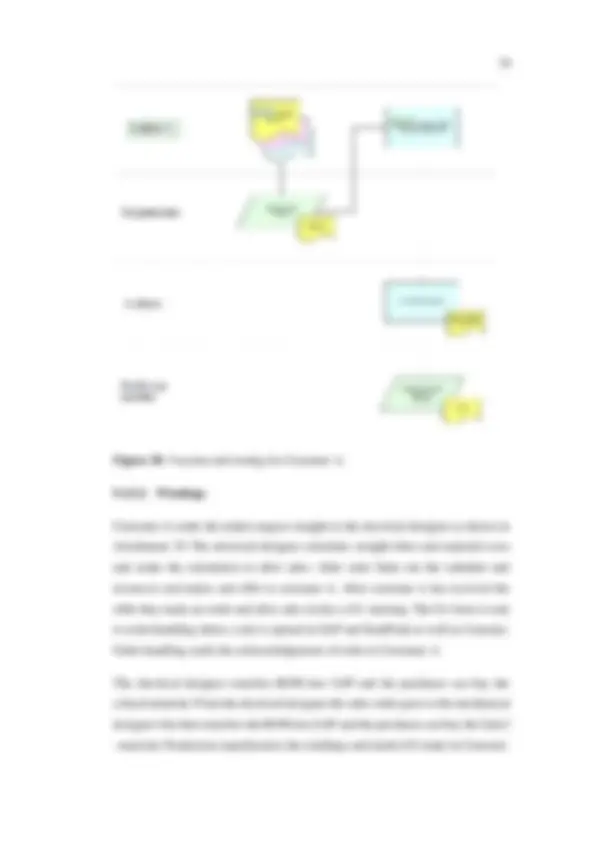
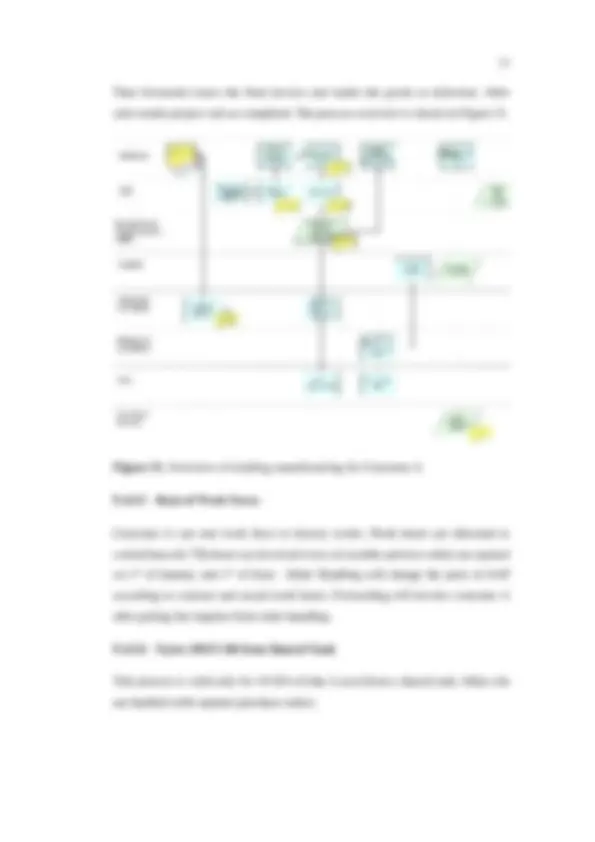
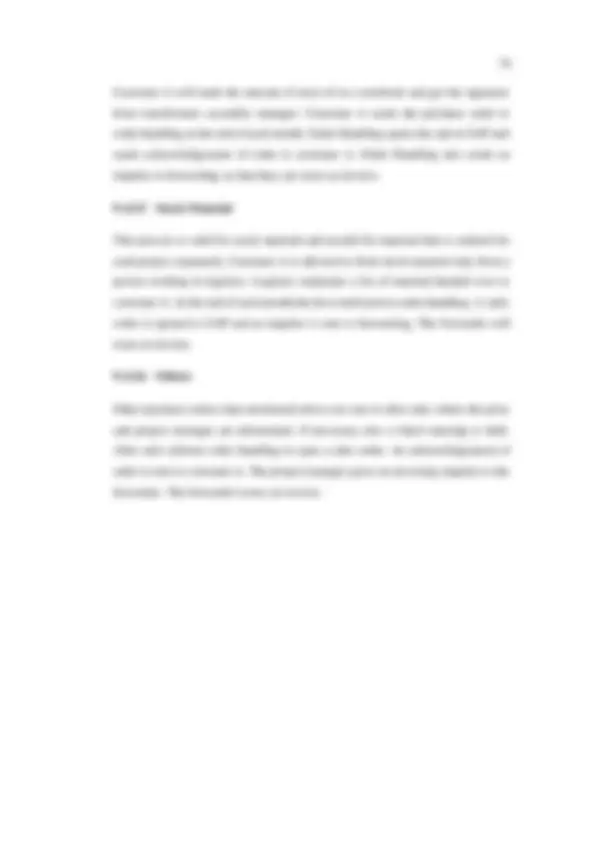
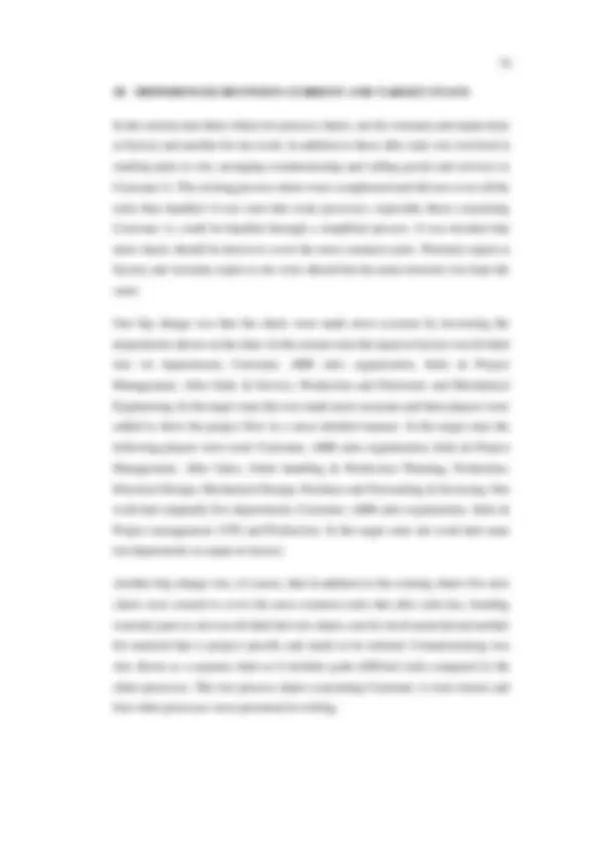
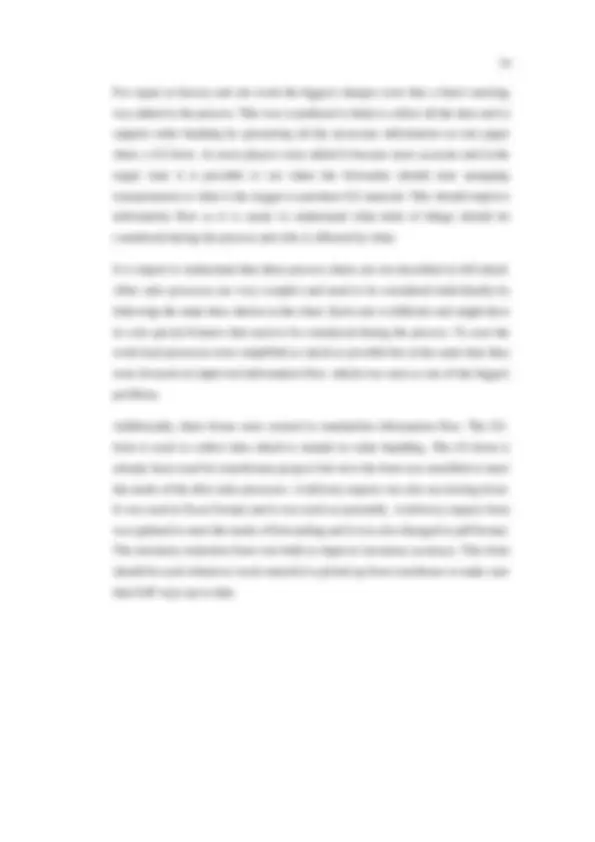
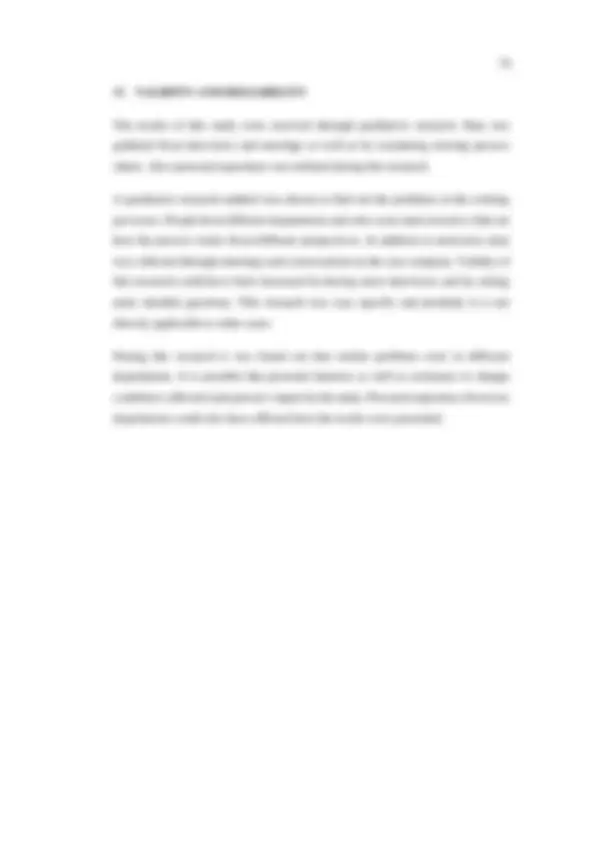
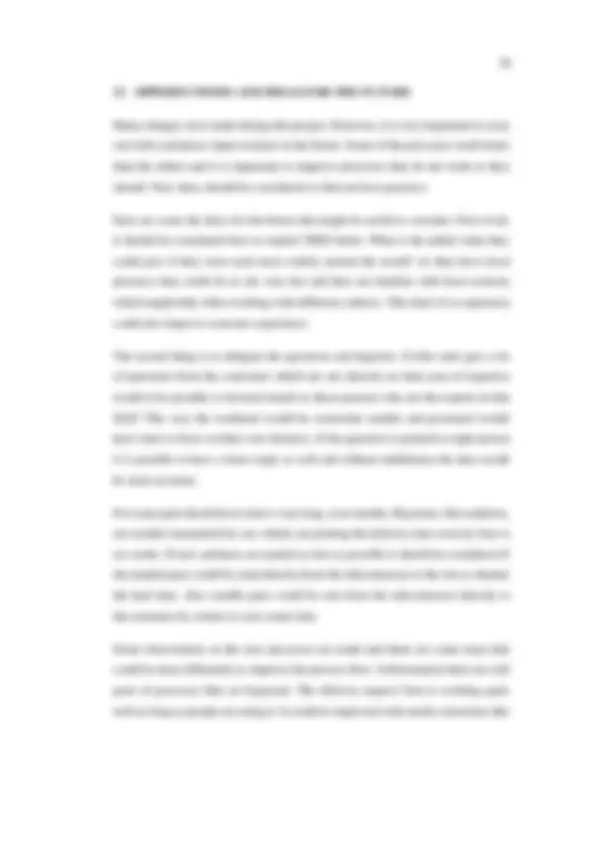
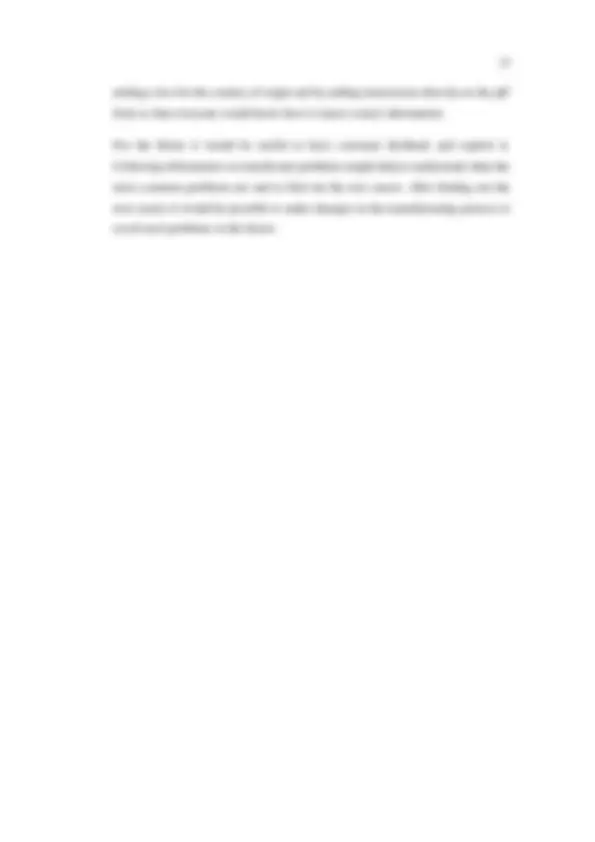


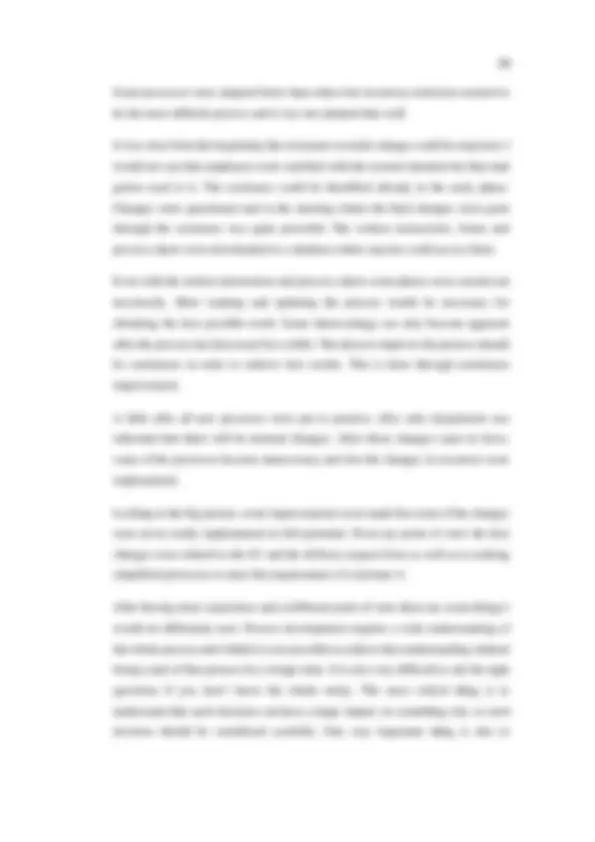
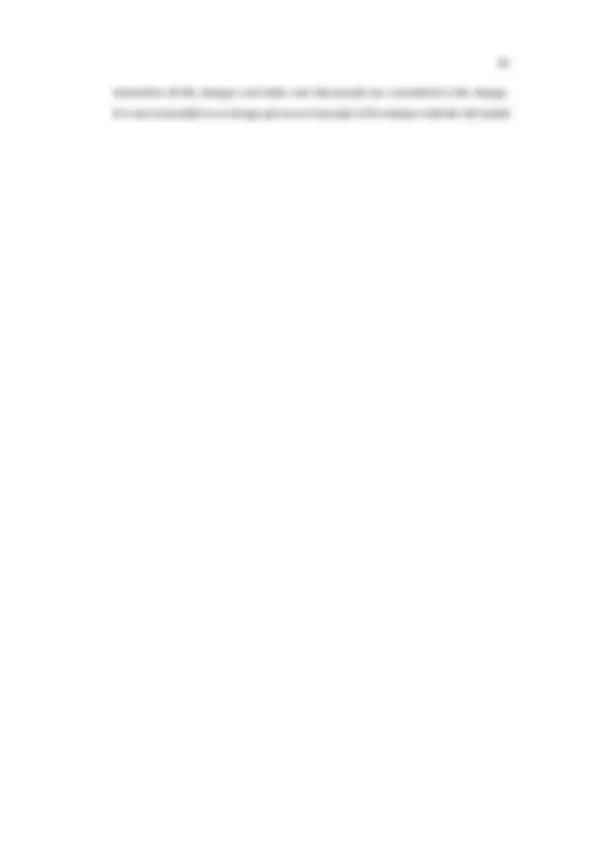
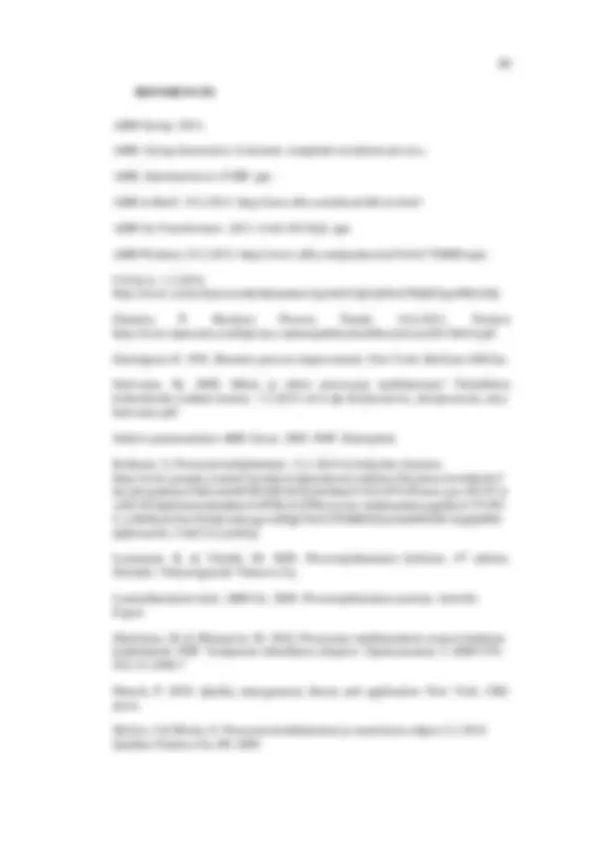
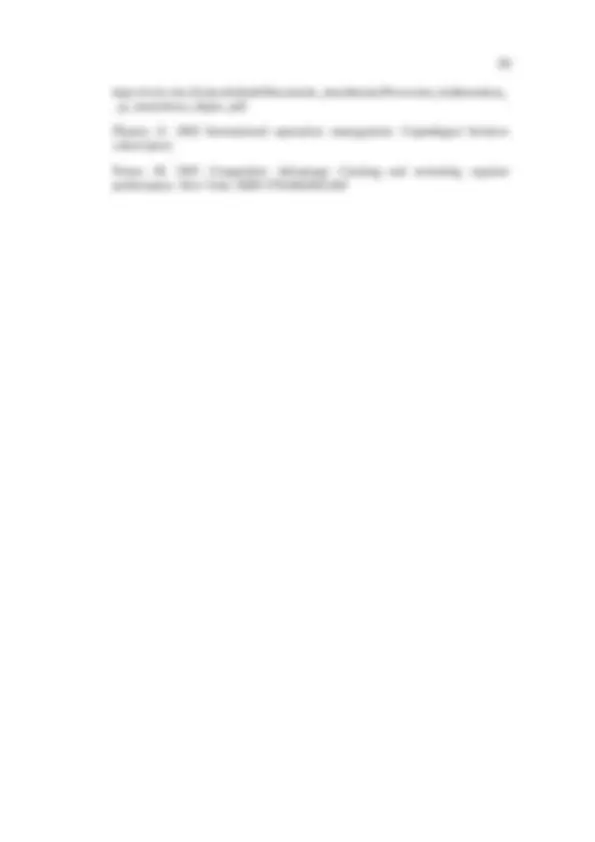
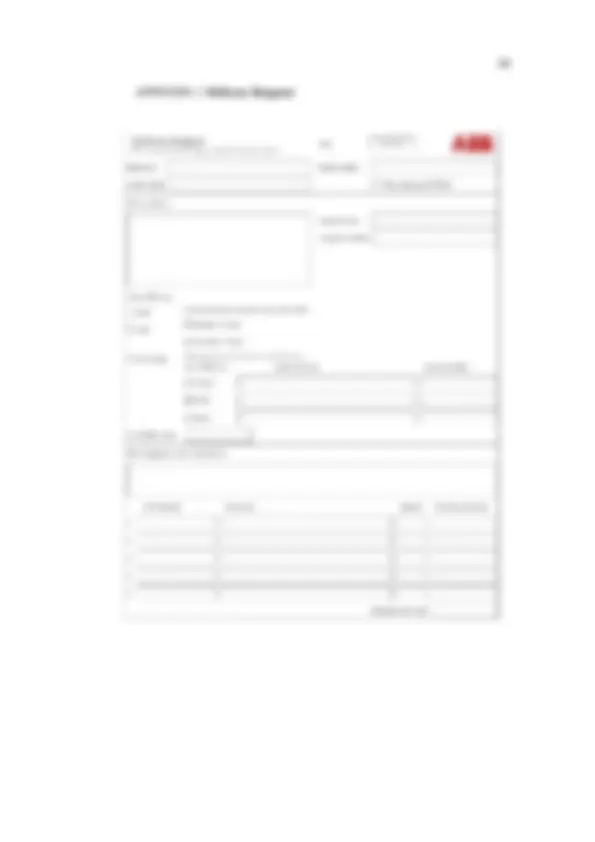
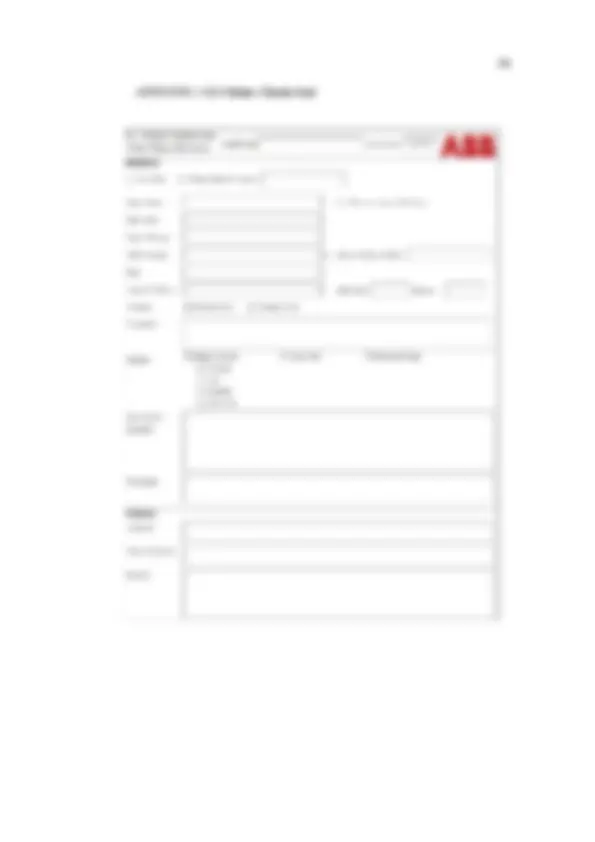
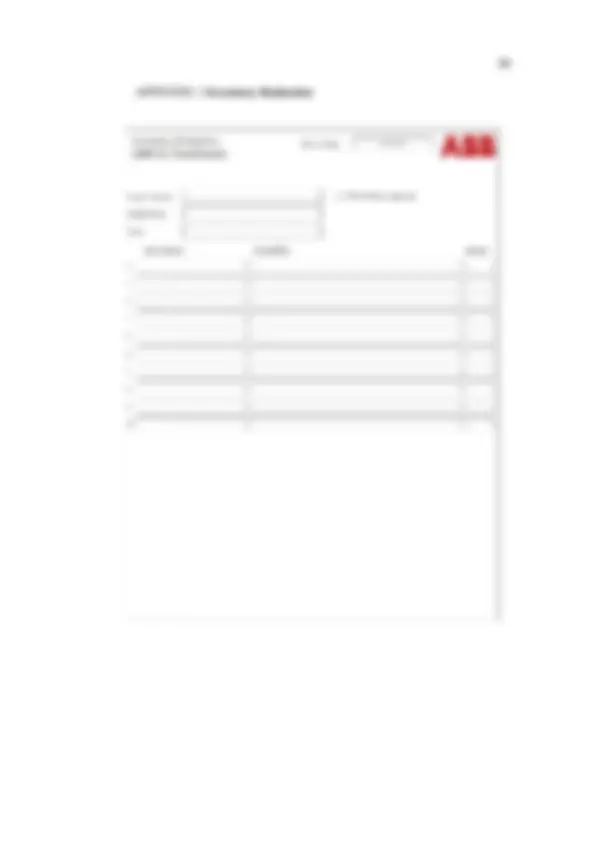
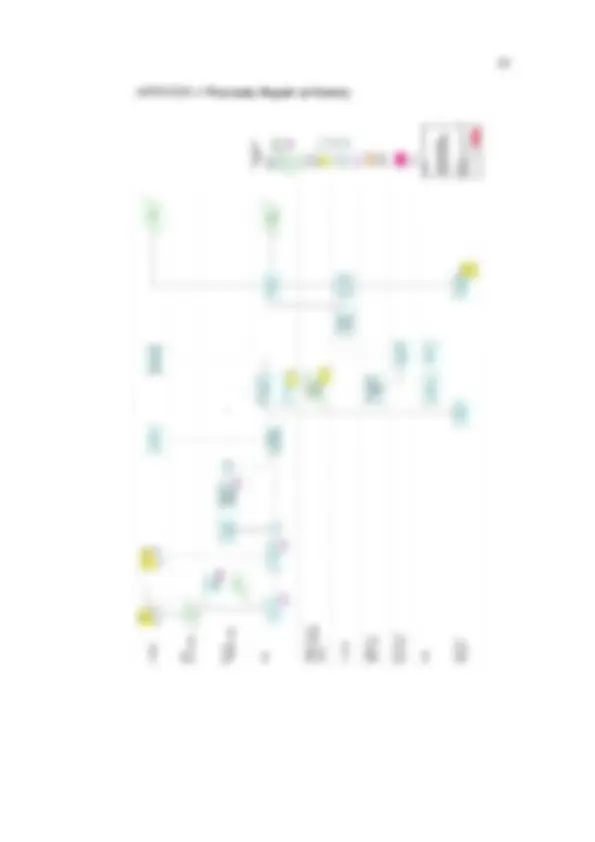
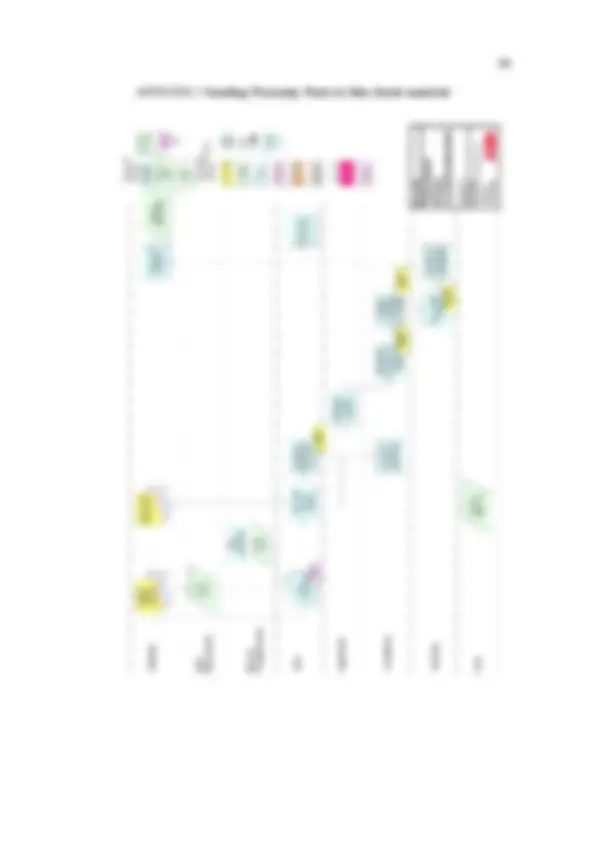
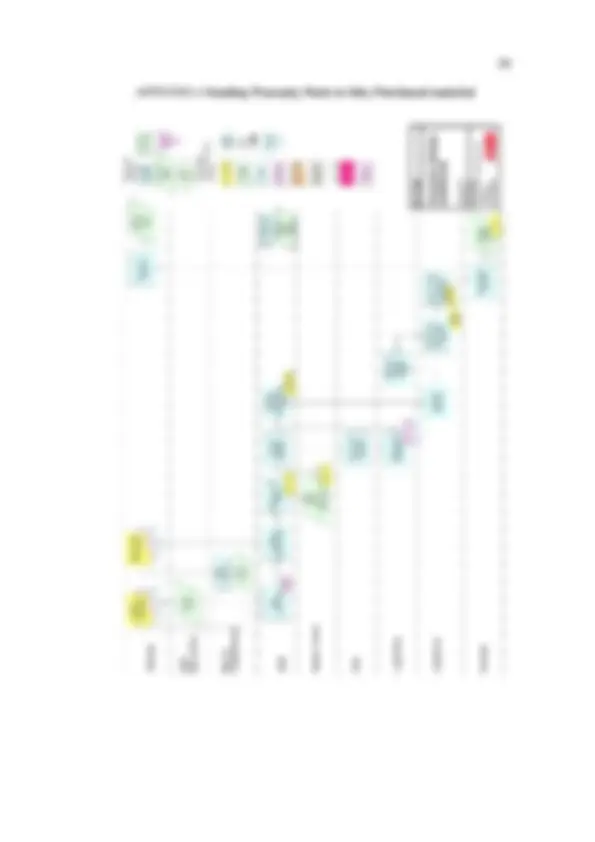
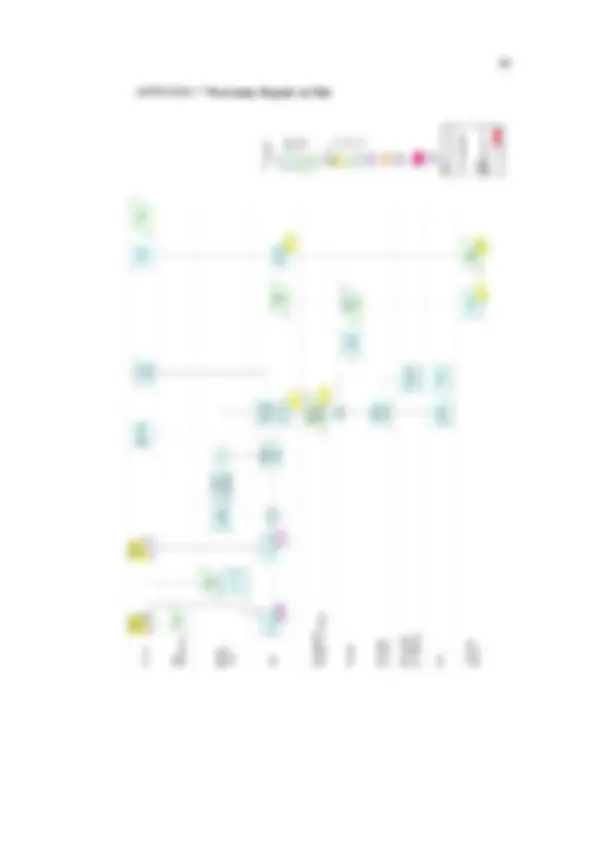
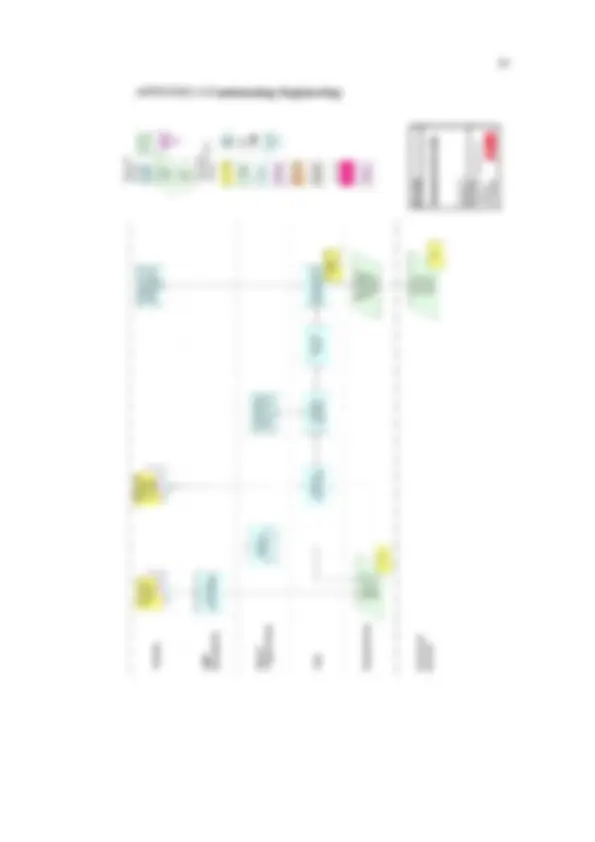
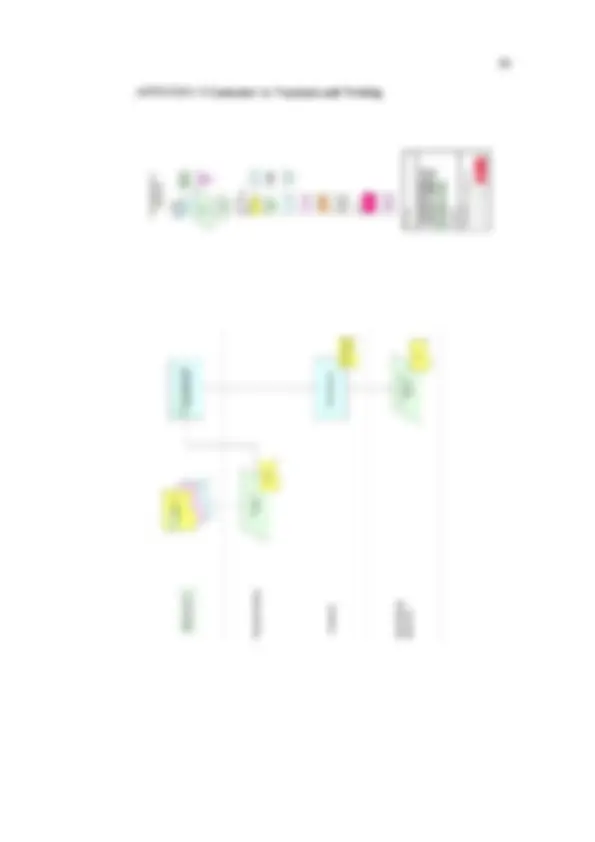
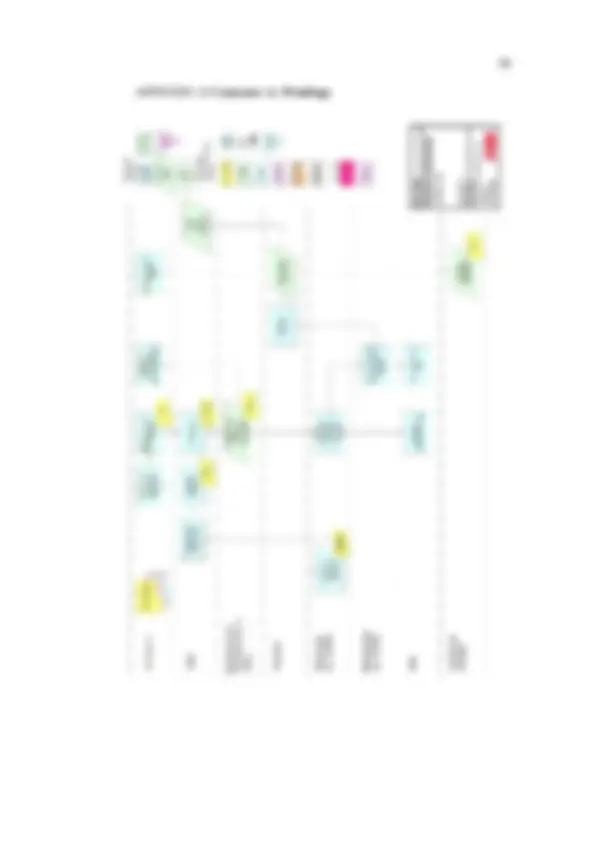
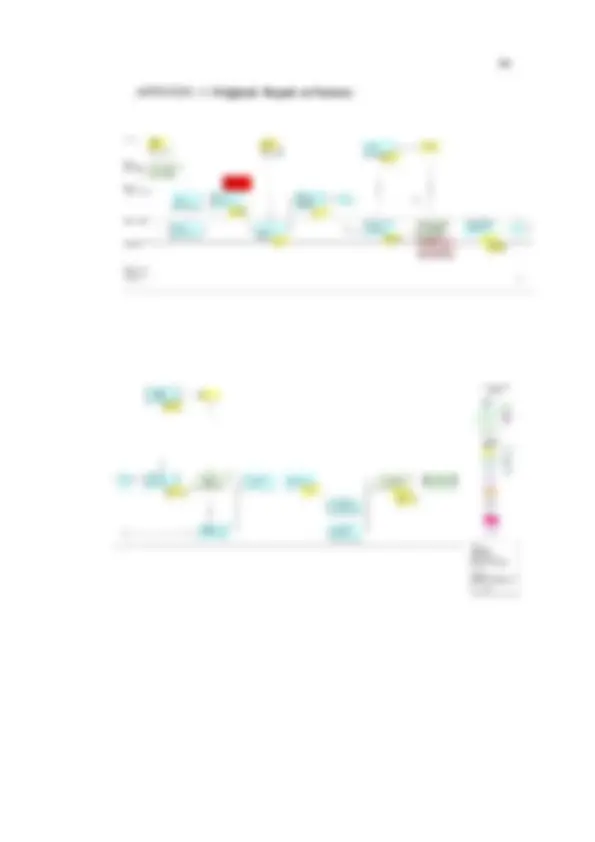
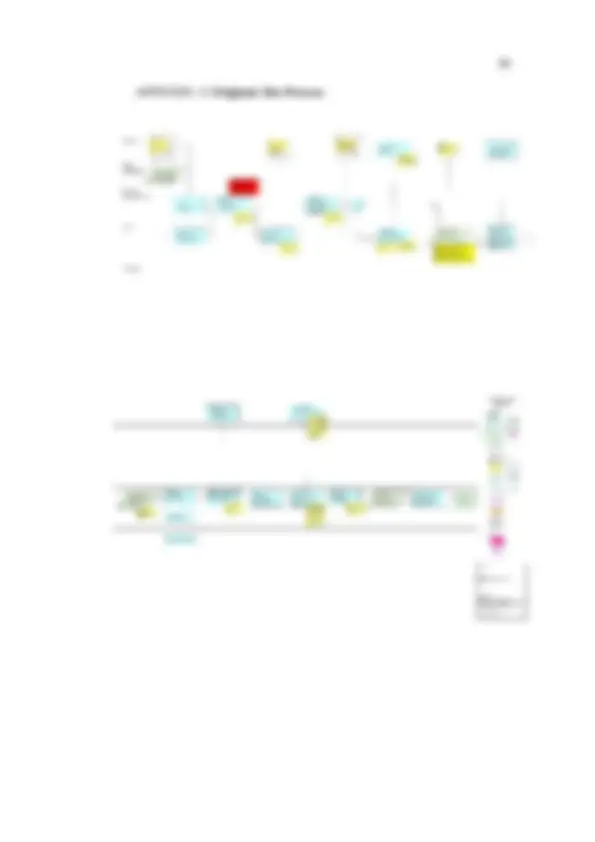
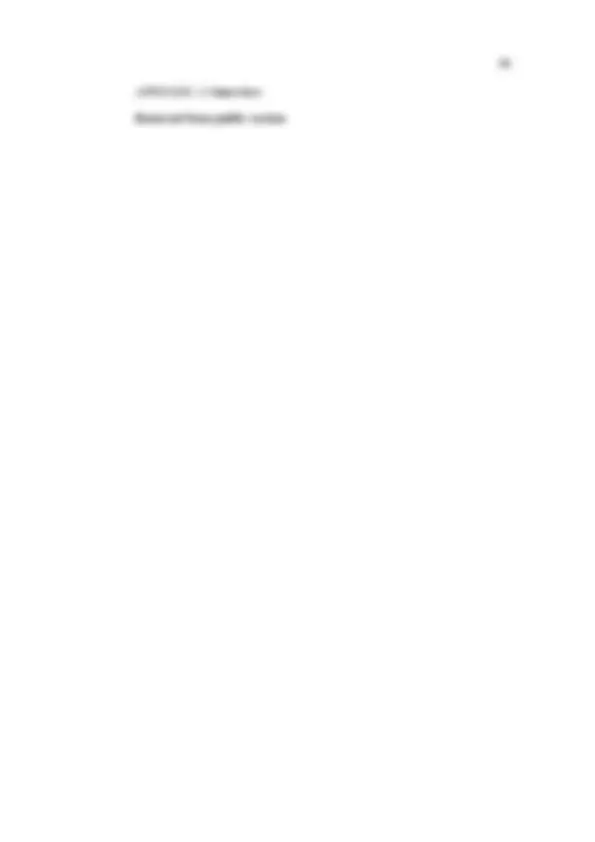
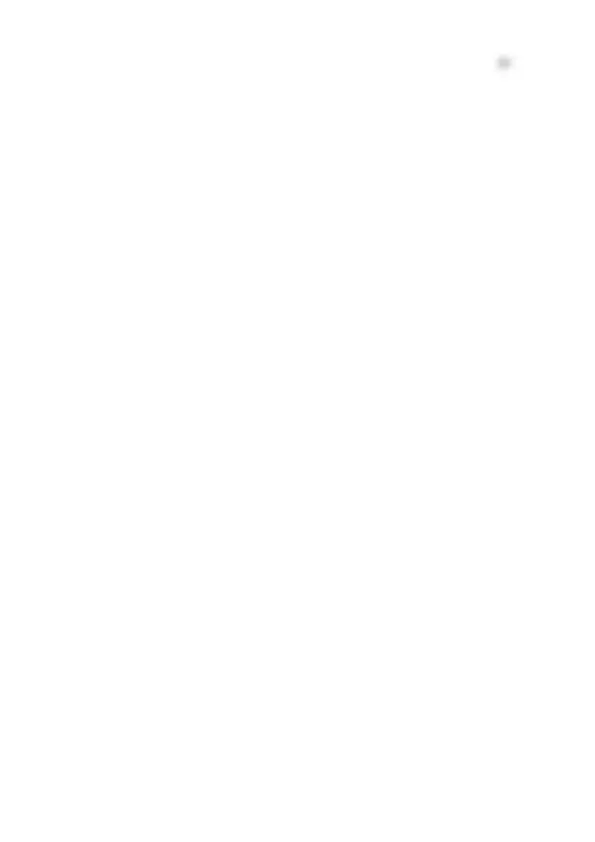
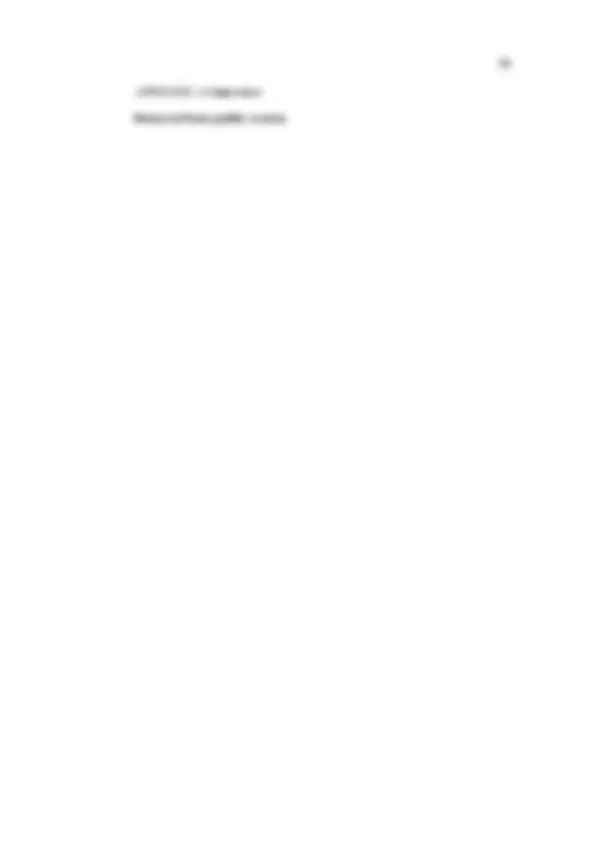
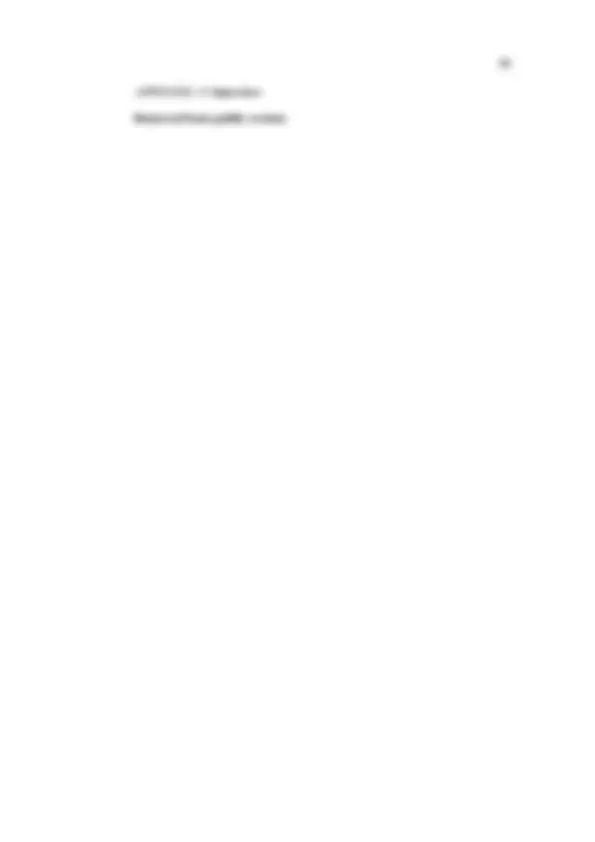
Study with the several resources on Docsity
Earn points by helping other students or get them with a premium plan
Prepare for your exams
Study with the several resources on Docsity
Earn points to download
Earn points by helping other students or get them with a premium plan
Community
Ask the community for help and clear up your study doubts
Discover the best universities in your country according to Docsity users
Free resources
Download our free guides on studying techniques, anxiety management strategies, and thesis advice from Docsity tutors
This thesis explores the after sales processes of ABB Oy Transformer and identifies challenges to make them more stable and efficient. The study is based on process development, focusing on process description, process modelling, and continuous improvement. New processes were introduced in 2013 but require continuous improvement. Keywords: process, process development, process modelling, continuous improvement.
What you will learn
Typology: Summaries
1 / 100
This page cannot be seen from the preview
Don't miss anything!
International Business
Tekijä Varpu Pajukoski Opinnäytetyön nimi Jälkimarkkinointiprosessien kehittäminen Vuosi 2015 Kieli Englanti Sivumäärä 83 + 15 Ohjaaja Kim Skåtar
Globalisaatio, tietoverkkojen kehitys, lisääntynyt liikkuvuus sekä monet muut tekijät ovat muuttaneet merkittävästi organisaatioiden toimintaympäristöä vuosien saatossa. Jotta uusiin haasteisiin voidaan vastata tehokkaasti, tulee päivittäisen tekemisen olla sujuvaa ja tehokasta. Tämän opinnäytetyön tarkoituksena on kartoittaa ABB Oy Muuntajien jälkimarkkinointiprosesseja sekä niissä esiintyviä haasteita, jotta nykyisiä prosesseja voidaan tehostaa ja tehdä niistä vakaampia.
Teoreettinen viitekehys rakentui prosessin kehittämisen ympärille. Prosessin kehittämisen lähtökodaksi tarkentui itse prosessi ja sen määritelmä, josta oli luontevaa jatkaa prosessin kehittämiseen ja sen eri vaiheisiin. Lisäksi korostui prosessin mallintaminen ja jatkuva parantaminen, jotka ovat tärkeä osa prosessin kehittämistä.
Tutkimuksen aikana paljastui useita ongelmakohtia. Suurimmat ongelmat liittyivät tiedonkulkuun sekä selkeiden toimintamallien puuttumiseen, joka puolestaan aiheutti epävakautta prosessissa. Koska jälkimarkkinoinnin resurssit ovat rajalliset, oli erityisen tärkeää keventää prosesseja mahdollisuuksien mukaan. Tämän työn puitteissa tehtiin uudet prosessikuvaukset, joilla pyrittiin selkeyttämään prosesseja. Uudet prosessit otettiin käyttöön vuonna 2013, mutta parhaan hyödyn saamiseksi ne vaativat jatkuvaa parantamista. Prosessinkuvauksia tulisi jatkossa päivittää tarpeen mukaan ja muuttaa tarvittaessa olemassa olevia käytäntöjä.
Avainsanat Prosessi, prosessin kuvaus, prosessin kehittäminen, mallinnus, jatkuva parantaminen
9
1 INTRODUCTION
The operating environments of organizations’ are undergoing fundamental changes due to globalization, increased mobility, e-business models, new productivity requirements as well as evolution of information networks and digitalization. This has increased the importance of competence, speed, flexibility and innovativeness. This kind of complexity has made organizations to become more specialized and to focus their know-how on smaller areas. (Laamanen & Tinnilä, 2009)
Process modeling and development has been an essential means of improving company’s performance since the 1970’s. Process thinking has been a central part of Japanese quality philosophy for decades and it has also had a strong influence on western production operations. It can be applied to almost every private business, to public administration as well as to non-profit organizations to increase their performance. (Martinsuo, M. & Blomqvist, M., 2010, 3)
The key features of process thinking are systematic thinking, issue-centered thinking, goal orientation, focusing on value adding actions, utilization of feedback as well as systematic improvement of the performance by improving the process. Process thinking is often related to removing the unnecessary work and making the work more efficient. Sometimes process thinking can also highlight tools, documentation and information systems since they are important ways of spreading the practices and automate work phases. (Martinsuo, M. & Blomqvist, M., 2010,
Even though the goals are quite the same, the means of how to achieve the goals are different from those used previously. Hard personal goals have been changed to organization-wide co-operation and emphasis on team-work. The focus on cost- effectiveness has been expanded to cover also speed and flexibility. The relationship between the supplier and the customer has changed – before suppliers had to compete for bids and the customers were seen as a necessary sales targets whereas now they are partners in a value-creating network. (Laamanen & Tinnilä, 2009, 7)
10
The main aim of this study is to find out how a process can be improved and what the effects are in real life. In today’s world we are forced to find out better practices to be competitive. By improving processes we are able to create steadier processes with less errors and also to reduce costs which is very important factor in today’s business world as well. I am choosing this topic because I have worked for a case company and seen the problems in its every day operations. It seems that by improving the process it could be possible to improve the flow of information and to make the work easier and more transparent. This could help several departments, shorten lead times and make the process steadier. Unnecessary work could be avoided and even customer satisfaction could be eventually increased.
1.1 Problem Statement
The research problem is to improve the case company’s after sales process. In order to solve this problem, the following plan is made. The first objective is to examine the existing processes and examine how well the existing process charts describe the current situation. This is done by working in group gathered from different departments and also by conducting interviews. The second objective is to analyze sales statistics and to find out what tools and resources are available. By examining this data it will be possible to find out some areas of improvement. The third objective is to set the target state and see what kind of changes should be made in order to reach the target state. Finally, the changes will be implemented in practice.
1.2 Structure of the Study
The theoretical study is divided into four main sections. The first section is about the process; what the process is and how it can be divided into different groups. The second section is about process development. It shows the principles of process development as well as finds out why the process is going through changes, how the changes should be made and what the goals are. The third section reveals what process modeling is and why and how to model a process. The final section, continuous improvement, is an important area of process development so that the improvements are made also in the future and the process is developed further as
12
2 PROCESS
In this chapter a basic description of a process is introduced. This will give the basic knowledge on what is meant by process and how it can be divided into smaller areas like for example core and support process or current and target process.
2.1 Description
Any activity or change can be described as a process. Process is a set of logically related activities and resources which are used to transform inputs to outputs. (Laamanen & Tinnilä 2009, 121-122) It is an entity that is assembled from multiple actions and tasks and it is a way of working efficiently and seamlessly in order to fulfill a customer’s needs. (Laatujohtamisen tiimi 2009, 2)
Process is a chain of actions that creates added value to the customer and in which a company uses its resources. A customer can be an internal or an external customer, known or unknown but there are always expectations, needs and demands from the customer towards the process. (Martinsuo & Blomqvist 2010, 4) A process can go from customer to customer crossing departmental and organizational boundaries. (Laamanen & Tinnilä 2009, 121-122) Pocess creates added value to the inputs when transforming them into outputs. Added value is related to the customer’s expectations, needs or demands and as an output it can mean, for example, a product, a solution or a service. (Martinsuo & Blomqvist 2010, 4)
Process may involve any part of the company’s business or other organizations’ activities seeking for benefits; creation of new innovations, production, products and services, finance or customer relations etc. (Martinsuo & Blomqvist 2010, 3) In a process the value adding action is formed from several actions connected to each other. The chain of actions can be simple or complicated, pre-determined or un-determined. Resources like raw material, labor, capacity, money, equipment or information are needed in the process. Resources can be owned by the company or acquired externally but they always cause costs and the resources available are limited. (Martinsuo, M. & Blomqvist, M., 2010, 4)
13
The basic elements of efficient processes are functional processes, efficient production equipment as well as advanced practices. Operational excellence is built on these factors and it aims at a work culture where problem solving, development and an innovative mindset are seen as an asset. (Jatkuva Parantaminen ABB Oy:ssa 2005, 5)
The process starts from the customer’s needs and ends after the needs have been fulfilled (Laatujohtamisen tiimi ABB Oy 2009, 2). The relationship between the customer and the company is extremely important. In the business world the interest is mainly in those processes which are critical to success. These processes are known as key processes, business processes or main processes and are often presented by using process charts. (Laamanen & Tinnilä 2009, 121-122) It is very important for companies to lead and guide their processes in order to reach their objectives (Martinsuo & Blomqvist 2010, 5).
2.2 Process Division
Especially in the business world there is a difference between process and business process. Business process describes those processes which are used to make money whereas process can describe any process. (Martinsuo & Blomqvist 2010, 3) This study deals with processes in general.
2.2.1 Core and Support Process
Processes can be divided into core and support processes. Core processes are always connected to external customer whereas support processes are internal and support core processes. Different level processes are called main process, sub process and part process. The main process can be divided into several sub or part processes and in that way it can be modeled on several levels. (Martinsuo & Blomqvist 2010, 4)
Porter’s value chain (Porter 1985, 87), presented below in Figure 1., shows the core and support processes. The core processes are flowing across the bottom of the figure whereas the support processes are layered above them. Together they form the margin. (Harmon 2011)
15
Core processes are critical to a company’s success. (Martinsuo & Blomqvist 2010,
Support process is critical for the functionality and improvement of the core process. Processes that support core processes are, for example, strategic planning, financial planning and information systems maintenance. (Laatujohtamisen tiimi ABB Oy 2009, 2.)
A core process can be divided in to sub processes. As an example a sales process can be separated from the order-delivery process. A key process, on the other hand, can be core, support or even sub process but it is always an essential process for the company’s success. (Laatujohtamisen tiimi ABB Oy 2009)
2.2.2 Current and Target Process
A current process describes the current situation and a target process describes the process as it should be in order to fulfill the goals of performance. The difference between a current process and a target process shows the concrete changes that should be made in order to reach the target. (Martinsuo, M. & Blomqvist, M., 2010,
16
3 PROCESS DEVELOPMENT
Process development is a wider concept that includes process improvement. This chapter introduces the basics of process development and improvement. The development process is led by process owners who are in charge of development, whereas the involvement of employees is more important in process improvement. In this chapter, also the goals and reasons behind the changes are discussed as well as typical areas of improvement.
3.1 Description
Process development begins by understanding the process. Even the hardest work is not enough if the entity is not in control and processes are unclear. A functional process requires continuous listening of the customer, common goals and measurements in the organization, fluent flow of information and material, well planned, instructed and trained actions, quick response to changing conditions and know-how. (Laatujohtamisen tiimi 2009, 4-5)
The aim is to change the process so that it becomes more effective and it focuses directly on action. People are not expected to do more but to do things differently. (Laamanen & Tinnilä 2009) Tasks are done in their natural order and place. Loops, waste and work in progress are minimized so that work would be smooth, clear and as fast as possible. (Martinsuo, M. & Blomqvist, M., 2010, 14)
Process development includes both process modelling, and process improvement and measurement. Process modelling produces process descriptions which can describe either the current or the target state. Current state descriptions show the current ways of working and how different functions and tasks work together whereas target state descriptions works as a plan for creating and implementing new ways of working. Process development must to be aligned as a part of organizational development. (COALA, 1.2.2014)
A customer can be internal or external but the customer always values on-time deliveries, high-quality products and services and, of course, a competitive price. This makes reliability and fluent processes high in priority. In Figure 3. unclear and
18
a process as well as continuous improvement. A development projects are usually bigger changes that require bigger investments. Development process starts when there is a problem that needs to be solved. (Kollanus, S. 2014) In the following two chapters two different approaches are presented.
3.2.1 Principles of Process Development by Moisio and Ritola
According to Moisio & Ritola (2005) there are four steps of process development and they are shown in Figure 4. The first step of process development is to identify the process. It includes grouping but also defining limitations that will help in seeing the process. If there are no limitations the process will be never ending and there will be problems in the next step which is process modeling. (Moisio & Ritola 2005, 6.)
Process modeling helps to see the process as a whole and how different parts of the process are linked to each other. The third step is to implement the process in daily operations. This phase needs to have full support from the management because it is important get the whole organization to commit to the change. (Moisio & Ritola 2005, 6.)
The fourth step is continuous improvement. The process can be developed even further by measuring, analyzing, evaluating and comparing information and experiences received from the implemented processes. After finding out the problems in the processes it is good to return to process modeling to fix the problems. (Moisio & Ritola 2005, 6.)
Figure 4. Steps of process development by Moisio and Ritola.
Principles of process development are shown in Figure 5. systematic process development model by Moisio and Ritola (2005). When developing a better process
19
there are a lot of factors to consider. It is important to listen to the customer, reduce unnecessary work, simplify the process and take advantage of the opportunities offered by the technology among others.
Figure 5. Systematic process development model by Moisio and Ritola (2005).
3.2.2 Principles of Process Development by Martinsuo & Blomqvist
Developing a company’s performance through processes can mean extensive transition to process related approach, introduction of one new process, re- engineering or making smaller improvements to the existing processes. Even though these development methods are implemented differently, there are some basic steps that are similar and are shown in figure 6. (Martinsuo & Blomqvist 2010, 6)